拉深件缺陷与消除
拉深加工的质量缺陷分析及对策

? " / / A
图1 压边 圈不平所 产生的制件缺 陷
圈
一处
图3 凸模中心线与凹模平面不垂直时所产生的制件缺陷
对策 :检查 凸 凹模轴 心 线 是 否 由于长 期振 动 而 不 重 合 ,压 边 圈螺 钉是 否 长短 不 一 ,凹模 几 何形 状
2 . 拉深件 表面 出现起皱 、裂纹或破裂现象
圆筒 件 边 缘 褶 皱 ( 见 图4 ) 。原 因分 析 :凹 模 圆角半 径 太大 ,在拉 深 过程 的 末 阶段 ,脱离 了压边 圈 ,但 尚未超 过 凹模 圆角 材料 ,压边 圈压不 到 ,起
皱 后被 继 续拉 入 凹模 ,形 成边 缘 褶皱 。对 策 :减 小
半 径 ,使 之 保持 均 匀 。 ( 3 )制 件 侧 壁 高 低 不 一 ,薄 厚 不 一 。原 因分 析 :模具 定 位部 分 产 生偏 差 或板 料 定 位板 的 中心 与
凹模 中 心不 重 合 。对 策 :检 查 凸凹模 中心 线 是 否共
凹模 圆角半 径 或采 用 弧形 压边 固。
部位 即凹模的圆角部位 。 原 因分析 :在 拉深 中 ,凹模 圆角部位压 力很
图5 工件壁部拉 毛
大 ,因而 滑 动面 的摩 擦 阻 力很 大 ,会产 生 可能 达 到
( 2 )检查 凸凹模是否 存在间隙不均匀 ,或研
配不 好 、导 向不 良等 问 题造 成 局 部 压料 力增 高 ,使 侧 面 产 生局 部 接 触 划 痕 或变 薄 性 质 的擦 伤 。对 策 : 调 整 凸 凹模 间 隙使 其 均 匀 ,保 证 凸凹模 工作 部 位 的 研 配 质量 ,保证 凸 凹模 工 作表 面 低 的表 面 粗 糙 度 值 和 尺 寸 的一 致 性 。
拉深件缺陷及消除(共261张精选PPT)

深拉深破裂
⑤ 模具安装不良。 该缺陷是由模具安装不良,上下模不对中所造成的。近来,几乎所有的模
具都备有导向装置,由于模具不对中产生的故障已很少见。
⑥ 缓冲销的长短不齐。 缓冲销在使用过程中,由于出现压弯,冲击伤痕等,往往变得长短不一,拉深过程
拉深件缺陷及消除
一. 深拉深破裂 二. 胀形破裂
三. 凸缘延伸裂纹
四. 纵弯曲折皱 五. 壁增厚折皱
六. 表面精度不良 七. 表面形状不良
拉深件缺陷及消除
一. 深拉深破裂
1. 凹模肩部相应部位裂纹
2. 壁破裂
3. 纵向破裂
4. 自然时效破裂
5. 凸模肩部相应部位裂纹 6. 直边壁破裂
因此,在进行深拉深时,要尽量减少拉深引起的磨擦,另外,还需要同时考虑积极 的冷却方案。
深拉深破裂
③ 毛坯形状不当。 根据经验,在试拉深阶段产生壁破裂时,只要改变毛坯形状,就可消除缺陷,这种
实例非常多。 拉深方筒时,首先使用方形毛坯进行拉深,rd部位如果产生破裂,就对毛坯四角进
行切角。 在此阶段,如果发生倒W字形破裂和网格疵病,则表示四角的切角量过大。切角的
深拉深破裂
原因及消除方法
(1)制品形状。 ① 拉深深度过深。 由于该缺陷是在深拉深时产生的,如将拉深深度降低即可解决。但是
必须按图纸尺寸要求进行拉深时,用其他方法解决的例子也很多。 ② rd、rc过小。
由于该缺陷是在方筒角部半径(rc)过小时发生的,所以就应增大rc。 凹模圆角半径(rd)小而进行深拉深时,也有产生壁破裂的危险。如果 产生破裂,就要好好研磨(rd),将其加大。
