关于超声无损检测技术在金属焊接中的应用研究
金属材料焊接中超声无损检测技术的应用胡青健

金属材料焊接中超声无损检测技术的应用胡青健发布时间:2022-02-23T01:13:50.518Z 来源:《基层建设》2021年31期作者:胡青健[导读] 近年来,随着科技水平的不断发展镇江市建设工程质量检测中心有限公司江苏镇江 212004摘要:近年来,随着科技水平的不断发展,人们的生活质量也有所提高,科技成为了我国第一生产力。
目前,人们对于金属材料的焊接技术关注度越来越高,在金属材料进行焊接的过程中,一般会应用超声无损检测技术对焊接工作进行检测,进而提高金属材料焊接的质量和效率。
本文将针对超声无损检测技术在金属材料焊接中的应用展开分析,以供参考。
关键词:金属材料;焊接;超声无损检测技术引言在应用金属材料的过程中,合理的焊接工艺非常重要,如果金属材料在焊接的过程中并没有严格按照相关标准进行,很容易影响到金属材料的使用性能。
因此,在对金属材料进行焊接的过程中,施工和检验人员需要高度重视焊接工作的质量,但是大部分质量问题很难用肉眼发现,因此需要应用超声无损检测技术帮助施工和检验人员及时发现焊接的质量问题。
一、金属材料焊接过程中,超声无损检测技术的简述超声无损检测技术,顾名思义,主要是通过合理地应用超声波技术,深入检测金属材料的内部以及焊接工作的质量,然后对超声波所负载的信息数据进行有效的收集、处理和分析,进而了解金属材料的焊接情况。
超声无损检测技术的应用,可以在第一时间内检测出金属材料的质量问题,促使施工和检验人员可以及时分析金属材料的内部结构,更重要的是,超声无损检测技术的应用不会破坏金属材料的使用性能和结构(无损检测),因此得到了广泛的应用。
二、超声无损检测技术的特点超声无损检测技术是一种现代的新型检测技术,在应用的过程中可以在金属材料的内部形成声波,以此同时还不会对金属材料造成破坏。
超声无损检测技术最大的特点是为了保证金属材料焊接工作结束之后保持结构的稳定性,与此同时确保检测结果的准确性。
焊接工艺中的射线检测与无损检测

焊接工艺中的射线检测与无损检测焊接是一种常见的金属连接方法,广泛应用于建筑、制造业、航空航天等领域。
然而,焊接过程中常常存在焊缝质量问题,这对于相关产品的安全性和可靠性产生了重要影响。
为了确保焊缝的质量,射线检测与无损检测成为了必不可少的方法。
本文将重点讨论焊接工艺中的射线检测与无损检测。
一、射线检测在焊接工艺中的应用射线检测是一种利用射线通过被测对象来获取材料内部结构信息的方法。
在焊接工艺中,射线检测主要用于检测焊缝的质量,包括焊接接头的缺陷、孔洞、裂纹等问题。
常用的射线检测方法包括X射线检测和γ射线检测。
1. X射线检测X射线检测是利用X射线通过被测对象后形成的透射或散射图像来判断焊缝的质量。
这种方法具有迅速、高效的特点,能够有效发现焊缝中的各类缺陷。
X射线检测设备主要包括射线源、探测器和显像设备。
在进行X射线检测时,需要严格遵守相关的安全操作规程,以避免对人体造成伤害。
2. γ射线检测γ射线检测是利用γ射线通过被测对象后形成的透射或散射图像来检测焊缝的质量。
与X射线检测相比,γ射线的穿透能力更强,可以检测更厚的金属焊缝。
γ射线检测设备与X射线检测设备类似,但射线源的选择以及防护措施会有所不同。
二、无损检测在焊接工艺中的应用无损检测是一种在不破坏被测对象外部结构的前提下,通过检测技术来获取内部缺陷信息的方法。
在焊接工艺中,无损检测主要用于检测焊缝的质量以及焊接接头的可靠性。
1. 超声波检测超声波检测是利用超声波在材料中传播时受到材料内部结构变化的影响而产生回波信号的方法。
在焊接工艺中,超声波检测可以检测焊缝中的各类缺陷,如焊缝结构不均匀、气孔、裂纹等。
该方法非常灵敏,可以检测出微小的缺陷,并可定量评估焊缝的可靠性。
2. 磁粉检测磁粉检测是利用磁场在被测对象表面形成漏磁场,从而检测材料内部缺陷的方法。
在焊接工艺中,磁粉检测可以发现焊缝中的裂纹、缺陷等问题。
该方法操作简单,适用性广泛,并且对于表面缺陷的检测效果较好。
金属管道超声波无损检测方法的研究
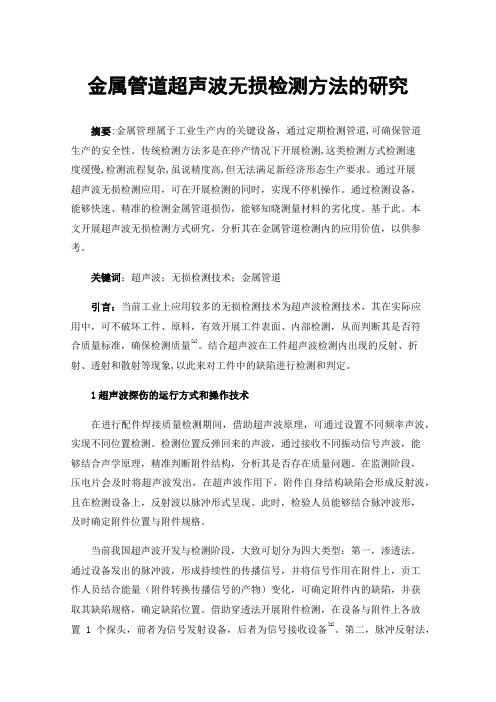
金属管道超声波无损检测方法的研究摘要:金属管理属于工业生产内的关键设备,通过定期检测管道,可确保管道生产的安全性。
传统检测方法多是在停产情况下开展检测,这类检测方式检测速度缓慢,检测流程复杂,虽说精度高,但无法满足新经济形态生产要求。
通过开展超声波无损检测应用,可在开展检测的同时,实现不停机操作。
通过检测设备,能够快速、精准的检测金属管道损伤,能够知晓测量材料的劣化度。
基于此。
本文开展超声波无损检测方式研究,分析其在金属管道检测内的应用价值,以供参考。
关键词:超声波;无损检测技术;金属管道引言:当前工业上应用较多的无损检测技术为超声波检测技术,其在实际应用中,可不破坏工件、原料,有效开展工件表面、内部检测,从而判断其是否符合质量标准,确保检测质量[1]。
结合超声波在工件超声波检测内出现的反射、折射、透射和散射等现象,以此来对工件中的缺陷进行检测和判定。
1超声波探伤的运行方式和操作技术在进行配件焊接质量检测期间,借助超声波原理,可通过设置不同频率声波,实现不同位置检测。
检测位置反弹回来的声波,通过接收不同振动信号声波,能够结合声学原理,精准判断附件结构,分析其是否存在质量问题。
在监测阶段,压电片会及时将超声波发出,在超声波作用下,附件自身结构缺陷会形成反射波,且在检测设备上,反射波以脉冲形式呈现。
此时,检验人员能够结合脉冲波形,及时确定附件位置与附件规格。
当前我国超声波开发与检测阶段,大致可划分为四大类型:第一,渗透法。
通过设备发出的脉冲波,形成持续性的传播信号,并将信号作用在附件上,贡工作人员结合能量(附件转换传播信号的产物)变化,可确定附件内的缺陷,并获取其缺陷规格,确定缺陷位置。
借助穿透法开展附件检测,在设备与附件上各放置1个探头,前者为信号发射设备,后者为信号接收设备[2]。
第二,脉冲反射法,工作人员通过发射波,可及时检测附件缺陷,整个检测过程开展基于缺陷回波法基础上开展,借助仪器设备快可及时获取相关信息。
超声波无损检测技术在失效分析中的应用

