光刻机分辨率
先进的光刻机纳米级关键核心技术测试参数数据详解

先进的光刻机纳米级关键核心技术测试参数数据详解先进的光刻机纳米级关键核心技术测试参数数据详解1. 简介光刻机是一种在集成电路制造过程中广泛使用的重要设备,用于在硅片表面上制造微细图案。
而先进的光刻机则是目前光刻技术的最新突破,具备更高的分辨率和更大的生产能力。
本文将详细解释先进的光刻机纳米级关键核心技术测试参数数据。
2. 关键核心技术参数先进的光刻机的关键核心技术参数有以下几个方面:•分辨率:分辨率是光刻机的一个重要指标,表示其在处理微细图案时所能达到的最小尺寸。
纳米级光刻机通常具备更高的分辨率,能够制造更小的图案。
•焦深度:焦深度是指在光刻过程中,光在光刻胶层中的聚焦深度。
纳米级光刻机具备更深的焦深度,使得在复杂的图案制作中能够更好地控制光的聚焦位置。
•接纳率:接纳率表示光刻机在生产过程中能够成功制造目标图案的概率。
先进的光刻机通常具备更高的接纳率,能够提高生产效率和降低生产成本。
•硅片尺寸:硅片尺寸指的是光刻机能够处理的硅片的大小范围。
纳米级光刻机通常具备更大的硅片尺寸,能够同时处理多个目标图案,提高生产效率。
•速度:光刻机的速度是指在光刻过程中每单位时间内能够处理的硅片数量。
纳米级光刻机通常具备更高的速度,能够大幅提高生产效率。
3. 数据详解以下是一些典型的先进光刻机纳米级关键核心技术测试参数数据:•分辨率:纳米级光刻机的分辨率通常能达到10纳米以下,甚至更小。
这使得它们在制造微细结构时能够获得更高的精度和更小的尺寸。
•焦深度:纳米级光刻机的焦深度通常在几百纳米至几微米之间。
这使得它们能够处理复杂的多层结构,同时在各层之间保持良好的对准和聚焦。
•接纳率:纳米级光刻机的接纳率通常能达到99%以上。
这意味着在大规模生产中,只有极少数的硅片会出现制造失败,从而提高了生产的效率和质量。
•硅片尺寸:纳米级光刻机通常能够处理300毫米直径的硅片,以适应当前集成电路制造的需求。
•速度:纳米级光刻机的速度通常在每小时几百片至几千片之间。
光刻机参数

光刻机参数1. 什么是光刻机?光刻机(Photolithography)是一种重要的微电子制造工艺,用于制造集成电路(IC)和其他微纳米器件。
它是将光敏材料(通常是光刻胶)涂覆在硅片上,并使用光刻机将图案投影到光敏材料上的过程。
通过光刻机的精确控制,可以在硅片上制造出微小而精确的结构,如晶体管、电容器和电阻器等。
2. 光刻机的工作原理光刻机主要由以下几个部分组成:•掩模(Mask):用于制造所需图案的光刻掩膜。
•光源(Light Source):产生紫外光或深紫外光。
•投影系统(Projection System):将掩模上的图案投影到光敏材料上。
•光刻胶(Photoresist):涂覆在硅片上的光敏材料。
•曝光台(Exposure Stage):用于控制硅片和掩模的相对位置。
•控制系统(Control System):用于精确控制光刻机的运行。
光刻机的工作流程如下:1.准备:将硅片清洗干净,并涂覆一层光刻胶。
2.对准:将掩模放置在光刻机上,并使用对准系统确保硅片和掩模的对准。
3.曝光:通过控制光源和投影系统,将掩模上的图案投影到光刻胶上。
4.显影:将硅片浸入显影液中,使未曝光的光刻胶被去除,形成所需图案。
5.检查:使用显微镜或其他检测设备检查硅片上的图案是否符合要求。
6.后处理:根据需要进行清洗、刻蚀或其他后处理步骤。
3. 光刻机参数光刻机的性能和参数对于制造高质量的微电子器件非常重要。
以下是一些常见的光刻机参数:3.1 分辨率(Resolution)分辨率是光刻机能够实现的最小特征尺寸。
它通常以“线宽”(Line Width)来表示,即最小线条的宽度。
分辨率越高,光刻机能够制造出更小、更精确的结构。
3.2 曝光剂量(Exposure Dose)曝光剂量是指在曝光过程中每单位面积所接受的光能量。
它对于控制光刻胶的曝光程度非常重要。
曝光剂量过高或过低都会导致图案的失真或模糊。
3.3 曝光能量均匀性(Exposure Energy Uniformity)曝光能量均匀性是指在曝光过程中光能量的分布均匀性。
光刻机专题研究

光刻机专题研究光刻机专题研究一、光刻机:芯片制造的支柱设备光刻定义:将掩膜板上的图形曝光至预涂了光刻胶的晶圆表面上。
光刻胶受到照射的部分,将发生化学变化,从而易溶于显影液。
光刻机是芯片制造的支柱设备,一般分为准直透镜系统、掩膜板对准系统、曝光系统等。
光刻机设备的核心零部件包括光源、镜头以及精密结构等。
光刻行业的关键定理——瑞利公式:CD=k1*(λ/NA)。
CD为关键尺寸,为了降低CD,有三种方式:(1)降低波长λ;(2)提高镜头的数值孔径NA;(3)降低综合因素k1。
生产参数:(1)分辨率:可达的最小光刻图形尺寸;(2)套准精度:图形尺寸在亚微米数量级上,套刻误差在特征尺寸10%;(3)产率:对给定掩膜板,每小时能曝光的晶片数量。
光刻机演变史,目前以步进式为主,EUV应用于先进制程。
光刻机在1985年之前,以g线(436nm)为主;1985年以后,出现少量i线(365nm)光刻机;1990年开始出现DUV光刻机;踏入21世纪,193nm的深紫外线开始使用。
13.5nm的EUV在近十年兴起,应用于先进制程。
光刻机从分类方式的演变,从接触式向接近式,最后演变成步进式为主。
EUV的高分辨率大幅降低重复曝光所需要的沉积、刻蚀等工艺步骤。
利用ArF的193nm光源从1990年出现,然而在进一步推进更短波长的157nm受到技术阻碍,镜片和光刻胶都需要重新研制,因此当时成本更低的浸入式193nm技术通过改良的方案成为了主流。
在水中193nm的光波长这射程134nm,通过不断提升NA的方法,并重复曝光,一直用到了7m。
直到13.5nm 波长的EUV成功商用,大幅提升了光刻机分辨率。
同样的7nm 工艺,使用EUV技术后,晶体管密度和性能都更好。
TSMC7nmEUV (N7+)工艺比7nm工艺提升20%的密度、10%的性能或降低15%的功耗。
在光刻机曝光下,光刻胶(未)被曝光的部分将溶于显影液,从而实现将图形从掩膜板转移至光刻胶,并在后续的刻蚀环节将图形进一步转移至薄膜。
光刻机参数

