PDCA-FTA Training - 培训教材
PDCA管理循环培训课件

实施解决方案
按照计划执行解决方案,确保实 施过程中的协调与沟通。
PDCA的四个阶段
监控进度与效果
收集数据,监控实施进度,评估实施效果。
检查实施效果
对比预期目标与实际效果,评估解决方案的有效性。
PDCA的四个阶段
分析差异与原因
分析实际效果与预期目标的差异,找出原 因。
总结经验教训
总结实施过程中的经验教训,明确改进方 向。
优化解决方案
根据分析结果,优化解决方案,为下一轮 PDCA循环做准备。
02
P(Plan)计划阶段
确定目标
明确改进方向
在计划阶段,首先需要明 确改进的目标和方向,包 括产品、过程、系统或服
务质量等方面的改进。
设定具体指标
为了衡量改进的效果,需 要设定具体的指标,如合
降低质量成本
通过有效的质量管理,企业可以减少质量缺陷和售后维修成本,降 低整体质量成本。
提升品牌形象
持续的质量改进有助于提升企业的品牌形象,增强消费者对企业的 信任和忠诚度。
项目管理中的应用
确保项目目标实现
通过PDCA循环,项目 经理可以确保项目按照 预定目标进行,及时调 整项目计划和资源分配 。
持续改进
根据总结的经验教训,持续优化PDCA循环,完善各阶段的操作和 管理流程,提高管理效果。
推广应用
将优化后的PDCA循环应用于其他领域或项目,扩大其应用范围,提 高组织整体的管理水平。
06
PDCA管理循环应用案例
企业质量管理中的应用
持续改进产品质量
通过PDCA循环,企业可以不断优化产品质量,提高客户满意度 ,增强市场竞争力。
PDCA培训教材课件
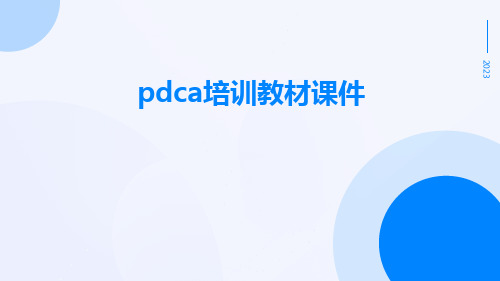
PDCA循环强调持续改进和优化,每个循环完成后,都需要对整个过程进行总结和反思, 找出问题和不足,提出改进措施,推动质量提升。
02
PDCA应用范围及案例
质量管理PDCA应用范围
01
制造业产品质量优化
在制造业中,PDCA循环被广泛应用于持续改进产品质量,降低缺陷
率,提高生产效率和客户满意度。
项目风险管理
运用PDCA循环,可以及时识别项目风险,制定应对措施 ,降低风险对项目的影响。
03
PDCA的计划阶段
计划阶段的目标和任务
描述组织或项目的目标和愿景 明确计划的范围和目标
确定需要改进的关键问题或挑战 确定成功实施计划的标准和预期结果
如何制定PDCA计划
收集数据和信息
分析数据和信息
通过调查、访谈、数据分析等方式,收集与 问题或挑战相关的数据和信息
06
PDCA的处理阶段
处理阶段的目标和任务
01Βιβλιοθήκη 02030405
目标和任务概 述
处理计划
PDCA处理阶段旨在针对检 查结果采取相应的措施和 行动,以达到改进和提高 的目的。这一阶段主要包 括明确处理计划、实施改 进措施、监控改进效果以 及调整改进策略等任务。
根据检查结果,制定相应 的处理计划,包括改进目 标、具体措施、时间安排 、责任人等方面的规划。
生产成本控制
通过PDCA循环,可以降低生产成本,提高产品质量和生产效 益。
生产现场管理
运用PDCA循环,可有效管理生产现场,确保生产过程顺利进 行。
PDCA在项目管理中的应用案例
项目进度控制
运用PDCA循环,可以实时监控项目进度,及时调整计划 ,确保项目按时完成。
PDCA-FTA Training - 培训教材
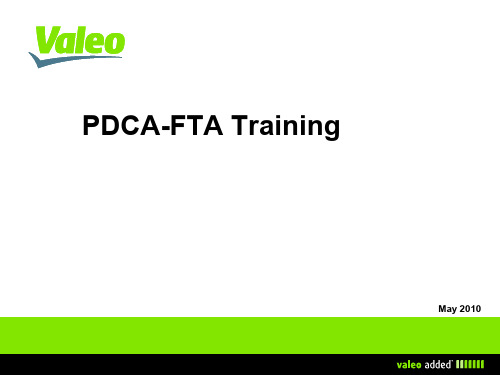
QUALITY
COST
GLOBAL PRESENCE
TECHNOLOGY
VALEO 5000
QRQC activity
Valeo 5000
5 AXES
基于 三现主义 Based on „San Gen Shugi‟ attitude
2010.05 I 4 Always place client logo on the right bottom corner, equidistant from the grey line, with a maximum height equivalent to the Valeo logo. I
SAN GEN SHUGI Attitude
San means "3" – Gen means "real" or "actual" – Shugi means "ideology"
San Gen Shugi
1. Gen-ba : Real Place 现场
2. Gen-butsu : Real Parts 现物 3. Gen-jitsu : Reality ( Real data ) 现实数据
PDCA-FTA Training
May 2010
Agenda
1.
