毕业设计(论文)-液压提升机设计
拖拉机液压提升实验台设计毕业设计

目录摘要 (1)关键词 (1)1前言 (2)1.1选题目的 (2)1.1.1实验一般要求 (2)1.1.2下悬挂点的提升力实验 (2)1.1.3框架上的提升力实验 (2)1.1.4静沉降实验 (3)1.2选题背景 (3)1.3选题意义 (3)1.4研究的主要内容 (4)2 液压缸的计算和选择 (4)2.1液压缸工作压力计算 (4)2.2液压缸缸径和活塞杆直径计算 (5)2.3 液压缸的有效工作面积计算 (5)3 计算液压缸在工作循环各阶段的压力、流量和功率值 (6)3.1上升时液压缸的压力、流量和功率值 (6)3.2下降时液压缸的压力、流量和功率值 (6)4设计液压系统工作原理图 (6)4.1选择基本回路 (6)4.1.1调速回路 (6)4.1.2油路循环形式 (6)4.1.3换向回路 (7)4.1.4压力控制回路 (7)4.2回路合成 (7)5 液压元件的计算和选择 (8)5.1液压泵的选择 (8)5.2电动机的选择 (9)5.3元件、辅件列表 (9)5.4确定油管尺寸 (10)5.5油箱的设计 (10)5.6液位计的选用 (11)5.7过滤器的选用 (12)5.7.1吸油过滤器的选用 (12)5.7.2回油过滤器的选用 (13)6 液压油的选用 (15)7 液压系统性能的验算 (15)7.1回路中压力损失验算 (15)7.1.1上升时压力损失验算 (15)7.1.2下降时压力损失验算 (17)7.2液压泵各阶段的工作压力验算 (20)7.3系统油液温升验算 (20)8机械系统性能的校核 (21)8.1滚动轴承的选用与校核 (21)8.2各部件强度校核 (21)8.2.1油缸连接销剪切强度校核 (21)8.2.2提升架传感器连接销剪切强度校核 (22)8.2.3提升架下悬挂点销轴剪切强度校核 (22)8.2.4 A C杆的抗拉强度校核 (23)8.2.5油缸轴承轨道剪切强度校核 (23)8.2.6地脚螺栓危险截面的拉伸强度校核 (24)8.2.7轨道座和轨道连接块的连接螺栓挤压强度和剪切强度校核 (25)9结论 (26)参考文献 (27)致谢 (28)附录…………………………… (28)拖拉机液压提升实验台设计摘要:此设计是载荷为4吨重的拖拉机液压提升实验台。
机械毕业设计(论文)液压叉车提升机结构设计【全套图纸】
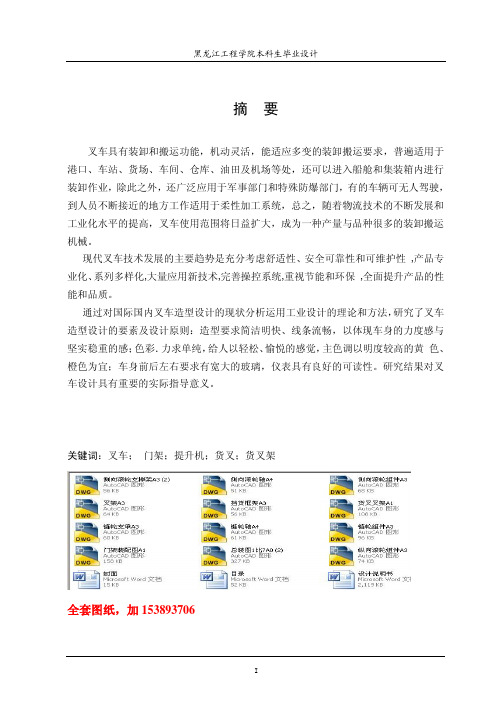
The major trend of modern technology development of the fork truck is to be fully in consideration of the friendly operation, the reliability, the safety, the good maintenance, the specialization, the series, and the diversifiable, and to adopt new technology, to improve steering system, and to focus on energy saving and environment protection in order to promote the truck’s capacity and quality.
液压升降机毕业设计论文

摘要液压升降平台是一种广泛应用于工厂、商店、机关、码头、建筑装修行业的一种高空作业工具。
本设计采用无线遥控,以提高设备操控的自化和灵活性。
其次,本液压升降平台的四个支腿臂的内外伸缩臂设计采用液压缸驱动,节省了人力,提高了平台的工作效率。
再者,本设计较一般液压升降平台改进之处是其升降高度采用传感器监控,提高了其升降的精度。
最后设计过程采用有限元分析的方法,对零部件进行强度校核,优化了零部件的结构。
本设计采用逆向工程的方法,对现有的各种液压升平台比较分析,重点是在传统的结构设计的基础上加以有限元分析;改进一般液压升降平台的线控方式为无线电遥控方式,无线电遥控采用单路八通道遥控方式;在原有液压升降平台的基础上,改进人工拖动液压升降平台的支撑腿为液压缸驱动。
最后本设计取得了预想的效果,有较好的市场前景。
关键词:液压升降平台;无线电遥控;有限元分析;传感器AbstractA hydraulic lifting platform is a tool for high-altitude operations that is widely used in factories, shops and offices, terminals, building decoration industry .The design of a wireless remote control is to enhance the self-control equipment and flexibility.Finally, designing process use finite element analysis, to check the strength of parts and components, and to optimize the structure of the parts.Secondly, the four outrigger arm of the hydraulic lifting platform use the design of the internal and external telescopic boom driven by hydraulic cylinders, saving human resources, improving the efficiency of the platform. Furthermore, the improvement of the design of the hydraulic lifting platform is that sensors monitor is used to accurate the height of platform and improve the accuracy of their movements.This design uses the method of reverse engineering and comparing with the various existing hydraulic platform or , focusing on the traditional design of the structure on the basis finite element analysis, the general improvement of the hydraulic lifting platform for radio-controlled wire way. A radio-controlled remote control one-way four-lane way in the original hydraulic lifting platform on the basis of improving the artificial drag hydraulic lifting platform for the support legs hydraulic cylinder drive.The design has achieved the desired effect,has a bright market prospects Keywords: hydraulic lifting platform; radio control ;finite element analysis; sensors monitor目录摘要 (I)Abstract (II)1 绪论 (1)1.1液压升降平台在机械工业中的应用及相关技术概况 (1)1.1.1 传感技术 (2)1.1.2 遥控技术 (2)1.1.3 有限元分析技术 (3)1.1.4 液压传动技术 (4)1.1.5 液压升降平台在机械行业中的应用 (5)1.2 本课题研究的目的及意义 (6)2 液压系统的方案设计 (7)3 液压系统的参数计算及选型设计 (12)3.1 电动机的选择 (12)3.2 液压泵的设计 (13)3.2.1 齿轮泵的参数计算 (13)3.2.2 齿轮泵的选型设计 (14)3.2.3 齿轮泵使用说明和常见故障 (15)3.3液压缸的设计 (16)3.4 液压元件的选择 (19)3.4.1 液控单向阀的选用 (19)3.4.2 手动换向阀的选用 (20)3.4.3 平衡阀的选用 (22)3.4.4 电磁换向阀的选用 (23)3.4.5 溢流阀的选用 (26)3.4.6 滤油器的选用 (28)3.4.7管路的选用 (30)3.4.8 油箱的选用 (33)4 液压升降平台遥控系统的设计 (35)5 遥控液压升降平台结构设计 (38)5.1遥控液压升降平台内外绞板的设计 (38)5.2 遥控液压升降平台底盘的设计 (43)6 液压升降平台的C语言编程受力分析 (47)7 遥控液压升降平台的有限元分析 (52)参考文献 (57)致谢 (58)附录 (59)1 绪论液压升降平台是一种广泛用于工厂、商店、机关及建筑装修行业,物流产业及机械加工产业的作业工具。
毕业设计--液压升降机
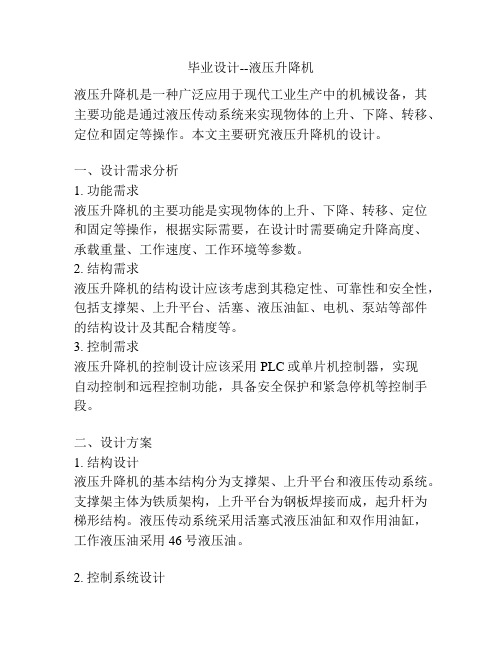
毕业设计--液压升降机液压升降机是一种广泛应用于现代工业生产中的机械设备,其主要功能是通过液压传动系统来实现物体的上升、下降、转移、定位和固定等操作。
本文主要研究液压升降机的设计。
一、设计需求分析1. 功能需求液压升降机的主要功能是实现物体的上升、下降、转移、定位和固定等操作,根据实际需要,在设计时需要确定升降高度、承载重量、工作速度、工作环境等参数。
2. 结构需求液压升降机的结构设计应该考虑到其稳定性、可靠性和安全性,包括支撑架、上升平台、活塞、液压油缸、电机、泵站等部件的结构设计及其配合精度等。
3. 控制需求液压升降机的控制设计应该采用PLC或单片机控制器,实现自动控制和远程控制功能,具备安全保护和紧急停机等控制手段。
二、设计方案1. 结构设计液压升降机的基本结构分为支撑架、上升平台和液压传动系统。
支撑架主体为铁质架构,上升平台为钢板焊接而成,起升杆为梯形结构。
液压传动系统采用活塞式液压油缸和双作用油缸,工作液压油采用46号液压油。
2. 控制系统设计液压升降机的控制系统主要包括控制器、传感器、电机和液压泵站等部件。
控制器采用PLC控制器,传感器采用压力传感器和限位开关,电机采用交流电机,液压泵站采用单联泵和双联泵,控制手段包括自动控制和远程控制。
三、设计计算和实验1. 承载重量计算液压升降机承载重量应根据其使用环境而定,计算公式如下:P=F×S其中,P为承载重量,F为升降杆所能承受的最大力,S为杆长。
2. 液压系统参数计算根据升降高度、承载重量和工作速度等参数,计算液压油缸和油泵的合适参数,包括工作压力、液压缸直径、液压油缸行程、油泵排量和功率等。
