立磨常见问题及处理.
立磨常见问题及处理

立磨常见问题及处理 Document number:WTWYT-WYWY-BTGTT-YTTYU-2018GT立磨常见问题及处理立磨操作相对来说工艺原理简单些,但恰恰是目前水泥厂有效运转率提不高的一个系统。
如何稳定料层。
料层厚,物料有效粉磨稍有下降,成品率下降,主电机电流大,差压升高。
料层薄,振动大,吐渣大。
不同磨机料层控制厚度不同,料层厚度一般是±20mm 但在其控制范围内上述现象是一致的。
稳定料层是操作立磨的关键。
料层通过压力增减或喂料量增减来控制,喷水量一般是在料层稳不住时作为手段。
如何稳定差压和主电机电流。
差压是反映磨内气流阻力大小的参数,在正常工况下其变化,可从磨盘物料的增多和气流中粉尘浓度增加两个方向上去理解。
是喂料与成品动态平衡的反映。
一般地在主电机电流平衡、料层平稳、振动平衡时,差值高说明磨机能力发挥出来了。
压差在上升时,同时伴随主电机电流上升、选粉机电流上升。
一般地通过喂料量来适应差压值,动工作压力影响料层、动风在正常负荷时空间不大,会引起磨内风速变化、选粉转速与细度有影响。
工作压力高,磨机电流高。
料层厚,磨电流高。
但料层过薄时,磨主电机电流波动大,瞬间易过流。
磨机的振动磨机振动是立磨存在的一个现象,振动过大会造成磨盘和磨辊衬板及附属设备的损坏。
引起因素较多,如入磨物料粒度不均匀、磨辊和磨盘衬板磨损严重、风量及风温的波动、研磨压力过高或过低、磨内异物、料层过厚或过薄、蓄能器压力不当、刮料板磨损导致的刮料腔积料多引起的风量分布不均、喂料量波动大等。
常见问题立磨入料溜子堵料。
入磨三道锁风阀或回转阀跳停。
磨机差压降低,选粉机电流降低,相应地出磨风温升高,磨机振动持续在较高的水平上波动。
这种振动不同于磨内异物引起的突发性振动,即瞬间出现很高的峰值,是较正常值高1-2mm/s的振幅上持续振动。
堵的部位不同,如回转下料器卡料、其上方或下方出磨溜子堵料。
主电机电流异常升高30%,如果料层厚度正常,则预示刮料腔内有积料可能。
立磨生产过程中出现的各类问题及解决方法(全)

立磨生产过程中出现的各类问题及解决方法(全)1.立磨差压高的原因及处理措施1)喂料量大,粉磨能力不够。
处理:根据磨机功率,适当减产。
2)产品太细,内部循环负荷值高。
处理:降低选粉机转速。
3)选粉机可能堵塞。
处理:停磨检查。
4)选粉机导向角太窄或者长度太长,限制了料子顺利通过出口。
5)挡料环过高,造成内部循环负荷高。
处理:停磨调整。
6)刮料板断或掉,未形成回料。
物料挡板断或掉,形成大量回料。
处理:停磨检修。
7)磨内气流量小,影响物料通过选粉机。
处理:磨机风机加大抽风量,调节风机进口风门。
8)入磨压力管发生堵塞,入磨压力(负压值)返回变小,造成磨内差压显示值偏高。
处理:通知仪表工进行处理。
9)入磨风温太高、风速太快,物料在磨盘上无法形成料层,悬浮在磨内,造成压差高。
处理:调节增湿塔温度或调节外风(或循环风),降低入磨风温,减缓风速。
10)操作中外风利用太多或回料(拉链机)侧门被打开,致使入磨压下降,减缓了磨系统的内循环,加大了外循环的回料,使其富集,造成磨内差压变高。
处理:操作中调节磨系统的内循环,加大外循环的回料,关闭各门,杜绝漏风现象的发生。
11)物料的研磨性很差,物料难磨,造成磨内压差很高。
处理:减产运行或适量增加研压或现场检查压力罐。
12)立磨长时间运行,使磨内石英晶体含量增大,致使物料难磨,差压升高。
处理:减产运行或把这部分物料排出磨外。
2.立磨振动大的原因及处理措施正常操作中没有维持立磨合理料层和料面形状,就会引起立磨振动。
经实践分析,我们认为引起立磨振动原因以及处理措施有以下几个方面:1)磨内进入异物引起振动。
来自磨内和磨外的金属异物,如导风叶片,检修后遗留工具等。
若是较小金属则可提起磨辐、降低抽风,由回料下料口处拿出;若是较大金属则要开磨门取出。
2)料层过厚引起振动。
入磨物料量过大f料层变厚一研磨能力降低一物料不能及时被研细一磨内存留不合格粉料较多,而系统风量又不足,喷环风速减小一不能将合格粉料及时带出系统外f磨腔内循环浓度加重一粉状物料又回到磨盘上一加厚料层。
立磨在生产中出现的几个问题及解决办法
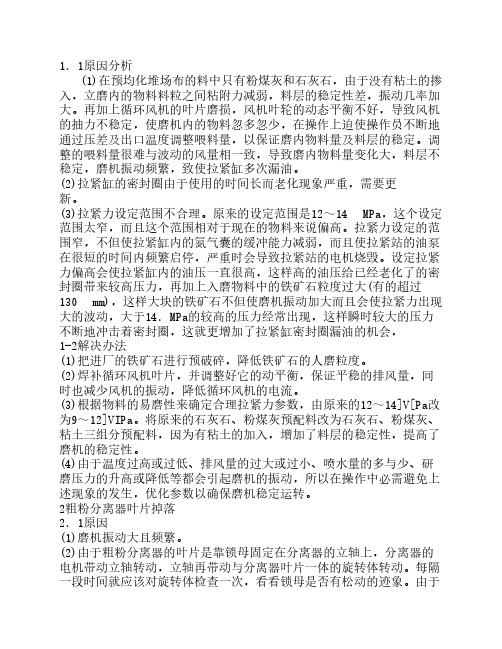
1.1原因分析(1)在预均化堆场布的料中只有粉煤灰和石灰石,由于没有粘土的掺入,立磨内的物料料粒之间粘附力减弱,料层的稳定性差,振动几率加大。
再加上循环风机的叶片磨损,风机叶轮的动态平衡不好,导致风机的抽力不稳定,使磨机内的物料忽多忽少,在操作上迫使操作员不断地通过压差及出口温度调整喂料量,以保证磨内物料量及料层的稳定。
调整的喂料量很难与波动的风量相一致,导致磨内物料量变化大,料层不稳定,磨机振动频繁,致使拉紧缸多次漏油。
(2)拉紧缸的密封圈由于使用的时间长而老化现象严重,需要更新。
(3)拉紧力设定范围不合理。
原来的设定范围是12~14 MPa,这个设定范围太窄,而且这个范围相对于现在的物料来说偏高。
拉紧力设定的范围窄,不但使拉紧缸内的氮气囊的缓冲能力减弱,而且使拉紧站的油泵在很短的时间内频繁启停,严重时会导致拉紧站的电机烧毁。
设定拉紧力偏高会使拉紧缸内的油压一直很高,这样高的油压给已经老化了的密封圈带来较高压力,再加上入磨物料中的铁矿石粒度过大(有的超过130 mm),这样大块的铁矿石不但使磨机振动加大而且会使拉紧力出现大的波动,大于14.MPa的较高的压力经常出现,这样瞬时较大的压力不断地冲击着密封圈,这就更增加了拉紧缸密封圈漏油的机会,1-2解决办法(1)把进厂的铁矿石进行预破碎,降低铁矿石的人磨粒度。
(2)焊补循环风机叶片,并调整好它的动平衡,保证平稳的排风量,同时也减少风机的振动,降低循环风机的电流。
(3)根据物料的易磨性来确定合理拉紧力参数,由原来的12~14]V[Pa改为9~12]VIPa。
将原来的石灰石、粉煤灰预配料改为石灰石、粉煤灰、粘土三组分预配料,因为有粘土的加入,增加了料层的稳定性,提高了磨机的稳定性。
(4)由于温度过高或过低、排风量的过大或过小、喷水量的多与少、研磨压力的升高或降低等都会引起磨机的振动,所以在操作中必需避免上述现象的发生,优化参数以确保磨机稳定运转。
2粗粉分离器叶片掉落2.1原因(1)磨机振动大且频繁。
MLS3626生料立磨调试过程中出现的问题及处理.

