锂电车间工序名称翻译
锂电行业工序中英名称对照

数量 1 1 1 1 1 1 1 1 1 1 2 1 3 1 1 1 1
编号
Manufacturing Dept. Engineering Dept. Warehouse Woman's Dressing Rm. Man's Dressing Rm. Air Shower Rm. Anode Slurry Mixing Cathode Slurry Mixing Cathode Slurry Mixing Coating Coating Anode Rolling Cathode Rolling Anode Die Cutting Cathode Die Cutting Electrode Assembling Heat Sealing Electrolyte Injection Aging Room Capacity Grading Battery Formation Capacity Grading Instruments Battery Formation Instruments Pouch Cell Sealing Electrolyte Injection Pouch Cell Packing Warehouse Battery Packing Workshop Electrolyte Storage Rm. Warehouse Equipment Repair Rm. Dehumidification Equipments Gas Source Rm. Rest Room Performance Testing System R&D Rm. 这个牌子给技术部办公楼用
名称 制造部 设备部 综合仓库 女更衣室 男更衣室 风淋室 负极和浆 正极和浆 油系搅拌 油系涂布 涂布 负极辊压 正极辊压 负极制片 正极制片 叠片 热封 注液1 老化 分容 化成 分容机柜 化成机柜 封装 注液2 包装 半成品仓库 Pack间 电解液房 原材料仓库 机修间 空调除湿机房 三气机房 休息室 综合检测 系统研发
圆筒形锂电池生产工艺流程英语
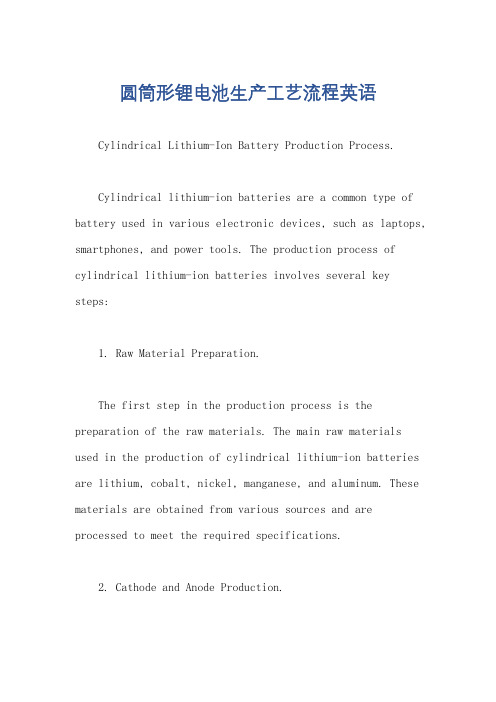
圆筒形锂电池生产工艺流程英语Cylindrical Lithium-Ion Battery Production Process.Cylindrical lithium-ion batteries are a common type of battery used in various electronic devices, such as laptops, smartphones, and power tools. The production process of cylindrical lithium-ion batteries involves several key steps:1. Raw Material Preparation.The first step in the production process is the preparation of the raw materials. The main raw materials used in the production of cylindrical lithium-ion batteries are lithium, cobalt, nickel, manganese, and aluminum. These materials are obtained from various sources and are processed to meet the required specifications.2. Cathode and Anode Production.The cathode and anode are the two electrodes of a lithium-ion battery. The cathode is typically made of a lithium-metal oxide compound, such as lithium cobalt oxide (LiCoO2) or lithium nickel manganese cobalt oxide (NMC). The anode is typically made of a carbon-based material, such as graphite or silicon.The cathode and anode materials are synthesized through a series of chemical processes. The cathode material is typically synthesized by mixing lithium salts with metal salts and then heating the mixture at high temperatures. The anode material is typically synthesized by mixing carbon precursors with a binder and then heating the mixture at high temperatures.3. Electrode Coating.Once the cathode and anode materials have been synthesized, they are coated onto metal current collectors. The current collectors are typically made of aluminum or copper. The cathode material is coated onto the positive current collector, and the anode material is coated ontothe negative current collector.The electrode coating process is typically carried out using a slurry method. The cathode or anode material is mixed with a solvent and a binder to form a slurry. The slurry is then coated onto the current collector using a doctor blade or a slot die coater.4. Electrode Drying and Calendering.After the electrodes have been coated, they are dried to remove the solvent. The electrodes are then calendered to improve their density and electrical conductivity. Calendering is a process in which the electrodes are passed through a series of rollers under pressure.5. Cell Assembly.The next step in the production process is the cell assembly. The cell assembly process involves stacking the electrodes together with a separator between them. The separator is a porous material that prevents the electrodesfrom making contact with each other and causing a short circuit.The electrodes and separator are typically stacked together in a winding machine. The winding machine rolls the electrodes and separator into a cylindrical shape.6. Cell Formation.Once the cells have been assembled, they are subjected to a formation process. The formation process involves charging and discharging the cells several times under controlled conditions. The formation process helps to stabilize the electrochemical reactions within the cells and improve their performance.7. Cell Testing.After the cells have been formed, they are tested to ensure that they meet the required specifications. The cells are tested for capacity, voltage, and internal resistance. The cells that do not meet the specificationsare rejected.8. Cell Packaging.The final step in the production process is the cell packaging. The cells are typically packaged in a metal can or a plastic pouch. The packaging protects the cells from the environment and prevents them from being damaged.The cylindrical lithium-ion battery production process is a complex and multi-step process. The quality of the batteries depends on the quality of the raw materials, the precision of the manufacturing processes, and the quality control procedures.。
锂电池生产工艺流程讲解
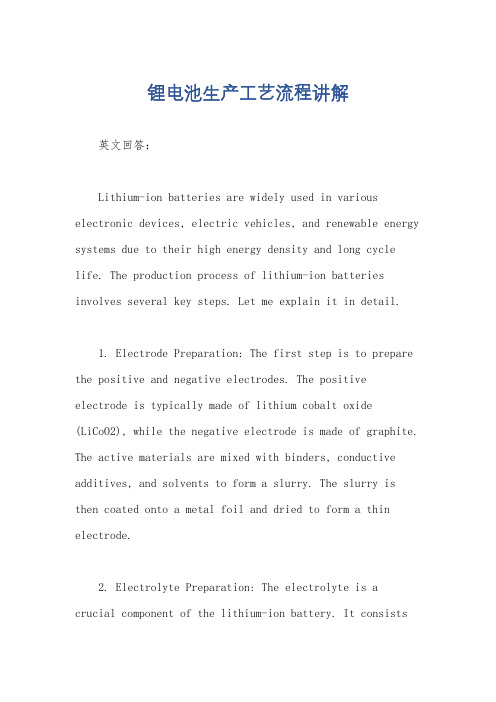
锂电池生产工艺流程讲解英文回答:Lithium-ion batteries are widely used in various electronic devices, electric vehicles, and renewable energy systems due to their high energy density and long cycle life. The production process of lithium-ion batteries involves several key steps. Let me explain it in detail.1. Electrode Preparation: The first step is to prepare the positive and negative electrodes. The positive electrode is typically made of lithium cobalt oxide (LiCoO2), while the negative electrode is made of graphite. The active materials are mixed with binders, conductive additives, and solvents to form a slurry. The slurry is then coated onto a metal foil and dried to form a thin electrode.2. Electrolyte Preparation: The electrolyte is acrucial component of the lithium-ion battery. It consistsof a lithium salt dissolved in an organic solvent. The most commonly used lithium salt is lithium hexafluorophosphate (LiPF6). The electrolyte is prepared by dissolving the lithium salt in the solvent under controlled conditions.3. Cell Assembly: The next step is to assemble the battery cell. The positive and negative electrodes are stacked together with a separator in between to prevent short circuits. The separator is typically made of a porous polymer material that allows the flow of lithium ions while preventing the direct contact between the electrodes. The electrodes and separator are then rolled or folded into a compact structure.4. Electrolyte Filling: Once the cell is assembled, it is filled with the electrolyte. The electrolyte is injected into the cell through small openings or ports. Care must be taken to ensure that the cell is filled with the correct amount of electrolyte to avoid overfilling or underfilling.5. Sealing: After the electrolyte filling, the cell is sealed to prevent leakage. The sealing process involvesapplying a heat-sealable material or using a laser to weld the cell edges together. This ensures that the cell is hermetically sealed and prevents the escape of electrolyteor the ingress of moisture or contaminants.6. Formation: The final step is the formation process, which involves charging and discharging the battery to activate the electrodes and stabilize the cell performance. During the formation process, the battery undergoes several cycles of charging and discharging at specific voltages and currents. This helps to improve the battery's capacity and overall performance.中文回答:锂离子电池由于其高能量密度和长循环寿命,在各种电子设备、电动车和可再生能源系统中得到广泛应用。
(完整版)锂电池英文生产流程

