第2部分 面向装配的设计指南-DFA-钟元 PPT
面向制造和装配的设计(DFMA) PPT

41
42
43
44
45
46
47
48
49
50
51
52
53
54
55
56
57
58
59
60
61
62
63
64
65
66
使用双重功能模块和子系统
使用组件来提供结构的框架而不是使用独立的结构装配 (例如:汽车单体式结构设计)
7
8
9
10
11
12
13
14
15
16
17
18
19
20
21
22
消除 通过重新设计产品或过程使得任务和零件不再被需要来消除犯
错误的可能性
替换 替换更可靠的装配,部件或过程来防止错误,提高持久性
制造试运行 15%
40%
5
产品设计 & 面向加工/装配的设计(DFM/A)
概念/体系结构设计
装配设计
部件、材料以及过 程选择
部件设计 过程、工具和装置
设计和选择
对简化的体系结构和接口的 创意(减少互相连接)
部件合并的创意对装配的灵活性 和固定部件和防误措施的设计
对更经济的部件材料以及过程 的标准化和创意
消除 通过重新设计产品或过程使得任务和零件不再被需要来消除犯
错误的可能性
简化 使用产品,过程设计技术和机制使得更轻松的正确实现工作
探查 使用方法来在进一步工作进行之前检测错误,使用户能够迅速
纠正问题
减轻 试图将错误的影响最小化
23
24
25
26
27
28
29
30
31
32
面向装配的设计概述

Page
5
过程
设计中的制造商和供应商协作 参考面向装配的设计(DFA)指导方针
初步的生产规划和定义
面向装配的设计评估(手工或基于软件的) 成本估计
公差分析
工程建造方面的反馈 测量面向装配的设计的衡量参数 升级生产和供应链规划 在设计回顾中确定可制造性
Page 6
减轻 试图将错误的影响最小化
Page
9
防误措施过程
确定装配次序 对于每个装配步骤,要么执行正式的FMEA过程, 要么口头不正式的询问可能会发生什么样的错误 判断哪些错误是最容易出现或者将对优先考虑的 行动产生最大影响的 确保防误措施的时机和步骤 首先着眼于预防 然后才是检测
Page
CSC TeamSet面向制造的设计(DFM)
Valor-电子产品的面向制造的设计(DFM)
Savantage-电子产品的面向制造的设计(DFM) Moldflow喷射模塑法
生产过程定案 从供应商处获得对初期产品的反馈
通过建造报告获得反馈
合作来精炼设计的可制造性 升级产品估算
升级面向装配的设计衡量参数
产品准备就绪回顾时再次确定可制造性 解决关键的可生产问题 进行产品回顾,确保关键的可生产问题已经解决,得到的 教训已经捕获
Page
7
防错装配(Mistake
Page
15
proofing assembly
ቤተ መጻሕፍቲ ባይዱ
)
防误措施是面向装配的 设计(DFA)的一个必不 可少的组成部分 1.产品中的控制或特性, 以及预防错误、促进正确 生产的过程 2.产品中的简单的,花费 不多的控制和特性以及在 每步操作时发现(然后就 改)错误的过程.
