环氧丙烷反应器的设计PPT课件
环氧丙烷反应器设计
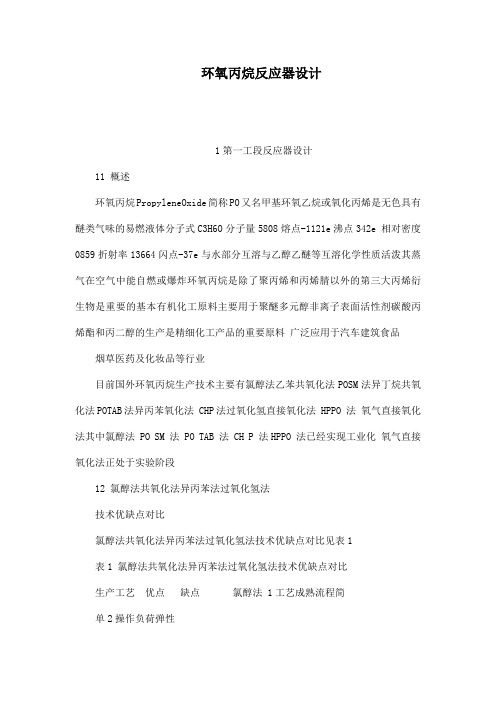
环氧丙烷反应器设计1第一工段反应器设计11 概述环氧丙烷PropyleneOxide简称PO又名甲基环氧乙烷或氧化丙烯是无色具有醚类气味的易燃液体分子式C3H6O分子量5808熔点-1121e沸点342e 相对密度0859折射率13664闪点-37e与水部分互溶与乙醇乙醚等互溶化学性质活泼其蒸气在空气中能自燃或爆炸环氧丙烷是除了聚丙烯和丙烯腈以外的第三大丙烯衍生物是重要的基本有机化工原料主要用于聚醚多元醇非离子表面活性剂碳酸丙烯酯和丙二醇的生产是精细化工产品的重要原料广泛应用于汽车建筑食品烟草医药及化妆品等行业目前国外环氧丙烷生产技术主要有氯醇法乙苯共氧化法POSM法异丁烷共氧化法POTAB法异丙苯氧化法 CHP法过氧化氢直接氧化法 HPPO 法氧气直接氧化法其中氯醇法 PO SM 法 PO TAB 法 CH P 法HPPO 法已经实现工业化氧气直接氧化法正处于实验阶段12 氯醇法共氧化法异丙苯法过氧化氢法技术优缺点对比氯醇法共氧化法异丙苯法过氧化氢法技术优缺点对比见表1表1 氯醇法共氧化法异丙苯法过氧化氢法技术优缺点对比生产工艺优点缺点氯醇法 1工艺成熟流程简单2操作负荷弹性大3选择性好4对原料丙烯的纯度要求不高5安全性高6投资少7有成本竞争力 1水耗大 2 产生大量废水及废渣每生产1t环氧丙烷产生40 50 t含氯化物废水和2 1 tCaCl2 3 消耗大量氯气和石灰原料污染环境 4 产生的次氯酸对设备的腐蚀严重共氧化法PO SM 法PO T BA 法 1 共氧化法克服了氯醇法腐蚀废水量大缺点 2 产品成本低联产品分摊成本 3 环境污染小 1 工艺流程长 2 原料品种多 3 丙烯纯度要求高 4 工艺操作压力高 5 设备造价高设备材质多采用合金钢 6 联产2 2 2 5t 苯乙烯或2 3 t 叔丁醇受市场因素制约7 废水含C OD 高异丙苯氧化法CH P 法与氯醇法相比 1 不需要氯气减少了设备腐蚀 2 废水量少与共氧法相比 1 无副产品使用异丙苯替代了乙苯异丙苯循环使用 2 不联产苯乙烯无需辅加设备 3 装置投资少比共氧化法低1 3 生产过程中产生大量A-甲基苯乙烯增加循环回收装置过氧化氢氧化法H PPO 法 1 工艺流程简单 2 产品收率高无副产品3 无污染属清洁工艺原料辅助原料产品的主要技术规格表1-3主要工艺物料消耗与规格名称规格用量丙烯工业级 22万ta 双氧水工业级18万ta 甲醇工业级 xxxta 氢气纯氢气 11万ta22 原辅料规格及消耗配比表2 原辅料规格及消耗配比原辅料规格配比原料双氧水工业级原料丙烯工业级原料丙烷工业级原料甲醇工业级催化剂 TS-1 7323 产品质量标准2-1产品规格等级项目指标优等品一等品合格水分质量分数002 002 01 醛质量分数001 003 01 环氧乙烷质量分数001 01 03 GB14491-2001产品外观要求透明液体无可见机械杂质工业用环氧丙烷应符合表1-1规格要求表2-2产品技术要求项目指标优等品一等品合格色度铂-钴色号号≤ 5 10 20 酸度质量分数以乙酸计算≤001 003 001 GB14491-2001环氧丙烷主要用与聚醚多元醇的生产和丙二醇和一些非离子表面活性剂这些靖西化工产品所以对于环氧丙烷的规格要求就要严格的多我们在项目生产中会严格把持产品的纯度和质量3 反应工段工艺简介4 反应工段工艺计算本工艺[4]是在压力为03MPa温度为55℃下在TS-1上进行的等温液固相催化反应41 催化反应过程的物料衡算411 计算用原始数据此处所选的8原始数据均为年产30万吨环氧丙烷的中间试验数据进入反应器时甲醇含量约为7226丙烯含量约为1093摩尔分数412 化学反应主反应[5]平行反应表5 反应中涉及到的物质的相对分子质量CH3OH H2O2 C3H6 C3H8 H2O C3H6O 32 34 42 44 18 58413 物料衡算过程催化合成甲醛过程是一个连续流动反应在定态下其物料衡算基本公式本工艺计算[6]以生产30万吨甲醛按300天计工业级别的甲醛质量分数为96则每小时一个反应器生产工业级别的环氧丙烷的质量其物质的量为并以其为基准4131 反应器进口物料的计算根据表3表5中各组分的数据计算可得纯甲醇的物质的量10133kmolh水物质的量18281kmolh丙烯153226kmolh丙烷9428kmolh双氧水36264kmolh表6原料液的组成及含量物质摩尔分数物质的量kmolh CH3OH 7226 10133 H2O2 259 36264 H2O 1303 18281 C3H6 1093 153226C3H8 07 9428 NH3 05 7243 4132 反应器出口物料的计算甲醇的物质的量 10133kmolh生成环氧丙烷的物质的量34814kmolh水的物质的量217623kmolh未反应的双氧水的物质的量1451kmolh丙烯的物质的量1184kmolh丙烷的物质的量9427kmolh丙二醇甲醚的物质的量068kmolh表7 反应器出口主要气体的组成及含量物质摩尔分数物质的量kmolh CH3OH 84 10133 C3H6O 15 34814 H2O 91 217623 H2O2 006 1451 PE 004 1022C3H8O2-2 001 068 NH3 002 7243 C3H6 50 1184 42 合成甲醛过程的热量衡算热量衡算过程以03MPa下的液体为计算基准反应液体于常压下进入反应器在催化剂作用下进行恒温反应反应器出口气体以离开反应器总的热量衡算式为421 各物质比热容的计算每个组分的热容与温度的函数式即CpabTcT2表8 各物质平均温度为的物性物质 C3H8 1837 250-1500 C3H6 8256 250-1500 H2O 1907 250-1500 CH3OH 250-1500 CpC3H818372816×10-1T-1319×10-8T2 CpC3H682562174×10-1T-09692×10-6T2Cp32241907×10-3T-10057×10-6T2Cp21147084×10-3T-2586×10-6T2把T27350323K带入上述公式得同理可计算其他物质的比热容其结果如下表表9 各物质在平均温度为的物质C3H8 C3H6 H2O CH3OH C3H6O H2O2 9424 78207 318 4133 13799 50284422 各物质焓值的计算计算焓热量是时在等温条件下反应的参考态32315℃03Mpa又双氧水的消耗量为由得即为了维持反应器内温度为32315℃应每小时从反应器移走的热量43用量的确定列管式固定床反应器的壳程走冷凝水移走反应放出的热量使冷凝水从20 ℃升温到40℃表10 冷凝水的物性数据名称平均分子量密度比热容导热系数冷凝水 