第一章.熔模铸造ppt课件
合集下载
一铸造ppt课件

浇注温度低流动性差,易产生浇不到或冷隔。浇注温度过高,铸件晶粒粗大, 缩孔增大,易产生缩孔、裂纹和粘砂。
浇注温度由铸造合金`种类、铸件大小及形状确定。 形状复杂、薄壁灰铸铁件,浇注温度1400℃; 形状简单、厚壁灰铸铁件,浇注温度1300℃; 铸钢件浇注温度1500℃。
(2)浇注速度:
速度高流动性好,易冲砂;速度低,易于补缩,但易产生冷隔、夹砂、砂眼。 浇注速度由铸件大小、形状确定。
除了以上性能的要求外,还有溃散性、发气性、吸湿性等的性能要求。 • 型、芯砂的诸多性能,有时是相互矛盾的,如强度高、塑性好,透气性
就可能下降,因此应根据铸造合金的种类,铸件大小、批量、结构等, 具体决定型、芯砂的配比。 型砂种类:
面砂 填充砂 单一砂 型芯砂
型(芯)砂的制备过程 • 烘干---筛分---混砂(先干混后湿混)---松砂---停放(闷砂)。
1.1 砂型铸造
三、造型和制芯
(一)造型方法 手工造型和机器造型
1 手工造型:全部用手工或手动工具完成的造型工序。 (1)、整模造型的模样是整体的,分型面是平面,铸型型腔全部在
半个铸型内,其造型简单,铸件不会产生错型缺陷。适用于铸件最大截面 在一端,且为平面的铸件。
1.1 砂型铸造
(2)、分模造型是将模样沿最大截面处分成两半,型腔位于上、下两
个砂箱内,造型简单省工。常用于最大截面在中部的铸件。
1.1 砂型铸造
(4)、活块造型是在制模时将铸件上的妨碍起模的小凸台,肋条等这些 部分作成活动的(即活块)。起模时,先起出主体模样,然后再从侧面取出 活块。其造型费时,工人技术水平要求高。主要用于单件、小批生产带有突 出部分、难以起模的铸件。
1.1 砂型铸造
芯撑
(6)、铸件结构设计应考虑的其它问题
浇注温度由铸造合金`种类、铸件大小及形状确定。 形状复杂、薄壁灰铸铁件,浇注温度1400℃; 形状简单、厚壁灰铸铁件,浇注温度1300℃; 铸钢件浇注温度1500℃。
(2)浇注速度:
速度高流动性好,易冲砂;速度低,易于补缩,但易产生冷隔、夹砂、砂眼。 浇注速度由铸件大小、形状确定。
除了以上性能的要求外,还有溃散性、发气性、吸湿性等的性能要求。 • 型、芯砂的诸多性能,有时是相互矛盾的,如强度高、塑性好,透气性
就可能下降,因此应根据铸造合金的种类,铸件大小、批量、结构等, 具体决定型、芯砂的配比。 型砂种类:
面砂 填充砂 单一砂 型芯砂
型(芯)砂的制备过程 • 烘干---筛分---混砂(先干混后湿混)---松砂---停放(闷砂)。
1.1 砂型铸造
三、造型和制芯
(一)造型方法 手工造型和机器造型
1 手工造型:全部用手工或手动工具完成的造型工序。 (1)、整模造型的模样是整体的,分型面是平面,铸型型腔全部在
半个铸型内,其造型简单,铸件不会产生错型缺陷。适用于铸件最大截面 在一端,且为平面的铸件。
1.1 砂型铸造
(2)、分模造型是将模样沿最大截面处分成两半,型腔位于上、下两
个砂箱内,造型简单省工。常用于最大截面在中部的铸件。
1.1 砂型铸造
(4)、活块造型是在制模时将铸件上的妨碍起模的小凸台,肋条等这些 部分作成活动的(即活块)。起模时,先起出主体模样,然后再从侧面取出 活块。其造型费时,工人技术水平要求高。主要用于单件、小批生产带有突 出部分、难以起模的铸件。
1.1 砂型铸造
芯撑
(6)、铸件结构设计应考虑的其它问题
特种铸造技术介绍PPT
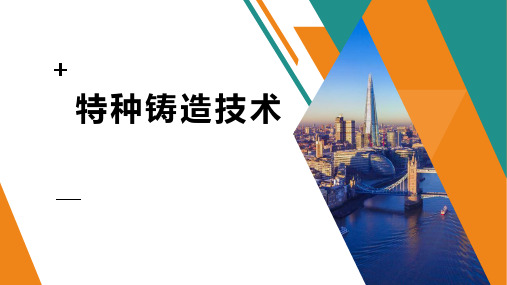
▆ 应用范围
(1)适用于生产形状复杂、精度要求高或难以切削加工成形的各种金属材料(尤其是碳钢及合金 钢)小型零件。如汽轮机、涡轮机的叶片或叶轮,汽车、拖拉机或机床用的各种小件。
2.压力铸造
█ 定义:是指将液态或半液态合金浇入压铸机的压室中,使之在高压和高速 下充填型腔,并在高压下成形结晶而获得铸件的一种铸造方法。常用压射压力 为5-70MPa,压射速度0.5-5m/s,充填时间很短,约0.01-02s。
6、适于有色金属薄壁复杂铸件的大批量生产。
3.低压铸造
█ 定义:是指液态金属在低的气体压力作用下从坩埚中自下而上地充填型腔 并凝固而获得铸件的一种铸造方法。常用压力为0.02~0.06MPa,介于重力和 压力铸造之间。
➢ 工艺过程:
3.低压铸造
3.低压铸造
特点和应用:
1、液态金属自下而上平稳的充填型腔, 型腔中的液流的方向与气体排出的方向一 致,避免了液态金属对型壁、型芯的冲刷 以及气体和氧化物,从而防止了铸件产生 气孔和非金属夹杂物;
3.应用范围
离心铸造是生产管套类铸件的主要方法,广泛应用于生产铸铁水管、缸套、轴套等。
各种铸造方法与砂型铸造加工精度对比:
结束
1.熔模铸造
◆◆ 熔模精密铸造:是指利用易熔材料制成模样,并在模样表面粘结一定厚度的耐火材料,然
后将模样熔化而使金属液充满型腔的一种铸造方法。(也称失蜡铸造)
熔 模 铸 造 工 艺 过 程
