孔位加工方法
孔加工技术
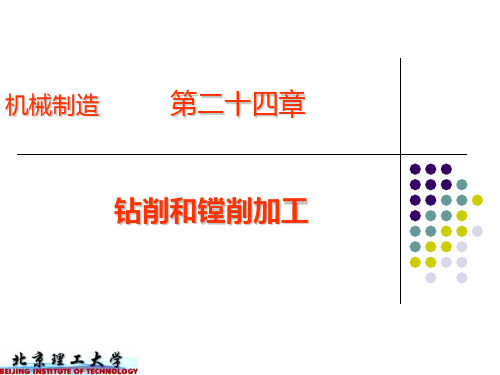
所用刀具 规格 ф18 ф19.8 ф20
钻孔 扩孔 铰孔
钻头 扩孔钻 铰刀
攻螺纹工具
丝锥 丝锥一般成组使用。M6 ~ M24
矩形尾部
的丝锥每组有两个。加工粗牙螺纹M6以
下和M24以上的丝锥每组有三个。加工 细牙螺纹的丝锥不论大小,每组都是两
个。丝锥柄部一般用标记I、II、III代
表头锥、二锥和三锥。
攻螺纹和套螺纹
用丝锥来加工内螺纹的操作称为攻螺纹。用板牙加工外螺纹 的方法称为套扣。攻螺纹和套螺纹可以在钻床上也可以在车床上 进行。但单件小批生产主要用手工操作。
在工件上加工一个直径为ф20H9的圆孔,要求孔的 加工质量达到IT7、表面粗糙度Ra0.8。试将加工工艺列 于下表。
加工顺序及方法 名称
Dቤተ መጻሕፍቲ ባይዱ
倒角
D1
L
塑
H
底孔示意图
攻螺纹操作
工件安装 将加工好底孔的工件固定好,孔的端面应基本保持 水平。 倒角 在孔口部倒角,直径可略大于螺孔大径。 丝锥选择 攻螺纹时必须按头锥、二锥、三锥的顺序攻至标 准尺寸。 攻螺纹 攻螺纹时两手用力要均匀,每攻入1 ~ 2圈,应将丝 锥反转1/4圈进行断屑和排屑。攻不通孔时,应做好记号,以防丝 锥触及孔底。 润滑 对钢件攻螺纹时应加乳化液或机油。
机械制造
第二十四章
钻削和镗削加工
在制造业中,孔的应用非常广泛。回 转体工件中心的孔通常在车床上加工,非 回转体工件上的孔以及回转体上非中心的 孔通常在镗床和钻床上加工。
孔的常见类型
孔的类型很多。 常见孔:如轴承孔、销孔、螺纹孔、喷嘴等。 深孔:如油缸活塞孔、枪管、炮管等。 特型孔:如内花键孔、内齿轮等。 根据各种孔的应用情况及常用的加工方法,可以把孔粗略地分 为以下四类: 普通小直径圆孔 普通大直径圆孔 微孔、深孔及超大圆孔 特型孔
孔加工工艺

结论 : 应用定径销孔钻头加工零件销孔可实现以 下四方面的作用。
1.效率提高节约加工费用,降低生产成本。 通过试验可以看出,使用定径销孔钻头后加
工效率提高,零件加工时间大大缩短,可节省人
工费、设备占用费、综合管理费等,即工缴费用。
按月产细纱机100台,全年降低零件加工费60万元。
2.减少数控设备占用时间,提升企业生产能力。 按每件龙筋节约实际加工时间300秒计算,
采用定径销孔钻头仅加工头尾段龙筋,按月产
100台,每年可减少数控设备占用时间2950小时
约合368.8天(即节省一台数控设备)。
3.提高零件加工质量水平
定径销孔钻头加工出的孔一致性很好,目前
我们试验检测出的孔径相差均在0.004-0.005,
因此可以很大程度的提高工序能力和产品质量水
平。
4.降低工具费用 定径销孔钻头由于本身材料及涂层的原因,其
1、起钻
预钻锥形定心孔,即先用小顶角起钻或中心钻,钻一个锥 形浅坑,作为钻孔的定位孔,再用所需尺寸的钻头钻孔。由于 横刃未参加工作,因而钻头不会出现由此引起的弯曲。
2、钻
钻削是使用钻头在实体材料上加工孔的
最常用的方法,其加工精度可达IT12~IT11 表面粗糙度Ra可达12.5~6.3μm,可作为攻 丝、扩孔、铰孔和镗孔的预备加工。
• 零件:
孔数:
落纱传动管
2
零件材料: 20#冷拉钢管
使用设备: 辛辛那提加工中心
原工艺 工序 起钻-钻-扩-铰
新工艺 钻(1道工序)
刀具
中心钻,钻头,扩孔钻,铰刀 合金钻头Φ11H9 V:55-90mm/min F:0.2mm/r 孔一致性:0.002-0.003 圆度: 0.004 轴对称度:0.03
8字孔的加工方法
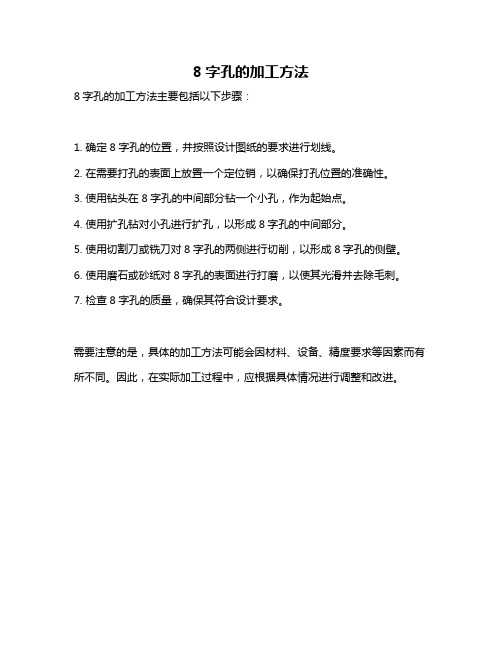
8字孔的加工方法
8字孔的加工方法主要包括以下步骤:
1. 确定8字孔的位置,并按照设计图纸的要求进行划线。
2. 在需要打孔的表面上放置一个定位销,以确保打孔位置的准确性。
3. 使用钻头在8字孔的中间部分钻一个小孔,作为起始点。
4. 使用扩孔钻对小孔进行扩孔,以形成8字孔的中间部分。
5. 使用切割刀或铣刀对8字孔的两侧进行切削,以形成8字孔的侧壁。
6. 使用磨石或砂纸对8字孔的表面进行打磨,以使其光滑并去除毛刺。
7. 检查8字孔的质量,确保其符合设计要求。
需要注意的是,具体的加工方法可能会因材料、设备、精度要求等因素而有所不同。
因此,在实际加工过程中,应根据具体情况进行调整和改进。
气膜孔加工定位方式_解释说明以及概述

气膜孔加工定位方式解释说明以及概述引言1.1 概述气膜孔加工定位方式是一种用于加工过程中定位孔位置的方法。
在制造和加工领域,高精度的定位是极为重要的,因为它直接影响到产品质量和装配效率。
通常情况下,气膜孔加工定位方式结合了传统的机械定位和先进的气体力学原理,以实现更精确、可靠且高效的定位。
1.2 文章结构本文将分为四个主要部分来讨论气膜孔加工定位方式。
首先,在引言部分,我们将对气膜孔加工定位方式进行概述,并介绍文章整体结构。
其次,我们将在第二部分详细解释和说明不同气膜孔加工定位方式的定义、背景以及原理与特点。
然后,在第三部分中,我们将对基础定位方式和高级定位方式进行概述,并探讨这些技术的发展趋势和挑战。
最后,在结论部分我们将回顾要点,并对气膜孔加工定位方式未来发展进行展望。
