IE基础知识资料
IE基础知识培训

找问题的方法: ➢5W1H ➢效率改善查检表法
三、IE导入的10种精神
1、抛弃固有的制作方法及观念; 2、积极寻找达成的方法而不时做不到的理由; 3、严禁为现状问题进行辩解或找借口,实事求是
否定现状; 4、不求完美,50分即可,马上行动; 5、错了请马上改正; 6、改革不许大量投资; 7、不遇问题不出智慧; 8、WHY请问5次找出真正原因; 9、10人的智慧大于1个人的知识; 10、革新永无止境。
四、IE手法
概要
IE的基本手法,是由IE始祖泰勒发明的时间研 究和F.B夫妇发明的动作研究为基础发展开来的。
手法包括:方法研究、作业、直接时间研究法
方法研究
工作时间的过程的直接测量,有时间分析及运转率分析等方法,测量 上以直接测量和录像测量为主
2、间接时间研究法
2、动作分析
对工序的作业方法、动作进行分析设计的方法
谢 谢!
IE基础知识培训
一、IE的基本定义
定义: 是对人员、机器、物料、能源和信息所组成的集
成系统进行设计、改善和设置的一门学科。
综合运用数学、物理学、社会科学的专业知识和 技术,以及工程分析设计的原理与方法,对该系统所 取得的成果进行确定、预测和评价。
二、IE的基本特点
特点
1、IE的核心是降低成本、提升生产质量和生产效率; 2、IE是综合性的应用知识体系; 3、以人为本是IE区别于其他工程学的特点之一; 4、IE的重点是面向微观管理(注重三化); 工业简化 专业化 标准化 5、IE是系统化技术。
对作业单位细分化设定后,通过经验数据的合成设定时间的方法
3、PTS法
时间预置法,全部作业的基本工作进行标准化,用此标准对工程作业 的时间进行预置设定,是一种间接时间研究和动作分析相结合的方法
(完整版)IE基础知识

• 程序流程图根 据研究对象的 不同,可分为: 1) 产品或 物料程序流程 图 2)人员程序 流程图
• 现举例说明: 例一:一张
火车票自售出、 使用至回收为 止的程序流程 图
例二:用量 规和对工件尺 寸
例一
例二
在票架上
到仪器柜
1
拿起并查看票价
1
开仪器柜
用手拿至窗口
2
拿起量规
2
打印日期
带量规到工作台
等待找钱
IE概述
• IE定义:是对人员、物料、设备、能源及信息所组成的集成系 统,进行设计、改善和设置的一门学科。它综合运用数学、物 理学和社会科学方面的专门知识以及工程分析和设计的原理和 方法,对该系统所取得的成果进行确定、预测和评价。简而言 之,就是运用人、机、料、能、信做最有效的组合。以达到低 成本的输入,高效益的产出。
连接更合理
①改变布置,使动作边境更顺畅。
4
简化 simplify
使之更简单 去除多余动作
②使机器操作更简单。 ③使零件标准化,减少材料种类。
“ECRS”四原则
①取消(Eliminate) 在经过“完成了什么?”、“是否必要”及“为什么”
等问题的提问,而不能有满意答案者皆非必要,即予消除。 取消为改善的最佳效果,如取消不必要的工序、操作、动 作,这是不需投资的一种改进,是改进的最高原则。
“ECRS”四原则
②合并(Combine) 对于无法取消而又必要者,看是否能和拼,以达到省
时简化的目的。如何拼一些工序或动作,或将由多人于不 同地点从事的不同操作。改为由一人或一台设备完成。
• 合并突然改变方向的短程小动作,使之成为连续的曲线运动; • 合并工具 • 合并控制; • 合并动作。
IE 基础知识

生产率提高
5.工厂中的七大浪费
(1)不良改正的浪费
处置不良品——废品返修
(2)制造过多的浪费
中间在制过多造成的浪费
(3)加工过剩的浪费
实际加工精度比加工要求要高
5.工厂中的七大浪费
(4)搬运的浪费
(5)库存过多的浪费
5.工厂中的七大浪费
(6)等待的浪费
(7)动作的浪费(共有12种)
6. IE的手法
著名实验:将一只青蛙放进一锅热水中,它一 下子就跳出来。但是,如果将青蛙放进一锅准备加
热的冷水中,慢慢的冷水变成温水,随着水温
越来越高,青蛙行动越来越慢,最后在锅中
被煮熟了。
2.为什么要进行IE改善?
最好的公司
目的
公司盈利 提高客户满意度 降低质量成本 降低运作成本 提高生产力
2.为什么要进行IE改善?
