鲁奇阀门说明(翻译)
Valves, But Manua VALVES The Series PBFV热敏塑料旋钮阀门说明

(314) (265) (180) (40) (35) (24)
10˝* 14-7/8 12-19/32 8-35/64 1-31/32 1-55/64 29/32
(378) (320) (217) (50) (47) (23)
Weight
G
H
K
L
M
NS
Holes lb (kg)
4-13/32 1-57/64 4-59/64 (125)/ 8-21/32 2-3/4 23/64 13/32 4
Wetted Materials: Body material: PPH; Disc: PVC or CPVC; Liner and seals: FPM or EPDM; Stem: 316 SS. Temperature Limits: PVC: 150°F (66°C); CPVC: 215°F (102°C). Operator: L at end of model number denotes locking hand lever. G at end of model number denotes manual gear.
13.5
(112) (66) 8-15/32 (215) (320) (70) (9) (20)
(6.1)
4-13/32 2-53/64 9-29/64
12-19/32 2-3/4 23/64 25/32 8
21 (9.5)/
(112) (72) (240)
(320) (70) (9) (20)
30 (13.6)
(201) (156) (120) (40) (35) (18)
3˝ 9-9/64 7-31/64 5-23/64 1-37/64 1-3/8 3/4
甲醇(鲁奇)装置操作规程2019.06.06

甲醇(鲁奇)装置操作规程2019.06.06鲁奇甲醇合成甲醇装置操作规程编制:审核:批准:前⾔根据⼤甲醇分⼚⽣产准备⼯作的需要,为了使操作⼈员熟练掌握甲醇装置装置开⼯要领和⽇后正常操作的规范化编写本操作规程。
本操作规程是根据鲁奇公司提供的技术资料,结合国内诸多以煤为原料制甲醇⼯艺技术,从我⼚⼯艺设计实际出发⽽编写的规范操作的技术⽂件。
内容涉及到本装置⼯艺设计数据和指标、本装置开、停操作法、岗位维护操作、⽣产过程中事故和异常情况处理;以供操作⼈员学习。
引⽤⽂件:1、鲁奇公司提供《设备操作⼿册》译制;2、鲁奇公司提供的⼯艺包;3、设计院提供PSA⼯艺说明书、PID图;4、鲁奇提供PID图;5、西门⼦提供合成压缩机PID图、操作说明;6、沈⿎提供燃料⽓压缩机PID图、操作说明。
本⼿册属于技术标准体系中的⼯艺技术⽂件,编号Q/JS-04-JC-021-2010。
本⼿册由甲醇分⼚起草。
——起草⼈:——校稿⼈:——审核⼈:——审查⼈:——本⼯艺技术操作规程⾃2011年06⽉1⽇开始实施,有效期为⼀年。
⽬录第⼀章压缩、合成岗位操作规程 (6)1.1岗位任务和职责 (6)1.1.1岗位任务 (6)1.1.2岗位职责 (6)1.2岗位管辖范围 (7)1.3正常⼯艺指标 (7)1.4⼯艺流程 (10)1.5开车操作 (11)1.6停车操作 (43)1.7不正常现象及事故处理 (49) 1.8压缩机操作维护管理规定 (59)第⼆章精馏岗位操作规程 (62)2.1岗位任务和职责 (62)2.2岗位管辖范围 (63)2.3正常⼯艺指标 (63)2.4⼯艺流程 (65)2.5开车操作 (66)2.6精馏装置停车操作 (77)2.6.1正常停车 (77)2.6.2紧急停车操作 (78)2.7不正常现象及事故处理 (79)第三章罐区岗位操作规程 (85)3.1岗位任务和职责 (85)3.3正常⼯艺指标 (86)3.4⼯艺流程 (86)3.5开车操作 (87)3.6装置停车操作 (90)3.7不正常现象及事故处理 (90)第四章PSA岗位操作规程 (93)4.1岗位任务和职责 (93)4.2岗位管辖范围 (93)4.3正常⼯艺指标 (94)4.4⼯艺流程 (95)4.5开车操作 (97)4.5.1正常开车 (97)4.5.2正常⽣产维护 (101)4.6PSA装置停车操作 (103)4.6.1正常停车 (103)4.6.2紧急停车操作 (104)4.7不正常现象及事故处理 (104)第五章燃料⽓系统操作规程 (108)5.1岗位任务和职责 (108)5.2岗位管辖范围 (109)5.3正常⼯艺指标 (109)5.4⼯艺流程 (111)5.5开车操作 (112)5.6燃料⽓系统停车操作 (121)5.6.1.1计划长期性停车 (121)5.6.1.2短期临时性停车 (121)5.6.1.3紧急停车 (122)5.6.1.4触发联锁停车 (122)5.7不正常现象及事故处理 (122)第六章其他 (129)6.1与本装置密切相关的重⼤注意事项 (129)6.2设计变更项⽬ (134)6.3合成⽓压缩机特殊设备切换操作 (134)6.4环保的要求 (135)第⼀章压缩、合成岗位操作规程1.1岗位任务和职责1.1.1岗位任务将净化⼯序送来含有CO、CO2、H2的原料⽓经过压缩提压后送⼊甲醇合成反应器,在适宜温度、压⼒、空速和有催化剂存在的条件下⽣成粗甲醇;在将粗甲醇送⼊精馏单元进⾏产品精制的同时,将合成粗甲醇过程中产⽣的驰放⽓送⼊PSA氢回收单元进⾏氢⽓回收。
阀门大全

阀门大全(中英对照)air-compressor valve空气压缩机阀门automatic cutout valve自动切断阀门backlash valve无游隙阀门High temperature valve高温阀门hose valve水带阀门pipe manifold valves管道汇集器阀门pneumatic cylinder cock valve风动汽缸排水阀阀门pneumatic positioner valve气动阀门定位器pneumatic sander valve风动撒砂器阀门quick opening valve快开阀门quick-opening gate valve速启阀门standby valve应急阀门;备用阀门two selenoid双螺管阀门valve chest阀门室valve clearance阀门间隙;阀余隙valveman阀门操作者wash-out valve清洗阀门adjusting valve调整阀,调节阀admission valve进气阀;进浆阀air admission valve进气阀air bleed(ing) valve排气阀;排气嘴air control valve空调阀air cylinder valve气筒阀air escape valve泄气阀air inlet valve (=air intake valve)进气阀;进风阀air operated throttle motor风动节流器,风动节流阀马达air pilot valve空气导向阀air pressure governor valve风压调压阀air relay valve空气中继阀air release valve (=air relief valve)排气阀;放空阀air reversing valve空气换向阀air shut-off valve空气关闭阀air signal reducing valve空气信号减压阀air slide valve空气分配阀air starting (control) valve空气起动(控制)阀air straining check valve空气滤尘止回阀air valve空气阀air vent valve气动调压阀,排气阀air-actuated direction valve气动控制换向阀air-compressor valve空气压缩机阀门air-operated valve气动换向阀air-vacuum proportional valve空真比例阀air-vacuum two way valve空真二位阀alarm valve报警阀aligned grid valve栅极中点校直的电子管阀Allan valve阿伦滑阀altitude valve【航空】高度阀(航空发动机汽化器的可调整阀) ammonia valve【工】氨阀angle back-pressure valve背压角阀angle globe valve折角球形阀angle stop valve弯形止阀,折角止阀angle valve角阀angle water valve折角水阀annular ring valve环形阀;环状阀anti-g valve【航空】防超重活门,抗重力阀application pilot valve作用导阀application valve作用阀,控制阀ashpan blower valve灰盘吹风阀Askania valve射流管阀atmos valve (=atmospheric valve)大气阀,空气阀;放空阀autocontrol valve自动控制阀automatic air valve自动空气阀automatic brake valve自动制动阀automatic control valve自动控制阀automatic cutout valve自动切断阀门automatic delivery control valve自动输送控制阀automatic drain valve自动排水阀automatic expansion valve (定压式)自动膨胀阀automatic gas sampling valve自动气体进样阀automatic reducing valve自动减压阀(高速制动机) automatic regulating valve自动调节阀automatic spring loaded valve自动弹簧阀automatic supplementary air valve自动补充(空)气阀automatic unloading valve自动卸载阀automatic valve自动阀automatic water level valve自动水准阀automatically operated valve自动操作阀automatic-control servo valve自动控制伺服阀auxiliary changeover valve辅助切换阀auxiliary valve辅助阀(暖汽调整阀用)back valve回动阀,止回阀,逆止阀,单向阀backflush valve反冲阀backlash valve无游隙阀门back-pressure valve止回阀back-up valve列车后端制动阀balance pressure reducing valve平衡减压阀balance slide valve平衡滑阀balance valve平衡阀,均压阀balanced distribution valve平衡配气阀balanced safety valve平衡式安全阀(可变动背压)ball check valve止回球阀,球形节流阀ball float valve浮子阀,浮球阀ball non-return valve球形止回阀ball relief valve球形安全阀ball safety valve球形安全阀ball stop valve球形止阀ball valve球阀,弹子阀ball-and-lever valve杠杆球阀bell valve钟形阀,装料钟bellows valve波纹管阀bellows-operated pilot valve膜盒控制导阀,膜盒导引阀bevel seat valve斜座阀,角阀biased valve承载阀blast furnace gas valve高炉煤气阀blast regulation valve通风调节阀bleed valve排出阀;放泄阀bleeder valve放液阀,放水阀block valve隔断阀blocking valve闭塞阀blow valve通风阀,安全阀,放空阀blow-down valve排气阀blower drain valve鼓风机放泄阀blower regulation valve通风调节阀blower valve鼓风机阀blow-off valve排出[泄]阀,放泄[空]阀,喷放阀blowout valve排气管,排出阀boiler check valve锅炉止回阀boiler feed valve锅炉给水阀bonnet valve帽状阀bottom drain valve底部放泄阀bottom valve底阀brake application magnet valve电磁制动阀brake application valve制动作用阀brake control valve制动控制阀brake cylinder release valve制动缸缓解阀,制动缸放风阀brake metering valve制动调节阀brake pipe compensating valve制动管补偿阀brake release magnet valve缓解电磁阀brake valve制动阀brass valve黄铜阀brass-fitted cast-iron valve黄铜配制铸铁阀brass-trimmed valve黄铜配制阀breather valve通气阀,呼吸阀breathing type safety valve呼吸式安全阀(罐车)brine retaining valve盐水箱保持阀bucket valve活塞阀buffer change valve缓变阀building block valve积木式阀,集成阀built-in check valve内装式单向阀bullet valve球阀buried valve with key液下控制阀butterfly control valve蝶形控制阀butterfly throttle valve蝶形节流阀butterfly valve蝶阀by-pass valve旁通阀,辅助阀,回流阀by-path valve旁通阀,辅助阀,回流阀caboose valve守车阀cage type valve笼形阀cam-operated valve凸轮控制阀capless tyre valve无帽胎阀car discharge valve车辆放风阀car signal valve车辆信号阀,车辆放风阀cartridge inserted valve筒式插装式阀,插装阀cement valve【机】水泥止回阀center valve中心阀centre bypass valve中间位置旁通的换向阀, M型机能换向阀centre spool valve中心柱形阀centrifugal saw plate valve离心机的圆盘保险(溢流)阀centrifugal type injection valve离心式喷射阀change valve活页阀;旋转阀,转换阀;多向阀charge valve充气阀,加载阀,加液阀charging check valve充气止回阀charging valve充气阀,加载阀,加液阀check valve单向阀,止回阀,防逆阀;检验阀check-valve pump止回阀配流泵chimney valve烟道阀choker checkvalve阻气单向阀cindervalve卸灰阀Cineston controller brake valve钦式控制制动联合阀(用于地下铁道) circulating-water valve循环水阀circulation valve环流阀clack valve止回阀clapper valve瓣阀clock valve单向绞链阀closed center valve中间位置封闭的阀(方向阀);闭中心阀closed crossover valve正遮盖的换向阀closed exhaust valve密闭排气阀closed-type fuel valve密闭形燃油阀closing valve隔离阀,节制阀,隔断阀,停汽阀clutch application valve离合器作用阀clutch temperature adjusting valve离合器温度调节阀coasting valve滑行阀,惯性运动阀coaxial valve同轴管[阀]cold water stop valve凉水止阀column shut-off valve柱关闭阀column switching valve柱转换阀column valve柱阀combination sliding and rotary spool valve又移动又旋转的圆柱滑阀combination valve组合阀combined inlet-outlet valve进出组合阀combined strainer and check valve混合滤尘止回阀common slide valve普通滑阀compensated flow control valve带压力补偿的流量控制阀;调速阀compensated relief valve平衡式溢流阀compensating air valve补充空气阀,补偿气阀,平衡气阀compensating valve补偿阀compensation valve平衡阀,补偿阀compression release valve减压阀compression valve (减振器的)压缩行程阀concentric valve同心阀condensate valve凝结水阀condenser level control valve凝汽器水位调节阀condenser relief valve凝气器安全阀condenser valve凝汽阀conductor‘s valve车长阀,紧急制动阀cone valve锥形阀cone-way valve单向阀conical seat valve锥形座阀conical valve锥形阀constant pressure expansion valve恒压膨胀活门,恒压膨胀阀constant pressure valve恒压阀control air type reducing valve控制空气型减压阀control air valve控制空气阀control valve控制阀,调节阀;控制管,调节管controllable check valve可控单向[止回检验]阀controller pilot valve控制器管制阀conversion valve转换阀;转向阀。
Modutrol IV 电动阀门链接器 Q5001 说明书

