发电厂直流炉300MW机组化学柠檬酸+氨基磺酸清洗技术方案
氨基磺酸在发电厂板式换热器化学清洗中的应用

表1 序号
作开展前应当加强相关人员的培训工作,并重视宣传,相关技术负责人应当编制应急预案及操作措施,以避免在清洗过程中出现意外事故。
化学清洗工艺及步骤
化学清洗流程
经拆卸板式换热器的换热版检查后,换热板冷端结垢严重,热端无结垢现象,因此本次化学清洗的范围主要是换热器的冷端。
清洗方法采用单回路统。
为了保证本次板式换热器的化学清洗工作顺利的进行,清洗系统的构架选在宽阔、平坦场地,能够确保清洗系统补水及加热的问题,同时也能够确保场地位置便于废水收集及运输。
清洗系统安装完毕后,应对清洗系统内的转动设备、电气设备、阀门及清洗水箱挂临时设备铭牌,清洗系统外围应设置围栏,挂警示牌,禁止无相关人员出入。
化学清洗所需要的化学药品及分析仪器应当就位,加药操作人员所需要的安全防护具准备完
图2 板式换热器化学清洗流程
0.3MPa
水排掉,并清理清洗水箱,用除盐水将清洗水箱注
图4 板式换热器清洗前
图5 板式换热器清洗后
的化学药品,避开了因战争而导致的限制运输及使用问题,能够有效的解决战乱地区板式换热器的化11 图12
图9 图10
(上接第12页)。
发电厂直流炉300MW机组化学柠檬酸+氨基磺酸清洗技术方案

目录1.概述 32.化学清洗范围及清洗系统 33.化学清洗工艺 54.化学清洗前临时系统的安装、系统检查及清洗系统应具备的条件75.化学清洗工艺过程及其控制106.清洗质量技术标准127.安全措施128.化学清洗组织措施及分工原则139.化学清洗设备、药品及水量估算1410.工期1611.化学清洗系统图16 1.概述黄埔电厂#5炉为上海锅炉厂生产的SG-1025/16.7-M313UP型直流燃煤锅炉,已经成功运行多年。
由于水质对锅炉运行造成的影响,日积月累在锅炉汽水系统部位形成了一层致密的水垢,达到了再次清洗的时限,并且经割管检测,水冷壁腐蚀严重,有很多很明显的裂痕,且垢最里层有单质铜(≥3%)沉积覆盖,针对如此实际情况,并根据DL/T794-2001《火力发电厂锅炉化学清洗导则》规定,对#5炉汽水系统采用柠檬酸+氨基磺酸清洗及氨洗除铜工艺,在不损害机组设备的前提下清除汽水系统所有的水垢,从而保证机组的安全运行。
锅炉主要参数如下:锅炉蒸发量1025t/h过热器出口蒸汽压力16.72MPa过热蒸汽温度540℃再热蒸汽压力 3.54/3.32MPa(绝对)再热蒸汽温度320/540℃给水压力21.36MPa给水温度265.4℃预热器热风温度333.9℃锅炉排烟温度130.68℃2.化学清洗范围及清洗工艺2.1.化学清洗范围高压给水管道、省煤器、水冷壁、炉顶过热器、包覆管、低温过热器、前屏过热器、后屏过热器、高温过热器、主蒸汽母管和启动分离器(包括内部装置)及有关联箱,包括临时系统,总的水容积约为200m3。
2.2.化学清洗工艺要点由于被清洗的材质有20A、15CrMo、12Cr1MoV、SA213、TP-304H、TP-347H、St45、8Ⅲ、13CrMo44和10CrMo910等碳素钢、合金钢和奥氏体钢,被清洗材质表面腐蚀严重,垢中铜含量较大,以及过热器内垢清洗难等因素,故本次化学清洗采用复合柠檬酸+氨基磺酸酸洗工艺,添加缓蚀剂、消泡剂、还原剂等清洗助剂,酸洗后采用氨洗除铜,然后采用柠檬酸漂洗及联胺钝化。
柠檬酸酸洗方案要点
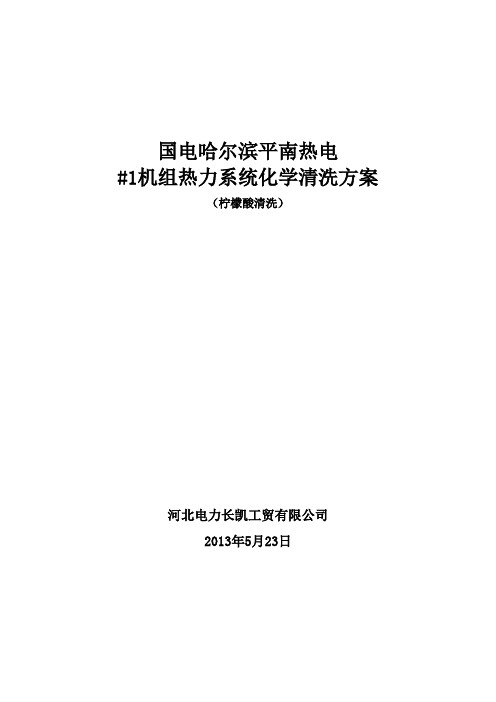
国电哈尔滨平南热电#1机组热力系统化学清洗方案(柠檬酸清洗)河北电力长凯工贸有限公司2013年5月23日目录1 清洗目的2 编制依据3 系统设备简介4 清洗范围及清洗工艺5 清洗系统安装应完成的工作6 清洗前应具备的条件7 清洗用药品及水量等估算8 清洗过程及化学监督9 清洗废液的处理10 清洗后的检查与评定11 组织分工12 安全注意事项附清洗系统图1 清洗目的除去新建锅炉在轧制、加工过程中形成的高温氧化轧皮以及在存放、运输、安装过程中所产生的腐蚀产物、油污、焊渣和泥沙等污染物,并形成良好的钝化保护膜,保持热力设备内表面清洁,提高热力系统水汽品质,防止受热面因结垢、腐蚀引起事故,保证机组顺利启动和安全、经济运行。
2 编制依据2.1 《火力发电厂锅炉化学清洗导则》( DL/T 794−2012)。
2.2 《火电工程启动调试工作规定》(1996 年)。
2.3 《电力建设施工及验收技术规范》火力发电厂锅炉篇(1996 年版)、管道篇(1994 年版)、化学篇(2002 年版)。
2.4 《火力发电厂基本建设工程启动及竣工验收规程(1996 年版)及相关规程》。
2.5 《火电工程调整试运质量检验及评定标准》(1996 年)。
2.6 《电力建设安全工作规程》(第1 部分:火力发电厂2002 年)。
2.7 《电力建设安全健康与环境管理工作规定》(2002 年)。
2.8 设备厂家、设计院等有关资料。