MLS3626生料立磨调试过程中出现的问题及处理我公司5000t/d熟料生产线的生料制备主要由两台MLS3626立磨来完成的。
该磨机从2009年3月初调试以来出现了较多问题,直到7月底才正常运行。
这期间因生料紧张一直制约窑的喂料量,因而延长了整条生产线的调试期。
本文就该磨机出现的有关问题及处理方法作一介绍,以供同行参考。
1、出现的问题及处理1.1磨机频繁跳俘磨机启动过程中或者启动完成几分钟后或者运行不超过l h就频繁出现跳停(最多ld开停了47次),成为调试期间最严重的问题,并严重威胁设备的安全。
中控显示故障的原因大多是振动大引起的。
该立磨对料层、压差等参数的稳定性及磨辊张紧压力合理性非常敏感。
正常操作台时在200t/h时料层一般控制在80-120mm左右,压差大于7 000 kPa,磨辊张紧压力在10~13 MPa 之间。
上述参数随着喂料量的变化应适当调整,但调试初期操作及现场人员缺乏一定的经验,无法稳定和合理调整参数。
分析认为,这是磨机频繁跳停的主要原因。
为控制和避免磨机频繁跳停的出现,我们首先邀请了兄弟单位的专业人员对操作及现场人员进行培训,以减少他们的心理压力并提高他们的操作技能;其次是测定喂料量与料层、张紧压力的对应关系,逐渐摸索一定的规律并采取相应的技术措施;第三,在稳定料层方面我们采取的主要措施是只要磨内不形成料饼,就适当增大磨内喷水量,同时降低石灰石等原料的粒度;第四,在工艺操作上控制磨内通风压差不宜过小,否则悬浮的物料容易塌落造成料层突然变化,引起振动过大而跳车;第五,在调试初期喂料量小的情况下,磨辊张紧压力不宜过高控制,只要略高于低限就可;第六,遇到磨机频繁跳停时,绝对不可随意增大跳车保护的定值或拆除磨机相关的保护,否则很可能会引发磨辊脱落及减速机损坏等恶性事故。
1.2立磨水平晃动大磨机在运行中整体(包括外壳体)水平晃动明显,曾一度造成砼框架的摆动及磨机系统几处膨胀节的断裂。
立磨在生产中出现的几个问题和解决办法
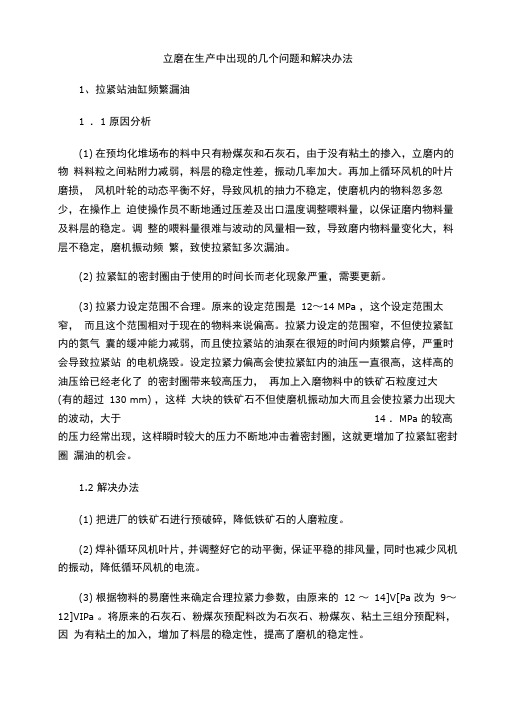
立磨在生产中出现的几个问题和解决办法1、拉紧站油缸频繁漏油1.1 原因分析(1)在预均化堆场布的料中只有粉煤灰和石灰石,由于没有粘土的掺入,立磨内的物料料粒之间粘附力减弱,料层的稳定性差,振动几率加大。
再加上循环风机的叶片磨损,风机叶轮的动态平衡不好,导致风机的抽力不稳定,使磨机内的物料忽多忽少,在操作上迫使操作员不断地通过压差及出口温度调整喂料量,以保证磨内物料量及料层的稳定。
调整的喂料量很难与波动的风量相一致,导致磨内物料量变化大,料层不稳定,磨机振动频繁,致使拉紧缸多次漏油。
(2)拉紧缸的密封圈由于使用的时间长而老化现象严重,需要更新。
(3)拉紧力设定范围不合理。
原来的设定范围是12~14 MPa ,这个设定范围太窄,而且这个范围相对于现在的物料来说偏高。
拉紧力设定的范围窄,不但使拉紧缸内的氮气囊的缓冲能力减弱,而且使拉紧站的油泵在很短的时间内频繁启停,严重时会导致拉紧站的电机烧毁。
设定拉紧力偏高会使拉紧缸内的油压一直很高,这样高的油压给已经老化了的密封圈带来较高压力,再加上入磨物料中的铁矿石粒度过大(有的超过130 mm) ,这样大块的铁矿石不但使磨机振动加大而且会使拉紧力出现大的波动,大于14 .MPa 的较高的压力经常出现,这样瞬时较大的压力不断地冲击着密封圈,这就更增加了拉紧缸密封圈漏油的机会。
1.2 解决办法(1)把进厂的铁矿石进行预破碎,降低铁矿石的人磨粒度。
(2)焊补循环风机叶片,并调整好它的动平衡,保证平稳的排风量,同时也减少风机的振动,降低循环风机的电流。
(3)根据物料的易磨性来确定合理拉紧力参数,由原来的12 ~14]V[Pa 改为9~12]VIPa 。
将原来的石灰石、粉煤灰预配料改为石灰石、粉煤灰、粘土三组分预配料,因为有粘土的加入,增加了料层的稳定性,提高了磨机的稳定性。
(4)由于温度过高或过低、排风量的过大或过小、喷水量的多与少、研磨压力的升高或降低等都会引起磨机的振动,所以在操作中必需避免上述现象的发生,优化参数以确保磨机稳定运转。
立磨液压系统常见故障和处理

