乙烯裂解炉辐射段炉管堵塞原因分析及对策
乙烯裂解炉辐射段炉管堵塞原因分析及对策
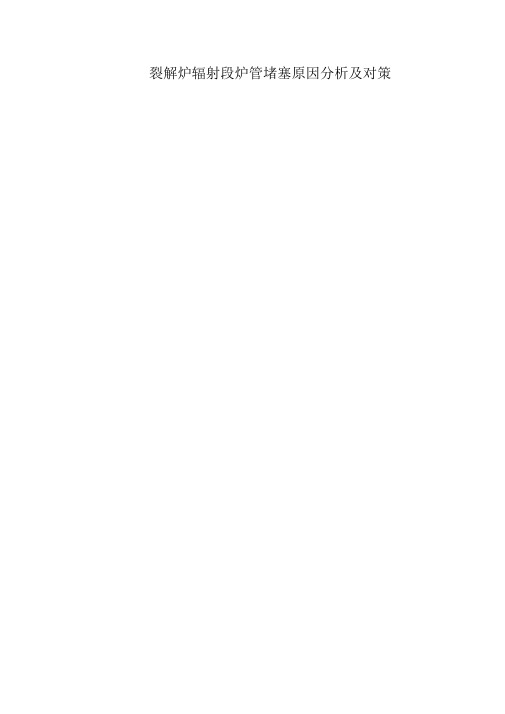
裂解炉辐射段炉管堵塞原因分析及对策的文丘里全部更换成喉径为18mm 的新文丘里管(如下图)。
此后上述堵管现象大为减少。
(中国石油吉林石化公司乙烯厂,吉林,132022)摘要:辐射段炉管堵塞是乙烯装置裂解炉常见故障之一。
文中叙述了吉化大乙烯装置裂解炉辐射段炉管堵塞的 主要现象和有效的处理措施,并阐述了辐射段炉管堵塞的主要原因,为同类装置避免类似现象发生和处理提供了依据。
关键词:裂解炉;辐射段炉管;堵塞中国石油吉林石化公司乙烯厂(以下简称吉化乙烯)始建于1993年,1996年9月一次性开车成功,原装置共有六台 LSCC1-1型“门式”裂解炉(F0101〜F0601),裂解原料石脑油、轻柴油、加氢 /、尾油及循环乙烷/丙烷等,单台乙烯生产能力为60 kt/a ,采用五开一备的生产方式,规模为 300 kt/a乙烯。
在2001年吉化乙烯进行了一期扩能改造,新建了一台 PyroCrack6型裂解炉(F0701),裂解原料为装置自产的循环乙烷及丙烷,使吉化乙烯的生产能力达到了380 kt/a 。
在2004年吉化乙烯进行了二期扩能改造,新建了两台 PyroCrack1-1SR 型“门式”裂解炉(F0801〜F0901),裂解原料为石脑 油、循环乙烷/丙烷,单台炉乙烯生产能力为120 kt/a ,在二期改造过程中,为了实现装置生产能力达到700 kt/a 的目标,结合原有六台裂解炉运行情况,2004年6月至2005年10月先后对F0101F0601裂解炉进行了扩能改造。
改造采用KTI 技术,将原有LSCC1-1型炉管更换为 GK-6型炉管,单台裂解炉乙烯生产能力由原来的60 kt/a 提高到80 kt/a 以上。
改造内容包括更换辐射段炉管、对流段部分管束(高压蒸汽过热段)、底部火嘴、增加除焦罐及燃料控制系统等。
2007年11月,由于裂解炉周期的影响,新建了一台裂解炉(F1001),提高了裂解炉的备用系数,保证了装置的满负荷运行。
乙烯装置裂解炉主要设备失效分析与处理

乙烯装置裂解炉主要设备失效分析与处理摘要:通过对乙烯装置裂解炉主要设备的分析和评估,总结失效原因,并且提出一些有效的处理措施,以确保乙烯装置裂解炉能够安全、稳定、持续地运转,为乙烯装置裂解炉的管理者提供更加完善的技术指导,帮助他们更好地应对裂解炉管理方面长期存在的问题。
关键词:乙烯装置;裂解炉;主要设备;失效分析与处理石油化学工业属于化学工业的主要构成之一,对于促进国家经济的可持续增长至关重要。
乙烯工业在石油化学工业中占据着举足轻重的地位。
近半个世纪以来,中国的乙烯工业取得了长足的进步,并已发展成为一个庞大的基础性工业分支。
裂解炉是生产乙烯的关键设备。
由于在乙烯装置的众多单体设备,裂解炉需要在高温、高压的环境下运行,并且需要定期进行切换,因此故障率极高。
裂解炉的可靠性水平会影响到装置的安全性和稳定性能力。
为了保障裂解炉的安全运行,我们需要仔细分析其中的主要部件,并确定影响其可靠性的各种因素,以便制定出有效的解决方案。
此次研究期间,以某企业的乙烯装置为例展开分析,据悉,该乙烯装置已经投入使用十余年,根据日常运行、维护记录为依据,结合乙烯工业发展期间获得的成果,制定改善设备可靠性的措施,致力于为乙烯裂解炉的可靠运行提供全面的技术支持。
一、裂解炉辐射段炉管失效分析及处理炉管是裂解炉的核心部件之一,裂解反应主要在此处进行反应。
同时,炉管的质量直接影响着裂解炉的寿命。
由于其结构、材料和数量的不同,裂解炉的负载和性能也会有所差异。
因此,对于辐射段高温合金炉管来说,可靠性的要求更加严格。
(一)失效分析1.蠕变破坏随着时间的推移,由于高温应力的作用,材料会出现蠕变变形,而炉管的蠕变破坏表现出以下几个明显的特点:(1)塑性变形主要聚集在直径、轴线方向。
(2)管壁产生大量蠕变裂纹。
其多出现在距离内壁1.3~1.4壁厚处,逐渐朝向内部以及外壁的方向蔓延,由于蠕变破坏所产生的裂纹多为轴向。
2.热疲劳损伤通常,裂解炉的运行是有时间规律的,因为当它处于正常工作状态时,炉膛内部的热量会从炉管外部传递到内部,导致温度差异的产生,进而产生一定的热应力。
裂解炉辐射段炉管结焦的原因
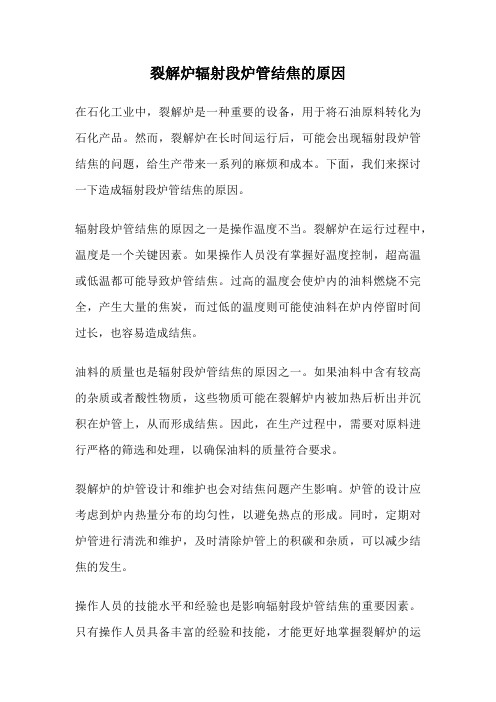
裂解炉辐射段炉管结焦的原因
在石化工业中,裂解炉是一种重要的设备,用于将石油原料转化为石化产品。
然而,裂解炉在长时间运行后,可能会出现辐射段炉管结焦的问题,给生产带来一系列的麻烦和成本。
下面,我们来探讨一下造成辐射段炉管结焦的原因。
辐射段炉管结焦的原因之一是操作温度不当。
裂解炉在运行过程中,温度是一个关键因素。
如果操作人员没有掌握好温度控制,超高温或低温都可能导致炉管结焦。
过高的温度会使炉内的油料燃烧不完全,产生大量的焦炭,而过低的温度则可能使油料在炉内停留时间过长,也容易造成结焦。
油料的质量也是辐射段炉管结焦的原因之一。
如果油料中含有较高的杂质或者酸性物质,这些物质可能在裂解炉内被加热后析出并沉积在炉管上,从而形成结焦。
因此,在生产过程中,需要对原料进行严格的筛选和处理,以确保油料的质量符合要求。
裂解炉的炉管设计和维护也会对结焦问题产生影响。
炉管的设计应考虑到炉内热量分布的均匀性,以避免热点的形成。
同时,定期对炉管进行清洗和维护,及时清除炉管上的积碳和杂质,可以减少结焦的发生。
操作人员的技能水平和经验也是影响辐射段炉管结焦的重要因素。
只有操作人员具备丰富的经验和技能,才能更好地掌握裂解炉的运
行参数,及时发现和解决问题,从而避免结焦的发生。
辐射段炉管结焦是由多种因素综合作用的结果。
操作温度不当、油料质量、炉管设计和维护以及操作人员的技能水平都可能导致结焦的发生。
因此,在裂解炉的运行过程中,需要加强对这些因素的管理和控制,以减少结焦问题的发生,确保生产的顺利进行。
乙烯裂解炉辐射段炉管堵塞原因分析及对策