介绍 Introduction 问题描述(5W2H) – 通知 Problem characterisation (5W2H) - Notification 保护客户,从挑选中得到信息 – QR How to secure the customer and learn from sorting - QR 找到根本原因 – PD How to find the root causes - PD 对策实施,检查有效性,经验学习卡 – CA Counter-measure implementation, check of efficiency and LLC writing - CA
PDCA培训教材 PPT课件
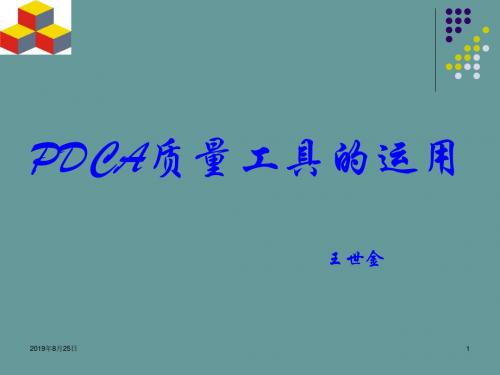
王世金
2019年8月25日
1
课程介绍
培训目的:使受训人员掌握科学思维方式 与工作技巧。
培训内容: 1、什么是PDCA? 2、PDCA的步骤? 3、PDCA对现代企业的重要
性。
2019年8月25日
2
PDCA方法的引入
每个企业的员工都想很漂亮的完成上级所部署的任 务,但仅仅靠勤奋是不够的,还要讲究科学的方法, 在管理学上,有一个公认的好方法,那就是PDCA。
2019年8月25日
3
Plan Do Check Action
第一, 要先策划一下,想达到什么样的目标,考虑为了完成 计划,需要哪些资源以及
通过哪些步骤去做。 第二, 执行:拿到资源后,去做这件事。 第三, CHECK验证执行的结果是否在预期的范围内。 第四, 总结,通过做这件事,得到哪些教训
及经验,可能下次做这件事的时候, 可能用上这些教训及经验。
2019年8月25日
8
第四阶段总结(Action):巩固成绩,把成功的经验尽可 能纳入标准,进行标准化,对遗留问题转入下一PDCA 循环去解决。
PDCA法具有两个鲜明特点: (1)循环前进,阶梯上升(见图-1) (2)大循环套小循环(见图-2)。
2是:
每 通 过 一 次PDCA 循 环, 都 要 进 行 总 结, 提 出 新 目 标, 再 进 行 第 二 次PDCA循 环, 使 质 量 管 理 的 车 轮 滚 滚 向 前。PDCA 每 循 环 一 次, 质 量 水 平 和 管 理 水 平 均 提高 一 步, 如 图3 所 示。
图3
13
PDCA工作方法对现代企业的重要性
1.分析现状:找出存在的主要质量问题也叫现状调查。 2.原因分析:诊断分析生产质量问题的各种影响困素即Y=F(X) 3.确认原因;找出充分的证据影响质量的关键因素X 4.拟定措施:制定计划;(5W1H),即:为什么制定该措施(Why)?达到什么目标
2024年度pdca培训ppt课件完整版
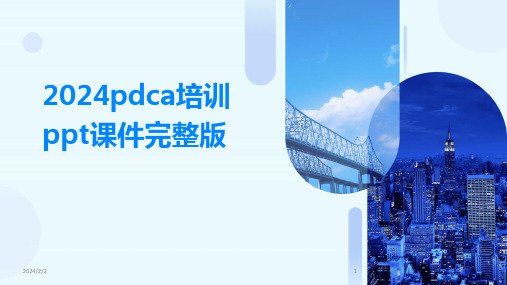
评估目标完成情况
识别问题和亮点
在全面检查的过程中,识别出存在的 问题和不足之处,同时发现执行过程 中的亮点和成功经验。
根据设定的目标,评估实际执行结果 是否达到预期效果。
2024/2/2
16
发现问题并分析原因
问题分类
将发现的问题进行分类,如技术 问题、管理问题、资源问题等。
原因分析
针对每个问题,深入分析其产生 的原因,包括直接原因和根本原
结合培训进度表,制定资源使用计 划,明确每个阶段所需资源的种类 、数量和使用时间。
10
03
CATALOGUE
执行阶段(Do)
2024/2/2
11
按照计划落实执行措施
制定详细的执行步骤 和时间表,确保计划 得以有序实施。
遵循已制定的流程和 规范,确保执行过程 符合相关标准和要求 。
2024/2/2
意义
提升企业管理水平,促进企业持续发 展;增强学员综合素质,提高职场竞 争力。
2024/2/2
6
02
CATALOGUE
计划阶段(Plan)
2024/2/2
7
明确目标与任务
确定培训目标
