涂装车间减少面漆颗粒qcd项目
降低一次喷粉不良率QC项目

到位时间 负责人
1
有油污不能 有油污不能 上线 保证挂具导 电性 及时排放空 气冷凝水 控制磷化膜 的附着力及 厚度 对接油盘进 行整修
Dream come true. We can do it !
6
Hero Haier 2010
目标可行性分析
为了验证99.5%的目标值能否实现,我们对2009年 为了验证99.5%的目标值能否实现,我们对2009年9月1-8日不良现象进行细致的分 99.5%的目标值能否实现 2009 统计各种不良现象的数量,并整理得资料如下: 析,统计各种不良现象的数量,并整理得资料如下:
时间
Dream come true. We can do it !
12
Hero Haier 2010
巩固措施
为了巩固本次活动取得的成果,我们将对策表中有效措施制定成《现场工艺指导书》 为了巩固本次活动取得的成果,我们将对策表中有效措施制定成《现场工艺指导书》 进行标准管理。 进行标准管理。
序号
对策
磷化处理不当, 磷化处理不当,磷化膜厚度不一 悬挂链油污滴落到工件上 粉末受潮
Dream come true. We can do it !
8
Hero Haier 2010
制定对策
要因确认完成后,小组全体成员展开热烈讨论,对症下药, 要因确认完成后,小组全体成员展开热烈讨论,对症下药,根据不良原因制定了以下 有效对策,具体如下: 有效对策,具体如下:
Dream come true. We can do it !
讲解减少涂装颗粒的控制措施

讲解减少涂装颗粒的控制措施汇报人:2023-12-15•涂装颗粒问题概述•生产环境控制•原材料质量控制目录•涂装工艺过程控制•人员操作规范培训•质量检测体系完善01涂装颗粒问题概述颗粒问题定义与分类颗粒问题定义涂装过程中,涂膜表面或内部出现的大小不一、形状各异的颗粒物。
颗粒分类按照颗粒来源可分为外界颗粒和内部颗粒;按照颗粒大小可分为大颗粒和小颗粒。
施工环境不洁,空气中灰尘、杂质等漂浮物附着在涂膜表面。
涂料本身含有杂质,或施工过程中涂料搅拌不均匀,导致颗粒沉淀在涂膜内部。
颗粒产生原因分析内部颗粒产生原因外界颗粒产生原因颗粒会导致涂膜表面不平整,影响产品的外观质量。
外观质量防腐性能使用寿命颗粒的存在会破坏涂膜的致密性,降低产品的防腐性能。
颗粒会加速涂膜的老化和破损,缩短产品的使用寿命。
030201颗粒对产品质量影响02生产环境控制定期清扫车间地面,保持地面无灰尘、油污等污染物。
地面清洁定期清洁车间墙面和天花板,防止积尘和蛛网。
墙面与天花板清洁确保生产设备和工具在使用前后进行清洁,避免残留物影响涂装质量。
设备与工具清洁车间清洁度管理空气过滤系统优化高效过滤器选用高效过滤器,有效去除空气中的微小颗粒和污染物。
定期更换滤芯根据使用情况,定期更换过滤器滤芯,保持过滤效果。
车间通风加强车间通风,保持空气流通,降低污染物浓度。
定期对生产设备进行检查,确保设备处于良好工作状态。
设备定期检查按照设备保养要求,定期对生产设备进行保养,延长设备使用寿命。
设备保养发现设备异常情况时,及时处理并记录,防止问题重复出现。
异常处理生产设备维护与保养03原材料质量控制选用品牌知名度高、质量稳定的涂料产品,确保涂料本身质量可靠。
选择优质涂料建立严格的涂料检验标准,对涂料的外观、粘度、细度、遮盖力、干燥时间等性能指标进行检测,确保涂料符合使用要求。
检验标准涂料选择与检验标准底材处理及前处理工艺优化底材处理对底材进行除油、除锈、磷化等处理,提高底材的附着力和涂装效果。
QC活动在降低立式喷涂挂具处理成本的应用