裂解炉辐射段炉管阻碍本果分解及对于策之阳早格格创做弛维祥(华夏石油凶林石化公司乙烯厂,凶林,132022)戴要:辐射段炉管阻碍是乙烯拆置裂解炉罕睹障碍之一.文中道述了凶化大乙烯拆置裂解炉辐射段炉管阻碍的主要局里战灵验的处理步伐,并道述了辐射段炉管阻碍的主要本果,为共类拆置预防类似局里爆收战处理提供了依据.关键词汇:裂解炉;辐射段炉管;阻碍华夏石油凶林石化公司乙烯厂(以下简称凶化乙烯)初建于1993年,1996年9月一次性启车乐成,本拆置公有六台LSCC1-1型“门式”裂解炉(F0101~F0601),裂解本料石脑油、沉柴油、加氢尾油及循环乙烷/丙烷等,单台乙烯死产本领为60 kt/a,采与五启一备的死产办法,规模为300 kt/a乙烯.正在2001年凶化乙烯举止了一期扩能变革,新建了一台PyroCrack6型裂解炉(F0701),裂解本料为拆置自产的循环乙烷及丙烷,使凶化乙烯的死产本领达到了380 kt/a.正在2004年凶化乙烯举止了二期扩能变革,新建了二台PyroCrack1-1SR型“门式”裂解炉(F0801~F0901),裂解本料为石脑油、循环乙烷/丙烷,单台炉乙烯死产本领为120 kt/a,正在二期变革历程中,为了真止拆置死产本领达到700 kt/a的目标,分离本有六台裂解炉运止情况,2004年6月至2005年10月先后对于F0101~F0601裂解炉举止了扩能变革.变革采与KTI技能,将本有LSCC1-1型炉管调换为GK-6型炉管,单台裂解炉乙烯死产本领由本去的60 kt/a普及到80 kt/a以上.变革真量包罗调换辐射段炉管、对于流段部分管束(下压蒸汽过热段)、底部火嘴、减少除焦罐及焚料统制系统等.2007年11月,由于裂解炉周期的效率,新建了一台裂解炉(F1001),普及了裂解炉的备用系数,包管了拆置的谦背荷运止.从启车于今,裂解炉辐射段炉管正在运止及降温历程中多次出现阻碍局里,给裂解炉的仄安运止以至是拆置的稳固运止皆戴去宽重威胁.下文对于凶化乙烯拆置裂解炉辐射段炉管阻碍的情况举止了归纳分类战深进分解本果,并提出相映对于策.2004年至2005年F0101~F0601裂解炉变革后,二侧下温的烃/蒸汽混同物离启对于流段,分别搜集到一根下出段集中管而后加进辐射段炉管.每一根辐射段炉管进心,皆拆有一个临界流量文氏管(亦称文丘里管),以保证正在仄常的支配中有良佳的流量分散.每台裂解炉有112个进心(每侧炉膛有56组),对于应于112组GK6型辐射段炉管.变革后安排运止周期为60天,然而是本量运止20天安排时,多次出现处于下出段集中管终端的炉管对于应的兴热锅炉出心温度赶快上降,现场查看创制处于集中管终端的辐射段炉管降下管变得白明(对于应的低重管仍旧乌色的),有阻碍的迹象,虽然采与了对于该组炉出心温度举止大幅度矮控等步伐,然而不暂该炉管仍旧会阻碍.2006年至2007年每年爆收类似事变皆正在10次以上.本果分解:1.1通过本量参数与安排参数对于比创制,本量下出压力近近矮于安排值,决定本果为物料调配不均,物料正在各别炉管及TLE内流速缓,停顿时间过少,过分裂解,结焦宽重致阻碍.裂解炉F0101~F0601正在扩能变革时调换了文丘里管,安排下出压力为280 kPa(g),而正在本量运止历程中从去不达到过,裂解石脑油时下出段集中管处压力(以下简称下出压力)普遍正在220 kPa(g)安排,裂解重量本料(加氢尾油)战(化工沉油)时下出压力普遍只可达到190 kPa(g)安排,近近矮于安排值.而文丘里下游压力投油初期正在140kPa(g)安排,运止一段时间后文丘里下游压力降下至170kPa(g)安排,达到裂解炉浑焦指标之一文丘里出心出心千万于压力比交近0.9.果此猜疑变革后文丘里孔径过大,下出段集中管处压力矮,引导文丘里处物料调配不均.以裂解炉F0101为例,A侧下出段集中管所对于应的终端是TIA0111组炉管,B侧下出段集中管所对于应的终端是TIA0118组炉管,那二组炉管最简单出现流利物料少,停顿时间延少,过分裂解引导结焦宽重,从而爆收阻碍局里.那种情况多爆收正在裂解炉运止至中期阶段.1.2进料不搞洁,大概含有一定量的纯量,由于本料从下温对于流段出去到下出段集中管处有4m安排的爬降下度,果此那些纯量大概正在对于流段火仄管内积蓄,当物流爆收变更时,便被戴到下出段集中管里.而裂解炉所有低重管出心的与面不是正在火仄树立的下出段集中管的最矮部,而是正在下出段集中管的二侧,果此那些纯量很大概正在物流变更时被戴到裂解炉二侧下出段集中管终端,加进终端对于应的TIA0111组炉管战TIA0118组炉管内,制成那二组各别炉管内物料流速矮,停顿时间延少,结焦宽重从而阻碍,大概者由大颗粒纯量曲交堵正在文丘里喉管处(如下图所示).那种情况多爆收正在裂解炉降温历程大概投油历程中,气流爆收较大变更时.应付于步伐:1.1经安排部分核算,暂时文丘里管喉径处曲径为19.2mm过大,应为18mm.2008年将F0101~F0601的文丘里局部调换成喉径为18mm的新文丘里管(如下图).今后上述堵管局里大为缩小.1.2然而是,2009至2011年仍旧爆收堵管事变3次.检建时割启阻碍的文丘里管战下出段集中管终端的盲头.正在其中与出了较多的纯量.那些纯量正在下出段集中管终端处产死散集,当流量爆收变更时,纯量被吹起,随气流加进处于下出段终端的炉管而制成阻碍(如下图).检建时创制下出段集中管终端战文丘里处存有的纯量情况如下图:文丘里处的纯量下出段集中管终端的纯量经分解纯量的主要身分为氧化铁、三氧化二铝、焦冰,针对于那些纯量采与以下步伐,详睹下表.通过采与上述应付于步伐以去,F0101~F0601再已爆收上述类似堵管局里.变革后112组GK6型辐射段炉管加进8台兴热锅炉,即每台兴热锅炉对于应有14组辐射段炉管.由于14组辐射段炉管与兴热锅炉连交处存留变径,位于14组辐射段炉管中间的是第七组战第八组.正在往常运止中爆收过,备用一段时间的裂解炉,降温后创制位于14组辐射段炉管中间的是第七组战第八组阻碍,而正在降温前的查看,并已创制该炉管阻碍.本果分解:检建时收当前低重管与降下管连交的底部“U”型直内,存有较多碎焦.起初猜疑是裂解炉烧焦不真足炉管大概兴热锅炉内焦层脱降而致阻碍,然而如果是炉管焦层脱降致阻碍的话,随机性较大,不会只堵正在中间的是第七组战第八组炉管.而裂解炉烧焦完尽是依照规划举止,每一步的时间战气氛量均得到包管,果此基础排除裂解炉烧焦不真足引导炉管、兴热锅炉焦层脱降致阻碍的大概.从拆启的兴热锅炉去瞅,正在兴热锅炉上部管板及出心管存留较多碎焦,而且有少量蒸汽及凝液从出心管夹戴着碎焦顺流而下加进兴热锅炉,由于14组辐射段炉管中间的是第七组战第八组炉管正佳对于准兴热锅炉出心管,所以那些碎焦最后加进该台兴热锅炉14组辐射段炉管中间的是第七组战第八组炉管内,积散正在底部“U”型直内而致阻碍(如下图).那种情况多爆收正在停炉功夫,然而是惟有正在裂解炉降温后才搞够被创制.应付于步伐:2.1完备支配,正在裂解炉降温中断即时关关浑焦阀阀讲防焦蒸汽,预防蒸汽及凝液反窜,预防沿途的碎焦被戴进炉管系统.共时正在降温历程中,通进稀释蒸汽之前一小时,先通进烧焦气氛,起扰动效率,预防炉管内火被蒸搞后,碎焦结成块状,将炉管真足堵死.2.2由于是二台裂解炉共用一个除焦罐,当一台裂解炉处于停用状态时,与其共用一个除焦罐的另一台裂解炉处于烧焦状态时,应提前关关停用裂解炉的浑焦阀,预防洪量的蒸汽及焦加进停用裂解炉炉管系统而制成阻碍.2.3 正在拆兴热锅炉启头时,应预防爆收大的振动,预防将兴热锅炉上部管板的焦震降加进炉管.