3. 实验验证为了验证设计的合理性和实现最优化设计,进行实验验证是非常必要的。
通过实验观察液压升降机的升降高度、承载重量、工作速度及其控制等方面的性能指标。
四、设计总结本文讨论了液压升降机的设计需求分析、设计方案、计算和实验等方面,设计结果表明,设计的液压升降机具有稳定性、可靠性和安全性等优点。
(完整版)典型液压系统汽车起重机液压系设计毕业设计论文
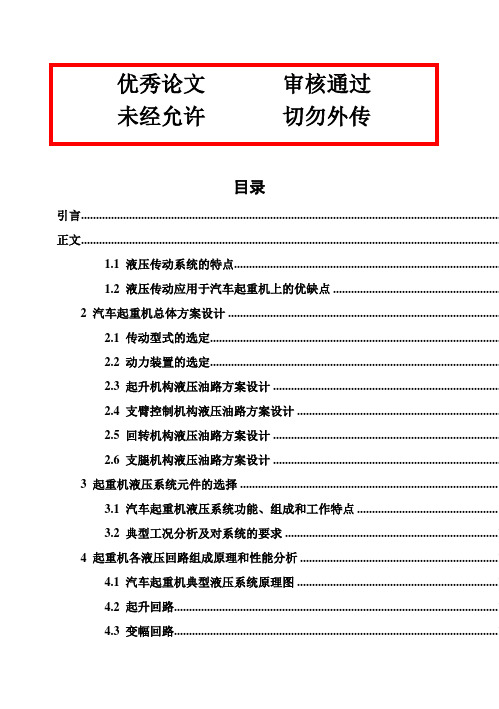
优秀论文审核通过未经允许切勿外传目录引言............................................................................................................................................正文............................................................................................................................................1.1 液压传动系统的特点.........................................................................................1.2 液压传动应用于汽车起重机上的优缺点 ........................................................2 汽车起重机总体方案设计 ...........................................................................................2.1 传动型式的选定.................................................................................................2.2 动力装置的选定.................................................................................................2.3 起升机构液压油路方案设计 ............................................................................2.4 支臂控制机构液压油路方案设计 ....................................................................2.5 回转机构液压油路方案设计 ............................................................................2.6 支腿机构液压油路方案设计 ............................................................................3 起重机液压系统元件的选择 ......................................................................................3.1汽车起重机液压系统功能、组成和工作特点 ...............................................3.2 典型工况分析及对系统的要求 (1)4 起重机各液压回路组成原理和性能分析 (1)4.1 汽车起重机典型液压系统原理图 (1)4.2 起升回路 (1)4.3 变幅回路 (1)4.4 伸缩回路 (1)4.5 回转回路 (1)4.6 支腿回路 (1)4.7 制动回路 (1)5 起重机液压系统的常见故障及预防 (2)5.1 起重机液压系统的主要故障 (2)5.2 汽车起重机液压系统故障的预防 (2)5.3 起重机液压系统故障的排除 (2)结论 (2)致谢 (2)参考文献 (2)引言汽车起重机是各种工程建筑广泛应用的起重设备,是用来对物料进行起重、运输、装卸或安装等作业的机械设备,在工业和民用建筑中作为主要施工机械而得到广泛运用。
毕业设计(论文)-矿井提升机的选型设计及电气控制
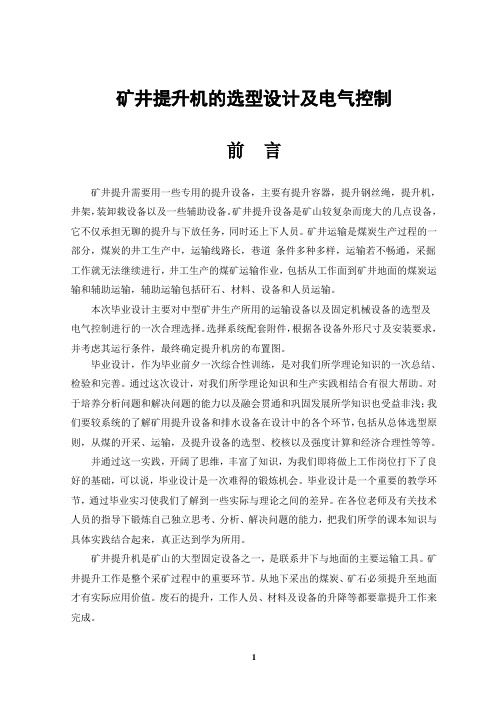
矿井提升机的选型设计及电气控制前言矿井提升需要用一些专用的提升设备,主要有提升容器,提升钢丝绳,提升机,井架,装卸载设备以及一些辅助设备。
矿井提升设备是矿山较复杂而庞大的几点设备,它不仅承担无聊的提升与下放任务,同时还上下人员。
矿井运输是煤炭生产过程的一部分,煤炭的井工生产中,运输线路长,巷道条件多种多样,运输若不畅通,采掘工作就无法继续进行,井工生产的煤矿运输作业,包括从工作面到矿井地面的煤炭运输和辅助运输,辅助运输包括矸石、材料、设备和人员运输。
本次毕业设计主要对中型矿井生产所用的运输设备以及固定机械设备的选型及电气控制进行的一次合理选择。
选择系统配套附件,根据各设备外形尺寸及安装要求,并考虑其运行条件,最终确定提升机房的布置图。
毕业设计,作为毕业前夕一次综合性训练,是对我们所学理论知识的一次总结、检验和完善。
通过这次设计,对我们所学理论知识和生产实践相结合有很大帮助。
对于培养分析问题和解决问题的能力以及融会贯通和巩固发展所学知识也受益非浅;我们要较系统的了解矿用提升设备和排水设备在设计中的各个环节,包括从总体选型原则,从煤的开采、运输,及提升设备的选型、校核以及强度计算和经济合理性等等。
并通过这一实践,开阔了思维,丰富了知识,为我们即将做上工作岗位打下了良好的基础,可以说,毕业设计是一次难得的锻炼机会。
毕业设计是一个重要的教学环节,通过毕业实习使我们了解到一些实际与理论之间的差异。
在各位老师及有关技术人员的指导下锻炼自己独立思考、分析、解决问题的能力,把我们所学的课本知识与具体实践结合起来,真正达到学为所用。
矿井提升机是矿山的大型固定设备之一,是联系井下与地面的主要运输工具。
矿井提升工作是整个采矿过程中的重要环节。
从地下采出的煤炭、矿石必须提升至地面才有实际应用价值。
废石的提升,工作人员、材料及设备的升降等都要靠提升工作来完成。
提升设备的安全运行,不仅直接影响整个矿井生产,而且涉及人身安全。
液压升降机设计 毕业论文

液压升降机设计摘要本次设计的题目是全液压升降机的设计,它主要包括三个部分的内容:主机的设计,液压系统的设计,控制部分的设计。
在本设计中将液压系统的设计做为主要的内容进行设计,主机的设计根据升降台工作时的主要工作部件进行大概的估算。
液压系统的设计又主要包括了动力源,控制元件,执行元件,辅助元件的设计。
控制部分的设计为附加部分,主要设计控制电路图。
关键字:升降机液压系统执行元件ABSTRACTThis design topic is the entire plunger elevator design, it mainly includes three partial contents: Host computer design, hydraulic system design, control section design. Makes in this design the hydraulic system design for the main content carries on the design, time the host computer design basis shengjiangtai work main working part carries on the general estimate. The hydraulic system design has mainly included the power supply, checks the part, the functional element, auxiliary part design. The control section design for supplements the part, mainly designs the check circuit diagram.Keywords: Elevator hydraulic system functional element目录摘要 (1)ABSTRACT (2)第 1 章绪论 (5)第 2 章液压升降机的设计 (7)2.1升降机为全液压系统,相关工艺参数为: (7)2.2工况分析 (7)2.3升降机机械结构形式和运动机理 (7)2.4升降机的机械结构和零件设计 (8)2.5升降机系统的设计 (20)2.6执行元件速度和载荷 (21)2.7速度和载荷计算 (21)第 3 章液压系统方案的拟定 (25)3.1系统压力的初步确定 (25)3.2液压执行元件的主要参数 (25)3.3油路循环方式的分析和选择 (30)3.4开式系统油路组合方式的分析选择 (31)3.5调速方案的选择 (31)3.6液压系统原理图的确定 (32)3.7油泵和电机选择 (32)3.8控制阀的选用 (36)3.9管路,过滤器,其他辅助元件的选择计算 (38)3.10液压元件的连接 (40)第 4 章油箱及液压缸的设计 (42)4.1油箱的容积 (42)4.2缸筒 (44)4.3活塞和活塞杆 (48)4.4活塞杆导向套 (49)4.5排气装置 (50)4.6进出油口尺寸的确定 (50)4.7密封结构的设计选择 (51)4.8性能验算 (51)总结 (53)致谢..................................................................... 错误!未定义书签。
毕业设计--液压升降机

目录摘要 (2)一.设计题目 (5)二.工况分析 (6)三.拟定液压系统原理 (8)四.机械系统设计方案 (13)五.液压系统设计方案 (23)六.PLC设计 (35)七.总结 (45)八.参考文献 (46)摘要液压传动相对于机械传动来说,是一门发展较晚的技术。
自18世纪末英国制成世界上第一台水压机算起,液压传动技术只有二三百年的历史。
直到20世纪30年代它才较普遍地用于起重机、机床及工程机械。
在第二次世界大战期间,由于战争需要,出现了由响应迅速、精度高的液压控制机构所装备的各种军事武器。
第二次世界大战结束后,战后液压技术迅速转向民用工业,液压技术不断应用于各种自动机及自动生产线,从而使它在机械制造、工程机械、农业机械、汽车制造等行业得到推广应用。
机电专业课程设计环节是为了学生能够更好地巩固和实践所学专业知识而设置的,在本次课程设计中,我们以机电传动控制以及液压与气压传动中所学知识为基础,设计了压块机液压及控制系统。
本系统的液压系统主要由液压缸,换向阀,溢流阀,压力继电器,插装阀及各类泵组成,能实现颗粒散料的压制加工。