Mixing(配料)Mix solvent and bound separately with positive and negative active materials. Make into positive and negative pasty materials after stirring at high speed till uniformity.Coating(涂布)Now, we are in coating line. We use back reverse coating. This is the slurry-mixing tank. The anode(Cathode)slurry is introduced to the coating header by pneumaticity from the mixing tank. The slurry is coated uniformly on the copper foil, then the solvent is evaporated in this oven. (下面的依据情况而定)There are four temperature zones, they are independently controlled. Zone one sets at 55 degree C, zone two sets at 65 degree C, zone three sets at 80 degree C, zone four sets at 60 degree C. The speed of coating is 4 meters per minute.You see the slurry is dried. The electrode is wound to be a big roll and put into the oven. The time is more than 2 hours and temperature is set at 60 degree C.Throughout the coating, we use micrometer to measure the electrode thickness per about 15 minutes. We do this in order to keep the best consistency of the electrode.Vocabulary:coating line 涂布车间back reverse coating 辊涂coating header 涂布机头Al/copper foil 铝/铜箔degree C 摄氏度temperature zones 温区wind to be a(big)roll 收卷evenly/uniformly 均匀oven 烘箱evaporate 蒸发electrode 极片CuttingCut a roll of positive and negative sheet into smaller sheets according to battery specification and punching request.PressingPress the above positive and negative sheets till they become flat.PunchingPunching sheets into electrodes according to battery specification,ElectrodeAfter coating we compress the electrode with this cylindering machine at about 7meters per minute. Before compress we clean the electrode with vacuum and brush to eliminate any particles. Then the compressed electrode is wound to a big roll. We use micrometer to measure the compressed electrode thickness every 10 minutes. After compressing we cut the web into large pieces. We tape the cathode edge to prevent any possible internal short. The large electrode with edge taped is slit into smaller pieces. This is ultrasonic process that aluminum tabs are welded onto cathodes using ultrasonic weld machine. We tape the weld section to prevent any possible internal short. And finally, we clean the finished electrodes with vacuum and brush.Vocabulary:cylindering 柱形辊压vacuum 真空particle 颗粒wound 旋紧卷绕micrometer 千分尺internal short 内部短路slit 分切ultrasonic 超声波weld 焊接Anode makingIn anode making process, we cut the material into certain length strips. At the mean time, we put a small piece of insulation tape to the tab in order to prevent any possible internal short. Then the prepared nickel tab is riveted on anode and pat plain. We also tape the rivet section to prevent any possible internal short. And finally, we clean the finished electrodes with vacuum and brush.Jelly rollThis is Jelly roll, a manual winding process. In the course of Jelly roll, firstly, we place the separator in between central pins, press the foot switch to turn central pins about 120 degrees. Secondly, place the anode to the edge of central pins, and turn central pins about 180 degrees. Lastly, place the cathode to the edge of central pins. During the winding process, we apply tension by pressing the electrodes and the separator. We put the termination tape at the end.After Jelly roll, we check the short circuit, then form the Jelly roll by pressing, so that it is easier to insert the Jelly roll into the can.Control points:1. When winding to the end of the anode, covering the anode completely by the separator.2. In the whole process, it is the most important points to ensure the best alignment among the cathode, the anode and the separator for the Jelly roll. The separator has to cover the anode and the cathode, and the anode has to cover the cathode completely. These points are mainly checked before short checking.Vocabulary:Jelly roll 卷绕Manual 手工的Separator 隔膜纸central pin 卷针foot switch 脚踏开关anode 负极片cathode 正极片termination tape 尾端胶纸short circuit 短路alignment 整齐Taping & insertingPut the tape on the two side of J/R, To prevent J/R being hurt in the insertion process.Put a piece of tape between cathode tab and J/R .Because anode electrode is wider than cathode electrode.Put the bottom tape.Insert the finished J/R into the can manually and then short circuit check by multi-meter.Spot welding Ni tab to cap.Ultrasonic welding the Al tab to cap using ultrasonic weld.We have the second spot welding to ensure the best contact between the tab and cap.Apply top insulator, to prevent Ni tab contacting with can.Final J/R insertion by the centrifuge.Cap positioning by hand. Then check the cap in the suitable position, or the defects is put into red bin ,Finally , short circuit check again to ensure that there be no internal short J/R flowing to next line.Vocabulary:J/R 极芯tape 胶纸electrode 极片multi-meter 万用表Spot welding 点焊Ni tab 极耳Ultrasonic weld 超焊Insulator 隔圈centrifuge machine 甩壳机defect 次品red bin 红盒Laser weldingThis is the Laser welding room! The first process is welding for the aluminum cap, specially connect the rivet with the weld plate to prevent the cell impedance excursion.The second process is the Laser seam welding. In the process, it must ensure the intensity and airproof characters of the weld.After the cell is welded, we would perform the leak checking, the short circuit checking and the weighing checking.Vocabulary:Laser welding room 激光焊接车间Cap 盖板Rivet 铆钉Plate 镍片impedance excursion 内阻漂移intensity 强度leak checking 检漏short circuit checking 测短路weighing checking 称重Oven drying electrolyte filling and storingThis is the process of cells oven drying at 80℃ for more than 12 hours under vacuum. After oven drying, the cells are transferred to the process of electrolyte filling through this channel. The electrolyte filling performs in dry room. The electrolyte is injected in two times so that it can be filled easily and sufficiently. When filling, vacuum first, then inject electrolyte. After that, we repeat vacuum and vent to room pressure several times. Finally the cell is put off at room pressure, then weigh the cell in order to check the amount of electrolyte. After weighing, we seal with tape onto the filling port to prevent the cells absorbing water during storing.We store the filled cells for 24 hours at room temperature so that the electrolyte can be saturated sufficiently by the anodes and cathodes.Vocabulary:oven drying 烘烤vacuum 真空electrolyte filling 注液electrolyte 电解液room pressure 大气压filling port 注液孔storing 陈化saturated 浸润anode 正极cathode 负极Pre-charge and ball sealAt first, we place a piece of absorb cotton above the filling port to absorb the excess electrolyte. This is the first process.The second process is performing a pre-charge at 0.1C rate for 390 minutes.After the pre-charge, we take a voltage checking to the cell at once. If the voltage is lower than the standard, it needs to be re-charged.The fourth process is the ball seal. we must complete this process in 15 minutes.First, put the steel ball in the right place. Then, give pressure to it so that the steel ball can fill the filling port.In the whole process, we must make sure that the temperature and humidity are in the regular range.Finally, the process is cleaning to eliminate the electrolyte on the cell surface with acetone solvent.Vocabulary:filling port 注液孔electrolyte 电解液pre-charge 预先充电ball seal 封口voltage checking 量电压regular range 合格范围eliminate 消除acetone solvent 丙酮溶剂Aging and FormationThis is the aging room. We age cells at 35~40 Degree C for 7 days. The temperature is controlled by two heating instruments which are set at 38 Degree C. Then we transfer cells to the testing workshop. First, we check the voltage of cells with multi-meters. According to voltage, we divide the cells into acceptables and defects. Formation is done at 1.0 Capacity rate for 140 minutes to 4.2 Voltage. After that, check thickness and impedance. At last, we transfer the acceptables to the storehouse.Vocabulary:aging room 老化房heating instrument 加热器testing workshop 检测车间acceptables 良品defects 次品formation 化成thickness 尺寸,厚度impedance 内阻storehouse 仓库标识牌内容(中文) 英文1 正极球磨Cathode Ball Mill Mixing2 负极球磨Anode Ball Mill Mixing3 正极混浆Cathode Slurry Mixing4 负极混浆Anode Slurry Mixing5 正极涂布Cathode Coating6 负极涂布Anode Coating7 极片烘烤Electrode Drying 8 正极压片Cathode Compress9 负极压片Anode Compress 10 正极分大片Cathode Cutting11 正极分小片Cathode Slitting 12 负极分大片Anode Cutting13 负极分小片Anode Slitting 14 切镍带Anode Tab Cutting15 极耳铆接Anode Riveting 16 极耳贴胶纸Anode Tab Taping17 大片贴胶纸Cathode Edge Taping 18 刷片Electrode Brushing19 极耳超焊#1 Cathode Tab Welding #1装配车间英语极片烘烤Electrode Drying Area裁隔膜纸Separator Cutting壳体贴膜Out-film Apply超焊铝镍带Cathode Tab Welding贴内壁胶纸Inner Insulation Taping卷绕Jelly Roll Winding检验#1 Checking Station#1整形Jelly Roll Forming贴侧面胶纸J/R Side Taping贴上端胶纸J/R Top Taping贴底部胶纸J/R Bottom Taping装壳Jelly Roll Insertion点焊负极Anode Tab Welding剪正极耳Cathode Tab Cutting 超焊正极耳#2 Cathode Tab Welding #2二次点焊Spot Welding套隔圈Insulator Insertion甩壳Final J/R Insertion卡盖板Cap Installation检验#2 Checking Station #2点焊盖板Cap Pre—Welding激光焊接Laser Seam welding 整形Forming检验漏气Leak Checking短路测试Hi—pot称重分档Weighing Sorting。