光刻机参数
光刻机是一种用于微电子制造的关键设备,用于在半导体芯片制造过程中将精确的图案投射到硅片上。
以下是一些常见的光刻机参数:
1.分辨率(Resolution):表示光刻机能够实现的最小尺寸。
它
通常以单位长度内可区分的图像特征数量(如每毫米的线条数)来表示,以纳米(nm)为单位,如90nm、45nm、7nm 等。
2.NA(Numerical Aperture):表示光刻机镜头系统中有效接收
和聚焦光线的能力。
它根据光刻机镜头的设计参数,通常以小数形式表示,如0.75、1.35等。
3.曝光时间(Exposure Time):表示在光刻过程中对每一个图
案区域进行曝光的时间长度。
这个时间会影响到曝光的深度和清晰度。
4.焦距(Focal Length):指光刻机镜头的焦距,即镜头所能聚
焦的距离。
5.接触方式(Contact Mode):用于光刻机的接触式曝光方式。
硅片与光刻胶(光刻层)直接接触。
6.非接触方式(Non-contact Mode):用于光刻机的非接触式曝
光方式。
硅片与光刻胶之间通过非机械接触的方式进行曝光。
7.比色系统(Alignment System):用于光刻机中对硅片上的图
案与模板图案进行对准的系统。
8.硅片舞台(Wafer Stage):用于固定和移动硅片的平台,通
过控制硅片的位置和运动来完成精确的曝光。
光刻机的参数会影响到光刻过程的精度、分辨率和速度等方面,工程师需要根据具体的制造需求和设备规格来设定和优化参数,以获得最佳的制造结果。
光刻机的种类特点

光刻机的种类特点光刻机是半导体制造中使用的一种重要设备,用于在半导体芯片上进行微细图形的投影。
光刻技术在半导体制造、平板显示、光学器件等领域具有广泛的应用。
光刻机的种类主要有紫外光刻机、电子束光刻机和离子束光刻机。
每种光刻机都有其特点和适用场景。
紫外光刻机是最常用的光刻机之一,其原理是利用紫外光源照射在掩模上的图形,通过透镜系统将图形缩小后投影到硅片上。
紫外光刻机的特点包括:1.分辨率高:紫外光刻机可以实现纳米级的分辨率,能够满足芯片制造中对微细结构的要求。
2.产能高:紫外光刻机具有较高的生产效率,能够在短时间内完成大批量芯片的生产。
3.成本低:相比其他光刻机,紫外光刻机的投资和运营成本相对较低,适合大规模生产。
4.技术成熟:紫外光刻技术经过长期的发展和应用,具有成熟的工艺和设备。
电子束光刻机是一种利用电子束投影进行微细图形制备的设备,其原理类似于紫外光刻机,但使用的是电子束作为光源。
电子束光刻机的特点包括:1.分辨率极高:电子束光刻机可以实现亚纳米级的分辨率,能够制备出极其微小的结构。
2.高精度:电子束光刻机具有高度的定位精度和对齐精度,能够实现复杂结构的制备。
3.易受污染:电子束光刻机的光学系统容易受到污染影响,需要严格的环境控制。
4.成本高:电子束光刻机的投资和运营成本较高,适合对分辨率和精度要求极高的应用领域。
离子束光刻机是一种利用离子束进行微细结构制备的设备,其原理是利用离子束从掩模上刻写出要制备的图形。
离子束光刻机的特点包括:1.适用于非常微小结构:离子束光刻机可以实现微米级以下的微细结构制备,适用于MEMS、光子学等领域。
2.高速制备:离子束光刻机具有较高的制备速度,能够在短时间内完成复杂结构的制备。
3.高能量粒子:离子束光刻机使用高能量离子束进行刻写,对材料表面产生严重伤害,需要适当的后处理技术。
4.成本较高:离子束光刻机的设备和维护成本较高,适用于对精度和分辨率要求高的特殊领域。
0.35um 光刻机技术参数

