烧结计算公式
烧结煤气单耗公式

烧结煤气单耗公式
其中,烧结煤气消耗量是指在烧结过程中所需的煤气的消耗量,烧结矿产量是指烧结矿的产量。
烧结煤气消耗量的计算公式如下:
烧结煤气消耗量=燃料消耗*烧结煤气提纯系数
其中,燃料消耗是指在生产过程中所需的燃料的消耗量,烧结煤气提纯系数是指将原材料中的煤气提纯成烧结煤气的系数。
燃料消耗的计算公式如下:
燃料消耗=煤气发生量*可燃物的含量/可燃物的发热值
其中,煤气发生量是指在生产过程中产生的煤气的量,可燃物的含量是指煤气中可燃物的含量,可燃物的发热值是指单位质量可燃物所释放的热量。
这是一个基本的计算公式,但实际上,烧结煤气单耗的计算过程可能更加复杂,需要考虑各种因素如燃料的燃烧效率、烧结矿的成分和煤气的处理过程等。
详细的计算方法需要根据具体的生产工艺和设备,以及相应的数据进行精确计算。
烧结机利用系数的计算公式

烧结机利用系数的计算公式烧结机利用系数的计算公式烧结机是冶金行业中必不可少的设备之一,用于把多种粉状物料烧结成一体,从而得到所需的产品。
在烧结过程中,烧结机的利用系数是非常重要的指标之一,因此需要对其进行精确的计算。
下面就来介绍一下烧结机利用系数的计算公式。
1. 利用系数的定义烧结机的利用系数是指烧结机实际出料量与烧结机理论出料量之比,是评价烧结机生产效率的重要指标。
2. 利用系数的计算公式烧结机的利用系数计算公式如下:利用系数=烧结机实际出料量÷烧结机理论出料量×100%其中,烧结机实际出料量指的是烧结机实际出料量与烧结机的理论出料量之差。
而烧结机的理论出料量可以通过烧结机的设计参数来计算得出。
3. 计算实例为了更好地理解利用系数的计算方法,下面给出一个实例:例如,一台烧结机的设计参数为:烧结带宽度为2400mm,烧结带速为0.5m/s,出料口宽度为500mm,出料口高度为200mm,则该烧结机的理论出料量为:理论出料量=烧结带速×烧结带宽度×出料口高度×60÷出料口宽度理论出料量=0.5m/s×2400mm×200mm×60÷500mm理论出料量=17.28t/h假设该烧结机实际出料量为15t/h,则该烧结机的利用系数为:利用系数=15t/h÷17.28t/h×100%利用系数=86.8%通过这个计算实例,我们可以看到,烧结机利用系数与烧结机的设计参数、实际出料量等因素密切相关。
4. 影响利用系数的因素除了设计参数和实际出料量之外,烧结机利用系数还会受到其他因素的影响,例如:(1)烧结矿粒度和成分的不同,会影响烧结机的料层气流性质和热特性,从而影响烧结机的利用系数;(2)烧结机运行中的温度、压力、气流速度等参数的变化,均会对烧结机的利用系数产生影响。
5. 计算公式的应用烧结机利用系数的计算公式可以应用于生产实践中,包括但不限于以下方面:(1)评价烧结机生产效益,了解烧结机的工作状态;(2)优化烧结机的生产流程,提高烧结机的利用率;(3)对比不同烧结机的利用系数,进行烧结机选型和技术改进。
主要生产指标的计算公式

主要生产指标的计算公式一、烧结厂1、烧结矿产量=皮带速度x料批x作业时间x(100-混合料水分)x残存量2、反推产量=高返×+落地量-上落地量+高炉入炉烧结矿量3、台时产量=产量/作业时间4、烧结机有效面积利用系数(t/(m2·台时))= 烧结矿产出量/(有效面积×实际作业时间)5、烧结矿品位=烧结矿含铁量(吨)/烧结矿产出量(吨)x100%6、日历作业率(%)=实际作业时间/日历时间%(取参数报表中时间)7、干料量=该原料湿料量×(1-H2O%)8、干料单耗=某物料干料量/产量×1000 (kg)9、铁料原料消耗(单耗)=1吨消耗多少公斤该物料。
10、烧结矿固体燃料消耗(kg/t)=烧结矿固体燃料耗用量kg/烧结矿产出量t11、烧结矿煤粉消耗(kg/t)=烧结矿煤粉耗用量kg/烧结矿产出量t12、烧结矿焦粉消耗(kg/t)=烧结矿焦粉耗用量kg/烧结矿产出量t13、一次配料:某料下料量=某料的百分比×总下料量∕100 (t)14、一次配料某物料配比=某料总配比表中配比/一次配料物料在总配比表配比之和15、某物料下料量=某物料下料量(吨/小时)×运行时间段16、成品率=产量/(产量+返矿)%(返矿取配料配比变更)17、出矿率=产量/(混合料总量×) %18、返矿率=返矿/(产量+返矿)%二、炼铁厂1、生铁合格率(%)=生铁检验合格量(吨)/生铁检验总量(吨) x100%2、生铁一级品率(%)=一级品生铁总量/合格生铁检验总量x100%3、入炉焦比是反映高炉冶炼每1吨合格生铁所消耗的干焦炭量。
入炉焦比(kg/t)=干焦耗用量kg/合格生铁产量t4、干焦量=湿焦量x(1-湿焦含水%)5、综合焦比是指高炉冶炼每1吨合格生铁所消耗的综合干焦(将各种燃料均折合成干焦计算)量。
综合焦比(kg/t)=综合干焦耗用量kg/合格生铁产量t6、综合干焦量=干焦量+其他各种燃料量x折合干焦系数7、喷煤比是反映高炉冶炼1吨合格生铁所消耗的煤量。