251管理及其他M anagement and otherQC 活动在降低立式喷涂挂具处理成本的应用钟坤斌(广东华昌铝厂有限公司,广东 佛山 528231)摘 要:应用QC 活动降低立式喷涂挂具处理成本,通过现状调查确定喷涂立式线挂具发外承包处理成本较高,针对症结问题进行原因分析和要因确认,制定降低立式喷涂挂具处理成本的措施,使每月挂具处理成本降低2.5万元以上。
关键词:立式喷涂挂具处理;QC 活动;生产成本;精细化管理中图分类号:U472 文献标识码:A 文章编号:11-5004(2020)16-0251-2收稿日期:2020-08作者简介:钟坤斌,男,生于1992年,汉族,广东惠州人,本科,助理工程师,研究方向:铝型材喷涂生产工艺。
随着某厂生产精细化管理的推进,达到降本增效的目的,某厂对各项高成本高消耗的项目进行立项,通过QC 活动逐步降低立项的项目成本,并把QC 成果标准化、成果化。
运用QC 活动来解决生产过程中的问题,有利于改善和加强管理工作,提高管理水平,同时也有助于提高员工的科学思维能力、组织协调能力、分析与解决问题的能力,从而使员工岗位成才。
既有直接经济效益,又有长期的隐形效益。
1 QC活动步骤及成果 1.1 成立QC 小组涂涂 QC 小组成立于2020年3月,小组由技术部、喷涂车间、机修部门、采购部、财务部的12位工程师和生产技术人员组成,团队成员有着丰富工作经验,为问题的公关提供了有力的保障。
1.2 课题的选定2018年6月份某厂提出精细化管理、降本增效。
某厂决定对各项高成本高消耗的项目进行立项,通过QC 活动逐步降低立项的项目成本。
根据以上课题某厂QC 小组马上开始开会讨论,用决策制定表的方法根据以上4个课题的可行度高低、紧急度,小组最终选择了《降低喷涂立式线挂具处理成本》这一课题。
1.3 活动计划小组基于实际生产情况,针对本次QC 活动进行活动计划的制作,小组在未来的12周中将按照计划进行开展QC 活动。
20.(案例)涂装车间QCD改善
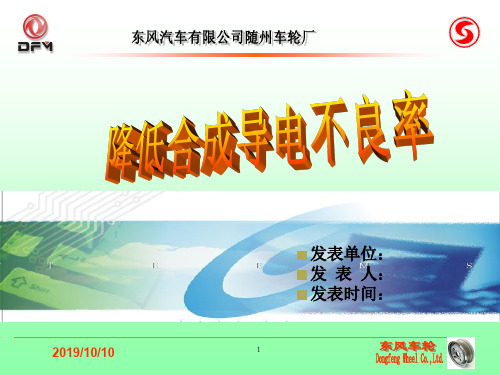
2019/10/10
11
制定对 策
序号
要因
挂钩悬挂横杆倾斜
1 角度有偏差
2 挂具检修的频率少
挂具导电肋片为直
3
边,不易卡住工件 中心孔
对策
目标
措施
负责人 日期
调整挂钩悬挂 横杆倾斜角度
定期检修
调整适当的 角度,使工 件容易导电
保持挂具导 电功效
挂钩悬挂横杆与 挂具90度的角调 整为80度,向上 倾斜10度。
2019/10/10
6
三、现状调查(数据)
日期
8月8日 8月9日 8月10日 8月11日 8月12日 8月13日 8月14日
产品 种类 06D 22D 06D 22D 06D 22D 12E
生产 数量 132 369 3552 1138 944 841 1246
导电 不良
4 20 66 66 15 10 20
2019/10/10
3
小组成员介绍
序号 姓名
1
黄建波
2
冷胜利
3
潘建辉
4
杨明
5
吕银川
职务
涂装工段长 涂装二线班长 技术工程师 涂装二线上挂工 涂装二线下挂工
组内职务
组长 副组长 副组长
组员 组员
主要分工
规划指挥、组织协调
原因分析、制定目标、 方案规划、检查效果 质量改进、制定对策、 实施对策、效果检查 原因分析、实施对策
2019/10/10
发表单位: 发 表 人: 发表时间:
1
目录
小选 组题 简理 介由
现目解 对 对 效 今小
状标
策 策果 后
工业涂装治理方案

工业涂装治理方案1. 背景介绍在工业生产过程中,涂装是一项重要的工艺环节。
然而,工业涂装过程中会产生大量污染物和废水,对环境造成负面影响。
为了减少和控制涂装过程中的污染物排放,制定一套科学有效的工业涂装治理方案是必要的。
2. 目标本方案的目标是: - 减少涂装过程中的污染物排放 - 确保涂装质量和生产效率 - 降低治理成本 - 提高企业形象和社会责任感3. 治理方案3.1 选用环保型涂料环保型涂料是一种具有低挥发性有机化合物(VOC)含量的涂料,其特点是低污染、低气味、低毒性。
企业在涂装过程中应尽可能选择环保型涂料,以减少有机溶剂的排放。
3.2 完善涂装设备涂装设备的完善可以有效控制涂装过程中的污染物排放。
应选用性能优良的喷枪、喷枪清洗设备等,以确保涂料喷洒的均匀性和降低溢漏的可能性。
另外,还可以安装废气处理装置,对涂装过程中的废气进行净化处理。
3.3 强化工艺管理合理的工艺管理可以降低涂装过程中的污染物排放。
在涂装前,应进行充分的工艺规划和准备工作,包括车间净化、涂装区域的密封、废气排放口的设置等。
在涂装过程中,要严格执行操作规程,保证每个环节都符合标准要求。
3.4 加强员工培训与意识教育员工是涂装过程中的关键环节,加强员工培训和意识教育对污染物控制非常重要。
企业应定期开展员工培训,包括涂装技能的培训和环保意识的教育,使员工充分了解涂装工艺中环境保护的重要性,并合理使用和管理涂装设备。
3.5 定期检测和监测定期检测和监测涂装过程中的污染物排放情况,是评估治理效果的重要手段。
企业应建立完善的检测和监测机制,监测并记录涂装过程中的污染物浓度和排放量。
根据检测结果,及时调整涂装工艺和治理措施,以达到减少污染物排放的目标。
4. 治理效果评估为了追踪和评估治理效果,企业可以采用以下方法: - 污染物排放量的统计和分析 - 涂装质量和成品率的监测 - 定期进行环境影响评估5. 注意事项在实施工业涂装治理方案时,需要注意以下事项: - 遵守环境相关法律法规和标准 - 与相关部门进行沟通和合作 - 多方面考虑和平衡治理成本和治理效果6. 结论工业涂装治理是一个综合性工作,需要从涂料选用、设备设施、工艺管理、员工培训等多个层面来进行整体治理。
涂装漆面颗粒问题改进策略研究