PRODUCT DATA63-2425-01Q5001 Valve Linkage for Modutrol IV MotorAPPLICATIONThe Q5001 Valve Linkage connects a Modutrol Motor to a 2- or 3-way valve. It is used primarily on steam and water valves such as the V5011 or V5013.FEATURES•Q5001 Valve Linkage is applicable to 2-way or 3-way valves in modulating or two position service.•Linkage requires no adjustment when used withHoneywell valves and Modutrol IV Motors (can also be used with Modutrol III motors).•Q5001 Valve Linkage replaces Q601 and Q618 Valve Linkages.•Linkage mounts directly to the valve bonnet; motor mounts on linkage bracket.•Easy-to-read position indicator.•Valve stem lift height cam selectable.•Overtravel permits tight closeoff without excessive motor strain.•Easy mounting and valve connection.•Available brackets make linkages adaptable to many valve bodies.•80 lb, 160 lb, and 320 lb stem force models available.ContentsApplication ........................................................................1Specifications ...................................................................2Ordering Information ........................................................2Installation ........................................................................4Operation and Checkout ..................................................8Replacement ....................................................................9Q5001 VALVE LINKAGE FOR MODUTROL IV MOTOR63-2425—012ORDERING INFORMATIONWhen purchasing replacement and modernization products from your TRADELINE® wholesaler or distributor, refer to the TRADELINE® Catalog or price sheets for complete ordering number.If you have additional questions, need further information, or would like to comment on our products or services, please write or phone:1.Your local Honeywell Automation and Control Products Sales Office (check white pages of your phone directory).2.Honeywell Customer Care1885 Douglas Drive NorthMinneapolis, Minnesota 55422-4386In Canada—Honeywell Limited/Honeywell Limitée, 35 Dynamic Drive, Toronto, Ontario M1V 4Z9.International Sales and Service Offices in all principal cities of the world. Manufacturing in Australia, Canada, Finland, France, Germany, Japan, Mexico, Netherlands, Spain, Taiwan, United Kingdom, U.S.A.SPECIFICATIONSIMPORTANT:The specifications given in this publication do not include normal manufacturing tolerances.Therefore, an individual unit may not exactly match the listed specifications. Also, this product is tested and cali-brated under closely controlled conditions and some minor differences in performance can be expected if those conditions are changed.TRADELINE MODELSTRADELINE MODELS are selected and packaged to provide ease of stocking, ease of handling and maximum replace-ment value. TRADELINE model specifications are the same as those of standard models unless specified other-wise.Table 3 on page 4TRADELINE MODELS AVAILABLE:Q5001D1000 Valve Linkage: 3/4 in. lift, 80/160 lb force.Q5001D1018 Valve Linkage: 3/4 in. lift, 160/320 lb force.Q5001D1026 Valve Linkage: 1-1/2 in. lift, 160/320 lb force.TRADELINE FEATURES:•Selectable close-off force to meet application requirements.Table 1 on page 3•Special pack with Tradeline Cross Reference on label.STANDARD MODELSQ5001A,B Valve Linkage for Modutrol IV Motors.See Table 1 on page 3 for model specifications. (Can also be used with Modutrol III motors.)LIFT: Selectable based on cam selection. See Table 3 on page 4 for part numbers of alternate cams.•Q5001A is shipped with 3/4 in. lift cam, part number 220861A.•Q5001B is shipped with 1-1/2 in. lift cam, part number 220867A.CLOSE-OFF FORCE:See Table 2 on page 4 for motor/valve/linkage selection.VALVE BONNET SIZE:See Table 2 on page 4 for bonnet size.TEMPERATURE RATINGS:-40° to 150° F [-40° to 66° C] ambient air temperature.-40° to 337° F [-40° to 169° C] valve bonnet temperature.MOTOR REQUIRED:See Table 3 on page 4.MOTOR STROKE:160 degree rotation, mechanically normally open or nor-mally closed.VALVE ACTION:Determined by motor rotation, cam orientation and valve type. Cam mounting option (up or down) allows proper control action with normally open or normally closed motors and valves.DIMENSIONS: See Fig. 1.WEIGHT: 6.2 pounds.ACCESSORIES:4074ETB: Anti-spin clip, valve button and set screws for 1/4 in. [6 mm] valve stem.Cams: See Table 3 on page 4 for merchandise cam part numbers.Q5001 VALVE LINKAGE FOR MODUTROL IV MOTOR363-2425—01Fig. 1. Approximate Q5001 Valve Linkage dimensions in in. [mm].NOTE:High torque spring return motor shown. Medium torque spring return and nonspring return motors require less clearanceon auxiliary end of motor. Linkage for 3/4 in. stroke and 1-3/8 in. valve bonnet shown. Linkage for large valve bonnet and larger stroke maximum 12 in. of clearance is required.aIf valve stroke is not 3/4 in. [19 mm], a merchandise cam must be purchased.b If valve stroke is not 1-1/2 in. [38 mm], a merchandise cam must be purchased.Table 1. Standard Models.Model Valve Stem ForceLift Adjust-ment Bonnet Connect Bonnet Size (O.D.)Stem Connect Anti-Spin Linkage Replaced (lb)N Q5001A100680355.93/4 fixedSetscrew1-3/8Button and clipNoQ618A1016,Q618A1032,Q618A1040,Q618A1014, Q601L, M a Q5001A1014160711.73/4 fixed Setscrew 1-3/8Button and clip No Q618A1008,Q618A1024, Q601J, K a Q5001A102232013553/4 fixed Setscrew 1-3/8Button and clip No Q601Q a Q5001B1004160711.71-1/2 fixed Setscrew 1-7/8Button and clip Yes Q601E b Q5001B101232013551-1/2 fixed Setscrew 1-7/8Button and clip Yes Q601P bQ5001D1000Tradeline 80, 160355.9-711.73/4 fixed Setscrew 1-3/8Button and clip Yes Q601J, K, L, M a Q618A Q5001D1018Tradeline 160, 320711.7-13553/4 fixedSetscrew1-3/8Button and clipYesQ601J, K, Q Q618A1008a ,Q618A1024Q5001D1026Tradeline160, 320711.7-13551-1/2 fixed Setscrew 1-7/8Button and clip YesQ601E, P bQ5001 VALVE LINKAGE FOR MODUTROL IV MOTOR63-2425—014aMerchandise cam required.aRefer to Modutrol Motor specifications to select motor with equal or greater torque. Modutrol IV Motors are available with 25 and 60 lb-in. outputs (spring return); 35, 75, 150 and 300 lb-in. (nonspring return).bThe 320 lb stem force linkage must be used with a 300 lb-in. motor.INSTALLATIONWHEN INSTALLING THIS PRODUCT…1.Read these instructions carefully. Failure to follow them could damage the product or cause a hazardous condi-tion.2.Check the ratings and description given on the product to make sure the product is suitable for your application.3.Installer must be a trained, experienced service techni-cian.4.After installation is complete, check out product opera-tion as provided in these instructions.5.Refer to the instruction sheet packed with the valve body for information on installing the valve.6.Refer to the instruction sheet packed with the Modutrol IV Motor for wiring diagrams and additional installation information for the motor.LocationSelect a location that allows ample clearance for adjustment and maintenance. Allow at least 4 in. [102 mm] above the linkage to remove the valve assembly for maintenance.Linkages may be mounted in a variety of positions. The 320 lb stem force linkage must be assembled to a 300 lb-in. Modutrol IV Motor. The linkage and motor may be rotated 360 degrees around the valve stem. However, in all installations, the motor shaft must be horizontal to ensure proper gear train lubrication and the valve stem must be above horizontal.Table 2. Valve-Linkage Selection Guide.Honeywell Valve TypeValve Body Style Pipe Size (in.)Linkage Bonnet Size (O.D.)Lift (in.)V5011A 2-way Flanged 2-1/2, 3Q5001A, D 1-3/83/4V5011A, B 2-way Flanged 4, 5, 6Q5001B, D1-7/81-1/2V5011F 2-way Screwed 1/2, 3/4, 1, 1-1/4, 1-1/2, 2, 2-1/2, 3Q5001A, D 1-3/83/4V5011G 2-way Screwed 1/2, 3/4, 1, 1-1/4,1-1/2, 2, 3Q5001A, D 1-3/83/4V5013B 3-way mixing Flanged 2-1/2, 3Q5001A, D 1-3/83/4V5013B 3-way mixing Flanged 4, 5, 6Q5001B, D 1-7/81-1/2V5013C 3-way diverting Flanged 2-1/2, 3Q5001A, D 1-3/83/4V5013C 3-way diverting Flanged 4, 5, 6Q5001B, D 1-7/81-1/2V5047A 2-way Screwed 1, 1-1/4, 1-1/2Q5001A, D 1-3/89/16a V5047A 2-way Screwed 2Q5001A, D 1-3/83/4V5051A2-wayFlanged2-1/2, 3, 4, 5, 6Q5001B, D1-3/81-1/2Table 3. Cam Selections Available.Cam NumberType Lift Required Torque a (lb-in.)Application80 lb stem force 160 lb stem force 320 lb stem force b 220858A Custom 9/16 in.2550100V5047A, 1 in. to 1-1/2 in.220861A Standard 3/4 in.2550100V5011/V5013, 1/2 in. to 3 in.;V5047A, 2 in.220863A Custom 1 in.3060120220864A Custom 1-1/8 in.3060120220865A Custom 1-1/4 in.50100200220867AStandard1-1/2 in.50100200V5011/V5013, 4 in. to 6 in.Q5001 VALVE LINKAGE FOR MODUTROL IV MOTOR563-2425—01that the set screws holding the valve linkage to the valve body are properly tightened to preventimproper operation or damage to the equipment. The torque for tightening these screws should be in the range of 72 to 120 lb-in.MountingToolsTools required for installing the linkage are:•5/32 in. hex wrench.•7/16 in. open end or box end wrench.Mount Linkage to Valve1.Loosen the two valve bracket set screws, if necessary, and slide the linkage over the valve stem and bonnet until the valve bracket rests on the shoulder of the valve bonnet.2.Tighten the two valve bracket set screws to secure the linkage to the valve. Make sure that the set screws hold-ing the valve linkage to the valve body are properly tight-ened to prevent damage to the equipment. The torque for tightening these screws should be in the range of 72 to 120 lb-in.Connect Valve Stem to Linkage Slide (Modutrol IV)1.Position the stem and stem button so that the sides are parallel to the entry of the anti-spin clip (Fig. 2). This will allow using the clip without disassembling and turning the stem and button as described in step 5.Fig. 2. Installing anti-spin clip2.Move the slide up or down until the top slot matches the slot in the stem button as indicated in Fig. 4.3.Push clip retainer lever to the left.4.Insert clip into upper slot until clip stops reach linkage slide front plate. The clip must engage the slot on the stem button and rear slide plate slot for proper valve operation.5.OPTIONAL: To insert the anti-spin clip, push clip retainer lever to the left, and insert the anti-spin clip in the middle slot. Insert until clip contacts linkage slide front plate. If clip will not fully insert, remove anti-spin clip and stem button clip. Turn stem and button until the button sides are parallel to the entry of the anti-spin clip. Replace stem button clip and anti-spin clip.6.Release clip retainer lever. When slide is moved, entireslide and valve stem should move up and down together.that the set screws holding the cam to the motor shaft are properly tightened to prevent damage to the equipment. The torque for tightening these screws should be in the range of 72 to 120 lb-in.Mount Cam to Motor1.Place 1/2 in. diameter plastic washer on motor shaft.2.Select cam appropriate to linkage and valve combination (standard model Q5001 Linkages include only one cam). Refer to Table 3 on page 4 for alternate cam selections.3.Determine correct position of the cam to provide proper valve operation. To achieve normally closed operation (stem down to close valve), the cam must be mounted on the power end of the motor as shown in Fig. 3. For a normally closed motor, the shaft rotates clockwise on an increase in signal, lifting the valve stem. If normally open operation is desired, install the cam rotated 180 degrees.4.Loosen the two cam set screws, if necessary, and slide the cam over the motor shaft to the stops and tighten the set screws. Make sure the set screws holding the cam to the motor shaft are properly tightened to prevent dam-age to the equipment. The torque for tightening these screws should be in the range of 72 to 120 lb-in.Fig. 3. Mounting the cam on the Modutrol MotorMounting the Motor Without Power1.On Tradeline selectable stem force models, select the proper hole for the pin to obtain the desired closeoff force needed for your application. The stem force holes are labeled on the slide.2.If the cam is pointing upward, go to Step 5. If the cam is pointing downward, slide motor and cam assembly into the linkage, aligning the motor mounting holes with the linkage mounting holes and mount the motor on the link-age bracket using the enclosed 1/4-20 x 1 in. bolts. The linkage will raise the motor power end off the linkageQ5001 VALVE LINKAGE FOR MODUTROL IV MOTOR63-2425—016motor bracket. It may be necessary to squeeze themotor auxiliary end of the linkage bracket slightly to align the mounting holes.3.Start all four motor bolts, then tighten the bolts on the power end first, pulling the motor snugly to the linkage motor bracket and compressing the linkage springs.4.Tighten the auxiliary end mounting bolts.5.If the cam is pointing upward, remove motor wiring cover (on nonspring return motors) and raise the linkage slide.6.Tilt the motor power end face down about 30° and slide motor and cam assembly into linkage opening at an angle to align one power end bolt hole. Make sure that the cam is between the linkage rollers. See Fig. 5(A).Fig. 4. Stem force pin position selection.Q5001 VALVE LINKAGE FOR MODUTROL IV MOTOR763-2425—01Fig. 5. Mounting Modutrol Motor to Q5001 Valve Linkage with cam pointing up.7.Install bolt but do not tighten.8.Rotate motor to align the other power end bolt hole (B) and install second bolt, but do not tighten at this time.9.Install auxiliary end mounting bolts and tighten (C), pull-ing auxiliary end of motor snugly to linkage motorbracket. It may be necessary to squeeze the motor auxil-iary end of the linkage bracket slightly to align the mount-ing holes.10.Tighten power end mounting bolts.NOTE:If motor and linkage are assembled without power,the operation and checkout must be performed to guarantee proper performance.Mounting the Motor With Power Available (Optional Means)1.For easier assembly, run the motor to mid-stroke. Refer to Modutrol Motor Specification for instructions on oper-ating the motor.2.OPTIONAL: Remove the upper force pin, push up the lever arm as indicated in Fig. 4 and replace pin in posi-tion to hold the lever arm away from the opening to allow the cam and motor assembly to slide into position easily. Repeat for the lower force pin. The lower force pin must be placed in the outer hole, because the valve stem but-ton limits the lever movement, preventing inner hole alignment. Refer to Fig. 4.3.Slide motor and cam assembly into opening, align the motor mounting holes with the linkage mounting holes and assemble the motor to the motor brackets using the enclosed 1/4 - 20 x 1 in. bolts, but do not tighten. It maybe necessary to squeeze the motor auxiliary end of the Q5001 Valve Linkage slightly to align the mounting holes. See Fig. 1.4.If levers were held out of the way in Step 2, remove the force pins and allow levers to return to operating posi-tion. Insert pins in the proper hole for the pin to obtain the desired closeoff force needed in your application and rotate to the locked position as shown in Fig. 4.5.Tighten the 1/4 x 20 x 1 in. motor bolts.NOTE:Both upper and lower stem force pins must be in thesame force hole location to make sure that proper seal off force for the valve is applied. Failure to lock arms in location with stem force pins will prevent the valve from closing.Final AssemblyAfter checkout (see “Operation and Checkout” on page 8), install the position indicator on the cam. The center of theindicator should coincide with the center of the motor shaft, see Fig. 3. This will allow the indicator to show position of the valve through the cover of the motor.The indicator is shipped with arrow label for normally closed valve operation. On a normally open valve, install the spare indicator label at 180° to the original label.Place the cover on the linkage by positioning the cover with the hole centered over the indicator, label oriented upwards. Press the cover over the linkage frame until the indents snap into place on the frame. Run the valve through two operating cycles to make sure that no binding occurs during operation.Q5001 VALVE LINKAGE FOR MODUTROL IV MOTOR63-2425—018OPERATION AND CHECKOUTThe Q5001 Valve Linkage operates the valve in a 160-degree stroke. See Fig. 6. As shown, a normally closed spring return motor will rotate the cam through the 160-degree stroke to lift the stem the distance prescribed by the selected cam. On loss of power, the spring will return the motor, linkage and valve to the closed position.For normally open spring return models, reverse the closed and open captions in Fig. 6.After installation and adjustment are completed, run valve/linkage/motor combination through two or more full cycles to make sure the combination operates properly.Refer to the appropriate Modutrol IV Motor instruction sheet for information on running the motor during checkout.1. A 2-way valve should close off tightly at the closed end ofits stroke.2. A 3-way valve should close off tightly at both ends of itsstroke. See Table 4 on page 8.3.The motor should be free to run through its completestroke without stalling.4.The linkage should operated freely without binding.LubricationThe Q5001 does not require any lubrication.Spring CompressionSpring compression for the Q5001 is shown in Table 4 onpage 8.If spring compression is less than minimum or more than maximum, verify that the correct cam was used. If the correct cam was used, remove valve stem clip and adjust valve stem button after set screw has been loosened. See Table 4 on page 8.Measure spring compression by measuring the distancebetween the lever end and the end of the spring slot. See Fig. 7.Fig. 6. Q5001 operation.Maximum spring compression = 11/32 in. [8.7 mm].Table 4. Minimum Spring Compression in in. [mm] (SeeFig. 6.).O.S. Number Stem Force Load80 lb 160 lb320 lbQ5001A10063/64 [1.2]Q5001A10143/32 [2.4]Q5001D10003/64 [1.2]3/32 [2.4]Q5001D10183/64 [1.2]3/32 [2.4]Q5001D10263/64 [1.2]3/32 [2.4]Q5001 VALVE LINKAGE FOR MODUTROL IV MOTOR963-2425—01Fig. 7. Spring compression.REPLACEMENTWhen replacing a motor or linkage in a valve application, make sure that the motor stroke is 160° to operate Q5001 withHoneywell V5011 two-way and V5013 threeway valves. Refer to Installation section for further details. Refer to Mount Cam to Motor and Mounting the Motor in the Installation section for details on mounting and removing the Modutrol Motor from the linkage.Q5001 VALVE LINKAGE FOR MODUTROL IV MOTOR63-2425—0110Q5001 VALVE LINKAGE FOR MODUTROL IV MOTOR 1163-2425—01Automation and Control SolutionsHoneywell International Inc.Honeywell Limited-Honeywell Limitée 1985 Douglas Drive North35 Dynamic Drive Golden Valley, MN 55422Toronto, Ontario M1V Q5001 VALVE LINKAGE FOR MODUTROL IV MOTOR® U.S. Registered Trademark© 2008 Honeywell International Inc.63-2425—01 M.S. Rev. 12-08By using this Honeywell literature, you agree that Honeywell will have no liability for any damages arising out of your use or modification to, the literature. You will defend and indemnify Honeywell, its affiliates and subsidiaries, from and against any liability, cost, or damages, including attorneys’ fees, arising out of, or resulting from, any modification to the literature by you.。
Victaulic阀门维修说明书