烧结工艺公式
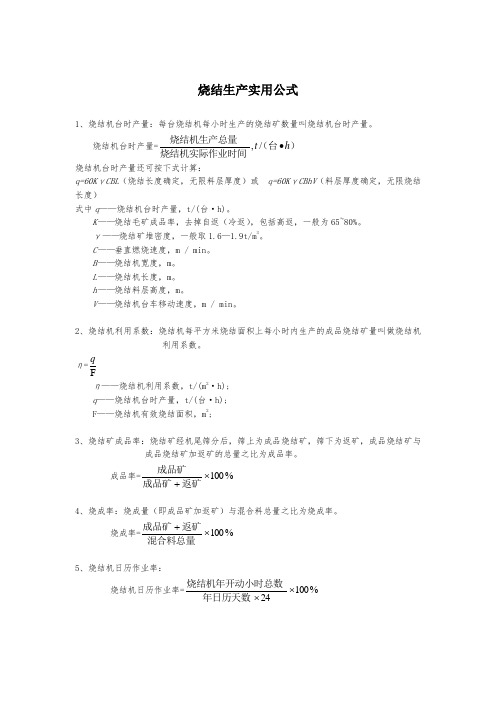
烧结生产实用公式
1、烧结机台时产量:每台烧结机每小时生产的烧结矿数量叫烧结机台时产量。
烧结机台时产量=)(台烧结机实际作业时间
烧结机生产总量h t •/, 烧结机台时产量还可按下式计算:
q=60K γCBL (烧结长度确定,无限料层厚度)或 q=60K γCBhV (料层厚度确定,无限烧结长度)
式中q ——烧结机台时产量,t/(台·h)。
K ——烧结毛矿成品率,去掉自返(冷返),包括高返,一般为65~80%。
γ——烧结矿堆密度,一般取1.6—1.9t/m 3。
C ——垂直燃烧速度,m / min 。
B ——烧结机宽度,m 。
L ——烧结机长度,m 。
h ——烧结料层高度,m 。
V ——烧结机台车移动速度,m / min 。
2、烧结机利用系数:烧结机每平方米烧结面积上每小时内生产的成品烧结矿量叫做烧结机
利用系数。
η=F
q η——烧结机利用系数,t/(m 2·h);
q ——烧结机台时产量,t/(台·h);
F ——烧结机有效烧结面积,m 2
;
3、烧结矿成品率:烧结矿经机尾筛分后,筛上为成品烧结矿,筛下为返矿,成品烧结矿与
成品烧结矿加返矿的总量之比为成品率。
成品率=
%100⨯+返矿成品矿成品矿
4、烧成率:烧成量(即成品矿加返矿)与混合料总量之比为烧成率。
烧成率=
%100⨯+混合料总量返矿成品矿
5、烧结机日历作业率:
烧结机日历作业率=%10024
⨯⨯年日历天数烧结机年开动小时总数。
烧结配料的计算调整

烧结配料的计算调整一、现场简易计算调整1、干料配比=湿料配比×(100-水分)%2、残存量=干料配比×(100-烧损)%3、焦粉残存=焦粉干料配比×(100-烧损)%=焦粉干料配比×灰分4、烧结矿残存率=(总残存量÷总干料量)×%5、进入配合料中TFe=原料含铁量×干料配比SiO2=原料SiO2含量×干料配比CaO=原料CaO含量×干料配比6、烧结矿碱度R的工业计算R2=(CaO矿×矿石量+ CaO灰×灰石量) ÷(SiO2矿×矿石量+ SiO2灰×灰石量﹍+S(0.5-1.5))7、配合料及烧结矿的化学成分TFe料=各种物料带入TFe之和÷各种干原料之和TFe矿=各种物料带入TFe之和÷总残存量SiO2料=各种物料带入SiO2之和÷各种干原料之和SiO2矿=各种物料带入SiO2之和÷总残存量CaO料=各种物料带入CaO之和÷各种干原料之和CaO矿=各种物料带入CaO之和÷总残存量二、配用石灰石的计算公式(阿尔希波夫公式)100×(k×a-b)/【k×(a-c)+(d-b)】=加入量%K----规定的碱度a----料中SiO2+AI2O3的含量(石灰石中的除外)b----料中CaO+MgO的含量(石灰石中的除外)c----石灰石中SiO2+AI2O3的含量%d----石灰石中CaO+MgO的含量%三、燃料配用量和配比的计算公式Q燃=C混×(Q配+Q返)-C返×Q返/C煤kg B燃=Q燃÷Q配%式中:Q燃、Q配、Q返分别为燃料配用量、配料室总流量、返矿流量C混、C返、C煤----分别为混合料固定碳、返矿残碳、煤粉固定碳%B燃----为燃料配比%四、白云石配加量(干)的简易计算公式白云石配比=(MgO A- MgO A‵)%×A/(1-H2O白%) ×MgO白%式中:MgO A----烧结矿要求的MgO A%MgO A‵--未加白云石烧结矿的MgO A%H2O白----白云石中含H2O%五、已知高炉渣中MgO含量,求烧结矿MgO含量。
烧结计算公式.doc

烧结计算公式产量台时台时=利用系数=作业时间 210作业时间作业率=%(取参数报表中时间)日历时间作业时间扣外作业率=%(取参数报表中时间、影响因素)日历时间-外因时间产量成品率=%(返矿取配料配比变更)产量+返矿某物料干料量干料量=该原料湿料量×(1-H2O%)单耗=×1000 (kg)产量铁料原料消耗(单耗)=1吨消耗多少公斤该物料。
匀矿×印粉配加百分比×(1-H2O%)例:印粉=━━━━━━━━━━━━━━━━━×1000 (kg)烧结矿产量一次配料:某料下料量=某料的百分比×总下料量∕100 (t)某料总配比表中配比一次配料某物料配比=━━━━━━━━━━━━━━━━━一次配料物料在总配比表配比之和某物料下料量=某物料下料量(吨/小时)×运行时间段产量返矿出矿率=%返矿率=%混合料总量×0.92 产量+返矿反推产量=高返×0.97+落地量-上落地量+高炉入炉烧结矿量其它计算公式黑料合量公式(FeO×0.777-TFe)×1.43-FeO-SiO2-CaO-MgO=98-99 白料合量公式CaO×1.784+MgO×2.09+SiO2=96-99有效CaO石=CaO石-SiO2石×R基(R烧-R基)×SiO2石∕有效CaO石=需加减灰石量(混合料SiO2总-SiO2石)×R基-(混合料CaO总-CaO石)=R基需要CaO