第1部分:面向制造和装配的产品设计钟元
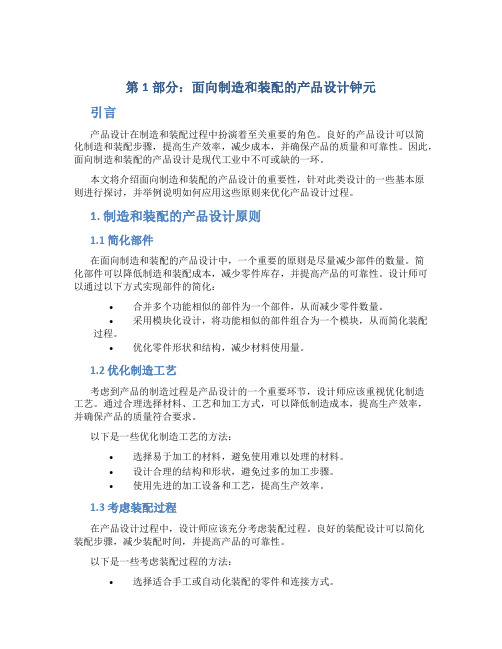
第1部分:面向制造和装配的产品设计钟元引言产品设计在制造和装配过程中扮演着至关重要的角色。
良好的产品设计可以简化制造和装配步骤,提高生产效率,减少成本,并确保产品的质量和可靠性。
因此,面向制造和装配的产品设计是现代工业中不可或缺的一环。
本文将介绍面向制造和装配的产品设计的重要性,针对此类设计的一些基本原则进行探讨,并举例说明如何应用这些原则来优化产品设计过程。
1. 制造和装配的产品设计原则1.1 简化部件在面向制造和装配的产品设计中,一个重要的原则是尽量减少部件的数量。
简化部件可以降低制造和装配成本,减少零件库存,并提高产品的可靠性。
设计师可以通过以下方式实现部件的简化:•合并多个功能相似的部件为一个部件,从而减少零件数量。
•采用模块化设计,将功能相似的部件组合为一个模块,从而简化装配过程。
•优化零件形状和结构,减少材料使用量。
1.2 优化制造工艺考虑到产品的制造过程是产品设计的一个重要环节,设计师应该重视优化制造工艺。
通过合理选择材料、工艺和加工方式,可以降低制造成本,提高生产效率,并确保产品的质量符合要求。
以下是一些优化制造工艺的方法:•选择易于加工的材料,避免使用难以处理的材料。
•设计合理的结构和形状,避免过多的加工步骤。
•使用先进的加工设备和工艺,提高生产效率。
1.3 考虑装配过程在产品设计过程中,设计师应该充分考虑装配过程。
良好的装配设计可以简化装配步骤,减少装配时间,并提高产品的可靠性。
以下是一些考虑装配过程的方法:•选择适合手工或自动化装配的零件和连接方式。
•设计易于取下和安装的零件,便于维修和更换。
•提供清晰的装配指导,确保装配过程顺利进行。
2. 例子:汽车发动机盖设计为了更好地理解面向制造和装配的产品设计原则的应用,我们来研究一个例子:汽车发动机盖设计。
汽车发动机盖是汽车的一个重要部件,它需要在制造和装配过程中考虑各种因素。
以下是一些关于汽车发动机盖设计的原则应用:1.简化部件:设计师可以通过将多个相似的零件合并为一个单一的零件来简化发动机盖的设计。
面向装配的设计

• 墨菲定律:可能出:
对于任何一条设计指南 都不能盲目的遵守!
79
谢 谢!
七、减少调整,避免干涉
八、防错
• 不需要注意力---即使疏忽也不会发生错误; • 不需要经验和知觉---外行人也可以做; • 不需要专门知识---谁做都不会出错; • 不需要检查---第一次就把事情做好; • 减少错误、提高产品利润率; • 减少时间浪费、提高生产效率; • 减少由于检查而导致的浪费; • 消除返工及其引起的浪费; • 提高产品质量和可靠性;
五、减少零件—种类
对称零件 相似零件 合并 统一规格 合并
六、避免过约束
• 零件都通过了检查,尺寸都在公差范围之内,为什么还是装配不上?
七、减少调整,避免干涉
• 零件装配方向越少越好,装配方向过多造成在装配过程中对零件进行移动、旋转和 翻转等动作,降低零件装配效率,使得操作人员容易产生疲惫,同时零件的移动、 旋转和翻转等动作容易造成零件与操作台上的设备碰撞而发生质量问题
DF A
零件能够自我对齐到正确的位置
零件只有一个唯一正确的装配位置
零件很少,快速装配
一、零件识别
• 案例: 2018年5月,XXX电子扇XXXX,线束卡子 装错,导致顾客抱怨并进行了处罚。
?
一、零件识别
合并
夸大
二、零件抓取、放置
抓取 放置
三、自动对齐
• 导向特征能够使得零件能够自动对齐到正确的位置,从而可以减少装配过程中零件位置的 调整,减少零件互相卡住的可能性,提高装配质量和效率。
面向装配的设计
2018.6.30
什么是装配 ?
