各种钻头图片及原理
方孔钻头原理
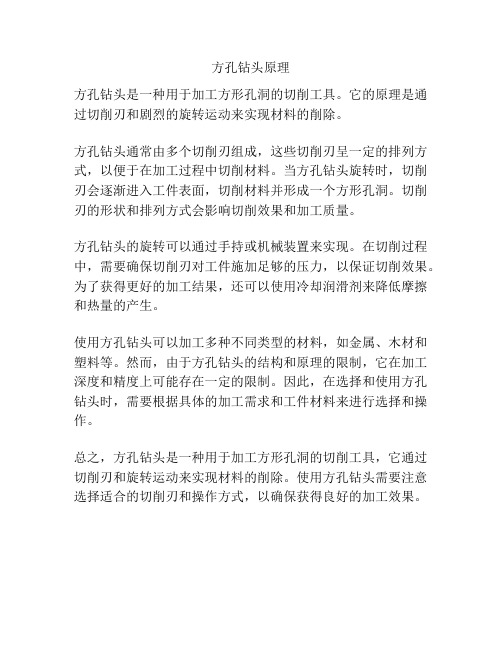
方孔钻头原理
方孔钻头是一种用于加工方形孔洞的切削工具。
它的原理是通过切削刃和剧烈的旋转运动来实现材料的削除。
方孔钻头通常由多个切削刃组成,这些切削刃呈一定的排列方式,以便于在加工过程中切削材料。
当方孔钻头旋转时,切削刃会逐渐进入工件表面,切削材料并形成一个方形孔洞。
切削刃的形状和排列方式会影响切削效果和加工质量。
方孔钻头的旋转可以通过手持或机械装置来实现。
在切削过程中,需要确保切削刃对工件施加足够的压力,以保证切削效果。
为了获得更好的加工结果,还可以使用冷却润滑剂来降低摩擦和热量的产生。
使用方孔钻头可以加工多种不同类型的材料,如金属、木材和塑料等。
然而,由于方孔钻头的结构和原理的限制,它在加工深度和精度上可能存在一定的限制。
因此,在选择和使用方孔钻头时,需要根据具体的加工需求和工件材料来进行选择和操作。
总之,方孔钻头是一种用于加工方形孔洞的切削工具,它通过切削刃和旋转运动来实现材料的削除。
使用方孔钻头需要注意选择适合的切削刃和操作方式,以确保获得良好的加工效果。
麻花钻头原理

麻花钻头原理
麻花钻头是一种在钻岩过程中使用的工具,其原理是利用旋转运动和一定的压力来钻穿硬质岩石。
它的设计结构使得在钻探过程中能够更高效地破碎岩石,提高钻探速度和效率。
麻花钻头主要由钻头身、钻翼、钻杆连接等部分组成。
钻头身具有扭矩传递功能,能够将旋转动力传递到钻翼上,从而实现岩石的破碎。
钻翼则是麻花钻头的重要部分,其外形呈螺旋状,具有一定的锋利度和硬度。
当麻花钻头旋转时,钻翼与岩石表面摩擦,施加压力并破碎岩石。
在实际工作中,麻花钻头通常与钻杆连接在一起。
钻杆通过传递旋转和推进力来控制钻探方向和速度。
钻杆和钻头的连接方式通常采用螺纹连接,使得钻头能够与钻杆紧密结合,实现有效的传递力量。
麻花钻头的工作原理可总结为以下几个步骤:首先,钻杆和麻花钻头被下到井口。
然后,开始施加旋转运动,通过传递动力到钻头,使其旋转。
同时,沿着钻孔方向施加一定的压力。
这样,钻翼就会与岩石表面摩擦,逐渐破碎岩石。
在钻探过程中,固体废渣会随着钻孔洞口卸出,通过泥浆或其他介质排出。
总之,麻花钻头通过旋转运动和压力来破碎岩石,实现钻探作业。
其结构设计和操作方法的合理性和灵活性,使得麻花钻头成为现代钻井工具中重要的一部分。
pdc钻头分析
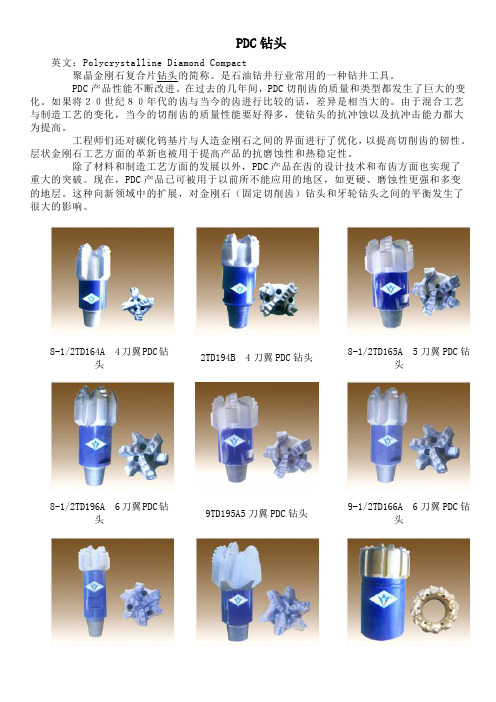
PDC钻头英文:Polycrystalline Diamond Compact聚晶金刚石复合片钻头的简称。
是石油钻井行业常用的一种钻井工具。
PDC产品性能不断改进。
在过去的几年间,PDC切削齿的质量和类型都发生了巨大的变化。
如果将20世纪80年代的齿与当今的齿进行比较的话,差异是相当大的。
由于混合工艺与制造工艺的变化,当今的切削齿的质量性能要好得多,使钻头的抗冲蚀以及抗冲击能力都大为提高。
工程师们还对碳化钨基片与人造金刚石之间的界面进行了优化,以提高切削齿的韧性。
层状金刚石工艺方面的革新也被用于提高产品的抗磨蚀性和热稳定性。
除了材料和制造工艺方面的发展以外,PDC产品在齿的设计技术和布齿方面也实现了重大的突破。
现在,PDC产品已可被用于以前所不能应用的地区,如更硬、磨蚀性更强和多变的地层。
这种向新领域中的扩展,对金刚石(固定切削齿)钻头和牙轮钻头之间的平衡发生了很大的影响。
8-1/2TD164A 4刀翼PDC钻头2TD194B 4刀翼PDC钻头8-1/2TD165A 5刀翼PDC钻头8-1/2TD196A 6刀翼PDC钻头9TD195A5刀翼PDC钻头9-1/2TD166A 6刀翼PDC钻头最初,PDC 钻头只能被用于软页岩地层中,原因是硬的夹层会损坏钻头。
但由于新技术的出现以及结构的变化,目前PDC 钻头已能够用于钻硬夹层和长段的硬岩地层了。
PDC 钻头正越来越多地为人们所选用,特别是随着PDC 齿质量的不断提高,这种情况越发凸显。
由于钻头设计和齿的改进,PDC 钻头的可定向性也随之提高,这进一步削弱了过去在马达钻井中牙轮钻头的优势。
目前,PDC 钻头每天都在许多地层的钻井应用中排挤掉牙轮钻头的市场。