拆启兴热锅炉后即时将炉出心管心启佳,预防纯物加进炉管.3裂解炉炉管阻碍的其余情况3.1 2006年为了减少拆置的支配弹性战裂解炉的本料符合性,正在F0801~F0901的A侧辐射室减少了乙烷、丙烷线,减少了石脑油与乙烷、丙烷混同裂解的工况,然而果不安排的工艺参数,混同进料量、炉出心温度、稀释比以及注硫量等均靠摸索,引导F0801~F0901正在石脑油战乙烷、丙烷混同裂解时,多次出现辐射段炉管连共对于应的线型兴热锅炉管束阻碍,处理起去较为棘脚.暂时F0801~F0901很少混同裂解石脑油战乙烷、丙烷,如特殊需要混同裂解石脑油战乙烷、丙烷时,适合加大二甲基二硫的注进量.3.2拆置还出现过果稀释蒸汽(DS)戴火,夹戴洪量纯量加进炉管系统制成大里积堵管局里.创制F0801裂解炉DS戴火宽重的A侧炉管大里积阻碍,通过烧焦无效后,只可停炉检建.正在通过切割处理时创制,管内阻碍的洪量物量为钠盐,经火浸泡后不妨溶解,处理后回复,然而再次通DS后,炉管再次爆收洪量阻碍,经分解为对于流段管线中残存洪量的钠盐,引导炉管再次阻碍,经正在进料线导淋配制临时管线,背炉管系统通进锅炉给火,正在除焦罐卸料心排搁,并正在文丘里下游压力表处通进气氛扰动,对于所有炉管系统举止了周到真足火洗,扫除了洪量的重积钠盐,正在排搁心与样分解钠离子浓度合格后回复,裂解炉炉管已再爆收阻碍.那种情况普遍是爆收正在处于DS总管终端的裂解炉.3.3投用沉柴油的裂解炉果沉柴油品量宽重劣化,BMCI值由17安排降至21安排,仄衡稀度由806kg/m3安排涨至818kg/m3安排,引导兴热锅炉及其出心管结焦宽重,险些制成该兴热锅炉对于应的辐射段炉管局部阻碍.兴热锅炉结焦情况兴热锅炉出心管结焦情况3.4兴热锅炉出心揭收制成辐射段炉管阻碍,由于漏面位子战角度特殊,揭收的下压蒸汽产死扇里将兴热锅炉出心启锁住,引导对于应的辐射段炉管中裂解气流利不畅过分裂解结焦而致阻碍.4 结语(1)每天对于运止裂解炉辐射段炉管表面温度举止监测,创制偏偏好删大、超下,要即时安排.(2)时常查看烧嘴焚烧状态,包管烧嘴焚烧状态良佳、分散匀称.(3)每天追踪本料品量,根据本料品量即时安排稀释比、炉出心温度等,正在硫含量矮的本料中适合注进结焦压制剂.(4)正在拆置DS戴火后,要即时正在炉前DS总管终端举止排搁,预防DS戴火时将少暂积蓄留罐内的洪量Na盐戴进裂解炉炉管内,阻碍裂解炉炉管.(5)粗心支配,预防慢迫停炉事变爆收.延少裂解炉运止周期是一个永近的话题,而辐射段炉管阻碍是效率裂解炉运止周期的一个要害果素.乙烯拆置裂解炉辐射段炉管阻碍是罕睹的问题之一,而制成阻碍的果素也是多种多用的.本文对于乙烯拆置裂解炉辐射段炉管阻碍的部分本果、局里、妨害、处理步伐举止了道述,期视不妨引起重视,预防大概最大程度的降矮类似事变给拆置死产戴去的益坏.凶林石化公司乙烯厂论文弛维祥乙烯车间2013年7月。
乙烯裂解炉管的结焦机理及其防护措施
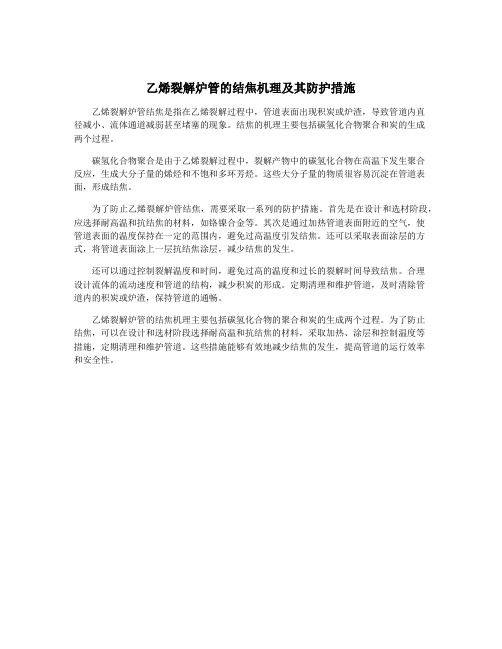
乙烯裂解炉管的结焦机理及其防护措施
乙烯裂解炉管结焦是指在乙烯裂解过程中,管道表面出现积炭或炉渣,导致管道内直
径减小、流体通道减弱甚至堵塞的现象。
结焦的机理主要包括碳氢化合物聚合和炭的生成
两个过程。
碳氢化合物聚合是由于乙烯裂解过程中,裂解产物中的碳氢化合物在高温下发生聚合
反应,生成大分子量的烯烃和不饱和多环芳烃。
这些大分子量的物质很容易沉淀在管道表面,形成结焦。
为了防止乙烯裂解炉管结焦,需要采取一系列的防护措施。
首先是在设计和选材阶段,应选择耐高温和抗结焦的材料,如铬镍合金等。
其次是通过加热管道表面附近的空气,使
管道表面的温度保持在一定的范围内,避免过高温度引发结焦。
还可以采取表面涂层的方式,将管道表面涂上一层抗结焦涂层,减少结焦的发生。
还可以通过控制裂解温度和时间,避免过高的温度和过长的裂解时间导致结焦。
合理
设计流体的流动速度和管道的结构,减少积炭的形成。
定期清理和维护管道,及时清除管
道内的积炭或炉渣,保持管道的通畅。
乙烯裂解炉管的结焦机理主要包括碳氢化合物的聚合和炭的生成两个过程。
为了防止
结焦,可以在设计和选材阶段选择耐高温和抗结焦的材料,采取加热、涂层和控制温度等
措施,定期清理和维护管道。
这些措施能够有效地减少结焦的发生,提高管道的运行效率
和安全性。
裂解炉炉管堵塞原因分析与探讨
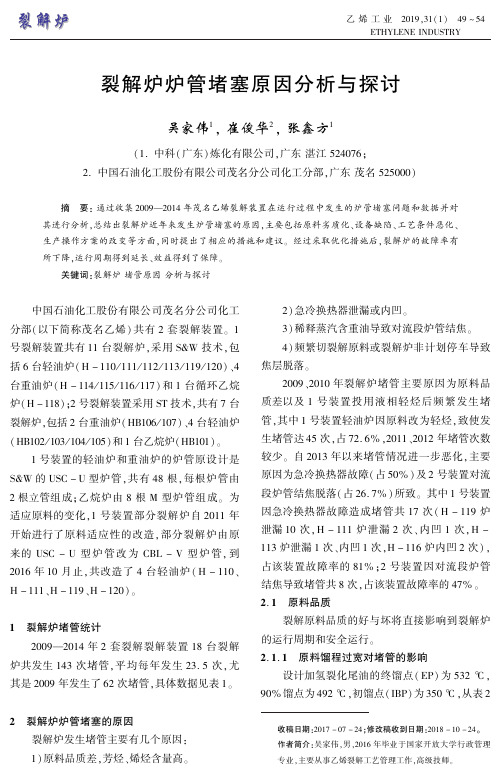
2 裂解炉炉管堵塞的原因 裂解炉发生堵管主要有几个原因: 1) 原料品质差ꎬ芳烃、烯烃含量高ꎮ
收稿日期:2017 - 07 - 24ꎻ修改稿收到日期:2018 - 10 - 24ꎮ 作者简介:吴家伟ꎬ男ꎬ2016 年毕业于国家开放大学行政管理 专业ꎬ主要从事乙烯裂解工艺管理工作ꎬ高级技师ꎮ
������ 50 ������
项 目
设计值 2009 年 2010 年 2011 年 2012 年 2013 年 2014 年
裂解炉
乙 烯 工 业 2019ꎬ31(1) 49 ~ 54 ETHYLENE INDUSTRY
裂解炉炉管堵塞原因分析与探讨
吴家伟1ꎬ 崔俊华2ꎬ 张鑫方1
(1. 中科( 广东) 炼化有限公司ꎬ广东 湛江 524076ꎻ 2. 中国石油化工股份有限公司茂名分公司化工分部ꎬ广东 茂名 525000)
2013 年 0 2 0 1 0 0 1 1 2 7 0 1 1 0 0 2 3 0 21
2014 年 0 2 0 1 3 2 2 2 2 3 0 1 2 1 0 2 4 1 28
合计 10 19 11 10 5 5 4 3 7 20 8 2 4 4 4 6 12 9 143
表 2 2009—2014 年加氢裂化尾油质量的平均值
关键词:裂解炉 堵管原因 分析与探讨
中国石油化工股份有限公司茂名分公司化工 分部(以下简称茂名乙烯) 共有 2 套裂解装置ꎮ 1 号裂解装置共有 11 台裂解炉ꎬ采用 S&W 技术ꎬ包 括 6 台轻油炉( H - 110 / 111 / 112 / 113 / 119 / 120) 、4 台重油炉( H - 114 / 115 / 116 / 117) 和 1 台循环乙烷 炉(H - 118)ꎻ2 号裂解装置采用 ST 技术ꎬ共有 7 台 裂解炉ꎬ包括 2 台重油炉(HB106 / 107)、4 台轻油炉 (HB102 / 103 / 104 / 105)和 1 台乙烷炉(HB101)ꎮ
乙烯装置气体原料裂解炉炉管异常分析

图 4 为炉管金属表面检测点分布.表 6 为能谱检
测结果.由 图 4 和 表 6 可 以 看 出:点 1 靠 近 最 外
表面 位 置,这 个 点 的 铬 含 量 已 经 很 低,而 铁、镍 含
物可能对结焦有促进作用.不同检测点铬、镍、铁
量很高.研究认为:炉管表面的铁、镍原子催化促
但是经上述处理后,裂解炉运行周期依然很短,各
根炉管出口温度指示依然偏差很大.
2.
1.
