如何分析拉伸曲线
拉伸试验曲线的分析及控制

拉伸试验曲线的分析及控制拉伸试验是钢铁材料物理性能评价的重要手段之一。
本实验室在实际生产中使用较先进的ZWICK电子拉伸试验机。
但在实际生产中还是会出现由于试样夹持,试样打滑,参数设置等引起的试验机自动采集数据错误。
为了便于操作人员及时对异常情况做出判断和处理,确保拉伸试验数据的准确性。
本文针对以上问题,进行了研究和整理。
标签:拉伸曲线;试样夹持;试样打滑;参数设置;曲线异常1.引言近年来随着科技的发展进步,电子拉伸试验机已经得到认可。
ZWICK拉伸试验机实现了试验数据和试验曲线的同步性,它是通过不同传感器或测量装置,采集力值信号、应变信号、位移信号和时间。
利用软件对这些信息进行处理,绘制出力值和位移或力值和应变曲线,通过公式计算得出需要的力学性能指标。
并且在曲线上直观的表现出来[1]。
但是电子拉伸试验机也存在着弊端。
在试验过程中难免会出现异常状况,试验机无法自行进行判断。
因此在出现数据异常时,操作者必须清楚应该如何处理,才能确保数据的真确性。
2.试验机精度经过辽宁省计量院的鉴定,本实验室使用的ZWICK拉伸试验机符合《GB/T228》[2]的要求。
按照试验机鉴定计量要求,为了保证在2次试验机鉴定期间,试验机性能的稳定行,实验室自身建立了良好有序的期间核查程序,完成对拉伸试验机整体的运行及精度的控制。
从而排除试验机精度对试验结果的影响。
3.对拉伸试验出现的异常曲线分析及控制当出现拉伸试验结果异常时,首先要确认试验曲线,通过试验曲线判断出现异常结果的原因,从而判断出试验机出现了什么问题。
这样可以很快的对故障点予以修复。
以下对几种拉伸曲线异常情况进行分析。
3.1试样夹持不当造成拉伸曲线异常随着市场的需求不断变化,厚板及特厚板的产量越来越多。
因此检验室检验的圆拉伸试样数量增多了。
由于圆拉伸试验需要安装卡罐(图1,图2),试样与卡罐接触部位易存在间隙,间隙过大对试验曲线会有影响,不利于试验结果的采集,会出现位移增加力值没有改变的情况(图3)。
钢筋机械连接拉伸曲线
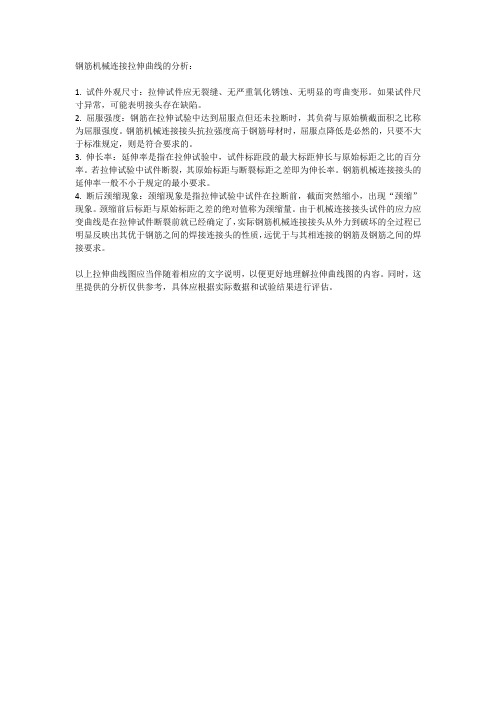
钢筋机械连接拉伸曲线的分析:
1. 试件外观尺寸:拉伸试件应无裂缝、无严重氧化锈蚀、无明显的弯曲变形。
如果试件尺寸异常,可能表明接头存在缺陷。
2. 屈服强度:钢筋在拉伸试验中达到屈服点但还未拉断时,其负荷与原始横截面积之比称为屈服强度。
钢筋机械连接接头抗拉强度高于钢筋母材时,屈服点降低是必然的,只要不大于标准规定,则是符合要求的。
3. 伸长率:延伸率是指在拉伸试验中,试件标距段的最大标距伸长与原始标距之比的百分率。
若拉伸试验中试件断裂,其原始标距与断裂标距之差即为伸长率。
