Chapter 11 金属的化学热处理
金属热处理知识课件

历史与发展
历史
金属热处理起源于古代,人类在长期实践中逐渐摸索出了金 属材料的加热、冷却和改变性能的方法。随着工业革命的发 展,金属热处理逐渐成为一门独立的学科,并得到了广泛的 应用。
发展
现代金属热处理技术不断发展,新的工艺和方法不断涌现, 如真空热处理、激光热处理、化学热处理等。同时,计算机 技术和自动化技术的应用也推动了金属热处理技术的进步, 提高了生产效率和产品质量。
PART 06
金属热处理安全与环保
安全操作规程
操作人员需经过专业培训 ,熟悉热处理设备及工艺 流程,掌握安全操作技能 。
设备运行前应检查电源、 水源、热源等是否正常, 确保设备处于良好状态。
ABCD
操作过程中应穿戴防护服 、手套、鞋帽等个人防护 用品,防止烫伤、触电等 事故发生。
操作过程中应保持注意力 集中,随时观察设备运行 情况,发现异常及时处理 。
节能减排技术
01
采用新型的热处理技术和设备, 提高能源利用效率和热处理效果 。
02
对现有设备进行技术改造和升级 ,降低能耗和减少污染物排放。
开发和应用新型的环保材料和工 艺,替代传统的高污染材料和工 艺。
03
加强科研和创新能力,推动热处 理技术的进步和创新,为节能减
排提供技术支持和保障。
04
2023 WORK SUMMARY
THANKS
感谢观看
REPORTING
测温仪
用于测量金属件的温度,确保热处理工艺的 准确性。
热处理吊具
用于吊装金属件,便于在加热和冷却设备中 移动。
热处理辅助材料
如保护气氛、脱氧剂等,用于改善热处理效 果和保护金属件。
PART 05
金属热处理应用
金属热处理方法及工艺介绍
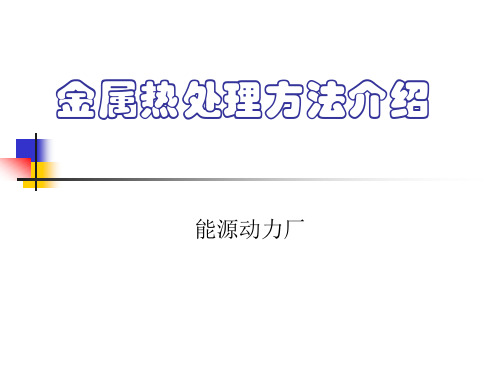
金属热处理方法介绍
表面热处理是只加热工件表层,以改变其表层力学性能的金属热 处理工艺。为了只加热工件表层而不使过多的热量传入工件内部, 使用的热源须具有高的能量密度,即在单位面积的工件上给予较 大的热能,使工件表层或局部能短时或瞬时达到高温。表面热处 理的主要方法,有激光热处理、火焰淬火和感应加热热处理,常 用的热源有氧乙炔或氧丙烷等火焰、感应电流、激光和电子束等。
淬火→将工件加热保温后,在水、油或其它无机盐、有机水溶 液等淬冷介质中快速冷却。淬火后钢件变硬,但同时变脆。为了 降低钢件的脆性,将淬火后的钢件在高于室温而低于710℃的某
金属热处理方法介绍
一适当温度进行长时间的保温,再进行冷却,这种工艺称为回火。 退火、正火、淬火、回火是整体热处理中的“四把火”,其中的 淬火与回火关系密切,常常配合使用,缺一不可。
金属热处理方法介绍
另外转变需要一定的时间,因此当金属工件表面达到要求的加热 温度时,还须在此温度保持一定时间,使内外温度一致,使显微 组织转变完全,这段时间称为保温时间。采用高能密度加热和表 面热处理时,加热速度极快,一般就没有保温时间或保温时间很 短,而化学热处理的保温时间往往较长。
冷却也是热处理工艺过程中不可缺少的步骤,冷却方法因工艺 不同而不同,主要是控制冷却速度。一般退火的冷却速度最慢, 正火的冷却速度较快,淬火的冷却速度更快。但还因钢种不同而 有不同的要求,例如空硬钢就可以用正火一样的冷却速度进行淬 硬。
金属热处理原理及工艺总结-整理版

金属热处理原理及工艺总结-整理版引言金属热处理是一种通过改变金属内部结构来提高其性能的工艺。