立磨液压系统常见故障和处理立磨液压系统运行过程中会出现各种故障,如磨辊升不起来或无法加载加压,也可能出现储气罐氮气囊破裂损坏、液压系统振动不稳定等问题。
本文分享立磨液压系统9种故障现象及对应解决办法。
1.蓄能器储气罐氮气囊破损,出现“砰砰”声音,管道产生冲击振动。
用专用压力表检测诊断储气罐氮气囊压力是否降低或严重为零,如果是压力降低或为零,说明氮气囊出现渗漏损坏。
主要原因:氮气囊质量不好、储气罐进出口阀损坏、液压油内杂质导致氮气囊破损压力波动产生振动冲击和“砰砰”噪音。
解决办法:更换专业厂家制作的质量优良的氮气囊或更换损坏的储气罐进出口阀并改进菌型阀结构提高阀杆强度、清理液压管道杂质并采用过滤精度不大于5μm的滤油机过滤,添加液压油达到NAS7级。
2.液压管路法兰漏油。
主要原因:密封件老化损坏或安装不正压出毛边或两法兰不平及法兰错位螺栓松动、管道有应力法兰不同心导致法兰漏油。
解决办法:定期(12个月检查一次)更换老化密封件;安装密封件时要摆正、完全放入沟槽内,防止挤压受力损坏密封件而失效;调整管道两片法兰同心并平行,均匀紧固连接螺栓并固定管道牢靠防止摆动漏油。
3.油泵和过滤器工作正常情况下,磨辊升辊正常,降辊时磨辊不降或出现升降辊都不动故障。
主要原因:液压油没有进入油缸有杆腔,导致无法加压,不能降磨辊。
升降辊都不动主要原因是液压油没有进入油缸无杆腔和有杆腔,导致无法加载,不能升降辊。
解决办法:经分析检查三位四通电磁阀因磨损或油脏卡住,阀芯只能一侧工作,另一侧不能工作,或者两侧都不能正常换向工作。
磨损的三位四通电磁阀更换新件;油脏导致卡住,拆卸、清洗三位四通电磁阀,并过滤液压油,油缸正常工作,升降磨辊都正常。
4.四个磨辊中有两个可以升辊到限定位置,另外两个磨辊升辊速度较缓慢,在设定时间内(120s)不能升辊到位。
主要原因:根据已经有两个磨辊可以升起来状态,诊断液压系统没有问题,检查没有其他机械问题。
立磨机常见故障与解决方法

立磨机常见故障与解决方法立磨机在使用过程中所出现的故障,可按如下进行处理故障一:不出粉或出粉少产量低产生原因:(1)锁粉器未调整好,密封不严,造成粉倒吸。
(2)铲刀磨损大物料铲不起。
排除方法;(1)检查和调整好锁粉器密封,发现漏气处应堵住。
(2)更换铲刀故障二:成品粉子过粗或过细。
产生原因:(1)分析机叶片磨损严重,不起分级作用。
(2)风机风量不适当。
排除方法:(1)更换叶片并适当关小风机进风量能解决过粗。
(2)过细应该提高进口风量。
故障三:主机电流上升,机温上升,风机电流下降。
产生原因:(1)给料过量,风道被粉料堵塞,管道排气不循环,气流发热使之主机电流,机温升高,风机电流下降。
排除方法:(1)减少进料量,清除风道积粉。
(2)开大余风管闸门,进机物料温度控制在6%以下。
故障四:主机噪音大并有较大振动。
产生原因:料硬冲击大,或无料层。
(2)磨辊磨环失圆变形严重。
排除方法:(1)减少进料粒度。
(2)更换磨辊磨环。
故障五:风机振动产生原因;(1)风叶上积粉或磨损不平衡。
(2)地脚螺栓松动。
排除方法:(1)清除叶片积粉或更换叶片。
(2)拧紧地脚螺栓故障六:分析机油箱发热。
产生原因;(1)机油粘度太油厚,螺纹泵油打不上去使上部轴承缺油。
排除方法:(1)检查机油的牌号和粘度是否与要求相符。
(2)检查分析机运转方向故障七:磨辊装置进粉轴承易损坏。
产生原因:(1)断油或密封圈损坏。
(2)长期缺乏维修和清洗。
排除方法:(1)按规定时间及时加油。
(2)定期清洗,更换油封。
一般来说,立磨机粉机配件的工作环境可以说是灰尘比较严重的,所以说机器在长期的使用过程中都会被灰尘累积的无法正常的运行,这就要求人们在一定的时间内要对机器经常地清洗。
立磨机粉机的除尘设备是利用旋转气流所产生的离心力将尘粒从合尘气流中分离出来的除尘装置。
它具有结构简单,体积较小,不需特殊的附属设备,造价较低.阻力中等,器内无运动部件,操作维修方便等优点。
水泥原料立磨设备问题分析及解决方案

水泥原料立磨设备问题分析及解决方案磨机轰鸣,粉尘弥漫,在这片工业的乐章中,水泥原料立磨设备扮演着至关重要的角色。
然而,岁月的痕迹和技术的局限,让这些问题逐渐浮现,成了我们不得不面对的难题。
今天,就让我们深入分析这些问题,并提出针对性的解决方案。
一、问题分析1.设备磨损严重立磨设备在长期运行过程中,物料与磨盘、磨辊的摩擦,使得设备磨损严重。
尤其是磨盘和磨辊,磨损速度较快,影响了设备的稳定性和生产效率。
2.粉尘污染问题水泥原料立磨设备在运行过程中,物料破碎产生的粉尘,容易造成环境污染。
这不仅影响了员工的健康,也对周边环境造成了影响。
3.设备故障率高由于磨损、污染等因素,立磨设备的故障率较高,影响了生产的连续性和稳定性。
4.能耗问题立磨设备在运行过程中,能耗较高,尤其是磨盘和磨辊的驱动系统,能耗占比较大。
这不仅增加了生产成本,也对环境保护不利。
二、解决方案1.优化设备设计针对设备磨损严重的问题,我们可以从设备设计入手,采用耐磨材料,提高磨盘和磨辊的耐磨性能。
同时,优化磨盘和磨辊的结构,减少磨损。
2.改进生产工艺为了解决粉尘污染问题,我们可以改进生产工艺,采用封闭式生产,减少物料破碎过程中产生的粉尘。
同时,加强通风和除尘设备的使用,降低粉尘浓度。
哎哟,这个解决方案听起来不错。
不过,设备故障率高的问题怎么解决呢?3.强化设备维护针对设备故障率高的问题,我们需要加强设备的日常维护和保养。
定期检查设备,发现磨损严重的部件及时更换,避免因磨损导致的故障。
同时,提高员工的操作技能,减少误操作。
4.降低能耗(1)优化设备驱动系统,提高电机效率。
(2)采用变频调速技术,实现电机转速的精确控制。
(3)加强设备散热,降低设备运行温度,减少能耗。
5.创新技术应用当然,我们还可以探索新的技术应用,如:(1)采用先进的磨盘和磨辊材料,提高耐磨性能。
(2)引入智能控制系统,实现设备的自动优化运行。
(3)开展设备故障预测研究,提前发现并解决潜在问题。
原料立磨操作及异常情况处理