装配的详细步骤(装配工序): • 放置好基座零件 • 把零件组装在一起? • 将零件按规定的 技术要求组装起 来,并经过调试 、检验使之成为 • 识别零件 • 抓取零件 • 移动零件到装配位置
面向制造和装配的设计DFADFM

面向制造和装配的设计(Design for Manufacturing and Assembly,DFMA) 面向制造和装配的设计概述在传统的部门制及串行工程的产品开发模式中。
产品设计过程与制造加工过程脱节.使产品的可制造性、可装配性和可维护性较差,从而导致设计改动量大、产品开发周期长、产品成本高和产品质量难以保证,甚至有大量的设计无法投入生产,从而造成了人力和物力的巨大浪费。
面向制造和装配的设计(DFMA.Design for Manufacturing and Assembly)这一设计理念的提出.向传统的产品开发模式提出了挑战。
应用DFMA的设计思想和相关工具.设计师可以在设计的每一个阶段都获得有关怎样选择材料、选择工艺以及零部件的成本分析等设计信息。
它是一种全新的更加简单、更为有效的产品开发方法,为企业降低生产成本、缩短产品开发周期、提高企业效益提供了一条可行之路。
DFMA是并行工程关键技术的重要组成部分,其思想已贯穿企业开发过程的始终。
它涵盖的内容很多,涉及产品开发的各个阶段.除了上面所提到的DFMA.还包括面向成本的设计个通用的产品模型.以达到易于装配、提高装配效率和降低装配成本的目的。
在制造业日益发达的今天.在满足各种行业标准和法规的前提下,许多公司都形成了各具特色的产品开发模式。
任何一种行而有效的产品开发方法,都必须在充分考虑目前现有的产品开发和生产能力的同时进行最优化的产品设计。
对一个新产品来讲,产品的成本和开发周期是决定这个设计成败的关键因素。
国际上有一个著名的5%,但它却影响产品整个成本的70%。
还有一个著名的“28“原则:产品设计约占整个新产品开发周期的20%.但它却决定了产品总成本的80%。
可以看出仅占产品成本5%的产品设计在很大程度上决定了整个产品的成本及质量。
DFMA的主要内容DFMA设计概念的提出是为了解决由于设计与制造.装配各自独立而造成的产品成本增加和产品开发周期长等现实问题.它的核心是通过各种管理手段和计算机辅助工具帮助设计者优化设计,提高设计工作的一次成功率。
面向制造和装配设计总结——20171201更新

《面向制造和装配的设计》——钟元第一章产品设计的重要性1.1产品设计成本只占开发投入成本的5%,但是决定了75%的产品成本。
因为产品设计在很大程度上影响了产品的材料、管理、劳动力的成本。
1.2并行工程(把设计这个产品究竟是怎样的项目和定位先搞清楚)1.3开发了新产品请何师来提意见第二章面向装配的设计2.1面向装配的设计2.1.1、抓起一个零件能自动对到相应的位置,且是唯一的位置(导轨就应该设计成6*10的孔)2.1.2、快速装配,减少紧固件(散热器旁边固定件下端打1个孔就行了。
用卡扣来替代一部分螺钉)2.1.3、不需要工具或者夹具的辅助(购买那个机柜的隔板尺寸做小一点,以免装的时候干涉了。
这种一般涉及到家电的很多)2.1.4、零件尺寸超过规格依然能够装配(将1U的盖板缩进了0.5mm)2.2 设计指南2.2.1、考虑去除每个零件,这个例子还简化了工艺,原设计需要钣金折弯和车削加工及焊接(2U机箱就是最好的例子)2.2.2、相似零件合并成一个、对称的零件一样,这样还可以减少装配的防错性2.2.3、减少紧固件数量和类型A、使用同一类型的紧固件(机箱上尽量使用尽可能少类型的螺钉),第二个例子好像不太可取B、使用卡扣代替紧固件,钣金可以通过这边压紧代替紧固件数量(好像没遇到过)C、避免分散的紧固件设计(印制板螺钉固定)D、最理想的装配方式(金字塔形的装配,这样子可以靠重力)音柱的装配就不太合理E、设计零件容易被抓取,不要太小、太柔、太滑(我设计的机箱可能主要是螺钉太小了)F、避免零件相互缠绕(零件不要开口,我好像没遇到过G、减少零件装配方向,最好利用重力从上往下装配H、设计导向特征(机柜的侧门就涉及)I、先定位,后固定,减少装配调整的时间(我们的导轨就涉及),涉及到PCB 