IMPORTANT INFORMATIONCONTENTS OF CLAPPER SEAL KITThis kit may contain two clapper seals. It is important to determine theappropriate clapper seal for the valve being serviced. THESE SEALSARE NOT INTERCHANGEABLE. For example: If the clapper currentlycontains a seal that looks like “A” below, it MUST be replaced with theexact seal provided in this kit. Refer to the notes below for details.SEAL "A"THIS SEAL CONTAINS A WHITE SEAL WASHER AND A SEAL RING.INSTRUCTIONS START ON PAGE 3.NOTE: THIS IS THE ONLY SEAL THAT CAN BE USED IN THECLAPPER FOR SERIES 756, 758, 764, 768, OR 769 FIRELOCKVALVES.SEAL “B”FOR DOMESTIC SERIES 751 ALARM CHECK VALVES: THIS SEALIS A SOLID DESIGN FOR 4 – 6-INCH/114.3 – 168.3-MM SIZES.INSTRUCTIONS START ON PAGE 5.FOR EUROPEAN SERIES 751 FIRELOCK ALARM CHECK VALVESTATIONS: THIS SEAL IS A SOLID DESIGN FOR 3 - 6-INCH/88.9- 168.3-MM (INCLUDING 165.1 MM) SIZES. INSTRUCTIONS STARTON PAGE 5. NOTE: The solid seal design for Series 751 FireLockEuropean Alarm Check Valve Stations must be ordered specifically forthe European valve. NOTE: European Alarm Check Valves contain aname plate with VdS and CE markings.I-30_1 REPLACING THE CLAPPER SEAL FOR SERIES 751, 756, 758, 764, 768, AND 769FIRELOCK® FIRE PROTECTION VALVESVICTAuLIC IS A REgISTEREd TRAdEmARk oF VICTAuLIC CompAny. © 2006 VICTAuLIC CompAny. ALL RIghTS RESERVEd. pRInTEd In ThE uSA.REV_DREMOVING THE SYSTEM FROM SERVICE AND1.notify the authority having jurisdiction, remote station alarm moni-tors, and those in the affected area that the system is being taken out of service.2. open the water supply main drain valve fully to flush the water supply of any contaminants.3. Close the water supply main drain valve.4. Close the water supply main control valve to take the system out of service.5. open the water supply main drain valve.6. Confirm that water is not flowing from the water supply main drain valve.7. Close the piston-charge-line ball valve (Series 756 and 758) or dia-phragm-charge-line ball valve (Series 764, 768, and 769).8.open the system main drain valve to drain any water that has accumulated and to release system air pressure.NOTE: If the system has operated, open the remote system test valve (inspector's test connection) and any auxiliary drain valves.9.SHUT OFF THE AIR SUPPLY.10. PUSH DOWN ON THE AUTO DRAIN SCREW TO REMOVEPRESSURE IN THE PISTON CHARGE LINE OR DIAPHRAGM CHARGE LINE.11. After all pressure is released from the system, loosen the coverplate bolts slowly. NOTE: do noT remove any cover plate bolts until all cover plate bolts are loosened.12. Remove all cover plate bolts, along with the cover plate and coverplate gasket.13. For Series 764, 768, and 769 valves, push the latch back (towardthe diaphragm).14. Rotate the clapper out of the valve body. At this point, deter-mine which seal is currently installed in the clapper. Refer to the “Contents of Clapper Seal kit” section on page 1 for details.15. Follow the appropriate replacement steps on the following pages.I-30_ REPLACING THE CLAPPER SEAL FOR SERIES 751, 756, 758, 764, 768, AND 769 FIRELOCK ® FIRE PROTECTION VALVESVICTAuLIC IS A REgISTEREd TRAdEmARk oF VICTAuLIC CompAny. © 2006 VICTAuLIC CompAny. ALL RIghTS RESERVEd. pRInTEd In ThE uSA.REV_DREPLACEMENT OF CLAPPER SEAL “A”1.Remove the seal-assembly bolt/bolt seal from the clapper seal.2.Remove the seal-retaining ring.3.pry the edge of the old seal washer from inside the clapper seal,as shown above.4.Remove the seal washer from the clapper seal. This will aid inremoving the clapper seal in step 5. discard the seal washer.5.pry the old clapper seal, along with the seal ring, out of the clap-per. discard the clapper seal/seal ring.6.Wipe away any contaminants, dirt, and mineral deposits from the clapper. Clean out any holes that are plugged in the valve-body seat ring.DO NOT USE SOLVENTS OR ABRASIVES.I-30_3REPLACING THE CLAPPER SEAL FOR SERIES 751, 756, 758, 764, 768, AND 769 FIRELOCK ® FIRE PROTECTION VALVES VICTAuLIC IS A REgISTEREd TRAdEmARk oF VICTAuLIC CompAny. © 2006 VICTAuLIC CompAny. ALL RIghTS RESERVEd. pRInTEd In ThE uSA.REV_D-BSHFS EJBNFUFS PG DMBQQFS TFBM JT JOTUBMMFE JO DMBQQFS4FBMJOH TJEF PG DMBQQFS TFBM GBDFT PVU PG DMBQQFS4NBMMFSEJBNFUFST PG TFBM SJOH BOE DMBQQFS TFBMmake sure the seal ring is installed in the new clapper seal properly, as shown above. The smaller diameter of the seal ring must be installedtoward the sealing surface of the clapper seal.7.Install the new clapper seal into the clapper carefully. make surethe seal ring snaps into the clapper completely.8.place the seal-retaining ring onto the seal washer of the clapperseal.9.Install the seal-assembly bolt/bolt seal through the seal-retaining ring and the clapper. Tighten the seal-assembly bolt/bolt seal to the torque value, listed in the table below, to ensure a proper seal.REqUIRED SEAL-ASSEMBLY BOLT/BOLT SEAL TORqUES FOR10.Follow all steps in the “Installing the Cover plate” section.I-30_4REPLACING THE CLAPPER SEAL FOR SERIES 751, 756, 758, 764, 768, AND 769 FIRELOCK ® FIRE PROTECTION VALVESVICTAuLIC IS A REgISTEREd TRAdEmARk oF VICTAuLIC CompAny. © 2006 VICTAuLIC CompAny. ALL RIghTS RESERVEd. pRInTEd In ThE uSA.REV_DREPLACEMENT OF CLAPPER SEAL “B”1.Remove the seal-assembly bolt/bolt seal from the clapper seal.2.Remove the seal-retaining ring.3.Remove the old solid seal from the clapper. discard the solid seal.4.Wipe away any contaminants, dirt, and mineral deposits from the clapper. Clean out any holes that are plugged in the valve-body seat ring.DO NOT USE SOLVENTS OR ABRASIVES.5.Install the new solid seal into the clapper, as shown above. NOTE:make sure the sealing lip is pointing upward.6.place the seal-retaining ring onto the solid seal, as shown above.I-30_5REPLACING THE CLAPPER SEAL FOR SERIES 751, 756, 758, 764, 768, AND 769 FIRELOCK ® FIRE PROTECTION VALVES VICTAuLIC IS A REgISTEREd TRAdEmARk oF VICTAuLIC CompAny. © 2006 VICTAuLIC CompAny. ALL RIghTS RESERVEd. pRInTEd In ThE uSA.REV_D7. Install the seal-assembly bolt/bolt seal through the seal-retainingring and the clapper. Tighten the seal-assembly bolt/bolt seal to the torque value, listed in the table below, to ensure a proper seal.REqUIRED SEAL-ASSEMBLY BOLT/BOLT SEAL TORqUES FOR8. Follow all steps in the "Installing the Cover plate" section.1.Verify that the cover plate gasket is in good condition. If the gasketis torn or worn, replace it with a new, Victaulic-supplied gasket.2.Align the holes of the cover plate gasket with the holes in the cover plate.3.Insert one cover bolt through the cover plate and cover gasket toease alignment.I-30_6REPLACING THE CLAPPER SEAL FOR SERIES 751, 756, 758, 764, 768, AND 769 FIRELOCK ® FIRE PROTECTION VALVESVICTAuLIC IS A REgISTEREd TRAdEmARk oF VICTAuLIC CompAny. © 2006 VICTAuLIC CompAny. ALL RIghTS RESERVEd. pRInTEd In ThE uSA.REV_D4. Align the cover plate/cover plate gasket to the valve. make sure theclapper spring's arms are rotated to their installed position. Tightenall cover plate bolts into the cover plate/valve body.5. Torque all cover plate bolts in an even, crossing pattern. Refer tothe “Required Cover plate Bolt Torque” table on this page for the required torque values. do noT over-tighten the cover bolts.6. place the system back in service by following the “placing theSystem in Service” section in the appropriate installation, mainte-nance, and testing manual supplied with the valve.I-30_7REPLACING THE CLAPPER SEAL FOR SERIES 751, 756, 758, 764, 768, AND 769FIRELOCK® FIRE PROTECTION VALVESVICTAuLIC IS A REgISTEREd TRAdEmARk oF VICTAuLIC CompAny. © 2006 VICTAuLIC CompAny. ALL RIghTS RESERVEd. pRInTEd In ThE uSA. REV_DI-30REPLACING THE CLAPPER SEAL FOR SERIES 751, 756, 758, 764, 768, AND 769 FIRELOCK ® FIRE PROTECTION VALVESUPDATED 4/ 007I-30 617 REV D ZI00751001VICTAuLIC IS A REgISTEREd TRAdEmARk oF VICTAuLIC CompAny. © 2006 VICTAuLIC CompAny. ALL RIghTS RESERVEd. pRInTEd In ThE uSA.US & WORLD HEADQUARTERS P .O.Box 31Easton,PA 18044-0031USA 4901Kesslersville Road Easton,PA 18040USA1-800-PICK-VIC (1-800-742-5842)1-610-559-33001-610-250-8817(fax)*********************CANADA 905-884-7444905-884-9774(fax)***********************EUROPE32-9-381-15-0032-9-380-44-38(fax)********************UNITED KINGDOM44(0)143874110044(0)1438313883(fax)CENTRAL AND SOUTH AMERICA1-610-559-33001-610-559-3608(fax)*******************ASIA PACIFIC86-21-5425330086-21-54253671(fax)*******************MIDDLE EAST971-4-883-88-70971-4-883-88-60(fax)。
Series WE03 3-Piece Tri-Clamp钢球阀说明书

