Design for Assembly
汽车行业术语缩写

常用汽车行业英文缩写及词汇DCCDesignChangeControl ; DFA-DesignForAssembly 面向装;DOEDesignOfExamination 试验;DQESDeliveryQualityEvalu ; DTLDirectToLine ; DVP&RDesignValidateP ; EDIelectronicdatainterch ; ERPE nterpriseResDCC Desig n Cha nge Con trolDFA- Design For Assembly 面向装配的设计DOE Desig n Of Exami natio n 试验设计DQES Delivery Quality Evaluation SystemDTL Direct To Li neDVP&R Design Validate Pla n&Report 设计验证计划报告EDI electro nic data in tercha nge 电子数据交换ERP En terprise Resource Pla nningES Engin eeri ng Specificatio n 工程规格ESI Early Supplier In volveme nt 供应商先期参与Ex-Work (工厂交货)、FOB (船上交货)、FAS (船边交货)或CIF (运保费在内交货)FEU- Field Evaluation Units 用户市场实际体验与评估first gear 一档Flow Chart流程图FMEA Failure Mode and Effects An alysisfour-wheel drive 四轮驱动FRG- Ford Reliability Guideli ne 福特可靠性指导Fro nt Win dshield 前挡风玻璃Tempered glass 钢化玻璃fron t-wheel drive 前轮驱动FSS- Full service supplier 全服务供应商FTA Fault Tree An alysisGD&T- Geometric Dime nsio ning & Tolera ncing 标准公差GR&R Guage Repeatabilit y&reproducibility 量具的重复性和再现性HTFB- Hard Tooli ng Fun ctio nal Build 工装集成调试与验证IPO In dividual Parts OrderISIR In itial Sample In specti on ReportJIT Just In TimeKD- knocked down/ Semi Knock Down(SKD) /Completely Knock Dow n( CKD)KO Kick-offLam in ated glass 夹层玻璃LP —Lea n Productio n 精益生产LR Launch Read in essLS Launch SupportLVPM Local Ven dor Packag ing MethodMPV Multi-PurposeVehicle 多用途汽车MRD Material Required DateMRO Mai nte nan ce,Repair,a nd Operati onMTP- Make to print supplier 照图加工供应商N/A- Not ApplicableNCDR No n-Co nformi ng Delivery ReportNCMAR No n-Co nformi ng Material Actio n ReportNDA Non Disclosure Agreeme nt 保密协定NDS Nissa n Desig n SpecificationNML Nissa n Motor LtdNVH- System Noise, Vibration & Harshness 系统噪音,振动及粗糙性OSM- Outside of MaterialPA Program Approvalpallet n.托盘Passe nger Vehicle 乘用车PAT- Program Attributes Team 产品属性小组PDL Product Desig n LetterPH Proportio ns&Hardpoi ntsPIPC- Perce ntage of In dexes with Process Capability 能力指数百分PIST- Perce ntage of In specti on points Satisfy ing Tolera nee 满检测点意工差百分比PMT- Program Moudle Team 产品模块小组PO Purchase OrderPPAP- Production Part Approval Process 生产件批准程序PPSR Production Preparation Status ReportPQA Process Quality Assura neePR Program Read in essPre-Lau nch 试生产price-drive n cost ing 价格弓丨导成本Production Preparatio n-Final Nissan - PT2/Re nault - PPProduction Preparati on-ln itial Nissa n - PT1/Re nault - PPP3Production Trial Run 试生产Prototype 样件QFD Quality Fun tion Deploy 质量功能展幵QFTT Quality Fun ctio nal Task TeamQR- Quality Reject 质量拒收QS Quality Sta ndardRAN Release Authorisation Numberreverse 倒车档RFQ Request For Quotation 询价RKD Reverse Knock Dow nRLQ Receivi ng Lot Qua ntityROC Rate of ClimbROI return on in vestme nt 报酬率ROP Re-Order PointRTO Required To OperateSAIS Supplier Assessme nt & Improveme nt SystemSC Strategic Con firmatio n/sig nifica nt CharacteristicsSDS- System/ Desig n Specificatio ns 系统/ 设计说明sec ond gear 二档SFMEA System FMEAShippi ng Date 出货日、In voice Date 发票日或On Board Date 装船日Side Win dshield 侧窗玻璃SJ Strategic IntentSNP Sta ndard Number of PartsSOW- state of work 工作申明SPC Statistical Process Con trolSQA Supplier Quality Assura neeSREA- Supplier Request for Engin eeri ng Approval 供应商工程设计更改申请ST Surface Tra nferSTRS Supplier Test Report SystemSubc on tractor 分承包商Sunroof Win dshield 天窗玻璃SUV Sports Utility VehicleTAG Test Aptitude GraphiqueTCO Total Cost of Own ership 总持有成本TCRA Total Cost Reduction ActivityTGR Thi ngs Gone RightTGW Th ings Go ne WorstTM Techi nical Man ualTPM Total Preve ntive Mai nte nanceTTO-Tool Try Out 工装验证UOM Unit Of MeasureVES Vehicle Evaluati on SystemVO- Vehicle Operatio n 主机厂VPP- Vehicle Program Pla n 整车项目计划VQA Vehicle Quality Assura neeVTTO- Ven dor Tool Try-Out 供应商工装验证WERS- World Wide Engineering Release SystemWVTA Whole Vehicle Type ApprovalOTS OFF TOOL SAMPLE 用批量生产的工模器具制造出的样件PVS Produktio ns Versuchs Serie 批量试生产TMA Trial Manu facturi ng Agreeme nt2TP两日试生产,主要是验证供应商的批量供货能力OS零批量,是批量生产前的总演习,批产的全面验证SOP Standard Operation 即批量生产Start-Of-ProductionSta ndard Operat ing Procedure 标准操作程序QSV Qualitaes-Sicher un gs-Vere inbarung 质量保证协议BMG Bau-Muster-Ge nehmigu ng 产品工程样件性能检验认可Nullserie零批量QSR质量体系要求Bias偏差DB Durability Build 样车阶段lead time n.订货至交货的时间sink mark 缩痕LRR launch read in ess reviewYC (Pote ntial Critical Characteristic) 潜在关键特性YS (Potential Significant Characteristic) 潜在重要特性Restriction of Hazardous Substances 简称RoHS SGS, BV, TUV, In tertek, ETC BV-Bureau Veritas 法国国际检验局Front bumper 前保险杠Rear bumper 后保险杠Radiator grille 格栅Headlamp 前大灯Tail lamp-liftgate 尾灯-行李箱盖上Tail lamp-quarter 尾灯-后侧围上Front door trim panel 前门内饰板Rear door trim panel 后门内饰板In terior release han dle bezel 内幵手把手框Power con trols bezel 电动车窗幵关框Window in terior capp ing 窗框饰条Exterior mirror 夕卜后视镜Body side mouldi ng 防擦条Cowl grille通风格栅Roof moldi ng 车顶装饰条Lift gate moldi ng 牌照板支架Lift gate han dle 行李箱盖拉手Weather strip_door openings 门框胶条Weather strip_liftgate行李箱胶条A Pillar Trim A 柱B Pillar Trim upper B 柱上B Pillar Trim lower B 柱下Fro nt scuff Plate 前门槛条Rear scuff plate 后门槛条Back panel trim lower 行李箱门槛条Gar nish trim-Quarter wi ndowCowl trim panel A 柱下Liftgate upper trim 尾门内饰板上Liftgate side trim 尾门内饰板中Liftgate lower trim 尾门内饰板下IPDefroster panel 除霜盖板Con sole中控台Steering column cover 方向机柱上下盖板Cluster 组合仪表Carpet前地毯Trunk carpet 后地毯Front seat 前座椅2nd row seat 第二排座椅burr(金属)flash(塑件)毛边gap间隙defective products 不良品fini shed products 成品disposed products 处理品。
dfa 面向装配的产品设计定义

dfa 面向装配的产品设计定义面向装配的产品设计(Design for Assembly,简称DFA)是指在产品设计阶段充分考虑装配性要求,以便在生产制造阶段实现高效、快速、经济的装配过程。
它是将装配性设计纳入产品设计的重要环节,旨在提高产品的装配性能,降低生产成本,提高生产效率和质量。
在进行面向装配的产品设计时,首先需要考虑产品的结构设计。
产品结构设计应简单明了,尽量减少零部件数量,并且零部件之间的连接应尽量采用简单可靠的方式,以便在装配过程中能够轻松完成。
此外,还应尽量避免使用过多的特殊工具和设备,以减少装配过程中的复杂性和难度。
面向装配的产品设计还需要考虑零部件的标准化和模块化。
通过将零部件进行标准化和模块化设计,可以实现零部件的通用性和互换性,简化装配过程,减少零部件库存,提高生产效率。
此外,标准化和模块化设计还能够降低生产成本,提高产品的可维护性和可升级性。
面向装配的产品设计还需要考虑零部件的尺寸和形状。
尺寸和形状的设计应合理,以便在装配过程中能够减少零部件之间的配合间隙,提高装配的精度和速度。
此外,还应尽量避免零部件之间的复杂装配关系,以减少装配过程中的错误和重复操作。
面向装配的产品设计还需要考虑装配工艺的合理性。
装配工艺应简单明了,以减少装配过程中的操作步骤和工时。
同时,应尽量避免使用过多的专用工具和设备,以降低装配成本。
面向装配的产品设计还需要进行装配性能评估和优化。
通过对产品装配性能的评估,可以发现并解决装配过程中存在的问题和瓶颈,提高装配效率和质量。
同时,还可以通过优化产品设计,进一步提高产品的装配性能,降低生产成本。
面向装配的产品设计是一种重要的设计方法,它将装配性设计纳入产品设计的各个环节,以实现高效、快速、经济的装配过程。
通过合理考虑产品结构设计、零部件标准化和模块化、尺寸和形状设计、装配工艺合理性以及装配性能评估和优化,可以有效提高产品的装配性能,降低生产成本,提高生产效率和质量。
Design for Assembly (DFA)

Design For Assembly
DFA Evaluation Procedure (Lucas Method)
The Lucas method is based on 3 separate and sequential analyses;
4) Select a major functional component for the starting point of the analysis.
5) Categorise all mating components in a logical progression using the Functional Criteria Chart.
Design For Assembly
Functional Analysis
1) Determine the functional requirements of the product.
2) Decide whether the product can be considered as a whole or a series of functional sub-sections.
Design For Assembly
When to use DFA?
DFA is one tool within Concurrent Engineering (CE) – a design philosophy that enhances productivity for time to market, cost and quality.
Hence, the most beneficial time to use the technique is at the concept development stage.
长安福特常用缩写词