原料立磨操作及异常情况处理一、原料立磨安全操作注意事项:1、严禁磨机断料运行;2、磨内通风前,密封风机必须开启;3、烘磨或冷磨时升降温要平缓;4、长时间停磨后,烘磨时间要相对延长,开始喂料量和研磨压力也要相对低一些;5、严禁磨盘上无料或料太少时向磨内喷水;6、注意观察废料仓料量,磨机运行后,最好将仓内物料放空。
7、要防止石灰石仓料位出现“HH”报警造成紧急停车或满仓;8、防止系统出现正压,特别是利用热风炉开磨时;9、切勿原料磨主电机与其他主机设备同步启动;10、启动EP风机、循环风机前,一定要确认风机挡板关闭;11、窑尾电收尘尘必须由现场荷电,紧急情况时中控可以停止荷电;12、注意观察入库斗提电流变化;13、加减风、料要平缓;14、页岩、铁质原料断料或进错料时,一定要及时通知质控处协调处理。
15、增湿塔物料含水分大时,一定要外排。
并安排人员检查增湿塔喷水雾化情况。
二、原料立磨运行中常常会出现以下异常情况,作为操作员要冷静及时正确处理好,争取把损失减小到最小。
1、页岩仓、铁粉仓堵料或断料页岩、铁粉断料后,立即通知现场人员处理。
如10min内仍不能处理好,则停止喂料,磨辊顶起,必要时停磨处理;2、磨主电机跳停迅速打开旁路挡板,适当打开618风机挡板,降低循环风机入口挡板,保证磨入口微负压状态,检查跳停原因,通知相关人员处理。
3、618风机跳停全开旁路挡板,618风机挡板,查找原因,通知相关专业人员处理。
4、回转阀跳停回转阀跳停后,磨机喂料组联锁跳停,磨辊顶起,三通阀自动打到吐渣仓侧,中控要迅速打开旁路挡板,适当打开618风机挡板,降低循环风机入口挡板,调节热风挡板、循环风挡板,冷风挡板来控制磨出口温度,并通知现场处理。
5、电收尘下拉链机或输送电收尘物料分格轮跳停中控减料运行,立即通知现场检查处理,10min后不能处理好,则停止原料磨喂料组,将三通阀打至废料仓侧,打开旁路挡板、冷风挡板、减小热风挡板,控制磨出口温度。
立磨故障分析以及处理

电磁阀故障
联系相关人员及时处理
4.磨内吐渣量偏多
序号
原因
处理方法
1
喂料量过多
设定合适的喂料量
2
系统通风不足
加强系统通风
3
研磨压力过低
重新设定
4
入磨物料易磨性差且粒度大
根据物料特性调整喂料量
5
选粉机转速过高
调整转速
6
喷口环磨损大
更换
7
挡料环偏低
重新调整
8
衬板,辊皮磨损严重
更换或调整
5.磨主电机跳停
序号
故障分析
处理方法
1
振动高高报
检查测振元件,失灵需重新校正,检查液压站有无压力太高和不平衡,调整好压力,检查磨内是否有大块铁件及硬物,加强物料除铁工作,风料要平稳,设定合适的研磨压力,根据细度要求调整好选粉机转速,根据主电机电流,料层高度及时调整
2
密封风机跳停或压力低低报
通知现场检查密封风机及管道,并清洗过滤网
8
废料仓放料不稳
调整喂料
9
喂料量过大,过小或不均
调整喂料量
10
系统用风量过大或过小
调整相应挡板
11
研磨压力过高或过低
重新设定研磨压力
12
选粉机转速过高
根据细度要求调节
13
出磨温度波动大
稳定出磨温度
2.磨机差压急剧上升
序号
故障分析
处理方法
1
喷口环堵塞
停机处理
2
磨本体漏风大
加强密封
3
喂料量过大
重新调整
4
联系电气检查绕组及检查稀油站运行情况
9
研磨压力高高报或低低报
立磨常见问题及处理.

立磨常见问题及处理立磨操作相对来说工艺原理简单些,但恰恰是目前水泥厂有效运转率提不高的一个系统。
如何稳定料层。
料层厚,物料有效粉磨稍有下降,成品率下降,主电机电流大,差压升高。
料层薄,振动大,吐渣大。
不同磨机料层控制厚度不同,料层厚度一般是0.02D ±20mm但在其控制范围内上述现象是一致的。
稳定料层是操作立磨的关键。
料层通过压力增减或喂料量增减来控制,喷水量一般是在料层稳不住时作为手段。
如何稳定差压和主电机电流。
差压是反映磨内气流阻力大小的参数,在正常工况下其变化,可从磨盘物料的增多和气流中粉尘浓度增加两个方向上去理解。
是喂料与成品动态平衡的反映。
一般地在主电机电流平衡、料层平稳、振动平衡时,差值高说明磨机能力发挥出来了。
压差在上升时,同时伴随主电机电流上升、选粉机电流上升。
一般地通过喂料量来适应差压值,动工作压力影响料层、动风在正常负荷时空间不大,会引起磨内风速变化、选粉转速与细度有影响。
工作压力高,磨机电流高。
料层厚,磨电流高。
但料层过薄时,磨主电机电流波动大,瞬间易过流。
磨机的振动磨机振动是立磨存在的一个现象,振动过大会造成磨盘和磨辊衬板及附属设备的损坏。
引起因素较多,如入磨物料粒度不均匀、磨辊和磨盘衬板磨损严重、风量及风温的波动、研磨压力过高或过低、磨内异物、料层过厚或过薄、蓄能器压力不当、刮料板磨损导致的刮料腔积料多引起的风量分布不均、喂料量波动大等。
常见问题立磨入料溜子堵料。
入磨三道锁风阀或回转阀跳停。
磨机差压降低,选粉机电流降低,相应地出磨风温升高,磨机振动持续在较高的水平上波动。
这种振动不同于磨内异物引起的突发性振动,即瞬间出现很高的峰值,是较正常值高1-2mm/s的振幅上持续振动。
堵的部位不同,如回转下料器卡料、其上方或下方出磨溜子堵料。
主电机电流异常升高30%,如果料层厚度正常,则预示刮料腔内有积料可能。
差压升高,入口负压值降低,磨机振动持续在较高水平如何控制细度。
立磨系统及常见故障

原料立磨系统及常见故障第一部分:关于立磨一.立磨的工作原理:经过搭配的物料从进料口送到磨盘上,磨盘在主电机的驱动下转动,由于离心力的作用,物料被分散在磨盘的四周,在磨辊的重力和施加研磨力的作用下,磨辊对物料的剪切力,转化为物料挤压而粉磨,一部分大颗粒掉入喷嘴环,经刮板刮出磨腔,磨辊同时在物料的摩擦力下产生自转;来自窑尾或热风炉的高温废气,经喷嘴环入磨,产生涡流风,对物料进行预热烘干,被粉磨的物料在排风机的抽力下,悬浮起符合某一细度要求的物料进入选粉机;一部分颗粒由于与导向叶片碰撞,物料与物料的碰撞及离心力作用,经重锤阀重新入磨粉磨,合格的物料经旋风筒收集入均化库。
二.立磨在生产中比管磨具有的优越性:1.台时产量高,电耗,能耗低2.工艺操作简单,预热,粉磨,提升于一体,流程短,占地小3.自保性强,配有减速机稀油站,液压站,磨辊润滑,喷水装置等辅助设施。
4.物料研磨在可变压力下5.动静态选粉调节产品质量,具有更高的研磨效率6.维修量小,磨损件小,便于维护保养三.操作指导思想1.磨操作主要是风、料、功三者平衡,发挥立磨最佳工艺参数。
a、风:来自窑尾(热风炉)废气,起预热,烘干,提升功能;依赖磨尾排风机所产生通风量与喂料量是否匹配。
b、料:配料一般使用石灰石、页岩(粘土)、铁粉三者按一定比例入磨。
主要考虑入磨物料的粒度,颗粒易磨性,水分。
c、功:研磨压力来自辊自重,对物料进行剪切力,物料与物料挤压所粉磨,研磨压力大小应该与喂料量相匹配。
2.内循环:指物料在磨盘上粉磨后,经过选粉机收集后,不合格产品重新入磨,调整好选粉机导向叶片及转子转速,使合格物料能够及时出磨,节约磨机有效空间,避免过粉磨现象,提高粉磨效率。
3.外循环:指物料被甩出磨盘,从喷嘴环掉入到刮板腔内的物料,即吐渣料。
外循环大小影响磨喂料,一般控制在设计能力10%以内。
4窑磨配风:磨机热源主要来自窑尾的高温废气,磨机开停对窑系统影响很大(特别是停时,负压难控制,波动大),开停机时,动风幅度要缓和有序(主要是618风机挡板)。
立磨常见故障及处理方法