深拉深破裂
③ 凹模尺寸(rd)过小。 a 将rd修正到适当值。 b 图纸上的rd过小时,首先用适当rd值进行拉深,然后再增加一道工序,
拉深件常见质量问题及预防措施
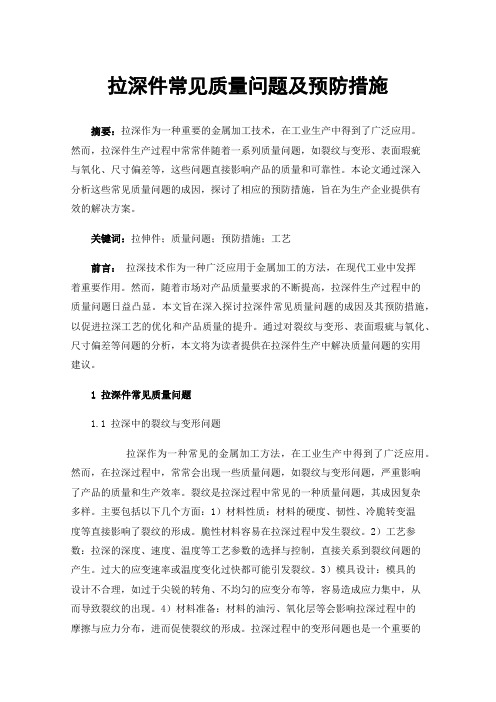
拉深件常见质量问题及预防措施摘要:拉深作为一种重要的金属加工技术,在工业生产中得到了广泛应用。
然而,拉深件生产过程中常常伴随着一系列质量问题,如裂纹与变形、表面瑕疵与氧化、尺寸偏差等,这些问题直接影响产品的质量和可靠性。
本论文通过深入分析这些常见质量问题的成因,探讨了相应的预防措施,旨在为生产企业提供有效的解决方案。
关键词:拉伸件;质量问题;预防措施;工艺前言:拉深技术作为一种广泛应用于金属加工的方法,在现代工业中发挥着重要作用。
然而,随着市场对产品质量要求的不断提高,拉深件生产过程中的质量问题日益凸显。
本文旨在深入探讨拉深件常见质量问题的成因及其预防措施,以促进拉深工艺的优化和产品质量的提升。
通过对裂纹与变形、表面瑕疵与氧化、尺寸偏差等问题的分析,本文将为读者提供在拉深件生产中解决质量问题的实用建议。
1拉深件常见质量问题1.1 拉深中的裂纹与变形问题拉深作为一种常见的金属加工方法,在工业生产中得到了广泛应用。
然而,在拉深过程中,常常会出现一些质量问题,如裂纹与变形问题,严重影响了产品的质量和生产效率。
裂纹是拉深过程中常见的一种质量问题,其成因复杂多样。
主要包括以下几个方面:1)材料性质:材料的硬度、韧性、冷脆转变温度等直接影响了裂纹的形成。
脆性材料容易在拉深过程中发生裂纹。
2)工艺参数:拉深的深度、速度、温度等工艺参数的选择与控制,直接关系到裂纹问题的产生。
过大的应变速率或温度变化过快都可能引发裂纹。
3)模具设计:模具的设计不合理,如过于尖锐的转角、不均匀的应变分布等,容易造成应力集中,从而导致裂纹的出现。
4)材料准备:材料的油污、氧化层等会影响拉深过程中的摩擦与应力分布,进而促使裂纹的形成。
拉深过程中的变形问题也是一个重要的质量挑战,材料的弹性模量、塑性变形能力等直接影响了变形的程度。
材料越脆性,变形越容易导致失真,并且不均匀的应变分布会引发不均匀的变形,从而造成拉深件的形状不准确。
此外,模具刚度不足会导致变形过大,模具变形甚至破坏,进而影响拉深件的准确性,拉深过程中的温度、压力等工艺参数的控制不当,都会导致不良的变形。
拉伸件、弯曲件缺陷及消除

目录【深拉深破裂】凸模肩部相应部位裂纹 (1)壁破裂 (2)纵向破裂 (3)自然时效破裂 (5)凹模肩部相应部位裂纹 (5)直边壁破裂 (5)侧壁端面裂纹 (6)侧壁纵向裂纹 (7)【胀形破裂】凹模肩部相应部位裂纹 (7)凸模肩部相应部位裂纹 (8)胀形时凸模棱线部位产生裂纹 (9)【凸缘延伸裂纹】凸缘延伸边缘裂纹 (9)凸缘延伸内裂纹 (9)凸缘延伸侧壁裂纹 (10)【纵弯曲折皱】凸缘折皱 (10)壁折皱 (11)薄壁容器筒体拉深皱纹、拉深筒体皱折 (14)不均匀拉伸折皱 (14)剪切折皱 (15)发生于凸模底部的纵向弯曲 (16)【壁增厚折皱】复杂形状的壁折皱 (16)由于拉深深度变化而引起的折皱 (17)在凸模纵断面形状急骤变化部位产生的壁增厚折皱 (18)反弯曲形、鞍形、葫芦形的壁减薄折皱 (19)【表面精度不良】折线 (20)冲撞痕线 (21)线偏移 (23)臌凸 (25)扭曲 (27)模子印痕 (27)弓背形 (27)凹陷 (28)收缩、垂驰 (28)模具碰撞伤痕 (29)麻点 (29)真空变形和排气伤痕 (30)【表面形状不良】表面粗糙 (31)拉伸滑带 (31)弯曲件缺陷及消除 (32)回弹 (32)弯曲裂纹 (34)弯曲线垂直度不好 (34)翘曲 (35)冲撞缺陷 (35)折边形状左右不对称 (36)扭曲 (36)孔精度不好 (36)进行V形弯曲时引起直边弯曲 (36)臌凸 (37)形状精度不好 (37)凸模肩部相应部位裂纹由于材料的强度不够,当拉深载荷达到材料破断载荷时就会发生此缺陷。
缺陷部位产生于凸模肩R相应的部位(r p处),即比冲撞痕线更接近r p的部分。
破裂部分的冲撞痕线,因与其他部位不同,可以对下面几种情况进行观察检查:或者被延展;或者在凸缘的上下面有发亮的部分;或者产生折皱。
另外,在侧壁上有时也有发亮的部分。
初期横向破裂,呈舌状。
如图1。
原因及消除方法(1)制品形状。
拉深缺陷及解决措施2(DOC)
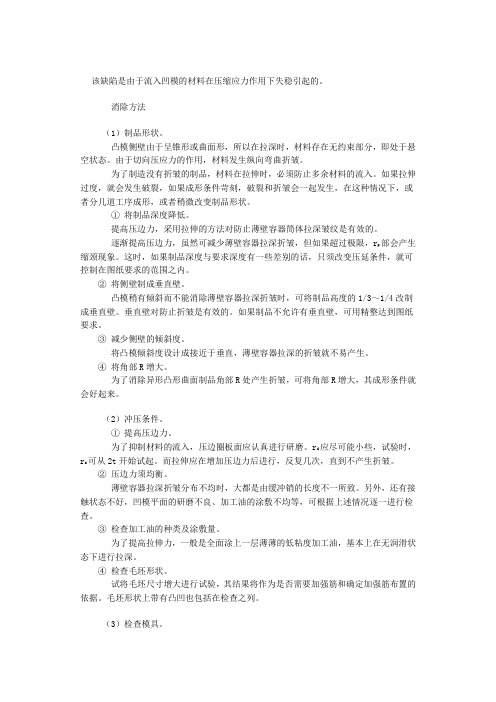
该缺陷是由于流入凹模的材料在压缩应力作用下失稳引起的。
消除方法(1)制品形状。
凸模侧壁由于呈锥形或曲面形,所以在拉深时,材料存在无约束部分,即处于悬空状态。
由于切向压应力的作用,材料发生纵向弯曲折皱。
为了制造没有折皱的制品,材料在拉伸时,必须防止多余材料的流入。
如果拉伸过度,就会发生破裂,如果成形条件苛刻,破裂和折皱会一起发生,在这种情况下,或者分几道工序成形,或者稍微改变制品形状。
① 将制品深度降低。
提高压边力,采用拉伸的方法对防止薄壁容器筒体拉深皱纹是有效的。
逐渐提高压边力,虽然可减少薄壁容器拉深折皱,但如果超过极限,r p部会产生缩颈现象。
这时,如果制品深度与要求深度有一些差别的话,只须改变压延条件,就可控制在图纸要求的范围之内。
② 将侧壁制成垂直壁。
凸模稍有倾斜而不能消除薄壁容器拉深折皱时,可将制品高度的1/3~1/4改制成垂直壁。
垂直壁对防止折皱是有效的。
如果制品不允许有垂直壁,可用精整达到图纸要求。
③ 减少侧壁的倾斜度。
将凸模倾斜度设计成接近于垂直,薄壁容器拉深的折皱就不易产生。
④ 将角部R增大。
为了消除异形凸形曲面制品角部R处产生折皱,可将角部R增大,其成形条件就会好起来。
(2)冲压条件。
① 提高压边力。
为了抑制材料的流入,压边圈板面应认真进行研磨。
r d应尽可能小些,试验时,r d可从2t开始试起。
而拉伸应在增加压边力后进行,反复几次,直到不产生折皱。
② 压边力须均衡。
薄壁容器拉深折皱分布不均时,大都是由缓冲销的长度不一所致。
另外,还有接触状态不好,凹模平面的研磨不良、加工油的涂敷不均等,可根据上述情况逐一进行检查。
③检查加工油的种类及涂敷量。
为了提高拉伸力,一般是全面涂上一层薄薄的低粘度加工油,基本上在无润滑状态下进行拉深。
④ 检查毛坯形状。
试将毛坯尺寸增大进行试验,其结果将作为是否需要加强筋和确定加强筋布置的依据。
毛坯形状上带有凸凹也包括在检查之列。
(3)检查模具。
① 加强拉伸的结构。
汽车覆盖件拉深成型缺陷产生的原因和解决措施