涂装漆面颗粒问题改进策略研究发布时间:2021-06-10T11:04:31.057Z 来源:《中国科技信息》2021年7月作者:刘艳慈[导读] 目前颗粒问题已经成为各个涂装行业控制的难点,解决颗粒问题能够最有效的提升一次合格率,由于涂装过程复杂,涉及的控制点较多,对过程中的环境要求十分严格,目前颗粒问题在涂装外观问题中占比最大,本文采用8D团队问题导向法为减少颗粒问题提供改进方向,为汽车涂装行业提供参考。
北京北汽模塑科技有限公司刘艳慈 102606摘要:目前颗粒问题已经成为各个涂装行业控制的难点,解决颗粒问题能够最有效的提升一次合格率,由于涂装过程复杂,涉及的控制点较多,对过程中的环境要求十分严格,目前颗粒问题在涂装外观问题中占比最大,本文采用8D团队问题导向法为减少颗粒问题提供改进方向,为汽车涂装行业提供参考。
关键词:汽车;涂装;颗粒;8D0前言随着汽车工业的发展,人们对汽车保险杠的要求不仅仅停留在安全性能方面,在增加汽车的美观性及使用寿命方面也有了更高的要求,而增加美观及提升寿命均离不开保险杠涂装,通过涂装确保保险杠使用寿命中的耐光照和自然老化的性能,通过涂装不同的颜色增加美观,汽车保险杠主要包括注塑、喷涂、装配三大生产工艺,其中涂装为生产工艺中核心组成部分也是能耗最高的工艺,涂装工艺所涉及的工艺控制点、设备控制点及物料控制点繁多,任意一控制点的波动都会对涂装一次下线合格率产生巨大的影响,引起交货风险从而造成巨大的成本损失。
而颗粒作为涂装外观中占比最大的问题,通过颗粒问题改进可有效提升一次合格率,降低产品的生产成本。
1.8D分析法介绍8D是8 Disciplines的英文缩写,又称团队导向的问题解决法、8D问题求解法是美国福特汽车公司处理问题的一种方法。
8D分析法使用描述、格式化、分析、量化等工具,提供彻底解决问题的指引,是用来分析问题的根本原因并解决问题的系统方法,它提供了一套符合逻辑的解决问题方法,以下对8D的主要内容详细阐述。
QC案例:降低产品底漆损耗量

QC案例:降低产品底漆损耗量QC案例:降低产品底漆损耗量方法应用编者按:围绕原材料的节约,Qc小组一直大有可为,效果显着.在今年上海市QC 小组擂台赛上获得二等奖的"降低205系列一遍底漆损耗量"项目,是上海惠工缝纫机三厂在开展节能降耗调查中,确立开展的项目.小组运用QC活动常见方法,特别是通过翔实的试验数据,确立最佳改进方案,涂料节省达25.1%,对于很多企业而言,这样改进很有借鉴意义. QC案例:降低产品底漆损耗量上海惠工缝纫机三厂涂装车间为响应国家节能减排的号召,围绕车间与厂部签订的节能降耗协议,在车间里开展了一系列调查.他们发现.生产用涂料的消耗量最大,而且公司生产的GC205系列又是车间最多的产品, 其中底漆的消耗量更为严重.所以,六位来自车间不同班组的工艺员,班组长,安全员组成了"亮剑小组, 希望通过QOJ\组活动达到降'f1~205系列一遍底漆损耗量. 调查现状,制定目标通过对历史数据的调查,小组发现,一遍涂饰底漆损耗量每百台最高达8千克,最低为5--T-克.且高耗量达到7个月,远高于二遍底漆的消耗量.同时,一遍涂饰后的废漆量明显多于二遍涂饰后的废漆量.而一个月的底漆损耗就达2700元.对比车间细化目标,2009年的目标是在2008年的基础实现:一遍底漆压缩率21%,二遍底漆压缩率为12%.说明车间把压缩的重头放在一遍底漆耗用量.通过前面的三项调查,小组确定了此次QC活动的颜琰目标是205系列机壳百件一遍底漆消耗量2009年相对于2008年而言,最高值从8千克下降到55千克,平均值从 5.84千克下降到5.o-T--克.分析原因,确认要因目标确定后.小组进行了原因分析,通过头脑风暴法和因果图,小组认为,造成20,5系列机壳一遍底漆消耗高的问题主要有四个方面9个末端原因造成. 首先,小组对九条末端原因确认的方法作了探讨, 对完成日期提出了要求,并具体落实到每个QC成员身上. 末端原因一现岗喷工技能低.通过对技术档案的查阅.现岗的喷工都是具有1O年以上工作经验的中级工. 通过技能测评.速度与质量稳定,耗漆量无异常.因此是非要因.同样方法对末端原因二临时喷工缺经验的确认,耗漆量无异常.因此也是非要因.末端原因三气压不稳定.通过现场实验得~lJ30对空压机压力与喷漆量的数据,经过散布图的绘制与计算, 发现两者问的影响微弱.是非要因.上温质窦."N(.~H,A.iQUA,L,ITY67f末端原因四喷枪13径大.经过小组对不同Iq径喷枪的实验.发现.大口径喷枪漆的损耗大于小口径喷枪的损耗主要反映在喷溅范围大.所以是要因. 末端原因五喷枪调节器失灵.经过测评,在生产过程中发生故障比较偶然,对涂料耗量的影响极小属于非要因.末端原因六废机壳未剔除,对涂料耗量的影响也极小,属于非要因.末端原因七涂料粘度不当.经过10次随机抽查,小组未发现明显影响涂料现象.属于非要因.末端原因八炉温不稳定.同样未发现明显影响涂料现象,也属于非要因.末端原因九空气湿度变化的确认,小组通过对各种天气下的耗漆量的测试,变化的幅度小,并且没有一定的比例关系.所以是非要因.制定对强化练兵对于确定的唯一一条要因喷枪13径大,小组制订了两条对策.措施一,通过实验选择合适的小口径喷枪.小组首先选择了18毫米,15毫米,10毫米,08毫米四种不同口径的喷枪,对涂膜厚度,作业时间,可喷数量,喷溅范围与机外损耗四个方面进行实验.实验显示在相同的15-T-克涂料下,随着喷枪口径的减小,涂装数量呈现明显上升趋势.喷溅在机外的涂料损耗呈现大幅下降趋势.并且随着喷枪13径缩小,涂膜厚度呈现下降趋势, 但仍在标准内喷涂时间呈现上升趋势,但在作业时间标准内.这两个结果说明不影响正常生产秩序. 根据四组实验数据,小组认为0.8毫米口径的喷枪是最为理想的选择.它保证原有涂层厚度,维护正常生产节拍,涂装数量明显增多,机外损耗大幅下降.小组向车间作了《Qc实验报告》,提出采用08毫米口径喷枪喷涂生产实践的建议.建议得到车间的批准.措施二,强化练兵规范一遍底漆喷涂技能.在采 ,瑚68m?1;,'.,n{:-20{0瓣1{用小El径的喷枪后,喷涂方法就有改变必须建立新的操作规范.小组决定采取一系列练兵措施来提高喷工的技能,确保新方法的实施.小组首先对涂饰过程中"试枪,起枪,运枪,关枪"各环节动作反复操练得到一套保质保量保节省的喷涂操作法.并将新的喷涂操作法在现岗喷工中推广. 同时加以不断地修正与完善.小组还通过"告之,提醒, 示范,操练,检验".让每一位临时喷工都了解,熟悉, 掌握新的喷涂操作法.经过前三个步骤的练兵,小组总结出了新的"一遍底漆喷涂操作流程".在效果检验阶段里.小组做了多项检验.首先是产品质量检验,经过4个月的跟踪.涂膜厚度控制在18— 21m之间,都在质量标准范围内.一遍涂装后的直接喷涂速度控制在50秒时间内.仍然满足90秒/件的生产节拍. 同时.经过半年的跟踪,一遍涂装后的耗漆量最高值与平均值都得到明显下降,改进后的百件耗漆量最高值为5.3千克,平均值为45u4千克,超过了预定目标. 小组通过半年的统计,Qc活动节省一遍涂料1993 千克,节省率达251%,为年初车间设想的节省率达到 21%立下了汗马之劳.小组车间还连续制定了"喷枪口径改为0.8毫米"机壳一遍涂饰操作规范两个文件, 使QC成果以标准形式得以巩固.现在小组已经锁定了新的目标.继续持续改进.o。
质量管理工具在涂装质量改善中的实际应用