故障及其处理:1.磨机振停原因处理方法喂料量过大减小喂料量风量不足加大拉风拉紧装置,拉紧力过高或过低控制拉紧力出磨温度骤然变化检查喂料与检查入磨温度分离器转速过高或过低调整转速入磨粒度过大清除大粒度物料磨内有异物清除异物料层波动过大控制喂料量入磨物料太细加大喂料量、磨内喷水料层过厚或过薄控制喂料量三个拉紧杆预充氮压力过高或过不平衡调整预充氮压力测振元件失灵更换测振元件2.生料跑粗原因处理方法喂料量过大或过小控制喂料量入磨粒度大控制喂料量研磨能力低调整研磨压力分离器转速低调大转速分流风量过大减小拉风入磨物料易磨性不好控制喂料量3.磨内压差过高原因处理方法喂料量过大控制喂料量拉紧力低调整研磨压力分离器转速高调小转速磨出口温度高加大磨内喷水、调大冷风门系统排风不畅停机处理磨内喷水装置失灵停机检修4.循环风机电流波动大原因处理方法碳刷打火停机处理风机挡板失灵停机处理磨内物料波动过大控制喂料量风机叶片变形停机更换风机轴承有故障停机处理外电网波动总降调整5.磨主电机电流波动过大原因处理方法碳刷打火停机处理喂料量变化大控制喂料量三个拉紧杆不平衡调整拉紧力磨内料层波动过大控制喂料量入磨物料粒度变化大控制喂料量分离器转速波动过大调整转速磨内有异物停机清除磨机振幅过高控制喂料量电机轴承有故障停机处理系统温度骤然变化检查喂料量与入磨风温外电网波动总降调整6.立磨排渣过多原因处理方法喂养料量过大控制喂料量入磨物料粒度大控制喂料量风量不足加大拉风拉紧力过低加大研磨压力磨系统漏料严重停机处理喷口环风量过低加大拉风磨内料层过厚控制喂料量物料易磨性不好控制喂料量挡料环过低控制喂料量7.立磨主电机跳停原因处理方法喂料系统停车检修除铁器金属探测仪停检修回转锁风阀停检修循环风机停检修生料输送机组停检修减速机高压泵的供油压力0.5bar调整供油压力减速机润滑油压力0.5bar调整油压力减速机油温大于65度检查油质与冷却水磨辊轴承密封风机停检修密封风机减速机油箱温度75度检查油质与冷却水磨辊轴承密封风压4000Pa检查密封风管分离器油泵及其减速机润滑泵停检修减速机高低压泵停检修磨机振动值过高控制喂料量8.出磨温度过高:调整方法采取磨内喷水增加喂料量打开冷风阀门降低入磨风温9.料层过厚调整方法减少喂料量增加张紧力增加系统排风降低磨机温度10.料层过薄调整方法增加喂料量采取磨内或磨外喷水降低拉紧力11.入磨物料粒度小调整方法采取磨内或磨外喷水加大喂料量适当减少排风量降低拉紧力启磨前磨内用大块铺料12.减速机油温高原因处理方法处理方法冷却水流量不够加大冷却水冷却水压力低调整冷却水压水冷却器堵塞清理冷却水阀门未开打开油过滤器堵塞,油循环不畅清理13.拉紧装置压力下降原因处理方法油路导管泄漏更换油路导管安全溢流阀失灵更换拉紧油站油泵故障检修14.密封空气压力下降原因处理方法密封风机故障检修密封空气管路泄漏更换导管15.成品太细原因处理方法转子转速太高降低转速风流量太低增加风流量。
立式磨常见故障的排除

一、TRM25辊磨常见故障的排除表
故障
原因分析
预防及排除方法
1.主减速机轴承温度超限。
油管长、弯头多、阻力大、压力分油器供油不足。
将油管由φ13mm改为φ16mm铜管,减少弯头。
2.磨辊液压系统漏油。
油管接头为螺纹联接,螺纹加工精度低造成漏油。
将油管螺纹联接改为法兰联接。
3.吐渣(生产中吐渣)。
2、输油量不足;
3、泵内铜套、齿轮等元件损坏或精度差;
4、压力板磨损大。
及时检修或更换零件,严重时换齿轮泵。
4.控制阀故障。
1、阀的调节弹簧永久变形、扭曲或损坏;
2、阀座磨损,密封不良;
3、阀芯拉毛、变形,移动不灵活、卡死、阻尼小孔堵塞;
4、阀芯与阀孔配合间隙大;
5、高低压油互通;
6、阀开口小,流速大,产生空穴现象。
5.振动。
1、入磨气体温度高,入磨物料过干;
2、磨辊压力不合适;
3、进磨物料粒度过大;
4、进磨物料量不均匀,粘土断料;
5、磨盘料层薄;
6、进出磨机压着增大。
1、控制入磨气体温度在110—125℃;
2、降低磨辊压力,适当降低产量;
3、杜绝大块料进磨。石灰石<25mm,粘土<50mm;
4、保证连续均衡喂料、无卡料、断料;
3、定期更换新油、及时清洗过滤器。
10.系统振动产生噪音油液变质。
油液中侵入空气。
1、更换不良密封件;
2、检查管接头及液压元件连接处,并及时紧固松动螺栓。
5、正确使用磨盘喷水,保持料层厚50—65mm;
6、调整磨内物料循环,减小磨内阻力控制压差值在7.0—7.6kPa。
二、ATOX立磨常见故障的排除表
立磨常见故障及方案