12.00 15.16 15.42 13.27 15.24 11.67
12.00 15.16 15.42 13.27 15.24
下工装排线 USB1 目检1 点胶 UV BO X
开始时间:焊线员工伸手去拿待焊线头堆的瞬间 结束时间:伸手去拿下一个待焊头堆的瞬间 开始时间:员工伸手去拿待目检头堆的瞬间 开始时间:员工伸手去拿待点胶头堆的瞬间 结束时间:伸手去பைடு நூலகம்下一个待目检头堆的瞬间 结束时间:伸手去拿下一个待点胶头堆的瞬间
当日本经济还处在漫长的、不见出口的隧道 之中时,丰田却取得了赢利一万多亿日元的惊人 成绩。其中一个主要原因是丰田有『赚钱的IE』。
À ú à ¤¿ Õ ¾ à ¤Á à ¹ Ó ¹ Á È ±Ó ¹ ¿ °ä » ¾ û µ ³Å Ò Á Æ ³ 33È Ë 14È Ë °ä » ¨µ í ³Å Ò Ì ³ É 9.5H 2.9H °ä » ¨²¯ ú ³Å Ò Ì ¢ ¶ » 6.8H 2.8H
IE基础知识
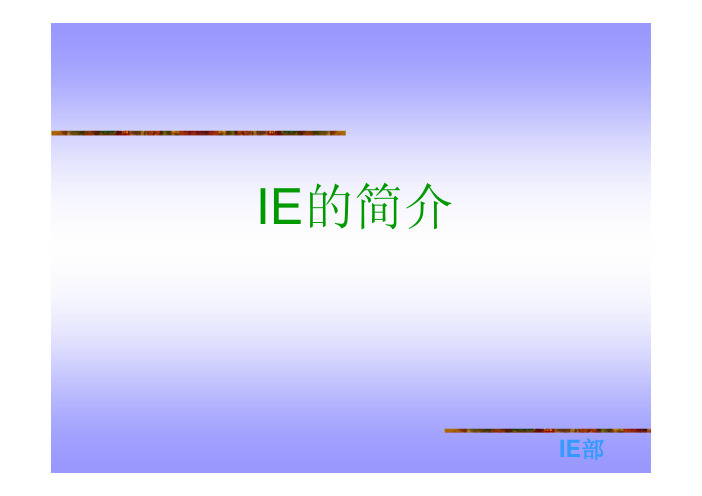
IE的简介IE部第一讲IE简介1、IE的定义2、IE的起源3、IE的研究目标4、IE的特点5、IE对制鞋业的作用6、IE专业术语7、IE实施抵抗情绪的10种表现IE部IE的定义IE----全称Industrial Engineering,即工业工程,简称IE;它是对人员、物IE部IE起源(一)1898年,泰勒在别兹列亭制钢公司,发现搬运工用铁锹一次可铲起1.6公斤煤粉,而铁矿石一次可铲起17公斤,在搬运重量上有相当的差异,为了获取一天最大搬运量,泰勒用不同大小的铁锹做实验,并用秒表记录时间。
最后发现:一锹铲起量为10公斤时一天搬运量最大进一步,设定了一天的工作标准。
结果如何?IE部IE起源(一)a、效率的提升:原搬运量12.5吨/天/人,改进后48吨/天/人,搬动效率提高近4倍;b、人员的减少;c、制钢厂人工成本的降低一半;搬运费由原来的8美分/吨,降到4美分/吨;d、员工的薪水增加2倍。
IE部IE起源(二)十九世纪末,吉尔布雷斯从事建筑业。
他发现当时砖头摆在地上,工人必须弯腰捡砖头,容易疲劳,效率不高。
吉尔布雷斯设置了放置砖头和混凝土的架子,并要求工人一手拿砖头的同时另一只手取混凝土。
按照他的方法培训的砌砖工人平均作业效率由120块/小时提高到350块/小时,1912年他将工人工作的动作拍成影片,进行更细微的研究。
1921年他又创造了工序图,为建立良好的作业顺序、作业环境提供了工具。
IE部IE起源(小结)1、在十九世纪末,泰勒率先用秒表对工作进行了时间的分析(包括作业员的劳动强度),被公认为工业工程的开端。
2、同一时期,吉布尔雷斯利用动作分析,对作业员的技能、疲劳程度进行细微的观察,创立了作业流程分析。
IE部IE的研究目标IE的研究目标就是使生产系统投入要素得到更高效的利用,降低成本,保证质量和安全,提高生产率,获取最大的经济效益。
具体的讲,就是通过分析、研究、评估,对生产过程中每个组成部分进行合理的设计、改善,制定出更系统、规范化的生产流程。
IE基础知识

IE 基础知識一、IE: Industrial engineering 的缩写,意指“工业工程“。
二、IE定义: 是一门管理与工程技术相结合的应用科学,是籍着设计、改善、设定人、机、料的工作系统,以求得到更高生产力的专门管理技术。
其中:设计—是指制定新的系统;改善—是指把原有的系统修改的更完善、更适合;设定—是指将设计或改善的系统,导入企业运作系统,并能稳固的发挥。
三、IE目的:以研究企业运作效率为核心,以最少的投入得到最大的产出,以获取最大的效益。
故与成本或经济效益有关,包括制度、作业方法、现场管理、机器、模具、夹具等均应予掌握并加以改善。
四、IE的范围:1、工程分析;2、工作标准;3、动作研究;4、时间研究;5、时间标准;6、价值分析;7、工厂布置;8、运搬设计。
五、IE的研究方法:一〉工作研究:1、是以工厂的整个制造系统为主要的活动对象,籍着物料、机器、工具及工作方法而产出产品,而此产出的方法是否是:a、生产过程最理想?b、生产的工作方法最好?c、机器和工具最适当?d、物料最正确?2、目的:a、生产工程可否简化或省略分析现有的生产过程,有哪些过程是否可以去除;b、工作方法更完善对每一项过程的工作方法,针对人、机、物及方法的研究,以期能找出更快速、更完善的方法;c、作业标准化对研究出来的最佳方法予以标准化,制定作业标准,并依作业标准训诫员工;d、决定标准时间工作研究的主要目的是取得最佳的工作方法(标准作业),故应迅速地、正确地决定标准时间,以作为管理工作上计划与控制的主要依据。
二〉方法研究1、以动作研究为中心,目的在于追求最完美、最有效率的生产系统及工作方法,并加以确定;2、方法研究技巧a、生产对象(物)应经由作业过程,经由时间、空间的变化,做逐一的分析研究(也既广义上的工程分析),从原料到成品,来做经济性的探讨;b、生产主体(人)人是生产的主体,对作业过程,在生产对象物的工作方面做分歧研究(也既广义上的作业分析或工作方法分析),可籍由作业者的作业规范、工作抽样、基本动作或影片进行分析,或应用(动作经济原则)在作业过程,人、机的移动状况,人与机的配合上,追求作业地区或作业者的作业方法的合乎目的性、合理性。