1.熔模铸造(1)熔模铸源自的工艺过程① 制作压型 压型根据铸件图制作,压型是压制蜡模的中间铸型。对高精度或大批量生产的铸件,常用机 械加工制成的钢或铝合金压型;对精度要求不高或生产批量不大的铸件常用低熔点合金(锡、铅、 铋)直接浇注的压型;对单件小批量的铸件可用石膏或塑料制作的压型。 ② 制作蜡模 将低熔点熔融态蜡料(常用50%的石蜡+50%的硬脂酸)压入压型中,冷凝后取出,得到单个蜡 模。将若干拉模粘到预制的蜡质浇口棒上,成为蜡模组。 ③ 制作壳型 将蜡模组浸入石英粉与水玻璃配成的浆料中,取出后在其表面撒上一层细石英砂,再浸入氯 化铵的溶液中硬化。如此由细到粗反复涂挂4-5次,指导表面结成5-10mm厚的硬壳后,放入8590℃的热水中,熔去蜡模而得到型腔与蜡模组一致的壳型。
(1)适用于生产形状复杂、精度要求高或难以切削加工成形的各种金属材料(尤其是碳钢及合金 钢)小型零件。如汽轮机、涡轮机的叶片或叶轮,汽车、拖拉机或机床用的各种小件。
2.压力铸造
█ 定义:是指将液态或半液态合金浇入压铸机的压室中,使之在高压和高速 下充填型腔,并在高压下成形结晶而获得铸件的一种铸造方法。常用压射压力 为5-70MPa,压射速度0.5-5m/s,充填时间很短,约0.01-02s。
6、适于有色金属薄壁复杂铸件的大批量生产。
3.低压铸造
█ 定义:是指液态金属在低的气体压力作用下从坩埚中自下而上地充填型腔 并凝固而获得铸件的一种铸造方法。常用压力为0.02~0.06MPa,介于重力和 压力铸造之间。
➢ 工艺过程:
3.低压铸造
3.低压铸造
特点和应用:
1、液态金属自下而上平稳的充填型腔, 型腔中的液流的方向与气体排出的方向一 致,避免了液态金属对型壁、型芯的冲刷 以及气体和氧化物,从而防止了铸件产生 气孔和非金属夹杂物;
3.应用范围
离心铸造是生产管套类铸件的主要方法,广泛应用于生产铸铁水管、缸套、轴套等。
各种铸造方法与砂型铸造加工精度对比:
结束
1.熔模铸造
◆◆ 熔模精密铸造:是指利用易熔材料制成模样,并在模样表面粘结一定厚度的耐火材料,然
后将模样熔化而使金属液充满型腔的一种铸造方法。(也称失蜡铸造)
熔 模 铸 造 工 艺 过 程
1.熔模铸造(1)熔模铸源自的工艺过程① 制作压型 压型根据铸件图制作,压型是压制蜡模的中间铸型。对高精度或大批量生产的铸件,常用机 械加工制成的钢或铝合金压型;对精度要求不高或生产批量不大的铸件常用低熔点合金(锡、铅、 铋)直接浇注的压型;对单件小批量的铸件可用石膏或塑料制作的压型。 ② 制作蜡模 将低熔点熔融态蜡料(常用50%的石蜡+50%的硬脂酸)压入压型中,冷凝后取出,得到单个蜡 模。将若干拉模粘到预制的蜡质浇口棒上,成为蜡模组。 ③ 制作壳型 将蜡模组浸入石英粉与水玻璃配成的浆料中,取出后在其表面撒上一层细石英砂,再浸入氯 化铵的溶液中硬化。如此由细到粗反复涂挂4-5次,指导表面结成5-10mm厚的硬壳后,放入8590℃的热水中,熔去蜡模而得到型腔与蜡模组一致的壳型。
《熔模精密铸造技术》课件
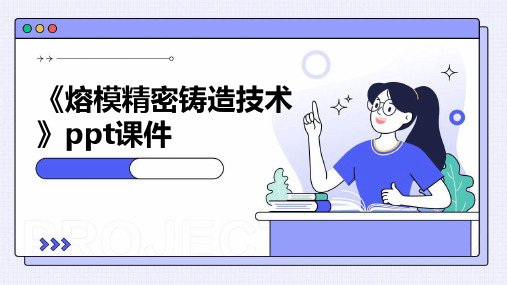
弃物的产生,有利于环保。
缺点
成本高
熔模精密铸造技术需要高昂的设备和工艺成 本,生产成本较高。
对操作人员要求高
熔模精密铸造技术需要经验丰富的操作人员 和技术人员,对工人的技能要求较高。
生产周期长
熔模精密铸造技术的生产周期较长,需要经 过多个工序和复杂的工艺流程。
不适合大规模生产
由于其高昂的成本和复杂的工艺流程,熔模 精密铸造技术不适合大规模生产。
03 熔模精密铸造技术的工艺 流程
模具设计
01
模具设计是熔模精密铸造技术 的第一步,需要综合考虑产品 结构、工艺要求、材料特性等 因素。
02
设计过程中,需要使用CAD等 计算机辅助设计软件进行建模 和模拟,以提高模具设计的准 确性和效率。
03
模具设计应注重细节处理,如 模具的浇口、排气口、冷却水 道等,以确保铸造过程的顺利 进行。
其他领域应用
能源领域
熔模精密铸造技术可用于制造燃气轮机叶片、核反应堆结构件等,提高能源转换效率和安全性。
医疗器械领域
熔模精密铸造技术可以生产高精度、高质量的医疗器械,如人工关节、牙科植入物等,提高医疗效果和使用寿命 。
感谢您的观看
THANKS
模具设计
根据铸件的结构和尺寸, 进行模具设计,确保模具 的精度和稳定性。
模具制作工艺
采用合适的工艺方法制作 模具,如雕刻、3D打印等 ,确保模具的表面质量和 尺寸精度。
金属充型
金属液制备
将熔融的金属液通过浇注系统送入模具型腔 。
充型速度与方向
控制金属液的充型速度和方向,以保证金属液能够 均匀填充型腔,避免气孔、夹渣等缺陷的产生。
特点
高精度、高效率、低成本、适用 范围广,可铸造复杂形状和薄壁 零件,广泛应用于航空、汽车、 船舶、能源等领域。
缺点
成本高
熔模精密铸造技术需要高昂的设备和工艺成 本,生产成本较高。
对操作人员要求高
熔模精密铸造技术需要经验丰富的操作人员 和技术人员,对工人的技能要求较高。
生产周期长
熔模精密铸造技术的生产周期较长,需要经 过多个工序和复杂的工艺流程。
不适合大规模生产
由于其高昂的成本和复杂的工艺流程,熔模 精密铸造技术不适合大规模生产。
03 熔模精密铸造技术的工艺 流程
模具设计
01
模具设计是熔模精密铸造技术 的第一步,需要综合考虑产品 结构、工艺要求、材料特性等 因素。
02
设计过程中,需要使用CAD等 计算机辅助设计软件进行建模 和模拟,以提高模具设计的准 确性和效率。
03
模具设计应注重细节处理,如 模具的浇口、排气口、冷却水 道等,以确保铸造过程的顺利 进行。
