冲压工艺与模具设计16PPT课件
合集下载
数控转塔冲床冲压与模具PPT课件

冲压变形过程
第11页/共20页
第12页/共20页
3.2转塔冲床模具结构
转塔:模具 安装转盘 通 过数控系统 控制精确换 模
第13页/共20页
锁紧螺母
转塔冲床模具结构
弹簧座
上模导杆 上模刃口 上模套 下模
第14页/共20页
3.2转塔冲床模具结构
第15页/共20页
3.3冲裁工艺条件
3.3.1冲裁变形原理: 板料冲压分离分为三个过程: 弹性变形、塑性变形、分离阶段
第4页/共20页 1、夹钳 2、送料机构 3、板材 4、转塔
床身既曲柄压力机:
传动系统: 电机能量传递给工作机构
工作机构: 曲轴滑块机构 操作系统: 离合器、制动器
第5页/共20页
电机
曲轴
冲 头
电机的旋转运动 通过曲轴变为冲 头的往复直线运 动 冲压产品
第6页/共20页
曲轴模拟动态仿真 第7页/共20页
成 确定位,自动选择转盘模具库中的模具, 型 按要求自动加工不同尺寸和孔距的不同形
状的孔,也可用小冲模以步冲方式冲大的 圆孔、方形孔、腰形孔及各种形状的曲线 轮廓,也可进行特殊工艺加工,如百叶窗、 浅拉伸、沉孔、翻边孔、加强筋、压印等。
第2页/共20页
数控系统 送料机构
转塔 数控转塔冲床
床身
第3页/共20页
送料机构:由数控系统控制送料机构按编订的程序顺序移动
板料的送进是双轴双向的(+/-X, +/- Y).
第8页/共20页
送料机构传动简图: Y
X
第9页/共20页
冷冲压的四个基本工序:
冲
弯
拉
成
裁
曲
伸
型
冲压工艺与模具设计电子PPT课件

(
()
2
3)
/
2
31
(
3
1)
/
2
第21页/共89页
图1.3 主剪应力面及主剪应力方向(用阴影线表示)
第22页/共89页
•
其中绝对值最大的主剪应力称为该点的最大剪应力,用τmax表示。若规定1≥2≥3,则
•
•
()
ma x (13)/2
第23页/共89页
•
最大剪应力对材料的塑性变形有重要意义。
•
大小取决于该点的应力状态,而与坐标系的选取无关,即
•
•
•
()
m 1 3(x y z)1 3(1 2 3)
第16页/共89页
•
任何一种应力状态都可以看成是由两种应力状态叠加而成,如图所示。其中一种是大小等于平均应力
m的球应力状态,另一种为偏应力状态。因球应力状态为三向等应力状态,不产生剪应力,故不能改变物
•
应力是指单位面积上的内力。单向拉伸试验过程中,试件横截面上的拉
应力有两种计算方法:
第42页/共89页
•
(1)不考虑横截面积的变化(F0—试样初始截面积)
•
•
()
0
P F0
第43页/共89页
•
求得的0称为条件应力。其条件就是只有当变形不大时才能用这种方
法近似计算。
第44页/共89页
•
(2)考虑横截面积的变化
以说明这种弹塑性变形的共存现象。
第33页/共89页
•
低碳钢试样在单向拉伸时的拉伸试验曲线图(或条件应力-应变曲线)
如图所示。
第34页/共89页
图1.5 拉伸试验曲线图(条件应力-应变曲线)
第二章冲压工艺及模具设计课件.pptx

第二章 板材冲压成型的基本知识
第二章 板材冲压成型的基本知识
❖ 学习内容 1、了解冲压工艺常用的基本设备。 2、掌握冲压设备相关的技术参数。 3、了解塑性成型的基本理论。 4、了解常用的冲压材料和模具材料。
Company Logo
第二章 板材冲压成型的基本知识
2.1 冷冲压设备 一、冲压设备分类
