CNC全检良率情况汇总
CNC-10月生产日报表10-17

8人。物料:1人。QC:2人,投影测量员:1人. 共25人。
4768 8 17 25
190.7
损失工时:
制 王倩妮
损失工时
待机
投影
5S
维修 待机
待料
5S
操机员
仇少蓬 梁祖飞 罗法广 彭珊志 梁祖德 赵亚雷 杨长江 杨秀彬
3.4
小 时
田远芳/谢安燕
刘细宏/廖柯臣/李坚/彭新梅/赵江彦/田力飞/曾志新 /李玲(组长)/张长伟/邓芳/梁瑞玲
2266
小计:8台
18794
5S
17.00 17.00
全检866//返修/抛光
107.00 107.00
合计
开机率:
全检 8 24%
稼动率:
11.00 11.00
223
220
98%
18794 总计划达成率:
合计
直接人数
间接人数
总人数
人均产值
注明 应有机台:33台,实开8台.待机:25台.(待维修:2台)
1
班次:白班
CNC领班: 孙海军
机台
规格名称
加工工序
加工时间 (秒)
标准产能 (PCS/H)
应开机时间 (小时)
实际开机时 间(小时)
计划数
A15
866
CNC1
16
225 11.00 10.50
2363
B8
866
CNC1
17
212 11.00 10.50
2224
B9
866
CNC1
15
240 11.00 10.50
64
24
0
88
16
1
CNC机床加工中的表面质量评估与提升策略
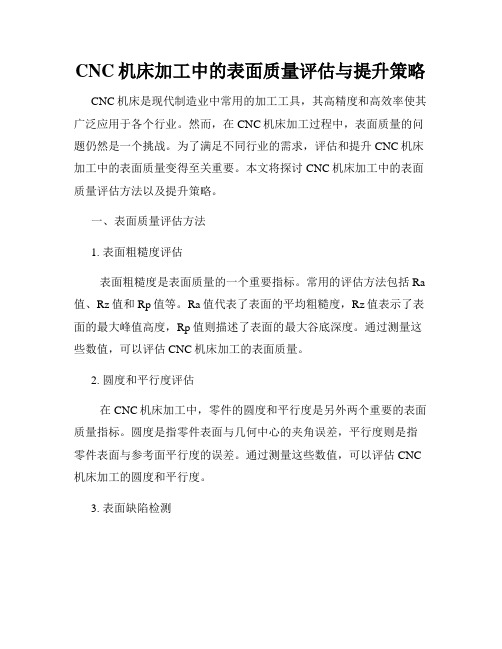
CNC机床加工中的表面质量评估与提升策略CNC机床是现代制造业中常用的加工工具,其高精度和高效率使其广泛应用于各个行业。
然而,在CNC机床加工过程中,表面质量的问题仍然是一个挑战。
为了满足不同行业的需求,评估和提升CNC机床加工中的表面质量变得至关重要。
本文将探讨CNC机床加工中的表面质量评估方法以及提升策略。
一、表面质量评估方法1. 表面粗糙度评估表面粗糙度是表面质量的一个重要指标。
常用的评估方法包括Ra 值、Rz值和Rp值等。
Ra值代表了表面的平均粗糙度,Rz值表示了表面的最大峰值高度,Rp值则描述了表面的最大谷底深度。
通过测量这些数值,可以评估CNC机床加工的表面质量。
2. 圆度和平行度评估在CNC机床加工中,零件的圆度和平行度是另外两个重要的表面质量指标。
圆度是指零件表面与几何中心的夹角误差,平行度则是指零件表面与参考面平行度的误差。
通过测量这些数值,可以评估CNC 机床加工的圆度和平行度。
3. 表面缺陷检测CNC机床加工中常常会出现表面缺陷,如划痕、凹坑等。
为了准确评估表面质量,需要进行表面缺陷检测。
常见的方法包括目视检查、磁粉探伤和超声波检测等。
二、表面质量提升策略1. 优化刀具选择刀具是CNC机床加工中影响表面质量的重要因素之一。
选择合适的刀具可以降低表面粗糙度和提高加工效率。
一般来说,切削速度越高,表面粗糙度越小;而切削深度越小,表面质量越好。
因此,在选择刀具时需要根据具体工件和加工要求进行合理的调整。
2. 控制切削参数在CNC机床加工中,切削参数的选择对表面质量有很大影响。
切削速度、进给速度和切削深度等参数需要进行合理的调整,以获得更好的表面质量。
同时,控制切削液的使用和冷却方式,可以有效降低表面粗糙度和减少热变形。
3. 提高机床的精度机床的精度对CNC机床加工的表面质量有决定性影响。
因此,通过提高机床的精度可以有效提升表面质量。
包括提高机床的稳定性、减小机床的刚度误差和提高供油系统的精度等措施。
CNC品质评估研究报告
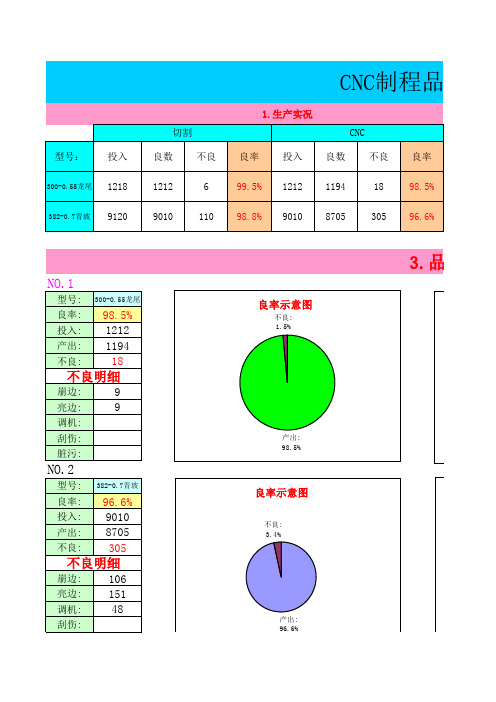
产出: 98.5% 300-0.55龙尾
98.5% 1212 1194 18 9 9
良率示意图
不良: 1.5%
不良明细
NO.2
型号: 良率: 投入: 产出: 不良: 崩边: 亮边: 调机: 刮伤:
382-0.7青玻
96.6% 9010 8705 305 106 151 48
因素是跟覆膜的粘度有关,有 住片。
不良分析
主要跟覆膜有关,有些磨 过程中会使片发生偏移,进
粘度合适的。
不良分析
膜粘度不够,CNC过程中易 边亮边,其二,人员技能 少调机损耗。
粘度合适的。作业人员需 作机台设备。
粘度合适的。作业人员需 作机台设备。
良率示意图
不良: 3.4%
不良明细
产出: 96.6%
96.6%
脏污:
制程品质评估研究报告
2.总结
300-0.55龙尾:25号A班-26号A班 订单:1000 投:1200 耗时:2个班次。 382-0.7青玻 :26号A班-28号A班 订单:7400 投:9000 耗时:5个班次。
玻璃损耗/板/片 58/21 76ቤተ መጻሕፍቲ ባይዱ/12
调机: 15.7%
脏污: 刮伤 0.0% 崩边: 34.8%