超声波无损检测技术在失效分析中的应用引言:在现代工业领域中,设备的失效往往会给企业带来严重的经济损失和安全风险。
因此,发展可靠、高效的失效分析技术是非常重要的。
超声波无损检测技术作为一种非侵入式的检测手段,在失效分析领域发挥着重要的作用。
本文将探讨超声波无损检测技术在失效分析中的应用,并分析其优势和局限性。
一、超声波无损检测技术概述超声波无损检测技术是一种基于超声波传播特性的材料检测方法。
它通过发送超声波脉冲至被测物体内部,利用超声波在不同材料中传播时的散射、反射和吸收等特性,来获取材料的内部结构和缺陷信息。
超声波无损检测技术具有分辨率高、检测速度快、非破坏性等优点,因此被广泛应用于失效分析领域。
二、超声波无损检测技术在失效分析中的应用1. 缺陷检测与定位超声波无损检测技术可以检测材料中的各类缺陷,如裂纹、气孔、夹杂等。
通过分析超声波的传播时间、幅度和特征波形,可以定量评估缺陷的尺寸、形状和位置。
这对于判断材料的完整性和可靠性非常重要,能够帮助工程师及时发现并处理潜在的失效风险。
2. 材料性能评估超声波无损检测技术可以通过测量材料中超声波的传播速度、衰减系数等参数,来评估材料的力学性能。
例如,通过测量材料中声速的变化,可以判断材料的硬度、弹性模量等特性。
这对于评估材料的可靠性和使用寿命非常重要,可以帮助企业选择合适的材料并预防可能的失效。
3. 焊接质量检测在工程和制造过程中,焊接是常见的连接方式,其质量对于产品的可靠性至关重要。
超声波无损检测技术可以检测焊接接头中的缺陷,如焊缝中的裂纹、夹杂以及未熔合区等。
通过准确检测和评估焊接接头的质量,可以避免由于焊接缺陷导致的失效风险。
4. 压力容器监测压力容器一旦发生失效可能会引发严重的事故,因此对于压力容器进行定期监测非常重要。
超声波无损检测技术可用于监测压力容器内部的缺陷和腐蚀情况。
通过检测超声波在压力容器壁上的反射和传播情况,可以判断压力容器的健康状况,并提前预警可能的失效风险。
超声波探伤论文-超声波探伤毕业论文

超声波探伤论文-超声波探伤毕业论文摘要本毕业设计的课题是板材焊缝超声波探伤测试。
主要任务是在掌握过程设备制造流程和焊接缺陷及其产生原因的基础上,研究超声波探伤技术在钢制压力容器对接焊接接头探伤检测中的应用,并给出焊缝返修的具体方案。
本文详述了国内外超声检测技术的发展和现状,并在简述过程设备制造、焊接及无损探伤的基础上详细介绍了超声波探伤技术及其在焊缝无损探伤中的应用及评定等级和注意事项。
针对给定的板材焊缝,通过实验检测该焊缝的缺陷,本文详细介绍了试块选用,设备调试,现场探伤中的常见问题及解决方法。
同时给出了现场探伤、缺陷定位和长度测量的具体方法,并通过GB11345-89标准对试验中检测到的缺陷进行了等级评定并得出了检测工艺卡。
关键词:焊缝;超声波探伤。
AbstractThe task of the graduation design is the plate weld ultrasonic testing. The main task is to master the process equipment manufacturing and welding defects and its causes, study of ultrasonic flaw detection technology in steel pressure vessel butt welded joint flaw detection, and gives the concrete plan of the weld repairing. This paper describes the domestic and foreign development and present situation of ultrasonic detection technology, and in the process equipment manufacturing, welding and nondestructive testing based on detailed introduces the ultrasonic detection technology and its application in weld NDE and rating and matters needing attention. For a given plate welding, the weld defects detection by experiment, this paper introduces the test block selection, equipment commissioning, on-site inspection of the common problems and solutions. At the same time provides on-site testing, defect location and length measurement methods, and through the GB11345-89 standard to test the detected defects were rating and the detection process card.Key words: Weld; ultrasonic testing目录1.1选题的背景及意义过程设备是各个工业部门不可缺少的重要生产设备,用于供热、供电和储存各种工业原料及产品,完成工业生产过程必需的各种物理过程和化学反应。
无损检测技术在焊接检验中的应用
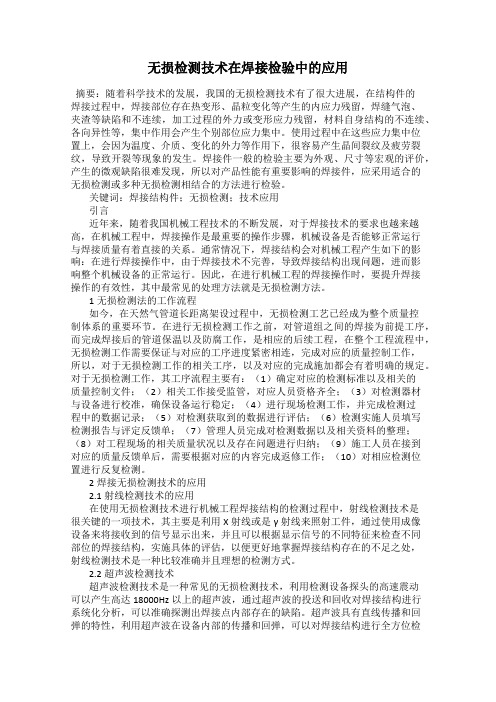
无损检测技术在焊接检验中的应用摘要:随着科学技术的发展,我国的无损检测技术有了很大进展,在结构件的焊接过程中,焊接部位存在热变形、晶粒变化等产生的内应力残留,焊缝气泡、夹渣等缺陷和不连续,加工过程的外力或变形应力残留,材料自身结构的不连续、各向异性等,集中作用会产生个别部位应力集中。
使用过程中在这些应力集中位置上,会因为温度、介质、变化的外力等作用下,很容易产生晶间裂纹及疲劳裂纹,导致开裂等现象的发生。
