几个重要工艺参数的计算
整经工艺计算公式
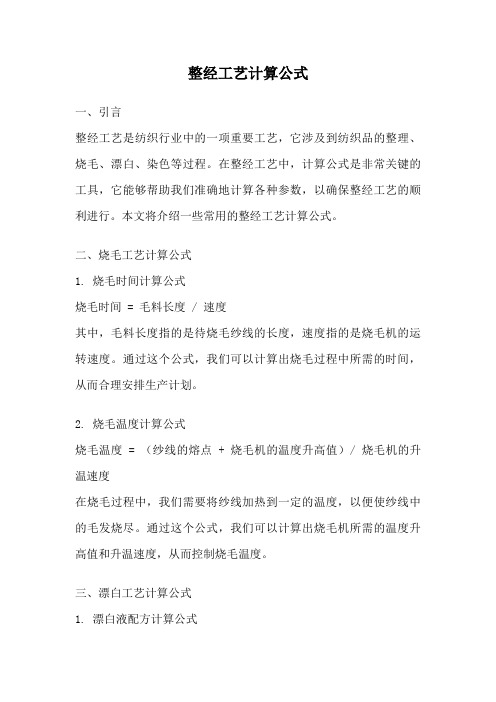
整经工艺计算公式一、引言整经工艺是纺织行业中的一项重要工艺,它涉及到纺织品的整理、烧毛、漂白、染色等过程。
在整经工艺中,计算公式是非常关键的工具,它能够帮助我们准确地计算各种参数,以确保整经工艺的顺利进行。
本文将介绍一些常用的整经工艺计算公式。
二、烧毛工艺计算公式1. 烧毛时间计算公式烧毛时间 = 毛料长度 / 速度其中,毛料长度指的是待烧毛纱线的长度,速度指的是烧毛机的运转速度。
通过这个公式,我们可以计算出烧毛过程中所需的时间,从而合理安排生产计划。
2. 烧毛温度计算公式烧毛温度 = (纱线的熔点 + 烧毛机的温度升高值)/ 烧毛机的升温速度在烧毛过程中,我们需要将纱线加热到一定的温度,以便使纱线中的毛发烧尽。
通过这个公式,我们可以计算出烧毛机所需的温度升高值和升温速度,从而控制烧毛温度。
三、漂白工艺计算公式1. 漂白液配方计算公式漂白液的配方可以根据纺织品的需求进行调整,一般包括漂白剂、稀释剂、助剂等。
配方的计算公式如下:漂白液配方 = (所需漂白剂量 / 漂白剂浓度)+ (所需稀释剂量/ 稀释剂浓度)+ (所需助剂量 / 助剂浓度)通过这个公式,我们可以计算出漂白液中各种成分的用量,从而调整漂白液的配方。
2. 漂白时间计算公式漂白时间 = 纺织品的长度 / 速度漂白过程中,我们需要将纺织品浸泡在漂白液中一段时间,以使其彻底漂白。
通过这个公式,我们可以计算出漂白过程中所需的时间,从而控制漂白过程的效率。
四、染色工艺计算公式1. 染料配方计算公式染料配方的计算公式根据染色的要求进行调整,一般包括染料的用量、助剂的用量等。
配方的计算公式如下:染料配方 = (染料用量 / 染料浓度)+ (助剂用量 / 助剂浓度)通过这个公式,我们可以计算出染色过程中染料和助剂的用量,从而调整染色液的配方。
2. 染色时间计算公式染色时间 = 纺织品的长度 / 速度染色过程中,我们需要将纺织品浸泡在染色液中一段时间,以使其染色均匀。
工艺参数的计算

采用未抛光的硅片进行加工,直径520.3m μ±,电阻率60~70cm Ω,厚度4208m μ±,晶向(111)面偏(110)方向3D 。
扩散源分为两种。
第一种:8:100g ml 23B O :乙醇=,超声8小时后,净置2~3天,配成饱和溶液,取1ml 的饱和溶液,加入10ml 乙醇,即可配置成110的扩散硼源,依例可配1100或1300的扩散源;第二种:Al(N 10:100g ml =33O ):乙醇,超声8小时后,净置2~3天,配成饱和溶液,涂源时可以直接使用。
扩散温度:1200C D ,扩散时间:44小时。
下面给出扩散时间的计算:22j x k Dt = (1)1200T C =D ,1228.310/D cm s −=×,60j x m μ=(2)17121131102(ln ) 5.51510k ×==× (3) 或131112175102(1)2(12(0.9995) 4.92110D S N k erf erf erf N −−−×=−=−× (4) 求平均 5.2k = (5)2422212(6010)16040544.65.28.310j x t s hr k D −−×==≈≈×× (6) 考虑到扩散后还需要慢降温,因此,我们取扩散时间为44hr 。
扩散22hr 后抽测结深,测试结果44.4j x m μ=。
扩散及慢降温结束后,测得结深62j x m μ=。
单项实验:一、预淀积硼,45/R =Ω,,(1个),30/R <Ω,,(2个)。
注意:温度不变,时间延长。
二、1140T C =D ,干2N 推进6′,硅片立放。
三、漂净BSG (1:10),去净,测量R ,四、推进,1140,3T C t hr ==D ,三片同时立放。
五、看硅片是否变形,光刻涂胶台能否吸住。
测量结深。
纺织品基础知识及常用工艺计算

纺织品基础知识及常用工艺计算纺织品是指人类使用纤维材料进行加工制作的各种织物、纱线和纤维制品。
纺织品广泛应用于日常生活中的各个方面,包括服装、家居装饰、家庭用品等。
在了解纺织品基础知识之前,我们先来了解一些常用的纺织品工艺计算。
常用的纺织品工艺计算主要包括纱线计算和织物计算。
纱线计算主要涉及纤维的长度和细度,纺纱工艺参数的计算等。
织物计算则关注于织物的密度、厚度、强度等方面的计算。
纱线计算是纺织品生产中的基础,其主要考虑纤维的长度和细度。
纱线的细度通常用纤维长度单位所含纱线长度的质量(TEX)来表示。
计算纱线的细度时,需要考虑纤维的长度和密度,通过将纤维长度除以纤维密度来计算。
例如,一根具有1米长度和1克质量的纤维,其细度为1TEX。
根据纤维的细度,可以确定纱线的适用范围和用途。
在纺纱工艺中,纱线的捻度是一个重要参数。
纱线的捻度对纱线的强度、柔软度和耐磨性等性能有着重要的影响。
纱线的捻度通常用“捻/英寸”或“捻/10厘米”来表示。
捻度的计算可以根据纱线的捻度和纺纱速度来确定。
捻度的选择需要根据纱线的用途和要求来进行调整。
织物计算是指根据织物的密度、厚度和强度等参数来计算织物的性能和使用范围。
织物的密度通常用“根/英寸"或“根/厘米"来表示。