2.改善:选膜要选粘度合适的。作业人员需 认真学习,熟练操作机台设备。
亮边: 49.5%
2.改善:选膜要选粘度合适的。作业人员需 认真学习,熟练操作机台设备。
49.5%
00 00
耗时:2个班次。 耗时:5个班次。
割机的刀头需更换为更为锋
不良分析
1.问题:亮边崩边主要跟覆膜有关,有些磨 粘度低在CNC生产过程中会使片发生偏移,进 而出现亮边崩边。
设备完好率统计及检查标准
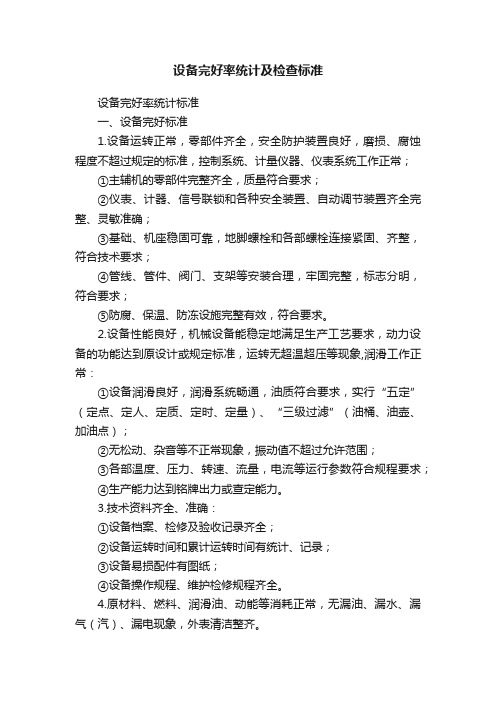
设备完好率统计及检查标准设备完好率统计标准一、设备完好标准1.设备运转正常,零部件齐全,安全防护装置良好,磨损、腐蚀程度不超过规定的标准,控制系统、计量仪器、仪表系统工作正常;①主辅机的零部件完整齐全,质量符合要求;②仪表、计器、信号联锁和各种安全装置、自动调节装置齐全完整、灵敏准确;③基础、机座稳固可靠,地脚螺栓和各部螺栓连接紧固、齐整,符合技术要求;④管线、管件、阀门、支架等安装合理,牢固完整,标志分明,符合要求;⑤防腐、保温、防冻设施完整有效,符合要求。
2.设备性能良好,机械设备能稳定地满足生产工艺要求,动力设备的功能达到原设计或规定标准,运转无超温超压等现象,润滑工作正常:①设备润滑良好,润滑系统畅通,油质符合要求,实行“五定”(定点、定人、定质、定时、定量)、“三级过滤”(油桶、油壶、加油点);②无松动、杂音等不正常现象,振动值不超过允许范围;③各部温度、压力、转速、流量,电流等运行参数符合规程要求;④生产能力达到铭牌出力或查定能力。
3.技术资料齐全、准确:①设备档案、检修及验收记录齐全;②设备运转时间和累计运转时间有统计、记录;③设备易损配件有图纸;④设备操作规程、维护检修规程齐全。
4.原材料、燃料、润滑油、动能等消耗正常,无漏油、漏水、漏气(汽)、漏电现象,外表清洁整齐。
二、设备完好率及日常统计方法设备按完好或不完好评级,用下列公式计算完好率:设备完好率=(设备台数×实际完好时间/设备台数×总时间)×100%.其中,实际完好时间=总时间-维修时间;设备日常维修需体现在日常工作日志中(写明维修设备名称·所在工段楼层·维修原因及结果·维修时限),设备科每日记录前一日各车间设备维修情况,月底总结计算各车间设备完好率进行考核,体考核评分标准见附表。
1.完好设备的考核(1) 完好标准中的主要项目,有一项不合格,该设备即为不完好设备。
产品数控加工评估技巧
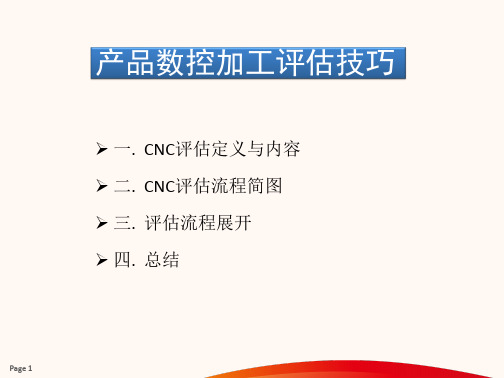
不锈钢开粗加工刀具参数表
刀具规格 转速(S) 进给(F) 每层切削(MM)
Ø8
6000-7000 2000-2500
0.25-0.3
Ø6
7000-8000 2000-2500
0.25-0.3
Ø4
8000-9000 1500-2000
0.2-0.25
Ø3 9000-10000 1200-1500
0.2-0.25
CNC胚料一般分以下几种,对比如图:
胚料种类 材质硬度 加工余量 开模(K/N) 单位耗材 胚料成本
冲胚 锻胚 拉枝料
不变 变化 不变较低
增加模具成 较低
本
较低
中等 较高 较低
板材 棒材
不变 不变
较小 较小
无须开模, 较高 可快速 打样 较低
较高 /
Page 2
2.拆分工序图
0.5-0.8
Ø2 10000-12000 1000-1200
0.3-0.5
Ø1.5 10000-12000 800-1000
0.2-0.3
Ø1.0 10000-12000 500-600
0.1-0.2
Page 2
定义加工顺序就是定义好CNC编程的工艺,一般的逻辑是,首先采用大的刀具来开 粗加工,然后用小刀清角加工,最后再统一的光刀,结构加工上先上后下,先外后里的 加工顺序。
电磁铁吸紧
Page 2
4.评估C/T时间与刀具成本
A.刀具的选择和参数的定义 B.加工顺序的选择和定义 C编程及在机床上试跑C/T D.刀具成本的预估
刀具的选择原则是:能用大刀就不用小刀,能够使用成型刀的就要选用成型刀。常 用刀具加工参数表如下图所示,大家可以参考以下参数评估CNC给过来的DFM的加工参 数是否合理。
控制板生产良率分析报告(最终版本)

按键,蜂对
跟踪
离起
169
1.要求技术更改防溢棒的焊盘孔 (改为0.9mm)。 2.工艺将一些离起的标准放在工 艺文件上,明确定义。 3.领班每小时需对总检处查看不 良,并将不良反馈给作业员。 4.工艺进行跟踪做工装改善。
魏方军 秦芳 吴洪对
跟踪
连焊
143
1.对执锡员工进行培训,领班及 IPQC不定时的抽检其状况。 2.对ICT测试出的不良每个小时给 不良品给作业员,时时提醒作业员 并要求后工序检查前一工序的作 业状况。
生产数量 110603 不良数量 不良率 49 0.02%