焊接件一般的检验主要为外观、尺寸等宏观的评价,产生的微观缺陷很难发现,所以对产品性能有重要影响的焊接件,应采用适合的无损检测或多种无损检测相结合的方法进行检验。
关键词:焊接结构件;无损检测;技术应用引言近年来,随着我国机械工程技术的不断发展,对于焊接技术的要求也越来越高,在机械工程中,焊接操作是最重要的操作步骤,机械设备是否能够正常运行与焊接质量有着直接的关系。
通常情况下,焊接结构会对机械工程产生如下的影响:在进行焊接操作中,由于焊接技术不完善,导致焊接结构出现问题,进而影响整个机械设备的正常运行。
因此,在进行机械工程的焊接操作时,要提升焊接操作的有效性,其中最常见的处理方法就是无损检测方法。
1无损检测法的工作流程如今,在天然气管道长距离架设过程中,无损检测工艺已经成为整个质量控制体系的重要环节。
在进行无损检测工作之前,对管道组之间的焊接为前提工序,而完成焊接后的管道保温以及防腐工作,是相应的后续工程,在整个工程流程中,无损检测工作需要保证与对应的工序进度紧密相连,完成对应的质量控制工作,所以,对于无损检测工作的相关工序,以及对应的完成施加都会有着明确的规定。
对于无损检测工作,其工序流程主要有:(1)确定对应的检测标准以及相关的质量控制文件;(2)相关工作接受监管,对应人员资格齐全;(3)对检测器材与设备进行校准,确保设备运行稳定;(4)进行现场检测工作,并完成检测过程中的数据记录;(5)对检测获取到的数据进行评估;(6)检测实施人员填写检测报告与评定反馈单;(7)管理人员完成对检测数据以及相关资料的整理;(8)对工程现场的相关质量状况以及存在问题进行归纳;(9)施工人员在接到对应的质量反馈单后,需要根据对应的内容完成返修工作;(10)对相应检测位置进行反复检测。
超声波相控阵无损检测技术在特种设备领域应用研究

超声波相控阵无损检测技术在特种设备领域应用研究摘要:特种设备是指用于生产、运输、储存、使用等特定场合的设备,如压力容器、锅炉、压力管道、起重机械等。
这些设备的安全运行对人们的生命财产安全具有重要的意义。
特种设备的无损检测技术是保障特种设备安全运行的关键技术之一。
本文将介绍超声波相控阵技术的基本原理、特点和应用,以期为特种设备无损检测技术的进一步发展提供参考。
关键词:超声波相控阵技术;特种设备;无损检测;相位;幅度引言:超声波检测技术是特种设备无损检测技术中最常用的一种技术。
它通过超声波的穿透、反射、衍射、散射等物理效应,检测目标对象内部的缺陷(比如裂纹、未熔合、夹渣等)。
然而,传统的超声波检测技术在应用中存在一些局限性,如分辨率低、检测速度慢等问题。
超声波相控阵技术是近年来发展起来的一种新型的超声波检测技术。
它通过控制多个超声波发射器和接收器的相位和幅度,实现对目标物体进行快速、准确的无损检测。
该技术具有分辨率高、信噪比高、检测速度快、适用性广、缺陷实时成像等优点,在特种设备无损检测中具有广泛的应用前景。
一、超声波相控阵技术的基本原理超声波相控阵技术是一种基于超声波相位调制原理的检测技术。
它利用多路超声发射器和接收器的阵列,通过控制每个发射器和接收器的相位和幅度,实现对目标物体的扫描和成像。
超声波相控阵技术的基本原理是利用超声波在不同介质中传播速度不同的特性。
当超声波从一个介质传播到另一个介质时,会发生反射、折射和散射等现象。
通过控制超声波发射器和接收器的相位和幅度,以灵活的声束偏转和聚焦能力实现缺陷的实时成像。
具体而言,超声波相控阵技术包括以下几个步骤:(一)发射器控制超声波相控阵技术中的发射器控制是实现波束控制和聚焦的关键步骤。
通过调节每个发射器的相位和幅度,可以控制超声波的传播方向和形状。
相位调节可以改变波束的传播方向,使其聚焦于目标物体的特定区域。
幅度调节可以控制超声波的能量分布,使波束的强度在聚焦区域最大,从而提高检测的灵敏度和精度。
钢结构无损检测中超声探伤的应用

钢结构无损检测中超声探伤的应用摘要:随着我国城镇化水平的不断提高,建筑业取得了长足的进步,而钢结构在这个过程中发挥着骨干支撑的重要作用,决定着我国社会主义发展的质量。
对钢结构工程质量进行必要的检查,及时发现问题,解决问题,尽可能减少损失,具有重要意义。
本文详细分析了超声波探伤在钢结构无损检测中的应用。
关键词:钢结构;无损检测技术;超声探伤;应用一、超声波探伤技术介绍及原理超声波探伤技术,顾名思义,就是利用超声波检测钢结构的缺陷。
它是一种重要的无损检测方法,应用范围很广。
超声波探伤设备结构简单,操作条件不是特别苛刻,安全性能好。
由于超声波穿透能力强,检测结果比较准确可靠,具有广阔的发展前景。
超声探伤主要构成有超声波探伤仪、耦合剂、探头、标准试块等部分。
根据设备运行所产生的波形不同,机械波可分为纵波、横波、板波和表面波,其中常用的波形为纵波和横波。
超声波探伤技术的应用主要是检测钢结构中是否存在气泡、缩孔、夹渣、、焊接裂纹以及不同部位的熔接,还可以确定铸件的厚度。
主要原理如下:超声波的频率在20000Hz以上,穿透能力强,设备产生超声波并通过探头发射,声波会在被检部位以一定的速度传播,当存在夹渣等异面介质时,部分超声波会被反射回来,通过接收机的处理,可以将缺陷的回波显示在示波器屏幕上,然后通过相关计算得到缺陷的深度和大小。
二、超声波探伤法在实际工作中的应用在进行探伤之前,我们需要了解图纸对焊接质量的技术要求。
目前,钢结构验收标准按照《钢结构工程施工质量验收规范》(GB50205-2001)执行。
标准规定:图纸要求焊缝焊接质量等级为一级,评定等级为一级时,规范要求100%超声波探伤;要求焊缝焊接质量等级为二级的图纸,评价等级为二级,按照现行规范,要求进行20%的超声波探伤;对于要求焊接质量等级 3 级的图纸,不进行超声波内部缺陷检查。
这里值得注意的是,超声波探伤用于全熔透焊缝,探伤率以每条焊缝长度的百分比计算,且不小于200mm。
超声扫描在IGBT模块焊层缺陷检测中的应用

2019电子工艺技术Electronics Process Technology第年1月40卷第1期29摘 要:超声扫描是一种常用的检测IGBT模块焊层缺陷的无损检测方法。
介绍了IGBT模块结构及超声扫描检测原理,指出了现有的检测方法存在的局限性。
用有限元模拟及实际结温测试的方法研究了超声扫描无法检测和分辨的焊层缺陷对模块散热性能的影响。