3 系统设备简介国电哈尔滨平南热电厂2×350MW机组锅炉是哈尔滨锅炉有限责任公司自主研发技术的超临界锅炉,型号HG-1110/25.4-HM2,锅炉是采用单炉膛、一次中间再热、平衡通风、固态排渣、全钢结构的直流锅炉。
锅炉采用全钢结构构架,高强螺栓连接,受热面呈“П”型布置方式,炉膛上部分隔屏、后屏过热器。
水平烟道中布置有末级再热器、末级过热器;后烟道有中间隔墙,竖井前部布置水平低温再热器、立式低温再热器,竖井后部布置水平低温过热器、立式低温过热器和省煤器。
新疆某电厂锅炉化学酸洗方案
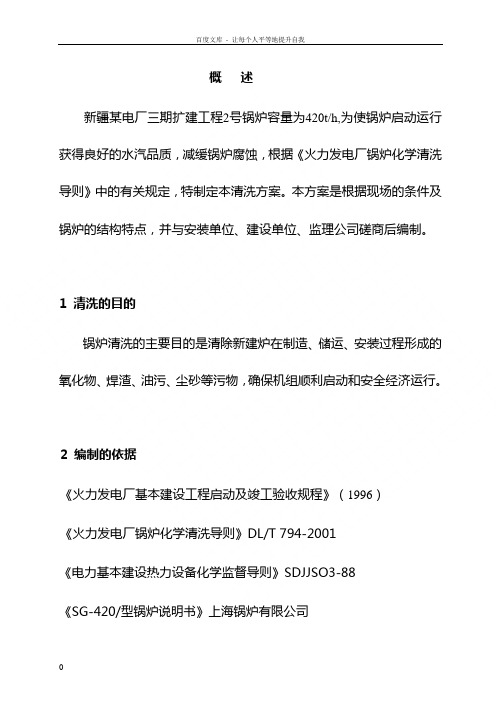
概述新疆某电厂三期扩建工程2号锅炉容量为420t/h,为使锅炉启动运行获得良好的水汽品质,减缓锅炉腐蚀,根据《火力发电厂锅炉化学清洗导则》中的有关规定,特制定本清洗方案。
本方案是根据现场的条件及锅炉的结构特点,并与安装单位、建设单位、监理公司磋商后编制。
1 清洗的目的锅炉清洗的主要目的是清除新建炉在制造、储运、安装过程形成的氧化物、焊渣、油污、尘砂等污物,确保机组顺利启动和安全经济运行。
2 编制的依据《火力发电厂基本建设工程启动及竣工验收规程》(1996)《火力发电厂锅炉化学清洗导则》DL/T 794-2001《电力基本建设热力设备化学监督导则》SDJJSO3-88《SG-420/型锅炉说明书》上海锅炉有限公司3 清洗范围及系统划分清洗范围主要包括水冷壁、省煤器、汽包(一半)及下降管。
根据酸洗导则的要求,对过热器系统不进行化学清洗,仅在锅炉整体水压试验时以除盐水加联氨200-300mg/L,氨水调pH至进行保护。
清洗系统的划分为了保证化学清洗范围内清洗效果尽可能一致,清洗流速控制在0.2m/s-0.5m/s的范围内,采用以下几个循环回路:1)省煤器→汽包→四周水冷壁2)1号+2号集中下降管→汽包→3号+4号集中下降管3)省煤器+3号+4号集中下降管→汽包→1号+2号集中下降管(集中下降管无酸洗接口时可与对应的联箱封头处连接)4 组织与分工化学清洗整个工作应在工程指挥部统一安排下进行,并成立由建设单位、安装公司、监理公司、调试所等单位组成的工作小组。
组长: 安装公司负责人;副组长:由调试所、建设单位、监理公司各指定一人。
现对具体分工做如下说明,以便做好清洗中的各项工作。
安装单位的职责4.1.1 临时系统的安装、冲洗、水压、升温试验。
4.1.2 清洗期间的检修及设备维护工作。
4.1.3 电源、照明、电话、液位讯号的安装和检修。
4.1.4 临时化验室、清洗平台防雨棚的搭设及电源、照明的安装。
4.1.5 清洗药品的运送和及时加入。
锅炉化学清洗柠檬酸作业指导书
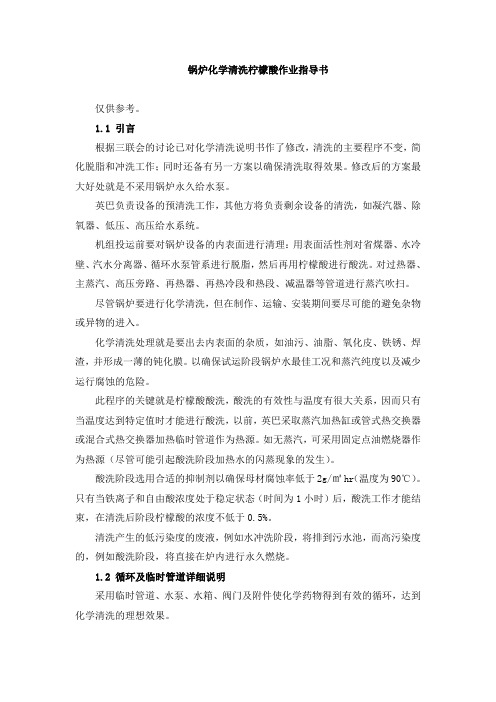
锅炉化学清洗柠檬酸作业指导书仅供参考。
1.1 引言根据三联会的讨论已对化学清洗说明书作了修改,清洗的主要程序不变,简化脱脂和冲洗工作;同时还备有另一方案以确保清洗取得效果。
修改后的方案最大好处就是不采用锅炉永久给水泵。
英巴负责设备的预清洗工作,其他方将负责剩余设备的清洗,如凝汽器、除氧器、低压、高压给水系统。
机组投运前要对锅炉设备的内表面进行清理:用表面活性剂对省煤器、水冷壁、汽水分离器、循环水泵管系进行脱脂,然后再用柠檬酸进行酸洗。
对过热器、主蒸汽、高压旁路、再热器、再热冷段和热段、减温器等管道进行蒸汽吹扫。
尽管锅炉要进行化学清洗,但在制作、运输、安装期间要尽可能的避免杂物或异物的进入。
化学清洗处理就是要出去内表面的杂质,如油污、油脂、氧化皮、铁锈、焊渣,并形成一薄的钝化膜。
以确保试运阶段锅炉水最佳工况和蒸汽纯度以及减少运行腐蚀的危险。
此程序的关键就是柠檬酸酸洗,酸洗的有效性与温度有很大关系,因而只有当温度达到特定值时才能进行酸洗,以前,英巴采取蒸汽加热缸或管式热交换器或混合式热交换器加热临时管道作为热源。
如无蒸汽,可采用固定点油燃烧器作为热源(尽管可能引起酸洗阶段加热水的闪蒸现象的发生)。
酸洗阶段选用合适的抑制剂以确保母材腐蚀率低于2g/㎡hr(温度为90℃)。
只有当铁离子和自由酸浓度处于稳定状态(时间为1小时)后,酸洗工作才能结束,在清洗后阶段柠檬酸的浓度不低于0.5%。
清洗产生的低污染度的废液,例如水冲洗阶段,将排到污水池,而高污染度的,例如酸洗阶段,将直接在炉内进行永久燃烧。
1.2 循环及临时管道详细说明采用临时管道、水泵、水箱、阀门及附件使化学药物得到有效的循环,达到化学清洗的理想效果。
1.2.1 化学加药管为临时化学加药装置和临时循环水泵管间的管道1.2.2 启动循环水泵回路为临时循环水泵和废液池间的回路,包括循环水泵接头、临时水泵(共2个,一个备用)、阀门及附件。
1.2.3 废液焚烧系统,包括水泵、喷头、阀门及附件1.2.4 阀门阀门≤100nb为膜式,100nb≤阀门≤200nb为门阀,阀门>200nb的为蝶阀(用于调节)或门阀(用于密封)1.2.5 分离器容器装有一临时水位计(塑料透明管)1.2.6 过热器反向上水过热器反向上水/冲洗采用临时水泵,包括管道、阀门及附件。
柠檬酸酸洗方案.

