大型矿用自卸车静液压传动系统设计设计
重型自卸汽车举升液压系统设计
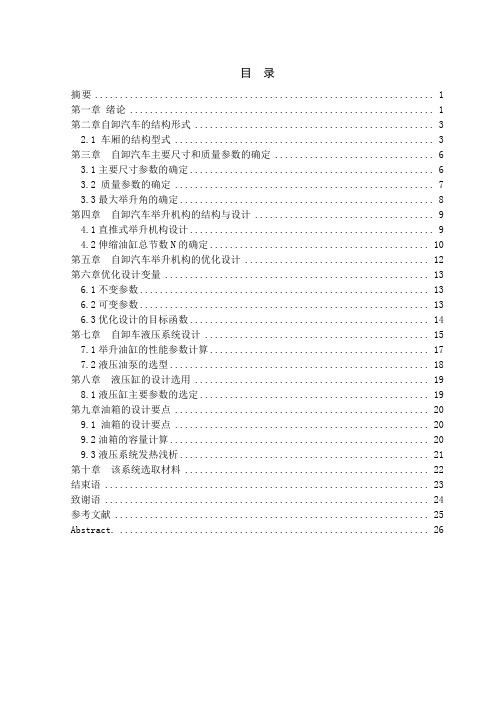
3.2质量参数的确定[1]
额定装载质量是自卸汽车的基本使用性能参数之一。目前,中、长距离公路运输趋向使用重型自卸汽车,以便提高运输效率、降低运输成本,额定装载质量一般为9~19t;而承担市区或市郊短途运输的自卸汽车额定装载质量为4.5~9t。同时,还应考虑到厂家的额定装载质量合理分级,以利于产品系列化、部件通用化和零件标准化。此外,额定装载质量还必须与选用的二类货车底盘允许的最大总质量相适应。
改装部分质量主要包括:车厢质量、副车架质量、液压系统质量、举升机构质量以及其他改装部件的质量。改装部分质量既可通过计算、称重求得,也可根据同类产品提供的数据进行估算。
自卸汽车整车整备质量是指装备齐全、加够燃料、液压油和冷却液的空车质量。它一般是二类底盘整备质量与改装部分质量的总和。是自卸汽车总体设计的重要设计参数之一。
通常由二类货车底盘改装的自卸汽车(Me<15t)质量利用系数略低于原货车的质量利用系数。国产自卸汽车的ηGO=1.0~1.5,国外自卸车的ηGO=1.3~2.0.如表3—2所示
图3—2自卸汽车质量利用系数
由此ηGO= =0.652(1—4)
自卸汽车的质心位置是指满载时整车质量中心位置,自卸汽车的质心位置对使用性能(例如汽车的制动性、操纵稳定性等)影响很大。因此,自卸汽车总体设计时应尽量使质心位置接近原货车的质心位置。
较低
系统倾卸稳定性
较差
较好
系统耐冲性
较好
较差
直推式举升机构结构简单,较易于设计。但这样易导致油缸泄漏或双缸不同步,进而造成车厢举升受力不均。目前,该类举升机构主要用于重型自卸汽车。
综上所述,结合选择车型情况,对于长安SC3043JD32自卸车,本文选用油缸直推式举升机构。并能承受较大的偏置载荷;举升支架在车厢后部,车厢受力状况较好。
自卸汽车液压系统设计

自卸汽车液压系统设计自卸汽车又称自卸车,是一种用于运输散装物料的特种车辆。
其主要特点是具有自行卸料功能,即可以将装载物体自行卸下,无需借助外力。
自卸汽车液压系统是其实现自卸功能的关键部件,对其性能和安全具有重要影响。
一、液压系统组成自卸汽车液压系统主要由以下部件组成:1.液压泵:将驱动装置提供的动力转化为液压能,提供能量给液压系统。
2.液压缸:将液压能转化为机械能,将卸载箱体提升并斜着倾卸。
3.液压阀:控制油液流动,保证机构的升降和倾卸。
4.油箱:存储液压油,供给液压泵使用。
5.油管:连接各液压元件,传递压力和流量。
6.过滤器:过滤液压油中的杂质,保护系统元件。
7.压力表:测量系统的压力值,保证液压系统工作在安全范围内。
自卸汽车液压系统采用液压原理实现自卸功能。
液压系统的能量转化和传递都依赖于液压油,在高压作用下,液压油产生一定的流量,将液压泵等元件中的活塞或柱塞带动,从而实现传递功效。
具体实现过程如下:1.自卸汽车液压系统的工作开始于油箱内的液压油。
液压泵通过吸油口从油箱中吸取液压油,通过驱动装置产生的动力来转动液压泵中的转子,从而产生压力和流量。
2.压力和流量传递至进口压力油管和回油口分别通过液压管路连接至液压阀组。
液压阀组中的各个阀功能不同,如配压阀、溢流阀、换向阀、电磁阀等,根据不同的控制信号和工作状态来控制液压油的流经和流量,使其他元件协调工作。
3.液压油进入液压缸腔,推动活塞使自卸罐体倾卸。
在倾倒进程中可以通过控制手柄控制升降高度。
4.液压系统中的安全阀起到保护作用,当液压系统油压过高时,安全阀开始工作,保证液压系统正常工作。
在液压系统控制方面采用的是手动控制,通过液压控制阀进行跨越控制。
自卸车的制动过程中,减速器的作用就体现出来了,液压系统的制动能让司机更加轻松地执行制动操作。
此外,液压系统具有很多优点,如下:1.传递能力强:液压系统可根据需要来调整系统中的压力和流量,可在多个执行机构上做功,实现集中控制。
煤矿液压传动控制系统设计

体 。由于煤矿工程周 计
煤 矿 中的液 压传 动控 制系 统在 正常 工作 时,执行元件 能够在 最高和最低旋转速度范围
内任 意 一个 旋 转速 度 下 稳 定 运 行 , 此 时 对 液 压
而 比较较适合采用开放式的循环回路。 1 . 2 _ 3制定调速控制方案 速度一流量控制速度和速度一 压力控制都 是对液压传动速度进 行控制 调节 的方式。在速 度一流量控制方式 中,如果采用变量马达或者
是 结构 较 为 复 杂 的变 量 泵 , 会 花 费 大 量 的成 本 :
而最大供油量可以通过 以下公式来计算 :
O K( QM 十 q Y _ n )
其 中 K为修 正系数,一般在 1 . 1 ~ 1 . 3之
间取值;Q M 是指液压马达实际所 需最大流量, 可 以用排量乘 以转速所得 的理论流量与其容积 效率的 比值求得 :q Y mi n是指一 溢流 阀最小溢 流量,一般取值 0 . 5 x 1 0 - 4 m3 / S 。 随着 机 电一体 化 的发展 ,液压 传动 控制 系统与微 电子、计算机等现代化技术相 结合 , 使得液压传动无级调速 的应用更加广泛 。对于 液压传动控制系统的设计没有定性的方式和步 骤,要根据实际生产需要进行科学合理 设计 , 使其更好的为生产服务 。
矿 的生产情 况。而 液压控 制系统作为煤矿生产
设 备 的 关键 性 组成 部 分 , 一 定 要 对 加 强 对 液 压
该 比计 算得 出 的最高 负荷 压高 ,通常 要高 出 再 由执行元件 的回油控制系统 排到油箱 中,不 2 5 %一 6 0 %左 右 , 因 此扩 充压 力 储 备 能 九 另 外 , 传 动 控 制 系 统 的 设 计 , 以提 升我 国 煤矿 生 产 效
自卸汽车举升机构的机械及液压系统设计
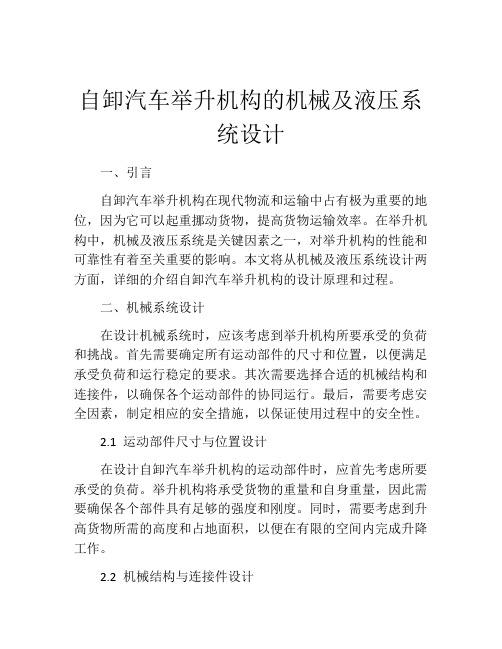
自卸汽车举升机构的机械及液压系统设计一、引言自卸汽车举升机构在现代物流和运输中占有极为重要的地位,因为它可以起重挪动货物,提高货物运输效率。
在举升机构中,机械及液压系统是关键因素之一,对举升机构的性能和可靠性有着至关重要的影响。
本文将从机械及液压系统设计两方面,详细的介绍自卸汽车举升机构的设计原理和过程。
二、机械系统设计在设计机械系统时,应该考虑到举升机构所要承受的负荷和挑战。
首先需要确定所有运动部件的尺寸和位置,以便满足承受负荷和运行稳定的要求。
