汽车齿轮热处理工艺
汽车齿轮的热处理工艺与质量控制

汽车齿轮的热处理工艺与质量控制汽车作为现代社会重要的交通工具,其性能和可靠性在很大程度上取决于各个零部件的质量。
而齿轮作为汽车传动系统中的关键部件,其质量更是至关重要。
其中,热处理工艺在汽车齿轮的制造过程中起着决定性的作用,它直接影响着齿轮的强度、硬度、耐磨性以及抗疲劳性能等。
同时,严格的质量控制措施也是确保齿轮质量稳定可靠的重要保障。
一、汽车齿轮的工作条件和性能要求汽车齿轮在工作过程中承受着巨大的载荷和复杂的应力。
它们需要在高速旋转的情况下传递动力,并且要在不同的工况下保持稳定的性能。
因此,汽车齿轮通常需要具备以下性能要求:1、高强度和高韧性:以承受弯曲、接触和冲击等多种应力,防止齿轮在工作过程中发生断裂或变形。
2、高硬度和耐磨性:减少齿面的磨损,延长齿轮的使用寿命。
3、良好的抗疲劳性能:能够经受长时间的循环载荷作用而不出现疲劳裂纹。
4、良好的齿面精度和表面质量:保证齿轮的传动平稳性和低噪声。
二、汽车齿轮常用的热处理工艺1、渗碳淬火渗碳淬火是汽车齿轮制造中应用最广泛的热处理工艺之一。
它是将齿轮放入含有碳源的介质中,在高温下使碳原子渗入齿轮表面,然后进行淬火处理,以获得高硬度、高耐磨性的表面和良好韧性的心部。
渗碳淬火后的齿轮表面硬度可达 58-62HRC,心部硬度则在 30-45HRC之间。
渗碳工艺通常可分为气体渗碳、液体渗碳和固体渗碳。
气体渗碳由于其可控性好、渗碳质量高而被广泛应用。
在渗碳过程中,渗碳温度、渗碳时间、碳势等参数的控制至关重要。
渗碳温度一般在 900-950℃之间,渗碳时间则根据齿轮的尺寸和要求的渗碳层深度来确定。
淬火工艺则通常采用油淬或水淬。
油淬可以减少齿轮的变形,但淬火硬度相对较低;水淬则可以获得更高的硬度,但变形较大。
因此,在实际生产中需要根据齿轮的具体情况选择合适的淬火介质。
2、感应淬火感应淬火是利用电磁感应原理,在齿轮表面产生涡流,从而迅速加热齿轮表面,然后进行淬火处理。
汽车齿轮使用的热处理工艺及其作用

汽车齿轮使用的热处理工艺及其作用一、热处理工艺的概念及作用热处理是通过加热、保温和冷却等工艺方法,使金属材料在固态结构下发生物理或物理化学变化,从而获得一定的组织和性能。
热处理可以改善金属材料的力学性能、物理性能和化学性能,提高材料的硬度、强度、韧性和耐磨性等。
二、汽车齿轮的热处理工艺1. 淬火淬火是指将汽车齿轮加热至临界温度以上,然后迅速冷却至室温。
这一过程能够使齿轮获得高硬度和强度,提高其耐磨性和抗疲劳性能。
淬火后的齿轮组织为马氏体组织,具有较高的硬度和韧性。
2. 调质调质是指将淬火后的齿轮加热至适当的温度,然后保温一段时间,最后在空气中冷却。
调质可以消除淬火过程中产生的内应力,提高齿轮的韧性和抗冲击性能。
调质后的齿轮组织为马氏体和回火组织的混合组织,既有一定的硬度,又有较高的韧性。
3. 淬火回火淬火回火是将淬火后的齿轮加热至一定温度,保温一段时间,然后在适宜介质中迅速冷却,最后再次加热至较低的温度进行回火。
淬火回火工艺能够使齿轮获得既有较高硬度,又有一定韧性和韧性的组织结构,提高齿轮的强度、韧性和耐磨性。
4. 等温淬火等温淬火是将汽车齿轮在加热至临界温度后保温一段时间,然后在适宜介质中迅速冷却。
等温淬火工艺能够使齿轮获得细小的马氏体组织,具有较高的硬度和强度,提高齿轮的耐磨性和抗疲劳性能。
三、热处理工艺对汽车齿轮的作用1. 提高齿轮的硬度和强度:通过热处理工艺,汽车齿轮的硬度和强度得到提高,能够更好地抵抗外界的冲击和压力,延长使用寿命。
2. 提高齿轮的耐磨性:热处理工艺能够使齿轮表面形成硬度较高的层,提高齿轮的耐磨性,减少磨损,提高传动效率。
3. 提高齿轮的韧性和韧性:通过热处理工艺,齿轮的组织结构得到调整,能够提高齿轮的韧性和韧性,增强其抗冲击性能。
4. 改善齿轮的尺寸稳定性:热处理工艺能够消除齿轮加工过程中产生的内应力,使齿轮的尺寸更加稳定,减少变形和变位。
5. 提高齿轮的抗腐蚀性:热处理工艺可以通过改变齿轮的组织结构,提高其抗腐蚀性能,延长使用寿命。
齿轮热处理工艺
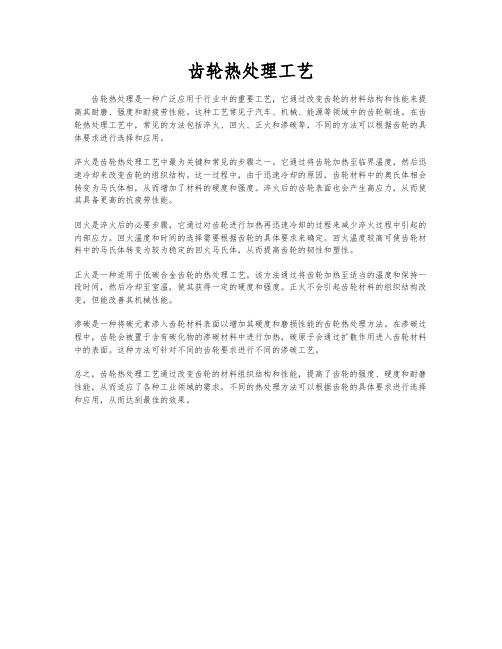
齿轮热处理工艺齿轮热处理是一种广泛应用于行业中的重要工艺,它通过改变齿轮的材料结构和性能来提高其耐磨、强度和耐疲劳性能。
这种工艺常见于汽车、机械、能源等领域中的齿轮制造。
在齿轮热处理工艺中,常见的方法包括淬火、回火、正火和渗碳等,不同的方法可以根据齿轮的具体要求进行选择和应用。
淬火是齿轮热处理工艺中最为关键和常见的步骤之一。
它通过将齿轮加热至临界温度,然后迅速冷却来改变齿轮的组织结构。
这一过程中,由于迅速冷却的原因,齿轮材料中的奥氏体相会转变为马氏体相,从而增加了材料的硬度和强度。
淬火后的齿轮表面也会产生高应力,从而使其具备更高的抗疲劳性能。
回火是淬火后的必要步骤,它通过对齿轮进行加热再迅速冷却的过程来减少淬火过程中引起的内部应力。
回火温度和时间的选择需要根据齿轮的具体要求来确定。
回火温度较高可使齿轮材料中的马氏体转变为较为稳定的回火马氏体,从而提高齿轮的韧性和塑性。
正火是一种适用于低碳合金齿轮的热处理工艺。
该方法通过将齿轮加热至适当的温度和保持一段时间,然后冷却至室温,使其获得一定的硬度和强度。
正火不会引起齿轮材料的组织结构改变,但能改善其机械性能。
渗碳是一种将碳元素渗入齿轮材料表面以增加其硬度和磨损性能的齿轮热处理方法。
在渗碳过程中,齿轮会被置于含有碳化物的渗碳材料中进行加热,碳原子会通过扩散作用进入齿轮材料中的表面。
这种方法可针对不同的齿轮要求进行不同的渗碳工艺。
总之,齿轮热处理工艺通过改变齿轮的材料组织结构和性能,提高了齿轮的强度、硬度和耐磨性能,从而适应了各种工业领域的需求。
不同的热处理方法可以根据齿轮的具体要求进行选择和应用,从而达到最佳的效果。
汽车后桥齿轮热处理

汽车后桥齿轮热处理学院:化工装备学院专业/班级:材料成型及控制工程1301班学号: *******XX学生姓名: XXX***师:***时间: 2015年12月前言金属材料是人类文明发展的产物,石器时代之后的铜器时代、铁器时代都是具有非常明显的金属材料使用的时代。
近年来我国的基础设施,汽车行业发展迅速。
通常汽车零部件的受力情况复杂,那么汽车零件就需要更高的工艺。
汽车后桥齿轮一般是指后驱汽车齿轮差速器。