R基需要CaO灰石湿配比=÷(1-H2O%)有效CaO石CaOR=SiO2反推产量=高炉入炉烧结矿+高返×0.97+落地量-上落地量铺底料使用量计算公式:铺底料用量=台车宽度×铺底料厚度×烧结矿堆比重×机速×运行时间例:3.5×0.04×1.7×720×1.05(机速)=180T残存=干料*(1-烧损%)各物料残留成份计算:TFe=干料×TFe%SiO2=干料×SiO2% CaO=干料×CaO%MgO=干料×MgO% Al2O3=干料×Al2O3%烧结矿成份计算:TFe=各物料残留TFe之和×100∕各物料残存之和SiO2=各物料残留SiO2之和×100∕各物料残存之和CaO=各物料残留CaO之和×100∕各物料残存之和MgO=各物料残留MgO之和×100∕各物料残存之和Al2O3=各物料残留Al2O3之和×100∕各物料残存之和。
烧结原理及配料计算
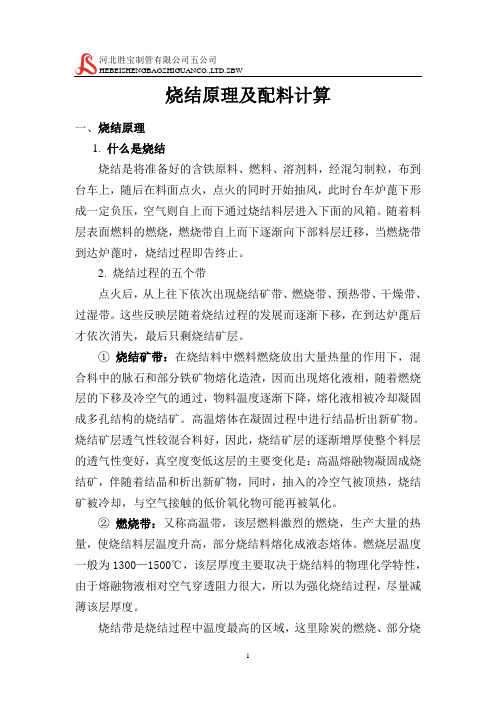
HEBEISHENGBAOZHIGUANCO.,LTD.SBW烧结原理及配料计算一、烧结原理1. 什么是烧结烧结是将准备好的含铁原料、燃料、溶剂料,经混匀制粒,布到台车上,随后在料面点火,点火的同时开始抽风,此时台车炉蓖下形成一定负压,空气则自上而下通过烧结料层进入下面的风箱。
随着料层表面燃料的燃烧,燃烧带自上而下逐渐向下部料层迁移,当燃烧带到达炉蓖时,烧结过程即告终止。
2. 烧结过程的五个带点火后,从上往下依次出现烧结矿带、燃烧带、预热带、干燥带、过湿带。
这些反映层随着烧结过程的发展而逐渐下移,在到达炉蓖后才依次消失,最后只剩烧结矿层。
①烧结矿带:在烧结料中燃料燃烧放出大量热量的作用下,混合料中的脉石和部分铁矿物熔化造渣,因而出现熔化液相,随着燃烧层的下移及冷空气的通过,物料温度逐渐下降,熔化液相被冷却凝固成多孔结构的烧结矿。
高温熔体在凝固过程中进行结晶析出新矿物。
烧结矿层透气性较混合料好,因此,烧结矿层的逐渐增厚使整个料层的透气性变好,真空度变低这层的主要变化是:高温熔融物凝固成烧结矿,伴随着结晶和析出新矿物,同时,抽入的冷空气被顶热,烧结矿被冷却,与空气接触的低价氧化物可能再被氧化。
②燃烧带:又称高温带,该层燃料激烈的燃烧,生产大量的热量,使烧结料层温度升高,部分烧结料熔化成液态熔体。
燃烧层温度一般为1300—1500℃,该层厚度主要取决于烧结料的物理化学特性,由于熔融物液相对空气穿透阻力很大,所以为强化烧结过程,尽量减薄该层厚度。
烧结带是烧结过程中温度最高的区域,这里除炭的燃烧、部分烧结料融化外,还伴随着碳酸盐的分解,硫酸盐的分解、硫化物和磁化矿的氧化,部分赤铁矿的热分解、还原等。
总之,这一带的物理化学变化异常复杂。
③预热带:空气通过燃烧带参加反映后,即携带一部分热量进入下部为预热带。
预热带厚度较薄,与燃烧带紧密相连,温度一般为400℃—800℃,在预热带,烧结料中的结晶水分解,部分碳酸盐,硫酸盐也开始分解,磁铁矿局部被氧化及组分间的固相反应等。
烧结法原料制备

第二章
2、碱比:
原料制备(十四)
碱比是孰料或生料桨中氧化钠与氧化铝和氧化铁的分子比 (也叫摩尔比)N/R=[Na2OT - Na2OS]/( [Al2O3+ Fe2O3]) = Na2O%/62/( Al2O3%/102+ Fe2O3%/160) =1.645 Na2O%/( Al2O3%+ 0.6375Fe2O3%) =1.645 N/( A+ 0.6375F) 由于烧成煤灰分的影响生料碱比=中心数+增量
第二章
原料制备(六)
一、原料制备在氧化铝生产中的作用
碱-石灰烧结氧化铝生产的特点是:生产工艺流程长,设 备类型多,生产连续性强,在生产过程中必须严格控制生产技 术条件,必须搞好配料,保证熟料质量,严格掌握湿式系统的 技术条件,认真贯彻“均衡、稳定、提高”的方针,达到优质、 高产、低消耗的目的。 原料制备是氧化铝生产的第一道工序,也是烧结法生产的 基础。主要生产任务就是为氧化铝生产磨制调配各项指标合格 的料浆,消化拜尔赤泥、达到生产氧化铝和回收碱的目的。主 要工序有铝矿破碎、配矿、磨制调配各项指标合格的料浆和生 产高浓度的CO2气体、生产合格石灰和石灰乳的任务。 能否制备出合格的生料浆,将直接影响到氧化铝和氧化钠 的净溶出率,也影响到熟料窑的操作等,直接影响到烧结法氧 化铝的产量和技术经济指标。
第二章
原料制备(十三)
(3)配矿计算 已知A矿、B矿成分如下: A矿 Al2O352.98%、SiO220.42%、Fe2O38.39%、A/S2.6 B矿 Al2O362.54%、SiO210.76%、Fe2O37.33%、A/S5.87 要求混矿A/S为a.3.2,b.4.4,c.4.6若铝土矿的容重1650千克/ 立方米kg/m3,无烟煤容重800kg/m3矿石若按8%的比例(重量百 分比)配入无烟煤。求100抓A矿要配入多少抓B矿?多少? 解:a.设100抓A矿要配入x抓B矿,y抓无烟煤 (52.98*100+62.54*x)/(20.42*100+10.76*x)=3.2(4.6) 解得:x≈44抓 配煤量为:y=(100+44)*0.11*1.65/0.8=32.7抓≈33抓 b.同样混矿4.4 ,x≈243抓,y=78抓 C.混矿4.6 ,x≈314抓,y=94抓
