锻压1
锻压生产特点及工艺简介
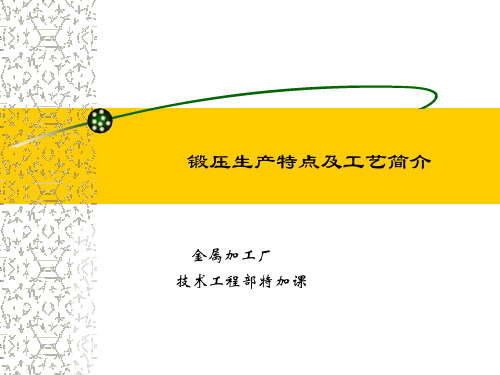
6、几种锻造结构图
第二节 金属的锻造性能
一、金属的塑性变形概述 金属塑性变形的实质,对于单晶体是由于金属原子某晶面两侧受切应力作用
产生相对滑移,或晶体的部分晶格相对于某晶面沿一定方向发生切变,即滑移理 论和孪生理论。
二、热锻、冷锻、温锻、等温锻
从金属学的观点划分锻压加工的界限为再结晶温度。 1.热锻 在金属再结晶温度以上进行的锻造工艺称为热锻。在变形过程中冷变形 强化和再结晶同时存在,属于动态再结晶。 2.冷锻 在室温下进行的锻造工艺称为冷锻。冷锻可以避免金属加热出现的缺陷, 获得较高的精度和表面质量,并能提高工件的强度和硬度。但冷锻变形抗力大, 需用较大吨位的设备,多次变形时需增加再结晶退火和其它辅助工序。目前冷锻 主要局限于低碳钢、有色金属及其合金的薄件及小件加工。 3.温锻 在高于室温和低于再结晶温度范围内进行的锻造工艺称为温锻。与热锻 相比,坯料氧化脱碳少,有利于提高工件的精度和表面质量;与冷锻相比,变形 抗力减小、塑性增加,一般不需要预先退火、表面处理和工序间退火。温锻适用 于变形抗力大、冷变形强化敏感的高碳钢、中高合金钢、轴承钢、不锈钢等。 4.等温锻 在锻造全过程中,温度保持恒定不变的锻造方法称为等温锻。
冲压:有时也称板材成形, 但略有区别。所谓板材成型是指用板材、薄壁管、 薄型材等作为原材料进行 塑性加工的成形方法统称为板材成形,此时,厚板厚 方向的变形一般不着重考虑
4、锻件与铸件相比的特点
金属经过锻造加工后能改善其组织结构和力学性能。铸造组织经过锻造方法 热加工变形后由于金属的变形和再结晶,使原来的粗大枝晶和柱状晶粒变为晶粒 较细、大小均匀的等轴再结晶组织,使钢锭内原有的偏析、疏松、气孔、夹渣等 压实和焊合,其组织变得更加紧密,提高了金属的塑性和力学性能。
锻压技术和热加工工艺
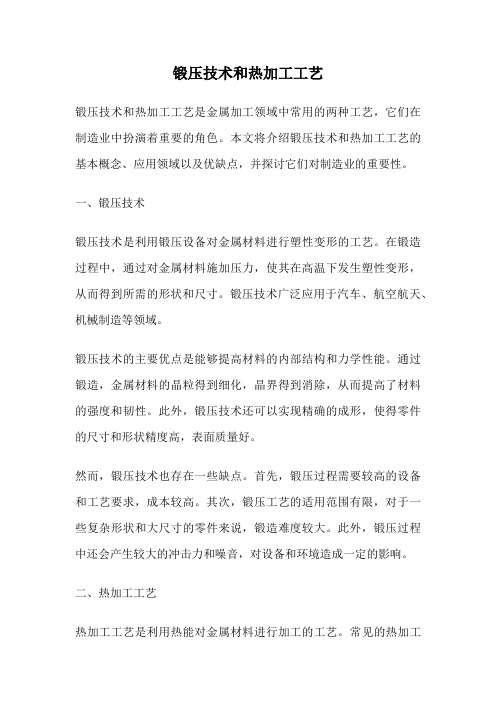
锻压技术和热加工工艺锻压技术和热加工工艺是金属加工领域中常用的两种工艺,它们在制造业中扮演着重要的角色。
本文将介绍锻压技术和热加工工艺的基本概念、应用领域以及优缺点,并探讨它们对制造业的重要性。
一、锻压技术锻压技术是利用锻压设备对金属材料进行塑性变形的工艺。
在锻造过程中,通过对金属材料施加压力,使其在高温下发生塑性变形,从而得到所需的形状和尺寸。
锻压技术广泛应用于汽车、航空航天、机械制造等领域。
锻压技术的主要优点是能够提高材料的内部结构和力学性能。
通过锻造,金属材料的晶粒得到细化,晶界得到消除,从而提高了材料的强度和韧性。
此外,锻压技术还可以实现精确的成形,使得零件的尺寸和形状精度高,表面质量好。
然而,锻压技术也存在一些缺点。
首先,锻压过程需要较高的设备和工艺要求,成本较高。
其次,锻压工艺的适用范围有限,对于一些复杂形状和大尺寸的零件来说,锻造难度较大。
此外,锻压过程中还会产生较大的冲击力和噪音,对设备和环境造成一定的影响。
二、热加工工艺热加工工艺是利用热能对金属材料进行加工的工艺。
常见的热加工工艺包括热轧、热挤压、热拉伸等。
热加工工艺主要适用于金属材料的塑性变形和形状修整。
热加工工艺的主要优点是能够提高材料的塑性和变形能力。
在高温下,金属材料的塑性增加,容易发生塑性变形,从而实现较大的形状变化。
此外,热加工还可以改善材料的内部结构和力学性能,提高材料的强度和韧性。
然而,热加工工艺也存在一些缺点。
首先,热加工过程需要大量的能源消耗,对环境造成一定的影响。
其次,热加工对设备和工艺要求较高,需要控制好加热温度和加工速度,以避免产生缺陷和变形。
此外,热加工过程中还会产生较大的热应力和残余应力,对材料的性能和寿命产生影响。
三、锻压技术和热加工工艺的应用锻压技术和热加工工艺在制造业中有着广泛的应用。
锻压技术主要应用于汽车、航空航天、机械制造等领域,用于生产发动机零部件、车轮、轴承等关键零件。
热加工工艺主要应用于钢铁、有色金属等行业,用于生产钢材、铝材等金属材料。
锻压机的工作原理
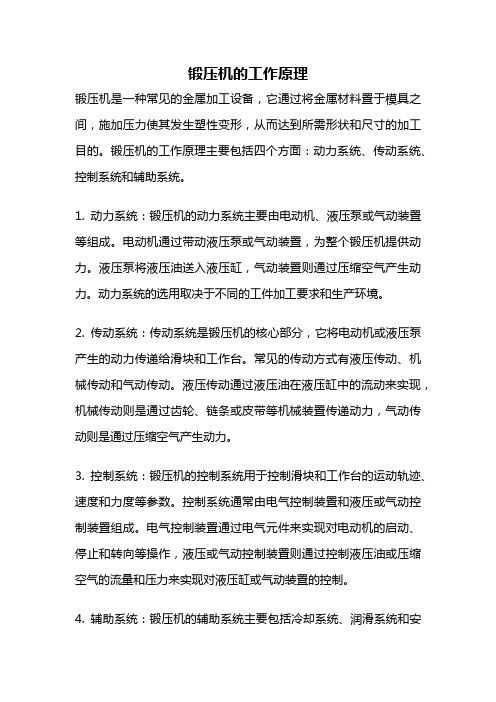
锻压机的工作原理锻压机是一种常见的金属加工设备,它通过将金属材料置于模具之间,施加压力使其发生塑性变形,从而达到所需形状和尺寸的加工目的。
锻压机的工作原理主要包括四个方面:动力系统、传动系统、控制系统和辅助系统。
1. 动力系统:锻压机的动力系统主要由电动机、液压泵或气动装置等组成。
电动机通过带动液压泵或气动装置,为整个锻压机提供动力。
液压泵将液压油送入液压缸,气动装置则通过压缩空气产生动力。
动力系统的选用取决于不同的工件加工要求和生产环境。
2. 传动系统:传动系统是锻压机的核心部分,它将电动机或液压泵产生的动力传递给滑块和工作台。
常见的传动方式有液压传动、机械传动和气动传动。
液压传动通过液压油在液压缸中的流动来实现,机械传动则是通过齿轮、链条或皮带等机械装置传递动力,气动传动则是通过压缩空气产生动力。
3. 控制系统:锻压机的控制系统用于控制滑块和工作台的运动轨迹、速度和力度等参数。
控制系统通常由电气控制装置和液压或气动控制装置组成。
电气控制装置通过电气元件来实现对电动机的启动、停止和转向等操作,液压或气动控制装置则通过控制液压油或压缩空气的流量和压力来实现对液压缸或气动装置的控制。