在差速器中,通过齿轮来增加扭转力矩,调节左右两车轮的转速,并通过齿轮将发动机的动力传递到主动轮,驱动汽车运行。
因此对齿轮耐磨性、疲劳强度、心部强度和冲击韧性等方面要求比一般齿轮高。
热处理是一项广泛应用的一项重要的基础工艺之一。
金属材料在严格控制的加热和冷却条件下进行处理,通过改变材料的部组织来达到人们所要求的的使用性能或使用寿命。
在充分发挥材料潜能,节约能源,进行清洁生产和人类社会可持续发展上,热处理技术的拓展是不可忽视的。
目录前言题目 (1)1.汽车后桥从动圆柱斜齿轮的工作条件和性能要求 (2)1.1汽车后桥从动圆柱斜齿轮的工作条件 (2)1.2 性能要求 (2)2.选择材料 (2)2.1 材料使用性能 (2)2.2 材料的工艺性能 (3)2.3 材料的经济性 (3)3.汽车后桥齿轮的工艺路线 (3)3.1 备料 (3)3.2 下料 (4)3.3 锻造 (4)3.4正火 (5)3.5 机械加工 (6)3.6渗碳、淬火及低温回火 (6)3.7喷丸 (6)3.8精加工 (7)3.9校直、检验 (7)参考文献 (7)题目一汽车后桥从动圆柱斜齿轮,其形状尺寸如下图所示。
要求齿轮表面耐磨,硬度为58-62HRC,轮齿中心的硬度为35-40HRC ,变形量要求尽可能小,齿中心的k A 冲击吸收功不应小于55J ,屈服强度s 不小于pa M 840。
齿轮节圆直径为125mm ,模数m=5。
试选择合适的材料,制定加工工艺路线,说明每步热处理的目的,工艺规及组织,并作出热处理工艺卡。
汽车齿轮热处理工艺

汽车齿轮热处理工艺嘿,朋友!咱今天来聊聊汽车齿轮那神奇的热处理工艺。
你知道吗?汽车齿轮就像是汽车身体里的小战士,它们得足够强大、坚韧,才能在高速运转的世界里冲锋陷阵。
而热处理工艺,就是让这些小战士变得厉害的魔法。
想象一下,齿轮在汽车里不停地转动,承受着巨大的压力和摩擦力。
如果没有经过恰当的热处理,它们可能很快就会累垮,甚至罢工。
这就好比一个没经过训练的新兵直接上战场,那不是等着被打得落花流水嘛!热处理工艺中的退火,就像是让齿轮先做个放松的瑜伽。
把齿轮加热到一定温度,然后慢慢冷却,让它内部的组织结构变得更均匀,减少应力。
这就好比给齿轮来了一次全身的按摩,让它舒舒服服地准备迎接挑战。
淬火呢,那可就是一场烈火的考验啦!把齿轮迅速加热到高温,然后猛地放到冷却介质里,让它瞬间变得坚硬无比。
这就像把一块普通的铁扔到炼钢炉里,出来就成了削铁如泥的宝剑!回火呢,又像是给刚刚淬火完的齿轮一个温暖的抱抱。
再次加热,让它的硬度和韧性达到一个完美的平衡。
不然,太硬了容易脆,太软了又没力气,这可不行。
渗碳处理,就像是给齿轮穿上一层厚厚的铠甲。
让碳原子渗进齿轮表面,增加表面的硬度和耐磨性。
这不就像给战士的盔甲加厚加固,让敌人的攻击都无可奈何嘛!在实际操作中,每一步的温度、时间、冷却速度,都得拿捏得恰到好处。
这就好比炒菜,火候、时间、调料,一个都不能错,要不然这道菜就不美味了。
而且,这热处理工艺可不是随便玩玩的,得有专业的设备和技术人员。
他们就像是齿轮的魔法师,用他们的经验和智慧,让每一个齿轮都能焕发出强大的力量。
要是这热处理工艺没做好,那后果可不堪设想!汽车可能会在路上抛锚,那得多让人头疼啊!所以说,这汽车齿轮的热处理工艺,那可是汽车制造里的关键一步,绝对不能马虎!总之,汽车齿轮的热处理工艺就像是一场精心编排的舞蹈,每个动作都要精准到位,才能跳出精彩的篇章,让汽车跑得又快又稳!。
20CrMnTi解放牌载重汽车变速箱变速齿轮热处理工艺设计

目录1. 绪论┄┄┄┄┄┄┄┄┄┄┄┄┄┄┄┄┄┄┄┄┄┄┄┄┄3 1.1 引言┄┄┄┄┄┄┄┄┄┄┄┄┄┄┄┄┄┄┄┄┄┄┄┄┄3 1.2 20CrMnTi钢的基本性质┄┄┄┄┄┄┄┄┄┄┄┄┄┄┄┄┄4 1.2.1 钢的化学成分和力学性能┄┄┄┄┄┄┄┄┄┄┄┄┄┄┄4 1.2.2 合金元素的作用┄┄┄┄┄┄┄┄┄┄┄┄┄┄┄┄┄┄┄5 1.2.3淬透性┄┄┄┄┄┄┄┄┄┄┄┄┄┄┄┄┄┄┄┄┄┄┄5 1.3解放牌汽车变速箱变速齿轮的热处理工艺设计┄┄┄┄┄┄┄5 1.3.1 服役条件┄┄┄┄┄┄┄┄┄┄┄┄┄┄┄┄┄┄┄┄┄┄6 1.3.2 失效形式┄┄┄┄┄┄┄┄┄┄┄┄┄┄┄┄┄┄┄┄┄┄61.3.3性能要求┄┄┄┄┄┄┄┄┄┄┄┄┄┄┄┄┄┄┄┄┄┄72. 20CrMnTi钢变速齿轮生产工艺路线及分析┄┄┄┄┄┄┄┄┄9 2.120CrMnTi钢变速齿轮生产工艺路线┄┄┄┄┄┄┄┄┄┄┄┄9 2.2各种加工工艺路线的分析┄┄┄┄┄┄┄┄┄┄┄┄┄┄┄┄9 2.2.1等温正火┄┄┄┄┄┄┄┄┄┄┄┄┄┄┄┄┄┄┄┄┄┄9 2.2.2渗碳+淬火+回火┄┄┄┄┄┄┄┄┄┄┄┄┄┄┄┄┄┄┄9 2.2.3喷丸┄┄┄┄┄┄┄┄┄┄┄┄┄┄┄┄┄┄┄┄┄┄┄┄112.2.4检验┄┄┄┄┄┄┄┄┄┄┄┄┄┄┄┄┄┄┄┄┄┄┄┄113. 各种热处理后的金相组织分析┄┄┄┄┄┄┄┄┄┄┄┄┄┄12 3.1 20CrMnTi等温正火后金相组织┄┄┄┄┄┄┄┄┄┄┄┄┄123.2 20CrMnTi淬火、回火处理金相组织┄┄┄┄┄┄┄┄┄┄┄┄134. 热处理工艺过程中的质量检验项目┄┄┄┄┄┄┄┄┄┄┄┄154.1渗碳淬火后齿轮的检验项目、内容和要求┄┄┄┄┄┄┄┄┄154.2渗碳齿轮的常见缺陷及防止措施┄┄┄┄┄┄┄┄┄┄┄┄┄165. 质量控制与检验方法┄┄┄┄┄┄┄┄┄┄┄┄┄┄┄┄┄┄19 5.1随炉试样检验┄┄┄┄┄┄┄┄┄┄┄┄┄┄┄┄┄┄┄┄┄19 5.2齿轮热处理质量检验┄┄┄┄┄┄┄┄┄┄┄┄┄┄┄┄┄┄22 总结┄┄┄┄┄┄┄┄┄┄┄┄┄┄┄┄┄┄┄┄┄┄┄┄┄┄┄24 致谢┄┄┄┄┄┄┄┄┄┄┄┄┄┄┄┄┄┄┄┄┄┄┄┄┄┄┄25 参考文献┄┄┄┄┄┄┄┄┄┄┄┄┄┄┄┄┄┄┄┄┄┄┄┄┄261. 绪论1.1引言热处理工艺是金属材料工程的重要组成部分。
汽车齿轮热处理工艺

汽车、拖拉机的变速箱齿轮多半用低碳渗碳钢制造,而机床变速箱多半用中碳(合金)2011-4-10 21:07提问者:991495331|浏览次数:289次我来帮他解答2011-4-11 11:10满意回答合金渗碳钢1. 用途主要用于制造汽车、拖拉机中的变速齿轮,内燃机上的凸轮轴、活塞销等机器零件。
这类零件在工作中遭受强烈的摩擦磨损,同时又承受较大的交变载荷,特别是冲击载荷。