其他领域应用
能源领域
熔模精密铸造技术可用于制造燃气轮机叶片、核反应堆结构件等,提高能源转换效率和安全性。
医疗器械领域
熔模精密铸造技术可以生产高精度、高质量的医疗器械,如人工关节、牙科植入物等,提高医疗效果和使用寿命 。
感谢您的观看
THANKS
模具设计
根据铸件的结构和尺寸, 进行模具设计,确保模具 的精度和稳定性。
模具制作工艺
采用合适的工艺方法制作 模具,如雕刻、3D打印等 ,确保模具的表面质量和 尺寸精度。
金属充型
金属液制备
将熔融的金属液通过浇注系统送入模具型腔 。
充型速度与方向
控制金属液的充型速度和方向,以保证金属液能够 均匀填充型腔,避免气孔、夹渣等缺陷的产生。
特点
高精度、高效率、低成本、适用 范围广,可铸造复杂形状和薄壁 零件,广泛应用于航空、汽车、 船舶、能源等领域。
毛坯的制造方法ppt课件

芯棒拔长是减小空心坯料的壁厚.增加其长度的锻造工序。
拔长用来生产轴杆类锻件或长筒类锻件。
27
(3)冲孔 冲孔是在坯料上冲出透孔或不透孔的锻造工序。 冲孔前一般需将坯料镦粗,以减小冲孔高度。 较薄的坯料可单面冲孔,较厚的坏料需双面冲孔。
28
2、模锻 模锻是利用模具使坯料变形而获得锻件的锻造方法。 模锻的特点: ①模锻与自由锻相比,具有生产率高、锻件外形复杂、尺寸精度高、面 粗糙度值小,加工余量小等优点;
砂型的冲击,阻挡熔渣流入型腔。
直浇道:直浇道以其高度产生的静压力使金属液充满型腔的各个部分。 横浇道:横浇道将金属液分配给各个内浇道,并起阻渣作用。 内浇道:控制金属液流入型腔的方向和速度。 冒口:对铸件的最后凝固部位供给金属液,起补缩作用。
18
三、其他铸造方法简介
1、熔模铸造 熔模铸造是利用易熔材料(如蜡料)制成模样,在模样上包覆若干层耐 火涂料,然后制成硬壳,熔去模样后,经高温焙烧即可浇注的铸造方法。
13
③尽量使铸件的全部或大部分处于同一砂箱中,以保证铸件的精度。 ④应考虑下芯、检验和合箱的方便。
上 下
上 下
14
2、主要铸造工艺参数
1)加工余量
为了保证铸件加工面尺寸和零件精度,在铸造工艺设计时应增加在机 械加工时切除的金属层厚度,它等于后续所有加工工序的加工余量之和。
加工余量过大,将增加金属的消耗和切削加工工时;加工余量过小,可能
造成零件报废。 对于某个具体零件,凡图纸上标注有表面粗糙度符号、尺寸公差、螺 纹符号或表面形位公差代号的部位,都应给出加工余量。 零件上的孔、槽是否要铸出,应考虑工艺上的可行性和使用上的必要 性。通常较大的孔和槽应铸出,以节省金属材料和切削加工工时;较小的 孔、槽不必铸出,留待机械加工反而更为经济。
精密铸造工艺-熔模铸造
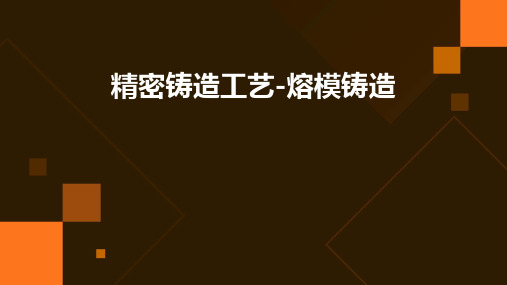
有利于金属液的充型和补缩,减少气 孔等缺陷的产生。
一定的强度
在搬运和组装过程中不易损坏。
易于脱壳
在铸件冷却后能够顺利脱去壳型,不 损伤铸件表面。
合金选择与性能要求
符合产品使用要求
良好的铸造性能
根据产品的使用环境和性能要求选择合适 的合金种类和牌号。
合金应具有较低的熔点和良好的流动性, 以便于充型和补缩。
安全操作规程及培训要求
制定安全操作规程
明确各工序的安全操作要求和注 意事项,确保操作人员严格遵守
。
应急预案与演练
对新员工和转岗员工进行安全培 训,提高员工的安全意识和操作
技能。
安全培训与教育
对涉及特种作业的员工,如电工 、焊工等,必须持证上岗,确保 操作安全。
特种作业人员持证上岗
制定针对熔模铸造过程中可能出现 的紧急情况的应急预案,并定期进 行演练,提高员工的应急处置能力。
加强人才培养
加强人才培养和引进,培养一支高素质、专业化的熔模铸造技术人才队伍,推动行业的技 术进步和可持续发展。例如,建立完善的人才培养和激励机制,吸引和留住优秀人才。
感谢您的观看
THANKS
蜡料选择与性能要求
低熔点和高流动性
确保蜡料在注射时能够充分填充模具,形成 精确的蜡模。
易于脱模
与模具材料之间有良好的分离性,降低脱模 难度。
稳定性好
在存放和使用过程中不易变质或产生缺陷。
对环境友好
无毒无害,符合环保要求。
壳型材料及其性能要求
高耐火度
能够承受高温金属液的冲刷而不破裂 或变形。
良好的透气性
较高的力学性能
良好的耐蚀性和耐磨性
合金应具有足够的强度、硬度和韧性等力 学性能,以满足产品的使用要求。
一定的强度
在搬运和组装过程中不易损坏。
易于脱壳
在铸件冷却后能够顺利脱去壳型,不 损伤铸件表面。
合金选择与性能要求
符合产品使用要求
良好的铸造性能
根据产品的使用环境和性能要求选择合适 的合金种类和牌号。
合金应具有较低的熔点和良好的流动性, 以便于充型和补缩。
安全操作规程及培训要求
制定安全操作规程
明确各工序的安全操作要求和注 意事项,确保操作人员严格遵守
。
应急预案与演练
对新员工和转岗员工进行安全培 训,提高员工的安全意识和操作
技能。
安全培训与教育
对涉及特种作业的员工,如电工 、焊工等,必须持证上岗,确保 操作安全。
特种作业人员持证上岗
制定针对熔模铸造过程中可能出现 的紧急情况的应急预案,并定期进 行演练,提高员工的应急处置能力。
加强人才培养
加强人才培养和引进,培养一支高素质、专业化的熔模铸造技术人才队伍,推动行业的技 术进步和可持续发展。例如,建立完善的人才培养和激励机制,吸引和留住优秀人才。