Service: Compatible liquids and gases. Power Requirements: 110 VAC,
Body: 3-piece.
220 VAC, 24 VAC or 24 VDC
Line Sizes: 1/2 to 2˝ .
(MD models not available in 24 VDC).
Pneumatic Model
Electric (110 VAC) Model
Electric (110 V来自C) Model1/2˝ 14.39 WE03-CHD00 WE03-CDA01
WE03-CSR02
WE03-CTD01-A
WE03-CMD01-A
3/4˝ 42.25 WE03-DHD00 WE03-DDA01
body and epoxy coated aluminum end aluminum.
caps.
Temperature Limits: -40 to 140°F
Temperature Limits: -40 to 176°F (-40 (-40 to 60°C).
to 80°C).
Electrical Connection: 1/2˝ female NPT.
Maximum Supply Pressure: 120 psi Duty Rating: See instruction manual.
(8.6 bar).
Enclosure Rating: NEMA 7, designed
Air Connections: DA01: 1/8˝ female to meet hazardous locations: Class I,
Ruelco RV-1 压力解压阀说明书

OPERATIONThe Ruelco RV -1 Relief Valve is a stainless steel, soft seat, poppet relief valve capable of relieving pressures from 50 psi to 1,250 psi. The size of the valve makes it ideal for small spaces while the stainless steel construction allows the valve to operate in highly corrosive systems.FEATURES• 316 stainless steel construction • Externally adjustable• Wide adjustable ranges using only three springs • 100% tested •Compact designPHONE: 504-340-0055 FAX: 504-340-0056EMAIL:****************1209 DISTRIBUTORS ROW NEW ORLEANS, LA 70123DIMENSIONSSPECIFICATIONSFEMALE INLETPARTS LISTPHONE: 504-340-0055 FAX: 504-340-0056EMAIL:****************1209 DISTRIBUTORS ROW NEW ORLEANS, LA 70123ITEM QUANTITYDESCRIPTION MATERIAL 1 1 SPRING CAP 316 ST. STL. 2 1 LOCK NUT 316 ST. STL. 3 1 SPRING HOUSING 316 ST. STL. 4A 1 BLUE SPRING SPRING WIRE 4B - RED SPRING SPRING WIRE 4C - GOLD SPRING SPRING WIRE 5 1 SPRING PLATE 316 ST. STL. 6* 1 BODY SEAL NITRILE 7 1 RELIEF VALVE BODY316 ST. STL. 8 1 SEAL GUIDE 316 ST. STL. 9* 1 HEAD SEAL FLUROCARBON10 1 OUTER SLEEVE 316 ST. STL. 11* 1 PISTON SEAL NITRILE 121PISTON17-4 PH ST. STL* INDICATES ITEMS IN THE REPAIR KITREPAIR KIT•75-023-000OTHER TEMPERATURE RANGES AND SEAL COMPOUNDS AVAILABLE UPON REQUESTORDERING CODEOPERATIONThe Ruelco RV -1 Relief Valve is a stainless steel, soft seat, poppet relief valve capable of relieving pressures from 250 psi to 10,000 psi. The size of the valve makes it ideal for small spaces while the stainless steel construction allows the valve to operate in highly corrosive systems.FEATURES• 316 stainless steel construction • Externally adjustable• Wide adjustable ranges using only three springs •100% testedPHONE: 504-340-0055 FAX: 504-340-0056EMAIL:****************1209 DISTRIBUTORS ROW NEW ORLEANS, LA 70123DIMENSIONSSPECIFICATIONSFEMALE INLETPARTS LISTPHONE: 504-340-0055 FAX: 504-340-0056EMAIL:****************1209 DISTRIBUTORS ROW NEW ORLEANS, LA 70123ITEM QUANTITYDESCRIPTION MATERIAL 1 1 SPRING CAP 316 ST. STL. 2 1 LOCK NUT 316 ST. STL. 3 1 SPRING HOUSING 316 ST. STL. 4A 1 BLUE SPRING SPRING WIRE 4B - RED SPRING SPRING WIRE 4C - GOLD SPRING SPRING WIRE 5 1 SPRING PLATE 316 ST. STL. 6* 1 BODY SEAL NITRILE 7 1 RELIEF VALVE BODY316 ST. STL. 8 1 SEAL GUIDE 316 ST. STL. 9* 1 HEAD SEAL FLUROCARBON 10 1 OUTER SLEEVE316 ST. STL. 11* 1 PISTON SEAL NITRILE 121PISTON17-4 PH ST. STL* INDICATES ITEMS IN THE REPAIR KITREPAIR KIT•75-015-000OTHER TEMPERATURE RANGES AND SEAL COMPOUNDS AVAILABLE UPON REQUESTORDERING CODEOPERATIONThe Ruelco RV -1 Relief Valve is a stainless steel, soft seat, poppet relief valve capable of relieving pressures from 250 psi to 15,000 psi. The size of the valve makes it ideal for small spaces while the stainless steel construction allows the valve to operate in highly corrosive systems.FEATURES• 316 stainless steel construction • Externally adjustable• Wide adjustable ranges using only three springs •100% testedPHONE: 504-340-0055 FAX: 504-340-0056EMAIL:****************1209 DISTRIBUTORS ROW NEW ORLEANS, LA 70123DIMENSIONSSPECIFICATIONSPARTS LIST PHONE: 504-340-0055FAX: 504-340-0056 EMAIL:****************1209 DISTRIBUTORS ROW NEW ORLEANS, LA 70123ITEM QUANTITY DESCRIPTION MATERIAL 11SPRING CAP316 ST. STL.21LOCK NUT316 ST. STL.31SPRING HOUSING316 ST. STL.4A1BLUE SPRING SPRING WIRE 4B- RED SPRING SPRING WIRE 4C- GOLD SPRING SPRING WIRE 51SPRING PLATE316 ST. STL.6*1BODY SEAL NITRILE71RELIEF VALVE BODY17-4 PH ST. STL.81SEAL GUIDE316 ST. STL.9*1HEAD SEAL URETHANE 101OUTER SLEEVE316 ST. STL.11*1PISTON SEAL NITRILE121PISTON17-4 PH ST. STL * INDICATES ITEMS IN THE REPAIR KITREPAIR KIT• 75-034-000OTHER TEMPERATURE RANGES AND SEAL COMPOUNDS AVAILABLE UPON REQUEST ORDERING CODE。
各种阀门,管件及其部件名称中英文对照表