锂离子电池技术英文词句
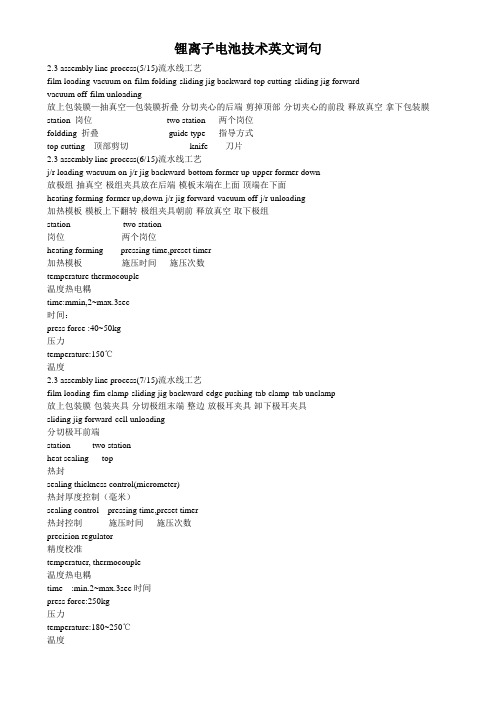
锂离子电池技术英文词句2.3 assembly line process(5/15)流水线工艺film loading-vacuum on-film folding-sliding jig backward-top cutting-sliding jig forward-vacuum off-film unloading放上包装膜—抽真空—包装膜折叠-分切夹心的后端-剪掉顶部-分切夹心的前段-释放真空-拿下包装膜station 岗位two station 两个岗位foldding 折叠guide type 指导方式top cutting 顶部剪切knife 刀片2.3 assembly line process(6/15)流水线工艺j/r loading-wacuum on-j/r jig backward-bottom former up-upper former down-放极组-抽真空-极组夹具放在后端-模板末端在上面-顶端在下面-heating forming-former up,down-j/r jig forward-vacuum off-j/r unloading加热模板-模板上下翻转-极组夹具朝前-释放真空-取下极组station two station岗位两个岗位heating forming pressing time,preset timer加热模板施压时间施压次数temperature thermocouple温度热电耦time:mmin,2~max.3sec时间:press force :40~50kg压力temperature:150℃温度2.3 assembly line process(7/15)流水线工艺film loading-fim clamp-sliding jig backward-edge pushing-tab clamp-tab unclamp-放上包装膜-包装夹具-分切极组末端-整边-放极耳夹具-卸下极耳夹具sliding jig forward-cell unloading分切极耳前端station two stationheat sealing top热封sealing thickness control(micrometer)热封厚度控制(毫米)sealing control pressing time,preset timer热封控制施压时间施压次数precision regulator精度校准temperatuer, thermocouple温度热电耦time :min.2~max.3sec时间press force:250kg压力temperature:180~250℃温度2.3 assembly line process(9/15)流水线工艺cell loading-vacuum on-sliding jig backward-side cutting-feeding-tab cutting-放上电芯-抽真空-滑动夹心后端-裁边-流入下工序-剪极耳sliding jig forward-cacuum off-cell unloaing滑动夹心前端-释放真空-取下电芯station two stationside cutting kinifeside cutting force 100kgtab cutting knifetab cutting force 100kg2.3 assembly line process(10/15)流水线工艺cell loading-sliding jig backward-vacuum pad down-open-needle down-e/l filling(e/l-needle up-needle up-vacuum pad up-sliding jig forward-cell unloadingstation two statione/l supply 3kuter sub-tank on equipmentmetering pump hi -bar pump,hbd-2bc-17accuracy; under 3.0;±0.1gocer 3.0; ±3.5g2.3 assembly line process(11/15)流水线工艺cell loading-sliding jig backward-jig backward-jig up-vacuum(vacuum chamber)-放上电芯-滑动夹心后端-夹心向后-再向上-抽真空-sealing block forward-sealing热封前端- 密封--sealing block backward-jig down-silding jig forward-cell loading-formation热封后端- 夹心翻转向下-滑动夹心前端-取下电芯-成型station two stationvacuum source 740mmhg max.vacuum pumpsealing control pressing time preset tiomerpressing force, precision regulatortemperature,thermocoupletime:min.3~max4secpress force:250kgtemperatrure:180~250℃2.3 assembly line process(12/15)流水线工艺cell loading-conveyor drive-numbering-numbering-head down-vacuum on-放上电芯- 启动传送带- 编号码-编号码-电芯朝下-抽真空head up-head forwward-head down-vacuum purge-head up-cell unloading电芯朝上- 电芯朝前- 电芯朝下-真空净化- 电芯朝上-取下电芯speed controller motor 25Wnumbering ink jet printercell unloading magacine2.3 assembly line process(13/15)流水线工艺piercing-cell loading-sliding jig backward-jig up-vacuum°assing-穿透??- 放电芯-滑动夹心后端-夹心向上- 抽真空&脱气sealing block forward-sealing-sealing block backward-jig down-sliding jig forward-cell loading热封前端- 热封–热封后端-滑动夹心前端–取电芯station two stationpiercing ∮6holevacuum source 750mmhg max.vacuum pumpsealing comtrol pressing time ,preset timerpressing force,preision regulator调整压力temperature,thermocouple(温度热电偶)time: min.3~max.4sec时间press force:250kg(压力)temperature:180~250℃(温度)2.3 assembly line process(14/15)流水线工艺cell loading-vacuum on-sliding jig backward-cutter down-cutting-cutter up-放电芯-抽真空-滑动夹心后端-切割刀具向下-切割-切割刀具向上sliding jig forward-vacuum off-cell loading滑动夹心前端- 释放真空-取下电芯电池封口--cutting(切断) knife(刀)2.3 assembly line process(15/15)流水线工艺cell loading-ist folding-2nd folding-heat pressing-3nd folding-4th folding(sicing)放电芯- 第一次折叠-第二次折叠-热压-第三次折叠-第四次折叠cell unloading取下电芯manual-loading-2st foliding-heat pressing-3nd folding-4th folding手工–放上- 第二次折叠- 热压- 第三次折叠- 第四次折叠cell transfer linear transferfolding actuator pneumatic actuatorheat pressing pressing time,preset timerpressing forceprecision regulatortemperature, thermocoupletime:min.2~max.3 secpress force:40kgtemperatrure:80~100℃2.3 assembly line process(1/6)流水线工艺jelly roll supply-jelly roll loading-cell alignment-tab straightening-提供极组-放上极组-电芯排列好-将极耳伸直sealant sealing(sealant film supply)-sealant sealing(sealant film supply)-final sealing- 密封胶密封(密封膜供给)-密封胶密封(密封膜供给)-最终的密封sealant film check-tab forming-jelly roll unloading(ng unloading)检验密封膜-极耳成型-取下极组2.3 assembly line process(2/6)流水线工艺al-foil supply-pre heating(contact)-pouch forming---pouch punch out-??—供应箔(铝塑膜???)-预热(连接)-成型成袋状- 袋状膜冲压打孔pouch loading(pouch pin hole check)-pouch loading-ist folding-lst folding-2nd folding- 放上袋状膜(检验针孔)-放上袋状膜- 第一次折叠-第二次折叠top cutting(ng unloading)-jelly roll insertion(jelly roll alignment-jelly roll loading)—剪掉顶部—插入极组(调整极组-放上极组)3nd folding-pre heat sealing-package unloading第三次折叠-预热密封—取下包好的电芯2.3 assembly line process(3/6)流水线工艺cell loading-lst top sealing--2nd top sealing-top cooling-side sealing-side cooling-放上电芯-第一次顶部密封-第二次顶部密封-顶部冷却—封边—两边冷却side cutting-short check-cell unloading-ng unloading裁边- 测短路—取下电芯—ng是什么啊???package loading-pre weighing-package opening-e/l filling(e/l dispensing e/l supply tank) 放上包装好的电芯—预称重—打开电芯--- 注液(分配电解液电解液供给罐)--lst vacuum-2nd vacuum --lst sealing-2nd sealing-plst-weighing-package unloading-第一次抽真空---第二次真空---第一次密封---第二次密封---???---称重---取下电芯package loading-package aging--formation放上电芯---电芯老化-----化成cell loader-cell-loading-piercing-vacuum°assing heat sealing-2nd sealing-装电芯设备-电芯-装上电芯—穿透(??)-抽真空& 脱气热封—第二次密封side trimming-cell unloading修边--- 取下电芯cell loading-lst folding-2nd folding-3rd folding-4th folding-5th folding(sizing)-放电芯---第一次折叠---第二次折叠---第三次折叠---第四次折叠---第五次折叠(量尺寸)5th folding(sizing)-tab cutting-height&vision check-final weighging-final weighting-第五次折叠(量尺寸)---剪极耳---检验高度&视觉---最后称重ng rejection-cell unloading-cell unloading-cell palleticing挑选,排除---取下电芯--- (用托盘)搬运电芯???1.1 assembly line specification –products流水线特殊产品can type(壳体类型) aluminum can(A3003) 铝壳(材质A3003)conventional prismatic type ,not oval type 传统的方型,不是椭圆型model of cell电池型号basic design model:xx-yy—zz基本设计型号:XX-YY-ZZ range 范围w:30~34mm t:4.0 ~10mm h:40~67mm宽:厚:高:cathode tab正极耳AL,t0.08~0.12mm,w3/4mm铝带,厚度0.08~0.12mm宽度3/4mm welding to top cap with ultrasonic welder 用超声波焊接机超焊在极片头部anode tab负极耳ni,t0.08~0.12mm,w3/4mm镍带,厚度0.08~0.12mm宽度3/4mm welding to top cap with resistance spot welder用阻抗点焊机焊在极片头部can seam welding壳盖的缝隙焊接side welding侧面焊接top insulator 顶部绝缘片injection molded注液模具bottom tape wrapping底部贴胶纸pp-tape,same as j/r wrapping tape, roll,w:28~32mmt:0.05~0.10mm o.d:200mm core id:3inchesfor xx30zz width 28mm,for xx34zz width 32mmfill port welding 补焊砂眼AL Ball (Al050,∮1.37±0.03mm),laser seam welding 激光焊接e/l filling accuracy 精确注液量under 3.0g; ±0.1gover 3.0g ±3.5g r/l filling volume:1~7g 注液量范围1~7gmodel change exchange tool,jig, carrier&tray搬运工具,夹具,搬运盒&托盘option:only carrier&tray (others:sutomatically adiusted其它:适当调整)tray托盘jr极组(256pcs),can壳(300pcs),cap盖帽(100pcs),(rivet)all trays are prepared user1.2 assembly line specification –equipment流水线特殊设备line tact time 流水线标准工时 2.0(30ppm)Drive mechanism 发动装置cam,ac servo drive&air actuatorelectrical power 电源286kva,3p-380v±10%,50hz±1hzpneumatic source 气源13300l/min,0.6mpa (include welding jig cooling包括焊接模具冷却)nitrogen gas 氮气285 l/min, 0.6mpa(for laser welding shield gas激光焊接防护气)laser cooling water激光焊冷却水320 l/min,below25℃fume collector 烟、气收集罐400cfm,explosion-proof type for al-fume,outdoor typefume suction main piping 抽气主管道系统 4 inchexhaust piping排气管道系统5inchdry air piping干燥气管道系统5inchdry chamber(total) 干燥室20.78m3total weight总重量14.8ton(approx大概),(not include laser welder不包括激光焊接机)floor load 场地负荷1500kg/m2dry room height干燥室高度2500mm(min)can seam welding壳盖的缝隙焊接side welding侧面焊接,welding speed 焊接速率10~15mm/sec.