4. 辅助系统:锻压机的辅助系统主要包括冷却系统、润滑系统和安全保护系统等。
冷却系统用于降低锻压机在工作过程中的温度,以保证设备的正常运行。
润滑系统用于对锻压机的各个运动部件进行润滑,减少磨损和摩擦。
安全保护系统则包括各种安全装置,如紧急停机按钮、安全防护栅栏等,用于保护操作人员的安全。
总结起来,锻压机的工作原理是通过动力系统提供动力,传动系统将动力传递给滑块和工作台,控制系统控制滑块和工作台的运动轨迹和参数,辅助系统提供冷却、润滑和安全保护等功能。
这些系统相互配合,使锻压机能够实现金属材料的加工和成形。
锻压机在制造业中有着广泛的应用,可用于锻造、冲压、压铸等各种加工工艺,为工件的制造提供了高效、精确和可靠的工艺保证。
锻压的心得体会(精选14篇)

锻压的心得体会(精选14篇)心得体会是表达个人主观体验和观点的一种方式,可以让他人更加了解我们的思考和想法。
通过阅读以下的心得体会范文,大家可以更好地理解这一写作形式的要点和特点。
锻压事故心得体会锻压作为一种常见的金属加工工艺,在工业生产中发挥着重要作用。
然而,由于操作不慎、设备故障等原因,锻压事故时有发生。
通过参与一次锻压事故的整治工作,我深刻认识到了事故的危害和预防的重要性。
在这次工作中,我对锻压事故有了全新的认识,获得了宝贵的经验和教训。
首先,锻压事故给人们带来了巨大的伤害。
在锻压事故中,我亲眼目睹了工人的严重受伤。
在一次锻造过程中,由于操作不当,工人的手被机械装置夹住,手指被剥落。
这一幕让我震惊不已。
工人的手指是他们生活和工作的重要工具,一旦受伤,不仅给他们带来巨大的痛苦,也会对他们的生活造成极大的影响。
这次事故还给工厂造成了经济损失,并对生产进程造成了延误。
因此,锻压事故不仅会给人们的身体健康带来损害,还会对企业带来重大的影响。
其次,锻压事故的发生大多是由于操作不当所致。
在整治工作中,我发现许多事故的发生是由于工人在操作设备时不规范、不谨慎所导致的。
有的时候,工人没有正确地佩戴个人防护装备,没有将手指和其他身体部位远离机械装置,更没有对设备进行及时检查和维护。
这些操作上的差错给工人的安全埋下了隐患。
因此,我深刻认识到,只有严格遵守操作规程,正确使用设备,才能减少事故的发生。
第三,预防是减少锻压事故的关键。
在整治工作中,我了解到预防是减少锻压事故的关键。
首先,有关方面应该加强对从业人员的培训和教育,提高他们对安全生产的认识和重视。
只有加强学习,掌握安全生产知识,才能在实际操作中做到临近事故时懂得应对。
其次,企业应定期对设备进行维护和检修,确保设备的正常运转。
此外,对设备操作规程也需要进行适时的调整和完善,以适应生产工艺的需求。
通过这些预防措施,可以有效减少锻压事故的发生,维护工人的安全和企业的利益。
锻压加工的名词解释

锻压加工的名词解释锻压加工是一种常见的金属成形工艺,它通过对金属材料施加压力,使其在受力作用下产生内部结构变化,从而达到改变形状和性能的目的。
锻压加工可以用于制造各种各样的零部件和成品,广泛应用于汽车、航空航天、机械制造等行业。
1. 锻压的基本原理锻压是通过施加压力使金属材料发生塑性变形,从而改变其形状和性能。
在锻压过程中,金属材料被放置在一对上下活动的模具之间,施加压力压制模具,使材料发生变形。
锻压的基本原理是利用金属材料的可塑性,通过施加压力使晶粒发生滑移和变形,从而使材料成形。
2. 锻压的分类根据施加压力的形式,锻压可以分为自由锻和模锻两种。
2.1 自由锻自由锻是指将金属材料放置在模具之间,用锤击或压力机施加冲击或压力,使材料发生变形。
自由锻可以分为手工锤锻和机械锤锻两种。
手工锤锻主要应用于小型零部件的生产,操作人员通过手工操作锤击工件,控制锤击的力度和方向。
机械锤锻则是通过机械锤头的冲击力来实现金属变形,可以大幅提高生产效率。
2.2 模锻模锻是指将金属材料放置在闭合的上下模具之间,施加压力使材料发生变形。
按照模锻过程的运动形式,可以将模锻分为下冲式模锻、上冲式模锻和复式模锻。
其中,下冲式模锻是最常见的模锻方式,模具通过由上至下的冲击力使材料变形;上冲式模锻是指模具从下方冲击材料,使其发生变形;而复式模锻是指模具从上下两个方向同时作用于材料,以实现更复杂的变形。
3. 锻压加工的优势与其他金属加工方法相比,锻压加工具有以下几个优势。
3.1 优化内部组织结构在锻压过程中,金属材料受到的应力较大,晶粒发生滑移和变形,从而使内部组织结构得以优化。
这种结构优化可以使材料的力学性能得到提升,提高材料的强度和硬度。
3.2 提高产品的密度和质量由于锻压过程中金属材料受到较大的压力,材料中的气孔和缺陷会被压实,从而提高产品的密度。
同时,锻压加工还可以清除金属材料表面的氧化皮、铁锈等杂质,使产品的质量得到提高。
锻压工艺介绍
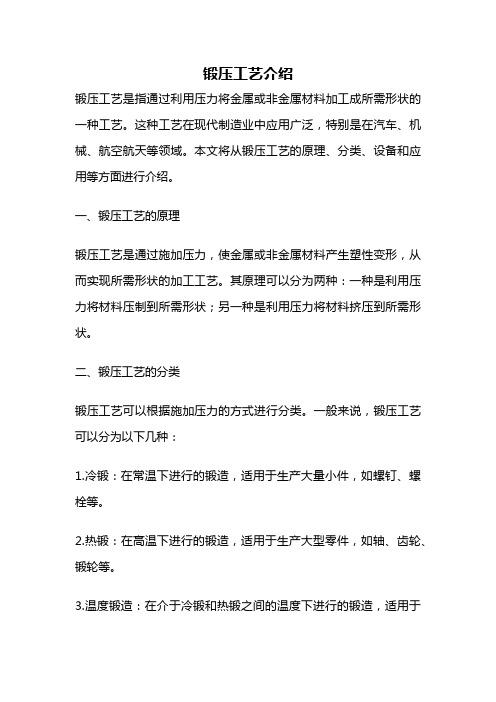
锻压工艺介绍
锻压工艺是指通过利用压力将金属或非金属材料加工成所需形状的一种工艺。
这种工艺在现代制造业中应用广泛,特别是在汽车、机械、航空航天等领域。
本文将从锻压工艺的原理、分类、设备和应用等方面进行介绍。
一、锻压工艺的原理
锻压工艺是通过施加压力,使金属或非金属材料产生塑性变形,从而实现所需形状的加工工艺。
其原理可以分为两种:一种是利用压力将材料压制到所需形状;另一种是利用压力将材料挤压到所需形状。