烧结配料计算办法及公式

精心整理烧结过程是一个非常复杂的氧化还原过程,氧的得失很难确定,原料成分的波动和水分的大小均会对最终结果产生影响,而要精确进行烧结配料的理论计算,在烧结生产中显得尤为麻烦,并且要占用大量的时间,所以,现场配料计算一般多采用简易计算方法,即:反推算法。
(100g—200g)加热至150摄氏度,恒温1h,已蒸发的水分重量占试样重量的百分比。
4、化学成分:原料的化学成分是指某元素或化合物含量占该种干原料试样重量的百分比。
二、具体计算公式1、烧残量=干料配比×(1—烧损)2、进入配合料中的TFe=该种原料含TFe量×该种原料配比3、进入配合料中的SiO2=该种原料含SiO2量×该种原料配比4、进入配合料中的CaO=该种原料含CaO量×该种原料配比5、进入配合料中的MgO=该种原料含MgO量×该种原料配比6、进入配合料中的Mn=该种原料含Mn量×该种原料配比烧结配料计算的主要公式1.干料配比=湿料配比*(100-水分)%2.残存量=干料配比*(100-烧损)%3.焦粉残存=焦粉干料配比*(100-烧损)%=焦粉干配比*灰分%4.烧结残存率=(总残存/总干料)*100%5.进入配合料中TFe=该原料含铁量*干料配比%??SiO2=该原料的SiO2含量*该料配比%CaO=该原料CaO含量*干料配比%.6.烧结矿碱度R的工业计算:R=CaO(矿)*矿石量+CaO(灰)*灰石量+.../SiO2(矿)*矿石量+SiO2*灰石量+...+S?[注:S---考虑生产过程的理化损失与燃料的影响引入的修正系数,其数值由实验决定,随着碱度的升高而升高,其值在0.5~1.5之间.]7.配合料及烧结矿的化学成分.TFe(料)=各种料带入TFe之和/各种干原料之和8.TFe(矿)=各种料带入TFe之和/中残存量SiO2(料)=各种料带入SiO2之和/各种干原料之和?SiO2(矿)=各种料带入SiO2之和/总残存量CaO(料)=各种料带入CaO之和/各种干原料之和??CaO(矿)=各种料带入CaO之和/总残存量。
主要生产指标的计算公式
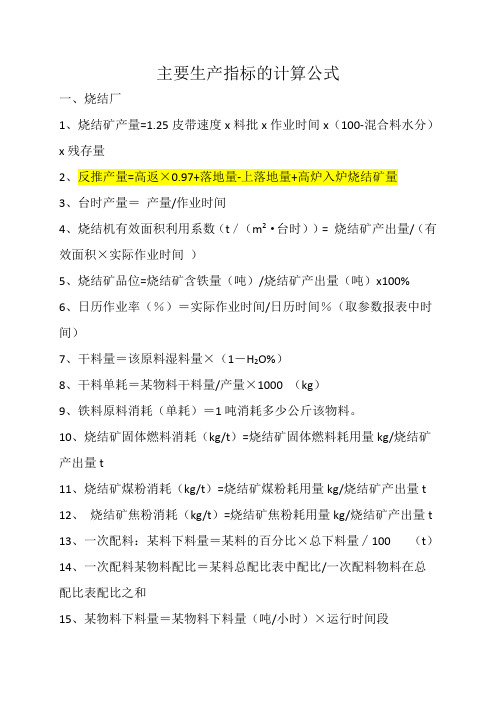
主要生产指标的计算公式一、烧结厂1、烧结矿产量=1.25皮带速度x料批x作业时间x(100-混合料水分)x残存量2、反推产量=高返×0.97+落地量-上落地量+高炉入炉烧结矿量3、台时产量=产量/作业时间4、烧结机有效面积利用系数(t/(m2·台时))= 烧结矿产出量/(有效面积×实际作业时间)5、烧结矿品位=烧结矿含铁量(吨)/烧结矿产出量(吨)x100%6、日历作业率(%)=实际作业时间/日历时间%(取参数报表中时间)7、干料量=该原料湿料量×(1-H2O%)8、干料单耗=某物料干料量/产量×1000 (kg)9、铁料原料消耗(单耗)=1吨消耗多少公斤该物料。
10、烧结矿固体燃料消耗(kg/t)=烧结矿固体燃料耗用量kg/烧结矿产出量t11、烧结矿煤粉消耗(kg/t)=烧结矿煤粉耗用量kg/烧结矿产出量t12、烧结矿焦粉消耗(kg/t)=烧结矿焦粉耗用量kg/烧结矿产出量t13、一次配料:某料下料量=某料的百分比×总下料量∕100 (t)14、一次配料某物料配比=某料总配比表中配比/一次配料物料在总配比表配比之和15、某物料下料量=某物料下料量(吨/小时)×运行时间段16、成品率=产量/(产量+返矿)%(返矿取配料配比变更)17、出矿率=产量/(混合料总量×0.92)%18、返矿率=返矿/(产量+返矿)%二、炼铁厂1、生铁合格率(%)=生铁检验合格量(吨)/生铁检验总量(吨)x100%2、生铁一级品率(%)=一级品生铁总量/合格生铁检验总量x100%3、入炉焦比是反映高炉冶炼每1吨合格生铁所消耗的干焦炭量。
入炉焦比(kg/t)=干焦耗用量kg/合格生铁产量t4、干焦量=湿焦量x(1-湿焦含水%)5、综合焦比是指高炉冶炼每1吨合格生铁所消耗的综合干焦(将各种燃料均折合成干焦计算)量。
综合焦比(kg/t)=综合干焦耗用量kg/合格生铁产量t6、综合干焦量=干焦量+其他各种燃料量x折合干焦系数7、喷煤比是反映高炉冶炼1吨合格生铁所消耗的煤量。
烧结工(中)计算