PDC 钻头厚层砾岩钻进技术探索与实践:为了降低海上钻井作业成本、提高作业效率,开发了PDC 钻头厚层砾岩钻进技术.在保持普通PDC 钻头快速切削性能的基础上,通过优选新型高强度PDC 切削 齿、改进钻头切削结构提高钻头的整体强度,通过采用后倾角渐变、力平衡设计、加强切削齿保护等方法提高钻头的稳定性,并且在使用中通过优化钻具组合、采用 合理的钻井参数和"中低排量-中低转速-中高钻压"的平稳钻进模式预防PDC 钻头在砾岩段的先期破坏,有效延长了钻头在砾岩钻进中的寿命.应用该技术实现 了用PDC 钻头在辽东湾一次性钻穿馆陶组和东营组上部疏松地层中垂厚近80 m 的砾岩段,有的井钻穿砾岩段后又直接钻下部中硬地层至完钻井深.采用PDC 钻头厚层砾岩钻进技术,可以大量节省海上钻井作业时间,显著降低钻井费用.PDC 钻头工程技术措施石油钻井装备:1)、首先做好PDC 钻头的选型工作,钻头水眼、流道设计应利于排屑;2)、下入PDC 钻头之前,应充分循环泥浆,清洗井眼,防止起钻后滞留在井眼内的钻屑继续水化分散;3)、下钻时钻头不断刮削井壁,井壁上的泥饼或滞留于井内的钻屑会在钻头下堆积,到一定程度便会压实在钻头上,那么下钻中途进行循环,将钻头 冲洗干净也是有其必要的;4)、下钻过程中还应适当控制速度,防止钻头突然冲入砂桥,钻进一堆烂泥中;另外如果速度恰当,PDC 钻头会顺着上一只钻头所钻的螺旋形井眼轨道行 进,而不是在井壁上划拉下大量泥饼。
常见工程钻机种类及工作原理

常见工程钻机种类及工作原理1.旋挖钻机:旋挖钻机是一种常见的工程钻机,主要用于土壤或软岩的钻探和钻孔施工。
其工作原理是通过旋转钻杆,驱动钻头在地面或土层下进入地面,进行开放式的钻探和孔洞挖掘作业。
旋挖钻机通过改变钻头的类型和结构,以适应不同地质环境下的钻探要求。
2.水洗钻机:水洗钻机是一种常用的工程钻机,主要用于钻取地下水的水井和岩心钻取。
其工作原理是通过高压水流将岩层碎屑冲刷出钻孔,然后将钻杆下放,继续进行钻孔作业。
水洗钻机一般配备岩心采集器,可以快速采集地质岩芯样品,用于地质勘探和工程设计。
3.螺旋钻机:螺旋钻机是一种常见的工程钻机,主要应用于岩土地质工程中的基桩、钢管灌注桩等施工。
其工作原理是通过旋转内中空的钻杆,驱动螺旋岩头进入地层,通过挖掘和推土的方式将岩土材料移除,同时形成一个稳定的钻孔。
螺旋钻机在施工过程中还可以通过注浆技术实现地层固结和强化的效果。
4.花岗岩钻机:花岗岩钻机是一种专用的工程钻机,主要用于花岗岩和其他坚硬岩石的钻孔作业。
其工作原理是通过高速旋转的花岗岩钻头,携带硬质合金刀片在岩石中进行挖掘。
花岗岩钻机一般采用液压或气动驱动方式,具有高效、精确、安全的特点。
5.方案钻机:方案钻机是一种常见的地下工程钻机,主要用于地下钻孔和孔洞施工。
其工作原理是通过旋转钻杆,驱动方案钻头在地下水平面或向下钻探进入地下,进行孔洞挖掘作业。
方案钻机通常具有强大的钻进力和稳定的孔洞质量,适用于复杂的地下工程环境。
以上是常见的几种工程钻机及其工作原理。
工程钻机种类繁多,根据不同的施工需求和地质情况,选择合适的钻机类型可以提高施工效率和质量。
钻头基本知识和选型(技术员培训)

钻头基本知识和选型
Technology Development Centre ( EOTDC).Southwest.Drilling company of Zhongyuan Petroleum Engineering Co.Ltd Sinopec
量的问题。
使用环境因素对钻头性能的影响
影响PDC钻头机械钻速的因素: 钻头本身的因素和使用环境因素 钻头本身因素(或内因)包括:
钻头选型 PDC钻头对地层相对比较敏感,根据地层情况选择合适的钻头 型号或根据地层情况进行针对性的设计钻头,是非常重要的,也是PDC 钻头能否取得较好经济指标的前提和关键。
钻井工程数据
– 井身结构 – 井眼轨迹 – 泥浆性能 – 钻具组合 – 钻井参数
邻井钻头使用资料
岩石力学分析及应用
常用测井方式、代码和单位
测井代码 DT, DTc RHOB, DEN GR, GRc Pe CAL RES S-POR,S-PORc D-POR,D-POR N-POR ND-POR UCS-psi CCS-psi
钻头设计参数和制造工艺; 切削齿性能及质量;
使用环境因素对钻头性能的影响
使用环境因素包括:
地层岩性和压实强度; 使用的钻井参数;包括钻压、转速和排量等。
✓ PDC的刚脆性要求钻头旋转要平稳、减少振动,钻具组合时最好加上减振器, 减少振动,防止跳钻和溜钻;
✓ PDC的热敏性要求选择合适的排量,以达到清洗和冷却切屑齿。通过水力参 数计算,一般选择的排量要求钻头喷嘴的射流冲击力要达到40米/秒以上,钻 头比水马力要达到1.5马力/in2以上,以满足清洗岩屑和冷却PDC的要求,泥 浆环空最低返速达到0.6-1米/秒。
钻头每个部位的学名竟然是这样的?