1.3 目的本文旨在深入研究和解析气膜孔加工定位方式,并提供对这些技术的全面理解和概述。
通过详细探讨各种定位方式的原理、特点和优缺点比较,我们旨在为读者提供一个清晰而准确的了解,使其能够更好地理解和应用气膜孔加工定位方式。
此外,我们还将探讨这些技术未来可能的发展方向,以及存在的挑战和机遇。
2. 气膜孔加工定位方式解释说明:气膜孔加工定位方式是一种广泛应用于工程领域的高效加工技术,它通过利用气流形成的薄膜作为加工定位的依据,在精确定位孔的位置和方向上具有独特的优势。
本节将对气膜孔加工定位方式进行详细解释和说明。
2.1 定义与背景:气膜孔加工定位方式是一种基于液压原理的无需机械接触即可实现精确定位的方法。
在此技术中,通过控制气流进出以及压力差来形成一个微小空间内局部高速气流,这样能够形成一个“吹垫”的效果,从而使得被加工对象能够靠在气垫上,并通过调整其位置来实现准确定位。
该技术最早由航天科技领域引入,主要应用于航空发动机零部件等高精度装配中。
随后,由于其独特优势和广阔应用前景,逐渐推广至其他领域如汽车制造、数控切割等。
2.2 不同气膜孔加工定位方式的原理与特点:气膜孔加工定位方式主要可分为两类:传统气垫定位和微通道气膜定位。
孔加工技术

第三节孔加工与外圆表面加工相比,孔加工的条件要差得多,加工孔要比加工外圆困难。
这是因为:(1)孔加工所用刀具的尺寸受被加工孔尺寸的限制,刚性差,容易产生弯曲变形和振动;(2)用定尺寸刀具加工孔时,孔加工的尺寸往往直接取决于刀具的相应尺寸,刀具的制造误差和磨损将直接影响孔的加工精度;(3)加工孔时,切削区在工件内部,排屑及散热条件差,加工精度和表面质量都不易控制。
一、钻孔与扩孔1.钻孔钻孔是在实心材料上加工孔的第一个工序,钻孔直径一般小于。
钻孔加工有两种方式(图图3-27 两种钻孔方式a)钻头旋转b)工件旋转如在车床上钻孔。
上述两种钻孔方式产生的误差是不相同的。
在钻头旋转的钻孔方式中,由于切削刃不对称和钻头刚性不足而使钻头引偏时,被加工孔的中心线会发生偏斜或不直,但孔径基本不变;而在工件旋转的钻孔方式中则相反,钻头引偏会引起孔径变化,而孔中心线仍是直的。
常用的钻孔刀具有:麻花钻、中心钻、深孔钻等。
其中最常用的是麻花钻,其直径规格为。
标准麻花钻的结构如图3-28所示,其柄部是钻头的夹持部分,并用图3-28 标准麻花钻的结构a)锥柄b)直柄来传递扭矩;钻头柄部有直柄与锥柄两种,前者用于小直径钻头,后者用于大直径钻头。
颈部供制造时磨削柄部退砂轮用,也是钻头打标记的地方,为制造方便直柄麻花钻一般不设颈部。
工作部分包括切削部分和导向部分,切削部分担负着主要切削工作,钻头有两条主切削刃,两条副切削刃和一条横刃,如图3-29所示;螺旋槽表面为钻头的前刀面,切削图3-29 麻花钻的切削部分削刃可视为一正一反安装的两把外圆车刀。
如图中虚线所示。
导向部分有两条对称的螺旋槽和刃带,螺旋槽用来形成切削刃和前角,并起排屑和输送冷却液作用;刃带起导向和修光孔壁的作用;刃带有很小的倒锥,由切削部分向柄部每长度上直径减小,以减小钻头与孔壁的摩擦。
麻花钻的主要几何角度有顶角、前角、后角、横刃斜角和螺旋角,如图3-30所示。
顶角是两条主切削刃在与其平行的平面上投影的夹角,加工钢料和图3-30 标准麻花钻的几何角度铸铁的钻头顶角取为118°±2°。
冲孔工艺流程

冲孔工艺流程
《冲孔工艺流程》
冲孔工艺是一种常用的金属加工方法,用于制作金属材料上的孔洞。
冲孔工艺流程通常包括以下几个步骤:
1. 设计孔位:首先,需要在金属材料上进行孔位的设计。
这需要根据最终产品的要求和规格来确定孔洞的尺寸、形状和位置。
2. 制作模具:根据设计好的孔位,需要制作相应的冲孔模具。
模具的制作需要考虑到孔洞的尺寸精度和表面质量要求。
3. 调试设备:在进行冲孔之前,需要对冲孔设备进行调试和检验。
确保设备的正常运行和模具的准确性。
4. 材料定位:将需要进行冲孔加工的金属材料固定在冲床上,并对其进行定位。
确保孔位的准确定位和稳定性。
5. 进行冲孔:在材料定位后,使用冲床对金属材料进行冲孔加工。
冲孔过程中需要控制冲头的下压力和速度,以确保孔洞的质量和尺寸准确。
6. 检验产品:冲孔完成后,需要对产品进行检验。
检查孔洞的尺寸、形状和表面质量,确保产品符合要求。
7. 后处理工艺:根据产品的要求,可能需要对冲孔加工后的产品进行清洗、去毛刺、抛光等后处理工艺。
以上就是冲孔工艺流程的基本步骤。
冲孔工艺在金属加工中应用广泛,可以用于制作各种金属产品,如筛网、滤网、通风孔板等。
通过精准的工艺控制和设备调试,可以实现高效、高质量的冲孔加工。
孔及螺纹加工

孔及螺纹加工钳工进行的孔加工,主要有钻孔、扩孔、铰孔和锪孔。
钻孔也是攻丝前的准备工序。
孔加工常在台式钻床、立式钻床或摇臂钻床上进行。
若工件大而笨重,也可使用手电钻钻孔。
铰孔有时也用手工进行。
一、钻床(一)台式钻床台式钻床简称台钻,如图11-43所示。
台钻是一种小型机床,安放在钳工台上使用。
其钻孔直径一般在12mm以下。
由于加工的孔径较小,台钻主轴转速较高,最高时每分钟可近万转,故可加工1mm以下小孔。
主轴转速一般用改变三角胶带在带轮上的位置来调节。
台钻的主轴进给运动由手动完成。