18 9957 4178 0618 由得冷凝水用量在工程上要确定反应器的几何尺寸首先得确定一定生产能力下所需的催化剂容积再根据工程实验所提供的反应器资料最后确定出反应器的几何尺寸522 催化剂容积的计算5221 催化剂用量的计算合成环氧丙烷的反应是一个气固相催化反应催化剂的用量需要根据反应工程上通过单位催化剂列物料衡算的动力学方程才能得出合成甲醛的动力学方程为其中PO环氧丙烷式中各物质摩尔分数的计算合成环氧丙烷的反应在双氧水转化率为84时到达平衡达平衡时双氧水的摩尔浓度为求解动力学方程由定义有查得令即则两边同时积分得其中用辛普森数值积分法求解定积分数值积分法为其中实用于奇数个数据点n为偶数f的角标代表选取数据点的编号且点与点之间等间距表11 与的关系0 012 024 036 048 060 072 084114913161515 1786 2203 2857 4167 7992 则因此催化剂所需质量反应采用的催化剂为钛硅分子筛催化剂成粒状粒度为6mm堆密度为比表面积为54故反应所需的体积523 列管根数的确定由催化剂所算得反应器体积太小反应物流量过大故选择用停留时间与流量的关系得出反应器总体积一小时的体积流量反应时间取十分钟反应器体积根据中间试验的结果列管规格为管长为L18m解方程得n2475根524 列管式固定床反应器壳体内径的确定由公式[11]式中D壳体内径 mmt管中心距 mm横过管束中心线的管束b 一般取 mm管子采用正三角形排列故带入公式得标准化后核算过程管长和壳径应相适应一般取LD为46对该反应器因此所设计的反应器符合实际情况实际催化剂用量53 等温固定床列管式反应器的设计计算结果表12 等温固定床列管式反应器的设计计算结果序号项目数据 123456789101112 列管式反应器入口温度列管式反应器出口温度反应压力原料甲醇的量原料丙烯的量原料水的量催化剂床层高度塔径催化剂用量列管根数列管规格管子排列方式50℃50℃03MPa10133kmolh153236kmolh18281kmolh18m38m58048kg2107根Φ57×25mm三角形排列第二工艺工段反应器设计4 反应工段工艺计算本工艺[4]是在压力为03MPa温度为55℃下在TS-1上进行的等温液固相催化反应41 催化反应过程的物料衡算411 计算用原始数据此处所选的8原始数据均为年产30万吨环氧丙烷的中间试验数据进入反应器时甲醇含量约为766丙烯含量约为58摩尔分数412 化学反应主反应[5]平行反应表5 反应中涉及到的物质的相对分子质量CH3OH H2O2 C3H6 C3H8 H2O C3H6O 32 34 42 44 18 58413 物料衡算过程催化合成环氧丙烷过程是一个连续流动反应在定态下其物料衡算基本公式此设备的进料为第一设备以生产50万吨甲醛按300天计工业级别的环氧丙烷质量分数为96则每小时一个反应器生产工业级别的环氧丙烷的质量其物质的量为并以其为基准4131 反应器进口物料的计算根据表3表5中各组分的数据计算可得纯甲醇的物质的量9840670kmolh水物质的量2171248kmolh丙烯744475kmolh丙烷45823molh双氧水10879kmolh氨水29432kmolh表6原料液的组成及含量物质摩尔分数物质的量kmolh CH3OH 9221 9840670H2O2 01 10879 H2O 1303 217124 C3H6 698 744475 C3H8 043 45823 NH3 028 29432 4132 反应器出口物料的计算甲醇的物质的量[7]984067kmolh生成环氧丙烷的物质的量10335kmolh水的物质的量218158kmolh未反应的双氧水的物质的量054kmolh丙烯的物质的量73414kmolh丙烷的物质的量4582kmolh氨水29432kmolh表7 反应器出口主要气体的组成及含量物质摩尔分数物质的量kmolh CH3OH 7663 984067 C3H6O 008 34814 H2O 1699 218158 H2O2 00 0544 NH3 023 29432 C3H8 036 45823 C3H6 57 73414 42 合成环氧丙烷过程的热量衡算热量衡算[8]过程以03MPa下的液体为计算基准反应液体于常压下进入反应器在催化剂作用下进行恒温反应反应器出口气体以离开反应器总的热量衡算式为421 各物质比热容的计算每个组分的热容与温度的函数式即CpabTcT2表8 各物质平均温度为的物性物质 C3H8 1837 250-1500 C3H6 8256 250-1500 H2O 1907 250-1500 CH3OH 250-1500 CpC3H818372816×10-1T-1319×10-8T2CpC3H682562174×10-1T-09692×10-6T2Cp32241907×10-3T-10057×10-6T2Cp21147084×10-3T-2586×10-6T2把T27350323K带入上述公式得同理可计算其他物质的比热容其结果如下表表9 各物质在平均温度为的物质C3H8 C3H6 H2O CH3OH C3H6O H2O2 9424 78207 318 4133 13799 50284422 各物质焓值的计算计算焓热量是时在等温条件下反应的参考态32315℃03Mpa又双氧水的消耗量为由得即为了维持反应器内温度为32315℃应每小时从反应器移走的热量43冷凝水用量的确定列管式固定床反应器的壳程走冷凝水移走反应放出的热量使冷凝水从20 ℃升温到40℃表10 冷凝水的物性数据名称平均分子量密度比热容导热系数冷凝水 18 9957 4178 0618 由得冷凝水用量522 催化剂容积的计算5221 催化剂用量的计算合成甲醛的反应是一个气固相催化反应催化剂的用量需要根据反应工程上通过单位催化剂列物料衡算的动力学方程才能得出合成甲醛的动力学方程为其中PO环氧丙烷式中各物质摩尔分数的计算合成环氧丙烷的反应在双氧水转化率为96时到达平衡达平衡时双氧水的摩尔浓度为求解动力学方程由定义有查得令即则两边同时积分得其中用辛普森数值积分法求解定积分数值积分法[10]为其中实用于奇数个数据点n为偶数f的角标代表选取数据点的编号且点与点之间等间距表11 与的关系0 012 024 036 048 060 072 08425833271438464602558823775491191258709 则因此催化剂所需质量反应采用的催化剂为活性炭吸附钛硅分子筛催化剂成粒状粒度为6mm堆密度为比表面积为54故反应所需的体积由催化剂所算得反应器体积太小反应物流量过大故选择用停留时间与流量的关系得出反应器总体积一小时的体积流量反应时间取十分钟反应器体积总体积根据中间试验的结果列管规格为管长为L18m解方程得n2385根524 列管式固定床反应器壳体内径的确定由公式[11]式中D壳体内径 