明确2024年PDCA培训的 目标,如提高员工对 PDCA循环的理解和应用 能力等。
2024/2/2
分析培训需求
通过问卷调查、访谈等方 式,了解员工在PDCA方 面的知识和技能需求。
2024/2/2
检查评估
定期检查产品质量,评估改进效 果。
执行落实
严格执行生产流程规范,确保员 工技能达标。
24
案例二:某企业生产效率优化项目
问题定义
生产效率低下,成本高昂 。
计划制定
PDCA培训教材课件

教师点评
对游戏中的问题和解决方 法进行评价和反馈,总结 提炼出相关的知识点和技 能要求。
THANKS
感谢观看
学生扮演
学生分别扮演不同的角色 ,例如领导、员工、客户 等,模拟真实的工作场景 进行对话和互动。
教师点评
对学生的表现进行评价和 反馈,指出存在的问题和 不足,提出改进意见和建 议。
互动游戏
设计游戏
设计具有代表性的互动游 戏,涵盖PDCA循环的不 同方面和阶段。
学生参与
学生参与游戏互动,通过 实际操作加深对PDCA循 环的理解和应用。
跟踪改进效果
对改进措施的实施效果进 行跟踪和评估,确保改进 措施的有效性。
05
PDCA的培训方法
案例教学
精选案例
选择具有代表性的案例,涵盖 PDCA循环的不同方面和阶段
。
分析讨论
引导学生对案例进行深入剖析, 讨论其中存在的问题、原因和解 决方案。
教师点评
总结学生的讨论成果,针对案例中 的问题进行深入剖析,提炼出 PDCA循环的实际应用技巧和方法 。
pdca培训教材课件
xx年xx月xx日
目录
• PDCA简介 • PDCA循环的基本步骤 • PDCA在质量管理中的应用 • 如何提高PDCA质量管理效果 • PDCA的培训方法
01
PDCA简介
PDCA的含义
PDCA循环是一种质量改进工具,通过计划、执行、检查和行 动四个阶段持续改进工作。
PDCA四个字母分别代表Plan、Do、Check、Act。
详细描述
在检查计划阶段,需要定期对任务的执行情况进行检查,并对检查结果进行分析,找出存在的问题和原因。然 后,需要提出改进措施,以解决问题和提高工作效率。
2024年PDCA培训课件
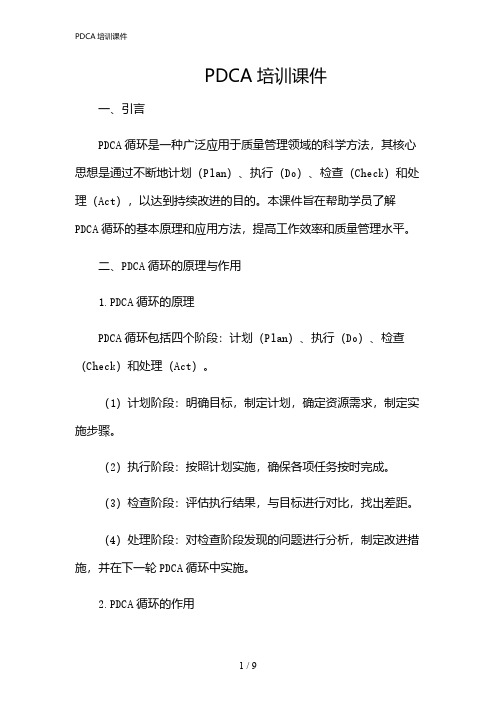
PDCA培训课件一、引言PDCA循环是一种广泛应用于质量管理领域的科学方法,其核心思想是通过不断地计划(Plan)、执行(Do)、检查(Check)和处理(Act),以达到持续改进的目的。
本课件旨在帮助学员了解PDCA循环的基本原理和应用方法,提高工作效率和质量管理水平。
二、PDCA循环的原理与作用1.PDCA循环的原理PDCA循环包括四个阶段:计划(Plan)、执行(Do)、检查(Check)和处理(Act)。
(1)计划阶段:明确目标,制定计划,确定资源需求,制定实施步骤。
(2)执行阶段:按照计划实施,确保各项任务按时完成。
(3)检查阶段:评估执行结果,与目标进行对比,找出差距。
(4)处理阶段:对检查阶段发现的问题进行分析,制定改进措施,并在下一轮PDCA循环中实施。
2.PDCA循环的作用(1)提高工作效率:通过PDCA循环,可以确保工作按照计划有序进行,避免盲目性和重复性。
(2)提升质量管理水平:PDCA循环有助于发现问题、分析原因,从而制定针对性的改进措施,提高产品和服务的质量。
(3)促进团队协作:PDCA循环要求团队成员共同参与,增强团队凝聚力,提高团队执行力。
(4)实现持续改进:PDCA循环是一个不断迭代的过程,有助于企业不断优化管理,提升竞争力。
三、PDCA循环的应用方法1.计划阶段(1)明确目标:确定要解决的问题或要实现的目标。
(2)制定计划:根据目标,制定详细的实施计划,包括任务分解、时间安排、资源分配等。
(3)风险评估:分析可能遇到的风险和挑战,制定应对措施。
2.执行阶段(1)按照计划实施:确保各项工作按照计划有序进行。
(2)沟通与协作:加强团队成员之间的沟通与协作,确保信息畅通。