0.35um光刻机技术参数1. 介绍光刻技术在半导体制造过程中扮演着至关重要的角色,其分辨率和精度对于芯片制造的质量和性能有着直接影响。
而0.35um光刻机技术参数作为目前半导体制造中普遍应用的一种工艺,其参数对于芯片的制造至关重要。
在本文中,将深入探讨0.35um光刻机技术参数,并对其进行全面评估。
2. 分辨率在0.35um光刻机技术中,分辨率是其中一个关键的技术参数。
分辨率指的是光刻机所能实现的最小特征尺寸,通常以单位长度来表示。
在当前的半导体制造中,0.35um的分辨率已经达到了较高的水平,能够实现非常小尺寸的元件制造,这对于提高芯片集成度和性能至关重要。
3. 精度除了分辨率外,0.35um光刻机的精度也是一个非常重要的技术参数。
精度指的是光刻机在制造过程中所能达到的准确度,包括对于图形形状、尺寸和位置的准确控制。
在当前的半导体制造中,要求对于芯片元件的制造精度非常高,而0.35um光刻机的精度能够满足这一需求,不仅可以保证芯片的性能,还能提高芯片的稳定性和可靠性。
4. 曝光源曝光源是影响0.35um光刻机技术参数的另一个重要因素。
曝光源的稳定性和光照强度直接影响着光刻机的制造效果。
在当前的半导体制造中,要求对于芯片的曝光要求非常高,而0.35um光刻机所采用的曝光源能够提供稳定而强大的光照能量,保证芯片的制造质量。
5. 抗干扰能力随着半导体制造工艺的不断提高,0.35um光刻机的抗干扰能力也成为了一个重要的技术参数。
抗干扰能力指的是光刻机在制造过程中受到外部干扰时的稳定性和鲁棒性。
在实际的生产中,0.35um光刻机要面对各种复杂的工作环境和工艺条件,在这种情况下,其抗干扰能力显得尤为重要。
【总结】0.35um光刻机技术参数在当前的半导体制造中扮演着非常重要的角色。
其分辨率、精度、曝光源和抗干扰能力等参数直接影响着芯片的制造质量和性能。
而随着半导体制造工艺的不断提高,对于0.35um光刻机技术参数的要求也日益增高。
光刻机分辨率
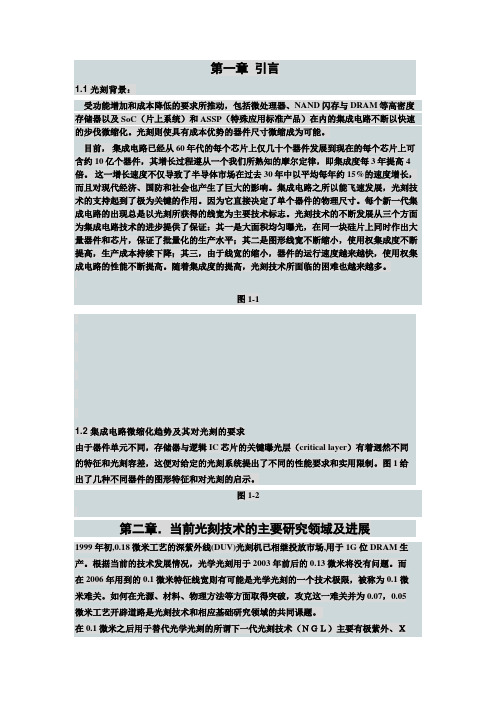
第一章引言1.1光刻背景:受功能增加和成本降低的要求所推动,包括微处理器、NAND闪存与DRAM等高密度存储器以及SoC(片上系统)和ASSP(特殊应用标准产品)在内的集成电路不断以快速的步伐微缩化。
光刻则使具有成本优势的器件尺寸微缩成为可能。
目前,集成电路已经从60年代的每个芯片上仅几十个器件发展到现在的每个芯片上可含约10亿个器件,其增长过程遵从一个我们所熟知的摩尔定律,即集成度每3年提高4倍。
这一增长速度不仅导致了半导体市场在过去30年中以平均每年约15%的速度增长,而且对现代经济、国防和社会也产生了巨大的影响。
集成电路之所以能飞速发展,光刻技术的支持起到了极为关键的作用。
因为它直接决定了单个器件的物理尺寸。
每个新一代集成电路的出现总是以光刻所获得的线宽为主要技术标志。
光刻技术的不断发展从三个方面为集成电路技术的进步提供了保证:其一是大面积均匀曝光,在同一块硅片上同时作出大量器件和芯片,保证了批量化的生产水平;其二是图形线宽不断缩小,使用权集成度不断提高,生产成本持续下降;其三,由于线宽的缩小,器件的运行速度越来越快,使用权集成电路的性能不断提高。
随着集成度的提高,光刻技术所面临的困难也越来越多。
图1-11.2集成电路微缩化趋势及其对光刻的要求由于器件单元不同,存储器与逻辑IC芯片的关键曝光层(critical layer)有着迥然不同的特征和光刻容差,这便对给定的光刻系统提出了不同的性能要求和实用限制。
图1给出了几种不同器件的图形特征和对光刻的启示。
图1-2第二章.当前光刻技术的主要研究领域及进展1999 年初,0.18 微米工艺的深紫外线(DUV)光刻机已相继投放市场,用于 1G 位 DRAM 生产。
根据当前的技术发展情况,光学光刻用于 2003 年前后的 0.13 微米将没有问题。
而在 2006 年用到的 0.1 微米特征线宽则有可能是光学光刻的一个技术极限,被称为 0.1 微米难关。
光刻机的分辨率与对位精度控制

光刻机的分辨率与对位精度控制光刻技术是半导体制造过程中至关重要的一环,它使用光刻机将光刻胶层上的芯片图案转移到硅片上。
而光刻机的分辨率和对位精度控制是影响芯片制造质量和性能的重要因素。
在本文中,我们将探讨光刻机如何实现高分辨率和精准的对位,并介绍一些常用的控制方法和技术。
首先,让我们详细了解一下光刻机的分辨率。
光刻机的分辨率是指光刻机可以将多小的细节或图案转移到硅片上。
分辨率通常用最小可分辨特征尺寸(L/S)来表示,即最小可以区分的线宽或间距。
分辨率的提升对于芯片制造来说非常重要,因为它直接影响到芯片的功能密度和性能。
在过去几十年中,光刻技术的分辨率经历了多次突破,从宏观光刻到近场光刻,再到现今的极紫外光刻技术,分辨率已经实现了亚奈米级别的突破。
要实现高分辨率,光刻机需要具备高性能的光源、光学系统和控制系统。
光刻机的光源需要产生高功率的紫外光,并具备短波长、窄线宽等特点,以便实现更小的L/S。
光刻机的光学系统需要通过透镜和光路的设计和优化,将光源上的芯片图案准确地投射到硅片上。
而控制系统则需要实时监控和调整光刻过程中各种参数,以保证图案的准确度和一致性。
其次,让我们来看一下光刻机的对位精度控制。
对位精度是指光刻机在投射芯片图案时,将图案位置与硅片上的已有特征对齐的能力。
对位精度对于多层芯片制造特别重要,因为不同层次的芯片图案需要准确对位,以确保电路连接的正确性。
对位精度的误差会导致芯片制造的失败和低产品良率。
光刻机的对位精度受到多种因素的影响。
首先,光刻机的机械结构和平台精度决定了投射过程中的稳定性和准确性。
其次,光刻机的光学系统对位控制能力也非常重要,它需要能够检测到硅片上已有图案的位置,并将新的图案与之对齐。
最后,光刻胶层的特性和涂覆过程也会对对位精度产生影响,因为光刻胶层的性质会随着涂覆的均匀性和干燥过程中的温度变化而改变。
为了实现高精度的对位,光刻机采用了许多控制方法和技术。
其中最常见的是通过图像传感器来实时检测硅片上已有图案的位置,并通过反馈控制的方式进行纠正。
光刻机分辨率和工艺节点-概念解析以及定义

