中间包干式料专用环保脱模剂的研制
中间包干式料的制备工艺流程

中间包干式料的制备工艺流程
中间包干式料是一种常用于冶金、建材和化工等领域的重要材料,其制备工艺流程包括以下几个步骤:
1. 原料准备:根据生产需要,选用适当的原料组成配方,包括各种矿石、矿渣、焦炭等,进行粉碎、筛分和混合等处理。
2. 中间包装填:将预先制作好的中间包装填装入挤压机中,通过挤压将其压缩成所需形状和尺寸的块状体。
3. 烘干处理:将挤压成型的中间包装块状体置于烘干室内,进行干燥处理,以去除其中的水分和挥发物质,提高其密度和强度。
4. 包干处理:将烘干后的中间包装块状体放入包干窑内,进行高温煅烧处理,使其成为具有一定耐火性和化学稳定性的中间包干式料。
5. 检验和包装:对制备好的中间包干式料进行质量检验和包装处理,以确保其质量和安全性。
整个制备工艺流程需要精确的工艺控制和严格的质量管理,以确保制备出的中间包干式料满足各种生产要求和使用要求。
- 1 -。
脱模剂制备
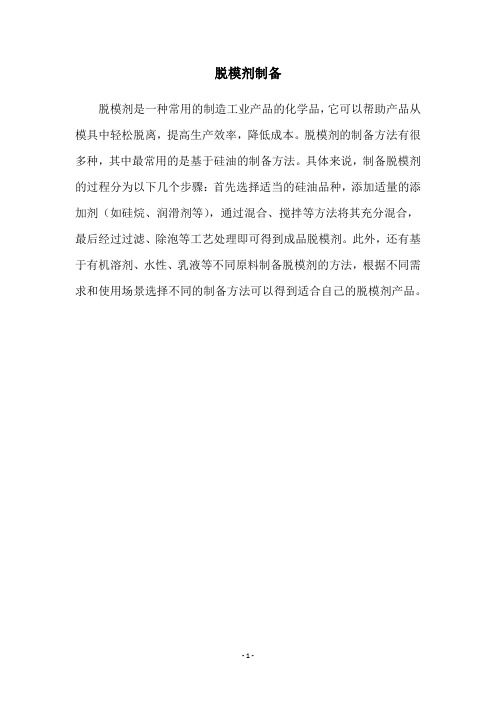
脱模剂制备
脱模剂是一种常用的制造工业产品的化学品,它可以帮助产品从模具中轻松脱离,提高生产效率,降低成本。
脱模剂的制备方法有很多种,其中最常用的是基于硅油的制备方法。
具体来说,制备脱模剂的过程分为以下几个步骤:首先选择适当的硅油品种,添加适量的添加剂(如硅烷、润滑剂等),通过混合、搅拌等方法将其充分混合,最后经过过滤、除泡等工艺处理即可得到成品脱模剂。
此外,还有基于有机溶剂、水性、乳液等不同原料制备脱模剂的方法,根据不同需求和使用场景选择不同的制备方法可以得到适合自己的脱模剂产品。
- 1 -。
环保中间包镁质干式料的研制与使用
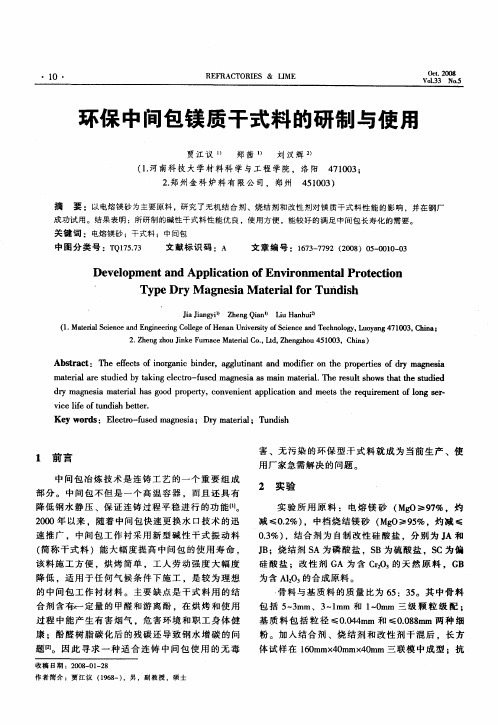
1 ・ 0
RE RAC ORI S & U ME F T E
O t2 0 c. 0 8
Vo_3 No5 l 3 .