(3)监控进度:对实施过程进行监控,确保任务按时完成。
3.检查阶段(1)评估结果:对执行阶段的结果进行评估,与目标进行对比。
(2)数据分析:运用数据分析方法,找出存在的问题和不足。
(3)反馈意见:收集相关人员对实施过程的意见和建议。
PDCA培训教材(带目录)

PDCA培训教材1.引言PDCA(计划-执行-检查-行动)是一种广泛应用于质量管理、项目管理、过程改进等领域的管理方法。
PDCA培训教材旨在帮助读者了解PDCA方法的基本原理、实施步骤和应用场景,提高工作效率和质量管理水平。
2.PDCA方法简介PDCA方法是一种循环迭代的管理方法,包括四个阶段:计划(Plan)、执行(Do)、检查(Check)和行动(Act)。
PDCA方法强调持续改进、问题解决和决策制定,适用于各种类型和组织规模的企业。
3.PDCA实施步骤3.1计划(Plan)计划阶段是PDCA方法的第一步,其主要任务是明确目标、制定计划和确定资源。
具体步骤如下:(1)确定目标:明确改进目标、问题和需求,确保目标的可衡量、可实现和有时间限制。
(2)制定计划:根据目标制定详细的实施计划,包括任务分配、时间安排和资源需求。
(3)风险评估:分析实施计划可能面临的风险和挑战,制定相应的应对措施。
3.2执行(Do)执行阶段是PDCA方法的第二步,其主要任务是按照计划实施改进措施。
具体步骤如下:(1)实施计划:按照计划执行任务,确保各项工作有序进行。
(2)沟通协调:加强与团队成员的沟通与协作,确保信息的及时传递和问题的及时解决。
(3)监控进度:跟踪项目进度,确保各项工作按计划完成。
3.3检查(Check)检查阶段是PDCA方法的第三步,其主要任务是评估改进效果,查找问题和不足。
具体步骤如下:(1)数据收集:收集与改进相关的数据,包括过程数据、结果数据和反馈数据。
(2)数据分析:对收集到的数据进行统计分析,评估改进效果。
(3)问题识别:根据数据分析结果,识别存在的问题和不足。
3.4行动(Act)行动阶段是PDCA方法的一步,其主要任务是制定和实施改进措施。
具体步骤如下:(1)制定改进措施:针对识别出的问题和不足,制定相应的改进措施。
(2)实施改进:按照改进措施执行任务,解决存在的问题。
(3)总结经验:总结本次PDCA循环的经验教训,为下一次改进提供参考。
2024年PDCA培训教程

PDCA培训教程引言:PDCA(计划-执行-检查-行动)是一种广泛应用于质量管理和持续改进的方法论。
它帮助企业识别、分析和解决问题,从而提高工作效率和产品质量。
本教程旨在向您介绍PDCA的基本概念、实施步骤和应用案例,帮助您更好地理解和应用PDCA方法。
第一部分:PDCA的基本概念1.1PDCA的起源和发展PDCA最早由美国质量专家W.A.休哈特在20世纪30年代提出,后来被美国质量管理协会(ASQ)和其他组织广泛推广和应用。
PDCA 是一种迭代的方法,通过不断的计划、执行、检查和行动,实现持续改进。
1.2PDCA的四个阶段PDCA包括四个阶段:计划(Plan)、执行(Do)、检查(Check)和行动(Act)。
每个阶段都有其特定的目标和任务,相互衔接,形成一个闭环系统。
第二部分:PDCA的实施步骤2.1计划阶段在计划阶段,我们需要明确目标、制定计划和确定资源。
具体步骤如下:(1)确定目标和范围:明确改进的对象和目标,确保目标的可衡量和可实现。
(2)分析现状:收集相关数据和信息,了解当前的工作流程、问题和瓶颈。
(3)制定改进计划:根据现状分析,制定具体的改进措施和行动计划。
(4)确定资源:明确所需的资源,包括人力、物力、财力等。
2.2执行阶段在执行阶段,我们需要按照计划实施改进措施。
具体步骤如下:(1)实施改进措施:按照计划执行改进措施,确保各项措施的落实。
(2)监控过程:在实施过程中,对关键指标进行监控,确保改进措施的有效性。
(3)沟通与协作:与团队成员保持良好的沟通,确保改进措施的顺利实施。