生产数量 82530 8464512331 28350 不良数量 不良率 62 0.03 59 0.03 31 0.01 17 0.01
Page:5
龙威电业有限公司
三.前三项不良改善措施
不良项目 数量 根本原因 1.按键不良为作业员浸1.按键不良为 作业员浸油时板放置不平导致油流进按 键。 2.部分按键不良为来料按力手感较差 。 3.蜂鸣器不良主要原因为来料不良(在 生产过程中盖子掉落),部分蜂鸣器为 作业员操作不当导致进油。 1.主要为A1/A2上防溢棒的焊盘孔偏 大,插件后易松脱离起。{对比旧板), 发现焊盘孔并无明显差异,均为 1.00mm±0.05,但板材不一样,估计为 板材不一致导致)。 2.执面作业员漏失,检查不到位,工艺 要求不是很明确,要求全部元件紧贴板 面,作业员不能很好把握标准。 3.领班督导不到位。 1.连焊主要为豆浆机通用一盘为执锡 作业员后焊线与变压器时造成其它焊点 连锡。 2.其次为A2显示板上的C3电容连焊。 改善措施 1.对浸油员工进行宣导,周转时轻 拿轻放避免板不平没流入按键。 2.将按键不良与蜂鸣器来料不良 交给品保要求供应商改善。 3.对员工进行跟踪,不定时的抽检 其状况。 责任人 改善效果 评估
年度良率总结报告(3篇)
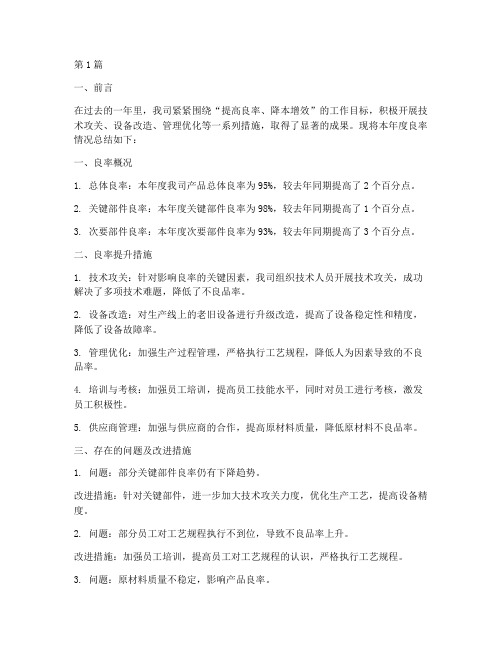
第1篇一、前言在过去的一年里,我司紧紧围绕“提高良率、降本增效”的工作目标,积极开展技术攻关、设备改造、管理优化等一系列措施,取得了显著的成果。
现将本年度良率情况总结如下:一、良率概况1. 总体良率:本年度我司产品总体良率为95%,较去年同期提高了2个百分点。
2. 关键部件良率:本年度关键部件良率为98%,较去年同期提高了1个百分点。
3. 次要部件良率:本年度次要部件良率为93%,较去年同期提高了3个百分点。
二、良率提升措施1. 技术攻关:针对影响良率的关键因素,我司组织技术人员开展技术攻关,成功解决了多项技术难题,降低了不良品率。
2. 设备改造:对生产线上的老旧设备进行升级改造,提高了设备稳定性和精度,降低了设备故障率。
3. 管理优化:加强生产过程管理,严格执行工艺规程,降低人为因素导致的不良品率。
4. 培训与考核:加强员工培训,提高员工技能水平,同时对员工进行考核,激发员工积极性。
5. 供应商管理:加强与供应商的合作,提高原材料质量,降低原材料不良品率。
三、存在的问题及改进措施1. 问题:部分关键部件良率仍有下降趋势。
改进措施:针对关键部件,进一步加大技术攻关力度,优化生产工艺,提高设备精度。
2. 问题:部分员工对工艺规程执行不到位,导致不良品率上升。
改进措施:加强员工培训,提高员工对工艺规程的认识,严格执行工艺规程。
3. 问题:原材料质量不稳定,影响产品良率。
改进措施:加强与供应商的合作,提高原材料质量,确保产品良率。
四、展望新的一年,我司将继续以提高良率为核心,不断优化生产工艺、加强设备管理、提升员工素质,努力实现以下目标:1. 产品总体良率达到97%以上。
2. 关键部件良率达到99%以上。
3. 次要部件良率达到95%以上。
4. 降低不良品率,提高客户满意度。
总之,我司将继续努力,为实现年度目标而努力拼搏,为我国制造业的发展贡献自己的力量。
第2篇一、报告概述尊敬的领导,亲爱的同事们:本报告旨在对2022年度公司良率情况进行全面总结,分析存在的问题,并提出改进措施。
XXT1试产TOP问题改善跟踪

tracking
张权 彭建平
抛光增加管控抛光后的材料 厚度,防止抛光太多,造成 料厚偏小NG
closed
俞建平 张权
1.更换氧化厂同步制作喷砂 治具及挂具,预计在8/31完 成夹具样品 2.同问题1改善后的夹具验证 尺寸变异,同氧化厂要求同 步增加高度,外宽管控,并 制作对应的SOP--在8/29完成 并拉通对应的标准
1.8月10号 2.8月12号 3.4.8月10 号 5.8月11号 6.8月12号
围,8月10号下午开始夹具修改,同步增
加压板,8月14号全部完成
R角有橘皮现象,冲压后抛光手法问 题,没有抛光到OK效果,之前已加工好 CNC工序的产品进行返抛侧面,造成侧 孔孔边踏角不良,且全检有漏检现象
1.项目签抛光效果OK与NG对照板,现场 质量跟进抛光效果, 2.后面全检工序挑选踏边不良
相差0.01,测量手法差异OK
1.员工的测量手法验证 2.冲压素材的弧度、长度方向直线度、 宽度边的直线度(上中下三段落差)的 影响排查 C治具的平面度、装夹素材后的直 线度 C夹具密封圈预留的高度排查 C后产品宽度尺寸变化量 6.真空吸的力度大小及吸气孔的排布状 况