mmt管中心距 mm横过管束中心线的管束b 一般取 mm管子采用正三角形排列故带入公式得标准化后核算过程管长和壳径应相适应一般取LD为46对该反应器因此所设计的反应器符合实际情况53 等温固定床列管式反应器的设计计算结果表12 等温固定床列管式反应器的设计计算结果序号项目数据 123456789101112 列管式反应器入口温度列管式反应器出口温度反应压力原料甲醇的量原料丙烯的量原料水的量催化剂床层高度塔径催化剂用量列管根数列管规格管子排列方式50℃50℃03MPa10133kmolh153236kmolh18281kmolh18m4m2385根Φ57×35mm三角形排列2132料液泵设计计算由于是泵加料取由于料液流量过大选用2个加料泵流量单个泵流量密度进料管管径设料液至加料孔的高度弯头取90弯头则料液由平均黏度和各组分黏度关系7液体料液加料泵在料液面与进料孔面之间列伯努利方程泵的实际功率取泵的总效率则泵的实际功率则流量为查泵性能图可得选型如下泵规格G263-165-132N 流量263m3 扬程165m汽蚀余量3m31 固定床DNPN将固定反应器视为筒体本设计采用一般的反应釜由反应器内物料为液相由则圆整32 筒体壁厚最大操作压力为设计压力P取最大工作压力的10511倍[2]本设计取设计压力设计温度T根据筒体设计压力和设计温度选择材料Q345R许用应力为焊缝系数=10双面对接焊100无损探伤表3-1 焊接接头系数φ无损检测的长度比例焊接接头形式全部局部双面焊对接接头或相当于双面焊的对接接头085 单面焊对接接头沿焊缝根部全长有紧贴基本金属的垫板09 08 理论厚度钢板负偏差C1腐蚀裕量C2C22mm单面面腐蚀表3-2 钢板负偏差C1钢板厚度 2 22 25 28-30 22-35 38-4 45-55 负偏差 013 014 015 016 018 02 02 钢板厚度6-7 8-25 26-30 32-34 36-40 42-50 52-60 负偏差 06 08 09 1 11 12 13根据内压圆筒壁厚的计算公式带入以上数据得根据工程要求和钢材的使用壁厚范围圆整后取校核筒体水压试验强度根据式因为Q345R的屈服极限所以取代入得故水压试验满足强度要求33 封头封头包括有椭圆形碟形锥形球冠形封头平板封头等多种类型从工艺操作要求考虑对封头形状无特殊要求球冠形封头平板封头都存在较大的边缘应力且采用平板封头厚度较大故不宜采用半球形封头受力最好壁厚最薄重量轻但深度大制造较难中低压小设备不宜采用碟形封头存在局部应力受力不如椭圆形封头标准椭圆形封头制造比较容易受力状况比碟形封头好综合考虑该精馏塔设计内压温度等因素最终确定采用标准椭圆形封头选釜体的封头选标准椭球型代号EHA标准JBT47462002封头以Q345R为材料标准形封头壁厚其中整体冲压钢板负偏差代入得根据工程要求和钢材的使用壁厚范围圆整后取与前计算的筒体壁厚一致内表面积封头的标准为EHA 4000×13-Q235R JBT 4746综上筒体和封头选材都为Q235R壁厚34 筒体长度HDN4000mmH18M以内径为公称直径的椭圆形封头的尺寸内表面积和容积可得由于使用的是标准封头所以所以可得封头的高度h2m整体塔高度第三部分塔设备设计第1章固定床反应器设备设计说明书1材料的选择在刚度或结构设计为主的场合应尽量选用普通碳素钢在以强度设计为主的场合应根据压力温度介质等使用限制选用Q235由于容器设计压力为014MPa使用温度为50℃故筒体和封头都选择Q345RQ345R钢是屈服强度为340MPa级的压力容器专用板它具有良好的综合力学性能和工艺性能选择椭圆形封头2 裙座材料的选择裙座不直接与塔内介质接触也不承受塔内介质的压力因此不受压力容器用材的限制可选用较经济的普通碳素结构钢故选用Q235-A3 接管的材料选用Q235-B作为补强圈的材料部分接管用20法兰选用20具体将在装配图上注明11气体和液体的进出口装置由Vs 为流体的体积流量m3su 为适宜的流体流速ms常压气体进出口管气速可取1020ms液体进出口速度可取0815 ms选用气体流速为15ms代入上式计算得圆整之后气体进出口管径为d250mm 选液体流速为15ms由代入上公式得圆整之后气体进出口管径为d40mm 底液出口管径选择12原料液进出管的选择1进料管300mm选的流体输送用无缝钢管《GBT8163-2008流体输送用无缝钢管》标记10- -GBT8163-2008查《GBT17395-2008无缝钢管尺寸外形重量及允许偏差》具体参数见表3-1 2出料管当时d034md40mm选的流体输送用无缝钢管《GBT8163-2008流体输送用无缝钢管》弯管结构R 为650mm标记10--GBT8163-2008查《GBT17395-2008无缝钢管尺寸外形重量及允许偏差》具体参数见表3-1表2-1普通钢管尺寸及单位长度理论重量外径mm 壁厚mm 单位长度理论重量kgm 325 75 5873 48 3 333 13筒体和封头的设计材料选择筒体的设计化工设备机械基础厚度计算解得圆整后表3-1筒体的容积面积及重量公称直径Dgmm 一米高的容积Vm3 一米高的内裹面积Fgm2 壁厚Smm 一米高筒节钢板理论重量kg 900 0636 283 4 79 封头的设计选用标准GB_T 25198-2010_压力容器封头图3-1椭圆形封头的结构示意图选用标准GB_T 25198-2010_压力容器封头表3-2筒体的容积面积及重量公称直径Dgmm 曲面高度h1mm 直边高度H2mm 厚度Smm 重量Gkg 900 220 30 4 292 14法兰的设计1管法兰的选择选用标准HG20593-97板式平焊钢制管法兰欧洲体系图3-2板式平焊钢制法兰PL表4-1PN06MPa60bar板式平焊钢制管法兰mm管子直径mm 法兰内径mm 螺栓孔中心圆直径mm 公称直径mm 螺栓孔直径mm 螺栓孔数量n 法兰外径mm 法兰厚度mm 法兰理论重量kg 液体进出口57 59 125 50 18 4 165 19 25 气体进出口325 328 400 300 22 12 445 26 135 标记液体进出口HG20593法兰PL57-06FFQ235-A气体进出口HG20593法兰PL325-06FFQ235-A2容器法兰的选择选用标准JBT4701-2000甲型平焊法兰标记法兰P900-4010-JBT4701-2000图3-3甲型平焊法兰平面密封面代号P表4-2PN025MPa甲型平焊法兰的结构尺寸mm公称直径 DNmm 法兰mm 螺柱D D1 δ d 规格数量900 1015 980 40 18 M16 36三反应釜釜体的设计31 固定床DNPN将固定反应器视为筒体本设计采用一般的反应釜由反应器内物料为液相由则圆整32 