1、(中级工,计算题,较易,专业知识,辅助要素,标准库)抽取100kg烧结矿做ISO转鼓,经粒级分级,其中<5mm、5-10mm、10-16mm、16-25mm、25-40mm、>40mm的粒级含量分别为8kg、12kg、20kg、23kg、25kg、22kg,那么应该取哪三个粒级分别为多少做转鼓试验?解:应取10-16mm、16-25mm、25-40mm三个粒级共15kg左转鼓试验,10-16mm粒级量=15×[20/(20+23+25)]=4.41(kg)16-25mm粒级量=15×[23/(20+23+25)]=5.07(kg)25-40mm粒级量=15×[25/(20+23+25)]=5.51(kg)答:应取10-16mm、16-25mm、25-40mm三个粒级分别为4.41kg、5.07kg、5.51kg共计15公斤做转鼓试验。
2、(中级工,计算题,中等,无,辅助要素,标准库)假设混合料矿槽的贮料能力为180t,现在矿槽里有料50t,上料量为70kg/s(假设已包括返矿和外配),请问:在烧结机不上料的情况下,问大约多少分钟后大矿槽将溢出?如果烧结机上料,泥辊的下料量为65kg/s(假设小矿槽处于平衡状态),问大约多少分钟后大矿槽将溢出?接b,如果现在需要将大矿槽的贮料量控制在100吨,问在多长时间后需要调整上料量(包括返矿和外配)?上料量需调整到多少才能保持平衡(假设返矿平衡)?解:a:(180-50)×1000÷70=1875秒;1875÷60=31分钟大约31分钟后大矿槽将溢出。
b:(180-50)×1000÷(70-65)=26000秒;26000÷60=433分钟大约433分钟后大矿槽将溢出。
c:(100-50)×1000÷(70-65)=10000秒;10000÷60=167分钟;大约167分钟后需要调整上料量,要保持平衡,上料量需要调整到同烧结机的实际上料量一样大小,即65kg/s。
烧结物料平衡计算4
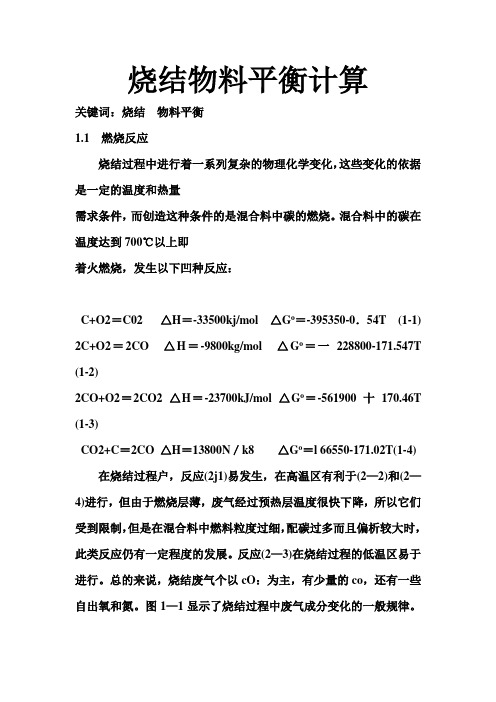
烧结物料平衡计算关键词:烧结物料平衡1.1 燃烧反应烧结过程中进行着一系列复杂的物理化学变化,这些变化的依据是一定的温度和热量需求条件,而创造这种条件的是混合料中碳的燃烧。
混合料中的碳在温度达到700℃以上即着火燃烧,发生以下凹种反应:C+O2=C02 △H=-33500kj/mol △G o=-395350-0.54T (1-1) 2C+O2=2CO △H=-9800kg/mol △G o=一228800-171.547T (1-2)2CO+O2=2CO2 △H=-23700kJ/mol △G o=-561900十170.46T (1-3)CO2+C=2CO △H=13800N/k8 △G o=l 66550-171.02T(1-4) 在烧结过程户,反应(2j1)易发生,在高温区有利于(2—2)和(2—4)进行,但由于燃烧层薄,废气经过预热层温度很快下降,所以它们受到限制,但是在混合料中燃料粒度过细,配碳过多而且偏析较大时,此类反应仍有一定程度的发展。
反应(2—3)在烧结过程的低温区易于进行。
总的来说,烧结废气个以cO:为主,有少量的co,还有一些自出氧和氮。
图1—1显示了烧结过程中废气成分变化的一般规律。
图(1-1)1.2 分解反应烧结过程中有三种分解反应发生:结晶水分解,碳酸盐分解,高价氧化物(Fe zo:,Mno 2.Mn 203)分解。
(1)结晶水分解。
一般固溶体内的水容易在120一200℃就分解出来,以OH—根存在的针铁矿(Fe z03·H:O系y—FeO.OH),针铁矿(Fe 2O3·H 2O系Y—FeO.OH),水锰矿[MnO2·Mn(OH)2系MnO.OH]由于分解过程伴随有品格转变,其开始分解温度要高些约300℃左右。
而脉石中的高岭土(A12O3·2SiO2·2H2O),拜来石[(Fe·AL)2O2·3SiO2·3H 2O]的早格中进入了OH-,它们均需到500℃才开始分解。
烧结原料配比计算公式

烧结原料配比计算公式烧结是一种重要的冶金工艺,通过将粉煤灰、矿石和其他原料混合在一起,然后在高温下加热,使它们结合成块状物,以便在高炉中使用。
在烧结过程中,原料的配比非常重要,它直接影响到烧结矿的质量和性能。
因此,烧结原料配比的计算是烧结工艺中的一个关键步骤。
烧结原料配比的计算公式可以帮助冶金工程师确定不同原料的比例,以便获得最佳的烧结效果。
在实际生产中,烧结原料通常包括铁矿石、焦炭、石灰石和其他添加剂。
这些原料的配比需要根据烧结矿的成分要求、烧结矿的性能要求和工艺条件等因素进行计算。
一般来说,烧结原料的配比计算可以采用以下公式:\[ X_i = \frac{m_i}{M_i} \times 100\% \]其中,\( X_i \) 表示原料 \( i \) 的配比,\( m_i \) 表示原料 \( i \) 的质量,\( M_i \) 表示所有原料的总质量。
在实际应用中,烧结原料的配比计算需要根据具体的原料性质和工艺要求进行调整。
下面以铁矿石、焦炭和石灰石为例,介绍烧结原料配比的计算方法。
1. 铁矿石配比的计算。
铁矿石是烧结原料中的主要成分,其配比计算通常是根据铁含量来进行的。