PLC控制部分主要由定时器,继电器及行程开关组成,对整个液压系统的起控制作用论文介绍了应用PLC技术对升降平台液压系统进行控制的设计方法和实现过程。
采用PLC控制,提高了该机器的可靠性,降低了人力成本,提高了企业的经济效益。
由于该行业在生产过程中,要求提高生产自动化。
若完全采用液压控制,这种控制方式电子线路复杂、继电器使用数量多,造成电气控制部分可靠性差、故障率高,日常维护量大。
随着可编程控制器(PLC)技术的发展,把PLC 控制技术应用于装药机液压装置的控制中,取代原有的液压装置控制线路。
简化了电器控制电路,提高了可靠性,取得了很好的使用效果。
并且易于修改控制程序,提高了控制系统的可扩展性。
关键字:升降平台,液压控制,可编程控制器,可靠性。
AbstractRelative to the hydraulic mechanical transmission, it is a late development of the technology. Since the 18th century the British made the world's first counting hydraulic press, hydraulic drive technology is only two or three hundred years of history. 30 years until the 20th century it was more commonly used in cranes, machine tools and construction machinery. During World War II, the War, emerged from the rapid response and high precision hydraulic control agencies of various military weapons and equipment. After World War II, after the war quickly to civilian industrial hydraulic technology, hydraulic technology continues to apply all kinds of automatic machines and automatic production lines, making it the machinery, engineering machinery, agricultural machinery, automotive manufacturing and other industries promote the useof .60 years since the 20th century, with the hydraulic technology of atomic energy, space technology, computer technology and rapid development and penetration into various industrial fields. Hydraulic technology has begun to high-speed, high-pressure, high power, high efficiency, low noise, durable, highly integrated direction. At the same time, new hydraulic components and hydraulic systems computer-aided design (CAD), computer-aided test (CAT), computer direct control (CDC), mechanical and electrical integration technologies, reliability, technology, and also the current hydraulic drive and control technology development and research direction.This paper describes the application of PLC technology to charge hydraulic system to control the design and implementation process.With PLC control and improve the reliability of the machine, reducing labor costs and improve the economic efficiency of enterprises.As the industry in a high risk of the production process, for greater automation.If the total hydraulic control, this control complex electronic circuits, relays quantity, resulting in poor reliability of electrical control failure rate, large amount of routine maintenance.With the programmable logic controller (PLC) technology, the PLC control technology in charge of hydraulic control device to replace the hydraulic control circuit devices.Simplifies the electrical control circuit, improved reliability, made good use of effects.And easy to change control procedures and improve the control system scalability.Key words:Charge Machine,Hydraulic control,PLC,Reliability.一.设计题目设计一液压顶升工作台及控制系统,该液压缸采用竖直放置,工进速度为0.2m/min,最大采用PLC控制,使其可以顺利完成工作状态及任意位置停止,整个顶升工作台可实现手动和自动的转换,并利用PLC完成顶升动作的自动循环,其动作为电机启动——>顶升装置快速上行——>行程开关——>顶升装置慢速上行——>行程开关——>顶升装置停留——>定时器20秒——>装/卸载重物——>压力传感器——>顶升装置慢速下降——>限位开关——>停止需要考虑以下特殊工况:1 顶到极限位置时,保持系统压力防止顶升物下滑;2 工作中,突遇断电情况,保持系统压力防止顶升物下滑;3 在任意位置需要停机时,保持系统压力防止顶升物下滑;4 故障自动停机,将顶升物锁在当前位置。
2015毕业设计(小型剪叉式液压升降机)DOC
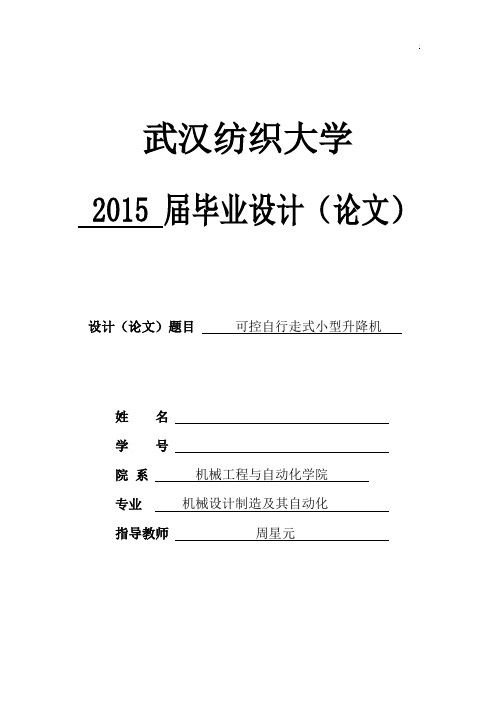
昆明学院毕业设计小型剪叉式液压升降机武汉纺织大学2015 届毕业设计(论文)设计(论文)题目可控自行走式小型升降机姓名学号院系机械工程与自动化学院专业机械设计制造及其自动化指导教师周星元摘要在设计机械结构时,采用剪叉式结构。
剪叉式机械结构,使升降机起升有较高的稳定性,宽大的作业平台,使高空作业范围更大。
它使高空作业效率更高,安全更保障。
在设计液压系统时,为了能使升降机在任何情况下工作,采用双电机带动液压泵,一个直流电机,工作电压为48V;一个交流电机,工作电压为220V。
液压泵采用柱塞泵,电磁换向阀采用三位三通阀,上升动力来源于液压液压泵,下降动力来源于工作人员和升降机自身的压力。
在设计控制电路时,要有限位和自锁装置,并设计交直流换向开关和充电开关。
关键词:剪叉式,液压系统,控制开关。
AbstractIn the design of mechanical structure, the scissor structure. Scissor mechanical structure, make elevator lifting a higher stability, wide operation platform, make more aerial work scope. It makes aerial work more efficient, safe and more security.In the design of hydraulic system, in order to enable elevator in any case work, the two motor drive hydraulic pump, a dc motor, working voltage of 48 V; A ac motor, working voltage of 220 V. Hydraulic pump the piston pump, electromagnetic reversing valves using three three-way valve, rising power comes from the hydraulic pump, drop power comes from the staff and lift their stress.In the design the control circuit, a limited and lock device since, and design ac/dc reversing switch and charging switch.Keywords: scissor, hydraulic system, control switch.目录摘要 (1)第一章概述 (5)1.1 升降机概述 (5)1.1.1 什么是升降机 (5)1.1.2 升降机的发展历史 (5)1.2 液压升降机的作用和特点 (6)1.2.1 液压升降机的作用 (6)1.2.2 液压升降机的特点 (6)1.3 铝合金液压升降机 (6)1.3.1 铝合金液压升降机的特点 (6)1.3.3 本设计的基本参数 (7)1.3.4 剪叉式铝合金液压升降机 (7)第二章受力分析 (9)2.1 结构分析 (9)2.1.1 第四层剪叉臂受力分析 (10)2.1.2 第三层剪叉臂受力分析 (11)2.1.3 第二层剪叉臂受力分析 (12)2.1.3 第一层剪叉臂受力分析 (13)第三章结构设计 (15)3.1 材料的选用 (15)3.1.1 选用材料的性能系数 (15)3.2 强度校核计算 (15)3.2.1 剪叉臂的抗弯强度校核计算 (15)3.2.2 连接螺栓的抗剪强度计算 (18)3.3 工作平台的设计 (19)3.3.1 结构设计 (19)3.3.2 强度校核设计 (19)3.4底座的设计 (20)3.4.1底座的框架设计 (20)3.4.2轮子的设计 (21)3.4.3支撑架的设计 (22)3.5导轨的设计 (24)3.6工作状态的锁紧装置 (26)第四章液压系统设计 (27)4.1液压传动简介 (27)4.2液压传动的组成及工作原理 (27)4.3液压泵的设计 (28)4.3.1液压泵站的选用 (28)4.4液压油管的选用 (32)4.4.1高压钢丝编织胶管介绍 (33)4.5液压控制阀 (34)4.6液压缸的设计 (35)4.6.1液压缸压力计算(单作用柱塞缸的计算) (35)4.6.2液压缸的行程计算 (37)4.6.3液压缸的选用 (38)4.7升降机上升速度的计算 (38)第五章电路设计 (40)5.1总电路图 (40)5.2 48V充电电路图 (40)参考文献 (42)致谢 (43)附图 (44)第一章概述1.1 升降机概述1.1.1 什么是升降机升降机是一种将人或者货物升降到某一高度的升降设备。