其次需要选择合适的机械结构和连接件,以确保各个运动部件的协同运行。
最后,需要考虑安全因素,制定相应的安全措施,以保证使用过程中的安全性。
2.1 运动部件尺寸与位置设计在设计自卸汽车举升机构的运动部件时,应首先考虑所要承受的负荷。
举升机构将承受货物的重量和自身重量,因此需要确保各个部件具有足够的强度和刚度。
同时,需要考虑到升高货物所需的高度和占地面积,以便在有限的空间内完成升降工作。
2.2 机械结构与连接件设计自卸汽车举升机构的机械结构和连接件要求具有足够的强度和稳定性,以保证各个运动部件之间的协同运行。
常用的机械结构包括点式连杆机构、摆杆机构、旋转机构等,连接件包括螺栓、销子、铰链等。
在选择机械结构和连接件时,应当根据实际工作情况和要求,进行合理的选择和安排。
2.3 安全措施设计在自卸汽车举升机构中,安全永远是重中之重。
设计安全措施是确保机构在工作期间的正确且稳定运行的必要条件。
一些常规的安全措施包括安装安全带、加强运动部件的抗摆性、设置限制器等。
任何的失误或差错都可能导致安全问题,因此一定要在设计阶段充分考虑和采取必要的安全措施。
三、液压系统设计在自卸汽车举升机构中,液压系统是将机械的能量转换为液体压力能量的关键,其主要功能是控制升降运动和保持稳定平衡。
液压系统设计的目的是保证油液的压力、流量、温度和清洁度等指标,在一定的工作条件下保持稳定运行,满足设备使用的需要。
自卸半挂车液压系统的设计浅谈

Internal Combustion Engine &Parts0引言在当前的物料运输、建筑施工等领域中,自卸半挂车是使用相对广泛的运输车辆之一。
在液压系统的控制下,自卸半挂车可完成限位、中停、举升、回位、顶棚开闭等多项功能,具有良好的应用价值[1]。
此外,该设备还存在操作简便、经济性高、运输效率高、物料剩余率低等优势,因此在工业领域具有重要作用。
下文就针对自卸半挂车液压系统的设计问题做深入探究。
1自卸半挂车液压系统结构用于一般用途的自卸半车主要由车架、支承装置、液压系统、制动系统、连接装置、悬挂系统、翻转装置、轮轴系统、顶棚装置淤积车厢等内容组成[2]。
其中,液压系统是自卸半挂车的重要构成模块,只有在液压系统的控制下,自卸半挂车才能完成中停、回位、举升、限位等相关工作。
在具体作业过程中,液压系统可以使自卸半挂车车厢按照设计多角度倾斜举升,当货物装卸完成后又按照原有轨迹自动回落至初始高度。
其他功能也都是在液压系统的控制下完成。
液压系统作用原理如下:自卸半挂车需要倾卸货物时,通过操作组合手动换向阀的手柄,使液压油进行在系统内运转,运转路径为经气控换向阀进入液压缸体A 腔,随着液压油的运动产生油压,由油压推动液压缸的各级缸筒按照次序依次渗出,随着这一动作,自卸半挂车的车厢会抬升到既定角度。
当达到自卸半挂车的最大设计行程需要回落时,再次操作组合手动换向阀的手柄,操控液压油回流,以此同时,在油压的作用下,液压油会进入缸体的B 腔,并对伸出的末级缸作用一定的回拉力,在回拉力的作用下,自卸半挂车车厢动力将逐渐下降,车厢随之回落。
在具体的装卸、运输过程中,如有需要,可操控顶棚的开启马达的控制换向阀,可以打开顶棚;反之则关闭顶棚[3]。
经过上述分析可以得知,较之其他同类型的验货车辆,自卸半挂车具有一定的应用优势,如运输效率相对较高,且便于操作与维修,系统结构也相对科学合理,设备安全性与可靠性高,在运输过程中对道路的环保、货物的安全性都有可靠保障。
平推式自卸汽车设计(液压系统) 本科毕业论文

平推式自卸汽车设计(液压系统)本科毕业论文一、绪论随着工程领域的不断发展,自动化技术在汽车工业中起到了至关重要的作用。
自卸汽车是一种重要的运输工具,具有将货物自动卸载的特点,可以提高运输效率和减少人工成本。
本文根据自卸汽车的使用环境和性能要求,设计了一种基于液压系统的平推式自卸汽车。
二、液压系统结构设计1. 液压泵组液压泵组是整个液压系统的核心部件,负责向液压缸供应高压液体以实现装载和卸载的操作。
泵组采用双联泵,即高压泵负责提供液压缸所需的高压液体,低压泵负责提供稳定的低压液体以保证泵组正常工作。
泵组采用封闭式设计,具有较强的抗污染和防漏性能。
2. 液压缸结构液压缸是平推式自卸汽车装卸货物的关键器件,本文设计的液压缸结构为双作用柱塞式。
液压缸采用高强度合金钢材料,具有承载能力强、耐磨性高等优点。
为了提高液压缸的输出力,本系统在设计中对液压缸的面积进行了优化,同时在液压缸内部设置了防爆装置以确保安全性。
3. 液压控制阀液压控制阀是液压系统的调节器,负责控制液压油在各个液压缸之间的流量和压力,以实现车体升、平推、降的操作。
本文设计的液压控制阀采用二位四通结构,具有结构简单、操作方便等优点。
同时,液压控制阀采用防爆设计,在使用过程中安全可靠。
三、自卸系统设计1. 倾斜平台结构倾斜平台是自卸汽车实现卸载功能的关键部件。
本文设计的倾斜平台采用加强型钢构架,并对其梁体进行加厚,以保证其承载力和稳定性。
同时,倾斜平台采用翘头式设计,可以在卸载时有效地减少货物残留。
2. 卸载控制系统卸载控制系统是指自卸汽车在实现卸载前,必须进行的操作。
本文设计的卸载控制系统采用液压控制方式,通过液压控制阀调节液压缸的压力和流量,实现卸载功能。
同时,卸载控制系统具有自动反转功能,可以在卸载完成后自动恢复到装载状态。
四、结论本文通过分析自卸汽车的使用环境和性能要求,设计了基于液压系统的平推式自卸汽车。
在该设计中,液压泵组、液压缸和液压控制阀构成了液压系统的核心部件。
自卸汽车举升机构的机械及液压系统设计
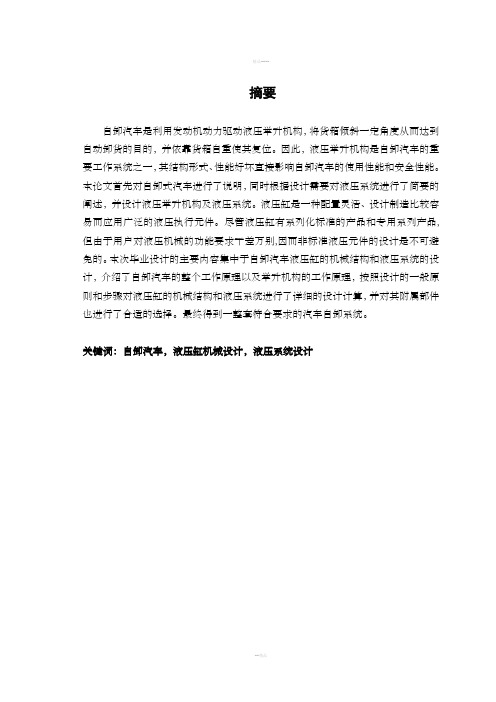
摘要自卸汽车是利用发动机动力驱动液压举升机构,将货箱倾斜一定角度从而达到自动卸货的目的,并依靠货箱自重使其复位。
因此,液压举升机构是自卸汽车的重要工作系统之一,其结构形式、性能好坏直接影响自卸汽车的使用性能和安全性能。
本论文首先对自卸式汽车进行了说明,同时根据设计需要对液压系统进行了简要的阐述,并设计液压举升机构及液压系统。
液压缸是一种配置灵活、设计制造比较容易而应用广泛的液压执行元件。
尽管液压缸有系列化标准的产品和专用系列产品,但由于用户对液压机械的功能要求千差万别,因而非标准液压元件的设计是不可避免的。