阀室式活塞泵
valve box type piston pump
133
阀室式活塞泵(美)
valve pot type piston pump
134
阀抬起装置
valve lifting device
135
阀体
body
136
阀体
valve body
137
阀箱
valve box
138
阀箱
valve cage
94
阀板式活塞泵
valve deck plate type piston pump
95
阀板式活塞泵
valve plate type piston pump
96
阀瓣
Disc
97
阀操纵杆
valve operating rod
98
阀痤槽
valve seat recess
99
阀挡
valve grid
100
阀挡
153
法兰端
flange end
154
法兰接头
flange joint
155
法兰连接紧固件(双头螺栓和螺帽)
flange bolting
156
法兰密封面,法兰面
flange facing
157
法兰面加工
flange facing finish
158
法兰球阀
Flange Ball Valves
159
翻板阀
177
辅助(副)阀
Auxiliary valves
178
负荷率
Rate of load condensate
179
阿尔法拉夫Unique 7000系列-坑口阀门说明书

Observe welding guideline in instruction manual)The tank flange is supplied with TÜV approval AD2000and inspection certificate3.1 according to EN10204.TECHNICAL DATATemperatureMax.product pressure in tank:145psi(1000kPa(10bar))-max.68°F....................123psi(850kPa(8.5bar))-max212°F....................109psi(750kPa(7.5bar))-302°F Temperature range:........14°F to+284°F(EPDM)PressureMax.product pressure inpipeline(depends on valve specifications)::..........145PSI(10bar)Max.product pressure in tank(depends on valve specificationsand temperature):.........145psi(10bar)-max.68°F.123psi(8.5bar)-max212°F109psi(7.5bar)-302°FMin.product pressure:.....Full vacuumAir pressure:............72.5to101.5PSI(5to7bar)Valve Body CombinationsValve Body CombinationsOptionsA.Weld ends or connection types other than Tri-ClampB.Control and Indication:IndiTop,ThinkTop or ThinkTop Basic.C.Aseptic versionD.Product wetted seals in HNBR or FPM.E.Replaceable elastomer plug sealsF.Manually operatedG.NO or A/A actuatorH.High pressure actuator.I.Long stroke actuatorJ.Maintainable actuator.K.External surface finish bright.Note!For further details,see instruction ESE00364.Other valves in the same basic designThe valve range includes several purpose built valves.Below are some of the valve models available,though please use the Alfa Laval computer aided selection tool(Anytime configurator)for full access to all models and options.-Single Seat valve.-Reverse acting valve.-Long stroke valve.-Manually operated valve.-Aseptic valve.DimensionsSize2"2½"3"4"A116.7917.2818.8419.81A215.4915.9817.518.51A314.5015.0016.3617.33A415.3715.8617.4218.39A514.3514.8416.2017.17C 1.18 1.2 1.18 1.18OD 2.01 2.5 3.04ID 1.88 2.37 2.87 3.84t0.060.060.060.08E 2.40 3.19 3.39 4.69E1 2.63 2.88 3.13 3.61F10.980.98 1.18 1.18F2 1.02 1.02 1.22 1.22H 4.52 4.52 6.07 6.07J 5.83 6.427.017.80S0.610.610.810.81 M/Clamp0.500.500.500.63 Weight(lb)Standard7.18.313.315.9 Reverse Acting7.28.413.516.1A1=min.Installation measure to allow that valve can be lifted out of the tank flange/valve body(if Indication Unit is mounted,height must beadded)Standard Reverse Acting elastomer plugseal Please note!Opening/closing time will be affected by the following:-The air supply(air pressure).-The length and dimensions of the air hoses.-Number of valves connected to the same air hose. -Use of single solenoid valve for serial connected air actuator functions.-Product pressure.Air Connections Compressed air:R1/8"(BSP),internal thread.Actuator functionAir consumption(In3free air)for one stroke2"-2½"3"-4"2.17x air pressure[psi] 5.51x air pressure[psi]Pressure drop/capacitydiagrams04080120160200240280320360400440480520Note!For the diagrams the following applies:Medium:Water (68°F/20°C)Measurement:In accordance with VDI2173Pressure drop can also be calculated in Anytime configurator.Pressure drop can also be calculatedwith the following formula:Q =Cv x √∆pWhereQ =Flow (gallon/minute).Cv =gallon/minute at a pressure drop of 1psi (see table above).∆p =Pressure drop in psi over the valve.WhereQ =Flow (gallon/minute).Cv =gallon/minute at a pressure drop of 1psi (see table above).∆p =Pressure drop in psi over the valve.2.5"shut-off valve,where Cv =128(See table above).Q =Kv x √∆p160=128x √∆p(This is approx.the same pressure drop by reading the y-axis above)Pressure data for Unique 7000Series Tank OutletValve1234A =AirP=Product pressure Table 1-Shut fully closedMax.pressure in PSI without leakage at the valve seat Valve size Actuator /Valve bodycombination and directionof pressure2"2½"3"4"11046193612122659964Table 2Max.pressure in PSI against which the valve can open Valve size Actuator /Valve bodycombination and direction of pressureAir pressure (PSI)2"2½"3"4"38714513114510048714512114496Alfa Laval reserves the right to change specifications without prior notification.How to contact Alfa LavalContact details for all countriesare continually updated on our website.Please visit toaccess the information direct.L F A L A V A L i s a t r a d e m a r k r e g i s t e r e d a n d o w n e d b y A l f a L a v a l C o r p o r a t e A B . E S E 00251e n u s 1612。
neumático VL-5 2-D-1-FR-C 5 2 方向切换阀说明书
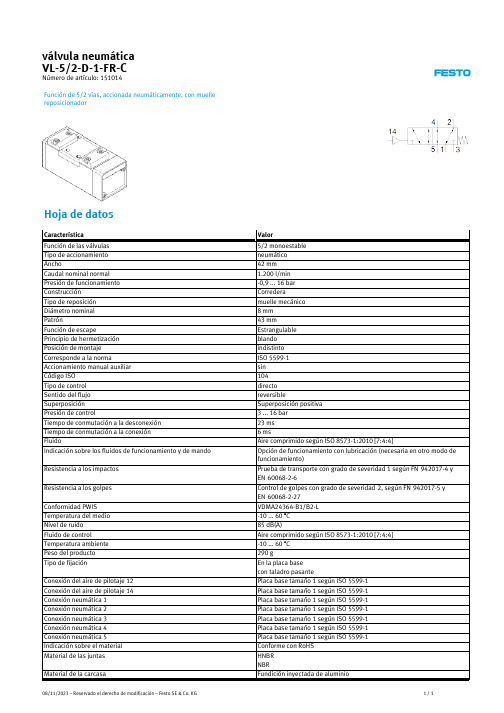
08/11/2023 – Reservado el derecho de modificación – Festo SE & Co. KG
Valor
5/2 monoestable neumático 42 mm 1.200 l/min -0,9 ... 16 bar Corredera muelle mecánico 8 mm 43 mm Estrangulable blando indistinto ISO 5599-1 sin 104 directo reversible Superposición positiva 3 ... 16 bar 23 ms 6 ms Aire comprimido según ISO 8573-1:2010 [7:4:4] Opción de funcionamiento con lubricación (necesaria en otro modo de funcionamiento) Prueba de transporte con grado de severidad 1 según FN 942017-4 y EN 60068-2-6 Control de golpes con grado de severidad 2, según FN 942017-5 y EN 60068-2-27 VDMA24364-B1/B2-L -10 ... 60 °C 85 dB(A) Aire comprimido según ISO 8573-1:2010 [7:4:4] -10 ... 60 °C 290 g En la placa base con taladro pasante Placa base tamaño 1 según ISO 5599-1 Placa base tamaño 1 según ISO 5599-1 Placa base tamaño 1 según ISO 5599-1 Placa base tamaño 1 según ISO 5599-1 Placa base tamaño 1 según ISO 5599-1 Placa base tamaño 1 según ISO 5599-1 Placa base tamaño 1 según ISO 5599-1 Conforme con RoHS HNBR NBR Fundición inyectada de aluminio
FESTO 品牌的 VUWS VTUS neumatic valves 产品说明书