研究表明:由于DBC-底板焊层缺陷的遮挡,芯片-DBC焊层中无法被检测到的缺陷会造成模块最大结温偏差30 ℃以上;同一焊层检测时,芯片-DBC焊层中无法被准确分辨和定位的缺陷,会造成模块最大结温偏差5 ℃以上。
在实际生产或应用中,可采用热阻测试、三维X-RAY检测、超声A-扫描或超声B-扫描等检测手段,作为超声C-扫描的辅助检测手段。
关键词:IGBT模块;焊层缺陷;超声扫描;有限元模拟;散热性能中图分类号:TN305.94 文献标识码:A 文章编号:1001-3474(2019)01-0029-06Abstract: Acoustic Scanning Microscope is widely used to nondestructively detect defects of solder joint layer of IGBT module. IGBT module structure, SAM technology and its limitation were introduced. The influence of soldering defects which cannot be detected and distinguished with SAM on the thermal dissipation performance of IGBT module was studied by Finite Element Analysis and experimental junction temperature tests. The research result shows that the maximum deviation of module junction temperature was over 30 ℃ due to the defects in solder joint layer between die and DBC which cannot be detected with SAM; the maximum deviation of module junction temperature was over 5 ℃ due to the defects in solder joint layer between die and DBC which cannot be distinguished and accurately located. The methods of thermal resistance measurement, three-dimensional X-ray, SAM A-scan and SAM B-scan can be introduced as an assistant method for SAM C-scan in practical production and application of IGBT module.Key Words: IGBT module; soldering defects; SAM; FEA; thermal performance Document Code: A Article ID: 1001-3474 (2019) 01-0029-06超声扫描在IGBT模块焊层缺陷检测中的应用王刚明1,2,李聪成1,2,牛利刚1,2,王玉林1,2,滕鹤松1,2(1 南京电子器件研究所,江苏 南京 210016;2 扬州国扬电子有限公司,江苏 扬州 225100)作者简介:王刚明(1984- ),男,硕士,毕业于西安电子科技大学,工程师,主要从事功率模块结构设计与研发工作; 李聪成(1989- ),男,硕士,毕业于天津大学,工程师,主要从事功率模块封装工艺的研究开发。
超声相控阵在异种钢焊缝检测中的应用
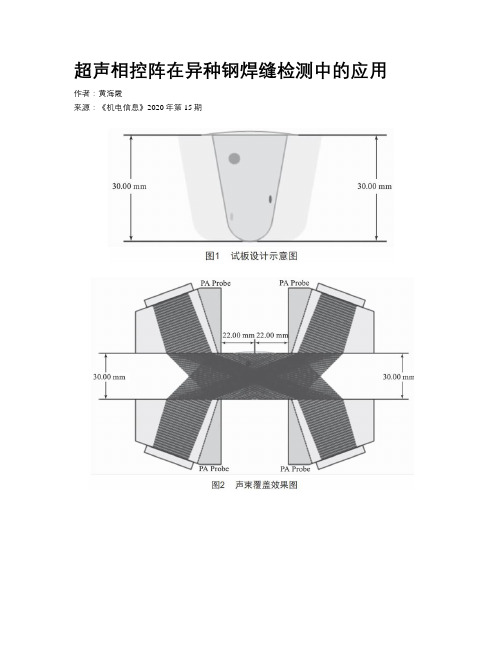
超声相控阵在异种钢焊缝检测中的应用作者:黄海霞来源:《机电信息》2020年第15期摘要:异种钢焊缝深刻影响着整体结构的安全,因此必须对焊接质量进行严格的检测,防止由于缺陷的存在而带来的严重后果。
异种钢焊缝通常具有形状不规则的特点,采用传统的超声波检测技术很难进行准确检测。
超声相控阵由于可以偏转和聚焦,因而在异种钢焊缝检测中得到了广泛的应用。
现通过实验手段对超声相控阵在异种钢焊缝检测中的应用进行了详细探讨,对常见缺陷的超声反射回波进行了分析。
实验结果表明:超声相控检测技术可以较好地满足异种钢焊缝检测的要求。
关键词:超声相控阵;异种钢焊接;焊缝检测0; ; 引言随着各类设备和材料的增加,不同材料之间的组合应用日益普遍,尤其是钢材的对接使用更是常见。
钢材对接会遇到异种钢焊接问题,由于不同种类的钢材料在物理、化学等特性上有明显的区别,二者之间的焊接成为应用的难点之一[1]。
无损检测技术是检测焊缝质量的主要技术,其中超声技术由于环保便捷而成为最主要的无损检测技术之一。
随着技术的发展,焊缝质量检测的要求也在不断提高,超声相控阵的应用更加广泛,并且技术日益成熟。
超声相控阵的出现,使焊缝缺陷可以通过二维成像结果清晰地显示出来,大大提高了检测的效率和可靠性。
本文通过实验手段对超声相控阵在异种钢焊缝检测中的应用进行了详细探讨,具有重要的现实意义。
1; ; 超声相控阵的原理及优势超声检测技术是工业无损检测四大常规技术中的重要一员,超声相控阵则是传统超声波检测技术的进一步发展,它已成为提高无损检测效率和质量的重要手段。
超声检测主要是利用了声波的反射现象进行材料缺陷的识别,是声学领域的重要应用方向。
超声探头中的压电晶片在电场的作用下发出高频振动,振动由探头传播出来后形成超声波,超声波在穿透材料的过程中,一旦遇到不规则的介质,其正常传播就会受到干扰,造成部分声波被吸收或反射回来,探头接收反射或透射的声场后通过仪器显示出来,即可分析出工件内部的缺陷信息[2]。
一种未焊透焊缝的超声波检测方法与流程

一种未焊透焊缝的超声波检测方法与流程以一种未焊透焊缝的超声波检测方法与流程为标题,写一篇文章。
超声波检测是一种常用的无损检测方法,广泛应用于焊接工艺中。
在焊接过程中,焊缝的质量是一个关键因素,而焊缝的完整性又与焊接工艺参数有关。