本次毕业设计的主要内容集中于自卸汽车液压缸的机械结构和液压系统的设计,介绍了自卸汽车的整个工作原理以及举升机构的工作原理,按照设计的一般原则和步骤对液压缸的机械结构和液压系统进行了详细的设计计算,并对其附属部件也进行了合适的选择。
最终得到一整套符合要求的汽车自卸系统。
关键词:自卸汽车,液压缸机械设计,液压系统设计目录1 绪论 (1)1.1 自卸汽车的作用 (1)1.2 自卸汽车的分类 (1)1.3 常见自卸汽车分类举例 (2)1.4 自卸汽车的举升机构 (3)1.5 自卸汽车的结构特点 (3)1.6 小结 (4)2 液压系统设计 (5)2.1 液压概述 (5)2.1.1 液压技术的发展 (5)2.1.2 液压传动 (5)2.2 自卸汽车液压系统设计 (6)2.2.1 液压缸概述 (6)2.2.2 液压系统原理图 (7)2.2.3 液压系统图 (8)2.3 小结 (9)3 液压缸结构设计 (10)3.1 液压缸结构设计的依据、原则和步骤 (11)3.1.1 设计依据 (11)3.1.2 设计的一般原则 (12)3.1.3 设计的一般步骤 (12)3.2 液压缸基本结构参数及相关标准 (13)3.2.1 液压缸的液压力分析和额定压力的选择 (14)3.2.2 液压缸内径D和外径D (16)13.2.3 活塞杆外径(杆径)d (17)3.2.4 液压缸基本参数的校核 (18)3.3 液压缸综合结构参数及安全系数的选择 (19)3.3.1 液压缸综合结构参数 (19)3.3.2 安全系数的选择 (19)3.4 液压缸底座结构设计 (21)3.5 缸体设计与计算 (22)3.5.1 缸筒设计 (23)3.5.2 缸头和油口设计 (26)3.6 活塞组件设计 (28)3.6.1 活塞杆设计 (28)3.6.2 活塞设计 (30)3.6.3 活塞与活塞杆的连接结构 (31)3.7 缸盖设计 (32)3.7.1缸盖材料和技术要求 (32)3.7.2 缸盖的结构设计 (33)3.8 焊接强度及螺纹连接计算 (34)3.8.1焊接强度计算 (32)3.8.2缸盖螺栓连接强度计算 (35)2.9 小结 (35)4 液压原件选择 (36)4.1 液压泵的确定 (36)4.2 阀类元件的确定 (37)4.2.1 选择阀类元件应注意的问题 (37)4.2.2 阀类元件的选择 (38)4.3 油箱的选择 (39)4.4 滤油器的选择 (39)4.5 管路的选择 (39)4.6 小结 (40)设计小结 (41)致谢辞 (42)参考文献 (44)1 绪论1.1 自卸汽车的作用自卸车的出现是随着时代的发展,搬运工作已经不是人力可以解决的情况下,使用高科技而开发的搬运器械。
90t矿用自卸车液压机械传动系统研究
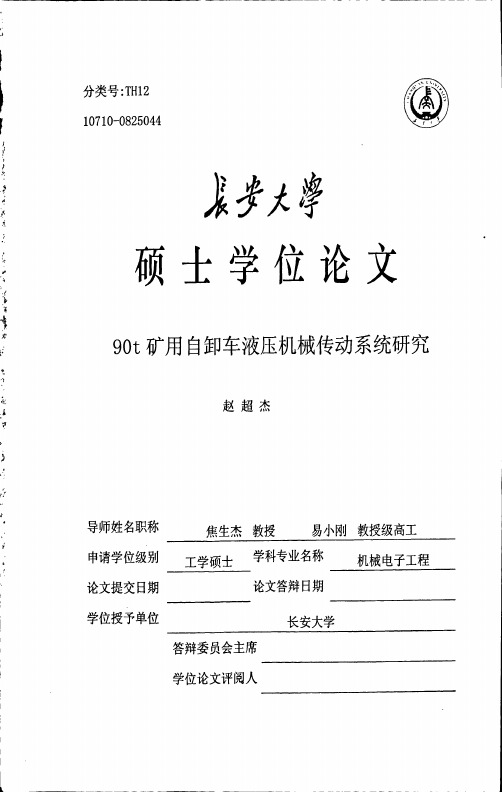
论文作者签名:起链
导师签名:
枷11年6只_7日
沙ff年厂月17日
摘
要
液压机械传动是一类由机械功率流和液压功率流合成的双功率流传动形式,其与先 进的控制技术相结合,能够实现大功率、高效率无级变速传动,在中大吨位车辆上具有 非常良好的应用前景。目前国内中、大吨位矿用自卸车重型动力换挡变速箱必须依赖进 口,导致整车成本高昂。针对上述问题,本文提出了双发动机液压机械传动系统解决方
and
hydraulic components.The synchronization problem of the proposed system is
start
studied in emphasis,which includes the under outside
process synchronization
paper
puts
forward
the double engine
hydro—mechanical transmission system,which of 55t mining truck、析tll two sides
combined
the mechanical transmission system dirve systems to is done
transmission systems of mining trucks are summarized and analyzed at
and
technology maturity of five kinds of mining
home and abroad.The efficiency,economy truck transmission forms are
大型矿用自卸车静液压传动系统设计

大型矿用自卸车是现代矿山企业重要的运输工具之一,目前普遍使用的是大型电动轮自卸车,已暴露出其体积庞大、重量大、故障率高等缺点。由于静液压传动具有工作平稳、冲击小、重量轻、无级调速及调速范围大、易于实现自动化、在恶劣工作条件下相对电传动性能更可靠等优点,近年来发展迅速,已受到车辆传动领域的广泛重视。在分析了矿用电动轮自卸车电动轮传动型式、工作条件及负载变化后,参考由湘潭电机集团有限公司生产的108t电动轮自卸车,结合静液压传动的优点,设计了大型矿用自卸车的静液压传动系统,驱动是由四个液压马达输出扭矩驱动车辆的四轮驱动型式,采用双泵供油的闭式变量系统;鉴于转向和举倾不同时发生,在设计中采用举倾时双泵合流的供油方式,从而充分利用了发动机功率,减少了能量损耗;同时还对大型矿用自卸车的制动性能进行了分析,能够满足其制动要求。
Keywords: dump truck; electric wheel dump truck; hydrostatic transmission
目录
摘要Ⅰ
AbstractⅡ
第1章绪论1
1.1大型矿用电动轮自卸车的现状及发展1
1.2现代液压技术的发展2
1.3大型矿用自卸车用静液压驱动的可行性与优越性3
3统传动方案12
3.5液压传动系统的设计计算12
3.5.1确定液压系统的工作压力13
3.5.2液压传动参数及性能的计算13
3.5.3辅助装置21
3.6拟定驱动液压系统工作原理图23
3.7液压元件的选择和设计25
第4章液压转向系统的设计27
4.1转向系统的基本要求27
第5章液压举倾系统的设计35
5.1概述35
5.2举倾系统的限速措施35
5.3液压举倾系统的设计计算36
矿用防爆车液压传动系统设计

摘要矿用防爆车是现代矿山企业重要的运输工具之一,目前普遍使用前后铰接式、机械式传动,经防爆发动机、离合器、变速箱、传动轴、驱动桥实现驱动。
暴露换挡时间长、零件冲击载荷大布局复杂等缺点。