密度的计算可以根据织物的纬线和经线数目来确定。
密度的选择需要根据织物的用途和要求来调整。
织物的厚度是指织物在垂直方向上的厚度。
厚度的计算可以通过测量织物的单位面积质量和密度来确定。
厚度的选择需要根据织物的用途和要求来调整。
织物的强度是指织物在拉伸过程中能够承受的力量。
强度的计算可以通过张力测试来确定。
强度的选择需要根据织物的用途和要求来调整。
总之,纺织品的基础知识和常用工艺计算对于纺织品生产和加工具有重要的意义。
通过了解纱线计算和织物计算,可以更好地理解纺织品的性能和适用范围,从而为纺织品的设计和生产提供依据。
同时,纺织品的工艺计算也为纺织品质量的保证和控制提供了重要的参考依据。
建筑结构设计七个重要参数

建筑结构设计七个重要参数建筑结构设计是建筑工程中至关重要的环节,它关乎到建筑的稳固性、经济性和安全性。
在进行建筑结构设计时,需要考虑七个重要参数,这些参数对于建筑结构的设计和建设起着至关重要的作用。
下面将详细介绍这七个重要参数。
参数一:荷载荷载是指对建筑结构施加的外力和外载荷。
外力包括自重、活载(人员、设备等)、风载、地震载、温度变化引起的荷载等。
荷载是建筑结构设计的基础,合理估计和分析荷载有助于确保结构的稳定性和安全性。
参数二:强度强度是指结构材料所能承受的最大外力或应力。
在建筑结构设计中,需要考虑材料的强度和抗力,以确保结构的安全性。
强度设计要充分考虑结构的各种不利因素,如荷载类型、弯曲、剪切、压缩等,并根据设计规范进行相应的计算和分析。
参数三:刚度刚度是指结构抵抗外力变形的能力。
在建筑结构设计中,需要考虑结构的刚度,以确保结构在受力后能够保持稳定。
刚度设计要充分考虑结构的几何形状、材料的性质,以及结构的连接方式,采用合适的刚度设计有助于提高结构的稳定性和整体性。
参数四:稳定性稳定性是指建筑结构在受到外力作用后仍能保持平衡和稳定的能力。
在建筑结构设计中,需要考虑结构的整体稳定性,以确保结构不会发生失稳和倒塌。
稳定性设计要充分考虑结构的几何形状、重心位置、支座条件等因素,采用合适的稳定性设计有助于提高结构的抗风、抗震能力。
参数五:耐久性耐久性是指建筑结构能够在长期使用条件下保持强度、刚度和稳定性的能力。
在建筑结构设计中,需要考虑结构的耐久性,以确保结构能够长期使用而不会出现损坏和退化。
耐久性设计要充分考虑结构材料的性质、外界环境的影响,采用合适的防护措施有助于延长结构的使用寿命。
参数六:经济性经济性是指在保证结构安全、稳定和耐久的前提下,以最少的材料和成本达到设计要求。
在建筑结构设计中,需要考虑结构的经济性,以确保在有限的资源条件下实现设计目标。
经济性设计要充分考虑结构的材料选择、结构形式和施工工艺,采用合适的经济性设计有助于减少成本和资源消耗。
高炉主要工艺参数计算公式

高炉主要工艺参数计算公式1、风口标准风速:V标=Q/(F×60)式中V标--风口标准风速,m/sQ――风量,m3/minF――风口送风总面积,m22.风口实际风速:V实= V标×(T+273)×0.1013/ (0.1013+P)X×(273+20)式中V实--风口实际风速m/sV标--风口标准风速m/sT--风温℃P--鼓风压力MPa3、鼓风动能:E=0.412 ×1/n × O3/F2 × (T+273)2/(P+P0)2式中E--鼓风动能,j/sQ--风量m3/minn--风口数目个F--风口总截面积m3T--热风温度℃P--热风压力MPaP0--标准大气压,等于101325PaV――炉缸煤气量m3V――炉缸煤气量m3 公式中未使用;(不用)4、焦炭负荷:P=Q矿/Q焦式中P--焦炭负荷Q矿--矿石批重kgQ焦--焦炭(干基)批重kg5、综合负荷:P=Q矿/Q焦式中P--综合负荷Q矿--矿石批重kgQ综焦--综合干焦量批重(干焦量十其它各种燃料量×折合干焦系数批重)kg6、休风率:u=t/T×100%式中u――休风率%t ——高炉休风停产时间minT——规定日历作业时间(日历时间减去计划达中休时间)min.7、生铁合格率生铁合格率是指检验合格生铁占全部检验生铁的百分比。
其计算公式为:生铁合格率(%)= 生铁检验合格量(t)×100%生铁检验总量(t)生铁检验合格量不进行折算,而焦比中合格生铁产量要进行折算计算说明:(1)高炉开工后,不论任何原因造成的出格生铁,均应参加生铁合格率指标的计算。
出格生铁指炼钢生铁S>0.070%,铸造铁生铁S>0.060% (2)用于炼钢的不合格铁水,不允许混罐,应按罐判定。
(3)入库前的混号铁,按出格铁计算。
8、生铁一级品率生铁一级品率是指一级品生铁量占合格生铁总量的百分比。
高炉炼铁技术主要工艺参数计算公式
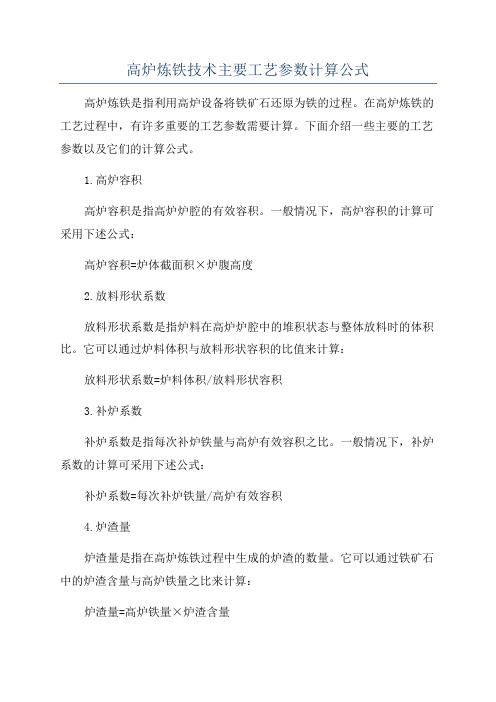
高炉炼铁技术主要工艺参数计算公式高炉炼铁是指利用高炉设备将铁矿石还原为铁的过程。
在高炉炼铁的工艺过程中,有许多重要的工艺参数需要计算。
下面介绍一些主要的工艺参数以及它们的计算公式。
1.高炉容积高炉容积是指高炉炉腔的有效容积。
一般情况下,高炉容积的计算可采用下述公式:高炉容积=炉体截面积×炉腹高度2.放料形状系数放料形状系数是指炉料在高炉炉腔中的堆积状态与整体放料时的体积比。