Pneumatic valves VUWS/valve manifold assembly VTUS2d Internet: /catalogue/...Subject to change – 2023/08Pneumatic valves VUWS/valve manifold assembly VTUSKey featuresInnovativeFlexibleReliableEasy to install• A reliable, robust valve with a long service life• Design principle:– Poppet seat, soft-sealing (VUWS-LT)– Piston spool with sealing cartridge (VUWS-L)• Flow rate up to 1800 l/min with VUWS-LT• Flow rate up to 2300 l/min with VUWS-L• Wide range of valve functions• In-line valves can be used as indi-vidual valves or manifold valves • Variable pressure zones• Wide range of mounting options• Ergonomic and safe operation • Durable thanks to tried and tested piston spools• Reliable servicing thanks to valves that can be replaced quickly and easily• Pre-assembled units on rails• Individual valves assembled ready for installation• Common supply manifolds for mounting on one or both sides • Secure mounting on wall or H-railOrdering data – Product optionsConfigurable product This product and all its p roduct options can be ordered using the configurator.The configurator can be found under Products on the DVD or atd /catalogue/...Part no. 5765178022015802201857730480220168022019Type VUWS-20VUWS-25VUWS-30VTUS-20VTUS-25VTUS-30Pneumatic valves VUWS/valve manifold assembly VTUS Key featuresIn-line valves are designed to be usedwithout being linked pneumatically. Allpneumatic connections are on thevalve and can be equipped with fit-tings/tubing. By using a special sealset, the in-line valves can also bemounted on a manifold rail (pneumaticlinking) as semi in-line valves.Pneumatic valves VUWS have a sturdydesign that enables them to be used inharsh environments.Pneumatic valves VUWS are extremelywell suited for controlling cylinders orcompressed air networks for easyclamping and locking processes insemi-automatic assembly andmanufacturing.Equipment optionsVUWS-LT Valve functions VUWS-LT• 3/2-, 2x 3/2- and 5/2-way valves• Size 20 (21 mm)Size 25 (26.5 mm)Size 30 (31 mm)• In-line valves3/2-way valve, normallyopen, monostable:• Reset via mechanical spring• Flow direction not reversible3/2-way valve, normallyclosed, monostable:• Reset via mechanical spring• Flow direction not reversible2x 3/2-way valve, normallyopen, monostable:• Reset via mechanical spring• Flow direction not reversible2x 3/2-way valve, normallyclosed, monostable:• Reset via mechanical spring• Flow direction not reversible2x 3/2-way valve, 1x normally open,1x normally closed, monostable:• Reset via mechanical spring• Flow direction not reversible5/2-way monostable valve:• Reset via mechanical spring• Flow direction not reversible• Can also be used as 3/2-way valveby closing one outlet port5/2-way bistable valve:• Flow direction not reversible3 2023/08 – Subject to change d Internet: /catalogue/...Pneumatic valves VUWS/valve manifold assembly VTUS Key featuresEquipment optionsVUWS-LValve functions VUWS-L• Size 20 (21 mm)• Size 25 (26.5 mm)• Size 30 (31 mm)• 3/2-, 5/2- and 5/3-way valves• In-line valves3/2-way valve, normallyopen, monostable:• External pneumatic springconnection (M32U-E)• Reset via pneumatic/mechanicalspring• Flow direction reversible with me-chanical spring return or externalpneumatic spring connection• Dual-pressure operation possible• If the external pneumatic springconnection is used as signal input,the result is a dominant bistablevalve3/2-way valve, normallyclosed, monostable:• External pneumatic springconnection (M32C-E)• Reset via pneumatic/mechanicalspring• Flow direction reversible with me-chanical spring return or externalpneumatic spring connection• Dual-pressure operation possible• If the external pneumatic springconnection is used as signal input,the result is a dominant bistablevalve5/2-way monostable valve:• External pneumatic springconnection (M52-E)• Reset via pneumatic/mechanicalspring• Flow direction reversible with me-chanical spring return or externalpneumatic spring connection• Can also be used as 3/2-way valveby closing one outlet port5/2-way bistable valve:• Flow direction reversible5/3-way valve, mid-positionexhausted, pressurised or closed:• Flow direction reversible• Reset via mechanical springKey features• A maximum of 16 valve positions can be configured in the standard version• A maximum of 12 valve positions can be configured in the compact version • Valve positions 2 ... 10 in incre-ments of 1, valve positions 10 (16)in increments of 2• Manifold block with a maximum of10 valve positions• Extension module with 2 valvepositions• Common supply manifold with amaximum of 10 valve positions• Creation of pressure zones (maxi-mum 9 pressure zones in the caseof a valve manifold assembly with16 valve positions)DesignValve replacement ExtensionEach valve is attached to the manifold block using two screws. The appropri-ate seal is mounted on the valve.This means that the valves can beeasily replaced.Valve positions covered with blanking plates can be replaced with valves at a laterdate.The dimensions, mounting points and existing pneumatic installations remainunchanged.For the standard manifold block, extension modules with 2 valve positions areavailable.4d Internet: /catalogue/...Subject to change – 2023/08Pneumatic valves VUWS/valve manifold assembly VTUS Key features-NoteH-A filter must be installed upstream of valves operated in vacuum mode.This prevents any foreign matter in the intake air getting into the valve(e.g. when operating a suction cup with connector).5 2023/08 – Subject to change d Internet: /catalogue/...Pneumatic valves VUWS/valve manifold assembly VTUS Key features – Pneumatic components Creating pressure zones and separating exhaust airCompressed air is supplied and exhausted via the manifold block/common supply manifold and via supply plates.The position of the supply plates and duct separations can be freely selected with the VTUS.A pressure zone is created by isolating the internal ducts between the valve positions with an appropriate separator.The separator can be used in the following ducts:• Duct 1• Duct 3• Duct 5H--Note• Use a separator if the exhaust air pressures are high• Use at least one supply plate/supply for each pressure zone6d Internet: /catalogue/...Subject to change – 2023/0872023/08 – Subject to changed Internet: /catalogue/...Pneumatic valves VUWS/valve manifold assembly VTUSKey features – Pneumatic components VUWS-LTStandard nominal flow rate per valve on standard manifold rail Standard nominal flow rate per valve on compact manifold rail8d Internet: /catalogue/...Subject to change – 2023/08Pneumatic valves VUWS/valve manifold assembly VTUSKey features – Pneumatic components VUWS-LTStandard nominal flow rate per valve on standard manifold rail Standard nominal flow rate per valve on compact manifold rail92023/08 – Subject to changed Internet: /catalogue/...Pneumatic valves VUWS/valve manifold assembly VTUSKey features – Pneumatic components VUWS-LTStandard nominal flow rate per valve on standard manifold rail Standard nominal flow rate per valve on compact manifold rail10d Internet: /catalogue/...Subject to change – 2023/08Pneumatic valves VUWS/valve manifold assembly VTUSKey features – Pneumatic components VUWS-LTStandard nominal flow rate per valve on standard manifold rail Standard nominal flow rate per valve on compact manifold railStandard nominal flow rate per valve on standard manifold railStandard nominal flow rate per valve on compact manifold railStandard nominal flow rate per valve on standard manifold railStandard nominal flow rate per valve on compact manifold railSize 20 – Standard nominal flow rate qnN, with several valves n switched in parallel For 3/2-way valvesFor 5/2- and 5/3-way valvesStandard nominal flow rate per valve on standard manifold rail Standard nominal flow rate per valve on compact manifold railStandard nominal flow rate per valve on standard manifold rail Standard nominal flow rate per valve on compact manifold railSize 25 – Standard nominal flow rate qnN, with several valves n switched in parallel For 3/2-way valvesFor 5/2- and 5/3-way valvesStandard nominal flow rate per valve on standard manifold rail Standard nominal flow rate per valve on compact manifold railStandard nominal flow rate per valve on standard manifold rail Standard nominal flow rate per valve on compact manifold railSize 30 – Standard nominal flow rate qnN, with several valves n switched in parallel For 3/2-way valvesFor 5/2- and 5/3-way valvesStandard nominal flow rate per valve on standard manifold rail Standard nominal flow rate per valve on compact manifold railStandard nominal flow rate per valve on standard manifold rail Standard nominal flow rate per valve on compact manifold railMounting the valve manifold assembly Sturdy manifold assembly thanks to:• Four through-holes for wall mounting• H-rail mountingH- -NoteUse the thread M4 (M5 for size 30) provided on the manifold block for earthing the valve manifold assembly.Wall mounting1Sturdy wall mounting of the manifold block using four through-holes.[1] Earth terminalH-rail mountingThe H-rail mounting VAME-T-M... con -sists of two mounting clips. These are screwed to the manifold block on the left and right.The prepared manifold block is then lowered onto the H-rail from above (arrow 1) and clipped into the H-rail at the bottom (arrow 2).H- -Note• Note the max. tightening torque of the screws for H-rail mounting.• Only horizontal H-rail mounting is permissible• Mounting only permissible on H-rail TH 35-... to EN 60715• Vibration/shock loads are not permissible with H-rail mounting.• Further information on assembly a Assembly instructions for H-rail mounting VAME-T-M...Mounting individual valve VUWSWall mountingFor mounting individual valves on a flat surface, e.g. aluminium profile systems.The pneumatic valves are provided with two through-holes for attaching to the wall mounting VAME-B10-20-W.The screw set required is included with the wall mounting VAME-B10-20-W.The wall mounting VAME-B10-20-W can be used for sizes 20, 25 and 30.Foot mountingFor mounting individual valves on a flat surface, e.g. aluminium profile systems.The pneumatic valves are provided with two through-holes for attaching to the foot mounting VAME-B10-...-A.The screw set required is included with the foot mounting VAME-B10-...-A.H- -NoteFurther mounting options for foot mounting VAME-B10-...-A a Data sheet – Pneumatic valves, dimensionsPneumatic valves VUWS/valve manifold assembly VTUS Product range overviewPneumatic valves VUWS Valve functionPneumatic valves VUWS Valve functionPneumatic valves VUWS Valve functionPneumatic valves VUWS/valve manifold assembly VTUSPeripherals overview VUWS-LT, VUWS-LManifold block for 3/2-way valvesPneumatic valves VUWS/valve manifold assembly VTUS Peripherals overview VUWS-LT, VUWS-L Manifold block for 5/2 and 5/3-way valvesPneumatic valves VUWS/valve manifold assembly VTUS Peripherals overview VUWS-LT, VUWS-LCommon supply manifold for mounting on both sidesPneumatic valves VUWS/valve manifold assembly VTUS Peripherals overview VUWS-LT, VUWS-L Common supply manifold for mounting on one sideValve manifold assembly VTUS Data sheet – Valve manifold assembly-M-Flow rateSize 20:up to 700 l/minSize 25:up to 1300 l/minSize 30up to 2300 l/min2530Valve manifold assembly VTUSData sheet – Valve manifold assembly1)More information: /x/topic/kbkH--NotePort 12 on the manifold rail (number 3 in the dimensional drawing) is not usedwhen equipped with pneumatic valves.H--NotePort 12 on the manifold rail (number 3 in the dimensional drawing) is not usedwhen equipped with pneumatic valves.Valve manifold assembly VTUS Data sheet – Valve manifold assemblyValve manifold assembly VTUSData sheet – Valve manifold assemblyPneumatic valves VUWSType codes – Pneumatic valvesPneumatic valves VUWS-LT, size 20Data sheet-M-Flow rateup to 600 l/min-K-Valve width21 mm5/2-way valveM52B5250050055173192 1)If several valves are to be screwed together via through-holes to form a block, a minimum distance of 0.3 mm must be ensured by placing spacer discs between them.Pneumatic valves VUWS-LT, size 20 Data sheet1)More information: /x/topic/kbkPneumatic valves VUWS-LT, size 20 Data sheetPneumatic valves VUWS-LT, size 20 Data sheetPneumatic valves VUWS-LT, size 20 Data sheetPneumatic valves VUWS-LT, size 20 Data sheetPneumatic valves VUWS-LT, size 20 Data sheet。
Victaulic Series 725阀门说明书

ALWAYS REFER TO ANY NOTIFICATIONS AT THE END OF THIS DOCUMENT REGARDING PRODUCT INSTALLATION, MAINTENANCE OR SUPPORT.Series 725with electric actuatorSeries 725with manual actuatorSeries 725with pneumatic actuator1.0 PRODUCT DESCRIPTIONAvailable Sizes•6"/150 mmPressure Rating/Maximum Working Pressure•Up to 1000 psi/6900 kPaFunction•3-way diverter valvePipe Preparation•Victaulic Original Groove System (OGS)Application•Intended for use in Paste Backfill mining operations•Exclusively for use with pipe and Victaulic products featuring ends formed with the Victaulic OGS groove profileActuation Options•Manual actuator, hand wheel with limit stop and standard ISO FA14 mounting flange•Manual actuator with chain wheel•Multi-turn Electric actuator•Pneumatic actuator•SO 5211, FA30 mounting flange, no operator2.0 CERTIFICATION/LISTINGSProduct designed and manufactured under the Victaulic Quality Management System, as certified by LPCB inaccordance with ISO-9001:2008.Diverter ValveSeries 72508.40System No.LocationSubmitted By DateSpec Section ParagraphApproved DateDISCONTINUEDPRODUCT-REPLACEDBYSERIES725SDIVERTERVALVEREQUESTPUBLICATION8.41Body/Bonnet Coupling and Body: Ductile iron conforming to ASTM A536, grade 65-45-12.Plug: Ductile iron conforming to ASTM A-536, grade 65-45-12. PPS coating standard.Body Seal: PTFEGasket and O-Rings: (specify choice 1) G rade “T” NitrileNitrile (Orange color code). Temperature range –20°F to +180°F/–29°C to +82°C. Recommended for petroleum products, air with oil vapors, vegetable and mineral oils within the specified temperature range; except hot, dry air over +140°F/+60°C and water over +150°F/+66°C. NOT RECOMMENDED FOR HOT WATER SERVICES.1S ervices listed are General Service Guidelines only. It should be noted that there are services for which these gaskets are not compatible. Reference shouldalways be made to the latest Victaulic Gasket Selection Guide for specific gasket service guidelines and for a listing of services which are not compatible.Drive Stem: 17-4 stainless steel.Bushing: Bronze conforming to C-932.Mounting Bracket: Structural steel conforming to ASTM A-500, Grade B.Manual Actuator: Gear operator contains internal stops to prevent damage to the valve. Manual actuator withchainwheel option available.Optional: Electric Actuator, Pneumatic Actuator, No ActuatorDuctile Iron BodyISO Mounting FlangeOperatorsPlug with 5D Bend ProfilePTFE O-RingsDI SCONT INUE D PROD U C T - RE P L A C E D B Y S E R I E S 725S D I V E RT E RV A L V ER E Q U E S T P U B L I C T I O N 08.41Series 725Series 725 with Manual Actuator Series 725 with Electric ActuatorNominalSizeActualOutsideDiameterDimensions WeightA B CDManualDElectricEManualGElectricH1ManualH2ElectricIManualIElectricJElectricTManual UApproximate(Each)lbkg inchesmminchesmminchesmminchesmminchesmminchesmminchesmminchesmminchesmminchesmminchesmminchesmminchesmminchesmminchesmminchesmmElectric.ActuatorGear.Operator6 6.62528.6323.2514.3830.1333.2543.8810.1326.7531.8814.509.6318.507.88361250.0980.0150168.3727.35903637628441112255679808367245469200914567.0444.5Series 725 with Pneumatic ActuatorNominalSizeActualOutsideDiameterDimensions WeightA B CDPneumaticH3PneumaticIPneumaticJPneumaticApproximate(Each) inchesmminchesmminchesmminchesmminchesmminchesmminchesmminchesmminchesmmlbkg6 6.62528.6323.2514.3830.7540.2514.5014.381250.0150168.3727.35903637801021368364567.0DISCONTINUEDPRODUCBYSERIES725SDIEREION8.4108.40 9203 Rev G Updated 03/2016 © 2016 Victaulic Company. All rights reserved.User Responsibility for Product Selection and SuitabilityEach user bears final responsibility for making a determination as to the suitability of Victaulic products for a particular end-use application, in accordance with industry standards and project specifications, and the applicable building codes and related regulations as well as Victaulic performance, maintenance, safety, and warninginstructions. Nothing in this or any other document, nor any verbal recommendation,advice, or opinion from any Victaulic employee, shall be deemed to alter, vary, supersede, or waive any provision of Victaulic Company's standard conditions of sale, installation guide, or this disclaimer.Intellectual Property RightsNo statement contained herein concerning a possible or suggested use of any material, product, service, or design is intended, or should be constructed, to grant any license under any patent or other intellectual property right of Victaulic or any of its subsidiaries or affiliates covering such use or design, or as a recommendation for the use of suchmaterial, product, service, or design in the infringement of any patent or other intellectual property right. The terms “Patented” or “Patent Pending” refer to design or utility patents or patent applications for articles and/or methods of use in the United States and/or other countries.NoteThis product shall be manufactured by Victaulic or to Victaulic specifications. All products to be installed in accordance with current Victaulic installation/assembly instructions. Victaulic reserves the right to change product specifications, designs and standard equipment without notice and without incurring obligations.InstallationReference should always be made to the Victaulic installation handbook or installation instructions of the product you are installing. Handbooks are included with each shipment of Victaulic products, providing complete installation and assembly data, and are available in PDF format on our website at .WarrantyRefer to the Warranty section of the current Price List or contact Victaulic for details.TrademarksVictaulic and all other Victaulic marks are the trademarks or registered trademarks of Victaulic Company, and/or its affiliated entities, in the U.S. and/or other countries.Not applicable - contact Victaulic with any questions.6.0 NOTIFICATIONSNot applicable - contact Victaulic with any questions.7.0 REFERENCE MATERIALSValve Numbering SystemClass Size End PrepV 060725M – Manual Actuator E – Electric Actuator P – Pneumatic O – OtherV 11060M 725Style OperatorOperator OptionsO – NoneManual Operators M – Hand Wheel N – Chain Wheel Electrical Voltage1 – 480V, 60Hz, 3 phase2 – 575V, 60 Hz,3 phase 3 – 380V, 50 Hz, 3 phase4 – 380V, 60 Hz, 3 phase5 – 220V, 60 Hz, 3 phase6 – 400V, 50 Hz, 3 phase7 – 415V, 50 Hz, 3 phase1 – OGS Grooved 3 – Other Specify05.01: Seal Selection Guide29.01: Terms and Conditions/Warranty I-100: Field Installation HandbookI-725: Series 725 Diverter Valve Installation ManualDI SCONT NUE D PROD U C T - RE P L A C E D B Y S E R I E S 725S D I V E RT E RV A L V ER E Q U E S T P U B L I C A T I O N 08.41。
鲁奇阀门说明(翻译)