由于静液压传动具有工作平稳、冲击小、重量轻、无级调速及调速范围大、易于实现自动化、在恶劣工作条件下相对电传动性能更可靠等优点,近年来发展迅速,已受到车辆传动领域的广泛重视。
在分析了国内防暴车的传动型式、工作条件及负载变化后,参考已有防爆车的设计,结合静液压传动的优点,设计了矿用防爆车的静液压传动系统,驱动是由两个液压马达输出扭矩驱动车辆的两轮驱动型式,采用双泵供油的闭式变量系统;鉴于转向和举倾不同时发生,在设计中采用举倾时双泵合流的供油方式,从而充分利用了发动机功率,减少了能量损耗;同时还对矿用防爆车的制动性能进行了分析,能够满足其制动要求。
关键词:矿用防爆车;马达驱动;静液压传动目录摘要ⅠAbstractⅡ第1章绪论11.1 矿用防爆车的现状及发展 (1)1.2 本设计的任务和目标 (2)第2章主要技术参数及对传动方案的分析确定 22.1 主要技术参数 (2)2.2 总体方案及传动方案确定 (2)2.3 现代液压技术的发展 (3)2.4 矿用防爆车用静液压驱动的可行性与优越性............................................................第3章静液压驱动系统的设计 63.1 车辆行走机构对液压传动系统的要求 (6)3.2 液压驱动系统的型式 (6)3.2.1 容积调速系统 (6)3.2.2 功率分流液压调速系统 (7)3.3 行走驱动系统性能的主要参数 (7)3.4 静液压驱动系统方案的确定 (8)3.4.1 液压驱动系统的型式 (8)第3章静液压驱动系统的设计3.4.2 液压驱动系统传动方案 (12)3.5 液压传动系统的设计计算 (12)3.5.1 确定液压系统的工作压力 (13)3.5.2 液压传动参数及性能的计算 (13)3.5.3 辅助装置 (21)3.6 拟定驱动液压系统工作原理图 (23)3.7 液压元件的选择和设计 (25)第4章液压转向系统的设计274.1 转向系统的基本要求 (27)4.2 转向方式及转向随动系统方框图 (27)4.2.1 轮式车辆转向方式 (27)4.2.2 转向随动系统方框图 (28)4.3 液压转向系统方案的选择 (28)4.4 液压转向系统设计计算 (29)4.4.1 转向阻力矩的计算 (29)4.4.2 转向油缸参数的确定 (30)4.4.3 转向器参数的确定 (32)4.4.4 油泵参数的确定 (33)4.5 拟定液压转向系统工作原理图 (33)第5章液压举倾系统的设计355.1 概述 (35)5.2 举倾系统的限速措施 (35)5.3 液压举倾系统的设计计算 (36)5.3.1 倾卸油缸行程及内径的计算 (37)5.3.2 倾卸油缸容积及油泵的计算 (39)5.4 拟定液压举倾系统工作原理图 (39)第6章制动性能分析416.1 制动力矩和制动力 (41)6.1.1 前轮制动力矩和制动力 (41)6.1.2 后轮制动力矩和制动力 (42)6.2 前后轮附着力及滚动阻力 (42)6.3 制动加速度和制动距离 (43)第7章系统总成457.1 液压转向系统和举升系统的组合 (45)7.1.1 系统的组合 (45)7.1.2 举升转向组合系统元件的选择 (47)7.2 大型矿用自卸车静液压传动系统的总成 (47)7.3 静液压传动系统动力来源传动装置的选择 (50)第8章液压系统性能验算518.1 液压系统压力损失 (51)8.2 液压系统的发热温升 (52)8.2.1 液压系统的发热功率 (52)8.2.2 液压系统的散热功率 (53)8.3 液压系统冲击压力 (54)结论57致谢58参考文献59附录60第1章绪论1.1 矿用防爆无轨胶轮车的现状及发展我国虽然已从上世纪80年代中期开始研制柴油机无轨胶轮车,但进展不大。
自卸半挂车液压系统的设计

自卸半挂车液压系统的设计作者:徐国坪来源:《企业技术开发·中旬刊》2016年第10期摘要:物料运输行业近年来的发展速度是非常可观的,自卸车作为物料运输与装卸的重要设施之一,其应用范围也日益广泛与发展。
但以往自卸半挂车液压系统设计运转存在一定缺陷,导致自卸半挂车在实际使用中频繁存在运输效率低下、运输货物容易受到污染、以及装卸料不彻底等问题。
在这一背景下,文章设计一种全新的自卸半挂车,通过对液压系统关键元件进行优化设计的方式,能够提高自卸半挂车整体结构的合理性,兼顾操作方便、工作效率高等优势,可以在自卸运输业内广泛推广。
关键词:自卸半挂车;液压系统;设计中图分类号:TH137 文献标识码:A 文章编号:1006-8937(2016)29-0005-02自卸半挂车是目前建筑施工等工业领域中广泛使用的运输车辆之一,此类运输车辆在液压系统的控制下可完成举升、中停、限位、回位、顶棚开闭等多个功能,具有良好的应用价值。
且既往工程实践经验表明,自卸半挂车无论是在作业效率、运输效率、还是物料剩余率方面均具有其他运输车辆所不可比拟的优势。
本文即针对此类型自卸半挂车液压系统的设计问题展开探讨与分析,望能够确保液压系统的安全、平稳运行。
1 自卸半挂车液压系统结构在自卸半挂车的运转过程中,液压系统是非常重要的模块之一,其主要作用是使车厢能够按照设计角度倾斜举升,在完成货物装卸作业后自动回落至初始高度,同时也是保证自卸半挂车车厢顶棚正常开闭的重要装置之一。
液压系统的基本结构设计图,如图1所示。
在自卸半挂车需要操作货物进行倾卸时,操控组合手动换向阀手柄,液压油经过气控换向阀装置引入液压缸体内部(A腔),此时受到油压的推动作用力影响,液压缸内各级油缸缸筒递次伸出,操作自卸半挂车车厢上升。
在自卸半挂车车厢上升至最大行程后转入回落程序,此时需要操作手动换向阀手柄装置,使油缸A腔内的液压油自动回路,而液压油由于具有一定压力,则引入液压缸体B腔内部,通过回拉伸出末级油缸的方式,操作自卸半挂车车厢下降。
液压专用机械传动系统设计

液压专用机械传动系统设计
液压专用机械传动系统是一种采用液体作为能量传递介质,将功率从发动机或电动机传递到机械装置的传动系统。
液压传动系统具有传动效率高、质量轻、可靠性高、可逆性好、能量密度大、传递力矩大等优点。
液压传动系统主要由液压泵、液压马达、液压缸、控制阀、油箱等组成。
液压泵将机械能转换为液压能,经过控制阀控制后,通过液压管路传递到液压马达和液压缸,再将液压能转换为机械能,实现机械装置的运动。
在液压专用机械传动系统的设计中,需要考虑以下方面:
1. 功率需求:根据机械装置的工作要求和功率需求,选择合适的液压泵和液压马达。