机械压力机:曲柄压力机、偏心压力机、拉深压 力机、摩擦压力机、粉末制品压力 机、模锻精压机、挤压用压力机、 专用压力机
液压压力机:冲压液压机、一般用途液压机、弯 曲校正压紧用液压机、打包压块用 液压机、专门化液压机
Company Logo
第二章 板材冲压成型的基本知识
1、曲柄压力机
图2-1 曲柄压力机结构示意图 1—电动机;2—皮带轮;3—皮带;4—飞轮;5—离合器;6—轴承;7—曲轴;
1、点的应力状态
图2-10 点应力状态
(a)任意坐标系统
(b)主轴坐标系统 Company Logo
第二章 板材冲压成型的基本知识
图 2-11 主应力图
❖ 板料成型时,大多数情况下板厚方向的应力很小,可以 忽略不计。所以一般可按平面应力状态处理板料成型过 程。
第二章 板材冲压成型的基本知识
3、高速压力机
Company Logo
第二章 板材冲压成型的基本知识
图2-8 高速压力机及其附属机构 1—开卷机;2—校平机构;3—供料缓冲装置;4—送料机构;5—高速自动压
力机;6—弹性支承
Company Logo
第二章 板材冲压成型的基本知识
4、数控冲模回转头压力机
Company Logo
第二章 板材冲压成型的基本知识
4、液压机 (1)结构组成
第二章 板材冲压成型的基本知识
❖ 学习内容 1、了解冲压工艺常用的基本设备。 2、掌握冲压设备相关的技术参数。 3、了解塑性成型的基本理论。 4、了解常用的冲压材料和模具材料。
Company Logo
第二章 板材冲压成型的基本知识
2.1 冷冲压设备 一、冲压设备分类
机械压力机:曲柄压力机、偏心压力机、拉深压 力机、摩擦压力机、粉末制品压力 机、模锻精压机、挤压用压力机、 专用压力机
液压压力机:冲压液压机、一般用途液压机、弯 曲校正压紧用液压机、打包压块用 液压机、专门化液压机
Company Logo
第二章 板材冲压成型的基本知识
1、曲柄压力机
图2-1 曲柄压力机结构示意图 1—电动机;2—皮带轮;3—皮带;4—飞轮;5—离合器;6—轴承;7—曲轴;
1、点的应力状态
图2-10 点应力状态
(a)任意坐标系统
(b)主轴坐标系统 Company Logo
第二章 板材冲压成型的基本知识
图 2-11 主应力图
❖ 板料成型时,大多数情况下板厚方向的应力很小,可以 忽略不计。所以一般可按平面应力状态处理板料成型过 程。
第二章 板材冲压成型的基本知识
3、高速压力机
Company Logo
第二章 板材冲压成型的基本知识
图2-8 高速压力机及其附属机构 1—开卷机;2—校平机构;3—供料缓冲装置;4—送料机构;5—高速自动压
力机;6—弹性支承
Company Logo
第二章 板材冲压成型的基本知识
4、数控冲模回转头压力机
Company Logo
第二章 板材冲压成型的基本知识
4、液压机 (1)结构组成
冲压工艺与模具设计课件(2016)

1.应力状态 2.应变状态 3.屈服准则(塑性条件) 4.塑性变形时应力应变关系
3种主应变状态
9种主应力状态
精品课件
2.3 塑性成形基本规律
1.加工硬化规律 2.卸载弹性恢复规律 3.最小阻力定律 4.塑性变形体积不变
定律
拉深 精品课件 翻孔
胀形
思考题
1.试说明冲压加工的含义 2.简述冲压加工的特点 3.试说明冲压加工的种类 4.简述冲压技术的发展趋势 5.冲压对板料的基本要求有哪些? 6.板料的力学性能对冲压成形性能有哪些影响? 7.常用的冲压原材料有哪几种规格? 8.试列举冲压加工设备的主要类型 9.冲床的主要技术参数与模具有怎样的关系?