全方位解剖钻头钻头的名称专业名称①螺旋角γ:不同型号角度不同,一般10°~40°。
②刃带:主要起导向和挤压的作用。
③刀背:介于刃带与槽之间的部位,但比刃带低,减小且切削力(摩擦力)。
④排屑槽表面:有时是前刀面,切屑流经的面。
⑤钻尖角:刃带与切削刃的交点。
钻头的角度⑥主切削刃:两个主切削刃的夹角为顶角б,真正的切削部位。
⑦后刀面:形成后角α的面。
⑧横刃:连接两个切削楔的部分,它承担50%的切削力(轴向)。
⑨刀背间隙:减少钻头和工件之间的摩擦力。
⑩排屑槽:较大空间,利于排屑。
孔口缺口和毛刺问题?通过减小钻尖角使钻尖顶住工件的宽度和高度进行改善。
较小的钻尖角118°1、径向分力,径向稳定性差。
2、轴向力小。
3、非延展性材料,减小崩碎。
较大的钻尖角135°~140°1、轴向分离大,径向稳定性好。
2、更大的进给能力。
3、软粘性材料,减小飞边。
4、孔的圆度,直径公差和直线度更好。
周边倒角式钻尖1、减小崩碎。
2、具有大钻尖角钻头的优点。
钻头应用问题/措施钻尖磨损原因:1.工件在钻头钻入力作用下工件会向下移动,钻头钻通后弹回。
2.机床刚性不足。
3.钻头材料不够结实。
4.钻头跳动太大。
5.夹持刚性不够,钻头滑动。
措施:1.降低切削速度2.增加进给量3.调整冷却方向(内冷)4.增加一倒角5.检查并调整好钻头的同轴度6.检查后角是否合理崩刃、破损原因:1.钻头的安装振摆,在一个切削刃上的冲击过大造成的。
2.工件的夹紧刚性低,在钻孔切出时发生。
3.进给量过大。
4.切削速度过高。
措施:1.安装振摆调整为0.02mm以下,使钻头的两个刃在平衡的条件下进行钻削加工。
2.降低进给量,减小钻头切出时的冲击。
3.如果是可转位钻头,更换刀片材质。
积屑瘤原因:1.切削材料与工件材料之间的化学反应引起的(含碳量较高的低碳钢)措施:1.改善润滑剂,增加油或添加剂含量。
2.提高切削速度,降低进给率减少接触时间。
勘探钻头知识点总结图
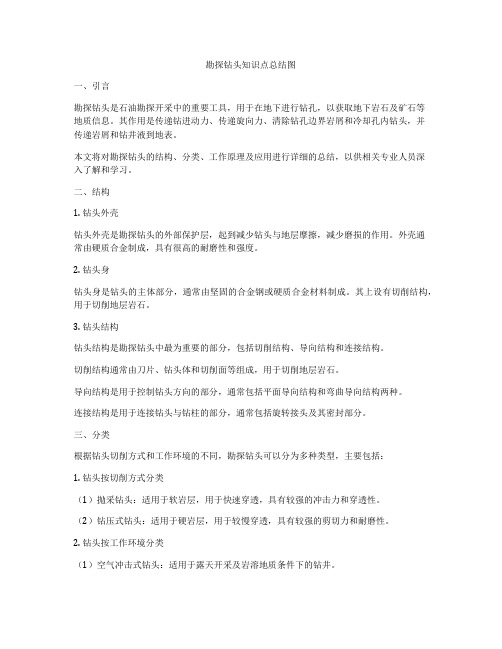
勘探钻头知识点总结图一、引言勘探钻头是石油勘探开采中的重要工具,用于在地下进行钻孔,以获取地下岩石及矿石等地质信息。
其作用是传递钻进动力、传递旋向力、清除钻孔边界岩屑和冷却孔内钻头,并传递岩屑和钻井液到地表。
本文将对勘探钻头的结构、分类、工作原理及应用进行详细的总结,以供相关专业人员深入了解和学习。
二、结构1. 钻头外壳钻头外壳是勘探钻头的外部保护层,起到减少钻头与地层摩擦,减少磨损的作用。
外壳通常由硬质合金制成,具有很高的耐磨性和强度。
2. 钻头身钻头身是钻头的主体部分,通常由坚固的合金钢或硬质合金材料制成。
其上设有切削结构,用于切削地层岩石。
3. 钻头结构钻头结构是勘探钻头中最为重要的部分,包括切削结构、导向结构和连接结构。
切削结构通常由刀片、钻头体和切削面等组成,用于切削地层岩石。
导向结构是用于控制钻头方向的部分,通常包括平面导向结构和弯曲导向结构两种。
连接结构是用于连接钻头与钻柱的部分,通常包括旋转接头及其密封部分。
三、分类根据钻头切削方式和工作环境的不同,勘探钻头可以分为多种类型,主要包括:1. 钻头按切削方式分类(1)拋采钻头:适用于软岩层,用于快速穿透,具有较强的冲击力和穿透性。
(2)钻压式钻头:适用于硬岩层,用于较慢穿透,具有较强的剪切力和耐磨性。
2. 钻头按工作环境分类(1)空气冲击式钻头:适用于露天开采及岩溶地质条件下的钻井。
(2)液压式钻头:适用于地下水位较高的钻井场合。
(3)钻插式钻头:适用于湿法钻井。
四、工作原理勘探钻头是通过钻台的旋转和推进,利用钻头本身的重量和旋转力在地层中进行切削,使岩石碎屑和钻井液一起上升至井口。
其工作原理主要包括冲击力、旋转力和制动力。
1. 冲击力冲击力是由钻头的下压重量和地层反力产生的,用于切削地层岩石。
在拋采钻头中,冲击力是由拋控器或拋泵提供的。
2. 旋转力旋转力是由钻台产生的,通过钻柱传递给钻头,用于使钻头旋转并切削地层岩石。
3. 制动力制动力主要由钻头与地层的摩擦力提供,用于保持钻头钻进的稳定性。
钻头工作原理