2.3检查阶段在检查阶段,我们需要评估改进措施的效果,以确定是否达到预期目标。
具体步骤如下:(1)收集数据:收集实施改进措施后的相关数据,与改进前的数据进行对比。
(2)分析结果:分析改进措施的效果,识别存在的问题和不足。
(3)评估目标达成情况:根据数据和分析结果,评估是否达到预期目标。
2.4行动阶段在行动阶段,我们需要根据检查阶段的结果,采取相应的措施进行持续改进。
《PDCA管理循环培训》课件

PDCA循环不仅适用于整个质量管 理,也适用于任何一个小环节或工 作单元。
PDCA循环的应用范围
01
02
03
质量管理
PDCA循环是质量管理的 基本方法,广泛应用于各 种质量管理活动中。
工作管理
PDCA循环也可以用于工 作管理,帮助我们更好地 组织和安排工作。
个人生活
PDCA循环也可以用于个 人生活,帮助我们更好地 规划和管理自己的生活。
PDCA循环是不断循环、不断提高的过程,每个循环都围绕着一个目标,经过四 个步骤,然后进入下一个循环。
PDCA循环的特点
不断循环
PDCA循环是不断循环的过程 ,一次循环结束并不意味着结
束,而是进入下一个循环。
阶梯式上升
在PDCA循环中,每个循环都会带 来一定的成果,然后进入下一个更 高的循环,从而实现阶梯式上升。
《pdca管理循环培训》课 件
2023-11-12
目录
• PDCA管理循环概述 • PDCA管理循环的四个阶段 • PDCA管理循环的实施步骤 • PDCA管理循环的实践案例 • PDCA管理循环的总结与展望
01 PDCA管理循环 概述
PDCA循环的基本概念
PDCA循环是由Plan(计划)、Do(执行)、Check(检查)和Act(行动)四个单词组成, 它是一个持续改进模型,是质量管理的基本方法。
强化与其他管理理论的融合
PDCA循环将进一步与精益生产、六西格玛等其他优秀管 理理论融合,形成更具指导意义的综合性管理框架。
THANKS
感谢观看
数据分析和趋势预测
通过对实施过程中的数据进行分析和趋势预测, 了解计划实施的效果及未来发展趋势。
3
pdca循环理念培训教材课件

pdca循环理念培训教材课件教学内容:本节课的教材章节为《质量管理方法与工具》的第一节,主要内容是介绍PDCA循环理念。
PDCA循环是一种持续改进的工作方法,包括计划(Plan)、执行(Do)、检查(Check)和行动(Act)四个阶段。
通过这四个阶段的循环往复,不断优化工作流程,提高工作效果。
教学目标:1. 让学生了解并理解PDCA循环的基本概念和四个阶段的含义。
2. 培养学生运用PDCA循环解决实际问题的能力。
教学难点与重点:重点:PDCA循环的基本概念和四个阶段的含义。
难点:如何运用PDCA循环解决实际问题。
教具与学具准备:教具:课件、黑板、粉笔。
学具:笔记本、笔。
教学过程:一、实践情景引入(5分钟)教师通过一个生活中的实例,如家庭作业完成情况不佳,引入PDCA循环的概念,让学生思考如何运用PDCA循环来改进这个问题。
二、知识讲解(10分钟)1. 教师讲解PDCA循环的基本概念和四个阶段的含义。
三、例题讲解(10分钟)四、随堂练习(10分钟)学生分组讨论,每组选择一个实际问题,运用PDCA循环制定解决方案,并分享给其他组。
五、课堂小结(5分钟)板书设计:PDCA循环计划(Plan)执行(Do)检查(Check)行动(Act)作业设计:请同学们结合自己的生活经验,选择一个实际问题,运用PDCA循环制定解决方案,并将其写成书面报告。
课后反思及拓展延伸:本节课通过生活实例引入PDCA循环的概念,让学生认识到其在实际生活中的重要性。
通过例题讲解和随堂练习,学生掌握了PDCA循环的基本步骤和应用方法。
在课后作业中,学生能够将所学知识运用到实际问题中,进一步巩固知识点。
拓展延伸:学生可以进一步学习更多关于PDCA循环的应用案例,了解其在不同领域的运用。