它可以通过炉料体积与放料形状容积的比值来计算:放料形状系数=炉料体积/放料形状容积3.补炉系数补炉系数是指每次补炉铁量与高炉有效容积之比。
一般情况下,补炉系数的计算可采用下述公式:补炉系数=每次补炉铁量/高炉有效容积4.炉渣量炉渣量是指在高炉炼铁过程中生成的炉渣的数量。
它可以通过铁矿石中的炉渣含量与高炉铁量之比来计算:炉渣量=高炉铁量×炉渣含量5.进料系数进料系数是指进入高炉的原料中铁矿石与高炉铁量之比。
一般情况下,进料系数的计算可采用下述公式:进料系数=铁矿石量/高炉铁量6.还原度还原度是指高炉还原反应的程度,也可以理解为高炉炼铁过程中铁矿石中铁元素的转化率。
还原度可以通过炉内原料的化学成分以及进气温度等因素进行估算。
7.炉渣碱度炉渣碱度是指炉渣中碱金属氧化物与二氧化硅之比。
一般情况下,炉渣碱度的计算可采用下述公式:炉渣碱度=(Na2O+K2O)/SiO2以上是一些高炉炼铁过程中常用的工艺参数及其计算公式。
当然,实际计算过程可能会更加复杂,因为高炉炼铁是一个多参数、多反应的复杂过程。
因此,在实际操作中需要根据具体情况综合考虑各个因素,并进行相应的修正计算。
化工工艺常用流速范围及管径计算
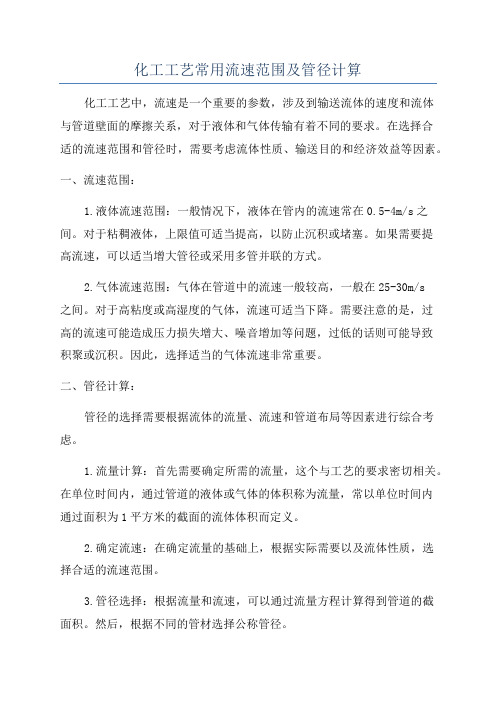
化工工艺常用流速范围及管径计算化工工艺中,流速是一个重要的参数,涉及到输送流体的速度和流体与管道壁面的摩擦关系,对于液体和气体传输有着不同的要求。
在选择合适的流速范围和管径时,需要考虑流体性质、输送目的和经济效益等因素。
一、流速范围:1.液体流速范围:一般情况下,液体在管内的流速常在0.5-4m/s之间。
对于粘稠液体,上限值可适当提高,以防止沉积或堵塞。
如果需要提高流速,可以适当增大管径或采用多管并联的方式。
2.气体流速范围:气体在管道中的流速一般较高,一般在25-30m/s之间。
对于高粘度或高湿度的气体,流速可适当下降。
需要注意的是,过高的流速可能造成压力损失增大、噪音增加等问题,过低的话则可能导致积聚或沉积。
因此,选择适当的气体流速非常重要。
二、管径计算:管径的选择需要根据流体的流量、流速和管道布局等因素进行综合考虑。
1.流量计算:首先需要确定所需的流量,这个与工艺的要求密切相关。
在单位时间内,通过管道的液体或气体的体积称为流量,常以单位时间内通过面积为1平方米的截面的流体体积而定义。
2.确定流速:在确定流量的基础上,根据实际需要以及流体性质,选择合适的流速范围。
3.管径选择:根据流量和流速,可以通过流量方程计算得到管道的截面积。
然后,根据不同的管材选择公称管径。
常用的计算公式有以下几种:a.流速公式:流速(m/s)=流量(m³/h)/(截面积(m²)*3600)b.等效直径公式:流量(m³/h)=流速(m/s)*(π/4)*管道内径²c. 直径公式:流量(m³/h)= 係数* π * 管道内径(mm)²其中,係数是根据具体的管道材料和内壁光滑程度确定的系数。
需要注意的是,选择管径时还要考虑管道材料、成本、施工条件等因素,综合考虑以满足工艺要求和经济效益。
总结起来,化工工艺中流速范围的选择需要结合流体性质、输送目的、经济效益等因素,常用的液体流速范围为0.5-4m/s,气体流速范围为25-30m/s。
轮对压装过程中几个关键工艺参数的分析

轮对压装过程中几个关键工艺参数的分析摘要:铁路客车轮对承受着车辆的全部载荷,并在负重的条件下沿轨道作高速运转,轮对压装作为重要工序之一,其参数直接影响着行车安全。
本文分析了轮对压装的工艺过程中的几个关键参数,阐述了压装过程中易产生的问题,分析了产生这些问题的原因。
关键词:轮对;工艺;参数轮对是铁路客车最主要的零部件之一,而轮对组装的质量是保证车辆在高速运行中安全的至关重要的环节,车轴、车轮经过几道工序的加工,最后冷压组装,轮轴的加工质量好坏直接影响到轮轴压装环节的合格与否。
通过对压装环节主要质量问题的分析,我们找到了引起这些问题的原因,并在相应生产工序中采取措施,加强了工艺管理。
1. 影响轮对一次压装合格率的因素轮轴压装合格与否是用压装曲线来判别的,所以压装曲线记录仪的灵敏度也直接影响着轮对一次压装合格率。
同时,为了保证所需的联接强度及防止轮对联接部分的应力过高,必须正确选择过盈量。
但在实践中只满足过盈量的选取值,并不能取得理想的压力曲线和终止压装力,它还受到配合表面几何形状误差等因素的制约。
1.1 轮座、轮毂孔锥度对压装合格率的影响通常,在车轮轮毂孔上加工0.04的正向锥度,车轴轮座上加工0.10的正向锥度,以保证曲线形状及终止压装力合格。
在轮对压装过程中,由于轮座、轮毂孔锥度不一致,轮轴配合表面各部位的尺寸(沿径向方向)都不相等,因而沿轴向方向每一横截面的过盈量也不相等。
如果轮座与轮毂孔圆锥度较大且方向一致时,在开始压装时,会出现压力小或没压力,而压装一定量的长度时随过盈量的增加压力迅速增大,造成曲线的长度不够。
1.2 测量误差对轮对压装合格率的影响由于外径干分尺和百分表本身的不确定度(外径千分±0.006 mm,百分表±0.O25mm),再加上选配时测量部位和测量温度及湿度的影响,对过盈量的选取值形成累积误差,不能反映轮轴尺寸的真实值,直接影响过盈量选取的准确性,导致轮对一次压装合格率下降。
(整理)几个重要工艺参数的计算.