长安福特常用缩写词(CP)Confirmation Prototype确认样车Final Status最终状态(J1)Job 1整车投产(PT)P/T Design Complete动力传动系统设计结束PT(P/T)Power Train动力传动系统(ST)Surface Transfer表面参数传递Change Cut-Off更改完成Launch Readiness投产准备就绪Launch Sign-Off投产验收Program Approval项目批准Proportions & Hardpoints比例与固定点Product Readiness产品准备就绪Pre Milestone 1SI前里程碑1Pre Milestone 2SI前里程碑2Strategic Confirmation策略确认Strategic Intent策略意向Strategic Planning策略计划(SP)Structural Prototype样车结构(TTO)Tool Try-Out工装设备试运行Global 8D Eight disciplinary ActionsG8D(福特公司解决问题的标准方法)14DMore Detailed than Global 8D (used to containand resolve stop-shipment/recall problems)更详细的细节(包括并解决停止运货/召回问题)1MIS One Month in Service投入使用1个月1PP First Production Proveout第一次试生产2PP Second Production Proveout第二次试生产3MIS Three Months in Service投入使用3个月4P Production Process Proveout Program生产程序验证项目AAA American Automobile Association美国汽车工业联合会ABS Affordable Business Structure可承受商业结构ABS Anti skid brake system防抱死制动系统AIAG Automotive Industry Action Group 机动车工业行动小组AIC Accelerated Implementation Centre快速实施中心AIM Automated Issues Matrix问题结构图AIMS Automated Issues Matrix System问题结构图系统AME Advanced Manufacturing Engineering先进制造工艺AMPPE Advanced Manufacturing Pre-Program Engineering 先进项目前制造工艺ANOVA Analysis of Variance多样性分析AP Attribute Prototype设计样车APEAL Automotive Performance Execution and Layout机动车性能实施与规划APQP Advanced Product Quality Planning先进产品质量计划ASQ American Society for Quality美国质量协会AV Appraiser Variation评估者的多样性AVT Advance Vehicle Technology先进车辆技术AWS Analytical Warranty System分析性的保修系统AXOD Automatic Transaxle Overdrive Transmission自动变速驱动桥超速档传动系B&ABody & Assembly Operations (New Term: VehicleOperations)车身与组装操作(新术语:车辆操作)BCG Business Consumer Group消费者工作组BIC Best in Class等级中的最佳BIS Body Shop Information System车身工作间信息系统BLI Business Leadership Initiative领导层初始意向BOM Bill OfMaterials零件清单BTB Bumper-to-Bumper保险杠到保险杠BTS Build-To-Schedule按日程建造BUR Business Unit Review业务小组讨论CAS Capacity Analysis Sheet能力分析表C/E Cause & Effect成因及影响CA Customer Attribute消费者特性CAD Computer Aided Design计算机辅助设计CAE Computer Aided Engineering计算机辅助工程CAP Corrective Action Plan纠正行动计划CBG Consumer Business Group消费者业务小组CB Continuous Build连续性生产CC Critical Characteristic评价特性CC Courtesy Copy抄送CC Carbon Copy副本CCC Customer Concern Classification客户问题分类CCC China compulsory certification中国强制认证CDS Component Design Specification零件设计参数CET Campaignable Events Team召回情况小组CETs Common External Tariff普通关税CETP Corporate Engineering Test Procedures公司工程测试程序CFR Constant Failure Rate连续故障率CHFCIM Computer Integrated Manufacturing计算机综合制造CIWG Continuous Improvement Work Group持续改进工作组CL Centerline中心线CMM Coordinate Measuring Machine协调测量设备CMMS Common Material Management System通用材料管理系统CMMS3Common Manufacturing Management System-3通用制造管理系统-3Code X Pre-build focusing on exterior components制造前关注的外部零件Code Y Pre-build focusing on interior components制造前关注的内部零件CP Cost plan(马自达用语)由ECN引起的价格变动估计CP Common Position通用位置CP Confirmation prototype确认样车(FORD 时间节点)C p Relates the allowable spread of thespecification limits to the measure of theactual variation of the process.将参数限制允许限度下的展开与程序实际多样性联系起来CPE Chief Program Engineer首席项目工程师C pk Measures the process variation with respect tothe allowable specification, and takes intoaccount the location of the process average测量程序的多样性并将其考虑到程序平均性的位置中CPU Cost Per Unit单位成本CQDC Corporate Quality Development Center公司质量开发中心CQIS Common Quality Indicator System一般质量指标系统CR Concern Responses问题回复CRT Component Review Team零件讨论组CSA Corporate Security Administrator公司安全管理员CSI Customer Service Index客户服务指数DCO Duty Cycle Output责任循环结果DCP Dynamic Control Planning动态控制计划DDL Direct Data Link直接数据连接Df Degrees of Freedom自由度DFA Design for Assembly总成设计DFM Design for Manufacturability制造能力设计DFMEA Design Failure Mode Effects Analysis故障模式影响分析设计DFR Decreasing Failure Rate故障下降率DMA Database Maintenance Administrator数据库维护管理人员DOE Design of Experiment试验设计DOM Dealer Operations Manager经销商业务经理DP Design Parameters参数设计DQR Durability Quality and Reliability耐久性质量与可靠性DTD Dock to Dock码头至码头DTD Design to Delivery设计到交付DCV Design Confirmation Vehicle设计确认车DV Design Verification设计验证DVM Design Verification Method设计验证方式DVP Design Verification Plan设计验证计划Design Verification Process and Production设计验证程序和产品验证DVP&PVValidationDVP&R Design Verification Plan & Report设计验证计划和结果DVPR Design Verification & Product Reliability设计验证和产品可靠性DVPV Design Verification and Process Verification设计验证和程序验证EAO European Automotive Operations欧洲机动车协会EASI Engineering And Supply Information工程和供应信息ECAR Electronic Connector Acceptability Rating电子连接接受比率EDI Electronic Data Interchange电子数据交换EESE Electrical and Electronic Systems Engineering电力及电子系统工程EMM Expanded Memory Manager扩展内存管理器EMS Environmental Management System环境管理系统EOL End of Line线的端点EQI Extraordinary Quality Initiative特别初始质量ES Engineering Specifications工程参数ESI Early Supplier Involvement早期供应商参与ESP Extended Service Plan延期服务计划ESTA Early Sourcing Target Agreement早期选点目标协议ESWP Early Sourcing Work Plan早期选点工作计划EV Equipment Variation设备变更F&T Facility & Tooling工装设备FACT Facilitation and Certification Training简易化及认证培训FASS Field Action/Stop Shipment区域行动/停止运货区域行动/停止运货(优先使用缩FA/SS Field Action/Stop Shipment (Preferred Acronym)写)FAO Ford Automotive Operations福特机动车协会FAP Ford Automotive Procedure福特机动车程序FAQ Frequently Asked Questions常见问答FCPA Ford Consumer Product Audit福特客户产品审核FCSD Ford Customer Service Division福特客户售后服务分枝机构FDVS Ford Design Verification System福特设计验证系统FER Fresh Eyes Review其它行业人员论证FER Final Engineering Review最终工程论证FEU Field Evaluation Unit区域评估组FIFO First in First Out先进先出FMEA Failure Mode Effects Analysis故障模式影响分析FMVSS Federal Motor Vehicle Safety Standards美国联邦机动车安全标准FPDS Ford Product Development System福特产品开发系统FPS Ford Production System福特生产系统FPSI Ford Production System Institute福特产品系统学院FPS IT Ford Production System Information Technology福特产品系统信息技术FOB Ford of Britain福特英国FQRs Frequent Quality Rejects经常性质量不合格品FR Functional Requirements功能要求FAO (福特机动车运作) 可靠性指FRG FAO Reliability Guide导FS Final Sign-off最终验收FSIC Ford System Integration Council福特系统综合委员会FSN Ford Supplier Network福特供应商网络FSS Full Service Suppliers全方位服务供应商FTDC Fairlane Training and Development Center培训和发展中心FTEP Ford Technical Educational Program福特技术培训项目FTT First Time Through首次通过FUNC-APPRV Functional Approvals功能批准FVEP Finished Vehicle Evaluation Program下线车辆评估项目GAP Global Architecture Process全球建筑设计程序GC Global Craftsmanship全球技术工艺GCARS Global Craftsmanship Attribute Rating System全球技术特性评分系统GCEQ Global Core Engineering Quality全球核心工程质量GEM Generic Electronic Module通用电子模块GIS1Global Information Standards全球信息标准Global Prototype Inventory Requisition andGPIRS全球样车库存及控制安排SchedulingGPP Global Parts Pricing全球零件定价GQRS Global Quality Research System全球质量调查系统GRC UN-ECE Group des Raporteurs de Ceintures欧盟 ECE 安全带规划小组GRC Government Regulations Coordinator政府法规协调员GR&R Gage Repeatability and Reproducibility量具重复性和再现性GRVW Gross Vehicle Weight车辆质量GSDB Global Supplier Database全球供应商数据库GSSM Global Sourcing Stakeholders Meeting全球选点股东大会GYR Green-Yellow-Red绿-黄-红HB Homologation Build法规车制造HI High-Impact重大影响HIC High-Impact Characteristics重大影响特性HR Human Resources人力资源HTFB Hard Tooled Functional Build成形机功能建造HVAC Heating Ventilating and Air Conditioning加热通风和空调ICA Interim Containment Action过渡性补救措施ICCD Intensified Customer Concern Database强化的客户问题数据库ICCD CRSIntensified Customer Concern Database ConcernResolution Specialist 强化的客户问题数据库解决问题专员IE Industrial Engineer产业工程师IFR Increasing Failure Rate 故障率增长ILVS In-Line Vehicle Sequencing车辆顺序IM Industrial Materials工业材料IP Instrument Panel仪表板IPD In Plant Date进厂日IQ Incoming Quality进货质量IQS2Initial Quality Study初始质量研究IR Internal Reject内部不合格品ISO International Organization for Standardization国际标准化组织ISPC In-Station Process Controls过程质量控制JIT Just in Time及时JPH Jobs Per Hour每小时工作量JSA Job Safety Analysis工作安全分析PSW (零件质量合格验收) 未做好KKK PSW not ready for inspection检测准备KLT Key Life Test关键使用寿命测试KO Kickoff起动LCL Lower Control Limit低控制限值LDEM Lean Design Evaluation Matrix设计评估表LOA Letter of Agreement协议书LP&T Launch Planning & Training投产计划和培训LR Launch Readiness投产准备就绪LRR Launch Readiness Review投产准备就绪论证LS Launch Sign-Off投产验收LSL Lower Specification Limit低参数限制LTDB Light Truck Data Base轻型卡车数据库MBJ1Months Before Job One Job1(投产)前1个月MBO Manufacturing Business Office制造办公室ME Manufacturing Engineering制造工程MIS Months in Service使用中的月份MMSA Material Management System Assessment物料管理系统评定MP Mass Production批量生产MP&L Materials, Planning and Logistics材料、计划与物流MPPS Manufacturing Process Planning System制造程序计划系统MOD Module模块MRB Material Review Board物料论证板MRD Material Required Date物料要求到厂日MS Material Specifications物料参数MS3(MSIII)Material Supply Version III物料供应(第三版)MTC Manage the Change管理变更MY Model Year年度车型NAAO North American Automotive Operations北美汽车工业协会NFM Noise Factor Management噪声管理NIST National Institute of Standards and Testing全国标准和测试协会NMPDC New Model Program Development Center新车型项目开发中心Nova C New Overall Vehicle Audit新车总评审NPPR New Program Product Review供应商技术支持NTEI New Tooled End Items新工具加工成品NVH Noise, Vibration, Harshness噪声、振动、操纵平顺性OCM Operating Committee Meeting工作委员会会议OEE Overall Equipment Efficiency总体设备效率OEM Original Equipment Manufacturer设备最初制造厂ONP Owner Notification Program车主告知程序OS Operator Safety操作者安全OTG Open to Go可进行P Diagrams Parameter Diagrams参数图表PA Program Approval项目批准PAG Premier Automotive Group首要机动车项目组PAL Project Attribute Leadership项目特性领导层PAT Program Activity Team, Program Attribute Team, 项目促进小组、项目特性小组和or Program Action Team项目行动小组PCA Permanent Corrective Action持续改进行动PCF Parts Coordination Fixture零件夹具验证PCI Product Change Information产品变更信息PD Product Development产品开发PDL Program Design Language项目设计语言PD Q1Product Development Q1产品开发Q1PDN2Phased Data NotificationPDSA Plan, Do, Study, Act计划、实践、研讨、实施PFMEA Process Failure Mode Effects Analysis程序故障模式影响分析PI Process Improvement程序改进PIPC Percentage of P pk Indices Process Capable P pk指数程序能力百分比Percentage of Inspection Point That SatisfyPIST满足公差要求的检查点百分比TolerancePM Program Manger项目经理PMA Project Management Analyst项目管理分析PMT Program Management Team or Program Module T eam 项目管理组或项目模式组PO Purchase Order采购订单POC Point of Contact联系点POT Process Ownership Team程序所有者小组P p Process Potential程序潜力PP Pilot ProductPP&T Product Planning & Technology产品计划和技术PPAP Production Part Approval Process生产零件批准程序P pk Process Capability程序能力PPC Product Planning Committee产品计划委员会PPL Program Parts List项目零件清单PPMParts per Million (applied to defectiveSupplier parts)零件的百万分比率(适用于供应商不合格零件)PPPM Program and Pre-Production Management程序和投产前管理PR Public Relations公共关系PR Product Requirement产品要求PR Product Readiness Milestone产品就绪时间节点PSO Production Standard Order制造标准订单PSS Private Switching Service私人转接服务PST Program Steering Team项目指导小组PSW Part Submission Warrant零件质量合格验收PTO Powertrain Operations传动系统操纵件PTR Platinum Resistance Thermometer铂金电阻温度计PV Production Validation产品验证PV Process Variables程序变更PV Part Variation零件变更PVBR Prototype Vehicle Build Requirements样车制造要求PVM Production Validation Method产品验证方法PVP Powertrain Validation Program 传动系统验证程序PVT Product Vehicle Team or Plant Vehicle Team产品车辆组或工厂车辆组QA Quality Assurance质量保证QC Quality Control质量控制QCT Quality Cost Timing质量成本时机选择QFD Quality Function Deployment质量功能配备QFTF Quality Focused Test Fleet质量节点测试行动组QLS Quality Leadership System质量领导体系QMS Quality Management System质量管理体系QOS Quality Operating System质量运作体系QOE Quality of Event质量事件QPM Quality Program Manager质量项目经理QPS Quality Process System质量程序系统QR Quality Reject质量不合格QS-9000Quality Systems – 9000质量体系-9000Quality System Assessment for ProductQSA-PD产品开发质量体系评估DevelopmentQTM Quality Team Member质量小组成员QVA Quality-Focused Value Analysis Workshop车间质量重点价值分析R Range范围RFQ Request For Quotation寻求报价R&M Reliability and Maintainability可靠性及可维护性RMS Resource Management System资源管理系统R&R Repeatability and Reproducibility重复性和再现性R&R Roles and Responsibilities职务与责任R&VT Research & Vehicle Technology研究与车辆技术R/1000Repairs per thousand修理千分率RAP Remote Anti-theft Personality module 防盗遥控器个性化模式Robust Engineering Design Process Enabler积极的工程设计程序计划REDPEPRProjectRIE Reliability Improvement Engineer可靠性改进工程师ROA Return on Assets资产回报率ROCOF Rate of Occurrence of Failure故障发生率RPN Risk Priority Number优先处理风险号码RRCL Reliability and Robustness Check List可靠性与强有力的核对表RRDM Reliability and Robustness Demonstration Matrix可靠性与强有力的演示图表RRR PSW rejected PSW (零件质量合格验收) 不合格RWUP RealWorld Usage Profile现实生活使用记录S Standard deviation标准偏差s2Variance多样性SC Significant Characteristics重要特性Significant Characteristics/CriticalSCs/CCs重要特性/评价特性CharacteristicsSCAC Supplier Craftsmanship Advisory Committee供应商技术顾问委员会SCTs Strategic Commodity Teams策略性商品组SDS System Design Specifications系统设计参数SDS Subsystem Design Specification子系统设计参数SEVA Systems Engineering Value Analysis系统工程价值分析Senko Drawing先行图SHARP Safety and Health Assessment Review Process安全和健康评估讨论程序SI System International des Unit国际单位制SIM Supplier Improvement Metrics供应商改进步骤SMART Synchronous Material and Replenishment Trigger同步物料与补给触发器SME Subject Matter Expert主题专家SMF Synchronous Material Flow同步物料流程SOW Statement of Work工作陈述SP Support PlanSP/AP Structural Prototype/Attribute Prototype结构原形/特性原形SP&PI Strategic Process & Product Improvement策略性程序和产品改进SPC Special Product Committee特殊产品委员会SPC Statistical Process Control统计程序控制SPROM Sample Promise Date承诺的样品到货日SREA Supplier Request for Engineering Approval供应商要求工程批准SRI Supplier Responsible Issues供应商责任SSI Sales Satisfaction Index销售满意度指标SSM Strategic Sourcing Meeting策略选点会议ST Surface Transfer表面转移STA Supplier Technical Assistance供应商技术支持STARS Supplier Tracking and Reporting System供应商跟踪及汇报系统SVC Small Vehicle Center小型车中心TA Target Agreement目标协议TB Training Build训练制造TAP Target Achievement Plan目标完成计划TCM Total Cost Management 总成本管理TED Things Engineers Do工程师任务TEG Tooling and Equipment Group工装及设备组TEM Total Equipment Management全部设备管理TGR Things Gone Right事态发展正确TGW Things Gone Wrong事态发展错误TIS Time in Service服务期限TOC Table of Contents目录TPM Total Productive Maintenance全部生产维护TPPS Torque Process Potential Study扭矩程序潜力研究TQC True Quality Characteristics真实质量特性TRIZ (Russian)Theory of Inventive Problem Solving创造性解决问题的理论(俄罗斯) TRMC Timing, Release and Material Control (also 时效性、发布和物料控制(同known as Tar-Mac)Tar-Mac)TS-16949Technical Specification – 16949技术规范-16949 TSP Technical Skills Program技术性技能项目TTO Tool Try Out工装试运行UCL Upper Control Limit上限控制USL Upper Specification Limit参数上限V/C Very or Completely Satisfied非常或完全满意VC Vehicle Center汽车中心VC BuyerVehicle Center Buyer (now Consumer BusinessGroup Buyer)车辆中心客户(现在为商务集团购买客户)VDI Vehicle Dependability Index车辆可靠性指标VDS Vehicle Design Specifications车辆设计参数VDS Vehicle Descriptor Section车辆描述组VER Vehicle Evaluation Ratings车辆评估等级VFG Vehicle Function Group车辆功能组VIN Vehicle Identification Number车辆识别代码VLD Vehicle Line Director车辆生产线总监VO Vehicle Office车辆办公室VO Vehicle Operations车辆运作VOGO Vehicle Operations General Office车辆运作综合办公室VP Vice President副总裁VPMC Vehicle Project Management Coordinator车辆项目管理协调员VPP Vehicle Program Plan车辆项目计划VQL Vehicle Quality Level车辆质量级别VQR Vehicle Quality Review车辆质量研讨VRT Vehicle Review Team车辆研讨小组VRT Variability Reduction Team减少差异小组VRT Vehicle Reduction Team车辆减产小组WAS Work Analysis Sheet工作分析表WCR Worldwide Customer Requirements全球客户需求WERS Worldwide Engineering Release System全球工程发布系统WIP Work In Progress进行中的工作WMI World Manufacturing Identifier世界制造商识别代码WPRC Warranty Parts Return Center维修部件回收中心Potential Significant and CriticalYS/YC潜在的重要和评价特性CharacteristicsRemark: Editor adds the content in shadow. 备注:阴影部分的内容为编者增加。
DFA设计指南-钟元

9.减少零件装配方向
A. 零件的装配方向越少越好
原始的设计
优化的设计
9.减少零件装配方向
B. 零件的装配方向从上至下最好
利用零件自身的重力,设计零件的装配方向从上至下,零件就可以轻松 地被放置到预定的位置,然后进行下一步的固定工序
重力是装配时最好的助手
装配方向
47
9.减少零件装配方向
B. 零件的装配方向从上至下最好
B. 最理想的装配方式:
最理想的装配方式是金字塔式装配方式,一个大而且稳定的零件充当产 品基座放置于工作台上,然后依次至上而下装配较小的零件,最后装配 最小的零件;同时基座零件能够对后续的零件提供定位和导向功能
金字塔式装配
39
6.设计一个稳定的基座
C. 避免把大的零件置于小的零件上装配:
原始的设计
手机的进化
23
2.简化产品设计,减少零件数量
F. 去除标签
标签通过模具成型Fra bibliotek原始的设计
G. 减少紧固件的数量和类型 H. 减少线缆的种类和数量
优化的设计
24
3.减少紧固件的数量和类型
A. 使用同一种类型的紧固件
好处:
减少在设计和制造过程中对多种类型紧固件的管控 对紧固件的购买带来批量上的成本优势 减少装配线上辅助工具的种类 减少操作员的培训 简化装配,提高装配效率 防错,防止产生装配错误
原始的设计
优化的设计
设计多功能塑胶件代替束线带或线夹 19
2.简化产品设计,减少零件数量
原始的设计
优化的设计
利用塑胶的弹性特性来代替弹簧
20
2.简化产品设计,减少零件数量
原始的设计 指甲刀的进化
优化的设计
面向装配的设计概述