2. 性能要求(1) 表面渗碳层硬度高,以保证优异的耐磨性和接触疲劳抗力,同时具有适当的塑性和韧性。
(2) 心部具有高的韧性和足够高的强度。
心部韧性不足时,在冲击载荷或过载作用下容易断裂;强度不足时,则较脆的渗碳层易碎裂、剥落。
(3) 有良好的热处理工艺性能在高的渗碳温度(900℃~950℃)下,奥氏体晶粒不易长大,并有良好的淬透性。
3. 成分特点(1) 低碳:碳含量一般为0.10%~0.25%,使零件心部有足够的塑性和韧性。
(2) 加入提高淬透性的合金元素:常加入Cr、Ni、Mn、B等。
(3) 加入阻碍奥氏体晶粒长大的元素:主要加入少量强碳化物形成元素Ti、V、W、Mo等,形成稳定的合金碳化物。
4.钢种及牌号20Cr低淬透性合金渗碳钢。
这类钢的淬透性低,心部强度较低。
20CrMnTi中淬透性合金渗碳钢。
这类钢淬透性较高、过热敏感性较小,渗碳过渡层比较均匀,具有良好的机械性能和工艺性能。
18Cr2Ni4WA和20Cr2Ni4A高淬透性合金渗碳钢。
这类钢含有较多的Cr、Ni 等元素,淬透性很高,且具有很好的韧性和低温冲击韧性。
5. 热处理和组织性能合金渗碳钢的热处理工艺一般都是渗碳后直接淬火,再低温回火。
热处理后,表面渗碳层的组织为合金渗碳体+回火马氏体+少量残余奥氏体组织,硬度为60HRC~62HRC。
心部组织与钢的淬透性及零件截面尺寸有关,完全淬透时为低碳回火马氏体,硬度为40HRC~48HRC;多数情况下是屈氏体、回火马氏体和少量铁素体,硬度为25HRC~40HRC。
新能源汽车齿轮的精密热处理与噪音控制
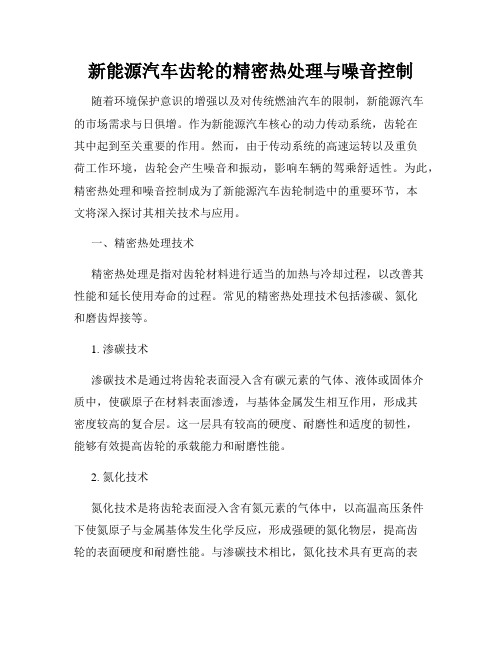
新能源汽车齿轮的精密热处理与噪音控制随着环境保护意识的增强以及对传统燃油汽车的限制,新能源汽车的市场需求与日俱增。
作为新能源汽车核心的动力传动系统,齿轮在其中起到至关重要的作用。
然而,由于传动系统的高速运转以及重负荷工作环境,齿轮会产生噪音和振动,影响车辆的驾乘舒适性。
为此,精密热处理和噪音控制成为了新能源汽车齿轮制造中的重要环节,本文将深入探讨其相关技术与应用。
一、精密热处理技术精密热处理是指对齿轮材料进行适当的加热与冷却过程,以改善其性能和延长使用寿命的过程。
常见的精密热处理技术包括渗碳、氮化和磨齿焊接等。
1. 渗碳技术渗碳技术是通过将齿轮表面浸入含有碳元素的气体、液体或固体介质中,使碳原子在材料表面渗透,与基体金属发生相互作用,形成其密度较高的复合层。
这一层具有较高的硬度、耐磨性和适度的韧性,能够有效提高齿轮的承载能力和耐磨性能。
2. 氮化技术氮化技术是将齿轮表面浸入含有氮元素的气体中,以高温高压条件下使氮原子与金属基体发生化学反应,形成强硬的氮化物层,提高齿轮的表面硬度和耐磨性能。
与渗碳技术相比,氮化技术具有更高的表面硬度和较低的表面粗糙度,能够有效减少齿轮在工作过程中的磨损和噪音产生。
3. 磨齿焊接技术磨齿焊接技术是将两个或多个齿轮通过磨齿焊接设备连接起来,形成一体化的传动装置。
这种技术能够有效提高齿轮的精度和刚度,减少零部件的数量,降低传动噪音和振动。
同时,磨齿焊接技术还具有生产效率高、成本较低等优点,被广泛应用于新能源汽车齿轮的制造中。
二、噪音控制技术噪音控制是指通过各种措施和技术手段,减少或消除齿轮工作过程中产生的噪音和振动。
常见的噪音控制技术包括减振、减速噪声和噪声隔离等。
1. 减振技术减振技术是通过改变齿轮体系的结构和减少相对振动的方法,来降低齿轮噪音的技术。
例如,采用减振装置、增加齿轮支撑点、增加齿轮的副数等措施,能够有效地减少齿轮在工作过程中产生的振动和噪音。
2. 减速噪声技术减速噪声技术是指通过改变齿轮传动比例和改进齿形设计,减少速度变化和齿轮啮合时产生的冲击噪声。
减速常见机械(含汽车)零件的热处理工艺路线。
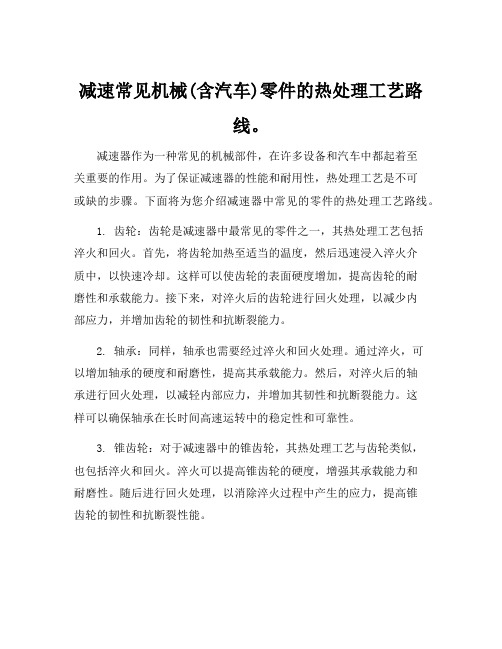
减速常见机械(含汽车)零件的热处理工艺路线。
减速器作为一种常见的机械部件,在许多设备和汽车中都起着至关重要的作用。
为了保证减速器的性能和耐用性,热处理工艺是不可或缺的步骤。
下面将为您介绍减速器中常见的零件的热处理工艺路线。
1. 齿轮:齿轮是减速器中最常见的零件之一,其热处理工艺包括淬火和回火。
首先,将齿轮加热至适当的温度,然后迅速浸入淬火介质中,以快速冷却。
这样可以使齿轮的表面硬度增加,提高齿轮的耐磨性和承载能力。
接下来,对淬火后的齿轮进行回火处理,以减少内部应力,并增加齿轮的韧性和抗断裂能力。
2. 轴承:同样,轴承也需要经过淬火和回火处理。
通过淬火,可以增加轴承的硬度和耐磨性,提高其承载能力。
然后,对淬火后的轴承进行回火处理,以减轻内部应力,并增加其韧性和抗断裂能力。
这样可以确保轴承在长时间高速运转中的稳定性和可靠性。
3. 锥齿轮:对于减速器中的锥齿轮,其热处理工艺与齿轮类似,也包括淬火和回火。
淬火可以提高锥齿轮的硬度,增强其承载能力和耐磨性。
随后进行回火处理,以消除淬火过程中产生的应力,提高锥齿轮的韧性和抗断裂性能。
4. 壳体:减速器的壳体一般采用铸铁材料,常见的热处理工艺是退火。
通过加热壳体至一定温度,然后缓慢冷却,可以改善铸铁材料的晶粒结构,减少内部应力,提高其韧性和可加工性。
在进行减速器零件的热处理工艺时,需要注意以下几点:1. 控制加热温度和时间:不同的材料和零件需要在不同温度下进行加热,且时间也需根据实际情况进行控制。
2. 选择合适的淬火介质:淬火介质的选择应根据材料的类型和要求确定,以保证零件的硬度和性能。
3. 合理的回火工艺:回火工艺应根据材料的硬度和应力状况确定,以获得最佳的韧性和抗断裂性能。
综上所述,对于减速器中的常见零件,如齿轮、轴承、锥齿轮和壳体,热处理工艺是不可或缺的步骤。
通过适当的热处理,可以提高零件的硬度、耐磨性和承载能力,同时保持其韧性和稳定性。
选用合适的热处理工艺路线,将有助于确保减速器的性能和可靠性,延长其使用寿命。
齿轮热处理工艺流程

齿轮热处理工艺流程
齿轮热处理工艺流程是指对齿轮进行加热、保温、冷却等一系列工艺处理,以改善其物理性能和机械性能的过程。
一般来说,齿轮热处理工艺流程包括以下步骤:
1. 预处理:齿轮在进入热处理前需要进行清洗、拆卸和去毛刺等预处理工作,以便于更好地进入加热工艺。
2. 加热:将齿轮放入加热设备中进行加热处理,通常采用气体或者电加热方式。
加热温度和时间根据齿轮的材料和大小来确定。