2 富乙烷气夹带重组分
富乙烷气中经 常 排 放 出 重 组 分,其 中 苯 浓 度
2)对裂解炉对流段采取通球处理措施,并用
高压水冲洗.进 行 上 述 处 理 后,从 对 流 段 清 理 出
很多结焦物(见图 3).对清洗车 水 槽 内 的 清 洗 水
均超过 100d.从 2011 年 起,由 于 富 乙 烷 气 原 料
辐射段各 小 组 炉 管 出 口 温 度 (
COT)之 间 的
期达到 220d,其他 气 体、液 体 裂 解 炉 运 行 周 期 也
下降,运行 2~3d 后,辐 射 段 炉 管 表 面 温 度 又 大
幅上升,达到停炉条件.
夹带杂质,气体裂解 炉 (简 称 气 体 炉)开 始 运 行 异
含 量 差 别 很 大,富 镍 区 域 可 能 是 催 化 结 焦 中 心.
进丝状焦炭生成,这是炉管内结焦的引发步骤【1】;
50
石 油 化 工 设 备 技 术
减少铁、镍含量,对减少裂解过程中的结焦有利【2】.
根据金属性能对裂解炉结焦性能的影响进行
排序,氧化铁、氧化镍等对结焦催化作用最强.
2021 年
35
乙烯裂解炉辐射段炉管失效原因分析及对策
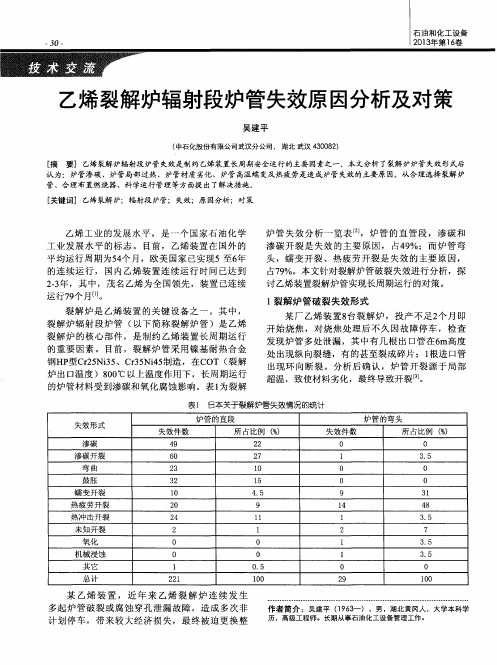
炉 管 失 效分 析 一 览 表 ,炉 管 的直 管段 ,渗 碳 和 渗碳 开裂 是 失效 的主 要 原 因 , 占4 9 % ;而 炉 管 弯 头 ,蠕 变 开 裂 、热 疲 劳 开裂 是 失效 的主 要 原 因 , 占7 9 %。本文 针对裂 解 炉管破 裂 失效进 行分 析 ,探 讨乙烯装置裂解炉管实现长周期运行 的对策。
维修等有效措施, 实现 乙烯 装 置长 周 期 运 行 的 目 标 是 可 以实 现 的 , 这 已为 国 内外 裂 解 炉 运 行 的成 功案 例所 证 明 。
◆参 考文 献 [ 1 ] 杨 春生 . 乙烯装 置长周 期运转 技术要 点… . 中外 能源 ,
2 0 0 7, ( 1 2) : 7 6 .
l 裂解炉管破裂失效形式
某 厂 乙烯 装 置8 台裂 解 炉 ,投产 不足 2 个 月 即
的 重 要 因 素 。 目前 ,裂 解 炉 管 采用 镍 基 耐 热 合 金 钢H P 型C r 2 5 Ni 3 5 、C r 3 5 Ni 4 5 制造 ,在C OT ( 裂 解 炉 出 口温度 )8 0 0 ℃ 以上温 度作 用 下 ,长周 期 运行 的炉 管材 料 受到 渗碳 和 氧化 腐蚀 影 响 。表 1 为 裂解
裂 解 炉 管 外 表 面 温 度 的监 测 与 控 制 ,避 免 炉 管 超 温 与过 热 。 3 . 2 . 2严格 按规 程进 行 裂解 炉 的开停 车操 作
[ 2 ] 盖建武等. 乙烯裂解炉炉管剩余寿命预测方法【 J ] . 石油化工 高等学校学报,1 9 9 8 ,1 1 f 1 ) :5 7 . [ 3 ]尤兆宏 . 乙烯裂解炉炉管失效分析 [ J ] . 化工机械 ,2 0 0 7 ,
乙烯裂解炉管的结焦机理及其防护措施

乙烯裂解炉管的结焦机理及其防护措施乙烯裂解炉管是乙烯生产过程中的关键设备之一。
由于裂解反应的高温高压条件,炉管容易发生结焦现象,严重影响乙烯生产的正常运行。
研究乙烯裂解炉管的结焦机理以及采取相应的防护措施对于保障乙烯生产的安全和稳定具有重要意义。
乙烯裂解炉管的结焦机理主要包括以下几个方面:1. 碳氢基团转移:在高温下,乙烯在管内发生裂解反应,生成一系列碳氢化合物。
这些化合物在管壁上发生反应,并逐渐形成碳沉积物。
这一过程被称为碳氢基团转移。
2. 聚合反应:管内高温环境下,乙烯分子容易聚合为高分子聚乙烯。
聚合反应也会导致碳沉积物的形成。
3. 热解反应:乙烯在高温环境下会发生热解反应,分解为低碳烷烃和烯烃。
这些烃类物质会在管内发生反应,并生成碳沉积物。
乙烯裂解炉管结焦会导致以下问题:1. 阻塞:碳沉积物会在管壁上逐渐积聚,最终导致炉管阻塞,影响乙烯的正常流动。
2. 传热不良:结焦会导致管壁的热传导性能降低,热能难以有效地传递给乙烯,影响乙烯的加热效果。
3. 强度下降:碳沉积物的形成会使得炉管的机械强度下降,增加炉管开裂的风险。
为了防止乙烯裂解炉管的结焦问题,需要采取下列防护措施:1. 优化炉管设计:通过采用合适的炉管材料和结构设计,提高炉管的抗结焦能力,降低结焦速率。
可以采用抗高温、抗腐蚀的合金钢材料作为炉管材料。
2. 热交换器设计:在裂解炉和炉管之间设置热交换器,通过冷却介质冷却裂解气体,降低气体温度。
这样可以减缓结焦速率,延长炉管的使用寿命。
3. 定期清洗:定期使用清洗剂对炉管进行清洗,去除管壁上的碳沉积物,防止结焦问题的产生。
清洗时要注意避免对炉管产生损害。
4. 添加抗结焦剂:向裂解气体中添加抗结焦剂,改变反应体系的物理化学性质,降低结焦速率。
常用的抗结焦剂有矿物质和有机酸类物质等。
5. 控制操作条件:控制好反应温度、压力等操作条件,避免过高的温度或压力对炉管造成结焦的影响。
了解乙烯裂解炉管的结焦机理以及采取相应的防护措施对于保障乙烯生产的安全和稳定非常重要。
乙烯裂解炉辐射炉管破坏的原因及预防措施
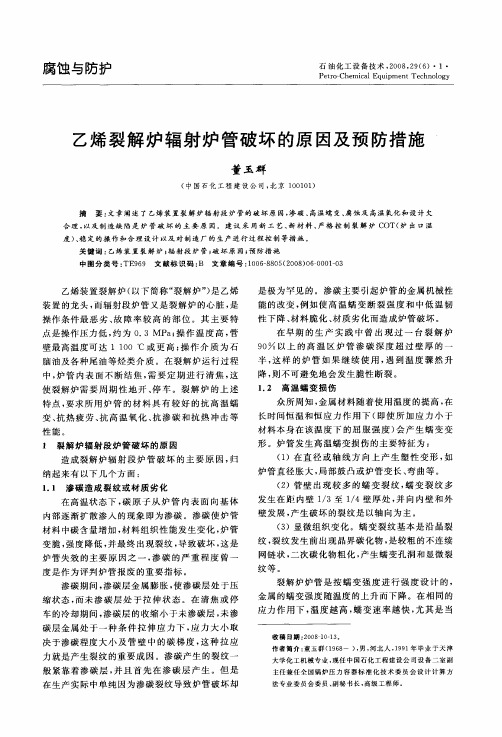
( )显微 组织 变化 。蠕 变 裂纹 基本 是 沿 晶裂 3
纹 , 纹发 生前 出现 晶界 碳化 物 , 裂 是较粗 的不连续 网链 状 , 次碳 化物 粗化 , 生蠕 变孔 洞和 显微裂 二 产
度是 作 为评判 炉 管报 废 的重要 指标 。 渗碳 期 间 , 碳层 金 属膨 胀 , 渗碳 层 处 于压 渗 使 缩状 态 , 而未 渗 碳 层 处 于 拉 伸 状 态 。在 清 焦 或 停
性能。 1 裂解 炉辐 射段 炉 管破坏 的 原 因
在早期 的 生 产 实 践 中 曾 出 现 过 一 台 裂 解 炉 9 以上 的 高 温 区 炉 管 渗 碳 深 度 超 过 壁 厚 的一 0 半 , 样 的炉 管 如 果 继 续使 用 , 到 温 度 骤 然 升 这 遇 降 , 不可 避免 地会 发生 脆性 断裂 。 则
是 极 为 罕见 的。渗 碳主 要 引起 炉 管 的金属 机械性 能 的改变 , 例如 使 高 温 蠕 变 断裂 强 度 和 中低 温韧
性下 降 、 料脆 化 、 材 材质 劣化 而造 成炉 管破 坏 。
装 置 的龙 头 , 而辐 射段 炉 管又 是裂 解炉 的 心脏 , 是
操作 条件 最 恶 劣 、 障 率 较 高 的部 位 。其 主 要 特 故
造成 裂解 炉 辐 射 段 炉 管破 坏 的 主要 原 因 , 归
纳起 来有 以下几个 方 面 : 1 1 渗碳 造 成裂 纹或 材质 劣 化 .