提升机毕业设计

摘要提升机是工业生产中一种常见的机械,具有悠久的发展历史,本次设计的提升机为用途专一的,专为在生产线上提升RM6机芯而设计,属于起重机范畴,提升重量和高度都有限,体积较大。
提升机用于在生产过程中提升RM6机芯,RM6机芯重达600kg,需要提升的高度为300mm,本机主要用电机通过螺旋传动来提升机芯,工人可以通过手来沿导轨平行移动机芯,也可以通过手柄来旋转机芯,通过这些可以控机芯的位置。
本机还有断电自锁功能,但本机体积大,只适于在生产线等固定地点工作。
设计用solidworks建模,生产图纸用cad编辑。
关键词:提升机;起重机;solidworks;cadAbstractHoist is a common industrial production of machinery,With a long istory,The design of the machine for purposes of ascension spent,Designed for in the production line ascension RM6 machine core and design ,decension weight and height are limited,Large size.The machine used to ascend in the process of production RM6 ascensionmovement ,Weighing 600 kg RM6 movement,The need to increase the height is 300 mm, This machine is mainly used to ascend through screw transmission motor acrylic,Workers can by hand along the guide parallel mobile movement Also through the handle to rotate the machine, through these can control the position of the movement,It also has the power function lock,But the machine is big, only comfortable in line, the fixed place work. Design with solidworks modeling, production drawings with cad editor.Key words:1 概述1.1 我国提升机发展概况国内提升机的发展经过了从开始的模仿设计,到现在的自主设计、自主制造,已经发展到皮带式、环链式、钢丝绳芯、板链型等一系列,多种类型、几十个型号的产品。
提升机毕业设计

提升机毕业设计提升机毕业设计随着现代工业的发展,提升机作为一种重要的机械设备,被广泛应用于各个行业中。
提升机的设计和优化对于提高生产效率、降低人力成本具有重要意义。
在毕业设计中,提升机的设计是一个具有挑战性和实践性的任务。
本文将探讨提升机毕业设计的一些关键因素和方法。
首先,提升机的设计需要考虑的因素很多。
首先是物料的特性,包括物料的形状、尺寸、重量、粘度等。
不同的物料对提升机的要求也不同,因此需要根据物料的特性选择合适的提升机类型和参数。
其次是工作环境的条件,包括温度、湿度、粉尘等。
这些条件会影响提升机的工作效率和寿命,因此需要在设计中考虑到这些因素。
此外,还需要考虑到工作场所的空间限制和安全要求。
在提升机的设计过程中,可以采用一些常见的方法和技巧来提高设计效果。
首先是利用计算机辅助设计软件进行模拟和优化。
通过建立提升机的数学模型,可以对不同的设计方案进行模拟和比较,从而选择最优的设计方案。
其次是进行实验验证。
通过在实验室或现场进行试验,可以验证设计方案的可行性和效果。
同时,还可以通过实验获得一些实际数据,用于进一步优化设计。
此外,还可以借鉴已有的提升机设计和经验,结合自身的需求进行改进和创新。
在提升机毕业设计中,除了设计本身,还需要考虑到一些细节和问题。
首先是材料的选择和加工工艺。
提升机的各个部件需要选择合适的材料,并采用适当的加工工艺,以确保其性能和寿命。
其次是装配和调试。
在设计完成后,还需要进行装配和调试工作,以确保提升机能够正常运行。
此外,还需要进行一些安全和可靠性的考虑,以保证提升机的使用安全和稳定。
最后,提升机毕业设计的成功与否,不仅仅取决于设计本身,还取决于团队的合作和沟通。
在设计过程中,团队成员之间需要密切合作,及时沟通,共同解决问题。
此外,还需要与相关的专家和企业进行合作,获得他们的指导和支持。
只有通过团队的努力和合作,才能最终完成一个优秀的提升机毕业设计。
综上所述,提升机毕业设计是一个具有挑战性和实践性的任务。
钢坯提升机称重液压系统的设计 毕业设计

摘要钢铁企业以其特有的生产方式和特有的原料与产品,使其与称重计量有着密不可分的联系。
在钢铁企业里的所有计量工作中,称重计量放在重中之重。
而在我国工业企业里唯有冶金企业对称重计量要求更为突出。
抓好冶金企业的称重计量工作是冶金生产顺行与发展的需要。
本设计主要是对钢坯提升机称重液压系统的设计。
其液压系统中的执行机构动作和系统的稳定将直接影响到称重精度,如果液压系统中的执行机构出现不稳定或者液压系统出现不稳定将会对称重精度和设备带来严重的后果。
根据对钢坯提升机称重液压系统工艺要求,在生产过程中液压系统要完成以下动作,液压缸:快速提升;液压缸:缓慢提升;液压缸:停止(电子称重设备称重);液压缸:缓降;液压缸:快降;液压缸:停止(完成一个称重周期)。
钢坯提升机称重系统主要是轧钢厂用于称量进入加热炉钢坯的重量,以便为检查、分析钢坯在加热过程中的烧损情况,而为精确计算成材率,提供参考数据的装置。
考虑由于钢坯表面的氧化皮受提升机振动的影响而脱落在压力应变电阻片(电子称重设备)上,影响称重精度,导致其不能正常使用。
采用钢坯提升机称重系统能很好的处理由钢坯氧化脱落带来的影响。
几亿吨的铁矿石和辅料,经过多道工艺周转变成近亿吨钢材,每一步都承受着巨额计量。
从排岩到采矿,从磨矿到选矿和铁精矿输出,从烧结的配料到烧结矿的输出,从炼铁的配料到铁水的输出,从炼钢的配料到连铸坯的形成,钢材的轧制与输出,它们承受着最大的计量数额。
关键词:称重计量;液压系统;精确计算;钢坯提升AbstractIron and steel enterprises with its unique mode of production and unique raw materials and products to match the weight measurement is inextricably linked. Weight measurement on the top priority in all metrological work in the iron and steel enterprises. Only metallurgical enterprises in China's industrial enterprises, more prominent weight measurement requirements. Anterograde and development of metallurgical production needs to grasp the weight measurement of the metallurgical enterprises.This design is the design billet hoist weighing the hydraulic system. Executive body movements and stability of the system in its hydraulic system will directly affect the weighing accuracy, if the implementing agency in the hydraulic system instability or hydraulic system instability will have serious consequences for weighing accuracy and equipment. Billet upgrade a machine weighing hydraulic system process requirements, the hydraulic system to complete the following actions in the production process, hydraulic cylinders: rapid promotion; hydraulic cylinder: slow improvement; hydraulic cylinder: stop (electronic weighing equipment, weighing); hydraulic cylinder : slow down; hydraulic cylinder: quick drop; hydraulic cylinder: stop (completion of a weighing cycle).The billet hoist weighing system is to enter the weight of the furnace and billet rolling mills used for weighing, in order to check the analysis of the burning of steel billet in the heating process for the accurate calculation of the finished