二、锻压工艺的分类
锻压工艺可以根据施加压力的方式进行分类。
一般来说,锻压工艺可以分为以下几种:
1.冷锻:在常温下进行的锻造,适用于生产大量小件,如螺钉、螺栓等。
2.热锻:在高温下进行的锻造,适用于生产大型零件,如轴、齿轮、锻轮等。
3.温度锻造:在介于冷锻和热锻之间的温度下进行的锻造,适用于
生产中等规模的零件,如法兰、板、带等。
三、锻压工艺的设备
常用的锻压设备有压力机、锻压机、冲压机等。
其中,压力机是最简单的设备,一般用于小型零件的生产;锻压机则是较为常用的设备,适用于各种规模的零件生产;冲压机则是专门用于生产大批量小件的设备。
四、锻压工艺的应用
锻压工艺在现代制造业中应用广泛,特别是在汽车、机械、航空航天等领域。
在汽车制造中,锻造技术可以用于制造轴承、齿轮、弹簧等零件;在机械制造中,锻造技术可以用于制造锻轮、齿轮、轴等零件;在航空航天领域,锻造技术可以用于制造飞机发动机零件、飞行器结构零件等。
锻压工艺是一种非常重要的加工工艺,具有广泛的应用前景。
通过锻压工艺,可以实现对各种材料的加工和成型,从而满足各种不同领域的生产需求。
锻压工艺介绍
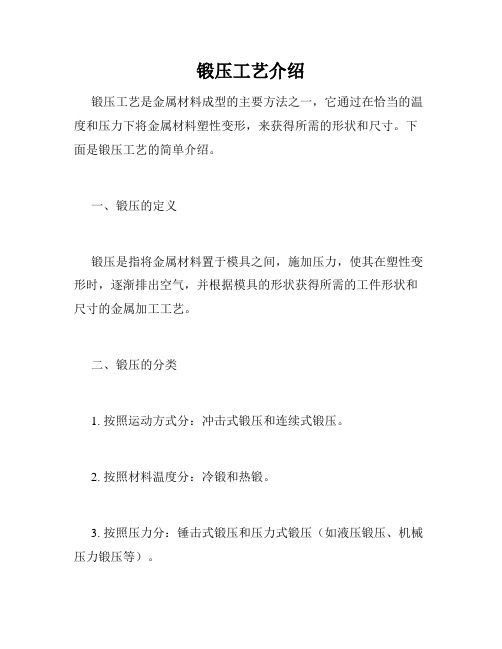
锻压工艺介绍
锻压工艺是金属材料成型的主要方法之一,它通过在恰当的温度和压力下将金属材料塑性变形,来获得所需的形状和尺寸。
下面是锻压工艺的简单介绍。
一、锻压的定义
锻压是指将金属材料置于模具之间,施加压力,使其在塑性变形时,逐渐排出空气,并根据模具的形状获得所需的工件形状和尺寸的金属加工工艺。
二、锻压的分类
1. 按照运动方式分:冲击式锻压和连续式锻压。
2. 按照材料温度分:冷锻和热锻。
3. 按照压力分:锤击式锻压和压力式锻压(如液压锻压、机械压力锻压等)。
三、锻压的工艺流程
1. 原材料切割或预成型
2. 加热,使材料温度达到锻造要求
3. 送入锻压机中进行锻造
4. 锻压完成后,对工件进行进一步加工(如裁剪、加工等)
四、锻压的优点
1. 提高金属材料的塑性,能制造出形状复杂、尺寸精确的零部件。
2. 增强金属材料的韧性和抗拉强度,并改善其加工硬度和机械性能。
3. 可以提高金属材料的利用率,减少废料和能源的消耗。
4. 锻造过程中一般无需使用润滑剂,不会污染环境。
五、锻压过程中需要注意的问题
1. 锻造温度需要控制好,过高会使金属材料软化而无法保持所需形状;过低则容易导致不良的流变工艺。
2. 模具的设计和制造需要精确,以确保获得所需的工件形状和尺寸。
3. 锻压时需要注意安全,必须保证锻压机的运转稳定、操作规范,避免事故的发生。
以上是对锻压工艺的简单介绍,希望能对您有所帮助。
机械制造基础 第2章-锻压1可锻性
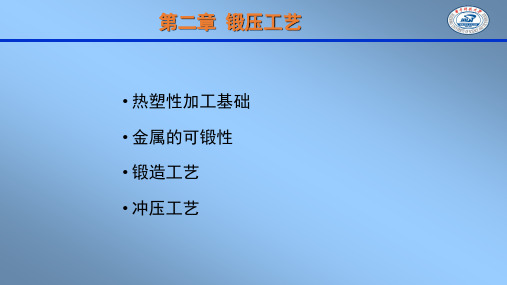
2.1 热塑性加工基础
2.1.3 纤维组织、流线与锻造比
➢ 钢锭开坯 热加工生产采用的原始坯料是铸锭。其内部组织很不均匀,晶粒较粗大,并存
在气孔、缩松、非金属夹杂物等缺陷。铸锭加热后经过热加工,由于塑性变形及再 结晶,从而改变了粗大、不均匀的铸态结构,获得细化了的再结晶组织。同时还可 以将铸锭中的气孔、缩松等压合在一起,使金属更加致密,力学性能得到很大提高 。
第二章 锻压工艺
• 热塑性加工基础 • 金属的可锻性 • 锻造工艺 • 冲压工艺
概述
1. 你知道枪管、炮管是如何制造的吗?什么是来复线?它是如何制造的? 来复线是径向锻造的。
概述
利用金属在外力作用下所产生的塑性变形,来获得具有一定形状、尺 寸和机械性能的原材料、毛坯或零件的生产方法,称为金属塑性成型(也 称为压力加工)。
压力加工中作用在金属坯料上的外力主要有两种:冲击力和静压力。 锤类设备产生冲击力,轧机与压力机设备产生静压力。 金属塑性成型的基本生产方法有以下几种:
压力加工工艺
各种块体压力加工工艺
各种板料冲压工艺
各种加工方法的应用范围
• 轧制、挤压、拉拔
主要用于金属型材、板材、
钢材和线材等原材料。
• 锻造 用于承受重载荷的机器零件,如机器的 主轴、重.1.2 冷变形与热变形
2.热变形: 在再结晶温度以上的变形。变形后,金属具有再结晶组织、而无加工硬化痕迹。
也称热加工。 ➢ 优点:金属能以较小的功达到较大的变形,加工尺寸较大和形状比较复杂的工件, 同时获得具有高机械性能的再结晶组织。 ➢ 缺点:金属表面容易形成氧化皮,而且产品尺寸精度和表面质量较低,劳动条件 和生产率也较差。
• 板料冲压 广泛用于汽车制造、电器、仪表及日 用品工业等方面。
锻压新技术简介

由于普通冲裁得到的冲压件尺寸精度低、表面质量差、断面微带斜度 且光亮带宽度小,当冲压件质量和精度要求较高时,应采用精密冲裁及半 精密冲裁或整修等工艺方法。
精密冲裁条件的形成主 要是依靠V形压边环、极小的 冲裁间隙、凹凸模刃口略带 小圆角和反压力顶杆等。材 料的塑性越好,精密冲裁效 果也越好。
图7-49 螺旋斜轧
四、超塑性成形
超塑性成形是指利用金属在特定条件下具有的超塑性来进行塑性变形 的工艺,目前常用的超塑性成形材料主要是锌铝合金、铝基合金、钛合金 及高温合金。
(一)超塑性成形工艺的应用
1.超塑性板料拉深
如图7-50所示,采用锌铝合金等超塑性材料,在法兰盘部位加热,并在 外围施加油压,一次能拉出很深的杯形件。
(3)可获得均匀细小的晶粒组织,使零件具有均匀一致的力学性能。