它广泛应用于机械制造、航空航天、汽车工业等领域。
本文档旨在总结金属热处理的基本原理、常见工艺以及实际应用。
金属热处理的基本原理金属晶体结构金属晶体是由金属原子按一定规则排列形成的。
金属的物理性能,如硬度、韧性等,与其晶体结构密切相关。
相变理论金属在不同的温度下会发生相变,如奥氏体化、珠光体化等。
通过控制加热和冷却过程,可以改变金属的相组成,从而改善其性能。
扩散原理金属热处理过程中,原子的扩散是改善金属性能的关键。
通过高温加热,原子获得足够的能量进行扩散,实现组织结构的优化。
常见的金属热处理工艺退火退火是将金属加热到一定温度,保持一定时间后缓慢冷却的过程。
目的是降低硬度,消除内应力,提高塑性。
正火正火是将金属加热到一定温度后,保持一段时间,然后以较快速度冷却的过程。
它能改善金属的组织结构,提高硬度和强度。
淬火淬火是将金属加热到奥氏体化温度后迅速冷却,形成马氏体或其他硬化组织,显著提高金属的硬度和强度。
回火回火是淬火后的金属再次加热到一定温度,保持一段时间后冷却的过程。
它用于降低淬火后的脆性,提高韧性和塑性。
调质调质是将金属加热到奥氏体化温度后淬火,再进行高温回火的过程。
它综合了淬火和回火的优点,使金属具有较好的综合机械性能。
金属热处理工艺的实际应用钢铁材料的热处理钢铁材料是金属热处理的主要对象。
通过不同的热处理工艺,可以生产出不同性能的钢材,满足各种工程需求。
非铁金属材料的热处理非铁金属如铝合金、钛合金等,也可以通过热处理改善性能。
例如,铝合金通过固溶处理和时效处理提高强度。
表面热处理表面热处理如渗碳、氮化等,可以在金属表面形成一层硬度高、耐磨性好的化合物层,提高零件的使用寿命。
控制气氛热处理在控制气氛中进行热处理,可以防止金属氧化和脱碳,保持金属表面光洁,提高热处理质量。
结语金属热处理是材料科学中的一个重要分支。
金属热处理的操作方法

金属热处理的操作方法金属热处理是通过改变金属的晶体结构和组织来改善金属材料的力学性能和其他性能的一种加工方法。
它主要包括退火、正火、淬火、回火以及固溶处理等工艺。
下面我将详细介绍金属热处理的操作方法。
1. 退火退火是通过加热金属至一定温度,持温一段时间,然后缓慢冷却至室温的过程。
退火的目的是消除金属内部的应力,改善金属材料的塑性和可加工性。
具体的操作步骤如下:1) 清洗金属表面,除去污垢和油脂。
2) 将金属放入退火炉中,提高温度至退火温度,一般退火温度为材料的临界温度。
3) 保温时间受材料的厚度和结构复杂程度等因素影响,一般为0.5-4小时。
4) 缓慢冷却至室温,可用炉内冷却或空气冷却等方法。
2. 正火正火是通过加热金属至临界温度,保温一段时间后,以水或油冷却的过程。
正火的目的是使金属材料具备一定的硬度和强度。
具体操作步骤如下:1) 清洗金属表面,除去油脂等污垢。
2) 将金属放入正火炉中,加热至临界温度,保温时间一般为30分钟至1小时。
3) 以快速速度将金属从炉中取出,放入水或油中进行冷却。
3. 淬火淬火是将金属材料加热到临界温度以上并保温一段时间,然后迅速冷却以形成马氏体的过程。
通过淬火,可以使金属材料具备高硬度和较高的抗拉强度。
具体操作步骤如下:1) 清洗金属表面,除去污垢和油脂。
2) 将金属放入淬火炉中,加热至临界温度,保温时间一般为15-30分钟。
3) 迅速将金属取出,放入冷却介质中进行淬火。