假设一种铁矿石的铁含量为 \( Fe_2O_3 \),则其配比计算公式为:\[ X_{Fe_2O_3} = \frac{m_{Fe_2O_3}}{M_{Fe_2O_3}} \times 100\% \]其中,\( X_{Fe_2O_3} \) 表示铁矿石的配比,\( m_{Fe_2O_3} \) 表示铁矿石的质量,\( M_{Fe_2O_3} \) 表示所有原料的总质量。
2. 焦炭配比的计算。
焦炭是烧结原料中的还原剂,其配比计算通常是根据固定碳含量来进行的。
假设一种焦炭的固定碳含量为 \( FC \),则其配比计算公式为:\[ X_{FC} = \frac{m_{FC}}{M_{FC}} \times 100\% \]其中,\( X_{FC} \) 表示焦炭的配比,\( m_{FC} \) 表示焦炭的质量,\( M_{FC} \) 表示所有原料的总质量。
烧结计算公式知识分享
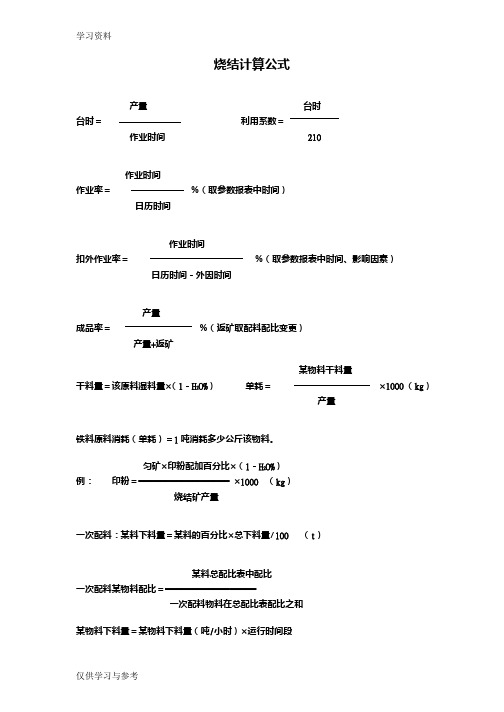
烧结计算公式产量台时台时=利用系数=作业时间 210作业时间作业率=%(取参数报表中时间)日历时间作业时间扣外作业率=%(取参数报表中时间、影响因素)日历时间-外因时间产量成品率=%(返矿取配料配比变更)产量+返矿某物料干料量干料量=该原料湿料量×(1-H2O%)单耗=×1000 (kg)产量铁料原料消耗(单耗)=1吨消耗多少公斤该物料。
匀矿×印粉配加百分比×(1-H2O%)例:印粉=━━━━━━━━━━━━━━━━━×1000 (kg)烧结矿产量一次配料:某料下料量=某料的百分比×总下料量∕100 (t)某料总配比表中配比一次配料某物料配比=━━━━━━━━━━━━━━━━━一次配料物料在总配比表配比之和某物料下料量=某物料下料量(吨/小时)×运行时间段产量返矿出矿率=%返矿率=%混合料总量×0.92 产量+返矿反推产量=高返×0.97+落地量-上落地量+高炉入炉烧结矿量其它计算公式黑料合量公式(FeO×0.777-TFe)×1.43-FeO-SiO2-CaO-MgO=98-99 白料合量公式CaO×1.784+MgO×2.09+SiO2=96-99有效CaO石=CaO石-SiO2石×R基(R烧-R基)×SiO2石∕有效CaO石=需加减灰石量(混合料SiO2总-SiO2石)×R基-(混合料CaO总-CaO石)=R基需要CaO R基需要CaO灰石湿配比=÷(1-H2O%)有效CaO石CaOR=SiO2反推产量=高炉入炉烧结矿+高返×0.97+落地量-上落地量铺底料使用量计算公式:铺底料用量=台车宽度×铺底料厚度×烧结矿堆比重×机速×运行时间例:3.5×0.04×1.7×720×1.05(机速)=180T残存=干料*(1-烧损%)各物料残留成份计算:TFe=干料×TFe%SiO2=干料×SiO2% CaO=干料×CaO%MgO=干料×MgO% Al2O3=干料×Al2O3%烧结矿成份计算:TFe=各物料残留TFe之和×100∕各物料残存之和SiO2=各物料残留SiO2之和×100∕各物料残存之和CaO=各物料残留CaO之和×100∕各物料残存之和MgO=各物料残留MgO之和×100∕各物料残存之和Al2O3=各物料残留Al2O3之和×100∕各物料残存之和。
烧结配料计算第二步

烧结配料计算第二步校准化验成分现场各种物料的化验数据代入烧结矿原料全量公式里进行校准。
各种物料成分带入配比前必须进行化验。
化验后用每种物料的全量公式校验主要成分,校验无误后方可带入配比表进行计算。
校验精度范围:99-100%。
烧结的物料种类:铁料中的澳洲矿粉、巴西矿粉、印度矿粉和国内铁精粉;燃料中的焦粉和白煤;熔剂中的石灰石、生石灰和白云石;辅料中的高炉灰、铁皮、钢渣。
最后讲解返矿。
一、全量公式澳粉全量公式(%):全铁/0.7+二氧化硅+氧化钙+氧化镁+三氧化二铝+化验烧损(结晶水)+1(烧结过程中三氧化二铁转化成氧化亚铁失重)+0.5~1(杂质)=100;巴西粉全量公式(%):全铁/0.7-0.11氧化亚铁+二氧化硅+氧化钙+氧化镁+三氧化二铝+化验烧损(结晶水)+1(烧结过程中三氧化二铁转化成氧化亚铁失重)+0.5~1(杂质)=100;印粉全量公式(%):全铁/0.7+二氧化硅+氧化钙+氧化镁+三氧化二铝+化验烧损(结晶水)+1(烧结过程中三氧化二铁转化成氧化亚铁失重)+1~1.5(杂质)=100;国内铁精粉全量公式(%):全铁/0.7-0.11氧化亚铁+二氧化硅+氧化钙+氧化镁+三氧化二铝+1(烧结过程中三氧化二铁转化成氧化亚铁失重)+0.5(杂质)=100;铁料全量普遍规律:前两项数值之和与结晶水及杂质成反比。