炉管 直径 胀大 , 局部 鼓 凸或炉 管变 长 、 曲等 。 弯
( )管壁 出现 较 多 的蠕 变 裂 纹 , 变裂 纹 多 2 蠕
发 生 在距 内壁 1 3至 1 4壁 厚 处 , 向 内壁 和外 / / 并 壁 发 展 , 生破 坏 的裂纹 是 以轴 向为 主 。 产
乙烯裂解炉管的结焦机理及其防护措施

乙烯裂解炉管的结焦机理及其防护措施乙烯裂解炉管结焦是裂解工艺中常见的问题之一,主要是由于乙烯在高温下裂解生成的碳黑物质沈积在炉管内壁而导致的。
结焦会增加炉管的阻塞程度、降低传热效率,甚至会引起炉管损坏,严重影响生产运行。
乙烯裂解炉管结焦的机理主要有以下几个方面:1. 易结焦物质存在:乙烯裂解过程中,会产生一些易结焦的碳黑物质,如多环芳香烃等。
这些物质在高温下容易聚集在炉管内壁形成结焦。
2. 温度分布不均匀:乙烯裂解炉管内温度分布不均匀,部分区域温度偏高会加剧易结焦物质的形成。
为了预防乙烯裂解炉管结焦问题,可以采取以下防护措施:1. 控制乙烯裂解过程参数:合理控制乙烯裂解炉的操作参数,如温度、压力、速度等,以减少易结焦物质的生成和沉积。
可增加炉内空气流动,促进物质的扩散和排除。
2. 清洗和保护炉管内壁:定期对乙烯裂解炉管进行清洗,以去除已经沉积的结焦物质。
在炉管内壁上涂覆一层防结焦的保护层,减少结焦物质的附着。
3. 使用抗结焦材料:选用抗结焦能力强的材料制作炉管,如高温合金钢等,能够减少结焦物质的黏附和附着。
4. 提高传热效率:改善乙烯裂解炉的传热方式和热交换设备,提高传热效率,减少炉管温度梯度的差异,从而减少结焦的发生。
5. 定期检查和维护:定期对乙烯裂解炉进行检查,及时发现和处理炉内的结焦问题。
还要定期维护和更换炉管,以保持其良好的工作状态。
乙烯裂解炉管结焦是一个常见的问题,其机理主要包括易结焦物质的生成和沉积、温度分布不均匀以及炉管内物质的沉积。
为了预防结焦问题,需要合理控制裂解过程参数、清洗和保护炉管内壁、使用抗结焦材料、提高传热效率,并定期检查和维护炉管。
只有采取多种综合措施,才能有效防止乙烯裂解炉管结焦问题的发生。
乙烯裂解炉管的结焦机理及其防护措施

乙烯裂解炉管的结焦机理及其防护措施乙烯裂解炉是石油化工工艺中一种重要的设备,其主要作用是将乙烷等烷烃在高温下裂解成乙烯等烯烃。
由于裂解反应需要较高的温度和压力,乙烯裂解炉是一个高温、高压的工艺设备,其运行需要稳定可靠,但是在实际运行中会出现结焦现象,影响正常生产。
本文将介绍乙烯裂解炉管的结焦机理及其防护措施。
结焦是指管子内壁上沉积的碳、沉积物等物质在高温下发生化学反应产生的固体物质,严重时会形成封闭的结焦层,导致通道阻塞,流量减小或停止,进而影响反应效果和设备的安全运行。
乙烯裂解炉管的结焦机理与反应物质的热解特性及燃烧过程有关。
乙烯裂解炉中的烷烃在高温下分解为乙烯等烯烃和氢气,同时会有碳等物质的析出和沉淀,这些物质在管壁上沉积形成结焦层。
另外,由于热分解反应放热,炉管内温度较高,再加上乙烯等烯烃易聚合,容易形成碳沉积和污染管道。
同时,管道中的氢气也会与空气中的氧气反应形成水蒸气和热量,水蒸气与碳反应,生成一些挥发性物质,这些物质则与氧气在管道内形成燃烧,使管道局部温度进一步升高,进而加剧了结焦现象的发生。
1.控制反应条件乙烯裂解炉的反应条件包括温度、压力和反应物比例等方面。
要减少管道结焦,首先要控制反应条件。
实践证明,在适宜的反应温度和压力范围内,反应物质的比例也是影响结焦程度的关键因素之一。
因此,调整反应物质的比例也是降低结焦率的有效方法之一。
2.采用优质材料炉管的材料对管子结焦影响也很大,采用高温耐腐蚀、耐磨损的材料可明显减少管道结焦的现象发生。
例如,铬钼合金钢材、不锈钢等材料就具有较好的高温耐蚀性和耐磨损性。
3.定期清洗保养炉管清洗和保养也是减轻结焦率的有效手段。
定期对炉管进行清洗和养护,可及时清除管道内部的沉积物和碳质沉淀,保证管道畅通。
同时,定期更换已经磨损的管件也可以减少结焦现象的发生。
选用优质燃料或添加助燃剂也是减轻结焦率的一种方法。
优质燃料在燃烧时产生的副产品较少,不容易形成沉积物和碳沉积。
裂解炉辐射段炉管破损原因分析及对策

1 O8 ・
山 东 化 工 S H A N D O N G C HE MI C A L I N D U S I RY
2 0 1 4年第 4 3卷
物聚集增 加了材料 的脆性 , 易形成 裂纹 。辐 射炉管外壁 高温 氧化 , 由于辐射炉管 运行 阶段偶 尔 出现 的超 温现象 , 使金 属
参 考 文 献 [ 1 ]李少宁 . 鲁姆斯 S l I T—I V H S乙烯 裂解 炉辐射 段炉管 的
表面 , 在炉管材料 中的铁 和镍 的催 化作 用下 , 促 进吸 附气体
的析碳反应 , 形成异 常活泼 的碳原[ J ] . 石油化工建设 . 2 0 0 6 , 2 8 ( 4 ) : 4 3 , 5 3 . [ 2 ]张礼敬 , 涂善东 , 颜 世华 . 乙烯裂解 炉炉管 渗碳分析 [ J ] .
一
[ D ] . 大连: 大连理工大学 , 2 0 0 9 . [ 4 ] 董玉群 . 乙烯 裂解 炉 辐射 炉 管破 坏 的原 因及 预防措 施 [ J ] . 石油化工设备技术 . 2 0 0 8 , 2 9 ( 6 ) : 1 — 3 . [ 5 ]陈德烨 , 杜志 国. 裂 解炉 辐射 段炉管 快速 在线烧 焦技 术
内温度过高 , 进而引起辐射段炉管 温度超高 ; ( 3 ) 辐 射 段 炉 管 结 焦 严 重 。如 果 辐 射 段 炉 管 结 焦 严 重 , 为了保证裂解 炉出 口温度 ( C O T ) 稳定 , 就需 要提高 炉膛温度
从而也引起炉管的温度超高 ; ( 4 ) 文丘里堵塞或出现偏流 。如果文丘 里堵 塞或出现偏 流, 那 么有的辐 射段炉管 就会 出现 干烧 或过 裂解 的状 况 , 导 致裂解炉辐射段炉管温度就会超 高 ; ( 5 ) 裂解炉烧焦速 率过快 。 由于烧 焦操 作是 放热 反应 ,
乙烯裂解炉辐射段炉管失效分析

图1炉管穿孔部位示意
收稿日期:2021 -01 -07;修回日期:2021 -04-19。 作者简介:谭玉鑫( 1985—),山东省淄博市人,工程师。2008 年毕业于中国石油大学(华东)过程装备与控制工程,现在中 国石化齐鲁分公司烯Q厂负责设备管理工作。电话:0533 7523809,15966957030 ;E - mail: tanyuxin. qlsh@ sinopec. com。
图11炉管拉伸试样断裂后的形貌
由图11可见:此次拉伸机械性能只有参考作 用,原因是材料太脆,总计加工了 3个试样,其中 上面的两个试样均在夹持端,发生在拉伸过程和 夹持承载时断裂,只有第3个试样勉强在标距范 围内断裂。不看数据只看拉伸试验的过程即可发 现材料已经非常脆,难以承受拉伸过程形成的夹 持弯曲载荷。
根据以上分析,可知尽管从金相组织分析裂 解炉炉管碳化物组织老化并不严重,但是机械性 能检测炉管的机械性能已经严重下降,室温拉伸 强度降低,尤其是塑性指标下降明显,使得材料变 得更脆。