钢筋机械连接接头的延伸率一般不小于规定的最小要求。
4. 断后颈缩现象:颈缩现象是指拉伸试验中试件在拉断前,截面突然缩小,出现“颈缩”现象。
颈缩前后标距与原始标距之差的绝对值称为颈缩量。
由于机械连接接头试件的应力应变曲线是在拉伸试件断裂前就已经确定了,实际钢筋机械连接接头从外力到破坏的全过程已明显反映出其优于钢筋之间的焊接连接头的性质,远优于与其相连接的钢筋及钢筋之间的焊接要求。
以上拉伸曲线图应当伴随着相应的文字说明,以便更好地理解拉伸曲线图的内容。
同时,这里提供的分析仅供参考,具体应根据实际数据和试验结果进行评估。
金属拉伸曲线课件
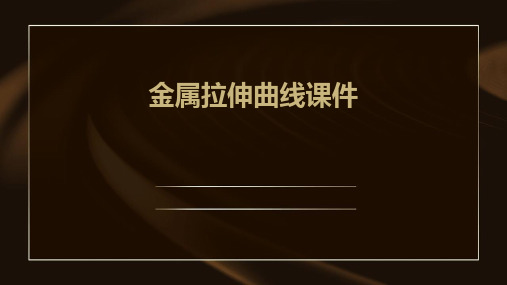
应用指导
金属拉伸曲线可以为实际工程应用提 供指导,例如在结构设计、选材等方 面提供依据。
通过对金属拉伸曲线的分析,可以优 化材料的加工工艺,提高产品的质量 和稳定性。
CHAPTER 02
金属拉伸曲线的形成原理
金属的晶体结构
晶体结构定义
金属的晶体结构是指金属内部原 子或分子的排列方式,决定了金
属的力学、物理和化学性质。
金属拉伸曲线课件
CONTENTS 目录
• 金属拉伸曲线的基本概念 • 金属拉伸曲线的形成原理 • 金属拉伸曲线的实验方法 • 金属拉伸曲线的应用实例 • 金属拉伸曲线的未来发展
CHAPTER 01
金属拉伸曲线的基本概念
金属拉伸曲线的定义
金属拉伸曲线
金属在拉伸过程中,应力与应变 之间的关系曲线。
常见晶体结构
常见的金属晶体结构有体心立方、 面心立方和密排六方等,不同的晶 体结构对金属的拉伸行为产生影响 。
晶体缺陷
在金属的晶体结构中,可能存在各 种缺陷,如空位、位错等,这些缺 陷会影响金属的塑性变形行为。
金属的塑性变形
塑性定义
金属的塑性是指金属在受到外力 作用时发生永久变形的特性。
塑性变形机制
金属制品的加工工艺优化
加工工艺参数优化
通过对金属拉伸曲线的分析,可以确定最佳的加工工艺参数,如拉伸速度、变 形程度等,以提高制品的质量和稳定性。
制品结构设计优化
根据金属拉伸曲线的变化规律,可以对制品的结构设计进行优化,以改善其受 力状况,提高制品的使用寿命。
新材料的研发与探索
新材料性能预测
通过模拟金属拉伸曲线,可以对新材料的基本性能进行预测,为新材料的研发提 供理论依据。
新材料探索与开发
拉伸曲线的四个阶段

拉伸曲线的四个阶段
拉伸曲线的四个阶段
拉伸曲线的四个阶段分别为:弹性阶段、屈服阶段、强化阶段、颈缩阶段
1、弹性阶段:随着荷载的增加,应变随应力成正比增
加。
如卸去荷载,试件将恢复原状,表现为弹性变
形,此阶段内可以测定材料的弹性模量E;
2、屈服阶段:超过弹性阶段后,载荷几乎不变,只是在