质量管理工具在涂装质量改善中的实际应用涂装质量是影响涂装产品质量和客户满意度的重要因素之一。
为了保障涂装质量和顾客满意度,企业需要引入一些有效的质量管理工具来改善涂装质量。
本文将介绍几个在涂装质量改善过程中常用的质量管理工具,并说明其实际应用。
1. PDCA循环PDCA循环是一种重要的质量管理工具,其含义是“计划—执行—检查—行动”。
在涂装质量改善过程中,企业可以通过PDCA循环实现质量管控和不断改善。
具体来说,可以采用以下步骤:(1)计划阶段:确定改善目标、制订涂装工艺和标准化流程。
(2)执行阶段:按照工艺和流程要求进行涂装,同时检查涂装过程的各个环节。
(3)检查阶段:对涂装产品进行全面、细致的检查,发现问题后进行分析。
(4)行动阶段:根据检查结果,制定纠正措施,继续循环,不断改善。
2. 5S管理5S是一种基于日本企业生产实践和管理方法的管理模式。
其中“5S”分别是整理、整顿、清洁、清理、素养。
在涂装质量改善中,企业可以通过5S管理来提高涂装工作台的整体管理水平,进而提高质量的稳定性和工艺的标准化水平,具体应用如下:(1)整理(Seiri):将涂装工作台必要的物品分类、整理、清理,避免过多物品混杂使用产生混乱和隐患。
(2)整顿(Seiton):排列工作台中的物品,使其按照需求进行排列,并设定明确的标记,有助于涂料工人更好地配合工作,提升生产效率。
(3)清洁(Seiso):定期清洗涂装工作台、工具和设备,保证工作环境的清洁、整洁,减少涂装品质污染的风险。
(4)清理(Seiketsu):保持工作环境的清洁、整洁,避免涂装过程中外在因素对涂装质量产生不良影响。
(5)素养(Shitsuke):促进企业文化以及员工素质的提升,让员工知道他们的工作对顾客的重要性,提高员工的责任心。
3. 流程图流程图是一种在涂装质量改善中广泛应用的质量管理工具。
在涂装生产中,流程图可以帮助企业分析生产流程中的工艺流转和控制点,准确找到问题的根源,有针对性地优化工艺流程和加强工艺监控。
涂装车间漆点防治措施

涂装车间的漆点防治措施可以从以下几个方面进行:
调整涂料配方:调整涂料的配方,降低漆膜表面的张力,提高涂层的表面张力,从而减少漆滴的形成。
改善涂料流平性:通过添加流平剂等助剂,改善涂料的流平性,使漆滴更容易沿涂层表面均匀摊开,减少漆点的形成。
提高涂装设备的清洁度:确保涂装设备清洁无污染,防止杂质和污染物进入涂料中,从而减少漆点的产生。
定期维护和清洗:定期对涂装设备进行清洗和维护,防止漆渣和污染物在设备内积累,从而减少漆点的形成。
加强生产管理:严格控制生产过程中的温度、湿度和空气清洁度等参数,确保生产环境的稳定和适宜,从而减少漆点的产生。
采取过滤措施:在涂料泵的出口处设置过滤器,对涂料进行过滤,去除其中的杂质和颗粒物,从而减少漆点的产生。
增加漆滴收集装置:在涂装设备的出口处增加漆滴收集装置,将飞溅的漆滴收集起来,减少漆滴对工件表面的污染。
加强员工培训:对涂装车间的员工进行培训,提高他们的技能和操作水平,使他们能够更好地掌握涂装设备的操作技巧和维护方法,从而减少漆点的产生。
综上所述,涂装车间的漆点防治措施需要从多个方面入手,包括调整涂料配方、改善涂料流平性、提高涂装设备的清洁度、定期维护和清洗、加强生产管理、采取过滤措施、增加漆滴收集装置以及加强员工培训等。
这些措施可以有效地减少涂装车间的漆点污染问题。
讲解减少涂装颗粒的控制措施