筒体壁厚最大操作压力为设计压力P取最大工作压力的10511倍[2]本设计取设计压力设计温度T根据筒体设计压力和设计温度选择材料Q345R许用应力为焊缝系数=10双面对接焊100无损探伤表3-1 焊接接头系数φ无损检测的长度比例焊接接头形式全部局部双面焊对接接头或相当于双面焊的对接接头085 单面焊对接接头沿焊缝根部全长有紧贴基本金属的垫板09 08 理论厚度钢板负偏差C1腐蚀裕量C2C22mm单面面腐蚀表3-2 钢板负偏差C1钢板厚度 2 22 25 28-30 22-35 38-4 45-55 负偏差 013 014 015 016 018 02 02 钢板厚度6-7 8-25 26-30 32-34 36-40 42-50 52-60 负偏差 06 08 09 1 11 12 13根据内压圆筒壁厚的计算公式带入以上数据得根据工程要求和钢材的使用壁厚范围圆整后取校核筒体水压试验强度根据式因为Q345R的屈服极限所以取代入得故水压试验满足强度要求33 封头封头包括有椭圆形碟形锥形球冠形封头平板封头等多种类型从工艺操作要求考虑对封头形状无特殊要求球冠形封头平板封头都存在较大的边缘应力且采用平板封头厚度较大故不宜采用半球形封头受力最好壁厚最薄重量轻但深度大制造较难中低压小设备不宜采用碟形封头存在局部应力受力不如椭圆形封头标准椭圆形封头制造比较容易受力状况比碟形封头好综合考虑该精馏塔设计内压温度等因素最终确定采用标准椭圆形封头选釜体的封头选标准椭球型代号EHA标准JBT47462002封头以Q345R为材料标准形封头壁厚其中整体冲压钢板负偏差代入得根据工程要求和钢材的使用壁厚范围圆整后取与前计算的筒体壁厚一致内表面积封头的标准为EHA 4000×13-Q235R JBT 4746综上筒体和封头选材都为Q235R壁厚34 筒体长度HDN4000mmH18M以内径为公称直径的椭圆形封头的尺寸内表面积和容积可得由于使用的是标准封头所以所以可得封头的高度h2m整体塔高度。
HPPO法制环氧丙烷工艺流程图册
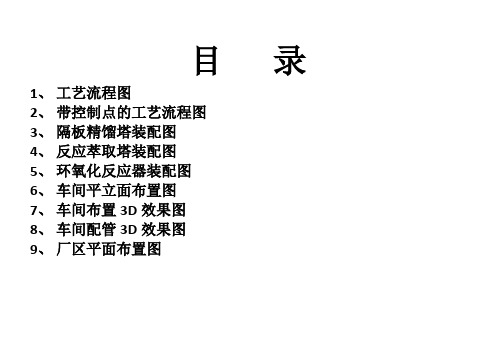
天津大学GB3432化学工程设计组 法兰类型及 密封面形式 RF RF RF
内螺纹 项目负责人 段兆阳 沈国强 沈国强 温嘉伟 温嘉伟 李敬楠 李敬楠
代号 a b c d1-3
公称直径 DN200 DN170 DN170 DN25
接管外壁与壁厚
标准号 HG20593 HG20593 HG20593 M25
7000
5000
T-0503
T-0404
T-0601
R-0302
5000
T-0602
T-0603
V-0301 R-0301
T-0401
T-0402
T-0403
T-0501
4000
T-0502
V0401
V0402
V0403
V0501
10000
V0504
V0404
V0502
3000
6000
7000
7000
5000
6000
6000
7000
7000
5000
T-0503
T-0404
T-0601
R-0302
5000
T-0602
T-0603
V-0301 R-0301
T-0501
T-0402
T-0403
T-0501
4000
T-0502
10000
E-0401
E-0404
E-0409
E-0301
E-0410
E-0601
690
10
670
22 21 20 19 18
9 8 A
700
28
17 16 15 14 13
800
环氧丙烷装置培训教材
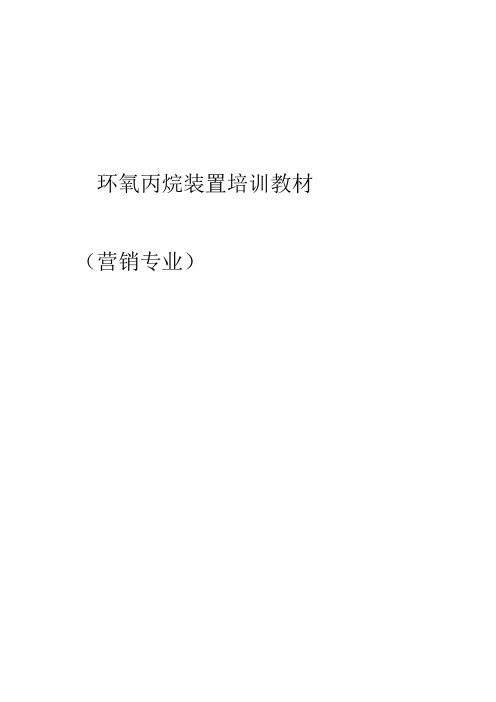
环氧丙烷装置培训教材(营销专业)生产流程简介第一章前言1.1在丙烯衍生产品中,环氧丙烷目前环氧丙烷是石油化工的重要中间体之一, 仅次于聚丙烯和丙烯腈的第三大衍生物。
,分子量为58.08OPO)分子式:CH)环氧丙烷(propylene oxide 简称63OCHCHCH。
结构式:32环氧丙烷是生产聚醚、表面活性剂、丙二醇、碳酸丙烯酯、烯丙醇等的主要原料。
我公司环氧丙烷装置采用氯醇法生产技术,连续法生产,年生产时间300天,装置生产能力50000吨/年,该装置的生产工艺比较完善合理,属国际先进水平,产品质量好,收率高,原料单耗低。
1.2装置组成本装置由下列单元组成:1)环氧丙烷主装置本系统分六个工序:(1)液氯汽化工序(2)氯醇化工序(3)尾气回收工序(4)皂化精馏工序(5)石灰乳制备工序(6)压滤工序2)丙烯原料罐区3)氯气原料罐区及液氯气化工序)石灰库区及石灰乳制备4.5)尾气回收装置6)产品及中间品罐区7)污水预处理及污水处理装置8)公用工程配套装置循环水、空压制氮站、冷冻站、工艺水站、消防水、锅炉房等9)原料、中控及成品化验室10)物流区及原料材料库区11)综合办公区1.3生产工艺(一)生产方法以丙烯、氯气、水为原料反应生成氯丙醇,氯丙醇再石灰乳发生皂化反应,生成粗环氧丙烷,在皂化过程中,生成的粗环氧丙烷中还含有水及少量氯化副产器(如二氯丙烷、二氯二异丙醚、丙醛等)。
为了生产出符合要求的环氧丙烷产品,需要精馏提纯。
粗环氧丙烷再经过精馏成为成品。
其传统工艺流程如图3-1所示。
3-1图环氧丙烷的传统工艺流程图(二)工艺特点)本装置采用国际上先进的管式反应器技术,工艺流程简单,安全可靠。
管式1.氯醇化反应设备是氯气与工艺水在喷射泵中充分预溶,然后与丙烯在管中混合并发生氯醇化反应。
管式反应设备由于采用圆管结构,径向返混激烈,气液接触充分;轴向返混少,近似平推流,反应可按理论等配比进行,氯丙醇选择性高,丙烯和氯气转化率高,因此不需要尾气循环,并节省了能源。
化学反应器设计基础学习PPT教案
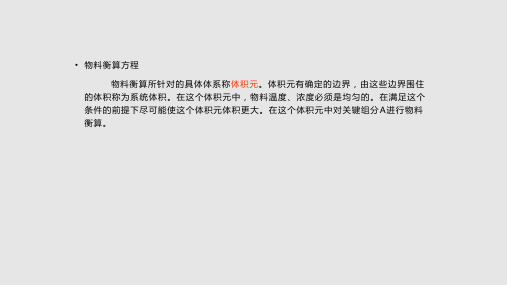
连续式完全混合(返混程度最大)
平推流反应器 (无返混)
非理想反应器
间歇反应器
• 间歇操作的充分搅拌槽式反应器(简称间歇反应器)。在反应器中物料被充分混合,但由于所有物料均为 同一时间进入的,物料之间的混合过程属于简单混合,不存在返混。
平推流反应器
• 理想置换反应器(又称平推流反应器或活塞流反应器)。在连续流动的反应器内物料允许作径向混合(属 于简单混合)但不存在轴向混合(即无返混)。典型例子是物料在管内流速较快的管式反应器。
t
• (3)空间时间τ 其定义为反应器有效容积VR与流体特征体积流率V0之比值。 即
VR
V • 空间时间是一个人为规定的参量,它表示处理在进口条件下一个反应器体积
的流体所需要的时间。
0
• 空间时间不是停留时间
空时为2h意思为每2个小时处理的物料量相当于一个反应器的体积
• (4)空间速度SV
• 有空速和标准空速之分。空速的一般定义为在单位时间内投入单位有效反应 器容积内的物料体积。即:
2
1 kcA0
xAf 1 xAf
• xA=0.6 tr=3.18h
•
•
xA=0.8 xA=0.9
t t
r= r=
8 1
.5 9.