立磨常见故障及处理一.磨机振动的原因及处理:1.测振元件失灵:磨辊刚降下便出现振动,操作各程序和个参数都正常,而且现场并没有感觉到振动,后经检查发现测振仪松动,重新拧紧,开磨正常。
测振仪松动是常事,这时中控操作画面各参数均无异常,现场无振感。
预防发生此事要求平时巡检多注意,并保持清洁。
2.辊皮松动和衬板松动中控振动偏大,现场发现磨内出现有规律的振动和沉闷的声音,紧急停磨,入磨检查各夹板螺栓均无明显松动,磨内有无异物,一切正常,进磨才发现一辊皮松动。
辊皮松动是振动很有规律,因磨辊直径比磨盘直径小,所以表现出磨盘转动不到一周,振动便出现一次,再加上现场声音辨认,便可判断某一辊出现辊皮松动。
衬板松动,一般表现出振动连续不断,现场感觉到磨盘每转动一周便出现三次振动。
当发现辊皮和衬板有松动时,必须立即停磨,进磨详细检查,并要专业人员指导处理,否则当其脱落时,必将造成严重事故。
囊的预加压力不平衡,或过高或过低3.液压站N2囊不平衡时,则各拉杆的缓冲力不同,使磨机产生振动。
过高、过低则缓冲板能力减弱,也易使磨机振当N2囊的预加载压力要严格按设定值给定,并定时给其检查,防止其漏油、漏气,压力不正常。
动偏大,所以每个N24.喂料量过大、过小或不稳磨机喂料多,造成磨内物料过多,磨机工况发生恶变,很容易瞬间振动跳停。
因废料仓不能使用,开磨时吐渣直接入磨,降磨辊后振动偏大,同时表现料层厚度大,入口正压,这是因为开磨时吐渣多,加上皮带秤喂料,入磨喂料变多而造成。
这时应大量减少皮带秤喂料,等吐渣正常后,再加至正常。
喂料量过小,则磨内物料太少,料层薄。
磨盘与磨辊之间物料缓冲能力不足,易产生振动。
立磨试生产时,因机械需要要求按70%喂料,则喂料偏小,这是试生产中立磨振动大的原因之一。
所以可通过喂入大颗粒物料来保证磨机平稳运行。
不平稳物料使磨内工况大乱,易振动,要实现立磨操作的平稳,其重要因素之一是使物料平均平稳喂入。
5、系统风量不足或不稳当窑减产至200t/h时,磨机一启动便产生大量吐渣,两分钟不到便振动跳停,以为热风口积料多,但清理干净后,磨机仍启动不起来。
立磨运行过程中常见问题及其处理

立磨与球磨机相比,具有很多重要的突出优势,如粉磨效率高、工艺流程简单、占地面积小、同时集烘干、粉磨、选粉为一体等优点被越来越广泛地应用于新型干法水泥生产线,是大型新型干法水泥生产线较为理想、有效的粉磨设备,据统计在已建和新建的新型干法生产线中,原煤和生料粉磨采用立磨的约占90%以上。
如何进行精细化管理、优化工艺参数、稳定运行、提高产量、降低能耗、提高运转率、不断提高经济效益是立磨维护和管理的中心问题。
甘肃永登祁连山水泥有限公司生料制备系统采用丹麦史密斯(FLS)公司提供的ATOX37.5型立磨。
该磨自投产运行以来,实际运转情况并不理想,但在使用过程中我们不断地探索和改进,不断优化操作方案和实施精细化管理,解决了自投入运行以来出现的各类问题,使系统运行日趋完善和稳定,运转率高达90%以上。
现从设备方面和操作方面进行介绍。
1.1设备方面1.1中心支架偏差的调整磨辊位置调整的目的是为了使磨辊和中心支架组合中心位于磨盘中心。
由于长期的磨损和振动,导致各个连接部位间隙变大,扭力杆缓冲垫老化和硬化而失去缓冲作用,受冲击厚度变薄(原来每块厚125mm,现在只有120mm),使磨辊的活动量变大,磨辊位置中心产生偏移(如果支架中心偏移较大,可以从磨辊空气密封的间隙看出来,两侧空气密封间隙会不一样大);同时由于振动和磨损使扭力杆和拉伸杆位置发生偏移,不仅使扭力杆失去保护作用,而且会对拉伸杆形成扭弯的作用,对拉伸杆产生扭矩,这是造成拉伸杆及螺栓频繁断裂的原因。
检查磨辊位置时,必须把磨辊放在磨盘上,并且不施加任何研磨压力,减速机润滑站处于正常的工作状态,通过人工转动减速机和电机之间的连轴器来转动磨盘。
通过人力转动磨盘一周后,测量磨辊衬板端部卡块到磨盘挡料圈边缘的距离,差值在±5mm以内,可以认为磨辊的位置正确,否则需要进行调整,直到调整到位置正确为止。
调整实例:第一次测量的数据见表1依据三角函数推导出计算公式,算出调整量;Δa=0Δb=-(2Yc-Yb-Ya)/1.732=-(2×114-121-90.6)/1.732=-9.4Δc=+(2Yb-Yc-Ya)/1.732=+(2×121-114-90.6)/1.732=21Ya:1#磨辊辊衬板端部卡快与挡料圈之间的平均值Yb:2#磨辊辊衬板端部卡快与挡料圈之间的平均值Yc:3#磨辊辊衬板端部卡快与挡料圈之间的平均值Δa:1#磨辊的缓冲块支座加垫片的厚度Δb:2#磨辊的缓冲块支座加垫片的厚度Δc:3#磨辊的缓冲块支座加垫片的厚度理论上在任何两个磨辊的缓冲块支座加钢板,都可以调整磨辊的位置,上面的计算是1#辊不动,2#辊减9.4mm,3#辊加21mm;在实际操作中,1#辊不动,2#辊减10mm,3#辊加20mm。
立磨系统常见故障及处理

等油温上升,必要时采用外部设备强制加热
检查设定并根据实际情况进行调整 检查更换 检查如有问题及时更换
根据结果更换冷却水阀
检查冷却水系统 堵塞严重更换,酸洗处理 根据加热器控制温度判断是否加热器故障或 控制系统故障,根据结果及时处理 供油泵开停时间1/2 检查如有问题更换 清洗严重更换 更换 取油样并且分析过滤器滤芯和油样中的金属 颗粒或生料含量,如果含有1%的金属颗粒, 说明轴承有问题。 更换 如果三个辊回油温度均升高,则表示磨机工 况发生变化,出入口温度及密封空气入口温 回油温度只有一个辊升高,可能是辊轴承有 问题 检查更换
清扫管道积灰调整挡板使进气量相等
加油 重新排放系统残余空气,在更换了油品出始 启动时必须让油沉淀一段时间,使得油中的 气泡升到油位表面或让混合在油中的空气分 处理密封 更换油品 重新校准联轴器安装精度 重新调整压力安全阀,一般出厂已经调整好 纠正旋转方向 纠正调整 给泵启动注油 检查冷却水系统,同事检查过滤器是否堵塞 堵塞严重更换 根据加热器控制温度判断是否加热器故障或 控制系统故障,根据结果及时处理 根据液压缸上下缸体温差可以判断,对故障 液压缸视情况更换密封 检查电磁阀和其他阀体,进行更换 重新调整压力设定,随着磨耗增加,研磨压 力会出现较大波动,根据实际情况调整 及时调整PLC控制压力设定值,避免泵的频 繁启动 逐一检查每一个氮气囊压力,不足需要补 充,泄露需要更换
3 4
油箱温度过低
温度控制开关设定值不正确 温度控制开关故障
5
循环油泵故障
6
冷却水阀控制温度值设定不合理或温度测量 元件故障
7
冷却水中断或不足
8
油箱温度过高
油冷器堵塞
9
油箱加热器长时间加热不停机
ATOX立磨故障判断原因与处理