的最多J、避免运动干涉,腾出辅助工具的空间(山西的门运动干涉了,室外机柜滤波器存在这样的问题)K、设计合理的间隙L、防错设计(USB就是典型的例子、蒋小献的那些盒子大多数都不具有防错设计,不过这样却有了更多装配的可能性,能够用到更多的机子上)M、人机方面a、避免视线受阻(山西音柱就有这个问题),可以考虑增加导向规避b、手拧螺钉的地方至少保证25的距离(装那个购买的破机柜就遇到这个问题)第四章钣金设计4.1、设计指南A、避免出现尖角,都倒圆角(风罩、散热器固定块这些)B、折弯的时候要考虑工艺性(保证折弯间隙,避免干涉、保证折弯强度(短而窄的边折弯强度高,浪费的材料也少)为了避免复杂的折弯,有时候反而将一个零件拆成两个零件(室外机顶部就存在这个问题)折弯后孔位对不齐解决办法(开大孔、增加内定孔)C、增加钣金的强度(最后一个反折压平,室外机上就有使用、增加凸包、折弯处增加三角筋、增加拉钉连接)D、避免十字型的展开,以免浪费材料(2U机箱就是为避免浪费材料,背板焊接的)E、减少零件也是一种方法(室外机的顶和后背挂块都可以考虑)F、其他一些方法(翻边转角处增加圆角)止裂槽的作用:防止在拉伸区域起毛边4.2钣金装配卡扣装配:都是卡扣和螺栓一起配合使用,因为卡扣往往只起到固定一个方向成本依次升高:以后在重要的装配尺寸地方注意标注正公差和付公差。
面向装配的设计(DFA)技术研究
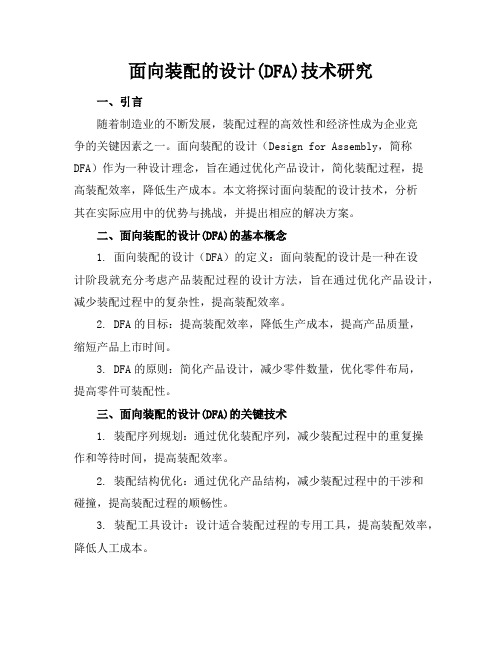
面向装配的设计(DFA)技术研究一、引言随着制造业的不断发展,装配过程的高效性和经济性成为企业竞争的关键因素之一。
面向装配的设计(Design for Assembly,简称DFA)作为一种设计理念,旨在通过优化产品设计,简化装配过程,提高装配效率,降低生产成本。
本文将探讨面向装配的设计技术,分析其在实际应用中的优势与挑战,并提出相应的解决方案。
二、面向装配的设计(DFA)的基本概念1. 面向装配的设计(DFA)的定义:面向装配的设计是一种在设计阶段就充分考虑产品装配过程的设计方法,旨在通过优化产品设计,减少装配过程中的复杂性,提高装配效率。
2. DFA的目标:提高装配效率,降低生产成本,提高产品质量,缩短产品上市时间。
3. DFA的原则:简化产品设计,减少零件数量,优化零件布局,提高零件可装配性。
三、面向装配的设计(DFA)的关键技术1. 装配序列规划:通过优化装配序列,减少装配过程中的重复操作和等待时间,提高装配效率。
2. 装配结构优化:通过优化产品结构,减少装配过程中的干涉和碰撞,提高装配过程的顺畅性。
3. 装配工具设计:设计适合装配过程的专用工具,提高装配效率,降低人工成本。
4. 装配仿真技术:利用计算机仿真技术,模拟装配过程,发现并解决潜在的问题,提高装配过程的可靠性。
四、面向装配的设计(DFA)的优势1. 提高装配效率:通过简化产品设计,减少零件数量,优化装配序列,提高装配效率。
2. 降低生产成本:通过减少装配过程中的重复操作和等待时间,降低人工成本和设备成本。
3. 提高产品质量:通过优化产品设计,减少装配过程中的干涉和碰撞,提高产品质量。
4. 缩短产品上市时间:通过提高装配效率,降低生产成本,缩短产品上市时间。
五、面向装配的设计(DFA)的挑战1. 设计复杂度:面向装配的设计需要充分考虑产品功能和装配过程,设计复杂度较高。
2. 技术要求:面向装配的设计需要一定的技术支持,如装配仿真技术、装配工具设计等。
装配设计指南(第1、2章)

对比零件原始设计图和成品图,可看出两者出现了极大偏 差,制造的零件完全不符合设计要求,这是由于设计与制造 脱节,设计时未考虑产品可制造性。 c)图是修改后正确的零件设计图。如果零件设计修改,注 射模具也要修改,大大增加了产品开发成本,产品开发周期 也加长。