光刻机分辨率和工艺节点-概述说明以及解释1.引言1.1 概述概述:光刻机是半导体制造中至关重要的设备之一,它在芯片制造过程中扮演着关键的角色。
光刻机的分辨率是衡量其性能和精度的重要指标,直接影响着芯片的制造质量和性能。
工艺节点则是半导体制造中一个重要的概念,代表着芯片制造工艺的进步和发展。
本文将探讨光刻机分辨率与工艺节点之间的关系,分析当前光刻机分辨率技术的发展现状,并展望未来光刻机分辨率技术的发展方向。
通过对光刻机分辨率的深入研究,可以更好地理解其对工艺节点的影响,为半导体制造技术的进步提供重要参考和指导。
1.2 文章结构部分:本文主要分为三个部分:引言、正文和结论。
在引言部分,首先概述了光刻机分辨率和工艺节点的关系,介绍了本文的目的。
然后简要说明了文章结构,即将在正文部分详细探讨光刻机分辨率的定义、工艺节点与光刻机分辨率的关系,以及当前光刻机分辨率技术的发展现状。
正文部分将详细讨论光刻机分辨率的定义,解释光刻机分辨率与工艺节点之间的关系,分析目前光刻机分辨率技术的发展现状,以及探讨光刻机分辨率对工艺节点的影响。
最后,在结论部分,将对光刻机分辨率对工艺节点的影响进行总结,展望未来光刻机分辨率技术的发展方向,并得出结论。
1.3 目的本文旨在探讨光刻机分辨率在半导体制造工艺中的重要性及其与工艺节点的关系。
通过对光刻机分辨率的定义、工艺节点与分辨率的关系以及当前技术发展现状的分析,旨在深入了解光刻机分辨率对工艺节点的影响,以及展望未来光刻机分辨率技术的发展方向。
希望通过本文的研究,能够为半导体制造领域的研究人员和工程师提供一定的参考和启发,推动光刻机分辨率技术的持续发展和进步,促进半导体行业的不断创新和发展。
2.正文2.1 光刻机分辨率的定义光刻机分辨率是指光刻机在制造微电子器件时能够实现的最小特征尺寸。
在半导体制造过程中,光刻技术被广泛应用于图案转移,即将设计图案通过光刻机投射到光刻胶上,形成所需的微细结构。
光刻机成像技术的创新突破案复杂性限制

光刻机成像技术的创新突破案复杂性限制光刻机是半导体制造过程中不可或缺的设备,其起到将电路图案投射到硅片上的关键作用。
然而,随着半导体制造工艺的日益复杂化,光刻机所面临的挑战也越来越大。
本文将探讨光刻机成像技术的创新突破,以应对复杂性限制。
一、光刻机成像技术的难题在现代半导体制造工艺中,芯片的尺寸越来越小,追求更高的集成度和更低的功耗成为行业发展的趋势。
然而,过去的光刻机成像技术面临着复杂性限制,主要体现在以下几个方面:1. 分辨率限制:随着芯片尺寸的缩小,要求光刻机能够实现更高的分辨率。
传统的紫外光刻机在分辨率上已接近瓶颈,无法满足现代工艺的要求。
2. 接近尺寸效应:当芯片尺寸接近或小于光波长的数量级时,光学物理现象的影响变得明显。
例如衍射效应和偏振效应会导致图案的衰减和失真。
3. 多层次曝光限制:复杂的工艺要求多层次曝光来形成不同层次的电路图案。
然而,成像层与层之间的误差累积和对准困难成为了制约因素。
二、创新突破应对复杂性限制为了解决光刻机成像技术的复杂性限制,业界进行了一系列的创新突破,以满足现代半导体工艺的需求。
1. 深紫外光刻技术:深紫外(DUV)光刻技术通过使用更短波长的光源,提高了分辨率和图案的准确性。
DUV光刻机采用了193nm或更低波长的光源,克服了紫外光刻机的分辨率限制。
2. 新型光刻胶材料:光刻胶是光刻工艺中的关键材料,直接影响图案的成像质量。
近年来,研究人员不断开发新型光刻胶材料,如低抗消光光刻胶(NIL),具有更好的光学性能和更低的衰减。
3. 非传统光刻技术:为了克服传统光刻技术的限制,研究人员也致力于开发非传统的成像技术。
例如,电子束光刻技术(EBL)利用电子束曝光取代光刻机,可以实现更高的分辨率和更好的图案控制。
4. 全息光刻技术:全息光刻技术基于全息干涉的原理,通过记录和再现光束的干涉图样,实现图案的成像。
这种技术能够克服多层次曝光的限制,并提供更高的分辨率和更好的失真控制。
光刻机分辨率_曝光系统的数值孔径_概述说明

光刻机分辨率曝光系统的数值孔径概述说明1. 引言1.1 概述在现代微电子工业中,光刻技术被广泛应用于芯片制造过程中的图形转移。
而光刻机作为一种关键设备,其分辨率和曝光系统的数值孔径成为了评估其性能的重要指标。
本文旨在对光刻机分辨率和曝光系统的数值孔径进行概述,并探讨它们对图形分辨能力的影响及如何提高这两个参数。
1.2 文章结构本文将围绕光刻机分辨率和曝光系统的数值孔径展开讨论。
首先,在第二部分中我们将对光刻机分辨率进行定义与解释,并探讨影响其性能的因素以及提高方法。
接下来,在第三部分中,我们将介绍曝光系统的数值孔径的概念与原理,并详细阐述它对图形分辨能力的影响以及增加数值孔径的方法。
最后,在结论部分总结文章主要观点,并展望未来研究方向。
1.3 目的本文旨在帮助读者深入了解光刻机分辨率和曝光系统的数值孔径这两个重要概念。
通过介绍其定义、影响因素和提高方法,读者将能够更好地理解光刻机性能评估和优化的原则与策略。
同时,本文还对数值孔径与分辨率之间的关系进行了深入探讨,以期为相关领域的研究者提供一些有益的参考和启发。
以上是“1. 引言”部分的内容。
2. 光刻机分辨率2.1 定义与解释光刻机分辨率是指在光刻过程中,可实现的最小特征尺寸。
它决定了光刻机能够制造出多大的特征尺寸,并直接影响芯片制造的精度和性能。
2.2 影响因素光刻机分辨率受到多个因素的影响,其中包括以下几个主要因素:a) 波长:通过选择合适的曝光光源波长,可以改变所需的最小特征尺寸。
一般来说,波长越短,分辨率越高。
b) 曝光系统数值孔径(NA):数值孔径是衡量曝光系统聚焦能力的一个参数。
数值孔径越大,光线会更集中,从而提高分辨率。
c) 曝光剂:曝光剂的性质也会对分辨率产生影响。
常见的曝光剂包括正丙醇和甲基异戊酮等。
d) 掩膜设计:掩膜设计中使用的图形形状和纹理也会对分辨率产生重要影响。
2.3 提高方法为了提高光刻机的分辨率,可以采取以下几种方法:a) 降低曝光波长:通过使用更短波长的光源,可以显著提高分辨率。
光刻机波长和分辨率关系