讲解减少涂装颗粒的控制措施颗粒在涂装中是最常见的涂膜缺陷之一,在任何一个涂装生产线都会不同程度的存在。
它是影响涂装一次交检合格率的最大的也是最难以根除的涂膜弊病。
因为颗粒造成的车体返修大大增加了涂装成本,经核算,每台车的中修费用100元左右,而一台车返大修,重新喷涂一遍面漆大约需要成本350元。
在外观上修理过的涂膜也略差于一次成型的涂膜。
在涂装生产中,涂膜颗粒弊病可以说是顽疾,几乎是无法杜绝的,只能是在生产过程中不断摸索,分析总结,采取相应的措施,使颗粒的产生降到最低,从而减少生产成本,提高生产效率。
Particles in the coating is one of the most common coating defects, in any coating production line will be the existence of different level. It is an especially affects the qualification rate of the largest and most difficult to eradicate the coating of ills. Because particles caused by the body repair greatly increase the painting cost, by the calculation, each vehicle repair costs about 100 yuan, while a car back to overhaul, spraying the paint again need to cost about 350 yuan. The appearance of repaired it does slightly less coating applied to the molding of a coating. In paintingproduction, coating grain ills can be said to be the ills, almost impossible to eliminate, can only fumble ceaselessly is in the process of production, analysis summary, take corresponding measures to make the generation of particles to a minimum, thus reducing the production cost, improve production efficiency.颗粒的定义the definition of particle涂膜上的突起物叫做颗粒,也称脏点,用目视或触摸可以辨别。
汽车主机厂涂装车间洁净度系统管理策略的探讨

汽车主机厂涂装车间洁净度系统管理策略的探讨作者:张治红宋淼李杰来源:《专用汽车》2021年第12期中图分类号:U468.2+1 文献标识码:A 文章编号:1004-0226(2021)12-0095-06在早前的文献中多以颗粒作为洁净度的代名词,其实从系统角度讲,颗粒问题只是洁净度管理中的一个突出方面。
漆面平整、光滑、无杂物是漆膜的关键特性和重要特性,控制漆面洁净度尤为重要。
漆面颗粒、纤维等污染物是油漆表面的主要缺陷。
也被视为涂装行业难以根治的顽症,一旦管理不当会造成后续处理工作量大、修复效率低等问题。
所以,洁净度管理工作是涂装车间的重要且必要的工作之一,同时又涵盖人、机、料、法、环、测等所有生产要素,具有管理范围广、投入成本高的特点。
1汽车主机厂涂装车间洁净度管理的特点1.1管理范围广洁净度受全生产要素以及现场管理的各个活动影响,涂装环节中的所有工序均与之相关,故洁净度管理范围极广,且管理难度较大。
1.2管理系统复杂因影响的工序及要素多,且生产要素之间存在较大的相互影响,因此洁净度管理工作系统复杂。
1.3投入成本高因为洁净度管理本身的特点,导致其管理成本高,而管理不良造成的处置后果、成本则更高。
2运用工具说明洁净度管理提升主要运用了“5M1E分析法”“PDCA循环”“5S管理”和“看板管理”四种现场管理工具。
2.1 5M1E分析法现场洁净度管理工作涉及到人、机、料、法、环、测各生产要素的影响,故应用5M1E要素分析法进行各要素分析,梳理各要素对洁净度管理的影响和改善空间、贡献。
应用5M1E分析法确定主要影响因素,为改善活动提供落脚点,同时为其他管理工具的使用提供基础支持。
各生产要素对洁净度的影响如表1所示。
2.2 PDCA循环洁净度管理是一项典型的持续改进的工作,需要持续性开展和提升,故应用PDCA循环迭代法对5M1E分析法梳理的生产要素进行改进和提升。
同时,为检查洁净度管理工作的效果,相关工作的绩效达成情况,需应用PDCA循环的方法分析结果、改进工作计划。
消除汽车车身中涂层颗粒缺陷的若干方法

消除汽车车身中涂层颗粒缺陷的若干方法牛新时【摘要】总结了工作人员、升降台升降速率、输送管路、中涂烘干炉、中涂漆内高沸点溶剂、电泳涂层研磨工具、台车等因素对中涂层颗粒缺陷的影响.明确了导致颗粒缺陷的主要原因是烘干炉出现焊缝缝隙以及台车被污染.给出了相应的解决措施,有效地降低了颗粒缺陷的发生.%The effects of worker,lifting speed of lifting platform,delivery line,midcoat furnace,high-boiling-point solvent in midcoat,grinding tool for electrophoretic coating and skid conveyor on particle defects in midcoat of car body were summarized.The causes for particle defects mainly includes cracking on weld seam of the furnace and contamination of skid conveyor.Some countermeasures weregiven,effectively reducing the appearance of particle defects.【期刊名称】《电镀与涂饰》【年(卷),期】2017(036)010【总页数】4页(P538-541)【关键词】车身;涂装;中涂层;颗粒缺陷;对策【作者】牛新时【作者单位】郑州日产汽车有限公司,河南郑州451450【正文语种】中文【中图分类】TQ639.8Author’s address:Zhengzhou N issan Motor Co., Ltd., Zhengzhou 451450, China某公司汽车车身涂装一车间在生产过程中,发现中涂层漆膜的颗粒缺陷较多,这不仅极大地增加了后续研磨工序的工作量,而且缺陷点经常遗留到面漆涂层(见图1),给该车间的一次合格率带来很大影响,造成生产效率低下,成本增多。
改进喷漆质量降成本QC展示