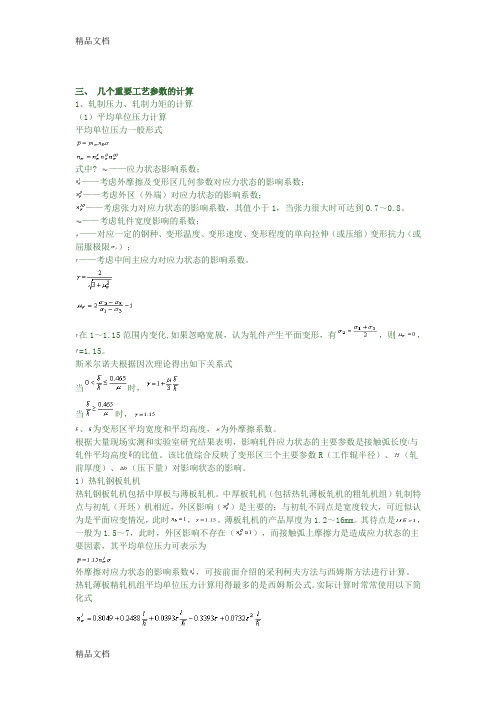
三、几个重要工艺参数的计算1、轧制压力、轧制力矩的计算(1)平均单位压力计算平均单位压力一般形式式中? ——应力状态影响系数;——考虑外摩擦及变形区几何参数对应力状态的影响系数;——考虑外区(外端)对应力状态的影响系数;——考虑张力对应力状态的影响系数,其值小于1,当张力很大时可达到0.7~0.8。
——考虑轧件宽度影响的系数;——对应一定的钢种、变形温度、变形速度、变形程度的单向拉伸(或压缩)变形抗力(或屈服极限);——考虑中间主应力对应力状态的影响系数。
在1~1.15范围内变化,如果忽略宽展,认为轧件产生平面变形,有,则,=1.15。
斯米尔诺夫根据因次理论得出如下关系式当时,当时,、为变形区平均宽度和平均高度,为外摩擦系数。
根据大量现场实测和实验室研究结果表明,影响轧件应力状态的主要参数是接触弧长度与轧件平均高度的比值。
该比值综合反映了变形区三个主要参数R(工作辊半径)、(轧前厚度)、(压下量)对影响状态的影响。
1)热轧钢板轧机热轧钢板轧机包括中厚板与薄板轧机。
中厚板轧机(包括热轧薄板轧机的粗轧机组)轧制特点与初轧(开坯)机相近,外区影响()是主要的;与初轧不同点是宽度较大,可近似认为是平面应变情况,此时,。
薄板轧机的产品厚度为1.2~16mm。
其待点是,一般为1.5~7,此时,外区影响不存在(),而接触弧上摩擦力是造成应力状态的主要因素,其平均单位压力可表示为外摩擦对应力状态的影响系数,可按前面介绍的采利柯夫方法与西姆斯方法进行计算。
热轧薄板精轧机组平均单位压力计算用得最多的是西姆斯公式。
实际计算时常常使用以下简化式或美板佳助简化式。
2)冷轧带钢轧机冷轧带钢轧机的轧件尺寸更接近于推导理论公式时所做的假设,即宽度比厚度大得多,宽展很小,可认为是平面变形问题。
轧件厚度小,轧件内部不均匀变形可忽略,因而平面断面假设和滑动摩擦理论与冷轧带钢(薄板)的情况较符合。
此外,冷轧时均采用张力轧制,因而计算冷轧平均单位压力时,必须考虑张力影响。
化学技术实验中的关键工艺参数选择与设定方法总结

化学技术实验中的关键工艺参数选择与设定方法总结在化学技术实验中,关键工艺参数的选择与设定是确保实验准确性和可重复性的关键步骤。
不同的化学实验需要根据具体要求选择不同的工艺参数,如温度、压力、浓度等。
本文将总结一些常见的关键工艺参数选择与设定方法,帮助研究人员进行实验设计和工艺优化。
首先,温度是化学实验中最常见的关键工艺参数之一。
不同的化学反应需要在特定温度下进行,以确保反应速率和产物品质。
选择适当的反应温度应考虑到反应的热力学和动力学要求。
一般来说,较高温度可以加快反应速率,但过高的温度可能导致副反应、产物分解或安全问题。
因此,实验中应通过文献查询或试验确定最佳的反应温度范围,并通过较小的步长进行优化。
其次,压力也是一些特定化学实验中的关键工艺参数。
例如,在高压条件下进行催化反应可以提高反应速率和选择性。
在选择压力时,需要考虑反应物的物理性质和反应条件的安全性。
实验中可以通过改变反应器尺寸、添加催化剂或调整反应物浓度来调节压力。
此外,压力传感器的应用也是确保实验稳定性和数据准确性的重要手段。
浓度是另一个决定化学反应性质的重要参数。
在涉及液相反应的实验中,合理控制反应物浓度可以调节反应速率和副产物生成。
一般来说,较高的浓度可以增加反应物分子间的碰撞频率,从而加速反应进程。
然而,过高的浓度可能导致剧烈的副反应或产物结晶。
因此,实验中应以较小的步长逐渐增加反应物浓度,并对反应过程进行实时监测。
此外,反应时间也是决定化学实验成功与否的重要参数之一。
在实验设计时,需要确定反应时间范围,并进行步长优化。
反应时间的选择应考虑到反应物的性质、反应速率和理想产物的收率。
短时间可能导致不完全反应,而过长时间可能导致反应物分解、产物副产物生成或设备损坏。
因此,通过实验或模型计算确定最佳反应时间是确保实验结果准确和可重复的关键步骤。
最后,pH值和溶剂选择也是化学实验中需要注意的关键工艺参数。
在一些催化反应或酶催化反应中,pH值可以影响反应速度和选择性。
几个重要工艺参数的计算

三、几个重要工艺参数的计算1、轧制压力、轧制力矩的计算(1)平均单位压力计算平均单位压力一般形式式中? ——应力状态影响系数;——考虑外摩擦及变形区几何参数对应力状态的影响系数;——考虑外区(外端)对应力状态的影响系数;——考虑张力对应力状态的影响系数,其值小于1,当张力很大时可达到0.7~0.8。
——考虑轧件宽度影响的系数;——对应一定的钢种、变形温度、变形速度、变形程度的单向拉伸(或压缩)变形抗力(或屈服极限);——考虑中间主应力对应力状态的影响系数。
在1~1.15范围内变化,如果忽略宽展,认为轧件产生平面变形,有,则,=1.15。
斯米尔诺夫根据因次理论得出如下关系式当时,当时,、为变形区平均宽度和平均高度,为外摩擦系数。