光刻机波长和分辨率关系光刻技术是微电子工艺中非常重要的一项技术,它在集成电路制造中起着至关重要的作用。
光刻机作为光刻技术的核心装备,其波长和分辨率之间存在着密切的关系。
光刻机的波长是指光刻机所使用的光源的波长。
光刻机通常使用紫外光作为光源,波长通常为365纳米、248纳米或193纳米。
随着光刻技术的发展,波长逐渐缩短,主要原因是波长的缩短可以提高分辨率,从而实现更小尺寸的芯片制造。
分辨率是光刻机的重要指标之一,它决定了光刻机能够实现的最小特征尺寸。
分辨率越高,光刻机可以制造的芯片尺寸就越小。
分辨率的计算公式为:分辨率= K * 波长/ NA,其中K为分辨率系数,NA为数值孔径。
分辨率系数是一个常数,与光刻机的光学系统有关,通常取值为0.5左右。
数值孔径是光刻机的一个重要参数,它决定了光刻机的分辨率。
从分辨率的计算公式可以看出,随着波长的减小,分辨率将会增加。
这是因为分辨率与波长成正比,波长越小,分辨率越高。
因此,随着光刻机波长的缩短,可以实现更小尺寸的芯片制造,这是光刻技术不断发展的重要原因之一。
然而,波长的缩短也会带来一些问题。
首先,随着波长的减小,光的穿透能力也会减弱,光刻机对光源的要求也会更高,这增加了光刻机的制造难度和成本。
其次,波长的缩短还会引发更多的光学效应,如衍射等,这些效应会对光刻机的分辨率产生负面影响。
因此,在实际应用中,需要在波长和分辨率之间找到平衡点,以满足对芯片尺寸和制造成本的要求。
除了波长和分辨率之间的关系,光刻机的分辨率还受到其他因素的影响。
例如,光刻机的光学系统、光刻胶的特性、掩膜的质量等都会对分辨率产生影响。
因此,在实际应用中,需要综合考虑各种因素,优化光刻机的参数设置,以实现更高的分辨率和更小尺寸的芯片制造。
光刻机的波长和分辨率之间存在着密切的关系。
随着波长的缩短,分辨率可以得到提高,从而实现更小尺寸的芯片制造。
然而,波长的缩短也会带来一些问题,需要在波长和分辨率之间找到平衡点。
紫外光刻机的性能分析与比较

紫外光刻机的性能分析与比较紫外光刻机是一种在半导体工艺、平面显示和其他微细加工领域中广泛应用的关键设备。
它通过使用紫外光源与光掩膜共同作用,将芯片集成电路等微细图形投射到硅片上,从而实现微电子器件的制造。
本文将对紫外光刻机的性能进行分析与比较,为读者提供更好的了解与选择依据。
一、光源类型与功率紫外光刻机的光源类型包括汞灯、氙气灯和固态激光器等。
其中,汞灯具有宽光谱、强烈的辐射能力和较低的成本,但其寿命较短。
氙气灯则具有较长的使用寿命和波长可调的优点,但其价格较高。
固态激光器兼具高功率、稳定性和波长窄的特点,但成本较高。
在选择光源时,需根据具体需求和经济考虑进行权衡。
二、分辨率与精度光刻机的分辨率和精度是评判其性能的重要指标。
分辨率指的是光刻机能表现出的最小线宽,也称为最小可分辨尺寸。
紫外光刻机的分辨率与掩膜、光刻胶和光学系统等因素有关。
较高的分辨率能够实现更微小的线宽,但同时也对工艺参数要求更高。
精度则是指在光刻过程中图形偏移与尺寸误差的程度,其决定了芯片的定位和准确度。
三、投影镜与光学系统光刻机中的投影镜和光学系统对于图形的放大、投射和对位起着重要的作用。
在比较不同光刻机性能时,需关注投影镜的放大倍率、工作距离和狭缝宽度等参数。
投影镜的高放大倍率能够实现更高的分辨率和更小的线宽,而较长的工作距离则有助于提高光学系统的稳定性。
同时,光学系统的对位误差也是评估性能的重要指标,它直接影响到芯片的精度和一致性。
四、稳定性与可靠性紫外光刻机在长时间运行过程中需要保持稳定性和可靠性。
稳定性包括光源稳定性、光功率稳定性、温度稳定性和机械稳定性等。
特别是在高精度微细加工中,稳定性对保持一致的线宽和图形形状至关重要。
可靠性则包括设备的寿命、故障率和维护周期等方面,以确保设备的长期稳定运行和生产效率。
五、附加功能和智能化程度随着科技的不断进步,现代紫外光刻机也逐渐具备了更多的附加功能和智能化特性。
例如,一些光刻机配备了自动补偿和自动对位功能,能够快速调整光刻过程中的误差。
封装制程光刻的瑞利公式
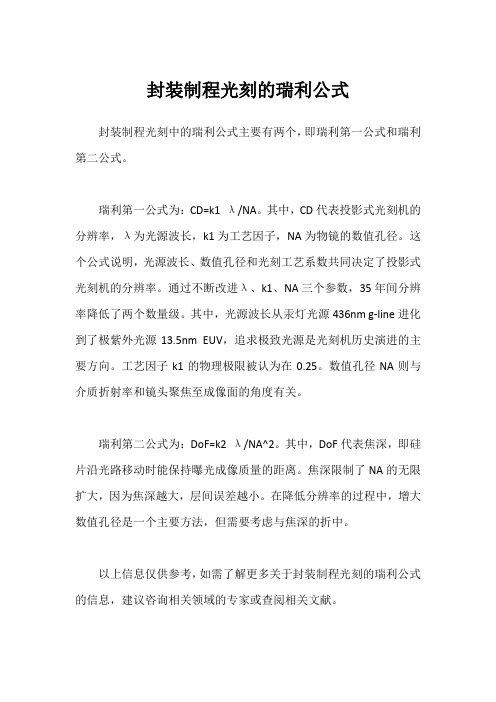
封装制程光刻的瑞利公式
封装制程光刻中的瑞利公式主要有两个,即瑞利第一公式和瑞利第二公式。
瑞利第一公式为:CD=k1 λ/NA。
其中,CD代表投影式光刻机的分辨率,λ为光源波长,k1为工艺因子,NA为物镜的数值孔径。
这个公式说明,光源波长、数值孔径和光刻工艺系数共同决定了投影式光刻机的分辨率。
通过不断改进λ、k1、NA三个参数,35年间分辨率降低了两个数量级。
其中,光源波长从汞灯光源436nm g-line进化到了极紫外光源13.5nm EUV,追求极致光源是光刻机历史演进的主要方向。
工艺因子k1的物理极限被认为在0.25。
数值孔径NA则与介质折射率和镜头聚焦至成像面的角度有关。
瑞利第二公式为:DoF=k2 λ/NA^2。
其中,DoF代表焦深,即硅片沿光路移动时能保持曝光成像质量的距离。
焦深限制了NA的无限扩大,因为焦深越大,层间误差越小。
在降低分辨率的过程中,增大数值孔径是一个主要方法,但需要考虑与焦深的折中。
以上信息仅供参考,如需了解更多关于封装制程光刻的瑞利公式的信息,建议咨询相关领域的专家或查阅相关文献。
光刻机对光学传感器制造的影响