Page
5
过程
设计中的制造商和供应商协作 参考面向装配的设计(DFA)指导方针
初步的生产规划和定义
面向装配的设计评估(手工或基于软件的) 成本估计
公差分析
工程建造方面的反馈 测量面向装配的设计的衡量参数 升级生产和供应链规划 在设计回顾中确定可制造性
Page 6
减轻 试图将错误的影响最小化
Page
9
防误措施过程
确定装配次序 对于每个装配步骤,要么执行正式的FMEA过程, 要么口头不正式的询问可能会发生什么样的错误 判断哪些错误是最容易出现或者将对优先考虑的 行动产生最大影响的 确保防误措施的时机和步骤 首先着眼于预防 然后才是检测
Page
CSC TeamSet面向制造的设计(DFM)
Valor-电子产品的面向制造的设计(DFM)
Savantage-电子产品的面向制造的设计(DFM) Moldflow喷射模塑法
生产过程定案 从供应商处获得对初期产品的反馈
通过建造报告获得反馈
合作来精炼设计的可制造性 升级产品估算
升级面向装配的设计衡量参数
产品准备就绪回顾时再次确定可制造性 解决关键的可生产问题 进行产品回顾,确保关键的可生产问题已经解决,得到的 教训已经捕获
Page
7
防错装配(Mistake
Page
15
proofing assembly
ቤተ መጻሕፍቲ ባይዱ
)
防误措施是面向装配的 设计(DFA)的一个必不 可少的组成部分 1.产品中的控制或特性, 以及预防错误、促进正确 生产的过程 2.产品中的简单的,花费 不多的控制和特性以及在 每步操作时发现(然后就 改)错误的过程.
SGM常用缩写
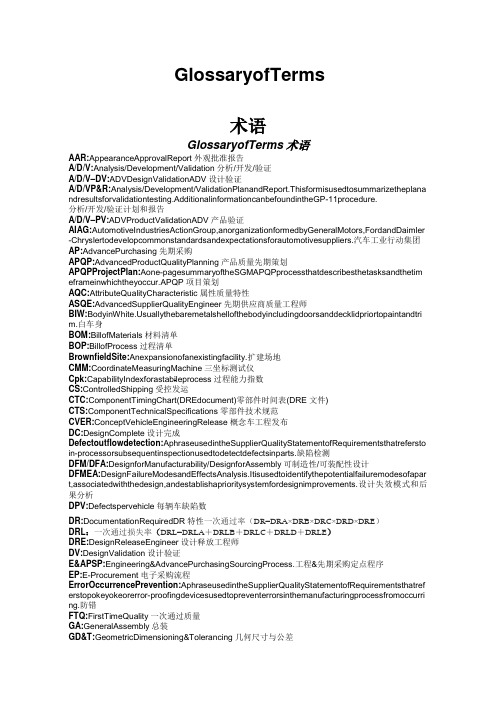
GlossaryofTerms术语GlossaryofTerms术语AAR:AppearanceApprovalReport外观批准报告A/D/V:Analysis/Development/Validation分析/开发/验证A/D/V–DV:ADVDesignValidationADV设计验证A/D/VP&R:Analysis/Development/ValidationPlanandReport.Thisformisusedtosummarizetheplana ndresultsforvalidationtesting.AdditionalinformationcanbefoundintheGP-11procedure.分析/开发/验证计划和报告A/D/V–PV:ADVProductValidationADV产品验证AIAG:AutomotiveIndustriesActionGroup,anorganizationformedbyGeneralMotors,FordandDaimler -Chryslertodevelopcommonstandardsandexpectationsforautomotivesuppliers.汽车工业行动集团AP:AdvancePurchasing先期采购APQP:AdvancedProductQualityPlanning产品质量先期策划APQPProjectPlan:Aone-pagesummaryoftheSGMAPQPprocessthatdescribesthetasksandthetim eframeinwhichtheyoccur.APQP项目策划AQC:AttributeQualityCharacteristic属性质量特性ASQE:AdvancedSupplierQualityEngineer先期供应商质量工程师BIW:uallythebaremetalshellofthebodyincludingdoorsanddecklidpriortopaintandtri m.白车身BOM:BillofMaterials材料清单BOP:BillofProcess过程清单BrownfieldSite:Anexpansionofanexistingfacility.扩建场地CMM:CoordinateMeasuringMachine三坐标测试仪Cpk:CapabilityIndexforastabileprocess过程能力指数CS:ControlledShipping受控发运CTC:ComponentTimingChart(DREdocument)零部件时间表(DRE文件)CTS:ComponentTechnicalSpecifications零部件技术规范CVER:ConceptVehicleEngineeringRelease概念车工程发布DC:DesignComplete设计完成Defectoutflowdetection:AphraseusedintheSupplierQualityStatementofRequirementsthatrefersto in-processorsubsequentinspectionusedtodetectdefectsinparts.缺陷检测DFM/DFA:DesignforManufacturability/DesignforAssembly可制造性/可装配性设计DFMEA:DesignFailureModesandEffectsAnalysis.Itisusedtoidentifythepotentialfailuremodesofapar t,associatedwiththedesign,andestablishaprioritysystemfordesignimprovements.设计失效模式和后果分析DPV:Defectspervehicle每辆车缺陷数DR:DocumentationRequiredDR特性一次通过率(DR=DRA×DRB×DRC×DRD×DRE)DRL:一次通过损失率(DRL=DRLA+DRLB+DRLC+DRLD+DRLE)DRE:DesignReleaseEngineer设计释放工程师DV:DesignValidation设计验证E&APSP:Engineering&AdvancePurchasingSourcingProcess.工程&先期采购定点程序EP:E-Procurement电子采购流程ErrorOccurrencePrevention:AphraseusedintheSupplierQualityStatementofRequirementsthatref erstopokeyokeorerror-proofingdevicesusedtopreventerrorsinthemanufacturingprocessfromoccurri ng.防错FTQ:FirstTimeQuality一次通过质量GA:GeneralAssembly总装GD&T:GeometricDimensioning&Tolerancing几何尺寸与公差SGM:ShanghaiGeneralMotors上海通用汽车GMAP:GeneralMotorsAsianPacific通用汽车亚太GME:GeneralMotorsEurope通用汽车欧洲GMNA:GeneralMotorsNorthAmerican通用汽车北美GP:GeneralProcedure通用程序GPDS:GlobalProductDescriptionSystem全球产品描述系统GPS:GlobalPurchasingSystem全球采购系统GPSC:GlobalPurchasing&SupplierChain全球采购及供应链GR&R:GageRepeatabilityandReproducibility检具重复性及再现性GreenfieldSite:Anewsupplierfacilitythatisbuilttosupportaprogram.GVDP:GlobalVehicleDevelopmentProcess全球整车开发流程IPTV:IncidentsperThousandVehicles每千辆车故障IVER:IntegrationVehicleEngineeringRelease集成车工程发布KCC:KeyControlCharacteristics.Itisaprocesscharacteristicwherevariationcanaffectthefinalpartand/ ortheperformanceofthepart.关键控制特性KCDS:KeyCharacteristicDesignationSystem关键特性指示系统Kick-OffMeeting:ThefirstAPQPsupplierprogramreview.启动会议(第一次APQP供应商项目评审) KPC:KeyProductCharacteristic.Itisaproductcharacteristicforwhichreasonablyanticipatedvariationc ouldsignificantlyaffectsafety,compliancetogovernmentalregulations,orcustomersatisfaction.关键产品特性LAUNCHPLAN:活动计划LAAM:(GeneralMotors)LatinAmerican,Africa&MeddleEast(通用汽车)拉丁美洲、非洲及中东LCR:LeanCapacityRate.ItistheGMdailycapacityrequirement.正常生产能力MCR:MaximumCapacityRate.ItistheGMmaximumcapacityrequirement.最大生产能力MOP:MakeorPurchase制造/采购MPC:MaterialProductionControl物料生产控制MPCE:MaterialProductionControlEurope欧洲物料生产控制MRD:MaterialRequiredDate;datematerialmustbedeliveredinordertoallowabuildeventtobegin.物料需求日期MSA:MeasurementSystemsAnalysis测量系统分析MVBns:ManufacturingValidationBuildnon-saleable非销售车制造验证MVBs:ManufacturingValidationBuildsaleable销售车制造验证NBH:NewBusinessHold停止新业务NoticeofDecision决议通知NS1、2、3、4:不可售阶段OEM:OriginalEquipmentManufacturer主机客户PAD:ProductionAssemblyDocuments生产装配文件PC&L:ProductionControl&Logistics生产控制&物流PDT:ProductDevelopmentTeam产品开发小组PFMEA:ProcessFailureModesandEffectsAnalysis.Itisusedtoidentifypotentialfailuremodesassociat edwiththemanufacturingandassemblyprocess.过程失效模式和后果分析PPAP:ProductionPartApprovalProcess生产件批准程序Ppk:Performanceindexforastableprocess过程能力指数PPM:1)ProgramPurchasingManager,2)PartsperMillion(rejectsandreturnstosuppliers)1)项目经理2)每百万件的产品缺陷数PPV:Product&ProcessValidation产品及过程验证PQC:ProductQualityCharacteristic产品质量特性PR/R:ProblemReporting&Resolution问题报告及解决PSA:PotentialSupplierAssessment,asubsetoftheQualitySystemAssessment(QSA)潜在供应商评审PV:ProductValidation产品验证PVV:准备模型、手工阶段PUS:pickupsheet交货计划单QSA:QualitySystemAssessment质量体系评审QSB:QualitySystemsBasics质量体系基础QTC:QuotedToolCapacity工装报价能力RASIC:Responsible,Approve,Support,Inform,Consult负责、批准、支持、通知、讨论R@R:RunatRate按节拍生产RFQ:RequestForQuotation报价要求RPN:RiskPriorityNumberrelatedtoFMEAdevelopment风险顺序数RPNReductionPlan:Anactionplanthatdescribeswhatisbeingdonetoreducetheriskprioritynumberfo ritemslistedintheDFMEAorPFMEA.降低RPN值计划S1、2、3、4:可销售阶段SDC:SupplierDailyCapacity:合同要求的供应商最高日产能SDE:SupplierDevelopmentEngineer供应商开发工程师SFMEA:SystemFailureModeandEffectsAnalysis系统失效模式分析SMT:SystemManagementTeam系统管理小组SOA:StartofAcceleration加速开始SORP:StartofRegularProduction正式生产SOR:StatementofRequirements要求声明SPC:StatisticalProcessControl统计过程控制SPO:(GeneralMotors)ServiceandPartsOperations(通用汽车)零件与服务分部SQ:SupplierQuality供应商质量SQE:SupplierQualityEngineer供应商质量工程师SQIP:SupplierQualityImprovementProcess供应商质量改进过程SSF:StartofSystemFill系统填充开始SSTS:Sub-systemTechnicalSpecifications子系统技术规范Sub-Assembly/Sub-System:Anassemblyofsub-componentsdeliveredtotheSGMmainproductionli neforinstallationtothevehicleasasingleunit.Subcontractor:Thesupplierofasub-componenttoaComplexSystem/Subassemblysupplier(Tier2,3, etc).分供方SVE:Sub-SystemValidationEngineer子系统验证工程师SVER:StructureVehicleEngineeringRelease.结构车工程发布TeamFeasibilityCommitment:AnAIAGAPQPformthatisprovidedwiththeRequestforQuotation.Itist hesupplier’sconcernswiththefeasibilityofmanufacturingthepartasspecified.小组可行性承诺TKO:ToolingKick-Off模具启动会议UG:UnigraphicsUG工程绘图造型系统VAC:现场控制VLE:VehicleLineExecutive车辆平台负责人VTC:ValidationTestingComplete验证试验完成WO:EngineeringWorkOrder工程工作指令。
质量、品质专业术语

品质专业术语AFR Annual Failure Rate 年度返修率ACC Acceptable 允收-质量AQL Acceptable Quality Level 品质允收水准.ASQ American Society for Quality 美国品质协会AVL Approved Vendor List 合格供应商清单-质量APQP Advanced Product Quality Plan 产品质量先期策划BOM Bill Of Material 材料清单B/R Batch Run 量试-质量C/R Corrective Action 矫正措施CA Customer Service Department 客户服务部-质量CAR Corrective Action Request 矫正措施要求CCC China Compulsory Certificate 中国强制认证(安规)CE Communate Europpene(法语)欧盟CET Customer Experience Test 顾客体验测试CIP Continuous Improvement Program 持续改善项目CLCA Closed Loop Corrective Action 闭环纠正措施CPK Process Capability Index 工序能力指数CSA Canadian Standards Association 加拿大标准协会(安规)CQC China Quality Certification Center 中国质量认证中心CR Control Run 控制运行(特控量试)DFA Design For Assembly 设计的组装性DFM Design For Manufacturing 设计的制造性DFSS Design For Six Sigma 6标准差设计-质量DOE Design Of Experiments 实验设计DPPM Defect Parts Per Million 百万分之不良率DPMO Defects Per Million Opportunities 百万分之不良机会DVT Design Verification Test 设计验证测试% E%DAP Dead after Purchase 购买后损坏DOA Dead On Arrival 开箱损坏ECN Engineering Change Notice 工程变更通知ECR Engineering Change Requirment 工程变更需求ESD Electric Static Discharge 静电放电EVT Engineering Verification Test 工程验证测试EMS Electronic manufacture service 电子制造服务FA Failure Analysis 不良分析FAI First Article Inspection 首件检验FIFO First In First Out 先进先出FPYR First Pass Yield Rate 直通率FMEA Failure Mode Effect Analysis 失效模式影响分析FQA Final Quality Assurance 最终品质保证IPQC In Process Quality Control 制程品质管制IQC Incoming Quality Control 进料品质管制IFIR Initial Field Incident Rate 初期市场不良率JQE Joint Quality Engineer 共同品质工程师. KPI Key Performance Indication 关键业绩指标LRR Lot Reject Rate 批退率LSL Low Specification Limit 规格下限MRB Material Review Board 材料审核会议MSA Measurement System Analysis 测量系统分析ME Manufacturing Engineering 制造工程NCM Non-Conformance Material 不合格品N/A None Available 不合适,不适用NG No Good 不良品NPL Non-Production Loss 非生产漏失ORT On Reliability Test 可靠性测试OQC Outgoing Quality Control 出货品质管制OEM Original equipment manufacturer 原设备制造者ODM Original Design Manufacturer 原设计制造者OBA Out of Box Audit 开箱检查PCB Printed Circuit Board 印刷电路板PCN Process Change Notice 制程变更通知PPAP Production Part Approval Process 生产件批准程序P/N Part Number 料号P/O Purchase Order 采购单(定购单)) PD Production Department 生产部PE Product Engineering 产品工程(部)PQA Process Quality Assurance 制程品质保证PPR Production Pilot Run 生产试做;QA Quality Assurance 品质保证-质量QC Quality Control 品质管制QCC Quality Control Cycle 品管圈QE Quality Engineer 品质工程QFD Quality Function Deployment 品质机能展开QRE Quality Reliability Engineer 品质可靠度工程QS Quality System 品质系统_QSA Quality System Audit 品质系统稽核QPA Quality Process Audit 制程品质稽核REJ Reject 判退RMA Returned Material Authority 客退品职责RPN Risk Priority Number 风险优先数SQE Supplier Quality Engineer 供应商品质工程师SCAR Supplier Corrective Action Report 供应商纠正措施报告SA Sample Approval 标准作业指导书S/N Serial Number 序列号SPC Statistical Process Control 统计制程管制ST Shipment Ticket 出货单SIP Supplier Quality Report Card 检验标准指导书SOP Standard Operation Procedure 作业标准指导书TQC Total Quality Management 全面品质管理TQM Total Quality Control 全面品质管理TÜV technischer überwachungsverein (德语)技术监督协会(安规)USL Upper Specification Limit 规格上限UL Underwriters Lab 美国保险商实验室(安规)VQA Vendor Quality Assurance 供应商品质保证WIP Work In Process 在制品W/H Ware House 仓库Y/R Yield Rate 良率1. 认可的实验室accredited laboratory2. 提前装运通知advanced shipment notification (ASN)3. 基准确定benchmarking4. 经营计划business plan5. 计算机辅助设计computer aided design (CAD)6. 计算机辅助工程computer aided engineering (CAE)7. 校准calibration8. 应急计划contingency plan9. 持续改进计划/方案continuous improvement plan/program10. 合同contract11. 控制计划control plan12. 纠正措施计划corrective action plan13. 不良质量成本cost of poor quality14. 横向职能方法cross-functional approach15. 装配性设计design for assembly (DFA)16. 实验设计design of experiment (DOE)17. 设计纪录design record18. 设计责任供方design-responsible suppliers19. 文件documentation20. 安全关注due care21. 设备equipment22. 工程批准的授权engineering approved authorization23. 执行职责executive responsibility24. 有限元分析finite element analysis (FEA)25. 可行性feasibility26. 先进先出first in first out (FIFO)27. 失效模式及后果分析failure mode and effects analysis (FMEA)28. 功能验证functional verification29. 几何尺寸与公差geometric dimensioning & tolerancing (GD&T)30. 作业指导书job instruction31. 实验室laboratory32. 实验室范围laboratory scope33. 末件比较last off part comparison34. 全尺寸检验layout inspection35. 防错mistake proofing36. 多方论证方法multi-disciplinary approach37. 运行业绩operational performance38. 预见性维护predictive maintenance39. 超额运费premium freight40. 预防性维护preventive maintenance41. 解决问题problem solving42. 程序procedures43. 过程审核process audit44. 过程流程图process flow diagram flow chart45. 产品product46. 产品实现product realization47. 产品审核product audit48. 项目管理project management49. 质量功能展开quality function deployment (QFD)50. 质量手册quality manual51. 反应计划reaction plan52. 外部场所remote location53. 重复性和再现性研究repeatability and reproducibility studies54. 现场site55. 特殊特性special characteristics56. 分承包方subcontractor57. 分承包方的开发subcontractor development58. 供方supplier59. 投标tender附:如何进行工程管理:1、完善筑工程管理相关法律法规在完善建筑工程管理的法律法规方面,首先国家应该给予积极的响应和支持,积极商讨和出台新的相关法律法规,并确保其能够有效实施和落实,为工程管理质量的提高提供逐步完善的法律法规。
上海通用术语

