现代设计方法
现代设计方法应用

现代设计方法应用
现代设计方法是指结合先进技术和设计思维的方法论,旨在更好地满足人们的需求,提高产品和服务的质量和可靠性。
现代设计方法的应用包括以下几个方面:
1. 用户体验设计:以用户为中心,通过调研、分析、测试等方法,设计用户喜欢和能够使用的产品和服务。
2. 人机交互设计:通过人机交互技术,实现用户与设备之间信息传递的有效交互,提高用户满意度和产品使用率。
3. 可持续设计:结合环保理念,利用新材料、新工艺等手段,设计出更加环保和可持续的产品和服务。
4. 创新设计:通过创新思维方法,突破传统设计思路,探索新产品和服务的可能性,推动企业持续发展。
5. 敏捷设计:迅速响应市场变化,快速设计出符合市场需求的产品和服务,提高企业竞争力。
6. 多样化设计:为了适应不同人群的需求,设计出多样化的产品和服务,满足用户不同的个性化需求。
总之,现代设计方法的应用可以帮助企业更好地理解和满足用户需求,提高产品和服务的品质和竞争力。
现代设计方法

现代设计方法现代设计方法是随着当代科学技术的飞速发展和计算机技术的广泛应用而在设计领域发展起来的一门新兴的多元交叉学科。
以满足市场产品的质量、性能、时间、成本、价格综合效益最优为目的,以计算机辅助设计技术为主体,以知识为依托,以多种科学方法及技术为手段,研究、改进、创造产品和工艺等活动过程所用到的技术和知识群体的总称。
1.并行设计2.虚拟设计3.绿色设计4.可靠性设计5.智能优化设计6.计算机辅助设计7.动态设计8.模块化设计9.计算机仿真设计10.人机学设计11.摩擦学设计12.疲劳设计13.反求设计14.无障碍设计15.共用性设计一、并行设计并行设计是一种对产品及其相关过程(包括设计制造过程和相关的支持过程)进行并行和集成设计的系统化工作模式。
强调产品开发人员一开始就考虑产品从概念设计到消亡的整个生命周期里的所有相关因素的影响,把一切可能产生的错误、矛盾和冲突尽可能及早地发现和解决,以缩短产品开发周期、降低产品成本、提高产品质量。
并行设计作为现代设计理论及方法的范畴,目前已形成的并行设计方法基本上可以分为两大类:基于人员协同和集成的并行化。
基于信息、知识协同和集成的并行化。
并行工程应用于整车项目开发案例研究一般地,汽车整车产品开发共有4个大的阶段,即策划阶段、设计阶段、样品试制阶段和小批试制阶段。
以模、夹具的开发为例,运用并行工程,其与车身工程设计几乎同时进行,从整个计划第4个月开始介入,在整个开发周期的第22个月完成。
而运用串行工程,其在车身工程设计完成后进行,从整个计划第15个月才介入,在整个开发周期的第34个月才完成。
运用并行工程开发时间上节约近36%,整个产品开发周期可以缩短40%~50%。
设计部门不断预发布、评审、输出,相关部门评审、验证意见和建议不断反馈,然后设计不断更改,通过预发布和设计评审、修改若干个循环,这样可以把不必要的失误和不足消灭在设计阶段,同时优化设计。
在各系统设计输出评审的时候,相关部门的意见至关重要。
现代设计方法

现代设计方法现代设计方法是指在当代设计领域中所采用的一系列创新方法和技术,以解决现实问题、提高效率和用户体验的设计理念和方法。
现代设计方法主要包括以下几个方面:1. 用户研究与需求分析:现代设计方法强调从用户角度出发,通过深入研究用户需求和行为,以获取对用户真实需求的洞见。
这可以通过用户观察、访谈、调查等方法来实现,从而为设计过程提供有力的参考和指导。
2. 全周期设计思维:现代设计方法强调整个设计过程的全周期性,从项目的启动到最终的交付和使用,要全程关注用户需求、功能实现和用户体验等方面。
同时,还要与多个相关方进行合作与协调,实现设计的全面性和协同性。
3. 迭代设计与快速原型:现代设计方法注重通过不断的测试和验证,不断优化和完善设计方案。
设计师可以利用快速原型工具和技术,快速制作出初步的产品原型,并与用户进行交互和反馈,从而及时发现问题和改进设计。
4. 基于数据的设计决策:现代设计方法强调基于数据和证据进行决策,通过数据分析和用户反馈来评估设计方案的成功与否。
这种方法可以帮助设计师做出更加科学和准确的决策,提高设计的效果和质量。
5. 跨学科与跨界合作:现代设计方法鼓励不同领域和背景的专业人士之间的合作与交流,通过跨学科的思维和跨界的创新,融合不同的观点和经验,以创造出更具有创新性和综合性的设计方案。
6. 可持续设计与社会责任:现代设计方法将可持续发展和社会责任融入到设计过程中,注重设计的环境友好性、社会影响和人类福祉。
设计师需要考虑产品的生命周期、材料的可再生性、资源的节约利用等方面,以减少对环境的负面影响。
以上是现代设计方法的一些基本内容,这些方法的应用可以帮助设计师更好地满足用户需求,提高设计效果和用户体验。
随着科技的不断发展和社会的不断进步,现代设计方法也在不断创新和演变,为设计领域带来更多的可能性和机遇。
“现代设计方法”教案讲义

“现代设计方法”教案讲义
一、课程介绍
现代设计方法是一门重要的社会科学门类,旨在培养学生掌握现代设
计方法的基本理论、思想和方法,实践现代设计方法在设计实践中的应用,掌握当今国际设计理论及其发展动态,以及对多元文化融合理解和设计技
术应用。
二、教学目标
1.通过理论和实践的训练,培养学生在现代设计方法领域的专业知识
和实践能力。
2.让学生理解多元文化融合与设计相关的理论和技术,掌握设计实践
的原理及其应用,掌握当今国际设计理论及其发展动态。
三、教学大纲
1.现代设计理论基础知识
(2)现代设计理论的特点:
现代设计方法强调的特点为简约、极简和模式化。
它以简约美学为基础,把设计从繁琐的装饰中剥离出来,更注重构思良好的空间结构,注重