环保 中间包镁 质干式料 的研 制与使 用
贾江议 郑 茜 刘 汉辉 4 10 : 7 0 3 ( . 南科 技 大 学材 料科 学 与工程 学 院 ,洛 阳 1 河 2郑 州金 科 炉料 有 限公 司 .郑州 . 4 10 ) 5 0 3
J a gi Z e gQa 。 LuH n u" iJ ny ̄ h n i J i a hi ai ) n ) (. ae a S i c n nier gC l g ea n es y f i c dT c nl y L oag4 10 , hn ; 1 M tr l ce eadE g e n o ee f n nU i rt o e ea eh o g , u yn 7 0 3 C ia i n n i l oH v i S n n c o
降低 。适 用 于 任何 气 候 条 件 下 施 工 。是 较 为 理 想
的 中 间包 工 作 衬材 料 。 主要 缺 点 是 干 式 料 用 的结
为含 A 2 3 l 的合 成原 料 。 o
.
骨 料 与基 质 料 的质 量 比为 6 :3 。 其 中骨 料 5 5
合 剂 含 有一 定 量 的 甲醛 和游 离 酚 。在 烘 烤 和使 用 过 程 中 能 产 生 有 害 烟气 ,危 害环 境 和 职 工 身 体 健
包 括 5 3 m、3 l m 和 1 O —m ~m ~ mm 三 级 颗 粒 级 配 ;
基 质 料8 m
康 ;酚 醛 树 脂 碳 化后 的残 碳 还 导 致 钢 水 增 碳 的 问
1 前 言
【CN109704728A】连铸中间包干式料环保型结合剂【专利】
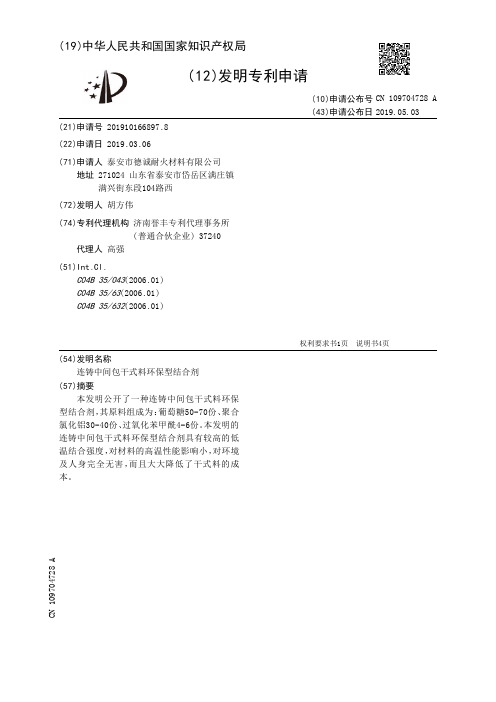
(19)中华人民共和国国家知识产权局(12)发明专利申请(10)申请公布号 (43)申请公布日 (21)申请号 201910166897.8(22)申请日 2019.03.06(71)申请人 泰安市德诚耐火材料有限公司地址 271024 山东省泰安市岱岳区满庄镇满兴街东段104路西(72)发明人 胡方伟 (74)专利代理机构 济南誉丰专利代理事务所(普通合伙企业) 37240代理人 高强(51)Int.Cl.C04B 35/043(2006.01)C04B 35/63(2006.01)C04B 35/632(2006.01)(54)发明名称连铸中间包干式料环保型结合剂(57)摘要本发明公开了一种连铸中间包干式料环保型结合剂,其原料组成为:葡萄糖50-70份、聚合氯化铝30-40份、过氧化苯甲酰4-6份。
本发明的连铸中间包干式料环保型结合剂具有较高的低温结合强度,对材料的高温性能影响小,对环境及人身完全无害,而且大大降低了干式料的成本。
权利要求书1页 说明书4页CN 109704728 A 2019.05.03C N 109704728A权 利 要 求 书1/1页CN 109704728 A1.一种连铸中间包干式料环保型结合剂,其特征在于,其原料组成为:葡萄糖50-70份、聚合氯化铝30-40份、过氧化苯甲酰4-6份。
2.根据权利要求1所述的环保型结合剂,其特征在于,其原料组成为:葡萄糖60份、聚合氯化铝35份、过氧化苯甲酰5份。
3.权利要求1或2所述的环保型结合剂的制备方法,其特征在于,包括以下步骤:将葡萄糖、聚合氯化铝和过氧化苯甲酰按比例混合,搅拌均匀,即制备得到连铸中间包干式料环保型结合剂。
4.权利要求1或2所述的环保型结合剂在生产连铸中间包干式料中的应用。
5.一种连铸中间包干式料,其特征在于,制备所述连铸中间包干式料的原料中包含5-5.5%(重量百分比)的权利要求1或2所述的环保型结合剂。
一种环保型混凝土构件脱模剂及其制备方法

一种环保型混凝土构件脱模剂及其制备方法
步骤一:准备材料。