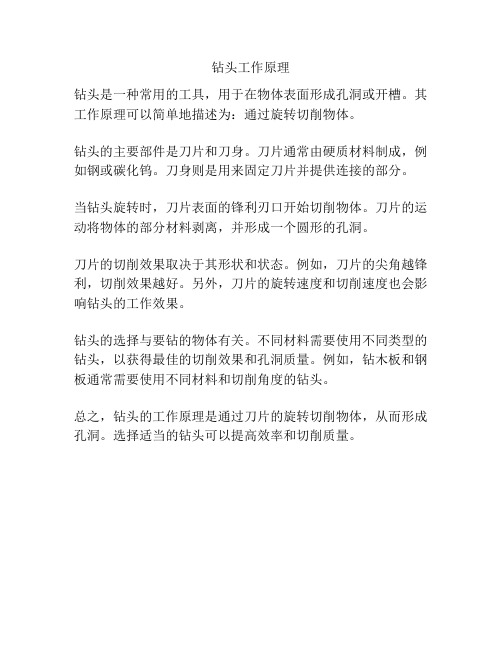
钻头工作原理
钻头是一种常用的工具,用于在物体表面形成孔洞或开槽。
其工作原理可以简单地描述为:通过旋转切削物体。
钻头的主要部件是刀片和刀身。
刀片通常由硬质材料制成,例如钢或碳化钨。
刀身则是用来固定刀片并提供连接的部分。
当钻头旋转时,刀片表面的锋利刃口开始切削物体。
刀片的运动将物体的部分材料剥离,并形成一个圆形的孔洞。
刀片的切削效果取决于其形状和状态。
例如,刀片的尖角越锋利,切削效果越好。
另外,刀片的旋转速度和切削速度也会影响钻头的工作效果。
钻头的选择与要钻的物体有关。
不同材料需要使用不同类型的钻头,以获得最佳的切削效果和孔洞质量。
例如,钻木板和钢板通常需要使用不同材料和切削角度的钻头。
总之,钻头的工作原理是通过刀片的旋转切削物体,从而形成孔洞。
选择适当的钻头可以提高效率和切削质量。
石油钻井之钻头介绍

四、金刚石钻头
金刚石钻头的正确使用: 金刚石钻头适用钻中到坚硬、研磨性地层和涡轮钻 井、深井超深井钻井以及取芯作业。使用金刚石钻头前 ,井底要打捞干净,保证没有金属落物。钻头刚下到井 底时,要先用小钻压、低转速跑合。然后采用相对较低 的钻压(和牙轮钻头相比),较高的转速和较大的排量 钻进。应尽量避免划眼。如果必须进行划眼,应采用低 钻压和低转速,操作要均匀,防止钻头规径部分金刚石 碎裂和过度磨损。
三、牙轮钻头
2)国产牙轮钻头分类 国产牙轮钻头按其结构特征分为八个系列,分别用代号Y、P 、MP、MPB、HP、HPB、XMP、XH表示,各代号的意义如下 : Y-普通齿牙轮钻头; P-喷射式齿钻头; MP-滚动密封轴承喷射式齿钻头; MPB-滚动密封轴承喷射式保径钻头; HP-滑动密封轴承喷射式铣齿钻头; HPB-滑动密封轴承喷射式保径钻头; XMP-镶齿滚动密封轴承喷射式钻头;
二、刮刀钻头
2、刮刀钻头的正确使用
刮刀钻头适用于软地层和粘软地层。钻进时需要适当控 制钻压与转速,注意防斜、防蹩、防止刀翼断裂。由于刮 刀钻头在软地层中的机械钻速较快,岩屑量较大,宜采用 大排量钻进,充分清洗井底和冷却钻头。刮刀钻头钻进时 ,刀翼外侧线速度较高,磨损速度较快,钻头容易磨损成 锥形,此时要特别注意防斜和防止井径缩小。
三、牙轮钻头
钻头在井底的纵向振动使钻 柱不断压缩与伸张,下部钻 柱把这种周期性变化的弹性 变形能通过牙齿转化为对地 层的冲击作用力用以破碎岩 石。这种冲击、压碎作用是 牙轮钻头破碎岩石的主要方 式。
三、牙轮钻头 牙轮钻头除了对井底岩石产生冲 击、压碎作用外,还对井底岩石产 生剪切作用。牙轮在井底滚动的同 时还产生牙齿对井底的滑动,牙齿 的滑动对井底岩石形成剪切作用, 象刮刀钻头那样刮削井底。牙齿的 滑动主要是由牙轮的超顶、副锥和 移轴布置引起的。牙轮的超顶布置 和复锥牙轮引起切线方向的滑动, 牙轮的移轴布置则引起轴向方向的 滑动。
麻花钻的结构以及工作原理和缺点

麻花钻的结构以及工作原理在金属切削中,孔加工占很大比重。
孔加工的刀具种类很多,按其用途可分为两类:一类是在实心材料上加工出孔的刀具,如麻花钻、扁钻、深孔钻等;另一类是对工件已有孔进行再加工的刀具,如扩孔钻、铰刀、镗刀等。
本节介绍常用的几种孔加工刀具。
(一)麻花钻1.麻花钻的结构要素图7-32为麻花钻的结构图。
它由工作部分、柄部和颈部组成。
(1)工作部分麻花钻的工作部分分为切削部分和导向部分。
①切削部分麻花钻可看成为两把内孔车刀组成的组合体。
如图7-33所示。
而这两把内孔车刀必须有一实心部分——钻心将两者联成一个整体。
钻心使两条主切削刃不能直接相交于轴心处,而相互错开,使钻心形成了独立的切削刃——横刃。
因此麻花钻的切削部分有两条主切削刃、两条副切削刃和一条横刃(如图7-32b所示)。
麻花钻的钻心直径取为(0.125~0.15)do(do为钻头直径)。
为了提高钻头的强度和刚度,把钻心做成正锥体,钻心从切削部分向尾部逐渐增大,其增大量每100mm长度上为1.4~2.0mm。
两条主切削刃在与它们平行的平面上投影的夹角称为锋角2Φ,如图7-34所示。