h
0trh
1.97
1 10
3
4
0.5 1 0.5
1 2.10 60
h
• (2)反应器体积的计算 • xA= 0.8时:tt=tr+t’=8.5+1=9.5h • 每小时己二酸进料量FA0,己二酸相对分子质量为146,则有:
设计计算过程
• 对于给定的生产任务,即单位时间处理的原料量FA[kmol.h-1]以及原料组成CA0[kmol.m-3]、达到的产品要 求xAf及辅助生产时间t’、动力学方程等,均作为给定的条件,设计计算出间歇反应器的体积。
环氧丙烷反应器的设计PPT课件
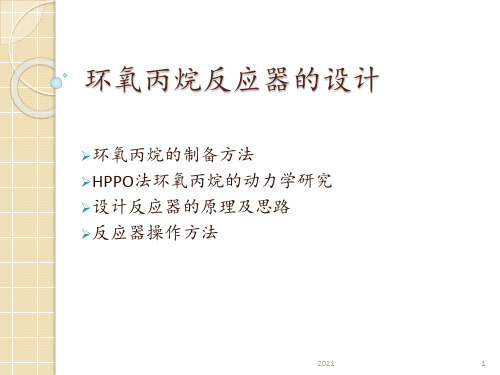
9
TS-1质量分数的影响
2021
10
2021
11
反应温度的影响
2021
12
2021
13
结论
2021
14
对于反应取上述反应条件时,其动力学 方程为:
2021
15
平推流反应器的设计方程
c
A0
xA 0
dxA rA
当反应温度为60℃时
r 0.0179 H2O2
2021
16
用Aspen模拟时的物流进料参数
2021
21
环氧丙烷反应器的设计
➢环氧丙烷的制备方法 ➢HPPO法环氧丙烷的动力学研究 ➢设计反应器的原理及思路 ➢反应器操作方法
2021
1
环氧丙烷的制备方法
环氧丙烷PO的生产工艺较多,目前国内外已 工业化的主要有:氯醇化法、共氧化法和过 氧化氢氧化法(简称HPPO法),其中共氧化法 又可以分为乙苯法和异丁烷法两种。根据 2007年世界PO生产能力统计,氯醇化法占总 生产能力的40.3%,共氧化法占51.5%,HPPO 法占5%。在共氧化法中,乙苯法占世界总生 产能力的24.9%,异丁烷法占26.6%。
氧化法
腐蚀;废水量小,环境污染小;
无联产品;装置投资少
过氧化
工程流程简单;产品收率
须解决过氧化氢的供应问题
氢 直 接 氧 化 高;无副产品;无污染,属环
法
境友好工艺
2021
3
HPPO法环氧丙烷动力学研究
2021
4
2021
5
反应压力的影响
2021
6
2021021
8
2021
2021
2
表 5-1 氯醇法、共氧化法、CHP 法和 HPPO 法技术优缺点对比
环氧丙烷精选 课件
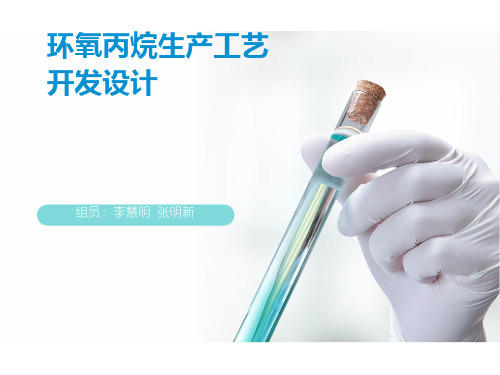
反应速率快
选择性高
钛 硅
分
子
筛
催
化
剂
4.流程模拟
1.原料预处理工段 2.双氧水合成工段 3.环氧丙烷工段
5.热集成
Aspen Energy Analyzer软件 Pinch分析方法
过程能量集成
选择最小 传热温差
确定夹点
换热网 络综合
5.热集成
未优化前的换热网络 优化后的换热网络
5.热集成
↓41.6%
5073
0.1612
↓25.0%
6.环境保护
1.循环利用
萃取剂乙腈的循环利用 甲醇的循环利用
2.高效催化剂
TS-1催化剂 反应速率快、选择性高 体现节能、减排、降耗、
清洁生产
7.厂区及车间平面布置
厂区平面布置各项技术指标
序号
名称
单位
数量
1
厂区占地面积
m2
33600
市场上主要用到的两种生产方法:氯 醇法和共氧化法
共氧化:与氯醇法工艺相比,共氧化法大幅度提高了单 套装置的生产规模,减少了污水的排放等。这在一定程 度上克服了氯醇法三废污染严重、腐蚀大和需求氯资源 的缺点,但也有其不利之处,如工艺流程长、防爆要求 严、投资大、对原料规格要求高、操作条件严格、联产 品比例大等,每生产1t环氧丙烷有2.5t叔丁醇或 1.8t苯乙烯生成,这远超过主产品的产量,而且副 产品的市场需求量波动大,所以PO生产受市场因素制 约严重。因此,PO/SM间接氧化法装置必须考虑对
环氧丙烷的市场需求
国内环氧丙烷的进口量
环氧丙烷的市场需求
我国环氧丙烷消费及预测(单位:万吨/年、%)
年份
2003 2004 2005 2006 2007 2008 2009 2010 2011 2012 2013(预计) 2020(预计)
HPPO法制环氧丙烷工艺描述及反应原理

HPPO环氧丙烷项目 工艺描述&反应原理一、流程概述HPPO工艺基于固定床反应系统制备环氧丙烷,该系统带有钛硅沸石挤出物粒子催化剂,粒子尺寸大约为3-5mm。
管束反应器(单段式反应器系统(R001A-C),用于移除反应过程中产生的相当大的反应热。
所有三个反应器系统通常都是平行操作的,但是也可以单独操作,例如,系统内其中一个反应器的再生操作。
反应器中以甲醇作为溶剂,质量百分比为50-70%的双氧水与丙烯反应生成环氧丙烷,并伴生少量的副产物。
在反应器入口,丙烯和过氧化氢的摩尔比,丙烷和丙烯的质量比以及甲醇和双氧水中水的质量比,明确了进入每个反应器内的进料组成。
为了达到反应目的,投用一个C3分离塔,精炼界区外来的丙烯,在此丙烷从原料丙烯中分离并送到界区外。
由于进入反应器的最初混合物和在每个反应器出口的产物混合物都是两相的,为了优化工艺条件,需要把丙烯和甲醇分开加料到每个反应器中,反应产物在反应器的底部也要相分离。
两个液体相的分布是通过位于每个反应器顶端的两相液体分布器完成的,从而实现反应系统的两相向下汇流至反应区。
通过闪蒸系统分离和回收过量的丙烯,此系统能回收90%未参与反应的丙烯。
C3汽提塔与回收C3压缩机成套单元,C3精馏塔和冷凝系统相连接回收剩余部分丙烯,经过冷凝后的残余气体送至净化气洗涤塔。
在净化气洗涤塔中用甲醇作为洗涤液,净化气洗涤塔作为废气的排放出口,可尽量避免任何丙烯损失。
环氧丙烷的分离通过由预分离塔、C3汽提塔和PO塔组成的系统完成。
预分离装置将环氧丙烷和丙烯中大部分的甲醇及水分离出去。
在C3汽提塔中,残余少量的丙烯会被去除,然后送入回收C3压缩机成套单元中。
最后,从PO塔顶产出提纯后的环氧丙烷产品,而带有一些水的甲醇会在塔底采出。
环氧丙烷精制是在PO塔萃取区内脱净甲醇,并在反应区内通过与精制剂反应去除乙醛。
两个部分整合在PO塔的中部,而水在塔上部精馏区内几乎全部被除去。
来自预分离塔底部和PO精馏塔底部甲醇和水的混合物中的乙醛及缩醛含量在加氢反应器中可以有效减少。
环氧丙烷装置培训教材
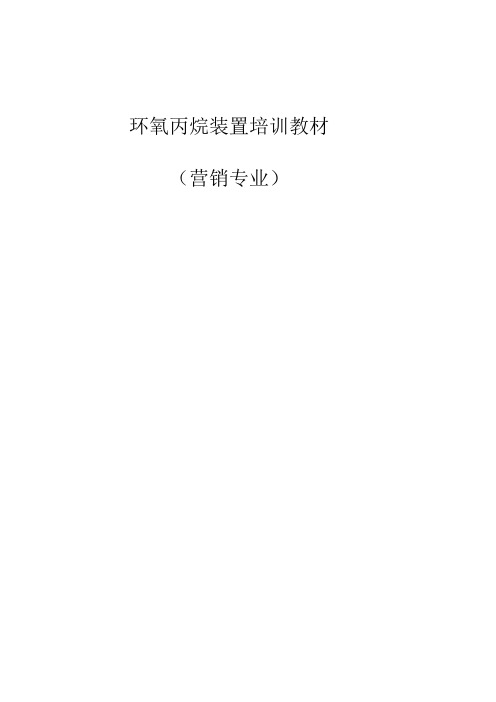