product rate, to provide reference data for the device. Consider off in the pressure strain resistance film (electronic weighing devices) on the hoist vibration due to the slab surface oxide, affect weighing accuracy, and result from normal use.Hundreds of millions of t of iron ore and accessories, multi-channel technology turnover into a hundred million t of steel, every step under a huge amount of measurement. From the row of rocks to the mining, dressing and iron ore concentrate output from the grinding, sintering ingredients to the output of the sinter from ironmaking ingredients to the hot metal output from the steel-making ingredients to the formation of billet, steel rolling and output them to withstand the greatest amount of measurement.Keywords: Weight measurement; Hydraulic system; Accurate calculation; Billet lifting目录前言 (1)1 系统设计方案的确定 (2)1.1设计要求 (2)1.11 液压系统控制的机械动作 (2)1.2主要技术参数 (2)1.3系统驱动方案的选择 (2)1.4控制方式 (3)1.5 草拟液压系统原理图 (3)2 执行元件主要参数的计算与选型 (4)2.1液压缸计算与选型 (4)2.1.1 液压缸主要参数计算与选型 (4)2.1.2 液压缸校核 (5)3 泵与电机 (6)3.1泵的计算 (6)3.1.1 确定泵的工作压力 (7)3.1.2 确定泵的流量 (7)3.1.3 泵的安装 (7)3.2电机的选择 (8)4 液压元件的选择 (8)4.1泵入口液压阀的选择 (9)4.1.1 溢流阀的选择 (9)4.1.2 截止阀及减震喉管的选择 (9)4.1.3 单向阀的选择 (9)4.2执行元件控制阀的选择 (9)4.2.1 提升液压缸回路阀的选择 (9)5 辅助元件的选择计算 (10)5.1油箱的设计 (10)5.1.1 油箱尺寸的确定 (11)5.1.2 油箱安装 (12)5.2工作介质的选择 (12)5.3冷却器的选择与计算 (12)5.4加热器 (14)5.5管路选择 (15)5.6吸油过滤器的选择 (16)5.7回油过滤器的选择 (17)5.8空气滤清器的选择 (17)5.9液位液温计的选择 (18)5.10压力表的选择 (18)5.11联轴器的选择 (18)5.12放油阀的选择 (18)5.13隔板 (18)5.14油箱清洗端盖 (18)5.15液压系统的日常维护和定期检查 (19)6 控制阀块的设计 (19)6.1.1 设计原则 (19)6.1.2 控制阀安装 (20)6.1.3 注意事项 (20)结论 (20)参考文献 (21)致谢 (22)前言钢铁企业以其特有的生产方式和特有的原料与产品,使其与称重计量有着密不可分的联系。
提升机毕业设计
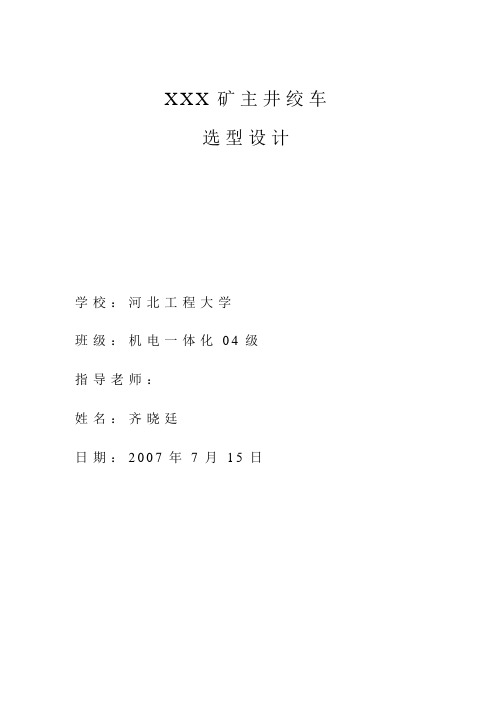
X X X矿主井绞车选型设计学校:河北工程大学班级:机电一体化04级指导老师:姓名:齐晓廷日期:2007年7月15日目录前言第一章井田概况和地质特征第一节井田概述第二节地质特征第二章井田开拓第一节井田境界及储量第二节矿井设计生产能力及服务年限第三章提升设备选型计算第一节提升容器选择计算第二节提升钢丝绳选择计算第三节提升机和天轮选择计算第四节提升机与井筒相对位置计算第五节提升电动机的初选计算第六节提升系统变位质量计算第七节提升设备的运动学计算第八节提升设备的动力学计算第九节提升电动机容量的计算第十节设备的电耗及效率的计算第四章电动机转子串电阻计算第五章提升机拖动控制系统简介第六章设计参考书第七章谢辞前言X X X井田位于峰峰矿区南部,与X X X毗邻,井田内上组煤为焦煤。
交通方便,开发该井田煤层对矿区生产和接续将起积极作用。
为了充分发挥上组煤较丰富的工业储量,矿井设计生产能力45万吨。
由于下组煤受澳灰水威胁,水文地质条件尚待进一步查明,本设计遵循地质报告审批意见,将下组煤储量列为暂难利用的表外储量,暂不考虑开采。
根据井田地质构造和年设计生产能力,按照煤炭开采的有关技术政策,规程规范,尽量提高矿井采、掘、运等机械水平,提高矿井效率和安全程度,提高资源回收率。
本设计的主要内容;矿井年设计能力为45万吨。
井田上组煤工业储量为5250.96万吨,可采储量为3210.277万吨。
矿井上组煤服务年限51年。
采用立井暗斜井开拓方式,工业场地利用原北大峪工业场地。
矿井为单水平开拓,水平标高-390m。
-3.5m水平为立井和暗斜井的转载水平。
矿井采用中央并列抽出式通风系统,并服务于矿井整个生产服务期限内。
大巷运输采用7t架线电机车牵引1t矿车,主暗斜井采用8t箕斗和主井采用3t箕斗提煤。
原副立井改为回风井,新建副井至-3.5m转载水平,并装备1对1宽1窄罐笼,担负矿井辅助提升。
矿井到达设计产量时布置一个生产采区和一个准备采区,装备2个高档工作面和1个普采工作面。
毕业设计(论文)剪叉式液压升降机设计

毕业设计(论文)剪叉式液压升降机设计1前言11课题研究的目的和意义升降机是一种升降性能好适用范围广的货物举升机构可用于生产流水线高度差设备之间的货物运送物料上线下线共件装配时部件的举升大型机库上料下料仓储装卸等场所与叉车等车辆配套使用以及货物的快速装卸等它采用全液压系统控制采用液压系统有以下特点1在同等的体积下液压装置能比其他装置产生更多的动力在同等的功率下液压装置的体积小重量轻功率密度大结构紧凑液压马达的体积和重量只有同等功率电机的122液压装置工作比较平稳由于重量轻惯性小反应快液压装置易于实现快速启动制动和频繁的换向3液压装置可在大范围内实现无级调速调速范围可达到2000还可以在运行的过程中实现调速4液压传动易于实现自动化他对液体压力流量和流动方向易于进行调解或控制5液压装置易于实现过载保护6液压元件以实现了标准化系列化通用化压也系统的设计制造和使用都比较方便当然液压技术还存在许多缺点例如液压在传动过程中有较多的能量损失液压传动易泄露不仅污染工作场地限制其应用范围可能引起失火事故而且影响执行部分的运动平稳性及正确性对油温变化比较敏感液压元件制造精度要求较高造价昂贵出现故障不易找到原因但在实际的应用中可以通过有效的措施来减小不利因素带来的影响12国内研究状况及发展前景我国的液压技术是在新中国成立以后才发展起来的自从1952年试制出我国第一个液压元件齿轮泵起迄今大致经历了仿制外国产品自行设计开发和引进消化提高等几个阶段进年来通过技术引进和科研攻关产品水平也得到了提高研制和生产出了一些具先进水平的产品目前我国的液压技术已经能够为冶金工程机械机床化工机械纺织机械等部门提供品种比较齐全的产品但是我国的液压技术在产品品种数量及技术水平上与国际水品以及主机行业的要求还有不少差距每年还需要进口大量的液压元件今后液压技术的发展将向着一下方向1提高元件性能创制新型元件体积不断缩小2高度的组合化集成化模块化3和微电子技术结合走向智能化总之液压工业在国民经济中的比重是很大的他和气动技术常用来衡量一个国家的工业化水平2工艺参数及工况分析21 升降机的工艺参数本设计升降机为全液压系统相关工艺参数为额定载荷2500kg 最低高度500 mm 最大起升高度1500mm最大高度1700mm 平台尺寸4000x2000mm 电源380v50Hz22工况分析本升降机是一种升降性能好适用范围广的货物举升机构和用于生产流水线高度差设备之间的货物运送物料上线下线工件装配时调节工件高度高出给料机运送大型部件装配时的部件举升大型机库上料下料仓储装卸场所与叉车等装运车辆配套使用即货物的快速装卸等该升降台主要有两部分组成机械系统和液压系统机械机构主要起传递和支撑作用液压系统主要提供动力他们两者共同作用实现升降机的功能3升降机机械机构的设计和计算31 升降机机械结构形式和运动机理根据升降机的平台尺寸参考国内外同类产品的工艺参数可知该升降机宜采用单双叉机构形式即有两个单叉机构升降台合并而成有四个同步液压缸做同步运动以达到升降机升降的目的其具体结构形式图31图31所示即为该升降机的基本结构形式其中1是工作平台2是活动铰链3为固定铰链4为支架5是液压缸6为底座在1和6的活动铰链处设有滑道4主要起支撑作用和运动转化形式的作用一方面支撑上顶板的载荷一方面通过其铰接将液压缸的伸缩运动转化为平台的升降运动1与载荷直接接触将载荷转化为均布载荷从而增强局部承载能力下底架主要起支撑和载荷传递作用它不仅承担着整个升降机的重量而且能将作用力传递到地基上通过这些机构的相互配合实现升降机的稳定和可靠运行两支架在0点铰接支架4上下端分别固定在平台和底座上通过活塞杆的伸缩和铰接点0的作用实现货物的举升32 升降机的机械结构和零件设计com 升降机结构参数的选择和确定根据升降台的工艺参数和他的基本运动机理来确定支架4的长度和截面形状升降台达要求高度时铰链ab的距离其液压缸的工作行程设ab x 则4支架的长度可以确定为即支架和地板垂直时的高度应大于这样才能保证其最大升降高度达到其运动过程中任意两个位置的示意图表示如下图34设支架都在其中点处绞合液压缸顶端与支架绞合点距离中点为t 根据其水平位置的几何位置关系可得下面根据几何关系求解上述最佳组合值初步分析值范围为取值偏小则工作平台ab点承力过大还会使支架的长度过长造成受力情况不均匀X值偏小则会使液压缸的行程偏大并且会造成整个机构受力情况不均匀在该设计中可以选择几个特殊值 04m 06m 08m分别根据数学关系计算出h和t然后分析上下顶板的受力情况选取最佳组合值便可以满足设计要求04支架长度为h 2-x2 18mh2 09m液压缸的行程设为l升降台上下顶板合并时根据几何关系可得到升降台完全升起时有几何关系可得到联合上述方程求得t 0355ml 0545m即液压缸活塞杆与2 杆绞合点与2 杆中com为0545m06支架长度为 2-x2 17mh2 085m液压缸的行程设为l升降台上下顶板合并时根据几何关系可得到lt 09升降台完全升起时有几何关系可得到联合上述方程求得t 032ml 053m即液压缸活塞杆与2 杆绞合点与2 杆中com为053m08支架长度为 2-x2 16mh2 08m液压缸的行程设为l升降台上下顶板合并时根据几何关系可得到升降台完全升起时有几何关系可得到联合上述方程求得t 