标准麻花钻的锋角2Φ=118°,此时两条主切削刃呈直线;若磨出的锋角2Φ>118°,则主切削刃呈凹形;若2Φ<118°,则主切削刃呈凸形。
②导向部分导向部分在钻孔时起引导作用,也是切削部分的后备部分。
导向部分的两条螺旋槽形成钻头的前刀面,也是排屑、容屑和切削液流入的空间。
螺旋槽的螺旋角β是指螺旋槽最外缘的螺旋线展开成直线后与钻头轴线之间的夹角,如图7-34所示。
愈靠近钻头中心螺旋角愈小。
螺旋角β增大,可获得较大前角,因而切削轻快,易于排屑,但会削弱切削刃的强度和钻头的刚性。
导向部分的棱边即为钻头的副切削刃,其后刀面呈狭窄的圆柱面。
标准麻花钻导向部分直径向柄部方向逐渐减小,其减小量每100mm长度上0.03~0.12mm,螺旋角β可减小棱边与工件孔壁的摩擦,也形成了副偏角。
钻头的原理

钻头的原理钻头是一种常见的工具,它通常用于在硬质材料上进行钻孔或者切削。
钻头的原理涉及到材料的物理性质和机械原理,下面我们就来详细了解一下钻头的原理。
首先,让我们来了解一下钻头的结构。
钻头通常由刀片、刀头和刀柄组成。
刀片是用来切削材料的部分,刀头是刀片的前端,用来对材料进行切削,而刀柄则是用来固定和操作钻头的部分。
钻头的结构设计旨在提供稳定的切削力和耐磨性,以便在钻孔或切削过程中能够高效地完成任务。
其次,钻头的原理涉及到切削力和摩擦力。
在钻孔或切削过程中,刀片和刀头对材料施加切削力,以便将材料切削或者钻孔。
同时,刀片和刀头与材料之间会产生摩擦力,这也是完成切削任务所必需的。
钻头的设计要能够有效地控制切削力和摩擦力,以便在切削过程中保持稳定的性能和高效的切削效果。
另外,钻头的原理还涉及到材料的物理性质。
不同的材料具有不同的硬度、韧性和脆性,这就要求钻头在切削不同材料时需要具备不同的切削性能。
例如,钻头在切削金属材料时需要具备较高的硬度和耐磨性,而在切削木材或塑料材料时则需要具备较高的锋利度和切削效率。
因此,钻头的原理也包括了针对不同材料的切削特性和要求。
最后,钻头的原理还涉及到切削过程中的热量和废屑处理。
在切削过程中,刀片和刀头会产生摩擦热量,而废屑则是切削过程中产生的材料碎片。
钻头的设计要能够有效地处理这些热量和废屑,以避免对切削效果和钻头寿命的影响。
因此,钻头的原理也包括了对热量和废屑的处理技术和要求。
综上所述,钻头的原理涉及到结构设计、切削力和摩擦力、材料性质以及热量和废屑处理等多个方面。
了解钻头的原理有助于我们更好地选择和使用钻头,以便在工程和制造领域中获得更好的切削效果和经济效益。
希望本文能够帮助您更好地理解钻头的原理和应用。
钻头的工作原理

钻头的工作原理
钻头是一种用于钻孔的工具,它的工作原理是通过快速旋转和施加压力来削减物体的表面,从而形成孔洞。
钻头通常由一个金属柄和一个钻头刀具组成。
在工作时,钻头被插入物体表面,并通过电动机或其他设备的旋转运动使其旋转起来。
同时,操作者向下施加压力,使钻头刀具与物体表面紧密接触,并以高速旋转的方式削减物体的表面。
钻头刀具通常具有硬度较高的材料,如钨钢或碳化钨。
这种材料能够在高速旋转时承受极高的压力,并保持锋利的切削边缘。
钻头刀具的设计也会根据不同的需求和材料进行调整,以确保获得最佳的钻孔效果。
在钻孔过程中,钻头刀具通过切削材料的方式,削减物体的表面,并形成孔洞。
同时,产生的切削碎屑会通过钻头的螺纹或其他设计特点被排出孔洞中。
钻头的工作原理基本上是通过旋转和削减物体表面来完成钻孔的过程。
不同类型的钻头可以用于不同的材料和应用,以满足不同的需求。
它们在建筑、制造业和日常生活中都有广泛的应用。
第1章潜孔钻机
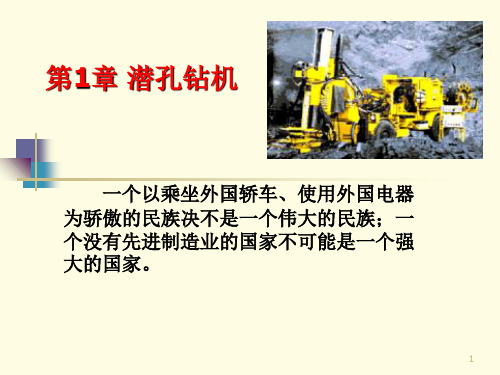
10
一 钻杆
用无缝钢管制做. 传递扭矩 承受轴压 中空通风
11
二 冲击器 Drill Hammer
22
有阀冲击器和无阀冲击器的比较
有阀冲击器的配气阀换向与气缸的排气压力有关。 只有当排气口被开启,气缸内压力降到某一数值后阀才 换向。所以,从活塞打开排气口开始,直到阀换向这段 时间内,压气从排气口排出,压气的能量没有被利用。
无阀冲击器则利用了压气的膨胀作功推动活塞运动。 减少了能量消耗,压气耗量比有阀冲击器节省30%左右, 并具有较高的冲击频率和较大的冲击功。但是,无阀冲 击器的主要零件精度要求较高,加工工艺较复杂。