根据大量现场实测和实验室研究结果表明,影响轧件应力状态的主要参数是接触弧长度与轧件平均高度的比值。
该比值综合反映了变形区三个主要参数R(工作辊半径)、(轧前厚度)、(压下量)对影响状态的影响。
1)热轧钢板轧机热轧钢板轧机包括中厚板与薄板轧机。
中厚板轧机(包括热轧薄板轧机的粗轧机组)轧制特点与初轧(开坯)机相近,外区影响()是主要的;与初轧不同点是宽度较大,可近似认为是平面应变情况,此时,。
薄板轧机的产品厚度为1.2~16mm。
其待点是,一般为1.5~7,此时,外区影响不存在(),而接触弧上摩擦力是造成应力状态的主要因素,其平均单位压力可表示为外摩擦对应力状态的影响系数,可按前面介绍的采利柯夫方法与西姆斯方法进行计算。
热轧薄板精轧机组平均单位压力计算用得最多的是西姆斯公式。
实际计算时常常使用以下简化式或美板佳助简化式。
2)冷轧带钢轧机冷轧带钢轧机的轧件尺寸更接近于推导理论公式时所做的假设,即宽度比厚度大得多,宽展很小,可认为是平面变形问题。
轧件厚度小,轧件内部不均匀变形可忽略,因而平面断面假设和滑动摩擦理论与冷轧带钢(薄板)的情况较符合。
此外,冷轧时均采用张力轧制,因而计算冷轧平均单位压力时,必须考虑张力影响。
工艺计算常用公式与数据
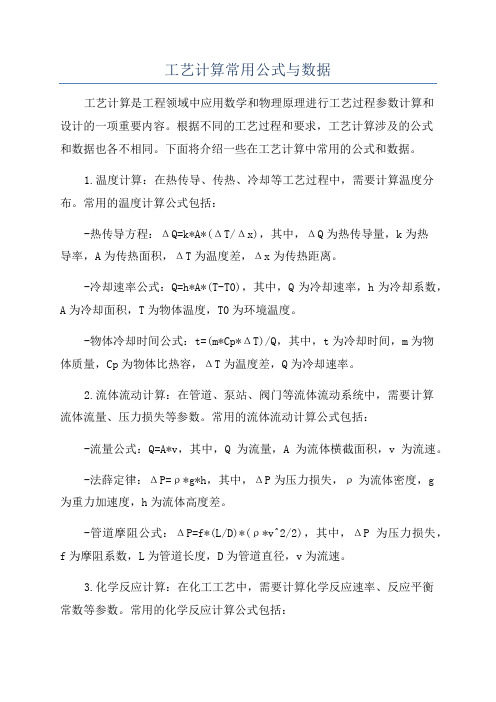
工艺计算常用公式与数据工艺计算是工程领域中应用数学和物理原理进行工艺过程参数计算和设计的一项重要内容。
根据不同的工艺过程和要求,工艺计算涉及的公式和数据也各不相同。
下面将介绍一些在工艺计算中常用的公式和数据。
1.温度计算:在热传导、传热、冷却等工艺过程中,需要计算温度分布。
常用的温度计算公式包括:-热传导方程:ΔQ=k*A*(ΔT/Δx),其中,ΔQ为热传导量,k为热导率,A为传热面积,ΔT为温度差,Δx为传热距离。
-冷却速率公式:Q=h*A*(T-T0),其中,Q为冷却速率,h为冷却系数,A为冷却面积,T为物体温度,T0为环境温度。
-物体冷却时间公式:t=(m*Cp*ΔT)/Q,其中,t为冷却时间,m为物体质量,Cp为物体比热容,ΔT为温度差,Q为冷却速率。
2.流体流动计算:在管道、泵站、阀门等流体流动系统中,需要计算流体流量、压力损失等参数。
常用的流体流动计算公式包括:-流量公式:Q=A*v,其中,Q为流量,A为流体横截面积,v为流速。
-法薛定律:ΔP=ρ*g*h,其中,ΔP为压力损失,ρ为流体密度,g为重力加速度,h为流体高度差。
-管道摩阻公式:ΔP=f*(L/D)*(ρ*v^2/2),其中,ΔP为压力损失,f为摩阻系数,L为管道长度,D为管道直径,v为流速。
3.化学反应计算:在化工工艺中,需要计算化学反应速率、反应平衡常数等参数。
常用的化学反应计算公式包括:-反应速率公式:r=k*[A]^n*[B]^m,其中,r为反应速率,k为速率常数,[A]、[B]为反应物浓度,n、m为反应级数。
-反应平衡常数公式:K=[C]^c/[A]^a*[D]^d/[B]^b,其中,K为平衡常数,[A]、[B]、[C]、[D]为反应物浓度,a、b、c、d为反应物摩尔比。
4.电路计算:在电子电路设计中,需要计算电流、电压、功率等参数。
常用的电路计算公式包括:-电流公式:I=V/R,其中,I为电流,V为电压,R为电阻。
简述工艺计算包括的内容。

简述工艺计算包括的内容。
工艺计算是指在工程和制造过程中,通过运用数学和物理等科学原理,对工艺参数进行计算和分析,以确定最佳的工艺方案和操作参数。
它是工程技术领域中的一项重要工作,能够提高生产效率、降低成本、改善产品质量。
工艺计算包括以下几个方面的内容:1. 工艺流程计算:工艺流程是指物料在生产中的处理过程,包括物料的输入、加工和输出等环节。
在工艺流程计算中,需要确定物料的流量、温度、压力等参数,以及各个环节中的能耗和产量等指标。
通过对工艺流程进行计算和分析,可以确定最佳的生产工艺,提高生产效率和产品质量。
2. 材料配方计算:材料配方是指在生产中使用的原材料的比例和配比关系。
在材料配方计算中,需要根据产品的要求和性能指标,确定各个原材料的比例和配比。
通过对材料配方进行计算和分析,可以确定最佳的原材料组合,提高产品的性能和质量。
3. 设备选型计算:设备选型是指在生产中选择适合的设备和工具。
在设备选型计算中,需要考虑生产的工艺要求、生产能力和设备的性能指标等因素。
通过对设备选型进行计算和分析,可以确定最佳的设备和工具,提高生产效率和产品质量。
4. 工艺参数优化计算:工艺参数优化是指在生产过程中,通过调整工艺参数,使产品的性能和质量达到最佳状态。
在工艺参数优化计算中,需要分析生产过程中各个环节的参数和指标,确定最佳的工艺参数。
通过对工艺参数进行优化计算,可以提高产品的性能和质量,降低生产成本。
5. 能耗计算:能耗是指生产过程中消耗的能量。