3. 保温:在齿轮达到所需的加热温度后,需要进行一段时间的保温处理,使其温度均匀分布,达到最佳的组织结构。
4. 冷却:对于齿轮的不同部位,需要采用不同的冷却方式,一般包括水淬、油淬、风淬等方法。
冷却速度的快慢也会影响齿轮的物理性能和机械性能。
5. 温度控制和回火:完成冷却后,需要对齿轮进行温度控制和回火,以进一步调整其组织结构和性能。
6. 后处理:对于经过热处理的齿轮,需要进行磨削、抛光和检测等后处理工作,以确保其质量和精度。
总之,齿轮热处理工艺流程是一个相对复杂的过程,需要根据齿轮的具体情况进行不同的处理方式和参数控制,以达到最佳的效果。
- 1 -。
汽车齿轮材料的选择及其热处理工艺
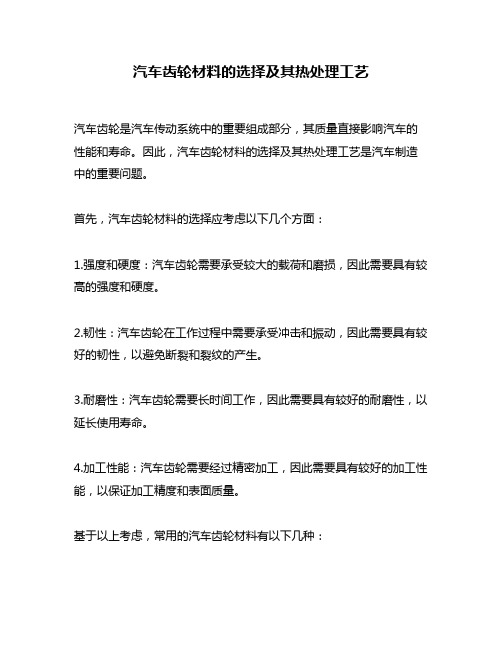
汽车齿轮材料的选择及其热处理工艺汽车齿轮是汽车传动系统中的重要组成部分,其质量直接影响汽车的性能和寿命。
因此,汽车齿轮材料的选择及其热处理工艺是汽车制造中的重要问题。
首先,汽车齿轮材料的选择应考虑以下几个方面:1.强度和硬度:汽车齿轮需要承受较大的载荷和磨损,因此需要具有较高的强度和硬度。
2.韧性:汽车齿轮在工作过程中需要承受冲击和振动,因此需要具有较好的韧性,以避免断裂和裂纹的产生。
3.耐磨性:汽车齿轮需要长时间工作,因此需要具有较好的耐磨性,以延长使用寿命。
4.加工性能:汽车齿轮需要经过精密加工,因此需要具有较好的加工性能,以保证加工精度和表面质量。
基于以上考虑,常用的汽车齿轮材料有以下几种:1.碳素钢:碳素钢具有较高的强度和硬度,但韧性较差,容易产生裂纹和断裂。
2.合金钢:合金钢具有较高的强度、硬度和韧性,但加工性能较差,需要采用先进的加工工艺。
3.铸铁:铸铁具有较好的耐磨性和韧性,但强度和硬度较低,适用于低速和中速齿轮。
4.不锈钢:不锈钢具有较好的耐腐蚀性和韧性,但强度和硬度较低,适用于低速和中速齿轮。
其次,汽车齿轮材料的热处理工艺也是影响其性能的重要因素。
常用的热处理工艺有以下几种:1.淬火:淬火可以提高齿轮的硬度和强度,但会降低韧性,容易产生裂纹和断裂。
2.回火:回火可以提高齿轮的韧性和耐磨性,但会降低硬度和强度。
3.正火:正火可以提高齿轮的强度和硬度,同时保持一定的韧性和耐磨性。
4.表面强化:表面强化可以提高齿轮的耐磨性和疲劳寿命,常用的方法有渗碳、氮化和喷涂等。
综上所述,汽车齿轮材料的选择及其热处理工艺是汽车制造中的重要问题,需要综合考虑材料的强度、硬度、韧性、耐磨性和加工性能等因素,选择合适的材料和热处理工艺,以保证汽车齿轮的性能和寿命。
20CrMnTi汽车变速箱齿轮的热处理工艺

20CrMnTi汽车变速箱齿轮的热处理工艺一、学习目标知识目标:·熟悉感应加热表面淬火原理、特点及应用;·了解火焰表面淬火原理、特点及应用;·了解化学热处理过程;·掌握渗碳、渗氮和碳氮共渗原理、特点、常用方法及应用。
能力目标:·能根据零件的化学成分、性能要求和技术条件,合理选择表面淬火和化学热处理方法。
二、任务引入变速箱齿轮位于汽车传动部分,用于传递扭矩与动力、调整速度。
由于传递扭矩,齿根要承受较大的弯曲应力和交变应力;由于变速箱齿轮转速变化范围广,齿轮表面承受较大的接触应力,并在高速下承受强烈的磨擦力;由于工作时不断换档,轮齿之间经常要承受换档造成的冲击与碰撞。
这就要求齿轮表面有高硬度和高耐磨性;齿面有高的接触疲劳强度;心部有较高的强度和高韧性。
图2-25所示20CrMnTi汽车变速箱齿轮的热处理技术要求如下:1.渗碳层表面含碳量为0.80~1.05%;2.渗碳层深度为0.80~1.3mm;3.淬火回火后齿面硬度为58~62HRC,心部硬度为33~48HRC。
图2-25 汽车变速箱齿轮简图三、相关知识在机械设备中,有许多零件(如齿轮、曲轴、活塞销等)是在冲击载荷及表面摩擦条件下工作的,这类零件表面需具有高硬度和高耐磨性,而心部需要足够的塑性和韧性。
为满足这类零件的性能要求,须进行表面热处理。
常用的表面热处理方法有表面淬火及化学热处理两种。
(一)钢的表面淬火表面淬火是通过快速加热,使钢件表层奥氏体化,然后迅速冷却,使表层形成一定深度的淬硬组织——马氏体,而心部仍保持原来塑性、韧度较好的组织的热处理工艺。
在钢的表面淬火法中,感应加热淬火应用最广。
1.感应加热表面淬火感应加热表面淬火时,将工件放在铜管制成的感应器内,即图2-26所示装置中,感应器中通入一定频率的交流电,以产生交变磁场,于是工件内部就会产生频率相同、方向相反的感应电流(涡流)。
由于涡流的趋肤效应,使涡流在工件截面上的分布是不均匀的,表面电流密度大,心部电流密度小。
汽车齿轮材料的选择及其热处理工艺

经过适 当的热处理. 以提高承载能力和延长使用寿命
环保 . 已成 为可行 的替代可控气氛的方法。低 压真空渗碳和高气淬技 油淬工艺相 比较 . 具有下优势 : 渗碳钢是制作 汽车齿轮 的主要材料 . 其中渗碳钢包括碳 素渗碳 钢 术与传统的气 氛渗碳 、 ( 1 ) 真空渗碳速度快 , 减少零件在高温下的保 温时间 . 有利于减少 和合 金渗碳 钢 碳素渗碳钢碳量一般都低, 介于 0 . 1 - 0 . 2 5 %之间, 属 于低 2 ) 高压气淬 的淬火烈度 比油淬低 , 在保证零件度的前提下 , 碳钢 低 的含碳量可保证渗碳零件心部具有 足够 的韧性和塑性 碳 素 高温变。( 3 ) 高压气淬不存在油淬过程 中的三个 渗碳 钢的淬透性低 . 对大模数齿轮心部淬火得不到低碳马 氏体. 热处理 零件的冷却变形量也小许多 。( 仅 对流传 导过程 , 零件较易得到较高的硬度 。( 4 ) 低压真空渗碳 后不能使碳钢渗碳零 件的心部获得明显的强化效果 。合金渗碳钢 , 具 阶段 , 可以避零件表面不 良组织 ( 如 内氧 化等) 出现 , 有 良好的淬透性高, 零件心部可 以得到低碳 马氏体 , 即热处理能使 合金 过程 中不存在氧原子 , ( 5 ) 处理后 的零件表 面清洁度高 , 无须后清洗和强 渗碳钢零件的心部获得较显著的强化效果 合金渗碳钢 中主要合金元 提高零件的用寿命。 降低了生产成本 。( 6 ) 环保性好 , 无火帘 , 无S 0 2 、 C O的排 素是 铬( < 2 %) 、 镍( < 4 . 5 %) 、 锰( < 2 %) 、 硼( < O . 0 0 5 %) 等, 钢 中硼的 最佳 含量 力抛丸工序 .