国电哈尔滨平南热电#1机组热力系统化学清洗方案(柠檬酸清洗)河北电力长凯工贸有限公司2013年5月23日目录1 清洗目的2 编制依据3 系统设备简介4 清洗范围及清洗工艺5 清洗系统安装应完成的工作6 清洗前应具备的条件7 清洗用药品及水量等估算8 清洗过程及化学监督9 清洗废液的处理10 清洗后的检查与评定11 组织分工12 安全注意事项附清洗系统图1 清洗目的除去新建锅炉在轧制、加工过程中形成的高温氧化轧皮以及在存放、运输、安装过程中所产生的腐蚀产物、油污、焊渣和泥沙等污染物,并形成良好的钝化保护膜,保持热力设备内表面清洁,提高热力系统水汽品质,防止受热面因结垢、腐蚀引起事故,保证机组顺利启动和安全、经济运行。
2 编制依据2.1 《火力发电厂锅炉化学清洗导则》( DL/T 794−2012)。
2.2 《火电工程启动调试工作规定》(1996 年)。
2.3 《电力建设施工及验收技术规范》火力发电厂锅炉篇(1996 年版)、管道篇(1994 年版)、化学篇(2002 年版)。
2.4 《火力发电厂基本建设工程启动及竣工验收规程(1996 年版)及相关规程》。
2.5 《火电工程调整试运质量检验及评定标准》(1996 年)。
2.6 《电力建设安全工作规程》(第1 部分:火力发电厂2002 年)。
2.7 《电力建设安全健康与环境管理工作规定》(2002 年)。
2.8 设备厂家、设计院等有关资料。
3 系统设备简介国电哈尔滨平南热电厂2×350MW机组锅炉是哈尔滨锅炉有限责任公司自主研发技术的超临界锅炉,型号HG-1110/25.4-HM2,锅炉是采用单炉膛、一次中间再热、平衡通风、固态排渣、全钢结构的直流锅炉。
锅炉采用全钢结构构架,高强螺栓连接,受热面呈“П”型布置方式,炉膛上部分隔屏、后屏过热器。
水平烟道中布置有末级再热器、末级过热器;后烟道有中间隔墙,竖井前部布置水平低温再热器、立式低温再热器,竖井后部布置水平低温过热器、立式低温过热器和省煤器。
(整理)氨基磺酸清洗冷却器施工方案

氨基磺酸清洗冷却器施工方案1、化学清洗工艺的确定原则化学清洗工艺的确定包括清洗剂的选择和清洗工艺条件的确定。
清洗剂应根据被清洗设备的材质、性能及清洗设备的结构、结垢的类型、组成及垢量的大小进行综合选择,然后根据选定的清洗剂确定合理的清洗工艺条件。
清洗剂的品种和清洗方法多种多样,被清洗设备与污垢页千差万别,但选择与确定具体的清洗剂与清洗工艺时;有一些共同的原则,才能选择出最有效、最安全、最经济的清洗方案。
2、氨基磺酸清洗技术2.1清洗特点氨基磺酸是中等强度的固体无机酸,可溶于水,相对分子质量为97,斜方晶系片状结晶,无色无臭,密度为2.126g/cm3,熔点约为205℃。
其特点是不挥发,可避免因挥发而造成的人员安全、环境污染等问题,又因是固体物料,所以便于运输。
氨基磺酸稳定性很高,室温下存放多年性质不变,不挥发、不吸潮,分解温度高达207℃-260℃才能完全分解,只要维持干燥,则性质稳定,水中溶解性能良好,清洗时不生成盐类沉淀,不含氯离子,对材质使用性广,且对金属的腐蚀性小,加水。
加热溶解后,易水解为酸或硫酸铵,它可同金属氧化物、硫酸盐等反应生成溶解度很大的氨基磺酸铁、钙、鎂等盐类,从而可将这一特性用于清洗水垢和钢铁表面除锈。
因此对钙镁垢清洗能力强。
但清洗铁垢特别是氧化皮的能力稍差。
目前仅用于材质为不锈钢、碳钢、铜及合金等的热交换器、管道等设备的清洗。
氨基磺酸在清洗水垢方面适合饮用茶炉等生活用品的除垢,安全可靠。
电力系统已经有关单位采用氨基磺酸进行大型锅炉的清洗。
2.2氨基磺酸除垢机理氨基磺酸与水垢有如下反应:CaCO3+2NH2SO3H→Ca(NH2SO3)2+H2O+CO2 ①Ca3(Pa4)2+6NH2SO3H→3Ca(NH2SO3)2+2H3PO4②氨基磺酸与钢铁的腐蚀产物有如下反应:Fe3O4+8NH2SO3H→Fe(NH2SO3)+2Fe(NH2SO3)2+2Fe(NH2SO3)+4H2O ③Fe3O3+6NH2SO3A→2Fe(NH2SO3)3+3H2O ④FeO+2NH2SO3H→Fe(NH2SO3)+H2O ⑤反应生成的氨基磺酸、钙、鎂、铁、盐等在水溶液中的溶解度很大,所以氨基磺酸清洗剂有优良的除垢和除锈效果。
电厂300MW机组柠檬酸酸洗方案
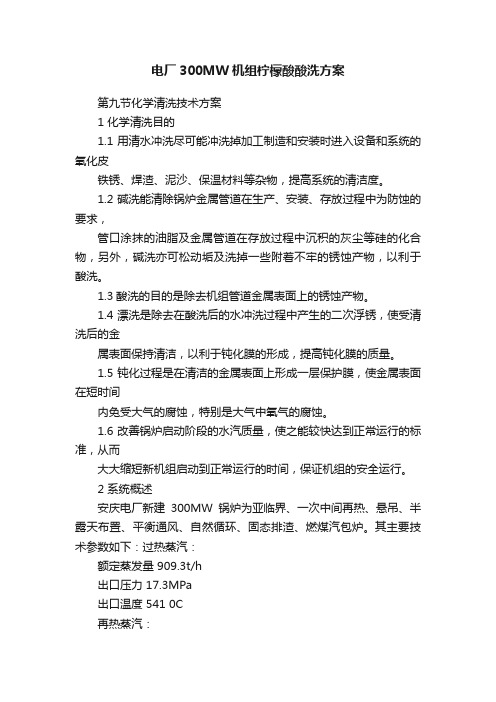
电厂300MW机组柠檬酸酸洗方案第九节化学清洗技术方案1 化学清洗目的1.1用清水冲洗尽可能冲洗掉加工制造和安装时进入设备和系统的氧化皮铁锈、焊渣、泥沙、保温材料等杂物,提高系统的清洁度。
1.2碱洗能清除锅炉金属管道在生产、安装、存放过程中为防蚀的要求,管口涂抹的油脂及金属管道在存放过程中沉积的灰尘等硅的化合物,另外,碱洗亦可松动垢及洗掉一些附着不牢的锈蚀产物,以利于酸洗。
1.3酸洗的目的是除去机组管道金属表面上的锈蚀产物。
1.4漂洗是除去在酸洗后的水冲洗过程中产生的二次浮锈,使受清洗后的金属表面保持清洁,以利于钝化膜的形成,提高钝化膜的质量。
1.5钝化过程是在清洁的金属表面上形成一层保护膜,使金属表面在短时间内免受大气的腐蚀,特别是大气中氧气的腐蚀。
1.6改善锅炉启动阶段的水汽质量,使之能较快达到正常运行的标准,从而大大缩短新机组启动到正常运行的时间,保证机组的安全运行。
2 系统概述安庆电厂新建300MW锅炉为亚临界、一次中间再热、悬吊、半露天布置、平衡通风、自然循环、固态排渣、燃煤汽包炉。
其主要技术参数如下:过热蒸汽:额定蒸发量 909.3t/h出口压力 17.3MPa出口温度 541 0C再热蒸汽:额定流量 742t/h进/出口温度 318/5410C进/出口压力 3.53/3.36MPa给水温度 2720C给水管分为三条,一条是主给水管,设进口电动闸阀一台;一条是启动旁路,设置进口电动调节阀一台和电动闸阀二台;第三条是上水与水压试验用小旁路,设电动截止阀二台。
自给水管路来的水由左右两侧进入标高32000mm处省煤器进口集箱(Φ273*40,20G),省煤器管径为Φ51*6。
给水经省煤器蛇形管加热后分三路进入三只省煤器中间集箱(Φ273*45,20G),再由此三只中间集箱引出省煤器吊挂管(Φ60*9,SA-210C),向上穿过顶棚管引入标高62700mm处省煤器出口集箱(Φ273*40,20G),然后通过12根Φ159*18(20G)的连接管引入汽包。
新建超临界机组的柠檬酸清洗

安全与 综合
湖
南
电 力
第 2 卷 / 0 7年第 6期 7 20
新建超临界机组的柠檬酸清洗
冯 斌 ,周 年光 ,袁新 民 ,李 石湘
( .湖 南省 电力 公 司试验研 究 院,湖 南 长沙 4 0 0 ;2 1 1 0 7 .湖 南湘 潭发 电有 限责任公 司 ,湖 南 湘 潭 4 1 0 ) 1 1 2
s p ro . u e i r
Ke r s s p r rtc 源自 i ;c e c lce n n y wo d : u e c iia un t h mia l a i g;c ti cd; p s i a i n ir a i c a sv t o
1 前 言
新建机 组的化学 清洗对 于清除锅 炉和 给水 系统
量优 良证 明清洗工 艺正确可行 。
关键 词 :超 临界 机组 ;化 学清洗 ;柠 檬酸 ;钝 化
中图分 类号 :T 2;K 2 M61 2 T 8 文献 标识 码 :B 文章 编号 :10—1820)6 000 08 9 (070— 4—2 0 0
Cir c a i l a ng o w -u l u r r tc lu i t i c d c e ni f ne b id s pe c ii a n t
内表 面 的氧化产物 ,形成钝 化膜 ,从 而改善 机组启
液进 行保护 。
2 1 碱洗 范围 .