2. 传动效率:要选择传动效率高、质量轻的液压元件,以提高系统的传动效率和运行稳定性。
3. 控制方式:根据机械装置的运行要求,选择合适的控制方式,并选择相应的控制阀和液压缸。
4. 系统支撑:设计液压传动系统时,需要考虑系统的支撑方式,以确保系统稳定可靠地运行。
5. 安全因素:在液压传动系统的设计中,需要充分考虑安全因素,防止系统出现泄漏、爆炸等意外事故。
综上所述,液压专用机械传动系统的设计需要充分考虑机械装置的工作要求和功率需求,选择合适的液压元件和控制方式,并考虑系统的支撑和安全因素,以确保系统稳定可靠地运行。
自卸装置液压元件与系统设计

汽车自卸装置液压系统构成
1. 能源装置:将机械能转换成液压能,如齿轮泵; 2. 执行装置:把液压能转换机械能,如液压缸; 3. 控制调节装置:控制压力、流量等,如转阀、单向阀、溢 流阀; 4. 辅助装置:如油箱、油管。 主要性能参数 举升时间 下降时间 最大举升角度 最大举升载货
转速:当泵的排量为恒定值时,提高泵的转速可增大泵 的流量。但应对最高转速进行限制。转/分,r/min,系统 应尽可工作在接近但不超过额定转速。 齿轮泵转速愈高,流量愈大。但转速过高会造成吸油不 足,油液不能充满齿谷,产生气蚀、振动。 功率:, 理论功率:液压泵输出压力为p,理论流量为Ql 的功率 。 输出功率:液压泵向系统供给的压力为p(Pa),实际 流量为Qs (l/min)的压力油,则泵向系 统的实际输出功 率。
?举升时间和齿轮泵上的额定转速有关吗? ?举升时间和齿轮泵上的排量有关吗?
举升货物多少 举升货物多少由溢流阀设定压力、油缸活塞大小、
机械相对尺寸决定。
?
齿轮泵上标明的额定压力与举升货物多少有关吗?
如果齿轮泵上标定的额定压力小于实际压力会不会举不起 来,有什么问题?
液压缸基本结构参数
外形尺寸(主要是长度) ; 活塞杆杆径; 缸筒内径(活塞直径); 工作行程; 最大行程; 最大输出速度; 最大输出力。
举升时间
发动机转速(油门大小) 变速器取力档速比 取力器速比 举升系统的总传动比应让发动机工作在油耗 较低水平,以节约能源的。 齿轮泵排量 三者乘积接近但不超过 齿轮泵额定转速
液 压 泵 分 类
高压泵 超高压泵
齿轮泵装配图动画
齿轮泵困油.avi
齿轮泵的基本性能参数
压力:输出压力由负载(包含管路系统阻力)决定。 额定压力(公称压力):指泵在连续运转情况下所允许使 用的工作压力,并能保证泵的容积效率和使用寿命的达到。 最大压力:指泵在短时间内超载时所允许的极限压力。由 液压系统中的安全阀限定。安全阀的调定值不能超过泵的 最大压力值。 实际工作压力: 排量:液压泵主轴旋转一周所排出的液体体积。ml/r, l/r 流量:指单位时间内输出的液体体积。 分理论流量和实际流量。米3 / 秒 (m3/s),升 / 分钟(l/min) 理论流量Ql等于排量q与与转速n的乘积。 Ql = q × n , m3/s ,或 Ql = q × n ×10-3 , l / min 泵的实际流量 Qs是泵工作时实际输出的流量,等于理论 流量减去因泄漏、压缩等损失的流量。实际流量与容积效 率YV有关。 YV = Qs / Ql
220t电传动矿用自卸车全液压制动系统设计

^_.HydrostaticsandHydrodynamics’二::二I:二’二_土程机械_二i≥二:!i,■二?:i三二第39卷2∞8年3月:中南大学机电工程学院罗春雷赵遵平张友林;摘要:大型矿用自卸车作业效率高,运营成本低,具有中小型设备无法比拟的优势,因而广泛;;应用于大型露天矿山。
矿用自卸车载重量大、行驶速度高,对制动性能要求很高,而且电传动矿用自:;卸车的前后制动压力、流量差别较大,因此设计了新型全液压制动系统。
该系统采用带液控功能的双i!路踏板阀作为先导阀,继动阀作为主阀,组成双路工作制动系统,通过电磁阀液控踏板阀来实现紧急÷i制动,电磁阀液控后继动阀间接锁定后制动器来实现制动锁定;停车制动为弹簧施加、电磁阀控制液i;压解除,并设置单向阀、压力开关和速度传感器,防止停车制动器意外施加。
系统分为多条油路,并设;;置各自的隔离单向阀、蓄能器和油路调节器,保证系统在部分油路故障的情况下能够安全停车,即实?;现次级制动。
另外系统设置了多个压力开关,实现与推进互锁和压力低报警,并采用顺序阀液控踏板;÷阀,实现在制动压力低报警一段时间后自动施加所有制动器。
}关键词:电传动自卸车全液压制动次级制动矿用汽车220t矿用自卸车作业效率高,运营成本低,具有中小型设备无法比拟的优势,广泛应用于大型露天矿山【l】。
220t矿用自卸车自重达170t,满载后的总质量达到390t,而且其行走速度也达到48km/h,这就要求自卸车必须具有非常可靠的制动。
因此,本文通过参考国外相关产品,设计了全液压制动系统,来保障行车的安全性和制动的可靠性。
1制动工况分析矿用自卸车有机械传动和电传动两种方式,电传动是通过驱动电动机经行星减速器减速后驱动后轮,电动机直接安装在后桥内。
因此,国内外大型电传动矿用自卸车普遍采用前轮为轮速制动,后轮为枢速制动(制动器装在电动机的轴上),制动器一般采用全液压钳盘式制动器或者湿式制动器。
自卸汽车液压系统设计探讨

/ 4x2000^ = 5643mm
T兀•耳V3.14x10x106x0.8
根据缸筒内径尺寸系列(GB/T2348-1993),取液压 缸内径Q=80mm。
《湖北农机化》2019年第19期[ 35
开发研究
在单杆油缸中,憑可由Q和求的,标准Xv系列值为1.06、 1.12、1.25、1.4、1.6、2、2.5、和 5,为了减少冲击,一般推 荐XvW1.6。活塞速度范围0.1〜0.2m/s < v < lm/s0
1液压系统的基本方案 1.1液压缸的选型及安装方式
(1)确定液压缸的类型:选用单杆活塞式液压杆。(2)
确定液压缸的安装方式:选用耳环连接的方式进行安装。
(3)缸盖连接的类型:按照设计要求,选用法兰连接式。 1.2液压执行元件运动控制回路的拟定
液压执行元件确定之后,其运动方向和运动速度的控 制是拟订液压回路的核心问题。方向控制用换向阀或是逻 辑控制单元来实现。对于一般中小流量的液压系统,大多数 通过换向阀的有机组合实现所要求的动作,对于高压大流量 的液压系统,现多采用插装阀与先导控制阀的组合来实现。
1.3液压源系统