常用的冷却介质包括水、油和盐溶液等。
4. 回火回火是将已经淬火的金属材料重新加热至介于临界温度和淬火温度之间的温度区域,然后以适当速度冷却的过程。
回火的目的是消除淬火产生的内部应力,提高材料的韧性和可塑性。
具体操作步骤如下:1) 清洗金属表面,除去污垢和油脂。
2) 将金属放入回火炉中,加热至回火温度,保温时间一般为1-2小时。
3) 以适当速度冷却至室温,可用炉内冷却或空气冷却等方法。
5. 固溶处理固溶处理是将合金金属加热至固溶温度以上,然后保温一段时间,最后迅速冷却的过程。
金属热处理方法及工艺介绍优选全文
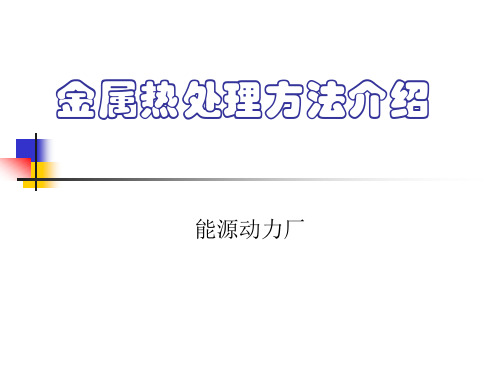
能源动力厂
金属热处理方法介绍
金属热处理是将金属工件放在一定的介质中加热到适宜的温度, 并在此温度中保持一定时间后,又以不同速度冷却的一种工艺方 法。
金属热处理是机械制造中的重要工艺之一,与其它加工工艺相 比,热处理一般不改变工件的形状和整体的化学成分,而是通过 改变工件内部的显微组织,或改变工件表面的化学成分,赋予或 改善工件的使用性能。其特点是改善工件的内在质量,而这一般 不是肉眼所能看到的。
为使金属工件具有所需要的力学性能、物理性能和化学性能, 除合理选用材料和各种成形工艺外,热处理工艺往往是必不可少 的。钢铁是机械工业中应用最广的材料,钢铁显微组织复杂,可 以通过热处理予以控制,所以钢铁的热处理是金属热处理的主要 内容。另外,铝、铜、镁、钛等及其合金也都可以通过热处理改 变其力学、物理和化学性能,以获得不同的使用性能。
金属热处理工艺大体可分为整体热处理、表面热处理、局部热 处理和化学热处理等。根据加热介质、加热温度和冷却方法的不 同,每一大类又可区分为若干不同的热处理工艺。同一种金属采 用不同的热处理工艺,可获得不同的组织,从而具有不同的性能。
金属热处理方法介绍
整体热处理是对工件整体加热,然后以适当的速度冷却,以改变 其整体力学性能的金属热处理工艺。钢铁整体热处理大致有退火、 正火、淬火和回火四种基本工艺。
金属热处理方法介绍
热处理是机械零件和工模具制造过程中的重要工序之一。大体来 说,它可以保证和提高工件的各种性能 ,如耐磨、耐腐蚀等。还 可以改善毛坯的组织和应力状态,以利于进行各种冷、热加工。 例如白口铸铁经过长时间退火处理可以获得可锻铸铁,提高塑性 ; 齿轮采用正确的热处理工艺,使用寿命可以比不经热处理的齿轮 成倍或几十倍地提高;另外,价廉的碳钢通过渗入某些合金元素 就具有某些价昂的合金钢性能,可以代替某些耐热钢、不锈钢; 工模具则几乎全部需要经过热处理方可使用。
金属热处理ppt课件

碳钢分类
按钢中含碳量多少分: 低碳钢 Wc < 0.25% 中碳钢 Wc = 0.25%—0.6% 高碳钢 Wc > 0.6%
低碳钢
特点: 塑性好、韧性好、硬度强度低〔软刚〕、耐 磨性差。
热处置: 通常情况下将其进展渗碳,然后淬火,再低 温回火后运用。
中碳钢
特点: 热加工及切削性能良好,强度硬度比低碳钢 高,韧性塑性低于低碳钢,焊接性能较差。
金属热处理
金属热处置:是将金属工件放在一定的介质中加热到适宜的 温度,并在此温度中坚持一定时间后,又以不同速度冷却的一种工艺。
金属热处置的意义:是经过改动工件内部的显微组织,或改动工 件外表的化学成分,赋予或改善工件的运用性能。其特点是改善工件 的内在质量,而这普通不是肉眼所能看到的。