台钻小巧灵便,主要用于加工小型工件上的各种孔。
在钳工中台钻使用得最多。
(二)立式钻床立式钻床简称立钻,如图11-44所示。
一般用来钻中型工件上的孔,其规格用最大钻孔直径表示,常用的有25mm、35mm、4Omm、5Omm等几种。
立式钻床主要由机座、立柱、主轴变速箱、进给箱、主轴、工作台和电动机等组成。
主轴变速箱和进给箱与车床类似,分别用以改变主轴的转速与直线进给速度。
钻小孔时,转速需高些;钻大孔时,转速应低些。
钻孔时,工件安放在工作台上,通过移动工件位置使钻头对准孔的中心。
图11-43台式钻床图11-44立式钻床(三)摇臂钻床摇臂钻床是用来钻削大型工件的各种螺钉孔、螺纹底孔和油孔等,如图11-45所示。
它有一个能绕立柱旋转的摇臂。
主轴箱可以在摇臂上作横向移动,并随摇臂沿立柱上、下作调整运动。
刀具安装在主轴上,操作时,能很方便地调整到所需钻削孔的中心,而不需移动工件。
摇臂钻床加工范围广泛,在单件和成批生产中多被采用。
图11-45 摇臂钻床二、钻孔用麻花钻在材料实体部位加工孔称为钻孔。
钻床钻孔时,钻头旋转(主运动)并作轴向移动(进给运动),如图11-46所示。
图11-46 钻削时的运动由于钻头结构上存在着一些缺点,如刚性差、切削条件差,故钻孔精度低,尺寸公差等级一般为ITl2左右,表面粗糙度Ra值为12.5μm左右。
(一)麻花钻及安装方法麻花钻是钻孔的主要工具,其组成部分如图11-47所示。
台式钻床加工高精度孔距方法

台式钻床加工高精度孔距方法作者:陈博范来源:《职业·下旬》2019年第05期在国家职业技能鉴定和职业技能大赛中,装配钳工、机修钳工及工具钳工等钳工类工种高级工、技师甚至高级技师技能操作考核试题中,大部分为组合件锉配试题。
该组合件锉配试件中都有精密孔和高精度孔距加工,也是考核的一项重要内容。
在钳工技师操作技能考核试题中有这么一组精孔加工内容,用10mm厚板进行锉配,板上有两个精孔10H7需钻孔加工,板侧面到两孔的距離(边孔距)为30±0.04mm,两孔中心距50±0.04mm。
往往在技能操作考核中,考场一般只准备台式钻床和普通平口钳,在其他准备通知单中不允许准备靠模及钻模等二类加工工具,并要求在规定时间内手工操作完成精孔加工。
这将给操作者带来很大难度,因此大部分操作者很难保证加工精度。
笔者曾多次参加技能大赛,并训练学生参加技能大赛及各类技能鉴定,本文总结出几种提高钻孔精度的方法,与大家共同分享探讨。
一、精密划线找正加工法一般情况下,钻孔划线是用高度尺划出孔位置线,冲眼规圆,然后通过规圆找正钻孔。
由于冲眼规圆误差较大很难保证孔距精度,现在笔者介绍一种精密划线找正加工法。
这种方法是用高度游标卡尺或量块校准划出孔位置加工线及不同孔径的方格线,以试件孔10H7为例,分别划出6、8、9.8mm孔径边框方格线,也可多划几个不同孔径边框方格线。
钻孔时采用9.8mm、顶角为90°~100°麻花钻头,钻锪窝边线依次与孔径边框线同时相切,若没有相切,应及时找正试件位置直至9.8mm孔窝相切(若没有相切可反面再试一次)。
钻孔时注意要不同方位观察相切情况,也可用精密游标卡尺测量孔窝边线到孔径边框线位置尺寸,位置确定后钻通9.8mm孔,孔口倒角后,机铰或手铰10H7至精度要求。
这里需要注意的是划线钻孔前,用样冲冲眼也非常关键。
冲眼是一项技术工作,如果冲眼小了钻孔时定心不好,开始钻孔时钻头钻尖就会偏移,有时无法定心,有时刚定心就得开始找正,费时费劲。
14孔的常规加工方法
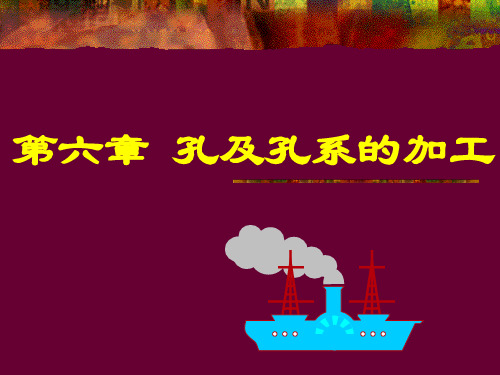
钻头 切削 部分
5个刀刃
两条主切削刃 两条副切削刃 一条横刃
6个刀面
两个螺旋形前刀面 两个经刃磨获得的后刀面 两个圆弧段的副后刀面
一、钻孔
3. 钻削用量 1) 背吃刀量asp
单位: mm
asp do
一、钻孔
3. 钻削用量 2)钻削速度vc
单位: m/min
vc do n 1000
一、钻孔
二、扩孔 2.扩孔钻的结构
图6-10 1) 齿数多(3.4齿); 2)不存在横刃; 3)切削余量小, 排屑容易。。
扩孔钻
三、铰孔 1.铰刀的类型
直柄机用铰刀 锥柄机用铰刀 硬质合金锥柄机用铰刀
手用铰刀
可调节手用铰刀 图6-14 铰刀的类型
套式机用铰刀
直柄莫氏圆锥铰刀 手用1: 50 锥度铰刀
三、铰孔 2.铰削过程的实质
1) 内圆磨削的表面较外圆磨削的粗糙。 2) 生产率较低。 3) 磨削接触区面积较大,砂轮易堵塞,散热和切削液
冲刷困难。
因此内孔磨削一般仅适用于淬硬工件的精加工, 在单件、小批生产中和在大批大量生产中都有应用。
七、高精度孔的珩磨
1.珩磨头及珩磨原理
图6-22)加工精度可达为IT7~IT6; 3)孔的表面粗糙度可控制在Ra6.3 ~
0.8μm。 4)能修正前工序造成的孔轴线的弯曲、
偏斜等形状位置误差;
四、镗孔
2.镗刀结构
五、拉孔
1.拉削过程
五、拉孔
1.拉削过程
图6-27 拉削圆孔
五、拉孔
1.拉削过程
图6-26 拉削键槽
五、拉孔
1.拉削过程
六、内圆磨削
六、内圆磨削
1. 工艺特点 1)磨削是零件精加工的主要方法之一; 2)对长径比小的, 内孔磨削的经济精度可达IT5~
第八章孔加工【Drill】.