IE管理基础知识

IE管理基础知识☺所谓IE是对综合人、材料、设备、能源等所有系统进行设计、改善、稳固化为目的的。
☺将综合后的所有系统进行稳固化时,为了显示与评价形成的结果,使用工学分析或者设计原则与技法,同时使用数学、自然科学、社会科学等专业知识或者技法。
(1)IE是以人为本形成的技术。
以人为本形成并以管理系统为对象。
(2)IE是把系统设计的改善与稳固化作为重点。
设计或者者新系统的稳固化过程中预测到会发生什么样的结果而做出评价是很重要的。
(3)依靠于系统与运营者的作用与组织化。
为了对应生产技术的变化务必改变系统运营者的作用,并对其进行规定与组织化。
IE是针对以生产现场为中心的作业进行(1)系统的分析:作为现在的系统应该达到的成果,实际没有达到估计的成果时,进行发现问题并进行操纵管理的研究。
(2)系统的改善:现在的系统达到的成果不够充分与作业不方便而有必要改善其中一部分的时候,研究其改善的办法。
(3)系统的设计:发生新的状况使得现在的系统难以达到充分的成果时,查找需求来研究设计新的系统。
图I 1—1表I1—1☺ 随着生产结构的复杂化,生产过程中对人与机器之间的相互作用等的分析,其必要性不断增加。
现象与对未来的分析结果,对决策起很大的作用。
(日本 94%,美国 87%)图I1—2(1) 作为常识性的IE通过基础性的IE 技法教育,使公司所有员工都应该懂得。
特别是对制造现场的管理者、监督者来说是有必要作为必修课学习。
(2) 作为管理系统的IE应用IE 的基本原理或者方法,开发解决现场问题的各类应用工具,并务必向管理系统进展。
为此,有必要引进日本或者美国已开发的系统,进行修改完善并对IE 理论进行取舍选择,使之进展成为与自己环境相吻合,特别是与我们公司生产系统相吻合,并成为现场管理中稳固的管理系统,即为进展IE 的方向。
(3) 培养IE 专家如上所述,为了开展以上两方面工作,首先应通过在企业内培养能够起先头作用的IE 专家,用更加体系化的方法推进IE 并进行普及;另外还有通过实践提高对IE 方法论的懂得程度,同时以此来培养更好、更高水平的专家也是非常重要的。
IE知识点总结

IE知识点总结IE(Industrial Engineering),工业工程是一门研究如何设计、改善和维护复杂系统的学科。
在IE领域中,工程师们可以运用数学、物理学和计算机科学等知识来研究和解决生产系统、服务系统和运营系统等方面的问题。
本文将从IE基础知识、IE工具与技术、IE在不同领域的应用等三个方面对IE知识点进行总结。
一、IE基础知识1. 线性代数:线性代数是IE领域中常用的数学工具。
它涉及线性方程、矩阵、向量空间等内容,可以帮助工程师们分析和解决复杂系统中的数学问题。
2. 概率论与数理统计:概率论与数理统计是IE领域中常用的统计工具。
工程师们可以通过概率论与数理统计的知识来分析复杂系统中的随机变量、概率分布、抽样调查等问题。
3. 运筹学:运筹学是IE领域中常用的优化工具。
它包括线性规划、整数规划、动态规划、网络流等内容,可以帮助工程师们对复杂系统进行优化设计。
4. 控制论:控制论是IE领域中常用的控制工具。
工程师们可以通过控制论的知识来设计、改善和维护复杂系统中的控制系统。
5. 工程经济学:工程经济学是IE领域中常用的经济工具。
它包括成本分析、效益分析、投资决策等内容,可以帮助工程师们进行经济评价和决策分析。
6. 人因工程学:人因工程学是IE领域中常用的人机工程工具。
它涉及人的生理学、心理学、人机界面设计等内容,可以帮助工程师们设计符合人体工程学原理的生产系统和服务系统。
7. 设计思维:设计思维是IE领域中常用的设计工具。
它包括创新思维、系统思维、综合思维等内容,可以帮助工程师们进行系统性、创新性和综合性的设计和改进。
二、IE工具与技术1. 仿真:仿真是IE领域中常用的建模工具。
工程师们可以通过仿真技术对生产系统、服务系统和运营系统进行模拟和分析,以评估设计方案的效果和风险。
2. 进程优化:进程优化是IE领域中常用的工程工具。
工程师们可以通过进程优化技术对生产系统、服务系统和运营系统进行优化设计,以提高效率和降低成本。
基础IE知识概述

➢ 工具万能原则 ➢ 易于操作策略 ➢ 适当位置原则 ➢ 定点放置原则 ➢ 双手可及原则 ➢ 工序排列原则 ➢ 使用容器原则 ➢ 用坠送法原则 ➢ 近使用点原则 ➢ 避免担心原则
关于人体应用
➢ 环境舒适原则Байду номын сангаас
关于工具设 备
关于工作场 所利用
三、IE七大手法说明
防错法 动改法 流程法 五五法 人机法 双手法 抽查法
3 为什么润滑油不足
4
为什么不能充分吸 入呢
5
为什么轴受到异常 磨损呢
润滑油不足
因为油泵没有充分 吸入润滑油
油泵的轴受到异常磨损 松了
润滑油中混有 磨损的金属粉屑
短期解决对策
更换保险丝 增大油泵的
容量 更换油泵
更换油泵 在润滑油的入 口处装滤网
三、IE七大手法说明
防错法 动改法 流程法 五五法 人机法 双手法 抽查法
抽查法
试
板 固 检 检板板 板 耐
面 定 焊 焊底底 面 压
Q加1 C锡
1 、 2
2
Q C 1
Q C 2
高 度 测
测 试
试