同时,可以尝试将PDCA循环应用于学习、生活和工作的各个方面,不断提高自身的能力和效率。
重点和难点解析:一、实践情景引入(5分钟)这是课堂教学的第一步,通过生活实例引入PDCA循环的概念,让学生初步接触到这一理论,并激发他们的学习兴趣。
PDCA循环管理(PDCA循环工作法培训教材)
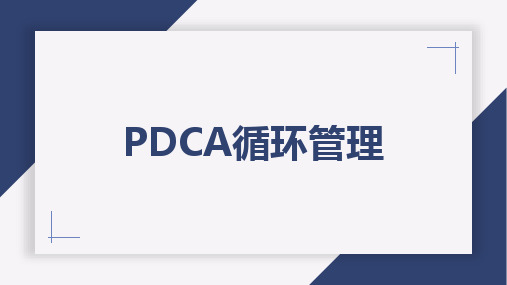
0
1月份产品不合格情况统计
60.00%
A产品
10.60%
11.40%
8.30%
B产品
C产品 不合格数
D产品 占比
9.70% E产品
70.00% 60.00% 50.00% 40.00% 30.00% 20.00% 10.00% 0.00%
项目 A产品 B产品 C产品 D产品 E产品 合计
不合格数
占比
项目
壳体 开裂
不合格 数
11750
占比 80.6%
包边 不良 1258
8.6%
缩水 617 4.2%
溢胶 374 2.6%
端子 氧化
326
色差 合计 261 14586
2.2% 1.8% 100.0%
2月份A产品不合格情况统计
1000
800
600 49.3%
400
200
0 壳体开裂
14.6% 包边不良
12.8% 缺胶
PDCA循环管理
质量管理体系运行图
小故事——汉斯&比尔的创业(通过为村民供水致富)
汉斯: 身强力壮,吃苦耐劳,
人缘好 他的方法是?
比尔:
富有学识,机智灵敏,善于思考 前3月没有为村里带来一滴水,他
在做什么?
➢ 首先快速找到距离较近的水井
➢ 买来水桶和扁担 ➢ 每天担水到村里,向村民卖1元
不合格 数
14586
2585
2767
2010
2345 24293
占比 60.0% 10.6% 11.4% 8.3% 9.7% 100.0%
A产品不合格占60%
14000 12000 10000
PDCA循环工作方法培训教材
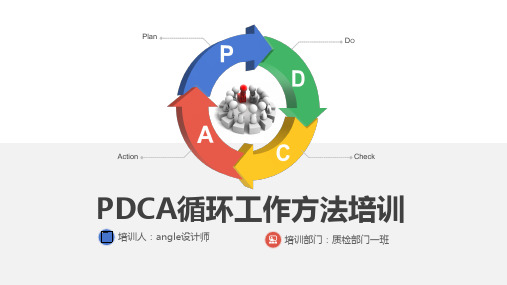
DO
Action
Check
PDCA循环工作方法培训
培训人:angle设计师
培训部门:质检部门一班
CONTENTS
目录
分析说明
循环步骤
特点
举例说明
第2页
1 分析说明
戴明PDCA循环
PDCA:是最早由休哈特(Shewart, 另译做舍瓦特)提出来后续由戴明 (Deming)予以发展的,所以又称 为“戴明环。
08
根据问题分析原因 (头脑风暴法)
找出解决问题 的方法
评价整改后的 效果
遗留的问题进 入下一个 PDCA。
第 32 页
4 持续质量改进(CQI)
定义:是在全面质量管理基础上发展起来的,它强调持续 的、全程的质量管理。在注重终末质量的同时更注重过程 管理、环节控制的一种新的质量管理理论。
第 33 页
第7页
2 PDCA循环运用与流程图
Plan Do
Action
Check
PDCA——P阶段
步骤三 : 找出影响质量的主要因素
影响质量的因素往往是多方面的,可能涉及人、方法、仪器、 设备、材料、环境等。每项大的影响因素中又包含小的因素。 应在诸多因素中,找出影响质量的最主要、最直接的因素。
区分主因和次因是最有 效解决题目的关键。
召集检验科,临床科室主任,三级医师以及护士长等人员召开会议,讨论问题产生的原 因,并作好记录(头脑风暴法)
第 20 页
4 危急值PDCA管理举例
检验科危急值管理落实不到位的原因分析
测量
材料
人员
工作量大
人员紧张
检验科与临床科 缺乏沟通
临床医师 未引起足够重视
环境
《PDCA培训教材》课件

PDCA循环强调预防为主,通过 发现问题、分析问题、解决问 题,预防类似问题再次发生。
02Байду номын сангаас
CATALOGUE
P(Plan)计划阶段
确定目标
01
02
03
明确目标
在计划阶段,首先需要明 确目标,包括要解决的问 题、要达成的指标等。
目标可衡量
目标应该是具体、可衡量 的,以便于评估进度和成 果。