(approx) cartesian robot stageelectrolyte filling process注电解液工序40station-80 jig index unit,vacuum真空&pressurize加压elctrolyte filling range注液范围depend on internal dead space of cell design根据电池设计内部的绝对空间hbd-2bc series of hibar pum, japan hibarleak check 测漏differential pressure check system,100pa max.不同压力测试系统,最大为100pa accuracy:+/-0.5%精确度need test actual work 需要通过实际操作测量2.1 assembly parts name&compositionball-top cap assembly盖板流水线(t/c)--top insulator顶部绝缘片(t/l)-cathode正极耳(al-tab铝带)-anode负极耳(ni-tab镍带)-bottom tape底部胶纸(b/t)-jelly roll极芯(j/r)-aluminum can铝壳2.2 assembly process basic specification装配过程概述3.1 prismatic lib assembly processbottom tape底部胶纸-jelly roll insertion极芯入壳-top insulator顶部绝缘片-tab forming极耳修整-top-cap welding顶部极耳焊接-top cap folding极耳折叠-top cap setting卡极耳-seam welding焊缝焊接-leak check测漏-electrolyte filling注液-ball insertion压钢珠-fill port welding补焊砂眼(???)3.2 assembly line process(1/8)can supply供应壳non dust paper tray无尘的纸盘can tray size装壳的盘子尺寸270*212*22/32htray capacity盘子容量423048-450can/tray343450-496can/tray(suppiled by user)stack volume堆叠范围48/50h:8tray65/67h:6traycan supply供应壳体-can loading放上壳体-can check检验壳体-jelly roll loading放上极芯(ng reject-bottomtape check检验底部胶纸-bottom tape wrapping贴底部胶纸-jelly roll supply供应极芯-from winder从卷绕机)-jelly roll centering极芯放在正中央-jelly roll insertion插入极芯-insertion height check检验极芯入壳高度-ng rejectj/r supply 极芯供应tray from winder来自卷绕机的盘子j/r tray size放极芯盘子的尺寸540*540*50hj/r capacity 容纳极芯的数量48/50h:40*8=320/tray65/67h:40*6=240/tray supplied by userstack volume堆叠范围8 traytray handling盘子搬运using manual cart用手推车bottom tape底部胶纸pp tape,rollcore size标准尺寸 3 inch paper coreb/t color 底部胶纸颜色blue or green兰色或绿色b/t check 检验底部胶纸color sensor颜色传感器3.2 assembly line process(2/8)tab straightening拉直极耳—tab position check检查极耳位置—top insulator insertion插入绝缘片(t/I escapement镊子??—top insulator supply供应绝缘片)—T/I presence check检查绝缘片—tab forming极耳修整—j/r final insertion极芯入壳—t/c welding盖板焊接(ni tab镍带)—(t/c direction check检查盖板方向—top cap supply盖板供应)—al tab welding铝带超焊—cap/tab welding check检验焊接是否牢固—tab folding极耳折叠—t/csetting&check固定、检验盖板—ng rejecttop cap supply盖板供应tray from cap ass’y m/ccap tray size 装盖板盘子的尺寸340*240*18hcap capacity能装盖板的数量18*6=108 cap/traystack volume 堆叠范围24 tray(2592 cap)j/r final insertion极芯入壳include j/r insertion height check包括检验极芯入壳高度ni-tab welding焊接镍带resistance spot welding,2points阻抗点焊机,2点include welding current monitor包括焊接电流监控器al-tab welding铝带超焊ultrasonic welding超声波焊接40khx/800w/branson brandtop insulator顶部绝缘片pull check拉力测试cap height check盖板高度检验t/c setting check 检验盖板牢固性setting height check检验固定的高度3.2 assembly line process(3/8)height check#1高度检验1#—pre spot welding预点焊—height check#2高度检验2#—ng reject排除不合格品??—seam welding#1焊缝焊接1#—seam welding#2焊缝焊接2#—seam welding#3焊缝焊接3#—seam welding#4焊缝焊接4# (jig cooling模具冷却)—short check测短路—ng reject排除不合格品pre spot welding预点焊laser spot welder激光点焊机,3-points 50w/2-fiber,1system(supplied by user)height check#1 高度检验1# check the top cap setting height检查盖板固定的高度height check#2 高度检验2# check the top cap welded height检查盖板焊接高度seam welding缝隙焊接laser welder激光焊接机,10~15mm/sec,700w/2-fiber,4systemsrequire speed down for 34xxyy 对于34xxyy需减速models (prevent against overheat预防过热)supplied by userjig cooling 模具冷却vortex tube,using compressed air热交换管道,采用压缩气体air pressure 0.65mpa (minimum)气压shield gas supply保护气供应nitrogen gas,0.65mpa18/min氮气with digital flow meter数显流动仪表fume collector烟气收集罐400 cfm,1.5kw,amanl/japanexplosion proof,outdoor type户外气体排放装置short check测短路lcr meter3.2 assembly line process(4/8)vacuum out释放真空—equilibrium平衡状态—leak detection测漏—vent排除气体—ng reject排除不合格品leak check procedure测漏程序atmosphere气体—vacuum抽真空—equilibrium平衡状态—detection测漏—leaked cell漏气电芯—normal cell 正常电芯leak check测漏differential pressure,100pa max.. 不同压力测试系统,最大为100pavacuum out-100kpa max.释放真空leak detection time 8.0sec.max.测漏时间using master cell采用好的电芯accuracy:+-0.5%精确度cell handling搬运电芯8 cells,simultaneously check 8只电芯,同时检查3.2 assembly line process(5/8)pre weighing预称重—cell loading放上电芯—e/l dispensing电解液分配—vacuum/vent抽真空/排气—vacuum 抽真空—pressurize加压—vent排气—cell unloading取下电芯—post weighting快速称重—ng rejectelectrolyte supply供应电解液drum桶,200 literusing nitrogen gas使用氮气, 0.02~0.04mpasub-tank in equipment装置内的储槽,3 litermetering pump 抽吸仪表hibar pump,japan hibarhbd-2bc series*2vacuum抽真空-700mmhg,(max.-740mmhg)suction capacity抽吸泵容量310/min.r5c 0040e*02,busch/germany德国??Pressurize加压nitrogen gas氮气,0.15~0.2mpaWeighing称重load-cell,6digits,nmb/japan日本Display显示;000.00gnozzle cleaning 清洗喷嘴nitrogen gas blow out用氮气吹,0.15~0.2mpafor blow out the remained e/l 把剩余的电解液吹出来process time 工序工时128sec (max)filling accuracy 注液精确度under 3.0g;±0.1g 小于3.0g,±0.1gover 3.0g; ±3.5% 大于3.0g; ±3.5%3.2 assembly line process(8/8),al ball typecleaning paper supply供应纸巾-cap face cleaning清洁盖帽表面-cleaning paper supply供应纸巾-cap face wet cleaning盖帽表面除湿-solvent dispenser溶剂给料器-fill port cleaning清洁注液孔-cleaning paper supply供应纸巾-ball insertion钢珠插入-ball supply钢珠供应-ball press压钢珠-ball height check检验压钢珠的高度--ball seam welding钢珠缝隙焊接-welding check焊接检验-uv glue dispensing UV胶水给料-ng reject-uv curing紫外光固化????-cell unloading取下电芯cleaning paper清洁纸巾non-dust paper,roll,width 14mm无尘纸巾,卷,14mm宽3 inch paper coreballsupply钢珠供应bowl feeder钢珠进料器requies testing by the actual sample目前测试样版ball press force压力35~40kgfseam welding定位焊接方法laser seam welder,6.5mm/sec激光焊接工作350w/-fiber,1 system焊接系统(supplied by user)适当调整6.1 model change time 型号变化时间manual conversion type 46-30-48 vs 46-30-xx:6 hours approx.(only different'heieght)xx-xx-xx vs yy-yy-yy:3days6.2 delivery交货manual conversion type 7months to shipping,after l/c open6.3 customer scope 客户范围primary main power wiring to control panel of the each equipment,with main power panel.主要的电源线控制每一个设备的主电路板????Primary main pneumatic piping to beside the each equipment, with main air-filter unit.主要的气管道系统装在每个设备的旁边,主要的气体过滤器????Primary main nitrogen gas piping to beside the each equipment, with main gas -line filter unit.主要的氮气管道系统装在每个设备的旁边,主要的气体过滤器???/All duct piping for suction &exhaust from equipment's inlet/outlet to main duct.所以用于从设备上的进口/出口抽气或排气的输送管道Installation &piping/wiring/wiring for fume collector(outdoor type)给烟气收集器(户外类型)安装管道系统/配线系统Inlet/drain water piping of the washing machine,with water strainer.清洗设备的进水/排水管道,水过滤器Laser welding system &laser welder welder import/export fee激光焊接系统&激光输入/输出Cooling water piping for each laser system,below 25℃.(it requires a water filter (strainer)用于激光系统的冷却水,25℃以下(需要一个水过滤器)Cooler or chiller for laser cooling water.激光冷却水的冷却器Dry pneumatic piping for laser shutter operation to each laser system.用于每一个激光系统的激光开关操作的干燥气管道Installation&wiring/cabling for laser fiber and laser control cable.给激光光纤和激光控制电缆安装配线/电缆Installation &wiring/cabling for laser control pendant.给激光控制的悬吊物安装配线/电缆????6.4 laser system location outdoor of the dry room. It requires air-conditioning or sufficient ventilation.激光系统位于干燥间的外面。
锂电工艺流程英语
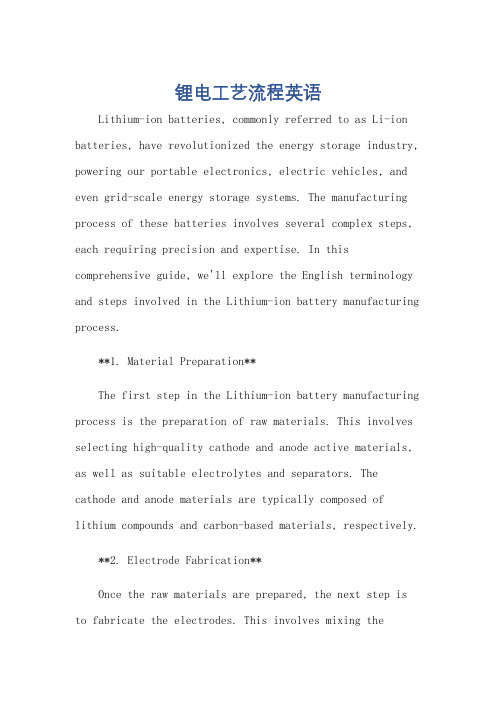