2.冲压素材弧度、长度方向直线度OK, 宽度尺寸上中下差异值中间小,两头 大,模具改善侧面模印后,宽度差异值 在0.06-0.08MM,T1试产限度生产。 C夹具装机测量直线跳动在0.03以 内,T1后优化在0.01以内; C工序CNC夹具密封圈预留的高度在 0.1-0.2MM,OK 5.每台机测量10PCSCNC前CNC后数据变化 对比 6.一夹吸气孔排布再加宽延伸到最宽范
1.氧化挂具重新设计,由尖点改成平 面,制作5只,8月14号上午10点前完 成,投产并统计改善良率,另外5只8月 16号晚上到位; C工序根据新挂具结构,增加锣平 台,来降低掉槽风险---根据新挂具验证 结果再决定是否本次试产导入
(铝业公司)加工二处cnc生产部计件方案+加工 质检绩效评价表

加工二处CNC生产部K01计件推动方案一、目的为了充分体现多劳多得、按劳取酬的薪资分配原则,最大程度调动全员的工作积极性,提高生产效率,特此制定本计薪方案。
二、运行时间及适用范围2.1运行时间年9月1日起2.2适用范围2.2.1直接生产人员岗位:主机手1/2、终检(模组计件方案产品除外)2.2.2生产辅助人员岗位:物流、掏铝屑、换刀、加切削液(换水)、保养刀库、清理水箱2.2.3生产干部岗位:线长(含副/代线长)、组长(含副组长)三、权责3.1技术工程部负责相关产品的Flowchart、标准工时的制定;3.2企划部根据标准核算各产品的人均标准产能及单片工资;3.3由生产部负责本单位相关的数据记录、汇总及分配;3.4计件产能数量由经管审核无误后确认为计薪产能。
四、薪资结构及构成明细4.1薪资结构4.1.1员工计件薪资结构实际薪资=计件薪资+异常产能补加薪资+全勤奖+伙食补贴适用范围:直接生产人员、生产辅助人员4.1.2干部计件薪资结构实际薪资=现有薪资*1.3*对应模组达成率*模组人员使用率+全勤奖+伙食补贴4.1.2.1模组人员使用率=计件标准使用人力/实际使用人力(模组使用率上限100%)4.1.2.2干部现有薪资详见附表适用范围:生产干部4.1.3临时工薪资结构实际薪资=签约工时单价*出勤工时(注:现依11.3元/小时核算)备注:所有机种的单片费用,均为包含节假日天数后进行核算之单价4.2薪资构成明细4.2.1计件薪资=计薪产能*单片计件标准4.2.2计薪产能=计件产能(适用于直接生产人员)计薪产能=计件产能*模组达成率(适用于生产辅助人员)模组达成率=直接模组产能/标准产能其中:标准产能=3600/CT*11*标准机台数(适用于直接生产人员及生产干部)标准产能=3600/CT*11.5*标准机台数(适用于生产辅助人员)4.2.3计件产能计算标准4.2.3.1 计件产能=直接模组产能-扣除产能(适用于直接生产人员及生产干部)其中:1).直接模组产能=对应主机手1直接模组产能之和(适用于CNC1夹线长) 2).直接模组产能=对应主机手2直接模组产能之和(适用于CNC2夹线长)3).直接模组产能=对应终检直接模组产能之和(适用于终检线长、组长(含副组长))4.2.3.2 计件产能=理论模组产能-扣除产能(适用于生产辅助人员)理论模组产能=标准产能*实际负责机台数/总机台数扣除产能:指依奖罚制度进行相应的产能减除(详见6.2奖惩制度)4.3异常产能补加薪资4.3.1定义:生产过程中的异常停机(非主机手操作责任、非计划性停机/停产)4.3.2异常产能补加薪资=6.896/机台数*异常损失时间(适用于员工)6.896元/H=1200元/21.75天/8H4.3.3异常产能补加薪资=签约工时单价/机台数*异常损失时间(适用于临时工,现依11.3元/小时核算)4.4量试产品补加薪资4.4.1定义:有计划性安排生产、暂无单片计件标准之产品4.4.2量试产品补加薪资=11.016*生产时间(适用于员工)11.016元/H=3393元/28天/11H4.4.3量试产品补加薪资=现有薪资的每小时薪资*生产时间(适用于生产干部)4.4.4量试产品补加薪资=签约工时单价*生产时间(适用于临时工,现依11.3元/小时核算)注:3393元=底薪+技能津贴+岗位津贴+加班费+伙食补贴。
自动化设备钣金件来料检验标准
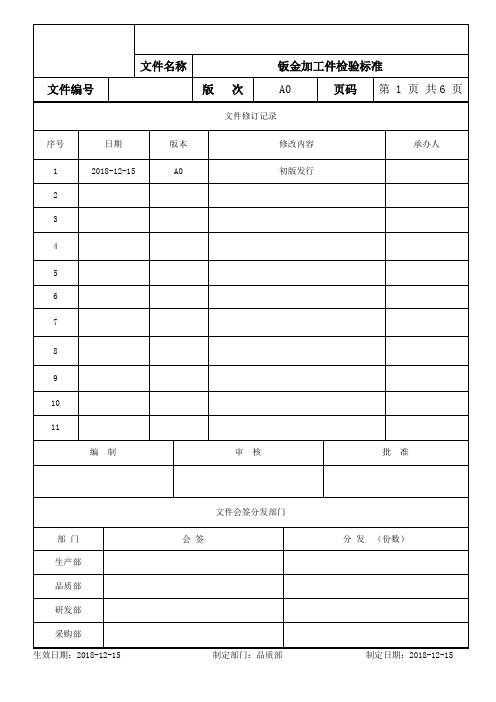
同批来料,其外形、规格尺寸、使用材料、加工工艺、表面处理、互换性、颜色、字唛、包装等均应有良好的一致性,批与批之间应没有明显差别。
7.3外观:
外观检视条件及方法:
--视力:校正视力1.0以上。
--目视距离:检查物距眼睛一臂之远约30-50cm。
--目视角度:45度~90度(检查时产品应转动)。
本标准的尺寸未注单位为mm。
GB/T 5000.9《重型机械通用技术条件切削加工件》
GB/T 1031《表面粗糙度参数及其数值》
GB/T 1800.4《极限与配合标准公差等级和孔轴的极限偏差表》
GB/T 32535《普通螺纹收尾、肩距、退刀槽和倒角》
GB/T 197《普通螺纹公差》
GB/T 1184《形状和位置公差未注公差值》