液压系统工作过程中所需要的介质由液压源提供。其 中,在没其他油源的时候,液压泵供油的需求量会很大,其 中多余的油会从溢流阀回流到油箱,并且溢流阀还有一个 重要的作用就是稳控油压。以既减少开支又能保证高效率 为前提,泵的出油尽可能与系统中所需要的流量相接近。过 滤净化:一般都配备有多个过滤器,进入泵口的油要符合要 求,使元件不受损害,通过精密滤器进行再次过滤。为了防 止污物再次回流到油箱,可设置高效过滤器来过滤杂质。
2 液压系统设计 2.1液压缸主要零件结构和材料 2.1.1缸体_____________________ 作者简介:刘晓光(19ቤተ መጻሕፍቲ ባይዱ2-),男,河南许昌人,教研室副主任,商丘
DKC20自卸卡车液压系统设计与计算
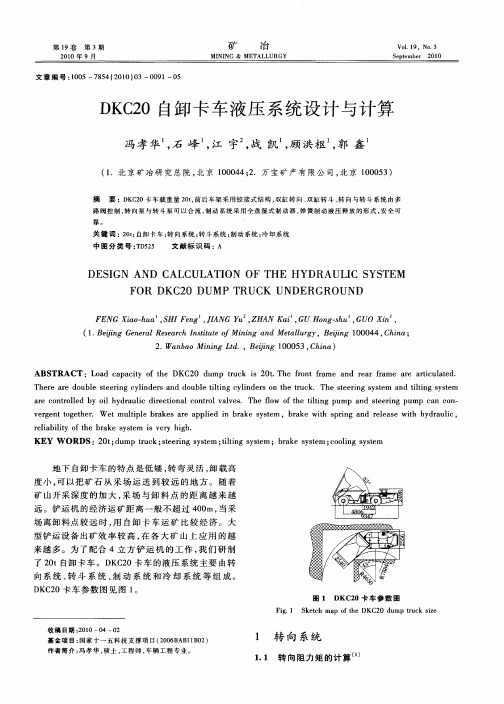
( . e g G nrl eer ntue fMii n tl ry B i g 10 4 , hn ; 1 B n ee sac Is tt o n g a dMe l g , e i 0 4 C ia aR h i n au j n 0 2 Wa boMiigLd , e g 1 0 5 , hn ) . na nn t. B n 0 0 3 C ia
场离 卸料 点较 远 时 , 自卸 卡 车运 矿 比较 经 济 。大 用
型铲 运设 备 出矿效 率 较 高 , 在各 大矿 山上 应 用 的越
来 越 多 。为 了配合 4立 方 铲 运 机 的工 作 , 们 研 制 我
了 2t 0 自卸 卡车 。D C 0卡车 的液 压 系统 主要 由转 K 2 向系 统 、 斗 系 统 、 动 系 统 和 冷 却 系 统 等 组 成 。 转 制
DES GN I AND CALCULAT 0N 1 OF THE HYDRAULI YS C S TEM
F OR DKC2 0 DUMP TRUCK UNDERGR0UND
F ENG Xi o h a , HIF n , I NG Y ZH N a GU Ho g s u , O Xi , a . u S e g J A u , A K i , n .h GU n
K EY O RD S :2 ; u p tu k; t e i y t m ;i i g s se ;b a e s se ; o ln y t m W 0t d m r c se rng s se t tn y tm l r k y t m c oi g s se
地 下 自卸卡 车 的特点 是低 矮 , 弯灵 活 , 转 卸载 高 度小 , 以把 矿 石从 采 场运 送 到较 远 的地 方 。随着 可 矿 山开采 深度 的加 大 , 场 与 卸 料 点 的距 离越 来 越 采 远 。铲运 机 的经 济运 矿距 离一 般不 超 过 4 0 当采 0 m,
高位自卸汽车液压系统设计
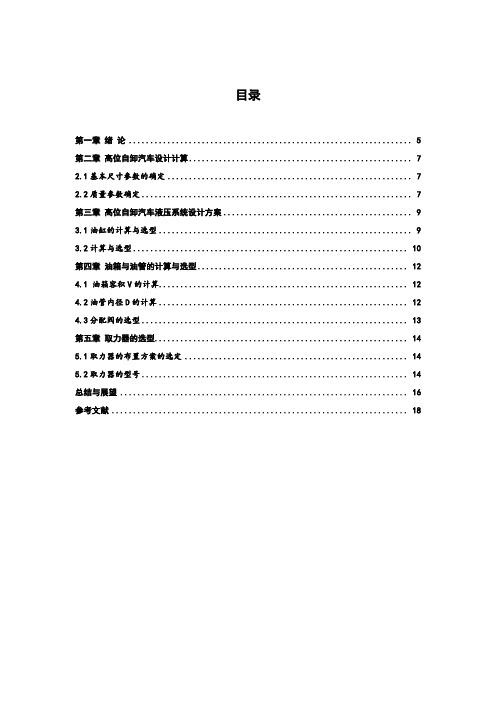
目录第一章绪论 (5)第二章高位自卸汽车设计计算 (7)2.1基本尺寸参数的确定 (7)2.2质量参数确定 (7)第三章高位自卸汽车液压系统设计方案 (9)3.1油缸的计算与选型 (9)3.2计算与选型 (10)第四章油箱与油管的计算与选型 (12)4.1 油箱容积V的计算 (12)4.2油管内径D的计算 (12)4.3分配阀的选型 (13)第五章取力器的选型 (14)5.1取力器的布置方案的选定 (14)5.2取力器的型号 (14)总结与展望 (16)参考文献 (18)高位自卸汽车液压系统设计摘要高位自卸汽车液压系统设计的好坏,将直接影响整车的性能和生产效率。
自卸汽车液压系统一般包括举升液压系统和转向液压系统。
自卸汽车液压系统原理上相对来说比较简单,但其中有许多具体问题需要认真去研究。
国内自卸汽车液压系统设计,基本上采用的是传统的经验性设计,整体性能很难达到最优。
本文通过对高位自卸汽车的研究,提出了自卸汽车举升液压系统和转向液压系统的一般设计流程和现代设计方法,并对其中的重要环节做了说明,给出了一些比较成熟的解决方案,以期对国产高位自卸汽车液压系统的设计有所启发。
关键字:高位自卸汽车、液压系统、液压缸AbstractThe design of hydraulic system of high dump truck will directly affect the performance and production efficiency. The hydraulic system of dump truck generally includes lifting hydraulic system and steering hydraulic system. Dump truck hydraulic system principle is relatively simple, but there are many specific issues need to seriously study. The design of the hydraulic system of the dump truck in China is mainly based on the traditional empirical design. Based on the research of high dump truck, the hydraulic system of dump truck lifting and steering hydraulic system of general design process and modern design methods, and one of the important aspects described, given some mature solutions, in order to inspire the design of domestic high truck hydraulic system.Key words: high dump truck, hydraulic system, hydraulic cylinder引言高位自卸汽车是专用自卸汽车一种,高位自卸汽车主要用于运输散装并可以散堆的货物(如沙、土、以及农作物等),服务于建材厂、矿山、工地等。
超大型矿用挖掘机液压系统的优化设计与分析

超大型矿用挖掘机液压系统的优化设计与分析摘要:随着矿产资源的开发需求不断增加,超大型矿用挖掘机的应用逐渐广泛。