五、高速高能成形
高速高能成形有多种加工形式,主要包括爆炸成形、放电成形、电磁 成形和高速锻造成形等,其共同特征就是在很短的时间内将化学能、电能 和电磁能或机械能等传递给被加工的金属材料,使之迅速成形。该技术具 有成形速度快、加工精度高和适用范围广等优点。
辊锻轧制是通过装有圆弧形模块的一对旋转轧辊,使坯料受压变形的 生产方法,它是将轧制工艺应用到锻造生产中的一种新工艺。
图7-47 辊锻轧制
辊锻轧制主要用于生产以下三类锻件。
(1)扁断面的长杆件,如扳手、活动扳手、链环等。 (2)带有不变形头部且横截面积沿长度方向递减的锻件。 (3)连杆成形辊锻件。国内已有不少工厂采用辊锻轧制工艺锻制连 杆,生产效率高,工艺过程简单,但还需用其他锻压设备进行修整。
锻压相关知识点总结

锻压相关知识点总结一、锻压的基本原理锻压是通过将金属材料置于模具中,然后施加压力来改变其形状和结构的加工方法。
通过锻压,可以使金属材料得到均匀的压缩和拉伸,从而提高其强度和硬度。
锻压过程中,金属材料会受到较大的变形应力,使得晶粒重新排列,形成更加致密的结构,提高了材料的力学性能。
锻压的基本原理包括以下几点:1. 施加压力:通过机械设备或液压系统,对金属材料施加一定的压力,使其发生塑性变形。
2. 变形应力:金属材料在受到压力作用下,会发生塑性变形,使得晶粒重新排列,形成更加致密的结构。
3. 模具设计:通过模具将金属材料加工成所需的形状和尺寸,同时避免出现裂纹和变形。
二、锻压的工艺流程锻压的工艺流程通常包括以下几个步骤:材料准备、加热、锻造、冷却和后续处理。
具体步骤如下:1. 材料准备:选择合适的金属材料,并根据产品要求进行切割和预加工。
2. 加热:将金属材料加热至一定温度,使其变得更加柔软,易于塑性变形。
3. 锻造:将加热后的金属材料放置在模具中,然后施加压力进行锻制,使其得到所需的形状和结构。
4. 冷却:对锻造后的产品进行适当的冷却处理,使其达到一定的硬度和强度。
5. 后续处理:对产品进行表面处理、热处理和清洁等操作,使其得到最终的性能和外观要求。
三、锻压的设备锻压设备通常包括锻压机、冷冲机、摩擦压力机和液压机等。
它们根据不同的工艺要求和产品类型,可以实现不同的加工方法和效果。
其中,锻压机是最常见的设备,主要用于对金属材料进行锻造和压制,根据不同的动力来源和结构形式,可以分为机械式锻压机、液压式锻压机和气动式锻压机等。
四、锻压的材料选择在锻压加工中,常见的金属材料包括碳素钢、合金钢、不锈钢、铝合金和铜合金等。
根据不同的产品要求和使用环境,选用合适的材料来进行加工。
碳素钢具有良好的可加工性和机械性能,广泛应用于锻造和压制工艺;合金钢具有较高的强度和硬度,适用于对薄壁零件和复杂结构的加工;不锈钢具有抗腐蚀性能,适用于要求高的产品要求。
锻1

3、纤维组织和锻造流线
2)锻造比
纤维组织的明显程度与金属的变形程度有关。 变形程度越大,纤维组织越明显。 压力加工过程中,常用锻造比来表示变形程度
3、纤维组织和锻造流线
3)锻造流线和纤维组织对性能的影响
Y<2时——组织致密,力学性能提高。 Y=2--5时——各向异性,纵提高,横下降。 Y>5时——纵不提高,横急剧下降。
的倾向。(但室温不易实现)
“回复”——可消除或部分消除加工硬化。 再结晶——可以细化晶粒,消除全部加工硬化,消除应 力。
第二节 金属塑性成形原理
再结晶与同素异构不同 再结晶晶格类型不发生变化。
再结晶没有固定的温度。
冷变形程度越大、晶间碎晶越多、晶格畸变越严重—— 再结晶越容易,T再越低。
杂质和合金元素多——T再越高。
变形条件
应力状态
对塑性的影响——压应力数目越多,塑性越好;拉应力数 目越多,塑性越差。 对变形抗力的影响——同号应力状态下的变形抗力大于异 号状态下的变形抗力。
变形条件
所以,在选择变形方法时,对于塑性高的金
属,变形时出现拉应力有利于减少能量消耗;对 于塑性低的金属应尽量采用三向压应力以增加塑
性,防止裂纹。
2、影响因素
金属的本质 变形条件 变形温度 变形度度 应力状态
四、金属的塑性变形规律
1、体积不变条件 2、最小阻力条件——金属向阻力最小的方向移动。
最小阻力条件
最小阻力条件
为了提高拔长效率,拔长时送进量z应小于坯料宽度口。
最小阻力条件
对于塑性差的合金,用V形砧或圆形砧拔长,即可防 止裂纹的产生,又可提高拔长效率,
第二节 金属塑性成形原理
3、纤维组织和锻造流线 1)概念
锻压的工艺类别

锻压的工艺类别锻压工艺是一种将金属材料在受力作用下进行塑性变形的制造工艺。
它通过对金属材料施加压力,使其在一定条件下发生塑性变形,从而得到所需形状的零件或产品。
锻压工艺可以分为冷锻和热锻两大类。
冷锻工艺是指在常温下进行的锻造工艺。
常用的冷锻方法有冷轧、冷挤压、冷拉伸等。
冷锻工艺具有以下特点:1. 适用于各种金属材料。
冷锻可以用于锻造各种金属材料,包括铁、钢、铝、铜等。
2. 保持材料原有的晶粒结构。
冷锻过程中,由于温度较低,材料的晶粒结构不会发生显著变化,因此可以保持材料的原有性能。
3. 提高材料的强度。
冷锻可以通过加工变形,使材料的晶粒细化,从而提高材料的强度和硬度。
4. 降低材料的变形阻力。
由于冷锻温度较低,材料的塑性较好,因此可以降低锻压过程中的变形阻力,提高锻件的成形性能。
热锻工艺是指在高温下进行的锻造工艺。