7.5.3丝印耐化学试剂性检验:用纯净水浸过的擦布在有丝印的表面擦拭15秒,再用甲基化酒精浸过的擦布擦拭15秒,最后用异丙醇浸过的擦布擦拭15秒,(注:擦拭时施加约500克的压力,每秒一个来回),不允许有丝印字迹脱落、丝印油墨扩散及变色等现象发生。
7.6焊接要求:
7.6.1门板/封板弯折角图纸未标注不需要焊接,一律需要做焊接处理。
7.检验步骤:
7.1包装要求:
7.1.1所有物料必须使用相应的垫料、间隔物、填充物包装,避免运输过程遭到破坏,每单片产品之间必须隔开,机架运输必须用珍珠棉将所有边角包好,避免相互碰撞导致不良,检验前发现有不符合的包装方式,检验人员有权拒绝接收。
7.1.2外包装必须具有足够的抗外力强度,以便能保护内部包装物,检验人员发现有外包装破损或有产品
--灯光:大于500 LUX的照明度或正常公司车间照明度。
7.3.1表面光滑、平整、无毛刺、变形、锈蚀、裂纹、压折、夹渣等;预埋件、铆接件应牢靠、无松动,螺纹无缺损;不允许有加工遗留物存留在物件上;
CNC产品镭雕验证
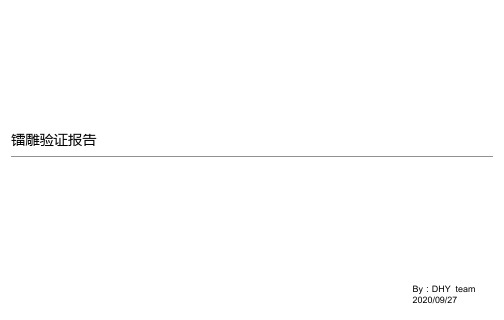
By:DHY team 2020/09/27
镭雕印验证 镭雕印验证步骤:
调整好镭雕参数
随机取5Pcs素材
5Pcs产品 对应镭雕
装入治具电镀.
2019/4/29
烤干取出全检镭雕印
Strictly Apple ConfidentAiaplp-leNeCeodnftiodeknntoiawl
验证2结果:
பைடு நூலகம்No
镭雕后
电镀后
1
2
3
4
5
2019/4/29
电镀前/后全检镭雕印结果
备注
全检5PCS都OK,良率 100%
Strictly Apple ConfidentAiaplp-leNeCeodnftiodeknntoiawl
DOE3(镭雕参数:功率95%,速度1200mm/s,频率50HZ)
验证1结果:
建议: 1.综合以上三种调整镭雕工艺参数(75W/85W/95W),优选使用85W参数;
2019/4/29
Strictly Apple ConfidentAiaplp-leNeCeodnftiodeknntoiawl
Thank you !
DOE1(镭雕参数:功率75%,速度1200mm/s,频率50HZ)
验证1结果:
No
镭雕后
电镀后
1
2
3
4
5
2019/4/29
电镀前/后全检镭雕印结果
备注
全检5PCS都OK,良率 100%
Strictly Apple ConfidentAiaplp-leNeCeodnftiodeknntoiawl
DOE2(镭雕参数:功率85%,速度1200mm/s,频率50HZ)
各工序良率状况
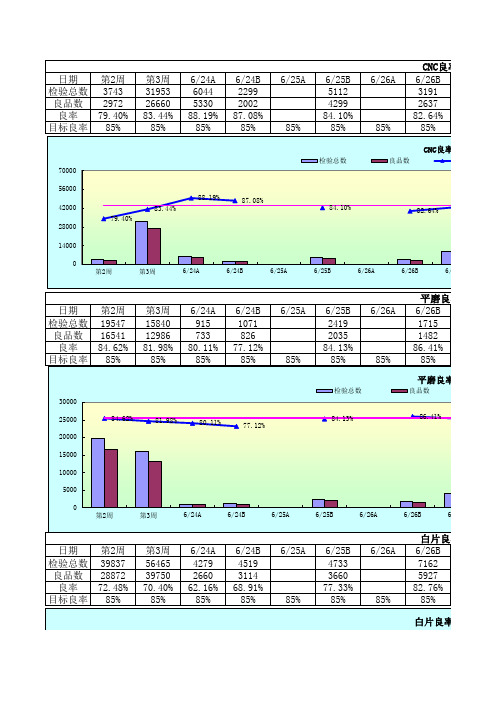
6/25B
6/26A
6/26B
6/27A
日期 检验总数
良品数 良率 目标良率
第2周 25300 18608 73.55% 80%
第3周 53002 39699 74.90% 80%
6/24A 410 346 84.39% 80%
6/24B 4757 3469 72.92% 80%
60000 40000
68.07%
57.82%
68.66%
66.71%
71.12%
70.10%
67.64%
80% 68.42%
60%
40%
20%
6/27A
6/27B
6/28A
6/28B
6/29A
6/29B
6/30A
6/30B
0% 第4周
ቤተ መጻሕፍቲ ባይዱ
`
100%
73.55%
74.90%
84.39%
72.92%
6/25A 80%
6/25B 6412 4356 67.94% 80%
6/26A 80%
检验总数
67.94%
包装良率汇总 6/26B 5933 4143 69.83% 80%
包装良率趋势图
良品数
69.83%
20000
0 第2周
第3周
6/24A
6/24B
6/26A 85%
白片良率汇总 6/26B 7162 5927 82.76% 85%
检验总数
白片良率趋势图
良品数
80000 60000 40000
72.48%
70.40%
62.16%
68.91%
检验总数
77.33%
机加工零部件质量检验标准
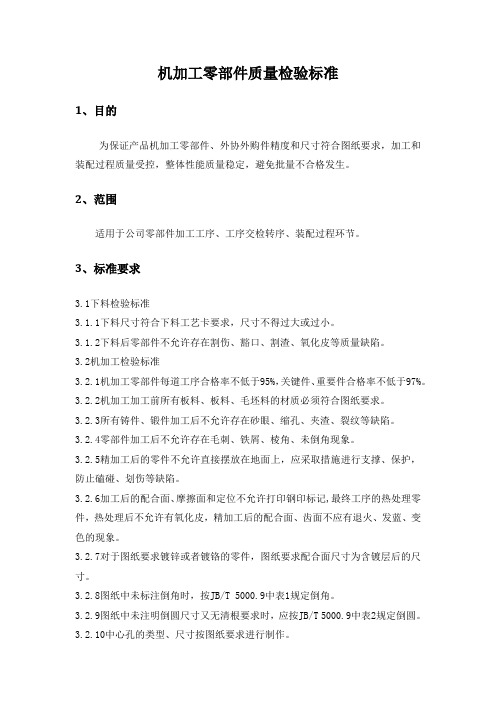
机加工零部件质量检验标准1、目的为保证产品机加工零部件、外协外购件精度和尺寸符合图纸要求,加工和装配过程质量受控,整体性能质量稳定,避免批量不合格发生。
2、范围适用于公司零部件加工工序、工序交检转序、装配过程环节。
3、标准要求3.1下料检验标准3.1.1下料尺寸符合下料工艺卡要求,尺寸不得过大或过小。
3.1.2下料后零部件不允许存在割伤、豁口、割渣、氧化皮等质量缺陷。