本文将介绍一种基于超声波检测的方法,用于检测焊缝的未焊透情况。
一、超声波检测原理超声波检测是利用超声波在材料中传播的特性来检测材料的内部缺陷或结构变化。
在焊接过程中,焊缝的未焊透通常指焊缝内部存在空洞或者未完全熔化的情况。
超声波在材料中传播时,遇到不同密度或声阻抗的界面会发生反射或折射,从而形成回波信号。
通过分析回波信号的特征,可以判断焊缝内部是否存在未焊透情况。
二、超声波检测流程1. 样品准备:选择代表性的焊接试件,确保试件的焊缝质量符合要求。
根据焊接工艺参数,确定焊缝的尺寸和位置。
2. 仪器调试:将超声波检测仪器接入样品,调整超声波探头的位置和角度,使其与焊缝垂直或接近垂直。
3. 超声波检测:开始进行超声波检测,将超声波探头放置在焊缝上方,通过仪器发送超声波信号。
超声波信号在焊缝内部传播,遇到未焊透的部分会发生反射或折射,形成回波信号。
4. 数据分析:将回波信号传输到计算机或仪器上,进行数据分析。
可以通过分析回波信号的振幅、时间和频率等参数,判断焊缝的完整性。
未焊透部分通常会表现为强回波信号或异常的回波信号。
5. 结果判定:根据数据分析的结果,判断焊缝的未焊透情况。
如果回波信号表明焊缝存在未焊透的情况,需要进行进一步的修复或改进焊接工艺参数。
三、未焊透焊缝超声波检测的优势1. 高精度:超声波检测具有高灵敏度和高分辨率的特点,可以准确地检测到未焊透的焊缝,并定位缺陷的位置。
2. 高效性:超声波检测可以实时进行,无需对样品进行破坏性检测,无需等待样品冷却。
因此,可以在焊接过程中进行检测,提高检测效率。
3. 无损检测:超声波检测是一种无损检测方法,不会对样品造成损伤,可以重复使用,降低了成本。
焊接超声无损检测技术指标
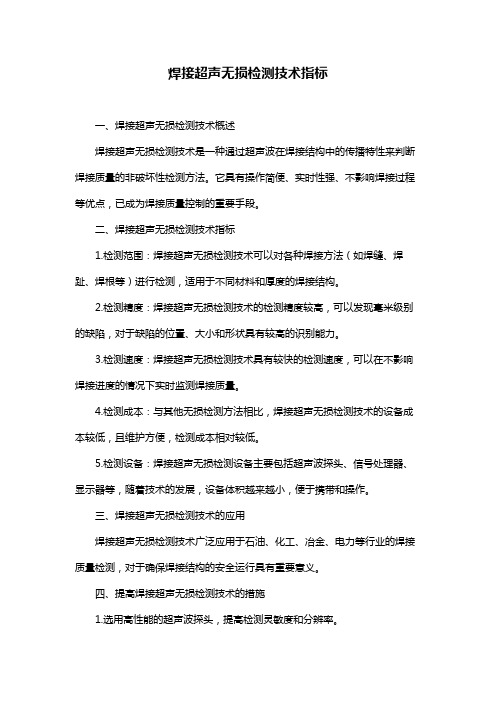
焊接超声无损检测技术指标一、焊接超声无损检测技术概述焊接超声无损检测技术是一种通过超声波在焊接结构中的传播特性来判断焊接质量的非破坏性检测方法。
它具有操作简便、实时性强、不影响焊接过程等优点,已成为焊接质量控制的重要手段。
二、焊接超声无损检测技术指标1.检测范围:焊接超声无损检测技术可以对各种焊接方法(如焊缝、焊趾、焊根等)进行检测,适用于不同材料和厚度的焊接结构。
2.检测精度:焊接超声无损检测技术的检测精度较高,可以发现毫米级别的缺陷,对于缺陷的位置、大小和形状具有较高的识别能力。
3.检测速度:焊接超声无损检测技术具有较快的检测速度,可以在不影响焊接进度的情况下实时监测焊接质量。
4.检测成本:与其他无损检测方法相比,焊接超声无损检测技术的设备成本较低,且维护方便,检测成本相对较低。
5.检测设备:焊接超声无损检测设备主要包括超声波探头、信号处理器、显示器等,随着技术的发展,设备体积越来越小,便于携带和操作。
三、焊接超声无损检测技术的应用焊接超声无损检测技术广泛应用于石油、化工、冶金、电力等行业的焊接质量检测,对于确保焊接结构的安全运行具有重要意义。
四、提高焊接超声无损检测技术的措施1.选用高性能的超声波探头,提高检测灵敏度和分辨率。
2.优化信号处理方法,提高信号质量,降低噪声影响。
3.开发智能化检测系统,实现缺陷自动识别和分级。
4.结合其他无损检测方法,如磁粉、渗透等,提高检测的全面性。
五、未来发展展望随着焊接技术的不断进步,焊接超声无损检测技术也将迎来新的发展机遇。
未来焊接超声无损检测技术将更加注重提高检测精度和速度,降低成本,实现智能化和自动化,为焊接质量控制提供更为强大的支持。
声波实验中如何分析超声波在工业中的应用

声波实验中如何分析超声波在工业中的应用在现代工业领域,超声波技术正发挥着日益重要的作用。
通过声波实验,我们能够深入探究超声波的特性,并更好地理解其在工业中的广泛应用。
超声波是频率高于 20000 赫兹的声波,其具有一系列独特的性质,使得它在工业中有着诸多不可替代的用途。
首先,在工业检测方面,超声波的应用极为广泛。
利用超声波的反射和穿透特性,可以对各种材料和构件进行无损检测。
例如,在航空航天领域,飞机的发动机叶片、机身结构等关键部件在长期使用过程中可能会出现微小的裂缝或缺陷。
通过超声波检测技术,能够在不破坏部件的情况下,准确地探测到这些潜在的问题,及时进行维修和更换,确保飞行安全。
在汽车制造中,发动机缸体、轮毂等部件的质量检测也离不开超声波。
它可以迅速发现内部的气孔、夹杂物等缺陷,提高产品的合格率和可靠性。
其次,超声波在工业清洗领域表现出色。
传统的清洗方法往往难以彻底清除复杂形状零件表面的污垢和油脂。
而超声波清洗则利用高频振动产生的微小气泡,在液体中迅速形成并破裂,产生强烈的冲击和搅拌作用。
这种“空化效应”能够有效地去除零件表面的污垢,而且不会损伤零件的表面。
在电子工业中,印刷电路板、集成电路芯片等精密部件的清洗,超声波清洗技术能够保证其清洁度,提高产品的性能和稳定性。
在机械加工行业,对各种工具、模具的清洗,超声波也能够发挥高效、节能的优势。
再者,超声波在焊接领域也有着重要的应用。
超声波焊接是一种固态焊接技术,通过高频振动使焊件表面产生摩擦热,从而实现材料的连接。
与传统的焊接方法相比,超声波焊接具有焊接速度快、焊接强度高、焊缝美观等优点。
在塑料焊接中,超声波能够将不同形状和材质的塑料部件快速、牢固地连接在一起,广泛应用于汽车零部件、电子电器外壳等产品的生产。
在金属焊接方面,超声波焊接对于薄型金属材料的连接效果显著,尤其适用于一些对焊接精度和外观要求较高的场合。
此外,超声波还在材料加工中发挥着重要作用。
金属薄板的超声兰姆波无损检测
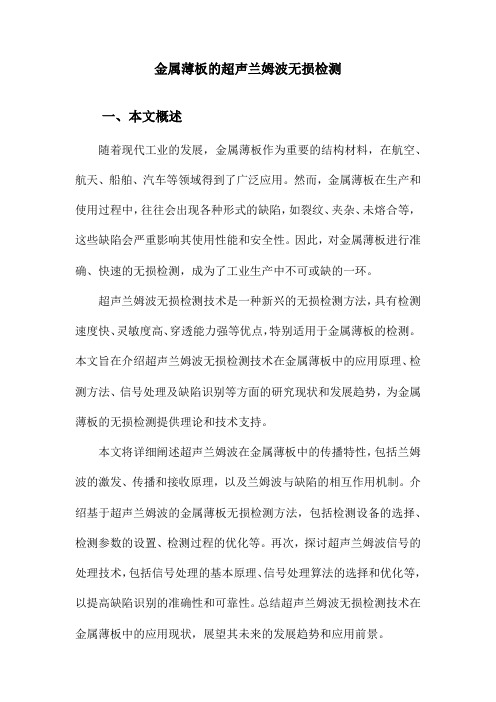
金属薄板的超声兰姆波无损检测一、本文概述随着现代工业的发展,金属薄板作为重要的结构材料,在航空、航天、船舶、汽车等领域得到了广泛应用。
然而,金属薄板在生产和使用过程中,往往会出现各种形式的缺陷,如裂纹、夹杂、未熔合等,这些缺陷会严重影响其使用性能和安全性。
因此,对金属薄板进行准确、快速的无损检测,成为了工业生产中不可或缺的一环。
超声兰姆波无损检测技术是一种新兴的无损检测方法,具有检测速度快、灵敏度高、穿透能力强等优点,特别适用于金属薄板的检测。