感谢您的观看
THANKS
蜡料选择与性能要求
低熔点和高流动性
确保蜡料在注射时能够充分填充模具,形成 精确的蜡模。
易于脱模
与模具材料之间有良好的分离性,降低脱模 难度。
稳定性好
在存放和使用过程中不易变质或产生缺陷。
对环境友好
无毒无害,符合环保要求。
壳型材料及其性能要求
高耐火度
能够承受高温金属液的冲刷而不破裂 或变形。
良好的透气性
较高的力学性能
良好的耐蚀性和耐磨性
合金应具有足够的强度、硬度和韧性等力 学性能,以满足产品的使用要求。
熔模精密铸造技术课件

铸件外炮火
特征:金属穿透型壳,在铸件表面上形成 不规则的多余金属。 原因:型壳强度低、压头太高、浇注工艺 不当、型壳局部损伤。
铸件内腔炮火
特征:在铸件的深孔或凹槽处有不规则的 多余金属。 原因:铸件结构不合理、制壳工艺不合理 或操作不当、型壳局部硬化风干不良。
铸件化学粘砂
特征:铸件表面粘附着一层难以清除的化 合物。 原因:型壳材料选用不当、浇注条件不当、 局部散热条件差、结构不合理。
特征:铸件局部Biblioteka 起 原因:①型壳抗高温变形能力低,②压头 太高,浇注温度太高。
铸件夹砂结疤与凹陷
特征:铸件表面有翘起的金属片,并夹有 型壳材料,有的铸件是不规则凹陷。 原因:①铸件结构不合理,有大平面,② 型壳在脱蜡或焙烧过程中向内鼓胀,③由 于型壳分层,在焙烧和浇注过程中,其内 表面局部破裂翘起,金属液钻进裂缝,形 成结疤。
镶宝石 “戒指树”
熔模铸造工艺特点之一
①、熔模铸件的尺寸精度高,表面粗糙度小
由于熔模铸造采用了尺寸精确、表面光滑 的可溶性模,而获得了几乎无分型面的整体型 壳,且无一般铸造方法中的起模、下芯、和型 等工序所带来的尺寸误差。熔模铸件的棱角清 晰、尺寸精度可达到0.005cm/cm,表面粗糙度 可达Ra1.25um。因此采用熔模铸件可大量减少 金属切削加工工作量或实现无余量铸造。
高尔夫球杆头 钛合金熔模铸件,空心杆头壁厚可达0.9mm
汽轮机叶片:
汽轮机四级导流器扇 段,尺寸为 609.6mm X 584.2rnm, 重量63kg
激光器底座
用铝合金 整体熔模铸 件代替原用 锻造合金经 机加工等工 序制成的激 光器底座, 使每个零件 成本节约 25000美元
电子课件——机械制造工艺基础(第七版) 1第一章 铸造

第一章 铸造
1 §1—1 概述 2 §1—2 砂型铸造 3 §1—3 特种铸造及铸造新技术
第一章 铸造
§1—1 铸造基础
一、 铸造及其分类
将熔融金属浇注、压射或吸入铸型型 腔中,凝固后获得具有一定形状、尺寸 和性能的毛坯或零件
砂型铸造
铸 造
特种铸造
熔模铸造 金属型铸造 压力铸造 离心铸造
§第1一—章1 铸铸造造基础
整模两箱造型
§第1—一2章 砂型铸铸造造
模样分成两 部分,分别 制造上型和 下型,型腔 则位于上型 和下型之间
分模两箱造型
§第1—一2章 砂型铸铸造造
2)脱箱造型 在可脱砂箱内造型,合型后浇注前脱去砂箱
§第1—一2章 砂型铸铸造造
3)挖沙造型 下型分型面挖成不平分型面(曲面、非平面)
§第1—一2章 砂型铸铸造造
气动微振压实造型机紧砂
§第1—一2章 砂型铸铸造造
3.造芯
制造型芯的过程称为造芯
手工造芯 机器造芯
芯盒造芯
§第1—一2章 砂型铸铸造造
4.合型
又称合箱,是将铸型的各个组元 组合成一个完整铸型的操作过程
5.熔炼
熔炼是使金属由固态转变为熔融状态的过程
§第1—一2章 砂型铸铸造造
6.浇注
(1)浇注工具
4.铸造圆角
相邻两表面的过渡圆角
§第1—一2章 砂型铸铸造造
5.芯头
在模样上:芯头是模样的凸出部分 在型芯上:芯头是型芯的外伸部分
§第1—一2章 砂型铸铸造造
6.浇注系统
(1)外浇口 (2)直浇道 (3)横浇道 (4)内浇道
7.冒口
§第1—一2章 砂型铸铸造造
三、砂型铸造的工艺过程
1.混砂
1 §1—1 概述 2 §1—2 砂型铸造 3 §1—3 特种铸造及铸造新技术
第一章 铸造
§1—1 铸造基础
一、 铸造及其分类
将熔融金属浇注、压射或吸入铸型型 腔中,凝固后获得具有一定形状、尺寸 和性能的毛坯或零件
砂型铸造
铸 造
特种铸造
熔模铸造 金属型铸造 压力铸造 离心铸造
§第1一—章1 铸铸造造基础
整模两箱造型
§第1—一2章 砂型铸铸造造
模样分成两 部分,分别 制造上型和 下型,型腔 则位于上型 和下型之间
分模两箱造型
§第1—一2章 砂型铸铸造造
2)脱箱造型 在可脱砂箱内造型,合型后浇注前脱去砂箱
§第1—一2章 砂型铸铸造造
3)挖沙造型 下型分型面挖成不平分型面(曲面、非平面)
§第1—一2章 砂型铸铸造造
气动微振压实造型机紧砂
§第1—一2章 砂型铸铸造造
3.造芯
制造型芯的过程称为造芯
手工造芯 机器造芯
芯盒造芯
§第1—一2章 砂型铸铸造造
4.合型
又称合箱,是将铸型的各个组元 组合成一个完整铸型的操作过程
5.熔炼
熔炼是使金属由固态转变为熔融状态的过程
§第1—一2章 砂型铸铸造造
6.浇注
(1)浇注工具
4.铸造圆角
相邻两表面的过渡圆角
§第1—一2章 砂型铸铸造造
5.芯头
在模样上:芯头是模样的凸出部分 在型芯上:芯头是型芯的外伸部分