AHE:外观颜色匹配工程师APQP:产品质量先期策划DRE:设计发布工程师DTS:尺寸技术准备ETR:工程试装要求EWO:工程更改FE:功能评估GCA:全球顾客评审GD&T:主要尺寸相关的零件、总成和整车的形位公差图纸,几何尺寸及公差图纸。
GMGlobalAAR---GM全球外观认可报告GP4:生产件批准状况通知-MC0/1基准必须与PTRTE:试验工程师TVE:(动力总成)总认证工程师VPM:整车性能经理IV:工程认可(需要提供零件尺寸报告、材料试验报告、总成性能报告等所有试验报告)MC1/2:尺寸匹配(提交尺寸报告,合格率80%/90%)PVV:产品验证,小批量制造(尺寸报告,零件必须通过GP12)NS:非销售车制造(零件必须通过GP12-100%检验)S:销售车制造(零件通过PPAP人认可,零件必须通过GP12-100%检验)SORP:量产开始(具体数量根据订单,一般IV80套,MC10套,PVV几套到几十套不等。
)AQC:AttributeQualityCharacteristic属性质量特性ASQE:AdvancedSupplierQualityEngineer先期供应商质量工程师BIW:uallythebaremetalshellofthebodyincludingdoorsanddecklidpriortopaintandtrim.白车身BOM:BillofMaterials材料清单BOP:BillofProcess过程清单BrownfieldSite:Anexpansionofanexistingfacility.扩建场地CMM:CoordinateMeasuringMachine三坐标测试仪Cpk:CapabilityIndexforastabileprocess过程能力指数CTC:ComponentTimingChart(DREdocument)零部件时间表(DRE文件)CTS:ComponentTechnicalSpecifications零部件技术规范CVER:ConceptVehicleEngineeringRelease概念车工程发布DC:DesignComplete设计完成Defectoutflowdetection:AphraseusedintheSupplierQualityStatementofRequirementsthatreferstoin-processorsu bsequentinspectionusedtodetectdefectsinparts.缺陷检测DFM/DFA:DesignforManufacturability/DesignforAssembly可制造性/可装配性设计DFMEA:DesignFailureModesandEffectsAnalysis.Itisusedtoidentifythepotentialfailuremodesofapart,associated withthedesign,andestablishaprioritysystemfordesignimprovements.设计失效模式和后果分析DPV:Defectspervehicle每辆车缺陷数DR:DocumentationRequiredDR特性DRE:DesignReleaseEngineer设计释放工程师DV:DesignValidation设计验证E&APSP:Engineering&AdvancePurchasingSourcingProcess.工程&先期采购定点程序EP:E-Procurement电子采购流程)LAAM:(GeneralMotors)LatinAmerican,Africa&MeddleEast(通用汽车)拉丁美洲、非洲及中东LCR:LeanCapacityRate.ItistheGMdailycapacityrequirement.正常生产能力MCR:MaximumCapacityRate.ItistheGMmaximumcapacityrequirement.最大生产能力MOP:MakeorPurchase制造/采购MPC:MaterialProductionControl物料生产控制MPCE:MaterialProductionControlEurope欧洲物料生产控制MRD:MaterialRequiredDate;datematerialmustbedeliveredinordertoallowabuildeventtobegin.物料需求日期MSA:MeasurementSystemsAnalysis测量系统分析MVBns:ManufacturingValidationBuildnon-saleable非销售车制造验证MVBs:ManufacturingValidationBuildsaleable销售车制造验证NBH:NewBusinessHold停止新业务OEM:OriginalEquipmentManufacturer主机客户PAD:ProductionAssemblyDocuments生产装配文件PC&L:ProductionControl&Logistics生产控制&物流PDT:ProductDevelopmentTeam产品开发小组PFMEA:ProcessFailureModesandEffectsAnalysis.Itisusedtoidentifypotentialfailuremodesassociatedwiththema nufacturingandassemblyprocess.过程失效模式和后果分析PPAP:ProductionPartApprovalProcess生产件批准程序Ppk:Performanceindexforastableprocess过程能力指数PPM:1)ProgramPurchasingManager,2)PartsperMillion(rejectsandreturnstosuppliers)1)项目经理2)每百万件的产品缺陷数PPV:Product&ProcessValidation产品及过程验证PQC:ProductQualityCharacteristic产品质量特性SSTS:Sub-systemTechnicalSpecifications子系统技术规范Sub-Assembly/Sub-System:Anassemblyofsub-componentsdeliveredtotheSGMmainproductionlineforinstallationtothevehicleasasingleunit.Subcontractor:Thesupplierofasub-componenttoaComplexSystem/Subassemblysupplier(Tier2,3,etc).分供方SVE:Sub-SystemValidationEngineer子系统验证工程师SVER:StructureVehicleEngineeringRelease.结构车工程发布TeamFeasibilityCommitment:AnAIAGAPQPformthatisprovidedwiththeRequestforQuotation.Itisthesupplier’sconcernswiththefeasibilityofmanufacturingthepartasspecified.小组可行性承诺TKO:ToolingKick-Off模具启动会议UG:UnigraphicsUG工程绘图造型系统VLE:VehicleLineExecutive车辆平台负责人VTC:ValidationTestingComplete验证试验完成WO:EngineeringWorkOrder工程工作指令。
术语词汇表(GM)
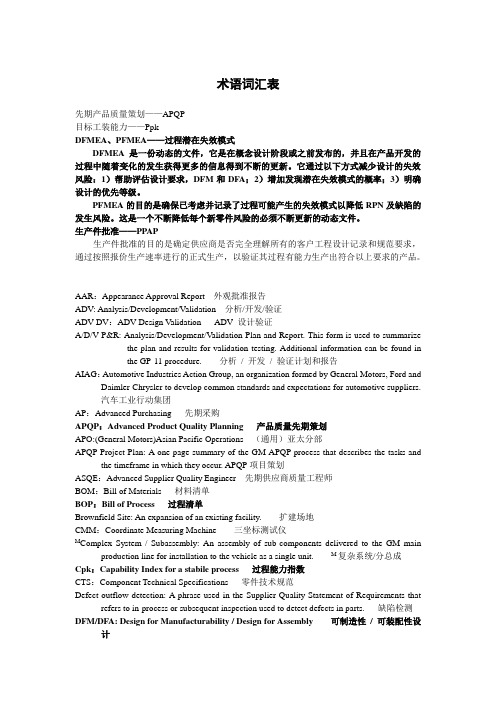
术语词汇表先期产品质量策划——APQP目标工装能力——PpkDFMEA、PFMEA——过程潜在失效模式DFMEA是一份动态的文件,它是在概念设计阶段或之前发布的,并且在产品开发的过程中随着变化的发生获得更多的信息得到不断的更新。
它通过以下方式减少设计的失效风险:1)帮助评估设计要求,DFM和DFA;2)增加发现潜在失效模式的概率;3)明确设计的优先等级。
PFMEA的目的是确保已考虑并记录了过程可能产生的失效模式以降低RPN及缺陷的发生风险。
这是一个不断降低每个新零件风险的必须不断更新的动态文件。
生产件批准——PPAP生产件批准的目的是确定供应商是否完全理解所有的客户工程设计记录和规范要求,通过按照报价生产速率进行的正式生产,以验证其过程有能力生产出符合以上要求的产品。
AAR:Appearance Approval Report 外观批准报告ADV: Analysis/Development/Validation 分析/开发/验证ADV-DV:ADV Design Validation ADV 设计验证A/D/V P&R: Analysis/Development/Validation Plan and Report. This form is used to summarize the plan and results for validation testing. Additional information can be found inthe GP-11 procedure. 分析/ 开发/ 验证计划和报告AIAG:Automotive Industries Action Group, an organization formed by General Motors, Ford and Daimler-Chrysler to develop common standards and expectations for automotive suppliers.汽车工业行动集团AP:Advanced Purchasing 先期采购APQP:Advanced Product Quality Planning 产品质量先期策划APO:(General Motors)Asian Pacific Operations (通用)亚太分部APQP Project Plan: A one-page summary of the GM APQP process that describes the tasks and the timeframe in which they occur. APQP项目策划ASQE:Advanced Supplier Quality Engineer 先期供应商质量工程师BOM:Bill of Materials 材料清单BOP:Bill of Process 过程清单Brownfield Site: An expansion of an existing facility. 扩建场地CMM:Coordinate Measuring Machine 三坐标测试仪M Complex System / Subassembly: An assembly of sub-components delivered to the GM main production line for installation to the vehicle as a single unit. M复杂系统/分总成Cpk:Capability Index for a stabile process 过程能力指数CTS:Component Technical Specifications 零件技术规范Defect outflow detection: A phrase used in the Supplier Quality Statement of Requirements that refers to in-process or subsequent inspection used to detect defects in parts. 缺陷检测DFM/DFA: Design for Manufacturability / Design for Assembly 可制造性/ 可装配性设计DFMEA:Design Failure Modes and Effects Analysis. It is used to identify the potential failure modes of a part, associated with the design, and establish a priority system for design improvements. 设计失效模式分析MPC:Material Production Control 物料生产控制MPCE: Material Production Control Europe 欧洲物料生产控制MRD:Material Required Date; date material must be delivered in order to allow a build event to begin (Pilot, SOR, etc.)物料需求日期MSA:Measurement Systems Analysis 测量系统分析MVBns: Manufacturing Validation Build non-saleable 非销售车制造验证MVBs: Manufacturing Validation Build saleable 销售车制造验证NAO:(General Motors)North American Operations (通用)北美分部NBH:New Business Hold 停止新业务N.O.D.: Notice of Decision 决议通知OEM: Original Equipment Manufacturer 主机客户PAD: Production Assembly Documents 生产装配文件PC&L: Production Control & Logistics 生产控制&物流PDT:Product Development Team 产品开发小组PFMEA:Process Failure Modes and Effects Analysis. It is used to identify potential failure modes associated with the manufacturing and assembly process. 潜在失效模式分析PPAP: Production Part Approval Process 生产件批准程序PPM:1)Program Purchasing Manager 项目采购经理2)Parts per Million(rejects and returns to suppliers) 每百万件的产品缺陷数Ppk: Perfomance index for a stable process 过程能力指数PQC:Product Quality Characteristic 产品质量特性PR/R:Problem Reporting & Resolution 问题报告及解决PSA: Potential Supplier Assessment, a subset of the Quality System Assessment(QSA) 潜在供应商评审QSA:Quality System Assessment 质量系统评审QTC:Quoted Tool Capacity 工装报价能力RASIC:Responsible, Approve, Support, Inform, Consult 负责,批准,支持,通知,讨论RFQ:Request For Quotation 报价要求RPN: Risk Priority Number relater to FMEA development 风险顺序数RPN Reduction Plan: An action plan that describes what is being done to reduce the risk priority number for items listed in the DFMEA or PFMEA. 降低RPN值计划DPV:Defects per vehicle 每辆车缺陷数DRE:Design Release Engineer 设计发放工程师Error Occurrence Prevention: A phrase used in the Supplier Quality Statement of Requirement that refers to poke yoke or error-proofing devices used to prevent errors in the manufacturing process from occurring. 防错EWO:Engineering Work Order 工程更改指令FE 1,2,3: Functional Evaluations 1,2, and 3 功能评估GD&T: Geometric Dimensioning & Tolerancing 几何尺寸&公差GM: General Motors 通用汽车公司GME:General Motors Europe 通用汽车欧洲分部GM 9000:A document provided through Boise Cascade that houses GM specific requirements (General Procedures-GPs) that are referenced in QS 9000.GP: General Procedure 总体步骤GPDS:Global Purchasing System 全球采购系统GQTS:Global Quality Tracking System 全球质量跟踪系统G R&R: Gage Repeatability and Reproducibility 量具的重复性与再现性Greenfield Site: A new supplier facility that is built to support a program. 新建工厂GVDP:Global Vehicle Development Process 全球车辆开发过程IPTV:Incidents per Thousand Vehicles 每千辆车缺陷数KCC:Key Control Characteristics. It is a process characteristic where variation can affect the final part and/or the performance of the part. 关键控制特性KCDS: Key Characteristic Designation System 关键特性指示系统Kick-Off Meeting: The first APQP supplier program review. 启动会议KPC: Key Product Characteristic. It is a product characteristic for which reasonably anticipated variation could significantly affect safety, compliance to governmental regulations, or customer satisfaction. 关键产品特性LAO:(General Motors)Latin American Operations (通用)拉丁美洲分部LCR:Lean Capacity Rate. It is the GM daily capacity requirement. 最低生产能力MCR:Maximum Capacity Rate. It is the GM maximum capacity requirement. 最大生产能力MOP:Make or Purchase 制造/采购SDE:Supplier Development Engineer 供应商开发工程师SCC: Standard Control Characteristics 关键控制特性SFMEA:System Failure Mode and Effects Analysis 系统失效模式分析SMT:System Management Team 系统管理小组SOA:Start of Acceleration 加速开始SOP:Start of Production 正式生产SOR:Statement of Requirements 要求声明SPC:Statistical Process Control 统计过程控制SPC: Standard Product Characteristic 标准产品特性SPO:(General Motors)Service and Parts Operations (通用汽车)零件与服务分部SQ:Supplier Quality 供应商质量SQE:Supplier Quality Engineer 供应商质量工程师SQIP:Supplier Quality Improvement Process 供应商质量改进过程SSF:Start of System Fill 系统填充开始SSTS:Sub-system Technical Specifications 分系统技术规范S.T.E.P: Sourcing Team Evaluation Process, a supplier assessment focused on a specific technology or process at a supplier’s facility. 采购定点小组评估过程M Subcontractor: The supplier of a sub-component to a Complex System/ Subassembly supplier(Tier 2,3,etc). M分供方Team Feasibility Commitment: An AIAG APQP form that is provided with the Request for Quotation. It is the supplier’s concerns with the feasibility of manufacturing the part as specified. 小组可行性承诺UG:Unigraphics UG工程绘图造型系统VDP:Vehicle Development Process 车辆开发过程VLE:Vehicle Line Executive 车辆平台负责人WWP:Worldwide Purchasing 全球采购Supplier DUNS No.: 供应商邓氏编码Commodity:产品Engineering Change Level: 工程更改级别Model Year: 年型----应用于哪年的车型MPC:Main product characteristic 主要产品特性MCC:Main control characteristic 主要过程特性ME:Manufacturing engineer 制造工程师PE:Project engineer 项目工程师PQE:Project quality engineer 项目质量工程师TM:Technical manager 技术经理DRE: Design release engineer 设计发放工程师GP-12 Early Production Containment GP-12早期生产遏制Error proofing:防错Pre-Launch Control Plan: 试生产控制计划PRR:Problem Report and Resolution 问题报告与解决CS:Controlled Shipping 受控发运Appearance Approval Report 外观件批准报告Design engineering approval: 工程设计批准N/A:NOT Applicable 不适用的Conforming: 合格数Non-conforming: 不合格数Product Specification : 产品规格书PCR: Problem Communication Report 问题交流报告Trial mould 软模(试验模),Formal mould硬模(正式模)IMDS : International Material Data SystemCoaxial tolerance: 同轴度,Round corner :圆角环保要求:Environment requirementRetention/contact force:固定力未注尺寸:unspecified dimension/non specified dimension DR:Dimension requirement 尺寸要求APQP 和PPAP过程专业术语AAR Appearance Approval Report 外观批准报告ADV Analysis/Development/Validation 分析/开发/验证ADV-DV ADV Design Validation A D V 设计验证A/D/V P&R Analysis/Development/Validation Plan and Report, This from is used to summarize the plan and results for validation testing. Additional informationCan be found in the GP-11procedure. 分析/开发/验证计划和报告AEC Additional Engineering Changes 附加工程更改ADV-PV ADV product Validation A D V产品验证AIAG Automotive Industries Action Group, an organization formed by General Motors, Ford and Daimler Chrysler to develop common standards and expectationsfor automotive suppliers.汽车工业行动集团AP Advanced Purchasing 先期采购APO (General Motors) Asian Pacific Operations (通用)亚太分部APQP Advanced Product Quality Planning 产品质量先期策划AQE Advanced Quality Engineer 先期质量工程师ASQE Advanced Supplier Quality Engineer 先期供应商质量工程师ANOVA Analysis of Variance方差分析法ASDE Advanced Supplier Development Engineer 高级供应商开发工程师BOM Bill of Materials 材料清单BOP Bill of Process 过程清单CCAR Concern ed and Corrective Action Report 相关整改报告CAR Corrective Action Request 整改需求CFT Cross function Team 多方论证小组CMM Coordinate Measuring Machine三坐标测试仪CPV Weekly Production Volume 周产能CPK Capability Index for a Stabile process 过程能力指数CR Customer Requirements 客户要求CM Commodity Manager 产品经理CCM Corporate Commodity Manager 公司产品经理CS Customer Satisfaction 客户满意度CS 1/2 Level 1/2 Controlled Shipping 1/2级受控发运CTS Component Technical Specifications 零件技术规范DFM/DFA Design for Manufacturability/Design for Assembly 可制造性/可装配性设计DCP Dimension Control Plan (Dynamic Control Plan) 尺寸控制计划(动态控制计划) DOE Design of Experiment试验设计DPV Daily Production Volume 日产量DVP&R Design Validation Plan and Report 设计验证计划和报告DV Design Validation 设计验证DRE Design Release Engineer设计发放工程师DFMEA Design Failure Mode and Effects Analysis设计失效模式及后果分析EWO Engineering Work Order 工程更改指令EDI Electronic Data Interchange 电子数据交换FE1,2,3 Functional Evaluations1,2,and 3 功能评估ES Engineering Specification工程规范EPC Early Production Containment 早期生产遏制FAI First Article Inspection 首件检验FCR Field Call of RateFE Function Evaluation 功能评估FTA Failure Tree Analysis 故障树状分析FTC First Time Capability 试生产能力FTQ First Time Quality 直通率(一次合格率)GR&R Gage Repeatability and Reproducibility 量具的重复性与再现性GD&T Geometric Dimensioning & Tolerancing 几何尺寸&公差GM General Motors 通用汽车公司GME General Motors Europe 通用汽车欧洲部分GP General Procedure 总体步骤GPDS Global Product Description System 全球产品描述系统GPS Global Purchasing System 全球采购系统GQTS Global Quality Tracking System 全球质量跟踪系统GVDP Global Vehicle Development Process 全球车辆开发过程ISIR initial Sample Inspection Report 首次样品检验报告IPTV Incidents per Thousand Vehicles 每千辆车缺陷数IAA Interim Approval Authorization 临时批准授权ICAL Integral Corrective Action List 整体整改列表LCL Lower Control Limit 下控制限控制下限LSL Lower Specification Limit工程规范下限KCC Key Control Characteristic 关键控制特性KCDS Key Characteristics Designation System 关键特性指示系统KPC (GM)Key Product Characteristic关键产品特性LAO (General Motors) Latin American Operations (通用)拉丁美洲分部LCR Lean Capacity Rate, It is the GM daily capacity requirement 最低生产能力MCR Maximum Capacity Rate, It is the GM maximum capacity requirement 最大生产能力MPP Modified Production Part (Nissan Form) 改良生产零件MOP Make or Purchase 制造/采购MRP Manufacturing / Materials Resource Planning 加工/物料资源计划MRR Material Reject Report 物料拒收报告MPC Material Production Control 物料生产控制MPCE Material Production Control Europe 欧洲物料生产控制MRB Material Review Board物料评审MRD Material Required Date 物料需求日期MSA Measurement Systems Analysis 测量系统分析NAO (General Motors) North American Operations (通用)北美分部NCC Non Conformity Cost不良品成本NBH New Business Hold 停止新业务NDA/O Non Disclosure Agreement/Obligation保密协议/和约N.O.D Notice of Decision 决议通知OEE Operating Equipment Effectiveness 操作装置效率OEM Original Equipment Manufacturer原始设备制造商(整车厂)OTS Off Tooling Sample 正式工装/模具生产样品PPAP Production Part Approval Process 生产件批准程序PAD Production Assembly Documents 生产装配文件PC&L Production Control & Logistics 生产控制&物流PSW Part Submission Warrant 零件提交保证书PDT Product Development Team 项目开发组PFMEA Process Failure Modes and Effects Analysis 过程失效模式及后果分析PPM Parts per Million 每百万PSA Potential Supplier Assessment 潜在供应商评审PPK Performance index for a stable process 过程能力指数PFC Process Flow Chart 过程流程图PQC Product Quality Characteristic 产品质量特性PFD Process Flow Diagram 过程流程图PTC Pass Through Characteristic 过程特性?PTR Production Trial Run 生产试行PVP&R Production Validation Plan and Report 产品验证计划与报告PR/R Problem Reporting & Resolution 问题报告及决策PV Production Validation 生产产品验证PRR Problem Resolution Report 问题决策报告QSA Quality System Assessment 质量系统评审QSB Quality System Base 质量体系基础QSR Quality System Requirement质量体系要求QTC Quotes Tool Capacity 工装报价能力QFD Quality Function Deployment质量功能展开QOS Quality Operating System 质量运行体系QR Quality Reject/Report 质量拒收/报告?R@R Run at Rate 产能审核(产能审核指的是按照正常的生产状态进行审核,其中包括人员,设备,工装,材料和工艺。
DFA_PRES_TO_NPI_NY