功能效率和实用性;还要求以模式化、系统化的方式来表达空间。
2.现代设计实践方法
(1)现代设计实践的内容:。
现代化设计方法的典型案例

现代化设计方法的典型案例随着科技的不断发展,现代化设计方法在各个领域得到了广泛应用。
这些方法旨在提高设计效率、优化设计质量,并降低设计成本。
本文将介绍几个典型的现代化设计方法,并分析其在实际应用中的效果。
一、数字化设计数字化设计是现代化设计方法中最常见的一种,它通过计算机辅助设计(CAD)软件来实现。
CAD软件能够快速、准确地完成设计任务,提高设计精度和效率。
数字化设计的典型案例包括汽车、飞机、建筑等领域的设计。
例如,在汽车设计中,数字化设计使得汽车零部件的制造精度和效率得到了显著提高,同时也降低了制造成本。
二、人工智能辅助设计人工智能技术的发展为设计领域带来了革命性的变革。
人工智能辅助设计(AI-Design)通过机器学习、深度学习等技术,能够自动识别设计问题、生成解决方案,并不断优化。
这种方法的典型案例包括智能家居、智能交通、智能医疗等领域的设计。
例如,在智能家居设计中,人工智能辅助设计能够自动识别家居环境中的各种因素,并据此进行智能化的控制和调节,提高家居生活的舒适度和便利性。
三、绿色设计随着环保意识的不断提高,绿色设计已成为现代化设计方法的重要组成部分。
绿色设计旨在降低产品设计对环境的影响,包括减少能源消耗、降低废弃物排放等。
绿色设计的典型案例包括电子产品、建筑材料等领域的设计。
例如,在电子产品设计中,绿色设计能够降低产品的能耗和废弃物排放,提高产品的可持续性和环保性。
四、模块化设计模块化设计是一种将复杂产品分解为多个可重复使用的模块的设计方法。
这种方法的优点在于能够降低设计成本、提高生产效率,同时也有利于产品的升级和扩展。
模块化设计的典型案例包括智能硬件、可穿戴设备等领域的设计。
例如,在可穿戴设备设计中,模块化设计能够将不同的功能模块进行组合和替换,以满足不同用户的需求,提高产品的灵活性和适应性。
综上所述,现代化设计方法在各个领域的应用已经取得了显著的成效。
数字化设计提高了设计的精度和效率;人工智能辅助设计为设计领域带来了革命性的变革;绿色设计降低了产品设计对环境的影响;模块化设计则有利于产品的升级和扩展。
常用现代设计10大方法
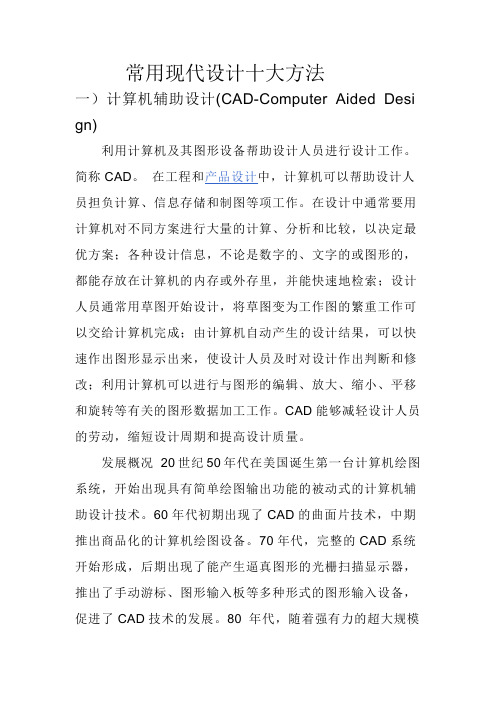
常用现代设计十大方法一)计算机辅助设计(CAD-Computer Aided Desi gn)利用计算机及其图形设备帮助设计人员进行设计工作。
简称CAD。
在工程和产品设计中,计算机可以帮助设计人员担负计算、信息存储和制图等项工作。
在设计中通常要用计算机对不同方案进行大量的计算、分析和比较,以决定最优方案;各种设计信息,不论是数字的、文字的或图形的,都能存放在计算机的内存或外存里,并能快速地检索;设计人员通常用草图开始设计,将草图变为工作图的繁重工作可以交给计算机完成;由计算机自动产生的设计结果,可以快速作出图形显示出来,使设计人员及时对设计作出判断和修改;利用计算机可以进行与图形的编辑、放大、缩小、平移和旋转等有关的图形数据加工工作。
CAD能够减轻设计人员的劳动,缩短设计周期和提高设计质量。
发展概况20世纪50年代在美国诞生第一台计算机绘图系统,开始出现具有简单绘图输出功能的被动式的计算机辅助设计技术。
60年代初期出现了CAD的曲面片技术,中期推出商品化的计算机绘图设备。
70年代,完整的CAD系统开始形成,后期出现了能产生逼真图形的光栅扫描显示器,推出了手动游标、图形输入板等多种形式的图形输入设备,促进了CAD技术的发展。
80 年代,随着强有力的超大规模集成电路制成的微处理器和存储器件的出现,工程工作站问世,cad技术在中小型企业逐步普及。
80 年代中期以来,C AD技术向标准化、集成化、智能化方向发展。
一些标准的图形接口软件和图形功能相继推出,为CAD 技术的推广、软件的移植和数据共享起了重要的促进作用;系统构造由过去的单一功能变成综合功能,出现了计算机辅助设计与辅助制造联成一体的计算机集成制造系统;固化技术、网络技术、多处理机和并行处理技术在CAD中的应用,极大地提高了C AD系统的性能;人工智能和专家系统技术引入CAD,出现了智能CAD技术,使CAD系统的问题求解能力大为增强,设计过程更趋自动化。
《现代设计方法》教学大纲

《现代设计方法》教学大纲一、课程概述:二、课程目标:1.熟悉现代设计方法的概念和发展历程。
2.掌握现代设计方法的基本理论和实践技巧。
3.培养学生的创新思维和解决问题的能力。
4.提高学生的设计实践能力和团队合作意识。
三、课程内容:第一章现代设计方法概论(6课时)1.1现代设计方法的定义与作用1.2现代设计方法的研究领域与方法论1.3现代设计方法的发展历程与趋势第二章问题定义与用户需求分析(12课时)2.1设计问题定义的重要性与技巧2.2用户需求分析的方法与实践2.3问题定义与用户需求分析的案例分析与讨论第三章创意发散与评估(18课时)3.1创意发散的概念与方法3.2创意评估的标准与技巧3.3创意发散与评估的实践案例分析与讨论第四章设计方案生成与优化(24课时)4.1设计方案生成的方法与工具4.2设计方案优化的原则与策略4.3设计方案生成与优化的实践案例分析与讨论第五章原型制作与用户测试(18课时)5.1原型制作的方法与技巧5.2用户测试的设计与实施5.3原型制作与用户测试的案例分析与讨论第六章项目管理与团队合作(12课时)6.1项目管理的基本概念与流程6.2团队合作的原则与技巧6.3项目管理与团队合作的案例分析与讨论四、教学方法与评价方式:1.教学方法:本课程采用以学生为主体、教师为引导的探究式学习方法,注重理论与实践的结合。