在能耗计算中,需要对生产过程中的各个环节进行能耗分析,确定能耗的来源和消耗情况。
通过对能耗进行计算和分析,可以找出能耗的问题和瓶颈,采取相应的措施减少能耗,提高能源利用效率。
6. 生产成本计算:生产成本是指生产过程中所需的各种资源和费用。
在生产成本计算中,需要对生产过程中的各个环节进行成本分析,确定各项费用的来源和消耗情况。
通过对生产成本进行计算和分析,可以找出成本的问题和瓶颈,采取相应的措施降低成本,提高生产效益。
TOFD检测中相关工艺参数计算

31 上 表 面盲 区深 度 计 算 .
关于厚壁焊缝T F 分 区检测 ,国内外标准 中有等深度分 OD 区和不等深度 分区两种思路 。本 文按J f4 301 2 0 的规 Br7 . 0— 0 5
影响上表面盲 区的因素主要是探头频率 和P S 对于近表 C, 面 的埋藏缺 陷, 由于脉 冲宽度 的原因 , 通波信号和缺陷 的衍 直 射信号肯定会混在一起 , 这样 即使 能发现缺陷 , 此时对缺 陷高
板对接接头的探 头推荐性选择 和设置 的规定 。
13 探 头 中心 距PC . S
上测试 出上表面盲区深度 , 同时在检测工艺 中也通常要求计算
出上表面盲区深度 。 我们在实际计算 中直通波脉冲持续时间通 常取 1 . 个信号周期 。 5~2
32 下表 面盲 区深 度 计 算 .
对探 头中心距 P S C 的确 定 ,按 照J /4 301 2 0 的规 BT 7 . 0— 0 5
245 5= 22 。 . . )2 . ; /9 7
度; 计算下表 面盲 区深度 ; 根据 给定 的盲 区深度和偏离值 , 计算 偏置扫查次数 ; 计算最 大扫查速度 ; 计算检测 宽度范 围和 打磨
宽度等 。 本文通过对个参数 的距离计算 , 来简要说 明整个T F OD 工艺 中的计算过程。
度的测量也会有很大 的误差 。 在实际工作 中通常是通过在试块
定, 采用不等深度分层 。 分的几个 区域厚度逐渐变化 , 所 一般是
第一对 探头检测 的深度较小 , 即采用较 小的P S 后 面探 头检 C,
测 的深度范 围逐渐增大 。具体要求按J / 7 01— 0 0 1 BT4 3 . 2 1表 平 0
机械工艺技术计算

机械工艺技术计算机械工艺技术是机械制造业的核心技术之一,它对于机械制造过程中的各种工艺参数的计算至关重要。
本文将探讨机械工艺技术的计算方法以及其在机械制造过程中的应用。
首先,机械工艺技术的计算方法主要包括几何尺寸计算、工艺参数计算和加工工艺数值模拟等。
几何尺寸计算是指根据物体的形状、尺寸和公差要求,进行几何参数的计算。
例如,在零件的设计过程中,需要计算出其长度、宽度、高度等几何尺寸。
工艺参数计算包括工作量的计算、工时的计算、生产能力的计算等。
例如,在机械制造过程中,需要计算出每个工序的加工时间,以及整个工艺流程的总加工时间。
加工工艺数值模拟是通过利用计算机软件进行数值模拟,对机械加工过程进行仿真和优化。
通过模拟计算,可以验证机械加工过程的可行性,并且找到最优化的工艺参数。
其次,机械工艺技术的计算方法在机械制造中有着广泛的应用。
首先,它可以对机械零件的几何尺寸进行计算,从而保证零件的尺寸精度和公差要求。
例如,在机械加工过程中,需要根据设计图纸上的几何要求,计算出机械零件的精确尺寸,以便于进行下一步的加工操作。
其次,它可以对机械制造过程中的工艺参数进行计算,以保证加工效率和质量。
例如,在数控加工中,需要计算出每个工序的加工时间,并根据不同的工艺参数进行优化,以提高加工效率和质量。
此外,机械工艺技术的计算方法还可以在机械制造过程中进行加工工艺的数值模拟,以预测加工过程中的变形、剧变等问题,从而优化工艺参数并提高加工质量。
最后,在进行机械工艺技术计算时,需要注意一些关键问题。
首先,需要使用合适的计算方法和工具,例如使用数学计算软件、计算机辅助设计软件等。
其次,需要根据实际情况进行准确的数据输入,以保证计算结果的准确性。
此外,需要不断学习和掌握新的工艺技术和计算方法,以适应快速发展的机械制造业。
总之,机械工艺技术的计算是机械制造过程中必不可少的一环。
通过准确计算几何尺寸、工艺参数和进行加工工艺数值模拟,可以保证机械零部件的质量和加工效率,并提高机械制造的水平。
第七章1工艺参数的计算
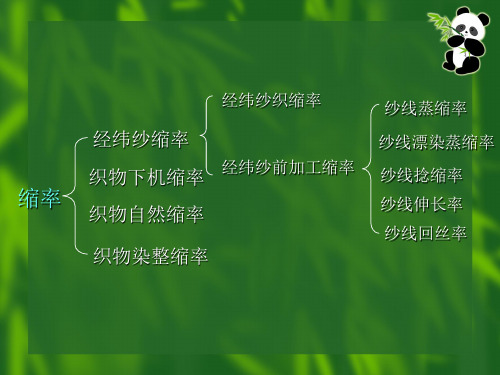
(三)筘号的确定和计算 筘号是根据经纱特数、密度、织物组织及每筘穿入数等来确定。筘号选用正确与否会影响经纱断头率、织物幅宽、经密和织物风格等。 筘号分公制筘号Nk和英制筘号Ne。(Ne=0.508Nk) 1.筘号计算公式
一般情况下: 斜纹布,哔叽,色织府绸,平布等为2%左右 卡其,府绸,色织格布为3% 劳动布,鞋用帆布大于3% 毛织品:2%~3%