3--压力机的级别 63--公称压力 A--改进设计号
C--锤
T--其它 63T开式双柱可倾式第二种改进型压力机
精品课件
指滑块在下死点前 某一位置滑块所具 有的压力。
(2)技术参数 1)公称压力 F
2)公称压力行程 S F 3) 滑块行程S
上死点→下死点
4)滑块行程次数n
上死点→下死点 →上死点
5)压力机的闭合高度
4)根据需方要求,经供需双方协商,可以供应其他尺寸的钢 板
和钢带。
精品课件
2.冲压材料的下料方法
(1)剪板机下料
精品课件
(2)圆盘剪床下料
精品课件
(3)其他下料方法
➢激光切割机 ➢等离子切割机 ➢高压水切割机 ➢电火花线切割机 ➢电冲剪等
精品课件
1.4 冲压设备
冲压设备的选用原则:
➢ 冲压工序的性质:分离或成型工序 ➢ 冲压力的大小:开式、闭式 ➢ 模具结构形式 ➢ 模具闭合高度、轮廓尺寸 ➢ 生产批量 ➢ 生产成本 ➢ 产品质量 ➢ 结合单位现有设备条件
冲压工艺与模具设计ppt
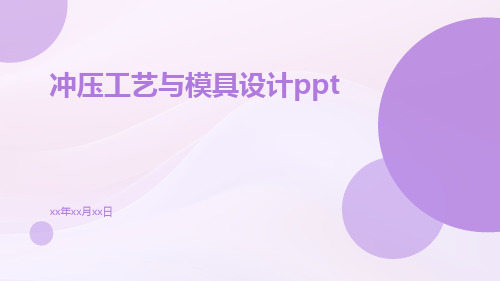
设计模具结构
根据工艺方案和产品图 样,设计模具的结构, 包括凸模、凹模、定位 板、压料板等零件的设 计。
绘制模具总装 图
根据设计的模具结构, 绘制模具的总装图,标 注尺寸和技术要求。
绘制零件加工 图
根据总装图,绘制每个 零件的加工图,包括凸 模、凹模、定位板等零 件的详细加工尺寸和技 术要求。
03
模具的装配工艺
模具零件的定位与固定 模具零件的调整与修整
模具零件的配合与连接 模具零件的润滑与防锈
模具的调试与验收
模具调试前的准备 模具的验收与检测
模具的安装与调试 模具的维护与保养
06
冲压工艺与模具设计的发展趋势
数字化设计与制造技术应用
01
基于计算机的模具设 计
利用CAD软件进行模具设计,实现高 效的设计与修改。
冲压工艺参数设计
冲压件的工艺性分析
1 2
工艺性分析的意义
通过对冲压件的形状、尺寸、精度等工艺性指 标进行分析,确保模具设计的合理性和生产过 程的顺利进行。
常见问题
如局部变形、起皱、开裂等,需要在设计阶段 尽量避免。
3
工艺性分析的方法
采用经验总结、模拟分析等方法,结合实际生 产情况,对冲压件的工艺性进行评估。
复合工艺是指将两个或多个分离或成形工艺组合 在一起,以获得所需形状和尺寸的制品,如拼接 、装配等。
冲压工艺的特点
高效性
冲压工艺可以大规模、连续化生产 ,提高生产效率和降低成本。
精度高
模具的精度决定了制品的精度,冲 压工艺可以实现高精度的加工要求 。
制造成本低
冲压工艺使用的设备和模具相对简 单,制造成本较低。
冲压设备的选择与计算
冲压设备的选择
第三章冲压工艺及模具设计课件.pptx

第三章 冲裁工艺及冲裁模具
3.4.2 工作部分尺寸计算方法
1.凸模和凹模分开加工时工作部分尺寸计算
凸模和凹模分开加工时,应分别计算和标注凸模和凹模工作部分
尺寸与制造公差。适合圆形或形状简单的凸模和凹模及大量生产冲
冲
压 工
模时采用。
艺
及
模 具
模具的制造公差与冲裁间隙之间应满足:
设
计
|δp|+|δd| ≤Zmax-Zmin
越高。
影响因素:
(1)冲裁模的制造精度。
冲
压
(2)材料性质。
工
艺 及
• 塑性好的材料,裂纹出现较迟,材料被剪切的深度较大,光亮带较大,断裂
模
具
带较小,但塌角及毛刺高度相应增大。反之,光亮带较小,断裂带增大,塌
设
计
角及毛刺较小。
• 弹性变形大小不同,导致回弹量不同。
(3)冲裁间隙。
• 过大:使制件的尺寸向实体方向收缩;
冲 压 工 艺 及 模 具 设 计
第三章 冲裁工艺及冲裁模具
