模具表面强化技术一
模具表面强化技术及其应用
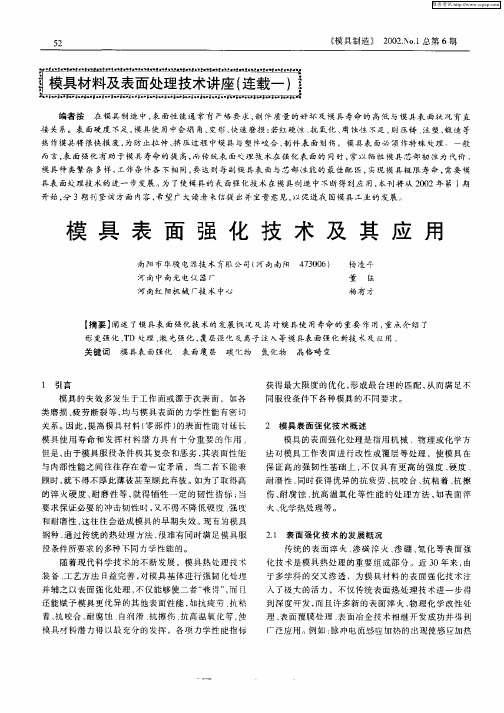
l 引 言
获得 晟 大限 度的优 化 , 形成最 合理 的匹 配 , 而满 足不 从
同服役 条件 下各 种模具 的不 同要 求 。
2 模 具 表 面 强 化 技 术 概 述
模具 的失 效 多发 生于 工作 面或 源 于次 表面 ,如各 类磨 损 、 劳断 裂等 , 与模 具表 面 的力学 性能 有密 切 疲 均
并 辅 之 以表面 强化 处理 , 不仅 能够使 二者 “ 得 ”而 且 兼 , 还能 赋予 模具 更咬台 、 腐蚀 、 抗 耐 自润滑 、 擦伤 、 高 温氧化 等 , 抗 抗 使
模具 材料 潜力 得 以最充 分 的发 挥 ,各项 力 学性 能指标
热作模 县将很 快报 废 , 为防 止拉 仲 、 挤压 过程 中摸具 与 塑件 喧夸 、 制件 表 面划 伤 ,模 具 表 面必 须作 特殊 处理 一一般
而言 . 面强化 有助 于模 具 寿命 的提 高 , 表 而传 统表 面处理技 术在 强化 表 面的 同时 , 以牺 牲 模具 芯部 韧性 为 代 价。 常 模具种 类繁 杂 多样 , I作条件 各 不相 同, 达 到每 副模 具表 面与芯部 一 要 洼能的 最佳 配 匹 , 实现 模 具极 限寿命 , 需要 模
模具 的表 面强 化处 理是 指 用机 械 、物 理 或化 学方
法对 模 具工 作表 面进行 改性 或 覆层 等处 理 ,使模 具在
保 证 高的强 韧 性 基础 上 , 仅具 有 更 高 的 强 度 、 度 、 不 硬
耐磨 性 . 时获得 优异 的抗 疲 劳 、 同 抗咬 合 、 抗粘 着 、 抗擦
关 系。因此 , 高模 具 材料 ( 提 零部 件 ) 的表面性 能对 延长 模 具使 用 寿命 和 发 挥 材 料潜 力 具 有 十分 重 要 的作 用 。 但 是 , 于模 具 服役条 件 极其 复杂 和恶 劣 , 由 其表 面性 能
关于塑料模具表面强化技术的研究

讨了 如何 正确运 用表 面强化技 术、 提 高塑料模具使 用寿命 , 表 明了我 国塑料模具表 面强化技术的发展方向 , 旨在进 一步推 动塑料模 具的发展及
应 用。
【 关键词】 塑料模具; 表面强化; 技术研究
我 国的塑料模具技术水平在工业化进程 中取得 了巨大 的进 步 . 但 与发达 国家的塑料模具技 术水平相 比 . 仍 存在着很 大的差距 . 我 国塑 料模具技术水平有着很大 的提升和发展空间 。 如何提高塑料模具使用 性能及使用寿命 . 是 当前塑料模具研究的一大课题 。对 塑料模 具表面 进行 强化 处理可以提高 塑料模具表 面硬度 、 耐磨性及 耐蚀性 . 进而有 效提高其使用性能及使用寿命 。 具失效 . 这种失效形式称为塑形变形失效。发生变形失效 的根本原 因 是模具型腔表面硬化层厚度过低 . 模具变形抗力不足或模具热处 理时 组织结构发生变化 塑料模具结构过于复杂 . 在成型过程中存在的较薄 的部位或 者塑 料模具 回火处理不足 . 在塑料制品生产时受压力及温度 的作用容 易产 生 断裂. 称 为断裂失效 断裂失效是失效形式 中危害最大 的一种 失效
压铸模具冲蚀表面强化处理

四、ASN: 提高模具抗冲蚀性能的表面处理
ASN表面强化处理
什么ASN表面处理?
ASN是在通过特殊工艺析出活性氮,碳 原子的气氛中进行低温浅层氮碳共渗的方 法。从而获得以渗氮为主的无白亮层氮碳 共渗层,化合层深度约3-5丝.(此工艺结合 ASO效果佳)
膜
ASO表面强化处理的机理
• 对压铸模进行ASO处理,在不改变原材料机械性 能的前提下,模具表面产生致密的连续的保护性
Fe3O4膜,呈鱼鳞状,这层保护氧化膜隔离了液
体金属与模具材料的直接接触, 从而能有效延缓 液体金属对压铸模具材料表面的粘着和熔损从而
提高模具抵抗侵蚀, (ASN+ASO复合处理更能体现模具优良的抗冲蚀 和侵蚀性.) • 蒸汽氧化膜其表面鳞片状结构增强了模具表面对 润滑剂的附着,降低摩擦系数,易于脱模。
裂纹弥合,在制品上不再有明显裂纹复制的 痕迹
ABP是提高模具耐热疲劳性,抵抗早期龟 裂即经济又实惠的方法!!
三、 ASO: 提高模具抗侵蚀性能的表面处理
ASO表面强化处理
什么是 ASO 表面处理?
ASO采用特别开发专用的设备,进
行蒸汽加热,在模具表面生成致密 的,稳定的具有保护性的Fe3O4氧化
ABP使表面的应力状态改善
60
20
Stress (kg/cm2)
-20
0
-60
-100
-140
-180
机械应力
5 10 15 20 25 30 35
ABP
Distance form surface(μm)
改善表面显微组织
ABP
EDM
模具的表面处理技术