锂电工艺流程英语Lithium-ion batteries, commonly referred to as Li-ion batteries, have revolutionized the energy storage industry, powering our portable electronics, electric vehicles, and even grid-scale energy storage systems. The manufacturing process of these batteries involves several complex steps, each requiring precision and expertise. In this comprehensive guide, we'll explore the English terminology and steps involved in the Lithium-ion battery manufacturing process.**1. Material Preparation**The first step in the Lithium-ion battery manufacturing process is the preparation of raw materials. This involves selecting high-quality cathode and anode active materials, as well as suitable electrolytes and separators. The cathode and anode materials are typically composed of lithium compounds and carbon-based materials, respectively. **2. Electrode Fabrication**Once the raw materials are prepared, the next step is to fabricate the electrodes. This involves mixing theactive materials with binders and conductive additives, and then coating them onto a metal current collector. The most common metal current collectors are aluminum for the cathode and copper for the anode.**3. Electrode Drying and Cutting**After coating, the electrodes undergo a drying process to remove any moisture. Once dry, they are cut into the desired shape and size, ready for the next step in the manufacturing process.**4. Cell Assembly**Cell assembly is a crucial step, where the electrodes, electrolyte, and separator are combined to form the battery cell. The separator, typically made of porous polypropylene or polyethylene, is placed between the cathode and anode to prevent direct contact and thus, short-circuiting. The electrolyte, which is a liquid or solid material, is then added to facilitate the movement of ions between the electrodes.**5. Welding and Sealing**After assembly, the cell is sealed and welded to ensure its structural integrity and prevent leakage of the electrolyte. This step is crucial for ensuring the safety and performance of the battery.**6. Formation and Testing**The formed battery cell is then subjected to a formation process, which involves charging and discharging the cell to activate it. Following formation, the cell is tested to ensure its performance meets specifications. This testing may include capacity testing, internal resistance testing, and cycling tests.**7. Packaging and Final Testing**Once the individual cells are tested and approved, they are packaged into the final battery pack. This packaging may include additional safety features such as thermal cut-off devices and fuses. The final battery pack is then tested again to ensure it meets the required performance and safety standards.**8. Quality Control and Shipping**Quality control is an ongoing process throughout the manufacturing process. However, a final inspection is conducted before the batteries are shipped to customers. This inspection ensures that each battery meets therequired specifications and is safe for use.In conclusion, the Lithium-ion battery manufacturing process is a complex and meticulous procedure, requiring precision and expertise. Understanding the terminology and steps involved in this process is crucial for ensuring the safety, performance, and reliability of the final product. As the demand for Lithium-ion batteries continues to grow, so does the importance of understanding and improving their manufacturing processes.**锂电池生产工艺流程详解**锂电池,特别是锂离子电池(Li-ion),已彻底改变了储能行业,为便携式电子设备、电动汽车甚至电网级储能系统提供了动力。
锂电行业的常用语用英语
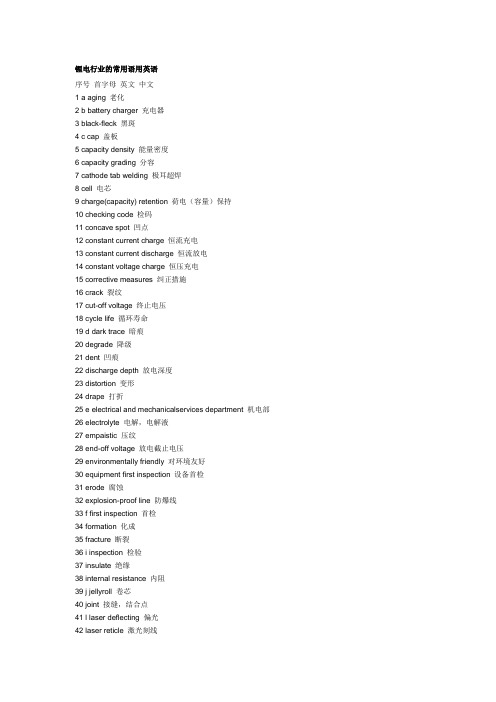
锂电行业的常用语用英语序号首字母英文中文1 a aging 老化2 b battery charger 充电器3 black-fleck 黑斑4 c cap 盖板5 capacity density 能量密度6 capacity grading 分容7 cathode tab welding 极耳超焊8 cell 电芯9 charge(capacity) retention 荷电(容量)保持10 checking code 检码11 concave spot 凹点12 constant current charge 恒流充电13 constant current discharge 恒流放电14 constant voltage charge 恒压充电15 corrective measures 纠正措施16 crack 裂纹17 cut-off voltage 终止电压18 cycle life 循环寿命19 d dark trace 暗痕20 degrade 降级21 dent 凹痕22 discharge depth 放电深度23 distortion 变形24 drape 打折25 e electrical and mechanicalservices department 机电部26 electrolyte 电解,电解液27 empaistic 压纹28 end-off voltage 放电截止电压29 environmentally friendly 对环境友好30 equipment first inspection 设备首检31 erode 腐蚀32 explosion-proof line 防爆线33 f first inspection 首检34 formation 化成35 fracture 断裂36 i inspection 检验37 insulate 绝缘38 internal resistance 内阻39 j jellyroll 卷芯40 joint 接缝,结合点41 l laser deflecting 偏光42 laser reticle 激光刻线43 laser welding-flatwise weld 激光焊接-平焊laser welding-standing weld 激光焊接-立焊44 leakage 漏液45 leak-checking 测漏46 leaving out of welding 漏焊47 limited charge voltage 充电限制电压48 local action 自放电49 m margin turnly 翘边50 measuring the dimension of cells 电芯卡尺寸51 meet requirement 达到要求52 memory effects 记忆效应53 n nick 划痕54 nominal voltage 标称电压55 notice-board confirmation 看板确认56 nugget 硬块57 o obverse 正面58 open circuit voltage 开路电压59 over charge 过充60 over discharge 过放61 over the thickness 超厚62 p particle 颗粒63 pe membrane pe膜64 pit 坑点65 placing cells into the box 电芯装盒66 point inspection 点检67 preventive measures 预防措施68 pricking the tapes 扎孔69 process inspection 制程检验70 put the battery piled up 将电芯叠放在一起71 q qualified products 合格品72 quality assurance 质量保证73 quality control 质量控制74 quality improvement 质量改进75 quality match 品质配对76 quality planning 质量策划77 r rated capacity 额定容量78 recharge 再充电79 refitting the can of cell 电芯壳口整形80 requirment 要求81 reverse 背面,反面82 rework 返工83 ringing cells into pyrocondensation films 套热缩膜84 s safety vent 安全阀85 sand aperture 砂眼86 scar 疤痕87 secondary battery 二次电池88 select appearance 选外观sharp-set 批锋89 short circuit checking 测短路90 smudginess 污物91 spot welding by laser 激光点焊92 spot welding place 点焊位置93 spraying the code 喷码94 spur 毛刺95 sticking the pvc cover boards 贴面垫96 storing 陈化97 storing with high voltage 高压储存98 t tabs deflection 极耳歪斜99 tabs excursion 极耳错位100 technics requiment 工艺要求101 u ultrasonic welding 超声波焊接102 ultrasonic welding strength 超焊强度103 unqualified products 不合格品104 w wave 波浪105 working procedure 工序Voltage:Units of measuring electrical current, all batteries are rated in volts DC. (Direct Current). This determines how much energy is needed to power your equipment.Voltage plateau:(电压平台)A slow decrease in voltage over a long period of time. As a rule, the plateau extends from the first voltage drop at the start of the discharge to the bend of the curve after which the voltage drops rapidly at the end. Nominal Voltage(标称电压)The voltage of a battery, as specified by the manufacturer, discharging at a specified rate and temperature.Working voltage(工作电压)The working voltage of a cell or battery begins at its electrical connections as soon as an electrical consumer is connected to it.Discharging voltage, average voltage (放电电压)The average discharging voltage is the average value of the discharging voltage during the entire discharging process with a related discharging current.Open circuit voltage (OCV开路电压)The voltage of a battery when there is no current flowing.Closed-Circuit Voltage (CCV闭路电压)The potential or voltage of a battery when it is discharging or charging.State of charge:The rate of charge capacity vs. whole capacity.Initial voltage(起始电压)A battery's initial voltage is the working voltage when discharging begins.End-point voltage (End voltage, Cutoff voltage, Final voltage)截止电压Specified closed circuit voltage at which a service output test is terminated.End-of-discharge voltageThe battery voltage when discharge is terminated.End-of-charge voltageThe battery voltage when charge is terminated.Cutoff voltage (V)The battery voltage at which charge or discharge is terminated.1.Self Discharge 自放电2.Uniformity of the Li-ion Batteries 锂离子电池的一致性3.steel strap 钢带4.Burst vent 防爆阀5.Filling port 注液孔6.spirally wound type cylindrical wound type 圆柱形7.foil 箔8.parallel-plate prismatic design 方形叠片式设计Ageing (老化)- Permanent loss of capacity with frequent use orthe passage of time due to unwanted irreversible chemical reactions in the cell.Anode(阳极)- The electrode in an electrochemical cell where oxidation takes place, releasing electrons. During discharge the negative electrode of the cell is the anode.During charge the situation reverses and the positive electrode of the cell is the anode.Cathode(阴极)- The electrode in an electrochemical cell where reduction takes place, gaining electrons. During discharge the positive electrode of the cell is the cathode. During charge the situation reverses andthe negative electrode of the cell is the cathode.Cycle (循环)- A single charge and discharge of a battery.Depth of discharge DOD (放电深度)- The ratio of the quantity of electricity or charge removed from a cell on discharge to its rated capacity.Internal impedance(交流内阻)- Resistance to the flow of AC current within a cell. It takes into account the capacitive effect of the plates forming the electrodes.Internal resistance (直流内阻)- Resistance to the flow of DC electric current within a cell,causing a voltage drop across the cell in closed circuit proportional to the current drain from the cell.A low internal impedance is usually required for a high rate cell.。