39中国设备工程Engineer ing hina C P l ant中国设备工程 2018.12 (上)1 汽车覆盖件的特点汽车覆盖件成型材料薄、结构尺寸大、形状复杂(多为立体曲面),不但要求具有特定的使用功能,而且要求有一定的观赏功能,被拉深的材料应经过充分的塑性变形,使制件有一定的刚性,有光顺挺拔的表面和均匀而清晰的棱线,不允许有缺陷,尺寸精度高,以保证装配准确。
2 汽车覆盖件的成型工艺汽车覆盖件通常采用高强度、高质量、抗腐蚀的钢板,成型设备采用具有稳定压边力的双动压床或三动冲床。
汽车覆盖件冲压工艺编制、冲模设计、冲模制造工艺都有一些特殊的要求,汽车覆盖件模具常把落料、拉深、修边、翻边、冲孔工序进行组合设计,力求减少冲压工序,降低生产成本。
拉深、修边和翻边是最基本的工序,其中拉深工序是覆盖件冲压成型的关键工序,它直接影响产品质量、材料利用率、生产效率和制造成本。
模具在设计过程中采取有限元来分析冲压过程中板料的受力和流动方向,并通过结构设计控制板料受力的大小和流动方向,大大提高模具成型质量。
3 汽车覆盖件拉深成型缺陷产生的主要原因模具设计质量、模具零件的制造精度、模具的装配精度直接影响模具本身质量,是影响汽车覆盖件拉深成型缺陷产生的主要原因。
模具材料的机械性能(拉深系数、屈强比等)、模具的间隙大小、模具加工工艺和热处理工艺的选择、模具零件使用过程中的正常磨损、使用状况和保养、模具在机床上安装或使用不当都会造成汽车覆盖件拉深成型过程中缺陷产生。
冲压设备的精度也会影响汽车覆盖件拉深成型质量。
4 汽车覆盖件拉深成型缺陷分析及解决措施4.1 拉伤 图1 拉伤缺陷 图2 模具成型表面整体镀铬上图1为汽车顶盖,成型过程中在侧面经常产生拉伤,应检查模具以下技术状态。
(1)检查上道工序模具(制品)是否有划伤。
(2)检查本工序模具表面是否有划痕拉伤制品表面。
(3)检查模具成型表面是否因粗糙度未达到要求拉伤制品表面。
不锈钢盒形拉深件外观缺陷的消除方法
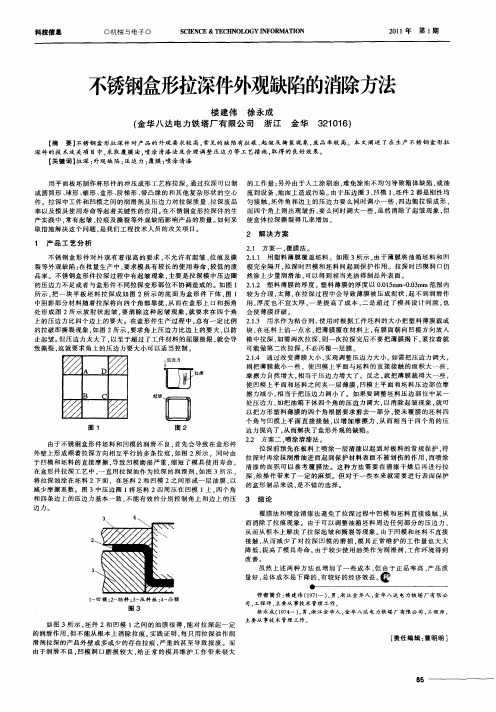
虽 然 上 述 两 种 方 法 也 增 加 了 一 些 成 本 , 由 于 正 品 率 高 、 品 质 但 产 量 好 , 体 成 本 是 下 降 的 , 较 好 的 经 济效 益 。 总 有
止 起 皱 。 压边 力 太 大 了 . 但 以至 于 超 过 了工 件 材 料 的屈 服 极 限 . 会 导 模 中拉 深 , 需 两 次 拉 深 , 一 次 拉 深 完 后 不 要 把 薄 膜 揭 下 , 就 如 则 紧拉 着 就 致 撕 裂 , 就 要求 角 上 的压 边 力 要 大 小 可 以适 当控 制 。 这 可能做第二次拉深 , 必再覆一层膜。 不 21 .. 通 过 改 变 薄膜 大 小 . 现 调 整压 边 力 大小 。 需 把 压边 力 调大 , 4 实 如 则 把 薄 膜 裁 小 一 些 ,使 凹 模 上 平 面 与 坯 料 的 直 接 接 触 的 面 积 大 一 些 , 摩 擦 力 自然 增 大 , 当 于 压 边 力 增 大 了 。 反 之 , 把 薄 膜 裁 得 大 一 些 , 相 就
1 一凹模 ;一坯 料 ;一 料 板 ;一凸模 2 3压 4
图 3
如 图 3所 示 , 件 2和 凹模 1之 间 的 油 膜 很 薄 , 对 拉 深 起 一 定 坯 能