白煤全量公式(%):全铁/0.7+二氧化硅+氧化钙+氧化镁+三氧化二铝+烧损+2(挥发分)+1(结晶水)+1(杂质)=100;焦粉全量公式%:全铁/0.7+二氧化硅+氧化钙+氧化镁+三氧化二铝+烧损+1(挥发分)+0.5(杂质)=100;生石灰全量公式(%):氧化钙+氧化镁+二氧化硅+三氧化二铝+烧损+1(杂质)=100;石灰石全量公式(%):氧化钙+氧化镁+二氧化硅+三氧化二铝+烧损+1~1.5(杂质)=100;白云石全量公式(%):氧化钙+氧化镁+二氧化硅+三氧化二铝+烧损+1~1.5(杂质)=100;高炉重力除尘灰全量公式(%):全铁/0.7-0.11亚铁+固定炭+二氧化硅+氧化钙+氧化镁+三氧化二铝+1(杂质)+0.5(烧结过程中三氧化二铁转化成氧化亚铁失重)=100;高炉布袋除尘灰全量公式(%):全铁/0.7-0.11亚铁+固定碳+二氧化硅+氧化钙+氧化镁+三氧化二铝+1(杂质)+0.5(烧结过程中三氧化二铁转化成氧化亚铁失重)=100;钢渣全量公式(%):全铁/0.7-0.11亚铁+二氧化硅+氧化钙+氧化镁+1(烧结过程中三氧化二铁转化成氧化亚铁失重)+烧损(残炭)+0.5(杂质)=100;氧化铁皮全量公式(%):全铁/0.7-0.11亚铁=100;纯净氧化铁皮,不含杂质和粉尘。
烧结砖抗压强度计算公式

烧结砖抗压强度计算公式烧结砖是咱们建筑领域里常见的材料,它的抗压强度那可是相当重要的指标。
要搞清楚烧结砖抗压强度的计算公式,咱们得先了解一些基础知识。
先来说说啥是抗压强度。
想象一下,你把一块烧结砖放在一个大力士的压机下面,压机不断施加压力,直到这块砖“咔嚓”一声被压坏了。
在砖被压坏之前,它能承受的最大压力,除以砖的受压面积,得到的结果就是抗压强度啦。
那烧结砖抗压强度的计算公式到底是啥呢?一般来说,抗压强度 P等于破坏荷载 F 除以受压面积 A 。
这里面的破坏荷载,就是把砖压坏时的那个最大的力。
我记得有一次去一个建筑材料检测实验室,亲眼看到他们检测烧结砖的抗压强度。
那场面,各种仪器设备,工作人员认真地操作着。
一块小小的烧结砖被放在压机的正中间,大家都紧紧盯着仪器上的数据变化。
当压力不断增加,砖开始出现细微的裂缝时,所有人都屏住了呼吸。
最终,“砰”的一声,砖被压坏了,数据也被准确地记录下来。
咱们再深入聊聊这个公式里的细节。
受压面积 A 可不能随便算,得根据砖的实际尺寸来。
比如说,常见的标准烧结砖,它的尺寸是240mm×115mm×53mm,那受压面积就得看是哪个面在承受压力。
如果是大面受压,那面积就是 240×115 平方毫米;要是条面受压,面积就是 240×53 平方毫米;要是顶面受压,那就是 115×53 平方毫米。
而且啊,在实际检测中,可不是测一块砖就算完事儿了。
为了保证结果的准确性,得测好几块砖,然后把得到的抗压强度值进行统计分析。
比如说,去掉一个最大值和一个最小值,再算剩下的平均值。
另外,烧结砖的质量也会影响抗压强度。
比如说,砖的原料配比、烧制温度和时间等等。
如果原料里杂质太多,或者烧制的时候温度不够、时间太短,那烧出来的砖质量就不咋地,抗压强度自然也高不到哪儿去。
总之,了解烧结砖抗压强度的计算公式,对于保证建筑质量那是至关重要的。
咱们可不能马虎,得认真对待每一块砖,让咱们盖的房子稳稳当当,住得安心!。
烧结矿有效钙的计算公式

烧结矿有效钙的计算公式烧结矿中的有效钙是指在高温下能够与硅酸盐相反应生成熔融物质的可溶钙含量。
有效钙的含量是矿石的一个重要指标,影响着烧结的熔化和渗透性能。
下面我们将介绍烧结矿有效钙的计算公式和一些相关的知识。
烧结矿(sinter)是将铁矿石、焦炭或焦炭代用品以及辅助原料混合在一起,并通过高温下的热反应、燃料氧化反应和烧结反应,制成微球状的矿石块料。
有效钙含量是烧结矿中的一个重要参数,可以通过实验室测试或大型烧结机的数据分析来确定。
烧结矿中主要以铁矿石(Fe2O3)和辅助原料(如石灰石(CaCO3))为主要成分。
有效钙的计算公式通常根据化学成分中的SiO2(硅酸盐)含量来估算。
硅酸盐是常见的硅(Si)和氧(O)化合物,在高温下有较高的反应性。
硅酸盐与石灰石反应生成熔融物质,提供烧结矿的熔融性和渗透性能。
一般来说,烧结矿中的有效钙含量(Cae)可以通过以下公式计算:Cae = 100 - [(%SiO2 × 2.8 + %Al2O3 × 2.4 + %Fe2O3 ×0.8)/(2.8 × %SiO2 + 2.4 × %Al2O3 + %Fe2O3)]其中,%SiO2代表矿石中含有的SiO2的质量比例,%Al2O3代表矿石中含有的Al2O3的质量比例,%Fe2O3代表矿石中含有的Fe2O3的质量比例。
这个公式是通过对矿石中的SiO2、Al2O3和Fe2O3的质量百分比进行加权平均来计算有效钙含量。
不同的矿石成分会影响烧结矿的熔化和渗透性能,因此公式中的系数也是经验性的。
需要注意的是,烧结矿中除了有效钙之外还含有其他形式的钙,如游离钙、死烧融钙、非熔钙等。
有效钙是烧结矿中可溶钙的一个指标,但并不代表烧结矿中全部的钙含量。
因此,在烧结过程中还需要考虑其他形式的钙和矿石的总钙含量。
同时,烧结矿中的有效钙含量也会受到烧结过程中的温度、燃料类型和配比等因素的影响。
烧结计算公式
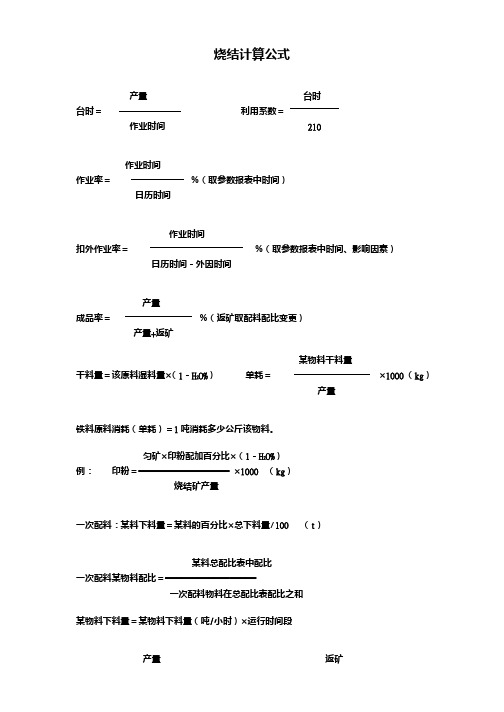