三、面向制造和装配的产品开发模式
• 1.面向制造和装配的产品开发流程 • 2.面向制造和装配的产品开发优点 • 3.面向制造和装配的产品开发与并行工程
零件尺寸超过规格,依然能够顺利装配
装配过程不需要过多的调整 装配过程很容易、很轻松
零件尺寸在规格范围之内,但依然装配不上
装配过程需要反复的调整 装配过程很难、很费力
3.面向装配的设计定义
面向装配的设计(Design for Assembly, 简称DFA):是指在产品设计阶段设计产 品使得产品具有良好的可装配性,确保装 配工序简单、装配效率高、装配质量高、 装配不良率低和装配成本低
6)面向制造和设计的设计讨论 当完成面向制造和装配的设计之后,机械工程师还需要同制造、装配 部门工程师一起合作,从制造和装配的角度对产品的可制造性和可装配 性提出改善意见。 7)样品制作 样品制作是指当产品设计完成后,需要通过简单快速的加工方式制作 样品来验证产品设计是否满足上述产品各种设计要求。 样品制作方法主要有:快速成型、数控加工和三维打印。 8)产品制造 制造工艺包括:注射加工、钣金冲压加工、铸造和机械加工等。 9)产品装配 一般来说,产品会经过小批量试产来发现和解决装配中出现的问题。 10)测试 安全性和可靠性测试,以及相关认证。 11)量产
最好装配工序 零件很容易识别 零件很容易被抓起和放入装配位置 零件能够自我对齐到正确的位置 最差的装配工序 零件很难识别 零件不容易被抓起,容易掉到某些位置 零件需要操作人员不断地调整才能对齐 1.在固定之前零件能够放到两个或者两个以 在固定之前,零件只有唯一正确的装配位 上的位置 置 2.很难判断哪一个装配位置是对的 3.零件在错误的位置可以被固定 螺钉、螺柱、螺母牙型、长度、头型多种多 快速装配,紧固件很少 样,令人眼花缭乱 不需要工具或者夹具的辅助 需要工具或者夹具的辅助
面向装配的设计
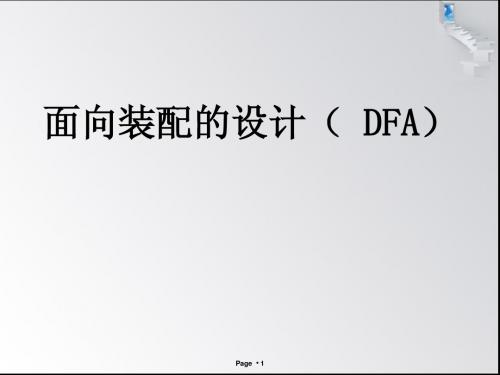
减轻 试图将错误的影响最小化
CSC TeamSet面向制造的设计(DFM)
Valor-电子产品的面向制造的设计(DFM)
Savantage-电子产品的面向制造的设计(DFM) Moldflow喷射模塑法
Page 2
目的
简化产品装配工序 缩短产品装配时间
减少产品装配错误
减少产品设计修改 降低产品装配成本
提高产品装配质量
提高产品装配效率 降低产品装配不良率 提高现有设备使用率
Page 3
设计对成本的影响
Page 4
历史
20世纪60和70年代,人们根据实际设计经验和装配操 作实践,提出了一系列有利于装配的设计建议,以帮助设 计人员设计出容易装配的产品,这些设计建议并辅以真实 的案例告诉人们如何从产品设计着手来改善产品的装配。 1977年,Geoff Boothroyd教授第一次提出了面向装 配的设计(Design for Assembly, DFA)这一概念,并被 广泛接受。面向装配的设计旨在提高零件的可装配性以减 少装配时间、降低装配成本和提高装配质量。1982年, Boothroyd教授在《自动化装配》一书中,提出了一套评 估零件可装配性的体系,并以此为基础,开发出面向装配 的设计软件。
面向装配的设计( DFA)
Page 1
定义
面向装配的设计(Design for assembly, DFA)是指 在产品设计阶段设计产品使得产品具有良好的可 装配性,确保装配工序简单、装配效率高、装配 质量高、装配不良率低和装配成本低。面向装配 的设计通过一系列有利于装配的设计指南例如简 化产品设计、减少零件数量等,并同装配工程师 一起合作,简化产品结构,使其便于装配,为提 高产品质量、缩短产品开发周期和降低产品成本 奠定基础。
面向装配的设计dfa案例

面向装配的设计dfa案例