本文旨在介绍超声兰姆波无损检测技术在金属薄板中的应用原理、检测方法、信号处理及缺陷识别等方面的研究现状和发展趋势,为金属薄板的无损检测提供理论和技术支持。
本文将详细阐述超声兰姆波在金属薄板中的传播特性,包括兰姆波的激发、传播和接收原理,以及兰姆波与缺陷的相互作用机制。
介绍基于超声兰姆波的金属薄板无损检测方法,包括检测设备的选择、检测参数的设置、检测过程的优化等。
再次,探讨超声兰姆波信号的处理技术,包括信号处理的基本原理、信号处理算法的选择和优化等,以提高缺陷识别的准确性和可靠性。
总结超声兰姆波无损检测技术在金属薄板中的应用现状,展望其未来的发展趋势和应用前景。
通过本文的研究,旨在为金属薄板的超声兰姆波无损检测提供全面、系统的理论指导和技术支持,推动该技术在工业生产中的广泛应用和发展。
二、超声兰姆波无损检测基本原理超声兰姆波无损检测是一种先进的无损检测技术,它利用兰姆波在金属薄板中的传播特性来进行缺陷检测和评估。
兰姆波是一种在板状结构中传播的弹性波,其特性使得它能够在金属薄板内部形成复杂的传播模式,从而有效地检测出板内的各种缺陷。
在超声兰姆波无损检测中,高频超声波被激发并注入到待检测的金属薄板中。
这些超声波在板内传播时,会受到板内缺陷的影响,如裂纹、夹杂、未熔合等。
当超声波遇到这些缺陷时,会发生反射、散射或模式转换等现象,导致波形的变化。
通过分析这些波形变化,可以推断出缺陷的位置、大小和类型。
超声波探伤检测在钢结构工程中的运用

超声波探伤检测在钢结构工程中的运用发布时间:2021-09-03T14:56:57.360Z 来源:《工程建设标准化》2021年5月10期作者:顾银华[导读] 现如今我国大型建筑规模不断增加,钢结构作为大型建筑中的重要结构,需要确保钢结构焊接质量,以此来保障建筑整体质量安全。
顾银华南通天和建设工程质量检测有限公司摘要:现如今我国大型建筑规模不断增加,钢结构作为大型建筑中的重要结构,需要确保钢结构焊接质量,以此来保障建筑整体质量安全。
超声波无损探伤检测技术作为钢结构焊接质量检测中的重要方法,就需要结合检测重点与要点,针对钢结构焊缝中可能存在的缺陷进行检测分析,采取有效的措施,提升检测准确性。
关键词:超声波无损探伤检测;钢结构焊接质量;技术前言:在钢结构焊接中超声波探伤技术得到了广泛的运用,对我国工业发展产生了积极的影响。
因超声波探伤检测对工作人员、超声波探伤仪等的要求比较严格,所以就需要确保工作人员掌握扎实的专业技术与知识,针对钢结构焊缝采取适合的检测方法,提高钢结构焊缝质量检测水平,避免焊缝缺陷对钢结构整体产生不利影响。
一、超声波探伤无损检测(一)超声波探伤无损检测技术在钢结构中使用超声波无损检测技术时,要求检测人员需要在运用中针对结构图纸进行细致化的研究,掌握其中的重点与要点环节。
超声波无损检测中还涉及到了GB50205-2020《钢结构工程施工质量验收标准》等标准,需要遵循钢结构施工、验收规范,做好执行等工作。
在使用超声波无损检测技术时,如图纸要求焊缝质量等级为一级时,要按照焊缝条数和长度的100%进行超声波探伤,即只要有焊缝的地方都必须检测到,不能漏检,而且它的评定等级至少为Ⅱ级;当图纸要求质量等级为二级时,则需要进行20%的比例进行超声波探伤。
很多人认为二级焊缝探伤就是抽检焊缝总条数的20%,这种理解其实是错误的,它需要分两种情况。
①抽检每条焊缝长度的20%(mm)钢结构加工厂的焊缝或现场安装的焊缝长度如果大于1m时,每条焊缝都要进行探伤,每条焊缝检测长度为整条焊缝的20%,检测部位在焊缝的两端。
超声波检测技术在工业领域中的应用
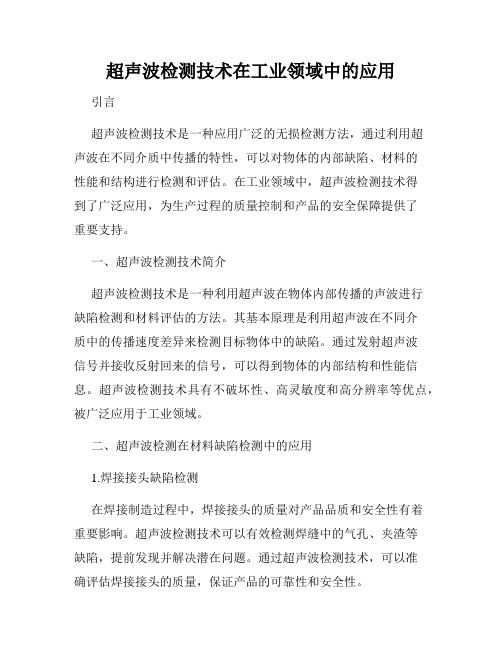
超声波检测技术在工业领域中的应用引言超声波检测技术是一种应用广泛的无损检测方法,通过利用超声波在不同介质中传播的特性,可以对物体的内部缺陷、材料的性能和结构进行检测和评估。
在工业领域中,超声波检测技术得到了广泛应用,为生产过程的质量控制和产品的安全保障提供了重要支持。
一、超声波检测技术简介超声波检测技术是一种利用超声波在物体内部传播的声波进行缺陷检测和材料评估的方法。
其基本原理是利用超声波在不同介质中的传播速度差异来检测目标物体中的缺陷。
通过发射超声波信号并接收反射回来的信号,可以得到物体的内部结构和性能信息。
超声波检测技术具有不破坏性、高灵敏度和高分辨率等优点,被广泛应用于工业领域。
二、超声波检测在材料缺陷检测中的应用1.焊接接头缺陷检测在焊接制造过程中,焊接接头的质量对产品品质和安全性有着重要影响。
超声波检测技术可以有效检测焊缝中的气孔、夹渣等缺陷,提前发现并解决潜在问题。
通过超声波检测技术,可以准确评估焊接接头的质量,保证产品的可靠性和安全性。
2.金属材料中的裂纹检测金属材料在使用过程中容易产生裂纹,如果未能及时发现和处理,将对产品的使用寿命和安全性造成严重影响。
超声波检测技术可以对金属材料中的裂纹进行快速、准确的检测和评估。
通过超声波检测,可以及时判定裂纹的位置、形态和大小,并采取相应的修复措施,保证产品的质量和可靠性。
三、超声波检测在结构评估中的应用1.混凝土结构评估混凝土结构的安全性和稳定性对于建筑物的使用寿命和居民的安全至关重要。
超声波检测技术可以对混凝土结构中的空洞、裂缝等缺陷进行检测和评估。
通过超声波检测技术,可以预测混凝土结构的老化程度、耐久性和稳定性,为维修和加固工作提供决策依据。
2.管道和容器的健康评估管道和容器的健康状况对于工业生产和环境保护都具有重要意义。
超声波检测技术可以对管道和容器中的腐蚀、疲劳裂纹等缺陷进行评估和监测。
通过超声波检测技术,可以实时监测管道和容器的健康状况,提前发现并解决潜在问题,避免事故和污染的发生。
五大无损检测的原理及应用

五大无损检测的原理及应用五大无损检测的原理及应用如下:1. 超声波检测(Ultrasonic T esting, UT)原理:超声波通过材料中的传播而发生不同程度的反射、折射、衍射等现象,通过对反射回波和传播时间的测量,可以判断材料内部是否存在缺陷。
应用:超声波检测广泛应用于金属材料的缺陷检测,如焊接接头、铸件、锻件等。
在航空航天、船舶制造、石油化工等领域中有着重要的应用。