由于汽车行驶状况随路况随机变化因而汽车齿轮的工作状况很复杂齿轮的齿根部受交变弯曲应力齿面承受大接触应力并产生强烈的摩擦在换挡启动和啮合不良时齿轮还承受定的冲击载荷齿轮的主要失效形式是疲劳断齿疲劳点蚀以及齿面的过量磨损根据齿轮的受力情况和失效分析可知
汽车齿轮材料的选择及其热处理工艺
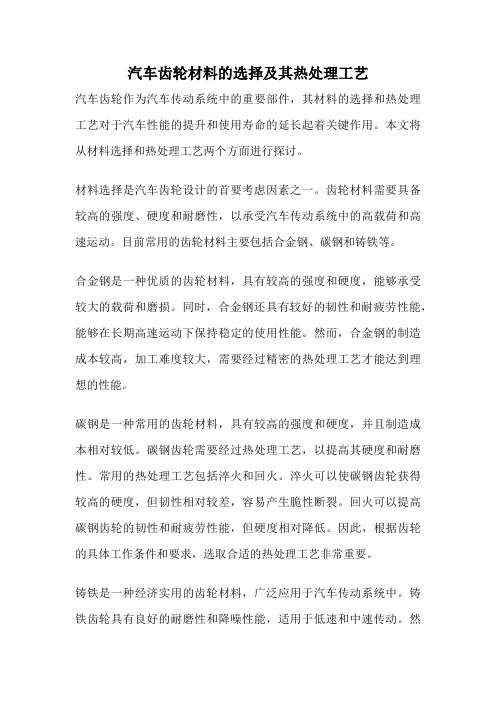
汽车齿轮材料的选择及其热处理工艺汽车齿轮作为汽车传动系统中的重要部件,其材料的选择和热处理工艺对于汽车性能的提升和使用寿命的延长起着关键作用。
本文将从材料选择和热处理工艺两个方面进行探讨。
材料选择是汽车齿轮设计的首要考虑因素之一。
齿轮材料需要具备较高的强度、硬度和耐磨性,以承受汽车传动系统中的高载荷和高速运动。
目前常用的齿轮材料主要包括合金钢、碳钢和铸铁等。
合金钢是一种优质的齿轮材料,具有较高的强度和硬度,能够承受较大的载荷和磨损。
同时,合金钢还具有较好的韧性和耐疲劳性能,能够在长期高速运动下保持稳定的使用性能。
然而,合金钢的制造成本较高,加工难度较大,需要经过精密的热处理工艺才能达到理想的性能。
碳钢是一种常用的齿轮材料,具有较高的强度和硬度,并且制造成本相对较低。
碳钢齿轮需要经过热处理工艺,以提高其硬度和耐磨性。
常用的热处理工艺包括淬火和回火。
淬火可以使碳钢齿轮获得较高的硬度,但韧性相对较差,容易产生脆性断裂。
回火可以提高碳钢齿轮的韧性和耐疲劳性能,但硬度相对降低。
因此,根据齿轮的具体工作条件和要求,选取合适的热处理工艺非常重要。
铸铁是一种经济实用的齿轮材料,广泛应用于汽车传动系统中。
铸铁齿轮具有良好的耐磨性和降噪性能,适用于低速和中速传动。
然而,铸铁齿轮的强度和韧性相对较低,容易产生断裂和疲劳损伤。
因此,在设计铸铁齿轮时,需要考虑到其工作条件和要求,合理选择材料和热处理工艺。
热处理工艺对齿轮材料的性能提升至关重要。
在热处理过程中,通过控制加热温度、保温时间和冷却速率等参数,使材料的组织结构发生变化,从而改善其机械性能和耐磨性。
常用的热处理工艺包括淬火、回火、表面渗碳和氮化等。
淬火是一种常用的热处理工艺,通过快速冷却使材料达到高硬度和高强度。
淬火后的材料具有较高的耐磨性和抗断裂能力,适用于高速传动。
然而,淬火过程中容易产生应力集中和变形问题,需要进行适当的回火处理以提高韧性。
回火是一种常用的热处理工艺,通过加热材料至适当温度并保温一段时间后,再进行适当冷却。
汽车传动系统零部件的热处理解决方案
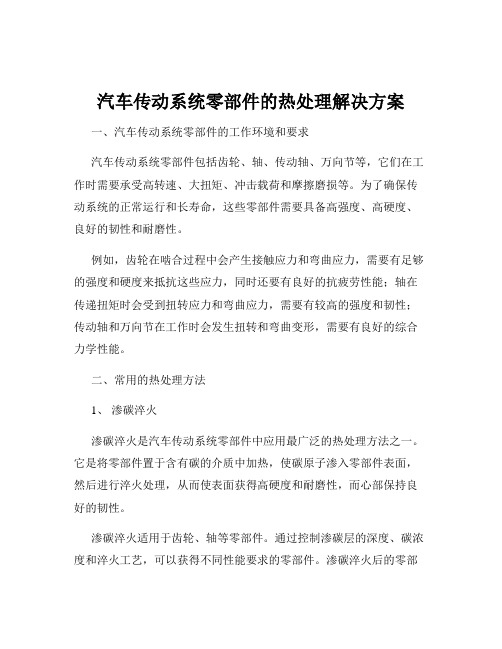
汽车传动系统零部件的热处理解决方案一、汽车传动系统零部件的工作环境和要求汽车传动系统零部件包括齿轮、轴、传动轴、万向节等,它们在工作时需要承受高转速、大扭矩、冲击载荷和摩擦磨损等。
为了确保传动系统的正常运行和长寿命,这些零部件需要具备高强度、高硬度、良好的韧性和耐磨性。
例如,齿轮在啮合过程中会产生接触应力和弯曲应力,需要有足够的强度和硬度来抵抗这些应力,同时还要有良好的抗疲劳性能;轴在传递扭矩时会受到扭转应力和弯曲应力,需要有较高的强度和韧性;传动轴和万向节在工作时会发生扭转和弯曲变形,需要有良好的综合力学性能。
二、常用的热处理方法1、渗碳淬火渗碳淬火是汽车传动系统零部件中应用最广泛的热处理方法之一。
它是将零部件置于含有碳的介质中加热,使碳原子渗入零部件表面,然后进行淬火处理,从而使表面获得高硬度和耐磨性,而心部保持良好的韧性。
渗碳淬火适用于齿轮、轴等零部件。
通过控制渗碳层的深度、碳浓度和淬火工艺,可以获得不同性能要求的零部件。
渗碳淬火后的零部件表面硬度可达 HRC58-62,心部硬度可达 HRC30-45,具有良好的综合力学性能。
2、感应淬火感应淬火是利用电磁感应原理在零部件表面产生涡流,从而使表面迅速加热并淬火的方法。
感应淬火具有加热速度快、淬火组织细小、变形小等优点。
感应淬火适用于轴、传动轴等表面需要高硬度和耐磨性的零部件。
通过调整感应加热的参数和淬火介质,可以控制淬火层的深度和硬度。
感应淬火后的零部件表面硬度可达 HRC50-55,淬火层深度一般为 2-8mm。
3、调质处理调质处理是将零部件加热到一定温度后淬火,然后高温回火的处理方法。
调质处理可以使零部件获得良好的综合力学性能,即较高的强度和韧性。
调质处理适用于轴、齿轮等零部件。
调质后的零部件硬度一般为HB220-280,具有较好的强度和韧性,能够承受较大的载荷和冲击。
4、氮化处理氮化处理是将零部件置于含氮的介质中加热,使氮原子渗入零部件表面形成氮化层的方法。
新能源汽车齿轮的精密热处理与噪音控制
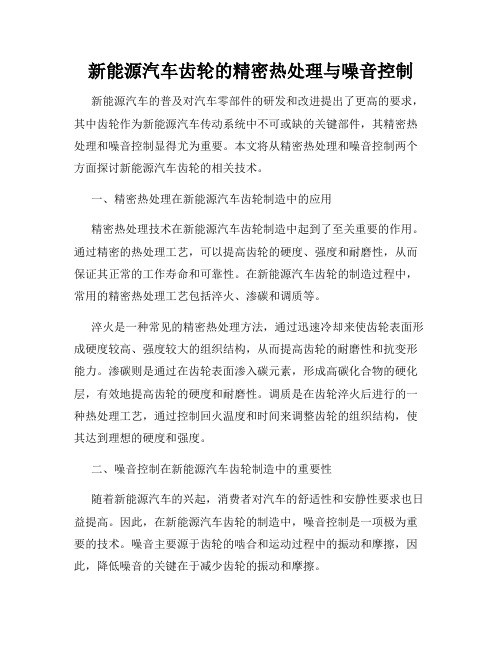
新能源汽车齿轮的精密热处理与噪音控制新能源汽车的普及对汽车零部件的研发和改进提出了更高的要求,其中齿轮作为新能源汽车传动系统中不可或缺的关键部件,其精密热处理和噪音控制显得尤为重要。
本文将从精密热处理和噪音控制两个方面探讨新能源汽车齿轮的相关技术。
一、精密热处理在新能源汽车齿轮制造中的应用精密热处理技术在新能源汽车齿轮制造中起到了至关重要的作用。
通过精密的热处理工艺,可以提高齿轮的硬度、强度和耐磨性,从而保证其正常的工作寿命和可靠性。
在新能源汽车齿轮的制造过程中,常用的精密热处理工艺包括淬火、渗碳和调质等。
淬火是一种常见的精密热处理方法,通过迅速冷却来使齿轮表面形成硬度较高、强度较大的组织结构,从而提高齿轮的耐磨性和抗变形能力。
渗碳则是通过在齿轮表面渗入碳元素,形成高碳化合物的硬化层,有效地提高齿轮的硬度和耐磨性。
调质是在齿轮淬火后进行的一种热处理工艺,通过控制回火温度和时间来调整齿轮的组织结构,使其达到理想的硬度和强度。