的 润 滑作 用 , 不 能 从 根 本 上 消除 拉 痕 。 践 证 明 , 只 用 拉 深 油 作 润 但 实 每 滑 剂 拉 深 的 产 品外 壁 或 多 或 少 的存 在 拉 痕 , 重 的 甚 至 导 致 报 废 。 而 严
【 键 词 】 深 ; 缺 陷 ; 边 力 ; 膜 ; 涂 清 漆 关 拉 ,观 压 覆 喷 用 平 面 板 坯 制 作 杯 形 件 的冲 压 成 形 工 艺 称 拉 深 。 过 拉 深 可 以 制 的工 作 量 ; 外 由于 人 工 涂 刷 油 , 免 涂 油 不 均 匀 导 致 箱 体 缺 陷 , 油 通 另 难 或 成 圆筒 形 、 形 、 形 、 形 、 梯 形 、 凸 缘 的 和 其 他 复 杂 形 状 的 空 心 流 到 设 备 、 面 上 造成 污 染 。由于 压 边 圈 3 凹 模 1 坯 件 2都 是 刚 性 均 球 锥 盒 阶 带 地 、 、 坯 四 件 。拉 深 中工 件 和 凹 模 之 问 的 润 滑 剂 及 压 边 力 对 拉 深 质 量 、 深 废 品 匀 接 触 , 件 角 和 边 上 的 压边 力要 么 同 时调 小一 些 , 边 能 拉 深 成 形 , 拉 率 以及 模 具 使 用 寿 命 等 起 着 关 键 性 的 作 用 。 不 锈 钢 盒形 拉 深件 的生 而 四 个 角 上 则 出 现 皱 折 , 么 同 时调 大 一些 , 然 消 除 了 起 皱 现 象 , 在 要 虽 但 产 实 践 中 , 有 起 皱 、 痕 及 撕 裂 等 外 观 缺 陷 影 响 产 品 的质 量 。 何 采 使 盒 体 拉深 撕 裂 得 几 率 增 加 。 常 拉 如
拉深缺陷及解决措施3

图7 由r p引起的冲撞痕线图8 由拉深筋引起的冲撞痕线消除方法从制品上完全消除冲撞痕线的方法:① 成形异形制品时,需要改变凹模平面形状,凸模轮廓、凸模形状而进行引伸,以达到与使用拉深筋同样的效果。
② 如果允许反面有冲撞痕线,可用拉深筋控制材料只从反面流入。
③ 要使冲撞痕线在制品形状之外,可将拉深筋的位置向外移。
④ 增加工序。
例如,对方形筒拉深时,首先不用拉深筋进行拉深,在下一道工序时,在制品形状外安装拉深筋,能完全控制材料的流入,并增加拉深深度,去除回弹瘪陷。
⑤ 拉深拱面形时,将压边圈作成反锥形以代替拉深筋。
反锥的角度为6~8度。
将产生的冲撞痕线尽可能变浅。
① 将拉深筋半径(R)尽可能增大。
(R/t≥3~5)② 对拉深筋进行精加工。
③ 给拉深筋镀硬铬。
④ 用精整,反拉深等工艺,进行变薄拉深。
(4)成形过程中发生的冲撞痕线。
成形过程中,由于侧壁部拉力的急骤变化会产生这种冲撞痕线。
例如,坯料越过拉深筋顶部后拉力急骤下降,或者,凸缘延伸加工时,成形过程中由于切口或工艺孔、拉力急骤减少,都可能产生冲撞痕线。
消除方法① 由于毛坯尺寸小,在成形结束前毛坯就脱离拉深筋,造成上述缺陷时,或者将拉深筋的位置移向内侧,或者增大毛坯尺寸。
② 由于修整线以外部分拉伸破裂,壁部拉力急骤减少而产生冲撞痕线时,应采取防破裂措施。
③ 为了防止凸缘延伸部分破裂,可用切口或冲工艺孔的办法,但由此造成拉力减少而发生冲撞痕线。
通过切口和拉深筋并用,尽量避免拉力急骤减少,从而达到防止冲撞痕线的产生。