2.冲裁件的精度
对于普通冲裁,冲裁件的尺寸精度在IT10~IT11以下,粗糙度高
于Ra12.5μm。
冲 压
冲孔精度可比落料精度高一级。
工
艺 及
3.冲裁件的尺寸基准
模
具
设 计
冲裁件的尺寸基准应尽可能和制模时的定位基准重合,孔位置
尺寸基准应尽量选择在冲裁过程中始终不参加变形的面或线上。
(4)孔间距、孔壁与孔壁之间的最小距离不应太小。
第三章 冲裁工艺及冲裁模具
(5)在弯曲或拉深零件上冲孔时,其孔壁与零件直壁之间应保持 一定的距离。
冲 压 工 艺 及 模 具 设 计
冲压工艺与模具设计ppt
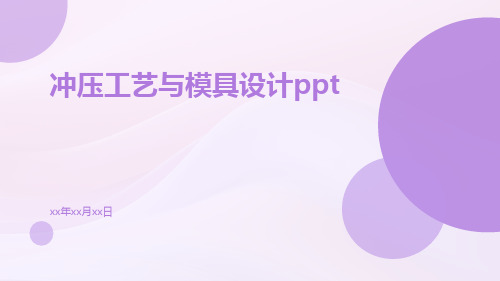
冲压技术的应用前景
汽车制造领域
01
冲压技术广泛应用于汽车制造中,未来随着新能源汽车和智能
汽车的兴起,冲压技术的应用前景将更加广阔。
航空航天领域
02
航空航天领域对材料的要求极高,冲压技术有着广泛的应用前
景。
家电和电子产品领域
03
家电和电子产品领域对产品的精度和品质要求较高,冲压技术
的应用前景广阔。
THANKS
对另一具体零件进行冲压工艺性分析,研 究其形状、尺寸、精度等对冲压效果的影 响。
确定工艺方案
根据零件特点,制定合理的冲压工艺方案 ,包括冲压次数、顺序、材料等。
试生产
通过试生产,验证模具设计和冲压工艺参 数的正确性,对存在问题进行修整。
模具设计
根据工艺方案,设计相应的冲压模具,包 括零件固定、卸料、导向等机构。
谢谢您的观看
05
冲压技术的发展趋势与未来展望
冲压技术的发展趋势
高效化
为了提高生产效率,冲压技术正朝 着更快速、更精准的方向发展。
自动化
自动化冲压技术有助于提高生产效 率和降低成本。
智能化
利用人工智能和大数据技术优化冲 压工艺,实现生产过程的可视化、 可控化和智能化。
绿色环保
为了响应环保要求,冲压技术正朝 着低能耗、低污染的方向发展。
冲压模具的维护和保养
定期检查
清洗保养
定期检查模具各部件的工作状态和精度,如 发现异常应及时处理。
定期清洗模具表面和内部,去除积尘和锈蚀 ,保持模具的清洁和润滑状态。
更换易损件
紧固调整
定期更换模具中的易损件,如刃口、顶针等 ,保证模具的正常工作状态。
定期紧固模具各部件的螺栓和螺钉,调整各 部件的工作间隙和位置精度,保证模具的正 常工作状态。
冲压工艺与模具设计概述 ppt课件
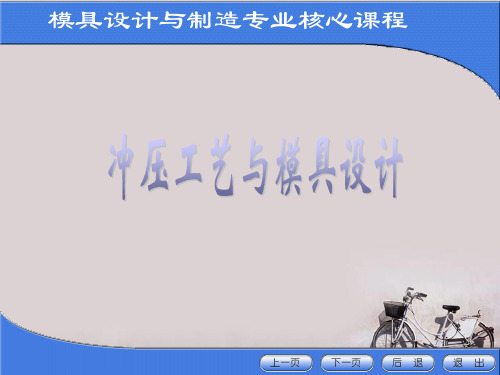
第一单元 冲压工艺与模具设计概述
五、冲压技术现状与发展方向(续)
2.冲压技术发展方向 满足产品开发在T(Time)、Q(Quality)、 C(Cost)、 S(Service)、E(Environment)的要求。 (1)冲压成形理论及冲压工艺 加强理论研究,开展CAE技术应用。 开发和应用冲压新工艺。
2.冲压技术发展方向(续) (3)模具新材料及热、表处理 提高使用性能,改善加工性能 ,提高寿命。 (4)模具CAD/CAM技术 二、三维相结合的数字化设计技术与数字化制造技术。 模具行业是最早应用CAD/CAM技术的行业之一。 (5)快速经济制模技术 加快模具的制造速度,降低模具生产成本。适应小批 量试制。 (6)先进生产管理模式 并行工程思想、标准化、专业化生产。
模具设计与制造专业核心课程
第一单元 冲压工艺与模具设计概述
内容简介:
本章讲述冲压模具设计与制造的基础知识。 涉及冲压和冲模概念、冲压工序和冲模分类;常见冲压 设备及工作原理、选用原则;冲压成形基本原理和规律;冲 压成形性能及常见冲压材料;模具材料种类、性能、选用原
则及热处理方法;模具制造特点、模具零件加工方法及应用