Improved serviceability of product in field
All reductions equal a reduction in total product cost!!!!
Serviceability
Cost savings
INFLUENCE OF DFA (CONT’D)
Cost savings Serviceability
INFLUENCE OF DFA (CONT’D)
HOW DOES DFA HELP REDUCE COSTS?
Less parts
Reductions in number of fixtures required Reduction in number of set-ups/ process steps Reduction in process footprint Reduction in number of suppliers
OUR HISTORY USING DFA (cont’d)
Things were getting better but, the were still issues:
When Reviews were held, the design was fully underway and already agreed upon as well as tooling underway. There was very little time to “go back” and address what Manufacturing’s needs and wants. To go back and “fix” Manufacturing’s wants could and would effect the Program’s 3 Ons On Time On Budget On Spec.
什么是DFA-DFM-DFMA

From the BDI website © Boothroyd & Dewhurst Institute website
1
Progression of the development of DFMA: how it developed DFA DFM DFMA DFE
Product Costs
4% 24%
Model T manufacturing requirements
• Shipping crates for floorboards • Choke • Operating Door • Paint colour • Assembly Line
DFA
simplify & reduce parts
DFM DFMA
4
Types of Assembly Types of Assembly
DFA Guidelines DFA Guidelines
1. 2. 3. 4. 5. 6. 7. Reduce number of parts Reduce number of different parts - Standardize parts Simplification of assembly Reduction number of processes Less fasteners especially screws & bolts Reduce tangling Orientation 1. Critical orientation – obvious – see & fit 2. Non-critical orientation – fit in any direction Ensure access & visibility Easy part handling Assemble from top Reduce locating/alignment operations – manual/time consuming
boothroyd-dewhurst method介绍 -回复

boothroyd-dewhurst method介绍-回复Boothroyd-Dewhurst Method: An Efficient Approach towards Design for AssemblyDesign for Assembly (DFA) is a crucial aspect of product development, aiming to optimize the assembly process by simplifying the product's design and reducing manufacturing costs. The Boothroyd-Dewhurst Method, also known as the Design for Assembly (DFA) method, is a systematic approach that helps engineers analyze product designs and identify areas for improvement in terms of assembly time, cost, and ease.First introduced by Dr. Geoffrey Boothroyd and Peter Dewhurst in the 1960s, the Boothroyd-Dewhurst Method has become widely adopted in various industries, from automotive to electronics, for its effectiveness in enhancing product manufacturability. This method utilizes a set of guidelines and rules to evaluate components and their interactions, ultimately providing design recommendations for achieving a more efficient assembly process.The Boothroyd-Dewhurst Method consists of several essential steps, which we will explore in detail below:Step 1: Functional AnalysisThe first step in applying the Boothroyd-Dewhurst Method is to conduct a thorough functional analysis. This involves breaking down the product's overall function into sub-functions and understanding how each component contributes to the product's overall performance. By developing a comprehensive understanding of the product's functional requirements, engineers can identify potential design improvements.Step 2: Component CountOnce the functional analysis is completed, engineers move on to the next step, which involves determining the total number of components required for assembly. Identifying unnecessary or redundant parts is essential as it contributes to reducing assembly time and cost.Step 3: Assembly Time CalculationIn this step, the Boothroyd-Dewhurst Method guides engineers in estimating the required time for assembling each component. By considering factors such as the number of fasteners, orientation requirements, and accessibility, engineers can pinpoint areas wherecomponent design modifications could lead to time savings during assembly.Step 4: Assembly Complexity AnalysisTo identify potential issues and complexity in the assembly process, engineers analyze the product's components and their interaction. This step involves evaluating factors such as part handling, insertion, alignment, and fastening. By identifying areas of complexity, engineers can propose design changes that simplify assembly operations.Step 5: Assembly EvaluationAfter analyzing the product's assembly complexity, engineers use a scoring system to evaluate the ease of assembly for each component. This evaluation is based on predetermined guidelines that consider factors such as part shape, size, and manufacturing tolerances. By quantifying the ease of assembly, engineers can prioritize design changes based on their impact on reducing assembly time and cost.Step 6: Assembly Improvement SuggestionsThe Boothroyd-Dewhurst Method suggests design modificationsbased on the outcomes of the previous steps. These modifications can include changes to component shapes, alterations to mating features, or improvements in fastening methods. By implementing these suggestions, engineers can minimize assembly time and costs while maintaining or enhancing the product's functionality and quality.Step 7: Evaluation of Suggested ImprovementsIn this final step, engineers assess the impact of the suggested design improvements on assembly time and cost. Using advanced software tools or simulation models, engineers can quantify the potential savings in terms of time and cost. This evaluation helps identify the most effective design modifications and allows engineers to refine and finalize the product design.By following the Boothroyd-Dewhurst Method, engineers can achieve significant improvements in the design for assembly process. This method facilitates the identification of design issues that may hamper efficient assembly and provides practical recommendations for optimizing product designs. By implementing these recommendations, manufacturers can reduce assembly time, lower manufacturing costs, increase product quality,and enhance overall customer satisfaction.In conclusion, the Boothroyd-Dewhurst Method is a systematic approach that revolutionizes the design for assembly process. Its step-by-step procedures and guidelines enable designers and engineers to identify inefficiencies in product designs and propose effective solutions that streamline the assembly process. By adopting this method across industries, manufacturers can benefit from enhanced productivity, reduced costs, and improved product quality.。
SGM常用缩写
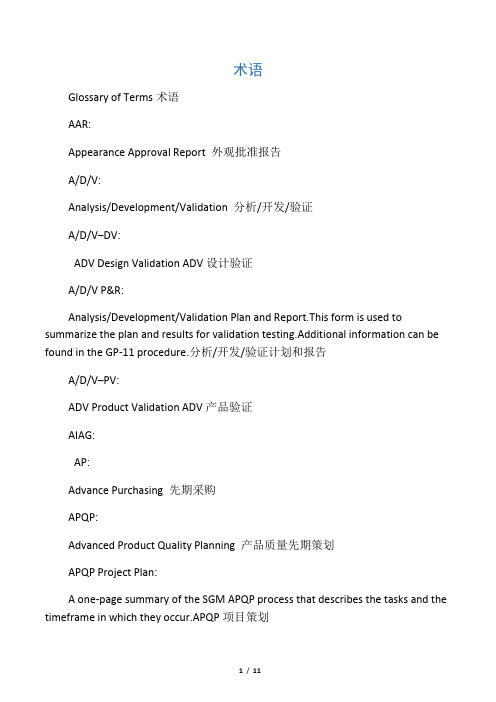
术语Glossary of Terms术语AAR:Appearance Approval Report 外观批准报告A/D/V:Analysis/Development/Validation 分析/开发/验证A/D/V–DV:ADV Design Validation ADV设计验证A/D/V P&R:Analysis/Development/Validation Plan and Report.This form is used to summarize the plan and results for validation testing.Additional information can be found in the GP-11 procedure.分析/开发/验证计划和报告A/D/V–PV:ADV Product Validation ADV产品验证AIAG:AP:Advance Purchasing 先期采购APQP:Advanced Product Quality Planning 产品质量先期策划APQP Project Plan:A one-page summary of the SGM APQP process that describes the tasks and the timeframe in which they occur.APQP项目策划Attribute Quality Characteristic 属性质量特性ASQE:Advanced Supplier Quality Engineer 先期供应商质量工程师BIW:Body in White. Usually the bare metal shell of the body including doors and deck lid prior to paint and trim.白车身BOM:Bill of Materials 材料清单BOP:Bill of Process 过程清单Brownfield Site:An expansion of an existing facility.扩建场地CMM:Coordinate Measuring Machine 三坐标测试仪Cpk:Capability Index for a stabile process 过程能力指数CS:Controlled Shipping 受控发运CTC:Component Timing Chart (DRE document)零部件时间表(DRE文件)Component Technical Specifications 零部件技术规范CVER:Concept Vehicle Engineering Release 概念车工程发布DC:Design Complete 设计完成DFM/DFA:Design for Manufacturability / Design for Assembly 可制造性/可装配性设计DFMEA:Design Failure Modes and Effects Analysis.It is used to identify the potential failure modes of a part, associated with the design, and establish a priority system for design improvements.设计失效模式和后果分析DPV:Defects per vehicle 每辆车缺陷数DR:Documentation Required DR特性一次通过率(DR=DRA×DRB×DRC×DRD×DRE)DRL:一次通过损失率(DRL= DRLA+DRLB+DRLC+DRLD+DRLE)DRE:Design Release Engineer 设计释放工程师DV:Design Validation 设计验证E&APSP:Engineering & Advance Purchasing Sourcing Process.工程&先期采购定点程序EP:E-Procurement 电子采购流程Error Occurrence Prevention:A phrase used in the Supplier Quality Statement of Requirements that refers to poke yoke or error-proofing devices used to prevent errors in the manufacturing process from occurring.防错FTQ:First Time Quality 一次通过质量GA:General Assembly 总装GD&T:Geometric Dimensioning & Tolerancing 几何尺寸与公差SGM:ShanghaiGeneral Motors 上海通用汽车GMAP:General Motors Asian Pacific 通用汽车亚太GME:General Motors Europe 通用汽车欧洲GMNA:General Motors North American 通用汽车北美GP:General Procedure 通用程序GPDS:Global Product Description System 全球产品描述系统GPS:Global Purchasing System 全球采购系统GPSC:Global Purchasing & Supplier Chain 全球采购及供应链GR&R:Gage Repeatability and Reproducibility 检具重复性及再现性Greenfield Site:A new supplier facility that is built to support a program. GVDP:Global Vehicle Development Process全球整车开发流程IPTV:Incidents per Thousand Vehicles 每千辆车故障IVER:Integration Vehicle Engineering Release 集成车工程发布KCDS:Key Characteristic Designation System 关键特性指示系统Kick-Off Meeting:The first APQP supplier program review.启动会议(第一次APQP供应商项目评审)KPC:LAUNCH PLAN:活动计划LAAM:(General Motors) Latin American, Africa & Meddle East(通用汽车)拉丁美洲、非洲及中东LCR:Lean Capacity Rate.It is the GM daily capacity requirement.正常生产能力MCR:Maximum Capacity Rate. It is the GM maximum capacity requirement.最大生产能力MOP:Make or Purchase 制造/采购MPC:Material Production Control 物料生产控制MPCE:Material Production Control Europe 欧洲物料生产控制MRD:Material Required Date; date material must be delivered in order to allow a build event to begin.物料需求日期MSA:Measurement Systems Analysis 测量系统分析MVBns:Manufacturing Validation Build non-saleable 非销售车制造验证MVBs:Manufacturing Validation Build saleable 销售车制造验证NBH:New Business Hold 停止新业务N.O.D.:Notice of Decision 决议通知NS1、2、3、4:不可售阶段OEM:Original Equipment Manufacturer 主机客户PAD:Production Assembly Documents 生产装配文件PC&L:Production Control & Logistics 生产控制&物流PDT:Product Development Team 产品开发小组PFMEA:Process Failure Modes and Effects Analysis.It is used to identify potential failure modes associated with the manufacturing and assembly process.过程失效模式和后果分析Production Part Approval Process 生产件批准程序Ppk:Performance index for a stable process 过程能力指数PPM:1) Program Purchasing Manager, 2) Parts per Million (rejects and returns to suppliers)1)项目经理2)每百万件的产品缺陷数PPV:Product & Process Validation 产品及过程验证PQC:Product Quality Characteristic 产品质量特性PSA:Potential Supplier Assessment, a subset of the Quality System Assessment (QSA)潜在供应商评审PV:Product Validation 产品验证PVV:准备模型、手工阶段PUS:pick up sheet 交货计划单QSA:Quality System Assessment 质量体系评审QSB:Quality Systems Basics 质量体系基础Quoted Tool Capacity 工装报价能力RASIC:Responsible, Approve, Support, Inform, Consult 负责、批准、支持、通知、讨论R@R:Run at Rate 按节拍生产RFQ:Request For Quotation 报价要求RPN:Risk Priority Number related to FMEA development 风险顺序数RPN Reduction Plan:An action plan that describes what is being done to reduce the risk priority number for items listed in the DFMEA or PFMEA.降低RPN值计划S1、2、3、4:可销售阶段SDC:Supplier Daily Capacity:合同要求的供应商最高日产能SDE:Supplier Development Engineer 供应商开发工程师SFMEA:System Failure Mode and Effects Analysis 系统失效模式分析SMT:System Management Team 系统管理小组SOA:Start of Acceleration 加速开始SORP:Start of Regular Production 正式生产SOR:Statement of Requirements 要求声明SPC:Statistical Process Control 统计过程控制SPO:(General Motors) Service and Parts Operations(通用汽车)零件与服务分部SQ:Supplier Quality 供应商质量SQE:Supplier Quality Engineer 供应商质量工程师SQIP:Supplier Quality Improvement Process 供应商质量改进过程SSF:Start of System Fill 系统填充开始SSTS:Sub-system Technical Specifications 子系统技术规范Sub-Assembly/ Sub-System:SVE:Sub-System Validation Engineer 子系统验证工程师SVER:Structure Vehicle Engineering Release.结构车工程发布Team Feasibility Commitment:An AIAG APQP form that is provided with the Request for Quotation.It is the supplier’s concernswith the feasibility of manufacturing the part as specified.小组可行性承诺TKO:Tooling Kick-Off 模具启动会议UG:Unigraphics UG工程绘图造型系统VAC:现场控制VLE:Vehicle Line Executive 车辆平台负责人VTC:Validation Testing Complete 验证试验完成WO:Engineering Work Order 工程工作指令11/ 11。
整车开发过程中的英文缩写-汽车行业的你一定要知道的