④ 有冲撞痕线的地方,通过精整等方法使之拉伸、变浅。
返回线偏移线偏移是指成形初期或过程中发生的棱线偏移,如果能模糊地看到制品的凸起部或棱线的R(半径)有大的偏移,或者能看到两根棱线,都称为线偏移。
外观很重要的制品,如发生折线、冲撞痕线、或者线偏移,都会影响表面质量。
尤其是发生线偏移时,在修整阶段难以消除,故在模具设计阶段,就应采取防止发生线偏移的措施,这一点非常重要。
拉伸模具常见缺陷及解决办法
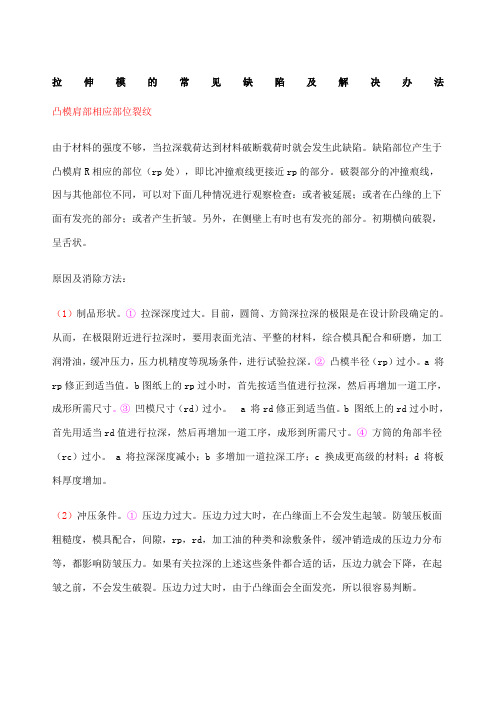
拉伸模的常见缺陷及解决办法凸模肩部相应部位裂纹由于材料的强度不够,当拉深载荷达到材料破断载荷时就会发生此缺陷。
缺陷部位产生于凸模肩R相应的部位(rp处),即比冲撞痕线更接近rp的部分。
破裂部分的冲撞痕线,因与其他部位不同,可以对下面几种情况进行观察检查:或者被延展;或者在凸缘的上下面有发亮的部分;或者产生折皱。
另外,在侧壁上有时也有发亮的部分。
初期横向破裂,呈舌状。
原因及消除方法:(1)制品形状。
①拉深深度过大。
目前,圆筒、方筒深拉深的极限是在设计阶段确定的。
从而,在极限附近进行拉深时,要用表面光洁、平整的材料,综合模具配合和研磨,加工润滑油,缓冲压力,压力机精度等现场条件,进行试验拉深。
②凸模半径(rp)过小。
a 将rp修正到适当值。
b图纸上的rp过小时,首先按适当值进行拉深,然后再增加一道工序,成形所需尺寸。
③凹模尺寸(rd)过小。
a 将rd修正到适当值。
b 图纸上的rd过小时,首先用适当rd值进行拉深,然后再增加一道工序,成形到所需尺寸。
④方筒的角部半径(rc)过小。
a 将拉深深度减小;b 多增加一道拉深工序;c 换成更高级的材料;d 将板料厚度增加。
(2)冲压条件。
①压边力过大。
压边力过大时,在凸缘面上不会发生起皱。
防皱压板面粗糙度,模具配合,间隙,rp,rd,加工油的种类和涂敷条件,缓冲销造成的压边力分布等,都影响防皱压力。
如果有关拉深的上述这些条件都合适的话,压边力就会下降,在起皱之前,不会发生破裂。
压边力过大时,由于凸缘面会全面发亮,所以很容易判断。
②润滑不良。
拉深加工与润滑有极为密切的关系,特别是包含有减薄拉深加工时,必须控制制品温度的升高。
如果是条件好的拉深加工,润滑油的选择不成什么问题;条件不好的拉深加工,如果润滑油选择不当,就会引起破裂。
③毛坯形状不良。
在试拉深阶段,决定毛坯形状是重要的工作之一。
必须将毛坯形状限制在最小尺寸。
当用方形毛坯进行圆筒拉深时,极限拉深率为0.58左右。
拉伸模具常见缺陷及解决办法

拉伸模具常见缺陷及解决办法拉伸模的常见缺陷及解决办法凸模肩部相应部位裂纹由于材料的强度不够,当拉深载荷达到材料破断载荷时就会发生此缺陷。
缺陷部位产生于凸模肩R相应的部位(rp处),即比冲撞痕线更接近rp的部分。
破裂部分的冲撞痕线,因与其他部位不同,可以对下面几种情况进行观察检查:或者被延展;或者在凸缘的上下面有发亮的部分;或者产生折皱。
另外,在侧壁上有时也有发亮的部分。
初期横向破裂,呈舌状。
原因及消除方法:(1)制品形状。
①拉深深度过大。
目前,圆筒、方筒深拉深的极限是在设计阶段确定的。
从而,在极限附近进行拉深时,要用表面光洁、平整的材料,综合模具配合和研磨,加工润滑油,缓冲压力,压力机精度等现场条件,进行试验拉深。