凝汽器 汽侧 、 凝结水 系统及 给水 系统 ( 含凝泵 、
汽前 泵 、精 处理旁路 、加热器 及旁路 ,高低加 汽侧
不参 加碱洗 ) 、省煤 器、水 冷壁 、启 动分离器 、储水
动时 的汽水 品质 ,缩短 试运周期 ,保 障机组投 用后
锅炉化学清洗方案

发电公司4号锅炉化学清洗方案编制日期 2016.07.04摘要摘要内容:本方案介绍了***发电有限责任公司4号锅炉化学清洗的有关事项,包括化学清洗工艺、化学清洗回路设计、化学清洗过程、安全质量控制措施,预防与应急措施,清洗质量标准及检验要求。
为锅炉本体化学清洗工作正常、有序地实施提供必要的参考。
关键词:化学清洗柠檬酸工艺目录1 概述 (1)2 编写依据 (2)3 系统及设备主要技术规范 (2)3.1 清洗范围及水容积 (2)3.2清洗用主要设备技术规范 (3)3.3 清洗回路中主要设备流速计算 (3)4化学清洗工艺参数 (3)5 炉本体清洗回路设计与临时系统的安装 (4)5.1 炉本体清洗回路 (4)5.2 炉本体化学清洗临时系统的接口 (4)6 化学清洗过程 (5)6.1 预冲洗及升温试验 (6)6.2柠檬酸清洗 (7)6.3 酸洗后水冲洗 (7)6.4 漂洗 (8)6.5钝化 (8)6.6 废液处理 (8)7 化学清洗工期计划 (8)8作业准备和条件 (9)8.1技术准备 (9)8.2 双方职责 (9)8.3清洗条件 (11)9 预防与应急措施 (13)9.1预防措施 (13)9.2 应急措施 (13)9.3成品防护措施 (14)10清洗质量标准及检验要求 (14)10.1 清洗质量标准 (14)10.2化学清洗记录 (15)11 危险源、环境因素辨识及防范措施、文明施工标准 (15)11.1危险源清单及防范措施 (15)11.2环境因素清单及防范措施 (19)11.3危险性作业项目 (19)11.4文明施工标准 (19)12 附录: (20)1 概述发电有限责任公司2×1000MW超超临界锅炉是由哈尔滨锅炉厂有限责任公司设计、制造的,本工程的锅炉是超超临界变压运行直流锅炉,采用П型布置、单炉膛、低NoX PM主燃烧器和MACT型低Nox分级送风燃烧系统、反向双切园燃烧方式,炉膛采用内螺纹管垂直上升膜式水冷壁、循环泵启动系统、一次中间再热、调温方式除煤/水比外,还采用烟气分配挡板、燃烧器摆动、喷水等方式。
电厂锅炉机组启动前化学水冲洗的方法和要求
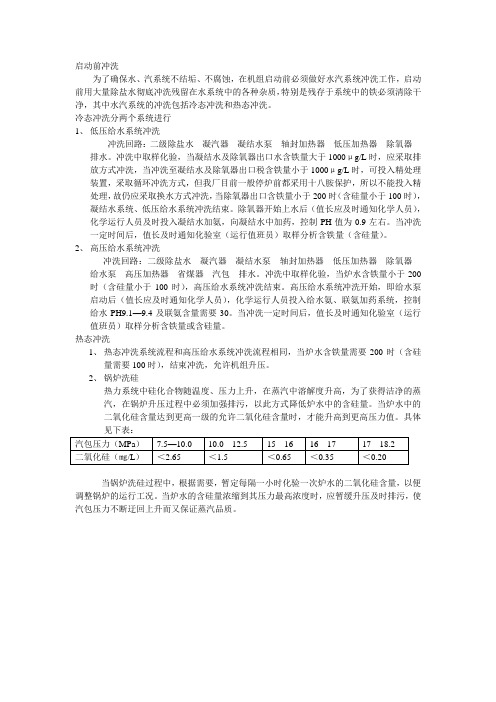
启动前冲洗为了确保水、汽系统不结垢、不腐蚀,在机组启动前必须做好水汽系统冲洗工作,启动前用大量除盐水彻底冲洗残留在水系统中的各种杂质,特别是残存于系统中的铁必须清除干净,其中水汽系统的冲洗包括冷态冲洗和热态冲洗。
冷态冲洗分两个系统进行1、低压给水系统冲洗冲洗回路:二级除盐水---凝汽器---凝结水泵---轴封加热器---低压加热器---除氧器---排水。
冲洗中取样化验,当凝结水及除氧器出口水含铁量大于1000μg/L时,应采取排放方式冲洗,当冲洗至凝结水及除氧器出口税含铁量小于1000μg/L时,可投入精处理装置,采取循环冲洗方式,但我厂目前一般停炉前都采用十八胺保护,所以不能投入精处理,故仍应采取换水方式冲洗,当除氧器出口含铁量小于200时(含硅量小于100时),凝结水系统、低压给水系统冲洗结束。
除氧器开始上水后(值长应及时通知化学人员),化学运行人员及时投入凝结水加氨,向凝结水中加药,控制PH值为0.9左右。
当冲洗一定时间后,值长及时通知化验室(运行值班员)取样分析含铁量(含硅量)。
2、高压给水系统冲洗冲洗回路:二级除盐水---凝汽器---凝结水泵---轴封加热器---低压加热器---除氧器---给水泵---高压加热器---省煤器---汽包---排水。
冲洗中取样化验,当炉水含铁量小于200时(含硅量小于100时),高压给水系统冲洗结束。
高压给水系统冲洗开始,即给水泵启动后(值长应及时通知化学人员),化学运行人员投入给水氨、联氨加药系统,控制给水PH9.1—9.4及联氨含量需要30。
当冲洗一定时间后,值长及时通知化验室(运行值班员)取样分析含铁量或含硅量。
热态冲洗1、热态冲洗系统流程和高压给水系统冲洗流程相同,当炉水含铁量需要200时(含硅量需要100时),结束冲洗,允许机组升压。
2、锅炉洗硅热力系统中硅化合物随温度、压力上升,在蒸汽中溶解度升高,为了获得洁净的蒸汽,在锅炉升压过程中必须加强排污,以此方式降低炉水中的含硅量。
电厂锅炉化学清洗技术方案
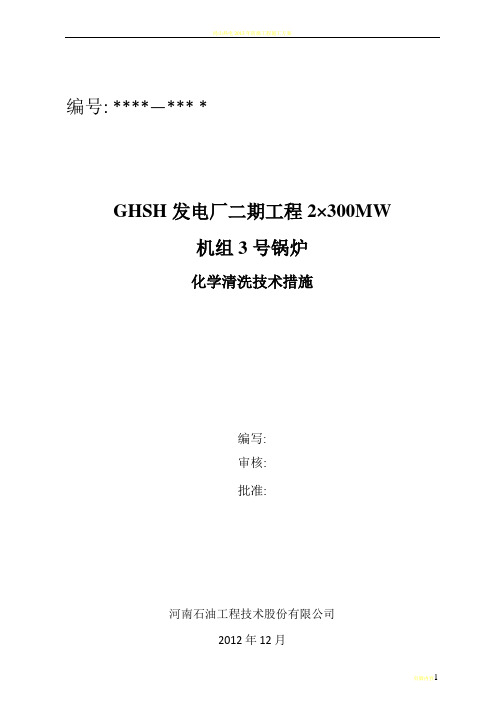
编号: ****—*** *GHSH 发电厂二期工程2×300MW机组3 号锅炉化学清洗技术措施编写:审核:批准:河南石油工程技术股份有限公司2012 年 12 月目录2. 编制依据 (4)3. 化学清洗质量目标: (4)4. 系统及主要设备技术规范 (4)4.1 系统简介 (4)4.2 主要设备技术规范 (4)5. 化学清洗方式及范围 (4)6. 化学清洗前应具备的条件 (5)6.1 对安装的要求 (5)6.2 通讯应具备下列条件 (7)6.3 酸洗化验间应具备的条件 (8)6.4 电厂配合化学清洗应具备的条件 (8)7. 化学清洗工作程序 (8)8. 化学清洗步骤 (8)8.1 清洗系统的划分 (8)8.2 临时系统的分部试运和水压试验 (9)8.3 冷态冲洗 (9)8.4 升温及保温试验 (10)8.5 碱洗 (10)8.6 酸洗 (10)8.7 水冲洗 (11)8.8 亚硝酸钠钝化 (11)8.9 化学清洗质量评定 (12)8.10 废液处理 (12)9. 