16
⑵有阀冲击器的工作原理
当钻头触及孔底后,钻头尾部顶起活塞,使活塞后端将防空打孔 ⑤堵死,露出前腔进气孔⑥,压气由此进入前腔,同时活塞前端密封 面把前腔密封。于是,前腔压力升高,压气推动活塞回程,活塞由静 止开始作加速运动。后腔气体由活塞中心孔排出。当活塞中心孔被阀 座上的配气杆堵死后,后腔气体被压缩,压力逐渐升高。活塞继续向 后运动,当活塞前端脱离衬套的密封面时,前腔气压从钻头中心孔排 出。这时前腔压力逐渐降低,阀片后侧的压力也随之逐渐下降;
15
⑵有阀冲击器的工作原理
当钻头未触及孔底时,钻头及活塞均处于下限位置,阀片 7前后两侧的压力相等,依靠自重落在阀座8上。由中空钻杆输 入的压气进入后接头,压缩弹簧,推开止逆塞后,分成两路。 一路进入止逆塞孔①,经阀盖、节流塞、阀座、活塞和钻头各 零件的中心孔直吹孔底;另一路经阀盖轴向孔②,通过阀片后 侧面与阀盖之间的间隙进入孔④,再经内外缸之间的环形气道, 从防空打孔⑤进入后腔,并排至孔底。
钻头的类型及破岩机理
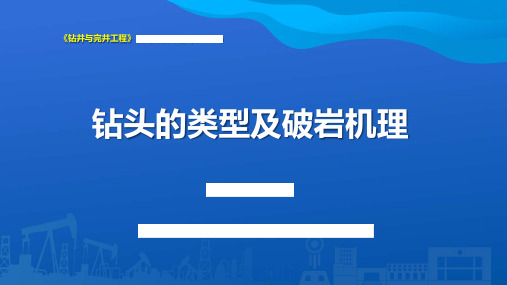
《钻井与完井工程》
本节主要内容
一、钻头的类型
牙轮钻头
全面钻进钻头
本节主要内容
二、刮刀钻头
优缺点和适用条件
刮刀钻头适用于松软一软的地层
本节主要内容
1.牙轮钻头的基本结构
2.牙轮钻头的破岩机理
2.牙轮钻头的破岩机理
单、双齿交替着地引起纵向振动
本节主要内容
四、金刚石钻头
1.金刚石钻头的类型
PDC钻头TSP钻头
天然金刚石钻头
喷嘴钻头体
2.PDC 钻头的基本结构钢体PDC 钻头胎体PDC 钻头
四、金刚石钻头
有缘学习更多+谓ygd3076考证资料或关注桃报:奉献教育(店铺)
四、金刚石钻头
3.PDC钻头的破岩机理
4.PDC钻头的正确使用
有缘学习更多+谓ygd3076考证资料或关注桃报:奉献教育(店铺)。
钻头工作的原理

钻头工作的原理
钻头的工作原理是通过旋转和切割来钻取材料。
具体而言,钻头的旋转是由钻机或者其他设备提供的扭矩力驱动的。
当钻头旋转时,刃口或者齿面会与被钻取的材料接触,从而切割材料。
钻头通常由高硬度的材料制成,如硬质合金、高速钢等,以确保其在与材料接触时能够保持刃口的锋利度和切削能力。
刃口的设计和几何形状也对钻头的性能有很大影响。
常见的钻头形状包括圆锥形、平头钝角、螺旋形等,每种形状都有不同的适用范围和特点。
在钻取过程中,钻头切削材料的方式主要有两种:切削和击碎。
切削是指钻头通过旋转,在材料上形成连续的切削刃,将材料切削成碎片。
击碎则是指钻头通过冲击和振荡,将材料内部的结构破坏,使其破裂成碎片。
除了旋转和切割,钻头的工作原理还涉及到冷却和润滑。
由于钻取过程中会产生大量的摩擦热,如果不及时散热和冷却,钻头可能会因过热而变钝或损坏。
因此,在钻取过程中往往需要使用冷却液或润滑剂来降低摩擦热,保持钻头的性能和寿命。
总之,钻头的工作原理是通过旋转和切削来钻取材料,同时需要注意冷却和润滑,以确保钻头的正常运行和寿命。
外国发明特殊钻头的原理
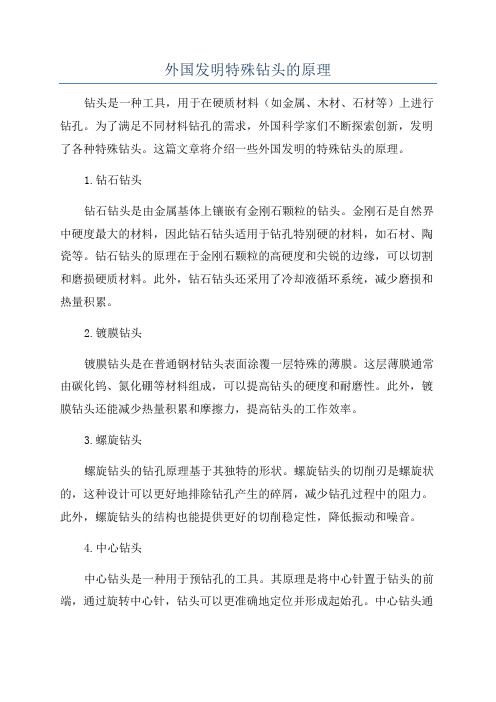
外国发明特殊钻头的原理钻头是一种工具,用于在硬质材料(如金属、木材、石材等)上进行钻孔。
为了满足不同材料钻孔的需求,外国科学家们不断探索创新,发明了各种特殊钻头。
这篇文章将介绍一些外国发明的特殊钻头的原理。
1.钻石钻头钻石钻头是由金属基体上镶嵌有金刚石颗粒的钻头。
金刚石是自然界中硬度最大的材料,因此钻石钻头适用于钻孔特别硬的材料,如石材、陶瓷等。
钻石钻头的原理在于金刚石颗粒的高硬度和尖锐的边缘,可以切割和磨损硬质材料。
此外,钻石钻头还采用了冷却液循环系统,减少磨损和热量积累。
2.镀膜钻头镀膜钻头是在普通钢材钻头表面涂覆一层特殊的薄膜。
这层薄膜通常由碳化钨、氮化硼等材料组成,可以提高钻头的硬度和耐磨性。
此外,镀膜钻头还能减少热量积累和摩擦力,提高钻头的工作效率。
3.螺旋钻头螺旋钻头的钻孔原理基于其独特的形状。
螺旋钻头的切削刃是螺旋状的,这种设计可以更好地排除钻孔产生的碎屑,减少钻孔过程中的阻力。