模具的表面处理技术模具在工作中除了要求基体拥有充足高的强度跟韧性的合理搭配外,其表面性能对模具的工作性能跟运用寿命至关紧要。
这些表面性能指:耐磨损性能、耐腐蚀性能、摩擦系数、疲乏性能等。
这些性能的改善,单纯倚靠基体材料的改进跟提升是非常有限的,也是不经济的,而通过表面处理技术,往往能够收到事半功倍的效果,这也正是表面处理技术得到快速进展的原因。
模具的表面处理技术,是通过表面涂覆、表面改性或复合处理技术,更改模具表面的形态、化学成分、组织结构跟应力状态,以取得所需表面性能的系统工程。
从表面处理的方式上,又可分为:化学方法、物理方法、物理化学方法跟机械方法。
虽然旨在提升模具表面性能新的处理技术连续涌现,但在模具制造中应用较多的重要是渗氮、渗碳跟硬化膜沉积。
渗氮工艺有气体渗氮、离子渗氮、液体渗氮等方式,每一种渗氮方式中,都有若干种渗氮技术,能够适应不一样钢种不一样工件的要求。
由于渗氮技术可形成优良性能的表面,而且渗氮工艺跟模具钢的淬火工艺有良好的协调性,同时渗氮温度低,渗氮后不需白热化冷却,模具的变形微小,因此模具的表面强化是采纳渗氮技术较早,也是应用zui广泛的。
模具渗碳的目标,重要是为了提升模具的整体强韧性,即模具的工作表面拥有高的强度跟耐磨性,由此引入的技术思路是,用较低级的材料,即通过渗碳淬火来取代较另外材料,从而降低制造成本。
硬化膜沉积技术目前较成熟的是CVD、PVD。
为了加添膜层工件表面的结合强度,现今进展了多种加强型CVD、PVD技术。
硬化膜沉积技术zui早在工具(刀具、刃具、量具等)上应用,效果,多种刀具已将涂覆硬化膜作为标准工艺。
模具自上个世纪80时代开始采纳涂覆硬化膜技术。
目前的技术条件下,硬化膜沉积技术(重要是设备)的成本较高,依旧只在一些精密、长寿命模具上应用,假如采纳建设热处理中心的方式,则涂覆硬化膜的成本会大大降低,越来越多的模具假如采纳这一技术,能够整体提升我国的模具制造水平。
压铸模的表面强化技术

第2 4卷
效 的表面强 化技 术 。
2 1 渗氦 ( . 氮化 )
渗氮的方法也有很多种 , 如气体渗氮 、 离子渗氮 、 激光渗氮 、 固体渗氮 、 盐浴渗氮等。而最简单实用 的 方法 就是 固体 渗氮 和盐 浴渗 氮 , 其他方 法则 需要投 资 贵重 设 备 , 运 行 成本 较高 , 以只介 绍 固体 渗 氮 和 且 所
() 3 摩擦磨损。由于金属型无退让性 , 而铸件冷却时又要收缩 , 在取出铸件时, 铸型中受到铸件包围
的部 位 , 特别 是 抽芯机 构 , 到 铸件 的表 面黏 着摩擦 , 而产 生磨 损 , 终 影 响铸件 的尺 寸精度 。 受 进 最
此外 , 还有高温空气的氧化作用和金属流的侵蚀等作用 , 这些都会导致压铸模具的过早失效和损坏 ,
中 图分 类号 :G 7 T 6 文献标 识 码 : A
重庆汽车、 摩托车业的发展 , 带动了铸造行业特别是压铸行业的蓬勃发展 , 压铸技术也 因此受到人们的
极 大重视 。而压铸 摸具的设计制造 和强化处 理是 一个非 常重 要 的技术 环 节 , 它直 接关 系到 铸件产 品 的质量 和企 业的经济效益 , 也是从 事压铸专 业的工程 技术人员直接 面对 的关 键问题 。
1 压 铸 模 工 况分 析
压铸模 的工作条 件是 非常恶 劣 的 , 到多 种破 坏应力 的共 同作用 。 受
( )热疲劳裂纹。压铸模整体特别是表 面受到反 复加热 一 1 冷却循环、 热胀冷缩 、 热疲劳引起 的交变
热应力 非 常大 , 当交变 热应力 超 过材 料 的热 疲 劳强度 时 , 铸 模 具 表 面就 会 在 应 力 较集 中 的部 位产 生 微 压 小 裂纹 , 随着热疲 劳循 环逐 渐扩 大 , 后 形成 “ 并 最 龟裂 ” 。 ( )热 冲刷擦 伤 。工作 时高 温液 态金 属对 型腔 进行 反 复 的高 速 冲击 和冲刷 , 型腔 的表 面很容 易 冲 2 使 蚀 和擦 伤 。如 果脱模 分 型剂被 金属 流 冲开 , 也容 易 造 成 型腔 表面 和 金 属 液 黏合 在 一 起 , 强力 取 出铸 件 当 时, 就会 造成模 具型腔 的表 面拉 伤 。
模具表面强化技术及其应用

硬“ 涂层 ” 实为渗 层 ) 由于这些 碳化 物具 有很 高 的硬 ( 。
度 . 以经 T 所 D法 处理 的模 具可获 得特别 优异 的力 学性 能 。一 般来说 , 采用 T D处理 与采用 C D( 学气相 沉 V 化 积 )P V 等 离子 化 学 气 相 沉 积 ) 方法 进 行 的表 面 、 C D( 等 硬 化 处理效 果 相近 似 , 由 于 T 但 D法 设备 简 单 、 操作 简 便 、 本低廉 、 以是一 种 很有 发展前 途 的表 面强化 处 成 所 理 技术 。T D处 理 在国外 应 用 已相 当普 遍 , 在 国 内报 但
《 模具 制造 》 2 0 .o2总第 7期 0 2N
不同。
5 1 处理 的性能 比较 。
由 于碳 化 物 中 的 C来 自工 件 ( 材 ) 身 , 此 要 基 本 因
求 基材 的台碳 量在 04 - %以上 , 般 以含碳 量 较高 的工 一
具钢最适 宜作 T 处理 的基材 。 D
44 T . D处理 的工 艺 参数 影响 T D涂层厚 度 的主要 因素是 盐浴 温度 、 理 时 处 间和 基材 的化 学 成分 , 关 系为 = t ̄ , 中 D 为 其 Ae 式 “ 覆 ” 厚 度 (I )t 浸 渍 时间 () T为工 艺 温 度 涂 层 [I ; 为 i1 1 s; ( ; 为 碳 化 物 层 的 扩 散 激 活 能 ( 为 174 ~ K)9 约 6. 7
道 并不 多见 。
43 碳 化 物 的 形 成 机 理 _
气相沉积技术