2. 磁粉检测(Magnetic Particle Testing, MT)原理:在被检测材料的表面施加直流或交流磁场,通过涂覆磁粉或喷射磁粉,当磁粉聚集在材料表面附近的缺陷处时,形成可见的磁粉堆积痕迹。
应用:磁粉检测用于检测表面和近表面的裂纹、裂纹痕迹以及其他磁性材料的缺陷。
广泛应用于航空、电力、汽车、船舶等行业。
3. 渗透检测(Dye Penetrant Testing, PT)原理:将高表面张力的渗透液涂覆在被检材料表面,经过适当的渗透时间后,渗透液会通过缺陷的毛细作用进入缺陷内部,再通过涂上显色剂和溶剂,显示缺陷的位置和形状。
应用:渗透检测适用于检测金属和非金属表面的细小裂纹、孔洞以及其他缺陷。
常用于航空、汽车、造船和金属制造等领域。
4. X射线检测(X-ray Testing, RT)原理:通过X射线的穿透、吸收和散射,检测材料内部的缺陷。
传统的X射线检测主要基于矢量模型,现代技术越来越多地使用CT(计算机断层扫描)技术。
应用:X射线检测广泛应用于检测金属和非金属材料的内部缺陷,如焊接缺陷、夹杂物、孔洞等。
在航空航天、核能、汽车、电子等行业中得到重要应用。
5. 热波无损检测(Thermal/Infrared T esting, IR)原理:基于材料或构件的热学性质差异,检测材料内部的缺陷或异物。
通过测量材料散热或吸热的温度变化,获得缺陷位置及性质的信息。
应用:热波无损检测适用于检测钢铁、塑料、陶瓷和复合材料等材料的内部和表面缺陷。
焊缝超声波检测时DAC曲线的制作与应用

图1-3平底孔实用AVG曲线
1.2.2.3
AVG曲线,即:DGS曲线。以KK的探头和仪器为例,KK的探头都会附带一张实用DGS曲线图。该曲线是此探头对各种尺寸反射体(各种孔径的平底孔和大平底)的DAC曲线的综合,这些曲线是该探头在多种尺寸的反射体上实测出来,并通过大量的数据归纳总结,最终得出代表性的[3],如图1-4~图1-5所示。
本文分析了超声波检测在检测时对检测结果的分析,应用DAC曲线和DAC曲线的多种制作方法,并对比分析了各种DAC曲线的制作方法优缺点如:直线连接法;最小二乘拟合法;拉格朗日拟合曲线法等,并且还介绍了增益型波检测DAC曲线与衰减型检测DAC曲线。
DAC曲线在实际工程中的应用很是广泛。其中本文以TC4大直径钛合金棒材超声波探伤为例证明DAC曲线可以对保证准确的灵敏度及建立曲线进行声程补偿,可有效解决材料探伤杂波较高的问题,保证大直径棒材的有效检测,以保证探伤结果的准确性、可靠性。
图1-4直探头MB2 S(E)
图1-5斜探头MWB4 5-4(E)
1.3
目前,国外超声波检测对于缺陷当量的绘制主要以模拟和仿真研究一方面集中在以解析方法为主开发工业应用的软件系统,进行超声波检测工艺及可行性、可靠性分析,以降低检测成本,提高效率;另一方面是采用数值方法进行模拟和仿真,针对现代工业广泛使用的各向异性材料和特殊结构件进行超声检测研究,以提高检测精度,拓宽超声波检测的应用范围。
焊缝超声波检测时DAC曲线的制作与应用
摘要
在超声波检测时,为了避免漏检,超声检测人员通常用较高的灵敏度(二次波或三次波的灵敏度)作为扫查灵敏度。当在扫查过程中发现缺陷时,根据缺陷波距一次波、二次波(三次波)的水平位置远近选用水平差值最小的波次的灵敏度对缺陷进行定量。因此在超声波检测时应用DAC曲线,不仅可灵敏的监测出缺陷的位置所在,而且简单方便。
超声波无损检测技术在工业中的应用
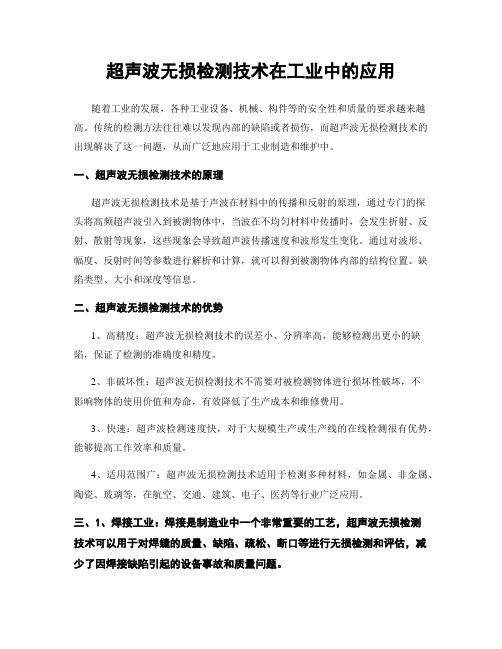
超声波无损检测技术在工业中的应用随着工业的发展,各种工业设备、机械、构件等的安全性和质量的要求越来越高。
传统的检测方法往往难以发现内部的缺陷或者损伤,而超声波无损检测技术的出现解决了这一问题,从而广泛地应用于工业制造和维护中。
一、超声波无损检测技术的原理超声波无损检测技术是基于声波在材料中的传播和反射的原理,通过专门的探头将高频超声波引入到被测物体中,当波在不均匀材料中传播时,会发生折射、反射、散射等现象,这些现象会导致超声波传播速度和波形发生变化。
通过对波形、幅度、反射时间等参数进行解析和计算,就可以得到被测物体内部的结构位置、缺陷类型、大小和深度等信息。
二、超声波无损检测技术的优势1、高精度:超声波无损检测技术的误差小、分辨率高,能够检测出更小的缺陷,保证了检测的准确度和精度。
2、非破坏性:超声波无损检测技术不需要对被检测物体进行损坏性破坏,不影响物体的使用价值和寿命,有效降低了生产成本和维修费用。
3、快速:超声波检测速度快,对于大规模生产或生产线的在线检测很有优势,能够提高工作效率和质量。
4、适用范围广:超声波无损检测技术适用于检测多种材料,如金属、非金属、陶瓷、玻璃等,在航空、交通、建筑、电子、医药等行业广泛应用。
三、1、焊接工业:焊接是制造业中一个非常重要的工艺,超声波无损检测技术可以用于对焊缝的质量、缺陷、疏松、断口等进行无损检测和评估,减少了因焊接缺陷引起的设备事故和质量问题。
2、机械行业:超声波无损检测技术可以用于检测机械设备中的零件缺陷、裂纹、腐蚀、磨损等问题,有助于及时维护维修,提高设备的可靠性和使用寿命。
3、航空航天工业:超声波无损检测技术在飞机、火箭、卫星等飞行器的制造和维护中起着重要的作用,可以检测到各种结构体内部的缺陷,提高了飞行器的安全性和可靠性。
4、汽车制造业:超声波无损检测技术可以用于汽车驱动轴、底盘和车身等部位的检测和评估,及时发现缺陷和裂纹,有助于提高汽车的质量和安全性。
- 1、下载文档前请自行甄别文档内容的完整性,平台不提供额外的编辑、内容补充、找答案等附加服务。
- 2、"仅部分预览"的文档,不可在线预览部分如存在完整性等问题,可反馈申请退款(可完整预览的文档不适用该条件!)。
- 3、如文档侵犯您的权益,请联系客服反馈,我们会尽快为您处理(人工客服工作时间:9:00-18:30)。
关于超声无损检测技术在金属焊接中的应用研究
发表时间:2019-07-23T15:05:08.900Z 来源:《科技研究》2019年5期作者:李绍波
[导读] 金属焊接工艺与成品质量存在密切关联,采用超声无损检测技术是定位焊接缺陷、优化金属焊接质量的重要举措。
(山东联友石化工程有限公司 250101)