环氧丙烷装置培训教材(营销专业)第一章 生产流程简介1.1前言环氧丙烷是石油化工的重要中间体之一,在丙烯衍生产品中,环氧丙烷目前仅次于聚丙烯和丙烯腈的第三大衍生物。
环氧丙烷(propylene oxide 简称PO )分子式:C 3H 6O ),分子量为58.08。
结构式:H 2CCHCH 3O。
环氧丙烷是生产聚醚、表面活性剂、丙二醇、碳酸丙烯酯、烯丙醇等的主要原料。
我公司环氧丙烷装置采用氯醇法生产技术,连续法生产,年生产时间300天,装置生产能力50000吨/年,该装置的生产工艺比较完善合理,属国际先进水平,产品质量好,收率高,原料单耗低。
1.2装置组成本装置由下列单元组成: 1)环氧丙烷主装置 本系统分六个工序: (1)液氯汽化工序 (2)氯醇化工序 (3)尾气回收工序 (4)皂化精馏工序 (5)石灰乳制备工序 (6)压滤工序 2)丙烯原料罐区3)氯气原料罐区及液氯气化工序 4)石灰库区及石灰乳制备5)尾气回收装置6)产品及中间品罐区7)污水预处理及污水处理装置8)公用工程配套装置循环水、空压制氮站、冷冻站、工艺水站、消防水、锅炉房等9)原料、中控及成品化验室10)物流区及原料材料库区11)综合办公区1.3生产工艺(一)生产方法以丙烯、氯气、水为原料反应生成氯丙醇,氯丙醇再石灰乳发生皂化反应,生成粗环氧丙烷,在皂化过程中,生成的粗环氧丙烷中还含有水及少量氯化副产器(如二氯丙烷、二氯二异丙醚、丙醛等)。
为了生产出符合要求的环氧丙烷产品,需要精馏提纯。
粗环氧丙烷再经过精馏成为成品。
其传统工艺流程如图3-1所示。
图3-1环氧丙烷的传统工艺流程图(二)工艺特点1)本装置采用国际上先进的管式反应器技术,工艺流程简单,安全可靠。
管式氯醇化反应设备是氯气与工艺水在喷射泵中充分预溶,然后与丙烯在管中混合并发生氯醇化反应。
管式反应设备由于采用圆管结构,径向返混激烈,气液接触充分;轴向返混少,近似平推流,反应可按理论等配比进行,氯丙醇选择性高,丙烯和氯气转化率高,因此不需要尾气循环,并节省了能源。
100kta丙烷制环氧丙烷生产项目3-3 反应器设计说明书

100kt/a丙烷制环氧丙烷生产项目——反应器设计说明书反应器计算说明书100kt/a丙烷制环氧丙烷生产项目第一章概述化学反应过程和反应器是化工生产流程中的中心环节,反应器设计往往占有重要地位。
由于反应器单元内部涉及很多复杂的过程,如:热量的传递,温度的变化,反应速率的变化,而这些都将影响产品的产量和质量。
所以反应器一直以来都是化工设计的一个难题。
反应器设计的好坏也关系到整个生产过程是否能正常运行。
1.1设计目标反应器为工艺流程中反应进行的场所,主要需要满足:(1) 反应器有良好的传热能力;(2) 反应器内温度分布均匀;(3) 反应器有足够的壁厚,能承受反应压力;(4) 反应器结构满足反应发生的要求,保证反应充分;(5) 反应器材料满足反应物腐蚀要求;(6) 保证原料有较高的转化率,反应有理想的收率;(7) 降低反应过程中副反应发生的水平。
1.2反应器介绍本设计的主要反应均为由固体催化剂催化的气相反应,常见的气固相反应器主要有固定床和流化床两大类。
1.2.1固定床反应器固定床反应器又称填充床反应器,是一种装填有固体催化剂用以实现多相反应的反应器。
固体催化剂通常呈颗粒状,粒径2~15 mm,堆积成一定高度(或厚度)的床层,床层静止不动,流体通过床层进行反应。
目前我国的固定床反应器技术比较成熟,主要用于气固相催化反应,反应器包括氨合成塔、二氧化硫接触氧化器、烃类蒸汽转化炉等设备。
固定床反应器可分类为三种基本形式:轴向绝热式固定床反应器(见图1-1)。
流体沿轴向自上而下流经床层,床层同外界无热交换。
径向绝热式固定床反应器(见图1-2)。
流体沿径向流过床层,可采用离心流动或向心流动,床层同外界无热交换。
径向反应器与轴向反应器相比,流体流动的距离较短,流道截面积较大,流体的压力降较小。
但径向反应器的结构较轴向反应器复杂。
以上两种形式都属绝热反应器,适用于反应热效应不大,或反应系统能承受绝热条件下由反应热效应引起的温度变化的场合。
反应设备微反应器PPT课件

日用化学品 和聚合物
德国西门子(Siemens)公司
美国UOP公司
药物合成(Ciprofloxazin) 里特(Ritter)反应 硝化甘油 颜料 复配(Formulations) 催化剂 环氧丙烷 聚丙烯酸酯 过氧化氢
第15页/共18页
16
8.3 微反应器
8.3.3 微反应器的特点及应用
三、应用情况
板片采用扩散焊实现连接密封。
8
第8页/共18页
8.3 微反应器 8.3.2 微反应器的结构及制造工艺
三、微反应器的封装技术
右图是路易斯安那理工大学设计 的把环己胺脱氢为苯的微反应器 设计图,尺寸为20×14×3 mm。 由三部分组成,上部是用聚二甲基 硅氧烷制作的端盖,中间是用钯 (Pd)制成的折叠式隔膜,下部则是 用硅制成的反应室,三者之间用聚 酰亚氨粘接,该反应器能在250℃ 以下稳定工作。
微反应系统的层次结构
第1页/共18页
2
8.3 微反应器
8.3.2 微反应器的结构及制造工艺
二、微反应器的加工技术
微反应器材料的选择取决于介质的腐蚀性能、操作温度、操作压力、加工方 法等。常用的材料有:
硅:硅的密度小(2.3 g/cm3);熔点高(1400℃),约为铝的两倍;热膨胀系 数小,只有铝的十分之一;单晶硅的屈服强度比不锈钢大三倍;硅具有各向 异性,便于进行选择性刻蚀。
塑料和聚合物等材料:易于光刻电镀和压模成型加工。
第2页/共18页
3
8.3 微反应器
8.3.2 微反应器的结构及制造工艺
二、微反应器的加工技术
微反应器常用加工技术可分为三类: 一是由IC(集成电路)平面制作工艺延伸而来的硅体微加工技术: 包括湿法刻蚀(各向同性刻蚀和各向异性刻蚀)、干法刻蚀(溅射刻蚀、 等离子刻蚀) 二是超精密加工技术:微细放电加工(micro-EDM)、激光束加工、电子束 加工和离子束加工。 三是LIAG工艺:包括光刻、电镀和压模三步的组合技术,由德国喀尔斯鲁 厄核研究中心发明。
年产25万吨环氧丙烷初步工艺设计

年产25万吨环氧丙烷初步工艺设计环氧丙烷是一种重要的有机化工产品,广泛用于化学工业和材料制备中。
下面是一个关于年产量为25万吨环氧丙烷的初步工艺设计。