物理气相沉积
物理气相沉积(简称PVD)是将金属、合金或化合物放在真空室中蒸发(或称溅射)。使这些气相原子或分子在 一定条件下沉积在工件表面上的工艺。物理气相沉积可分为真空蒸镀、真空溅射和离子镀互类。与CVD相比,PVD 法的主要优点是处理温度较低,沉积速度较快,无公害等,因而有很高的实用价值。它的不足之处是沉积层与工 件的结合力很小,镀层的均匀性稍差。此外它的设备造价高,操作维护的技术要求也较高。
涂层的特点
①涂层具有很高的硬度、低的摩擦系数和自润滑性能,所以耐磨损性能良好。 ②涂层具有很高的熔点、化学稳定性好,基体金属在涂层中的溶解度小,摩擦系数较低,因而具有很好的抗 黏着磨损能力。使用中发生冷焊和咬合的倾向也很小,而且TiN比TiC更好。 ③涂层具有较强的耐蚀能力。 ④涂层在高温下也具有良好的抗大气氧化能力。
③方法的复合。较先进的气相沉积工艺多是各种单一PVD,CVD方法的复合。它们不仅采用各种新型的加热源, 而且充分运用各种化学反应高频电磁(脉冲、射频、微波等)及等离子体等效应来激活沉积粒子。如反应蒸镀、反 应溅射、离子束溅射、多种等离子体激发的CVD等。
化学气相沉积
化学气相沉积(简称CVD)是利用气态物质在一定温度下于固体表面进行化学反应,并在其表面上生成固态沉 积膜的过程。其过程如下:
气相沉积技术
利用气相中发生的物理、化学过程,改变工件表面成分
01 应用
目录
02 发展前景
03 化学气相沉积
04 物理气相沉积
第5章 模具钢料的热处理-模具表面处理技术

第二节模具表面处理工艺概述模具是现代工业之母。
随着社会经济的发展,特别是汽车、家电工业、航空航天、食品医疗等产业的迅猛发展,对模具工业提出了更高的要求。
如何提高模具的质量、使用寿命和降低生产成本,成为各模具厂及注塑厂当前迫切需要解决的问题。
模具在工作中除了要求基体具有足够高的强度和韧性的合理配合外,其表面性能对模具的工作性能和使用寿命至关重要。
这些表面性能指:耐磨损性能、耐腐蚀性能、摩擦系数、疲劳性能等。
这些性能的改善,单纯依赖基体材料的改进和提高是非常有限的,也是不经济的,而通过表面处理技术,往往可以收到事半功倍的效果;模具的表面处理技术,是通过表面涂覆、表面改性或复合处理技术,改变模具表面的形态、化学成分、组织结构和应力状态,以获得所需表面性能的系统工程。
从表面处理的方式上,又可分为:化学方法、物理方法、物理化学方法和机械方法。
在模具制造中应用较多的主要是渗氮、渗碳和硬化膜沉积。
◆提高模具的表面的硬度、耐磨性、摩擦性、脱模性、隔热性、耐腐蚀性;◆提高表面的高温抗氧化性;◆提高型腔表面抗擦伤能力、脱模能力、抗咬合等特殊性能;减少冷却液的使用;◆提高模具质量,数倍、几十倍地提高模具使用寿命。
减少停机时间;◆大幅度降低生产成本与采购成本,提高生产效率和充分发挥模具材料的潜能。
◆减少润滑剂的使用;◆涂层磨损后,还退掉涂层后,再抛光模具表面,可重新涂层。
在模具上使用的表面技术方法多达几十种,从表面处理的方式上,主要可以归纳为物理表面处理法、化学表面处理法和表面覆层处理法。
模具表面强化处理工艺主要有气体氮化法、离子氮化法、点火花表面强化法、渗硼、TD法、CVD化学气相淀积、PVD物理气相沉积、PACVD离子加强化学气相沉积、CVA铝化化学气相沉积、激光表面强化法、离子注入法、等离子喷涂法等等。
下面综述模具表面处理中常用的表面处理技术:一、物理表面处理法:表面淬火是表面热处理中最常用方法,是强化材料表面的重要手段,分高频加热表面淬火、火焰加热表面淬火、激光表面淬火。
模具材料及表面强化处理1

模具材料及表面强化处理1引言模具是工业生产中必不可少的工具,它们在制造产品的过程中起着至关重要的作用。
模具材料的选择和表面强化处理对于模具的性能和寿命有着重要的影响。
本文将介绍常见的模具材料以及常用的表面强化处理方法。
一、模具材料1.1 铸造模具材料1.1.1 灰铁灰铁常用于生产小型模具,其具有良好的耐磨性和可加工性。
然而,由于其脆性较高,不适用于生产大型模具。
1.1.2 钢钢是最常用的模具材料之一,具有良好的强度和耐磨性。
根据工作条件的不同,可以选择碳素钢、合金钢或工具钢作为模具材料。
1.1.3 铝合金铝合金模具具有较低的密度和良好的导热性能,适用于高速冲压和热压成型。
1.2 塑料模具材料1.2.1 铝合金铝合金模具用于生产小型塑料制品,如手机壳等。
它具有良好的导热性和低重量,适用于高速注塑。
1.2.2 硅橡胶硅橡胶模具适用于制造高精度的塑料制品,如光学镜片。
它具有较低的粘附性和高弹性,便于脱模。
二、表面强化处理方法2.1 热处理热处理是常用的表面强化处理方法之一,通过控制材料的加热和冷却过程,使材料的组织结构得到改善,提高其硬度和耐磨性。
2.2 表面喷涂表面喷涂是一种常见的表面强化处理方法,通过在模具表面喷涂一层具有高硬度和耐磨性的材料,如陶瓷涂层或金属涂层,增加模具的寿命和耐磨性。
2.3 氮化处理氮化处理是一种提高模具硬度和耐磨性的表面强化处理方法。
在高温下,将模具表面与氨气反应,形成氮化层,提高模具的硬度和耐磨性。
2.4 氧化处理氧化处理是一种常用的提高模具抗氧化性能的表面强化处理方法。
通过在模具表面形成氧化层,阻止金属与氧气的直接接触,降低模具的氧化速度。
三、结论模具的材料选择和表面强化处理对于模具的性能和寿命有着重要的影响。
灰铁、钢和铝合金是常用的铸造模具材料,而铝合金和硅橡胶是常用的塑料模具材料。
常见的表面强化处理方法包括热处理、表面喷涂、氮化处理和氧化处理,通过这些方法可以提高模具的硬度、耐磨性和抗氧化性能。
第十章-模具表面强化技术

