高炉风口小套频繁烧损的原因分析及探讨(精制甲类)
055 柳钢高炉大量风口烧损原因分析与探讨

柳钢高炉大量风口烧损原因分析与探讨陆寿先(柳州钢铁股份有限公司炼铁厂)l 前言近两年来,柳钢高炉风口烧损比较多,严重影响高炉正常生产。
按每生产万吨铁烧损风口数目计算,从2005年的0.164个上升到2007年0.909年和2008年的O.917个,其中单炉单月烧损风口达30个以上的有5次,分别为于20017年5月4号炉烧损风口34个;2007年5、6月8号炉烧损风口36个、30个;2008年1月7号炉烧损风口30个;尤其是2008年11月新2号炉烧损风口高达53个。
(历年柳钢炼铁厂风口烧损统计情况见表1)。
2大量风口烧损的经过为了探讨风口大面积烧损的原因,现就7号炉和新2号高炉生产情况进行分析。
柳钢7号高炉炉容1080m3,无料钟炉顶,碳砖+陶瓷杯炉底,双出铁场布置,设有20个风口,于2004年6月28日建成投产,2007年全年高炉利用系数2.522 t/(m3.d),综合入炉焦比528 k g/t,综合冶炼强度1.364 t/(m3.d),全年烧损风口中小套共41个。
2008年1月10目7时05分7号炉按计划进行年度检修7天,于1月16日凌晨3时恢复生产。
开炉时用铁口两侧19号、20号、l号、2号共4个风口送风。
送风后3小时20分钟发现18号风口中套漏水,当即休风更换。
当日15时05分(即复风后12个小时05分钟)再次休风更换20号风口中、小套。
在之后的12个小时内(从复风后的19个小时到31个小时内),高炉冶炼进程加快,连续打开7个风口送风作业。
到第36小时时,再次休风更换15号和5号两个风口中套。
也就是在复风后38个小时内,高炉休风三次,共休风9小时39分钊,,更换4个中套和1个小套。
此后高炉炉况一直不好,风口烧损不断,1月份共烧损风口各套共30个。
新2号高炉炉容2000m3,无料钟炉顶,碳砖+陶瓷杯炉底,双出铁场布置,设有26个风口,于2008年元月23日建成投产。
2008年10月22日,新2号高炉按计划限产封炉,封炉前炉况稳定顺行,各项技术经济指标位于全厂的前例。
宁钢1号高炉风口小套破损原因分析及解决措施

7 . 5 。
6 . 5 60
8 9 8 8
矮
话 8 7 蝠
8 6
嚣 篱
5 5
e 2 7 5
2 7 0
5 月份 日 期
匠
2 65 26 0
图3 5月份宁钢 自产焦炭冷态指标
5月份 日期
图6 5月份 宁 钢 1 号 高 炉 风 速 与压 差
心亦偏 向第 2 象 限,应该说 1 号高炉下部风 口小套 布局不均与第 3 象限气流偏旺 、中心点偏离有较大
关联 , 特别 是风 量增 加后更 加 凸显 了这一 现象 。
2 焊缝 开焊风 口损 坏分 析
跟上, 造成风量增加后高炉冶强并没有提高 , 反而压 差较之前 降低 1 0 k P a 左右( 见图 6 ) , 风速和鼓风动
降至 4 7 . 5 %( 考 虑在线 分 析校 验 的影 响 , 煤气 利 用也
现了较大波动 , 与风 口小套的破损有一定 的关联。
另外 , 如下 页 图 8所 示 , 以热 风 总管进 入 围管 的
方向为中心线 ,将 1 号高炉风 口圆周方向平均分成
4个象 限 ,可 以看 出本 次损 坏 的风 口小 套集 中区域 为第 3象 限 ,而 6月 1日定 修后 观察 到炉 顶料 面 中
Ab s t r a c t :T h e r e a p p e a r s s l a g i r o n me l i t n g l o s s a n d we l d we l d i n g i n Ni n g Ga n g n o .1 b l a s t f u r n a c e t u y e r e . h e T c a u s e s na a l y s i s o f t h i s s i t u a i t o n i s p r e s e n t e d a n d t h e c o r r e s p o n d i n g s o l u t i o n me a s u r e s a r e p mp o s  ̄. he T na a l y s i s p r e s e n t s t h e
高炉风口频繁破损原因分析及生产对策
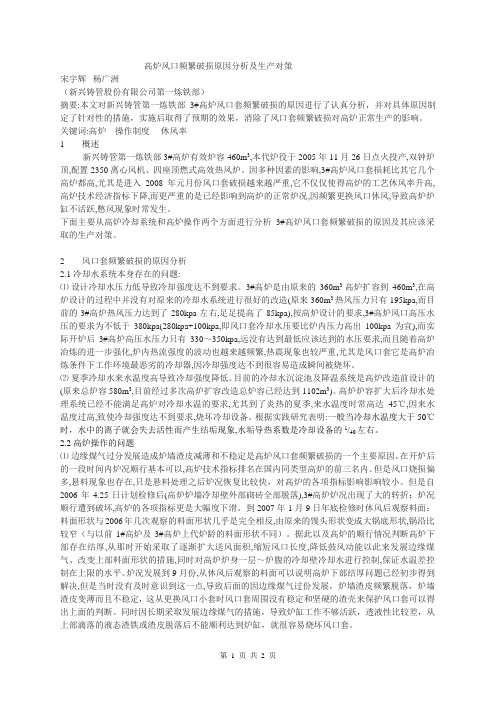
高炉风口频繁破损原因分析及生产对策宋宇辉杨广洲(新兴铸管股份有限公司第一炼铁部)摘要:本文对新兴铸管第一炼铁部3#高炉风口套频繁破损的原因进行了认真分析,并对具体原因制定了针对性的措施,实施后取得了预期的效果,消除了风口套频繁破损对高炉正常生产的影响。
关键词:高炉操作制度休风率1 概述新兴铸管第一炼铁部3#高炉有效炉容460m3,本代炉役于2005年11月26日点火投产,双钟炉顶,配置2350离心风机、四座顶燃式高效热风炉。
因多种因素的影响,3#高炉风口套损耗比其它几个高炉都高,尤其是进入2008年元月份风口套破损越来越严重,它不仅仅使得高炉的工艺休风率升高,高炉技术经济指标下降,而更严重的是已经影响到高炉的正常炉况,因频繁更换风口休风,导致高炉炉缸不活跃,憋风现象时常发生。
下面主要从高炉冷却系统和高炉操作两个方面进行分析3#高炉风口套频繁破损的原因及其应该采取的生产对策。
2 风口套频繁破损的原因分析2.1 冷却水系统本身存在的问题:⑴设计冷却水压力低导致冷却强度达不到要求。
3#高炉是由原来的360m3高炉扩容到460m3,在高炉设计的过程中并没有对原来的冷却水系统进行很好的改造(原来360m3热风压力只有195kpa,而目前的3#高炉热风压力达到了280kpa左右,足足提高了85kpa),按高炉设计的要求,3#高炉风口高压水压的要求为不低于380kpa(280kpa+100kpa,即风口套冷却水压要比炉内压力高出100kpa为宜),而实际开炉后3#高炉高压水压力只有330~350kpa,远没有达到最低应该达到的水压要求,而且随着高炉冶炼的进一步强化,炉内热流强度的波动也越来越频繁,热震现象也较严重,尤其是风口套它是高炉冶炼条件下工作环境最恶劣的冷却器,因冷却强度达不到很容易造成瞬间被烧坏。
⑵夏季冷却水来水温度高导致冷却强度降低。
目前的冷却水沉淀池及降温系统是高炉改造前设计的(原来总炉容580m3,目前经过多次高炉扩容改造总炉容已经达到1102m3)。
风口小套损坏的原因

风口小套损坏的原因第一篇:风口小套损坏的原因风口小套损坏的原因一、操作方面原因一般情况,导致风口大量破损的主要原因是操作方面,主要有下面几种:第一,高炉边缘过度发展。
由于边缘气流过剩,高炉在边缘的反应增加,生成的渣铁量也大,相对于正常情况下渣铁沿风口回旋区表面进入炉缸,此时就会出现少量渣铁沿炉墙下滴,当有少量渣铁滴打在风口上端,就会造成风口损坏。
这种原因造成的风口烧损部位一般多在风口的上部,烧漏的孔洞多呈现外大内小,类似水滴石穿的现象。
边缘过度发展时,通过风口镜,还可以看到风口前比较频繁的升降现象。
第二,高炉炉缸不活,有堆积。
无论是中心堆积还是边缘堆积,都会造成炉缸容积变小。
由于高炉的出铁次数、时间一般都是固定的,所以同等情况下,炉缸堆积后,渣铁面将比原来升高,高炉在外部就会表现出压量关系紧张,料慢等现象,炉内渣铁就容易把风口烧毁。
有时由于外围事故,延迟了出铁时间,也可能造成风口烧损。
不过,炉缸堆积造成风口破损最主要的原因是:炉缸堆积后,高炉死焦堆透液性变差,致使风口前有渣铁聚集,从而烧坏风口。
如高炉炉凉后恢复炉况,常常会造成大批的风口破损,其最主要的原因就是炉缸死焦透液性能差,加上刚刚生成的渣铁物理热低、流动性差,不能及时渗透到炉缸,渣铁在风口前聚集所致。
这类原因造成的风口烧损部位一般多在风口的下部。
第三,高炉鼓风动能不足。
比如高炉长期减风,风口面积不及时调整,由于鼓风动能不足,风口回旋区变小,渣铁就可能烧损风口的前端。
第四,高炉不顺,悬坐料原因。
悬料后,减风坐料甚至休风坐料,存在风口灌渣的可能,从而使风口烧损;也可能料柱从上部突然下落,导致风口破损,特别是长时间顽固悬料,更是危险。
曾经就有企业因为长时间恶性悬料,坐料时把风口砸掉的事故发生。
第五,喷煤工艺中煤粉冲刷的原因。
高炉喷吹煤粉后,由于喷枪枪位不正,可使风口在很短时间内被磨漏。
即使枪位很正,煤粉的摩擦对风口的磨损也是非常严重的。
有企业统计数据表明,煤粉的磨损可使风口内径每月扩大0.5~0.8 mm。
减少4号高炉风口小套损坏的措施
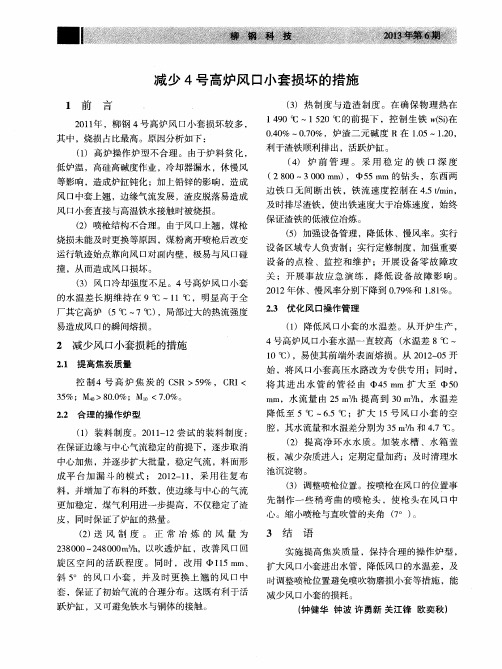
实 施 提高 焦 炭质 量 ,保 持 合 理 的操 作 炉型 , 扩 大风 口小套进 出水 管 ,降低 风 口的水温 差 ,及 时调整 喷枪位 置避 免喷 吹物磨损 小套 等措 施 ,能 减 少风 口小套 的损耗 。
(钟健 华 钟 波 许 勇新 关江 锋 欧 奕秋 )
(2) 喷枪结 构不合 理 。 由于风 口上 翘 ,煤枪 烧损 未能及 时更 换等 原 因 ,煤粉 离开 喷枪后 改 变 运行轨迹始点靠向风 口对面内壁 ,极易与风 口碰 撞 ,从 而 造成风 口损 坏 。
(3) 风 口冷却 强度 不 足 。4号 高炉 风 口小套 的水 温差 长 期 维 持在 9 cC 11℃ , 明显 高 于 全 厂其 它高 炉 (5℃ ~7 cC),局部 过大 的热流 强度 易造 成风 口的瞬间熔 损 。
(2)送 风 制 度 。 正 常 冶 炼 的 风 量 为 238000—248000m /h,以吹 透炉 缸 ,改善 风 口 回 旋 区空 间 的 活 跃 程 度 。 同 时 ,改 用 115 mm、 斜 5o 的 风 口小 套 ,并 及 时 更 换 上 翘 的 风 口 中 套 ,保证 了初 始气 流 的合 理分 布 。这既有 利 于活 跃 炉缸 ,又可避免 铁水 与铜 体的接 触 。
减 少 4号 高炉风 口小 套损 坏 的措 施
1 前 言
2011年 ,柳 钢 4号高 炉 风 口小 套损 坏 较 多 , 其中,烧损 占比最高。原因分析如下 :
(1) 高炉 操作 炉 型 不合 理 。 由于 炉料 贫 化 , 低炉 温 ,高硅高 碱度作 业 ,冷却器 漏水 ,休 慢风 等影 响 ,造成炉 缸钝 化 ;加 上铅 锌 的影 响 ,造成 风 口中套上 翘 ,边缘气 流发 展 ,渣 皮脱 落易 造成 风 口小套 直接 与高温铁 水 接触时 被烧损 。
武钢5号高炉风口频繁破损分析

摘要对武钢5号高炉风口破损的原因进行了分析,并对处理经验进行了总结。
主要操作经验有:适当发展中心和边缘两股煤气流,改全焦冶炼,洗炉,提高炉温并适当降低炉渣碱度等。
关键词高炉风口破损对策1风口破损状况武钢5号高炉有效容积为3 200 m3,设有32个风口,4个铁口。
自1991年10月19日投产以来,已进入第14年服役期。
2004年5月份年修更换炉顶-齿轮箱以后,高炉顺行一直处于不稳定的状态,特别是5、6、7几个月受齿轮箱溜槽停转及槽下计算机设备老化、热风炉等方面的影响,高炉拉风降压频繁。
加上原燃料变差,风口布局不够合理,严重影响了高炉的顺行,高炉炉型受到很大损伤。
11月中旬至12月中旬一个月左右的时间里,因干熄焦检修改用水熄焦后,高炉风量萎缩,风速降低,慢风时间增加。
加之近几个月来,原料中Al203含量大幅上升,使得高炉渣铁流动性差,渣铁不能及时排放,从而造成炉缸堆积,风口破损频繁。
从12月12日至12月22日共损坏风口28个(重复计算,见表1),高炉被迫休风6次,严重影响到高炉的顺行。
2风口破损期间高炉操作观察到的现象在武钢5号高炉这次风口频繁破损期间,主要有以下几方面的现象:(1)下料不均匀。
从12月12日至12月22日,下料时快时慢,在小批重轻O/C条件下,慢时3.5批料/h,快则6.0批料/h,而正常下料(大批重时)应该在7.0批料/h。
(2)有时出现管道行程,而且有小崩料现象发生。
(3)高炉不能接受压差,风量逐步萎缩。
比如12月12日夜班,操作中,在顶压为0.140MPa情况下,压差仅控制在0.140MPa以内,风量由接班时的5050m3/min萎缩到4480m3/min,在此期间风口破损了4个,这说明高炉所能接受的压差愈来愈低。
(4)高炉煤气流不稳定,顶温曲线较散且不规则,冷却壁温度变化大。
(5)风口破损多。
从12月12日至12月22日共破损风口达28个之多。
(6)炉缸容积变小。
比如12月18日这天,出铁次数达18次之多,而当天的产量却仅为4356.1t,这说明炉缸内所能排放出来的渣铁量比高炉正常时少,炉缸容积变小。
酒钢6号高炉风口破损事故分析与探讨

摘要:风是高炉生产的必不可少的原料,风口结构是否正常工作,直接影响到高炉的正常生产。
风口装置,是保证高炉正常生产的关键部件,包括风口大套、风口二套、风口也称风口小套或风口三套,是送风管路最前端的一个部件。
该文介绍风口装置的结构和作用,风口装置的结构、材质、砌砖以及高炉操作水平,直接影响风口的使用寿命,从而直接影响高炉的正常生产。
通过酒钢6号高炉风口破损事故的发生、处理和原因分析,总结出高炉风口破损的主要原因以及加强原燃料的筛分,改变布料思路,坚决控制边缘气流,稳定风温操作,稳定富氧喷煤操作,稳定渣铁正点排出率,控制碱金属入炉量等减少风口破损的主要措施,为确保高炉正常生产提供依据。
关键词:风口破损事故处理破损原因减损措施中图分类号:tf549 文献标识码:a 文章编号:1674-098x(2016)02(b)-0037-03 风是高炉生产的必不可少的原料,风口装置是否正常工作,直接影响到高炉的正常生产。
风口装置,是保证高炉正常生产的关键部件。
包括风口大套、风口二套、风口也称风口小套或风口三套,是送风管路最前端的一个部件。
它位于高炉炉缸上部,成一定角度探出炉壁。
风口与风口中套、风口大套装配在一起,加上冷却水管等其它部件,形成高炉的风口设备,其结构如图1所示。
风口前端炉缸回旋区温度约2 000 ℃左右,风口的工作条件十分恶劣,在使用一段时间后会损坏,从而迫使高炉休风,更换风口,风口是影响高炉生产效率的重要因素之一。
风口中套的作用是支承风口小套,中套的工作位置与风口小套相比,离炉缸较远,它不直接接触热风和高炉内的气氛。
但在大型高炉强化冶炼的工作条件下,风口中套周围仍受到300 ℃左右高温的影响。
风口中套用铸造紫铜制作。
风口大套的功能是支撑风口中套与小套,并将其与高炉炉体相连成为一体。
风口大套的工作温度约300 ℃。
对风口大套主要考虑其强度性能。
通常风口大套有铸钢件和带铸入冷却水管的铸铁件两种。
风口装置的结构、材质、砌砖以及高炉操作水平,直接影响风口的使用寿命。
高炉风口破损原因及预防

高炉风口破损原因及预防王喜兵(酒钢集团翼城钢铁股份有限公司)摘要高炉风口是高炉送风制度中关键设备,寿命的长短直接影响着高炉的连续强化生产,风口的破损破坏了高炉正常的生产秩序,对高炉的产量、经济技术指标、都有很大的影响。
本文根据多年操作高炉的实践谈谈对风口破损的认识,并提出预防风口破损的几点建议。
关键词风口破损防治煤气流1 风口破损的原因分析高炉风口处在高炉下部的要害部位,伸入炉内的外表面在1950℃-2450℃的高温环境下、不仅承受着高温液态渣铁的恶劣侵蚀、而且受到循环区焦炭的撞击及落下焦炭的磨损。
风口破损的原因据国内外风口破损统计,渣铁侵蚀造成的占80-92%,磨损的占3-15%,龟裂破损的占5%以下。
实践表明风口损坏的主要因素是渣铁对风口前端、上端、下端的熔蚀,当其热负荷急剧超过风口承受极限热负荷时就被烧坏;其次是风口内侧及外、上表面磨损和龟裂损坏。
1.1高炉煤气流紊乱由于炉体本身设备原因或炉腹煤气指数超过正常范围,风量与料柱透气性不适应,料柱透气性变差,高炉内的煤气流分布紊乱,在料柱疏松区容易吹出管道。
从炉顶成像仪可以看出焦炭被吹翻现象,管道方向的炉料得不到充分的预热与还原,大量生料下降到风口时降低了炉缸温度,在风口区形成堆积,影响渣铁渗透,风口下端热负荷将异常升高,超过正常工作下所承受的热流强度值942*103w/m2,风口瞬时即被烧损。
另一方面由于出现管道后,风口循环区缩短,渣皮不稳定频繁脱落致使风口上端磨损加剧。
1.2 送风制度不合理炉缸是高炉本体的要害部位,是高炉初始煤气的发源地,决定了高炉初始煤气流分布状态。
风口布局不合理,造成炉缸四周工作不匀,容易形成边缘与中心堆积,炉缸有效容积缩小导致渣、铁水面上升,滑尺崩料时高温铁水快速接触风口表面而烧熔风口。
1.3 原燃料条件恶化无论大高炉与小高炉焦炭质量直接影响高炉的顺行。
主要是焦炭强度与焦炭负荷要匹配在一定范围,随着煤比提高,焦炭负荷加重,焦炭骨架作用显的更为突出。
导致高炉风口损坏的3个基本原因
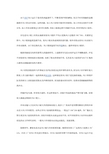
滴落在风口的水冷表面。
这些因素,加上风口结构可能存在的缺陷,加上冷却水流的不合理分布,加上冷却水硬度过大和含污染物,再加上炼铁过程中的操作失误,经常导致风口损坏。
首先是风口壁上有铁水滴落而使风口烧穿(平均占更换风口总数的70%~75%)。
在烧穿过程中,风口壁部温度急剧升高,使风口壁内形成顽固的蒸汽膜,使外有铁水的风口内表面与根据培赫曼及埃弗里德等人的最新研究,上述烧穿首先是由高炉运行不顺酿成的。
炉况不佳致使风口壁部底面出现结瘤,加重了铁水的侵蚀作用,尤其是风口前段因与向下汇集的大量铁水接触最容易发生烧穿。
风口的发热致损坏与炉渣成分及炉缸热度决定的炉渣性质有关,因为风口区炉渣在很大缸里的部分上表面最易受铁水及炉渣的损害,因为除基本热负荷外,还要承受熔融滴落物的热冲击。
伴随炉况失调,经常发生崩料。
在这种事故中,冶炼中形成的液态产物可能飞溅,结果使大量液态物落在风口壁上。
冷却水输入方法对风口耐久性的影响也很大。
很多工厂的高炉是用惯用断面支管将冷却水送入风口冷却腔里,水终点至风口前端的距离较远,一般远于100~250毫米。
各厂输水支管长度及风口前段构型各异,因而冷却腔内水流运动也不同。
对不同构型风口内冷却水循环状况的水力学研究表明,一般风口冷却腔内水流运动混乱,流速很慢。
除烧穿外,磨损也是决定风口耐久性的重要因素。
独联体各国工厂这类风口故障占3%~ 11%。
许多工厂对风口外壳进行焊接后,在风口前段经常留下凹窝和陡角,在风口运行中这些部位蒙上灰尘和沾满污垢后,严重妨碍热交换,导致产生内应力及裂纹。
因此,风口前段烧穿。
外锥套磨损及化学腐蚀及焊缝开裂是风口损坏的3个基本原因。
高炉风口破损影响因素及处理方案研究

高炉风口破损影响因素及处理方案研究风口是高炉送风的关键部件,通过高炉风口吹入的高温热风和炉底焦炭氧化燃烧生成CO,CO在高温上升中还原出原来以氧化物形态存在的铁。
高炉风口的特点是传导性好、冷却均匀、冷却效率高、组织致密、耐磨性好等。
通常安装于腹炉与炉底之间的炉壁中。
高炉风口一般应用于钢铁、冶金、化工等行业,是金属冶炼业中重要的器具,本文主要针对高炉风口的破损的影响进行分析,并探讨有关的处理方案,做好相关的高炉风口养护工作。
标签:高炉风口;破损;影响因素;处理方案高炉的生产技术水平直接影响着整个企业的冶炼水平,而高炉的生产水平则直接受到风口的运作情况的影响。
在高炉风口破損后,高炉的生产也情况随之而受到影响,需要对高炉风口进行频繁的维修和更换,将会投入大量的维护成本,高炉的生产效益则降低了许多。
在维修保养的同时还要根据不同的高炉工况和使用及经济要求,选择正确适宜的方法。
高炉风口的结构有空腔水冷风口、双腔旋流风口、贯流式风口、双进双出风口、偏心式风口等几种,在进行探究有关高炉风口的破损因素及应对的同时,还要考虑高炉风口的材质和结构,做好全面的应对策略。
1 关于高炉风口的概况高炉风口常处在于十分恶劣的环境中,一般温度都会达到1500度以上,并且在使用过程中会有高温的铁流等物质的冲刷和磨损。
目前的高炉风口材质主要为高纯紫铜,在制造时,要从风口的轻度、刚度、抗龟裂性能等方面俩进行考虑,并且高炉风口的状态也有锻制、铜版卷制、铸造等不同的状态,工业上大多选择的是风口重量低、制造成本也较低的铜版卷制状态的高炉风口。
纯度越是高的高炉风口,其强度和刚度也越高,受损程度也随之降低。
2 高炉风口近几年的损坏情况由于高炉风口的使用环境恶劣,且会经受工业上的冶金产品、炉料、炉渣等的冲刷腐蚀,日积月累会形成严重的受损,甚至会导致高炉风口无法再继续进行使用,有关近年来高炉风口的破损情况如下表1。
从表1中可以看出,近年来高炉风口的破损情况均较为严重,受到损坏的高炉风口比例一直高居不下,这与使用者对高炉风口的保养及维修有很大关系,要及时对高炉风口的破损原因进行针对性的排查和应对,做好有效的高炉风口维护工作,才能在提高成产技术的同时,减少成本增长经济效益。
优化高炉操作,减少小套烧损

优化高炉操作,减少小套烧损作者:王艺淞来源:《科学导报·学术》2017年第11期【中图分类号】 TF524【文献标识码】 B【文章编号】 2236-1879(2017)11-0219-011 前言造成风口小套烧损的原因很多,但最基本的烧损机理即是:风口小套受热超负荷,冷却介质难以及时传导散热,从而导致风口小套温度高于铜质固液相反应的700℃界限温度,当达到铜剧烈氧化的900℃界限温度时,风口很快在高温高压下烧坏漏水。
9#高炉风口小套烧损部位基本在风口小套前端下部,主要集中在高炉休风复风后风量恢复过程中及炉况波动情况。
造成风口小套烧损的因素大致有如下几个方面:1.1 风口小套本身的材质结构。
这包括风口小套铜质的纯度、性能,本身结构的合理性。
9#高炉都是铜质99%以上的贯流式风口,基本应能满足本高炉的风口要求。
1.2 冷却介质的压力、流量以及流速。
当前各地区的高炉均在强化生产,尤其是民营企业的高炉利用系数和指标都日趋提高。
之前的许多设计参数已难以满足强化冶炼的需求。
9#高炉的风口小套水压1.3-1.4Mpa,水量40t/h左右,同部分高冶强的同级高炉来比较,只能说是在中下限水平。
而对于流速来说,应该保持在1.4-16m/s,才能满足9#高炉的生产需求。
1.3 炉缸状况。
高炉炉缸活跃、稳定顺行是炼铁生产顺畅的基本要求。
所以说炉缸无论是产生哪种堆积,对风口套烧损都产生了巨大的影响。
造成炉缸堆积的原因主要有三种:一是低炉温堆积,二是高碱度堆积,三是石墨碳堆积。
在我厂的原燃料条件下,焦炭热强度一般,基本在64以下,反应性在25以上,同时入炉矿的转鼓强度较低,基本都在85以下,由此来看,在原燃料方面有对中心死焦柱不利因素。
另外因烧结碱度波动大且信息反馈不及时,炉渣碱度调剂慢,从而使中心料柱更容易堆积,造成料柱透气透液性变差。
2 存在的不足2.1 气流分布。
为了保障高炉顺行,在我厂的原燃料条件下,之前9#高炉都执行的是有意识的压制边缘的操作方针。
4#高炉风口小套破损原因分析及改进

4#高炉风口小套破损原因分析及改进周海林【摘要】简述了梅山炼铁厂4#高炉风口小套损坏的情况及其所造成的影响.通过现场调查,研究小套具体的破损位置,分析了其产生的原因并加以汇总,提出了防止风口小套破损的方法和措施.通过对风口区域的吹管、小管质量以及煤枪插入位置的管理,加强炉前渣铁处理保证及时出净渣铁等措施,小套破损得到了有效控制.【期刊名称】《天津冶金》【年(卷),期】2011(000)005【总页数】2页(P1-2)【关键词】高炉;风口;破损;原因;措施【作者】周海林【作者单位】上海梅山钢铁股份有限公司,南京210039【正文语种】中文梅钢4#高炉的有效容积为3 200 m3,是梅山真正意义上的第一座大高炉,于2009年5月12日顺利投产。
它共有4个铁口,32风口,现风口小套长度为640 mm。
自投产以来,小套损坏较多,造成高炉休风,严重时造成炉况恶化。
2011-01—04期间共计损坏29只小套,月均损坏7.25只,非计划休风时间达17.2 h,严重影响了4#高炉稳定顺行和各项经济技术指标的完成。
我们从小套的实际损坏位置分析得出小套破损的主要原因有渣铁侵蚀、煤粉磨坏小套、炉体渣皮剥落砸坏小套及小套自身质量问题等。
风口小套工作环境恶劣,它不仅要承受高温热风的高速冲刷,液态渣铁的冲蚀,而且还要承受高温焦炭的撞击以及喷煤时煤粉的高速磨损。
另外,风口内的冷却水温度很低,而风口壁外表面却要承受来自回旋区2 000℃左右的高温辐射和1 000℃以上的气流及渣铁的对流换热,从而导致风口壁要承受很大的温度梯度以及由此而引起的热应力[1]。
这就对风口的材质以及结构提出了一定的要求。
目前梅钢采用的是贯流式风口,顶端下斜5°,这种结构冷却水从风口小套进口直接进入小套前端的空腔,循环1周后进入外循环空腔,反向绕1周后从出口流出。
这样,冷却水在小套内流速快,滞留时间短,带走的热量多,对小套前端的高温冲刷部位冷却效果好。
025 10号高炉风口小套频繁漏水原因分析及处理措施

10号高炉风口小套频繁漏水原因分析及处理措施胡永平杨召永封冬贯(圣戈班穆松桥中国徐州基地炼铁厂)摘要:对圣戈班徐州基地10号高炉在2008年10月12月期间风口频繁漏水进行原因分析,确定了冷却水的水质及水压是风口小套损坏的直接原因,高炉操作因素的影响亦是风口损坏不可忽视的因素,通过实施一系列的措施处理后,到目前为止己连续6个月无风口小套漏水现缘的发生。
关键词:高炉小套漏水处理措施1 引言圣戈班徐州基地10号(420m3)高炉是圣戈班中国区徐州基地铸管配套节能降耗技术改造项目,于2008年9月16日建成投产,14个风口,风口小套采用双腔式斜风口,小套冷却水采用高压水(0.95Mpa),高炉净环水系统采用高循环率运行,为保证循环水水质,严格控制循环水系统的腐蚀率及热污垢系数,使系统长期稳定地正常运行。
在高炉净环水系统中设有投加水质稳定药剂的装置。
高炉开炉1月后,出现风口小套频繁漏水现象,严重影响着高炉的各项经济指标。
2风口小套损坏的数量及位置描述2.1 风口小套损坏的数量及分布自2008年10月22日(即开炉后36天)至2008年12月26日,风口小套共计损坏31个,在11月14日至11月28日期间平均一天更换一个,严重的11月27日及12月1日每天更换3个,风口寿命最短的为8天,最长的亦仅为72天。
平均寿命为28天。
(风口更换的数量及位置分布如表1)2.2风口损坏的位置描述小套的损坏相对于风口位置无明显的规律性,各风口均有损坏现象。
所有风口小套的损坏均在前端、上沿,其中小套内口损坏所占比例为20%,初期的损坏全是此种现象,烧损比例为55%,90%更换下来的风口小套存在龟裂现象,风口损坏形状如图1、图2、图3。
3原因分析3.1加工制作质量因素最初风口的损坏全部在内口的上沿,根据当时的现象分析并结合其他高炉小套损坏的经验判断,此种损坏应为小套的质量问题,而影响小套质量因素主要为材质及加工制作质量,后续的材质化验分析表明,小套材质含铜较高达99.6%,基本可以判断非材质因素引起,造成前端内口开裂的主要原因可以判定为风口小套的加工制作质量因素,通过对风口小套进行解剖及联系制作厂家,亦证明此种因素的存在。
玉钢3^#高炉风口频繁烧损的原因及对策
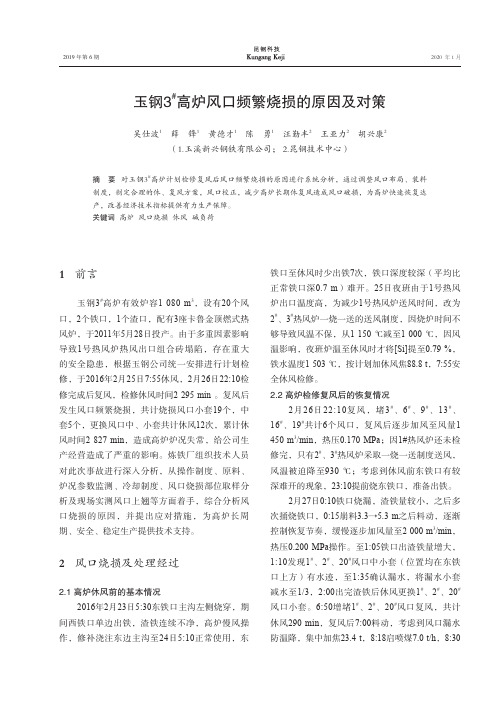
及改善料柱透气性,集中加焦70.2 t。1号热风炉
于16:20检修完并烧好炉后开始送风,之后分两次 加风温70 ℃至1 000 ℃。16:30发现12#、14#风口吹 开,视炉况迎集中焦18:25捅开9#,19:05东铁口出
铁,[Si]回升至1.8 %,物理热1435 ℃,渣铁排放 正常,视炉况19:25捅开19#风口,19:50发现5#风口
昆钢技术中心摘要对玉钢3高炉计划检修复风后风口频繁烧损的原因进行系统分析通过调整风口布局装料制度制定合理的休复风方案风口校正减少高炉长期休复风造成风口破损为高炉快速恢复达产改善经济技术指标提供有力生产保障
2019 年第 6 期
2020 年 1 月
玉钢3#高炉风口频繁烧损的原因及对策
吴仕波1 薛 锋1 黄德才1 陈 勇1 汪勤丰2 王亚力2 胡兴康2 (1.玉溪新兴钢铁有限公司; 2.昆钢技术中心)
堵砖并捅开,20:30 出铁炉温升至[Si]3.17 %,物 理热1 484 ℃,渣铁排放正常。21:25发现4#风口小
套漏水,并小套减水量至1/3,22:40Байду номын сангаас后休风更换 4#风口小套。
2月28日0:10增堵4#风口复风,共计休风90 min,0:30发现1#、7#、8#、18#风口小套漏水,减 水至1/3,2:08铁后休风更换1#、7#、8#、18#风口
中小套之间有水迹,减水至1/2,为改善料柱透气
马钢3号高炉风口小套破损原因分析及处理

破损时间小套序号破损部位破损方式破损时间小套序号破损部位破损方式2018-10-0812先上部后下部烧损2019-08-2817上部烧损2018-10-317上部烧损2019-09-2410下部烧损2018-11-1015上部烧损2019-09-259上部烧损2018-11-112上部烧损2019-12-0418先下部后上部烧损2018-12-296上部烧损2020-02-0218下部烧损2019-02-025上部烧损2020-02-051上部烧损2019-02-0318上部烧损2020-02-0917下部烧损2019-02-2816上部烧损2020-03-0212下部烧损2019-03-204上部烧损2020-03-1818下部烧损2019-04-267上部烧损2020-03-231上部烧损2019-05-026上部烧损2020-05-2116先上部后下部烧损山西冶金SHANXI METALLURGY Total 188No.6,2020DOI:10.16525/14-1167/tf.2020.06.37总第188期2020年第6期马钢3号高炉风口小套破损原因分析及处理高广静,胡杰,陈军,尹祖德,侯军(马鞍山钢铁股份有限公司炼铁总厂,安徽马鞍山243000)摘要:对马钢3号高炉风口小套破损的原因进行深入分析,找出3号炉小套破损主要原因为炉内气流分布不合理、炉况顺行不畅、炉缸活跃性差等。
通过调整高炉上、下部制度,优化炉内气流;强化炉前出铁,保证渣铁出净;调整槽下筛网间距,增加中心焦粒度以及加强日常炉体巡检等措施,小套破损得到了有效控制。
关键词:风口小套破损措施中图分类号:TF573.7文献标识码:A文章编号:1672-1152(2020)06-0095-04收稿日期:2020-10-20第一作者简介:高广静(1979—),男,本科,毕业于昆明理工大学,马钢3号高炉炉长,工程师,研究方向为高炉炼铁操作。
莱钢6#1080m3高炉提高风口小套使用寿命的措施
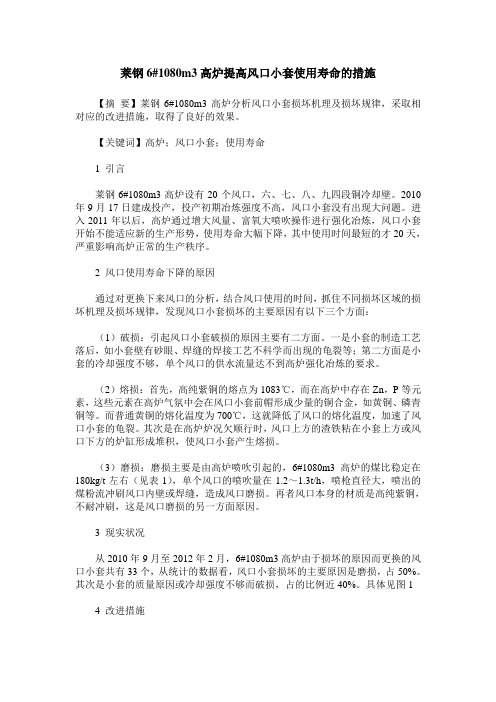
莱钢6#1080m3高炉提高风口小套使用寿命的措施【摘要】莱钢6#1080m3高炉分析风口小套损坏机理及损坏规律,采取相对应的改进措施,取得了良好的效果。
【关键词】高炉;风口小套;使用寿命1 引言莱钢6#1080m3高炉设有20个风口,六、七、八、九四段铜冷却壁。
2010年9月17日建成投产,投产初期冶炼强度不高,风口小套没有出现大问题。
进入2011年以后,高炉通过增大风量、富氧大喷吹操作进行强化冶炼,风口小套开始不能适应新的生产形势,使用寿命大幅下降,其中使用时间最短的才20天,严重影响高炉正常的生产秩序。
2 风口使用寿命下降的原因通过对更换下来风口的分析,结合风口使用的时间,抓住不同损坏区域的损坏机理及损坏规律,发现风口小套损坏的主要原因有以下三个方面:(1)破损:引起风口小套破损的原因主要有二方面。
一是小套的制造工艺落后,如小套壁有砂眼、焊缝的焊接工艺不科学而出现的龟裂等;第二方面是小套的冷却强度不够,单个风口的供水流量达不到高炉强化冶炼的要求。
(2)熔损:首先,高纯紫铜的熔点为1083℃,而在高炉中存在Zn,P等元素,这些元素在高炉气氛中会在风口小套前帽形成少量的铜合金,如黄铜、磷青铜等。
而普通黄铜的熔化温度为700℃,这就降低了风口的熔化温度,加速了风口小套的龟裂。
其次是在高炉炉况欠顺行时,风口上方的渣铁粘在小套上方或风口下方的炉缸形成堆积,使风口小套产生熔损。
(3)磨损:磨损主要是由高炉喷吹引起的,6#1080m3高炉的煤比稳定在180kg/t左右(见表1),单个风口的喷吹量在1.2~1.3t/h,喷枪直径大,喷出的煤粉流冲刷风口内壁或焊缝,造成风口磨损。
再者风口本身的材质是高纯紫铜,不耐冲刷,这是风口磨损的另一方面原因。
3 现实状况从2010年9月至2012年2月,6#1080m3高炉由于损坏的原因而更换的风口小套共有33个,从统计的数据看,风口小套损坏的主要原因是磨损,占50%。
高炉频繁烧套的原因
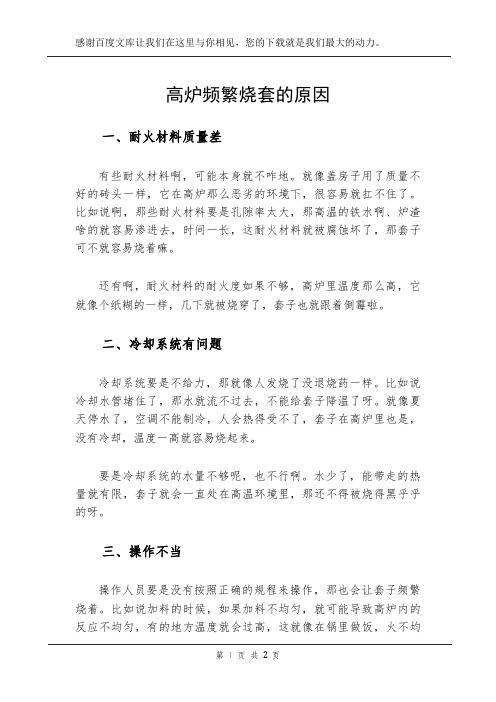
高炉频繁烧套的原因一、耐火材料质量差有些耐火材料啊,可能本身就不咋地。
就像盖房子用了质量不好的砖头一样,它在高炉那么恶劣的环境下,很容易就扛不住了。
比如说啊,那些耐火材料要是孔隙率太大,那高温的铁水啊、炉渣啥的就容易渗进去,时间一长,这耐火材料就被腐蚀坏了,那套子可不就容易烧着嘛。
还有啊,耐火材料的耐火度如果不够,高炉里温度那么高,它就像个纸糊的一样,几下就被烧穿了,套子也就跟着倒霉啦。
二、冷却系统有问题冷却系统要是不给力,那就像人发烧了没退烧药一样。
比如说冷却水管堵住了,那水就流不过去,不能给套子降温了呀。
就像夏天停水了,空调不能制冷,人会热得受不了,套子在高炉里也是,没有冷却,温度一高就容易烧起来。
要是冷却系统的水量不够呢,也不行啊。
水少了,能带走的热量就有限,套子就会一直处在高温环境里,那还不得被烧得黑乎乎的呀。
三、操作不当操作人员要是没有按照正确的规程来操作,那也会让套子频繁烧着。
比如说加料的时候,如果加料不均匀,就可能导致高炉内的反应不均匀,有的地方温度就会过高,这就像在锅里做饭,火不均匀,有的地方就糊了,套子也就容易被烧着。
还有啊,炉内的压力控制不好也是个大问题。
如果压力突然增大或者减小,对套子都会产生很大的冲击力,就像大风突然吹向一个小房子一样,时间一长,套子就容易损坏,然后就被烧着喽。
四、炉内气流不稳定炉内的气流就像风一样,如果它不稳定,到处乱吹,就会对套子产生不良影响。
气流可能会把高温的物质吹到套子上,让套子局部温度过高,就像一阵热风突然吹到脸上一样,会让人觉得很烫,套子也受不了呀。
而且不稳定的气流还可能影响炉内的反应平衡,使得炉内的温度分布更加不均匀,这对套子来说简直就是雪上加霜,更容易被烧着了。
高炉知识
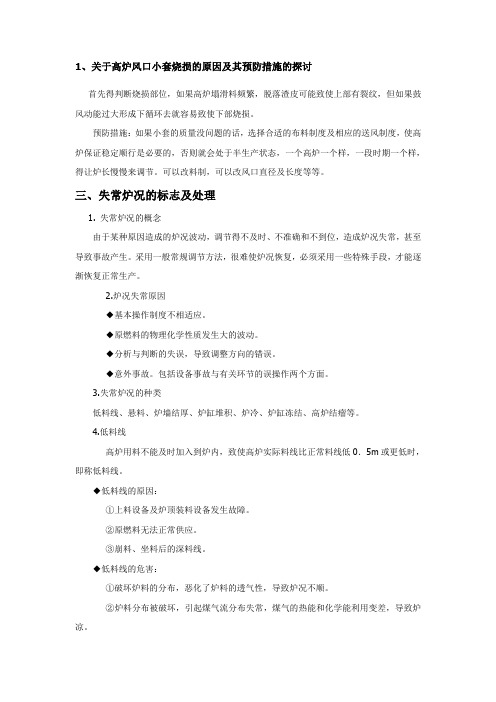
1、关于高炉风口小套烧损的原因及其预防措施的探讨首先得判断烧损部位,如果高炉塌滑料频繁,脱落渣皮可能致使上部有裂纹,但如果鼓风动能过大形成下循环去就容易致使下部烧损。
预防措施:如果小套的质量没问题的话,选择合适的布料制度及相应的送风制度,使高炉保证稳定顺行是必要的,否则就会处于半生产状态,一个高炉一个样,一段时期一个样,得让炉长慢慢来调节。
可以改料制,可以改风口直径及长度等等。
三、失常炉况的标志及处理1. 失常炉况的概念由于某种原因造成的炉况波动,调节得不及时、不准确和不到位,造成炉况失常,甚至导致事故产生。
采用一般常规调节方法,很难使炉况恢复,必须采用一些特殊手段,才能逐渐恢复正常生产。
2.炉况失常原因◆基本操作制度不相适应。
◆原燃料的物理化学性质发生大的波动。
◆分析与判断的失误,导致调整方向的错误。
◆意外事故。
包括设备事故与有关环节的误操作两个方面。
3.失常炉况的种类低料线、悬料、炉墙结厚、炉缸堆积、炉冷、炉缸冻结、高炉结瘤等。
4.低料线高炉用料不能及时加入到炉内,致使高炉实际料线比正常料线低0.5m或更低时,即称低料线。
◆低料线的原因:①上料设备及炉顶装料设备发生故障。
②原燃料无法正常供应。
③崩料、坐料后的深料线。
◆低料线的危害:①破坏炉料的分布,恶化了炉料的透气性,导致炉况不顺。
②炉料分布被破坏,引起煤气流分布失常,煤气的热能和化学能利用变差,导致炉凉。
③低料线过深,矿石得不到正常预热,势必降低焦炭负荷,使焦比升高。
④炉缸热量受到影响,极易发生炉冷,风口灌渣等现象,严重时会造成炉缸冻结。
⑤炉顶温度升高,超过正常规定,烧坏炉顶设备。
⑥损坏高炉炉衬,剧烈的气流波动会引起炉墙结厚,甚至结瘤现象发生。
⑦低料线时,必然采取赶料线措施,使供料系统负担加重,操作紧张。
◆低料线的处理:①由于上料设备系统故障不能拉料,引起顶温高,开炉顶喷水或炉顶蒸汽控制顶温,必要时减风。
②不能上料时间较长,要果断停风。
造成的深料线(大于4 m),可在炉喉通蒸汽情况下在送风前加料到4m以上。
沙钢2500m^3高炉风口小套磨损的原因及对策

【Abstract】 IntheinitialstageofthesecondcampaignlifeofShasteel’s2500m3blast furnace,heavywearwasoccurredinthelowerpartoftheinnerwallofsometuyeresmallsleeves, whichappearedasravineshapeabrasion.Itwasanalyzedthattheabrasionwasformedbycoal particlefriction.Atthesametime,itwasfoundthatthecoallancewasdeformedonabrasivetuyere, andthattheoutletofcoallancewasdeviatedfrom thecenterlineoftuyere.Byusingnumerical simulationmethod,themovementofpulverizedcoalundertwoworkingconditions,i.e.,coincidence oftheoutletofcoallancewiththecenterlineoftuyereordeviationdownward,wascomparedand analyzed.Researchresultsshowedthatwhentheoutletofcoallancedeviatedfrom thecenterlineof tuyere,thecontactbetweenpulverizedcoalattheoutletofcoallanceandthelowerpartoftuyere innerwallwasthemaincauseoftuyerewear.From furtherstudyonthecausesofcoallance deformationitwasfoundoutthatafteroverhaulingoftheblastfurnace,thediameterofthecoallance doubled,buttheflow rateofcarriergasdidnotincreasecorrespondingly.From thenumerical calculationofcoolingintensityofthecoallanceunderdifferentcarriergasflowratesitwasfoundthat thecarriergasflow ratewasrelativelysmall, sothecoolingintensityofthecoallancewas insufficient,whichledtothedeformationofthecoallance.Accordingly,afteradoptionofthe measuresofincreasingflowrateofcarriergas,thecoallancedeformationandthetuyeresmallsleeve abrasionwereeffectivelycontrolled.
- 1、下载文档前请自行甄别文档内容的完整性,平台不提供额外的编辑、内容补充、找答案等附加服务。
- 2、"仅部分预览"的文档,不可在线预览部分如存在完整性等问题,可反馈申请退款(可完整预览的文档不适用该条件!)。
- 3、如文档侵犯您的权益,请联系客服反馈,我们会尽快为您处理(人工客服工作时间:9:00-18:30)。
480m3 高炉风口小套频繁烧损的原因分析及探讨
第一炼铁厂生产科李霏
风口小套频繁烧损的生产现状始终是困扰我公司炼铁厂生产指标的瓶颈问题。
为解决此问题,公司各层领导及技术人员对此进行过多次的研讨分析,进行过相关措施进行预防,但收效甚微。
现笔者根据老区480m3高炉7、8月的风口套烧损情况及风口套烧损机理探讨如下,仅为个人观点,不足之处在所难免,仅供参考。
一、风口套烧损的情况分类。
风口套烧损机理可分为熔损、破损和磨损三类。
实际观察来看,我单位大部分为渣铁侵蚀滴落后造成的熔损,少部分为本身材质或焊接质量不合格造成的破损和磨损。
风口所处的工作环境恶劣,部分质量过关的风口套在热梯度的作用下,也有可能造成裂纹或渗漏,从而导致漏水。
而破损多发生在风口套本身焊接缝部位,同时可根据烧损后打磨观察,内孔大外孔小的状态即可断定为本身破损,而熔损多为外孔大,内孔小。
因我公司烧损风口的现状绝大部分为铁水滴落熔损,故着重探讨熔损情况的分析及预防。
二、造成风口小套熔损的机理。
造成风口套烧损的原因很多,但最基本的烧损机理即是:风口受热超负荷,冷却介质难以及时传导散热,从而导致风口套温度高于铜质固液相反应的700℃界限温度,当达到铜剧烈氧化的900℃界限温度时,风口很快在高温高压下烧坏漏水。
而影响导热的因素大致有如下几个方面:
1)风口套本身的材质结构。
这包括风口套铜质的纯度、性能,本身结构的合理性。
我单位大都是铜质99%以上的贯流式风口,基本应能满足本级别高炉的风口要求。
2)冷却介质的压力、流量以及流速。
当前各地区的高炉均在强化生产,尤其是民营企业的高炉利用系数和指标都日趋提高。
之前的许多设计参数已难以满足强化冶炼的需求。
我单位的风口套水压0.9-0.8Mpa,水量16-15t/h,均同部分高冶强的同级高炉来比较,只能说是在下限水平。
而对于流速来说,应该保持在7-16m/s,才能满足我单位的高炉生产需求。
(尚未计算,预计为下限值)3)炉缸状况。
高炉炉缸活跃、稳定顺行是炼铁生产顺畅的基本要求。
所以说炉缸无论是产生哪种堆积,对风口套烧损都产生了巨大的影响。
造成炉缸堆积的原因主要有三种:一是低炉温堆积,二是高碱度堆积,三是石墨碳堆积。
在我单位的原燃料条件下,焦炭热强度一般,基本在50-53左右,反应性在30左右,同时入炉矿的转鼓强度较低,基本都在70左右徘徊,由此来看,在原燃料方面有对中心死焦柱不利因素。
另外因烧结碱度波动较大范围(1.5-2.2不等),为保证铁水质量,长期采取碱度上限操作,从而使中心料柱更容易堆积,造成料柱透气透液性变差。
三、操作制度。
1、炉顶布料。
为了保障高炉顺行,在我单位的原燃料条件下,之前各高炉都执行的是有意识的发展边缘的操作方针。
高炉操作人员在布料时在焦矿布料方面基本都是负角差多环布料。
这虽然维持了顺行,但是由于煤气边缘发展,煤气利用率偏低,导致炉内化学热无法充分利用,高炉负荷难以提升,燃料比固然难
以降低,这在成本方面有很大的损失。
同时因边缘煤气的发展,导致炉墙温度升高,渣皮难以稳定,风口回旋区不能纵深到炉缸中心内,炉内料柱必然透气性较差。
更直接的后果就是冷却设施加重了负荷,受气流冲刷严重而难以维持长时间的正常使用。
2、风温。
高风温操作是高炉冶炼工作者追求的目标。
但是如何合理的使用同样要引起重视。
我单位考核风温的混风全关使用率指标,在某种角度上导致高炉操作人为影响炉况波动。
因热风炉的状态不同,透气保温的能力不同,全关混风操作造成了个别高炉在换炉前后的风温风压均波动幅度较大,这样导致高温区变化,渣带波动,渣皮不稳。
3、富氧喷煤。
我单位高炉入炉风量为1450-1480m3/min,风温1150-1180℃,喷煤比约在130-140kg/t水平,按照首钢的风口理论燃烧温度计算公式可知我单位此项参数处于略高水平。
因富氧达2500-3000m3/h即可满足2150℃的合理风口理论燃烧温度值。
超过此数值,将加剧风口前渣铁生成的温度和速度,从而加剧风口前热流交换剧烈,如处于渣铁难以及时渗透过死料柱到达炉缸时,风口前高速的气流将带动积蓄的渣铁对风口套的接触冲刷,从而导致风口套迅速磨损和烧熔。
而稳定的喷煤和富氧使用,避免过多的富氧导致的风口前氧过剩系数过大(超过1.15),对保护风口套有积极意义。
4、渣铁外排。
因客观条件的制约,我单位各高炉的出铁正点率大大低于正常值。
高炉内渣铁不能及时的排出炉外,导致炉内渣铁积攒空间减小,从而导致炉料透气性紧张,而随着渣铁的不均匀不及时的排出,炉内极易在出铁前后料速变化,难行、崩料、低料线等导致软熔带上下波动,渣皮脱落,脱落的渣皮对风口区的冷却设备造成的热负荷波动,机械冲刷等大大提高了风口烧损的机率。
5、碱金属影响。
高炉配吃烧结机头除尘灰,导致碱金属富集循环。
虽然碱金属对风口套无过多的直接影响,但是对焦炭的破损影响不容低估。
而焦炭的强度降低后加剧了炉内料柱的透气性影响,导致渣铁难以及时渗透,从而影响风口区域的传热导热,造成风口套烧损具备了前提。
虽然公司控制了此项因素,但碱金属的及时外排,不是一蹴而就的短期工作,仍需引起足够的重视,应采取措施定期排碱。
6、连续及长期休风的影响。
在这方面的影响下,高炉料柱内呆滞,透液透气性变差,渣铁温度不足,流动性差等都可能造成风口套烧损。
7、其他因素。
包括煤粉的质量、喷煤的风口均匀度等等,都不作为主要因素,但是同样要引起足够的重视,以便为高炉整体稳定顺行提供外部条件的保证。
以上仅是本人在6月底到公司第一炼铁厂工作后,对7月、8月份发生的连续风口套频繁烧损(个数均为60以上)的粗浅分析,现就此分析根据我单位实际提议部分可控措施。
四、预防及改进措施。
1、加强原燃料的筛分。
对高炉入炉料进行全程筛分监控考核。
严格制定和执行槽下清理筛底的工作。
尤其是在雨季,最大限度的避免大量粉末炉料入炉。
减少由此造成的炉料透气性差,炉内压差偏高,边缘气流发展的原料条件。
2、改变布料思路,坚决控制边缘气流。
发展中心气流,控制边缘气流,提高煤气利用率。
这是降成本、稳顺行的重要布料手段。
打透中心,控制边缘,稳定渣皮,严格执行“压边”操作,高炉顺行才有保证。
当然,具体手段及幅度视各炉的具体情况而定。