课堂将结合案例分析、小组讨论和实践操作等形式进行教学。
2.评价方式:本课程的评价方式包括平时表现、课堂参与、实践作业和期末综合考核等。
平时表现和课堂参与占比30%,实践作业占比40%,期末综合考核占比30%。
五、教材与参考资料:1.教材:2.参考资料:-相关学术论文及案例分析以上是《现代设计方法》教学大纲,旨在培养学生的现代设计思维和实践能力,帮助学生成为具有创新意识和团队合作能力的设计专业人才。
现代设计方法

绿色设计
在产品整个生命周期内,着重考虑产品环境属性(可 拆卸性,可回收性、可维护性、可重复利用性等)并将其 作为设计目标,在满足环境目标要求的同时,保证产品应 有的功能、使用寿命、质量等要求。
并行设计
并行设计是一种对产品及其相关过程(包括设计制造过 程和相关的支持过程)进行并行和集成设计的系统化工作模 式。 Nhomakorabea 虚拟设计
虚拟设计技术是由多学科先进知识形成的综合系统技 术,其本质是以计算机支持的仿真技术为前提,在产品设 计阶段,实时地并行地模拟出产品开发全过程及其对产品 设计的影响,预测产品性能、产品制造成本、产品的可制 造性、产品的可维护性和可拆卸性等,从而提高产品设计 的一次成功率。
相似性设计
人们在长期探索自然规律的过程中,逐渐形成了研究 自然界和工程中各种相似现象的“相似方法”、“模化设 计方法”和相应的相似理论、模拟理论。相似方法就是把 个别现象的研究结果推广到所有相似现象上去的方法。
模块化设计
模块化设计(Block-based design)就是将产品的某些 要素组合在一起,构成一个具有特定功能的子系统,将这 个子系统作为通用性的模块与其他产品要素进行多种组合, 构成新的系统,产生多种不同功能或相同功能、不同性能 的系列产品。
三次设计
三次设计即三阶段设计,所谓三阶段设计,是建立在 试验设计技术基础之上的一种在新产品开发设计过程中进 行三阶段设计的设计方法。
优化设计
优化设计(Optimal Design)是把最优化数学原理应 用于工程设计问题,在所有可行方案中寻求最佳设计方案 的一种现代设计方法。
可靠性设计
可靠性设计(Reliability Design)是以概率论和数理统 计为理论基础,是以失效分析、失效预测及各种可靠性试 验为依据,以保证产品的可靠性为目标的现代设计方法。
现代设计方法知识点
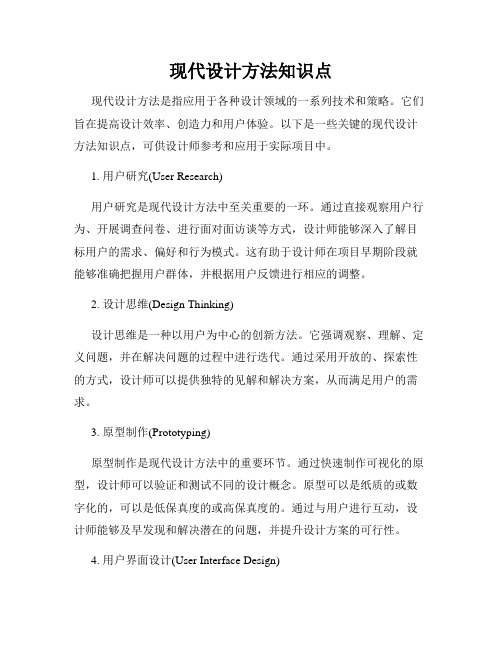
现代设计方法知识点现代设计方法是指应用于各种设计领域的一系列技术和策略。
它们旨在提高设计效率、创造力和用户体验。
以下是一些关键的现代设计方法知识点,可供设计师参考和应用于实际项目中。
1. 用户研究(User Research)用户研究是现代设计方法中至关重要的一环。
通过直接观察用户行为、开展调查问卷、进行面对面访谈等方式,设计师能够深入了解目标用户的需求、偏好和行为模式。
这有助于设计师在项目早期阶段就能够准确把握用户群体,并根据用户反馈进行相应的调整。
2. 设计思维(Design Thinking)设计思维是一种以用户为中心的创新方法。
它强调观察、理解、定义问题,并在解决问题的过程中进行迭代。
通过采用开放的、探索性的方式,设计师可以提供独特的见解和解决方案,从而满足用户的需求。
3. 原型制作(Prototyping)原型制作是现代设计方法中的重要环节。
通过快速制作可视化的原型,设计师可以验证和测试不同的设计概念。
原型可以是纸质的或数字化的,可以是低保真度的或高保真度的。
通过与用户进行互动,设计师能够及早发现和解决潜在的问题,并提升设计方案的可行性。
4. 用户界面设计(User Interface Design)用户界面设计关注的是如何使用户与产品或服务进行有效交互。
在现代设计方法中,用户界面设计强调简洁、直观和易用性。
通过运用合适的色彩、排版和互动元素,设计师可以创造出具有吸引力和良好用户体验的界面。
5. 响应式设计(Responsive Design)随着移动设备的普及,响应式设计已经成为现代设计方法中不可或缺的一部分。
响应式设计使得网页和应用程序能够适应不同屏幕尺寸和设备类型。
通过使用弹性布局、媒体查询和视口标签等技术,设计师可以确保用户无论使用手机、平板还是桌面电脑都能够获得良好的视觉和操作体验。
6. 交互设计(Interaction Design)交互设计关注的是用户与产品或服务之间的交互过程。
现代设计方法知识点总结

现代设计方法知识点总结现代设计方法是指在设计领域中运用创新的思维和技术来解决问题的一种方法论。
在当今快速发展的社会中,设计方法的应用已经变得越来越重要。
本文将从几个方面总结现代设计方法的知识点。
一、设计思维设计思维是现代设计方法的核心概念之一。
设计思维是一种以人为本的思维方式,强调观察、理解和满足用户需求。
它包括问题定义、创意生成、原型制作和用户测试等多个阶段。
设计思维强调跨学科的合作,通过多种视角来解决问题。
二、用户研究用户研究是现代设计方法中至关重要的一环。
通过深入了解用户的需求和行为,设计师能够更好地满足用户的期望。
用户研究的方法包括访谈、观察和可用性测试等。
通过与用户的交互,设计师能够探索用户需求,并根据用户的反馈进行调整和改进。
三、原型设计原型设计是现代设计中的关键步骤之一。
通过制作初步的产品原型,设计师可以快速验证和验证设计概念,并与用户进行反馈交流。
原型可以是手绘的草图、数字化的模型或者是可交互的界面。
通过原型设计,设计师能够提前发现潜在问题并进行改进。
四、可持续设计可持续设计是现代设计方法中越来越重要的一个方面。
可持续设计强调产品和系统的环境友好性,包括资源的节约、能源的有效利用和减少对环境的负面影响等。