一、冲压与冲模概念
2.冲压成形加工特点
低耗、高效、低成本 “一模一样”、质量稳定、高一致性 可加工薄壁、复杂零件
板材有良好的冲压成形性能
模具成本高
所以,冲压成形适宜批量生产。
第一单元 冲压工艺与模具设计概述
一、冲压与冲模概念
2.冲压成形加工特点(续)
冲压加工是制造业中最常用的一种材料成形加工方法。 冲压成形产品示例一——日常用品
冲模设计与制造必须有系统观点,必须考虑企业实际情况 和产品生产批量,在保证产品质量的前提下,寻求最佳的技术
冲压工艺及模具设计PPT课件

刃口尺寸计算表2.3.2
例1
冲制图示零件,材料为Q235钢,料厚 t=0.5mm。计算冲裁凸、凹模刃口尺寸及 公差。
解:由图可知,该零件属于无特殊要求 的一般冲孔、落料。
外形
3600.62
mm
由落料获得,2
6 0.12 0
mm
和18±0.09由冲孔同时获得。查表2.3.3得,
2Cmin 0.04mm, 2Cmax 0.06mm,则
故: Dd 35.6900.012 mm
mDp 35.6500.008 mm
例2
如图所示的落料件,其中
a 8000.42 mm
b 4000.34 mm c 3500.34 mm
d=
e 1500.12 mm
2板2料±0厚.1度4mt=m1mm,材料为10号钢。试计
算冲裁件的凸模、凹模刃口尺寸及制造公
设计与制造新模具时应采用最小合理间隙 Zmin
* 对模具寿命要求比较高,材料等级高, 在合理值范围内取大值。
* 对模具寿命要求比较低,材料等级低, 在合理值范围内取小值
* 高耐磨性材料本身硬度高,耐磨性好,其冲裁力, 磨损小,一定寿命范围内保证制件精度。
§2-3 凸模与凹模刃口尺寸的计算
一、刃口尺寸计算的依据和原则
按凸模与凹模图样分别加工法
( ) (1)落料
Dδ =
Dmax
-xΔ
+δd 0
( ) ( ) Dp =
Dd
-2C min
0 δp
=
Dmax - xΔ -2C min
0 δp
(2)冲孔
( ) d p
=
d min
+xΔ
0 δp
( ) ( ) dd
例1
冲制图示零件,材料为Q235钢,料厚 t=0.5mm。计算冲裁凸、凹模刃口尺寸及 公差。
解:由图可知,该零件属于无特殊要求 的一般冲孔、落料。
外形
3600.62
mm
由落料获得,2
6 0.12 0
mm
和18±0.09由冲孔同时获得。查表2.3.3得,
2Cmin 0.04mm, 2Cmax 0.06mm,则
故: Dd 35.6900.012 mm
mDp 35.6500.008 mm
例2
如图所示的落料件,其中
a 8000.42 mm
b 4000.34 mm c 3500.34 mm
d=
e 1500.12 mm
2板2料±0厚.1度4mt=m1mm,材料为10号钢。试计
算冲裁件的凸模、凹模刃口尺寸及制造公
设计与制造新模具时应采用最小合理间隙 Zmin
* 对模具寿命要求比较高,材料等级高, 在合理值范围内取大值。
* 对模具寿命要求比较低,材料等级低, 在合理值范围内取小值
* 高耐磨性材料本身硬度高,耐磨性好,其冲裁力, 磨损小,一定寿命范围内保证制件精度。
§2-3 凸模与凹模刃口尺寸的计算
一、刃口尺寸计算的依据和原则
按凸模与凹模图样分别加工法
( ) (1)落料
Dδ =
Dmax
-xΔ
+δd 0
( ) ( ) Dp =
Dd
-2C min
0 δp
=
Dmax - xΔ -2C min
0 δp
(2)冲孔
( ) d p
=
d min
+xΔ
0 δp
( ) ( ) dd