二、噪音控制在新能源汽车齿轮制造中的重要性随着新能源汽车的兴起,消费者对汽车的舒适性和安静性要求也日益提高。
因此,在新能源汽车齿轮的制造中,噪音控制是一项极为重要的技术。
噪音主要源于齿轮的啮合和运动过程中的振动和摩擦,因此,降低噪音的关键在于减少齿轮的振动和摩擦。
为了降低齿轮的噪音,可以从以下几个方面进行控制。
首先,优化齿轮的设计,采用合理的齿形参数和齿轮副配对参数,以减少齿轮的振动和啮合噪音。
其次,采用合适的润滑剂和润滑方式,减少齿轮的摩擦噪音。
此外,采用降噪装置,如减振器、隔振膜等,可以有效地降低齿轮的振动和噪音。
三、精密热处理与噪音控制的综合应用在新能源汽车齿轮的制造中,精密热处理和噪音控制往往是密切相关的。
精密热处理可以提高齿轮的硬度和强度,从而减少齿轮的变形和磨损,降低噪音的产生。
同时,通过合理的热处理工艺,可以控制齿轮的组织结构,减少齿轮的内应力,进一步降低振动和噪音的产生。
汽车齿轮材料的选择及其热处理工艺

汽车齿轮材料的选择及其热处理工艺一、引言汽车齿轮作为传动系统的核心部件之一,其性能对整个汽车的运行质量和寿命有着重要的影响。
齿轮的材料选择和热处理工艺对于其强度、硬度、耐磨性以及齿面质量等方面都有着关键作用。
本文将从材料的选择和热处理工艺两个方面,对汽车齿轮进行深入探讨。
二、汽车齿轮材料的选择2.1 材料要求汽车齿轮材料在选择时需要考虑以下要求: - 高强度:齿轮需要承受较大的载荷和冲击,因此材料需要具备较高的强度; - 耐磨性:齿轮在长时间摩擦中容易受到磨损,材料需要具备一定的耐磨性; - 高硬度:齿轮表面需要有足够的硬度,以提高齿面的使用寿命; - 良好的韧性:齿轮在受到冲击时需要具备良好的韧性,以避免断裂; - 低摩擦系数:材料需要具备较低的摩擦系数,以减少能量损失。
2.2 常用材料根据以上要求,目前常用的汽车齿轮材料主要包括以下几种:2.2.1 碳素钢碳素钢是最常见的齿轮材料之一,其具有良好的强度和耐磨性。
由于其制造成本较低,被广泛应用于中低档汽车的齿轮制造中。
2.2.2 低合金钢低合金钢相对于碳素钢来说,具有更好的强度和韧性,适用于中高档汽车的齿轮制造。
通过适当的热处理工艺,可以进一步提高其性能。
2.2.3 铸造钢铸造钢可以根据具体应用的要求,选择不同的成分和硬化方式。
其制造成本较高,但可以获得较高的硬度和强度,适用于高档车型。
2.2.4 渗碳钢渗碳钢是通过在碳含量较低的钢表面渗入碳元素,从而提高齿轮表面的硬度和耐磨性。
它在制造成本和性能之间取得了很好的平衡,适用于中档车型的齿轮制造。
三、汽车齿轮的热处理工艺3.1 热处理的目的热处理是通过对材料进行加热和冷却,改变其内部组织和性能的工艺。
对于汽车齿轮而言,热处理的目的主要包括以下几个方面: - 提高材料的硬度和强度; - 改善材料的韧性和抗疲劳性能; - 调整材料的组织结构,提高齿面的质量。
3.2 常用热处理工艺根据齿轮的材料和要求,常见的热处理工艺包括以下几种:3.2.1 淬火和回火淬火是将齿轮材料加热至临界温度后迅速冷却,使其获得高硬度和较好的强度。
20CrMnTi汽车齿轮的热处理工艺设计

攀枝花学院学生课程设计(论文)题目:20CrMnTi汽车齿轮的热处理工艺设计学生姓名: X X X 学号: 2011111020XX 所在院(系):材料工程学院专业: 20XX级材料成型及控制工程班级:材料成型及控制工程指导教师: X X X 职称:讲师2013年12月16日攀枝花学院教务处制攀枝花学院本科学生课程设计任务书注:任务书由指导教师填写。
课程设计(论文)指导教师成绩评定表摘要本课设计了20CrMnTi汽车齿轮热处理工艺设计。
主要的工艺过程包括下料、锻造、等温正火、机械加工、渗碳、淬火、低温回火、喷丸、磨削等过程。
通过各种不同的工艺过程进行恰当的处理可以获得各种性能良好的材料并且满足各项性能的要求。
20CrMnTi,其淬透性较高,在保证淬透情况下,具有较高的强度和韧性,特别是具有较高的低温冲击韧性。
20CrMnTi表面渗碳硬,化处理用钢。
良好的加工性,加工变形微小,抗疲劳性能相当好。
主要用途有:用于齿轮,轴类,活塞类零配件以及汽车,飞机各种特殊零件部位。
关键词:20CrMnTi,淬透,低温回火。
目录摘要 (Ⅰ)1、设计任务 (1)1.1设计任务 (1)1.2设计的技术要求 (1)2、设计方案 (2)2.1 汽车齿轮设计的分析 (2)2.1.1工作条件 (2)2.1.2失效形式 (2)2.1.3性能要求 (2)2.2钢种材料 (3)3、设计说明 (4)3.1加工工艺流程 (4)3.2具体热处理工艺 (4)3.2.1等温正火 (5)3.2.2退火+机械加工 (5)3.2.3渗碳+淬火+回火热处理工艺 (5)3.2.4喷丸 (6)4、分析与讨论 (8)5、结束语 (9)6、热处理工艺卡片 (10)参考文献 (11)1 设计任务1.1设计任务20CrMnTi汽车齿轮热处理工艺设计1.2设计的技术要求20CrMnTi钢是一种低碳钢材料,淬透性较高,具有良好的强度和韧性,特别是较高的低温冲击韧性,正火后可切削良好。
变速箱齿轮热处理工艺流程
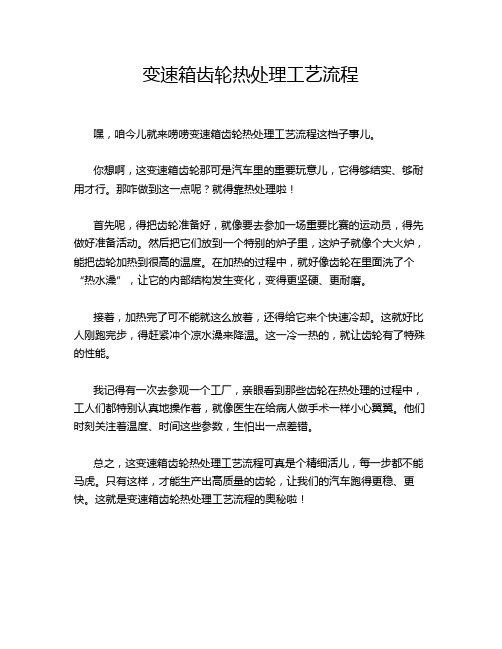
变速箱齿轮热处理工艺流程嘿,咱今儿就来唠唠变速箱齿轮热处理工艺流程这档子事儿。
你想啊,这变速箱齿轮那可是汽车里的重要玩意儿,它得够结实、够耐用才行。
那咋做到这一点呢?就得靠热处理啦!
首先呢,得把齿轮准备好,就像要去参加一场重要比赛的运动员,得先做好准备活动。
然后把它们放到一个特别的炉子里,这炉子就像个大火炉,能把齿轮加热到很高的温度。