面向装配的设计DFA(Deterministic Finite Automaton)案例是指根据装配过程中的需求和约束,设计出一个能够自动识别组装过程中正确和错误操作的有限状态机。
以下是一个面向装配的DFA案例:
假设有一个装配产品的过程,其中需要按照以下步骤进行操作:
1. 将零件A放入装配台,然后连接零件B。
2. 连接好的零件AB放入装配台,然后连接零件C。
3. 连接好的零件ABC放入装配台,然后连接零件D。
4. 连接好的零件ABCD放入装配台,并完成组装。
根据以上需求,我们可以设计一个DFA来检测装配过程中的错误操作。
状态机可以包括以下几个状态:
- 初始状态:未开始组装。
- 状态A:已放入零件A。
- 状态AB:已连接零件A和B。
- 状态ABC:已连接零件A、B和C。
- 状态ABCD:已连接零件A、B、C和D。
- 终止状态:组装完成。
根据以上状态,我们可以定义状态转移条件:
- 从初始状态到状态A需要满足条件:放入零件A。
- 从状态A到状态AB需要满足条件:连接零件B。
- 从状态AB到状态ABC需要满足条件:连接零件C。
- 从状态ABC到状态ABCD需要满足条件:连接零件D。
- 从状态ABCD到终止状态需要满足条件:完成组装。
通过以上定义的状态和状态转移条件,我们可以设计一个DFA,用于判断装配过程中的正确和错误操作。
当DFA检测到错误操作时,它可以发出警告或停止组装过程,以避免产生不合格的产品。
面向制造与装配设计的原理与应用PPT培训课件

装配设计原理
装配流程设计
根据产品结构和装配需求, 制定合理的装配流程,确 保产品装配的顺利进行。
装配工艺规划
为满足装配工艺需求,规 划合理的装配工艺,提高 装配效率和产品质量。
装配检测与验证
在装配过程中进行检测与 验证,确保装配结果的准 确性和可靠性。
制造与装配的关联性
工艺流程的衔接
制造与装配在工艺流程上相互衔接, 制造为装配提供基础,装配是制造的 延续。
02
面向制造与装配设计的基本 原理
制造设计原理
01
02
03
工艺流程设计
根据产品需求和制造条件, 制定合理的工艺流程,确 保产品制造的可行性。
工艺装备设计
为满足制造工艺需求,设 计相应的工艺装备,提高 生产效率和产品质量。
制造资源规划
合理规划制造资源,包括 原材料、设备、人员等, 确保生产过程的协调和高 效。
供应链管理
未来制造与装配设计将更加注重供应链管理,实 现供应链的优化和协同,提高生产效率和响应速 度。
人力资源管理
未来制造与装配设计将更加注重人力资源管理, 提高员工的技能和素质,培养高素质、高效率的 团队。
环境友好型设计
绿色材料
01
未来制造与装配设计将更加注重采用绿色、环保的材料,降低
对环境的污染和破坏。
废弃物处理
生产过程中产生的废弃物如何妥善处理,降低对环境的污染,是另 一个重要的环境影响挑战。
绿色制造
如何在产品设计、生产和包装等环节贯彻绿色理念,实现绿色制造, 是当前制造业面临的重大挑战。
05
未来展望
技术发展趋势
智能化技术
随着人工智能、机器学习等技术的不断发展,未来制造与装配设计 将更加智能化,实现自动化、自主化的生产模式。
面向制造和装配的产品设计钟元课件

材料选择与优化
材料性能评估
根据产品设计需求,评估不同材料的性能特 点。
环保与可持续性
优先选择环保、可回收和可持续性的材料。
成本效益分析
在满足产品设计需求的前提下,选择成本效 益最优的材料。
材料替代与优化
基于新材料或技术,提出对现有材料的替代 或优化建议。
03
面向装配的设计
装配流程分析
装配流程识别
总结词
高效性、可维护性、耐用性
详细描述
工业设备产品设计注重高效性、可维护性和 耐用性。为了提高设备的生产效率,设计时 充分考虑能源效率和加工性能。同时,工业 设备设计考虑易于维护和保养,降低维修成 本。为了确保设备的长期稳定运行,采用高 品质的材料和严格的生产工艺,提高产品的 耐用性。