监控关键节点
关注计划中的关键节点,确保关 键环节得到有效监控和管理。
及时调整
在执行过程中,如发现计划存在 问题或偏差,及时进行调整和修
正。
调整计划
分析偏差
对比实际执行情况与计划目标,分析存在的偏差 和问题。
调整方案
根据分析结果,对实施方案进行必要的调整和优 化。
重新分配资源
根据调整后的方案,重新分配资源和人力,确保 计划的有效执行。
详细描述
在制造业中,PDCA循环被广泛应用于质量管理。通过设定明确的计划和目标, 执行生产流程和质量控制,定期检查生产过程中的问题并进行调整,采取有效的 改进措施,持续优化生产过程,提高产品质量和生产效率。
医疗行业的持续改进
总结词
PDCA循环在医疗行业中有助于实现持续改进,提高医疗服务质量,保障患者安全。
PDCA循环是一种不断改进、不断完 善的循环过程,通过计划、实施、检 查、处理四个阶段,不断发现问题、 解决问题,推动质量持续改进。
PDCA的起源与发展
PDCA循环起源于20世纪20年代的美国,最初应用于质量管 理领域。
随着时间的推移,PDCA循环逐渐成为一种通用的管理方法 ,被广泛应用于各个行业和领域,帮助组织实现持续改进和 卓越运营。
2024版PDCA培训资料(完整版)

2024/1/30
17
总结经验教训,持续改进
总结经验教训
在完成检查工作后,需要对本次工作进行总结,提炼经验教训。
2024/1/30
持续改进
根据总结的经验教训,对工作流程、方法等进行改进,提高工作效 率和质量。
推广最佳实践
将本次工作中形成的良好实践和有效方法,在团队内部进行推广, 促进团队整体水平的提升。
2024/1/30
29
展望未来发展趋势和挑战
发展趋势分析
随着市场的不断变化和技术的不断进步,未来我们将面临更多的机遇和挑战。 我们需要密切关注市场动态和技术趋势,以便及时调整战略和业务模式。
挑战预测与应对
在未来的发展中,我们可能会遇到市场竞争加剧、客户需求多样化等挑战。为 应对这些挑战,我们需要加强市场调研,了解客户需求,提高产品质量和服务 水平。
回顾本次PDCA循环过程及成果
PDCA循环过程概述
成果展示
本次PDCA循环经历了计划、执行、 检查和行动四个阶段,每个阶段 都有明确的目标和任务,确保了 项目的顺利进行。
通过本次PDCA循环,我们成功完 成了项目目标,提高了产品质量 和客户满意度,同时也提升了团 队协作和沟通能力。
经验教训总结
在项目实施过程中,我们遇到了 一些挑战和困难,但通过团队成 员的共同努力和协作,我们克服 了这些困难并从中吸取了经验教 训。
PDCA培训资料(完整版)
2024/1/30
1
目录
2024/1/30
• PDCA循环概述 • 计划阶段(Plan) • 执行阶段(Do) • 检查阶段(Check) • 处理阶段(Act) • PDCA在培训中应用实践 • 总结与展望
2
01
- 1、下载文档前请自行甄别文档内容的完整性,平台不提供额外的编辑、内容补充、找答案等附加服务。
- 2、"仅部分预览"的文档,不可在线预览部分如存在完整性等问题,可反馈申请退款(可完整预览的文档不适用该条件!)。
- 3、如文档侵犯您的权益,请联系客服反馈,我们会尽快为您处理(人工客服工作时间:9:00-18:30)。
0/1/00
0/1/00
0/1/00
0/1/00
0/1/00
0/1/00
0/1/00
0/1/00
0/1/00
Defect quantity
Total Line reject PPM
- Why is it a problem? [16] - When detected [17] - Who detected? [18] (name of operator) - Where detected? [19] - How detected? [20] - How many bad parts? [21]
2.
3.
4.
5.