§第1—一2章 砂型铸铸造造
6.浇注系统
(1)外浇口 (2)直浇道 (3)横浇道 (4)内浇道
7.冒口
§第1—一2章 砂型铸铸造造
三、砂型铸造的工艺过程
1.混砂
机械制造工艺基础课件第一章铸造

2.制造模样与芯盒的注意要点
(1)分型面——铸型组元间的接合面。
1—上型
2—分型面 3—型芯
4—支座型腔
5—芯头 6—下型
第十七页,共五十八页,2022年,8月28日
(2)收缩余量——为了补偿铸件收缩,模样比铸件图样尺 寸增大的数值。
(3)加工余量——为保证铸件加工面尺寸和零件精度, 在铸造工艺设计时预先增加而在机械加工时切去的金属层厚 度。
第十八页,共五十八页,2022年,8月28日
(4)起模斜度——为使模样容易从铸型中取出或型芯从芯盒
中脱出,在模样或芯盒上平行于起模方向所设的斜度。
一般α=0.5 ° ~3°
第十九页,共五十八页,2022年,8月28日
(5)铸造圆角——制造模样时,凡相邻两表面的交角,都 应做成圆角。
铸造圆角(r为铸造圆角半径)
第四十五页,共五十八页,2022年,8月28日
握包
抬包
吊包
第四十六页,共五十八页,2022年,8月28日
2.浇注温度与浇注速度
浇注温度(℃)——金属熔液浇入铸型时所测量到的温度 。
浇注速度(kg/s)——单位时间内浇入铸型中的金属熔液质量
。
第四十七页,共五十八页,2022年,8月28日
二、落砂和清理
四、 造芯 五、浇注系统及冒口 六、合型
第十页,共五十八页,2022年,8月28日
一、砂型和造型材料
1. 造型材料 2. 型砂和芯砂 3. 砂型
第十一页,共五十八页,2022年,8月28日
1.造型材料
造型材料——制造砂型和砂芯的材料。 1砂 2 黏土
3 黏结剂 4 附加物
第十二页,共五十八页,2022年,8月28日
第八页,共五十八页,2022年,8月28日
熔模精密铸造技术PPT课件

.
11
2.3 制壳工艺流程
厚德博学 追求卓越
制壳工艺流程图
(1)模组除油和脱脂 为了改善模组与面层涂料的涂挂性能, 除了在面层涂料中加入表面活性剂外,通常是在模组涂挂涂料前 ,对模组进行除油和脱脂处理,以增加涂料对模样的润湿性。
(2)涂挂涂料和撒砂 涂挂涂料和撒砂工序相隔进行(一层涂料 、一层散砂),涂挂和撒砂层数根据铸件的大小和形状而不同,面 层和背层的涂料和砂类不同。
一.熔模精密铸造的发展历史
1.熔模铸造又称为失蜡铸造,熔模铸造的历史可以追溯到4000年 以前,最早起源于埃及、中国和印度,在我国的出土文物中发现 在公元前2500年以前,我们的祖先就能用熔模铸造的方式生产 各种铜器皿、钟鼎及艺术品。
.
3
厚德博学 追求卓越
2.现代熔模铸造工艺是在20世纪初期开始形成,最初用于制牙及 珠宝饰业。第二次世界大战期间, 由于国防、航空工业发展的 需要,英、美等国首先采用熔模精密铸造方法,生产喷气涡轮发 动机叶片等形状复杂、尺寸精确、表面质量要求很高且不易机械 加工的铸件。
.
21
厚德博学 追求卓越
圆盘零件: 陶瓷增强铝基.复合材料的熔模铸件
22
厚德博学 追求卓越
.
23
厚德博学 追求卓越
五.熔模精密铸造工艺发展趋势
1、更大更薄:目前,熔模铸造生产的精密铸件,最大 轮廓尺寸可 达1.8m,而最小壁厚却不到2mm,最大铸件重量接近1000kg。
2、精度更高:熔模铸件尺寸公差是CT4-6级,表面粗糙度值可达 到Ra0.8um。
3、强度更高:如飞机发动机用的涡轮叶片工作温度由980℃提高到 1200℃;热等静压技术的应用使得熔模铸造生产的镍基高温合金、钛合 金和铝合金的高温低周 波疲劳性能提高3~10倍。
熔模铸造工艺PPT课件

B、劣势
铸件尺寸不能太大:铸件重量最大可做到1000Kg, 超出重量铸件难度较大; 工艺过程复杂,生产周期长:影响铸件质量因素太 多,工序质量控制难度增大; 铸件冷却速度较慢:导致铸件晶粒粗大,碳钢件易 脱碳。
篮球比赛是根据运动队在规定的比赛 时间里 得分多 少来决 定胜负 的,因 此,篮 球比赛 的计时 计分系 统是一 种得分 类型的 系统
四、熔模铸造应用范围
从产品类别来看,熔模精密铸件主要分为两大 类:军工、航空类产品与商品类产品。前者质量 要求高,后者质量不如前者。随着冷战时代的结 束,各国军工产品大幅度减少,但民航、大型电 站及工业涡轮发动机的发展,使得军工、航空类 产品所占比例变化不大。现在熔模铸造除用于航 空、军工部门外,几乎应用于所有工业部门,如 电子、石油、化工、能源、交通运输、轻功、纺 织、制药、医疗器械等领域。
检验方法
化学分析 光谱分析
拉伸试验 硬度测试 冲击试验 疲劳试验
放大镜或低倍显微镜 工业CT
光学显微镜 电子显微镜
篮球比赛是根据运动队在规定的比赛 时间里 得分多 少来决 定胜负 的,因 此,篮 球比赛 的计时 计分系 统是一 种得分 类型的 系统
C、其它要求
检验内容
检验项目
物理化学性能或 特殊要求
抛丸清理 喷砂清理 化学清砂 电化学清砂 风动磨头磨光
风动异形旋转锉切 削
篮球比赛是根据运动队在规定的比赛 时间里 得分多 少来决 定胜负 的,因 此,篮 球比赛 的计时 计分系 统是一 种得分 类型的 系统
3.3.9、铸件热处理
A、铸钢件热处理
工艺 退火 正火 淬火 回火 固溶处理