装配序列优化
通过调整装配顺序,减少装配难度和成本,提高装配效率。
装配序列仿真
利用计算机仿真技术对装配序列进行模拟,预测装配过程中可能 出现的问题。
装配空间优化
01
02
03
装配空间布局
合理规划产品装配所需的 空间,确保装配操作顺利 进行。
装配空间利用
最大化利用装配空间,减 少空间浪费,提高生产效 率。
实例一:智能家居产品设计
总结词
智能、人性化、节能
详细描述
智能家居产品设计注重智能化、人性化以及节能环保。通过智能化技术,实现家居设备的远程控制和自动化操作, 提高生活便利性。同时,设计充分考虑人机交互,使产品易于使用。在节能方面,采用低功耗技术和绿色材料, 降低能耗,保护环境。
实例二:汽车零部件设计
创新性、时尚感、用户体验
VS
详细描述
消费电子产品设计注重创新性、时尚感和 用户体验。设计师不断探索新技术和新材 料,推动产品创新。同时,注重产品的外 观设计和色彩搭配,使其符合时尚潮流。 为了提升用户体验,消费电子产品设计注 重人机交互和细节处理,使产品易于使用 且满足用户需求。
- 1、下载文档前请自行甄别文档内容的完整性,平台不提供额外的编辑、内容补充、找答案等附加服务。
- 2、"仅部分预览"的文档,不可在线预览部分如存在完整性等问题,可反馈申请退款(可完整预览的文档不适用该条件!)。
- 3、如文档侵犯您的权益,请联系客服反馈,我们会尽快为您处理(人工客服工作时间:9:00-18:30)。
优化的设计
21
20
2. 简化产品设计,减少零件数量
E. DFA目的:
➢ 简化产品装配工序
➢ 缩短产品装配时间
➢ 减少产品装配错误
➢ 减少产品设计修改
➢ 降低产品成本
➢ 提高产品装配质量
➢ 提高产品装配效率
➢ 降低产品装配不良率
➢ 提高现有设备使用率
6
6
1. DFA的介绍
减少成本
DFMA
减少装配时间
减少零件数量
装配时间=金钱!
减少零件数量
提高零件的易 识别性
优化的设计
压铸件代替钣金件和五金件的组合
18
17
2. 简化产品设计,减少零件数量
DFMA
原始的设计
优化的设计
设计多功能塑胶件代替束线带或线夹
19
18
2. 简化产品设计,减少零件数量
DFMA
原始的设计 利用塑胶的弹性特性来代替弹簧
优化的设计
20
19
2. 简化产品设计,减少零件数量
DFMA
原始的设计 指甲刀的进化
零件A 零件B
零件A
零件C
DFMA
原始的设计 使用钣金件代替机械加工件
优化的设计
16
15
2. 简化产品设计,减少零件数量
不锈钢弹片 或导电布
塑胶件
压铸件
DFMA
原始的设计
优化的设计
压铸件代替塑胶件和不锈钢弹片的组合
17
16
2. 简化产品设计,减少零件数量
DFMA
定位柱 钣金件
衬套
压铸件
原始的设计
4
4
1. DFA的介绍
DFMA
C. 最好的装配工序和最差的装配工序:
最好的装配工序
最差的装配工序
1.零件很容易识别 2.零件很容易被抓起和放入装配位置 3.零件能够自我对齐到正确的位置
4.在固定之前,零件只有一个唯一正确的装 配位置
5.紧固件很少,快速装配 6.不需要工具或夹具的辅助 7.零件尺寸超过规格,依然能够顺利装配 8.装配过程不需要过多的调整 9.装配过程很容易很轻松
DFMA
13
12
2. 简化产品设计,减少零件数量
C. 把相似的零件合并成一个零件:
零件A
零件A
DFMA
零件B
原始的设计
优化的设计
14
2. 简化产品设计,减少零件数量
D.把对称的零件合并成一个零件:
零件A
零件A
DFMA
零件B
原始的设计
优化的设计
15
2. 简化产品设计,减少零件数量
E.合理选用零件制造工艺、设计多功能的零件
对装配的不正确看法:
➢ 装配就是把零件组装在一起,装配就是锁螺丝而已 ➢ 对装配不重视,轻视装配
DFMA
3
3
1. DFA的介绍
B. 一个零件装配的详细步骤(装配工序):