F C T 测 试
打总
胶 、
检
装
隔
离
柱
装 箱
三、IE七大手法说明
防错法 动改法 流程法 五五法 人机法 双手法 抽查法
五五法
一、简述 所谓5X5W1H: 5W:WHIRE何处,什么地方,——空间 WHEN何时,在什么时候——时间 WHAT何者,是什么东西/事——生产对象 WHO何人,是什么人做/生产主体 WHY为何,为什么如此 1H:HOW如何,怎么做的。
三、IE七大手法说明
防错法 动改法 流程法 五五法 人机法 双手法 抽查法
IE(工业工程)基础知识
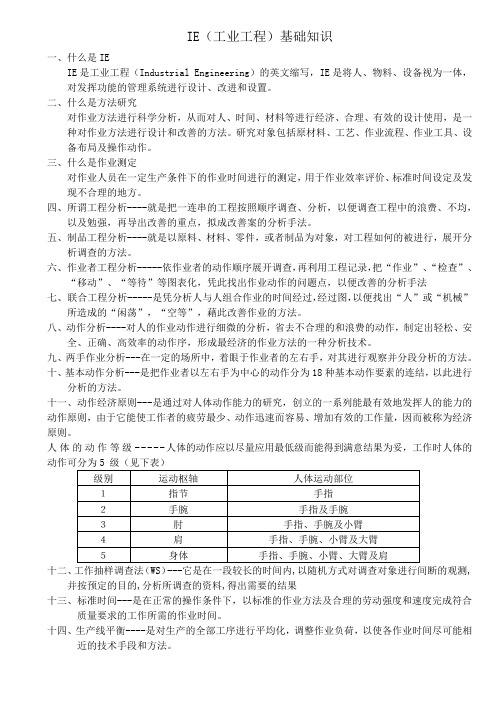
IE(工业工程)基础知识一、什么是IEIE是工业工程(Industrial Engineering)的英文缩写,IE是将人、物料、设备视为一体,对发挥功能的管理系统进行设计、改进和设置。
二、什么是方法研究对作业方法进行科学分析,从而对人、时间、材料等进行经济、合理、有效的设计使用,是一种对作业方法进行设计和改善的方法。
研究对象包括原材料、工艺、作业流程、作业工具、设备布局及操作动作。
三、什么是作业测定对作业人员在一定生产条件下的作业时间进行的测定,用于作业效率评价、标准时间设定及发现不合理的地方。
四、所谓工程分析----就是把一连串的工程按照顺序调查、分析,以便调查工程中的浪费、不均,以及勉强,再导出改善的重点,拟成改善案的分析手法。
五、制品工程分析----就是以原料、材料、零件,或者制品为对象,对工程如何的被进行,展开分析调查的方法。
六、作业者工程分析-----依作业者的动作顺序展开调查,再利用工程记录,把“作业”、“检查”、“移动”、“等待”等图表化,凭此找出作业动作的问题点,以便改善的分析手法七、联合工程分析-----是凭分析人与人组合作业的时间经过,经过图,以便找出“人”或“机械”所造成的“闲荡”,“空等”,藉此改善作业的方法。
八、动作分析----对人的作业动作进行细微的分析,省去不合理的和浪费的动作,制定出轻松、安全、正确、高效率的动作序,形成最经济的作业方法的一种分析技术。
九、两手作业分析---在一定的场所中,着眼于作业者的左右手,对其进行观察并分段分析的方法。
十、基本动作分析---是把作业者以左右手为中心的动作分为18种基本动作要素的连结,以此进行分析的方法。
十一、动作经济原则---是通过对人体动作能力的研究,创立的一系列能最有效地发挥人的能力的动作原则,由于它能使工作者的疲劳最少、动作迅速而容易、增加有效的工作量,因而被称为经济原则。
人体的动作等级-----人体的动作应以尽量应用最低级而能得到满意结果为妥,工作时人体的十二、工作抽样调查法(WS)---它是在一段较长的时间内,以随机方式对调查对象进行间断的观测,并按预定的目的,分析所调查的资料,得出需要的结果十三、标准时间---是在正常的操作条件下,以标准的作业方法及合理的劳动强度和速度完成符合质量要求的工作所需的作业时间。
IE基础知识

永续经营之根本
所谓管理,是指利用现有的
所谓管是指利用有的资源,建立过程控制,完成增加价值的转换(或称新的价值)过程。
值的转换或称新的价值过程IN OUT
过程控制
起源及发展历程起源及发展历程
起源及发展历程
二.工业工程(IE)定义
三.工业工程(IE)七大手法三.工业工程(IE)七大手法
三.工业工程(IE)七大手法三.工业工程(IE)七大手法
三.工业工程(IE)七大手法三.工业工程(IE)七大手法
三.工业工程(IE)七大手法三.工业工程(IE)七大手法
三.工业工程(IE)七大手法
方法研究
方法研究方法研究
方法研究方法研究
动作分析与经济性原则
动作分析与经济性原则
布局分析布局分析
布局分析
时间研究七.时间研究
七.时间研究七.时间研究
七.时间研究七.时间研究
七.时间研究七.时间研究
提高作业效率的改善方法
提高作业效率的改善方法提高作业效率的改善方法
提高作业效率的改善方法提高作业效率的改善方法
提高作业效率的改善方法提高作业效率的改善方法。
精益生产管理IE基础知识

精益生产管理IE基础知识目录一、精益生产管理概述 (2)1.1 精益生产的定义与理念 (3)1.2 精益生产的目标与价值 (4)1.3 精益生产的主要方法与工具 (5)二、工业工程(IE)基础 (6)2.1 工业工程的定义与作用 (7)2.2 工业工程的核心学科 (8)2.3 工业工程在精益生产中的应用 (9)三、生产计划与控制 (11)3.1 生产计划的基本概念与作用 (12)3.2 生产计划的编制方法与步骤 (13)3.3 生产控制的基本原则与方法 (14)3.4 精益生产中的生产计划与控制实践 (16)四、物流与供应链管理 (18)4.1 物流与供应链管理的基本概念 (19)4.2 物流与供应链管理的优化策略 (20)4.3 精益生产中的物流与供应链管理实践 (21)五、设备管理与维护 (23)5.1 设备管理的基本概念与任务 (24)5.2 设备维护与管理的方法与技巧 (25)5.3 精益生产中的设备管理与维护实践 (27)六、质量控制与持续改进 (30)6.1 质量控制的基本概念与方法 (31)6.2 持续改进的理念与方法 (32)6.3 精益生产中的质量控制与持续改进实践 (33)七、精益生产组织与文化 (34)7.1 精益生产组织的构建与职责 (36)7.2 精益生产文化的培育与传承 (37)7.3 精益生产组织与文化的实践案例 (39)一、精益生产管理概述精益生产管理(Lean Production Management)是一种以消除浪费、提高生产效率为核心目标的生产管理方式。