八.巩固措施
1. 持续创新,不满足于现有的成绩,向组员宣贯“创新只是零起 点,创新永无止境”的理念,引导班组员工,做一个学习型、创新型 的劳动者。
2. 继续对已实施的创新项目进行追踪、验证,收集数据,拓实创新 成果。
3. 对班组各项成本,继续精细制控,进行深度挖潜,拓展降成本空 间。
九. 体会和下一步打算
体积大,没用的面积多,沾漆多,易结厚,不方便 喷漆,损耗油漆较大 目前的油漆存储房较小,不方便喷漆两个组的责任 分清 有待在实践中不断验证和完善
结论
不是要因 不是要因 不是要因 不是要因 不是要因 是要因 是要因 是要因 是要因 不是要因 不是要因
小组成员
五.对策表
要因
现状
目标
措施
责任人
时间
1.创新 意识不 强
年龄
37 24 23 33 25 33 32 25
班组成员
性别
文化程度
职务
男
中技
组长
男
中技
男
中技
男
中技
男
大专
男
高中
男
中技
男
大专
接 受 QC 教 育课时
100% 100% 100% 100% 100% 100% 100% 100%
二. 选题理由
油漆成本耗用大 持续推进降低成本工作 持续创新 提高员工成本意识
谢谢
(2)工段推行成本预算方法,要求我小组的油漆平均成本 控制在≤20元/台,比06年的油漆平均成本下降7.7%。
(3)我们班组制定了更高的制降要求,要求单台机的油漆 耗用≤19.50元/台,比06年的单台耗用下降10%。
四. 寻找要因
1、寻找要因
涂装新车间质量提升措施

涂装新车间车厢表面质量提升措施为了提升新车间车厢表面质量达到要求,有效控制车厢前处理上线前的洁净,保证前处理槽液参数稳定和洁净度达到要求,同时固化前处理操作工艺,经过车间现场操作和对比试验,现控制措施如下:一、原白坯车厢擦斗工工作位置进行调整,改为白坯车厢上线前擦试处理,保证车厢表面不能有明显颗粒物和明显的油污。
20日白班开始实施。
(责任人:杜团结、殷国成)二、车厢上挂工吹水时必须站在焊接的台价上对车厢上表面进行吹水,保证车厢上表面无明显铁屑或其它颗粒物。
实施时间19日白班(责任人:杜团结、殷国成)三、电泳前吹水工重点对车厢上表面进行吹水,保证车厢电泳前车厢表面无明显颗粒物。
正在实施(责任人:杜团结、殷国成)四、电泳后吹水时原车厢吊挂时的上表面吹水,保证车厢表面无明显颗粒或用手摸无明显挂手感。
正在实施(责任人:杜团结、殷国成)五、前处理倒槽改变为每晚倒一个水槽,倒槽时要求把槽底进行彻底清理,第二天早上检查池底不能有明显的污物或絮状物沉淀。
19日晚开始实施(责任人:庞昆源)六、电泳前喷淋水泵进水口用过滤网进行防护,要求白班中午进行倒槽,夜班下班后进行倒槽,倒槽标准要求池底不能圾明显污物,并且要求倒槽时对水泵进水口的过滤网进行更换。
21日开始实施。
(责任人:庞昆源、王亚新)七、电泳后喷淋水泵用过滤网进行防护,每天晚上下班后倒槽一次,倒槽标准池底不能圾明显污物,并且要求倒槽时对水泵进水口的过滤网进行更换。
21日开始实施。
(责任人:庞昆源)八、电泳槽液内有电泳漆絮状物,倒槽时要求用过滤网进行过滤,后期按工艺要求进行超滤维护。
确定在五一倒槽。
(责任人:庞昆源、王亚新)九、达不到要求考核50元。
涂装车间2014年4月19日。
涂装车间漆渣收集方案

涂装车间漆渣收集方案涂装车间在进行喷涂作业时,会产生大量的漆渣,如果不及时清理和处理,不仅会影响车间的工作环境和生产效率,还可能对环境造成污染。
因此,建立一个有效的漆渣收集方案对于涂装车间的管理至关重要。
首先,应该配备专业的漆渣收集设备。
可以安装漆渣收集网,在喷涂设备下方设置一个可拆卸的容器,网孔尺寸要适中,能够过滤掉大部分的漆渣,而不会影响喷涂的正常进行。
同时,要定期清理和更换收集容器,避免漆渣积聚过多。
其次,为了提高漆渣的收集效率,可以在车间的喷涂区域周围设置防护墙。
防护墙的高度要能够有效地阻挡漆渣的飞溅和扩散,避免漆渣飘散到车间的其他区域。
此外,还可以在喷涂区域的天花板上安装漆渣收集板,能够将漆渣顺利引导到收集容器中。
另外,为了避免漆渣的二次扩散和污染环境,应该定期对收集容器进行清理和处理。
清理时,可以将漆渣倒入专门的漆渣储存桶中,再进行后续的处理工作。
可以将漆渣进行分类,对于还能使用的漆渣,可以进行再利用,减少浪费。
而对于无法再利用的漆渣,可以进行专门的处理,避免对环境造成污染。
如可以交由专业的废物处理公司进行处理,确保其经过合理的处理后对环境影响最小化。
最后,还应该加强对员工的培训和管理,确保他们理解漆渣收集的重要性,并能正确使用漆渣收集设备。
定期检查和维护设备,确保其正常运行和高效收集漆渣。
并建立相应的考核制度,通过对员工的考核来促使其重视漆渣收集工作,提高工作效率和质量。
总之,建立一个有效的漆渣收集方案对涂装车间来说至关重要。
通过配备专业的收集设备,并采取适当的防护措施和漆渣处理措施,能够高效地收集和处理漆渣,保持车间的清洁和生产环境的良好,并确保对环境造成的污染最小化。
+根据车间的实际情况,灵活调整和改进漆渣收集方案,以满足涂装车间的需求和要求。
喷漆车间环保节能措施