3.2机加工检验标准3.2.1机加工零部件每道工序合格率不低于95%,关键件、重要件合格率不低于97%。
3.2.2机加工加工前所有板料、板料、毛坯料的材质必须符合图纸要求。
3.2.3所有铸件、锻件加工后不允许存在砂眼、缩孔、夹渣、裂纹等缺陷。
3.2.4零部件加工后不允许存在毛刺、铁屑、棱角、未倒角现象。
3.2.5精加工后的零件不允许直接摆放在地面上,应采取措施进行支撑、保护,防止磕碰、划伤等缺陷。
3.2.6加工后的配合面、摩擦面和定位不允许打印钢印标记,最终工序的热处理零件,热处理后不允许有氧化皮,精加工后的配合面、齿面不应有退火、发蓝、变色的现象。
3.2.7对于图纸要求镀锌或者镀铬的零件,图纸要求配合面尺寸为含镀层后的尺寸。
3.2.8图纸中未标注倒角时,按JB/T 5000.9中表1规定倒角。
3.2.9图纸中未注明倒圆尺寸又无清根要求时,应按JB/T 5000.9中表2规定倒圆。
3.2.10中心孔的类型、尺寸按图纸要求进行制作。
3.2.11所有内径、外径、轴类加工表面粗糙度必须严格按照图纸制作。
4、职责和要求4.1技术部负责按照产品设计确认产品关键件、重要件并提供清单;负责产品在生产制作过程中图纸尺寸的修改和提供技术支持。
4.2工艺部负责确认关键工序和重要工序并制定工艺文件;负责产品制作过程中加工工艺的指导和工艺文件的制定并监督工作执行情况。
4.3 生产部负责按照最新版设计图纸和工艺文件进行派工,并将图纸和工艺卡一并交给操作者。
操作者在加工前必须熟悉图纸尺寸要求和工艺制作流程要求,熟练掌握本工序所用的工装、夹具和量具的使用,并复检上道工序(如:下料)零部件是否存在尺寸不合格或外观缺陷等质量问题。
各类设备完好率标准

各类设备完好率标准第一篇:各类设备完好率标准各类设备完好率标准各类设备完好标准一、金属切削机床(1~6项为主要项目)适用范围:车床、铣床、磨床、刨床、钻床、镗床、刻线机、拉床、齿轮及螺纹加工加工机床、切断机床、组合机床、简易专用机床、超声波及电加工机床。
1.精度、性能能满足生产工艺要求,精密、稀有机床主要精度性能达到出厂标准。
2.各传动系统运转正常,变速齐全。
3.各操作系统动作灵敏可靠。
4.润滑系统装置齐全,管道完整,油路畅通,油标醒目,油质符合要求。
5.电气系统装置齐全,管线完整,性能灵敏,运行可靠。
6.滑动部位运转正常,各滑动部位及零件无严重拉、研、碰伤。
7.机床内外清洁,无黄袍,无油垢,无锈蚀。
8.基本无漏油、漏水、漏气现象。
9.零部件完整,随机附件基本齐全,保管妥善。
10.安全、防护装置齐全,可靠。
二、锻压设备(1~6项为主要项目)适用范围:锻锤、锻造机、轧机、冲床、剪床、平板机、弯板机、弯管机、整形机、冷镦机、弹簧加工机、滚压机、压力机等。
1.精密、能力满足生产工艺要求。
2.各传动部位运转正常,变速齐全。
3.润滑系统装置齐全,管路完整,润滑良好,油质符合要求。
4.各操作系统动作灵敏可靠,各指示刻度准确。
5.电气系统装置齐全,管线完整,性能灵敏,运行可靠。
6.滑动部位运转正常,各滑导部位及零件无严重拉、研、碰伤。
7.机床内外清洁,无黄袍,无油垢,无锈蚀。
8.基本无漏油、漏水、漏气现象。
9.零部件完整,随机附件基本齐全,保管妥善。
10.安全、防护装置齐全,可靠。
三、铸造设备(1~3项为主要项目)适用范围:造型机、抛砂机、造芯机、混砂机、落砂机、抛丸机、喷砂机等。
1.性能良好,能力满足生产工艺要求。
2.设备运转正常,操作控制系统完整可靠。
3.电气、安全、防护、防尘装置齐全有效。
4.设备内外整洁,零部件及各滑动面无严重磨损,滑动、导轨面无锈蚀。
5.基本无漏水、漏气、漏砂现象。
6.润滑装置齐全,效果良好。
CNC全检良率情况汇总
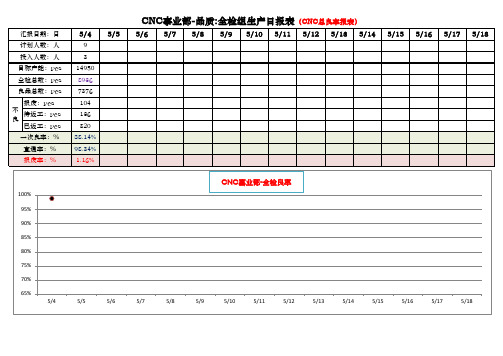
审核:吴雄伟
制表:朱金莲
PDE96B 2.0版 CNC每日全检日报表
检验日期 全检总数量 良品数量 可重工不良数 报废不良数 全检直通率
10.85±0.02偏小 未见光 振刀纹
ቤተ መጻሕፍቲ ባይዱ
5/4 8936 7876 956 104 88.14% 29 9 2 24 15 5 20
5/5 0
5/6 0
5/7 0
5/6
5/7
5/8
5/9
5/10
5/11
5/12
5/13
5/14
5/15
5/16
5/17
5/18
CNC事业部-全检良率
100%
95%
90% 85% 80% 75% 70% 65% 5/4 5/5 5/6 5/7 5/8 5/9 5/10 5/11 5/12 5/13 5/14 5/15 5/16 5/17 5/18
5/8 0
5/9 0
5/10 0
5/11 0
5/12 0
5/13 0
5/14 0
5/15 0
5/16 0
5/17 0
5/18 0
0 0 #DIV/0!