②凸模半径(rp)过小。
a 将rp修正到适当值。
b图纸上的rp过小时,首先按适当值进行拉深,然后再增加一道工序,成形所需尺寸。
③凹模尺寸(rd)过小。
a 将rd 修正到适当值。
b 图纸上的rd过小时,首先用适当rd值进行拉深,然后再增加一道工序,成形到所需尺寸。
④方筒的角部半径(rc)过小。
a 将拉深深度减小;b 多增加一道拉深工序;c 换成更高级的材料;d 将板料厚度增加。
(2)冲压条件。
①压边力过大。
压边力过大时,在凸缘面上不会发生起皱。
防皱压板面粗糙度,模具配合,间隙,rp,rd,加工油的种类和涂敷条件,缓冲销造成的压边力分布等,都影响防皱压力。
如果有关拉深的上述这些条件都合适的话,压边力就会下降,在起皱之前,不会发生破裂。
压边力过大时,由于凸缘面会全面发亮,所以很容易判断。
②润滑不良。
拉深加工与润滑有极为密切的关系,特别是包含有减薄拉深加工时,必须控制制品温度的升高。
如果是条件好的拉深加工,润滑油的选择不成什么问题;条件不好的拉深加工,如果润滑油选择不当,就会引起破裂。
③毛坯形状不良。
在试拉深阶段,决定毛坯形状是重要的工作之一。
必须将毛坯形状限制在最小尺寸。
当用方形毛坯进行圆筒拉深时,极限拉深率为0.58左右。
拉深模试模的常见缺陷、产生原因及调整方法

拉深模试模的常见缺陷、产生原因及调整方法试冲的缺陷产生原因调整方法制件起皱①压边力太小或不均②凸、凹模间隙太大③凹模圆角半径太大④板料太薄或塑性差①增加压边力或调整顶件杆长度、弹簧位置②减小拉深间隙③减小凹模圆角半径④更换材料制件破裂或有裂纹①压料力太大微信公众号:hcsteel②压料力不够,起皱引起破裂③毛坯尺寸太大或形状不当④拉深间隙太小⑤凹模圆角半径太小⑥凹模圆角表面粗糙⑦凸模圆角半径太小⑧冲压工艺不当⑨凸模与凹模不同心或不垂直⑩板料质量不好①调整压料力②调整顶杆长度或弹簧位置③调整毛坯形状和尺寸④加大拉深间隙⑤加大凹模圆角半径⑥修整凹模圆角,降低表面粗糙度⑦加大凸模圆角半径⑧增加工序或调换工序⑨重装凸、凹模⑩更换材料或增加退火工序,改善润滑条件制件拉①毛坯尺寸太大①减小毛坯尺寸深高度太大②拉深间隙太小③凸模圆角半径太大②整修凸、凹模,加大间隙③减小凸模圆角半径制件壁厚和高度不均①凸模与凹模间隙不均匀②定位板或挡料销位置不正确③凸模不垂直④压料力不均⑤凹模的几何形状不正确①重装凸模和凹模,使间隙均匀一致②重新修整定位板及挡料销位置,使之正确③修整凸模后重装④调整托杆长度或弹簧位置⑤重新修整凹模制件底面不平①凸模或凹模(顶出器)无出气孔②顶出器在冲压的最终位置时顶力不足③材料本身存在弹性①钻出气孔②调整冲模结构,使冲模达到闭合高度时,顶出器处于刚性接触状态③改变凸模、凹模和压料板形状制件表面拉毛①拉深间隙太小或不均匀②凹模圆角表面粗糙值大③模具或板料不清洁④凹模硬度太低,板料有黏附现象⑤润滑油质量太差①修整拉深间隙②修光凹模圆角③清洁模具及板料④提高凹模硬度,进行镀铬及氮化处理⑤更换润滑油。
深拉延模具拉毛缺陷的消除方法
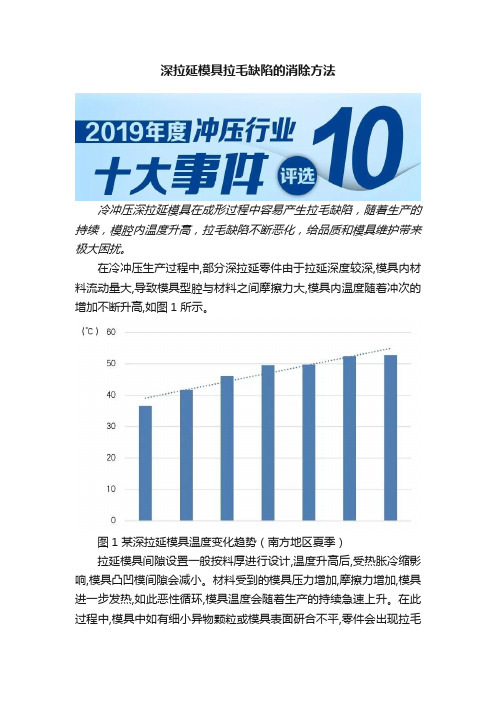
深拉延模具拉毛缺陷的消除方法冷冲压深拉延模具在成形过程中容易产生拉毛缺陷,随着生产的持续,模腔内温度升高,拉毛缺陷不断恶化,给品质和模具维护带来极大困扰。