此外,螺旋钻头的结构也能提供更好的切削稳定性,降低振动和噪音。
4.中心钻头中心钻头是一种用于预钻孔的工具。
其原理是将中心针置于钻头的前端,通过旋转中心针,钻头可以更准确地定位并形成起始孔。
中心钻头通常应用于金属材料的加工过程中,有效避免钻头在工件表面滑动或偏离预定位置。
5.磁力钻头磁力钻头是一种通过磁力固定在工件上的钻头。
其原理是利用电磁铁或永磁体产生的磁力将钻头固定在工件表面,从而保持钻孔的稳定性。
磁力钻头通常应用于钢材等磁性材料的加工过程中,提供更高的精度和安全性。
以上仅是一些外国发明的特殊钻头的原理,这些原理的应用能够满足不同材料和加工需求。
随着科学技术的不断发展,更多新型的特殊钻头可能会被发明出来,提高加工效率和质量。
- 1、下载文档前请自行甄别文档内容的完整性,平台不提供额外的编辑、内容补充、找答案等附加服务。
- 2、"仅部分预览"的文档,不可在线预览部分如存在完整性等问题,可反馈申请退款(可完整预览的文档不适用该条件!)。
- 3、如文档侵犯您的权益,请联系客服反馈,我们会尽快为您处理(人工客服工作时间:9:00-18:30)。
铁人精神
“为国分忧、为民族争气”的爱国主义精神;
“宁可少活20年,拼命也要拿下大油田”的忘我拼搏精神;
“有条件要上,没有条件创造条件也要上”的艰苦奋斗精神;
2.1 钻头
刮刀钻头
Dragbit
PDC 钻头
金刚石钻头Diamondbit 扩眼钻头Enlarging bit
牙轮钻头
Roller bit 取心钻头Annular bit
2.1.1 刮刀钻头
刮刀钻头
刮刀钻头特点结构简单,制造方便。
在软地层中,可以得到高的机械钻速和钻头进尺。
在较硬地层中,钻头吃入困难,钻井效率低。
二刮刀
三刮刀
四刮刀
§2-1-1 刮刀钻头 (Drag bit) 一、结构
§2-1-1 刮刀钻头 (Drag bit) 一、结构 二、结构参数 1.刀翼结构角 刃尖角 β
刀翼尖端前后刃之间的 夹角,它表示刀翼的尖 锐程度。
φ
β ϕ α
保证刀翼结构有足够强度的情况 下,尽可能减小刃尖角 β 软岩石 β 平均10度 较硬岩石 β 平均12-15度 夹层多井又较深时还要适当增大
(2)切削角 α
刀翼前刃和水平面之间的夹角。
α 越大吃入深度越大
松软地层 软地层 中硬地层
α = 70
o
φ
b
α = 70o ~ 80o α = 80o ~ 85o
β ψα
(3)刃前角 φ 和刃后角 ψ 刃前角φ与切削角互为余角
φ = 90o − α
ψ =α − β
φ
β ψα
θ
2.刀翼几何形状 背部形状 抛物线型 底部形状 底刃b 材质: 高强度材质,刀翼侧面、正面镶 装或平铺硬质合金及孕镶金刚石 块,提高耐磨性
φ
b
刀翼的厚度随距刀刃的距离增加应 逐渐增厚,呈抛物线形。
β ψα
三、刮刀钻头破岩基本原理
根据摩尔强度 理论,如果忽 略摩擦力,当 F力等于或大 于剪切面积与 岩石抗剪极限 强度乘积时, 岩石沿剪切面 破碎。
三、刮刀钻头破岩基本原理 1.塑性岩石
W
T
θ
刮刀钻头以切削方 式破碎岩石。
刮刀钻头 在软的塑性地层工作 时,其切削过程类似于 刀具切削软金属。
刀片 在钻压的作用下吃入地 层,与此同时刀刃前面 的岩石在扭转力的作用 下不断产生塑性流动, 井底岩石被层层剥起。
2、破碎塑脆性岩石
刮刀钻头钻进脆性较大的地层时,破碎岩石的过程则分为碰撞、压碎 及小剪切和大剪切三个阶段: (1)碰撞 刃前岩石被破碎后,岩石对刀片的扭转阻力减小,刀片向前推进,碰 撞刃前岩石; (2)压碎及小剪切 刀片在扭转力的作用下压碎前方的岩石,使其产生小剪切破碎; (3)大剪切 扭转力增大,刀片继续挤压 前方岩石,当扭转力增大到极限 值时,岩石沿剪切面产生大剪切 破碎,然后扭转力突然减小。
碰撞、压碎及小剪切、大剪 切这三个过程反复进行,形成刮 刀钻头破碎塑脆性岩石的全过 程。
§2-1-2 牙轮钻头 (Roller Bit)
单牙轮钻头 两牙轮钻头 三牙轮钻头 四牙轮钻头
牙 轮 钻 头 分 类
一 、 牙 轮 钻 头 的 结 构
牙轮钻头•结构:牙轮及牙齿、