喷漆车间环保节能措施喷漆车间是危险品存储和使用的场所,同时也是高能耗的工作区域,如何在保证生产质量和效率的情况下,采取有效的环保节能措施,成为了这些工厂所必须思考和解决的问题。
环保措施1. 废液回收喷漆车间中,废液是一种常见的污染源,如面漆喷涂过程中产生的废漆、废溶剂等物质。
收集这些废液,并对其进行处理和再利用,是喷漆车间环保的一项重要措施。
一些车间采用的废漆回收技术有:•冷凝回收法:将废漆通过冷凝器冷却,固化成粉末或颗粒状,然后进行处理和再利用。
•熔融回收法:通过高温加热,将废漆熔化后在熔化容器内进行处理,类似于再生塑料的处理方法。
•力学回收法:通过过滤或离心分离等力学手段,将废漆分离成不同组分进行处理和利用。
2. VOCs治理挥发性有机物(Volatile Organic Compounds,VOCs)是环保中的另一个难题,因为VOCs易挥发和扩散,对环境和人体健康的危害极大。
喷漆车间内的喷漆、溶剂等化学物质都有可能产生VOCs。
车间针对VOCs的治理措施一般有三种:•生物滤池:利用生物菌群将VOCs进行吸附、分解。
•吸附剂:通过物理吸附,把VOCs吸附在吸附剂表面,从而达到去除的效果。
•燃烧: 通过加热VOCs达到燃烧的状态,释放二氧化碳和水,以达到去除VOCs的效果。
3. 环保涂料在喷漆车间,选择环保涂料是防止环境污染的一种方法。
环保涂料通常指含有低挥发性有机化合物的涂料或是微米级别的纳米材料成分涂料。
此外,车间还可以通过使用电泳涂装,减少漆料浪费和避免空气污染。
节能措施1. 换气和回风系统喷漆车间中的气流和换气是影响车间工作环境及工作效率的关键因素。
车间需要设置好换气和回风系统,保证新鲜空气和老空气的流通,并达到有效循环和使用。
在系统设计上,需要体现节能特点。
在换气系统的设计过程中,应当考虑如何减少换气时热能或冷能损失的问题。
在回风系统的设计过程中,应避免冷热气流的混合和分层,以达到节能效果。
- 1、下载文档前请自行甄别文档内容的完整性,平台不提供额外的编辑、内容补充、找答案等附加服务。
- 2、"仅部分预览"的文档,不可在线预览部分如存在完整性等问题,可反馈申请退款(可完整预览的文档不适用该条件!)。
- 3、如文档侵犯您的权益,请联系客服反馈,我们会尽快为您处理(人工客服工作时间:9:00-18:30)。
3.在涂装调漆间内分厂将不同厂家的油漆定置定位,不混放在一起。 避免油漆稀释剂使用错误。
4.分厂每次25号的盘点中均对过期油漆进行排查退库。不使用不合 格油漆。
5.保证对每次使用的粘性砂布的质量把关,使用时及时翻面保证清 洁度。
分厂每天早上过来 先将压机内的水分
排一下
分厂每周对连接喷 漆室的油水分离器
排油
在喷枪的接口处接上铜网,阻 止油漆里的漆渣污染
料 颜料分散不均 、凝聚
颜料中混入杂 质
稀释剂使用不 当
颜料变质
粘性砂布脏, 掉纤维
点补和底色不 容
料的因素颗粒解决
5.对策讨论及实施
针对油漆材料可能引发的面漆颗粒现象:
1.分厂要求调漆工在每次调漆时先将漆桶倒置,然后在分厂要求调 漆工在调漆时将油漆充分搅拌。
环 空气不洁净 温度低
湿度大
过滤棉掉纤维 喷漆室较脏 喷漆室内负压 致空气进入
环境因素颗粒解决
5.对策讨论及实施
分厂要求喷漆工在休息 时进入喷漆线外侧的风 淋间通道休息,同时要 求员工必须不能坐在地 上,同时配上鞋柜,晾 衣架等,减少将颗粒带 入喷漆室。
喷漆工之前休息是在擦 净室处面,而且喷漆工 不爱惜卫生经常坐在地 上,将颗粒 带入喷漆室
3.目标定
有效的减少面漆颗粒 ,提升分厂的一次交 检合格率
增加分厂交检线的交检 效率,缩短交检时间
4.要因解析
5.对策讨论及实施
对策讨论及实施 为此分厂将从人、机、料、法、环五个方面对面漆 颗粒进行整改,以降低面漆颗粒现象。
项目 1 2
人 车身未擦净 员工手摸
吹灰不彻底 3
喷涂手法不对
4
,涂料流平差
涂装分厂目前本色系列油 漆在喷涂前都要进行过滤
将喷枪喷幅调小
将喷枪出漆量调小
将分厂员工的喷枪叶幅下调,出漆量下调
环 空气不洁净 温度低
湿度大
过滤棉掉纤维 喷漆室较脏 喷漆室内负压 致空气进入
环境因素颗粒解决
5.对策讨论及实施
将烘干炉出口 在不上班时将 卷帘门关闭, 减少颗粒进入