锂电工艺流程英语

锂电工艺流程英语The lithium-ion battery manufacturing process involves multiple intricate steps that transform raw materials into functional battery components. Here's a brief overview of the lithium-ion battery production process in English:First, raw materials, including lithium compounds, cobalt, nickel, manganese, graphite, and electrolytes, are sourced and carefully inspected to ensure they meet the required quality standards. Next, these materials undergo a meticulous preparation process, where they are mixed in precise ratios to create the cathode, anode, and electrolyte components of the battery. The cathode is typically composed of lithium-based compounds, while the anode is made of graphite or other carbon-based materials. The electrolyte, which facilitates the flow of ions between the cathode and anode, is formulated separately.After the preparation of the battery components, the next step is the assembly process. This involves coating the cathode and anode materials onto metal foils, which are then cut into thin strips called electrodes. These electrodes are stacked or wound together with separators in between to prevent direct contact, creating a cell structure.The assembled cells are then placed into a battery housing, and the electrolyte is injected into the cells. The housing is sealed tightly to prevent any leaks or contamination.Following assembly, the batteries undergo a series of testing procedures to ensure they meet performance and safety standards. This includes checking for proper voltage, capacity, and internal resistance, as well as conducting safety tests to ensure the batteries do not overheat or explode under normal operating conditions. Finally, the batteries are packaged and prepared for shipment to their end-use applications, such as portable electronic devices or electric vehicles.It's worth noting that the lithium-ion battery manufacturing process is highly automated and requires precision equipment to ensure consistent quality and safety. Additionally, the process may vary slightly depending on the specific type of lithium-ion battery being produced, such as lithium-cobalt oxide, lithium-iron phosphate, or lithium-titanate batteries.。
锂电池各车间工艺路线图

开始 Starting
配料QC Raw materials weighting QC
筛料 Materiasl bolting
烘烤 Materials drying
冷却 Materials cooling
搅拌 Materials mixturing
车间面 积 开始 start 制片
Electrode made
310 m²
着装颜 色 灰 色
对应职位
组合 Assembly
注液
流 水 线 日 产 能
2
Lines
主管、工程师
100K per day
红 黄 绿
色 色 色
品管人员 拉长 一线员工 电工、机修工
包装出货 入库 The End 分容 Chg & Dischg 储存
拉浆QC Coating QC
整片 Electrode sorting
裁小片 Slitting
修边 Electrode Edge repairing
对辊QC Thickness QC
对辊 Electrode pressing
烘烤 刮粉 裁大片 Electrode Electrode Big pieces drying Edge scratching cutting
车间面积 制片
Electrode made
3000 m²
着装颜色
对应职位
开始 start 入库 The End
组合 Assembly
流 水 线
注液 分容日 产 能 入库日 产能
2
Lines
灰 红
色 色
锂电池生产工艺流程图
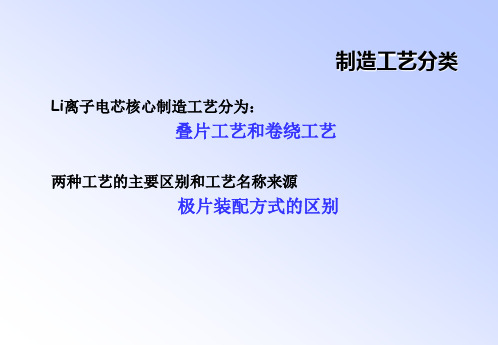
Mixing (搅拌)--与叠片工艺基本相同
工序功能:将正极或者负极粉料以及其他配料混合均匀,并调制成浆。
活性物质
导电剂
粘接剂
搅拌罐 溶剂
Mixing示意图
浆料检测点: 1.Viscosity粘度 2.Particle size颗粒度 3.Solid content固含量
卷绕工艺的主要工艺流程 ---Coating
Cold Lam (冷压)
工序功能:将Coating后的极片压实,达到合适的密度和厚度
原理:通过调节压辊的间隙以调节压 力,从而调节极片被压实的厚度和密 度
叠片工艺的主要工艺流程 --- Stacking
Stacking(叠片)
工序功能:通过手工或夹具将正极极片、隔离膜、负极 极片规则地重叠在一起。
卷绕工艺的主要工艺流程 --- Inject
Inject(注液)---与叠片工艺基本相同
工序功能:将电解液加入到电芯中,并将电芯完全封住
环境要求:电芯注液前要进行除水,关注过程要求低湿度
原理:水作为电解液中一种痕量组分,对锂离子电池SEI膜的形成 和电池性能有非常大的影响,满充状态的负极与锂金属性质相近, 可以直接与水发生反应。因此,在锂离子电池的制作过程中必须严 格控制环境的湿度和正负极材料、电解液的含水量。
卷绕工艺的主要工艺流程 --- Inject
卷绕工艺的主要工艺流程 --- Formation
Formation(预化成)---与叠片工艺原理相同,流程不同
工序功能:通过充电方式将其内部正负极物质激活, 同时在负极表面形成良好的SEI膜。 预化流程:
Formation: 0.1C CC 200min to 3.95V
预化流程:
锂电池工艺技术及流程介绍
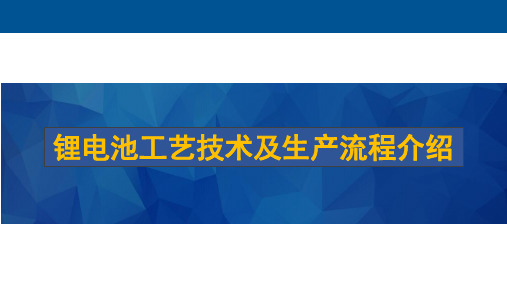
活性物质
导电剂
粘接剂
搅拌罐
溶剂
Mixing示意图
浆料控制点: 1.Viscosity粘度 2.Particle size颗粒度 3.Solid content固含量 工序控制点: 1.搅拌速度 2.搅拌温度 3.搅拌时间 4.搅拌次序
湿度≤20% 温度23±5℃ 洁净度百级
湿度≤20% 温度23±5℃ 洁净度百级
湿度-40℃露点 温度23±5℃
湿度-28℃露点 温度23±5℃
湿度-28℃露点 温度45±3℃
湿度-40℃露点 温度23±5℃
湿度-28℃露点 温度23±5℃
湿度-28℃露点 温度45±3℃
湿度-40℃露点 温度23±5℃
环境要求:电芯注液前要进行除水,关注过程要求低湿度
原理:水作为电解液中一种痕量组分,对锂离子电池SEI膜的形成和电池性能有非 常大的影响,满充状态的负极与锂金属性质相近,可以直接与水发生反应。因此, 在锂离子电池的制作过程中必须严格控制环境的湿度和正负极材料、电解液的含水 量。
工艺介绍
预化
工序功能:通过充放电方式将其内部正负极物质激活,同时在负极表面形成 良好的SEI膜。
输出控制点: 1.涂布尺寸 2.涂布重量或密度 3.膜片粘接 4.外观 5.干燥度
输入控制点: 1. 速度 2. 温度 3. 间隙(刀表) 4. 张力
Welding(焊接)
叠片工艺的主要工艺流程 --- Welding
工序功能:将多个Al、Ni 极耳一起焊接成为裸电芯
原理:超声波焊接利用超声频率(超过 16KH Z)的机械振动能量在静压力的共 同作用下,将弹性振动能量转变为工件间的摩擦功、形变能及随后有限的温升, 从而达到连接异种金属的目的。
锂电池生产工艺流程课件
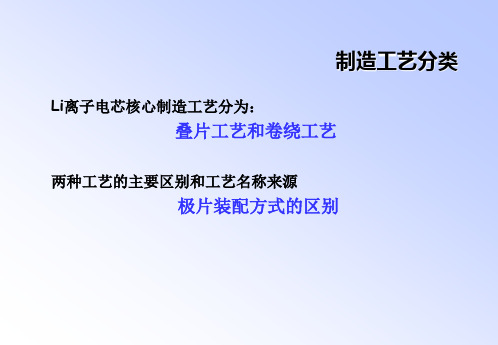
叠片工艺的主要工艺流程 --- Top sealing
叠片工艺的主要工艺流程 --- Inject
Inject(注液)
工序功能:将电解液加入到电芯中,并将电芯完全封住
环境要求:电芯注液前要进行除水,关注过程要求低湿度
原理:水作为电解液中一种痕量组分,对锂离子电池SEI膜的形成和电池性 能有非常大的影响,满充状态的负极与锂金属性质相近,可以直接与水发 生反应。因此,在锂离子电池的制作过程中必须严格控制环境的湿度和正 负极材料、电解液的含水量。
叠片工艺的主要工艺流程
---Coating
Coating示意图
输出控制点: 1.涂布尺寸 2.涂布重量或密度 3.膜片粘接 4.外观 5.干燥度
输入控制点: 1. 速度 2. 温度 3. 间隙(刀表) 4. 张力
叠片工艺的主要工艺流程
---Coating
卷绕工艺的主要工艺流程 ---Cold Lam
测试
叠片工艺物料形态流程图
叠片工艺的主要工艺流程 ---Mixing
Mixing (搅拌)
工序功能:将正极或者负极粉料以及其他配料混合均匀,并调制成浆。
活性物质
导电剂
粘接剂
搅拌罐 溶剂
Mixing示意图
浆料控制点: 1.Viscosity粘度 2.Particle size颗粒
度 3.Solid content固含
制造工艺分类
Li离子电芯核心制造工艺分为:
叠片工艺和卷绕工艺
两种工艺的主要区别和工艺名称来源
极片装配方式的区别
Part A:叠片工艺的主要工艺流程介绍
叠片工艺的定义
叠片工艺是将正极、负极切成小片与隔离膜叠合成小电芯单体,然后将 小电芯单体叠放并联起来组成一个大电芯的一种Li离子电芯制造工艺。
锂电工序英文名称
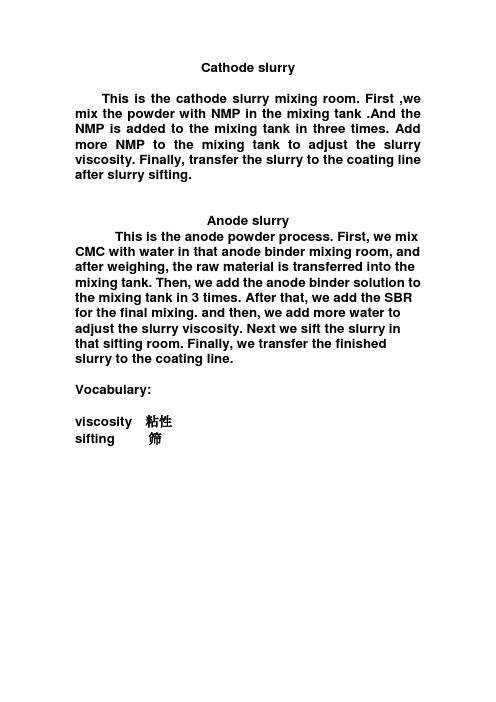
Cathode slurryThis is the cathode slurry mixing room. First ,we mix the powder with NMP in the mixing tank .And the NMP is added to the mixing tank in three times. Add more NMP to the mixing tank to adjust the slurry viscosity. Finally, transfer the slurry to the coating line after slurry sifting.Anode slurryThis is the anode powder process. First, we mix CMC with water in that anode binder mixing room, and after weighing, the raw material is transferred into the mixing tank. Then, we add the anode binder solution to the mixing tank in 3 times. After that, we add the SBR for the final mixing. and then, we add more water to adjust the slurry viscosity. Next we sift the slurry in that sifting room. Finally, we transfer the finished slurry to the coating line.Vocabulary:viscosity 粘性sifting 筛CoatingNow, we are in coating line. We use back reverse coating. This is the slurry-mixing tank. The anode (Cathode)slurry is introduced to the coating header by pneumaticity from the mixing tank. The slurry is coated uniformly on the copper foil, then the solvent is evaporated in this oven. There are four temperature zones, they are independently controlled. Zone one sets at 55 degree C, zone two sets at 65 degree C, zone three sets at 80 degree C, zone four sets at 60 degree C. The speed of coating is 4 meters per minute.You see the slurry is dried. The electrode is wound to be a big roll and put into the oven. The time is more than 2 hours and temperature is set at 60 degree C.Throughout the coating, we use micrometer to measure the electrode thickness per about 15 minutes. We do this in order to keep the best consistency of the electrode. Vocabulary:coating line 涂布车间back reverse coating 