➢ 放置好基座零件 ➢ 识别零件 ➢ 抓取零件 ➢ 移动零件到装配位置 ➢ 零件调整到正确位置 ➢ 零件被固定 ➢ 功能测试
DFMA
7.零件尺寸在规格范围之内,但依然装不上
8.装配过程需要反复的调整
9.装配过程很难很费力 5
1. DFA的介绍
DFMA
D. DFA概念:
➢ 面向装配的设计(Design for Assembly, 简称DFA):是指在产品设 计阶段设计产品使得产品具有良好的可装配性,确保装配工序简单、装 配效率高、装配质量高、装配不良率低和装配成本低。
DFMA
第2部分:面向装配的设计指南 Design for Assembly Guidelines
DFA 钟元
2013/05/23 1
内容:
DFMA
1. DFA 介绍 2. 减少零件数量 3. 减少紧固件的数量和类型 4. 零件标准化 5. 模块化产品设计 6. 设计一个稳定的基座 7. 设计零件容易抓取 8. 避免零件互相缠绕 9. 减少零件装配方向 10.设计导向特征
11.先定位后固定
12.避免零件装配干涉
13.为辅助工具提供空间
14.为重要零部件提供止位特征
15.防止零件欠约束和过约束
16.宽松的零件公差要求
17.装配中的人机工程学
18.电缆的设计
19.防错的设计
20.重要提示
2
1. DFA的介绍
A.装配的三层含义:
➢ 零件组装在一起 ➢ 实现相应的功能 ➢ 产品质量的载体
减少装配过程 的调整
7
7
2. 简化产品设计,减少零件数量
DFMA
➢ KISS原则(Keep It Simple, Stupid):产品的设计越简单 越好,简单就是美,任何没有必要的复杂都是需要避免的。
➢ 《乔布斯传》Jonathan Ive:“只要不是绝对必须的部件, 我们都想办法去掉”,“为达成这一目标,就需要设计师, 产品开发人员,工程师以及制造团队的通力合作。我们一次 次的返回到最初,不断问自己:我们需要那个部分吗?我们 能用它来实现其它部分的功能吗?”
设计修改
模具制作
零件再次试模
详细
工
零
CAE分析
设计修改
零件报价
零件验证
模具承认
DFMA检查
样品制作
模具讨论
设计修改
零件承认料号申请图 Nhomakorabea发行工程变更
图纸更新
10
9
2. 简化产品设计,减少零件数量
DFMA
减少零件数量对产品的质量、成本和开发周期具有非常大的帮 助:
➢ 更少的零件需要进行设计 ➢ 更少的零件需要进行制造 ➢ 更少的零件需要进行测试 ➢ 更少的零件需要进行购买 ➢ 更少的零件需要进行存储 ➢ 更少的零件需要进行运输 ➢ 更少的产品质量问题出现可能性 ➢ 更少的供应商 ➢ 更少的装配工具或夹具 ➢ 更少的装配时间
11
10
2. 简化产品设计,减少零件数量
A. 考查每个零件,考虑去除每个零件的可能性:
零件A
零件B
零件A
DFMA
焊接
原始的设计
优化的设计
12
11
2. 简化产品设计,减少零件数量
B. 把相邻的零件合并成一个零件. 合并的原则:
➢ 相邻的零件没有相对运动 ➢ 相邻的零件由一种材料组成 ➢ 相邻零件的合并不会阻止其他零件的固定、拆卸和维修等 ➢ 相邻零件的合并不会造成零件制造复杂、产品整体成本增加
1.零件很难识别
2.零件不容易被抓起,容易掉到任何位置
3.零件需要操作人员不断的调整才能对齐
4a.在固定之前零件能够放到两个或者两个以上的 位置 4b.很难判断哪一个装配位置是对的 4c.零件在错误的位置可以被固定 5.螺钉、螺柱、螺母牙型多种、长度多种、头 型多种,令人眼花缭乱 6.需要工具或夹具的辅助
➢ 最完美的产品是没有零件的产品;
➢ 把产品设计得复杂,是一件简单的事情;把产品设计得简单, 是一件复杂的事情。
8
大家有疑问的,可以询问和交流
可以互相讨论下,但要小声点
9
2. 简化产品设计,减少零件数量
产品开发中一个零件的生命周期
概念设计
DFMEA分析
样品验证
模具设计
DFMA
模具修改
概念讨论
公差分析