金属热处置过程:包括加热、保温、冷却三个过程,有时只需加 热和冷却两个过程。
按用途分类 按钢的用途可分为:构造钢、工具钢和特 殊性能钢
构造钢又分为:工程构件用钢和机器零件 用
工具钢分为:刃具钢、量具钢、模具钢
特殊性能钢分为:不锈钢、耐热钢等
按金相组织分类
按退火态的金相组织可分为:亚共析钢、 共析钢、过共析钢三种。
按正火态的金相组织可分为:珠光体钢、 贝氏体钢、马氏体钢、奥氏体钢等四种。
弹簧、钢丝 绳等
连杆、齿轮 及轴类
58~65 35~50 20~30
热处置中的“四把火〞
热处理方式
定义
作用
退火 正火 淬火 回火
将金属构件加热到高于或低于 临界点,保持一定时间,随后
缓慢冷却。
降低硬度,改善切削加工性;消除残余应 力,稳定尺寸,减少变形与裂纹倾向使金
属内部组织达到或接近平衡状态。
金属热处理知识课件
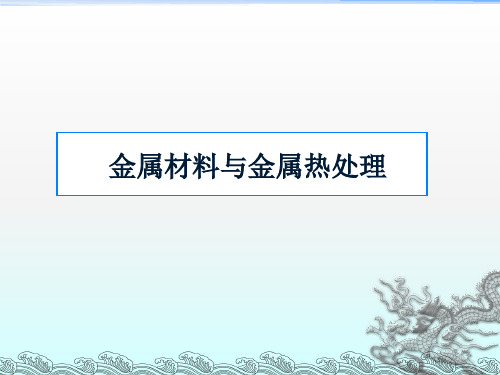
1
热处理是指通过对工件的加热、保温和冷却, 使 金属或合金的组织结构发生变化, 从而获得预期的性 能(如机械性能、加工性能、物理性能和化学性能等) 的操作工艺称为热处理。
工件热处理的目的是通过热处理这一重要手 段, 来改变(或改善)工件内部组织结构, 从而获得所 需要的性能并提高工件的使用寿命。
●去应力退火 将工件加热到 Ac1以下某一温度,保温后随炉冷却的热处理 工艺称为去应力退火。
目的: 消除铸、锻、焊的内应力。
11
●正火是将钢加热到 Ac3或 Accm以上30~50℃, 保温后 空气中冷却的热处理工艺。
●正火具有以下几方面的应用: ① 含碳量≤0.25%经正火后硬度提高,改善了切削加工性能。 ② 消除过共析钢中的二次渗碳体。 ③ 作为普通结构零件的最终热处理。
7
3 钢的热处理基本工艺及应用
四把火: 退火、正火、淬火、回火 1) 钢的退火与正火
● 退火与正火的目的 ① 调整硬度以便进行切削加工 ② 消除残余应力 ③ 细化晶粒, 改善组织 ④ 为最终热处理做好组织上的准备
8
●退火: 将钢加热、保温,然后缓慢冷却的热处理工艺。 退火工艺可分为完全退火、等温退火、球化退火、去应力
① 马氏体分解: 主要发生在 100~200℃, 马氏体中的碳 以ε碳化物(FexC)的形式析 出,析出的碳化物以极小片状 分布在马氏体基体上,这种组 织称为回火马氏体,用Байду номын сангаасM回” 表示。如图所示。
图12 回火马氏体
25
② 残余奥氏体分解 主要发生在200~300℃, 残余奥 氏体分解 为ε碳化物和过饱和α, 但组织仍是回火马 氏体。
获得均匀细小的奥氏体。 如图所示,一般淬火温度 在临界点以上。
金属热处理

1.Hall-Petch公式其中σ-材料本身的内摩擦应力,d-晶粒直径,k为相邻晶粒位向差对位错运动的影响系数,即俗称的晶界阻力;反映了材料的屈服极限与晶粒大小的关系。
2.加工硬化金属材料在再结晶温度以下塑性变形时强度和硬度升高,而塑性和韧性降低的现象。
3.回复冷塑性变形的金属在加热时,在光学显微组织发生改变前(即在再结晶晶粒形成前)所产生的某些亚结构和性能的变化过程。
4.再结晶冷变形后的金属加热到一定温度或保温足够的时间后,在原来的变形组织中产生了无畸变的新晶粒,位错密度显著降低,性能也发生显著变化,并恢复到冷变形前的水平的过程。