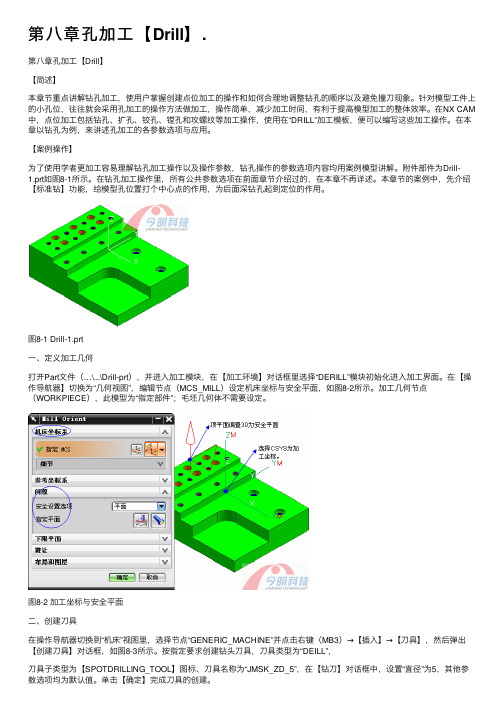
第⼋章孔加⼯【Drill】.第⼋章孔加⼯【Drill】【简述】本章节重点讲解钻孔加⼯,使⽤户掌握创建点位加⼯的操作和如何合理地调整钻孔的顺序以及避免撞⼑现象。
针对模型⼯件上的⼩孔位,往往就会采⽤孔加⼯的操作⽅法做加⼯,操作简单,减少加⼯时间,有利于提⾼模型加⼯的整体效率。
在NX CAM 中,点位加⼯包括钻孔、扩孔、铰孔、镗孔和攻螺纹等加⼯操作,使⽤在“DRILL”加⼯模板,便可以编写这些加⼯操作。
在本章以钻孔为例,来讲述孔加⼯的各参数选项与应⽤。
【案例操作】为了使⽤学者更加⼯容易理解钻孔加⼯操作以及操作参数,钻孔操作的参数选项内容均⽤案例模型讲解。
附件部件为Drill-1.prt如图8-1所⽰。
在钻孔加⼯操作⾥,所有公共参数选项在前⾯章节介绍过的,在本章不再详述。
本章节的案例中,先介绍【标准钻】功能,给模型孔位置打个中⼼点的作⽤,为后⾯深钻孔起到定位的作⽤。
图8-1 Drill-1.prt⼀、定义加⼯⼏何打开Part⽂件(…\...\Drill-prt),并进⼊加⼯模块,在【加⼯环境】对话框⾥选择“DERILL”模块初始化进⼊加⼯界⾯。
在【操作导航器】切换为“⼏何视图”,编辑节点(MCS_MILL)设定机床坐标与安全平⾯,如图8-2所⽰。
加⼯⼏何节点(WORKPIECE),此模型为“指定部件”;⽑坯⼏何体不需要设定。
图8-2 加⼯坐标与安全平⾯⼆、创建⼑具在操作导航器切换到“机床”视图⾥,选择节点“GENERIC_MACHINE”并点击右键(MB3)→【插⼊】→【⼑具】,然后弹出【创建⼑具】对话框,如图8-3所⽰。
按指定要求创建钻头⼑具,⼑具类型为“DEILL”,⼑具⼦类型为【SPOTDRILLING_TOOL】图标、⼑具名称为“JMSK_ZD_5”,在【钻⼑】对话框中,设置“直径”为5,其他参数选项均为默认值。
单击【确定】完成⼑具的创建。
图8-3 创建钻头⼑具三、创建标准钻孔操作在操作导航器“程序视图”⾥,选择节点“PROGRAM”并单击〖MB3〗→〖插⼊〗→〖操作〗,将弹出【创建操作】对话框。
孔位加工方法

孔旳技术要求
• 孔旳加工措施:钻孔、扩孔、铰孔、镗 孔、拉孔、磨孔、孔旳光整加工等。
高速钢刀具应用(钻头、铰刀)
(一)钻孔
台钻旳主轴进给由 转动进给手柄实现。
台钻小巧灵活,使 用以便,构造简朴, 主要用于加工小型 工件上旳多种小孔。
在仪表制造、钳工 和装配中用得较多。
• 立钻主轴旳轴向 进给可自动进给, 也可作手动进给。
2)主切削刃上各点前角不同(接近钻心处前角为负值), 切削性能差。
3)钻头旳副后角为零,摩擦力大。 4)主切削刃外缘处刀尖角小,刀齿单薄。 5)主切削刃长,且全刀宽切削,排屑困难。
特点图示
一、钻孔
3. 钻削用量
1) 背吃刀量asp
单位:mm
asp do
一、钻孔
3. 钻削用量
2)钻削速度vc
• 在立钻上加工多 孔工件可经过移 动工件来完毕。
用于大型工件、多 孔工件上旳大、中、 小孔加工,广泛用 于单件和成批生产
中。
钻孔
播放
麻花钻
主要用于孔旳粗加 工,IT11级下列;表面 粗糙度Ra25μm ~ 6. 3 μm 。
麻花钻旳构造
颈部:磨柄部时退 砂轮用,打标识
刀柄:钻头旳夹 持部分,用来传
磨孔时,砂轮旋转为 主运动,工件低速旋
转为圆周进给运动 (其方向与砂轮旋转 方向相反),工作台 带动工件作纵向进给 运动。 ,切深运动为 砂轮周期性旳径向进
给运动
磨孔旳工艺特点:
(七)研磨孔
在车床上研磨套类零件孔:研具为可调式研 磨棒。研磨前,套上工件,将研磨棒安装在 车床上,涂上研磨剂,调整研磨棒直径使其 对工件有合适旳压力,即可进行研磨。研磨
圆、螺纹及钻孔等。零件可在一次安装中完毕多表面旳加工。
7、孔加工
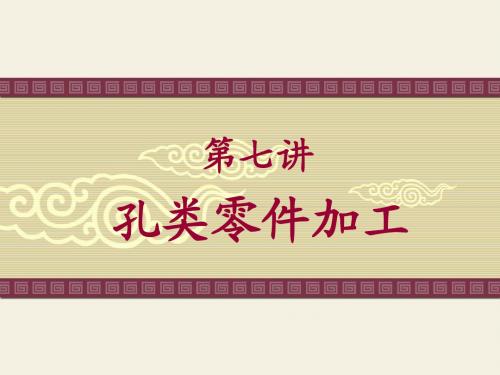
对于直径小于φ30mm无底孔的孔加工,通常采用 锪平端面——打中心孔——钻——扩——孔口倒角——铰加工方案, 对有同轴度要求的小孔,需采用锪平端面——打中心孔——钻——半 精镗——孔口倒角——精镗(或铰)加工方案。
二、孔加工方法的选择原则
内孔表面加工方法选择实例:
Φ40H7内孔可选择钻孔—粗镗(或扩孔)—半精镗—精镗方 案。阶梯孔Φ 13和Φ 22没有尺寸公差要求,因而可选择钻孔—锪 孔方案。
③ 孔加工:以切削进给的方式执行孔加工的动作。
④ 在孔底的动作:包括暂停、主轴准停、刀具位移 等动作。 ⑤ 返回到R点:继续孔的加工而又可以安全移动刀
具时选择R点。