0284ml 0516m即液压缸活塞杆与2 杆绞合点与2 杆中com为0516m现在对上述情况分别进行受力分析x 04m 受力图如下所示x 06m 受力图如下所示x 08m 受力图如下所示比较上述三种情况下的载荷分布状况x取小值则升到顶端时两相互绞合的支架间的间距越大而此时升降台的载荷为均布载荷有材料力学理论可知此时两支架中点出所受到的弯曲应力为最大可能会发生弯曲破坏根据材料力学中提高梁的弯曲强度的措施知合理安排梁的受力情况可以降低值从而改善提高其承载能力分析上述x com 06mx 08m时梁的受力情况和载荷分布情况可以选择第二种情况即x 06m时的结构作为升降机a的最终值由此便可以确定其他相关参数如下t 032m l 053m h 17mcom 升降机支架和下底板结构com1 上顶板结构和强度校核上顶板和载荷直接接触其结构采用由若干根相互交叉垂直的热轧槽钢通过焊接形式焊接而成然后在槽钢的四个侧面和上顶面上铺装4000x2000x3mm的钢板其结构形式大致如下所示图37沿平台的上顶面长度方向布置4根16号热轧槽钢沿宽度方向布置6根10号热轧槽钢组成上图所示的上顶板结构在最外缘延长度方向加工出安装上下支架的滑槽以便上下支架的安装滑槽的具体尺寸根据上下支架的具体尺寸和结构而定沿长度方向的4根16号热轧槽钢的结构参数为截面面积为理论重量为抗弯截面系数为沿宽度方向的6根10号热轧槽钢的结构参数为截面面积为理论重量为抗弯截面系数为其质量分别为4根16号热轧槽钢的质量为6根10号热轧槽钢的质量为菱形钢板质量为com2 强度校核升降台上顶板的载荷是作用在一平台上的可以认为是一均布载荷由于该平板上铺装汽车钢板其所受到的载荷为额定载荷和均布载荷之和其载荷密度为F钢板和额定载荷重力之和单位Nl 载荷的作用长度单位m沿长度方向为16m宽度方向为12m其中带入数据得F 29604N沿长度方向有带入数据有分析升降机的运动过程可以发现在升降机刚要起升时和升降机达到最大高度时会出现梁受弯矩最大的情况故强度校核只需要分析该状态时的受力情况即可校核如下其受力简图为该升降台有8个支架共有8个支点假设每个支点所受力为N则平很方程可列为即将N带入上式中根据受力图其弯矩图如下所示AB段1850-925BC段3700x-3145-925CD段与AB段对称由弯矩图可知该过程中的最大弯矩为根据弯曲强度理论即梁的最大弯曲应力应小于其许用弯曲应力式中 W 抗弯截面系数沿长度方向为16号热轧槽钢钢的屈服极限n 安全系数 n 3代入数据由此可知强度符合要求升降台升到最高位置时分析过程如下与前述相同弯矩如下FA段925AB段BC段CD段与AB段对称AF段和DE段对称由弯矩图可知该过程中的最大弯矩为根据弯曲强度理论即梁的最大弯曲应力应小于其许用弯曲应力式中 W 抗弯截面系数单位沿长度方向为16号热轧槽钢钢的屈服极限n 安全系数 n 3代入数据由计算可知沿平台长度方向上4根16 号热轧槽钢完全可以保证升降台的强度要求同样分析沿宽度方向的强度要求均布载荷强度为F 钢板及16号槽钢与载荷重力l 载荷作用长度 2x6 12m带入相关数据受力图和弯矩图如下所示由弯矩图知最大弯曲应力为故宽度方向也满足强度要求com3支架的结构支架由8根形状基本相同的截面为矩形的钢柱组成在支架的顶端和末端分别加工出圆柱状的短轴以便支架的安装支架在升降机结构中的主要功能为载荷支撑和运动转化将液压缸的伸缩运动通过与其铰合的支点转化为平台的升降运动支架的结构除应满足安装要求外还应保证有足够的刚度和强度一时期在升降运动中能够平稳安全运行每根支架的上顶端承受的作用力设为N则有等式求得N 3848N分析支架的运动形式和受力情况发现支架在运动过程中受力情况比较复杂它与另一支架铰合点给予底座的固定点的受里均为大小和方向为未知的矢量故该问题为超静定理论问题已经超出本文的讨论范围本着定性分析和提高效率的原则再次宜简化处理简化的原则时去次留主即将主要的力和重要的力在计算中保留而将对梁的变形没有很大影响的力忽略不计再不改变其原有性质的情况下可以这样处理根据甘原则再次对制假所收的力进行分析可以看出与液压缸顶杆联结点的力为之家所受到的最主要的力它不仅受液压缸的推力而且还将受到上顶班所传递的作用力因此与液压缸顶杆相连接的支架所厚道的上顶板的力为它所受到的最主要的力在此将其他的力忽略只计算上顶板承受的由载荷和自重所传递的载荷力计算简图如下所示图311所产生的弯矩为每个支架的支点对上顶板的作用力单位NL 液压缸与支架铰合点距支点之间的距离单位m代入数据假定改支架为截面为长为a宽为b的长方形则其强度应满足的要求是式中 M 支架上所受到的弯矩单位NmW 截面分别为ab的长方形抗弯截面系数所选材料为碳素结构钢将数据代入有求得上式表明只要截面为ab的长方形满足条件则可以满足强度要求取则其符合强度要求这些钢柱的质量为支架的结构还应该考虑装配要求液压缸活塞杆顶端与支架采用耳轴结构连接因此应在两支架之间加装支板以满足动力传递要求com4 升降机底座的设计和校核升降机底座在整个机构中支撑着平台的全部重量并将其传递到地基上他的设计重点是满足强度要求即可保证在升降机升降过程中不会被压溃即可不会发生过大大变形其具体参数见装配图4升降机系统的设计要求液压系统的设计在本升降台的设计中主要是液压传动系统的设计它与主机的设计是紧密相关的往往要同时进行所设计的液压系统应符合主机的拖动循环要求还应满足组成结构简单工作安全可靠操纵维护方便经济性好等条件本升降台对液压系统的设计要求可以总结如下升降台的升降运动采用液压传动可选用远程或无线控制升降机的升降运动由液压缸的伸缩运动经转化而成为平台的起降其工作负载变化范围为02500Kg 负载平稳工作过程中无冲击载荷作用运行速度较低液压执行元件有四组液压缸实现同步运动要求其工作平稳结构合理安全性优良使用于各种不同场合工作精度要求一般5执行元件速度和载荷51执行元件类型数量和安装位置类型选择表51 执行元件类型的选择运动形式往复直线运动回转运动往复摆动短行程长行程高速低速摆动液压马达执行元件的类型活塞缸柱塞缸液压马达和丝杠螺母机构高速液压马达低速液压马达根据上表选择执行元件类型为活塞缸再根据其运动要求进一步选择液压缸类型为双作用单活塞杆无缓冲式液压缸其符号为图51数量该升降平台为双单叉结构故其采用的液压缸数量为4个完全相同的液压缸其运动完全是同步的但其精度要求不是很高安装位置液压缸的安装方式为耳环型尾部单耳环气缸体可以在垂直面内摆动安装的位置为图36 所示的前后两固定支架之间的横梁之上横梁和支架组成为一体通过横梁活塞的推力逐次向外传递使升降机升降52速度和载荷计算com 速度计算及速度变化规律参考国内升降台类产品的技术参数可知最大起升高度为1500mm时其平均起升时间为45s就是从液压缸活塞开始运动到活塞行程末端所用时间大约为45s 设本升降台的最小气升降时间为40s最大起升时间为50s由此便可以计算执行元件的速度v式中 v 执行元件的速度单位msL 液压缸的行程单位mt 时间单位s当时001325当时液压缸的速度在整个行程过程中都比较平稳无明显变化在起升的初始阶段到运行稳定阶段其间有一段加速阶段该加速阶段加速度比较小因此速度变化不明显形成终了时有一个减速阶段减速阶段加速度亦比较小因此可以说升降机在整个工作过程中无明显的加减速阶段其运动速度比较平稳com件的载荷计算及变化规律执行元件的载荷即为液压缸的总阻力油缸要运动必须克服其阻力才能运行因此在次计算油缸的总阻力即可油缸的总阻力包括阻碍工作运动的切削力运动部件之间的摩擦阻力密封装置的摩擦阻力起动制动或换向过程中的惯性力回油腔因被压作用而产生的阻力即液压缸的总阻力也就是它的最大牵引力1切削力根据其概念阻碍工作运动的力在本设计中即为额定负载的重力和支架以及上顶板的重力其计算式为2摩擦力各运动部件之间的相互摩擦力由于运动部件之间为无润滑的钢-钢之间的接触摩擦取其具体计算式为式中各符号意义同第三章3密封装置的密封阻力根据密封装置的不同分别采用下式计算O形密封圈液压缸的推力Y形密封圈f 摩擦系数取p 密封处的工作压力单位Pad 密封处的直径单位m密封圈有效高度单位m密封摩擦力也可以采用经验公式计算一般取4运动部件的惯性力其计算式为式中 G 运动部件的总重力单位Ng 重力加速度单位启动或制动时的速度变量单位ms起动制动所需要的时间单位s对于行走机械取本设计中取值为5背压力背压力在此次计算中忽略而将其计入液压系统的效率之中由上述说明可以计算出液压缸的总阻力为20483161201882500 x98015 2048316120 x 98 20483161201882500 x04 20483161201882500 com40KN液压缸的总负载为40KN该系统中共有四个液压缸个液压缸故每个液压缸需要克服的阻力为10KN该升降台的额定载荷为2500Kg 其负载变化范围为02500Kg在工作过程中无冲击负载的作用负载在工作过程中无变化也就是该升降台受恒定负载的作用6液压系统主要参数的确定61 系统压力的初步确定液压缸的有效工作压力可以根据下表确定表61 液压缸牵引力与工作压力之间的关系牵引力FKN 5 5-10 10-20 20-30 30-50 50 工作压力PMPa 08-10 15-2 25-3 3-4 4-5 5-7由于该液压缸的推力即牵引力为10KN根据上表可以初步确定液压缸的工作压力为p 2MPa62 液压执行元件的主要参数com的作用力液压缸的作用力及时液压缸的工作是的推力或拉力该升降台工作时液压缸产生向上的推力因此计算时只取液压油进入无杆腔时产生的推力F式中 p 液压缸的工作压力 Pa 取pD 活塞内径单位m 009m液压缸的效率 095代入数据FF 103KN即液压缸工作时产生的推力为103KN表61com 缸筒内径的确定该液压缸宜按照推力要求来计算缸筒内经计算式如下要求活塞无杆腔的推力为F时其内径为式中 D 活塞杆直径缸筒内经单位mF 无杆腔推力单位NP 工作压力单位MPa液压缸机械效率 095代入数据D 0083mD 83mm 取圆整值为 D 90mm液压缸的内径活塞的的外径要取标注值是因为活塞和活塞杆还要有其它的零件相互配合如密封圈等而这些零件已经标准化有专门的生产厂家故活塞和液压缸的内径也应该标准化以便选用标准件com 活塞杆直径的确定1活塞杆直径根据受力情况和液压缸的结构形式来确定受拉时受压时该液压缸的工作压力为为p 2MPa 5MPa取d 05Dd 45mm2活塞杆的强度计算活塞杆在稳定情况下如果只受推力或拉力可以近似的用直杆承受拉压载荷的简单强度计算公式进行式中 F 活塞杆的推力单位Nd 活塞杆直径单位m材料的许用应力单位MPa 活塞杆用45号钢代入数据63MPa活塞杆的强度满足要求3稳定性校核该活塞杆不受偏心载荷按照等截面法将活塞杆和缸体视为一体其细长比为时在该设计及安装形式中液压缸两端采用铰接其值分别为将上述值代入式中得故校核采用的式子为式中 n 1 安装形式系数E 活塞杆材料的弹性模量钢材取J 活塞杆截面的转动惯量L 计算长度 106m代入数据371KN其稳定条件为式中稳定安全系数一般取 24 取 3F 液压缸的最大推力单位N代入数据 123KN故活塞杆的稳定性满足要求com 液压缸壁厚最小导向长度液压缸长度的确定com1 