5.动态回复金属在热变形中发生的一种软化过程,是通过位错的攀移、交滑移和位错从结点的脱钉来实现的。
6.动态再结晶金属在热变形中发生的一种软化过程,通过再结晶的晶核形成和长大来完成的。
7.固溶强化融入固溶体中的溶质原子造成晶格畸变,晶格畸变增大了位错运动的阻力,使滑移难以进行,从而使合金固溶体的强度与硬度增加。
这种通过融入某种溶质元素来形成固溶体而使金属强化的现象称为固溶强化。
8.时效处理时效处理是将淬火后的金属工件置于室温或较高温度下保持适当时间,以提高金属强度的金属热处理工艺。
9.沉淀强化金属在过饱和固溶体中溶质原子偏聚和由之脱溶出微粒弥散分布于基体中而导致硬化的一种热处理工艺。
10. 沸腾钢炼钢时仅加入锰铁进行脱氧,脱氧不完全。
这种钢液铸锭时,有大量的一氧化碳气体逸出,钢液呈沸腾状,故称为沸腾钢(百度)11. 半镇静钢脱氧程度介于沸腾钢和镇静钢之间,故称为半镇静钢(百度)12. 镇静钢炼钢时采用锰铁、硅铁和铝锭等作为脱氧剂,脱氧完全。
这种钢液铸锭时能平静地充满锭模并冷却凝固,故称为镇静钢(百度)13. 淬火时效低碳钢加热至接近Ac1温度淬火,于室温放置或稍经加热后,其强度提高而塑性韧性下降的现象。
14. 应变时效金属变形后,于室温经长时间停留。
金属的屈服点应力提高,并在拉伸试验中出现屈服平台的现象15. 双相钢双相钢又称复相钢。
金属热处理教案
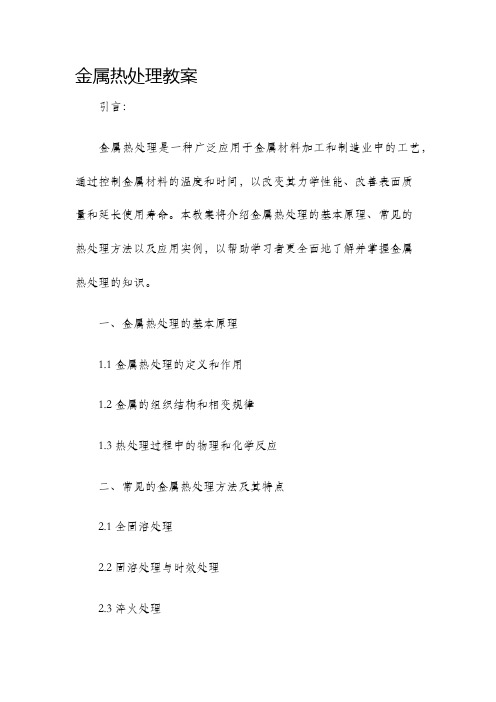
金属热处理教案
引言:
金属热处理是一种广泛应用于金属材料加工和制造业中的工艺,通过控制金属材料的温度和时间,以改变其力学性能、改善表面质
量和延长使用寿命。
本教案将介绍金属热处理的基本原理、常见的
热处理方法以及应用实例,以帮助学习者更全面地了解并掌握金属
热处理的知识。
一、金属热处理的基本原理
1.1 金属热处理的定义和作用
1.2 金属的组织结构和相变规律
1.3 热处理过程中的物理和化学反应
二、常见的金属热处理方法及其特点
2.1 全固溶处理
2.2 固溶处理与时效处理
2.3 淬火处理
2.4 空气冷却处理
2.5 淬火与回火处理
三、金属热处理技术的应用实例
3.1 钢材的热处理技术
3.2 铝合金的热处理技术
3.3 铜合金的热处理技术
3.4 不锈钢的热处理技术
四、金属热处理的设备和工艺控制
4.1 热处理设备的分类和特点
4.2 热处理工艺参数的选择和控制
4.3 高温环境下的安全防护
五、金属热处理技术的发展趋势
5.1 绿色环保金属热处理技术
5.2 智能化金属热处理设备
5.3 新型金属热处理材料的研发
结语:
金属热处理是提高金属材料性能与质量的重要工艺之一,它在现代制造业中具有广泛的应用。
通过本教案的学习,学习者将对金属热处理的基本原理、常见方法和应用实例有更深入的认识,为未来的实践应用奠定基础。
在不断发展的制造业中,金属热处理技术也将持续创新和改进,以满足不同行业的需求,提高产品质量和品牌竞争力。
- 1、下载文档前请自行甄别文档内容的完整性,平台不提供额外的编辑、内容补充、找答案等附加服务。
- 2、"仅部分预览"的文档,不可在线预览部分如存在完整性等问题,可反馈申请退款(可完整预览的文档不适用该条件!)。
- 3、如文档侵犯您的权益,请联系客服反馈,我们会尽快为您处理(人工客服工作时间:9:00-18:30)。
例如渗C的相界面反应
主要过程
活性碳原子
钢表面渗碳碳原子的来源