烧结计算公式产量台时台时=利用系数=作业时间 210作业时间作业率=%(取参数报表中时间)日历时间作业时间扣外作业率=%(取参数报表中时间、影响因素)日历时间-外因时间产量成品率=%(返矿取配料配比变更)产量+返矿某物料干料量干料量=该原料湿料量×(1-H2O%)单耗=×1000 (kg)产量铁料原料消耗(单耗)=1吨消耗多少公斤该物料。
匀矿×印粉配加百分比×(1-H2O%)例:印粉=━━━━━━━━━━━━━━━━━×1000 (kg)烧结矿产量一次配料:某料下料量=某料的百分比×总下料量∕100 (t)某料总配比表中配比一次配料某物料配比=━━━━━━━━━━━━━━━━━一次配料物料在总配比表配比之和某物料下料量=某物料下料量(吨/小时)×运行时间段产量返矿出矿率=%返矿率=%混合料总量×0.92 产量+返矿反推产量=高返×0.97+落地量-上落地量+高炉入炉烧结矿量其它计算公式黑料合量公式(FeO×0.777-TFe)×1.43-FeO-SiO2-CaO-MgO=98-99 白料合量公式CaO×1.784+MgO×2.09+SiO2=96-99有效CaO石=CaO石-SiO2石×R基(R烧-R基)×SiO2石∕有效CaO石=需加减灰石量(混合料SiO2总-SiO2石)×R基-(混合料CaO总-CaO石)=R基需要CaOR基需要CaO灰石湿配比=÷(1-H2O%)有效CaO石CaOR=SiO2反推产量=高炉入炉烧结矿+高返×0.97+落地量-上落地量铺底料使用量计算公式:铺底料用量=台车宽度×铺底料厚度×烧结矿堆比重×机速×运行时间例:3.5×0.04×1.7×720×1.05(机速)=180T残存=干料*(1-烧损%)各物料残留成份计算:TFe=干料×TFe%SiO2=干料×SiO2% CaO=干料×CaO%MgO=干料×MgO% Al2O3=干料×Al2O3%烧结矿成份计算:TFe=各物料残留TFe之和×100∕各物料残存之和SiO2=各物料残留SiO2之和×100∕各物料残存之和CaO=各物料残留CaO之和×100∕各物料残存之和MgO=各物料残留MgO之和×100∕各物料残存之和Al2O3=各物料残留Al2O3之和×100∕各物料残存之和。
- 1、下载文档前请自行甄别文档内容的完整性,平台不提供额外的编辑、内容补充、找答案等附加服务。
- 2、"仅部分预览"的文档,不可在线预览部分如存在完整性等问题,可反馈申请退款(可完整预览的文档不适用该条件!)。
- 3、如文档侵犯您的权益,请联系客服反馈,我们会尽快为您处理(人工客服工作时间:9:00-18:30)。
烧结计算公式
产量台时
台时=利用系数=
作业时间 210
作业时间
作业率=%(取参数报表中时间)
日历时间
作业时间
扣外作业率=%(取参数报表中时间、影响因素)
日历时间-外因时间
产量
成品率=%(返矿取配料配比变更)
产量+返矿
某物料干料量
干料量=该原料湿料量×(1-H2O%)单耗=×1000 (kg)
产量
铁料原料消耗(单耗)=1吨消耗多少公斤该物料。
匀矿×印粉配加百分比×(1-H2O%)
例:印粉=━━━━━━━━━━━━━━━━━×1000 (kg)
烧结矿产量
一次配料:某料下料量=某料的百分比×总下料量∕100 (t)
某料总配比表中配比
一次配料某物料配比=━━━━━━━━━━━━━━━━━
一次配料物料在总配比表配比之和
某物料下料量=某物料下料量(吨/小时)×运行时间段
产量返矿
出矿率=%返矿率=%
混合料总量×0.92 产量+返矿
反推产量=高返×0.97+落地量-上落地量+高炉入炉烧结矿量
其它计算公式
黑料合量公式(FeO×0.777-TFe)×1.43-FeO-SiO2-CaO-MgO=98-99 白料合量公式CaO×1.784+MgO×2.09+SiO2=96-99
有效CaO石=CaO石-SiO2石×R基
(R烧-R基)×SiO2石∕有效CaO石=需加减灰石量
(混合料SiO2总-SiO2石)×R基-(混合料CaO总-CaO石)=R基需要CaO
R基需要CaO
灰石湿配比=÷(1-H2O%)
有效CaO石
CaO
R=
SiO2
反推产量=高炉入炉烧结矿+高返×0.97+落地量-上落地量
铺底料使用量计算公式:
铺底料用量=台车宽度×铺底料厚度×烧结矿堆比重×机速×运行时间
例:3.5×0.04×1.7×720×1.05(机速)=180T
残存=干料*(1-烧损%)
各物料残留成份计算:
TFe=干料×TFe%SiO2=干料×SiO2% CaO=干料×CaO%MgO=干料×MgO% Al2O3=干料×Al2O3%
烧结矿成份计算:
TFe=各物料残留TFe之和×100∕各物料残存之和
SiO2=各物料残留SiO2之和×100∕各物料残存之和
CaO=各物料残留CaO之和×100∕各物料残存之和
MgO=各物料残留MgO之和×100∕各物料残存之和
Al2O3=各物料残留Al2O3之和×100∕各物料残存之和。