整车开发过程中的英文缩写-汽车行业的你一定要知道的小编整理的一份超级全面的整车开发过程中用到的英语,供大家参考整车开发通用英文缩写(按首字母排序)英文缩写英文全称中文含义(按首字母排序)100% Cal 100% Calibration 100%标定100% IVER 100% Integration Vehicle EngineeringRelease100%集成车工程发布100% PPAP All parts at full PPAP for Vehicleprogram为了整车项目,所有零件PPAP100% SVER 100% Structure Vehicle EngineeringRelease100%结构车工程发布65% Cal 65% Calibration 65%的动力总成标定80% Cal 80% Calibration 80%的动力总成标定8D 8 Disciplines 问题解决8步法A Alpha Alpha阶段(动力总成产品阶段)A MRD Alpha Material Required Date Alpha样件需求日期A/T Automatic Transmission 自动变速器A/T Automatic Transmission 自动变速器AA Architecture Approval 架构批准AAM Alliance of Automobile Manufactures 汽车制造商联盟ABS Anti-lock Brake System or Anti-BlockSteering防抱死制动系统AC Architecture Confirmation 架构确认ACE Assistant Chief Engineer 总工助理ACT Activity 工艺路线ACT BOM Assembly Component Tree BOM 总成件树形BOMAD Alternatives Development 主题开发ADV Analysis / Development / Validation 分析/开发/验证ADV Analysis, Development and Validation 分析,开发和认证AE Application Engineer 应用工程师AE Application Engineer 应用工程师AEM Assimilability evaluation method 可装配性评估方法AFI Architecture Framing Initiation 架构框架启动AIAC Automotive Industry Action Group 美国汽车工业行动集团ALY Alloy 铝合金AMT Automatic Machincal Transmission 机械式自动变速器ANSI American National Standards Institute 美国国家标准协会AP Advanced Purchasing 提前采购AP Assembly Plant 总装厂APB Automotive Product Board 汽车产品委员会APD Approved Product Description 批准的产品描述APE Annual Program Execution 年度项目执行APEC Asia Pacific Economic Cooperation 亚太经济联盟APQP/CP Advanced Product Quality Planning andControl Plan先期产品质量规划和控制计APSB Asia Pacific Strategy Board 亚太战略委员会(通用汽理组织)AR Appropriation Request 项目预算ARC Architecture Refinement Complete 架构优化完成ASB Automotive Strategy Board 汽车战略委员会(通用汽理组织)ASC 经销商售后管理系统ASE Automotive Safety Engineering 汽车安全工程ASE Aftersales Engineering 售后工程ASN Advanced shipping notice 发货通知单ASSI Architecture Statement of StrategicIntent战略意向的架构陈述Assy Check-in Assembly Line Check-in 装配线进场启动现场安调Assy PPAP Assembly Line PPAP 装配线通过PPAPAssy PPAP Assembly Line PPAP 装配线通过PPAPAssy PPV Assembly Line Products and ProcessValidation装配线交付后的产品工艺验Assy PPV Assembly Line Production and ProcessValidation装配线交付后产品工艺验证Assy Run-Off Assembly Line Run-Off 装配线试装交样日期Assy Run-off Assembly Line RUN-Off 装配线整线打通,启动试工装配Assy Run-off MRD Assembly Line RUN-Off Material RequiedDate装配线ATC Auto Temperature Controller 自动空调控制器ATF Automatic Transmission Fluid 自动变速箱油ATT Attachment 附件ATT Actual takt time 实际单件工时AVD Advanced Vehicle Development 先期车辆开发AVDC Advance Vehicle Development Center 先期车辆开发中心AVD-LT Advanced Vehicle Development-LeadershipTeam前期整车开发-领导小组AVDP Advanced Vehicle Development Process(Time between DSI and VPI)先期车辆开发流程(在DS间)AVPM Advanced Vehicle Planning Manager 先期车辆计划经理B Beta Beta阶段(动力总成产品阶段)B Build 制造B MRD Beta Material Required Date Beta样件需求日期B+U Building and Utility 土建公用BAD Build Authorization Document 试制授权文档BC Business Case 业务计划BCM Body Control Module 车身控制器BDC Body Distributon Central 车辆调配中心BESC Base Engine Steering Committee 发动机总成战略转向委员会BIQ Building in Quality 制造质量BIR Prototype Build Issue Report 试制问题报告BIR Build Issues Resolution 试制问题BIR Build Incident Report 装车问题报告BIR Bulding issue report 造车问题报告BIW Body-In-White 白车身BIW Body in White 白车身BOD Bill of Design 设计清单BOE Bill of Equipment 设备清单BOM Bill of Material 物料清单BOM Bill of Material 物料清单BOM Bill of Material 物料清单BOM Bill Of Material 物料清单BOM Bill Of Material 物料清单BOM Bill of Material 物料清单BOP Bill of Process 工艺清单BOP Bill Of Process 工艺清单BP Break Point 断点BPD Business Plant Deployment 业务计划实施BPP Best people practices 最佳人员准则BPR Business plan recompose 业务流程重组BS Body Shop 车身车间BSD Build Site Direction 试制现场指导书BUFFER Buffer 线边缓存区C/CAP Construction/Conversionand Acceleration Plan土建/改造和生产提速计划CAB Change Approval Board 更改审批会CAC 服务热线专员CAFE Corporate Average Fuel Economy 公司平均油耗Cal Calibration 动力总成标定CARE Customer acceptance review evaluation 整车报交检查CARE Customer Acceptance & Review Evaluation 用户接受度和审查评估CC Concept Confirmation 验证概念CC Consolidation Center 集散中心CC Confirmation Clinic 确认临床Cert LSO Certification Lift Stop Order 通过排放认证通知CET Cold Environment Test 寒区试验CH Chassis Department 底盘部CI Concept Initiation 提出项目概念CIM Customer Interface Manager 客户服务经理CIP Continue Improve Process 持续改进CIP Continue Improve Process 持续改进CIT Continuous Improvement Team 不断改进小组CIT Compartment Integration Team 车厢集成小组CMC Container Management Center 空箱管理中心CME Change Management Engineer 更改管理工程师Cmk N/A 临界机器能力指数Cmk Capability Machine Index 机器设备能力CMM 三坐标测量C-NCAP China New CAR Assessment Process 中国标准新车评估体系COC Centre of Competence 能力中心COE Center of Expertise 经验总结中心CP Control Plan 控制计划CPIT Current Product Improvement Team 现有产品改进小组Cpk Complex Process Capability 过程能力指数Cpk Process Capability Index 稳定过程的能力指数CPQE Current Product Quality Engineer 现有产品质量工程师CPV Cost per Vehicle 单车成本CR/DN Change Request / Decision Notice 更改决议CR/DN Change Request/Decision Notice 变更申请/决议通知CRB Change Review Board 更改评审小组CS Contract Signing 动力总成签署项目合同CS Contract Signing 合同签订CS1 Controled Shipping 1 一级受控发运CS2 Controled Shipping 2 二级受控发运CSC Controls Steering Committee 控制模块战略转向委员会CSI Customer Satisfaction Index 用户满意度指标CSI Customer Satisfaction Index 售后满意度CSN Current Sequence Number 流水号CSO Contract Sign-Off 合同签署CSO Contract Sign-Off (VDP) 整车签署项目合同(VDP术CSO HC Contract Sign-Off Health Check 合同签署健康检查CSO HC Contract Sign-Off Health Check 合同签署健康检查CT Cycle Time 制程周期CT Cycle time 周期时间CT Creativity Teams 创造性工作小组CT Critical Test 关键试验CTS Component Technical Specification 零部件技术标准CTT Common Timing Template 标准2级进度模板CVER Concept Vehicle Engineering Release 概念车工程发布CVER LL Concept Vehicle Engineering ReleaseLong Lead概念车工程发布--长周期CVIS Completed Vehicle Inspection Standards 整车检验标准CVQC Completed vehicle quality ceter 整车质量中心CVQCB Completed vehicle quality ceter board 整车质量目视板CVT Continuously Variable Transmission 无级变速器D.Q.R 合格率概况DAS Design & Analysis Section 设计分析科DC Deliver Charter 递交项目章程DCN Design Change Notice 设计更改通知DCN Design Change Notice 设计更改通知DCP Dimension Control Plan 尺寸控制计划DCS Design Concept Sheet 概念设计表DCT Double Clutch Transmission 双离合器变速箱DD Direct Delivery 直接投线DDSP Driver Door Switch Pack 驾驶席门控开关DEI Die Engineering Integration 模具工程集成DFA Design for Assembly 装配工艺性设计DFM Design for Manufacturability 制造工艺性设计DFMEA Design failure mode and effects analysis 设计失效模式和效果分析DFMEA Design FMEA 设计失效模式分析DIFF Differential 差速器DL 3b Design Level 3b 设计阶段3bDMS Dealer Manage System 经销商管理系统DOL Dealer On Line 经销商在线系统DP Demand Plan 需求计划DPV Defects per vehicle 单车缺陷数DPV Defect per Vehicle 单车缺陷数DQ&V Design Quality & Validation 设计质量和验证DR Direct run 直接通过率DRC Design Review Committee 设计评审委员会DRE Design Responsible Engineer 设计和发布工程师DRE Design Release Engineer 设计发布工程师DRE Design release engineer 设计发布工程师DRL Direct run loss 直接通过损失率Drop Off Drop Off 停产DS44 HIGH SPEED DURABILITY TEST 高速耐久试验(MGRES 标准DSG Direct shift gearbox 双离合器变速箱DSI Document of Strategic Intent 战略意向书DSM Driver Seat Module 驾驶席座椅控制模块DSO Design Sign Off 设计签署DTA Design Theme Alternatives 设计主题选项DTC Diagnostic Trouble Code 诊断故障码DV Design Validation 设计验证DV Design Validation 产品设计验证DVP Design Validation Plan 设计验证计划DVT Dynamic vehicle test 整车综合动态测试E/T/C Engine/Transmission/Controller 发动机/变速器/控制模块EBA Emergency Brake Assistant 紧急制动辅助系统EBD Electronical Brake Distribute 电子制动力分配系统EBOM Engineering BOM 工程BOMEC Embedded Controller 控制模块ECC ERP Central Component ERP核心组建ECR Engineering Change Request 工程更改请求ECR Engineering Change Request 工程更改请求ECR Engineering Change Request 工程更改申请ECR Engineering Change Request 工程项目变更申请ECS Engineering Change Summary 工程变更摘要ECT Emission Control System 电子控制自动变速器EDS Electronic Data Systems 电子数据系统EEVC European Enhanced Vehicle-Safety Committee欧洲提高车辆安全性委员会EFEO Emissions & Fuel Economy 排放和燃料经济EGM Engineering Group Manager 产品工程小组经理EI&S Electronics Integration & Software 电器零件集成和软件ELV End of life vehicle 整车寿命结束EMlS Emission 排放EMS Engine Management System 发动机管理系统ENB Build-Test Section 试制试验科E-NCAP Euro New Car Assessment Process 欧洲标准新车评估体系ENG Engineer 工程师EOA End of Acceleration 生产提速的完成EOLT End of Line Test 生产线试验结束EP Engineering Prototype 工程样车(件)EPA Environmental Protection Agency 环境保护厅EPC Engineering Program Committee 工程项目委员会EPN Engineering Project Number 工程项目数目ERD Early Requirement Document 早期的要求文件ESB European Strategy Board 欧洲战略委员会(通用汽理组织)ESO Engineering Sign Off 发动机整机工程签署ESO Engineering Sign Off 工程签署ESO Engineering Sign-off 工程签署ET Engineering Technology 工程技术EV Engineering Vehicle 工程样车EWO Engineering Work Order 工程工作指令EWO Engineering Work Order 工程更改号EWO Engineering workorder 工程更改流程Exp Cal Experimental Calibration 尝试性标定FA Final Approval 批准正式生产FAC 集团销售经理FATG Final Approval to Grain 生产最终批准FBIW First Body in White Complete 第一轮白车身完成FE Functional Evaluation 功能评估FE LSO Fuel Economy Label Lift Stop Order 通过油耗认证的通知FIVC First Integration Vehicle Complete 第1辆集成车制造完毕FIVC First Integration Vehicle Complete 第一轮集成车完成FLO Factory Layout 工厂布局FM 功能尺寸FM Finance Manager 财务经理FMC First Mule Complete 第一轮骡子车完成FMC 区域售后支持FMEA Failure model effectiveness analysis 失效模式分析FMEA Failure model effectiveness analysis 失效模式分析FMEA Failure Mode and Effects Analysis 潜在失效模式及后果分析FMEA Failure mode and effects analysis 失效模式和后果分析FMEA Failure Mode and Effect Analysis 失效模式和影响分析FMS Flexible manufacturing systems 柔性制造系统FMVSS Federal Motor Vehicle Safety Standards 联邦汽车安全标准FPPV BIW First Product/Process Body in WhiteComplete第一轮产品/工艺白车身完FPPVC First Product/ProcessValidation Vehicle Complete第一轮产品/工艺验证车辆FPS Fixed Point Stop 固定停止位置FTC First Time Capability 首次能力FTP/FTQ First time pass/quality 一次通过合格率FTQ First time quality 下线合格率FWD Four Wheel Drive 四轮驱动G Gamma Gamma阶段(动力总成产品阶段)G MRD Gamma Material Required Date Gamma样件需求日期G/L Group leader 工段长GA General Assembly 总装GA General Assembly 总装GADT Global Architecture Development Team 全球架构开发小组GBOM Global Bill of Material 全球物料清单GMNA General Motors North America 通用汽车北美分部GMPT General Motors Powertrain 通用汽车动力总成分部GPDC Global Product Development Council 全球产品开发理事会GPDP Global Powertrain Development Process 全球动力总成开发流程GPDS Global Product Description System 全球产品管理系统GSD Global Segment Director 全球细分主管GSS Global Sales and Service 全球销售和服务GVDP Global Vehicle Development Process 全球整车开发流程GVDP Global Vehicle Development Process 整车开发流程GVDP Global Vehicle Development Process 整车开发流程GVDP Global Vehicle Development Process 全球汽车开发流程GVDP Global Vehicle Development Process 全球整车开发流程GVDP Global Vehicle Development Process 整车开发流程GVLE Global Vehicle Line Executive 整车平台执行GVW Gross Vehicle Weight 车辆总重GW Gateway 网关HET Hot Environment Test 热带试验HRC Hardware Release Center 硬件发布中心ICD Interface Control Document 接口控制文件IDR Initial Data Release 初始数据发布IDSR Integration DrivenSubsystem Requirement集成驱动子系统要求ILP Inbound Logistic Planning 入厂物流规划IMES Integration Manufacturing ExecutiveSystem生产执行系统Initial Cal Initial Calibration 初始标定IOM Inspection operator method 检验操作方法IOS Inspection operator summary 检验操作概要IPPE integrated Product andProcess Engineering集成产品与工艺工程IPTV Incident per Thousand Vehicles 每千辆车的故障率IPTV Incidents Per Thousand Vehicles 每一千台车事故率IPTV Incidents Per Thousand Vehicles 每千辆车的故障率IPTV Incidents Per Thousand Vehicles 千辆车故障率IR Incident Report 事故报告IRP Issue Resolution Process 问题解决流程IRR Internal Rate of Return 内含报酬率ISO International Standard Organization 国际标准化组织IV Integration Vehicle 集成车IV MRD Integration Vehicle Material RequiredDate集成车的物料需求日期IVBR Integration Vehicle Build ReadinessReview集成车制造准备评审IVER Integration Vehicle Engineering Release 集成车工程发布JIS Just In Sequence 排序供货JIS Just In Sort 供应商排序供货方式JIS Job Instruction Sheet 岗位指导书JIT Just In Time 及时供货JIT Just In Time 供应商及时供货方式JPH Job per Hour 生产节拍JRS Joint Ride Session 联合评审JSC 生产采购委员会JSC-GP Joint Sourcing Committee - Generalpurchase联合采购委员会-一般采购Kcc Key Control Characteristic 关键过程控制特性KCC Key Control Character 关键控制特性KCDS Key Characteristic Designation System 产品关键特性定义系统KO Kick-Off 启动Kpc Key Product Characteristic 关键产品特性KPC Key Product Characteristic 关键产品特性KPC Key product characteristic 主要产品特性KPC Key product characteristic 主要产品特性KPC Key process control 关键过程控制KPC Key process control 关键过程控制LAAMSB Latin America, Africa, Middle EastStrategy Board通用的拉美,非洲,中东战LCL Lower Control Limit 管制下限LCS Logistic Confirmation Sheet 物流确认单LL Learning Loop 学习周期LL Long Lead 长周期LLPR Long Lead Production Release 长周期的产品发布LM Launch Manager 启动经理LOU Line of Usage BOM 整车BOM行LSL Lower Specification Limit 规格下限LSP Lean sales and marketing prograne 精宜营销LTR Launch Team Release 启动小组释放LWO Logistic Work Order 物流属性更改号M+E Machine & Equipment 机器设备MAC 区域经理MBOM Manufacturing BOM 制造BOMMDS Materiel Data Sheet 物料数据单ME Manufacture Engineer 样车试制工程师或生产线制ME Machine and Electronic 电器设备ME Manufacturing Engineering 制造工程ME Manufacturing Engineering 制造工程MEC 区域市场支持MEIS Manufacturing Engineering Info System 制造工程信息系统MES Manufacturing Execution System 制造执行系统MES Manufacturing Execution System 制造执行系统MFG Site Dec Manufacturing Site Decision 确定生产厂址MIC Marketing Information Center 市场信息中心MILKRUN Milkrun 循环取货MKT Marketing 营销MMR Manufacturable Math Release 制造数模发布MO Manufacturing Operations 生产管理部门MP OTS 100% 100% Made Parts in OTS 100%自制件达到OTS状态MP OTS 100%100% Made Parts in OTS 100%自制件达到OTS状态MP PPAP Made Parts PPAP 自制件通过PPAPMP PPAP Made Parts PPAP 自制件通过PPAPMP PPV Made Parts Production and ProcessValidation自制件生产线交付后的产品MP PPV Made Parts Production and ProcessValidation自制件生产线交付后的产品MPS Master Planning System 主计划系统MPV Multi-Purpose Vehicle 多用途轿车MR Manufacturing Requirements 制造要求MRD Material Required Date 交样日期MRD Material Requirement Date 物料需求日期MRD Material Required Date (for physicalbuilds)物料需求日期(用于制造样MRD Math Required Date (for virtual builds) 数模需求日期(用于虚拟制MRE Manufacturing Responsible Engineer 制造工程师MS Manufacturing Studies 制造车间MSA Measurement System Analysis 测量系统分析手册MSA Measurement System Analysis 测量系统分析MSA Measure System Analyse 测量系统分析MSA Measurement system analysis 测量系统分析MSS Market Segment Specification 市场细分规范MSS 区域销售支持MSS Market Segment Specification 市场分割规范MT Manual Transmission 手动变速箱MT&E Machines, Tools and Equipment 机床,工装和设备MTS Manufacturing Technical Specification 制造技术标准MVB Manufacturing Validation Build 用于认证制造工艺的整车制MVB Manufacturing Validation Build 制造验证造车MVB (ns) Manufacturing Validation Build (nonsaleable)用于认证制造工艺的整车销售的)MVB (s) Manufacturing ValidationBuild (saleable)用于认证制造工艺的整车售的)MVBns Manufacturing Validation Build Non-Salable非销售制造验证造车MVBs Manufacturing Validation Build Salable 销售制造验证造车MVSS Motor Vehicle Safety Standards 汽车安全标准MWO Manufacture Work Order 制造属性更改号MY Model Year年度款 MYM Model Year Manager车型年经理 NAO North American Operations 通用的北美分部 NEO New Employee Orientation 新员工培训 NOA Notice of Authorization 授权书 NOD Notice of Decision 决议 NOD Notice of Decision 决议通知 NPV Net Present Value 净现值 NRD Normal Road一般公路NSB North American Strategy Board通用的北美传略委员会(管理组织)OBD On Board Diagnostics 车载诊断系统 OEMOriginal Equipment manufacturers 原始设备制造商(主机厂)OEM Run-Off Original Equipment Manufacturer Run-Off零件供应商工装设备具备试生产条件OEM Run-off Original Equipment Manufacturer Run-off 零件供应商工装设备具备试OJT On Job Training 在岗培训 OPO Office of Product Operations 产品高层管理组织 ORS Occupant Restraint System 乘员约束系统 OT Overtime 加班 OTD Order to Delivery 订单到货时间 OTP On Time Performance 及时性能 OTS 装车评审 OTS Off-tool Sample 工装样件 OTS Off-tool Sample 工装样件 OTS Off-tool Sample 工装样件 OTS OFF-TOOL-SAMPLE 工装样件OTS QV OTS Quality ValveOTS 质量阀OTS 交付状态满足质保的开OTS QV OTS Quality ValveOTS 质量阀,OTS 交付状态开阀要求OTS TG2 Off Tooling Samples Tooling Go Level 2OTS 设计达到TG2阶段,发供应商启动工装和设备投入OTS TGL2 Off Tooling Samples Tooling Go Level 2 OTS 设计达到TG2阶段 P Pilot 批量试生产 P Pilot 小批量生产 PA Production Approval 批准正式生产 PA Program Administrator 项目管理专员 PaC Physical Alpha for Customer 提交客户的Alpha 样机 PACK Packaging 包装规划 PAD Product Assembly Documentation 产品装配文件 PAM Product Assemble Manual 样车装配指南 PAM Product Assemble Manual 产品装配手册PAPIRProduct and Process Integration Review 产品和工艺集成会议PAS Packaging Approval Sheet 包装确认单PAS Parking Aid System 泊车辅助系统PAS Parking Aid System 泊车辅助系统PbC Physical Beta for Customer 提交客户的Beta样机PBS Painted Body Store 油漆车身存储区PC Deliver Pilot to Customer 向客户提交Pilot产品PC Pullcord 拉环PC Problem Communication 问题信息PC&L Production Control and Logistics PC&L部门(GM的一个部门PCL Production Control Manager 生产控制与支持PCM Powertrain Control Module 动力总成控制模块PCM Process Control Manager 工艺控制负责人PCN Project Cost Change Notice 项目更改通知单PCN Project Costbook Change Notice 项目Costbook更改通知单PCR Problem communication report 问题交流报告PCR Problem communication report 问题交流报告PCR Problem Communication Report 问题交流报告PCR Problem Communication Report 问题交流报告PDC Parking Distance Control 泊车距离控制PDC Parking Distance Control 泊车距离控制PDCA Plan、Do、Check、Action 计划、实施、检查、行动PDCA Plan-Do-Check-Action 计划,实施,检查,行动PDI Product delivery inspection 产品交付检查PDI Preliminary Data Indicator 初步数据指示器PDI Pre-delivery Inspection 车辆行运“零公里”检查报PDS Product Data Structure 产品数据结构,在SCM中用象,集成了BOM、工艺和工PDT Product Development Team 产品开发组PDT Product Development Team 产品开发小组PDT Product Development Team 产品开发小组PDT Product Development Team 产品开发小组PDT Product Development Team 产品开发小组PE Product Engineering 产品工程PET Program Executive Team 项目执行小组PET Program Execution Team 项目组PET Program Execution Team 项目执行小组PFI Program Framing Initiated 项目框架启动PFMEA Process failure modeand effectsanalysis过程失效模式和后果分析PFMEA Process FMEA 工艺失效模式分析PFMEA Process failure mode & effects analysis 过程失效模式分析PFSE Product Focus Systems Engineer 产品系统工程师PG3 Powertrain Gateway 关键里程碑节点PgC Physical Gamma for Customer 向客户发运Gamma样机PGM Program Management / Project Management 项目管理PGM Program Management 项目管理PGM Program Management 项目管理Pilot Pilot 试生产Pilot Pilot 试生产Pilot QV Pilot Quality Valve 试生产质量阀满足启动试要球Pilot MRD Pilot Material Requied Date Pilot交样日期Pilot MRD Pilot Material Required Date Pilot的物料需求日期Pilot QV Pilot Quality Valve 试生产质量阀满足启动试生产的开阀要求PIM Powertrain Interface Manager 动力总成接口经理PLM Production Launch Manager 生产启动经理PLP 单车利润表PM Programme Manager 项目工程经理PM Program Manager 项目经理PM Program Manager 项目经理PM Plan maintain 计划维护PM Prevention Maintenance 预防性维护PM Program Manager 项目经理PMO Program Management Office 项目管理办公室(通用的一PMP 常规尺寸PMT Product Management Team 产品管理小组PN Part NO. 零件号PP Pre-pilot 前期试生产PP Pre-Pilot 预试生产PP Pre-pilot 试生产P-P Pre-Pilot 试生产PP PPAP Purchased Parts ProductionParts Approval Process外购件完成生产件批准程序PP Appr. Purchased Parts Approved 外购件批准SQE开具入库许可单PP ESO Purchased Parts Engineering Sign Off 外购件工程签署,完成OT 认可PP OTS 100%100% Purchased Parts in OTS 外购件的OTS交样率达到PP OTS 80% 80% Purchased Parts in OTS 外购件的OTS交样率达到PP OTS 80%80% Purchased Parts in OTS 外购件的OTS交样率达到PP PPAP Purchased Parts PPAP 外购件完成PPAPPPA Product Planning Approval 产品规划批准PPAP Production Parts Approval Process 生产件批准程序PPAP Production Part Approval Process 生产零部件批准程序PPAP Production Part Approval Process 生产件批准程序PPAP Production Part Approval Process 生产件批准程序PPAP Production Parts Approval Process 生产件批准程序PPAP Production Part Approval Process 生产件批准流程PPAP PPAP Production Part Approval Process 产品零部件批准流程PPAP Production Part Approval Process 生产零部件批准程序PPC Deliver Pre-Pilot to Customer 向客户发运Pre-pilot动力PPC Product Program Content 项目任务书。
机械常用英文缩写