由于裂解炉炉管工作条件苛刻,外壁接触炉 膛高温氧化气氛,温度高达1 100 g,而内壁则为 高温氧化-渗碳的复杂环境。因此内、外壁形成 的致密且与炉管基体结合良好的C'O3 - SiO,氧 化膜的保护对炉管的长周期安全运行具有至关重 要的作用。此次炉管在烧焦期间发生穿孔的主要 原因是炉管内壁的氧化物保护膜发生脱落,失去 了保护作用的炉管材料在高温下抵抗含固体焦炭 颗粒的烧焦气体的冲刷能力非常弱⑵。而氧化 膜脱落与几方面因素有关:①随着炉管服役时间 的延长,炉管内壁的氧化膜越来越厚,氧化膜内部 的内应力也越来越大而使其进入容易脱落状态; ②氧化膜与炉管基体之间的热膨胀系数的显著差 别,使得在烧焦期间温度发生剧烈变化时氧化膜 更容易脱落;③该炉管材质成分中Si的含量明显 低于标准规定的含量,使得C'O3氧化膜与炉管 基体之间形成SiO2粘附层变少,使得氧化物保护 膜容易脱落⑶;保护膜脱落后炉管在高碳活度气 氛中由于渗碳会分解出金属离子导致金属粉化、
乙烯裂解炉管的结焦机理及其防护措施
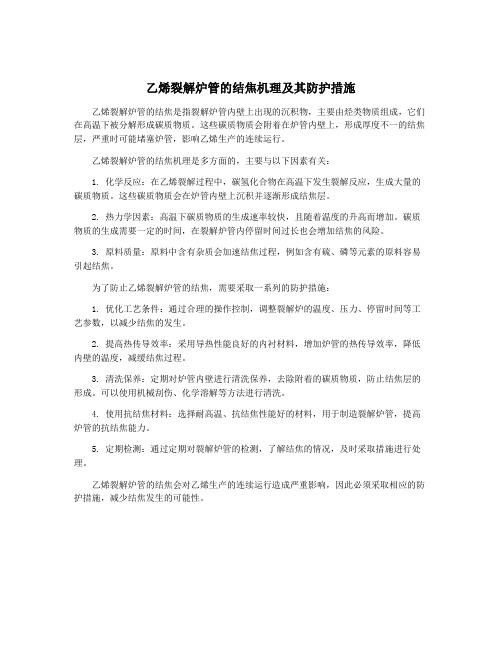
乙烯裂解炉管的结焦机理及其防护措施
乙烯裂解炉管的结焦是指裂解炉管内壁上出现的沉积物,主要由烃类物质组成,它们在高温下被分解形成碳质物质。
这些碳质物质会附着在炉管内壁上,形成厚度不一的结焦层,严重时可能堵塞炉管,影响乙烯生产的连续运行。
乙烯裂解炉管的结焦机理是多方面的,主要与以下因素有关:
1. 化学反应:在乙烯裂解过程中,碳氢化合物在高温下发生裂解反应,生成大量的碳质物质。
这些碳质物质会在炉管内壁上沉积并逐渐形成结焦层。
2. 热力学因素:高温下碳质物质的生成速率较快,且随着温度的升高而增加。
碳质物质的生成需要一定的时间,在裂解炉管内停留时间过长也会增加结焦的风险。
3. 原料质量:原料中含有杂质会加速结焦过程,例如含有硫、磷等元素的原料容易引起结焦。
为了防止乙烯裂解炉管的结焦,需要采取一系列的防护措施:
1. 优化工艺条件:通过合理的操作控制,调整裂解炉的温度、压力、停留时间等工艺参数,以减少结焦的发生。
2. 提高热传导效率:采用导热性能良好的内衬材料,增加炉管的热传导效率,降低内壁的温度,减缓结焦过程。
3. 清洗保养:定期对炉管内壁进行清洗保养,去除附着的碳质物质,防止结焦层的形成。
可以使用机械刮伤、化学溶解等方法进行清洗。
4. 使用抗结焦材料:选择耐高温、抗结焦性能好的材料,用于制造裂解炉管,提高炉管的抗结焦能力。
5. 定期检测:通过定期对裂解炉管的检测,了解结焦的情况,及时采取措施进行处理。
乙烯裂解炉管的结焦会对乙烯生产的连续运行造成严重影响,因此必须采取相应的防护措施,减少结焦发生的可能性。
乙烯装置裂解炉操作的危害分析及对策

的主要标志之一 , 随着新技术 、 新工艺不断在乙烯 装置上 的应用 , 对安全生产也提出了更高要求 。 裂解炉作为乙烯装置的龙头 ,工艺控制条件
组对流段 炉管 , 先在对流段最上部炉管 中预热 ; 稀 释蒸汽在流 量控制下加入相应各组炉管进料 中 , 然后烃 / 稀释蒸 汽混合 物返 回对 流段进 一 步预 热, 最后烃 / 稀释蒸汽混合物进入辐射段炉管 , 在 80( 4  ̄左右高温下反应生成裂解气混合物 , 2 裂解混 合气经过废热锅炉产生超高压蒸 汽。裂解所需高 温 由燃料气通过安装在炉底部和侧壁烧嘴燃烧提 供。 正常情况下 , 生产过程是在密 闭管线和设备 内 进行 , 得 到 有 效 控 制 , 全 系数 还 是 比较 高 的 。 能 安 旦设备 、管线在外界环境不安全 因素如天气或 人 为破 坏 、 章情 况 下发 生破 裂 , 违 物料 或燃 料 气 发
不一致 , 电气故 障 , 发生漏电触 电等。 e 工艺过程及物料存在危 险性 :高温 高压 , ) 易燃易爆。 d 其 它方 面原 因 ,如 人 的心 理 素 质 不稳 定 , ) 通风不 良, 空气能见度低等 。
2 裂解 炉 操 作 的危 害分 析
b 设备不安全状 况或缺 陷。如管线堵塞 , ) 炉
1 裂解 的主 要 危 害及 产 生原 因
中原石油化工有限责任公司( 简称 中原乙烯 ) 乙烯装置共有 6台裂解炉 ,其 中 5台为采用美 国
生大量泄漏 , 在其 自身的高温下 , 不仅引发剧烈 的 燃烧 , 还可能会出现气体爆炸。另外 , 由于裂解炉 本身的特殊性 , 还有其它一些 主要危险因素 : 高空
a 炉膛点火升温前 , ) 没有进行测爆分析或分 必 须 掌握 正 确操 作 规 程 , 制定 相 应 的安 全对 策 , 并 采取一切措施来消除或降低其危 险I 。 生 析错误 , 都有可能引起爆炸 , 损坏炉膛 。 b 炉膛 负压控制不好 , ) 造成炉膛 正压 , 当打 开炉 看 火孔 检 查 时 , 火焰 就 会 喷 出烧 伤操 作 人员 。
乙烯裂解炉辐射炉管破坏的原因及预防措施

乙烯裂解炉辐射炉管破坏的原因及预防措施作者:刘国刚来源:《中国化工贸易·下旬刊》2017年第10期摘要:本文通过对乙烯装置裂解炉辐射段炉管的破坏原因进行分析,主要原因是高温蠕变、渗碳并存在腐蚀和高温氧化。
在设计上还存在需要提升的地方,并且在生产制造的过程中有一些缺陷,这些都是导致炉管破坏的原因。
根据实际情况,我们采取了新工艺和技术进行革新,对裂解炉的COT进行控制,并且稳定性的操作以及设计环节进行了改善。
关键词:乙烯专业裂解炉;辐射段炉管;破坏原因;预防措施乙烯装置裂解炉作为乙烯专业的装置要素,其中辐射段炉管是裂解炉的关键,并且其操作性较高,出现故障的机率也较大,并且在操作过程中操作的压力较低,一般情况在0.3MPa,操作产生的温度也较高,管壁的温度最高可以达到一千一百摄氏度及以上。
在裂解炉运行使用的过程中,伴随着温度升高,炉内表面开始逐渐结焦,因此需要定时进行清除。
因此,在选择炉管材质时需要选择抗高温蠕变、耐热性好抗氧化强的材质,保证炉管使用的时间,确保裂解炉的正常运行。
1 裂解炉辐射炉段管破坏的原因炉管产生损坏痕迹的原因是多方面的,其一为渗碳造成了裂纹以及材质变差。
当炉管在高温状态下时,产生碳原子从炉管内表面向外逐渐扩散的现象称为渗碳。
由于此过程是的碳含量增加,造成材料组织的性能改变,因此炉管的硬度变弱,出现裂纹的现象,这是导致炉管损坏的原因之一。
其二为高温蠕变的伤害,由于金属材料会伴随着外界温度的升高进行升高,伴随着时间的延长以及力的作用,金属会产生蠕变的现象,当直径或者轴线方向产生塑形变化,可能会导致炉管直径变大,局部出现肿起或者弯曲现象。
当壁管出现较多蠕变裂纹时,也表面炉管受到损伤,一般裂纹呈现轴向分布,并向内壁和外壁发展。
也会产生不明显的组织变化。
腐蚀以及氧化也会让管壁变薄,由于裂解原料以及燃料中含有微量的硫,在高温环境下会产生晶体,所产生的晶体融点只有645摄氏度,因此消融的共晶体会渗透在金属与晶粒之间,在内外管壁发生晶体腐蚀的现象,造成壁管变薄。
乙烯裂解炉辐射段炉管失效原因分析及对策
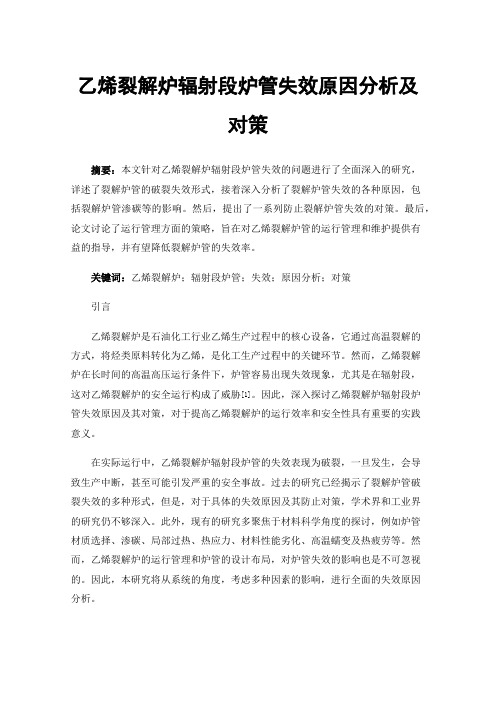
乙烯裂解炉辐射段炉管失效原因分析及对策摘要:本文针对乙烯裂解炉辐射段炉管失效的问题进行了全面深入的研究,详述了裂解炉管的破裂失效形式,接着深入分析了裂解炉管失效的各种原因,包括裂解炉管渗碳等的影响。
然后,提出了一系列防止裂解炉管失效的对策。
最后,论文讨论了运行管理方面的策略,旨在对乙烯裂解炉管的运行管理和维护提供有益的指导,并有望降低裂解炉管的失效率。