常用的热锻方法有热轧、热挤压、热拉伸等。
热锻工艺具有以下特点:1. 提高材料的塑性。
热锻温度较高,可以使材料的塑性显著提高,从而便于进行锻造。
2. 降低材料的应力。
热锻温度较高,可以降低材料的应力,减少材料的变形阻力,从而提高锻件的成形性能。
3. 改善材料的内部结构。
热锻温度较高,可以使材料的晶粒长大,消除材料内部的缺陷,从而改善材料的内部结构和性能。
4. 提高锻件的尺寸精度。
热锻温度较高,可以使锻件的变形能力增加,从而提高锻件的尺寸精度。
无论是冷锻还是热锻,锻压工艺在制造业中都起着重要的作用。
它可以制造出各种形状复杂的零件和产品,广泛应用于汽车、航空、航天、机械等领域。
锻压工艺的发展不仅推动了制造业的进步,也为人们的生活提供了更多便利和选择。
在锻压工艺的实践中,工程师们不断探索新的方法和技术,以提高锻压工艺的效率和质量。
他们不断研究材料的变形行为和力学性能,优化工艺参数,提升设备的性能,以满足不断增长的市场需求。
锻压工艺是一种重要的金属加工工艺,它通过对金属材料的塑性变形,制造出各种形状的零件和产品。
锻压术语(基本术语部分)
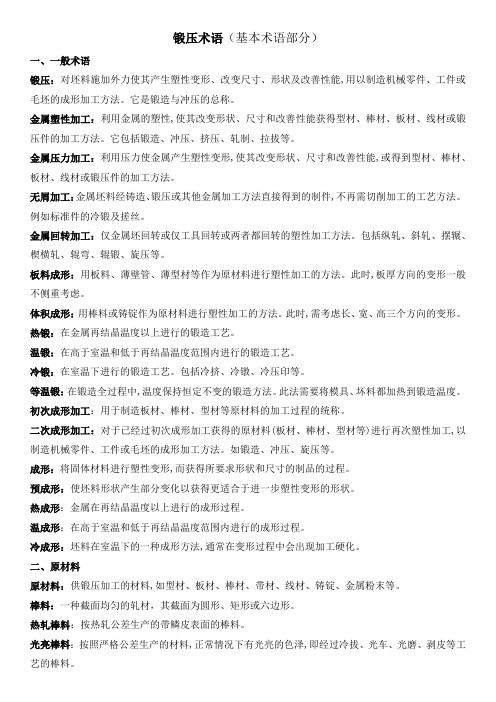
锻压术语(基本术语部分)一、一般术语锻压:对坯料施加外力使其产生塑性变形、改变尺寸、形状及改善性能,用以制造机械零件、工件或毛坯的成形加工方法。
它是锻造与冲压的总称。
金属塑性加工:利用金属的塑性,使其改变形状、尺寸和改善性能获得型材、棒材、板材、线材或锻压件的加工方法。
它包括锻造、冲压、挤压、轧制、拉拔等。
金属压力加工:利用压力使金属产生塑性变形,使其改变形状、尺寸和改善性能,或得到型材、棒材、板材、线材或锻压件的加工方法。
无屑加工:金属坯料经铸造、锻压或其他金属加工方法直接得到的制件,不再需切削加工的工艺方法。
例如标准件的冷锻及搓丝。
金属回转加工:仅金属坯回转或仅工具回转或两者都回转的塑性加工方法。
包括纵轧、斜轧、摆辗、楔横轧、辊弯、辊锻、旋压等。
板料成形:用板料、薄壁管、薄型材等作为原材料进行塑性加工的方法。
此时,板厚方向的变形一般不侧重考虑。
体积成形:用棒料或铸锭作为原材料进行塑性加工的方法。
此时,需考虑长、宽、高三个方向的变形。
热锻:在金属再结晶温度以上进行的锻造工艺。
温锻:在高于室温和低于再结晶温度范围内进行的锻造工艺。
冷锻:在室温下进行的锻造工艺。
包括冷挤、冷镦、冷压印等。
等温锻:在锻造全过程中,温度保持恒定不变的锻造方法。
此法需要将模具、坏料都加热到锻造温度。
初次成形加工:用于制造板材、棒材、型材等原材料的加工过程的统称。
二次成形加工:对于已经过初次成形加工获得的原材料(板材、棒材、型材等)进行再次塑性加工,以制造机械零件、工件或毛坯的成形加工方法。
如锻造、冲压、旋压等。
成形:将固体材料进行塑性变形,而获得所要求形状和尺寸的制品的过程。
预成形:使坯料形状产生部分变化以获得更适合于进一步塑性变形的形状。
热成形:金属在再结晶温度以上进行的成形过程。
温成形:在高于室温和低于再结晶温度范围内进行的成形过程。
冷成形:坯料在室温下的一种成形方法,通常在变形过程中会出现加工硬化。
二、原材料原材料:供锻压加工的材料,如型材、板材、棒材、带材、线材、铸锭、金属粉末等。
锻压技术
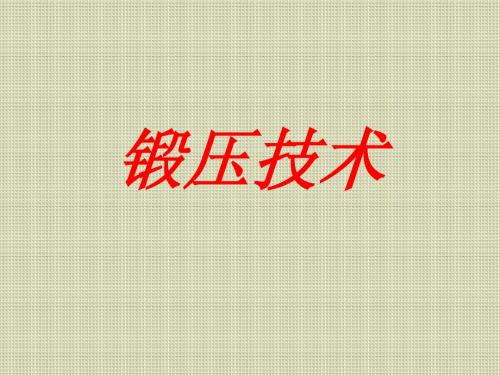
我国锻压工业中存在大量违背绿色制造原 则的问题, 应引起国内同行的足够重视。应 投入大量人力财力进行锻压工业中绿色制 造系统的研究与开发工作, 同时应注意平衡 资源效率和环境污染两方面的矛盾, 转变观 念, 真正行动起来进行这方面的工作。
锻压技术的应用
锻压技术广泛应用于航空航天、核电、海上平 台、高速列车等铸锻件,技术含量高,既是国家 装备制造业的基础行业,是国家独立建设的命脉 行业。例如航空工业把锻压技术作为重要支柱技 术。因为锻压技术制造出的锻件是飞机和发动机 的重要组成部分, 其制造水平对飞机性能及技术经 济效益有举足轻重的影响。所以,为适应航空工 业发展, 目前应集中力量重点发展等温模锻技术、 大型锻件的模锻技术、大型风扇叶片的成形及连 接技术、叶片精锻技术的推广应用及锻造过程的 物理模拟技术等。
锻压技术
• 锻压技术的概念及其特点 • 锻压技术的发展趋势 • 锻压机械设备介绍 • “绿色”锻压技术 • 锻压技术的应用
锻压技术的概念 及其特点
锻压技术的概念
• 金属在外力作用下产生塑性变形并获得所 需形状与性能的原材料、毛坯或零件的生 产方法称为锻压。
锻压是锻造和冲压的总称
锻造 锻压
高温状态
世界工业强国都十分重视航空大型模锻件生 产条件的建设,领先于我国30一50年建成了 450MN, 650MN, 750MN模锻液压机,生产了技 术含量居世界领先地位的铝合金、钦合金、高温 合金和合金钢优质大型模锻件。我国作为发展中 国家,历经半个多世纪的发展,已经具备了建设 世界顶级吨位且技术含量高的800MN模锻液压机 的技术与物质基础,该模锻液压机的建成与投产, 必将大大提升我国航空大型模锻件的研发和生产 能力,推动我国航空锻压制造技术跻身于世界强 者行列。
简述锻压特点
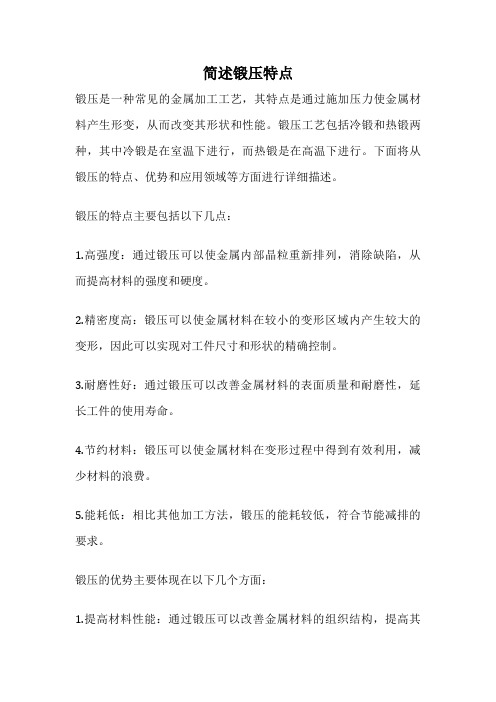
简述锻压特点锻压是一种常见的金属加工工艺,其特点是通过施加压力使金属材料产生形变,从而改变其形状和性能。