气体渗氮时,通入氨气与钢表面产生相界面反应
活性氮原子
渗入钢件表面
化学热处理有时只有扩散过程,例如热浸 法渗金属时,把工件浸在熔融的金属中, 直接吸附金属原子并向内部扩散
二、化学热处理渗剂及其在化学热处理过程中的化学反应机制 渗剂:欲渗元素的物质 + 一定比例的催渗剂 渗剂的活性:在相界面反应中易于分解出被渗元素原子的能力 例如普通气体渗氮不能用N2作为渗氮剂(在普通渗氮温度N2不能 分解出活性氮原子) 催化剂是促进含有被渗元素的物质分解或产生出活性原子的物质,它仅 是一种中间介质,本身不产生被渗无素的活性原子
例如低碳钢:表面渗碳 + 淬火 工件表面具有高HRC、高耐磨性 心部具有良好塑性和韧性
高速钢刀具:热处理后,再进行软氮化或离子渗氮,可进一步↑耐磨性 和抗腐蚀性能→↑刀具使用寿命
§11.1 化学热处理基本原理
一、化学热处理的基本过程
交叉进行
渗剂中的反应+扩散、渗剂与被渗金属表面的界面反应以及被渗元素原子的 扩散和扩散过程中相变等过程
☻渗碳件心部的硬度,不仅影响渗碳件的静强度,同时也影响表面残余应力的 分布,从而影响弯曲疲劳强度。在一定渗碳层深度情况下,心部硬度↑→表 面残余压应力↓。渗碳件心部硬度过高↑→渗碳件Ak↓;心部硬度过低,则 承载时易于出现心部屈服和渗层剥落
五、渗碳缺陷及控制 1、黑色组织:含Cr、Mn及Si等合金元素的渗碳钢渗碳淬火后,在渗层表
ξ相 ― 为斜方晶格的间隙化合物,N原子有序 地分布于间隙位置。也可认为是ε相的 扭曲变体(六方晶格),N=11.0~ 11.35%,分子式为 Fe2N。稳定温度 ≤450℃,>450℃ 发生分解
两个共析转变温度:在650℃,ε → γ + γ′ 590℃,γ → α + γ′
其中:γ相为含氮A,当从高于590℃的温度迅速冷却时将发生M转变,其转 变机理和含CA的M转变一样
6、表面腐蚀和氧化 原因: 渗碳剂不纯,含杂质多,如硫或硫酸盐的含量高 液体渗碳后零件表面粘有残盐,均会引起腐蚀 渗碳后零件出炉温度过高,等温盐浴或淬火加热盐浴脱氧不良 预防措施:仔细控制渗碳向金属表面渗入氮元素的工艺称为渗氮或氮化 特点:钢渗氮可以获得 比渗碳更高的表面硬度和耐磨性,HV950~1200
2、反常组织:特征是在先共析渗碳体周围出现F层 常在钢中含氧量较高(如沸腾钢)的固体渗碳时看到 具有反常组织的钢经淬火后易出现软点 补救办法:适当↑淬火温度或适当延长淬火保温时间,使A均匀化,并 采用较快的淬火冷却速度
3、粗大网状碳化物组织 形成原因:由于渗碳剂活性太大,渗碳阶段温 度过高,扩散阶段温度过低及渗碳 时间过长引起
面组织沿晶界出现呈断续网状的黑色组织 原因:渗碳介质中的O向晶界扩散,形成Cr、Mn、Si等的氧化物 → 内氧化
氧化使晶界及附近的合金元素贫化,淬透性↓→淬火后出现非M组 织
预防办法:注意渗碳炉的 密封性能, ↓炉气中的含O量
补救措施:出现黑色组织时, 若深度≯0.02mm , 可磨去或表面 喷丸处理
金属表面溶入被渗元素的原子后,表面该种元素的浓度↑→表面与内部存在 着浓度差→发生原子迁移现象,即扩散
纯扩散与反应扩散
§11.2 钢的渗碳
一、渗碳的目的、分类及应用
最广泛
钢的渗碳是钢件在渗碳介质中加热和保温,使碳原子渗入表面,获得 一定的表面含碳量和一定碳浓度梯度的工艺
目的是使机器零件获得高的表面硬度、耐磨性及高的接触疲劳强 度和弯曲疲劳强度。
缺点:多数盐浴有毒!!