轴承、储油润滑密封
系统、钻头水眼
•结构:牙轮及牙齿、轴承、储油润滑密封系统、钻头水眼
•结构:牙轮及牙齿、轴承、储油润滑密封系统、钻头水眼
牙轮钻头的寿命:很大程度上取决于轴承的寿命
二、牙轮钻头的工作原理
D
bx
D
b
•3.牙齿对地层的剪切作用
剪切作用是通过牙轮的滑动来实现的;
(1)超顶:牙轮锥顶超过钻头轴心引起切向滑动,其大小与超顶距c成正比。
切向滑动→剪切掉同一齿圈相邻牙齿破碎坑之间的岩石。
(2)移轴:牙轮轴线偏离钻头轴心
引起轴向滑动,其大小与偏移值s 成正比。
轴向滑动→剪切掉齿圈之间的岩石;
(3)复锥:牙轮母线有两个不同的锥度
4.牙轮钻头的自洗
三、牙轮钻头的发展
1909:第一个牙轮钻头问世
1925:自洗式牙轮钻头
1933:滚动轴承三牙轮钻头
1935:移轴三牙轮钻头,钻速提高30%
1930_1948:普通水眼
1949:jet drilling
1951:镶硬质合金球齿钻头
1960:密封润滑轴承,寿命提高30—40%
金刚石钻头
--钻头中的战斗机
一、天然金刚石钻头(Diamond bit)
特点:镶嵌有金刚
石,适用于研磨性强
的地层
金刚石特点:高耐
磨、自锐作用、高温
碳化
破岩原理:研磨作用
1、金刚石钻头的结构
聚晶金刚石层+碳化钨底层+柱状体部→切削元件(块)
切削机理:以切削
方式破岩(1)钢体
(2)胎体(碳化钨)
(1)冠部几何形状
①双锥阶梯形剖面
适用于软到中硬地层(硬石膏、泥岩、砂岩、灰岩等);
②双锥形剖面
适用于较硬、致密地层(较硬的砂岩、石灰岩、白云岩等);
③“B”型剖面
适用于硬地层(硬砂岩、致密的白云岩等);
④脊圈式B型剖面
适用于坚硬地层(石英岩、燧石、火成岩等)。
(2)水眼及水槽
①逼压式水槽结构
②辐射型水槽结构
③辐射型逼压式水槽
④螺旋型水槽结构
(3)金刚石在钻头工作面上的排列有三种常见方式:
①交错排列方式;②圆周排列方式;③脊圈排列方式。
交错排列方式适用于软到中硬地层的钻头,圆
周排列方式适用于金刚石粒度较小、出刃较低的
硬地层钻头,脊圈式排列方式适用于金刚石粒度
更细、出刃更低的坚硬地层钻头。
2、天然金刚石钻头破岩原理
天然金刚石钻头
(1)硬地层在压力作用下呈现塑性
(2)塑性地层(岩石在应力作用下呈现塑性)在扭矩作用下,使前方岩石内部发生
破碎或塑性流动(蠕变)形成岩屑
(3)脆性地层:以剪力和张力破碎岩石脆性破坏(4)坚硬岩石:磨成粉末
金刚石钻头适用于钻中到坚硬、研磨性地层和涡轮钻井、深井超深井钻井以及取芯作业。
使用金刚石钻头前,井底要打捞干净,保证没有金属落物。
钻头刚下到井底时,要先用小钻压、低转速跑合。
然后采用相对较低的钻压(和牙轮钻头相比),较高的转速和较大的排量钻进。
应尽量避免划眼。
如果必须进行划眼,应采用低钻压和低转速,操作要均匀,防止钻头规径部分金刚石碎裂和过度磨损。
3、天然金刚石钻头的正确使用
二、
PDC钻头
Polycrystalline Diamond Compact bit
聚晶金刚石层+碳
化钨底层+柱状体
部→切削元件
(块)
破岩机理:以切削
方式破岩
1、结构
PDC 钻头
Polycrystalline Diamond Compact bit
单齿式刮刀式组合式
刚体PDC钻头的整个钻头体都
采用中碳钢材料并采用机械制造工艺加工成形。
在钻头工作面上钻孔,以压入紧配合方式将PDC切削齿固紧在钻头冠部。
钻头冠部采用表面硬化工艺(喷涂碳化钨耐磨层、渗碳等)进行处理,以增强其耐冲蚀能力。
这种钻头的主要优点是制造工艺简单;缺点是钻头体不耐冲蚀,切削齿难以固牢,目前应用较少。
胎体PDC钻头的钻头体上部为钢体,下部为碳化钨耐磨合金胎体,采用粉末冶金烧结工艺制造成型。
用低温焊料将PDC切削齿焊接在胎体预留窝槽上。
碳化钨胎体硬度高,耐冲蚀,因而胎体PDC钻头寿命长,进尺高,目前应用比较广泛。
2、钻头的切削齿材料
天然金刚石
PDC: 聚晶金刚石复合片
TSP: 热稳定聚晶金刚石
•金刚石优点:
-最硬、抗压强度最大、抗磨能力最高
•金刚石缺点:
-脆性大,遇到冲击会引起破裂
-热稳定性差,高温下会燃烧。
(455-860℃碳
化)。