⑥ 返回到初始点:孔加工完成后一般应选择初始点
四、固定循环功能
表1
2、固定循环的代码组成
① 固定循环平面 初始平面 初始平面是为了安全下刀而规定的一个平 面。初始平面到零件表面的距离可以任意设定在一个 安全的高度上 R点平面 R点平面又叫R参考平面,这个平面是刀具 下刀时自快进转为工进的高度平面。距工件表面的距 离主要考虑工件表面尺寸的变化,一般可取2~5mm。 孔底平面 加工盲孔时孔底平面就是孔底的Z轴高度, 加工通孔时一般刀具还要伸出工件底平面一段距离, 主要是保证全部孔深都加工到尺寸,钻削加工时还应 考虑钻头钻尖对孔深的影响。
60 80
40
25
3)高速深孔往复排屑循环G73 指令格式:G73
X_ Y_ Z_ R_ Q_ F_ ;
功能:该循环用于深孔加工。 孔加工动作如图所示,钻头先快速定位至X、Y所指定的坐标 位置,再快速定位至R点,接着以F所指定的进给速度向下钻 削至Q所指定的距离(Q必须为正值,用增量值表示),再快 速回退d 距离(d 是CNC系统内部参数设定的)。依此方式 进刀若干个Q,最后一次进刀量为剩余量(小于或等于q), 到达Z所指的孔底位置。G73指令是在钻孔时间断进给,有利 于断屑、排屑,冷却、润滑效果佳。
孔加工方法及实例

孔的精加工方法
孔的精加工
٭铰孔 ٭镗孔
加工精度高(形位精度好) 加工效率高(切削速度高, 不同材质对应不同刀片) 柔性好(直径可调)
加工范围宽:Φ1-880mm
成本低(刀片可换)
孔加工案例一
用户: 柳工箱体厂
工件: 箱体
材质: 球墨铸铁
硬度: HB190
孔径:
Φ25
+0.021 0
粗糙度: Ra1.6
套镗
段差加工
用户:襄阳亿普机械制造 有限公司 工件:主轴承盖 材质:45#钢 孔径:R47.62±0.08 单边余量:4.5mm 粗镗头:RW68-100CK6 刀片座:RW86106E 刀片:CCMM120408EFM – AC2000 前刃:R46,后刃:R47.62
段差加工
反镗加工
用户:北京机床所 工件:机床立柱 材质:HT200 孔径:Φ80mm 镗刀组合:BT50-CK6300 镗头:EWN68150CKB6 刀片: TCGT110204FN(H1)
工序二 粗镗至¢24.9
刀柄: BT50-CK1-135 座:TW2026A
粗镗头:TWN20-31CKB1 刀片
刀片: SCMP060204EFM(AC300G)
切削速度: V= 80m/min S=1020rpm 进给量:F=0.2mm/rev
深孔加工案例
用户:浙江凯达机床
工件:数控车床传动箱
用户: 长春天合转向器
工件: 转向器壳体
材质: QT400
孔径:Φ36
+0.025 0
(H7)
余量:Φ3.5mm
精镗: 刀柄BT50-CK6300
减径器:CK63-80
孔位加工方法

高速钢刀具应用(钻头、铰刀)
(一)钻孔
钻孔(drilling) :在工件的实体部位加工 孔的工艺过程 刀具:麻花钻。 机床:钻床、车床、镗床、铣床
台钻的主轴进给由 转动进给手柄实现。
台钻小巧灵活,使 用方便,结构简单, 主要用于加工小型 工件上的各种小孔。
在仪表制造、钳工 和装配中用得较多。
特点图示
一、钻孔
3. 钻削用量
1) 背吃刀量asp
单位:mm
asp do
一、钻孔
3. 钻削用量
2)钻削速度vc
单位:m/min
vc do n 1000
一、钻孔
3. 钻削用量
3)钻削进给量与进给速度:
f 单位:mm/r fz 单位:mm/z Vf 单位:mm/min
钻孔用的夹具
钻孔的工艺特点
• (1)易引偏
a)在钻床上钻孔
b)在车床上钻孔
• 引偏是孔径扩大或孔轴 线偏移和不直的现象。
• 由于钻头横刃定心不准, 钻头刚性和导向作用较 差,切入时钻头易偏移、 弯曲。
• 在钻床上钻孔易引起孔 的轴线偏移和不直;
• 在车床上钻孔易引起孔 径扩大
• (2)排屑困难
• 钻孔的切屑较宽,在孔内被迫 卷成螺旋状,流出时与孔壁发 生剧烈摩擦而刮伤已加工表面, 甚至会卡死或折断钻头。
两个圆弧段的副后刀面
1、麻花钻结构特点
1)横刃较长,横刃处前角为负值切削阻力大,据实验50% 的轴向力和15%的扭距。
2)主切削刃上各点前角不同(靠近钻心处前角为负值), 切削性能差。
3)钻头的副后角为零,摩擦力大。 4)主切削刃外缘处刀尖角小,刀齿薄弱。 5)主切削刃长,且全刀宽切削,排屑困难。
铰孔的方式有机铰和手铰两种。
数控车床的孔加工编程方法举例
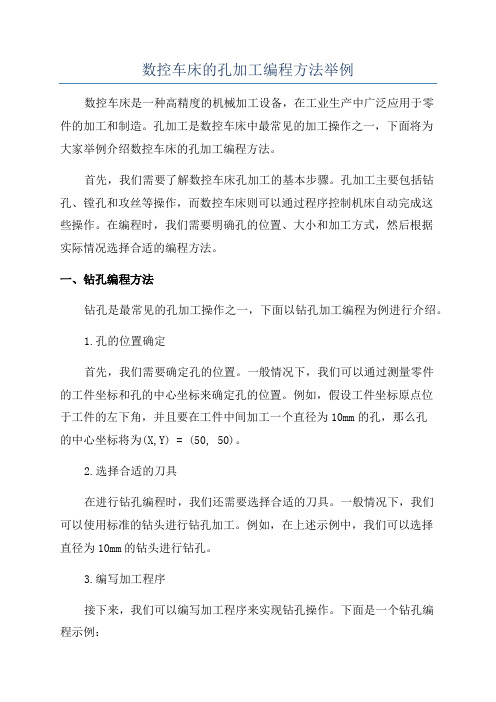