辊涂coating header 涂布机头Al/copper foil 铝/铜箔degree C 摄氏度temperature zones 温区wind to be a(big)roll 收卷evenly/uniformly 均匀oven 烘箱evaporate 蒸发electrode 极片ElectrodeAfter coating we compress the electrode with this cylindering machine at about 7meters per minute. Before compress we clean the electrode with vacuum and brush to eliminate any particles. Then the compressed electrode is wound to a big roll. We use micrometer to measure the compressed electrode thickness every 10 minutes. After compressing we cut the web into large pieces. We tape the cathode edge to prevent any possible internal short. The large electrode with edge taped is slit into smaller pieces. This is ultrasonic process that aluminum tabs are welded onto cathodes using ultrasonic weld machine. We tape the weld section to prevent any possible internal short. And finally, we clean the finished electrodes with vacuum and brush.Vocabulary:cylindering 柱形辊压vacuum 真空particle 颗粒wound 旋紧卷绕micrometer 千分尺internal short 内部短路slit 分切ultrasonic 超声波weld 焊接Anode makingIn anode making process, we cut the nickel roll into certain length strips. At the mean time, we put a small piece of insulation tape to the tab in order to prevent any possible internal short. Then the prepared nickel tab isriveted on anode and pat plain. We also tape the rivet section to prevent any possible internal short. And finally, we clean the finished electrodes with vacuum and brush.Jelly rollThis is Jelly roll, a manual winding process. In the course of Jelly roll, firstly, we place the separator in between central pins, press the foot switch to turn central pins about 120 degrees. Secondly, place the anode to the edge of central pins, and turn central pins about 180 degrees. Lastly, place the cathode to the edge of central pins. During the winding process, we apply tension by pressing the electrodes and the separator. We put the termination tape at the end.After Jelly roll, we check the short circuit, then form the Jelly roll by pressing, so that it is easier to insert the Jelly roll into the can.Control points:1. When winding to the end of the anode, covering the anode completely by the separator.2. In the whole process, it is the most important points to ensure the best alignment among the cathode, the anode and the separator for the Jelly roll. The separator has to cover the anode and the cathode, and the anode has to cover the cathode completely. These points are mainly checked before short checking.Vocabulary:Jelly roll 卷绕Manual 手工的Separator 隔膜纸central pin 卷针foot switch 脚踏开关anode 负极片cathode 正极片termination tape 尾端胶纸short circuit 短路alignment 整齐Taping&insertingPut the tape on the two side of J/R, To prevent J/R being hurt in the insertion process.Put a piece of tape between cathode tab andJ/R .Because anode electrode is wider than cathode electrode.Put the bottom tape.Insert the finished J/R into the can manually and then short circuit check by multi-meter.Spot welding Ni tab to cap.Ultrasonic welding the Al tab to cap using ultrasonic weld.We have the second spot welding to ensure the best contact between the tab and cap.Apply top insulator, to prevent Ni tab contacting with can.Final J/R insertion by the centrifuge.Cap positioning by hand. Then check the cap in the suitable position, or the defects is put into red bin ,Finally , short circuit check again to ensure that there be no internal short J/R flowing to next line.Vocabulary:J/R 极芯tape 胶纸electrode 极片multi-meter 万用表Spot welding 点焊Ni tab 极耳Ultrasonic weld 超焊Insulator 隔圈centrifuge machine 甩壳机defect 次品red bin 红盒Laser weldingThis is the Laser welding room! The first process is welding for the aluminum cap, specially connect the rivet with the weld plate to prevent the cell impedance excursion.The second process is the Laser seam welding. In the process, it must ensure the intensity and airproof characters of the weld.After the cell is welded, we would perform the leak checking, the short circuit checking and the weighing checking.Vocabulary:Laser welding room 激光焊接车间Cap 盖板Rivet 铆钉Plate 镍片impedance excursion 内阻漂移intensity 强度leak checking 检漏short circuit checking 测短路weighing checking 称重Oven drying electrolyte filling and storingThis is the process of cells oven drying at 80℃for more than 12 hours under vacuum. After oven drying, the cells are transferred to the process of electrolyte filling through this channel. The electrolyte filling performs in dry room. The electrolyte is injected in two times so that it can be filled easily and sufficiently. When filling, vacuum first, then inject electrolyte. After that, we repeat vacuum and vent to room pressure several times. Finally the cell is put off at room pressure, then weigh the cell in order to check the amount of electrolyte. After weighing, we seal with tape onto the filling port to prevent the cells absorbing water during storing.We store the filled cells for 24 hours at room temperature so that the electrolyte can be saturated sufficiently by the anodes and cathodes.Vocabulary:oven drying 烘烤vacuum 真空electrolyte filling 注液electrolyte 电解液room pressure 大气压filling port 注液孔storing 陈化saturated 浸润anode 正极cathode 负极Pre-charge and ball sealAt first, we place a piece of absorb cotton above the filling port to absorb the excess electrolyte. This is the first process.The second process is performing a pre-charge at 0.1C rate for 390 minutes.After the pre-charge, we take a voltage checking to the cell at once. If the voltage is lower than the standard, it needs to be re-charged.The fourth process is the ball seal. we must complete this process in 15 minutes.First, put the steel ball in the right place. Then, give pressure to it so that the steel ball can fill the filling port.In the whole process, we must make sure that the temperature and humidity are in the regular range.Finally, the process is cleaning to eliminate the electrolyte on the cell surface with acetone solvent.Vocabulary:filling port 注液孔electrolyte 电解液pre-charge 预先充电voltage checking 量电压ball seal 封口regular range 合格范围eliminate 消除acetone solvent 丙酮溶剂Aging and FormationWelcome! I am the owner! This is the high temperature aging room. Because the temperature is very high, Let’s go out and I will introduce it. We age the cells at 35~40 Degree Celsius for 7 days. The temperature is controlled by two heating units. Then we transfer the cells to the testing workshop.Let me introduce the next process. First, we check the volt of cells with multi-meters over there. In this process we must ensure the multi-meters can normally work. Then we charge the cells at 1 C rate to 4.2.V olt. According to capacity, we divide the cells into 7 grades --A0、A1、A2、A3、B、D、E。
中英文对照PCB生产流程常用术语