锻压工艺包括冷锻和热锻两种,其中冷锻是在室温下进行,而热锻是在高温下进行。
下面将从锻压的特点、优势和应用领域等方面进行详细描述。
锻压的特点主要包括以下几点:1.高强度:通过锻压可以使金属内部晶粒重新排列,消除缺陷,从而提高材料的强度和硬度。
2.精密度高:锻压可以使金属材料在较小的变形区域内产生较大的变形,因此可以实现对工件尺寸和形状的精确控制。
3.耐磨性好:通过锻压可以改善金属材料的表面质量和耐磨性,延长工件的使用寿命。
4.节约材料:锻压可以使金属材料在变形过程中得到有效利用,减少材料的浪费。
5.能耗低:相比其他加工方法,锻压的能耗较低,符合节能减排的要求。
锻压的优势主要体现在以下几个方面:1.提高材料性能:通过锻压可以改善金属材料的组织结构,提高其强度、硬度和耐磨性等性能。
2.节约成本:锻压可以降低生产成本,提高生产效率,从而提高企业的竞争力。
3.保护环境:锻压过程中不需要使用化学物质,不会产生废气、废水和废渣,对环境友好。
4.提高产品质量:锻压可以减少产品的内部缺陷,提高产品的质量稳定性和可靠性。
锻压在航空航天、汽车制造、机械加工、军工等领域有着广泛的应用。
在航空航天领域,锻压可以制造高强度、高硬度的航空零部件,提高飞行器的安全性和可靠性;在汽车制造领域,锻压可以制造车轮、车架等零部件,提高汽车的性能和舒适性;在机械加工领域,锻压可以制造各种机械零部件,提高设备的工作效率和稳定性;在军工领域,锻压可以制造各种军用装备,提高国防实力和安全保障能力。
锻压是一种重要的金属加工工艺,具有高强度、精密度高、耐磨性好、节约材料、能耗低等特点,其优势包括提高材料性能、节约成本、保护环境、提高产品质量等。
锻压在航空航天、汽车制造、机械加工、军工等领域有着广泛的应用前景,对促进工业发展和提高国防实力具有重要意义。
锻压是指锻造和板料冲压

• 3.2.2 自由锻设备
常用的自由锻设备有空气锤、蒸汽-空气锤和水压机等。其砧座质量一般为落 下部分的10~15倍,蒸汽-空气自由锻锤的落下部分质量一般为1~5t,小于 1t的使用相应的空气锤,大于5t的使用水压机。
1.空气锤结构及工作原理 空气锤是自由锻最常见的设备,如图3.1(a)所示。由锤身、压缩缸、工作 缸、传动机构、操纵机构、落下部分及砧座等组成。锤身、压缩缸和工作缸 缸体铸成一体。传动机构包括减速机构、曲柄、连杆等。操纵机构包括踏杆 (或手柄)、旋阀及其连接杠杆。空气锤的规格用落下部分的质量来表示, 其落下部分包括工作活塞、锤杆等。例如70kg的空气锤是指落下部分的质量 为70kg。空气锤打击力为落下部分质量的1000倍左右。空气锤规格依据锻件 的尺寸与质量选择。 空气锤的传动原理如图3.1(b)所示。电动机通过减速装置带动曲柄连杆机 构运动,使压缩气缸的压缩缸活塞上下运动,产生压缩空气。通过手柄或踏 脚杆操纵上、下旋阀,使其处于不同位置时,使压缩空气进入工作气缸的上 部或下部,推动由活塞、锤杆和上砧铁组成的落下部分上升或下降,完成各 种动作。
3.1 概 述
• 锻压是指锻造和板料冲压的总称,属于塑性加工方法,是指金属材料在一定
外力作用下,使其产生塑性变形,从而获得一定尺寸、形状及具有一定力学 性能毛坯或零件的加工方法。塑性加工作为金属加工方法之一,是机械制造
领域的重要加工方法。 锻造是利用锻造设备,通过工具或模具使金属毛坯产生塑性变形,从而获得
冲压是指利用冲模在冲床上对金属板料施加压力,使其产生分离或变形,从
而得到一定形状、满足一定使用要求零件的加工方法。冲压通常在常温下进 行,也称冷冲压,又因其主要用于加工板料零件,故又称板料冲压。
3.2 自由锻
锻压手册(第1卷)锻造

8 孙杰 , 映林. 柯 残余应力对航空整体结构件加工变形的影 响分析 . 机
械 工 程学 报 ,0 5,1 2 :1 20 4 ( ) 17~12 2
4 结 语
本文 首先对 引起 弱刚度 复杂 构件加 工变 形 的原 因 进 行 了分 析总结 , 为 弱 刚度 件 的加 工 误 差 主要 是 由 认 于其在加 工过程 中的变形 引起 的。为 了详细 了解 薄壁 件 和薄壁 孔 的加 工变 形 规 律 , 采用 有 限元 方法 对 其 变 形 进行 了分析 。最后认 为 对弱 刚度复 杂构件 的加工 变
近的孔 。
3 万 敏, 张卫红. 薄壁件周 铣切削力建模与表面误差 预测方法研究. 航
空学 报 ,0 5,6 5)5 8~ 0 20 2 ( :9 6 3
4 王志刚, 何宁等. 薄壁 零件加 工变形分 析及控 制方案. 国机械工 中
程 ,0 2 1 ( ) 14~17 2 0 ,3 2 :1 1
工艺与检测 Thl o — on ̄ n eo /d o
—
的合理选择以及加工前后工件处理等各方面因素, 从 而减小弱刚度件加工变形 , 提高弱刚度件的加工质量。
参 考 文 献
1 J r—S y n s i e h o gT a ,Ch n u g—L io ii iL a .Fnt e—ee n deigo tt lme tmo l fsai n c
德国哈默hermle的c系列五轴加工中心z统快速进给系统高性能cnc控制系统高性能刀夹上世纪80年代世界机床制造强国德国日本就锻压手册第1卷锻造第2卷冲压第3卷锻压车间设备第3版中国机械工程学会塑性工程学会编2008为了提高我国机械电子行业的工艺水平推动企业技术进步满足科研生产发展的需要中国机械工程学会塑性工程锻压新一轮修订增补新内容删去技术陈旧的部分压缩一些用量少且各行业已有相应标准的内容