数控车床的孔加工编程方法举例数控车床是一种高精度的机械加工设备,在工业生产中广泛应用于零件的加工和制造。
孔加工是数控车床中最常见的加工操作之一,下面将为大家举例介绍数控车床的孔加工编程方法。
首先,我们需要了解数控车床孔加工的基本步骤。
孔加工主要包括钻孔、镗孔和攻丝等操作,而数控车床则可以通过程序控制机床自动完成这些操作。
在编程时,我们需要明确孔的位置、大小和加工方式,然后根据实际情况选择合适的编程方法。
一、钻孔编程方法钻孔是最常见的孔加工操作之一,下面以钻孔加工编程为例进行介绍。
1.孔的位置确定首先,我们需要确定孔的位置。
一般情况下,我们可以通过测量零件的工件坐标和孔的中心坐标来确定孔的位置。
例如,假设工件坐标原点位于工件的左下角,并且要在工件中间加工一个直径为10mm的孔,那么孔的中心坐标将为(X,Y) = (50, 50)。
2.选择合适的刀具在进行钻孔编程时,我们还需要选择合适的刀具。
一般情况下,我们可以使用标准的钻头进行钻孔加工。
例如,在上述示例中,我们可以选择直径为10mm的钻头进行钻孔。
3.编写加工程序接下来,我们可以编写加工程序来实现钻孔操作。
下面是一个钻孔编程示例:O0001(程序号)N1G90G54G64G80(绝对坐标系,工件坐标系,等距插补模式,取消固定循环)N2S500M3(设置主轴转速为500转/分钟,开启主轴)N3G0X50Y50(快速定位到孔的中心坐标)N4 G81 Z-10 R2 F100 (启动钻孔循环,Z轴下降10mm,每次进刀2mm,进给速度为100mm/分钟)N5G80(取消固定循环)N6M5(关闭主轴)N7M30(程序结束)在上述示例中,首先通过G90指令设置绝对坐标系和工件坐标系。
然后通过G64指令设置等距插补模式,取消固定循环。
接着,通过G0指令进行快速定位,将刀具移动到孔的中心坐标处。
然后通过G81指令启动钻孔循环,设置Z轴下降10mm,每次进刀2mm,进给速度为100mm/分钟。
第六章 孔加工
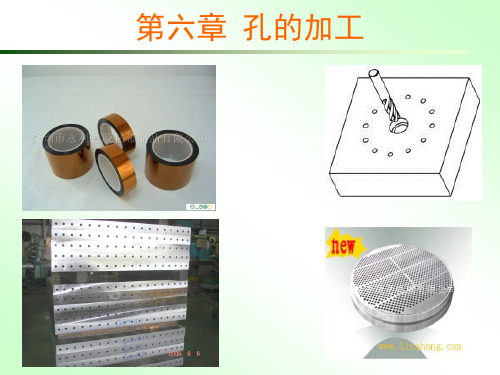
图6.3
标准型群钻结构
16
2.可转位浅孔钻 适合在车床上加工d=17.5~80mm、l/d≤3 的中等直径浅孔。
17
图6.4 可转位浅孔钻
18
3.错齿内排屑深孔钻 对于直径较大的深孔(孔深度与直径之比 大于5~10),由于切削量很大,必须较好地 解决排屑和冷却问题。错齿内排屑深孔钻是常 用的深孔加工钻头。工作时钻头由浅牙矩螺纹 与钻杆联接,通过刀架带动,经液封头钻入工 件。通过刀齿的交错排列实现了分屑,便于切 屑的排出;通过钻管与工件孔壁之间的间隙加 入高压切削液,使之充分地对切削区进行冷 却,并利用高压切削液把切屑从钻头和钻管的 内孔中冲出。硬质合金条起导向的作用。
拉削加工
1.拉床及拉削方法 拉削是用拉刀加工工件内、外表面的方法。拉削在拉 床上迸行。拉床分卧式和立式两类,下图为卧式拉床的示 意图。拉削时工作拉力较大,所以拉床一般采用液压传动。 常用拉床的额定拉力有100,200,400kN等。
卧式拉床示意图
l-压力表 2-液压传动部件 3-活塞拉杆 4-随动支架 5-刀架 6-床身 7-拉刀 8-支挣 9-工件 10-随动刀架
26
3.深孔钻
通常把孔深与孔径之比大于5~10倍的孔称为深孔,加工 所用的钻头称为深孔钻。 由于孔深与孔径之比大,钻头细长,强度和刚度均较差, 工作不稳定,易引起孔中心线的偏斜和振动。为了保证孔 中心线的直线性,必须很好地解决导向问题;由于孔深度 大,容屑及排屑空间小,切屑流经的路程长,切屑不易排 除,必须设法解决断屑和排屑问题;深孔钻头是在封闭状 态下工作,切削热不易散出,必须设法采取措施确保切削 液的顺利进入,充分发挥冷却和润滑作用。
图10 铰刀
34
铰刀
35
- 1、下载文档前请自行甄别文档内容的完整性,平台不提供额外的编辑、内容补充、找答案等附加服务。
- 2、"仅部分预览"的文档,不可在线预览部分如存在完整性等问题,可反馈申请退款(可完整预览的文档不适用该条件!)。
- 3、如文档侵犯您的权益,请联系客服反馈,我们会尽快为您处理(人工客服工作时间:9:00-18:30)。
• 孔是箱体、支架、套筒、环、盘类零件上 的重要表面,也是机械加工中经常遇到的 表面。
• 在加工精度和表面粗糙度要求相同的情 况下,加工孔比加工外圆面困难,生产 率低,成本高: • (1)刀具的尺寸受到被加工孔的尺寸的 限制,故刀具的刚性差,不能采用大的 切削用量。 • (2)刀具处于被加工孔的包围中,散热 条件差,切屑排出困难,切削液不易进 入切削区,切屑易划伤加工表面。