Glossary of Terms术语Glossary of Terms术语AAR: Appearance Approval Report 外观批准报告A/D/V: Analysis/Development/Validation 分析/开发/验证A/D/V–DV: ADV Design Validation ADV设计验证A/D/V P&R: Analysis/Development/Validation Plan and Report. This form is used to summarize the plan and results for validation testing. Additional information can be found in the GP-11 procedure.分析/开发/验证计划和报告A/D/V–PV: ADV Product Validation ADV产品验证AIAG: Automotive Industries Action Group, an organization formed by General Motors, Ford andDaimler-Chrysler to develop common standards and expectations for automotive suppliers. 汽车工业行动集团AP: Advance Purchasing 先期采购APQP: Advanced Product Quality Planning 产品质量先期策划APQP Project Plan: A one-page summary of the SGM APQP process that describes the tasks and the timeframe in which they occur. APQP项目策划AQC:Attribute Quality Characteristic 属性质量特性ASQE: Advanced Supplier Quality Engineer 先期供应商质量工程师BIW: Body in White. Usually the bare metal shell of the body including doors and deck lid prior to paint and trim. 白车身BOM: Bill of Materials 材料清单BOP:Bill of Process 过程清单Brownfield Site: An expansion of an existing facility. 扩建场地CMM: Coordinate Measuring Machine 三坐标测试仪Cpk: Capability Index for a stabile process 过程能力指数CTC: Component Timing Chart (DRE document) 零部件时间表(DRE文件)CTS: Component Technical Specifications 零部件技术规范CVER: Concept Vehicle Engineering Release 概念车工程发布DC: Design Complete 设计完成Defect outflow detection: A phrase used in the Supplier Quality Statement of Requirements that refers to in-process or subsequent inspection used to detect defects in parts. 缺陷检测DFM/DFA: Design for Manufacturability / Design for Assembly 可制造性/可装配性设计DFMEA: Design Failure Modes and Effects Analysis. It is used to identify the potential failure modes of a part, associated with the design, and establish a priority system for design improvements. 设计失效模式和后果分析DPV: Defects per vehicle 每辆车缺陷数DR: Documentation Required DR特性DRE: Design Release Engineer 设计释放工程师DV: Design Validation 设计验证E&APSP: Engineering & Advance Purchasing Sourcing Process. 工程&先期采购定点程序EP: E-Procurement 电子采购流程Error Occurrence Prevention: A phrase used in the Supplier Quality Statement of Requirements that refers to poke yoke or error-proofing devices used to prevent errors in the manufacturing process from occurring. 防错FTQ: First Time Quality 一次通过质量GA: General Assembly 总装GD&T: Geometric Dimensioning & Tolerancing 几何尺寸与公差SGM: Shanghai General Motors 上海通用汽车GMAP: General Motors Asian Pacific 通用汽车亚太GME: General Motors Europe 通用汽车欧洲GMNA: General Motors North American 通用汽车北美GP: General Procedure 通用程序GPDS: Global Product Description System 全球产品描述系统GPS: Global Purchasing System 全球采购系统GPSC: Global Purchasing & Supplier Chain 全球采购及供应链GR&R: Gage Repeatability and Reproducibility 检具重复性及再现性Greenfield Site: A new supplier facility that is built to support a program.GVDP: Global Vehicle Development Process 全球整车开发流程IPTV: Incidents per Thousand Vehicles 每千辆车故障IVER: Integration Vehicle Engineering Release 集成车工程发布KCC: Key Control Characteristics. It is a process characteristic where variation can affect the final part and/or the performance of the part. 关键控制特性KCDS: Key Characteristic Designation System 关键特性指示系统Kick-Off Meeting: The first APQP supplier program review. 启动会议(第一次APQP供应商项目评审)KPC: Key Product Characteristic. It is a product characteristic for which reasonably anticipated variation could significantly affect safety, compliance to governmental regulations, or customer satisfaction. 关键产品特性LAAM: (General Motors) Latin American, Africa & Meddle East (通用汽车)拉丁美洲、非洲及中东LCR: Lean Capacity Rate. It is the GM daily capacity requirement. 正常生产能力MCR: Maximum Capacity Rate. It is the GM maximum capacity requirement. 最大生产能力MOP: Make or Purchase 制造/采购MPC: Material Production Control 物料生产控制MPCE: Material Production Control Europe 欧洲物料生产控制MRD: Material Required Date; date material must be delivered in order to allow a build event to begin. 物料需求日期MSA: Measurement Systems Analysis 测量系统分析MVBns: Manufacturing Validation Build non-saleable 非销售车制造验证MVBs: Manufacturing Validation Build saleable 销售车制造验证NBH: New Business Hold 停止新业务N.O.D.: Notice of Decision 决议通知OEM: Original Equipment Manufacturer 主机客户PAD: Production Assembly Documents 生产装配文件PC&L: Production Control & Logistics 生产控制&物流PDT: Product Development Team 产品开发小组PFMEA: Process Failure Modes and Effects Analysis. It is used to identify potential failure modes associated with the manufacturing and assembly process. 过程失效模式和后果分析PPAP: Production Part Approval Process 生产件批准程序Ppk: Performance index for a stable process 过程能力指数PPM: 1) Program Purchasing Manager, 2) Parts per Million (rejects and returns to suppliers) 1)项目经理2)每百万件的产品缺陷数PPV: Product & Process Validation 产品及过程验证PQC: Product Quality Characteristic 产品质量特性PR/R: Problem Reporting & Resolution 问题报告及解决PSA: Potential Supplier Assessment, a subset of the Quality System Assessment (QSA) 潜在供应商评审PV: Product Validation 产品验证QSA: Quality System Assessment 质量体系评审QSB: Quality Systems Basics 质量体系基础QTC: Quoted Tool Capacity 工装报价能力RASIC: Responsible, Approve, Support, Inform, Consult 负责、批准、支持、通知、讨论R@R: Run at Rate 按节拍生产RFQ: Request For Quotation 报价要求RPN: Risk Priority Number related to FMEA development 风险顺序数RPN Reduction Plan: An action plan that describes what is being done to reduce the risk priority number for items listed in the DFMEA or PFMEA.降低RPN值计划SDE: Supplier Development Engineer 供应商开发工程师SFMEA: System Failure Mode and Effects Analysis 系统失效模式分析SMT: System Management Team 系统管理小组SOA: Start of Acceleration 加速开始SORP: Start of Regular Production 正式生产SOR: Statement of Requirements 要求声明SPC: Statistical Process Control 统计过程控制SPO: (General Motors) Service and Parts Operations (通用汽车)零件与服务分部SQ: Supplier Quality 供应商质量SQE: Supplier Quality Engineer 供应商质量工程师SQIP: Supplier Quality Improvement Process 供应商质量改进过程SSF: Start of System Fill 系统填充开始SSTS: Sub-system Technical Specifications 子系统技术规范Sub-Assembly/ Sub-System: An assembly of sub-components delivered to the SGM main production line for installation to the vehicle as a single unit.Subcontractor: The supplier of a sub-component to a Complex System/Subassembly supplier (Tier 2, 3, etc). 分供方SVE: Sub-System Validation Engineer 子系统验证工程师SVER: Structure Vehicle Engineering Release. 结构车工程发布Team Feasibility Commitment: An AIAG APQP form that is provided with the Request for Quotation. It is the suppli er’s concerns with the feasibility of manufacturing the part as specified.小组可行性承诺TKO: Tooling Kick-Off 模具启动会议UG: Unigraphics UG工程绘图造型系统VLE: Vehicle Line Executive 车辆平台负责人VTC: Validation Testing Complete 验证试验完成WO: Engineering Work Order 工程工作指令。
通用术语