规范 Ac3+20-30℃,炉冷 Ac3+30-50℃,空冷 Ac3+20-30℃,快冷(水、油) Ac1以下,空冷或炉冷 Ac3以上较高温度,快冷
铸件尺寸不能太大:铸件重量最大可做到1000Kg, 超出重量铸件难度较大; 工艺过程复杂,生产周期长:影响铸件质量因素太 多,工序质量控制难度增大; 铸件冷却速度较慢:导致铸件晶粒粗大,碳钢件易 脱碳。
篮球比赛是根据运动队在规定的比赛 时间里 得分多 少来决 定胜负 的,因 此,篮 球比赛 的计时 计分系 统是一 种得分 类型的 系统
四、熔模铸造应用范围
从产品类别来看,熔模精密铸件主要分为两大 类:军工、航空类产品与商品类产品。前者质量 要求高,后者质量不如前者。随着冷战时代的结 束,各国军工产品大幅度减少,但民航、大型电 站及工业涡轮发动机的发展,使得军工、航空类 产品所占比例变化不大。现在熔模铸造除用于航 空、军工部门外,几乎应用于所有工业部门,如 电子、石油、化工、能源、交通运输、轻功、纺 织、制药、医疗器械等领域。
检验方法
化学分析 光谱分析
拉伸试验 硬度测试 冲击试验 疲劳试验
放大镜或低倍显微镜 工业CT
光学显微镜 电子显微镜
篮球比赛是根据运动队在规定的比赛 时间里 得分多 少来决 定胜负 的,因 此,篮 球比赛 的计时 计分系 统是一 种得分 类型的 系统
C、其它要求
检验内容
检验项目
物理化学性能或 特殊要求
抛丸清理 喷砂清理 化学清砂 电化学清砂 风动磨头磨光
风动异形旋转锉切 削
篮球比赛是根据运动队在规定的比赛 时间里 得分多 少来决 定胜负 的,因 此,篮 球比赛 的计时 计分系 统是一 种得分 类型的 系统
3.3.9、铸件热处理
A、铸钢件热处理
工艺 退火 正火 淬火 回火 固溶处理
规范 Ac3+20-30℃,炉冷 Ac3+30-50℃,空冷 Ac3+20-30℃,快冷(水、油) Ac1以下,空冷或炉冷 Ac3以上较高温度,快冷
第一章.熔模铸造
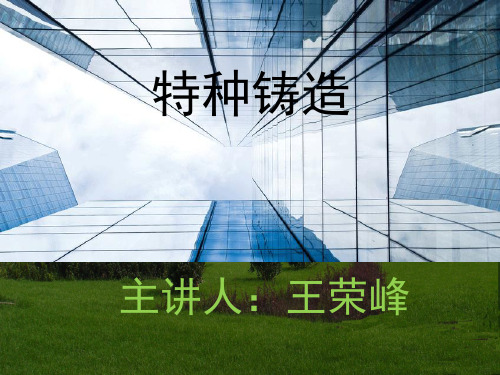
目前常用的铝硅系耐火材料有以下几种: 1)粘土质耐火材料 是指Al2O3的质量分数约30%一46%,矿物组成以 高岭石为主的耐火粘土,其分子式为 Al2O3·2SiO2·2H2O。分为生料(软质粘土) 和熟 料(硬质粘土),主要用于加固层涂料。
2)铝矾土( Al2O3含量在45~80% )
高岭石及含水氧化铝(水铝石αAl2O3·H2O、波 美石γAl2O3·H2O,三水铝石Al2O3·3H2O等)。 3)莫来石质耐火材料( Al2O3含量在67~72% ) Al2O3含量在67~72% 。
1、对粘结剂性能的要求 应能将粉状和粒状耐火材料牢固地粘结在一起。使 型壳具有足够高的强度; 应具有良好的耐热性,以保证型壳在高温焙烧、浇 注以及铸件凝固过程中具有足够的高温强度, 粘结剂最终生成的耐高温氧化物,在高温下应具有 良好的化学稳定性。 应能很好润湿熔模,与模料不起化学反应,保证准 确复制出熔模轮廓,使型壳内表面光滑; 具有适当的粘度,保证制壳过程中有良好的涂挂性 和渗透性。
α鳞石英应在1470℃时转变为α方石英,但若快 速加热,α鳞石英将过热而在1670℃熔化为熔体 (DD‘)。
正常条件下,α鳞石英不变为α石英。 在高低温转变中,方石英之间的体积变化最为剧烈, 其次是石英,鳞石英变化最微弱。 熔体(熔融石英)经急冷后得到石英玻璃。
(2)熔模铸造用硅砂牌号:
硅砂适用于碳钢、低合金钢、铸铁及铜合余铸件 不适用于高锰钢及高合金钢铸件。
2)浓度
水玻璃的浓度实际指的是其中硅酸钠的含量,一般用 密度来间接表示。
一般用密度表示:
低密度:粘度低,可配制粉液比高的涂料,型壳工作 表面的致密,但制的的型壳强度低,一般只用在制 面层涂料,常取ρ=1.25~1.27g/cm3。
熔模铸造工艺讲述资料课件

流槽与流道
流槽和流道是连接浇包与型壳的通道,用于将金属熔液 引导至型壳内。流道设计对浇注效果和铸件质量有重要 影响。
其他辅助设备和工具
模具
熔模铸造工艺中使用的模具通常分为压制模具和铸造 模具两类。压制模具用于压制熔模,铸造模具则用于 最终成型。
修整工具
修整工具用于对型壳进行微调、修整和清砂等操作,通 常包括刮刀、砂轮、钻头等。
金属材料的熔炼。
02
真空炉
真空炉主要用于熔炼高纯度金属材料,通过真空环境减少气体杂质和氧
化物对熔炼金属的影响。其具有熔炼温度高、熔炼时间短、金属纯度高
等优点。
03
电渣炉
电渣炉是一种利用电流通过渣池产生热能熔炼金属的设备,主要用于大
型铸件的近净形熔炼。其具有熔炼成本低、生产效率高等优点。
型壳制造设备种类与特点
案例二:某涡轮叶片熔模铸造工艺
总结词:某涡轮叶片熔模铸造工艺是一种精密铸造技 术,具有高精度、高复杂度、高生产效率等特点。
详细描述:某涡轮叶片熔模铸造工艺采用高强度、高精 度的模具和砂型,以及高质量的合金材料。在制壳过程 中,采用逐层堆积的方法,形成高精度的叶片形状和内 部结构。熔炼时,要严格控制熔液的成分和纯度,以保 证叶片的性能和质量。浇注时,要控制好温度和浇注速 度,保证叶片的充型和组织结构。冷却过程中,要合理 控制冷却时间和温度,防止叶片出现裂纹等缺陷。打磨 时,要选用合适的磨具和研磨剂,对叶片表面进行精细 打磨,保证其表面质量和精度。