气体渗碳是工件在气体介质中进行碳的渗入过程的方法 渗碳气体可 用碳氢化合物有机液体:如煤油、丙酮等直接滴人炉内汽化
事先制备好的一定成分气体通入炉内
吸热式气氛渗碳 氮基气氛渗碳
滴注法渗碳
分解出活性碳原 子渗入工件表面
二、气体渗碳工艺原理 1、滴注式可控气氛渗碳原理
一种气体碳势较低→稀释气 另一种气体碳势较高→ 富化气
渗碳方法:固体渗碳法、液体渗碳法及气体渗碳法
渗碳工件装入有固体渗剂的密封箱内 (一般采用黄泥或耐火粘土密封),在 渗碳温度加热渗碳 固体渗碳剂:由一定大小的固体炭粒和
起催渗作用的碳酸盐组成 渗碳温度:900~930℃
液体渗碳是在能析出活性碳原子的 盐浴中进行的渗碳方法
优点:加热速度快,加热均匀,便 于渗碳后直接淬火
面含碳量控制在‾0.9%
➢一般认为表面粒状碳化物增多, 可↑表面耐磨性及接触疲劳强度
➢但碳化物数量过多,特别是呈粗 大网状或条块状分布时,将使冲 击韧性、疲劳强度等性能变坏
☻渗碳层的深度↑→承载接触应力↑。因为由接触应力引起的最大切应力发生 于距离表面的一定深度处。若渗层过浅,最大切应力发生于强度较低的非渗 碳层(即心部)组织→渗碳层塌陷剥落。但渗碳层深度↑→渗碳件Ak↓
渗剂耗量 温度和时间 最佳工艺规范的获得
三、渗碳后的热处理
1、直接淬火:工件渗碳后,预冷到一定温度,然后立即进行淬火冷却
本
这种方法一般适用于气体渗碳或液体渗碳
质
固体渗碳时,由于工件装箱,出炉、开箱比较困难→不用
细 淬火前的预冷可以随炉降温或出炉冷却 晶 粒 预冷的目的:使工件与淬火介质的温度差↓,↓应力与变形
滴注式渗剂的选择原则: ★应该具有较大的产气量:产气量高的渗碳剂,炉内装入新的工件时,可 以在较短时间内把空气尽快地排出 ★ 碳氧比>1: 碳氧比↑→析出的活性碳原子↑,渗碳能力↑ 当碳氧比=1 时,如甲醇( CH3OH ),高温分解产物主要是CO和H2,而 CO是一种极弱的渗碳气体→可选作稀释剂 ★ 碳当量:碳当量↑→物质的渗碳能力↓ 渗碳能力:丙酮>异丙醇>乙酸乙脂>乙醇>甲醇 ★ 气氛中CO和H2 成分的稳定性:用CO2红外仪或露点仪控制碳势 ★ 考虑原料的价格及其来源
钢渗氮时氨的分解主要在炉内管道、工件、渗氮箱及挂具等钢铁材料的 构件表面通过催化作用来进行
通入渗氮箱的NH3,经过工件表面而落入表面原子的引力场时,被钢件 表面所吸附→化学吸附
在化学吸附作用下,解离出的活性氮原子,被钢件表面吸收并渗入工件 表面
二、渗氮层的组织和性能 纯铁渗氮层的组织和性能 在520℃ 渗氮时,若表面氮原 子能充分吸收,则自表面→中 心依次为ε相→γ′相→α相
四、渗碳后钢的组织与性能
自渗碳温度直接淬火后,渗层组织无过剩碳 化物,仅为针状M+A′ A′量自表面→内部逐渐减少 渗层硬度:在C=0.6%最高
表面由于A ′较多,硬度稍低
离表面0.2mm处A中含C量最高、A′量最多,HRC最低。