关键词:乙烯裂解炉;辐射段炉管;失效;原因分析;对策引言乙烯裂解炉是石油化工行业乙烯生产过程中的核心设备,它通过高温裂解的方式,将烃类原料转化为乙烯,是化工生产过程中的关键环节。
然而,乙烯裂解炉在长时间的高温高压运行条件下,炉管容易出现失效现象,尤其是在辐射段,这对乙烯裂解炉的安全运行构成了威胁[1]。
因此,深入探讨乙烯裂解炉辐射段炉管失效原因及其对策,对于提高乙烯裂解炉的运行效率和安全性具有重要的实践意义。
在实际运行中,乙烯裂解炉辐射段炉管的失效表现为破裂,一旦发生,会导致生产中断,甚至可能引发严重的安全事故。
过去的研究已经揭示了裂解炉管破裂失效的多种形式,但是,对于具体的失效原因及其防止对策,学术界和工业界的研究仍不够深入。
此外,现有的研究多聚焦于材料科学角度的探讨,例如炉管材质选择、渗碳、局部过热、热应力、材料性能劣化、高温蠕变及热疲劳等。
然而,乙烯裂解炉的运行管理和炉管的设计布局,对炉管失效的影响也是不可忽视的。
因此,本研究将从系统的角度,考虑多种因素的影响,进行全面的失效原因分析。
本文旨在通过对乙烯裂解炉辐射段炉管失效原因的深入研究,提出有效的预防和管理对策。
我们将探讨炉管材质选择、炉膛尺寸设计、燃烧器布局以及运行管理等多个方面的策略,提高乙烯裂解炉的运行效率和安全性。
1 裂解炉管破裂失效形式乙烯裂解炉管在其运行过程中可能出现的失效形式主要表现为破裂。
炉管的破裂失效形式在实际操作中具有多样性,其中常见的包括纵向裂纹、环向裂纹、孔洞和剥落等。
乙烯裂解炉管的结焦机理及其防护措施
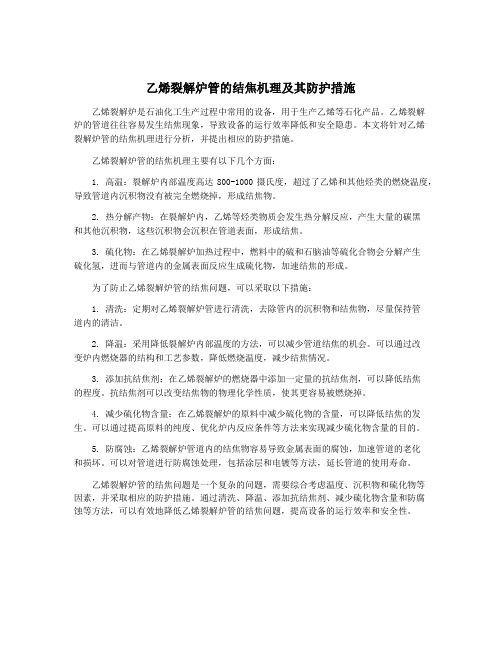
乙烯裂解炉管的结焦机理及其防护措施乙烯裂解炉是石油化工生产过程中常用的设备,用于生产乙烯等石化产品。
乙烯裂解炉的管道往往容易发生结焦现象,导致设备的运行效率降低和安全隐患。
本文将针对乙烯裂解炉管的结焦机理进行分析,并提出相应的防护措施。
乙烯裂解炉管的结焦机理主要有以下几个方面:1. 高温:裂解炉内部温度高达800-1000摄氏度,超过了乙烯和其他烃类的燃烧温度,导致管道内沉积物没有被完全燃烧掉,形成结焦物。
2. 热分解产物:在裂解炉内,乙烯等烃类物质会发生热分解反应,产生大量的碳黑和其他沉积物,这些沉积物会沉积在管道表面,形成结焦。
3. 硫化物:在乙烯裂解炉加热过程中,燃料中的硫和石脑油等硫化合物会分解产生硫化氢,进而与管道内的金属表面反应生成硫化物,加速结焦的形成。
为了防止乙烯裂解炉管的结焦问题,可以采取以下措施:1. 清洗:定期对乙烯裂解炉管进行清洗,去除管内的沉积物和结焦物,尽量保持管道内的清洁。
2. 降温:采用降低裂解炉内部温度的方法,可以减少管道结焦的机会。
可以通过改变炉内燃烧器的结构和工艺参数,降低燃烧温度,减少结焦情况。
3. 添加抗结焦剂:在乙烯裂解炉的燃烧器中添加一定量的抗结焦剂,可以降低结焦的程度。
抗结焦剂可以改变结焦物的物理化学性质,使其更容易被燃烧掉。
4. 减少硫化物含量:在乙烯裂解炉的原料中减少硫化物的含量,可以降低结焦的发生。
可以通过提高原料的纯度、优化炉内反应条件等方法来实现减少硫化物含量的目的。
5. 防腐蚀:乙烯裂解炉管道内的结焦物容易导致金属表面的腐蚀,加速管道的老化和损坏。
可以对管道进行防腐蚀处理,包括涂层和电镀等方法,延长管道的使用寿命。
乙烯裂解炉管的结焦问题是一个复杂的问题,需要综合考虑温度、沉积物和硫化物等因素,并采取相应的防护措施。
通过清洗、降温、添加抗结焦剂、减少硫化物含量和防腐蚀等方法,可以有效地降低乙烯裂解炉管的结焦问题,提高设备的运行效率和安全性。
- 1、下载文档前请自行甄别文档内容的完整性,平台不提供额外的编辑、内容补充、找答案等附加服务。
- 2、"仅部分预览"的文档,不可在线预览部分如存在完整性等问题,可反馈申请退款(可完整预览的文档不适用该条件!)。
- 3、如文档侵犯您的权益,请联系客服反馈,我们会尽快为您处理(人工客服工作时间:9:00-18:30)。
裂解炉辐射段炉管堵塞原因分析及对策张维祥(中国石油吉林石化公司乙烯厂,吉林,132022)摘要:辐射段炉管堵塞是乙烯装置裂解炉常见故障之一。
文中叙述了吉化大乙烯装置裂解炉辐射段炉管堵塞的主要现象和有效的处理措施,并阐述了辐射段炉管堵塞的主要原因,为同类装置避免类似现象发生和处理提供了依据。
关键词:裂解炉;辐射段炉管;堵塞中国石油吉林石化公司乙烯厂(以下简称吉化乙烯)始建于1993年,1996年9月一次性开车成功,原装置共有六台LSCC1-1型“门式”裂解炉(F0101~F0601),裂解原料石脑油、轻柴油、加氢尾油及循环乙烷/丙烷等,单台乙烯生产能力为60 kt/a,采用五开一备的生产方式,规模为300 kt/a 乙烯。
在2001年吉化乙烯进行了一期扩能改造,新建了一台PyroCrack6型裂解炉(F0701),裂解原料为装置自产的循环乙烷及丙烷,使吉化乙烯的生产能力达到了380 kt/a。
在2004年吉化乙烯进行了二期扩能改造,新建了两台PyroCrack1-1SR型“门式”裂解炉(F0801~F0901),裂解原料为石脑油、循环乙烷/丙烷,单台炉乙烯生产能力为120 kt/a,在二期改造过程中,为了实现装置生产能力达到700 kt/a的目标,结合原有六台裂解炉运行情况,2004年6月至2005年10月先后对F0101~F0601裂解炉进行了扩能改造。
改造采用KTI技术,将原有LSCC1-1型炉管更换为GK-6型炉管,单台裂解炉乙烯生产能力由原来的60 kt/a提高到80 kt/a以上。
改造内容包括更换辐射段炉管、对流段部分管束(高压蒸汽过热段)、底部火嘴、增加除焦罐及燃料控制系统等。
2007年11月,由于裂解炉周期的影响,新建了一台裂解炉(F1001),提高了裂解炉的备用系数,保证了装置的满负荷运行。
从开车至今,裂解炉辐射段炉管在运行及升温过程中多次出现堵塞现象,给裂解炉的安全运行甚至是装置的平稳运行都带来严重威胁。
下文对吉化乙烯装置裂解炉辐射段炉管堵塞的情况进行了总结分类和深入分析原因,并提出相应对策。
1.处于横跨段集合管末端的炉管堵塞2004年至2005年F0101~F0601裂解炉改造后,两侧高温的烃/蒸汽混合物离开对流段,分别汇集到一根横跨段集合管然后进入辐射段炉管。
每一根辐射段炉管进口,都装有一个临界流量文氏管(亦称文丘里管),以确保在正常的操作中有良好的流量分布。
每台裂解炉有112个进口(每侧炉膛有56组),对应于112组 GK6型辐射段炉管。
改造后设计运行周期为60天,但是实际运行20天左右时,多次出现处于横跨段集合管末端的炉管对应的废热锅炉出口温度迅速上涨,现场检查发现处于集合管末端的辐射段炉管上升管变得红亮(对应的下降管还是黑色的),有堵塞的迹象,虽然采取了对该组炉出口温度进行大幅度低控等措施,但不久该炉管还是会堵塞。
2006年至2007年每年发生类似事件都在10次以上。
原因分析:经过实际参数与设计参数对比发现,实际横跨压力远远低于设计值,确定原因为物料分配不均,物料在个别炉管及TLE内流速慢,停留时间过长,过度裂解,结焦严重致堵塞。
裂解炉F0101~F0601在扩能改造时更换了文丘里管,设计横跨压力为280 kPa(g),而在实际运行过程中从来没有达到过,裂解石脑油时横跨段集合管处压力(以下简称横跨压力)一般在220 kPa(g)左右,裂解重质原料(加氢尾油)和(化工轻油)时横跨压力一般只能达到190 kPa(g)左右,远远低于设计值。