2.自然缩率 指织物在折叠成件打包存放后所产生的缩率 自然缩率=(成包前织物长度-成包后织物长度) ÷成包前织物长度×100% 棉布成包后1-2个月内缩变较大,随时间延长逐渐稳定.一般:高特纱织物和卡其织物约为1%-2%(全线卡其3%);平布约0.5%-1.5%;色织物:0.55%-0.85%
2. 织物密度 可分为成品密度,坯布密度,公制单位为:根/10cm, 小数后不足0.5舍去;在0.5-1之间计0.5; 英制单位为:根/英寸,一般取整数 坯布密度又分为机上和机下密度 本白坯织物规格中所给的经纬密度一般指下机坯布的经纬密度,其与成品密度的关系如下: (下机)坯布经密(根/10cm)=成品经密×成品幅宽/坯布幅宽 (下机)坯布纬密(根/10cm)=成品纬密×(1-染整长缩率)
(1)经纱百米用纱量(kg/百米) = (2)纬纱百米用纱量(kg/百米) =
例题:某一中平布,其规格如下:254*248(根/10cm),25*28tex,91.5cm,1/1, 其中边纱共24根,地入筘数为2,边入筘数为4, 求: 1、总经根数 2、经织缩率 3、百米经、纬纱用纱量 (附:(25+28)tex分档织缩系数为:0.0208; 25 tex用纱量系数:0.002509;28 tex用纱量系数:0.002855)
包覆纱机工艺计算方法

包覆纱机工艺计算方法
包覆纱机是一种用于生产各种包覆线的设备。
它通过将一根或多根芯线缠绕在外层纤维上来制成包覆线。
在包覆纱机中,有几个关键的工艺参数需要考虑,包括包覆比、绕线速度和张力等。
接下来将分别介绍这些参数以及计算方法。
1. 包覆比
包覆比是指包覆线中外层纤维的重量与总重量之比。
包覆比的大小对织物的品质和性能起着至关重要的作用。
包覆比的计算方法如下:
包覆比= (外层纤维重量/ 总重量) ×100%
其中,外层纤维重量是指包覆线中外层纤维所占的重量,总重量是指包覆线的总重量。
2. 绕线速度
绕线速度是指芯线在包覆纱机上的运动速度。
绕线速度的大小对包覆线的品质和生产效率有着重要的影响。
绕线速度的计算方法如下:
绕线速度= π×直径×转速
其中,π是圆周率,直径是指芯线或外层纤维的直径,转速是指包覆轮的转速。
3. 张力
张力是指芯线或外层纤维在包覆过程中所受的拉力。
张力的大小对于包覆线的品质和成品的物理性能有着重要的影响。
张力的计算方法如下:
张力= 力/ 面积
其中,力是指所施加的拉力,面积是指所受力的截面积。
总之,包覆纱机工艺的计算方法主要涉及包覆比、绕线速度和张力等关键参数的计算,这些参数的大小对于包覆线的品质和生产效率有着重要的影响。
在生产过程中需要根据具体的情况进行适当的调整,以确保生产出高品质的包覆线。
芯片 工艺复杂度计算

芯片工艺复杂度计算
芯片工艺复杂度的计算是一个综合考虑多个因素的过程。
下面是一些常见的计算指标和方法:
1. 晶圆直径:晶圆直径是一个重要的参数,通常以英寸为单位。
较大的晶圆直径可以容纳更多的芯片,从而提高生产效率。
常见的晶圆直径包括8英寸、12英寸等。
2. 制程层级:制程层级指的是芯片制造过程中不同工艺步骤的数量和复杂程度。
通常包括沉积、刻蚀、光刻、离子注入等多个层级。
制程层级越多,芯片工艺复杂度就越高。
3. 特征尺寸:特征尺寸是指芯片上最小可制造结构的尺寸。
特征尺寸越小,代表着制造过程的精度要求越高,工艺复杂度也会相应增加。
4. 工艺规则:工艺规则是指制造芯片时需要遵循的一系列设计要求和限制条件。
不同工艺规则对芯片设计和制造的要求不同,具体的工艺规则也会对工艺复杂度产生影响。
5. 设备和材料:芯片制造过程需要使用特定的设备和材料,例如光刻机、蚀刻机、掺杂装置等。
这些设备的性能和工艺要求会对工艺复杂度产生影响。
综上所述,芯片工艺复杂度的计算需要综合考虑晶圆直径、制程层级、特征尺寸、工艺规则以及设备和材料等因素。
不同芯片的工艺复杂度会有所差异,一般来说,工艺复杂度越高,制造成本和技术难度也会相应增加。
年产14万吨液氨合成工段工艺计算

年产14万吨液氨合成工段工艺计算液氨是一种广泛应用于化工、农业和其他领域的重要化工原料。
为了满足市场需求,液氨的生产必须高效、稳定和可持续。
本文将以年产14万吨液氨的合成工段工艺计算为题,介绍液氨的生产过程及其相关工艺参数。
液氨的合成是一种通过催化剂将氮气和氢气反应生成氨的过程。
合成氨的主要工艺是哈伯-博什过程,该过程在高温高压条件下进行。
具体来说,液氨的合成工段通常包括以下几个步骤:1. 氮气的净化和压缩:从大气中获取氮气后,需要通过净化工艺去除其中的杂质,如氧气、水分和其他杂质。
净化后的氮气被压缩到合成反应所需的压力。
2. 氢气的制备和净化:氢气一般通过蒸汽重整和变换反应制备。
制备后的氢气需要经过净化工艺去除其中的杂质,如氧气、硫化物和其他杂质。
3. 氮气和氢气的混合:净化后的氮气和氢气按照一定的比例混合,以便在合成反应中获得最佳的反应效果。