设计师需要考虑材料的选择、产品的生命周期和循环利用等因素,以实现可持续发展的目标。
五、团队协作团队协作是现代设计方法中不可或缺的一部分。
现代设计往往需要跨学科的合作,包括设计师、工程师、市场人员等不同领域的专业人才。
通过有效的团队协作,设计师可以获得不同角度的反馈和建议,提高设计的质量和可行性。
总结:现代设计方法是一种以创新思维和技术为基础的设计方法论。
它强调设计思维、用户研究、原型设计、可持续设计和团队协作等方面的知识和技能。
通过合理运用这些方法,设计师可以更好地满足用户的需求,并创造出优秀的产品和解决方案。
在未来的发展中,现代设计方法将持续发展和创新,为社会的进步和发展做出更大的贡献。
现代设计方法
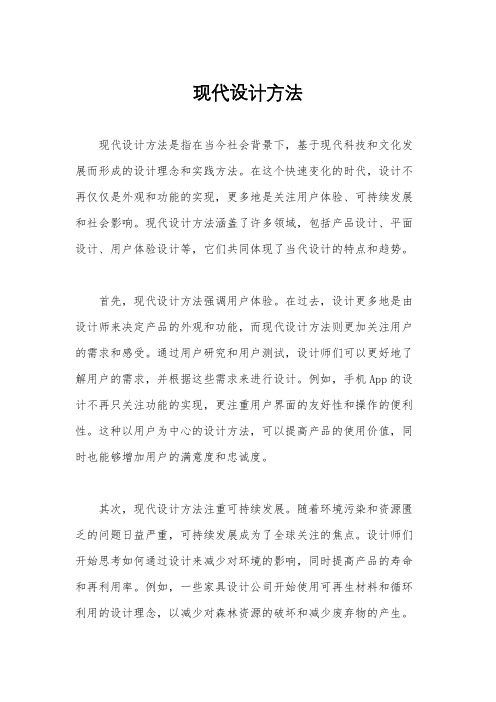
现代设计方法现代设计方法是指在当今社会背景下,基于现代科技和文化发展而形成的设计理念和实践方法。
在这个快速变化的时代,设计不再仅仅是外观和功能的实现,更多地是关注用户体验、可持续发展和社会影响。
现代设计方法涵盖了许多领域,包括产品设计、平面设计、用户体验设计等,它们共同体现了当代设计的特点和趋势。
首先,现代设计方法强调用户体验。
在过去,设计更多地是由设计师来决定产品的外观和功能,而现代设计方法则更加关注用户的需求和感受。
通过用户研究和用户测试,设计师们可以更好地了解用户的需求,并根据这些需求来进行设计。
例如,手机App的设计不再只关注功能的实现,更注重用户界面的友好性和操作的便利性。
这种以用户为中心的设计方法,可以提高产品的使用价值,同时也能够增加用户的满意度和忠诚度。
其次,现代设计方法注重可持续发展。
随着环境污染和资源匮乏的问题日益严重,可持续发展成为了全球关注的焦点。
设计师们开始思考如何通过设计来减少对环境的影响,同时提高产品的寿命和再利用率。
例如,一些家具设计公司开始使用可再生材料和循环利用的设计理念,以减少对森林资源的破坏和减少废弃物的产生。
这种可持续发展的设计方法不仅符合当代社会的价值观,也能够为企业带来更多的商业机会和社会声誉。
另外,现代设计方法强调跨学科合作。
在过去,设计师们往往是独自工作或者是在同一领域内进行合作。
而现代设计方法更加倡导不同领域之间的合作和交流。
例如,产品设计师和工程师、艺术家和科学家之间的合作,可以为设计带来更多的创新和可能性。
跨学科的合作不仅可以促进设计的进步,也能够为社会带来更多的创新和解决方案。
总的来说,现代设计方法是一个综合性的设计理念和实践方法,它不仅关注产品的外观和功能,更注重用户体验、可持续发展和跨学科合作。
在当今快速变化的社会中,现代设计方法为设计带来了更多的可能性和挑战,同时也为社会的发展和进步做出了积极的贡献。
随着科技和文化的不断发展,现代设计方法也将不断演变和完善,为人类创造更美好的未来。
现代设计方法

现代设计方法一、回顾设计方法的发展,可以划分为四个阶段:直觉设计阶段、经验设计阶段、中间试验辅助设计阶段、现代设计法设计阶段。
二、现代设计法总的可分成现代设计哲学和现代设计方法论两部分研究内容。
三、信号分析法是现代设计的前提,以突变论为机理的创造性方法是现代设计的基石,智能论是现代设计的核心,广义优化论是现代设计的宗旨。
四、现代设计方法论包括:突变论方法、智能论方法、系统论方法、离散论方法、信息论方法、对应论方法、优化论方法、控制论方法、寿命论方法、模糊论方法等。
五、常用的现代设计方法有:技术预测法、科学类比法、系统分析设计法、创造性设计法、逻辑设计法、信号分析法、相似设计法、模拟设计法、优化设计法、计算机辅助设计法、有限元法、可靠性设计法、动态分析设计法、模糊设计法等。
六、什么是最优化?并请简述优化设计的目的。
最优化就是要使问题的解决在一定条件下达到无可争议的完善化。
优化设计的目的就是对于一个给定的设计问题,在一定的技术和物质条件下,按照某种技术的和经济的准则,找出它的最佳的设计方案。
七、工程设计的优化有直觉优化、进化优化、探索试验优化、价值分析优化和数值计算优化等。
八、可靠性指系统在规定条件和规定时间内,完成规定功能的概率量度。
使用寿命是可靠性的前提。
可靠性必须建立在寿命论的基础上,只有经济合理地对使用寿命做出决策的基础上,再进一步考虑在此期限内充分地保证系统正常有效的工作。
在整个使用期间要实现全面地可靠性管理,不允许在制造、保管、维修、运输、包装等过程中影响可靠性。
可靠性的问题应包括可靠性预测及分配、可靠性设计和可靠性管理三个内容。
影响可靠性的因素:1、系统所能完成的功能容量与精度;2、系统工作要求的寿命及外界条件的干扰;3、组成系统的结构与元件的质量。
九、提高可靠性的途径:1.设计方面:人机系统经合考虑;简单性与冗余性辩证分析;原材料与零部件有机选配。
2.制作方面:元件正确的预处理;部件、组件高质量装配;部件、整机严格地试验。
简述现代设计方法

简述现代设计方法现代设计方法是指在现代科技、文化和社会背景下,以科学的方法和技术手段为基础,通过创新思维和跨学科的合作来实现设计目标的一种设计方式。
它具有高效、可持续、创新等特点,被广泛应用于各个领域。
一、现代设计方法的特点1. 高效性:现代设计方法注重过程的管理和控制,采用系统化、规范化的流程,能够提高设计效率,缩短开发周期。
2. 可持续性:现代设计方法注重环境保护和资源利用,通过绿色设计、循环经济等方式实现可持续发展。
3. 创新性:现代设计方法鼓励创新思维,通过跨学科合作和多元化的视角来进行创意开发。
二、现代设计方法的应用领域1. 产品设计:在产品开发过程中,采用现代设计方法可以提高产品质量和用户体验,并且减少成本。
2. 建筑设计:在建筑领域中,采用现代设计方法可以实现节能减排、绿色建筑等目标,并且提高建筑品质。