0 0 #DIV/0!
0 0 #DIV/0!
0 0 #DIV/0!
0 0 #DIV/0!
0 0 #DIV/0!
0 0 #DIV/0!
0 0 #DIV/0!
0 0 #DIV/0!
0 0 #DIV/0!
0 0 #DIV/0!
0 0 #DIV/0!
0 0 #DIV/0!
0 0 #DIV/0!
报 外观不良(碰刮) 废 加工不良 不 良 倒角大
1.20±0.05偏小
各工序良率状况
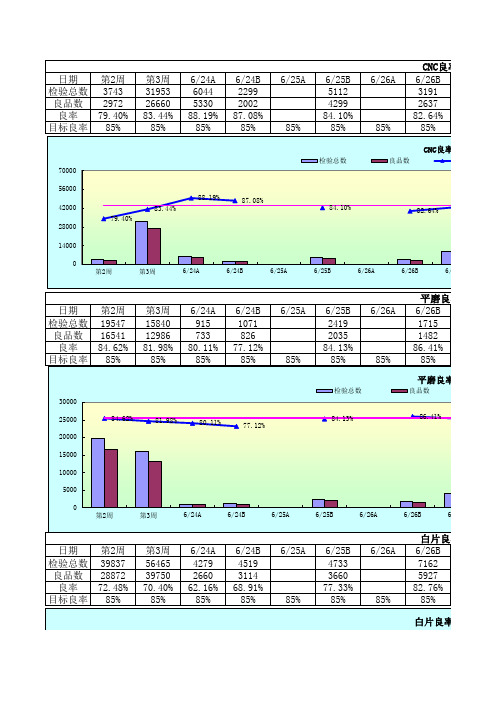
6/30A 4747 4052 85.36% 85%
85.36%
6/30B 1524 1299 85.24% 85%
第4周 28344 23892 84.29% 85%
85.24%
100% 84.29%80%
60%
40%
20%
6/27A
6/27B
6/28A
6/28B
6/29A
6/29B
6/30A
包装良率趋势图
良品数
69.83%
20000
0 第2周
第3周
6/24A
6/24B
6/25A
6/25B
6/26A
6/26B
6/27A
CNC良率汇总 6/27A 9750 8213 84.24% 85%
6/27B 4565 3980 87.19% 85%
6/28A 8238 6493 78.82% 85%
100% 75.34%80%
60%
40%
20%
6/27A
6/27B
6/28A
6/28B
6/29A
6/29B
6/30A
6/30B
0% 第4周
包装良率汇总 6/27A 4496 3046 67.75% 80%
6/27B 3714 2528 68.07% 80%
6/28A 3113 1800 57.82% 80%
良率
56000 42000 28000
79.40%
83.44%
88.19%
87.08%
84.10%
82.64%
14000
0 第2周
第3周
6/24A
6/24B
AOI良率偏低分析
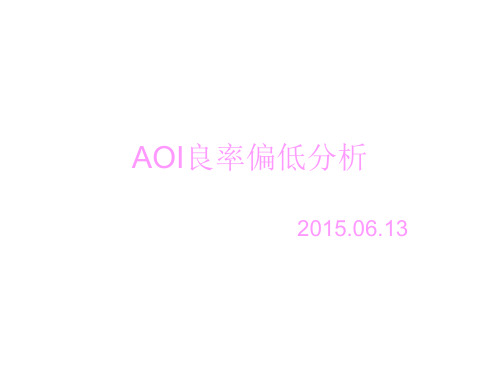
汇报完毕,谢谢指教!