液压系统作为挖掘机的核心部分,其性能直接影响到挖掘机的工作效率和使用寿命。
本文针对超大型矿用挖掘机液压系统进行了优化设计与分析,探讨了系统设计原则、关键参数选择以及仿真分析方法,以期为实际工程应用提供参考。
关键词:超大型挖掘机;液压系统;优化设计;仿真分析1. 液压系统设计原则与关键参数选择1.1 设计原则超大型矿用挖掘机液压系统的设计需要遵循一些重要原则,以确保系统具有良好的性能和可靠性。
首先,设计需考虑挖掘机在工作过程中所需的力和速度,以满足挖掘不同类型土壤和岩石的需求。
其次,设计应充分考虑系统的安全性和稳定性,包括防止液压元件过载、泄漏等问题,并确保系统能够适应恶劣的工作环境。
此外,设计时还应注重系统的节能性能,通过合理配置以及优化流体动力学特性来降低能耗。
最后,设计需考虑整个挖掘机的维护和维修便捷性,以减少停机时间并提高生产效率。
1.2 关键参数选择超大型矿用挖掘机液压系统的关键参数选择对系统的性能影响巨大。
其中,液压泵和液压缸是两个重要的部件。
液压泵的选择应基于挖掘机所需的流量和压力范围,同时要考虑泵的效率和寿命等因素。
液压缸的选择取决于工作装置的负载需求和工作速度,液压缸的尺寸、材料以及密封件的选用都需要考虑到系统的可靠性和耐久性。
此外,还需要合理选择液控阀、马达、冷却器等配件,并根据挖掘机的具体要求进行优化。
在参数选择过程中,还需要注意液压系统的整体布局和结构设计。
合理布局可以最大限度地减少管道长度和压力损失,提高系统的响应速度和效率。
2. 液压系统优化设计方案2.1 工作装置液压系统优化设计工作装置液压系统是超大型矿用挖掘机的核心部分,直接影响挖掘机的工作效率和性能。
为了优化设计该系统,需要考虑以下几个方面。
首先,根据挖掘机的工作需求,确定合适的流量和压力范围,并选择高效的液压泵和液压缸。
- 1、下载文档前请自行甄别文档内容的完整性,平台不提供额外的编辑、内容补充、找答案等附加服务。
- 2、"仅部分预览"的文档,不可在线预览部分如存在完整性等问题,可反馈申请退款(可完整预览的文档不适用该条件!)。
- 3、如文档侵犯您的权益,请联系客服反馈,我们会尽快为您处理(人工客服工作时间:9:00-18:30)。
第1章绪论1.1 大型矿用电动轮自卸车的现状及发展自1963年由美国Unit-Rig公司G.E公司合作研制出世界上第一台装载质量问77t矿用电动轮自卸车以来,经过多年的不断完善和大量新技术、新材料、新工艺的采用,重型矿用电动轮自卸车作为汽车中的新品种已发展成熟,已经有108t、154t、170t、280t等多个系列。
它是目前过内外大型露天矿普通采用的高效运输设备,已占有大份额市场。
国内矿用电动轮自卸车在我国大型露天矿山的使用始于70年代中期,使用单位主要分布在煤炭、冶金等行业,其装载质量主要为108t和154t两种。
国外生产重型矿用自卸车的主要厂家有:小松矿用设备公司、尤克里德-日产公司、卡特彼勒、利勃海尔公司等,其共同特点是:车型全系列、部件专业化、有完整的配套体系。
我国重型矿用电动轮自卸车的生产厂商主要有三家:湘潭电机厂、本溪重型汽车厂和常州冶金机械厂。
湘潭电机厂生产的自卸车经过不断改进和完善,吸收国外技术的基础上已经形成了几个系列,辽宁本溪重型汽车厂由于多种原因现已停产,江苏常州冶金机械厂主要与美国Unit-Rig公司合作生产Mark-36型154t矿用电动轮自卸车。
目前重型矿用电动轮自卸车驱动的传动方式都是采用交-直流传动,由柴油机带动发电机发出三相中频交流电,经外部整流装置整流变成直流电后输往汽车后桥两侧的直流牵引电机,以驱动汽车行驶。
举升和转向采用液压系统,有两种形式:常流式和常压式,转向系统均采用动力转向,举升系统才采用侧置式双缸三级双作用油缸外置于车架两侧。
电传动系统是由发电机、牵引电机、和电控制三大部分组成,其主要满足恒功控制的要求。
驱动形式通常都采用4×2后轴驱动。
重型矿用电动轮自卸车的发展趋势主要是三点:1. 大型化。
促使矿用电动轮自卸车朝大型化方向发展的动因主要有两个:一是大型露天矿山开采的需要,二是大型机械传动自卸车的发展。
随着大型矿山的发展和开采运输量的增大,为了提高运输效率、降低成本,许多大型矿山都倾向于采用大吨位矿用自卸车,这促使许多制造厂家相继研制开发出大吨位矿用电动轮自卸车一满足矿山用户的需要。
高速发展的电子技术、控制技术和新型电子元器件的出现、大功率车用柴油机的问世、高负荷大型轮胎材料的研制成功及相关技术的解决和发展又为矿用电动轮自卸车的大型化铺平了道路。
因此,矿用电动轮自卸车的大型化已经成为许多制造厂家为开拓市场吸引更多客户而普遍采用的一种竞争策略。
2.计算机控制和大量新的电控元器件的使用。
80年代中后期开始,计算机控制技术已经逐步用于矿用电动轮自卸车的车速自动调节、柴油机燃油喷射及整车的故障分析诊断等领域。
随着计算机技术、通信技术、传感器技术等的进一步发展,计算机控制技术将在矿用电动轮自卸车的许多方面得到应用,从而减轻驾驶员和矿山维护人员的劳动强度,提高电动轮自卸车的自动化程度和劳动生产率,使其性能和工作可靠性将得到进一步的提高。
随着交流变频调速技术的发展和大功率逆变器的问世,重型矿用电动轮自卸车已开始采用交-交传动。
3.整车性能和工作可靠性进一步提高。
目前国内外许多厂家已将大量先进的设计方法和成熟的分析软件应用在矿用电动轮自卸车的前后桥悬架系统、车架、后桥壳等关键零部件的结构设计及应力分析中,以提高整车的工作可靠性、操纵稳定性及整车使用寿命。
4.采用双能源作动力。
重型电动轮自卸车采用辅助架线供电和本身柴油发动机作为双能源运行也是一个值得关注的新趋向。
双能源矿用自卸车的出现既解决了矿用电动轮自卸车重载上坡时柴油发动机动力不足、车速慢等问题,又节约了能源,降低了柴油机废气的排放,利于环境保护。
但是电动轮自卸车有体积庞大、重量大、故障率高、维修次数多等缺点,因此,结合现代传动技术的发展,探索一种矿用自卸车新的传动方法是必要的。
1.2 现代液压技术的发展液压技术是实现现代化传动与控制的关键技术之一,世界各国对液压工业的发展都给予很大重视。
世界液压元件的总销售额为350亿美元。
据统计,世界各主要国家液压工业销售额占机械工业产值的2%~3.5%,而我国只占1%左右,这充分说明我国液压技术使用率较低,努力扩大其应用领域,将有广阔的发展前景。