3. 服装设计:在时尚领域中,采用现代设计方法可以推动时尚产业的创新发展,并且提高服装的舒适度和美观度。
4. 交互设计:在数字化时代中,采用现代设计方法可以提高用户体验、增强用户参与感,并且推动数字化产业的发展。
三、现代设计方法的流程1. 研究和分析阶段:在这个阶段,需要了解用户需求、市场趋势、竞争对手等信息,并进行调研和分析。
2. 创意开发阶段:在这个阶段,需要进行头脑风暴、创意激荡等活动,以产生创新的点子。
3. 原型制作阶段:在这个阶段,需要将创意转化为具体形态,并通过模型或样品来进行测试和验证。
4. 产品开发阶段:在这个阶段,需要进行产品设计、工艺流程规划等活动,并进行试制和批量生产。
四、现代设计方法的实践案例1. 苹果公司的设计方法:苹果公司采用“人性化”的设计理念,注重用户体验和产品细节,在产品设计中融入艺术元素,并且不断推陈出新,引领行业潮流。
2. 特斯拉公司的设计方法:特斯拉公司采用“科技感”和“环保”为设计理念,注重车辆性能和外观设计,通过数字化技术和智能化系统来提高用户体验。
现代设计方法

现代设计方法现代设计方法已经成为设计领域的一种趋势。
它不仅仅是一种解决方案的提供者,更是一种创新力和思维方式的体现。
通过现代设计方法,设计师能够更好地理解用户需求,同时也能够更高效地实现设计目标。
本文将对现代设计方法进行探讨,并介绍其中的一些常见方法。
一、用户研究现代设计方法强调以用户为中心,在设计之初就进行深入的用户研究。
通过观察、访谈、调查等方法,设计师能够了解用户的需求、偏好、行为以及痛点。
这些信息可以有效指导设计的方向,确保设计最终能够满足用户的期望。
二、原型设计在现代设计方法中,原型设计是一种常见的方法。
通过创建初步的交互原型或界面原型,设计师可以快速验证和优化设计方案。
原型设计能够帮助设计师更好地展示和沟通设计思路,也可以帮助用户更好地理解产品或服务的功能和使用方法。
三、迭代设计现代设计方法鼓励设计师进行迭代设计,即通过不断的尝试和改进来逐渐完善设计。
在设计的不同阶段,设计师可以进行多次迭代,收集反馈并进行调整。
这样可以有效地降低设计的风险,并最终实现更好的设计效果。
四、跨学科合作在现代设计方法中,跨学科合作被赋予了很高的重要性。
设计师与其他领域的专家(如工程师、市场营销人员等)合作,能够集思广益,汇集各方优势,促进设计的全面性和创新性。
跨学科合作有助于打破学科壁垒,推动设计的跨界应用和创新。
五、可持续设计现代设计方法强调可持续设计,即将环境和社会责任纳入设计的考量之中。
设计师需要关注产品或服务的生命周期,减少对环境的负面影响,提高资源利用效率,促进社会的可持续发展。
可持续设计不仅是一种道德要求,也是设计发展的必然趋势。
六、数据驱动设计现代设计方法倡导数据驱动的设计。
通过收集和分析大量的用户数据,设计师能够更好地了解用户行为和需求,从而进行有针对性的设计。
数据的应用可以帮助设计师做出更加客观准确的决策,提高设计效果和用户体验。
七、敏捷设计敏捷设计是现代设计方法中的一种重要方法。
通过将设计过程模块化、迭代化和团队化,设计师能够更灵活地应对需求和变化。
现代设计方法
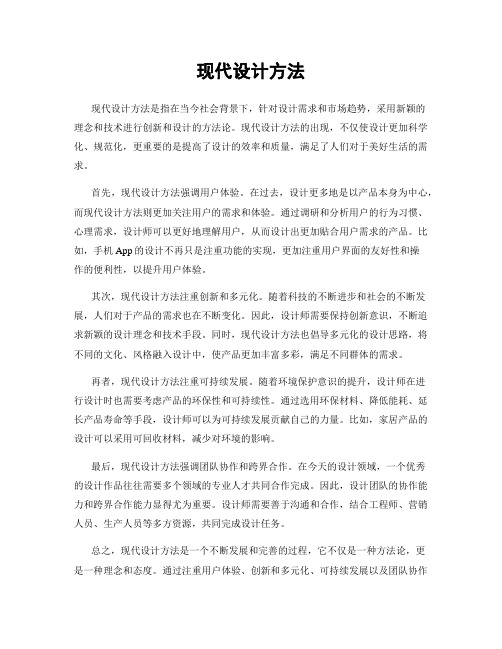
现代设计方法现代设计方法是指在当今社会背景下,针对设计需求和市场趋势,采用新颖的理念和技术进行创新和设计的方法论。
现代设计方法的出现,不仅使设计更加科学化、规范化,更重要的是提高了设计的效率和质量,满足了人们对于美好生活的需求。
首先,现代设计方法强调用户体验。
在过去,设计更多地是以产品本身为中心,而现代设计方法则更加关注用户的需求和体验。
通过调研和分析用户的行为习惯、心理需求,设计师可以更好地理解用户,从而设计出更加贴合用户需求的产品。
比如,手机App的设计不再只是注重功能的实现,更加注重用户界面的友好性和操作的便利性,以提升用户体验。
其次,现代设计方法注重创新和多元化。
随着科技的不断进步和社会的不断发展,人们对于产品的需求也在不断变化。
因此,设计师需要保持创新意识,不断追求新颖的设计理念和技术手段。
同时,现代设计方法也倡导多元化的设计思路,将不同的文化、风格融入设计中,使产品更加丰富多彩,满足不同群体的需求。
再者,现代设计方法注重可持续发展。
随着环境保护意识的提升,设计师在进行设计时也需要考虑产品的环保性和可持续性。
通过选用环保材料、降低能耗、延长产品寿命等手段,设计师可以为可持续发展贡献自己的力量。
比如,家居产品的设计可以采用可回收材料,减少对环境的影响。
最后,现代设计方法强调团队协作和跨界合作。
在今天的设计领域,一个优秀的设计作品往往需要多个领域的专业人才共同合作完成。
因此,设计团队的协作能力和跨界合作能力显得尤为重要。
设计师需要善于沟通和合作,结合工程师、营销人员、生产人员等多方资源,共同完成设计任务。
总之,现代设计方法是一个不断发展和完善的过程,它不仅是一种方法论,更是一种理念和态度。
通过注重用户体验、创新和多元化、可持续发展以及团队协作和跨界合作,现代设计方法必将带来更多更好的设计作品,满足人们对美好生活的向往。
希望设计师们能够不断学习和实践,将现代设计方法发挥到极致,为社会发展和人民生活贡献更多的力量。
现代设计方法
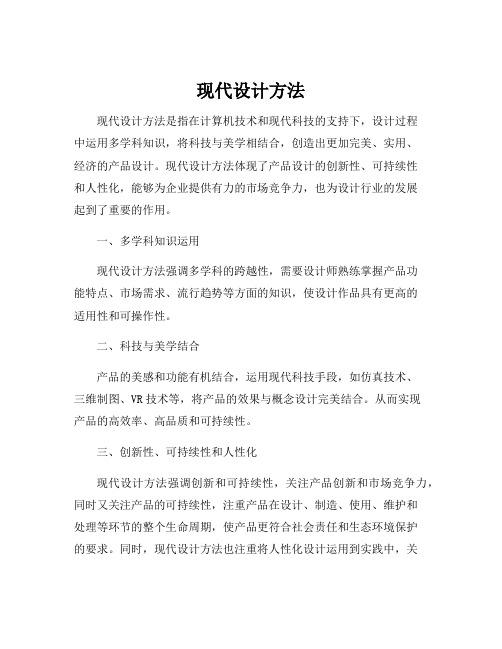
现代设计方法现代设计方法是指在计算机技术和现代科技的支持下,设计过程中运用多学科知识,将科技与美学相结合,创造出更加完美、实用、经济的产品设计。
现代设计方法体现了产品设计的创新性、可持续性和人性化,能够为企业提供有力的市场竞争力,也为设计行业的发展起到了重要的作用。