V380
107
GLOBE VALVE W.EXTENDED STUFFING BOX - BOLTED BONNET (BB) /ISO 15761 (SUBSTITUTION FOR BS 5352) -
(SUITABLE FOR AMMONIA SERVICE) / ASTM A 350 GR.LF2 - CRNI
16
WEDGE GATE VALVE - FLEXIBLE WEDGE - BOLTED BONNET (BB) / ASME - API 600 / ASTM A 216 GR.WCB - SEATS A.STEM: 13CR / RF
楔式闸阀弹性闸板BB阀体WCB阀座和阀杆13Cr RF
18.
S360G
ASTM A 351 GR.CF3 - SEATS A.STEM: CRNI / RF
15.
S357
165
WEDGE GATE VALVE BOLTED BONNET (BB) / API 602 / ASTM A 350 GR.LF2 - SEATS AND STEM: CRNI - SOUR GAS RESISTANT
截止阀BB BS1873阀体F316L或CF3M阀座阀杆CRNI
12.
V663
194
GLOBE VALVE W.REG.PLUG DISC - A.W.EXTENDED INSULATION YOKE -BOLTED BONNET (BB) / BS 1873 / ASTM A 182 GR.F316LOR
SOUR GAS RESISTANT
LURGI STANDARD GNA 0865 SEVERITY LEVEL 1 (CATEGORY 1) - ADDITIONAL TESTS 3.1B / RF
阿尔法拉瓦尔Unique RV-P调节阀门说明说明书

actuator is fitted to the valve body by means of a clamp. The Kv value is flexible as lower element can be exchanged.Manual and aseptic versions are available. Upon request, the valve can also be supplied with a normally closed (NC)actuator.Working principleThe Alfa Laval Unique RV-P Regulating Valve is controlled from a remote location by means of compressed air. An actuator with an integrated IP converter IP convertertransforms the electrical signal to a pneumatic signal. This signal conversion is based on a highly accurate and reliable contactless AMR sensor, making it insensitive to vibrations and pressure shocks. The pneumatic signal is transmitted to the integrated positioner which operates by means of the force-balance principle, ensuring that the position of the actuator piston is directly proportional to the input signal.Signal range and zero point can be adjusted individually. The actuator can be used for split-range operation by using a different measuring spring.CertificatesTECHNICAL DATAMin. product pressure:Full vacuumTemperature range:-10 °C to 140 °C (EPDM)Flow range Kv (Δ P = 1bar):0.5 to 110 m3/hMax. pressure drop:500 kPa (5 bar)Max. pressure:600 kPa (6 bar)Working pressure:400 kPa (4 bar)Max. size of particles:0.01 mmMax. oil content:0.08 ppmDew point:10 °C below ambient temp. or lowerMax. water content:7.5 g/kgInput resistance:200 ΩInductivity/capacitance:NegligiblePHYSICAL DATAOther steel parts: 1.4301(304)Product wetted seals:EPDMExternal finish:Semi-bright (blasted)Internal finish:Bright (polished) RA<0.8 µmDiaphragms:NBR with reinforced fabric insertSprings:Stainless steel uncovered/spring steel epoxy resin coatedActuator stem:PolyamideScrews, nuts:Stainless steel, polyamideOther parts:Stainless steelValve body combinations64-542200300AccuracyDeviation:≤1.5%Hysteresis:≤0.5%Sensitivity:<0.1%Influence of air supply pressure:≤0.1% between 1.4 and 6 barAir consumption at steady state condition:With 0.6 bar signal pressure and supply pressures up to 6 bar ≤100 In/h Ambient temperature:-25 °C to +70 °CProtection class:IP 66Flow sizes/tube connections1.0 E1038403277-52 E1238403277-5 4 E1438403277-5 8 E2338403277-5 16 E2938403277-5 25 E3851503277-5 32 E48.551503277-5 40 E4263.5653277-5 64 L5163.5653277-5 75 L5176.1803277-5110 L72101.61003277-5Options•Male parts or clamp liners in accordance with required standard•Product wetted seals of HNBR or Fluorinated rubber (FPM)•Profibus communication•Aseptic configuration Max 8 barA- aseptic411426412446470488414427418454472490 E566367859696576470899898 G49.561818611911949.5627887120120 H168168168168168280168168168168168280 OD385163.576.1101.6101.641537085104104 ID34.847.860.372.997.697.638506681100100 t 1.6 1.6 1.6 1.622 1.5 1.52222M/ISO clamp212121212121------M/DIN clamp------212128282828 M/DIN male------222325253030 M/SMS male202024243535------Weight kg8.29.39.711.215.424.98.29.39.711.215.424.9Capacity diagram For Δ P= 100 kPa (1bar).Figure 1. StandardFigure 2. Aseptic*Recommended working areaNote! For the diagram the following applies:Medium: Water (20 °C).Measurement: In accordance with VDI 2173.Alfa Laval recommend max. flow velocity in tubing and valves to be 5 m/sec.Conversion Table 100 kPa = 1 bar = 14.5 PSI 10 mm = 0.39 inch 10 m 3/h = 44.03 US GPM Pressure drop calculationThe Kv designation is the flow rate in m 3/h at a pressure drop of 1 bar when the valve is fully open (water at 20°C or similar liquids). To select the Kv value it is necessary to calculate the Kv q value using the following formula:Where:Kv q = Kv value at specific flow and specific pressure drop Q = Flow rate (m 3/h)Δ P = Pressure drop over valve (bar)Electrical connectionElectrical connection - Analogue 4-20 mA Positioner 37252405-0035Cable gland Cover240500362405-0037Terminal screws4-20 mA control signalRoute the two-wire line to the screw terminals marked “11 and 12”, whereby the correct polarity has to be ensured 1.Open the cover of the positioner for electrical connection2.Fit the cable through the cable gland and connect the cable wires to the terminal screws. (+11 and -12)3.Tighten the cable gland and close the cover of the positioner Electrical connection - Profibus PA Positioner 3730-42405-0035Cable gland Cover2405-00382405-0039Terminal screwsBus control signalRoute the two-wire bus line to the screw terminals marked “IEC 1158-2”, whereby no polarity has to be observed 1.Open the cover of the positioner for electrical connection2.Fit the bus cable through the cable gland and connect the cable wires to the terminal screws. (IEC 1158-2)3.Tighten the cable gland and close the cover of the positionerBy searching on positioner type 3730-4 you can either retrieve the GSD files for PROFIBUS PA communication directly from the World Wide Web server of Samson or the PROFIBUS User OrganizationThis document and its contents are subject to copyrights and other intellectual property rights owned by Alfa Laval Corporate AB. No part of this document may be copied, re-produced or transmitted in any form or by any means, or for any purpose, without Alfa Laval Corporate AB’s prior express written permission. Information and services provided in this document are made as a benefit and service to the user, and no representations or warranties are made about the accuracy or suitability of this information and these services for any purpose. All rights are reserved.200003961-1-EN-GB© Alfa Laval Corporate AB How to contact Alfa LavalUp-to-date Alfa Laval contact details for all countries are always availableon our website at 。
Ruelco VC-2 速度检测阀门操作手册说明书

“VC-2”VELOCITY CHECK VALVE OPERATION MANUAL OMP # 20V2- 8/05 1.0 PRINCIPLE OF OPERATIONThe Ruelco VC-2 velocity checkvalve is a 2-way control valve. It isideal for line brake or process upsetdetection when using pipelineprocess pressure to operate anactuated valve. The valve is designedto operate with liquid or gas processfluids with pressures ranging from100 to 6,000 PSI. The valveincorporates a unique soft sealdesign to ensure zero leakage whilealso providing trip indication.A red indication band on the shaftindicates that the valve is in thetripped position. With the valve inthe tripped position, supply pressureis blocked from entering the “OUT”port.The valve is manually reset bypushing down on the knob. The knobis held pressed in the down positionuntil the pressure equalizes on bothsides after which the shaft stays inthat position. Pressure loss in thedownstream side of the “OUT” portcauses the valve to trip, therebyexposing a red indication band on theshaft.2.0 INSTALLATIONThe “VC-2” can be supported bypiping from the sense port in eithervertical or horizontal positions. If thevalve is mounted horizontally, it isrecommended that the small venthole in the side of the body beoriented in a downward position.This will prevent any debris fromaccumulating in the body bore.Proper pipe thread sealant should beused on any pipe fittings threadedinto the valve “OUT” port. Ifstainless steel fittings are used, asealant that will prevent galling isrequired. The supply fluid flowingthrough the valve body should befiltered and free of large particles.When the valve is mounted using the½” NPT base connection and thevalve “OUT” port is not in thedesired position after the baseconnection is adequately tightened,DO NOT loosen the base connectionto re-position the port. Instead,remove the valve and remake the ½”NPT connection.3.0DISASSEMBLY (See Spec Sheet)Tools and materials required forproper disassembly, repair andassembly are as follows:1.7/16” open end wrench.2.Locktite3.High quality silicone baselubricant.4.An appropriate safetysolvent.3.1 FULLDISASSEMBLY1.If the valve is installed in anoperating instrument system,precautions should be taken toavoid any unwanted reactions.Make sure the valve is isolatedfrom all pressure.2.Place the 7/16” wrench on thelock nut (Item 2)and rotate itclockwise while holding the knob(Item 1) until the knob is loose.Rotate the knobcounterclockwise and remove itfrom the shaft (Item 7). At thistime also remove the lock nut.3.Rotate the Cap (Item 3) counterclockwise and remove. Next,Place the knob back on the shaftand rotate until it stops. Now,pull the shaft out of the body.4.The seals on the shaft may nowbe replaced5.Next, with the 7/16” wrench,rotate the Retainer Screw (Item13) Counter clockwise andremove it from the body. Makesure you do not lose the PushRod (Item 10) or the ball (Item12).6.Remove the small o-ring (Item11) in the body.7.At this time place the Sleeve(Item 4) over the shaft. Nextplace the Knob onto the shaft.While applying pressure to theknob, hold the sleeve in placewith your thumb and fore fingerand push the shaft back into thebody.8.Remove the knob from the shaftand rotate the Cap onto the bodyin a clockwise direction. Then,place the lock nut and knob backonto the shaft. 9.The shaft should slide up anddown easily.10.Place the Ball Seal into the Body,making sure that the seal is flushwith the bottom face.11.Then put the rod into the holefollowed by the ball and finally,thread the Retainer screw back inplace. Locktite is recommendedfor the Retainer Screw threads.4.0 RECOMMENDED MANITENNACEOperate Manually – Every thirty (30)days.Disassemble, inspect and lubricate –Yearly or as required.Replace all seals – Every two (2)years or as required.。
L-352-WAY 蒸汽阀门系列说明书