光刻机对光学传感器制造的影响光学传感器作为一种重要的电子元件,广泛应用于光学通信、图像处理、测距仪器等领域。
而光刻机作为制造集成电路的关键设备之一,也在光学传感器的制造过程中起到至关重要的作用。
本文将详细探讨光刻机对光学传感器制造的影响。
第一部分:光刻机在光学传感器制造中的作用光刻机是一种利用光敏胶浆对光学器件进行微细图案化处理的设备。
在光学传感器的制造中,光刻机主要负责以下几个方面的工作:1. 光刻胶的涂布:光刻机通过涂布系统将光刻胶均匀涂布在硅基片上,使得胶层厚度均匀一致,确保后续的光刻过程能够顺利进行。
2. 软对准:在光学传感器制造中,光刻机通过软对准系统实现对硅基片和光掩模之间的对准。
软对准的精确度将直接影响到最终图案的质量和传感器性能。
3. 光刻曝光:光刻机将预先制作好的光掩模放置在硅基片上,并通过曝光光源对光刻胶进行照射,形成所需的微细图案。
曝光过程中,光刻机需要确保光线的均匀性和强度的稳定性,以保证图案的准确传递。
第二部分:光刻机对光学传感器制造的影响1. 分辨率:光刻机的分辨率决定了最小可制作的光刻图案的尺寸。
对于一些要求较高的光学传感器,需要采用分辨率较高的光刻机来确保制造过程的精度。
2. 对准精度:光刻机的对准精度对最终图案的质量和传感器性能有着重要的影响。
高精度的对准能够有效避免图案错位和误差,提高传感器的精度和灵敏度。
3. 曝光光源:光刻机的曝光光源是光学传感器制造中的重要参数之一。
稳定、均匀的光源能够确保光刻胶的曝光效果均匀一致,避免图案失真和缺陷。
4. 工艺控制:光刻机通过工艺控制系统对光刻过程进行监控和控制,保证制造过程的稳定性和重复性。
合理的工艺参数设置能够提高光学传感器的制造效率和一致性。
第三部分:光刻机技术的发展趋势随着科技的不断进步,光刻机技术也在不断发展和创新,并对光学传感器的制造带来了更多的影响和改进。
以下是一些光刻机技术的发展趋势:1. 紫外光刻技术的应用:紫外光刻技术由于其高分辨率和高效率的特点,在光学传感器制造中得到广泛应用。
光刻机中曝光模式对曝光分辨率的影响分析

光刻机中曝光模式对曝光分辨率的影响分析光刻机是一种在集成电路制造中广泛应用的工具,用于将芯片上的电路图案投影到硅片上,从而进行制造。
曝光是光刻机中的一个重要步骤,直接影响到曝光分辨率和芯片的制造质量。
本文将分析光刻机中曝光模式对曝光分辨率的影响。
曝光是通过光刻机中的曝光源将芯片上的电路图案投影到硅片上的过程。
在曝光过程中,曝光模式扮演着关键的角色。
曝光模式决定了曝光的方式和强度分布,进而影响到曝光的分辨率和图案的清晰度。
首先,我们来看一种常见的曝光模式,即全场曝光模式。
在全场曝光模式中,光刻机会将光线均匀地照射到整个硅片上。
这种曝光模式的优点是操作简单、适用范围广,但曝光分辨率相对较低。
由于整个硅片都会接受光线的照射,相邻的电路图案容易发生干涉和重叠,导致曝光分辨率下降,芯片的制造质量也相应降低。
与全场曝光模式相对应的是局部曝光模式。
在局部曝光模式中,光刻机只会将光线照射到芯片上需要曝光的区域。
这种曝光模式的优点是能够提高曝光分辨率,降低曝光的干涉和重叠现象。
通过准确控制曝光的位置和强度,可以实现更高的分辨率和更清晰的图案。
然而,局部曝光模式的操作相对复杂,需要进行精确的定位和调整,对设备和操作人员的要求也更高。
除了全场曝光模式和局部曝光模式之外,还有一种常见的曝光模式是阵列曝光模式。
阵列曝光模式将芯片上的多个电路图案进行分组,每次曝光只处理一个分组。
这种曝光模式可以提高曝光的效率和均匀性,减少曝光的干涉和重叠现象,进而提高曝光分辨率。
然而,阵列曝光模式的操作也较为复杂,需要精确的分组和定位,同时要求曝光源的稳定性和一致性。
通过上述分析可以得出结论,光刻机中曝光模式对曝光分辨率具有重要影响。
全场曝光模式操作简单,但曝光分辨率相对较低;局部曝光模式和阵列曝光模式能够提高曝光分辨率,但操作相对复杂。
在实际制程中,可以根据芯片的要求和制造的复杂程度选择适合的曝光模式。
同时,还需注意采取合适的曝光参数和控制手段,如曝光时间、光源强度、焦距等,以保证曝光的准确性和稳定性。
光刻机的工艺节点和波长
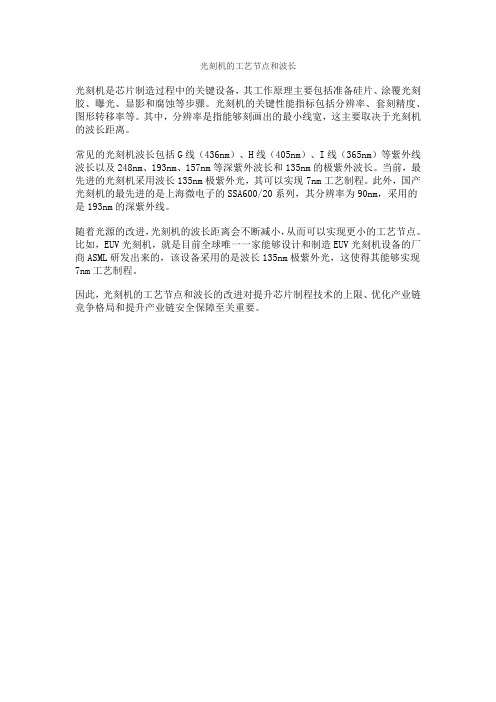
光刻机的工艺节点和波长
光刻机是芯片制造过程中的关键设备,其工作原理主要包括准备硅片、涂覆光刻胶、曝光、显影和腐蚀等步骤。
光刻机的关键性能指标包括分辨率、套刻精度、图形转移率等。
其中,分辨率是指能够刻画出的最小线宽,这主要取决于光刻机的波长距离。
常见的光刻机波长包括G线(436nm)、H线(405nm)、I线(365nm)等紫外线波长以及248nm、193nm、157nm等深紫外波长和135nm的极紫外波长。
当前,最先进的光刻机采用波长135nm极紫外光,其可以实现7nm工艺制程。
此外,国产光刻机的最先进的是上海微电子的SSA600/20系列,其分辨率为90nm,采用的是193nm的深紫外线。
随着光源的改进,光刻机的波长距离会不断减小,从而可以实现更小的工艺节点。
比如,EUV光刻机,就是目前全球唯一一家能够设计和制造EUV光刻机设备的厂商ASML研发出来的,该设备采用的是波长135nm极紫外光,这使得其能够实现7nm工艺制程。
因此,光刻机的工艺节点和波长的改进对提升芯片制程技术的上限、优化产业链竞争格局和提升产业链安全保障至关重要。
我国光刻机发展史