职责分工 (12)9.1 安装单位职责 (12)9.2 电厂职责 (12)9.3 化学清洗单位职责 (13)9.4 化学清洗的组织落实 (13)10. 安全注意事项及防范措施 (14)11.附录 (16)附录 1 化学清洗质量控制点 (16)附录 2 化学清洗前应具备的条件检查清单 (17)附录 3 SH 电厂锅炉化学清洗材料清单 (18)附录 4 化学清洗试验方法 (21)附录 5 SH 电厂二期工程锅炉化学清洗交底记录 (26)附录 6 三河发电厂二期工程锅炉化学清洗系统图 (27)1. 编制目的1.1 为了指导及规范锅炉的化学清洗工作,保证锅炉能够安全正常投入运行,制定本措施。
1.2 新装机组,对其受热面污垢、锈蚀进行清洗。
1.3 检查及设备的运行情况,检验系统的性能,发现并消除可能存在的缺陷。
2. 编制依据2.1 火力发电厂锅炉化学清洗导则 DL/T794-20122.2 锅炉化学清洗规则 TSG G5003-20082.3 化学清洗缓蚀剂应用性能评价指标及试验方法 DL/T 523-20072.4 污水综合排放标准 GB 8978-19963. 化学清洗质量目标:符合《火力发电厂锅炉化学清洗导则》 DL/T794-2012 质量标准要求。
300MW燃煤电站化学清洗
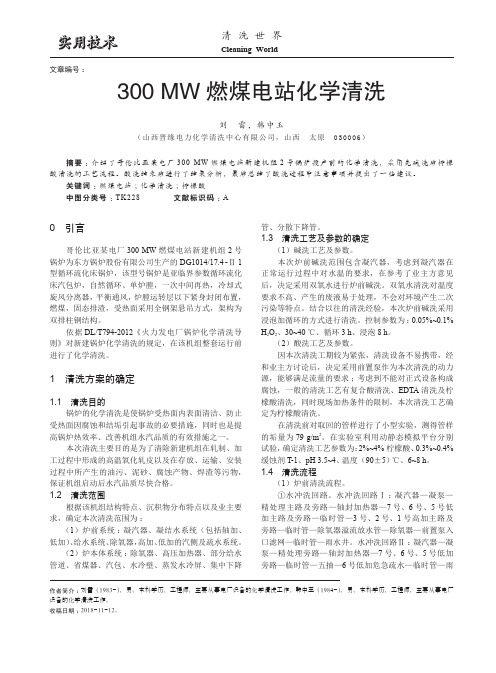
清洗世界Cleaning World实用技术第35卷第1期2019年1月0 引言哥伦比亚某电厂300 MW 燃煤电站新建机组2号锅炉为东方锅炉股份有限公司生产的DG1014/17.4-Ⅱ1 型循环流化床锅炉,该型号锅炉是亚临界参数循环流化床汽包炉,自然循环、单炉膛,一次中间再热,冷却式旋风分离器,平衡通风,炉膛运转层以下紧身封闭布置,燃煤,固态排渣,受热面采用全钢架悬吊方式,架构为双排柱钢结构。
依据DL/T794-2012《火力发电厂锅炉化学清洗导则》对新建锅炉化学清洗的规定,在该机组整套运行前进行了化学清洗。
1 清洗方案的确定1.1 清洗目的锅炉的化学清洗是使锅炉受热面内表面清洁、防止受热面因腐蚀和结垢引起事故的必要措施,同时也是提高锅炉热效率、改善机组水汽品质的有效措施之一。
本次清洗主要目的是为了清除新建机组在轧制、加工过程中形成的高温氧化轧皮以及在存放、运输、安装过程中所产生的油污、泥砂、腐蚀产物、焊渣等污物,保证机组启动后水汽品质尽快合格。
1.2 清洗范围根据该机组结构特点、沉积物分布特点以及业主要求,确定本次清洗范围为:(1)炉前系统:凝汽器、凝结水系统(包括轴加、低加)、给水系统、除氧器,高加、低加的汽侧及疏水系统。
(2)炉本体系统:除氧器、高压加热器、部分给水管道、省煤器、汽包、水冷壁、蒸发水冷屏、集中下降管、分散下降管。
1.3 清洗工艺及参数的确定(1)碱洗工艺及参数。
本次炉前碱洗范围包含凝汽器,考虑到凝汽器在正常运行过程中对水温的要求,在参考了业主方意见后,决定采用双氧水进行炉前碱洗。
双氧水清洗对温度要求不高、产生的废液易于处理,不会对环境产生二次污染等特点。
结合以往的清洗经验,本次炉前碱洗采用浸泡加循环的方式进行清洗。
控制参数为:0.05%~0.1% H 2O 2、30~40 ℃、循环3 h 、浸泡8 h 。
(2)酸洗工艺及参数。
因本次清洗工期较为紧张,清洗设备不易携带,经和业主方讨论后,决定采用前置泵作为本次清洗的动力源,能够满足流量的要求;考虑到不能对正式设备构成腐蚀,一般的清洗工艺有复合酸清洗、EDTA 清洗及柠檬酸清洗,同时现场加热条件的限制,本次清洗工艺确定为柠檬酸清洗。
火电工程机组化学(柠檬酸)清洗施工方案

目录1. 施工概况 (3)2. 依据的图纸、文件及标准 (4)3. 清洗范围、清洗回路设计及清洗参数 (4)4. 清洗前安装与检查 (6)5. 化学清洗过程 (8)6. 清洗质量标准及检查项目 (11)7. 化学清洗组织措施及分工原则 (11)8. 安全措施 (13)9. 环境保护措施 (14)10. 化学清洗设备材料、药品及用水用汽量 (14)11. 工期计划 (16)12. 附录 (17)发文范围:(共8 份)归档夹类:施工方案夹号: 14本版文件于2011年月日开始实施。
批准人:1号机组化学(柠檬酸)清洗1. 施工概况1.1. 佛山市山水恒益电厂“上大压小”工程2×600MW超临界机组锅炉为超临界参数变压运行螺旋管圈直流炉,单炉膛、一次中间再热、四角切圆燃烧方式、平衡通风、∏型露天布置、固态排渣、全钢架悬吊结构。
锅炉设计燃煤为神府东胜煤。
炉后尾部布置两台转子直径为Φ13492mm的三分包容克式空气预热器。
1.2. 锅炉的主要参数:1.3. 清洗的目的和清洗工艺1.3.1. 清洗目的➢根据DL/T794-2001《火力发电厂锅炉化学清洗导则》规定,直流锅炉在安装完毕投产前必须进行化学清洗,以除去锅炉受热面在轧制、储存、运输及安装过程中所产生的铁锈、焊渣等有害杂质,保证锅炉安全运行,提高锅炉热效率和水汽品质,使汽水品质尽快达到DL/T 561-1995 《火力发电厂水汽化学监督导则》的标准。
1.3.2. 清洗工艺简述:➢根据《火力发电厂锅炉化学清洗导则》(DL/T794-2001)的要求,结合本期机组的实际情况,本清洗方案分两部分:碱洗和酸洗。
本次化学清洗碱洗采用当前最为环保的除油清洗工艺:双氧水清洗除油;酸洗采用柠檬酸清洗及漂洗、双氧水钝化工艺,清洗废液排放至废水贮存池后进行综合处理。