高速钢刀具应用(钻头、铰刀)
(一)钻孔
钻孔(drilling) :在工件的实体部位加工 孔的工艺过程 刀具:麻花钻。 机床:钻床、车床、镗床、铣床
台钻的主轴进给由 转动进给手柄实现。 台钻小巧灵活,使 用方便,结构简单, 主要用于加工小型 工件上的各种小孔。 在仪表制造、钳工 和装配中用得较多。
铰削用量的选择:
进给量不能取得过小,否则切削厚度过薄,铰刀的挤压 作用会明显加大,加速铰刀后刀面的磨损。 一般铰削钢体时,进给量为0.3 ~2mm/r,铰铸铁时, 0.5 ~3mm/r 。
钻头、扩孔钻、铰刀都是标准刀具。 中等尺寸以下较精密的孔,单件小批乃至 大批大量生产,采用钻—扩—铰这种典型 加工方案进行加工非常方便。
孔的技术要求
①尺寸精度: 孔径和长度的尺寸精度。 ②形状精度: 孔的圆度、圆柱度及轴线的直线 度。 ③位置精度: 孔与孔或孔与外圆面的同轴度, 孔与孔或孔与其它表面之间的尺寸精度、平行 度、垂直度等。 ④表面质量: 表面粗糙度、表层加工硬化和表 层物理力学性能要求等。
• 孔的加工方法:钻孔、扩孔、铰孔、镗 孔、拉孔、磨孔、孔的光整加工等。
拉刀的类型
拉刀的类型
拉刀的结构
• • • • • • • •
头部——与机床连接,传递运动和拉力。 颈部——头部和过渡锥连接部分。 过渡锥部——使拉刀容易进入工件孔中,起对准中心的作用。 前导部——起导向和定心作用,防止拉刀歪斜,并可检查拉削前孔径是否 太小,以免拉刀第一刀齿负荷太大而损坏。 切削部——切除全部的加工余量,由粗切齿、过渡齿和精切齿组成。 校准部——起校准和修光作用,并作为精切齿的后备齿。 后导部——保持拉刀最后几个刀齿的正确位置,防止拉刀即将离开工件时, 工件下垂而损坏已加工表面。 尾部——防止长而重的拉刀自重下垂,影响加工质量和损坏刀齿。
颈部:磨柄部时退 砂轮用,打标记 刀柄:钻头的夹 持部分,用来传 递扭矩
为了保证钻头必 要的刚性和强度, 工作部分的钻心 直径向柄部方向 递增。
麻花钻的组成和切削部分
一、钻孔
2. 高速钢麻花钻的 两条主切削刃 结构
5个刀刃 两条副切削刃
钻头 切削 部分 6个刀面
一条横刃
两个螺旋形前刀面 两个经刃磨获得的后刀面 两个圆弧段的副后刀面
1、麻花钻结构特点
1)横刃较长,横刃处前角为负值切削阻力大,据实验50% 的轴向力和15%的扭距。 2)主切削刃上各点前角不同(靠近钻心处前角为负值),
切削性能差。
3)钻头的副后角为零,摩擦力大。 4)主切削刃外缘处刀尖角小,刀齿薄弱。 5)主切削刃长,且全刀宽切削,排屑困难。
特点图示
一、钻孔
• (3)切削温度高,刀具磨损快 • 切削时产生的切削热多,加之钻 削为半封闭切削,切屑不易排出, 切削热不易传出,使切削区温度 很高。
提高孔的加工精度的措施
(1)仔细刃磨钻头,使两个切削刃的长度 相等和顶角对称;在钻头上修磨出分屑槽, 将宽的切屑分成窄条,以利于排屑。
• (2)用顶角 2φ=90~100°的短 钻头,预钻一个锥 形坑可以起到钻孔 时的定心作用。
扩孔钻
用于对已钻孔的进一 步加工,IT10 ~ IT11级; 表面粗糙度6. 3 ~ 3.2μm 。
二、扩孔
1. 工艺特点 1)扩孔是孔的半精加工方法; 2)一般加工精度为IT10~IT9; 3)孔的表面粗糙度可控制在Ra6.3 ~ 3.2μm。
当钻削 dw >30mm直径的孔时,为了减小钻削力 及扭矩,提高孔的质量,一般先用(0.5~0.7)dw 大小的钻头钻出底孔,再用扩孔钻进行扩孔,则可 较好地保证孔的精度和控制表面粗糙度,且生产率 比直接用大钻头一次钻出时还要高。
a)手用铰刀 b)机用铰刀
¢20mm,锥柄: ¢5mm~ ¢50mm,
L1—工作部分;L2—切削部分;L3—修光部分;L4—柄部
铰刀特点:
1)刀齿数多(6~12个),制造精度高;具 有修光部分,可以用来校准孔径、修光孔壁; 2)刀体强度和刚性较好(容屑槽浅,芯部直 径大);故导向性好,切削平稳; 3)铰孔的余量小切削力较小;铰孔时的切速 度较低,产生的切削热较少。 因此,铰孔的加工质量更好。
拉削运动
拉刀以切削速度vc 作主运动,进给运 动是由后一个刀齿 高出前一个刀齿 (齿升量af)来完 成的,从而能在一 次行程中一层一层 地从工件上切去多 余的金属层,获得 所要求的表面
拉孔时,工件的预制孔不必 精加工,工件也不需夹紧, 工件以端面靠紧在拉床的支 承板上,因此工件的端面应 与孔垂直,否则容易损坏拉 刀。
用于加工机座、箱体、支架等大型零件上孔 径较大、尺寸精度和位置精度要求高的孔系, 也可加工单个孔、台阶孔和孔内环形槽、镗 平面等。