1. 原料准备环氧丙烷的主要原料是丙烯和过氧化氢。
丙烯是一种石油化工产品,可由石油 cracking 反应得到。
过氧化氢则是通过氢气和氧气在催化剂存在下反应得到。
2. 反应器设计环氧丙烷的制备主要通过丙烯与过氧化氢的反应进行。
该反应是一个三元反应,需要一个反应器来提供适宜的反应条件。
反应器一般使用不锈钢材料制成,以抵抗反应过程中的高温和高压。
反应器内部有大小不同的搅拌桨和传热器,以确保反应的均匀性和高效性。
3. 过程步骤首先,将丙烯和过氧化氢以一定的比例加入反应器中,控制反应器内的温度和压力。
在适当的温度和压力条件下,反应开始进行。
反应出来的环氧丙烷通过毛细管泵送出反应器,并经过冷却和分离处理。
4. 冷却和分离处理经过反应的产物还含有未反应的丙烯和过氧化氢,以及一些副产物和杂质。
冷却处理会使环氧丙烷凝固,而丙烯和过氧化氢则继续保持气态。
通过冷却器和分离装置,可以将环氧丙烷与气态的丙烯和过氧化氢分离开来,并收集纯净的环氧丙烷。
5. 产品收集和储存分离出来的环氧丙烷经过一系列的收集、储存和包装处理,最终以液体形式储存。
储存设施需要加强安全措施,以防止环氧丙烷的泄漏和事故发生。
以上是一份关于年产量为25万吨环氧丙烷的初步工艺设计。
在实际的生产中,还需要进行更详细的工艺设计和设备选型,以及考虑安全环保等因素。
这个初步设计提供了一个基本的框架,可以作为后续工艺设计的参考。
继续写相关内容,1500字6. 能源消耗和废物处理在环氧丙烷的生产过程中,需要消耗大量的能源,包括加热反应器、冷却凝固、分离和储存等环节。
因此,能源消耗的优化对于整个工艺的经济性和可持续性非常重要。
可以通过高效的能源回收和利用系统,将废热转化为有用的热能,降低能源消耗。
与能源消耗密切相关的是废物处理。
HPPO法制环氧丙烷工艺描述及反应原理

HPPO环氧丙烷项目 工艺描述&反应原理一、流程概述HPPO工艺基于固定床反应系统制备环氧丙烷,该系统带有钛硅沸石挤出物粒子催化剂,粒子尺寸大约为3-5mm。
管束反应器(单段式反应器系统(R001A-C),用于移除反应过程中产生的相当大的反应热。
所有三个反应器系统通常都是平行操作的,但是也可以单独操作,例如,系统内其中一个反应器的再生操作。
反应器中以甲醇作为溶剂,质量百分比为50-70%的双氧水与丙烯反应生成环氧丙烷,并伴生少量的副产物。
在反应器入口,丙烯和过氧化氢的摩尔比,丙烷和丙烯的质量比以及甲醇和双氧水中水的质量比,明确了进入每个反应器内的进料组成。
为了达到反应目的,投用一个C3分离塔,精炼界区外来的丙烯,在此丙烷从原料丙烯中分离并送到界区外。
由于进入反应器的最初混合物和在每个反应器出口的产物混合物都是两相的,为了优化工艺条件,需要把丙烯和甲醇分开加料到每个反应器中,反应产物在反应器的底部也要相分离。
两个液体相的分布是通过位于每个反应器顶端的两相液体分布器完成的,从而实现反应系统的两相向下汇流至反应区。
通过闪蒸系统分离和回收过量的丙烯,此系统能回收90%未参与反应的丙烯。
C3汽提塔与回收C3压缩机成套单元,C3精馏塔和冷凝系统相连接回收剩余部分丙烯,经过冷凝后的残余气体送至净化气洗涤塔。
在净化气洗涤塔中用甲醇作为洗涤液,净化气洗涤塔作为废气的排放出口,可尽量避免任何丙烯损失。
环氧丙烷的分离通过由预分离塔、C3汽提塔和PO塔组成的系统完成。
预分离装置将环氧丙烷和丙烯中大部分的甲醇及水分离出去。
在C3汽提塔中,残余少量的丙烯会被去除,然后送入回收C3压缩机成套单元中。
最后,从PO塔顶产出提纯后的环氧丙烷产品,而带有一些水的甲醇会在塔底采出。
环氧丙烷精制是在PO塔萃取区内脱净甲醇,并在反应区内通过与精制剂反应去除乙醛。
两个部分整合在PO塔的中部,而水在塔上部精馏区内几乎全部被除去。
来自预分离塔底部和PO精馏塔底部甲醇和水的混合物中的乙醛及缩醛含量在加氢反应器中可以有效减少。
100kta丙烷制环氧丙烷生产项目3-3 反应器设计说明书

100kt/a丙烷制环氧丙烷生产项目——反应器设计说明书反应器计算说明书100kt/a丙烷制环氧丙烷生产项目第一章概述化学反应过程和反应器是化工生产流程中的中心环节,反应器设计往往占有重要地位。
由于反应器单元内部涉及很多复杂的过程,如:热量的传递,温度的变化,反应速率的变化,而这些都将影响产品的产量和质量。
所以反应器一直以来都是化工设计的一个难题。
反应器设计的好坏也关系到整个生产过程是否能正常运行。
1.1设计目标反应器为工艺流程中反应进行的场所,主要需要满足:(1) 反应器有良好的传热能力;(2) 反应器内温度分布均匀;(3) 反应器有足够的壁厚,能承受反应压力;(4) 反应器结构满足反应发生的要求,保证反应充分;(5) 反应器材料满足反应物腐蚀要求;(6) 保证原料有较高的转化率,反应有理想的收率;(7) 降低反应过程中副反应发生的水平。
1.2反应器介绍本设计的主要反应均为由固体催化剂催化的气相反应,常见的气固相反应器主要有固定床和流化床两大类。
1.2.1固定床反应器固定床反应器又称填充床反应器,是一种装填有固体催化剂用以实现多相反应的反应器。
固体催化剂通常呈颗粒状,粒径2~15 mm,堆积成一定高度(或厚度)的床层,床层静止不动,流体通过床层进行反应。
目前我国的固定床反应器技术比较成熟,主要用于气固相催化反应,反应器包括氨合成塔、二氧化硫接触氧化器、烃类蒸汽转化炉等设备。
固定床反应器可分类为三种基本形式:轴向绝热式固定床反应器(见图1-1)。
流体沿轴向自上而下流经床层,床层同外界无热交换。
径向绝热式固定床反应器(见图1-2)。
流体沿径向流过床层,可采用离心流动或向心流动,床层同外界无热交换。
径向反应器与轴向反应器相比,流体流动的距离较短,流道截面积较大,流体的压力降较小。
但径向反应器的结构较轴向反应器复杂。
以上两种形式都属绝热反应器,适用于反应热效应不大,或反应系统能承受绝热条件下由反应热效应引起的温度变化的场合。
催化反应工程华东理工大学第五章2环氧乙烷合成反应器
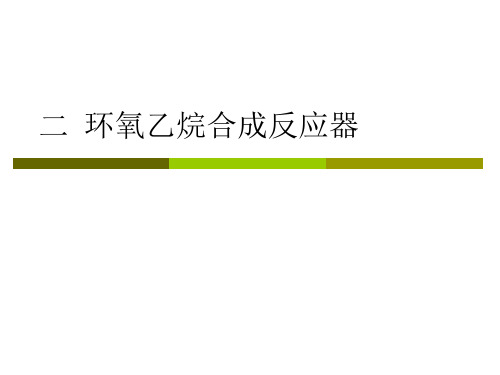
边界条件(无因次化)
Z 0 0
yC2H4
y , o C2H4
yCO2
yo CO2
,
1
yC2H4 yCO2 0, s 0