在加热的过程中,就好像齿轮在里面洗了个“热水澡”,让它的内部结构发生变化,变得更坚硬、更耐磨。
接着,加热完了可不能就这么放着,还得给它来个快速冷却。
这就好比人刚跑完步,得赶紧冲个凉水澡来降温。
这一冷一热的,就让齿轮有了特殊的性能。
我记得有一次去参观一个工厂,亲眼看到那些齿轮在热处理的过程中,工人们都特别认真地操作着,就像医生在给病人做手术一样小心翼翼。
他们时刻关注着温度、时间这些参数,生怕出一点差错。
总之,这变速箱齿轮热处理工艺流程可真是个精细活儿,每一步都不能马虎。
只有这样,才能生产出高质量的齿轮,让我们的汽车跑得更稳、更快。
这就是变速箱齿轮热处理工艺流程的奥秘啦!。
- 1、下载文档前请自行甄别文档内容的完整性,平台不提供额外的编辑、内容补充、找答案等附加服务。
- 2、"仅部分预览"的文档,不可在线预览部分如存在完整性等问题,可反馈申请退款(可完整预览的文档不适用该条件!)。
- 3、如文档侵犯您的权益,请联系客服反馈,我们会尽快为您处理(人工客服工作时间:9:00-18:30)。
汽车、拖拉机的变速箱齿轮多半用低碳渗碳钢制造,而机床变速箱多半用中碳(合金)2011-4-10 21:07提问者:991495331|浏览次数:289次我来帮他解答2011-4-11 11:10满意回答合金渗碳钢1. 用途主要用于制造汽车、拖拉机中的变速齿轮,内燃机上的凸轮轴、活塞销等机器零件。
这类零件在工作中遭受强烈的摩擦磨损,同时又承受较大的交变载荷,特别是冲击载荷。
2. 性能要求(1) 表面渗碳层硬度高,以保证优异的耐磨性和接触疲劳抗力,同时具有适当的塑性和韧性。
(2) 心部具有高的韧性和足够高的强度。
心部韧性不足时,在冲击载荷或过载作用下容易断裂;强度不足时,则较脆的渗碳层易碎裂、剥落。
(3) 有良好的热处理工艺性能在高的渗碳温度(900℃~950℃)下,奥氏体晶粒不易长大,并有良好的淬透性。
3. 成分特点(1) 低碳:碳含量一般为0.10%~0.25%,使零件心部有足够的塑性和韧性。
(2) 加入提高淬透性的合金元素:常加入Cr、Ni、Mn、B等。
(3) 加入阻碍奥氏体晶粒长大的元素:主要加入少量强碳化物形成元素Ti、V、W、Mo等,形成稳定的合金碳化物。
4.钢种及牌号20Cr低淬透性合金渗碳钢。
这类钢的淬透性低,心部强度较低。
20CrMnTi中淬透性合金渗碳钢。
这类钢淬透性较高、过热敏感性较小,渗碳过渡层比较均匀,具有良好的机械性能和工艺性能。
18Cr2Ni4WA和20Cr2Ni4A高淬透性合金渗碳钢。
这类钢含有较多的Cr、Ni 等元素,淬透性很高,且具有很好的韧性和低温冲击韧性。
5. 热处理和组织性能合金渗碳钢的热处理工艺一般都是渗碳后直接淬火,再低温回火。
热处理后,表面渗碳层的组织为合金渗碳体+回火马氏体+少量残余奥氏体组织,硬度为60HRC~62HRC。
心部组织与钢的淬透性及零件截面尺寸有关,完全淬透时为低碳回火马氏体,硬度为40HRC~48HRC;多数情况下是屈氏体、回火马氏体和少量铁素体,硬度为25HRC~40HRC。
心部韧性一般都高于700KJ/m2。
1 汽车齿轮热处理工艺概述汽车齿轮通常采用低碳合金渗碳钢制造,齿轮毛坯一般需经过锻坯→预先热处理→切削加工→渗碳淬火→精加工等多道冷热加工工序,以获得较高的表面硬度和良好的心部韧性,使成品齿轮具有耐磨、耐疲劳、耐腐蚀等优良性能。
目前,国内汽车齿轮锻造毛坯预先热处理主要采用正火和等温退火,并呈现采用等温退火取代正火处理的趋势,而常用的热处理工艺主要有渗碳、碳氮共渗、渗氮以及感应淬火[ 4 ] 。
1. 1 预先热处理工艺对汽车齿轮锻造毛坯进行预先热处理,主要是为了获得适宜的锻件表面硬度并为第二热处理作好金相组织准备。
传统的预先热处理方法大多采用常规正火处理。
该工艺设备简单、能耗少、工艺要求不高,因此应用较为广泛。
随着对汽车齿轮质量要求的提高,特别是引进车型用钢材料的多样化,由于普通正火时钢的组织转变是在一定温度范围内进行,因此得到的组织不均匀;而且批量正火冷却时,锻坯往往成堆在空气中冷却或吹风冷却,其冷却速度易受其在堆中的位置及周围环境的影响, 造成同批零件的硬度波动较大(156~207HB) ,同时又会增大渗碳淬火时的变形量,而对于淬透性较高的钢,甚至会产生贝氏体组织[ 5 ] 。
因此,国内逐步采用等温退火工艺进行预先热处理, 通常等温温度在560~650 ℃范围内,以保证现代化大批量生产时,齿坯在预先热处理后能获得均匀的组织和硬度(160~180HB) ,这对于减少齿轮的渗碳淬火变形,降低运行时的噪音具有重要意义[ 6 ] 。
在国外,汽车齿轮锻坯普遍采用等温退火处理,而且对不同的材料规定了不同的等温退火工艺,如德国大众公司、奔驰公司、意大利菲亚特公司等。
国外生产实践表明[ 7 ],经等温退火处理的齿轮不仅机加工性能大大提高,而且渗碳淬火后的变形也明显减小。
当然, 采用等温退火仍需将锻坯重新自室温加热至900 ℃以上高温,这将消耗大量能源。
由于汽车齿轮锻造的终锻温度一般在900 ℃以上,此时工件仍处于奥氏体状态,如迅速将其均匀冷却到Ar1 以下珠光体相变区进行等温转变,可获得与常规等温退火相似的显微组织和硬度,从而大大节约能源和提高劳动生产率并改善锻坯质量。
近年来,在汽车工业,利用锻造余热进行等温退火已有研究和应用,但要进行大批量生产依然还存在一些技术难点[ 8 ] 。
3 汽车齿轮热处理工艺进展汽车齿轮热处理工艺的发展除了对产品质量实行更加严格的控制之外,也更加重视节能与环保,美国2020 年热处理技术发展路线图对齿轮处理也提出了这一要求。