中英文对照PCB生产流程常用术语A. 开料( Cut Lamination)a-1 裁板( Sheets Cutting)a-2 原物料发料(Panel)(Shear material to Size)B. 钻孔(Drilling)b-1 内钻(Inner Layer Drilling )b-2 一次孔(Outer Layer Drilling )b-3 二次孔(2nd Drilling)b-4 雷射钻孔(Laser Drilling )(Laser Ablation )b-5 盲(埋)孔钻孔(Blind & Buried Hole Drilling)C. 干膜制程( Photo Process(D/F))c-1 前处理(Pretreatment)c-2 压膜(Dry Film Lamination)c-3 曝光(Exposure)c-4 显影(Developing)c-5 蚀铜(Etching)c-6 去膜(Stripping)c-7 初检( Touch-up)c-8 化学前处理,化学研磨( Chemical Milling )c-9 选择性浸金压膜(Selective Gold Dry Film Lamination) c-10 显影(Developing )c-11 去膜(Stripping )Developing , Etching & Stripping ( DES )D. 压合Laminationd-1 黑化(Black Oxide Treatment)d-2 微蚀(Microetching)d-3 铆钉组合(eyelet )d-4 叠板(Lay up)d-5 压合(Lamination)d-6 后处理(Post Treatment)d-7 黑氧化( Black Oxide Removal )d-8 铣靶(spot face)d-9 去溢胶(resin flush removal)E. 减铜(Copper Reduction)e-1 薄化铜(Copper Reduction)F. 电镀(Horizontal Electrolytic Plating)f-1 水平电镀(Horizontal Electro-Plating) (Panel Plating) f-2 锡铅电镀( Tin-Lead Plating ) (Pattern Plating)f-3 低于1 mil ( Less than 1 mil Thickness )f-4 高于1 mil ( More than 1 mil Thickness)f-5 砂带研磨(Belt Sanding)f-6 剥锡铅( Tin-Lead Stripping)f-7 微切片( Microsection)G. 塞孔(Plug Hole)g-1 印刷( Ink Print )g-2 预烤(Precure)g-3 表面刷磨(Scrub)g-4 后烘烤(Postcure)H. 防焊(绿漆/绿油): (Solder Mask)h-1 C面印刷(Printing Top Side)h-2 S面印刷(Printing Bottom Side)h-3 静电喷涂(Spray Coating)h-4 前处理(Pretreatment)h-5 预烤(Precure)h-6 曝光(Exposure)h-7 显影(Develop)h-8 后烘烤(Postcure)h-9 UV烘烤(UV Cure)h-10 文字印刷( Printing of Legend )h-11 喷砂( Pumice)(Wet Blasting)h-12 印可剥离防焊(Peelable Solder Mask)I . 镀金Gold platingi-1 金手指镀镍金( Gold Finger )i-2 电镀软金(Soft Ni/Au Plating)i-3 浸镍金( Immersion Ni/Au) (Electroless Ni/Au)J. 喷锡(Hot Air Solder Leveling)j-1 水平喷锡(Horizontal Hot Air Solder Leveling)j-2 垂直喷锡( Vertical Hot Air Solder Leveling)j-3 超级焊锡(Super Solder )j-4. 印焊锡突点(Solder Bump)K. 成型(Profile)(Form)k-1 捞型(N/C Routing ) (Milling)k-2 模具冲(Punch)k-3 板面清洗烘烤(Cleaning & Backing)k-4 V型槽( V-Cut)(V-Scoring)k-5 金手指斜边( Beveling of G/F)L. 开短路测试(Electrical Testing) (Continuity & Insulation Testing) l-1 AOI 光学检查( AOI Inspection)l-2 VRS 目检(Verified & Repaired)l-3 泛用型治具测试(Universal Tester)l-4 专用治具测试(Dedicated Tester)l-5 飞针测试(Flying Probe)M. 终检( Final Visual Inspection)m-1 压板翘( Warpage Remove)m-2 X-OUT 印刷(X-Out Marking)m-3 包装及出货(Packing & shipping)m-4 目检( Visual Inspection)m-5 清洗及烘烤( Final Clean & Baking)m-6 护铜剂(ENTEK Cu-106A)(OSP)m-7 离子残余量测试(Ionic Contamination Test )(Cleanliness Test)m-8 冷热冲击试验(Thermal cycling Testing)m-9 焊锡性试验( Solderability Testing )N. 雷射钻孔(Laser Ablation)N-1 雷射钻Tooling孔(Laser ablation Tooling Hole)N-2 雷射曝光对位孔(Laser Ablation Registration Hole)N-3 雷射Mask制作(Laser Mask)N-4 雷射钻孔(Laser Ablation)N-5 AOI 检查及VRS ( AOI Inspection & Verified & Repaired) N-6 Blaser AOI (after Desmear and Microetching)N-7 除胶渣(Desmear)N-8 微蚀(Microetching )流程简介:开料Cut Lamination--钻孔Drilling--干膜制程Photo Process(D/F)--压合Lamination--减铜Copper Reduction--电镀Horizontal Electrolytic Plating--塞孔Plug Hole--防焊(绿漆/绿油)SolderMask--镀金Gold plating--喷锡Hot Air Solder Leveling--成型Profile--开短路测试ElectricalTesting--终检Final Visual Inspectionpcb电路板又称印制电路板、印刷线路板,简称印制板,英文简称PCB(printed circuit board )或PWB(printed wiring board),以绝缘板为基材,切成一定尺寸,其上至少附有一个导电图形,并布有孔(如元件孔、紧固孔、金属化孔等),用来代替以往装置电子元器件的底盘,并实现电子元器件之间的相互连接。
锂电池包装车间工艺流程

锂电池包装车间工艺流程英文回答:The process flow of lithium battery packaging in the workshop involves several steps to ensure the safe and efficient packaging of the batteries. Here is a detailed explanation of the process flow:1. Battery Inspection: Before packaging, the batteries need to go through a thorough inspection to check for any defects or damages. This includes checking the voltage, capacity, and overall condition of each battery. Any batteries that fail the inspection will be rejected andsent for further analysis or disposal.2. Battery Sorting: Once the batteries pass the inspection, they are sorted based on their specifications and requirements. This includes sorting them by size, voltage, and capacity. The sorting process helps in organizing the batteries for the subsequent packaging steps.3. Cell Wrapping: The next step is to wrap each individual battery cell with a protective layer. This layer acts as a barrier against moisture, dust, and other external factors that could potentially damage the battery. The wrapping process involves using a heat-sealing machine to securely wrap the battery cells.4. Battery Assembly: After wrapping, the battery cells are assembled into battery packs. This involves connecting the cells together in a series or parallel configuration, depending on the desired voltage and capacity of the final battery pack. The assembly process requires precision and accuracy to ensure the proper functioning of the battery pack.5. Battery Enclosure: Once the battery pack is assembled, it is enclosed in a protective casing. The casing provides additional protection to the battery pack and helps in preventing any external damage. The enclosure process involves placing the battery pack into a pre-designed casing and securing it with screws or clips.6. Labeling and Packaging: The final step in the process is to label and package the battery packs. Each battery pack is labeled with important information such as voltage, capacity, and safety warnings. The packs are then carefully packaged in boxes or cartons, ready for shipment or distribution.中文回答:锂电池包装车间的工艺流程包括多个步骤,以确保电池的安全有效地进行包装。
干货丨锂电池pack工序知识
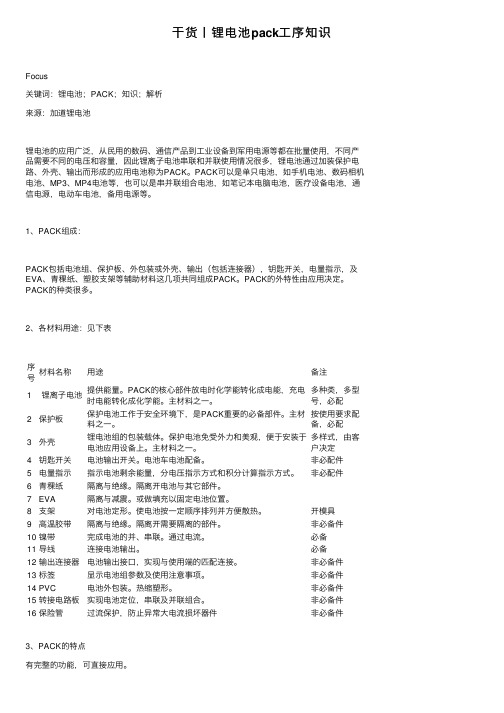
⼲货⼁锂电池pack⼯序知识Focus关键词:锂电池;PACK;知识;解析来源:加道锂电池锂电池的应⽤⼴泛,从民⽤的数码、通信产品到⼯业设备到军⽤电源等都在批量使⽤,不同产品需要不同的电压和容量,因此锂离⼦电池串联和并联使⽤情况很多,锂电池通过加装保护电路、外壳、输出⽽形成的应⽤电池称为PACK。
PACK可以是单只电池,如⼿机电池、数码相机电池、MP3、MP4电池等,也可以是串并联组合电池,如笔记本电脑电池,医疗设备电池,通信电源,电动车电池,备⽤电源等。
1、PACK组成:PACK包括电池组、保护板、外包装或外壳、输出(包括连接器),钥匙开关,电量指⽰,及EVA、青稞纸、塑胶⽀架等辅助材料这⼏项共同组成PACK。
PACK的外特性由应⽤决定。
PACK的种类很多。
2、各材料⽤途:见下表序号材料名称⽤途备注1锂离⼦电池提供能量。
PACK的核⼼部件放电时化学能转化成电能,充电时电能转化成化学能。
主材料之⼀。
多种类,多型号,必配2保护板保护电池⼯作于安全环境下,是PACK重要的必备部件。
主材料之⼀。
按使⽤要求配备,必配3外壳锂电池组的包装载体。
保护电池免受外⼒和美观,便于安装于电池应⽤设备上。
主材料之⼀。
多样式,由客户决定4钥匙开关电池输出开关。
电池车电池配备。
⾮必配件5电量指⽰指⽰电池剩余能量,分电压指⽰⽅式和积分计算指⽰⽅式。
⾮必配件6青稞纸隔离与绝缘。
隔离开电池与其它部件。
7EVA隔离与减震。
或做填充以固定电池位置。
8⽀架对电池定形。
使电池按⼀定顺序排列并⽅便散热。
开模具9⾼温胶带隔离与绝缘。
隔离开需要隔离的部件。
⾮必备件10镍带完成电池的并、串联。
通过电流。
必备11导线连接电池输出。
必备12输出连接器电池输出接⼝,实现与使⽤端的匹配连接。
⾮必备件13标签显⽰电池组参数及使⽤注意事项。
⾮必备件14PVC电池外包装。
热缩塑形。
⾮必备件15转接电路板实现电池定位,串联及并联组合。
⾮必备件16保险管过流保护,防⽌异常⼤电流损坏器件⾮必备件3、PACK的特点有完整的功能,可直接应⽤。
锂电工艺流程

锂电生产工艺流程
叠片电池流程:
物料确认、称重→粉料烘烤→混料→涂布→极片辊压→分切→极片烘烤→叠片→点焊(包括预焊、焊极耳)→贴胶带→测短路→套壳→顶、侧封→测短路→贴膜→烘烤→注液→封口→老化→一次整形(稍压)→预充→老化→化成(二次充电)→测内阻、电压→抽气二封→贴条形码→分容→测试(OCV1、OCV2)
卷绕电池流程:
物料确认、称重→粉料烘烤→混料→涂布→极片辊压→分切→极片烘烤→点焊(包括焊极耳、贴胶纸)→卷绕→平压→套壳→顶、侧封→测短路→贴膜→烘烤→注液→封口→老化→一次整形(稍压)→预充→老化→化成(二次充电)→测内阻、电压→抽气二封→贴条形码→分容→测试(OCV1、OCV2)。
- 1、下载文档前请自行甄别文档内容的完整性,平台不提供额外的编辑、内容补充、找答案等附加服务。
- 2、"仅部分预览"的文档,不可在线预览部分如存在完整性等问题,可反馈申请退款(可完整预览的文档不适用该条件!)。
- 3、如文档侵犯您的权益,请联系客服反馈,我们会尽快为您处理(人工客服工作时间:9:00-18:30)。
锂电生产车间工序名称英文翻译
正极搅拌 Cathode mixing
负极搅拌 Anode mixing
涂布车间 coating workshop
正极涂布 Cathode coating
负极涂布 Anode Coating
辊压车间 Roll workshop
正极辊压 Cathode roll
负极辊压 anode roll
成品仓库 Finished product warehouse
激光点焊室 laser welding room
烘烤室 Baking Room
化成室 Kasei Room
分容室 Sub-capacity Room
生产部 Production Department
品质部 Quality Department
技术研发部 technology room
试验室 Laboratory
装配车间 Assembly shop
注液室 injecting electrolyte room
封口室 sealing room
培训室 Training room
采购部 Purchasing Department
设备管理部 equipment department
高压危险 High-voltage danger
节约用水 economize for water
节药用电economize for electricity
卫生间 toilet
男更衣室change room for men
女更衣室change room for women
正极点焊 Cathode Welding
负极点焊 Anode Welding
正极贴胶Cathode Sticking Tape
负极压极耳Anode Tab Pressing
正极压极耳Cathode Tab Pressing
负极压极耳Anode Tab Pressing
正极压极耳Cathode Tab Pressing
正极折极耳 Cathode Folding
负极折极耳 Anode Folding
负极刷粉Anode Cleaning
正极刷粉 Cathode Cleaning
备胶 Preparing Tape
卷绕 Winding
冷压 Cold Pressing
平压测短路 Short Testing
分切 Slitting
冲压成型Press for Forming
剪极耳 Tab Cutting
裁极耳 Tab Shearing
断切隔膜 Separator Cutting
贴PET膜 PET Sticking
切边 Side Cutting
热压 Hot Pressing
检验合格区 Qualified Area
断切 Cutting
顶侧封 Top--side Sealing
极耳测测短路Tap Short Circuit Testing 贴保护膜 Film Sticking
套PET膜 PET-Wrapping
扩口 Opening
装篮 Installing
注液 Injecting Electrolyte
静置 Standb
真空封装 Vaccum Sealing
二次封装 Second Sealing
切边 Side Cutting
切极耳 Tab Cutting
点焊 Welding
贴顶侧封胶Sticking Top Tape
折边 Folding
烫边 Smothing
备料 Material Prepairing
压边 Side Pressing
极耳放置区 Tab Area
拉力测试 Power Testing
首件The First Prduct
首检 The First Ispection
自动切边 Auto Cutting
擦边 Sidewipe
刮边 Scraping Film
贴双面胶 Sticking Double-Tape
检外观 Appearance Inspection
测电阻 Impedance Check
测电压 Valtage Check
卡厚 Measure Thickness
卡宽 Measure Width
喷码 Spouting
测内阻 Resistance Check
撕膜 Separator Tearing
卡长 Measure Length
包胶 Sticking Tape
备胶 Prepairing Tape
套热缩管 Tube Setting
复检工位 Recheck
标准工位 Standard Operate
半自动卷绕 Half-auto Winding
电芯全检 Full Check
压芯 Cell Pressing
包底胶Sticking Bottom Tape
包上胶Sticking Top Tape
上隔圈Separator Ring Installing
入壳、测短路 Short Testing
点负极盖板Welding Anode Board 点正极盖板Welding Cathode Board 离芯 Cell Disjoining。