- 1、下载文档前请自行甄别文档内容的完整性,平台不提供额外的编辑、内容补充、找答案等附加服务。
- 2、"仅部分预览"的文档,不可在线预览部分如存在完整性等问题,可反馈申请退款(可完整预览的文档不适用该条件!)。
- 3、如文档侵犯您的权益,请联系客服反馈,我们会尽快为您处理(人工客服工作时间:9:00-18:30)。
You Know, The More Powerful You Will Be
6
谢谢大家
荣幸这一路,与你同行
It'S An Honor To Walk With You All The Way
演讲人:XXXXXX
时 间:XX年XX月XX日
7
§4-3 非直壁旋转体零件拉深成形的特点 一、曲面形状零件的拉深特点 1、曲面形状零件的拉深不能简单的用
拉深系数来衡量成形的难易程度。
压边圈下面的环行部分。
3、球面零件拉深时,毛坯的凸缘部分与中间部分
都是变形区,在很多情况下, 中间部分反而是主要的变形区
(起皱不仅仅在凸缘部分产生, 也可能在中间部分产生,尤其对于薄板材料)
*当t/D=0.5%~3%,采用带压边圈的拉深模
*当t/D <0.5%时,则采用有拉深筋的凸凹模
或者反拉深模,加拉深筋
3
2、按照几何形状分类
* 毛坯直径D较小时,毛坯不易起皱,但移动回弹较大,故采用带底拉深 模。
*当毛坯直径D较大时,起皱将成为必须解决的问题,常采用强力压边装 置,或者带拉深筋的模具。也有增加工艺凸缘进行拉深,拉深后切除工艺余 量,提高制件质量。
三、抛物面零件的拉深方法
相对高度h /d 比球形件大,故 拉深难度更大。
•浅抛物面形 ( h /d <0.5~0.6)
接近球形件故拉深方法与球形 件相同.
*深抛物面形( h/d>0.5~0.6)
拉深难度大
4
常常采用的办法——拉深筋 / 多道工序 / 正拉深或者反拉深
液ቤተ መጻሕፍቲ ባይዱ成型
多道工艺拉深的制件,为保证质量,在最后一道工序时,要使中间毛坯面 积略小于最后成形制件的面积,以获得胀形效果,实际胀形量为5~10%
一般对成型件的几何参数控制不是很严,惟独对抛物线形状要求比较严格。 解决这类问题的方法———
加大凸缘尺寸 / 增加压边圈下面的摩擦系数 / 增大压边力 / 采用拉深筋 / 采用反拉深
二、球面零件的拉深方法
1、拉深系数为恒数 m=0.71
拉深系数不决定拉深的难易程度。
毛坯的相对厚度 t / D是选择拉深方法的依据。 *当 t/D > 3%,不用压边圈,但是需要校正(有底)
a、直壁回转拉深在拉深工艺中是最简单的,因起变形区容易控制 b、随着底部形状不同,难度逐渐增加,球面、锥面、
抛物形体是在筒形基础上底部变化而来的 c、此拉深变形是拉深与胀形两种变形方式的复合,
且同时具有拉深和压缩类变形的特点。
2
d、抛物线成型较之锥形体使用更多,更容易出现变形量过大,
使底部断裂拉深过程中要求最后一步进行胀形。
4、锥形零件的拉深特点
凸模接触面积小,压力集中,容易引起局部变薄及自由面积
增大,压力圈作用相对减弱。悬空带过大,容易起皱。
1
高度越大,直径差越大越困难。回弹也比较严重, 较球面零件的拉深更为困难。
5、抛物面零件的拉深特点
具有球面零件和锥形零件加工是特点
但是其相对高度增加,头部更尖,更易开口,且母线形状 更加复杂,拉深时变形区的位置,受力情况,变形特点更复 杂。(常常采用橡皮液囊一次成型)
四、锥形件的拉深方法
几何参数——
相对高度 h / d ; 锥角 α ;相对料厚 t / D
1、浅锥形件
( h / d 2<0.25~0.30 α =50°~80°)
可以一次拉深,回弹严重,采用带拉深筋 的凸模或者压边圈,也可以用软模进行拉 深)
5