一、多学科知识运用现代设计方法强调多学科的跨越性,需要设计师熟练掌握产品功能特点、市场需求、流行趋势等方面的知识,使设计作品具有更高的适用性和可操作性。
二、科技与美学结合产品的美感和功能有机结合,运用现代科技手段,如仿真技术、三维制图、VR技术等,将产品的效果与概念设计完美结合。
从而实现产品的高效率、高品质和可持续性。
三、创新性、可持续性和人性化现代设计方法强调创新和可持续性,关注产品创新和市场竞争力,同时又关注产品的可持续性,注重产品在设计、制造、使用、维护和处理等环节的整个生命周期,使产品更符合社会责任和生态环境保护的要求。
同时,现代设计方法也注重将人性化设计运用到实践中,关注人们的使用习惯、口感感受、设计美观性等方面,使产品更符合人们对美好生活的期望。
四、市场竞争力得到提高现代设计方法是集现代化技术和创新设计的于一体的设计方式,通过将多学科知识结合,科技与美学相结合,从而为企业提供市场竞争力和创新价值。
在市场竞争激烈的今天,运用现代设计方法可以大大提高企业的产品可持续性和竞争力,实现企业的快速发展。
总之,现代设计方法是一个多学科、创新、可持续和人性化的设计方式,为现代企业提供了有效的市场竞争力和创新价值。
作为一名设计师,我们应该不断学习新概念、新技术,不断探索新的设计方向和风格,将设计理念转化为具有实际可操作性的产品,为人们创造更好的生活。
现代设计方法

现代设计方法现代设计方法是一种从创意到实现全过程的设计方式。
它始于20世纪初期并不断演进至今。
这种方法的目的是为了创造出具有可持续性、美观、功能强大和具有实用性的产品,满足人们的需求。
现代设计方法主要由以下步骤组成:1. 需求分析:设计师需要准确地了解客户的需求,包括目标用户、所需的功能和预算。
此步骤非常关键,因为它将确定设计的方向和范围,而这后面将影响整个设计过程。
2. 原型设计:通过设计出原型,设计师可以在客户得到看到和感受产品的视觉和物理方面的原始阶段实现想法转化。
该过程通常包括手绘草图、3D建模、CAD绘图和3D打印。
3. 反馈:设计师会将原型带给客户进行反馈,从而再次确定设计的方向和范围。
客户可以改变原来的设计方向或包括一些新的设计元素。
4. 改进和测试:设计师会根据客户的反馈对原型进行进一步改进。
这可能涉及到产品性能的改进、原材料的选择及其他因素的考虑。
设计师也会将样品给客户进行测试和反馈。
5. 确定细节:完成修改后,设计师会确定最终的细节和设计语言。
这可能涉及到产品的颜色、材质、外观、形状、尺寸和细微的设计。
6. 生产和上市:设计师的任务完成后,产品将进入生产环节进行加工制造,并上市进行销售。
现代设计方法已经成为了设计领域的强力工具。
这种设计方法主要是因为在处理设计问题和解决方案时,它强调了客户和用户的反馈和参与。
除此之外,现代设计方法还可以帮助设计师实现更好的效率和可持续意识。
例如,使用生态敏感的材料和工具,采用可持续的生产过程以及考虑到了环境和人类资源成本。
总之,现代设计方法是一个完整的流程,从需求分析到上市都有明确的阶段和步骤,通过有效的沟通和反馈来完成。
这种方法强调了用户参与和可持续性的考虑,以创造出具有高价值和高质量的设计方案。
随着不断的发展和创新,现代设计方法将会继续在设计领域发挥重要作用。
现代设计方法是一种面向未来的设计思维,它以用户为中心,强调设计的可持续性和人性化。
现代设计方法与传统设计方法之区别

现代设计方法与传统设计方法之区别
首先,现代设计方法与传统设计方法在技术方面的区别。
现代设计方
法追求精确性和精准性,强调计算机的使用,采用计算机辅助设计技术,
使用三维虚拟现实技术,实现在计算机中构建三维模型,从而实现客观可
视的设计模拟,以提高设计质量。
传统设计方法的技术多是依赖于经验和
直觉,侧重于传统工程学,偏重于经验,没有太多计算机和虚拟现实等技
术的支持。
其次,现代设计方法与传统设计方法在灵活性和可操控性方面存在明
显差异。
现代设计方法建立在计算机技术基础上,具有海量的数据库和计
算资源,可以根据设计要求快速的进行设计优化调整,实现设计可操控性,灵活性强,设计效率更高;而传统设计方法由于技术手段的局限性,其设
计工作存在效率低、灵活性差、可操控性较差的缺点。
此外,现代设计方法与传统设计方法在环节数量上也有所不同。
现代设计方法总结

现代设计方法总结现代设计方法是指在现代设计领域中广泛应用的一系列设计方法和原则。
这些方法和原则通过结合科技与创意,以满足用户需求并实现设计目标为核心,旨在提升设计的效率、创新和质量。
现代设计方法包括设计思维、用户体验设计、可持续设计等,以下将对这些方法进行详细介绍。
首先,设计思维是一种以解决问题为导向的思考方式,强调从终端用户的角度出发,结合创造力和批判性思维,以创新的方式寻找解决方案。
它将用户需求和市场洞察融入到设计过程中,通过反复验证和迭代,不断改善产品或服务的设计。
设计思维注重从用户需求和问题出发,倡导团队合作和跨学科合作,对于解决复杂问题具有重要作用。
其次,用户体验设计是一种以用户为中心的设计方法,旨在提供令用户满意的产品或服务。
它从用户的角度出发,通过研究用户需求、行为和心理,为用户提供更好的使用体验。
用户体验设计注重用户的感受、行为和反馈,通过用户研究、信息架构、交互设计等手段来优化产品或服务的界面和功能,以提高用户的满意度和忠诚度。
另外,可持续设计也是现代设计方法中的重要一环。
可持续设计强调设计的环境友好性和社会影响,注重减少资源消耗和环境压力。
它通过优化材料选择、生产过程、使用寿命以及材料回收与再利用等方面来实现可持续发展的目标。
可持续设计不仅关注产品的生命周期,也考虑产品与社会、文化和经济环境的关系,通过减少对环境的负面影响,提高资源利用效率,促进可持续的社会发展。