我国光刻机发展史我国光刻机发展史光刻机是一种重要的微纳加工工具,主要应用于芯片制造等领域中。
我国光刻机的发展历程虽然短暂,但取得了一定的成就。
20世纪80年代初期,我国开始研制光刻机。
当时由于基础条件和研发水平的限制,我国的光刻机主要靠进口。
1984年,中国科学院长春光学精密机械研究所研制出我国的第一台光刻机。
虽然这台光刻机的分辨率只有5微米,而国际上的先进水平已经发展到1微米甚至更高,但这仍然是我国光刻机研究的重大突破。
当时,这台光刻机被广泛应用于民用和国防领域,成为我国自主生产的光刻机的开端。
1986年,上海微电子装备厂开始研制光刻机。
经过近4年的努力,1990年,该厂研制出我国的第一台半导体专用光刻机SF100。
这台光刻机的分辨率达到了1微米,适用于CMOS尺寸的加工,在国际上处于先进水平。
实现了我国在这一领域的领先地位。
1990年代,我国各地的企业和高校开始涌现出自主研制光刻机的势头。
1993年,北京大学研究团队在国家863计划的支持下,研制出我国第一台全自动光刻机LC-626。
随着我国经济的持续发展,光刻机制造企业也迅速发展壮大。
现在我国已有多家企业生产光刻机,如中微半导体设备、浙江华大光电技术股份有限公司等。
而中微半导体设备是其中最大的厂商之一,其光刻机发展达到国际领先水平,2005年推出的QL1100配备的是高质量的目标导向系统、光控系统和模板辅助对位系统,其分辨率为70纳米,已经达到了国际水平。
总的来说,我国光刻机的发展历程虽然较短暂,但仍然取得了一定的成就。
未来随着我国科技水平的不断提高以及光刻机市场需求的不断增加,相信我国的光刻机行业会取得更大的进步和发展。
- 1、下载文档前请自行甄别文档内容的完整性,平台不提供额外的编辑、内容补充、找答案等附加服务。
- 2、"仅部分预览"的文档,不可在线预览部分如存在完整性等问题,可反馈申请退款(可完整预览的文档不适用该条件!)。
- 3、如文档侵犯您的权益,请联系客服反馈,我们会尽快为您处理(人工客服工作时间:9:00-18:30)。
第一章引言
1.1光刻背景:
受功能增加和成本降低的要求所推动,包括微处理器、NAND闪存与DRAM等高密度存储器以及SoC(片上系统)和ASSP(特殊应用标准产品)在内的集成电路不断以快速的步伐微缩化。
光刻则使具有成本优势的器件尺寸微缩成为可能。
目前,集成电路已经从60年代的每个芯片上仅几十个器件发展到现在的每个芯片上可含约10亿个器件,其增长过程遵从一个我们所熟知的摩尔定律,即集成度每3年提高4倍。
这一增长速度不仅导致了半导体市场在过去30年中以平均每年约15%的速度增长,而且对现代经济、国防和社会也产生了巨大的影响。
集成电路之所以能飞速发展,光刻技术的支持起到了极为关键的作用。
因为它直接决定了单个器件的物理尺寸。
每个新一代集成电路的出现总是以光刻所获得的线宽为主要技术标志。
光刻技术的不断发展从三个方面为集成电路技术的进步提供了保证:其一是大面积均匀曝光,在同一块硅片上同时作出大量器件和芯片,保证了批量化的生产水平;其二是图形线宽不断缩小,使用权集成度不断提高,生产成本持续下降;其三,由于线宽的缩小,器件的运行速度越来越快,使用权集成电路的性能不断提高。
随着集成度的提高,光刻技术所面临的困难也越来越多。
图1-1
1.2集成电路微缩化趋势及其对光刻的要求
由于器件单元不同,存储器与逻辑IC芯片的关键曝光层(critical layer)有着迥然不同的特征和光刻容差,这便对给定的光刻系统提出了不同的性能要求和实用限制。
图1给出了几种不同器件的图形特征和对光刻的启示。
图1-2
第二章.当前光刻技术的主要研究领域及进展
1999 年初,0.18 微米工艺的深紫外线(DUV)光刻机已相继投放市场,用于 1G 位 DRAM 生产。
根据当前的技术发展情况,光学光刻用于 2003 年前后的 0.13 微米将没有问题。
而
在 2006 年用到的 0.1 微米特征线宽则有可能是光学光刻的一个技术极限,被称为 0.1 微米难关。
如何在光源、材料、物理方法等方面取得突破,攻克这一难关并为 0.07,0.05 微米工艺开辟道路是光刻技术和相应基础研究领域的共同课题。
在 0.1 微米之后用于替代光学光刻的所谓下一代光刻技术(NGL)主要有极紫外、X
射线、电子束的离子束光刻。
由于光学光刻的不断突破,它们一直处于“候选者”的地位,并形成竞争态势。
这些技术能否在生产中取得应用,取决于它们的技术成熟程度、设备
成本、生产效率等。
第三章.光刻的原理和分类
3.1光刻的原理:
光刻是通过一系列生产步骤将晶圆表面薄膜的特定部分除去的工艺(图 4.7)。
在此之后,晶圆表面会留下带有微图形结构的薄膜。
被除去的部分可能形状是薄膜内的孔或是残留的
岛状部分。
光刻工艺也被称为大家熟知的Photomasking, masking, photolithography, 或microlithography。
在晶圆的制造过程中,晶体三极管、二极管、电容、电阻和金属层的
各种物理部件在晶圆表面或表层内构成。