同时,在信息时代,齿轮热处理工艺会更加充分利用计算机技术,使热处理生产管理、工艺过程控制、工艺设计与质量预测分析实现高度数字化、智能化。
汽车齿轮热处理工艺发展趋势,总体将朝着高品质、低能耗、环保、智能化方向发展[ 50 ,51 ] 。
高品质进行齿轮热处理变形与控制技术研究,开发新型汽车齿轮用钢材料及精密齿轮。
主要表现在: (1) 材料的均匀性,即要求材料具有良好的成分和组织的均匀性; (2) 温度场和流体场,即不断改善温度场和各种流体场,如渗碳、渗氮、碳氮共渗的气流场和淬火的液态流体场的改善。
低能耗(1) 齿轮热处理先进设备的研制和发展,如开发更好的炉衬耐热和保温节能材料,尽可能降低炉壁温升,减小炉壁热损耗; (2) 开发汽车齿轮成形新工艺,如净成形技术; (3) 废热综合利用,如锻造余热的利用。
环保研究开发齿轮热处理新工艺,如低压真空渗碳、双频感应淬火、离子渗氮等技术的发展。
智能化智能化是齿轮热处理控制技术发展的必然趋势,计算机—传感器—智能库将构建成智能热处理的核心。
主要表现在: (1) 根据零件的材料、技术要求等,系统自动生成工艺; (2) 生产过程的完全闭环自动控制; (3) 零件热处理质量的预测、预判;(4) 系统故障自动诊断与处置; (5) 在线的自适应及应急应变能力,如开发离子渗氮、碳氮共渗所用的氮势传感器和低压渗碳的碳势传感器。
2.2 渗碳工艺渗碳淬火工艺过程中, 要防止齿轮变形, 要严格控制渗碳齿轮的表面碳浓度和渗层深度。
因它们会对渗层组织的膨胀系数产生影响, 渗碳后若表面形成不良碳化物分布, 将增加齿形、齿向及花键孔的变形,因此必须控制渗碳时的碳势,以防止表面碳浓度过高和碳量不均匀。
渗碳层深度越厚,也将使畸变加大。
表面含碳量影响渗碳淬火齿轮的淬透性, 而材料的淬透性对组织、性能、畸变有直接的影响[5]。
因此应使渗碳层深度及其表面含碳量控制在合理适宜的范围内。
齿轮渗碳的方法较多,常用气体渗碳,目前应用电解质气相离子(ECA)催渗技术控制渗碳变形也取得较好效果[6]。
现以可控井式炉中气体渗碳为例优化工艺, 滴入煤油、苯、甲醇等渗碳剂, 加热温度从一般采用的930℃改为900℃[3]。
这些介质在高温下分解,产生活性碳原子,主要化学分解式如下:2CO→[C]+CO2CH4→2H2+[C]活性碳原子溶入钢表面奥氏体中, 并向内部扩散,最后形成一定深度的渗碳层。
一般渗碳层深度取决于保温时间, 可按每小时渗入0.2mm~0.25mm的速度估算。
渗碳时要控制渗碳的时间、活性碳的浓度,使表面的含碳量控制在0.80 %~1.0 %范围内[4],并从表面到心部逐渐减小,心部仍保持原来低碳钢的含碳量。
渗碳的温度越高,时间越长, 奥氏体晶粒越大, 齿轮的畸变越大,把加热温度控制900℃左右,目的是控制奥氏体晶粒长大,获得细小的奥氏体晶粒,淬火后获得细小的马氏体组织。
由于渗碳只改变工件表面的含碳量, 要使渗碳齿轮表面具有高的硬度、高的耐磨性和心部良好韧性渗碳后必须进行热处理。
常用的是淬火后低温回火。
3 淬火低温回火3.1 淬火钢的加热温度一般可根据Fe-Fe3C相图选择,亚共析钢淬火加热温度选择Ac3以上30℃~50℃,过共析钢淬火加热温度选择Ac1以上30℃~50℃。
根据渗碳后齿轮的表层含碳量的分布状况及实践经验从900℃预冷到820℃左右进行油冷[3]可以得到好的效果。
加热温度过高或保温时间过长,会引起奥氏体的晶粒粗大引起过热或晶界氧化并部分熔化的过烧现象。
过热时奥氏体的晶粒粗大不仅降低齿轮力学性能, 也容易引起齿轮的变形和开裂。
过烧后的工件只能报废。
加热温度过低、保温时间不足会引起硬度不足。
故可选择900℃温度渗碳,预冷8 2 0℃左右油冷淬火。
淬火冷却速度太快,奥氏体向马氏体组织转变剧烈、体积收缩,引起很大的内应力,容易造成齿轮的变形和开裂,由于20CrMnTi是合金钢,淬透性较好,故选择油冷减小冷却速度,防止淬火造成齿轮变形或开裂。
同时也能获得马氏体组织,达到较高的硬度。
3.2 低温回火淬火后的钢组织是马氏体及少量残余奥氏体,它们都是不稳定的组织,有向稳定组织转变的趋势,同时淬火时产生内应力。
为了减小或消除淬火内应力, 稳定组织和尺寸,获得所需的力学性能,实践证明重载齿轮选择在200℃进行4小时低温回火[3]工艺较好。
低温回火时马氏体中过饱和碳原子以碳化物的形式逐步析出, 马氏体晶格畸变程度减弱,内应力有所降低。
此时的回火组织由马氏体和碳化物组成, 称为回火马氏体。
虽然马氏体的分解使α-Fe中碳的过饱和程度降低,钢的硬度相应下降,但析出的碳化物又对基体起强化作用, 部分的残余奥氏体分解为回火马氏体, 所以钢仍保持很高的硬度和耐磨性和一定的韧性。
齿轮材料为20CrMnTi。
工艺参数:9200C渗碳,渗层为0.8~1.1mm,齿部于盐炉中800"C 淬火,油冷,18O℃回火,保温lh,空冷。
汽车变速齿轮工作条件比机床齿轮差,特别是主传动系统中的齿轮,受力较大,受冲击较频繁,因此对材料要求较高。
由于弯曲与接触应力都很大,所以重要齿轮都需渗碳、淬火处理,以提高耐磨性和疲劳抗力。
为保证心部有足够的强度及韧性,材料的淬透性要求较高,心部硬度应在35~45HRC 之间。
另外,汽车生产批量大,因此选钢材时,在满足力学性能的前提下对工艺性能必须予以足够重视。
实践证明,20CrMnTi钢具有较高的力学性能,在渗碳、淬火、低温回火后,表面硬度可达58~62HRC,心部硬度30~45HRC,正火态切削加工工艺性和热处理工艺性均较好。
为提高齿轮的耐用性,渗碳、淬火、回火后,还可采用喷丸处理,增大表面压应力。
渗碳齿轮的工艺路线为:下料- 锻造- 正火- 切削加工- 渗碳、淬火及低温回火- 喷丸- 磨削加工。