1)磨机振动过大(1)喂料不均匀,当入磨的混合料多为粉料时,磨内的负荷率大,导致磨盘上料层薄,甚至磨盘与磨辊直接接触,造成振磨;当入磨的混合料多为块料物料时,造成磨辊的压差不稳定,产生振磨。
解决的方法是稳定入磨物料的粒度,适当调整喂料速度或降低粉磨压力,在保证需要物料细度的前提下,适当降低选粉机转速。
(2)金属件进入磨机,检查金属探测器,磁铁分离器工作是否正常。
(3)窑废气风机损坏引起振动或入磨的窑尾废气压力高,不稳且含尘浓度大使磨内温度过高从而加大了磨内负荷,此时应加大循环风门的开度,增大入磨的循环风门,提高了磨机的入口负压,使磨机运转平衡。
2)磨机生产能力过低可能的原因为:(1)喂料速率低;(2)粉磨压力低;(3)产品细度太细;(4)系统风量低。
解决的方法为增加喂料速率或增加粉磨压力,降低选粉机转速,加大系统排风量。
反之磨机的生产能力过高时,解决的方法相反。
3)喂料不足当发现喂料仓储料不足时应停机,此时如果继续往外输料有空磨的危险,应向供料装置和磨机喂料,否则会使料床变薄,发生隆隆响声,致使减速机损坏。
4)磨机压差太大此时应立即减少供料,观察压差指示装置。
检查其可能的原因:(1)由于仪表指示传送失误,若磨系统主要运行参数值在正常范围内,通知仪表工去处理,磨不停。
(2)由于喂料装置调速控制失灵导致入磨喂料量过大,若磨机电流有上涨趋势,手动操作相应减少喂料量,并加大磨内总抽风量,磨电流过大时,可迅速大幅度降低分离器转速,尽量避免磨过载跳停,造成再次开磨困难。
(3)磨盘部的喷口环阻塞;若采取措施加大磨内通风,减产量无效果时,入磨负压为正压,且磨机仍振动大,应立即停磨,清堵。
(4)风量过低或不稳定,调整加大磨内抽风量或相应减少喂料量,并叫现场检查系统有无漏风源。
系统风量急剧变化,可能由风管内或预热器旋风筒积灰塌料所致加大磨系统抽风量,开大入磨冷风。
(5)选粉机调整的细度过细。
分离器整定值过高,降低分离器转速。
- 1、下载文档前请自行甄别文档内容的完整性,平台不提供额外的编辑、内容补充、找答案等附加服务。
- 2、"仅部分预览"的文档,不可在线预览部分如存在完整性等问题,可反馈申请退款(可完整预览的文档不适用该条件!)。
- 3、如文档侵犯您的权益,请联系客服反馈,我们会尽快为您处理(人工客服工作时间:9:00-18:30)。
立磨常见问题及处理立磨操作相对来说工艺原理简单些,但恰恰是目前水泥厂有效运转率提不高的一个系统。
如何稳定料层。
料层厚,物料有效粉磨稍有下降,成品率下降,主电机电流大,差压升高。
料层薄,振动大,吐渣大。
不同磨机料层控制厚度不同,料层厚度一般是0.02D ±20mm但在其控制范围内上述现象是一致的。
稳定料层是操作立磨的关键。
料层通过压力增减或喂料量增减来控制,喷水量一般是在料层稳不住时作为手段。
如何稳定差压和主电机电流。
差压是反映磨内气流阻力大小的参数,在正常工况下其变化,可从磨盘物料的增多和气流中粉尘浓度增加两个方向上去理解。
是喂料与成品动态平衡的反映。
一般地在主电机电流平衡、料层平稳、振动平衡时,差值高说明磨机能力发挥出来了。
压差在上升时,同时伴随主电机电流上升、选粉机电流上升。
一般地通过喂料量来适应差压值,动工作压力影响料层、动风在正常负荷时空间不大,会引起磨内风速变化、选粉转速与细度有影响。
工作压力高,磨机电流高。
料层厚,磨电流高。
但料层过薄时,磨主电机电流波动大,瞬间易过流。
磨机的振动磨机振动是立磨存在的一个现象,振动过大会造成磨盘和磨辊衬板及附属设备的损坏。
引起因素较多,如入磨物料粒度不均匀、磨辊和磨盘衬板磨损严重、风量及风温的波动、研磨压力过高或过低、磨内异物、料层过厚或过薄、蓄能器压力不当、刮料板磨损导致的刮料腔积料多引起的风量分布不均、喂料量波动大等。
常见问题立磨入料溜子堵料。
入磨三道锁风阀或回转阀跳停。
磨机差压降低,选粉机电流降低,相应地出磨风温升高,磨机振动持续在较高的水平上波动。
这种振动不同于磨内异物引起的突发性振动,即瞬间出现很高的峰值,是较正常值高1-2mm/s的振幅上持续振动。
堵的部位不同,如回转下料器卡料、其上方或下方出磨溜子堵料。
主电机电流异常升高30%,如果料层厚度正常,则预示刮料腔内有积料可能。
差压升高,入口负压值降低,磨机振动持续在较高水平如何控制细度。
在磨机满负荷、工况稳定、压差稳定时调整选粉机转速即可。
在磨机满负荷、工况稳定、压差相对偏低时,细度偏粗,增加选粉机转速;反之,压差相对偏高时,降低选粉机转速。
原料离析料中块料集中下料时,生料易偏粗,此时应增加选粉机转速,压差偏高控制;反之亦然。
如果工況发生变化,降低产量,压差偏低,增加粉机转速,细度反而偏粗时,说明磨内拉风过大。
在粉磨条件不变的情况下,产品细度主要取决于选粉机的转速,通过对喂料量和选粉机转速调整满足时,要及时调整磨内用风量。
循环提升机负荷增大。
在排除掉异物、设备本体及其出料口堵后,一般认为是吐渣量的增加。
不同类磨机吐渣循环量设计不同。
在料层稳不住时,先稳料层。
料层稳的情况下可提当提高压力,减少吐渣。
吐渣中粉尘量多时说明拉风偏少:如出磨风温过高导致实际通风量降低。
或者选粉转速过高(或其导向叶片角度偏小),或者喷环风速不够。
辊皮磨损的影响。
不同类磨机反映不一样。
一般是稍减产和减压力,加强拉风。
磨机振动变化不大。
特殊情况有料层稳不住,磨机工况恶化。
入磨粒度对立式磨系统的影响立式磨允许更大的入磨粒度,但由人磨的物料粒度太大带来的影响却与球磨机有较大的不同,一般情况下,球磨机的入磨粒度的变化只对磨机的产量和出磨细度带来影响。
入磨粒度大,球磨机的产量降低,产品细度增大,但对立磨来说,人磨粒度过大,不仅使得产品的质量下降,还更容易造成磨机的系统故障。
一些企业由于工艺条件或管理等方面的原因,未能将入磨物料粒度控制在要求范围。
特别是在过去使用球磨机粉磨系统的企业,对控制入磨物料粒度重要性认识不清,导致过大物料进入立式磨,产生了一系列的问题。
粉磨过程简析立式磨种类较多,其工作原理基本一致。
磨机的磨盘在主电机的带动下旋转,磨辊受到液压力的作用下,紧压在磨盘的料层上,由于摩擦力作用使磨辊绕心轴作自转运动。
物料在磨盘和磨辊之间受挤压和研磨的联合作用粉磨后,被磨盘的离心力抛自四周,烘干用的热风通过围绕磨盘的风嘴把物料带入上部的分级器进行分级,细粉带走,并通过收尘器将细粉收集下来,粗粉回磨再粉磨。
但是由于入磨的粒度太大,有的大块物料难以进入磨辊与磨盘之间,下面作一个简单的分析。