1.4. 组织措施:➢佛山市山水恒益电厂、监理公司、调试单位、安装单位及清洗单位组成化学清洗领导小组,负责化学清洗工作过程中的协调、准备和实施。
柠檬酸酸洗方案要点
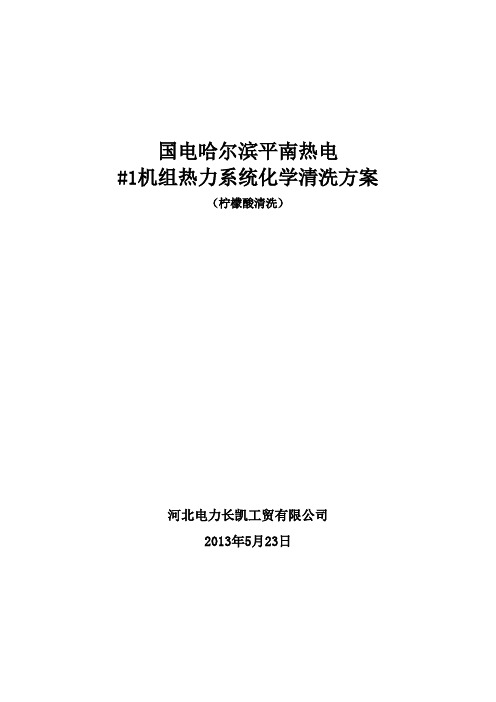
国电哈尔滨平南热电#1机组热力系统化学清洗方案(柠檬酸清洗)河北电力长凯工贸有限公司2013年5月23日目录1 清洗目的2 编制依据3 系统设备简介4 清洗范围及清洗工艺5 清洗系统安装应完成的工作6 清洗前应具备的条件7 清洗用药品及水量等估算8 清洗过程及化学监督9 清洗废液的处理10 清洗后的检查与评定11 组织分工12 安全注意事项附清洗系统图1 清洗目的除去新建锅炉在轧制、加工过程中形成的高温氧化轧皮以及在存放、运输、安装过程中所产生的腐蚀产物、油污、焊渣和泥沙等污染物,并形成良好的钝化保护膜,保持热力设备内表面清洁,提高热力系统水汽品质,防止受热面因结垢、腐蚀引起事故,保证机组顺利启动和安全、经济运行。
2 编制依据2.1 《火力发电厂锅炉化学清洗导则》( DL/T 794−2012)。
2.2 《火电工程启动调试工作规定》(1996 年)。
2.3 《电力建设施工及验收技术规范》火力发电厂锅炉篇(1996 年版)、管道篇(1994 年版)、化学篇(2002 年版)。
2.4 《火力发电厂基本建设工程启动及竣工验收规程(1996 年版)及相关规程》。
2.5 《火电工程调整试运质量检验及评定标准》(1996 年)。
2.6 《电力建设安全工作规程》(第1 部分:火力发电厂2002 年)。
2.7 《电力建设安全健康与环境管理工作规定》(2002 年)。
2.8 设备厂家、设计院等有关资料。
3 系统设备简介国电哈尔滨平南热电厂2×350MW机组锅炉是哈尔滨锅炉有限责任公司自主研发技术的超临界锅炉,型号HG-1110/25.4-HM2,锅炉是采用单炉膛、一次中间再热、平衡通风、固态排渣、全钢结构的直流锅炉。
锅炉采用全钢结构构架,高强螺栓连接,受热面呈“П”型布置方式,炉膛上部分隔屏、后屏过热器。
水平烟道中布置有末级再热器、末级过热器;后烟道有中间隔墙,竖井前部布置水平低温再热器、立式低温再热器,竖井后部布置水平低温过热器、立式低温过热器和省煤器。
论在运行锅炉上的柠檬酸清洗工艺

袁 2 柠檬酸浓度选择 试验
柠檬酸 浓度 gL , 缓蚀剂浓度 gL 加氨量 , 温度 时间 p H值 2 0 3 0 4 0 3 3 3 清洗效果 1 9 ± 6 37 垢洗脱率 9 % 1 5 2 35 . o 1 9 士2 3 5 _ 垢洗脱率 9 % 1 5 6 . 37 7 1 9 ± 6 37垢洗脱率 1 0 1 5 2 35 0%
酸洗时结垢量分析如下 : 前墙 : 标高 2 . 35 第 8 25~2 .m 1根 : 向 火侧 4 gm 1 / ; 5 背火侧 8 gm 2/ ; 后墙 : 高 2 .~2 .m 第 1 7根 ; 标 23 33 1
向火 侧 5 0 / : 7 gm
从表 2可知 , 柠檬酸浓度 4 gL的 2 3号配方清洗效果为 0/ — 10 , 0 % 加氨水量 为 1 L 1/ 。上述 定性试验表 明, g 柠檬酸含 量是
适 量 氨 水 。 其 反应 如下 :
H3 H5 +NH4 — C6 07 OH NH4 C6 O7 H2 H5 +H2 O
在 相 同 条 件 下 《5C・ h3 3号 试 片 表 面 光 亮 , 点蚀 , 9 o 6 )— 无 外
观最佳。 以柠檬酸浓度 4 gL 0 /+柠檬 1号 为小试最佳条件。 虽腐
背火 侧 1 7 / 。 gm 2
2 柠檬 酸清 洗的特 点 和机理
在用柠檬 酸作清洗剂时 ,要在清洗液 中加氨水将溶 液 p H 值调至 35~40 柠檬酸在 不同的 p . .。 H值条件下, 其离解程度也 不周。 p 在 H值 为 30 . , .~44时 柠檬酸主要是 以 HC HO 一 形式 存在 , 与氨生成柠檬 酸单铵 , 柠檬酸单铵对 铁的溶解 效果最好 。 在p H值 为 35时 , . 柠檬 酸离解成 负离子 H CH 0 一H 5 , C HO 一 此时柠檬酸单铵与铁 的络合效果最好 。所 以, 在酸洗 时要加入
论在运行锅炉的柠檬酸清洗工艺

摘 要: 通过 大量 的动 、 态试验 , 静 从加 药方式 、 檬 酸浓度 、 柠 缓蚀 剂 的选 用及 其浓 度 、 清洗 温度 、
清洗液 的 p 以及锅 炉的热 态造膜 工 艺等 进 行 了筛选 , 定 了适 用新 建 、 行 锅 炉 的柠 檬 酸 清 H 确 运
运行 几年 后 , 4号 锅 炉 结 垢 量 已超 过火 力 发 电
前墙 : 高 2. 标 2 5~2 . 第 8 35 m 1根 ; 火 侧 向
厂锅炉化 学 清洗 导 则 规定 的 40gm , 以准 备 对 0 / 所
45 m , 1 背火侧 8 m ; 2
后墙 : 高 2. 标 23~2 . 第 17根 : 火 侧 33m 1 向
50 m , 7 背火 侧 17g m 。 2 /
4 号炉进行酸洗 。针对 4号炉水冷壁管有微裂纹 的
实际情 况 , 经过 多次 柠檬 酸清 洗小试 , 对缓 蚀剂 的配 比及 酸洗后 的钝 化 工 艺 进 行 了 大 量静 态 试 验 , 步 初 确定 了酸洗 方案 , 此 方 案 基 础 上 又进 行 了动 态 试 在
3 2 2 试 验 结 果 ..