缺陷占有状况
70.00% 60.00% 50.00% 40.00% 30.00% 20.00% 10.00% 0.00% 总不良率 短路占有 开路占有 缺口占有 27.80% 不良占有比例 23.20% 18% 61.34%
取样跟进
• • • • • • • • • • 2015.056.13日取样型号 149-2R6674-00进行跟中, 结果如下: 检验数量:131PNL 不良数量:59PNL 总不良率:45% 短路:49PNL 短路占有率:83.05% 开路:6PNL 开路占有率:10.17% 缺口:4PNL 缺口占有率:6.78%
蚀刻不净4(退膜)
蚀刻不净5
胶迹1
胶迹2
胶迹3
胶迹4
胶迹5
胶迹6
平短(压膜不良或垃圾)1
平短(压膜不良或垃圾)2
平短(压膜不良或垃圾)3
曝光脏点(垃圾)4
开路1
开路2
开路3(镀锡)
蚀刻后擦花开路4
擦花缺口5
新增缺陷图片
新增缺陷图片
新增缺陷图片
结论或建议
• 1,从短路分布的状况来看,主要在于图形成像后打包--运输---图电前过程中的擦花,主要从这三个方面的操作以 及维护。包含厂内和电镀两个部门共同管控。 • 2,从胶迹的状况来看,极大的可能性在于我司使用的多 次回收的纸皮,在重复利用前为进行清理。我司在供应商 现场查看时我司的纸皮是最差的。同时纸皮的在打包时因 为残缺也是造成擦花的原因之一。 • 3,蚀刻不净的不良为点状,并且可明显见到退膜不净的 状况。并且开路中有两处为二铜长于一铜的现象,这些应 由供方电镀协助处理。 • 4,整个不良的现状反射出的不良点,不管是开路还是短 路,最终擦花缺陷占有为40%,胶迹占有率为20%,蚀刻 退膜为16.7%,如上第一点提及,这三点是目标改善推进 项目。建议主要从过程操作以及纸皮出发。
各工序良率状况
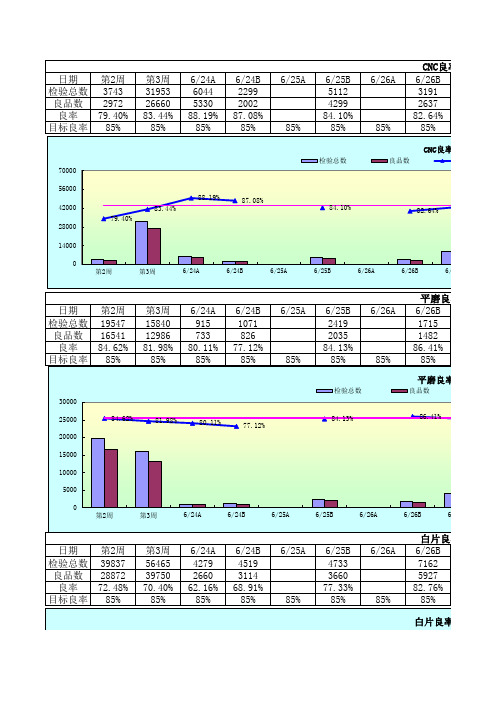
良品数 良率 目标良率
第2周 3743 2972 79.40% 85%
第3周 31953 26660 83.44% 85%
6/24A 6044 5330 88.19% 85%
6/24B 2299 2002 87.08% 85%
6/25A 85%
6/25B 5112 4299 84.10% 85%
6/25A
6/25B
6/26A
6/26B
6/27A
CNC良率汇总 6/27A 9750 8213 84.24% 85%
6/27B 4565 3980 87.19% 85%
6/28A 8238 6493 78.82% 85%
6/28B 4547 3947 86.80% 85%
6/29A 8492 7198 84.76% 85%
6/29B 1482 1327 89.54% 85%
6/30A 6288 5189 82.52% 85%
6/30B 2460 2211 89.88% 85%
第4周 62468 52826 84.56% 85%
良率趋势图
良率
目标良率
100%
84.24%
87.19%
78.82%
86.80%
84.76%
89.54%
6/27B 5212 3747 71.89% 85%
6/28A 6641 5468 82.34% 85%
6/28B 8302 6468 77.91% 85%
6/29A 10501 7933 75.55% 85%
6/29B 7542 5653 74.95% 85%
6/30A 8083 5947 73.57% 85%
85.36%
cnc良率检讨

cnc良率检讨
CNC不良分析及改善
1.来料抽检是否存在崩角严重划伤或尺寸偏小
改善措施:抽检来料杜绝不良产品上机既浪费人力物力财力,不良产品退上工序。
2.正确的操作手势和操作流程以免在后续的生产中给本工序或后工序造成良率效率的下滑。
改善措施:严格按照作业指导书进行操作或在适当的时间对员工加强培训。
3.阴阳边
改善措施; 1 调机应秉承确认确认再确认的原则在进行生产
2生产中进行自检管理者隔2小时巡检一次
3每10分钟清理夹具表面
4刀具磨损严重,更换刀具
4.未车到
改善措施; 1 正确的操作手势
2靠角磨损
3气压不足导致移位
目前CNC存在的问题很多,从产品上机到产品下机都没有完整的作业流程。
上机前应该做什么(例如:检查刀具是否存在磨损,水泵正常开启,保护膜是否需要更换)。
生产中应该注意哪些,防止问题的发生(生产中应当进行自检)。
下机生产完每架产品进行抽检,
防止不良品流入下工序。
针对CNC上次生产大量不良做出以上分析及改善措施,在以后的生产中将会以基本方针不良对策:原则1 不接收不良品2不制造不良品3不流出不良品。
在后期将会在各方面进行改善及优化:比如加强员工的品质意识。
励志提高CNC良率,保证CNCF定能达到预期的目标。
- 1、下载文档前请自行甄别文档内容的完整性,平台不提供额外的编辑、内容补充、找答案等附加服务。
- 2、"仅部分预览"的文档,不可在线预览部分如存在完整性等问题,可反馈申请退款(可完整预览的文档不适用该条件!)。
- 3、如文档侵犯您的权益,请联系客服反馈,我们会尽快为您处理(人工客服工作时间:9:00-18:30)。
5/5
5/6
5/7
5/8
5/9
5/10
5/11
5/12
5/13
5/14
5/15
5/16
5/17
5/18
CNC事业部-全检良率
100%
95%
90% 85% 80% 75% 70% 65% 5/4 5/5 5/6 5/7 5/8 5/9 5/10 5/11 5/12 5/13 5/14 5/15 5/16 5/17 5/18
CNC事业部-品质:全检组生产日报表(CNC总良率报表)
汇报日期:日 计划人数:人 投入人数:人 目标产能:pcs 全检总数:pcs 良品总数:pcs 报废:pcs 不良 待返工:pcs 已返工:pcs 一次良率:% 直通率:% 报废率:% 5/4
9 8 14950 8936 7876 104 136 820 88.14% 98.84% 1.16%
5/8 0
5/9 0
5/10 0
5/11 0
5/12 0
5/13 0
5/14 0
5/15 0
5/16 0
5/17 0
5/18 0
0 0 #DIV/0!
0 0 #DIV/0!
0 0 #DIV/0!
0 0 #DIV/0!
0 0 #DIV/0!
0 0 #DIV/0!
0 0 #DIV/0!
0 0 #DIV/0!
审核:吴雄伟
制表:朱金莲
PDE96B 2.0版 CNC每日全检日报表
检验日期 全检总数量 良品数量 可重工不良数 报废不良数 全检直通率
10.85±0.02偏小 未见光 振刀纹
5/4 8936 7876 956 104 88.14% 29 9 2 24 15 5 20
5/5 0Βιβλιοθήκη 5/6 05/7 0
0 0 #DIV/0!
0 0 #DIV/0!
0 0 #DIV/0!
0 0 #DIV/0!
0 0 #DIV/0!
0 0 #DIV/0!
报 外观不良(碰刮) 废 加工不良 不 良 倒角大
1.20±0.05偏小
71.60+0.03/-0.10偏大 71.60+0.03/-0.10偏小
640 180 56 17 63
可 漏刻字 重 工 漏加工 不 良 1.20±0.05偏大
备注
已整形OK
审核:吴雄伟
制表:朱金莲