(五)拉孔
拉孔(hole broaching)是用拉刀在拉 床上加工孔的过程
拉 刀
拉削加工质量好,生产 率高。拉刀寿命长,并且拉 床结构简单。但拉刀结构复 杂,制造比较麻烦,价格较 高,因而多用于大量和批量 生产的精加工。
• 立钻主轴的轴向 进给可自动进给, 也可作手动进给。 • 在立钻上加工多 孔工件可通过移 动工件来完成。
用于大型工件、多 孔工件上的大、中、 小孔加工,广泛用 于单件和成批生产 中。
钻孔
播放
麻花钻
主要用于孔的粗加 工,IT11级以下;表面 粗糙度Ra25μm ~ 6. 3 μm 。
麻花钻的构造
钻、扩、铰只能保证孔本身的精度,而不 易保证孔与孔之间的尺寸精度及位置精度。 为此,可以利用钻模进行加工,或者采用 镗孔。
(四)镗孔
镗孔(boring) :利用镗刀对已有的孔进行 加工 对于直径较大的孔(一般D>φ80~100mm)、 内成形面或孔内环槽等,镗削是唯一合适 的加工方法。
三 镗孔
图 镗床镗孔
(3)用钻模为钻头导向, 可减少钻孔开始时的 引偏, 特别是在斜面或曲面 上钻孔时更有必要。
钻孔的应用
• 钻孔加工精度很低,生产率低。 • 可用于质量要求不高的孔的终加工,如螺 钉孔、油孔等;也可用于技术要求高的孔 的预加工或攻螺纹前的底孔加工。
5、切削液的选择
种类:乳化油液(冷却)、硫化切削油(润滑)、 动植物油(润滑) 。
1—球面垫板 2—工件 3—拉刀
如果工件的端面与孔不垂直, 则应采用球面自动定心的支 承垫板来补偿。通过球形支 承垫板的略微转动,可以使 工件上的孔自动地调整到与 拉刀轴线一致的方向。
五、拉孔
1. 拉削过程
图6-27 拉削圆孔
拉削特点:
(1)生产率高。拉刀同时工作的刀齿多,而且一次行 程能够完成粗、精加工。 (2)拉刀耐用度高。拉削速度低,每齿切削厚度很 小,切削力小,切削热也少。 (3)加工精度高。拉削的尺寸公差等级一般可达 IT8~IT7,表面粗糙度Ra值为0.8~0.4μm。 (4)拉床只有一个主运动(直线运动),结构简单, 操作方便。 (5)加工范围广。拉削可以加工圆形及其它形状复 杂的通孔、平面及其它没有障碍的外表面,但不能加工台 阶孔、不通孔和薄壁孔。 (6)拉刀成本高,刃磨复杂,除标准化和规格化的 零件外,在单件小批生产中很少应用。
图 车床镗孔
镗刀旋转作主运动,工件或镗刀作进给运动的切削 加工方法称为镗削加工。镗削加工主要在铣镗床、镗 床上进行,是常用的孔加工方法。 铣镗床镗孔主要用于机座、箱体、支架等大型零 件上孔和孔系的加工。此外,铣镗床还可以加工外圆 和平面。由于一些箱体和大型零件上的一些外圆和端 面与它们上的孔有位置精度要求,所以在镗床上加工 孔的同时,也希望能在一次装夹工位内把这些外圆和 端面都加工出来。镗孔加工精度为IT7~IT8,表面粗 糙度Ra值为0.8~0.1μm。
铰削用量的选择:
精铰时,一般半径上铰削余量为0.03~0.15mm, 其值取决于工件材料及对孔要求的精度及表面粗糙 度。 余量过大,则孔的精度不高,表面粗糙;
余量过小,切不掉表面缺陷层,影响孔的质量。
一般铰削钢体时,切削速度为1.5 ~5m/min,铰铸铁 时, 8 ~10m/min,切削速度过高,加剧刀具磨损, 还会引起振动。
• (1)易引偏
a)在钻床上钻孔
b)在车床上钻孔
• 引偏是孔径扩大或孔轴 线偏移和不直的现象。 • 由于钻头横刃定心不准, 钻头刚性和导向作用较 差,切入时钻头易偏移、 弯曲。 • 在钻床上钻孔易引起孔 的轴线偏移和不直; • 在车床上钻孔易引起孔 径扩大
• (2)排屑困难 • 钻孔的切屑较宽,在孔内被迫 卷成螺旋状,流出时与孔壁发 生剧烈摩擦而刮伤已加工表面, 甚至会卡死或折断钻头。
a) 车通孔
b)车不通孔
c)车槽
在车床上镗孔
播放
镗床上镗孔:镗刀刀杆随主轴一起旋转,完成主运 动;进给运动可由工作台带动工件纵向移动,也可 由主轴带动镗刀杆轴向移动完成。
a)工件不动、刀具旋转并进给 b)刀具旋转、工件进给
镗刀:单刃镗刀和浮动式镗刀
单刃镗刀:结构简单,制造 容易,通用性好。
双刃镗刀:两边都 有切削刃,工作时, 可以消除径向力对 镗杆的影响,工件 的径向尺寸与精度 是由镗刀保证的。
3. 钻削用量 1) 背吃刀量asp 单位:mm
asp do
一、钻孔
3. 钻削用量 2)钻削速度vc 单位:m/min
vc
do n
1000
一、钻孔
3. 钻削用量 3)钻削进给量与进给速度: f fz Vf 单位:mm/r 单位:mm/z 单位:mm/min