AHE:外观颜色匹配工程师 APQP:产品质量先期策划 DRE:设计发布工程师 DTS:尺寸技术准备 ETR:工程试装要求 EWO:工程更改 FE:功能评估GCA:全球顾客评审GD&T:主要尺寸相关的零件、总成和整车的形位公差图纸,几何尺寸及公差图纸。
GM Global AAR---GM全球外观认可报告 GP4:生产件批准状况通知GP5:供应商质量监控流程(GM1746) GP8:持续改进程序(GM1747) GP9:按节拍生产品(GM1960)GP10:供应商检测设备的评价和鉴定(GM1796) GP12:早期生产遏制(GM1920)IMDS:国际材料数据系统 MC:匹配-MC0/1交样前,检具不能按时完成时,经过MC工程师批准,允许用三坐标进行代替测量。
但测量时使用的基准必须与GD&T/Control Drawing一致,并得到SGM检具工程师的设计认可(A表),且基准的精度和重复性必须得到验证,符合要求。
-MC2检具必须经SGM检具工程师设计认可(A表)和制造认可(B表)。
交样数量原则上MC0,MC1,MC2各5套 PATAC:泛亚汽车技术中心 PCR:问题交流报告 PDT:产品开发小组 PLP:主定位基准Pre-texture Instruction-Global Form ---GM全球皮纹认可报告PTR:供应商提供的零件必须是合格的,可用于正常的可销售车生产的零件。
(所有新零件在作为正常零件供给SGM之前,均必须已成功地通过PTR的实施) S1:第一轮可销售车制造 SMT:系统管理小组 SVE:系统认证工程师 SQE:供应商质量工程师 S GE:外观皮纹工程师TA:Technology assent:技术赞成(定点前的技术,能力方面的交流) TE:试验工程师TVE:(动力总成)总认证工程师 VPM:整车性能经理IV:工程认可(需要提供零件尺寸报告、材料试验报告、总成性能报告等所有试验报告) MC1/2:尺寸匹配(提交尺寸报告,合格率80%/90%)PVV:产品验证,小批量制造(尺寸报告,零件必须通过GP12) NS:非销售车制造(零件必须通过GP12-100%检验)S:销售车制造(零件通过PPAP人认可,零件必须通过GP12-100%检验) SORP:量产开始(具体数量根据订单,一般IV80套,MC10套,PVV几套到几十套不等。
DesignForManufacturingAndAssembly

Ken Youssefi
UC Berkeley
9
DFM and DFA Design Guidelines
• Distinguish different parts that are shaped similarly by non-geometric means, such as color coding.
Ken Youssefi UC Berkeley 3
DFM and DFA Design Guidelines
• Minimize part count by incorporating multiple functions into single parts. Several parts could be fabricated by using different manufacturing processes (sheet metal forming, injection molding). Ask yourself if a part function can be performed by a neighboring part.
Minimizing the Number of Parts
• Must the parts move relative to each other? • Must the parts be electrically or thermally insulated? • Must the parts be made of different material? • Does combing the parts interfere with assembly of other parts? • Will servicing be adversely affected?
- 1、下载文档前请自行甄别文档内容的完整性,平台不提供额外的编辑、内容补充、找答案等附加服务。
- 2、"仅部分预览"的文档,不可在线预览部分如存在完整性等问题,可反馈申请退款(可完整预览的文档不适用该条件!)。
- 3、如文档侵犯您的权益,请联系客服反馈,我们会尽快为您处理(人工客服工作时间:9:00-18:30)。
DFA
•本课的目的
– 将DFA放入文章中
– 学习装配设计的基本规则
– 理解背景和历史
– 理解它的优缺点
依照Ford和GM的多元化
或:为什么DFM/DFA重要
•对于每个产品部分,大约有1000制造装备零件
•或者,对于每一个关于产品部分的公差尺寸或性质,关于制造装备大约有1000的公差尺寸或性质。
•像“装备”包括固定设备、运输机、冲模、夹具、自动设备、机床元件等
*注释:Ford的评估是1000,GM的是1800。
两者都是不正式的评估。
一些引言
•仅仅因为你能制造一些东西不意味着你能制造它
•制造便宜的[低成本]原料—你会被自己的错误葬送
•我不了解为什么它不能装配。
它已经通过检查
•传下来这样一句话我们不能用螺丝钉。
所以我们用按扣装配。
然后有传下来这样一句话通过下降测试很难。
所以我们放弃了它并且它崩溃了…
DFM/DFA的目标
•在历史上,按着惯例
– 降低成本,简化工艺
– 在设计过程中提高对制造问题的了解
•更宽广(本课的目标)
– 为了一个大的目标对制作和装配方法排序
•自动化、系统化、提高质量、柔性化的能力
•有权使用驱动装配的商业方法像定时交货
•创新设计、外购(Siemens进口簇)
•不可避免的推动DFM/DFA更早的进入产品生产工艺中,在这里它混合了结构。
(参考AITL基本问题和产品结构课程)
完成外购部件
来自天堂的装配*
•能够被一个戴拳击手套的盲人用一个手装配
•是稳定的并且可以自动校准
•公差是自由的并且宽大
•几乎没有夹具
•几乎没有工具和固定设备
•零件出现在合适的方位上
•对于自由进给零件不对称
•零件容易加紧和插入
*Peter Will博士,ISI
来自地狱的装配
•与前面幻灯片所显示的每种情况都相反
DFA的历史
•在群组技术中有着深远的背景
– 分类计划
•欧洲设计传统
•工程经济学
– 每个零件必须调整合适
•Boothroyd
- 零件进给物理学 – 1960s
- 零件处理和插入实验 – 1970s
- 主张装配成本=制造成本的30-50%
- DFA方法学和软件 – 1970s-80s
- 转换到主张零件是主要的成本并且更少的零件=更少的成本,即使那些零件更加复杂
样品成本细目分类
•VCR:90%零件,5%劳动力
•汽车发动机:75%零件,7%劳动力,7%资产,7%消费品
•袖珍电脑:65%零件,25%劳动力
•战斗机:50%零件和工具,40%劳动力
•上面的大部分恰是粗略估计,因为对于大部分零件,公司不能确切的知道他们的成本
*数据来自27个发动机生产线,国际机动车辆计划
传统DFA的特性
•采用简单的来理解驱动节奏的方法(关于逾期费的节奏经历)
•采用相关成本和时间韵律
•小的DFA使每一个装配步骤单一化
–单一零件
–手工装配
–小零件
–采用很多自由联系的节奏来评估不同水平的进给和处理
•大的DFA强调零件计数缩减
–它实质是在产品结构方面的另一种影响
–高级的塑料使零件计数缩减更加吸引人
复杂模型零件
Poschmann AG允许。
许可使用。
DFA02.ppt 2/3/2004
家庭热水系统族零件
铸型花费$100K到$500K并且一直到一年来发展和完善Poschmann AG允许。
许可使用。
DFA02.ppt 2/3/2004
融化点技术
Poschmann AG允许。
许可使用。
DFA02.ppt 2/3/2004
零件折中计算
衰退模型对于模型成本和时间
• $成本= 22500 + .82*尺寸, cc + 30*#尺度+ 2940*#激励者 + 7630*高精度结果+ 5470* 高公差
• 时间(周) = 13 +0.000055*尺寸 +0.007*#尺度
参考A. Fagade 和D. Kazmer,“最优组成合并在塑料产品设计中,”
ASME DETC/DFM-8921, 1999
• Boothroyd的模型包括一个复杂的因素,那就是驱动成本C=(特征数)1.24
DFM战略
范围的问题
•什么时候DFA能应用?
•什么时候DFA应该应用?
•在DFA能应用之前什么信息是所需的?
•设计者的优先权是什么?
• DFA能/应该从产品设计的“其他”中被分离出来?
抽水机的重新设计•了解Redford 和 Chal ,pp 118-119
•在新旧设计之间的不同是什么?
– 从产品功能的POV
– 从装配的POV
•在这个例子中我们看到了什么?
Redford—Chal 抽水泵的重新设计
Alan Redford授权。
许可使用。
气胎活塞的重新设计
•原始功能被完全理解了吗?
•在重新设计中被禁止了吗?
*按照Boothroyd 和Dewhurst的产品装配设计,业务手册1991
B&D抽水泵重新设计
传统DFA
•问题是:(Boothroyd除了注释外)
–装配每个零件-估计和减少时间
•进给和提出
•处理/运输/进入位置(Sony开发观点)
•无损害、碰撞、摸索的插入
-减少零件计数(最初由局部经济分析驱动,现在由零件本身驱动)
•两个相同材料的相邻零件?
•装配后他们向对于每个零件移动吗?
•过后需要拆卸吗?
•零件是主要功能的传递者吗?(Fujitsu,Lucas(Pahl & Beitz))
•如果不是,考虑将他们结合(但是要了解结构等级)•有太多的紧固件吗?
-识别成本驱动(Denso)
Sony的DFA
•像Handicams应用于产品
• “我们的设计者及早的将装配纳入估计中。
”
•方法:
- 概念设计在开发见解中被勾画
- 每个概念都受制于DFA分析和刻画
- 概念选择标准包括DFA刻痕
•一个Sony的技师20分钟内制作一架拍立得照相机的完整的开发描绘图。
Denso的DFA
怎样实行DFA
•制作材料的结构清单
•鉴别每一个零件配合并了解它
•选择一个合理的装配序列
•利用表格来估计操作和配合的时间
•理论上将必要的零件标记,包括所有的紧固装置•计算3*#理论上必须的零件
装配效率=
预知整体装配时间
•这个变动范围从组装机的5%到好的设计的30%
处理时间
零件只需要一个手
零件需要两只手
(Boothroyd Dewhurst授权, Inc. © 1999.) 许可使用.
插入时间
零件插入但是没有立刻被保护没,或合适的扣住来保护
一些概念上的问题
•什么是“基础零件”?
-记住交流发电机 – 在唯一的装配序列家族中螺母是基础,这一族可以不用重新定位来达
装配。
- “产品结构”的不同类型存在(拱形类)
• “不同”的意义是什么?
- 对于手工装配,Boothroyd有一些以时间为基础的数据(最初起源于研究生)
•为什么避免螺孔?
-25年前的经验可能不在应用
-看Blonder视频
人工对自动装配DFA
•对于一个人什么是流畅的
-使适应装配
-采用像镊子这样的工具
•在进给轨道上零件堵塞发生的最经常
- Denso:完美的零件没有堵塞
-一个不同的平衡在总运动和纯粹的运动时间
•插入的不同方法
Hitachi装配评估方法
回收和再利用的设计
Greg Blonder视频(17分钟1:45)•在Bell Labs讲演,1900,1月16日
•已经精密分析客户产品,大约5年
•谈论一天来分析每一个
•分类~4000零件包括60螺钉(!)
•告诉它意味着什么来得到高装配领域
•试图解释它来达到一个高水平实行阶段
•讨论快门和闪光部件
•他后来成为美国朗讯科技公司的VP。