液压缸壁厚的确定液压缸壁厚又结构和工艺要求等确定一般按照薄壁筒计算壁厚由下式确定式中 D 液压缸内径单位m缸体壁厚单位cm液压缸最高工作压力单位Pa 一般取 12-13p缸体材料的许用应力钢材取代入数据考虑到液压缸的加工要求将其壁厚适当加厚取壁厚com2 最小导向长度活塞杆全部外伸时从活塞支撑面中点到导向滑动面中点的距离为活塞的最小导向长度H如下图所示如果最小导向长度过小将会使液压缸的初始挠度增大影响其稳定性因此设计时必须保证有最小导向长度对于一般的液压缸液压缸最大行程为L缸筒直径为D时最小导向长度为图61即取为72cm活塞的宽度一般取导向套滑动面长度在时取在时取当导向套长度不够时不宜过分增大A和B必要时可在导向套和活塞之间加一隔套隔套的长度由最小导向长度H确定com 液压缸的流量液压缸的流量余缸径和活塞的运动有关系当液压缸的供油量Q不变时除去在形程开始和结束时有一加速和减速阶段外活塞在行程的中间大多数时间保持恒定速度液压缸的流量可以计算如下式中 A 活塞的有效工作面积对于无杆腔活塞的容积效率采用弹形密封圈时 1采用活塞环时098为液压缸的最大运动速度单位ms代入数据即液压缸以其最大速度运动时所需要的流量为以其最小运动速度运动时所需要的流量为7液压系统方案的选择和论证液压系统方案是根据主机的工作情况主机对液压系统的技术要求液压系统的工作条件和环境条件以成本经济性供货情况等诸多因素进行全面综合的设计选择从而拟订出一个各方面比较合理的可实现的液压系统方案其具体包括的内容有油路循环方式的分析与选择油源形式的分析和选择液压回路的分析选择合成液压系统原理图的拟定71 油路循环方式的分析和选择油路循环方式可以分为开式和闭式两种其各自特点及相互比较见下表表71油路循环方式的选择主要取决于液压系统的调速方式和散热条件比较上述两种方式的差异再根据升降机的性能要求可以选择的油路循环方式为开式系统因为该升降机主机和液压泵要分开安装具有较大的空间存放油箱而且要求该升降机的结构尽可能简单开始系统刚好能满足上述要求油源回路的原理图如下所示图7172 开式系统油路组合方式的分析选择当系统中有多个液压执行元件时开始系统按照油路的不同连接方式又可以分为串联并联独联以及它们的组合---复联等串联方式是除了第一个液压元件的进油口和最后一个执行元件的回油口分别与液压泵和油箱相连接外其余液压执行元件的进出油口依次相连这种连接方式的特点是多个液压元件同时动作时其速度不随外载荷变化故轻载时可多个液压执行元件同时动作73 调速方案的选择调速方案对主机的性能起决定作用选择调速方案时应根据液压执行元件的负载特性和调速范围及经济性等因素选择常用的调速方案有三种节流调速回路容积调速回路容积节流调速回路本升降机采用节流调速回路原因是该调速回路有以下特点承载能力好成本低调速范围大适用于小功率轻载或中低压系统但其速度刚度差效率低发热大74 液压系统原理图的确定初步拟定液压系统原理图如下所示见下图8液压元件的选择计算及其连接液压元件主要包括有油泵电机各种控制阀管路过滤器等有液压元件的不同连接组合构成了功能各异的液压回路下面根据主机的要求进行液压元件的选择计算81 油泵和电机选择com定流量和额定压力com1泵的额定流量泵的流量应满足执行元件最高速度要求所以泵的输出流量应根据系统所需要的最大流量和泄漏量来确定。
小型提升机毕业设计

小型提升机毕业设计小型提升机毕业设计在现代工业生产中,提升机是一种非常重要的设备,用于垂直或倾斜地运输各种物料。
它们广泛应用于矿山、建筑工地、港口等场所,提升机的设计和性能对于提高生产效率至关重要。
本文将讨论小型提升机的毕业设计,探讨其结构和功能的优化。
首先,小型提升机的设计必须考虑到其使用环境和物料特性。
在狭小的空间内,提升机的尺寸和重量必须尽可能小,以便适应不同的工作场所。
同时,不同的物料具有不同的特性,如粉状物料、颗粒状物料和块状物料等,提升机的设计必须能够适应这些特性,并确保物料的安全和稳定运输。
其次,小型提升机的结构设计需要考虑到其运输能力和效率。
提升机的运输能力取决于其载重量和升降速度,因此设计师需要合理确定这些参数。
此外,提升机的结构应该简单可靠,易于安装和维修。
采用优质材料和先进的制造工艺,可以提高提升机的耐用性和可靠性。
在小型提升机的毕业设计中,还可以考虑一些创新的功能和技术。
例如,可以引入自动化控制系统,实现提升机的自动化运行和监控。
通过传感器和计算机控制,可以实时监测提升机的工作状态和物料流量,提高运输效率和安全性。
此外,还可以考虑使用节能技术,如变频调速和能量回收等,减少能源消耗和环境污染。
除了结构和功能的优化,小型提升机的毕业设计还应该考虑到成本和经济效益。
提升机的制造成本和维护成本应该尽可能低,以提高设备的竞争力。
同时,设计师还应该考虑到提升机的使用寿命和维修周期,以确保设备的长期可靠运行。
最后,小型提升机的毕业设计还应该注重安全性和环保性。
提升机在运行过程中可能存在一些安全隐患,如物料堵塞、滑轮故障等,设计师需要合理设计安全保护装置,以防止事故的发生。
此外,提升机的运行还会产生一定的噪音和振动,设计师需要采取相应的措施,减少对周围环境和人员的影响。
综上所述,小型提升机的毕业设计需要考虑到结构、功能、成本、安全和环保等多个方面。
通过合理的设计和优化,可以提高提升机的性能和竞争力,满足不同工作场所的需求。
机械毕业设计1033矿井液压提升机多绳摩擦提升机
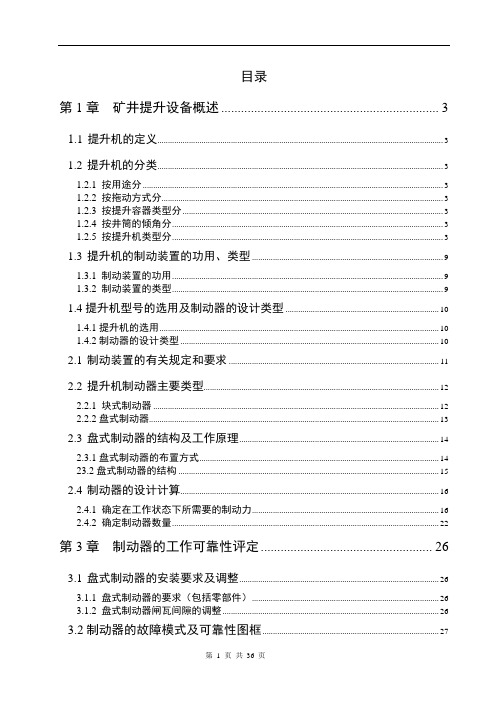
目录第1章矿井提升设备概述 (3)1.1提升机的定义 (3)1.2提升机的分类 (3)1.2.1 按用途分 (3)1.2.2 按拖动方式分 (3)1.2.3 按提升容器类型分 (3)1.2.4 按井筒的倾角分 (3)1.2.5 按提升机类型分 (3)1.3提升机的制动装置的功用、类型 (9)1.3.1 制动装置的功用 (9)1.3.2 制动装置的类型 (9)1.4提升机型号的选用及制动器的设计类型 (10)1.4.1提升机的选用 (10)1.4.2制动器的设计类型 (10)2.1制动装置的有关规定和要求 (11)2.2提升机制动器主要类型 (12)2.2.1 块式制动器 (12)2.2.2盘式制动器 (13)2.3盘式制动器的结构及工作原理 (14)2.3.1盘式制动器的布置方式 (14)23.2盘式制动器的结构 (15)2.4制动器的设计计算 (16)2.4.1 确定在工作状态下所需要的制动力 (16)2.4.2 确定制动器数量 (22)第3章制动器的工作可靠性评定 (26)3.1盘式制动器的安装要求及调整 (26)3.1.1 盘式制动器的要求(包括零部件) (26)3.1.2 盘式制动器闸瓦间隙的调整 (26)3.2制动器的故障模式及可靠性图框 (27)3.3制动器的优化设计及工作可靠性评定 (29)3.3.1 设计变量 (29)3.3.2 优化策略 (29)3.4制动器的维护可靠性评定 (30)第4章结论 (33)致谢 (34)参考文献 (36)第1章矿井提升设备概述1.1 提升机的定义矿井提升机是矿井大型固定设备之一,它的主要任务就是沿井筒提升煤炭、矿石和矸石;升降人员和设备;下放材料和工具等。
矿井提升设备是联系井下与地面的纽带,是主要的提升运输工具,因此它整个矿井生产中占有重要的地位。
1.2 提升机的分类1.2.1 按用途分(1) 主井提升设备主井提升设备的任务是专门提升井下生产的煤炭。
[优秀毕业设计精品]液压升降机设计
![[优秀毕业设计精品]液压升降机设计](https://img.taocdn.com/s3/m/e53e1fa243323968001c9259.png)
错误!未指定书签。
专业错误!未指定书签。
作者姓名指导教师定稿日期:2020年05月29日XXX机械工程系毕业设计(论文)任务书注:此表发给学生后由指导教师填写,学生按此表要求开展毕业设计(论文)工作。
XXX机械工程系毕业设计(论文)成绩表摘要本次设计的题目是全液压升降机的设计,它主要包括三个部分的内容:主机的设计,液压系统的设计,控制部分的设计。
在本设计中将液压系统的设计做为主要的内容进行设计,主机的设计根据升降台工作时的主要工作部件进行大概的估算。
液压系统的设计又主要包括了动力源,控制元件,执行元件,辅助元件的设计。
控制部分的设计为附加部分,主要设计控制电路图。
关键字:升降机液压系统执行元件ABSTRACTThis design topic is the entire plunger elevator design, it mainly includes three partial contents: Host computer design, hydraulic system design, control section design. Makes in this design the hydraulic system design for the main content carries on the design, time the host computer design basis shengjiangtai work main working part carries on the general estimate. The hydraulic system design has mainly included the power supply, checks the part, the functional element, auxiliary part design. The control section design for supplements the part, mainly designs the check circuit diagram.Keywords: Elevator hydraulic system functional element目录摘要 (3)ABSTRACT (4)第 1 章绪论 (7)第 2 章液压升降机的设计 (9)2.1升降机为全液压系统,相关工艺参数为: (9)2.2工况分析 (9)2.3升降机机械结构形式和运动机理 (9)2.4升降机的机械结构和零件设计 (10)2.5升降机系统的设计 (22)2.6执行元件速度和载荷 (23)2.7速度和载荷计算 (23)第 3 章液压系统方案的拟定 (27)3.1系统压力的初步确定 (27)3.2液压执行元件的主要参数 (27)3.3油路循环方式的分析和选择 (32)3.4开式系统油路组合方式的分析选择 (33)3.5调速方案的选择 (33)3.6液压系统原理图的确定 (34)3.7油泵和电机选择 (34)3.8控制阀的选用 (38)3.9管路,过滤器,其他辅助元件的选择计算 (40)3.10液压元件的连接 (42)第 4 章油箱及液压缸的设计 (44)4.1油箱的容积 (44)4.2缸筒 (46)4.3活塞和活塞杆 (50)4.4活塞杆导向套 (51)4.5排气装置 (52)4.6进出油口尺寸的确定 (52)4.7密封结构的设计选择 (53)4.8性能验算 (53)总结 (55)致谢 (56)参考文献 (57)第 1 章绪论这次毕业是学校为我们每个工科学生安排的一次实践性的总结,使就业前的一次大练兵,是对每个学生三年来所学知识的总体检测,使我们为进入工厂工作做好了准备。