注 : 蚀 剂 为 3 L若 ]原 粉 ; 洗 温 度 ( 5±2 ; 缓 清 9 ) 清
清 洗温 度 :9 2 (5± )℃ ;
表 2 加氨 量 1 / 1g L时柠檬 酸质 量 浓度 选择 试验
清洗 液 p 37 ; H:. 3
清洗 时 间 : h 6 ;
钝化 方 式 : 性钝 化 ,% 亚硝 酸钠 ; 碱 2 钝化 液 p 95~1 ; H:. 0
柠檬酸酸洗方案

国电哈尔滨平南热电#1机组热力系统化学清洗方案(柠檬酸清洗)河北电力长凯工贸有限公司2013年5月23日目录1 清洗目的2 编制依据3 系统设备简介4 清洗范围及清洗工艺5 清洗系统安装应完成的工作6 清洗前应具备的条件7 清洗用药品及水量等估算8 清洗过程及化学监督9 清洗废液的处理10 清洗后的检查与评定11 组织分工12 安全注意事项附清洗系统图1 清洗目的除去新建锅炉在轧制、加工过程中形成的高温氧化轧皮以及在存放、运输、安装过程中所产生的腐蚀产物、油污、焊渣和泥沙等污染物,并形成良好的钝化保护膜,保持热力设备内表面清洁,提高热力系统水汽品质,防止受热面因结垢、腐蚀引起事故,保证机组顺利启动和安全、经济运行。
2 编制依据2.1 《火力发电厂锅炉化学清洗导则》( DL/T 794−2012)。
2.2 《火电工程启动调试工作规定》(1996 年)。
2.3 《电力建设施工及验收技术规范》火力发电厂锅炉篇(1996 年版)、管道篇(1994 年版)、化学篇(2002 年版)。
2.4 《火力发电厂基本建设工程启动及竣工验收规程(1996 年版)及相关规程》。
2.5 《火电工程调整试运质量检验及评定标准》(1996 年)。
2.6 《电力建设安全工作规程》(第1 部分:火力发电厂2002 年)。
2.7 《电力建设安全健康与环境管理工作规定》(2002 年)。
2.8 设备厂家、设计院等有关资料。
3 系统设备简介国电哈尔滨平南热电厂2×350MW机组锅炉是哈尔滨锅炉有限责任公司自主研发技术的超临界锅炉,型号HG-1110/25.4-HM2,锅炉是采用单炉膛、一次中间再热、平衡通风、固态排渣、全钢结构的直流锅炉。
锅炉采用全钢结构构架,高强螺栓连接,受热面呈“П”型布置方式,炉膛上部分隔屏、后屏过热器。
水平烟道中布置有末级再热器、末级过热器;后烟道有中间隔墙,竖井前部布置水平低温再热器、立式低温再热器,竖井后部布置水平低温过热器、立式低温过热器和省煤器。
直流锅炉柠檬酸洗后水冲洗和漂洗工艺的改进

文 章 编 号 :6 1 9 9 2 1 ) 5一 o 5一 5 1 7 —80 ( 0 0 0 o o o
Cani g ord 清 洗世 界 l e n W l
第 2 卷 第5 6 期
2 0年 5 01 月
直 流 锅 炉 柠 檬 酸 洗 后 水 冲 洗 和 漂 洗 工 艺 的 改 进
c ta in o a e i h ns o u in wh c a ii ts d rc o v rin t a sv tn . er to fFe nd F ¨ n t e r e s l to i ih fai g a
Absr t Th o ma e u i 4 b ie fa s a i e p we ln s a o c —h o g u e c iia ie , t ac : e h me d n t olr o e sd o r p a ti n e t r u h s p r rtc lbolr wh c sp c l d b i c a i lu h d b o d ns t ump wi a g o ih i ik e y c t c d,f s e y c n e a ep i r t lr e f w,rn e y ct ca i h l i s d b i cd,a d i r n p s iae y h d o e p r xd d rng c nsr c in Th c e c l l a i g x e e c s o t a a sv t d b y r g n e o i e u i o tu t . o e h mi a ce n n e p r n e h ws h t i l s i g w h lr e f w tb y s o tn s i a d ef in l e uc ss c n a y r t n ha e fu h n t a g o noa l h re sfu h t n f ce ty rd e e o d r s ,a d t ttm— i l l me i u
鸿山热电#1机组柠檬酸清洗措施8.12

目录1 工程概况及工程量 (1)1.1 工程概况.... (1)1.2 化学清洗的目的 (2)1.3 化学清洗范围 (2)1.4 工程量和工期 (2)1.4.1 工程量 (2)1.4.2 施工日期 (3)2.编制依据 (3)3.作业前的准备与条件 (3)3.1 技术准备 (3)3.2 作业人员 (4)3.3 作业工器具 (6)3.4 材料和设备 (7)3.5 安全器具 (11)3.6 工序交接 (12)3.7 其他 (12)4 作业程序.方法 (12)4.1 施工工艺流程 (12)4.2 施工方案及要求 (13)5 质量控制点的设置和质量通病预防 (20)5.1 质量标准及评定 (20)5.2 质量目标 (20)5.3 作业过程中控制点的设置 (20)5.4 质量控制与质量通病预防 (21)6 作业要求和环境条件 (21)6.1 安全危害因素辩识和控制 (21)6.2 环境条件 (23)6.3 消防管理 (24)6.4 作业指导书应急处置预案 (24)7 组织与分工 (26)8 附录(包括记录表样.附表.附图) (27)8.1 化学清洗网络计划安排 (27)8.2 清洗前必需要隔离阀门清单 (27)8.3 清洗过程化学分析测试方法 (28)8.4 化学清洗表格 (32)8.5 化学清洗系统图 (43)1 工程概况及工程量1.1 工程概况福建鸿山热电厂新建工程建设规模为一期2×600MW超临界燃煤机组。
锅炉为哈尔滨锅炉厂有限责任公司生产的超临界参数变压本生直流炉,一次中间再热、单炉膛平衡通风、露天布置、固态排渣、全钢构架、全悬吊结构Π型布置,锅炉型号为HG-1962/25.4-YM3型。
与其配套的有东方汽轮机厂有限公司提供的N600-24.2/566/566型超临界、单轴、一次中间再热、三缸四排汽、双背压凝汽式汽轮机和东方电机股份有限公司生产的型式为QFSN-600-2-22C三相同步汽轮发电机,发电机冷却方式为水、氢,机组额定容量为600MW。
- 1、下载文档前请自行甄别文档内容的完整性,平台不提供额外的编辑、内容补充、找答案等附加服务。
- 2、"仅部分预览"的文档,不可在线预览部分如存在完整性等问题,可反馈申请退款(可完整预览的文档不适用该条件!)。
- 3、如文档侵犯您的权益,请联系客服反馈,我们会尽快为您处理(人工客服工作时间:9:00-18:30)。
目录1.概述 32.化学清洗范围及清洗系统 33.化学清洗工艺 54.化学清洗前临时系统的安装、系统检查及清洗系统应具备的条件75.化学清洗工艺过程及其控制106.清洗质量技术标准127.安全措施128.化学清洗组织措施及分工原则139.化学清洗设备、药品及水量估算1410.工期1611.化学清洗系统图16 1.概述黄埔电厂#5炉为上海锅炉厂生产的SG-1025/16.7-M313UP型直流燃煤锅炉,已经成功运行多年。
由于水质对锅炉运行造成的影响,日积月累在锅炉汽水系统部位形成了一层致密的水垢,达到了再次清洗的时限,并且经割管检测,水冷壁腐蚀严重,有很多很明显的裂痕,且垢最里层有单质铜(≥3%)沉积覆盖,针对如此实际情况,并根据DL/T794-2001《火力发电厂锅炉化学清洗导则》规定,对#5炉汽水系统采用柠檬酸+氨基磺酸清洗及氨洗除铜工艺,在不损害机组设备的前提下清除汽水系统所有的水垢,从而保证机组的安全运行。
锅炉主要参数如下:锅炉蒸发量1025t/h过热器出口蒸汽压力16.72MPa过热蒸汽温度540℃再热蒸汽压力 3.54/3.32MPa(绝对)再热蒸汽温度320/540℃给水压力21.36MPa给水温度265.4℃预热器热风温度333.9℃锅炉排烟温度130.68℃2.化学清洗范围及清洗工艺2.1.化学清洗范围高压给水管道、省煤器、水冷壁、炉顶过热器、包覆管、低温过热器、前屏过热器、后屏过热器、高温过热器、主蒸汽母管和启动分离器(包括内部装置)及有关联箱,包括临时系统,总的水容积约为200m3。