脱壳与清理
脱壳
待金属冷却后,将型壳从金属件 中脱出。
清理
对金属件进行清理,去除表面残留 的型壳材料和浇口等。
修整与抛光
对金属件进行修整和抛光,以满足 产品要求。
熔模铸造
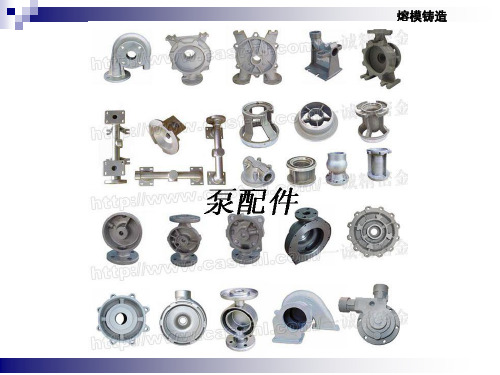
第一节 熔模的制造
熔模铸造
二、模料的种类、组成和性能 1、蜡基模料(低温模料) (1)烷烃蜡 其分子式为CnH2n+2。烷烃蜡在室温下是非常 稳定的,烷烃蜡在100 ℃以上会氧化,氧化反应 的结果使碳-碳链断裂,并生成低分子量的脂肪酸、 醇、二元羟酸、水等产物。由此说明,烷烃蜡的 使用温度应不超过100 ℃。 1)石蜡 n=17~36,主要由正构烷烃组成,n越大,熔点 越高,铸造上常用58 ~64度石蜡。石蜡是晶体。 石蜡的强度低,塑性好,硬度差(针入度为150)。
第一节 熔模的制造
熔模铸造
四、熔模的制造及组装 1、熔模的制造 压型主要有自由浇注和压铸两种。 压制前在压型表面涂薄层分型剂: 压制蜡基模料时,分型剂为机油、松节油等; 压制树脂基模料时,蓖麻油和酒精混合液或硅油。 压制熔模的方法有三种:
气压法
活塞加压法
柱塞法
第一节 熔模的制造
熔模铸造
2、熔模的组装
第二节 制壳工艺性能 可焊性:具有良好的焊接性能和焊接强度。 流动性:获得形状准确和表面光洁的熔模。 图挂性:模料应能很好的为耐火材料所润湿。 灰分:要尽可能少,应低于0.05%。 4、其他性能 还要求模料的密度小,回收方便,复用 性好,无公害及来源丰富,价格低廉等。
熔模铸造
熔模铸造
熔模铸造
熔模铸造
熔模铸造
熔模铸造
熔模铸造
熔模铸造
熔模铸造
工艺流程: 熔模铸造的工艺过程包括:蜡模制造、 结壳、脱蜡、焙烧和浇注等,流程图如下:
第一节 熔模的制造
熔模铸造
熔模铸造过程示意图
第一节 熔模的制造
熔模铸造
第一节 熔模的制造
熔模铸造
熔模铸造的特点: 铸件的精度和表面质量较高(精度可达 CT4~7,Ra1.6~12.5)。 合金种类不受限制,钢铁及有色金属均可适 用。 可铸出形状复杂的铸件(壁厚最小0.5mm, 最小孔径0.5mm,最小重量1g)。 生产批量不受限制。 工艺过程较复杂,生产周期长,成本高,铸 件尺寸不能太大。 铸件冷却速度慢,铸件晶粒粗大。
熔模铸造
二、模料的种类、组成和性能 1、蜡基模料(低温模料) (1)烷烃蜡 其分子式为CnH2n+2。烷烃蜡在室温下是非常 稳定的,烷烃蜡在100 ℃以上会氧化,氧化反应 的结果使碳-碳链断裂,并生成低分子量的脂肪酸、 醇、二元羟酸、水等产物。由此说明,烷烃蜡的 使用温度应不超过100 ℃。 1)石蜡 n=17~36,主要由正构烷烃组成,n越大,熔点 越高,铸造上常用58 ~64度石蜡。石蜡是晶体。 石蜡的强度低,塑性好,硬度差(针入度为150)。
第一节 熔模的制造
熔模铸造
四、熔模的制造及组装 1、熔模的制造 压型主要有自由浇注和压铸两种。 压制前在压型表面涂薄层分型剂: 压制蜡基模料时,分型剂为机油、松节油等; 压制树脂基模料时,蓖麻油和酒精混合液或硅油。 压制熔模的方法有三种:
气压法
活塞加压法
柱塞法
第一节 熔模的制造
熔模铸造
2、熔模的组装
第二节 制壳工艺性能 可焊性:具有良好的焊接性能和焊接强度。 流动性:获得形状准确和表面光洁的熔模。 图挂性:模料应能很好的为耐火材料所润湿。 灰分:要尽可能少,应低于0.05%。 4、其他性能 还要求模料的密度小,回收方便,复用 性好,无公害及来源丰富,价格低廉等。
熔模铸造
熔模铸造
熔模铸造
熔模铸造
熔模铸造
熔模铸造
熔模铸造
熔模铸造
熔模铸造
工艺流程: 熔模铸造的工艺过程包括:蜡模制造、 结壳、脱蜡、焙烧和浇注等,流程图如下:
第一节 熔模的制造
熔模铸造
熔模铸造过程示意图
第一节 熔模的制造
熔模铸造
第一节 熔模的制造
熔模铸造
熔模铸造的特点: 铸件的精度和表面质量较高(精度可达 CT4~7,Ra1.6~12.5)。 合金种类不受限制,钢铁及有色金属均可适 用。 可铸出形状复杂的铸件(壁厚最小0.5mm, 最小孔径0.5mm,最小重量1g)。 生产批量不受限制。 工艺过程较复杂,生产周期长,成本高,铸 件尺寸不能太大。 铸件冷却速度慢,铸件晶粒粗大。
- 1、下载文档前请自行甄别文档内容的完整性,平台不提供额外的编辑、内容补充、找答案等附加服务。
- 2、"仅部分预览"的文档,不可在线预览部分如存在完整性等问题,可反馈申请退款(可完整预览的文档不适用该条件!)。
- 3、如文档侵犯您的权益,请联系客服反馈,我们会尽快为您处理(人工客服工作时间:9:00-18:30)。
2、硅砂 (1)二氧化硅的变体及其转变 主要晶型有三种:方石英、鳞石英和石英。
变体:α石英、β石英、α鳞石英、β鳞石英、γ 鳞石英、α方石英、β方石英及熔融石英。 自然界的硅砂(粉)为β石英。α表示高温稳定型变体; β、γ表示低温稳定型变体。 在不同温度下,石英晶型的转化分两类: 一类为主要晶型的高低温转变
三、模料的配制与回收 1、模料的配制 按照模料的规定成分和配比,将各种原材料熔 融成液态,混和并搅拌均匀,滤去杂质,浇制成锭 块或调制成糊状模料,以待压制熔模。
熔化蜡基模料的加热槽 1、绝热层 2、温度计 3、盖 4、 模料 5、水 6、蜡桶 7、电热器