在冷冲压生产过程中,部分深拉延零件由于拉延深度较深,模具内材料流动量大,导致模具型腔与材料之间摩擦力大,模具内温度随着冲次的增加不断升高,如图1 所示。
图1 某深拉延模具温度变化趋势(南方地区夏季)拉延模具间隙设置一般按料厚进行设计,温度升高后,受热胀冷缩影响,模具凸凹模间隙会减小。
材料受到的模具压力增加,摩擦力增加,模具进一步发热,如此恶性循环,模具温度会随着生产的持续急速上升。
在此过程中,模具中如有细小异物颗粒或模具表面研合不平,零件会出现拉毛缺陷,随着生产的持续拉毛会不断恶化,甚至造成零件开裂,如图2 所示。
温度的升高也会造成材料机械性能的降低,相关研究表明,汽车用电镀锌钢板的力学性能随着温度的升高而降低。
因此,模具温度的升高更容易造成深拉延时零件开裂。
图2 零件拉毛缺陷和开裂缺陷确认拉毛开裂原因根据拉延模具特性,在深拉延零件发生拉毛或开裂时,应对拉毛和开裂的特性进行分析:⑴确认拉毛缺陷发生的时间,是在量产刚开始时,还是在量产一段时间后。
如果是由于深拉延模具温度升高导致的拉毛,发生阶段一般在生产开始一段时间后,且随着生产的持续而不断恶化。
⑵确认开裂产生的原因。
若是由拉毛缺陷引起的,则该类开裂是在拉毛发生一段时间后,由于拉毛严重,拉痕深度超过了零件板料厚度,从而导致开裂,且此种开裂裂纹与拉毛位置重合。
根据以上分析,可以快速找出造成拉毛及开裂问题的原因,即模具过热。
确认模具高温区域利用红外热成像仪,在生产过程中对模具的温度进行监控,找出深拉延模具上模、下模温度最高的区域。
红外热成像仪的监控要点为,生产过程中进行不停机动态拍摄,对模具刚开始生产至生产结束的全过程,每间隔200 件进行热成像数据对比,如图3 所示。
图3 某模具热成像图一般情况下,热成像测量温度最高的区域为拉延深度最深,且易出现拉毛缺陷的位置。
不锈钢薄板拉深时出现的问题及对策
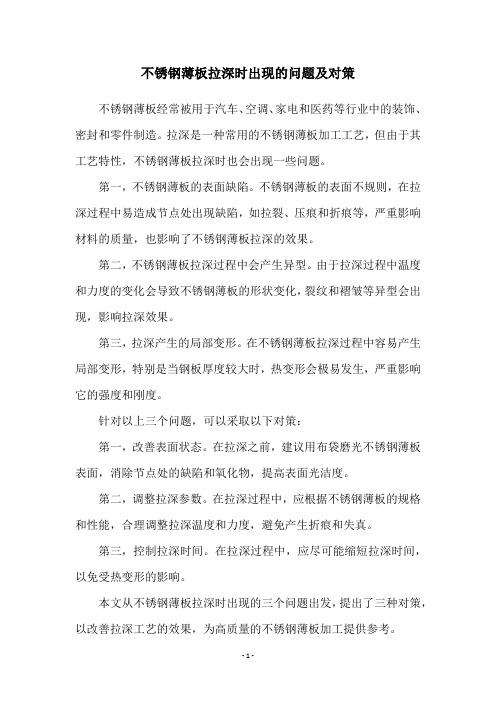
不锈钢薄板拉深时出现的问题及对策
不锈钢薄板经常被用于汽车、空调、家电和医药等行业中的装饰、密封和零件制造。
拉深是一种常用的不锈钢薄板加工工艺,但由于其工艺特性,不锈钢薄板拉深时也会出现一些问题。
第一,不锈钢薄板的表面缺陷。
不锈钢薄板的表面不规则,在拉深过程中易造成节点处出现缺陷,如拉裂、压痕和折痕等,严重影响材料的质量,也影响了不锈钢薄板拉深的效果。
第二,不锈钢薄板拉深过程中会产生异型。
由于拉深过程中温度和力度的变化会导致不锈钢薄板的形状变化,裂纹和褶皱等异型会出现,影响拉深效果。
第三,拉深产生的局部变形。
在不锈钢薄板拉深过程中容易产生局部变形,特别是当钢板厚度较大时,热变形会极易发生,严重影响它的强度和刚度。
针对以上三个问题,可以采取以下对策:
第一,改善表面状态。
在拉深之前,建议用布袋磨光不锈钢薄板表面,消除节点处的缺陷和氧化物,提高表面光洁度。
第二,调整拉深参数。
在拉深过程中,应根据不锈钢薄板的规格和性能,合理调整拉深温度和力度,避免产生折痕和失真。
第三,控制拉深时间。
在拉深过程中,应尽可能缩短拉深时间,以免受热变形的影响。
本文从不锈钢薄板拉深时出现的三个问题出发,提出了三种对策,以改善拉深工艺的效果,为高质量的不锈钢薄板加工提供参考。