而文丘里下游压力投油初期在140 kPa(g)左右,运行一段时间后文丘里下游压力上升至170 kPa(g) 左右,达到裂解炉清焦指标之一文丘里出口入口绝对压力比接近。
因此怀疑改造后文丘里孔径过大,横跨段集合管处压力低,导致文丘里处物料分配不均。
以裂解炉F0101为例,A侧横跨段集合管所对应的末端是TIA0111组炉管,B侧横跨段集合管所对应的末端是TIA0118组炉管,这两组炉管最容易出现流通物料少,停留时间延长,过度裂解导致结焦严重,进而发生堵塞现象。
这种情况多发生在裂解炉运行至中期阶段。
进料不干净,可能含有一定量的杂质,由于原料从高温对流段出来到横跨段集合管处有4m左右的爬升高度,因此这些杂质可能在对流段水平管内积存,当物流发生变化时,就被带到横跨段集合管里。
而裂解炉所有下降管入口的取点不是在水平设置的横跨段集合管的最低部,而是在横跨段集合管的两侧,因此这些杂质很可能在物流变化时被带到裂解炉两侧横跨段集合管末端,进入末端对应的TIA0111组炉管和TIA0118组炉管内,造成这两组个别炉管内物料流速低,停留时间延长,结焦严重进而堵塞,或者由大颗粒杂质直接堵在文丘里喉管处(如下图所示)。
这种情况多发生在裂解炉升温过程或投油过程中,气流发生较大变化时。
应对措施:经设计部门核算,目前文丘里管喉径处直径为过大,应为18mm。
2008年将F0101~F0601的文丘里全部更换成喉径为18mm的新文丘里管(如下图)。
此后上述堵管现象大为减少。
Φ48.3Φ4.89400805619187Φ18流向文丘里结构图但是,2009至2011年还是发生堵管事件3次。
检修时割开堵塞的文丘里管和横跨段集合管末端的盲头。
在其中取出了较多的杂质。
这些杂质在横跨段集合管末端处形成堆积,当流量发生变化时,杂质被吹起,随气流进入处于横跨段末端的炉管而造成堵塞(如下图)。
检修时发现横跨段集合管末端和文丘里处存有的杂质情况如下图:文丘里处的杂质横跨段集合管末端的杂质经分析杂质的主要成分为氧化铁、三氧化二铝、焦炭,针对这些杂质采取以下措施,详见下表。
横跨段集合管杂质成分杂质来源应对措施氧化铁金属管中铁的氧化物每三年利用停炉机会割开横跨段集合管末端清理一次焦炭对流段存在一定结焦现象每三年利用停炉机会割开横跨段集合管末端清理一次三氧化二铝脱砷催化剂的成分之一去往炉前进料线增加过滤器通过采取上述应对措施以后,F0101~F0601再未发生上述类似堵管现象。
2.处于每台废热锅炉对应14组炉管中间的炉管堵塞改造后112组 GK6型辐射段炉管进入8台废热锅炉,即每台废热锅炉对应有14组辐射段炉管。
由于14组辐射段炉管与废热锅炉连接处存在变径,位于14组辐射段炉管中间的是第七组和第八组。
在以往运行中发生过,备用一段时间的裂解炉,升温后发现位于14组辐射段炉管中间的是第七组和第八组堵塞,而在降温前的检查,并未发现该炉管堵塞。
原因分析:检修时发现在下降管与上升管连接的底部“U”型弯内,存有较多碎焦。
起初怀疑是裂解炉烧焦不彻底炉管或废热锅炉内焦层脱落而致堵塞,但如果是炉管焦层脱落致堵塞的话,随机性较大,不会只堵在中间的是第七组和第八组炉管。
而裂解炉烧焦完全是按照方案进行,每一步的时间和空气量均得到保障,因此基本排除裂解炉烧焦不彻底导致炉管、废热锅炉焦层脱落致堵塞的可能。
从拆开的废热锅炉来看,在废热锅炉上部管板及出口管存在较多碎焦,并且有少量蒸汽及凝液从出口管夹带着碎焦逆流而下进入废热锅炉,由于14组辐射段炉管中间的是第七组和第八组炉管正好对准废热锅炉入口管,所以这些碎焦最终进入该台废热锅炉14组辐射段炉管中间的是第七组和第八组炉管内,积聚在底部“U”型弯内而致堵塞(如下图)。
这种情况多发生在停炉期间,但是只有在裂解炉升温后才能够被发现。
废热锅炉应对措施:完善操作,在裂解炉降温结束及时关闭清焦阀阀道防焦蒸汽,防止蒸汽及凝液反窜,防止沿途的碎焦被带进炉管系统。
同时在升温过程中,通入稀释蒸汽之前一小时,先通入烧焦空气,起扰动作用,防止炉管内水被蒸干后,碎焦结成块状,将炉管彻底堵死。
由于是两台裂解炉共用一个除焦罐,当一台裂解炉处于停用状态时,与其共用一个除焦罐的另一台裂解炉处于烧焦状态时,应提前关闭停用裂解炉的清焦阀,防止大量的蒸汽及焦进入停用裂解炉炉管系统而造成堵塞。
在拆废热锅炉封头时,应避免产生大的震动,防止将废热锅炉上部管板的焦震落进入炉管。
拆开废热锅炉后及时将炉出口管口封好,防止杂物进入炉管。
3裂解炉炉管堵塞的其它情况2006年为了增加装置的操作弹性和裂解炉的原料适应性,在F0801~F0901的A侧辐射室增加了乙烷、丙烷线,增加了石脑油与乙烷、丙烷混合裂解的工况,但因没有设计的工艺参数,混合进料量、炉出口温度、稀释比以及注硫量等均靠摸索,导致F0801~F0901在石脑油和乙烷、丙烷混合裂解时,多次出现辐射段炉管连同对应的线型废热锅炉管束堵塞,处理起来较为棘手。
目前F0801~F0901很少混合裂解石脑油和乙烷、丙烷,如特殊需要混合裂解石脑油和乙烷、丙烷时,适当加大二甲基二硫的注入量。
装置还出现过因稀释蒸汽(DS)带水,夹带大量杂质进入炉管系统造成大面积堵管现象。
发现F0801裂解炉DS带水严重的A侧炉管大面积堵塞,经过烧焦无效后,只能停炉检修。
在经过切割处理时发现,管内堵塞的大量物质为钠盐,经水浸泡后能够溶解,处理后恢复,但再次通DS后,炉管再次发生大量堵塞,经分析为对流段管线中残存大量的钠盐,导致炉管再次堵塞,经在进料线导淋配制临时管线,向炉管系统通入锅炉给水,在除焦罐卸料口排放,并在文丘里下游压力表处通入空气扰动,对整个炉管系统进行了全面彻底水洗,清除了大量的沉积钠盐,在排放口取样分析钠离子浓度合格后恢复,裂解炉炉管未再发生堵塞。
这种情况一般是发生在处于DS总管末端的裂解炉。
投用轻柴油的裂解炉因轻柴油质量严重劣化,BMCI值由17左右升至21左右,平均密度由806kg/m3左右涨至818kg/m3左右,导致废热锅炉及其出口管结焦严重,险些造成该废热锅炉对应的辐射段炉管全部堵塞。
废热锅炉结焦情况废热锅炉出口管结焦情况废热锅炉入口泄漏造成辐射段炉管堵塞,由于漏点位置和角度特殊,泄漏的高压蒸汽形成扇面将废热锅炉入口封锁住,导致对应的辐射段炉管中裂解气流通不畅过度裂解结焦而致堵塞。
4 结语(1)每天对运行裂解炉辐射段炉管表面温度进行监测,发现偏差增大、超高,要及时调整。
(2)经常检查烧嘴燃烧状态,保证烧嘴燃烧状态良好、分布均匀。
(3)每天跟踪原料质量,根据原料质量及时调整稀释比、炉出口温度等,在硫含量低的原料中适当注入结焦抑制剂。
(4)在装置DS带水后,要及时在炉前DS总管末端进行排放,避免DS带水时将长期积存在罐内的大量Na盐带入裂解炉炉管内,堵塞裂解炉炉管。
(5)精心操作,避免紧急停炉事故发生。
延长裂解炉运行周期是一个永恒的话题,而辐射段炉管堵塞是影响裂解炉运行周期的一个重要因素。
乙烯装置裂解炉辐射段炉管堵塞是常见的问题之一,而造成堵塞的因素也是多种多用的。
本文对乙烯装置裂解炉辐射段炉管堵塞的部分原因、现象、危害、处理措施进行了阐述,希望能够引起重视,避免或最大程度的降低类似事故给装置生产带来的损失。