面漆擦净室门 口也增加卷帘 门,在不生产 时也将其用卷 帘门关闭,减 少灰尘进入
减少面漆颗粒
1.选题理由 2.现状把握
目录3.目标设定
4.要因解析
5.对策讨论及实施 6.效果确认
7.巩固措施
1.选题理由
1
减少返工现象,提 升涂装分厂一次交 检合格率
2
提升涂装分厂面漆 品质,增加车身表 面平整度
3
推进分厂面漆工序 标准化作业,加强 员工工艺纪律执行
2.现状把握
2012年1-12月份涂装分厂因颗粒导致的面漆返工 月份 1月 2月 3月 4月 5月 6月 7月 8月 9月 10月 11月 12月 返工台数 5 0 5 0 8 15 2 0 4 15 17 21
将坏掉的喷枪用气管接在擦净 室,用于吹车身缝隙处的细灰
机的因素颗粒解决
5.对策讨论及实施
机
喷漆室送风系 统不清洁
烘干炉过滤袋 及风道未清洁
喷枪内带来的 涂料渣
压缩空气不洁 净、有水分
要求保洁公司定时对送风空调压力表进 行检查,压差大于标准后及时告知分厂
分厂要求保洁公司在分厂休息时,都要对烘干炉地面进行打扫,每同对 烘干炉内壁板进行清扫,待烘干炉上压力表压差过大时及时通知分厂
6.点补和底色不容的时候,由分厂内部进行统一协调,保证将点补 晾干后再晒底色漆,同时增加点补中涂的挥发速度。
法
油漆未过滤
油漆搅拌不均
出漆量大,喷 幅大,油漆雾 化不良
法的因素颗粒解决
5.对策讨论及实施
分厂要求调漆工在每次调漆时均使用 搅漆棒从底部进行搅拌,保证将油漆 搅匀,同时分厂面漆员工对喷漆室内 的油漆进行确认。
吹灰不彻底
对车身上灰吹不掉的用砂纸细磨
3
擦
喷涂手法不对
净
4
,涂料流平差
处
的
细
砂
纸
1.在两道漆之间保证1分钟左右的流平时间。
2.喷涂时严格按照先上后下、先里后外,先棱后面的喷
漆顺序,增加车身A级面的流平时间。
3.要求员工将喷漆的距离适量拉大,保证油漆挥发速度。
4.将底色漆的油漆粘度适量下调,增加流平性。
环 空气不洁净 温度低
湿度大
过滤棉掉纤维 喷漆室较脏 喷漆室内负压 致空气进入
环境因素颗粒解决
5.对策讨论及实施
12月初时,喷漆室内温度过低,湿度大,而在喷涂T330车身时 点补与底色又有些不容,金属底色漆里面的金属粉发生絮凝,在 车身表面形成了颗粒,严重影响了车身的正常交检。针对此种情 况,分厂及时将喷漆室内的面漆段升温设施开启,杜绝了此类现 象。
车门门缝处
人为因素颗粒解决
5.对策讨论及实施
要求水磨员工在车身上楼时先用粘性砂布进行擦拭,在进入面漆 擦净室内再过细擦灰,同时对一些边角部位重点关注,如:
顶盖流水槽
前围搭接缝
前围流水槽
门槛处
顶盖R角处
车门上边处
人为因素颗粒解决
5.对策讨论及实施
项目 1 2
人 车身未擦净 员工手摸
坚决杜绝车身进入喷漆室员工触摸行为
环境因素颗粒解决
5.对策讨论及实施
环 空气不洁净 温度低
湿度大
过滤棉掉纤维 喷漆室较脏 喷漆室内负压 致空气进入
将喷漆工的喷漆服外现增 加一套新式防静电喷漆服, 减少老式喷漆上掉纤维的
现象
将面漆工序的手套由原先的毛线手套 更换为新式细线手套
将分厂面漆线的玻璃门配上铁锁封闭 起来,减少人员随意进入而带入颗粒
12月12日有22台T330顶车身因面漆出来颗粒较多而 只对办理让步。12月13日又出现大面积的颗粒现象,对 车身交检带来较多麻烦。
返漆成本:1.辅料:6张320#砂纸+2张水砂纸+3kg油漆+2张粘性砂布 =6*0.9+2*0.6+3*30+2*0.6≈98元/台.
2.能耗:返漆一台至少需要时间为20min(而T330车身需1小时左右) 面漆喷漆室功率:(11+90*2+132+110*2+90*2+30*4)=843kw 面漆烘干炉:(37*2+11+3+11)=99kw; 费用为:942kw*0.85/3=267元(电费为0.85元/度,不算天然气费用) 即返漆一台车生产成本约为365元。
喷漆室内天然气加 热开启
环 空气不洁净 温度低
湿度大
过滤棉掉纤维 喷漆室较脏 喷漆室内负压 致空气进入
环境因素颗粒解决
5.对策讨论及实施
分厂在领取过滤棉时由分厂领料人员严格对粘性砂布的质量进行确认, 确保粘性砂布的质量,避免在2011年11月份出现的过滤棉大量掉纤维 事件,减少因此带来的面漆颗粒。