液压技术具有独特的优点,如:液压技术具有功率重量比大,体积小,频响高,压力、流量可控性好,可柔性传送动力,易实现直线运动,并易与微电子、电气技术相结合,形成自动控制系统等优点。
因此,液压技术广泛用于国民经济各部门。
但是近年来,液压技术面临与机械传动和电气传动的竞争,如:数控机床、中小型塑机已采用电控伺服系统取代或部分取代液压传动。
其主要原因是液压技术存在渗漏、维护性差等缺点。
为此,努力发挥液压技术的优点,克服缺点,注意和电子技术相结合,不断扩大应用领域,同时降低能耗,提高效率,适应环保需求,提高可靠性,这些都是液压技术继续努力的永恒目标,也是液压产品参与市场竞争取胜的关键。
为了和最新技术的发展保持同步,液压技术必须不断发展,不断提高和改进元件和系统的性能,以满足日益变化的市场需求。
这是液压技术的创新特征,液压技术的不断发展体现在如下一些比较重要的特征上:一、提高元件性能,创制新元件,体积不断缩小。
为了能在尽可能小的空间里传递尽可能大功率,液压元件的结构不断地在向小型化发展。
市场上出现了一种新型的被称为“肌腱”的执行元件。
它的形状像一根两端有接头的软管,把它接入系统使用时,它的径向和轴向都会发生伸缩,轴向的伸缩量可达其总长的15%--30%。
在相同条件下,它的作用力是普通汽缸的10倍。
这种元件抗污染,运动时不会生抖动,在有些场合还可用它的径向膨胀去夹持工件等,是一种极有应用前景的元件,而微型元件也得到发展,如活塞直径小到2.5mm的汽缸,10mm 宽的气阀以及相关的辅助元件已成为系列化产品。
由于这些元件能在0.2---0.7Mpa压力下工作,所以可被方便地集成到标准的系统中。
新小型阀,在流量相同时,它的体积仅是过去的7%。
这些小,微型的元件已被应用于精密机械加工,电子工业,制药工业,食品加工和包装技术等场合。
二、高度的组合化,集成化和模块化。
液压系统由管式配置经板式配置,箱式配置,集成块式配置发展到叠加式配置,插装式配置,使连接的通道越来越短。
也出现了一些组合集成件,如把液压泵和压力阀作成一体,把压力阀插装在液压泵的壳体内,把液压缸和换向阀作成一体,只需接一条高压管与液压泵相连,一条回油管与油箱相连,就可以构成一个液压系统。
这种组合件不但结构紧凑,工作可靠,而且简便,也容易维护保养。
三、与微电子结合,走向智能化。
液压技术从本世纪70年代中期起就开始和微电子工业接触,并相互结合。
在迄今30多年时间内,结合层次不断提高,由简单拼装,分散混合到总体组合,出现了多种形式的独立产品如数字液压泵,数字阀,数字液压缸等,其中的高级形式已发展到把编了程的芯片和液压控制元件,液压执行元件或能源装置,检测反馈装置,数模转换装置,集成电路等汇成一体,这种汇在一起的联结体只要一收到微处理机或微型计算机处送来的信息,就能实现预先规定的任务。
液压技术的智能化阶段虽然开始不久,但是从它的星星点点实践成功的事例来看,成果已非常诱人。
液压技术在与微电子技术紧密结合后,在微型计算机或微处理机的控制下,可以进一步拓宽它的应用领域,形形式式机器人和智能元件的使用不过是它最常见的例子而已。
现在国外已在着手开发多种行业能通用的智能组合硬件,它们只需配上适当的软件就可以在不同的行业中完成不同任务。
这样一来,用户的主要技术工作将只是挑选,改编或自编计算程序了。
综上所述可以看到,液压元件将向高性能、高质量、高可靠性、系统成套方向发展;向低能耗、低噪声、低振动、无泄漏以及污染控制、应用水基介质等适应环保要求方向发展;开发高集成化高功率密度、智能化、机电一体化以及轻小型微型液压元件;积极采用新工艺、新材料和电子、传感等高新技术。
液压工业在国民经济中的作用实在很大,它常常可以用来作为衡量一个国家工业水平的重要标志之一。
与世界上主要的工业国家相比,我国的液压工业还是比较落后的,标准化的工作有待于继续做好,优质化的工作须形成声势,智能化的工作则刚刚在准备起步,为此必须急起直追,才能迎头赶上。
可以预见,为满足国民经济发展需要,液压技术也将继续获得飞速的发展,它在各个工业部门中的应用越来越广泛。
1.3 大型矿用自卸车用静液压驱动的可行性与优越性与车辆的其它系统相比,行走驱动系统不仅需要传输更大的功率,要求器件具有更高的效率和更长的寿命,还希望在变速调速、差速、改变输出轴旋转方向及反向传输动力等方面具有良好的能力。
于是,采用何种传动方式,如何更好地满足各种车辆行走驱动的需要,一直是车辆研究和使用所要面对的课题。
尤其是近年来,随着我国交通、能源等基础设施建设进程的快速发展,矿山开发规模将不断扩大,大型矿用自卸车在市场需求大大增强的同时,更面临着作业环境更为苛刻、工况条件更为复杂等所带来的挑战,也进一步推动着对其行走驱动系统的深入研究。
静液压传动技术在国内应用始于上世纪80年代,主要应用于联合收割机、叉车、市政工程机械等。
它是伴随着液压传动技术与元件制造技术的快速发展而成长起来的先进传动方式,由于具有传递效率高,可进行恒功率输出控制,功率利用充分,系统结构简单,输出转速无级调速,可正、反向运转,速度刚性大,动作实现容易等突出优点,其在各种车辆的系统中已经得到了广泛的应用,其优异的微动性能,使驾驶员能够更加准确定位。
静液压传动装置以液压泵和液压马达为主组成,附加各种变量控制单元和传动元件(减速器或变速箱),成为一种无级变速的传动装置。
静液压传动与现在重型矿用自卸车上采用的交-直流传动和交-交传动相比,具有以下优点:1.实现无级变速更加方便,且调速平稳、均匀、准确、加速性能好,调速性能更可靠,换向方便。
2.发动机在任一调定转速下工作,传动系统都能发挥出较大的牵引力。
在静态启动时对应与大的阻力矩,能迅速建立起相应大的工作压力,从而获得大的启动力矩。
通过液压泵和液压马达的变排量可以保证很好的低速运行工况。
3.传动系统能在很宽的输出转速范围内保持较高的效率。
4.行走功率和作业装置功率可以合理匹配,使发动机功率充分利用。
5.液压泵和液压马达的位置布置比较灵活。
6.能够较大地减轻矿用自卸车的自重,提高矿山运输能力和运输效率。
7.液压泵和液压马达都容易采用电比例变量控制,微机技术的飞速发展,使二者很好的结合,实现智能化控制。
8.在矿山开发和运输作业环境苛刻、工况条件复杂的情况下,静液压传动比交-直流传动和交-交传动有更高的可靠性。
车辆合理运用静液压驱动装置,能改善机构性能,提高生产效率,节省能量消耗,使机器的品质上升到一个新的阶段。
借助电子技术与静液压传动技术的结合,可以很方便地实现对液压系统的各种调节和控制。