此外,现代设计方法包括原型设计、系统思考、敏捷设计等。
原型设计是通过制作产品或系统的雏形来验证和改进设计的方法,可以让设计师更直观地了解产品的外观、功能和用户体验。
系统思考是一种综合性的思维方法,将问题视为一个系统,从整体的角度思考和解决问题,旨在找到系统中的关键要素和相互关系。
敏捷设计是一种快速迭代、以用户反馈为驱动的设计方法,通过短周期的迭代,及时调整设计策略,以达到更好的设计效果。
综上所述,现代设计方法在创新、用户体验和可持续发展等方面发挥着重要作用。
- 1、下载文档前请自行甄别文档内容的完整性,平台不提供额外的编辑、内容补充、找答案等附加服务。
- 2、"仅部分预览"的文档,不可在线预览部分如存在完整性等问题,可反馈申请退款(可完整预览的文档不适用该条件!)。
- 3、如文档侵犯您的权益,请联系客服反馈,我们会尽快为您处理(人工客服工作时间:9:00-18:30)。
一、 可靠性设计
机械零件的可靠性设计又称概率设计, 它是将概率论和数理统计理论运用到机 !!!!! !!!! 械设计中, 并将可靠度指标引进机械设计的一种方法。其任务是针对设计对象的失 效和防止失效问题, 建立设计计算理论和方法, 通过设计, 解决产品的不可靠性问题, 使之具有固有的可靠性。 传统的机械设计往往以许用应力或者安全系数来判断机械零件性能是否满足要 求, 是否失效。这种设计方法将在一定条件下的材料强度或许用应力、 载荷及其产生 的应力、 材料性能及零件尺寸等都视为常量。然而, 由于受许多偶然因素的影响, 它 们都是在一定范围内取值并服从某种概率密度分布规律的随机量。因此, 传统的机 械设计方法已很难说明所设计的机械零件究竟在多大的程度上是安全的。生产和技
图)&*&%
应力 & 强度分布干涉模型
机械零件的可靠性设计方法是以 “应力 & 强度干涉理论” 为理论基础的, 该理论 的随机变量, 而 认为机械零件材料的强度 (极限应力) & !) ! 是服从于概率密度函数 ( 作用于机械零件危险截面上的工作应力 ’ 是服从于概率密度函数 ( ( ’) 的随机变量。 如图 ) & * & % 所示, 当机械零件的强度和应力的概率密度函数曲线相互重叠时, 即发 生 “干涉” 现象, 阴影部分表示不能保证工作应力在任何情况下都小于极限应力, 说明 设计时原属于安全的零件, 实际上并不一定安全, 存在一定的失效概率。可靠性设计 的基本原理就是要保证在一定的可靠度的前提下, 确定有关的设计参数。其核心问 题是确定零件的可靠度。在实际设计中, 往往预先规定可靠度, 或已知应力和强度分 布的均值及标准差值时, 按相关的计算确定其可靠度, 再利用概率分布和数理统计的
・ ,#+ ・
第二篇
机械设计
方法求得所需的设计参数。 对机械零件采用可靠性设计具有很大的经济价值, 因为机械零件的可靠性水平 主要取决于设计阶段。统计表明, 在设计阶段未考虑可靠性的机械零件, 其维修费用 比已考虑可靠性的相同的机械零件要高 ! 倍。机械系统及其零部件的可靠性设计的 具体过程和步骤参见有关文献。
・ ’&% ・
第二篇
机械设计
用优化设计程序来求解各种专门类型的优化设计问题。 对优化结果和方案进行评价、 决策, 是优化设计的最后环节, 必须以适合生产实 际条件为评价目标, 分析优化参数是否有必要调整, 优化结果是否为在给定条件下的 最优解等问题, 以作出最合理的决策。
四、 摩擦学设计
摩擦学是研究具有相互运动的接触表面间的科学技术和有关实践的科学。摩擦 学是近二十多年来发展起来的一门边缘学科, 它的研究内容是摩擦、 磨损和润滑。根 机械 据有关统计资料, 目前世界上大约 !"# $ %"# 的能源消耗在克服摩擦的过程中; 最近十多年 零部件的各种失效形式中, 大约 &%# 是由于摩擦副的磨损而引起。因此, 以来, 机械零件的设计方法已经从传统材料力学的整体强度研究发展到表面强度, 包 括接触强度、 挤压强度、 磨损强度和胶合强度等。所以, 无论是在理论研究还是工业 生产实际方面, 都迫切需要将摩擦学与机械设计的有关知识结合起来, 这就产生了所 谓的摩擦学设计。 摩擦学设计至今还没有一个确切的定义, 但可以肯定的是摩擦学设计就是要求 设计人员用摩擦学的观点考虑机械设计问题, 也就是将摩擦学的原理、 知识和已有的 研究成果有效地应用到机械设计的过程中; 在设计过程中始终考虑摩擦学的要求, 使 所设计的机器达到正确的润滑、 有控制的摩擦和预期的磨损寿命。一般来说, 运用摩 擦学的知识, 正确选择设计结构和参数、 润滑剂和材料, 尽量减少摩擦和磨损, 可以大 大提高机械零部件和机器设备的使用寿命, 取得的经济效益是非常可观的。 在整个机械设计过程中, 还应该正确处理摩擦学设计和其他设计 (如强度设计 等) 内容的关系。假如说过去的强度设计主要是指 “整体” 强度的话, 则摩擦学设计侧 重于 “表面” 强度。作为强度设计, 既要考虑结构体的强度要求, 又要考虑表面强度的 需要。有些机器 (如航空发动机) 结构强度是主要的; 有的机械 (如精密机械) 表面强 度则是首要的。
・ 6&! ・
第五章
现代设计方法
(!"##) 、 计算机辅助制造 (!"$) 等技术一起构成了系列技术。
三、 优化设计