它起源于日本的丰田汽车生产系统,通过优化制造流程、人员管理、资源配置以及持续改进,从而实现企业价值的最大化。
精益生产管理强调对过程的持续改进和员工参与,以实现更好的生产效果。
以人为本:精益生产管理注重激发员工的创造力和主动性,通过提供培训和发展机会,使员工能够积极参与到生产过程中,提高生产效率和质量。
以客户需求为导向:精益生产管理始终将满足客户需求作为最终目标,通过对市场需求和客户反馈的快速响应,不断优化生产流程,提高产品质量和服务水平。
基础IE知识课件
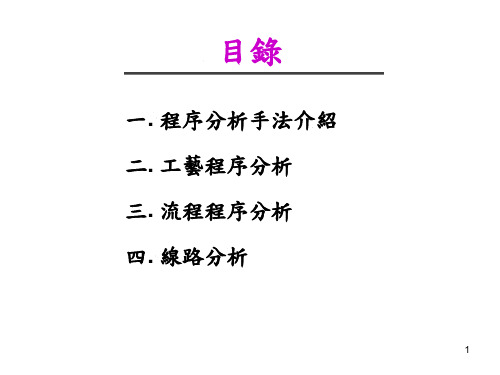
(二).工藝程序圖的繪制
二.工藝程序分析
1.工藝程序圖由箭線、加工符號(2種)和資源 需求三部分组成2.工藝路線用垂直線表示,物料資源的进入用 水平箭線表示,两線中途不相交3.以主要零件作為主要垂直線﹐畫在最右邊﹐ 其余零件按其裝配順序﹐自右向左排列4. 物料資源的名稱﹑規格﹑型號﹑數量填寫在 水平箭線上
作業流程
作業路線
適用
生產作業
製造工藝
製程
工廠Layout
現場工程師
采購作業
采購6項
采購流程
工作地
采購工程師
教育訓練
養成項目
訓練流程
工作地
人力資源
設備開發
作業項目
開發流程
工作地
設備工程師
財務管理
處理項目
表單流程
工作地
會計師
日常工作
工作項目
工作流程
工作地
All
……Βιβλιοθήκη 二.工藝程序分析(一).工藝程序圖
電視機包裝工藝程序圖
箱子投入及外觀檢查
11
將附件/遙控器放入電視機襯套
12
電視機連襯套裝箱,取干燥劑放入箱內
13
封裝及貼出廠標簽
搬運到暫存區
暫存等待出貨
12”
6”
6”
12”
6”
6”
6”
6”
18”/18
5”
18”
12”
6”
2”
電視機x1
標簽x1
膠袋x1
襯套x2
膠袋x1
遙控器x1
附件x1
紙箱x1
膠袋x1
幹燥劑x1
IE基础知识及应用考点

一、IE基础知识1、IE定义:IE 是一门涉及人、机、料、法等要素的集成规划、设计、改善、控制的创新工程科学;它应用自然科学、数学、社会科学特别是工程技术的理论和方法,为实现生产制造管理和服务系统的低成本、高效率和高效益的管理目标提供有力的技术支持。
简言之:工业工程是一门在生产线上寻找浪费,不合理现象和不规则现象并加以改善的一门技法。
2、IE目的:提升效率降低成本3、IE发展阶段:科学管理---系统管理---现代管理(1)科学管理(1911-1945):管理成为科学、管理成为职业代表技术:泰勒的时间研究、吉尔布雷斯的动作研究、甘特的甘特图(2)系统管理(1945-1980)代表技术:运筹学、系统工程、计算机应用生产领域的三种典型生产组织形式:大批量流水线生产、成批生产、单件小批生产代表人物:亨利福特(3)现代管理(1980-现在)信息时代:以计算机为代表的信息技术的应用时代背景:市场全球化、无国家化、多品种小批量生产新的管理模式:柔性生产系统FMS计算机集成制造系统CIMS丰田生产系统TPS敏捷制造AM代表人物:大野耐一4、IE精神:追求创新、追求效率、永不满足现状、永不停滞的改善5、IE的基本意识:成本和效率意识问题和改善意识工作简化和标准化意识全局和整体化意识以人为中心的意识二、制造业八大浪费1、浪费的三种形态:(1)勉强:超过能力界限的超负荷状态(会导致设备故障、品质低下、人员不安全)(2)浪费:有能力,但未给予充分的工作量,使处于不饱和状态(人员工作量不饱满,设备稼动率低)(3)不均衡:有时超负荷有时又不饱和的状态(差异状态)。
2、八大浪费:(1)不良修正浪费:定义:生产过程中因来料或制程的不良,造成的各种损失,需进行处置的时间、人力、物力影响:产品报废、降价处理、材料损失、出货延误取消订单、信誉下降如何减少浪费:作业管理---标准作业指导书,标准作业、标准持有、教育训练;全面质量管理(TQM)、品管统计手法(SQC)、品管圈(QCC)活动、异常管理(看板管理)、斩首示众、首件检查、不制造不良的检查(源流检查、自互检、全数检查)、防错法。
IE基础知识
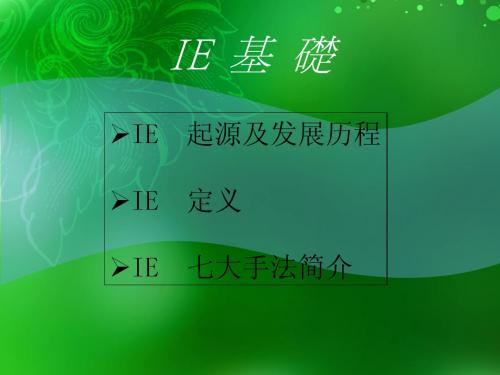
2、设施规划与设计:对系统进行具体的规划和设计, 包括厂址选择,工厂平面布置,物流分析和物料搬 运方法和设备选择等,使各生产要素和各系统实现 整体优化。 3、生产计划与控制:研究生产过程和资源的组织、 计划、调度和控制,包括生产计划过程的时间和空 间组织,生产和作业计划生产线平衡,库存控制等, 分析研究生产作业和库存控制的理想方案,通过对 人、财、物、信息的合理组织调度,加快物流、信 息流和资金周转率,达到高效率。 方法:物料需求计划(MRP)、生产资源计划 (MRPⅡ)、企业资源计划(ERP)、准时制(JIT)
如何避免做错事情,使工作第一次就做好的精神能 够具体实现。 改善人体动作的方式,减少疲劳使工作更为舒适、 更有效率、不要蛮干。 研究探讨牵涉到几个不同工作站或地点之流动关 系,藉以发掘出可资改善的地方。 藉著质问的技巧来发掘出改善的构想。 研究探讨操作员与机器工作的过程,藉以发掘出可 资改善的地方。 研究人体双手在工作时的过程,藉以发掘出可资改 善的地方。 藉著抽样观察的方法能很迅速有效地了解问题的真 象。
流程法
五五法 人机法 双手法 抽查法
WHO
WHY
何人,是什么人做/生产主体
为何,为什么如此
这五个字母之开关都是由“W”开始,的以称之为 “5W”。 1H是指HOW如何,怎么做的。 这个英文字母是由“H”开头,所以称之为“1H”。
五五法
防错法 动改法
流程法
五五法 人机法
以上六项质问(5W1H),对所有的操作或 制程亦完全适用。在改善阶段中,最重要的事 乃是: *明确掌握现状的所有事实。
防错法 动改法 流程法 五五法 人机法
储存 加工
搬运
双手法
抽查法
停滞
表示违反计划而使原料、材料、零件或制品发生停滞的状态。 衡量原料、材料、零件或制品的量或个数,其结果与基准比较, 以获知差异的过程。 试验原料、材料、零件或制品的品质特性,其结果与基准比较, 以判定批的合格、不合格,或制品的不良、不良的过程。
IE基础知识介绍

IE基础知识介绍一、ECRS原则(1)删除(E : Eliminate) 不要去做不必要的事情。
(2)合并(C : Combine) 不能排除的事情或作业用简单的方法去重新整理思路。
(3)重组(R : Rearrange) 考虑重新组合作业动作。
(4)简化(S : Simplify) 简化是考虑每个作业的简化、舒适、缩短距离、减轻重量等方面的改善。
二、线体平衡率三、人均产值人均产值(PPH)指每人每小时的产出数,公式为:总产出 .总人数*总作业时间PPH改善的方向:(1)、动作分析 a、删除、合并、重排、简化 b、动作停滞,搬运之浪费排除c、动作经济原则之运用d、时间分析(2)、工位分析工治具摆放位臵的调整(3)、产线平衡(4)、每日改善追踪IE手法运用一、防错法防错法:又称防愚法, 也就是说,连愚笨的人也不会做错事的设计方法.狭义: 如何设计一个东西(一套方法),使错误绝不会发生.广义: 如何设计一个东西(一套方法),而使错误发生的机会减至最低的程度防误设计的种类:控制法:1.定位插座法定位凹凸槽正确装臵2.光电开关法光电照射带动某些动作3.通过法 GO,NO GO 量规4.形状法视觉辨别,如装配5.错列法尺寸大小或易混淆之物错开放臵注意法:6.标准化法单纯化、规格化、减少失误7.颜色管理法以颜色区别作业8.检核表法设备保养检点,防止失误9.声音法异状发声,加红色内光灯10.提示法工作说明,特别加注及粗线提示结论:不管什么样子的人,做出来的质量,都是一致的方法。
二、动改法1、又称动作改善法,简称为“动改法”,是:*省力动作原则*省时动作原则*动作舒适原则*动作简化原则此原则以最少的劳力达到最大的工作效果2 .动改法分为三大分类:1>. 有关于人体动用方面之原则.2>. 有关于工作场所之布臵与环境之原则.3>. 有关于工具和设备之设计原则.三、流程法现场作业改善方法四、五五法五五法即5 * 5W 1H法,又称5 * 5何法,又称质疑创意法。
IE基础知识培训(内部培训)课件

秒表时间研究
总结词
秒表时间研究是一种测量完成某项任务所需时间的工具,用于评估工作效率和制 定标准时间。
详细描述
通过使用秒表或计时器,记录完成某项任务所需的时间,并进行分析和评估。这 种方法可以帮助确定最佳工作方法,制定标准时间,并发现潜在的改进空间。
03
IE基本原则
效率原则
总结词
提高生产效率,降低成本
动作分析
总结词
对作业人员的动作进行分解和优化,消除多 余和无效动作。
详细描述
动作分析是对作业人员在进行操作时的动作 进行分解和记录,识别出多余和无效动作, 通过优化动作顺序和方式,提高工作效率。
搬运分析
总结词
对物品在生产过程中的搬运进行合理规划, 减少搬运距离和时间。
详细描述
搬运分析是对生产过程中物品的移动进行合 理规划,通过改进搬运方式和工具,减少搬
IE基础知识培训(内部培训) 课件
汇报人: 2023-12-23
目录
• IE基本概念 • IE基本工具 • IE基本原则 • IE基本方法 • IE在生产现场的应用 • IE的未来发展
01
IE基本概念
什么是IE
工业工程(IE)是一门工程管理学科,旨在提高生产效率和降低生产成本。它通过研究生产 制造过程中人、设备、材料、信息等各要素的优化配置,实现高效、低耗、灵活、准时地生 产合格产品。
运距离和时间,提高生产效率。
05
IE在生产现场的应用
生产布局优化
要点一
总结词
生产布局是生产现场的骨架,合理的布局能够提高生产效 率、降低生产成本。
要点二
详细描述
通过对生产设备、生产线、仓库等进行合理布局,减少物 料搬运距离和时间,提高物料流动的顺畅性,从而提高生 产效率。同时,合理的布局还能够减少生产过程中的浪费 ,降低生产成本。
- 1、下载文档前请自行甄别文档内容的完整性,平台不提供额外的编辑、内容补充、找答案等附加服务。
- 2、"仅部分预览"的文档,不可在线预览部分如存在完整性等问题,可反馈申请退款(可完整预览的文档不适用该条件!)。
- 3、如文档侵犯您的权益,请联系客服反馈,我们会尽快为您处理(人工客服工作时间:9:00-18:30)。
Ø工业工程在欧美企业谓之IE( Industrial Engineering),在日本企业界称为“生产技术"或“管理工学"。
IE最早起源于“工作研究",而“工作研究"的主要构成是来自泰勒(F. W. Toylor 1856~1915)的“时间研究"与吉尔布雷斯(F.B. Gilbreth 1868~1924)的“动作研究",相对“企业管理"来说,IE起步较晚,但发展快速. 二十世纪中期以后,在美国企业界,IE几乎取代了大部分的传统管理工作。
Ø 企业的目的是希望以最小的投入(Imput)得到最大的产出(Output),以致获得最大的效益这些投入包括资金(Fund)、人力(Manpower)、材料(Material)、机器(Machine)及厂房(Wor kshop)等。
如何将这些投入,做最有效的组合,以达到效率高、品质稳定、纳期准、浪费少、成本低之目的, 是IE之主要工作内容. 故IE是一门应用科学,兼有管理及工程技术的内容。
随着IE的导入,传统的工程技术融合于现代的科学管理技巧之中,可弥补原有管理及工程技术的脱节,起到省钱增效之最终目的。
现阶段IE之主要工作内容1. 工程分析(Engineering analysis) 用工程符号(“ "代表加工、“”代表物料停滞、“ ”代表搬运、“"代表检查) 将产品从原材料到成品的生产过程制成流程图,发现其瓶颈工序并运用IE手法改善之,使生产线趋于平衡(流程图的制作参考“IE之理论课题II");2. 价值分析(Value analysis) 通过成本核算(Cost accounting),可知产品之制造成本(含人工费、机器折旧费、用房租金、辅料等)的合理性,通过IE手法,降低制造成本,提高产品竞争力,是我们的主要工作内容之一。
(成本核算可参考IE 理论课题I);3. 动作研究(Motion Research) 目的是分析每一个基本动作的合理性。
即对一个工作者使用两眼、两手、两脚的动作予以细分并进行分析及研究,把“不必要"的“去除",把“有必要"的动作变为既“有效率",又“不易疲劳"的最“经济性动作"。
“动作研究"对于大批量生产型(Mass-production)企业作用更大,往往一个动作的改善,可获得相当可观的效果。
IE理论将基本动作分为三大类(共十七种动作要素),即:第一类: A..空手移动(Transport Empty); B. 抓起(Grasp); C. 载重移动(Transport Loaded); D. 位置(Position); E.组合Assemble);F. 分解(Disassemble);G. 使用(Use); H. 放下(Release load)。
第二类:I. 寻找(Search);J.选择(Select);K.检查(Inspect);L.思考(Plan)M.放置前面(Pre-position)第三类: N. 保持(Hold); O. 不可避免的等待(Unavoidable Delay), P. 可避免的等待(Avoidable Delay);Q. 休息(Rest). 通过IE手法,保留第一类动作,简化第二类动作,除去第三类动作,便可达到动作研究之目的。
4. 时间研究(Time Research) 工程分析、价值分析、动作研究等,最终目的无非是要取得最有经济、最有效率、最低成本、最轻松的工作方法,而这些方法最后还是以时间衡量,所以时间研究的目的有两点:(1) 制订客观的标准时间,以此作为绩效衡量标准和管理工具;(2) 作业改善.时间研究的步骤:A. 准备观测工具(秒表/专用表格/笔);B. 作业分割:根据动作研究之原理,将作业者的动作细分为动作要素(十七种的某几种或全部);C. 观测次数:一般不少于三次,作为标准用的最好测3~5次;D. 对象确定:如果是改善用,最好选择一个最熟练的和一个不熟练的。
熟练的人熟能生巧,他的一些细微动作,可能给我们许多启示。
假如是要制订标准时间用的,则选取对象最好是效率在平均水平以上或担任该项工作的时间6个月至一年为宜;E. 观测并记录(具体略);F. 步骤(E)得来的只是实质时间;标准时间=实质时间× (1+宽裕率)宽裕率:一般为实质时间的18%~24%如果时间研究的目的是为了作业改善,则需继续下面的步骤;G. 通过改善作业方法,作业工具(含设备、模具)降低作业时间;H. 重复步骤(A-F),得到新的标准时间和以前之标准时间相效,便可计算出绩效。
5. 标准制订-----含操作标准和检验标准(具体参考IE理论课题III);6. 工作简化(Operation simplicity) 简化的目的就是消除浪费,一个企业中浪费主要表现在以下几个方面:A. 工厂布置(Layout)不当,场所的浪费;B. 流程设计或配置不当,造成场所及搬运的浪费;C. 材料、零件停滞的浪费;D. 机器开机率低之浪费;E. 不知使用最好工具之浪费;F. 不知应用最好的工作方法之浪费;G. 品质不良之浪费;H. 工具士气低落之浪费;I. 等待之浪费;J. 人体动作不当之浪费。
工作简化的步骤:A. 选择项目:根据分析,选择A-J项中对生产影响最大的几个项目;B. 使用“工程分析"、“价值分析"、“动作研究"、“时间研究"等IE手法,对现状进行分析和检讨;C. 运用5W2H法提问:a. Why? 为何如此做,有没有必要?b. What? 目的是什幺,这个工作(动作)可否考虑?c. Where? 有无比这里更合适的地方?d. When? 时间的安排好不好?有无更好的安排方法?e. Who? 谁来做?几个人做?有否更适当的?f. How to do? 这样做法有没有更好的?g. How much?这样做的成本几何?改善后的成本又如何?D. 运用IE手法剔(除)、合(并)、排(重排)、简化来寻求改善;a. 剔除:经过Why、What、How to do分析后认为没必要的,可试着剔除;b. 合并:数人同一工作、数地同一工作或数次来回地做,可以考虑合并;c. 重排:经过剔除、合并后的工作,继续以When、Where、Who加以研究,考虑工作顺序是否重排;d. 简化:经过上面剔、合、排后之工作是否最简单、最佳之效果,是否可再简化。
E. 制定新的工作标准(Standard Formulation) 再好的方法也会受到抵制和排拆,当新的方法产生后,如何有效持久的实施就成为新的课题。
故新的方法产生后,应制定成新的工作标准(具体参考理论课题III),取得相关部门主管认可后,便可大范围推广;F. 效果跟催(Follow Up)新的方法实施应加予跟催及控制、查看a. 有无按新方法作业;b. 新方法实际效果与预期效果的比较;c. 新方法实施过程中,迅速排除产生之问题。
Ø IE的工作性质决定了IE工程师必须具有管理和技术两方面特长,故我们在解决实际技术问题的同时,应该多学习管理方面的知识. 学理与务实的统一,才能最大限度地发挥IE的作用。
时间研究的定义、特点及用途1.时间研究的定义时间研究是一种作业测定技术,旨在决定一位合格适当、训练有素的操作者,在标准状态下,对一特定的工作以正常速度操作所需要的时间。
以上定义的含义为:(1)合格适当、训练有素的操作者即操作者必须是一个合格的工人,而且该作业必须适合于他做;操作者对该项特定工作的操作方法,必须受过完全的训练;操作者必须在正常速度下工作,不能过度紧张,也不能故意延误,工作时生理状态正常。
(2)在标准状态下系指用经过方法研究后制定的标准的工作方法、标准设备、标准程序、标准动作、标准工具、标准机器的运转速度及标准的工作环境等。
2.时间研究的用途(1)决定工作时间标准,并用以控制人工成本。
(2)制定标准时间作为资金制度的依据。
(3)决定工作日程及工作计划。
(4)决定标准成本,并作为标准预算的依据。
(5)决定机器的使用效率,并用以帮助解决生产线的平衡。
二、时间研究的研究方法时间研究也称秒表时间研究、直接时间研究或密集抽样时间研究——即采用抽样技术进行研究。
抽样调查是一种非全面的科学的调查方法。
它是按随机的原则,抽选总体中的部分单位进行调查,以推断总体的有关数据。
抽样调查是按随机的原则从总体中抽选少部分单元,无任何主观意图的影响,因此具有充分的代表性。
抽样调查的次数是根据科学的计算确定的,在调查次数上,有最低限度的保证。
抽样调查的结果,其误差可在调查之前根据抽样的次数和总体中各单位时间标志的差异程度,事先通过计算,将其控制在一定范围之内,因此调查结果比较可靠。
密集抽样与后面介绍的工作抽样(分散抽样)不同之处在于:密集抽样是在一段时间内,利用秒表连续不断地观测操作者的作业,而分散抽样(工作抽样)则是在较长时间内,以随机的方式,分散地观测操作者。
时间研究的步骤一、时间研究的工具1.秒表(停表、马表)2.观测板3.时间研究表格4.铅笔5.计算器6.测量距离及速度的仪器等二、时间研究的步骤1.第一步骤:收集资料为制定某一操作的标准时间,必须对整个操作有详细而完整的了解,不能遗漏操作的任何一部分,或有任何错误,否则将导致标准时间的失误。
通常记录资料的项目均应填入时间研究表格的表头或首页。
一般收集的资料,可按其性质分类如下:(1)能迅速识别研究内容的资料1)研究号码;2)页数与总页数;3)研究者的姓名;4)研究日期;5)研究批准者的姓名。
(2)能正确识别制造的产品或零件的资料1)产品或零件的名称;2)图样或规格的号码;3)材料;4)品质要求(3)能正确识别制造程序、方法、工厂或机器的资料1)操作的部门或地点;2)操作或动作的说明;3)“方法研究单”或“标准操作单”的号码:4)机器的制造厂名称、型式、大小或能量:5)工具、夹具及量规;6)工作现场的布置图、零件表面加工图:(4)能识别操作者的资料1)操作者的姓名;2)性别;3)操作者所具有操作经验程度(技术水平)。
(5)研究的期间1)研究开始时间;2)研究完成时间;3)研究经过的时间。
(6)有关工作环境的资料温度、湿度、照明、噪声以及其它影响操作者生理与心理的资料。
2.第二步骤:划分操作(单元)划分单元必须依据下列要求进行。
(1)检查现行操作方法(2)划分操作单元的目的1)便于评估操作速率2)可将操作内生产工作(有效时间)与非生产工作(无效时间)分开。
3)各单元分别评比,使标准时间更为精确4)每单元予以详细说明,并测计其标准时间,则详细的操作规则即可产生,且以后如某单元需更换动作与时间,可就已建立的相同单元时间相加而获得。
5)如巳制定出每个单元的标准时间,将其综合,即为整个操作的标准时间。
且以后单元如有增减时,亦可迅速算出其标准时间。