准备滑石粉、环保型溶剂、甘油、纯水和表面活性剂。
步骤二:将滑石粉加入一容器中,逐渐加入环保型溶剂,并搅拌混合直至形成均匀的糊状物。
步骤三:在另一容器中,加入适量的甘油和纯水,并搅拌均匀。
步骤四:将步骤三中的甘油水溶液逐渐加入步骤二中的滑石糊状物中,并继续搅拌混合。
步骤五:加入适量的表面活性剂,并继续搅拌混合,直至形成均匀的混凝土构件脱模剂。
步骤六:将步骤五中得到的混凝土构件脱模剂放置静置一段时间,使其达到最佳性能。
该环保型混凝土构件脱模剂主要成分为滑石粉、环保型溶剂、甘油和表面活性剂。
它具有环保无害、易于制备和使用,能够有效减少对环境的污染和对人体的伤害。
同时,在混凝土构件脱模过程中,它能够提供良好的脱模效果,使混凝土构件表面光滑、无损坏。
- 1、下载文档前请自行甄别文档内容的完整性,平台不提供额外的编辑、内容补充、找答案等附加服务。
- 2、"仅部分预览"的文档,不可在线预览部分如存在完整性等问题,可反馈申请退款(可完整预览的文档不适用该条件!)。
- 3、如文档侵犯您的权益,请联系客服反馈,我们会尽快为您处理(人工客服工作时间:9:00-18:30)。
中间包干式料专用环保脱模剂的研制
严培忠,唐宁,吴开道,翁小燕,潘晶锦
(浙江红鹰集团股份有限公司,浙江湖州313000)
摘要:以滑石粉、轻质碳酸钙粉、少量鳞片石墨以及乳化剂、膨松剂、快干剂为原料,采用在300℃强烈分解的多羟基糖类为结合剂,研制出一种中间包干式料专用环保脱模剂。
研制的脱模剂涂刷容易,脱模方便,易于清理,不损伤干式料层,干燥时间短,成浆存放时间长,且在300~400℃烘烤时不产生污染烟气。
关键词:脱模剂;环保;多羟基糖类
0 前言
中间包干式料因其使用寿命长,施工方便,适于快速烘烤,翻包容易等特点,已在国内大规模运用,且目前正向无碳、环保方向发展。
部分环保型干式料的使用寿命已达到或接近酚醛树脂结合干式料的,也做到了不排放有害烟雾的目的。
目前的干式料在振动成型后脱模时大都使用机油、机油+石墨或黄油等作为脱模剂,这不仅消耗了可贵的石油资源,也对环境造成了污染,因此,为进一步完善中间包耐火材料的无害化,研发了中间包干式料专用环保型脱模剂。
l研制思路
根据中间包干式料脱模剂的使用过程,良好的脱模剂应具备以下特点:①涂刷容易,干燥时间短;②料浆稳定性好,填料不易下沉;③常温干燥后强度适宜,不易脱落;④300℃左右模层强度下降到最低,脱模效果良好;⑤对金属内模无腐蚀,脱模后脱模剂不与内模发生粘连,容易清理;⑥为水性涂料,且对环境及操作人员友好。
2试验
2.1原料及试验配比
根据脱模剂应具备的特点,采用具有润滑作用的滑石粉(≤45μm)作为脱模剂的主原料,辅以碳酸钙细粉(≤0.074mm)和少量鳞片石墨粉,用在300℃左右强烈分解的多羟基糖类化合物作为结合剂,并外加乳化剂、膨松剂NH4HCO3和快干剂。
部分原料的化学组成见表1。
脱模剂的基本配比(质量百分数)如下:滑石粉69%,碳酸钙细粉30%,鳞片石墨1%。
2.2试验过程
将30%滑石粉与乳化剂、膨胀剂、快干剂等少量组分先预混,再依次加入碳酸钙、剩余的滑石粉、鳞片石墨和多羟基糖类结合剂混匀,然后进行以下试验:
(1)在40×40×160(mm)模具中成型成型后的试样自然干燥1d后脱模,然后在干燥箱内干燥,其干燥制度分别为:30℃保温24h;干燥后试样加热到300℃保温3h。
冷却后按国家标准测定试样在30%干燥后和300℃加热后的常温耐压强度。
(2)采用模拟中间包模胎的自制模具进行涂刷试验用毛刷把调制完毕的脱模剂涂料均匀地涂刷在试验专用模具的外壁,自然干燥后,将模具置于自制的小型中间包内,模拟现场环境加干式料进行振动烘烤试验,根据脱模剂涂层脱落程度来确定使用效果。
3结果与分析
3.1 脱模历程
在模具表面涂刷脱模剂之后,干式料成型时的实际界面如图1所示。