*
表面化学热处理技术
二、渗氮(氮化)
(一)气体渗氮
表2 部分模具钢的气体渗氮工艺规范
牌号
处理 方法
渗氮工艺规范
渗氮层 深度/mm
表面硬度
阶段
渗氮温度/℃
时间/h
氨分解率/%
30CrMnSiA
一段
—
500±5
25~30
20~30
0.2~0.3
(一)气体渗氮
(1) 经过渗氮后钢表面形成一层极硬的合金氮化物,渗氮层的硬度一般可达到68~72HRC,不需要再经过淬火便具有很高的表面硬度和耐磨层,而且还可以保持到600~650℃而不明显下降。
(2) 渗氮后钢的疲劳极限可提高15%~35%。这是由于渗氮层的体积增大,使工件表面产生了残余压应力。
(3) 渗氮后的钢具有很高的抗腐蚀能力。
>58HRC
Cr12MoV
760~800HV
*
表面化学热处理技术
二、渗氮(氮化)
(二)离子渗氮
离子渗氮有如下特点:
(1) 渗氮速度快,生产周期短。
(2) 渗氮层质量高。
(3) 工件的变形小。
(4) 对材料的适应性强。
氮碳共渗
提高硬度、耐磨性、抗粘附性、抗蚀性、耐热疲劳性
冷挤模、拉深模、挤压模穿孔针
渗硼
具有极好的表面硬度、耐磨性、抗粘附性、抗氧化性、热硬性、良好的抗蚀性
挤压模、拉深模
碳氮硼三元共渗
提高硬度、强度、耐磨性、耐疲劳性、抗蚀性
挤压模、冲头针尖
盐浴覆层 (TD处理)
提高硬度、耐磨性、耐热疲劳性、抗蚀性、抗粘附性、抗氧化性
表面强化技术

• 2.机理: 加工硬化机理。即随变形量的 增加,金属强度硬度升高,塑性韧性下 降。
• 原因:a、位错密度随变形量增加而增加, 从而变形抗力增加;b、随变形量增加, 亚结构细化,亚晶界对位错运动有阻碍; c、随变形量增加,空位密度增加;d、 几何硬化。
件、轴类零件和沟槽类零件等,对形状
复杂的零件表面就无法应用了。
四、孔挤压强化
• 1.定义:利用特定的工模具(棒、衬套、 开合模具等)对工件的孔壁或周边进行 连续、缓慢、均匀的挤压,使其形成一 定厚度的塑性变形层,达到提高表面疲 劳强度和抗应力腐蚀能力的一种表面强 化工艺。
• 2.工艺方法:棒挤压、套挤压、压印模挤 压、旋压挤压。
HRC=20+60(2C-1.3C2)
• (4)加热温度的确定
• (5)感应加热淬火设备参数确定
• 包括感应电源、感应圈、喷火装置。
• 感应电源的输出频率主要有高频(100~ 500KHz)、超音频(20~100KHz)、中频 (0.5~10KHz)、和工频(50Hz)。频率是根 据零件的尺寸和硬化层深度确定的。
(4)需很大的设备投入,所以单件小批量生产时 生产成本高。大型的工件淬火,它无法完成。 设备无法移动,因此灵活性相对较差。
• 3、工艺流程和技术要点
预先调质 处理
确定加热温 度与加热方式
根据工件要 求选择功率
制定回火 工艺参数
确定冷却方 式与冷却介质
设计感应 加热器
• (1)前期的预先处理
中高碳钢经过调质处理后,心部可以获得强度和
成本低、应用范围广的零件表面强化技术。它 的强化效果主要表现在延长承受交变负荷的零 件使用寿命。这个效果特别明显,也特别立竿 见影,是其它强化方法难以比拟的。
压铸模具的表面处理(完整版)

黏着的机理
• 黏着是指压铸产品与模具之间粘合,造成产 品和模具的表面损伤. A,原因 1,脱模剂没有均匀附着模具表面. 2,模具表面受到损伤 3,模具表面硬度偏低
黏着
B,解决方案 1,模具表面要有一定粗糙度,以利于脱模剂 的均匀附着.(ABP处理) 2,增加表面硬度和表面强度。(ASN处理)
ASSAB表面强化处理的定义
镁压铸模
AfterASN
AfterASO
ASN+ASO Case Study
Component : 电加热水壶 Tool type: Zn 压铸 Work material: 3# Zn 合金 Die Casting Type: Hot Chamber Working Load:150 T
Original Tool steel Hardness Surface treatment performance Failure due to 8407 50 HRC 使用早期发生侵 蚀 侵蚀 Replacement 8407 50HRC ASN+ASO 60,000 Still use
处理方法: 焊接+ ABP+ ASO 结果 : 20,000 模后发生侵蚀
NINGBO
ASN+ASO的应用
• ASN+ASO 搭配(特殊浅层氮化与蒸汽氧化)处理,既达 到了氮化的耐磨性,又有氧化膜隔离铝液。 从而提高模具抵抗冲蚀,侵蚀能力。(氮 化深层约3-5丝,氧化层3-5um.)
ASN+ASO
压铸模具表面强化处理
目录
一、模具的失效方式及解决方案 二、ABP: 提高模具抗热疲劳龟裂的表面处理 三、 ASO: 提高模具抗侵蚀性能的表面处理 四、ASN: 提高模具抗冲蚀性能的表面处理 五、ABP+ASN ABP+ASO ASN+ASO 套餐应用 六、未来计划
模具表面喷丸强化

模具表面喷丸强化随着现代工业技术的发展,对于模具使用性能提出了更高的要求。
努力缩短模具的生产周期提高模具的质量,延长模具寿命,直接或间接带来的社会效益和经济效益是难以估量的。
材料和热处理是影响模具质量、性能和使用寿命最重要的内在因素。
60%模具的早期失效,是由材料和热处理的因素造成的。
为了提高模的强度及模具的耐磨性,充分挖掘模具材料的性能潜力,延长模具服役寿命,采取了许多有效的措施,从省能源、省资源、充分发挥材料的性能潜力,获得特殊性能和最大技术经济效益出发,发展和应用表面强化工艺技术是提高模具使用性能和寿命的极重要的发展方向,喷丸强化就是其中的一项经济、简便而有效的模具表面处理工艺方法,值得大力推广。
喷丸强化是借助于硬丸粒,高速、连续锤击金属表面,使其产生强烈的冷作硬化。
通过喷丸可以明显改变金属表面的应力状态、显微硬度、表层的微观形貌和相成分,从而提高模具的疲劳强度、抗冲击磨损及抗应力腐蚀性能。
喷丸还可改变模具的表面粗糙度,并有效地去除电火花加工而产生的表面变质层。
喷丸强化方法简单易行,节约能源,适用于落料模、冷作模、冷镦模和热锻模等以疲劳失效形式为主的模具,如锻模服役时,要经受弯曲和热膨胀,常发生因局部屈服而导致显微裂纹,喷丸处理产生压应力能推迟显微裂纹的形成,从而延迟模具龟裂发生,模具经喷丸强化后使用寿命情况如表1所示。
喷丸强化原理喷丸过程就是大量弹丸喷射到零件表面上的过程,而弹丸喷射到零件表面上有如无数小锤对表面锤击,因此,金属零件表面产生极为强烈的塑性形变,使零件表面产生一定厚度的冷作硬化层,称为表面强化层,此强化层会显著地提高零件在高温和高湿工作下的疲劳强度。
零件表面形成的强化层之所以会改善其疲劳性能,其原因是在此层内有着完全不同于基体(即零件心部)的应力状态及组织结构,一般地说零件疲劳强度的提高与表面强化层内以下三个因素有关:(1)表面层的宏观残余应力;(2)表面层的微观应力;(3)表面层的微细嵌镶组织。
模具表面强化技术及其应用

高密度 能量 ( 能束 ) 面强 化是近 年来 发展 起 来 高 表
,
属表 面施 以极 高能 量使 之发 生物理 、化 学 变
化, 达到金 属表 面 强化 的一种 新 技术 , 利用高 密度 能 量 进 行热 处理 , 具有 节 约能 源 , 防止 环 境 污染 、 提高 生 产 率及产 品质量 等优 点 , 光 热处 理是最 重要 的一 种 , 激 其
有 :红 宝石 激 光器 、钕玻 璃 激光器 和 钇铝石 榴激 光 器 ( A 目f Y G) 水激光 器效 率一 般 不超 过 3 , 用 于穿 孔 、 % 可
1. 纵 台 l 控装 置 1_ 记 录 装 置 1. 统 打字 机 4操 5数 6磁带 7系
C 光器 是在 谐 振腔 内通过 放 电 ,激 发 激 光器 O激
一
见图 l。 2
般是 连续 波 , 也 可 以脉 冲式工 作 . 但 由于 C 光器 O激
一
能够长 时间稳定 连续 振荡 , 故具 有 以下 优点 :
() 1电一光 转 换效 率 高 , 一般 约为 1%~ 0 , 0 2% 而其
他类 型 如红 宝石 激光 器仅 为 2 %
中 的 C N 、 e ( 积 比约为 11 j利 用电 激发 O 、 H 气 体 :56 ,
现象获得 激光 。C 光器按 气 流循 环方 向 、 电方 向 O激 放
维普资讯
《 具制 造》 2 0 .o 模 0 2N . 3总第 8 期
制 、 作 安全 、 格 便宜 。 操 价
6 . 檄光射束
1 0气体 喷嘴
7弯曲反射镜 .
1.- 工作 台 1 Y x
8聚光系统
1. 处 理 工 件 2 被
浅谈模具钢H13的表面强化技术及发展趋势 1

浅谈模具钢H13的表面强化技术及发展趋势摘要随着高科技的迅猛发展,人们改善材料的性能,扩大其能力,延长了零件的使用寿命和设备,以改善经济,提出了更高的要求。
失败的许多部分是由于该材料的表面不能由于服务的苛刻条件下,如磨损,腐蚀和表面氧化指南。
提高材料的表面性能,延长机件的使用寿命和材料起着非常重要的作用,它诞生于表面强化技术是潜力得到了快速发展,已被广泛重要性,成为当前材料科学研究中的重点领域之一。
H13钢是最具代表性的热作模具之一,其传统的热处理工艺得到不断完善和优化的表面改性工艺打破了传统的表面热处理的限制,在表面涂层和高能束表面处理方面得到了极大的发展。
本论文选题的意义主要在于通过对模具钢H13的表面强化技术的综述,总结出为提高模具寿命的表面强化方法、工艺及发展趋势。
应用各种表面强化技术可以充分发挥材料的潜力、节约能源;制备特殊的表面强化层;提高经济效益。
关键字:模具钢;表面强化;H13AbstractWith the rapid development of high technology , it improve the performance of materials, expanding its ability to extend the life of parts and equipment to improve the economy, put forward higher requirements. Many parts of the failure is due to the surface of the material can not be due to the harsh conditions of service , such as wear, corrosion and surface oxidation guide . Improve the surface properties of materials to extend the life of parts and materials plays a very important role, it was born in the surface potential of enhanced technology has been rapid development , has been widely importance , become the focus in the field of materials science one .H13 steel is one of the most representative of hot die , its traditional heat treatment process has been continuously improved and optimized surface modification technology to break the traditional limitations of surface treatment , surface coating and high-energy beam surface treatment has been great development. The significance of this topic by topic lies mainly H13 tool steel surface enhanced technical review , summed up in order to improve surface hardening methods, processes and trends die life . Application of surface enhancement technology can realize the full potential of materials, energy saving ; preparation of special surface hardening layer ; improve economic efficiency .Keywords: mold steel;surface hardening;H13目录摘要 (2)Abstract (3)1 H13模具钢应用及模具表面强化技术的综述 (5)1.1综述H13在模具行业的广泛应用 (5)1.2模具表面强化技术的必要性 (6)2 H13模具钢不改变表面化学成分的强化技术的综述 (8)2.1综述不改变表面化学成分的强化技术原理及介绍应用现状 (8)2.2激光处理和表面镀膜的原理及应用 (8)2.2.1 激光表面处理 (8)2.2.2 表面镀膜处理 (8)3 H13模具钢改变表面化学成分的强化技术的综述 (10)3.1综述改变表面化学成分的强化技术原理及应用现状; (10)3.2离子化学处理和渗金处理的原理及应用 (10)4 H13模具钢表面强化技术对比剂发展趋势 (12)5 结束语 (13)参考文献 (14)1 H13模具钢应用及模具表面强化技术的综述1.1综述H13在模具行业的广泛应用模具材料模具行业是最重要的技术和物质基础,其性能,质量,服务模具,模具制造周期以及工业产品的生命高档,多元化,个性化的和具有决定性意义的增值发展方向,因而模具材料的研究一直是各国的重视。
模具的热处理及表面强化技术

第9章模具的热处理及表面强化技术模具热处理及表面强化是模具制造中的关键工艺之一,直接关系到模具的制造精度、力学性能(如强度等)、使用寿命以及制造成本,是保证模具质量和使用寿命的重要环节。
模具在实际生产使用中表明,在模具的全部失效中,由于热处理不当所引起的失效居于首位。
在模具设计制造过程中,若能正确选用钢材,选择合理的热处理及表面强化技术工艺,对充分发挥材料的潜在性能、减少能耗、降低成本、提高模具的质量和使用寿命都将起到重大的作用。
当前模具热处理技术发展较快的领域是真空热处理技术和模具的表面强化技术。
9.1模具的热处理9.1.l模具钢的热处理模具钢的热处理工艺是指模具钢在加热、冷却过程中,根据组织转变规律制定的具体热处理加热、保温和冷却的工艺参数。
根据加热、冷却方式及获得组织和性能的不同,热处理工艺可分为常规热处理、表面热处理(表面淬火和化学热处理等)等。
根据热处理在零件生产工艺流程中的位置和作用,热处理又可分为预备热处理和最终热处理。
模具钢的常规热处理主要包括退火、正火、淬火和回火。
由于真空热处理技术具有防止加热氧化、不脱碳、真空除气、变形小及硬度均匀等特点,近年来得到广泛的推广应用。
1.退火工艺退火一般是指将模具钢加热到临界温度以上,保温一定时间,然后使其缓冷至室温,获得接近于平衡状态组织的热处理工艺。
其组织为铁素体基体上分布着碳化物。
目的是消除钢中的应力,降低模具材料的硬度,使材料成分均匀,改善组织,为后续工序(机加工、冷加工成形、最终热处理等)做准备。
退火工艺根据加热温度不同可分为:1)完全退火将模具钢加热到临界温度A c3以上20~30℃,保温足够的时间,使其组织完全奥氏体化,然后缓慢冷却,以获得接近平衡状态组织的热处理工艺。
其目的是为了降低硬度、均匀组织、消除内应力和热加工缺陷、改善切削加工性能和冷塑性变形性能,为后续热处理或冷加工做准备。
2)不完全退火将钢加热到A c1~A c3(亚共析钢)或A c1~A ccm(过共析钢)之间,保温一定时间后缓慢冷却,以获得接近于平衡组织的热处理工艺。
塑料模具的表面强化技术研究

塑料模具表面强化技术的方法 , 手段和效 果以及其优缺 点。
二、 塑 料 模 具 的简 介 及 其 分 类
料杂质 少、 组织微细均一 、 无纤维方 向性 、 抛光时不应 出现麻 点 或桔皮状缺 陷。 ( 4 ) 良好的热 稳定性 。 塑料注射模的零件形状往
淬 火后难 以加工 , 因 此 应 尽 量 选 用 具 有 良好 的 热 1 . 塑料 模 具 的简 介 。塑 料模 具 , 是 塑料 加 工 工业 中和 塑料 往 比较 复 杂 , 当模 具 成 型 加 工 经 热 处 理 后 因 线 膨 胀 系 数 小 , 热 处 成型机配套 , 赋予塑料制 品以完整 构型和精确 尺寸的工具 。由 稳 定 性 的 ,
2 ) 优 良的切削加工性 。大多数塑料成型模 塑料模 具的表面强化技术是提高塑料模具使用寿命 , 提 升模具 于提高其耐磨性 。(
除E MD 加工 外 还 需 进 行 一 定 的切 削 加 工 和 钳 工 修 配 。 为延 的 使 用 性 能 的 一 项 重 要 的技 术 和 途 径 , 是 国 内外 模 具 工 业 和 技 具 ,
要求 型腔表面 的粗糙度值小 。例如, 注塑模型腔表面 粗糙 具的使用性能和 使用寿命 。这种表 面强化技术在发达 国家 的模 制 品,
具 制 造 中 已经 得 到 了广 泛 的应 用 , 取 得 了非 常 显 著 的成 果 。本 度 值 要 求 小 于 R a 0 . 1 ~O . 2 5的水 平 , 光学面 则要求 R a < 0 . 0 1 i r m, 减 小 表 面 粗 糙度 值 。 为 此 选 用 的 钢 材 要 求 材 文 从 塑 料 模 具 的工 作 条 件 和 失 效 方式 等 进 行 分 析 , 介 绍 了 一 些 型腔 须进 行抛 光 ,
模具表面强化技术

本 工艺处 理模 具 :下料 一全 部 加工到 位 ( 无须 力 ,使模具容易磨损 ;另一方面 ,不锈 钢板料 易与模 热处理 )一本工艺处理 ( 基体硬 化与表面处理 一次完
具表面形 成粘结 ( 咬合 ) ,使焊 管及 模具 表面 形成拉 成 ) 。一磨 内孔 一成 品 伤 。因此 ,好的不锈钢成型模具必须具备极 高的耐磨 由 工艺流 程可 看 出 ,采 用本 工艺 可缩 短模具 的
1 技术简介 ,
扩散法金 属碳化物覆 层技术是将 工件置于特 挥 超硬膜 层 的性能优 势 ,此外 ,该技 术不存 在绕
种介 质 中 ,经 扩散作 用于 工件表面形 成一层 数微 镀 性 问题 ,后 续基体 硬化 处理 方便 ,并可 多次重 米至 数十微米 的金 属碳化物层 。该碳 化物 层具有 复处理 ,使 该技术 的适 用性 更为广 泛 。 极高的硬 度 ,H V可达 10 ~3 0 ( 0 0 0 由碳化物种类 6
4适 用范 围 .
.
1 8.第0 数控机床市场 1 6期
维普资讯
超 硬化 处 理技 术 已成 功应 用
于不锈钢焊管成 型模具上。 经 该技 术 处理 的模 具 在其 表 面形成硬 度高达 H 3 0 左右 V 00
的金 属 碳 化物 层 ,该 碳化 物
维普资讯
技术 前 沿
模 具表面强化 技木
● 文 / 层技术 化物覆层 ,与基体形成冶金结合 .具有 P D、P V V CD
无法 比拟 的膜基 结合 力 ,因此该 技术 真正能 够发
由扩 散法金 属碳化 物覆层 技术形 成的金 属碳
层致密 ,与基体结合紧密 ,不 影 响工件 的表 面光 洁 度 ,具 有极高 的耐 磨 ,抗咬合 性能 , 可从 根本 上 解决 焊 管 的拉毛
- 1、下载文档前请自行甄别文档内容的完整性,平台不提供额外的编辑、内容补充、找答案等附加服务。
- 2、"仅部分预览"的文档,不可在线预览部分如存在完整性等问题,可反馈申请退款(可完整预览的文档不适用该条件!)。
- 3、如文档侵犯您的权益,请联系客服反馈,我们会尽快为您处理(人工客服工作时间:9:00-18:30)。
• 一、渗碳、渗氮、渗硫、渗硼
• 1.渗碳Biblioteka • (1)什么是渗碳?• 在渗碳介质中加热,使钢的表层渗入碳的热处 理过程称为渗碳。一般情况下,渗碳在AC3 以 上(850~950°C)进行。渗碳方法是最古老、应 用最广泛的一种化学热处理工艺方法。
• (2)渗碳的作用:
• 它提 高了模具表面层的碳浓度,使硬度、接触 疲劳强度、耐磨性较心部有较大的提高,而心 部仍 具有一定的强度和良好的韧性。
• 渗铌工艺可用于冲模、弯曲模、成形模、拔管模、热 锻模和粉末冶金成形模等模具,可以使模具的寿命提 高几倍至几十倍。
• 3.盐浴渗铬
• 渗铬具有优良的耐磨性、抗高温氧化和耐磨损 性能,适用于碳钢、合金钢和镍基或钴基合金 工件。
• 处理工序为把工件浸入盐浴中,取出直接淬火、 回火后,再清理表面。
• 中、高碳钢或合金钢渗铬后,表层硬度分别提 高到1300~1600HV或1700~1800HV,耐磨性、 尤其是抗磨粒磨损性能优良。
浴法、粉末法和气体法。其中以硼砂为基的盐浴渗钒、 渗铌和渗铬并形成碳化物的方法又称为反应浸镀法 (TD法)。
• TD法是在熔融的硼砂中加入欲渗的元素或其合金的 粉粒,然后将零件浸入其中,靠欲渗 元素原子向零
件表面扩散并与零件基体的碳原子形成金属的碳化物 覆层来改善零件表层性能 的工艺方 法。
• TD法具有以下优点:设备简单,工艺简便易行,无公 害;被覆层均匀、致密而平整,与 母材结合良好,不 易剥落;涂覆材料和基体材料广;价格低廉。
• 渗硼方法有固体渗硼、被体渗硼、气体渗硼等。 以固体法和液体浴法应用最多。
• 工件渗硼后一般应进行热处理(淬火和回火)。
• 渗硼适用于各种成分的钢,它在多种冷、热作 模具(如冷挤压模、拉丝模、冲裁模、冷 锻模、 热挤模、热锻模、压铸模等)上应用,效果非常 显著。
• 二、多元共渗
• 将工件表层渗入多于一种元素的化学热处理工艺称 为多元共渗。在模具上应用的多元共 渗主要有:碳氮 共渗、氮碳共渗、硫氮共渗、硼氮共渗、硫氮碳共渗 等。
在较高的温度下使油膜耐压性增大。更可贵的 是在干摩擦的条件下有较小的摩擦系数,减 少
磨损、咬卡、擦伤和拉毛,对抗咬合磨损和点 蚀磨损特别有效。
• 具有工业应用价值的渗硫方法有低温电解渗硫、 离子渗硫、气体渗硫等。
• 4.渗硼
• 渗硼是模具制造中比较有效的一种化学热处理 工艺。在钢的表面渗硼会形成由硼化物组成的 渗硼层,渗硼层具有硬度高、耐磨性高、耐热 性高、红硬性高和耐蚀性高的优异特性。
铌的目的分别是什么?
• 1.碳氮共渗
• 碳氮共渗是向工件表层同时掺入碳和氮,并以渗碳为 主的化学热处理工艺。因兼顾了渗碳和渗氮的优点, 所以在模具上也有应用。碳氮共渗方法有气体法和液 体法,生产上大多应 用的是气体碳氮共渗。
• 碳氮共渗适用于基体具有良好韧性,而表面硬度高、 耐磨性好的模具零件。塑料模、陶 瓷模中的凸模、 凹模和型芯等型腔部位零件以及冲裁模中的凸模和凹 模等零件,有些就适合 采用碳氮共渗处理。
• 高碳钢或中、高碳合金钢冷、热作模具的渗铬 应用亦广,冷、热作模具渗铬后使用寿命能大 幅度提高。
课堂小结
• 1、模具表面强化处理的目的和方法 • 2、表面化学热处理及其常用方法 • 3、常用化学热处理方法的目的、作用、方法及其
在模具生产中的应用。
作业
• 1、模具表面强化处理的目的是什么? • 2、在TD处理法中,盐浴渗钒和盐浴渗
• 2.盐浴渗铌
• 盐浴渗铌是在模具表面处理后,在模具表面被覆以硬 度为 2100~3500HV的渗铌层,以提高模具的抗磨损、 抗咬合、耐氧化和抗热疲劳等性能,它比渗 硼和气相
沉积碳化铁有更好的性能。
• 渗铌时先将无水硼砂熔化,然后加入干燥的铌粉,在 900~1000°C下加入铝粉后,即可将 模具放入盐浴内 进行渗铌。然后取出直接淬火、回火,最后清理表面。
• 4.硼氮共渗
• 渗硼层具有高硬度和高耐磨性,但性脆、易 剥落,而氮的渗入可增加渗层深度,降低渗层 脆性,强化了过渡层,提高了对表面渗硼层的 支撑作用,从而可避免渗硼层的剥落。
• 用3Cr2W8V钢制造的热挤压凸模,常规处理后 只生产0.1~0.2万件;经氮碳共渗后只生产 0.2万件;渗硼后寿命提高到0.3~0.4万件; 而采用硼氮共渗后寿命提高到0.7~1万件, 最高可达4.15万件。
• 5.硫氮碳共渗
• 硫氮碳共渗可在盐浴、气体介质、粉末渗剂中 实现,气体法最常用。
• 硫氮碳共渗具有优良的减摩性能、抗咬合性能、 抗疲劳和较好的耐蚀性,因此适应范围 相当广 泛。
• 三、盐浴渗钒、渗铌和渗铬
• 钢渗钒、铌、钛、钽等可获得碳化物型渗层。这类 渗层的硬度和耐磨性极高〈硬度可达 1800~3200HV) . 工艺简便易行,不需复杂的设备,已进入工业应用阶 段。形成金属碳化物 型渗层有三种方法,即硼砂盐
• 3.硫氮共渗
• 渗氮后渗硫能获得耐磨、抗疲劳与减摩等性能, 但需先后采用两种工艺。为简化工序,采 用 硫氮共渗。
• 硫氮共渗有气体法、无氧盐浴法,常用气体硫 氮共渗。
• 用碳钢、合金钢制造的模具,经硫氮共渗处理 后,渗层组成为FeS、Fe2-3N、Fe4N等;渗层 厚度为硫化物<0.01mm,氮化物0.01~ 0.03mm;表面硬度300~1200HV。提高了模 具的抗咬合能力、耐磨性、疲劳强度,但渗层 抗蚀性差。
• 1.盐浴渗钒
• 盐浴渗钒是在中、高碳钢或合金钢表面,被覆 硬度为2800~ 3200HV的钒碳化物层,以 提高模 具的耐磨性和抗粘着性能。
• 模具渗钒温度为850~1200°C,渗钒时间为 2~6h,模具渗钒后可进行空冷、油冷或水 冷。
• 盐浴渗钒可以用于冲裁模、弯曲模、挤压模、 切边模、冷镦模、制管模和粉末冶金模等 各种 冷作模具,使用寿命与渗氮处理的模具相比, 可提高几倍至几十倍。
• 渗氮的目的是提高工件表面硬 度、耐磨性、疲劳强度及抗咬 合性,提高零件抗大气、过热蒸汽的腐蚀能力,提高抗回火 软 化能力,降低缺口敏感性。
• 渗氮方法有主要有气体渗氮和离子渗氮。 气体渗氮广泛应用 于模具制造中 ,但由于气体渗氮处 理时间长、渗层浅、渗层 脆性较大,且只适合于合金渗氮钢。因此气体渗氮现已逐渐 由离子渗氮、氮碳共渗、真空渗氮、电解催渗渗氮等取代 。 离子渗氮广泛用于处理热锻模、冷挤压模、压铸模、冷冲模 等。
• 2.氮碳共渗(软氮化)
• 氮碳共渗是向钢件表面同时渗入氮和碳,并以 渗氮为主的化学热处理工艺。其处理结果 与 气体渗氮相比,渗层硬度较低,脆性较小,故 称软氮化。
• 氮碳共渗方法有液体法和气体法, 生产中应 用的大多是气体氮碳共渗。
• 氮碳共渗主要应用于热态下工作的压铸模、塑 料模、热挤模,锤锻模等。也常用于某 些冷 作模具,但都取得较小的效果。
• 模具在渗氮前一般进行调质处理,为了不影响模具的性能, 渗氮温度不得高于调质处理 的回火温度,一般采用 500~570°C。
• 3.渗硫
• 己硬化的钢铁工件渗硫,表面可形成厚度为 5~15µm的FeS+FeSz化学转化膜,渗层很 薄, 渗层硬度并不高,为70HV以下,因此无助于 抗磨粒磨损。但是,它有较大减磨作用,这 是 由于渗层中的FeS呈鳞片状。多孔并易滑移。 它的减摩作用不仅在有滑移条件下有效,并 能
第五章 模具表面强化技术
• 模具在使用过程中承受着各种形式的复杂应力。其表面更是 处于较大的应力 状态下,服役条件更为恶劣,模具的失效 和破坏,往往发生在表面或由表面开始。模具表面 性能的 优劣将直接影响模具的使用及寿命。
• 模具表面强化处理的目的主要是赋于基体表面所不具备的 性能,或者是进一步提高其所 固有的性能。这些性能主要 是表面的耐磨性、抗咬合性、抗冲击性、抗热粘附性、抗冷 热疲 劳性及抗腐蚀性等。 几乎所有的表面处理及表面强化 处理方法均在模具表面处理上得到应用。目前已开发的适合 模具表面强化的主要方法见表5-1。
• (3)渗碳的方法:
• 根据渗碳介质的物理状态,渗碳方法可分为固 体渗碳、液体渗碳、气体渗碳、真空渗碳 和离 子渗碳。
• (4)渗碳在模具生产中的应用
• 渗碳主要用于要求承受很大冲击载荷、高的强 度和好的抗脆裂性能。使用硬度为58~ 62HRC 的小型模具。
• 2、渗氮
• 渗氮是向钢的表面渗氮以提高表层氮浓度的热处理过程。
第一节 表面化学热处理技术
• 化学热处理是指将金属或合金工件置于一定 的活性介质中保温,使一种或几种元素渗入 它的表层,以改变其化学成分、组织和性能 的热处理工艺。化学热处理的种类很多,一 般都 以渗入的元素来命名,常用的化学热处 理方法有:渗碳、渗氮、碳氮共渗、渗硫、碳 氮共渗、 渗硼、硼氮共渗、渗铝、渗铬、渗 硅、渗锌、盐浴渗金属,等等。