优化设计方法是根据最优化原理和方法并综合各方面的因素, 以人机配合的方 式或用 “自动探索” 的方式, 借助计算机进行半自动或自动设计, 寻求在现有工程条件 下最优设计方案的一种现代设计方法。 优化设计方法建立在最优化数学理论和现代计算技术的基础之上, 首先建立优 化设计的数学模型, 即设计方案的设计变量、 目标函数、 约束条件, 然后选用合适的优 化方法, 编制相应的优化设计程序, 运用计算机自动确定最优设计参数。 优化设计方案中的设计变量是指在优化过程中经过调整或逼近, 最后达到最优 值的独立参数。目标函数是反映各个设计变量相互关系的数学表达式。约束条件是 设计变量间或设计变量本身所受限制条件的数学表达式。 机械系统及其零部件的优化设计过程, 是在给定的工况 (例如载荷) 条件下, 在对 机械系统的性态、 几何尺寸关系或其他因素的限制 (约束) 范围内, 选取设计变量, 建 立目标函数并获得最优值。 进行机械结构的优化设计一般包括三方面的内容: 一是将工程实际问题抽象成 为最优化的数学模型, 即建立优化方程。二是选择和应用优化数值方法求解这个数 学模型, 即优化问题的求解。三是对求解结果进行分析评价并做出决策, 即设计方案 的评价和决策。 在建立数学模型时, 一般要避免两种倾向。一种倾向是数学模型过分精细和复 杂, 导致求解失败或使计算成本过高; 另一种倾向是数学模型过分简化, 使优化问题 没有能反映设计的最本质要求。对于机械结构类型的设计对象, 则需要运用力学、 机 械设计的基础知识和专用机械设备的专业知识。对于静态问题, 其数学模型通常是 建立一个代数方程组; 而对于动力学问题, 则多为常微分方程组。这些方程组反映了 所分析的结构各参数之间的内在联系, 因此通过它们就可以研究各参数对设计对象 工作性能的影响。 数学模型建立以后, 就要研究求解的具体方法, 即优化设计方法。优化的方法有 很多, 按目标函数的个数可分为单目标优化和多目标优化方法; 按设计变量的数目可 分为一维优化和多维优化方法; 按设计对象有无约束分为约束优化和无约束优化等。 从本质上讲, 优化过程就是函数或泛函求极值的问题。可以用解析法求解, 也可以用 迭代法求解。机械设计问题多数是设计变量较多的约束优化问题, 而且多为非线性 的, 因此不宜采用解析法求解, 而宜采用迭代法逐步求解。由于我国已经编制建立了 常用机械零部件及机构优化设计程序库, 在完成优化求解的过程中, 对一般的设计问 题就不需要自己编写优化方法计算程序, 只要根据设计题目的具体特点和要求, 在优 化设计程序库中选用合适的优化设计程序进行优化计算即可; 只有必要时才编制专
" ( ") ( # " ") ( $ !% ! "# & ") $"
式中, ( 为失效时间随机变量的概率密度函数。 & ") 按概率互补原理, 产品的可靠度应是: ( ") ( ") ( # ’ ") ! !%& $ !% 则可靠度表示为:
" ( ") ( ! ! % & "# & ") $ " ! "( & ") $" " (
五、 虚拟设计及其应用
(一) 概述
虚拟设计技术是以虚拟现实技术为基础、 以三维产品模型为核心、 以实现产品设 计高度数字化和高度人机交互为标志、 以快速准确直观的产品设计 ’ 评价 ’ 优化为目 标的计算机辅助设计技术。虚拟设计技术与计算机技术在产品开发中所取得的显著 ( ()+、 技术的发展为虚拟 应用成果和成效是密切相关的, 特别是 ()* (),、 ()- 等) 设计技术的产生奠定了深厚的技术基础。 虚拟设计技术允许设计人员在设计阶段便对产品进行真实的虚拟加工、 虚拟装 配以及虚拟样机的运行仿真和分析, 从而实现在早期设计阶段对产品全面的分析和
二、 计算机辅助设计
传统机械产品的设计过程通常分成三个阶段: 产品或部件的总体设计阶段 ! 零 即在总 部件的结构设计阶段!工作图的设计阶段。这三个阶段是反复交替进行的, 体方案确定后, 进行各零件的结构设计和工作图设计; 在进行结构设计和工作图设计 过程中, 如发现问题还需回头去修改总体方案。这样不断进行修改、 完善, 反复循环 直至得到一个较满意的设计结果。由于机械产品日趋复杂, 要求日益提高, 设计者的 负担也日趋繁重。 随着计算机技术的发展, 在设计工作中出现了由计算机辅助设计计算和绘图的 ("#$) 。计算机辅助设计就是设计中应用计算机进行设计 技术— — —计算机辅助设计 """"""" 信息处理。它包括分析计算和自动绘图两部分功能。"#$ 系统应支持设计过程的各 个阶段, 即从方案设计入手, 使设计对象模型化; 依据提供的设计技术参数进行总体 设计和总图设计; 通过对结构的静态和动态性能分析, 最后确定设计参数。在此基础 三维几何造型、 上, 完成详细设计和技术设计。因此, "#$ 设计应包括二维工程绘图、 有限元分析等方面的技术。 但由于一般使用者认为, 通常 虽然理论上 "#$ 的功能是参与设计的全过程的, 的设计中制图工作量占的比重较大 (%&’ ( )&’ ) , 因此在应用中, "#$ 的重点实际上 最 是放在制图自动化方面。目前国际上已有比较成熟的二维和三维 "#$ 绘图软件, 常用的如国外的 #*+, "#$、 我国也研制或开发了许多具 -.、 /,0123245 等。近几年来, 有自主版权的二维和三维 "#$ 支撑软件及其应用软件, 并得到了较好的推广应用, 已能满足我国企业 “甩掉图板” 的要求。 机械系统及其零部件的计算机辅助设计的一般过程是: 输入设计所需数据 ! 建 一个完整的 "#$ 系 立数学模型!进行性能分析!结构设计 ! 自动绘图。也就是说, 统, 应由科学计算、 图形系统和工程数据库等组成。 制造的工作内容和方式发生了根本性的变 "#$ 技术的应用使产品和工程设计、 革, 它可以缩短产品设计周期, 提高设计工作效率, 还可提高产品设计的精确度和可 靠性, 并可将先进的优化设计方法等引入设计过程, 使产品设计的最优化和自动化成 为可能。这一技术已经成为工业发达国家制造业保持竞争优势、 开拓市场的重要手 越来越深入, 集 段。随着 "#$ 技术的普及应用越来越广泛, "#$ 技术正向着开放、 成、 智能和标准化的方向发展, 并与计算机辅助分析 ( "#3) 、 计算机辅助工艺设计