写在最后
经常不断地学习,你就什么都知道。你知道得越多,你就越有力量 Study Constantly, And You Will Know Everything. The More
6
谢谢大家
荣幸这一路,与你同行
It'S An Honor To Walk With You All The Way
演讲人:XXXXXX
时 间:XX年XX月XX日
7
§4-3 非直壁旋转体零件拉深成形的特点 一、曲面形状零件的拉深特点 1、曲面形状零件的拉深不能简单的用
拉深系数来衡量成形的难易程度。
压边圈下面的环行部分。
3、球面零件拉深时,毛坯的凸缘部分与中间部分
都是变形区,在很多情况下, 中间部分反而是主要的变形区
(起皱不仅仅在凸缘部分产生, 也可能在中间部分产生,尤其对于薄板材料)
*当t/D=0.5%~3%,采用带压边圈的拉深模
*当t/D <0.5%时,则采用有拉深筋的凸凹模
或者反拉深模,加拉深筋
3
2、按照几何形状分类
* 毛坯直径D较小时,毛坯不易起皱,但移动回弹较大,故采用带底拉深 模。
*当毛坯直径D较大时,起皱将成为必须解决的问题,常采用强力压边装 置,或者带拉深筋的模具。也有增加工艺凸缘进行拉深,拉深后切除工艺余 量,提高制件质量。
三、抛物面零件的拉深方法
相对高度h /d 比球形件大,故 拉深难度更大。
•浅抛物面形 ( h /d <0.5~0.6)
接近球形件故拉深方法与球形 件相同.
*深抛物面形( h/d>0.5~0.6)
拉深难度大
4
常常采用的办法——拉深筋 / 多道工序 / 正拉深或者反拉深
液ቤተ መጻሕፍቲ ባይዱ成型
多道工艺拉深的制件,为保证质量,在最后一道工序时,要使中间毛坯面 积略小于最后成形制件的面积,以获得胀形效果,实际胀形量为5~10%
一般对成型件的几何参数控制不是很严,惟独对抛物线形状要求比较严格。 解决这类问题的方法———
加大凸缘尺寸 / 增加压边圈下面的摩擦系数 / 增大压边力 / 采用拉深筋 / 采用反拉深
二、球面零件的拉深方法
1、拉深系数为恒数 m=0.71
拉深系数不决定拉深的难易程度。
毛坯的相对厚度 t / D是选择拉深方法的依据。 *当 t/D > 3%,不用压边圈,但是需要校正(有底)
a、直壁回转拉深在拉深工艺中是最简单的,因起变形区容易控制 b、随着底部形状不同,难度逐渐增加,球面、锥面、
抛物形体是在筒形基础上底部变化而来的 c、此拉深变形是拉深与胀形两种变形方式的复合,
且同时具有拉深和压缩类变形的特点。
2
d、抛物线成型较之锥形体使用更多,更容易出现变形量过大,
使底部断裂拉深过程中要求最后一步进行胀形。
4、锥形零件的拉深特点
凸模接触面积小,压力集中,容易引起局部变薄及自由面积
增大,压力圈作用相对减弱。悬空带过大,容易起皱。
1
高度越大,直径差越大越困难。回弹也比较严重, 较球面零件的拉深更为困难。
5、抛物面零件的拉深特点
具有球面零件和锥形零件加工是特点
但是其相对高度增加,头部更尖,更易开口,且母线形状 更加复杂,拉深时变形区的位置,受力情况,变形特点更复 杂。(常常采用橡皮液囊一次成型)
四、锥形件的拉深方法
几何参数——
相对高度 h / d ; 锥角 α ;相对料厚 t / D
1、浅锥形件
( h / d 2<0.25~0.30 α =50°~80°)
可以一次拉深,回弹严重,采用带拉深筋 的凸模或者压边圈,也可以用软模进行拉 深)
5
写在最后
经常不断地学习,你就什么都知道。你知道得越多,你就越有力量 Study Constantly, And You Will Know Everything. The More