旋转桨叶搅拌蜡基模料 1 模料 2浆叶
2、模料的回收
熔模铸造过程示意图
熔模铸造的特点: 铸件的精度和表面质量较高(精度可达CT4~7, Ra1.6~12.5)。 合金种类不受限制,钢铁及有色金属均可适用。 可铸出形状复杂的铸件(壁厚最小0.5mm,最小孔径 0.5mm,最小重量1g)。 生产批量不受限制。 工艺过程较复杂,生产周期长,成本高,铸件尺寸不能太大。 铸件冷却速度慢,铸件晶粒粗大。
第二节 制壳原材料
对制壳用耐火材料提出相应的性能要求:
(1)耐火材料的耐火度及最低共熔点
必须具有高于金属浇注温度的耐火度,耐火度 和熔点这两个概念的区别。 (2)耐火材料的热膨胀性
各种耐火材料的热膨胀性能主要取决于其化学 矿物组成和所处的温度。
(3)耐火材料的化学稳定性 耐火材料对于粘结剂和熔融金属应具有良好的 化学稳定性。
3、其他模料 (1)泡沫聚苯乙烯塑料 是单体苯乙烯的聚合物,分料 是一种水溶性模料,分子式为CO(NH2)2,熔点130 ~ 140℃,用于做熔模的可溶性型芯。 (3)充填模料 在模料中加入固体、液体或气体等作为充填物质组成的模 料,固体充填料有聚乙烯、聚苯乙烯、聚乙烯醇及合成树 脂等。
图挂性:模料应能很好的为耐火材料所润湿。
灰分:要尽可能少,应低于0.05%。 4、其他性能 还要求模料的密度小,回收方便,复用性好,无 公害及来源丰富,价格低廉等。
二、模料的种类、组成和性能 1、蜡基模料(低温模料) (1)烷烃蜡 其分子式为CnH2n+2。烷烃蜡在室温下是非 常稳定的,烷烃蜡在100 ℃以上会氧化,氧化反应 的结果使碳-碳链断裂,并生成低分子量的脂肪酸、 醇、二元羟酸、水等产物。由此说明,烷烃蜡的使 用温度应不超过100 ℃。 1)石蜡 n=17~36,主要由正构烷烃组成,n越大,熔点越 高,铸造上常用58 ~64度石蜡。石蜡是晶体。 石蜡的强度低,塑性好,硬度差(针入度为150)。
(3)酯蜡 是高级脂肪酸和高级饱和一元醇进行脂化反应生 成酯的混合物,其分子式为RCOOR′。 主要包括川蜡C25H51COOC26H53和蜂蜡C15H31COOC30H61 。 在实际生产中采用石蜡-硬脂酸各50%的配比。 2、树脂基模料(中温模料) 松香是一种天然树脂,其化学成分主要是 松香酸C19H29COOH,熔点70 ~75 ℃较 高,但是软化点较低<33 ℃,液态时 粘度大,固态时硬度高,易被皂化。 还有改性松香和聚合松香。
气压法
活塞加压法
柱塞法
2、熔模的组装
焊接法 粘结法 机械组装法 3、制模机械化
(1)压蜡机
(2)压铸生产线
第一章 熔模铸造
§1-2 制壳原材料 一、耐火材料 1、耐火材料的应用与对他性能的要求 按照用途可分为三种: 一是粉状耐火材料,它与粘结剂配制成型壳面层用耐火材料: 石英、电熔刚玉、锆石和高铝矾土等。 二是粒状耐火材料,作型壳加固层用耐火材料:硅石、耐火 粘土、高岭石类耐火材料和铝矾土等。 三是用作制造陶瓷型芯的原材料:石英玻璃、电熔刚玉、锆 石等。
2)地蜡 n=35~53,主要由异构烷烃组成,是微晶型蜡。 熔点比石蜡高,热稳定性好,能与石蜡互溶。 有提纯地蜡和合成地蜡两种,地蜡价高。 (2)脂肪酸蜡 分子式CnH2n+1COOH,为晶体。 酸性:固态时酸性不明显,熔融时随温度升高,酸 性增强,能与Al、Fe起置换反应。 反应:一是与碱性物质起中和反应—皂化反应。 二是与醇发生脂化反应,生成脂肪 酸脂和 水。
第一章.熔模铸造
绪论
• 铸造 :将熔熔金属液浇入具有铸件形状的铸型空腔内, 经冷却凝固后获得具有一定性能的铸件的方法 铸造 = 充型 + 凝固 (浇铸系统) (冒口系统 )
特种铸造:除普通砂型铸造方法以外,其他所有的铸
造 方法都叫做特种铸造 补充: 铸铁 铸钢 C≥2.11% C≤2.11% G(石墨) 体积膨胀 体积收缩 小冒口 大冒口
第一章
熔模铸造
概念:
熔模铸造又称“失蜡铸造”,通常是在蜡模表面涂上 数层耐火材料,待其硬化干燥后,将其中的蜡模熔去而制 成型壳,再经过焙烧,然后进行浇注,而获得铸件的一种 方法,由于获得的铸件具有较高的尺寸精度和表面光洁度, 故又称“熔模精密铸造”。
金属材料工程教研室
工艺流程: 熔模铸造的工艺过程包括:蜡模制造、结壳、脱 蜡、焙烧和浇注等,流程图如下:
§1-1 熔模的制造
一、对模料的性能要求 1、热物理性能 熔点:一般在60 ~ 100度范围内。 开始和终了熔化温度范围:以5~10℃为宜。 软化点:一般不低于35 ~ 40度。
收缩率:一般要求小于1%。
2、力学性能 强度:不应低于2.0MPa。
表面硬度:针入度以4 ~6度为佳。
3、工艺性能 可焊性:具有良好的焊接性能和焊接强度。 流动性:获得形状准确和表面光洁的熔模。
蜡基模料在使用中经常发生以下皂化反应而变质:
(1)酸处理法
(2)电解处理法 阳极:
阴极:
(3)活性白土处理法 主要是利用膨润土具有大的吸附能力,将模料中经酸处理后所形 成的盐类及其它杂质吸附在它的周围并凝聚沉淀,使蜡料得到净化。
四、熔模的制造及组装 1、熔模的制造 压型主要有自由浇注和压铸两种。 压制前在压型表面涂薄层分型剂: 压制蜡基模料时,分型剂为机油、松节油等; 压制树脂基模料时,蓖麻油和酒精混合液或硅油。 压制熔模的方法有三种: