基于逆向工程的快速成型技术应用
逆向工程和快速成型的手机外型快速设计
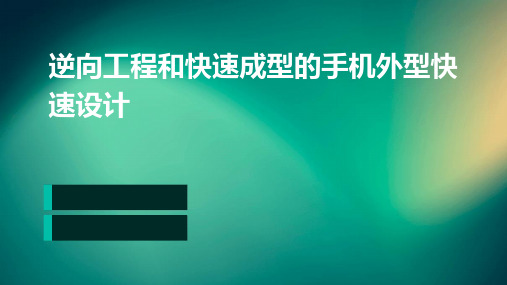
06 手机外型设计未来发展趋 势预测
个性化定制服务需求增长
1 2
用户参与设计
消费者越来越希望参与到手机外型设计的过程中, 表达自己的独特审美和个性化需求。
3D打印技术应用
3D打印技术的成熟使得个性化手机外壳的定制 成为可能,满足用户对于独特外观的追求。
3
定制化软件支持
手机外型设计软件的发展,为用户提供更加便捷 的设计工具,降低个性化定制门槛。
与艺术家、设计师跨界合作,将手机外型设 计提升为艺术品,展现科技与艺术的完美结 合。
时尚元素的引入
借鉴时尚界的流行元素和设计理念,打造具有时尚 感的手机外型,引领潮流趋势。
多元文化交融
汲取不同国家和民族的文化精髓,设计出具 有多元文化背景特色的手机外型,满足全球 市场需求。
THANKS FOR WATCHING
02 手机外型设计现状及挑战
当前手机外型设计趋势
全面屏设计
追求更高的屏占比,减少边框 和额头,增加视觉冲击力。
多摄像头配置
采用多个摄像水功能
加入无线充电和防水功能,提 高用户便利性和手机耐用性。
轻薄化和多彩配色
追求更轻薄的手机身材和多样 化的颜色搭配,满足用户个性
材质、颜色还原与快速成型技术结合
材质还原
通过分析手机外型的材质特性,选择合适的3D打印材料,如PLA、 ABS等,以还原真实的质感。
颜色还原
采用多色3D打印技术,将手机的颜色信息进行精确还原,实现彩色 打印。
快速成型
利用3D打印技术,将重建后的三维模型进行快速成型,得到手机外型 的实体模型。
创新设计思路及实践案例分享
感谢您的观看
消费者需求多样化
消费者对手机外型的需求 多样化,包括颜色、材质、 形状等。
基于逆向工程的快速成型技术的应用

.
图 1
扫描 点 云 数据处 理 图
,
m
。
通过扫描
获 得 了 零 件 曲面 的 点 云 数 据 之 后 据导 入 到
Im
a
,
将扫描所 得到 的点 云 数
,
3
零件快速成 型
快速成型技术 (Ra
p id
Im
a
g
e w a r e
软 件 中进 行 处 理
形 到 图纸
。
而 逆 向工 程 的设 计是从 零 件或 实物原
,
在产 品丌 发过 程 中
,
由于 形 状 复 杂
,
,
含许多空间曲面
很 难 直接 建市 数据模 型
常 常需 要 以
、
、
实物模 型 (样 件 ) 为依据 或参考 原 型 进 行仿 型
或造 型设计
。
本 文 以 导 流 罩 的逆 向反 求 为 例
,
通 常用 于 仿制没 有 设 计
,
: 翟 谳 ; i X;蹒 ;
”
, 每0 【^
!
~
。
’
图纸 文 件 的产 品
。
是对存在 的实物模型进行测量
,
并根
修改
、
据测 得 的数据重 构 出数据 模 型 检验
、
进 而进行分析
。
、
加工
,
然 后 制 造 出 产 品 的过 程
,
传统设 计 和 制造 其 巾包
改型
是从 图纸到零 件
譬 受
也 各 有 不 同 ,但 是 , 其 基 本 原 理 都 是 一 样 的 , 那 就 是 “ 层 制 造 ,逐 层 叠 加 ” 分 。快 速 成 型 ( ) 技 术 可 以 在 无 RP 需 准 备 任 何 模 具 、 刀 具 和 工 装 夹 具 的 情 况 下 , 直 接 接 受 产 品设 计 ( AD)数 模 的 数 据 ,快 速 制 造 出 新 产 品 的 样 C
第3 章 快速成型关键技术—快速逆向(反求)工程
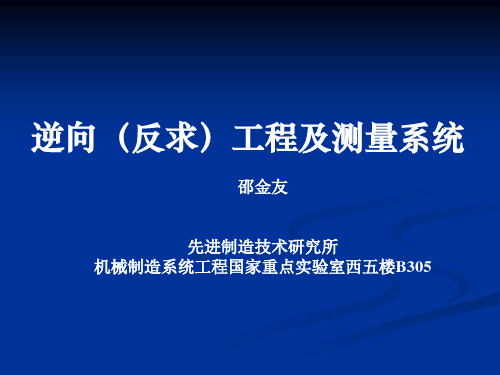
激光线扫描数字化仪
基于三角测量原理的激光扫描数字化仪 首先,由光源系统形成结构光,投射到被测物体表面上, 而与结构光成一定角度的位置传感器(如CCD 摄像机、
PSD等)摄取经物体表面形状调制的变形图像信息,经由信
号转换电路(如图像采集卡等) 把图像模拟信号转化为数字图 像信号输入计算机进行一系列数据处理,解调图像即将位置
平面扫描 旋转扫描 相位扫描 混合扫描
CCD2 CCD1
Laser
图9 单线光刀扫描反求设备
激光线扫描实例
飞行时间法
飞行时间法的原理是基于测量激光或其他光源脉冲光束
的飞行时间进行点位测量。在测量过程中,物体反射脉冲光
束经反射回到接收传感器,通过光纤传输的参考脉冲光束也 被传感器接收,这样会产生时间差,就可以把两脉冲时间差 转换成距离。飞行时间法典型的分辨率在1 mm左右,采用由 二极管激光器发出的亚微秒脉冲和高分辨率设备,可以获得 亚毫米级的分辨率。
图像分析法(数字照相系统 )
这种方法的关键 是多幅图像上同名点 的搜索及自动匹配较 为困难,通常求取同 名点的方法有: ①依据被测物体上的 人工的或固有的特征 点(角点、局部灰度 极值点等)在各个视 角方向的图像中形态 的相似性进行匹配; ②利用窗口或模板求 对应点。
光学测量中的问题
相位法原理
三维光学测量结构图
光栅投射到工件图案
参考文献:曹康,周贤斌,面外云纹法与相位法关系的研究, 航空材料学报,Vol. 15, No. 3, 1995: 50~55
当投影光源将基准栅线投影至被测试件表面时,栅线像发 生变形调制,形成调制栅线图像,光强分布函数可表示为:
基于逆向工程的复杂工艺品设计及快速成型

No2Apr第2期(总第225期)2021年4月机 械 工 程 与 自 动 化MECHANICAL ENGINEERING & AUTOMATION文章编号= 1672-6413(2021)02-0052-03基于逆向工程的复杂工艺品设计及快速成型櫜夏会芳,汤剑,张琳琅,苏秀芝(武汉华夏理工学院智能制造学院,湖北武汉430223)摘要:为解决复杂工艺品的逆向建模及成型问题,以兵马俑人俑工艺品为例,应用三维激光扫描设备、Geomagic Wrap 软件、Geomagic Design X 软件、Geomagic Control X 软件和3D 打印技术进行逆向设计和快速成型,实现模型的快速复制,提高了复杂型面产品的开发能力,降低了产品的研发成本。
关键词:逆向工程;工艺品;快速成型中图分类号: TP3917 文献标识码: A0 引言1. 1 扫描前处理逆向工程(Reverse Engineering )也称反求工程或 逆向设计,是将已有产品模型(实物模型)转化为工程 设计模型和概念模型,并在此基础上解剖、深化和再创 造的一系列分析方法和应用技术的组合[1]。
逆向工程的过程大致如下:首先由数据采集设备 获取样件表面数据,其次导入专门的数据处理软件或 带有数据处理的三维CAD 软件进行前处理,然后进 行曲面和三维实体重构,在计算机上复现实物样件,并 在此基础上进行修改和创新设计,最后对再设计的对 象进行实物制造。
其中从数据采集到CAD 模型的建 立是反求工程中的关键技术。
本文以兵马俑人俑工艺品为研究对象,利用逆向 工程技术对人俑模型进行逆向建模。
1人俑三维数据采集本次扫描选用日本柯尼卡美能达三维扫描仪 RANGE7对人俑模型进行数据采集。
柯尼卡美能达 三维扫描仪属于非接触式光学扫描仪,物体表面明暗 程度会影响扫描数据的质量,另外要获得物体表面完 整的数据,需多方位扫描[]。
所以扫描前处理主要是 表面处理、贴标记点。
《逆向工程及快速成型技术》课程标准

《逆向工程与快速成型技术》课程标准一、基本信息1.课程地位:逆向工程与快速成型技术是“模具设计与制造专业”的一门专业选修课程,通过本课程学习,学生应掌握逆向工程的基本概念和技术体系,了解学科发展趋势;掌握面向实物样件的数字化、数据处理、模型重建与评价的基本理论与技术;培养学生建立面向机电产品的逆向工程方法论,初步掌握一种支持逆向工程的应用软件工具。
2.课程任务:本课程教学任务是使学生认识逆向工程与正向设计的关系,掌握逆向工程的设计思路;掌握几种快速原型制造工艺,具备面向实物样件的数字化、数据处理、模型重建与评价的基本理论与技术的能力。
3.课程衔接:《数控加工工艺与编程》、《UG设计基础》、《CAD制图》、《三维扫描与逆向建模》等课程。
三、课程目标本课程目的是使学生掌握逆向工程的基本概念和技术体系,了解学科发展趋势;掌握面向实物样件的数字化、数据处理、模型重建与评价的基本理论与技术;培养学生建立面向机械产品的逆向工程方法论,初步掌握一种支持逆向工程的应用软件工具。
四、课程理念1.课程设计原则:围绕专业知识、能力与素质矩阵,根据本课程教学内容,结合后续课程及工程技术岗位的需要,优化课程教学内容,分解课程知识与能力模块,以实施理论与实践双融合教学为理念,借助课堂精讲(或精品课程平台、工厂实际操作视频),完成课程理论知识的教学,以实验设计和生产问题解决形式(课内训练、课外作业)实现动手能力训练。
通过“教、学、做、评一体化”完成该课程教学。
2.课程内容结构:(1)课程项目学习安排:课内以项目讨论学习为主,过课堂教学和应用实践等多个环节,使学生掌握快速成型与快速制模的理论原理、技术方法和工程应用,为今后从事相关领域的科学技术研究,解决工程实际问题奠定坚实的基础。
通过实验,了解逆向工程中原始数据的采集方法和应注意的问题;掌握三维结构光扫描装置的基本操作和相关知识元;掌握Geomagic软件的基本操作。
了解快速成型的原理及其与传统加工工艺的区别;了解不同快速成型方式的优点、缺陷和应用范围。
反求工程在快速成型技术中的应用
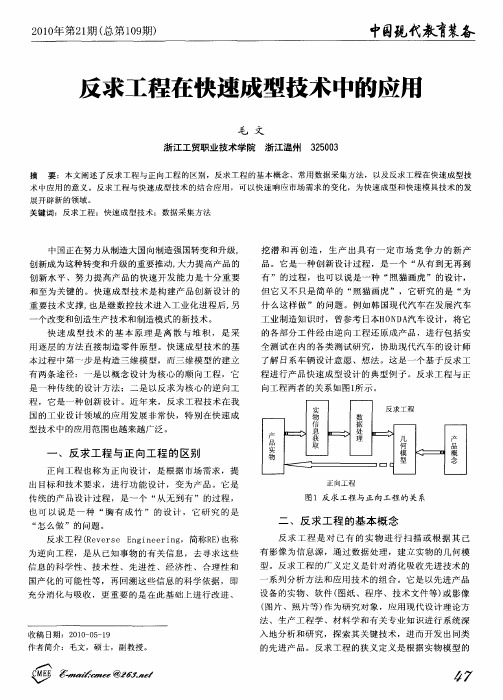
程 ,它 是 一 种 创 新 设 计 。 近 年 来 ,反 求 工 程 技 术 在 我 国 的 工业 设计 领 域 的应 用 发展 非 常快 ,特 别 在 快速 成
型 技术 中的应 用 范 围 也越 来 越 广 泛 。
一
、
反 求 工 程 与 正 向工 程 的 区别
正 向工 程
正 向工 程 也 称 为 正 向设 计 ,是 根 据 市 场 需 求 ,提 出 目标 和 技 术 要 求 ,进 行 功 能 设 计 ,变 为产 品 。它 是 传 统 的产 品设 计 过 程 ,是 一 个 “ 无 到有 ” 的过 程 , 从
描 臂 的硬 探 头和 3 激 光 扫 描 头 能 交 替进 行 数 字化 处 理 D
而 无 需 拆 下任 何 部 件 。用 户 可 以用 扫 描 臂 的硬 探 头 采
集简单点变化 。然后将 需要较大量数据 的( 每秒10 0 30
个 点 以上 ) 域 进 行 数 字 化 处理 就 可输 出 数 据一 不 用 区
一
挖 潜 和 再 创 造 , 生 产 出 具 有 一 定 市 场 竞 争 力 的 新 产 品 。它 是 一 种 创 新 设 计 过 程 , 是 一 个 “ 从有 到无 再 到 有 ” 的过 程 ,也 可 以说 是 一 种 “ 猫 画 虎 ”的 设计 , 照 但 它 又 不 只 是 简 单 的 “ 猫 画 虎 ” ,它 研 究 的 是 “ 照 为 什 么 这 样 做 ”的 问 题 。例 如 韩 国 现 代 汽 车 在发 展 汽 车 工 业 制 造 知 识 时 , 曾参 考 日本 H N A 车 设计 ,将 它 O D汽
也 可 以 说 是 ~ 种 “胸 有 成 竹 ” 的 设 计 , 它 研 究 的 是 “ 么做 ”的 问题 。 怎 反求 工程 ( e e s E g n e i g R v r e n i e r n ,简 称 R ) 称 E也 图1反 求 工程 与 正向 工程 的 关系
逆向工程与快速成型技术应用试题答案

1.适合大尺寸零件快速成型制造的是:(5.0分)A.熔积成型FDMB.光固化成型SLAC.激光选区烧结成型SLSD.分层实体制造成型LOM我的答案:D √答对2.快速成型技术在新产品开发中的主要用途不包括(5.0分)A.设计模型可视化及设计评价B.零部件修补C.功能验证D.装配校核我的答案:B √答对3.下列快速成型制造工艺中,通常制造成本最高的是:(5.0分)A.熔积成型FDMB.光固化成型SLAC.激光选区烧结成型SLSD.分层实体制造成型LOM我的答案:D ×答错4.下列说法正确的是:(5.0分)A.反求思维在工程中的应用是近几年开始的B.专业分工越来越粗略促成了逆向工程技术的发展C.逆向工程是解决产品如何做得更多的最好途径D.逆向工程是对引进产品进行改进、创新,目的是开发出符合我国国情的先进产品我的答案:A √答对5.1. 曲面的连续性主要有三种形式:G0连续、G1连续与G2连续。
G1连续指的是(5.0分)A.两个曲面桥接相连或者位置连续B.两个曲面相切连续C.两个曲面曲率连续D.两个曲面法向连续我的答案:D ×答错6.2. 不属于专业逆向工程设计的软件是:(5.0分)A.ImagewareB.AutoCADC.Geomagic DesignXD.Copy CAD我的答案:B √答对7.运用分离的方法,把一部分材料有序地从基体上分离出去的成型方法是:(5.0分)A.去除成形B.受迫成形C.堆积成形D.生长成形我的答案:A √答对8.与接触式测头相比,非接触式测头更适用于测量:(5.0分)A.较窄较深的槽壁平面度B.空间棱柱式物体C.复杂未知曲面形状的零件形貌D.仅要求提供规则尺寸测量结果的零件我的答案:C √答对9.关于正向工程说法错误的是:(5.0分)A.设计完成后设计信息无法用参数精确描述B.从构思到数字模型,再到产品(实物)的演化过程C.是对产品实物进行测量和工程分析的过程D.通常是一个“从有到无”的过程我的答案:A ×答错10.下面关于快速成型技术产生背景错误说法是:(5.0分)A.计算机、CAD、材料、激光技术的发展推动了快速成型技术的产生B.快速成型技术于20世纪80年代后期产生于德国C.快速成型技术将CAD/CAM集成于一体,构建三维模型D.快速成型技术改善了人机交流,缩短了开发周期,降低了新产品开发的风险我的答案:B √答对1.1. Geomagic软件的主要功能包括(5.0分))A.自动将点云数据转换为多边形B.快速减少多边形数目C.把多边形转换为曲面D.曲面的公差等分析我的答案:ABC ×答错2.三坐标测量机测量前的准备包括:(5.0分))A.校准探针B.工件找正C.测量机械手臂的调整D.工件表面喷显影剂我的答案:ABC ×答错3.三角网格化模型的特点是:(5.0分))A.模型简单B.能够表示测点的邻接关系C.可以直接用于3D打印D.生成的三角网格应该保证二维流形我的答案:ABCD √答对4.测量过程中因为贴定位片、遮挡等原因导致部分数据测量不完整的解决方案是(5.0分))A.重新测量B.软件中修补C.用游标卡尺量出定位片的长度与宽度D.调整测量环境中的光源照射方向我的答案:CD ×答错5.数字化测量所获取的点云数据类型包括:(5.0分))A.散乱“点云”B.扫描线“点云”C.栅格“点云”D.多边形“点云”我的答案:ABCD √答对1.逆向工程不是简单地将原有物体还原,它是在还原的基础上进行二次创新(5.0分)我的答案:正确√答对2.快速成型技术是将复杂的三维型体转化为二维截面进而完成快速成型制造。
基于逆向工程与快速成型技术的产品设计
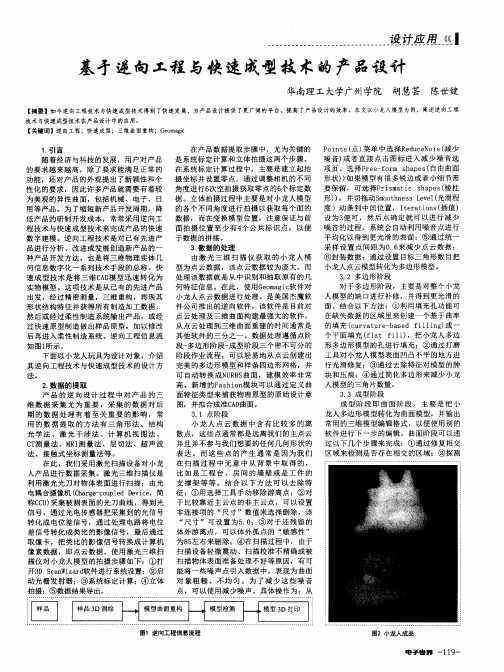
1 . 引 言
随着 经济 与 科 技 的发 展 ,用户 对 产 品 的 要求 越 来越 高 , 除 了要 求能 满足 出 了新颖 性 和个 性 化 的要 求 , 因此许 多 产 品就 需要 有 着较 为 美观 的异性 曲面 ,包 括 机械 、电子 、 日
在 产 品 数据 提 取步 骤 中 ,尤为 关键 的 是 系统 标 定计 算 和立 体 拍摄 这 两个 步 骤 。 在 系 统标 定计 算 过程 中 ,主 要 是 建立 起 拍 摄 坐标 并 设置 零 点 ,通 过调 整 相机 的不 同 角 度进 行 6 次空 拍摄 获取 零 点 的6 个 标 定 数
出发 ,经过 精 密测 量 ,三 维 重 构 ,再现 其 小 龙人 点 云数 据进 行 处 理 。是美 国杰魔 软 人模 型 的缺 口进 行 补 修 ,并得 到 更光 滑 的 件 公司 推 出 的逆 向软 件 ,该 软件 是 目前对 面 。结 合 以下 方法 :① 利 用填 充 孔功 能 可 形状 结 构特 征 并获 得 所有 制 造 加工 数据 , 在缺 失 数据 的区域 里 来创 建一 个 基于 曲率 然 后 或 经 过柔 性制 造 系 统输 出产 品 ,或 经 点 云处 理及 三 维 曲面 构 建最 强 大 的软件 , c u r v a t u r e — b a s e d f i U i n g ) 或 一 过快 速 原 型制 造做 出样 品原 型 ,加 以修 改 从 点云 处 理 到三 维 曲面 重建 的时 间通 常是 的填充 ( f l a t f i l 1 ) ,把 小 龙人 多 边 后 再进 入 柔性 制造 系 统 。逆 向工程 信 息流 其 他软 件 的三 分 之一 。数据 处 理遵 循 点阶 个 平 面填 充 ( 如 图1 所示 。 段一 多 边形 阶 段一 成 型阶 段三 个 密 不可 分 的 形 多边 形 模型 的 孔进 行填 充 ;② 通过 打 磨 工 具对 小 龙人 模 型表 面 凹 凸不平 的地 方 进 下面 以小龙 人玩 具 为设 计 对 象 ,介绍 阶 段作 业 流程 ,可 以轻 易地 从 点 云创 建 出
逆向工程、快速成型技术介绍

产品快速数字化设计技术——逆向工程技术(RE)
逆向工程技术应用领域
汽 车 、 摩 托 车 制 造
逆向工程技术应用领域
汽 车 、 摩 托 车 制 造
逆向工程技术应用领域
新 型 汽 车 设 计 概 念 型 产 品 ) (
逆向工程技术应用领域
产 品 的 开 发 与 模 具 生 产 、 工 业 设 计
•装配、加 工、成形工艺 •标准化
•外观质量 •工艺性 •精度与配合
•规程化
反求CAD软件
产品快速数字化设计技术——逆向工程技术(RE) 复合式三坐标测量机 适用于常用工件的逆向数 据采集以及对“分模线” 等细小特征的接触式扫描
复合式三坐标:激光扫描
产品快速数字化设计技术——逆向工程技术(RE) 复合式三坐标测量机 接触式扫描方式:可以 弥补激光扫描方式无法 扫描的“分模线”和“死 角” 的缺陷
点云、曲面数据 误差比较分析
分析结果
点云处理优化 (偏置、过滤、对齐 逆向曲面造型 公差、排序等) 快速原型 逆向CAD模型 数控编程 数字化仿型及模具
逆向工程技术
正向设计和逆向设计比较:
正向设计
产品功能描述
逆向设计
产品/实物/模型
产品概念设计
数据采集 反求CAD建模
CAD模型
抽象→CAD (艰难)
实物→CAD (容易)
产品快速数字化设计技术——逆向工程技术(RE) 技术优势 快速设计: 快速复制:从产品实物快速获取产品CAD模型 改良创新:在原有产品CAD模型上进行改良,实现快速二次开发 作为正向设计的有益补充,贯穿于整个产品的开发过程 提高创新能力的有效途径: 获取优秀产品信息
→
观察、剖析 →
关于“反求工程与快速成型一体化应用研究”的学习总结

关于“反求工程与快速成型一体化应用研究”的学习总结——机研0804 朱晓博(104972081074)快速成型技术(Rapid Prototyping&Manufacturing,RP&M)是20 世纪80 年代末期发展起来的一项先进制造技术, 它借助计算机、激光、精密传动、精密伺候等现代化手段, 将计算机辅助设计(CAD) 、计算机辅助制造(CAM) 、计算机数字控制(CNC) 集成于一体, 根据在计算机上构造的三维模型, 能在短时间内运用一定材料制造产品样品, 无需传统的机械加工机床和模具的一种添加成型技术[1]。
反求工程技术(Reverse Engineering, RE) 又称逆向工程技术, 是以产品及设备的实物、软件( 图样、程序及技术文件) 或影像(图片、照片)等作为研究对象, 反求出初始的设计意图。
简单说, 反求就是对存在的实物模型或零件进行测量并根据测量数据重构出实物的CAD 模型, 进而对实物进行分析、修改、检验和制造的过程。
这里所指的反求是实物反求。
反求工程是快速成型制造的重要数据来源之一, 将反求工程与快速成型技术相结合, 能够在已有样件或原型的基础上进行复仿制, 进行迅速评价、修改和产品的创新再设计, 并自动快速地将设计转化为具有相应结构和功能的原型产品或直接制造出零部件, 缩短新产品的设计和研制周期, 降低新产品的研制成本和风险, 从而快速响应市场需求, 提高企业竞争力。
作为一种处理难以用CAD 设计的零件模型以及表面形状极不规则的产品模型的最有利的土具, 可以实现零件的快速三维复制、CAD 建模和快速制造。
它与快速成型的结合形成了一个设计、制造、检测的快速设计制造闭合系统。
本文主要讨论反求工程和快速成型的一些技术, 并举出实例。
1 反求工程数据处理的主要内容1.1 数据处理构造CAD 几何模型前, 反求工程大致分三个阶段: 首先对已有三维实体模型进行数据采集(又称零件数字化) , 生成数据“点云”; 然后对数据“点云”进行滤波去噪处理, 去除点云数据中的“坏点”; 最后通过曲面构造技术对数据点云进行曲面拟合, 生成三维曲面模型。
逆向工程技术及其在模具设计制造中的应用分析
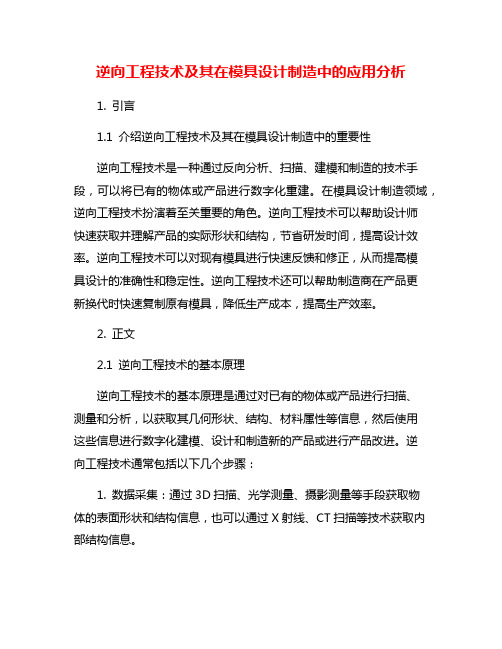
逆向工程技术及其在模具设计制造中的应用分析1. 引言1.1 介绍逆向工程技术及其在模具设计制造中的重要性逆向工程技术是一种通过反向分析、扫描、建模和制造的技术手段,可以将已有的物体或产品进行数字化重建。
在模具设计制造领域,逆向工程技术扮演着至关重要的角色。
逆向工程技术可以帮助设计师快速获取并理解产品的实际形状和结构,节省研发时间,提高设计效率。
逆向工程技术可以对现有模具进行快速反馈和修正,从而提高模具设计的准确性和稳定性。
逆向工程技术还可以帮助制造商在产品更新换代时快速复制原有模具,降低生产成本,提高生产效率。
2. 正文2.1 逆向工程技术的基本原理逆向工程技术的基本原理是通过对已有的物体或产品进行扫描、测量和分析,以获取其几何形状、结构、材料属性等信息,然后使用这些信息进行数字化建模、设计和制造新的产品或进行产品改进。
逆向工程技术通常包括以下几个步骤:1. 数据采集:通过3D扫描、光学测量、摄影测量等手段获取物体的表面形状和结构信息,也可以通过X射线、CT扫描等技术获取内部结构信息。
2. 数据处理:将采集到的数据进行处理和分析,包括数据清理、数据配准、建模等步骤。
通常需要使用CAD软件进行数据处理和建模。
3. 数字化建模:根据采集到的数据,进行三维数字化建模,生成几何模型、工程图纸等设计数据。
4. 设计与仿真:基于数字化建模数据进行产品设计、工艺设计、性能分析、模具设计等工作,可以使用CAD/CAM软件进行设计和仿真。
5. 制造与验证:基于数字化设计数据,进行数控加工、3D打印、快速成型等制造过程,然后进行产品验证和测试。
逆向工程技术的基本原理就是通过数据采集、处理、建模和制造来实现对现有产品的重建和改进,从而实现产品设计与制造的快速和灵活性。
逆向工程技术的发展对模具设计制造领域具有重要的意义和应用价值。
2.2 逆向工程技术在模具设计中的具体应用1. 借助逆向工程技术,可以快速获取现有模具的设计数据,包括尺寸、形状、结构等信息。
快速成型技术的应用与发展趋势

快速成型技术的应用及发展趋势摘要:;快速成型技术凭借其加工原理的独特性和相对传统加工时间的大大节省,在模具工业和修复医学方面得到了大力的推广和应用.同时也是一种结合计算机、数控、激光和材料技术于一体的先进制造技术,并提出快速成型技术未来的发展方向。
关键词:快速成型;快速模具;修复医学;成型方法;成型材料;引言快速成型(Rapid Prototyping,简称RP)是80年代末期开始商品化的一种高新制造技术,它是集CAD/CAM技术、激光加工技术、数控技术和新材料等技术领域的最新成果于一体的零件原型制造技术.快速成型不同于传统的用材料去除方式制造零件的方法,而是用材料一层一层积累的方式构造零件模型.它利用所要制造零件的三维CAD模型数据直接生成产品原型,并且可以方便地修改CAD模型后重新制造产品原型.由于该技术不像传统的零件制造方法需要制作木模、塑料模和陶瓷模等,可以把零件原型的制造时间减少为几天、几小时,大大缩短了产品开发周期,减少了开发成本.随着计算机技术的快速发展和三维CAD软件应用的不断推广,越来越多的产品基于三维CAD设计开发,使得快速成型技术的广泛应用成为可能.快速成形技术已广泛应用于宇航、航空、汽车、通讯、医疗、电子、家电、玩具、军事装备、工业造型(雕刻)、建筑模型、机械行业等领域[1]。
1.快速成型技术的应用1.1 工业产品开发及样件试制作为一种可视化的设计验证工具,RP具有独特的优势。
(1)在国外,快速原型即首版的制作,已成为供应商争取订单的有力工具。
美国Detroit的一家制造商,利用2台不同型号的快速成型机以及快速精铸技术,在接到№rd公司标书后的4个工作日内生产出了第一个功能样件,从而拿到了Ford公司年生产总值300万美元的发动机缸盖精铸件的合同。
(2)在RP系统中,一些使用特殊材料制作的原型(如光敏树脂等)可直接进行装配检验、模拟产品真实工作状况的部分功能试验。
Chrysler 直接利用RP技术制造的车体原型进行高速风洞流体动力学试验,节省成本达70%。
逆向工程与快速成型技术应用
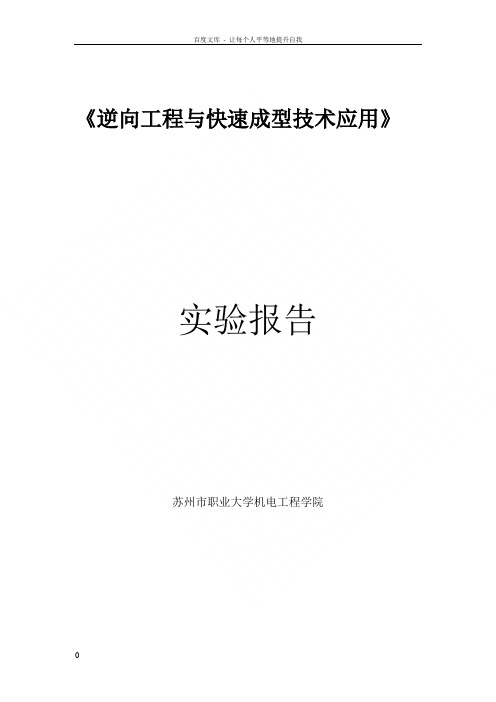
百度文库- 让每个人平等地提升自我《逆向工程与快速成型技术应用》实验报告苏州市职业大学机电工程学院实验名称三维数据扫描姓名:黄佳伟班级:12模具设计与制造3班日期:小组成员:黄佳伟蒋程飞解翔宇李长江刘凯李臻目录一.实验目的 (3)二.实验要求 (3)三.实验步骤及方法 (3)四.所需的设备、仪器、工具或材料 (3)五.思考题 (10)六.实验小结 (10)一、实验目的1. 掌握一种非接触光学测量设备三维扫描的方法2. 掌握Geomagic Studio 软件点阶段数据处理的方法,熟悉点阶段数据处理主要命令的使用。
二、实验要求完成实物的三维数据扫描及点阶段的数据处理,得到一个完整的多边形数据模型。
三、所需的设备、仪器、工具或材料1. 扫描件(学生自己准备)2. 柯尼卡美能达VIVID910 扫描仪3. Geomagic 逆向设计软件4. 电脑四、实验步骤及结果(一)数据的扫描Step1 扫描件的准备。
该扫描件反光效果较为合理,则不需要喷涂上显像剂;为了以后该数据拼合的方便与准确,应在被扫描件表面上做上点标记。
Step2 启动Konica Minolta VIVID 910三维扫描仪,再启动电脑,打开Geomagic Studio。
点击工具栏上的“插件”按钮出现图 1所示的对话框。
Step3 调整扫描仪与扫描件之间的距离与视角,保证扫描件在显像框的中心位置。
Step4 点击图1所示对话框中的Scan 按钮,开始扫描。
等待数秒后,显像框更新为图 2所示,根据出现的点的色谱,分析数据的质量,扫面图以颜色来表示距离,越红表示扫描仪与物体距离越近,越蓝则越远,图2中可以看出小猪存钱罐的额头距离扫描仪最近,四周部分距离较远。
图1图2物体扫描后的显像框Step5 点击图1所示对话框的“确定”按钮,完成一个视角的扫描。
Step6 将扫描物选择一个角度,重复步骤(4)(5),直至所有实体都被扫描到。
(二)数据的预处理物体扫描后的显像框Step 1 将扫描数据导入Geomagic Studio 软件,删除每片点云数据体外孤点。
逆向工程项目四 快速成型技术认知

缺点
1)成型件结构疏松、多孔,且有内应力, 制件易变形。
项目四 快速成型技术的认知
任务一 认识快速成型技术 任务二 了解快速成型的典型工艺 任务三 了解快速成型技术的应用
任务四 了解快速成型技术的发展趋势
任务一 认识快速成型技术
快速成型(Rapid Prototype,简称RP)又称快速原型 “增材制造”( additive manufacturing,AM) “材料累加制造”( material increse manufacturing) “分层制造”( layered manufacturing,LM) “实体自由制造”( solid free - form fabrication) “3D 打印”( 3D printing) 等
用 SLS成型的零件
在内腔 和孔未 烧结的 粉末作 为支撑 非常容 易移除
优点
1)可以采用多种材料(包括类工程塑料、 蜡、金属、陶瓷等)。
2)过程与零件复杂程度无关,制件的强度 高。
3)材料利用率高,未烧结的粉末可重复使 用,材料无浪费。
4)无需支撑结构。 5)与其他工艺相比,能生产较硬的模具。
二、 快速成型技术的原理
快速成型基于离散/堆积的思想, 将一个物理实体复杂的三维加工,离散 成一系列二维层片,然后逐点、逐面进行 材料的堆积成型。 是一种降维制造或者 称增材制造技术。
快速成型的过程
CAD模型
后处理
数据转换
STL模型
快速原型
模型分层
堆积成型 生成支撑和加工路径
快速成型包括了前处理、堆积成型、 后处理三个阶段
学性能。 4)可进行切削加工。 5)无需后固化处理。 6)无须设计和制作支撑结构。 7)废料易剥离。 8)可制作尺寸大的制件。 9)原材料价格便宜,原型制作成本低
逆向工程及快速成型技术的应用
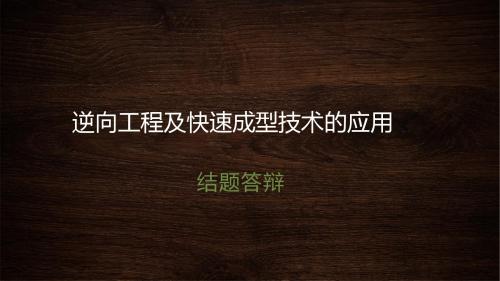
快速成型技术实验
步骤:
1、三维建模(solid 3、导入模型数据,新建打印任务
打印过程及结果预览
实验总结:
在本次课程中我了解到了关于逆向工 程和快速成型技术的发展概况,以及他 们的发展前景,拓宽了视野,学到了许 多在课堂上所学不到知识。课堂之外, 发现问题解决问题的能力得到锻炼,感 谢各位老师的悉心指导!
谢谢!
逆向工程及快速成型技术的应用
结题答辩
逆向工程
• 步骤
1、数据采集 2、数据处理实验中的处理结果
• 实验中的处理结果
逆向工程实验总结
• 数据采集阶段应当进行细致的扫描处理,未后期的点 云数据处理打下基础; • 后期合成阶段一方面是合成已有的数据,另一方面是 对一些无法合成的部位进行手动建模;
• 结合手动建模和采集到的点云数据合成,完美再现目 标物体的逆向建模。
逆向工程与快速成型技术的应用
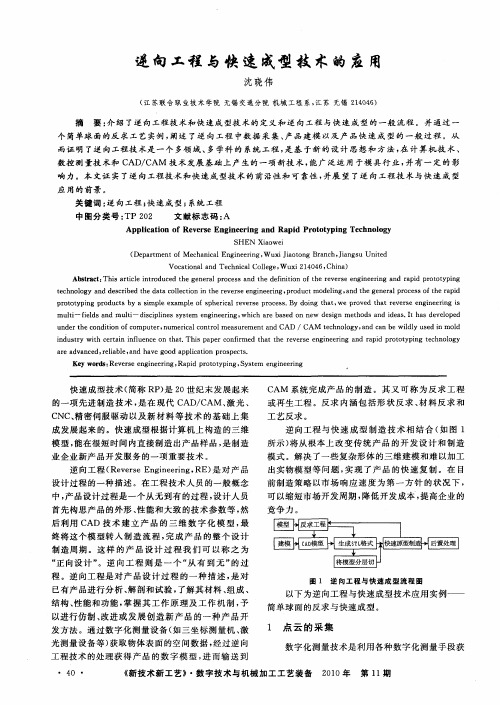
t c n l g n e c i e h a a c l c in i h e e s n i e rn p o u t e h o o y a d d s rb d t e d t o l t n t er v r ee g n e ig, r d c d l g, n h e e a r c s ft er p d e o mo e i a d t eg n r l o e so h a i n p p o o y i g p o u t y a smp e e a l fs h r a e e s r c s . y d i g t a , r v d t a e e s n i e r g i r t t pn r d c s b i l x mp e o p e i lr v r e p o e s B o n h t we p o e h t r v r e e g n e i s c n mu t f l s a d mu t— d s i l e y t m ቤተ መጻሕፍቲ ባይዱn i e rn , ih a e b s d o e d s n me h d n d a . th s d v l p d li i d n li icp i s s s e e g n e i g wh c r a e n n w e i t o s a d i e s I a e e o e — e n g
i d s r t e t i n l e c n t a . i a e o f me h t t e r v r e e g n e i g a d r p d p o o y i g t c n l g n u t y wi c r an i f n e o h t Th sp p r c n i d t a h e e s n i e rn n a i r t t p n e h o o y h u r
浅谈逆向工程与快速成型技术在机械制造领域中的应用——评《逆向工程与快速成型技术应用》

第53卷•第4期• 2020年4月浅谈逆向工程与快速成型技术在机械制造领域中的应用—评《逆向工程与快速成型技术应用》刘雯(四川航天职业技术学院,四川成都610100)随着计算机技术的快速发展,逆向工程技术为制造业提供了一个全新的产品开发方向;快速成型技术则改变了制造业的生产方式,两种技术的结合加速革新了传统制造业,虽然我国是世界的制造中心,但是技术的革新才是未来发展的必然之选,如何将传统的制造业往高精尖方向上引导,才是制造业的关键环节,其中机械制造行业备受关注,作为国家的支柱产业,不仅能提供技术装备,而且也是国 家工业化程度的标志。
由于逆向工程和快速成型技术是高新技术,能够熟练掌握、应用这些技术的人才缺口较大,进行这方面的培训和普及工作意义重大。
鉴于此,由陈雪华、孙春华主编的《逆向工程与快速成型技术应用》(机 械工业出版社,2014年8月版)立足于当下,现状分析客观准确,详细地探讨了逆向工程与快速成型技术在机械制 造领域的应用。
总览此书,具有以下特色。
1结构编排合理,逻辑性强写作思路清晰、内容结构层次分明、逻辑性强是本书的一大亮点。
首先,该书将逆向工程作为本书的开端,详 细地论述了逆向工程技术的工作原理、流程、应用领域,同时探讨了逆向工程与创新设计间的关系;其次,详细介绍 了快速成型技术的核心及与传统机械加工的区别;最后,作者将逆向工程与快速成型技术构建成集成系统,为实际 的应用要求提供了柔性和实用的解决方法。
具体而言,本书共为7个章节,可划分为3部分。
第一部分(第1、2、3 章),主要向大家解释了何为逆向工程技术,详细阐述了相关的数据测量与处理工艺、模型的重构,通过“认识原型 -再现原型-超越原型”的过程,剖析了逆向工程与创新设计的关系;第二部分(第4、5、6章),在介绍快速成型技术 的原理、应用、工艺特点基础上,探究了快速成型技术现状及发展趋势;第三部分(第7章),介绍了集成逆向工程系 统的框架和实现方法。
- 1、下载文档前请自行甄别文档内容的完整性,平台不提供额外的编辑、内容补充、找答案等附加服务。
- 2、"仅部分预览"的文档,不可在线预览部分如存在完整性等问题,可反馈申请退款(可完整预览的文档不适用该条件!)。
- 3、如文档侵犯您的权益,请联系客服反馈,我们会尽快为您处理(人工客服工作时间:9:00-18:30)。
基于逆向工程的快速成型技术应用探讨
作者:机电学院工业设计雾蒙蒙
【摘要】本文主要介绍了逆向工程的快速成型技术应用流程,并重点对导流罩作为实物原形,分析了快速成型技术及快速制模在逆向工程中的应用,以及零件快速成型和模具加工制造等关键技术的研究与探讨。
【关键词】逆向工程导流罩模具加工制造质量评析
逆向工程是对产品设计过程的一种描述。
在工程技术人员的一般概念中,产品设计过程是一个从设计到产品的过程,即设计人员首先在大脑中构思产品的外形、性能和大致的技术参数等,然后在详细设计阶段完成各类数据模型,最终将这个模型转入到研发流程中,完成产品的整个设计研发周期。
这样的产品设计过程我们称为“正向设计”过程。
逆向工程产品设计可以认为是一个从产品到设计的过程。
简单地说,逆向工程产品设计就是根据已经存在的产品,反向推出产品设计数据(包括各类设计图或数据模型)的过程。
从这个意义上说,逆向工程在工业设计中的应用已经很久了。
比如早期的船舶工业中常用的船体放样设计就是逆向工程的很好实例。
随着计算机技术在各个领域的广泛应用,特别是软件开发技术的迅猛发展,基于某个软件,以反汇编阅读源码的方式去推断其数据结构、体系结构和程序设计信息成为软件逆向工程技术关注的主要对象。
软件逆向技术的目的是用
来研究和学习先进的技术,特别是当手里没有合适的文档资料,而你又很需要实现某个软件的功能的时候。
也正因为这样,很多软件为了垄断技术,在软件安装之前,要求用户同意不去逆向研究。
逆向工程的实施过程是多领域、多学科的协同过程。
本文以导流罩作为实物原形,分析了快速成型技术及快速制模在逆向工程中的应用。
该项技术大大缩短了新产品的开发和上市周期,实现了产品质量和实际效益的双提高。
逆向工程又称为反求工程,通常用于仿制没有设计图样文件的产品,是对存在的实物模型进行测量,并根据测得的数据重构出数据模型,从而进行分析、修改、检验、加工,然后制造出产品的过程。
传统设计和制造是从图样到零件,而逆向工程的设计是从零件或实物原形到图样。
在产品开发过程中,由于形状复杂,其中包含许多空间曲面很难直接建立数据模型,常常需要以实物模型(样件)为依据或参考原型进行仿型、改型或造型设计。
导流罩是具有复杂空间曲面的对称配合塑料零件,其材质为ABS。
由于零件没有图样和数据模型,同时需要检验对称两个零件的配合情况是否满足使用要求,以及产品设计合格后需要进行模具的设计制造和零件的批量生产。
在只有零件的一个样件的情况下,采用逆向工程的思路,应用快速成型技术及快速制模技术修整零件模型,在零件的形状、尺寸确定之后进行模具的设计制造,再利用模具进行零件的批量生产。
一、零件快速成型
快速成型(RP)技术是20世纪90年代发展起来的一项先进制造技术。
是为制造业企业新产品开发服务的一项关键共性技术,它对促进企业产品创新、缩短新产品开发周期、提高产品竞争力有积极的推动作用。
自该技术问世以来,已经在制造业中得到了广泛应用,并由此产生一个新兴的技术领域。
快速成型(RP)技术是在现代CAD/CAM技术、激光技术、计算机数控技术、精密伺服驱动技术以及新材料技术的基础上集成发展起来的,不同种类的快速成型系统因所用成形材料不同,成形原理和系统特点也各有不同。
但是,其基本原理都是一样的,那就是“分层制造,逐层叠加”。
形象地讲,快速成形系统就像是一台“立体打印机”。
快速成型(RP)技术可以在无需准备任何模具、刀具和工装夹具的情况下,直接接受产品设计(CAD)数模的数据,快速制造出新产品的样件、模具或模型等,由传统的“去除法”到“增长法”,由有模制造到无模制造,快速直接地实现零件的单件生产。
每次制作一个具有一定微小厚度和特定形状的截面,然后再把它们逐层粘结起来,就得到了所需制造的立体零件,整个过程是在计算机的控制下,由快速成型系统自动完成。
这种工艺可以形象地叫做“增长法”或“加法”。
自美国3D公司1988年推出第一台商品SLA快速成型机以来,现在已经有了十几种不同的成形系统,其中比较成熟的有SLA、SLS、LOH和FDH等方法。
快速成型(RP)技术具有制造复杂零件的能力、提高新产品投产的一次成功率、支持同步(并行)工程的实施、支持技术创新并改进产品外观设计以及成倍降低新产品研发成本等优点,可迅速实现单件及小批量生
产,使新产品上市时间大大提前,迅速占领市场。
利用Z—Printer 310快速成型机对零件进行快速成型,快速成型系统操作过程体现了快速成型的特点,通过分层制造、逐层叠加的过程,快速成型系统自动将零件的高度尺寸分成若干层,每一层叠加的厚度为0.01mm,经过分层制造成零件的实物;通过两个对称零件的组合装配,进行零件的实际使用实验:通过使用实物发现其局部形状尺寸的配合存在一些问题,之后对零件的三维数据模型进行修整,确定最终的产品零件模型。
二、模具加工制造
根据最终确定的产品零件模型,进行模具的设计及加工制造,利用三维加工软件对模具的阴模和阳模进行模拟加工,生成NC程序,进行数控加工。
模具满足工作条件要求:
1、耐磨性坯料在模具型腔中塑性变性时,沿型腔表面既流动又滑动,使型腔表面与坯料间产生剧烈的摩擦,从而导致模具因磨损而失效。
模具零件的硬度越高,磨损量越小,耐磨性也越好。
另外,耐磨性还与材料中碳化物的种类、数量、形态、大小及分布有关。
2、强韧性:模具的工作条件大多十分恶劣,有些常承受较大的冲击负荷,从而导致脆性断裂。
为防止模具零件在工作时突然脆断,模具要具有较高的强度和韧性。
模具的韧性主要取决于材料的含碳量、晶粒度及组织状态。
3、疲劳断裂性能:模具工作过程中,在循环应力的长期作用下,往往导致疲劳断裂。
其形式有小能量多次冲击疲劳断裂、拉伸疲劳断裂接触疲劳断裂及弯曲疲劳断裂。
模具的疲劳断裂性能主要取决于其强度、韧性、硬度、以及材料中夹杂物的含量。
4、高温性能:当模具的工作温度较高进,会使硬度和强度下降,导致模具早期磨损或产生塑性变形而失效。
因此,模具材料应具有较高的抗回火稳定性,以保证模具在工作温度下有较高的硬度和强度。
5、耐冷热疲劳性能:有些模具在工作过程中处于反复加热和冷却的状态,使型腔表面受拉、压力变应力的作用,引起表面龟裂和剥落,增大摩擦力,阻碍塑性变形,降低了尺寸精度,从而导致模具失效。
冷热疲劳是热作模具失效的主要形式之一,帮这类模具应具有较高的耐冷热疲劳性能。
6、耐蚀性:有些模具如塑料模在工作时,由于塑料中存在氯、氟等元素,受热后分解析出HCI、HF等强侵蚀性气体,侵蚀模具型腔表面,加大其表面粗糙度,加剧磨损失效。
模具的制造一般都要经过锻造、切削加工、热处理等几道工序。
为保证模具的制造质量,降低生产成本,其材料应具有良好的可锻性、切削加工性、淬硬性、淬透性及可磨削性;还应具有小的氧化、脱碳敏感性和淬火变形开裂倾向。
最后将模具组装,进行零件的正式批量生产。
三、结束语
逆向工程与一般的设计制造过程相反,是先有实物后有模型。
仿形加工就是一种典型的逆向工程应用。
目前,逆向工程的应用已从单纯的技巧性手工操作,发展到采用先进的计算机及测量设备,进行设计、分析、制造等活动,如获取修模后的模具形状、分析实物模型、基于现有产品的创新设计、快速仿形制造等。
软件的逆向工程是分析程序,力图在比源代码更高抽象层次上建立程序的表示过程,逆向工程是设计的恢复过程。
逆向工程工具可以从已存在的程序中抽取数据结构、体系结构和程序设计信息。
本文基于逆向工程技术,以先进的软件平台,通过对导流罩零件进行激光扫描、点云的处理、建模、快速成型、修整数模和生成NC 程序等过程,对导流罩模具的阴模和阳模进行数控加工,实现了CAD/CAM无缝连接以及基于逆向工程的快速成型技术的实际应用,从而为笔者积累了相关技术应用经验,也为企业解决了难题,实现了产品质量和实际效益的双提高。