锻压
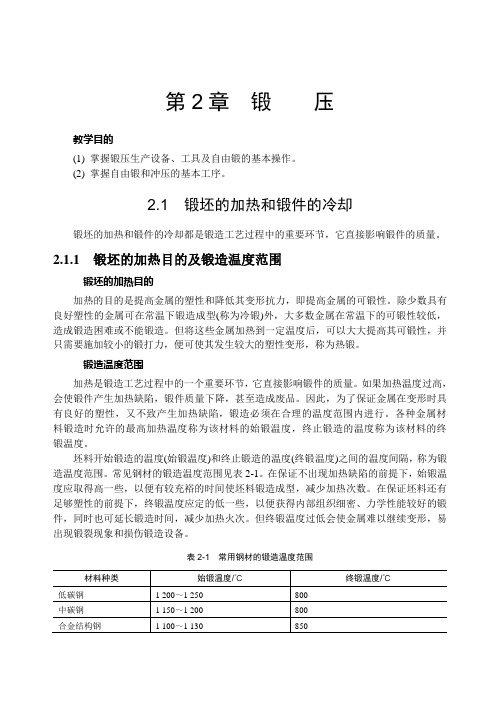
第2章锻压教学目的(1) 掌握锻压生产设备、工具及自由锻的基本操作。
(2) 掌握自由锻和冲压的基本工序。
2.1 锻坯的加热和锻件的冷却锻坯的加热和锻件的冷却都是锻造工艺过程中的重要环节,它直接影响锻件的质量。
2.1.1 锻坯的加热目的及锻造温度范围锻坯的加热目的加热的目的是提高金属的塑性和降低其变形抗力,即提高金属的可锻性。
除少数具有良好塑性的金属可在常温下锻造成型(称为冷锻)外,大多数金属在常温下的可锻性较低,造成锻造困难或不能锻造。
但将这些金属加热到一定温度后,可以大大提高其可锻性,并只需要施加较小的锻打力,便可使其发生较大的塑性变形,称为热锻。
锻造温度范围加热是锻造工艺过程中的一个重要环节,它直接影响锻件的质量。
如果加热温度过高,会使锻件产生加热缺陷,锻件质量下降,甚至造成废品。
因此,为了保证金属在变形时具有良好的塑性,又不致产生加热缺陷,锻造必须在合理的温度范围内进行。
各种金属材料锻造时允许的最高加热温度称为该材料的始锻温度,终止锻造的温度称为该材料的终锻温度。
坯料开始锻造的温度(始锻温度)和终止锻造的温度(终锻温度)之间的温度间隔,称为锻造温度范围。
常见钢材的锻造温度范围见表2-1。
在保证不出现加热缺陷的前提下,始锻温度应取得高一些,以便有较充裕的时间使坯料锻造成型,减少加热次数。
在保证坯料还有足够塑性的前提下,终锻温度应定的低一些,以便获得内部组织细密、力学性能较好的锻件,同时也可延长锻造时间,减少加热火次。
但终锻温度过低会使金属难以继续变形,易出现锻裂现象和损伤锻造设备。
表2-1 常用钢材的锻造温度范围锻坯金属的加热温度可以用仪表测量,还可以通过观察加热毛坯的火色来判断,即用火色鉴定法,火色鉴定法是实际生产中较为常用的方法。
碳素钢加热温度与火色的关系见表2-2。
表2-2 碳素钢加热温度与火色的关系2.1.2 锻造加热设备在锻造生产中,根据加热采用热源的不同,分为火焰加热和电加热。
前者利用烟煤、重油或煤气燃烧时产生的高温火焰直接加热金属,后者是利用电能转化为热能加热金属。
- 1、下载文档前请自行甄别文档内容的完整性,平台不提供额外的编辑、内容补充、找答案等附加服务。
- 2、"仅部分预览"的文档,不可在线预览部分如存在完整性等问题,可反馈申请退款(可完整预览的文档不适用该条件!)。
- 3、如文档侵犯您的权益,请联系客服反馈,我们会尽快为您处理(人工客服工作时间:9:00-18:30)。
概述
锻造生产的发展趋势
新材料的方面
计算机技术在锻压技术中的应用 如何制造出性能要求更高的锻件
概述
压力加工方法的工作原理、应用于发展趋势
名称 示意图 工作原理 是金属坯料通 过一对回转轧 辊间的空隙而 产生连续变形 是金属坯料从 挤压模的模孔 中挤出而变形 使金属坯料从 挤压模的模孔 中拉出而变形 应用与发展趋势 应用:生产钢板、无缝钢管及各种型材 (如圆钢、方钢、扁钢、角钢、槽钢、工 字钢、钢轨等) 发展趋势:高速轧制、精密轧制、轧锻组 合等 应用:生产低碳钢、有色金属及其合金的 型材、管件和零件 发展趋势:高速精密挤压、挤锻结合 应用:可拉制直径仅为0.02毫米的金属丝 和薄壁管,也可用于提高轧制型材和管材 的精度和表面质量 发展趋势:高尺寸精度、低表面粗糙度
轧制
挤压
拉拔
概述
压力加工方法的工作原理、应用于发展趋势
名称 示意图 工作原理 使金属坯料放在 上、下砧贴间受 冲击力或压力而 变形 将金属坯料放在 模锻模堂内受冲 击力或压力而变 形 利用冲模,使金 属板料产生分离 或变形 应用与发展趋势 应用:单件小批生产力学性能高形状简 单的零件毛坯,是制造大型锻件的唯一 方法 发展趋势:锻件大型化、操作机械化, 液压机代替大锻锤 应用:成批大量生产形状较复杂的中、 小型模锻件 发展趋势:少、无切削,精密化(如精 密模锻) 应用:成批大量生产形状复杂薄板件、 仪器、仪表件、中空零件或汽车覆盖件 发展趋势:自动化、精密化、非传统成 型工艺的发展
变形抗力:对塑性变形的阻力(表征塑 性变形的难易程度)
δ↑,锻造性能↑,不易开裂
变形抗力↓,锻造性能↑
金属的锻造性能
影响因素
金属的本质
化学成分
组织状态
纯金属的可锻性 > 合金 低C钢的可锻性 >高碳钢 含C量↑,HB ↑,δ、αk ↓,变形抗力↑ 单相组织,δ↑
固溶体的可锻性 > 化合物
晶粒大小影响锻造性能(粗晶组织<细晶组织、锻轧组织)
M12螺栓、冷镦210/分(自动冷镦机) M12螺母、冷镦150/分(自动冷镦机)
生产率较高(冷镦、冷挤压)
但:锻件的复杂程度不如铸件 (具有复杂内腔的零件:箱体件、汽缸体等 铸件)
概述
锻压加工的应用
锻压加工是以金属的塑性变形为基础的 , 各种 钢和大多数非铁金属及其合金都具有不同程度 的塑性 , 因此它们可在冷态或热态下进行锻压 加工 , 而脆性材料 (如灰铸铁、铸造铜合金、铸 造铝合金等)则不能进行锻压加工。 承受重载、使用要求高的机器零件,薄板件, 日用品
大多数锻件的锻压加工是在再结晶温度以上进行的, 这样,由变形引起的强化现象,会因随后的再结晶过程而消 失 , 所以锻造毛坯可以连续地锻压变形。