)5$1&( ZZZRPHJDIU
*(50$1< ZZZRPHJDGH 'HFNHQSIURQQ *HUPDQ\
%(1(/8; ZZZRPHJDQO
ports are not marked.
Dimensions: mm (in)
VALVE H
P
C
L
W
SV232 93.0 (3.66) 78.0 (3.07) 52.3 (2.06) 74.9 (2.95) 53.1 (2.09)
SV233 93.0 (3.66) 78.0 (3.07) 52.3 (2.06) 74.9 (2.95) 53.1 (2.09)
0 45 145 293 30 to 100 ms 350 to 900 ms
SV234
180
3⁄4
5⁄8"
5.5 EPDM
0 45 145 293 30 to 100 ms 350 to 900 ms
SV235
325 1
1"
11.7 EPDM
0 45 145 293 30 to 100 ms 350 to 900 ms
Operation: Direct lift Wetted Parts: Brass, stainless steel, copper and seal Medium: Liquid or gases Max Static Pressure: 5 times max psid Ambient Temp: -9 to 50°C (15 to 122°F) Mounting: Pipe mounting, any direction Power: 22 W, 120 Vac, 50 to 60 Hz, Class H
DynaQuip 阀门说明书

MANUALBUTTERFLY V ALVESEXCELLENCE IN OIL, AGRICULTURAL AND MANUFACTURING FLOW CONTROLDYNAFLY 700/722 SERIES: HVAC, COMMERCIAL, UTILITY AND GENERAL INDUSTRIAL APPLICATIONS a valve customized to your needs.Cartridge Seated | 200 PSI (2”-12”) * 150 PSI (14”-24”) CWPVisit for more informationDynaQuip Controls • 10 Harris Industrial Park • St. Clair, MO 63077 • Tel. 800-545-3636 Sizes2”-24”• W afer (700) or Lug (722) Style Bodies • C artridge Style Seat • L ow Torque• E xtended Neck for Insulating • O ne-Piece 416 SS Stem with Precision Taper PinsStabilizes seat to prevent movement. give a highly efficient seal; prevents 2”-12” Direct Mount for ActuationPrecision Profile Disc: Ductile iron provides bubble-tight shut-off and assures minimum torque and longer seat life.Finished Disc Flats: These mate with seat flats to give a highly efficient seal; prevents leakage into the shaft area.Optional Disc Material: Aluminum bronze, 316 stainless steel.One-Piece Thru Shaft: Ensures dependability and positive disc position. 416 stainless is standard.Precision Taper Pins: Ensure positive, vibration proof, shaft to disc connection. Easily field replaceable. 316 stainless standard.Supported Shaft Seal: Bondingof elastomer to phenolic backing ring protects against distortion, a common cause of shaft leakage. Teflon Bushings Standard (Four): Furnishes shaft support at three locations for positive shaft alignment and actuator support and less friction. Luberized bronze optional.DYNAFLY 700/722 SERIES: HVAC, COMMERCIAL, UTILITY AND GENERAL INDUSTRIAL APPLICATIONSAbout DynaQuipNow entering our sixth decade, DynaQuip Controls® continues its long-standing commitment to designing and manufacturing superior products and providing outstanding personal service. Electric actuators and valve automation designs lead our drive as we focus on the products of tomorrow. Today, our product lines and design expertise have grown to include electric actuators, electronic actuator controls, automated ball valves, automated butterfly valves, pneumatic actuators, manual ball valves and butterfly valves.Our VisionTo satisfy the individual needs and demands of our industrial, commercial and residential customers by providing innovative and solutions oriented valve and fluid control products.Visit for more informationDynaQuip Controls • 10 Harris Industrial Park • St. Clair, MO 63077 • Tel. 800-545-3636 • Fax. 636-629-5528MANUALBUTTERFLY V ALVESDisc: Ni-coated ductile iron, 316 stainless steel Stem: 416 stainless steel Resilient Seat: EPDM, Buna-N Stem Bushings: PTFEDisc Taper Pins: 316 stainless steel O-Ring: EPDM, Buna-N Set Screws: Carbon steelP HENOLIC BACKED SEAT PROVIDES THE FOLLOWING ADVANTAGES:1. W ide flange-face sealing area provides a tight flange-to-valve seal without the use of gaskets.2. A llows tight shut-off with minimum movement of the seatmaterial to reach the closed position in the center of the seat for ease of actuation.3. T he wide sealing area around the shaft provides a positive seal isolating the shaft from the media.more information。
- 1、下载文档前请自行甄别文档内容的完整性,平台不提供额外的编辑、内容补充、找答案等附加服务。
- 2、"仅部分预览"的文档,不可在线预览部分如存在完整性等问题,可反馈申请退款(可完整预览的文档不适用该条件!)。
- 3、如文档侵犯您的权益,请联系客服反馈,我们会尽快为您处理(人工客服工作时间:9:00-18:30)。
7.
V386
46
GLOBE VALVE W.REG.PLUG DISC BOLTED BONNET (BB) / BS 1873 /
ASTM A 352 GR.LCB - SEATS AND STEM: CRNI - SOUR GAS RESISTANT
16、23、77、140
WEDGE GATE VALVE W.GEAR - FLEXIBLE WEDGE - BOLTED BONNET (BB) /ASME - API 600 / ASTM A 216 GR.WCB - SEATS A.STEM: 13CR / RF
楔式闸阀弹性BB API600阀体WCB阀座和阀杆13Cr RF
ASTM A 351 GR.CF3M- SEATS A.STEM: CRNI / RF
加长支架
13.
V685
53
GLOBE VALVE W.REG.PLUG DISC - BOLTED BONNET (BB) / BS 1873 /ASTM A 182 GR.F304LOR ASTM A 351 GR.CF3 - SEATS A.STEM: CRNI / RF
19.
S371
31、100、158
WEDGE GATE VALVE - FLEXIBLE WEDGE - BOLTED BONNET (BB) / ASME - API 600 / ASTM A 352 GR.LCB - SEATS A.STEM: CRNI / RF
楔式闸阀弹性
20.
S385
45
WEDGE GATE VALVE BOLTED BONNET (BB) / API 602 / ASTM A 350 GR.LF2 - SEATS AND STEM: CRNI - SOUR GAS RESISTANT
截止阀BB BS1873阀体F316L或CF3M阀座阀杆CRNI
12.
V663
194
GLOBE VALVE W.REG.PLUG DISC - A.W.EXTENDED INSULATION YOKE -BOLTED BONNET (BB) / BS 1873 / ASTM A 182 GR.F316LOR
LURGI STANDARD GNA 0865 SEVERITY LEVEL 1 (CATEGORY 1) -ADDITIONAL TESTS 3.1B / RF
截止阀BB BS1873阀体LCB阀座和阀杆CRNi
8.
V388
166
GLOBE VALVE W.REG.PLUG DISC BOLTED BONNET (BB) / BS 1873 /
LURGI STANDARD GNA 0865 SEVERITY LEVEL 2 (CATEGORY 2) -
ADDITIONAL TESTS 3.1B / RF
截止阀BB BS1873阀体WCB阀座和阀杆CRNI抗酸性气体增加试验
11.
V661
70、131、185
GLOBE VALVE W.REG.PLUG DISC - BOLTED BONNET (BB) / BS 1873 /ASTM A 182 GR.F316LOR ASTM A 351 GR.CF3M- SEATS A.STEM: CRNI / RF
(NO COPPER PERMITTED) /RF
截止阀加长BB ISO 15761(或BS5352)适用于氨水阀体LF2不含铜RF
6.
V382
108
GLOBE VALVE W.EXTENDED STUFFING BOX - BOLTED BONNET (BB) /BS 1873 - (SUITABLE FOR AMMONIA SERVICE) / ASTM A 352 GR.LCB - CRNI(NO COPPER PERMITTED) / RF
SOUR GAS RESISTANT
LURGI STANDARD GNA 0865 SEVERITY LEVEL 2 (CATEGORY 2) - ADDITIONAL TESTS 3.1B / RF
楔式闸阀弹性闸板BB阀体LCB阀座和阀杆CRNI抗酸性气体RF
增加TEST3.1 B试验
17.
S360
SOUR GAS RESISTANT
LURGI STANDARD GNA 0865
SEVERITY LEVEL 1 (CATEGORY 1) - ADDITIONAL TESTS 3.1B / RF
楔式闸阀弹性BB API600阀体WCB阀座和阀杆CRNi抗酸性气体增加试验
24.
S397
114
WEDGE GATE VALVE BOLTED BONNET (BB) / API 602 / ASTM A 105 - SEATS AND STEM: CRNI - SOUR GAS RESISTANT
16
WEDGE GATE VALVE - FLEXIBLE WEDGE - BOLTED BONNET (BB) / ASME - API 600 / ASTM A 216 GR.WCB - SEATS A.STEM: 13CR / RF
楔式闸阀弹性闸板BB阀体WCB阀座和阀杆13Cr RF
18.
S360G
ADDITIONAL TESTS 3.1B / RF
截止阀BB BS1873阀体WCB阀座和阀杆CRNI抗酸性气体增加试验
10.
V398
115
GLOBE VALVE W.REG.PLUG DISC BOLTED BONNET (BB) / BS 1873 /
ASTM A 216 GR.WCB - SEATS AND STEM: CRNI - SOUR GAS RESISTANT
LURGI STANDARD GNA 0865 SEVERITY LEVEL 2 (CATEGORY 2) - ADDITIONAL TESTS 3.1B / RF
楔式闸阀BB API 602阀体A105阀座和阀杆CRNi抗酸性气体增加试验
25.
S398
115
WEDGE GATE VALVE - FLEXIBLE WEDGE - BOLTED BONNET (BB) / ASME - API 600 / ASTM A 216 GR.WCB - SEATS AND STEM: CRNI -
截止阀氨水RF WCB (不含铜)
4.
V371
31、100、158
GLOBE VALVE W.REG.PLUG DISC - BOLTED BONNET (BB) / BS 1873 /ASTM A 352 GR.LCB - SEATS A.STEM: CRNI / RF
截止阀BB BS1873阀体LCB阀座和阀杆CRNI RF
法兰截止阀WCB阀杆13Cr RF
3.
V365
92
GLOBE VALVE W.REG.PLUG DISC A.EXTENDED STUFFING BOX -
BOLTED BONNET (BB) / BS 1873 - (SUITABLE FOR AMMONIA SERVICE) /ASTM A 216 GR.WCB - CRNI (NO COPPER PERMITTED) / RF
ASTM A 352 GR.LCB - SEATS AND STEM: CRNI - SOUR GAS RESISTANT
LURGI STANDARD GNA 0865 SEVERITY LEVEL 2 (CATEGORY 2) -
ADDITIONAL TESTS 3.1B / RF
截止阀阀体LCB抗酸性气体阀座和阀杆铬镍标准BS 1873
低温甲醇洗阀门型号说明
序号
型号
页码
lurge标准描述
1.
V355
92
GLOBE VALVE W. REG. PLUG DISC A. EXTENDED STUFFING BOX -
BOLTED BONNET (BB) / ISO 15761 (SUBSTITUTION_FOR BS 5352) -
(SUITABLE FOR AMMONIA SERVICE) / ASTM A 105 - CRNI
LURGI STANDARD GNA 0865 SEVERITY LEVEL 2 (CATEGORY 2) - ADDITIONAL TESTS 3.1B / RF
16.
S358
166
WEDGE GATE VALVE - FLEXIBLE WEDGE - BOLTED BONNET (BB) / ASME - API 600 / ASTM A 352 GR.LCB - SEATS AND STEM: CRNI -
鲁奇标准0865
9.
V396
39GLOBE VALV来自 W.REG.PLUG DISC BOLTED BONNET (BB) / BS 1873 /
ASTM A 216 GR.WCB - SEATS AND STEM: CRNI - SOUR GAS RESISTANT
LURGI STANDARD GNA 0865 SEVERITY LEVEL 1 (CATEGORY 1) -
LURGI STANDARD GNA 0865 SEVERITY LEVEL 1 (CATEGORY 1) - ADDITIONAL TESTS 3.1B / RF
楔式闸阀BB API602阀体A105阀座和阀杆CRNi抗酸性气体增加试验
23.
S396
38
WEDGE GATE VALVE - FLEXIBLE WEDGE - BOLTED BONNET (BB) / ASME - API 600 / ASTM A 216 GR.WCB - SEATS AND STEM: CRNI -