4. 合成反应:混合后的氮气和氢气进入合成反应器,通过催化剂的作用,在高温高压条件下发生反应。
反应生成的氨气被冷却成液体状态,作为产品进行收集。
5. 氨气的分离和精制:产生的液氨需要经过一系列的分离和精制工艺,去除其中的杂质,以提高液氨的纯度和质量。
在年产14万吨液氨合成工段工艺计算中,需要考虑以下几个关键参数:1. 反应器规模:合成液氨的反应器规模直接影响年产量。
根据年产14万吨的要求,需要确定合适的反应器规模,以满足产量需求。
2. 反应温度和压力:合成氨的反应温度和压力对反应速率和产量有重要影响。
根据实验和工程经验,确定合适的反应温度和压力范围,以达到最佳的反应效果。
3. 催化剂选择和循环:催化剂是液氨合成的关键。
选择合适的催化剂类型和循环方式,以保证催化剂的活性和稳定性。
4. 氮气和氢气比例:合成氨的反应需要适当的氮气和氢气比例。
通过调整混合气体的比例,以获得最佳的反应效果和氨气产量。
5. 分离和精制工艺:液氨的分离和精制工艺决定了液氨的纯度和质量。
- 1、下载文档前请自行甄别文档内容的完整性,平台不提供额外的编辑、内容补充、找答案等附加服务。
- 2、"仅部分预览"的文档,不可在线预览部分如存在完整性等问题,可反馈申请退款(可完整预览的文档不适用该条件!)。
- 3、如文档侵犯您的权益,请联系客服反馈,我们会尽快为您处理(人工客服工作时间:9:00-18:30)。
三、几个重要工艺参数的计算
、轧制压力、轧制力矩的计算
()平均单位压力计算
平均单位压力一般形式
式中? ——应力状态影响系数;
——考虑外摩擦及变形区几何参数对应力状态的影响系数;
——考虑外区(外端)对应力状态的影响系数;
——考虑张力对应力状态的影响系数,其值小于,当张力很大时可达到~。
——考虑轧件宽度影响的系数;
——对应一定的钢种、变形温度、变形速度、变形程度的单向拉伸(或压缩)变形抗力(或屈服极限);
——考虑中间主应力对应力状态的影响系数。
在~范围内变化,如果忽略宽展,认为轧件产生平面变形,有,则,。
斯米尔诺夫根据因次理论得出如下关系式
当时,
当时,
、为变形区平均宽度和平均高度,为外摩擦系数。
根据大量现场实测和实验室研究结果表明,影响轧件应力状态的主要参数是接触弧长度与轧件平均高度的比值。
该比值综合反映了变形区三个主要参数(工作辊半径)、(轧前厚度)、(压下量)对影响状态的影响。
)热轧钢板轧机
热轧钢板轧机包括中厚板与薄板轧机。
中厚板轧机(包括热轧薄板轧机的粗轧机组)轧制特点与初轧(开坯)机相近,外区影响()是主要的;与初轧不同点是宽度较大,可近似认为是平面应变情况,此时,。
薄板轧机的产品厚度为~。
其待点是,一般为~,此时,外区影响不存在(),而接触弧上摩擦力是造成应力状态的主要因素,其平均单位压力可表示为
外摩擦对应力状态的影响系数,可按前面介绍的采利柯夫方法与西姆斯方法进行计算。
热轧薄板精轧机组平均单位压力计算用得最多的是西姆斯公式。
实际计算时常常使用以下简化式
或美板佳助简化式。
)冷轧带钢轧机
冷轧带钢轧机的轧件尺寸更接近于推导理论公式时所做的假设,即宽度比厚度大得多,宽展
很小,可认为是平面变形问题。
轧件厚度小,轧件内部不均匀变形可忽略,因而平面断面假设和滑动摩擦理论与冷轧带钢(薄板)的情况较符合。
此外,冷轧时均采用张力轧制,因而计算冷轧平均单位压力时,必须考虑张力影响。
其平均单位压力可表示为
计算冷轧带钢轧机平均单位压力常采用斯通方法,亦可采用考虑张力影响后的采利柯夫方法或其柯洛辽夫简化公式。
柯洛辽夫简化公式为
,
式中? ——变形程度(压下率);
、——变形区入口和出口处轧件受到的张应力。
由于冷轧带钢较薄较硬,因此接触弧上的单位压力较大,使轧辊在接触处产生压扁现象,加长了接触弧的实际长度。
由于接触弧长度的加大,势必增强轧辊与轧件接触面上摩擦力的影响,从而使单位压力加大。
因此,在计算冷轧薄板平均单位压力时,必须考虑轧辊弹性压扁现象。
冷轧时由于存在加工硬化现象,在计算冷轧薄板平均单位压力时,轧件材料变形抗力(对冷轧亦可称为屈服极限)需按考虑加工硬化后的选用。
由于存在加工硬化影响,各道次的变形抗力不仅与本道次变形程度有关,而且还与前面各道次的总变形程度有关。
对本道次来说,沿接触弧的也是变化的,出口处比入口处要大,计算时一般把变形区作为圆弧(或抛物线)变化来计算平均总变形程度,按此平均总变形程度来计算或选取平均变形抗力。
平均总变形程度用下式计算
式中? ——本道次入口处的总变形程度(从退火状态开始各道次变形程度的累计),
——本道出口处的总变形程度,
——退火状态坯料原始厚度;
、——本道次轧件轧前轧后厚度。
a——系数,一般取;
b——系数,一般取。
通常取,;在选取a、b数值时,a与b的和必须等于1。
()轧制压力的计算
轧件对轧辊的总压力P为轧制平均单位压力与轧件和轧辊接触面积F之乘积,即
接触面积F的一般形式为。