Reason:渗碳过程中剧烈形成碳化物这种钢中含有Ti、Cr碳化物形成元素,
钢 预冷的温度:稍高于心部成分的Ar3点,避免淬火后心部出现自由F
优点:减少加热、冷却次数,简化操作,减少变形及氧化脱碳
缺点:在较高渗碳温度停留较长→A晶粒↑
2、一次加热淬火:渗碳后缓冷,再次加热淬火
温度应根据工件要求 稍高于心部成分的Ac3点 心部要求强度较高
稍高于表面的Ac1
表面要求较高HRC和耐磨性
Chapter 11 金属的化学热处理
Definition: 金属制件在一定化学介质中,表面与介质相互作用,吸收其中某 些原子(或离子), 通过加热使该原子自表面向内部扩散的过程
作用:改变金属表面的化学成分和性能
目的 通过改变金属表面的化学成分及热处法获得单一材料难以实现的性能
进一步↑金属制件的使用性能
而且合金元素的扩散又极缓慢,在较短时间内很难扩散重新分
布。一旦C浓度达到A饱和极限浓度→析出合金渗碳体
正常情况,渗碳层淬火后的组织从表面→心部依次为:M+A′+碳化物 →M+A′→M→心部组织
心部组织:完全淬火为低碳M 淬火温度较低的为M+游离F 淬透性较差的钢为T or S+ F
一般希望渗层浓度梯度平缓 为了得到良好的综合性能,表
CO2含量↑→炉气碳势↓ 相同温度和CO2含量条件下:不同钢材的碳势不同 不同渗碳温度:同一CO2含量所得碳势不同。炉温↑→碳势↓
2、吸热式渗碳气氛渗碳: 吸热式气氛 + 富化气的混合气 碳势控制:调节富化气的添加量,一般常用丙烷作富化气 需要特设的气体发生设备 →适用于大批生产的连续作业炉
3、渗碳工艺规范的选择:如何以最快速度、最经济的效果获得合乎要求的 渗碳层
适用于固体渗碳以及液体、气体渗碳的工件(特别是本质粗晶粒钢),或
渗碳后不能直接淬火的零件
20Cr2Ni4A、18Cr2Ni4WA等高合金渗碳钢零件:渗C后保留有大量A′ 为了↑渗碳层表面HRC,在一次淬火加热前应进行高温回火
640~680℃×68h回火→A′发生
分解,碳化物充 分析出和集聚
540℃×2h ×三次 回火 更能促进冷 却过程中的 A′→M转变
回火温度的选择应以最 有利于A′转变为原则
Note:不论采用哪种淬 火方法,渗碳件在最终 淬火后均应180~
3、两次淬火:在渗碳缓冷后进行两次加热淬火 200℃ 低温回火
第一次淬火加热温度 > Ac3
细化心部组织,消除表面网状碳化物
第二次淬火加热温度 > 渗碳层成分的Acl温度(780~820℃)
细化渗碳层中A晶粒→隐晶M+ A′+ 均匀分布的细粒状碳化物渗层组织 缺点:多次加热,生产周期长、成本高,↑热处理时的氧化、脱碳及变形 等 适用于对性能要求较高的零件
最初:用煤油、焦苯作为渗碳剂直接滴入渗碳炉内进行渗碳
缺点:析出活性碳原子过多→不能全部被钢件表面吸收,在工件表面 沉积成碳黑、焦油等 →阻碍渗碳过程的继续进行→ 渗碳层深度及 碳浓度不均匀等
近年:发展了滴注式可控气氛渗碳(两种有机液体同时滴入炉内)