2.2.化学清洗工艺要点由于被清洗的材质有20A、15CrMo、12Cr1MoV、SA213、TP-304H、TP-347H、St45、8Ⅲ、13CrMo44和10CrMo910等碳素钢、合金钢和奥氏体钢,被清洗材质表面腐蚀严重,垢中铜含量较大,以及过热器内垢清洗难等因素,故本次化学清洗采用复合柠檬酸+氨基磺酸酸洗工艺,添加缓蚀剂、消泡剂、还原剂等清洗助剂,酸洗后采用氨洗除铜,然后采用柠檬酸漂洗及联胺钝化。
清洗废液中和且去除COD合格后排放。
2.3. 化学清洗工艺参数注:清洗过程中所有项目的测试方法依照DL/T794-2001《火力发电厂锅炉化学清洗导则》要求。
2.4. 各清洗回路管道特性、截面积及清洗流通速度(按400t/h的流量计算)2.5本次清洗加热方式采用投辅汽至#2高加进行加热。
3. 化学清洗系统(详见清洗系统图)本次清洗系统分为三个回路 第一回路:清洗箱→ 清洗泵→高加→ V 100→ V 101→省煤器→水冷壁V 203A → V 202-1、V 202-2→炉顶过热器→包复管→ V 300-1、V 300-2 →低压过热器→V204 → V207→ 启动分离器→V205-1、V 205-2→ 排1→ 清洗箱 (注:清洗时,V 203、V 203A 、V 204相互切换。
)第二回路:清洗箱→ 清洗泵→高加→ V 100→ V 101→省煤器→水冷壁 →炉顶过热器→包复管→ V 300-1、V 300-2 →低压过热器→V204 → V207→ 启动分离器→ V 241→V 241A →前屏过热器→ 后屏过→高温过热器→ 主蒸汽母管→ 排2→ 清洗箱(注:清洗时,V 203、V 203A 、V 204相互切换。
) 第三回路:清洗箱→ 清洗泵→高加→ V 100→ V 101 →省煤器→水冷壁→炉顶过热器→包复管→ V 300-1 、V 300-2 → 低压过热器→V 200-1 、V 200-2→ 前屏过热器→ 后屏过→高温V 205-1 、V 205-2过热器→ 主蒸汽母管→ 排2→ 清洗箱(注:清洗时,V200-1、V200-2 与V205-1、V205-2 间断切换。
)4.化学清洗前临时系统的安装、系统检查及清洗系统应具备的条件4.1系统安装要求:,将管内的残留污泥、铁锈等有害物质清除干净。
,在规定压力下试水压,水压合格的才能继续使用,不得使用带铜部件的阀门。
,如每个接口均采用氩弧焊打底、电焊盖面、合理的热处理措施等等,确保在化学清洗时无泄漏。
4.14清洗中所用到的泵在安装前应检修,泵的盘根应换为耐酸盘根,安装后调试,正常运转后才能用于化学清洗。
,指示要灵敏、准确。
,以防震动。
4.2临时系统与永久系统的接点,用Ф108×4.5连接至排放母管。
,用Ф219×6临时管接至酸洗临时系统。
,用Ф273×8临时管接至酸洗排放母管。
,用Ф219×6临时管连接至清洗循环泵出口。
,紧急排水接出临时的排水系统。
4.3系统检查,系统所有阀门有否按图纸编号。
,各仪表指示是否准确。
,用泵作1.5倍工作压力(即1.2MPa)水压试验。
,系统加药模拟试验、升温试验合格。
4.4清洗前应具备的条件,具备正常,可靠供应合格除盐水条件。
,照明、临时电源和通讯设施已经备好。
现场具备二路250KW、380V的动力电源。
,温度280~320℃)已准备好。
,位置正确。
,试验溶液及安全用品运到现场,所需要化学药品经抽样化验合格,应由购货方提供合格证或质保书。
所有清洗药品分类、整齐堆放于清洗现场。
,取样管应装冷却器,并有足够的冷却水量。
,分析试验仪器和化学试剂已准备好。
,熟悉系统和安全规程,并进行技术交底和安全交底。
;与不参酸洗设备系统(如再热器、汽机等)连接阀门是否断开或关严。
5.化学清洗工艺过程及其控制5.1水冲洗打开V100、V101、V241、V202-1、V202-2、V207、V203A、V204、排1、排总阀门,启动凝升泵上水到锅炉本体,当排放管有水流出时,调节排总阀门,维持背压0.6~0.8MPa,用大流量清水冲洗第一回路至出口无色透明,浊度≤10mg/L;然后打开排2阀门,关闭排1阀门,调节排总阀门,维持背压0.6~0.8MPa,用大流量清水冲洗第二回路至出口无色透明,浊度≤10mg/L。
在冲洗第回路时,间断地打开V205-1、V205-2,冲洗该汽水管道。
冲洗完后系统加满水。
5.2过热器冲通试验打开排1、排2阀门,往除氧水箱投入加热蒸汽,当水温达到45±5℃时调整凝升泵的流量为1000~1200t/h左右,打开排2,关闭排1,维持背压0.6~0.8MPa,对过热器单独进行冲通,同时迅速组织人员用手摸屏式过热器和高温过热器下弯头,以判断是否已冲通。
冲通时间约15~20min,在开凝升泵的同时,开凝结水泵向除氧水箱补水。
5.3加热升温试验启动清洗循环泵分别按第一、第二回路各循环半小时,向#2高压加热器和清洗箱同时投入蒸汽加热,保证蒸汽压力0.8~1.0MPa,蒸汽流量30t/h,并监测水温,调节蒸汽流量,使排总出口温度为85~90℃,维持10~15分钟后,排掉部分热水,开始进酸清洗系统各回路。
5.5.酸洗将已定量的柠檬酸、氨基磺酸及助剂加入清洗箱,并使柠檬酸、氨基磺酸初始浓度分别为2~4%、3~4%。
投入蒸汽进行加热,加热到85~90℃时停止加热,系统按第一、二、三回路分别进行循环酸洗。
一、二、三回路每小时切换一次。
清洗过程中按清洗工艺参数中的分析项目进行取样分析。
酸洗过程中,清洗流速一定要大于0.3m/s,但不能超过1m/s。
5.6. 除盐水顶酸及水冲洗酸洗结束后,维持凝升泵流量350~400t/h,背压0.6~0.8MPa,按一、二、三清洗回路,将酸液顶排至灰渣沟,然后大流量冲洗清洗回路,直到出口水质澄清透明,无细小颗粒,且(Fe2++Fe3+)<50mg/L、pH>4.5。
5.7. 氨洗除铜将定量的氨水和过硫酸铵洗液加入清洗箱,维持温度为25~30℃,启动循环泵按一、二、三回路进行氨洗除铜,时间大约1个半小时。
5.8. 漂洗氨洗除铜结束后,清洗系统先用除盐水冲洗一次,然后加入浓度为0.1~0.3%的柠檬酸溶液,并加助剂,加氨水调整pH值为3.5~4.0,投入蒸汽加热,使溶液温度维持在75~85℃,按第一、二、三回路循环漂洗共2小时。
漂洗溶液中总铁量≤300mg/L时,漂洗结束,方可进行钝化。
漂洗过程中每半小时检测pH值、温度和总铁量。
5.9. 钝化向清洗箱内加入联胺和氨水调节pH9.5~10.0,再维持温度在80~90℃,系统按第一、二回路依次循环钝化,每1小时切换一次回路。
8小时后,拆看监视管,合格后切换至第一回路循环钝化1小时,结束循环钝化。
整个化学清洗过程结束。
钝化过程中每半小时取样检测一次pH值和温度,并记录检测结果。
5.9. 废液排放清洗废液严格按照GB8978-1996《污水综合排放标准》要求进行处理,处理达标后,请业主确认,然后排放至业主指定的地方。
5.10. 质量检查及割管清洗结束后除检查监视管、腐蚀指示片外,还应检查启动分离器各联箱,同时截取水冷壁、过热器有代表性管段(长250~300mm)各一根进行检查记录。
(管样要用钢锯人工截取)6. 清洗质量技术标准酸洗质量必须符合DL/T794-2001《发电厂锅炉化学清洗导则》的要求。
6.1被清洗表面应清洁,基本无残留物,无二次浮锈,无点蚀、无明显金属粗晶析出的过洗现象,金属表面钝化膜均匀、致密;6.2除垢率≥90%(以监视管为准)为合格,除垢率≥95%为优秀;6.3金属指示片腐蚀率小于8g/(m2·h)(失重法);6.4固定设备不受损伤。
7.安全措施7.1酸洗现场杂物清理干净,安全标识、危险标识等牌均已挂上。
7.2现场已有良好的照明、通风设施及通讯联络系统。
7.3现场有足够的消防水源和粉状石灰。
7.4酸洗期间现场停止一切作业,无关人员禁止进入现场。
7.5凡接触酸、碱的操作阀门用尼龙薄膜包好(操作门杆除外)。
7.6凡接触酸、碱的工作人员应戴防护眼镜、防毒口罩、面具、胶手套围裙、穿长筒胶鞋等劳保用品。
7.7为了防止误操作,启动酸泵和阀门操作应有监护人在场。
7.8对化学清洗系统进行一次安全检查,对临时管道应试压、查漏等。
7.8排废处理现场应有强力通风设施。
7.9当酸、碱溅到眼睛或皮肤时,先迅速用大量清水冲洗,然后请医生医治。
7.10酸洗期间应有医生和检修人员在场,并备有10%碘化钠溶液、10%氯化钙、3%氨水、红汞水、可拉明、咖啡因及止痛片等药品。
7.11所有参加酸洗的人员要服从统一指挥。
8.化学清洗组织措施及分工原则8.1 成立化学清洗领导小组由黄埔电厂和广东科林化学清洗公司成立一个化学清洗领导小组,统一领导和指挥整个化学清洗工作,并负责化学清洗工作过程中的协调、准备、实施和质量环保控制。
本着分工、协作和相互配合的精神,确保整个化学清洗工作顺利进行。
8.2 黄埔电厂负责范围8.2.2 负责把二路380V、250kW的电源接至清洗现场,安装好清洗现场的照明及临时分析场地的电源。