这些部件是每次在一个掩膜层上生成的,并且结
合生成薄膜及去除特定部分,通过光刻工艺过程,最终在晶圆上保留特征图形的部分。
光
刻生产的目标是根据电路设计的要求,生成尺寸精确的特征图形,并且在晶圆表面的位置
正确且与其它部件(parts)的关联正确。
光刻是所有四个基本工艺中最关键的。
光刻确定了器件的关键尺寸。
光刻过程中的错误可
造成图形歪曲或套准不好,最终可转化为对器件的电特性产生影响。
图形的错位也会导致
类似的不良结果。
光刻工艺中的另一个问题是缺陷。
光刻是高科技版本的照相术,只不过
是在难以置信的微小尺寸下完成。
在制程中的污染物会造成缺陷。
事实上由于光刻在晶圆
生产过程中要完成5层至20层或更多,所以污染问题将会放大。
3.2光刻的分类:
1.光学光刻
光学光刻是通过光学系统以投影方法将掩模上的大规模集成电路器件的结构图形“刻”在
涂有光刻胶的硅片上,限制光刻所能获得的最小特征尺寸直接与光刻系统所能获得的分
辨率直接相关,而减小光源的波长是提高分辨率的最有效途径。
因此,开发新型短波长
光源光刻机一直是国际上的研究热点。
目前,商品化光刻机的光源波长已经从过去的汞
灯光源紫外光波段进入到深紫外波段(DUV),如用于 0.25 微米技术的 KrF 准分子激光(波长为248纳米)和用于0.18微米技术的ArF准分子激光(波长为193纳米)。
除此之外,利用光的干涉特性,采用各种波前技术优化工艺参数也是提高光刻分辨率的
重要手段。
这些技术是运用电磁理论结合光刻实际对曝光成像进行深入的分析所取得的
突破。
其中有移相掩膜、离轴照明技术、邻近效应校正等。
运用这些技术,可在目前的
技术水平上获得更高分辨率的光刻图形。
如 1999 年初 Canon 公司推出的 FPA-1000ASI 扫描步进机,该机的光源为 193 纳米 ArF,通过采用波前技术,可在 300 毫米硅片上实
现0.13微米光刻线宽。
光刻技术包括光刻机、掩模、光刻胶等一系列技术,涉及光、机、电、物理、化学、材
料等多个研究领域。
目前科学家正在探索更短波长的F2 激光(波长为157纳米)光刻技术。
由于大量的光吸收,获得用于光刻系统的新型光学及掩模衬底材料是该波段技术的
主要困难。
2.极紫外光刻(EUVL)
极紫外光刻用波长为10-14 纳米的极紫外光作光源。
虽然该技术最初被称为软X射线光刻,但实际上更类似于光学光刻。
所不同的是由于在材料中的强烈吸收,其光学系统必
须采用反射形式。
如果 EUVL 得到应用,它甚至可能解决 2012 年的 0.05 微米及以后的
问题,对此发展应予以足够重视。
3.X射线光刻(XRL)
XRL光源波长约为1纳米。
由于易于实现高分辨率曝光,自从XRL技术在70年代被发明以来,就受到人们广泛的重视。
欧洲、美国、日本和中国等拥有同步辐射装置的国家
相继开展了有关研究,是所有下一代光刻技术中最为成熟的技术。
XRL的主要困难是获得具有良好机械物理特性的掩膜衬底。
近年来掩膜技术研究取得较大进展。
SiC 目前被
认为是最合适的衬底材料。
由于与XRL相关的问题的研究已经比较深入,加之光学光刻技术的发展和其它光刻技术的新突破,XRL 不再是未来“惟一”的候选技术,美国最近对XRL的投入有所减小。
尽管如此,XRL技术仍然是不可忽视的候选技术之一。
4.电子束光刻(EBL)
电子束光刻采用高能电子束对光刻胶进行曝光从而获得结构图形,由于其德布罗意波长
为 0.004 纳米左右,电子束光刻不受衍射极限的影响,可获得接近原子尺度的分辨率。
电子束光刻由于可以获得极高的分辨率并能直接产生图形,不但在 VLSI 制作中已成为
不可缺小的掩模制工具,也是加工用于特殊目的的器件和结构的主要方法。
目前的电子束曝光机的分辨率已达 0.1 微米以下。
电子束光刻的主要缺点是生产效率较低,经贸部为每小时5~10个圆片,远小于目前光学光刻的每小时50~100个圆片的水平。
最近,美国朗讯公司开发的角度限制散射投影电子束光刻 SCALPEL 技术令人瞩目,该
技术如同光学光刻那样对掩模图形进行缩小投影,并采用特殊滤波技术去除掩模吸收体
产生的散射电子,从而在保证分辨率条件下提高产出效率,应该指出,无论未来光刻采
用何种技术,EBL都将是集成电路研究与生产不可缺小的基础设施。
5.离子束光刻(IBL)
离子束光刻采用液态原子或所态原子电离后形成的离子通过电磁场加速及电磁透镜的聚
焦或准直后对光刻胶进行曝光。
其原理与电子束光刻类似,但德布罗意波长更短(小于
0.0001纳米),且有无邻近效应小、曝光场大等优点。
离子束光刻主要包括聚焦离子束光刻(FIBL)、离子投影光刻(IPL)等。
其中 FIBL 发展最早,最近实验研究中已获得 10 纳米的分辨率。
该技术由于效率低,很难在生产中作为曝光工具得到应用,目前主要用
作VLSI中的掩模修补工具和特殊器件的修整。
由于 FIBL 的缺点,人们发展了具有较高曝光效率的 IPL 技术。
欧洲和美国联合了大量
企业、大学和研究机构,开展了一个名为 MEDEA 的合作项目,用于解决设备和掩模等
方面的问题,进行可行性验证,目前已取得不少进展。