- 1、下载文档前请自行甄别文档内容的完整性,平台不提供额外的编辑、内容补充、找答案等附加服务。
- 2、"仅部分预览"的文档,不可在线预览部分如存在完整性等问题,可反馈申请退款(可完整预览的文档不适用该条件!)。
- 3、如文档侵犯您的权益,请联系客服反馈,我们会尽快为您处理(人工客服工作时间:9:00-18:30)。
1 绪论1.1液压提升机概述1.1.1引言液压提升机是利用液压马达直接或通过减速箱来拖动滚筒的一种提升机,液压提升机的用途很广泛,常用于船舶、港口、建筑、矿山、冶金和林业等许多行业。
习惯把卷筒直径错误!未找到引用源。
< 2000mm 时的称为提升机, 而把错误!未找到引用源。
≥2000mm时的称为提升机,以下统称为提升机。
自60年代中期提升机出现以来,40多年发展迅速,在工业发达国家的煤矿井下已广泛使用,从大到小,从单绳到多绳,从有极绳到无极绳,从缠绕式到摩擦式,各种品种规格比较齐全。
液压提升机主要由液压驱动系统、液压制动系统、液压控制系统、卷筒-负载系统、操作系统及其它如深度指示、提升超速、过卷安全保护等辅助系统组成。
1.1.2液压提升机的用途、工作原理、类型(1)用途液压提升机主要用于煤矿井下,作为提升和下放人员、煤、矸石及运输材料、设备之用。
在煤矿主要是用于采区上、下山运输,同时也可用于井下暗立井、暗斜井和掘进时的提升运输及井下辅助运输.(2)工作原理液压提升机由机械、液压传动、电气部分等组成。
采用鼠笼型防爆主电机驱动双向变量主油泵;主油泵和二台内曲线低速大扭矩液压马达组成闭合回路、衡扭矩液压调速系统;二台液压马达分别布置在主组装置两侧与主组联接,拖动提升机运转。
提升机有二台辅助油泵,一台工作、一台备用。
辅助油泵中,其大泵作补油泵用,给主液压传动补油;小泵作控制用,给制动系统、操作系统、调绳系统供油。
提升机采用远距离液控操纵方式。
司机通过操作液压式比例先导伐给主油泵的比例油缸输入由低到高的压力油,使主油泵的行程调节器动作,改变主油泵摆动的缸体的倾角来改变主油泵的流量,以改变液压马达的转速,使提升机起动,加速运转。
司机通过操作液压式比例先导伐的手柄扳到不同角度,就可使主油泵输出不同的流量,使提升机得到不同的提升速度。
当液压式比例先导伐的手柄扳到最大位置时,提升速度最大。
当液压式比例先导伐的手柄扳到中立位置时,提升机停车。
当手柄反方向扳动时,提升机反方向运行。
提升机采用盘型闸制动,以实现提升机的正常和紧急制动。
正常制动的制动力靠液压传动装置本身产生的。
提升时负荷成为制动力。
下放重物时液压马达变为泵。
液压泵变为液压马达。
使电动机产生发电反馈制动。
盘型制动器不参与工作制动。
只是在提升机卷筒停止运转后作为保险装置来使用。
提升机在运行中出现故障,保险装置自动工作,也可由司机用脚踏开关进行紧急制动停车。
提升制动系统有压力油时,盘型闸制动打开,没有压力油盘型闸制动。
司机操作的液压式比例先导阀共有4个减压阀,其中两个减压阀操纵主油泵正反向供油,另两个减压阀控制盘型闸的开起,当司机操作液压式比例先导伐时,同时压下两个阀,一个阀输出的压力油进主泵的比例油缸,使主泵向液压马达供油并使其运转。
另一个阀输出的压力油供制动系统的液控换向阀,使制动系统向盘型制动器供油,盘型闸制动打开、使提升机运转。
当司机扳回液压式比例先导伐的手柄扳到中立位置时,(比例油缸向中位返回)主泵流量逐渐减小到零,液压马达停止运转。
同时液控换向阀由于没有压力油而复位,提升机制动。
这样就实现了开始提升运转时,盘型制动闸同时打开,提升机停止运转时,盘型制动闸同时立刻制动,保征了提升机的安全运行。
(3)类型液压提升机按传动系统有全液压传动和液压-机械传动两大类。
全液压传动液压提升图1.1 全液压传动提升机工作原理1.电机2.主液压泵3.液压马达4.滚筒机工作原理如图1.1所示,它是利用鼠笼式防爆电动机1,双向变量液压曲泵2,内线低速大扭矩液压马达3组成闭式回路,液压马达直接与滚筒4联接拖动提升机运转;液压-机械传动液压提升机工作原理如图1.2所示, 它是利用鼠笼式防爆电动机1带动双向变量液压泵2和高速液压马达3组成闭式回路, 液压马达经行星齿轮减速箱4再带动提升滚筒5直接拖动提升机运转,滚筒的正、反向运转依靠改变液压泵输出液流的方向来完成,提升机的转速大小由改变液压泵输入液压马达油量大小来调节。
图1.2 液压-机械传动提升机工作原理1.电机2.主液压泵3.液压马达4.减速箱5.滚筒1.2液压提升机发展历程1.2.1国外发展历程国外在50年代中期,随着新型轴向柱塞式和径向柱塞式液压马达的问世,研制出了在轮船和建筑机械上使用的液压提升机。
大约在60年代中期,研制出煤矿井下使用的液压提升机。
近20年液压提升机发展迅速,在工业发达国家的煤矿已广泛使用,从大到小,从单绳到多绳,从有极绳到无极绳,从缠绕式到摩擦式,各种各样规格比较齐全。
1.2.2国内发展历程我国煤矿井下液压提升机的研制工作和应用比欧洲、日本等大约晚了10年。
从1977年开始,由湖南省煤炭工业局液压提升机研制组、湖南省煤炭科学研究所和湖南省煤矿机械厂共同研制BYT-1.2型防爆液压提升机,于1981年3月经鉴定定型,转入批量生产。
随后,该厂又研制了直径1.6m、2m、2.5m等系列提升机,并在煤矿井下得到广泛推广应用。
此外国内其它单位如洛阳矿山机械工程设计研究院研制了JTY系列直径1.6m、2m、2.5m液压防爆提升机,淮南煤矿机械厂研制了JT-1200Y型防爆液压提升机,重庆矿山机械厂也研制了直径1.2m防爆液压提升机,山西机器厂也研制了直径1.6m防爆液压提升机,重庆煤炭研究所、鸡西煤矿机械厂、徐州煤矿机械厂等也研制了多种型号、规格的液压防爆提升机,并在不同程度的煤矿得到采用。
近年来,湖南株州煤矿机械厂、洛阳矿山机械工程设计研究院等单位,在提高液压防爆提升机产品性能和稳定性、降低能耗、降低噪声、控制漏油、提高运行工作效率和工作可靠性等方面进行了一系列的研究和探索, 在反馈控制系统和控制器的开发上进行探索性的工作,并取得较好的成果。
1.3技术特点液压提升机由于采用液压传动,减小了产生电火花的元件,空载直接启动,完全由液压系统实现调速,电气控制设备简单,便于实现防爆,安全可靠性好, 液压系统传递动力均匀平稳,而且通过液压变量泵能实现无级变速,起动换向平稳,低速运转性能好,电控提升机在启动和低速提升时电阻器消耗能量,在低速重载下放时靠制动闸与制动盘间摩擦来实现调速。
而液压提升机调节器无电阻器消耗电能, 且在下放重载时向电网反馈电能。
液压提升机不像电控制提升机那样频繁启动电动机,与同功率的电控防爆提升机相比:结构简单、体积小、占用碉室小;运输、安装费用低;安全保护设施齐全。
(1)防爆功能提升机的主要使用环境是含煤尘和易燃、易爆气体的煤矿井下或井口,防爆是其最基本的安全功能,液压提升机电控系统与电控式提升机电控系统相比更为简单,防爆问题更易解决。
因为,液压提升机由液压系统来实现矿井负载的提升与下放及其速度的控制与调节,因此驱动其主、辅助油泵的电动机只需朝一个方向旋转,不像电控式提升机那样电机有正、反转要求;液压提升机的主、辅助油泵为空载起动,起动设备更为简单;两液压泵的起动顺序是先起动辅助油泵,再起动主液压泵,其相应电机的磁力起动可利用控制回路中继电器的辅助触点联锁。
液压提升机电气控制系统主要采用隔爆型或安全火花型电气设备,常用的防爆元器件有防爆自动馈开关、鼠笼型防爆电机、防爆磁力起动器、防爆电磁阀、防爆干式变压器、防爆检漏器、防爆行程开关及防爆电铃等。
(2)超速、过卷保护功能液压提升机在工作过程中尤其是在下放负载过程中,容易发生跑车超速。
当速度超过额定最大速度运转时,不仅机械或液压元件如液压马达容易损坏,也是诱发重大事故的安全隐患。
因此,液压提升机设计中规定,当跑车速度超过额定速度15%时,系统必须能自动断电。
液压提升机的超速保护装置有机械和电气两种型式,电气超速保护装置由测速发电机和过速断电器组成,机械超速保护装置一般都采用离心式。
图1.3 液压提升机机械式超速保护装置图1.3为常见的机械式离心超速保护装置结构示意图,安装在液压提升机主轴上,内齿圈6与主轴相连,将主轴转速输入超速保护装置,内齿圈6与轴齿轮5构成超速保护装置的增速装置。
通过增速后,轴齿轮5带动旋转体高速旋转,在离心力的作用于下,离心块3被甩出,并通过杠杆4推动顶杆2;主轴转速越高,顶杆被推动的距离越大,当主轴速度超过额定速度15%时,顶杆触动超速保护行程开关1,使它的接点断开,使主油泵电机断电,液压制动器紧急制动,液压提升机停机。
(3)高、低压保护具有高、低压保护回路,当液压系统压力升高超过正常工作台压力(1. 2~1.25)倍时,高压溢流阀开启,液压油经高压安全阀、单向阀流入主回路的低压侧管道,而液压系统压力不会继续升高,液压马达带不动过重的负载,提升机自动停机;若辅助补油系统的补油压力过低,低压保护压力继电器动作,切断电源,提升机也会自动停机,且信号灯亮,报警铃声报警。
此外,液压提升机还有其它安全保护功能,例如:液压提升机有故障时,不能起动;在运行中发生故障时,提升机中途自动停机;在进行紧急制动,同时信号指示灯亮警示故障发生。
闸瓦磨损过大;卷筒-负载系统在减速点未减速;液压系统油箱油温过高,油位过低,都会使液压提升机的主油泵停转、制动闸紧急制动,事故信号灯亮,报警铃报警。
在紧急制动情况下,司机可操作脚踏制动开关(ES) ,使液压提升机紧急停车,并断开控制电源。
一旦下降负载时出现断绳现象,安装在提升容器两侧的防堕器会紧急抱紧罐道实现强制停车。
图1.4 提升机液压主回路在液压回路中设计1.4液压传动的优缺点随着液压技术的迅速发展,液压传动已经在各种各样的机械上得到越来越广泛的应用,代替了许多复杂的机械结构。
液压传动具有很多其它传动方式所没有的独特的优点:(1)易于获得很大的力和力矩,使液压传动成为实现省力的有效手段。
提升机往往需要产生很大的提升力,故这一优点使液压传动适用于提升系统。
(2)可以实现无级调速,而且能获得很大的调速比,还容易获得极低的运转速度,使整个传动系统简化。
这对于工作中需要调速的提升机来说是很重要的。
(3)能容量大,用较小重量和尺寸的液压件就可传递较大的功率,使机械结构紧凑,体积小,重量轻。
矿用液压提升机由于受井下空间尺寸限制,就要求体积小。
同时,液压系统惯性小,启动快,工作平稳,易于实现快速而无冲击的变速与换向。
这对于提升机的频繁启动、换向很有利。
(4)易于获得各种复杂的机械动作,以直接驱动工作装置,故可用低速大扭矩液压马达直接拖动滚筒,而不需要减速装置。
(5)动力传递很方便。
由于用管道传递压力油,所以液压元件和各种机械装置都易于布局,各元件的安装可以随意放在任何适当的位置上,因此便于液压提升机进行远距离操纵。
(6)容易实现安全保护,能自动防止过载,故能满足提升机安全工作的要求,避免发生事故。
(7)液压元件能自行润滑,延长了使用寿命。
(8)液压元件易于实现标准化、系列化、通用化、便于组织专业化大批量生产,从而提高生产率,提高产品质量、降低成本。