如图1所示:假设物料为一小圆球,在进入磨辊与磨盘之间时受到的力有:P1——磨辊作用于物料的力;P2——磨盘作用于物料的力;F1——磨辊与物料之间的摩擦力,F1=P1f;F2——磨盘与物料之间的摩擦力,F2=P2f;f——钢在物料上的摩擦系数,f≈0.24。
欲使物料顺利进入磨辊与磨盘之间必有:P2f+P1f1cosα≥P1sinα(1)同时还应有平衡方程:P1cosα+fP1sinα=P2(2)联之解此方程组得:tgα≤2f/(1一f2)令φ表示摩擦角,则f=tgφ由此可得tgα≤tg2φα≤2φ=2arctg0.24=27。
由于α的变化受辊子直径和人磨物料粒度影响,在辊子直径大小不变动的情况下,入磨粒度越大则α越大,当α超过2倍摩擦角时,物料便会被挤出,粉磨作业就难以进行,所以对物料的大小应有一个限制。
除此之外,磨辊与磨盘之间的间隙也对钳角有一定影响。
磨辊与磨盘之间的间隙越大,物料更容易被“咬”入,但间隙太大又将影响粉磨效率。
一般情况下,间隙h=KD。
K——系数,K=O.01~0.03;D——磨辊直径,m。
在这种情况下,立式磨常常取的最大人磨粒度为:d≤0.05D,这样完全可以保证α≤2φ中的条件,以保证立式磨工作更加有效可靠。
入磨粒度对立式磨系统的影响从上述分析中我们知道,立式磨的入料粒度取决于磨辊的大小。
在实际工作中,如果人磨物料的粒度d与磨辊的直径D的比值大于0.05,那么以下情况就很可能发生:(1)由于人磨物料太大,物料不能顺利被辊磨钳人,不能形成较好的研磨层。
这种情形就同行使的汽车的车轮压不住一个篮球,但能压住一个乒乓的情形一样。
例如,有的企业使用的ATOX32.5生料磨,磨盘直径3.25m,辊子直径1.95m,设计生产能力为160t/h,D/d≤0.05计算,入料粒度d≤97.5mm,实际要求为d=80mm,但该企业入磨粒度则远大于该控制范围,严重时一度达到200mm以上,不仅不能达到设计产量,还致使磨机不能正常工作。
当降低入磨物料粒度后,生产情况良好,台时产量稳定在170t /h以上。
(2)入磨物料太大,造成的另一后果是振动加大,致使磨辊、磨盘的衬板磨损严重,并造成不均匀沟槽、裂纹和断边现象。
由于一些较大的物料并非是图示那样的球体,这样钳角就会发生变化。
一些不规则的大块物料虽然能被磨辊钳入,但由于其粒度较大,会将磨辊稍微顶起,经压碎后,磨辊在液压系统的作用下,有一个回落,这种情形发生较多的情况下,磨辊的振动就非常明显。
众所周知,过度振动对于机械的系统来说,将大幅增大零件的动载荷,这冲击动载荷对于各种零部件都是十分有害的,致使磨辊、磨盘的衬板磨损加剧等不良工况频繁发生。
(3)入磨物料太大还会造成立磨刮料板松动、脱落。
磨盘甩出的细物料在风环处被气体吹起,不能吹起的大颗粒物料落进积料箱,由通过装在磨盘的刮料板刮出,由于入磨物料颗粒较大,不易被粉磨到理想的细度,落入积料箱的物料较多。
因此带负荷启动时刮板阻力大,使得固定刮板的螺丝松动,严重时,刮板脱落,产生填料现象,使得立磨主机负荷加大而跳机。
(4)在正常的情况下,液压系统的拉力杆、液压缸都会磨损。
立式磨本身在工作时的振动对这些零件的磨损影响较大。
如果入磨的粒度太大,振动将进一步加剧从而导致拉力杆、液压缸都会磨损更加严重,使密封装置受损导致液压系统渗油,使液压系统的压力提高困难,严重时无法正常工作。
以上仅仅分析了入磨物料太大造成的一些状况,已经说明立式磨的入磨粒度偏大影响的不仅仅是产量和质量,还会影响到立式磨的正常工作、机械零件寿命,带来系统的故障,使立磨的工作自然受到影响。
这一点应引起广泛的关注。
附:使用维护(1)日常巡检时注意振动、电机电流、供油压力、油量、温度及高压泵开启间隔时间等变化,油缸活塞杆表面磨损等情况。
停磨时要及时提升磨辊,避免磨辊与磨盘碰撞。
油质定时检测,杂质含量定期测检,并留有记录和油样。
(2)每周需安排一次临停检修,主要内容为:检查各紧固件是否有松动并及时紧固(包括选粉机的主轴涨套),检查磨损部位磨损状况,必要时测量磨损量(包括防护罩的磨损检查)。
结合工艺专业调整喷口环盖板位置及盖板面积,必要时更换部分磨损件,防止磨损件脱落及喷水管部位折断给磨机运行带来不利影响,检查各部位的密封状况并及时处理,利用停磨时间更换易损易耗件如滤芯等,通过手动操作各液压系统,以便诊断运行中出现故障的根源并及时解决。
(3)每年安排一、二次计划性检修,主要是系统性处理磨机运行中出现的故障,更换磨损、老化的备件,保养关键件,建议不论运行好坏均需解体扭力杆及水平拉杆处球面轴承,加以保养,并测量轴承间隙,必要时更换弹性块及轴承。
同时对系统风管、挡板、冷却水路、冷却器等进行仔细检查,必要时给予修复。
(4)定期检测磨辊辊皮及磨盘衬板的磨损量,建议当辊皮磨损最高点到最低点达30mm时应翻边后使用,可提高辊皮寿命;辊皮和磨盘衬板磨损量之和达120~150mm时需更换辊皮( 具体值需考虑拉紧油缸行程避免撞缸),辊皮翻边压板螺栓可以重新利用,换辊皮时需更换新的压板、螺栓。
附:常见问题存在不同程度的磨辊漏油现象。
主要原因有两点:(1)磨辊两侧密封的润滑方式和加入量不正确,正确的方式是3~4个月加一次,在磨辊热态且被液压顶起时加入,边加入边人工盘动磨辊,加入量磨辊外侧(靠磨机筒体侧)每只磨辊加50g,磨辊内侧(靠磨机中心架侧)每只磨辊加100g,不可加入过多,以免油脂挤翻密封。
(2)磨辊与油箱之间连接的平衡管堵塞,造成磨辊内部油位(稀油循环润滑) 偏高,加剧磨辊漏油,需要用压缩空气吹管道,清除堵塞。
同时磨辊的真空度也不能随便更改,否则会造成更为严重的磨辊漏油。
对配套设备的维护不够。
例如:(1)风管上的挡板,特别是入磨、出磨、旁路及排风机的挡板磨损确认,这直接影响操作,关系到设备的安全运行。
(2)原料入磨及生料入库输送系统的运行情况直接关系到磨机的运转率。
(3)除铁器的性能也直接关系到立磨及辅机设备安全运行。
(4)电气自动化设备一定要及时按要求保养,抓住一切停机机会对电机等关键设备进行保养、维护。
立磨的操作经验1 操作要点1.1 稳定料床维持稳定料床,这是辊式磨料床粉磨的基础,正常运转的关键。
料层厚度可通过调节挡料圈高度来调整,合适的厚度以及它们与磨机产量之间的对应关系,应在调试阶段首先找出。
料层太厚粉磨效率降低,料层太薄将引起振动。
如辊压加大,则产生的细粉多,料层将变薄;辊压减少,磨盘物料变粗,相应返回的物料多,料层变厚。
磨内风速提高,增加内部循环,料层增厚,降低风速,减少内部循环,料层减薄。