摘要:金属焊接工艺与成品质量存在密切关联,采用超声无损检测技术是定位焊接缺陷、优化金属焊接质量的重要举措。
本文简要分析了金属焊接中存在的主要缺陷类型,围绕质量检测环节把控、直接接触法、液浸法、导波技术以及周向导播技术等层面,探讨了超声无损检测技术在金属焊接中的具体应用,以供参考。
关键词:金属焊接;质量检测;超声无损检测技术
引言:通常在使用金属焊接工艺时会面临一系列干扰因素,诸如焊接工艺水平、金属材质、焊接作业环境等均会影响到焊接质量。
超声无损检测技术主要依据超声波在构件内部传播时遇到不同界面将有不同的反射信号(回波)。
利用不同反射信号传递到探头的时间差,可以检查到构件内部的缺陷。
根据在荧光屏上显示出的回波信号的高度、声程等可以判断缺陷的大小、位置,进而依据检测结果定位被测物质存在的缺陷点,提高金属焊接质量。
1金属焊接中存在的主要缺陷类型及超声回波特征
1.1气孔
通常在金属焊接的过程中,熔池在高温条件下会吸收外部气体,待其冷却后即会在焊缝中形成残留的空穴,同时倘若母材表面存在油污或锈蚀问题、焊剂未能完全烘干、采用低纯度的保护气体执行气体保护焊工艺、焊接电流过大、在施焊过程中未做好防风措施等,均有可能导致金属表面或焊缝处形成气孔。
在采用超声无损检测技术观察其波形特征时可以发现,单气孔的回波较低、波形稳定,经环绕扫查后可发现其反射波的高度保持一致,气孔密集处的波高起伏较大[1]。
1.2裂纹
因金属焊接产生的裂纹大体包含分热裂纹、冷裂纹、再热裂纹等几种类型,在承压设备中,裂纹是危害性最大的缺陷,多由施焊过程中熔池冷却速度过快导致,使焊缝处因受热不均匀产生偏析、拉应力等情况,同时焊接应力过大、焊件刚度过大、焊剂的氢含量过高等因素也有可能引发裂纹问题。
在探测裂纹波形时可以发现,其回波较高、波幅较宽,且在平移探头时会出现多次反射波,在转动探头时还会引发波峰错动情况。
1.3夹渣
焊缝坡口尺寸过大或过小、焊缝附近有杂质、焊接电流过小、焊剂中硫含量或磷含量过高等因素,均会导致金属焊缝表面处出现夹渣问题。
通过观察夹渣的波形特征可以发现,其波峰呈锯齿形、回波较弱,在平移探头时波幅出现明显变化,且不同方位处的反射波幅存在明显差异。
1.4未焊透或未熔合
坡口间隙过小、焊接电流过小、焊根未完全清洁等因素均会造成未焊透问题,通过观察其波形特征可以发现反射波幅较高,波形稳定;坡口处母材破损、焊接电流过小、焊接速度过快等因素均有可能引发未熔合问题,其波形较为稳定,两侧反射波幅存在明显差异。
2超声无损检测技术在金属焊接中的具体应用探讨
2.1质量检测环节把控
在金属焊接中采用超声无损检测技术,需围绕以下三个环节强化质量检测标准的把控:其一是金属焊接环节,检测人员首先利用超声检测技术对焊接母材质量进行检测,焊接完成后,需利用超声无损检测着重针对焊接接头质量进行检测,评级。
围绕技术层面检验焊缝内部有无气孔、裂纹、未焊透等缺陷,通过观察焊缝的缺陷回波最大处定位存在异常情况的焊接部位,进而依据焊接工艺及条件判断缺陷成因,以此提高金属焊接的质量与精度;其二是宏观缺陷检测,倘若在高温条件作用下使金属材料在焊接过程中生成液态金属,经由焊缝传递至母材表面,待其温度冷却后即会在金属表面产生金属瘤,严重影响到金属材料的美观性与宏观持续性,因此通常借助超声波探伤仪进行金属焊缝质量的探测,通过探查金属物表面获取到实际焊接厚度,将其与标准值进行对比即可判断有无焊接缺陷,以此实现对宏观焊接故障的有效检测;其三是检测结果的应用,将借助超声无损检测技术绘制的距离波幅曲线进行充分利用,即可定位具体的金属焊接缺陷严重程度并寻求其主要成因,以此为依据进行金属焊接工艺的调整,从而有效防范焊接缺陷的发生。
2.2超声无损检测方法
2.2.1直接接触法
作为超声无损检测技术中的常用方法之一,直接接触法主要在探头处均匀涂抹一层较薄的耦合介质,通过利用探头接触被测金属物质的表面,使超声波在传入两种介质接触面时形成反射,以此获取到反射波。
为确保检测结果的可靠性,需在检测前预先排除接触面间的空气,确保探头可有效发送并接收由被测对象处反射回的超声波,防范声能全部反射的问题。
同时,需针对被检测对象的表面进行打磨与清洁处理,确保表面的光洁,实现被测表面与探头的充分接触,提高检测结果的可信度。
此外,还需针对耦合剂的性能进行调控,优先选取硅油、甘油等高声阻抗、无腐蚀性的耦合剂,以此降低超声波在传递过程中的能量损失,进一步提高检测结果的精确度。
2.2.2液浸法
液浸法通常分为全部液浸、局部液浸与喷流式液浸三种类型,借助液体耦合层实现超声波的反射,确保声能有效入射到被测金属材料中,倘若被测金属材料内部存在缺陷则将会形成回波反射现象,无需探头与被测物质的直接接触,有效提高超声波发射、接收过程的稳定性。
2.3电磁超声无损检测技术
2.3.1导波技术
该技术适用于针对薄板激光焊缝中的气孔、裂纹、未熔合等缺陷进行检测,借助超声导波实现对焊缝区域内存在缺陷的有效判断。
通
常需利用声波反射特性在薄板激光焊缝处分别完成面缺陷、点缺陷通道的设置,其中面缺陷通道的声波发射方向应与焊缝呈垂直布设,依据焊缝两侧板厚的差异实现声波反射,存在缺陷部位的反射能量将显著增大,因而使接收到的回波信号强度明显增大;而点缺陷通道的声波发射方向应与焊缝间保持一定夹角,借助散射回波实现缺陷判断[2]。
2.3.2周向导波技术
该技术适用于针对电阻焊钢管焊缝的裂纹等缺陷进行无损检测,通常需将检测仪器布设在距焊剂的位置,利用电磁超声单向换能器发出导波,经由接收传感器传递至焊缝位置,在存在缺陷处形成反射回波。
为提高检测结果的精确度,还需优化检测装置的跟踪、定位功能,防范出现漏检问题,提高检测实效。
结论:超声无损检测技术主要利用介质的声学传播特性检测物体内部发生的变化,因此还应依据不同金属材料的材质性能、焊接工艺进行超声无损检测工艺的科学选取,确保能够有效判断金属材料的焊接缺陷及其特征。
未来还需配合超声相控阵技术、借助计算机智能化自动化等技术实现超声无损检测技术的创新,为检测精度的提高提供保障。
参考文献:
[1]谈雷.金属材料焊接中超声无损检测技术的有效应用[J].科技风,2018,366,(34):153.
[2]陈峰.超声波无损检测系统在金属焊接材料中的应用探究[J].江西建材,2018,236,(11):45+47.。