1
y C2 H 4
yCO2
0, w
Bi f
, w
s
Bis
s
模型参数的计算公式
径向弥散混合系数计算公式:
Der
ud p
10[119.4 d p / dl
核心设备反应器是立式列管固定床反应器,壳体走 蒸汽,反应的原料气走管内。
反应器特性和操作条件见下表
表 环氧乙烷合成反应器特性和操作条件
催化剂填充高度
反应管内径 列管数
催化剂外形尺寸 催化剂装填量
空速 反应压力 原料气进口温度 饱和蒸汽压力 饱和蒸汽温度
7.00m
31.3mm 8821
6.5×2.5×6mm 55.44ton
fCO2 2COR2r2 b ZRgT / Pk g,CO2 Se
b CORi Hi ri /sSeT 0 i1,2
反应器模型-二维非均相
气相方程(无因次化)
yC2H4 Z
Pe m ,C2 H 4
y2 C2 H 4 2
1
y C2 H 4
Da C2H4
y y C2H4
s C2 H 4
二 环氧乙烷合成反应器
1 环氧乙烷反应体系特性
在银催化剂上,乙烯(简称ET)氧化除得到 产物环氧乙烷(简称EO)外,主要副产物是 二氧化碳和水。
C2
H
+
4
1 2
O2
C 2H4O
(1)
C H +3O 2CO 2H O (2)
24
【精品】生产环氧丙烷换热器设计说明书
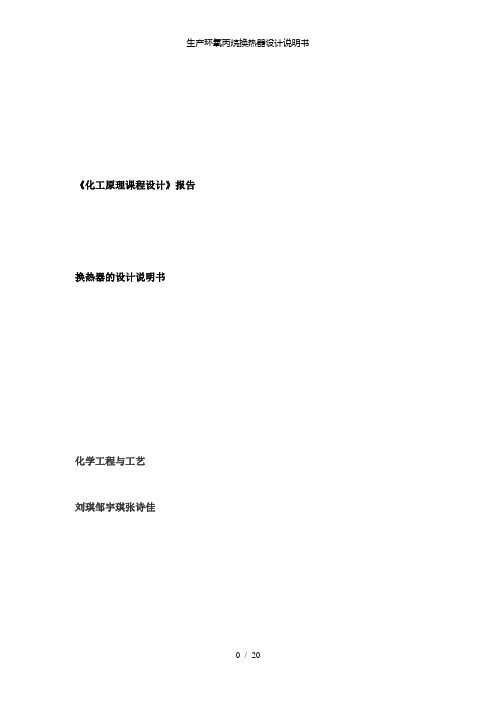
《化工原理课程设计》报告换热器的设计说明书化学工程与工艺刘琪邹宇琪张诗佳目录1.1换热器设计任务书21.2换热器的结构形式21.3换热器的材质选择41.4管板式换热器的优点51.5管板式换热器的类型及工作原理61.6确定设计方案72.1设计参数82.2计算总传热系数82.3工艺结构尺寸102.4热流量核算111.1换热器设计任务书1、设计题目1,2-丙二醇冷却器的设计。
设计课题工程背景:在化工生产过程中,常常需要将各种产品进行冷却,本设计以某厂冷却丙二醇产品为例,让学生熟悉列管式换热器的设计过程。
设计的目的:通过对丙二醇产品冷却的列管式换热器设计,达到让学生了解该换热器的结构特点,并能根据工艺要求选择适当的类型,同时还能根据传热的基本原理,选择流程,确定换热器的基本尺寸,计算传热面积以及计算流体阻力。
2、设计任务及操作条件(1)处理能力10万吨/年环氧丙烷(2)设备型式列管式换热器(3)操作条件①热流体:1,2-丙二醇入口温度139℃,出口温度25℃②冷流体:自来水,入口温度13℃,出口温度90℃③允许压强降:不大于0.2bar④每年按330天计,每天24小时连续运行⑤绘制换热器总装配图。
1.2换热器的结构形式1、管壳式换热器管壳式换热器又称列管式换热器,是一种通用的标准换热设备,它具有结构简单,坚固耐用,造价低廉,用材广泛,清洗方便,适应性强等优点,应用最为广泛。
管壳式换热器根据结构特点分为以下几种:(1)固定管板式换热器固定管板式换热器两端的管板与壳体连在一起,这类换热器结构简单,价格低廉,但管外清洗困难,宜处理两流体温差小于50℃且壳方流体较清洁及不易结垢的物料。
带有膨胀节的固定管板式换热器,其膨胀节的弹性变形可减小温差应力,这种补偿方法适用于两流体温差小于70℃且壳方流体压强不高于600Kpa的情况。
(2)浮头式换热器浮头式换热器的管板有一个不与外壳连接,该端被称为浮头,管束连同浮头可以自由伸缩,而与外壳的膨胀无关。
- 1、下载文档前请自行甄别文档内容的完整性,平台不提供额外的编辑、内容补充、找答案等附加服务。
- 2、"仅部分预览"的文档,不可在线预览部分如存在完整性等问题,可反馈申请退款(可完整预览的文档不适用该条件!)。
- 3、如文档侵犯您的权益,请联系客服反馈,我们会尽快为您处理(人工客服工作时间:9:00-18:30)。
-
2
表 5-1 氯醇法、共氧化法、CHP 法和 HPPO 法技术优缺点对比
生产工 艺
优点
缺点
氯醇法
工艺成熟,流程简单;操
石灰料和水资源耗量大;生成
作弹性大;选择性好;对原料 大量废水、废渣,污染环境;消耗
丙烯的纯度要求低;安全性 大量高能耗的氯气;设备腐蚀较严
高;投资少,有成本竞争力 重
共氧化
产品陈本低(联产品分摊
无联产品;装置投资少
过氧化
工程流程简单;产品收率
须解决过氧化氢的供应问题
氢 直 接 氧 化 高;无副产品;无污染,属环
法
境友好工艺
-
3
HPPO法环氧丙烷动力学研究
-
4
-
5
反应压力的影响
-
6
-
7
溶剂中水质量分数的影响
-
8
-
9
TS-1质量分数的影响
-
10
-
11
反应温度的影响
-12Leabharlann -13Hr 26KJ / mol
水蒸气的冷凝潜热r 2134KJ / kg
由于本次反应消耗0.83kmol的H 2O2 所以Hr n W r 解得W 10.1kg
-
20
反应器的操作方法
-
21
环氧丙烷反应器的设计
➢环氧丙烷的制备方法 ➢HPPO法环氧丙烷的动力学研究 ➢设计反应器的原理及思路 ➢反应器操作方法
-
1
环氧丙烷的制备方法
环氧丙烷PO的生产工艺较多,目前国内外已 工业化的主要有:氯醇化法、共氧化法和过 氧化氢氧化法(简称HPPO法),其中共氧化法 又可以分为乙苯法和异丁烷法两种。根据 2007年世界PO生产能力统计,氯醇化法占总 生产能力的40.3%,共氧化法占51.5%,HPPO 法占5%。在共氧化法中,乙苯法占世界总生 产能力的24.9%,异丁烷法占26.6%。
工艺流程长;原料品种多,丙
法
成本);废水量小,环境污染 烯的纯度要求高,受原料来源制约
小;产品中无设备腐蚀
因素较大;操作压力高,设备多采
用合金钢,投资大;联产 2.2~2.5t
苯乙烯或 2.3t 叔丁醇,受产品销售
制约因素较大;污水含 COD 较高
异丙苯
不需要氧气,减少了设备
循环回收装置
氧化法
腐蚀;废水量小,环境污染小;
结论
-
14
对于反应取上述反应条件时,其动力学 方程为:
-
15
平推流反应器的设计方程
c
A0
xA 0
dxA rA
当反应温度为60℃时
r 0.0179 H2O2
-
16
用Aspen模拟时的物流进料参数
-
17
详细物流参数表
-
18
反应的空时
cA0
xA 0
dxA rA
116s
-
19
热量衡算