2010.05 I 2
Always place client logo on the right bottom corner, equidistant from the grey line, with a maximum height equivalent to the Valeo logo. I
态度: ATTITUDE: 是否 Can you: -用事实和数据说话 Speak with facts and data 是否 Do you : -要求得到证明和数据 Request evidences and data -不接受”我觉得, 我相信,也许…” Forbid words such as “ I think, I believe, perhaps….” 好处: BENEFITS: -准确性 Be accurate -自信,也令人信服 Be convinced and be convincing -节省时间 Gain time
弄清问题是什么 Understand what is the problem
- Was part produced in the standard process? [23] - When was it manufactured at Valeo? [24] - Who manufactured? [25] - In which other application or processes product is used? [26] - Are we capturing the defect when reinjecting product in normal process? [27] - Did a similar problem happen previously at customer or internally? [28]
Genbutsu = Real parts 现物
态度: ATTITUDE: 是否 Do you -对比好/坏 (零件, 状态…) 和标准 Compare good and bad (parts, situation…) versus standard 好处: BENEFITS: -发现差异点 Detect differences -发现与标准的差异 Detect deviations to standard -识别相关”因素” Identify relevant factors
1,2
Revision 6.35_eng [7]
Group [2] CUSTOMER / Contact name [8]
TOTAL LINE REJECT SITUATION (Defect related) [33]
1 1
Quantity of defects
N PROBLEM DESCRIPTION BY CUSTOMER / LOCATION OF THE PROBLEM [12] PRODUCT SOP DATE [13] R LAST MODIFICATION DATE [14] Y N
– FTA,5个为什么,缺陷复现 FTA, 5 Whys, defect reproduction.
Always place of client logo on the right bottom corner, equidistant from the grey line, 检查有效性 Check efficiency 2010.05 I 11 with a maximum height equivalent to the Valeo logo. I
SAN GEN SHUGI Attitude
San means "3" – Gen means "real" or "actual" – Shugi means "ideology"
San Gen Shugi
1. Gen-ba : Real Place 现场
2. Gen-butsu : Real Parts 现物 3. Gen-jitsu : Reality ( Real data ) 现实数据
PDCA-FTA Training
May 2010
Agenda
1.
介绍 Introduction 问题描述(5W2H) – 通知 Problem characterisation (5W2H) - Notification 保护客户,从挑选中得到信息 – QR How to secure the customer and learn from sorting - QR 找到根本原因 – PD How to find the root causes - PD 对策实施,检查有效性,经验学习卡 – CA Counter-measure implementation, check of efficiency and LLC writing - CA
PDCA – FTA 概况 Overview
什么是PDCA-FTA? What is it ?
QRQC中使用的解决问题的方法 A methodology used during QRQC activities for problem solving. 法雷奥用来对应各种问题的标准表格格式 It is a standard format in Valeo for all kind of problems. 2个部分组成 2 majors steps:
介绍 Introduction
质量管理系统 Quality Management System
P
战略 Strategy
D
方法 Method
C
检查进度 Measure Progress
A
持续改进 Continuous Improvement
QRQC
Quick Response Quality Control
要了解其含意 Need to understand what is behind
2010.05 I 5 Always place client logo on the right bottom corner, equidistant from the grey line, with a maximum height equivalent to the Valeo logo. I
QUALITY
COST
GLOBAL PRESENCE
TECHNOLOGY
VALEO 5000
QRQC activity
Valeo 5000
5 AXES
基于 三现主义 Based on „San Gen Shugi‟ attitude
2010.05 I 4 Always place client logo on the right bottom corner, equidistant from the grey line, with a maximum height equivalent to the Valeo logo. I
- 快速反应
Quick response activity - 分析 Analysis activity
2010.05 I 10
Always place client logo on the right bottom corner, equidistant from the grey line, with a maximum height equivalent to the Valeo logo. I
2010.05 I 7
Always place client logo on the right bottom corner, equidistant from the grey line, with a maximum height equivalent to the Valeo logo. I
Genjitsu = Real data 现实数据
1 1 1 0 0 0 0 0
0,8
0,6
0,4
0,2
WHAT IS THE PROBLEM ? > Use 5W + 2H to know what is the Current Situation (C/S) ? CUSTOMER VIEW
- What happened? [15]
0
VALEO VIEW
2010.05 I 8
Always place client logo on the right bottom corner, equidistant from the grey line, with a maximum height equivalent to the Valeo logo. I
QRQC Based on San Gen Shugi
Video QRQC N°1(9‟), N°2(11‟) How to deal with a problem?
2010.05 I 9
Always place client logo on the right bottom corner, equidistant from the grey line, with a maximum height equivalent to the Valeo logo. I