图中,A面为干式
料层与脱模剂的接触面,B面为脱模剂层,C面为脱模剂与模具的接触面。
脱模剂层为凝聚层。
脱模时,当A面和C面剥离时称为界面剥离,而在B面剥离时叫做凝聚剥离。
由凝聚层引起的脱模,其脱模效果最好。
3.2原料的合理搭配
滑石粉从滑腻感方面来考虑,适合用于作隔离材料;为了缩短涂层在常温下的干燥硬化时间,引入了碳酸钙细粉。
滑石粉和碳酸钙粉作为主原料,有利于脱模剂的涂刷,不致于在涂层薄时发生断开现象,避免了涂刷返工问题。
为确保良好的脱模效果,且考虑脱模后使内胎残层更容易清理,又引人了适量的鳞片石墨。
石墨的引入量不宜过大,否则,脱模剂的加水量会明显提高,将导致脱模剂的常温干燥硬化时间延长。
3.3结合剂的选择
按脱模剂的脱膜历程分析,其结合系统最好是常温干燥后有一定强度,但加热到300℃左右强度尽可能消失,如此才能达到既轻松脱模又不黏模且不损坏干式料层的目的。
无机结合剂一般随温度升高强度增加;而残碳量较高的有机结合剂,尽管能部分分解,但仍有一定的残余强度,无法保证良好的脱模效果,因此选择在300℃左右强烈分解的多羟基糖类作结合剂。
在脱模剂基本配比的基础上,分别用0.5%~3%(质量分数)的多羟基糖类结合剂替代滑石,其加入量对脱模剂耐压强度的影响如图2所示。
从图2可以看出,随着多羟基糖类结合剂加入量的增大,脱模剂涂层干燥和300℃烘烤后的耐压强度也相应增加。
多羟基糖类结合剂的加入量过大,则烘烤后的残余强度也大,对顺利脱模不利。
试验证实:脱模剂涂层的常温耐压强度只要保证在1.2MPa以上,就不会因干式料的振动施工而产生涂层脱落现象。
因此,最终选择多羟基糖类结合剂的合适质量分数为1%。
由于多羟基糖类具有极少量的残碳率(2.3%,1000%),因此涂层强度在300~400℃烘烤时并没有完全消失,涂层达不到粉化的程度,还需配合加入0.5%(外加,质量分数)的膨松剂NH4HCO3,来达到此效果。
膨松剂在涂层烘烤时能分解完全,破环了脱模剂涂层的结构,从而提高了脱模效果。
3.4脱模剂施工性能的优化
3.4.1 乳化剂
脱模剂加水搅拌存放一段时间后会发生沉降现象,再次使用必须再搅拌均匀,给施工带来不便。
采用阴离子表面活性剂,可以使脱模剂搅拌后两天内不发生沉降。
3.4.2快干剂
喷雾铝粉遇水产生氢气,是比较常用的快干剂,对脱模剂的密度也不会产生较大影响。
在合理的配比下,加铝粉的涂层硬化时间比不加的快3~5h。
基本可以做到在胎模表面涂刷后2h即能进行干式料加料的振动成型施工。
虽然与油类脱模剂的即涂即用有一定差距,但也在施工人员的可操作范围之内。
如果急用,可运用现场排风设施,在30min左右即可达到干燥的目的。
4现场使用
研制的环保型水性脱模剂在邯郸钢厂120tBOF-LF单机单流薄板坯中间包干式料胎模上使用。
其中间包形状为船形,容量38t,冶炼钢种为超低碳钢、低碳钢、中碳钢,脱模烘烤时间为45~90 min(250~300℃)。
至2010年6月底,已成功涂刷脱模剂2.5t,没有发生过黏模现象;涂层的干燥硬化时间为1.5~2.5h;脱模后内胎清理只需用棕刷轻轻擦拭即可;成型的干式料层表面光整,表层强度较好,大火烘烤没有发生塌落现象;烘烤成型时没有油烟挥发现象,对环境友好。
5 结论
(1)利用滑石粉、碳酸钙粉及少量石墨粉作原料,多羟基糖类为结合剂配制出的水性脱模剂,脱模容易,不损坏干式料层,烘烤过程中不产生烟气,避免了对环境的污染。
(2)通过对结合剂的合理选择,膨松剂的引用,可以人为地控制干燥及300~400℃烘烤强度,从而达到与油性脱模剂相同的脱模效果。
(3)添加乳化剂,可以延长水性脱模剂施工时的存放时间,保证搅拌后2天内不沉降。
(4)通过快干剂的使用,可以缩短干燥时间,最快在涂刷后1.5h就能安装内胎模成型。