金属的纤维组织
锻造流线(纤维组织)
在锻造时,晶粒沿变形方向伸长,塑性夹杂物随 着金属变形沿主要伸长方向呈带状分布,脆性夹杂 物被打碎,顺着金属主要伸长方向呈碎粒状或链状 分布,呈流线组织。
金属的锻造性能
影响因素
变形条件 —— 变形温度T变
T变↑,原子活动能力↑,热能↑,塑性↑ ,变形抗 力↓,锻造性能↑ 可以消除→正火 尽量避免
T变 过高
过热:T变 ↑, A晶粒迅速长大(粗晶),δ↓ 过烧:T变 接近金属熔点 δ↓↓ 报废
金属的锻造性能
锻造温度范围的选择
金属锻造加热时允许的最高加热温度称为始锻温度。 (固相线以下200˚C左右)
金属的纤维组织
力学性能:
沿着流线方向 (纵向)抗拉强度较高 , 而垂直于流 线方向 (横向)抗拉强度较低。
生产中若能利用流线组织纵 向强度高的特点 , 使锻件中的流 线组织连续分布并且与其受拉力 方向一致 , 则会显著提高零件的 承载能力。 例如, 吊钩采用弯曲工序成形 时 , 就能使流线方向与吊钩受 力方向一致 , 从而可提高吊钩 承受拉伸载荷的能力。
塑性变形对金属组织和性能的影响
回复与再结晶
T↑,原子的活动能力↑ 由不稳定状态→稳定状态
回复
T回=(0.25~0.3)T熔(˚K) 组织:晶格畸变基本消失
性能: HB↓,δ↑αK ↑
应用: 高强度、有一定塑性的机械零件都可以通过回复处理 来提高它本身的性能。
比如:一般像弹簧,冷拉冷卷后进行回复处理,这样既可以 保证高的弹性,同时还可以保证一定的硬度。
应力状态
应力性质:大小和方向影响可锻性 压应力↑,数值↑,锻造性能↑,反之锻造性能↓
原因:拉应力促使晶间变,加速晶界破坏,裂纹扩展
知识点-小结
1.冷变形对金属组织与性能的影响
组织上:晶粒变形、晶格畸变、晶粒间产生碎晶 性能上:产生加工硬化 应用:强化金属材料(自行车链条、无相变材料),提高构件的实用安全性
停止锻造时的温度称为终锻温度。(800 ˚C左右)
锻造温度是指始锻温度与终锻温度之间的温度。
金属的锻造性能
影响因素
变形条件 —— 变形速度 V变 (单位时间的变形量)
一般,V变↓,锻造性能↑(V变↑,回复、再结晶来不能及时消除加 工硬化现象) V变 < C : V变↑,锻造性能↓ V变 > C : V变↑,锻造性能↑(热效应,↑金属实际温度) 注意:在高速锤上才能实现(V变>16~20m/s),水压机 0.1~0.3m/s,锻锤7~8m/s
技艺高超(湖北江陵楚墓:越王勾践的宝剑;秦始 皇陵:合金钢锻制的宝剑,外硬心韧)
概述
锻压是指在外力作用下,使金属坯
料产生塑性变形,以获得所需形状、尺
寸和力学性能的毛坯或零件的加工方法。
锻压是锻造和冲压的总称。
概述
压力加工的特点
能改善金属内部组织,提高金属的力学性能 节省原材料 精度较高
概述 锻压加工工艺基础 常用锻造方法
板料冲压
锻压件结构设计
锻压
教学要求:
1、了解锻压工艺概述(生产特点、适用范围、发展 趋势) 2、掌握铸造工艺基础(塑性变形过程、组织性能变 化、锻造性)
教学重点与难点:
1、铸造工艺基础(塑性变形过程、组织性能变化、 锻造性)
概述
发展概况
历史悠久 公元前14世纪的商代 兵器生产(1972 年出土铁韧铜钺)
晶内变形+晶间变形
产生滑移
塑性变形对金属组织和性能的影响
变形温度<T再结晶
冷变形对金属组织与性能的影响
组织上 性能上 产生加工硬化 σb↑、HB↑ 应用 强化金属材料 (自行车链条、 汽车覆盖件)
—晶粒变形 —晶格畸变 —晶粒间产生碎晶
δ↓、 αK ↓
加工硬化是一种 不稳定的现象
原因:滑移面附近的晶粒碎 晶块,晶格扭曲畸变,增大 滑移阻力,使滑移难以进行。
金属的纤维组织
热处理和再结晶无法消除 纤维组织的合理利用:
合理利用
零件工作时的最大正应力∥纤维方向,最大切应力⊥纤维方向 流线的分布与零件的外形轮廓相符合,而不被切断
分析: 图a采用棒料直接经 切削加工制造螺钉, 由于流线不连续 , 所以流线分布不合理。 图b采用同样棒料经 局部镦粗方法制造螺 钉,其流线的分布是 合理的。
2.热变形对金属组织与性能的影响
组织上:消除内部缺陷、细化晶粒(再结晶组织)、改变杂质分布 性能上:提高力学性能、产生各向异性、表面精度↓
自由锻
模锻
冲压
压力加工基本理论
金属的塑性变形与再结晶
金属的纤维组织 金属的锻造性能(可锻性)
塑性变形的实质
单晶体的塑性变形——产生滑移
滑移——晶体的一部分相对于另一部分沿某晶面 及晶向发生相对滑移
线缺 陷
滑移面整体 刚性移动
塑性变形的实质
多晶体的塑性变形
实质:
晶粒与晶粒 之间产生滑 移和转动
塑性变形对金属组织和性能的影响
再结晶
T再=(0.35~0.4)T熔(˚K) 组织:晶格畸变完全消失、碎晶、变形晶粒 等轴细晶
性能: HB↓,δ↑αK ↑
应用:冷轧、冷压过程进行再结晶退火。
塑性变形对金属组织和性能的影响 热变形对金属组织和性能的影响 变形温度>T再结晶 加工硬化与再结晶同时进行 不产生加工硬化
实例:
金属的纤维组织
纤维组织的明显程度与锻造比有关
锻造比
通常用拔长时的变形程度来衡量。
A0 锻造比: Y A
拔长前坯料的横截面积 拔长后坯料的横截面积
锻造比↑→变形量↑ ,各向异性↑
金属的锻造性能
进行压力加工 的难易程度
衡量指标
塑性:金属材料产生塑性变形而不破坏 的能力(表征塑性变形的能力)