某一小范围内上下波动,试样的伸长量急剧地增加,
这种现象称为屈服。
如果略去这种荷载读数的微小
波动不计,这一阶段在拉伸图上可用水平线段来表
示。
塑性变形是突然开始且载荷数会突然下降,如
果全部卸除荷载试样将不会恢复原长表现为永久
形变。
而对于铝合金来说,弹性区域的结束点并非
伴随着载荷的突然下降或其他明显的变化从弹性
阶段到塑性阶段是一条平滑渐变的曲线;
3、强化阶段:经过屈服阶段后,曲线呈现上升趋势,
由于材料在塑性变形过程中不断强化,材料的抗变
形能力有增强了,这种现象称为应变硬化。
若在此
阶段卸载载荷到零时,变形并未完全消失,应力减
小至零时残留的应变称为塑性应变或残余应变;
4、颈缩阶段:试样伸长到一定程度后,荷载读数反而
逐渐降低。
(仅供参考)拉伸曲线、成形极限图介绍
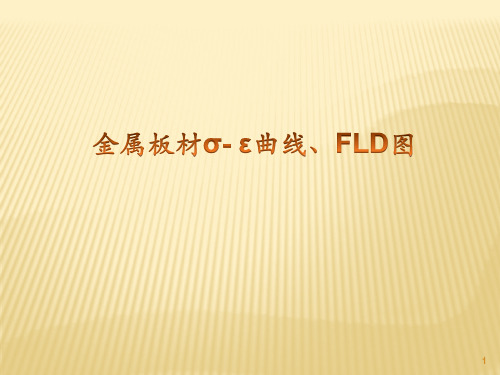
7
σ=F/S0
ReH
c
de
ReL
ε= △L/L0
第4阶段:屈服阶段(cde) 特点: (1)应力下降,应变增加; (2)Luders Band:在应力 达到c点时产生,试样表面沿 45 °度产生滑移带。 (3)c点:上屈服点
e点:屈服结束点 ce间最低点:下屈服点 (4)微观和Cottrell气团对位错 的定扎和反定扎有关。
注:屈服强度σs为下屈服应力;当屈服平台不明显时, σs=ReL
取σ0.2(变形量为0.2%时对应的应力)为屈服强度。
8
σ=F/S0
f
σb
e
ε= △L/L0
第5阶段:塑性变形加工硬化阶 段(ef) 特点: (1)试样在塑性变形下产生加 工硬化,应力不断上升,均匀塑 性变形阶段; (2)f点:应力应变曲线的最高 点;对应的应力为抗拉强度σb; (3)加工硬化阶段和位错密度 增加有关,位错在外力作用下发 生交割、增殖、塞积,要使位错 继续滑移,需进一步提高外力;
化达到平衡;
(2)不均匀塑性变形;
(3)力不再增加,试样最薄弱
的截面出现微孔,连接扩散成小
裂纹,裂纹扩展,形成缩颈,最 L m n ε= △L/L0 终断裂。
注:ok:最大力非比例伸长率; oL:最大力总伸长率; om:断后伸长率; on:断裂总伸长率。
11
12
成形极限图(FLD)或成形极限线(FLC)是评定金属板料 局部成形能力重要工具,在分析冲压成形的破裂问题时经 常使用。 FLD:冲压成形时,金属板料上缩颈或破裂区表面应变量称 为表面极限应变量。二维应变坐标系中,用不同应变路径 下表面极限应变量连成曲线或勾画出条带形区域称为冲压 成型时,成形极限曲线(Forming Limit Curve,缩写FLC), 极限应变量与极限曲线共同构成成形极限图(Forming Limit Diagram,缩写FLD) 。
拉伸试验曲线
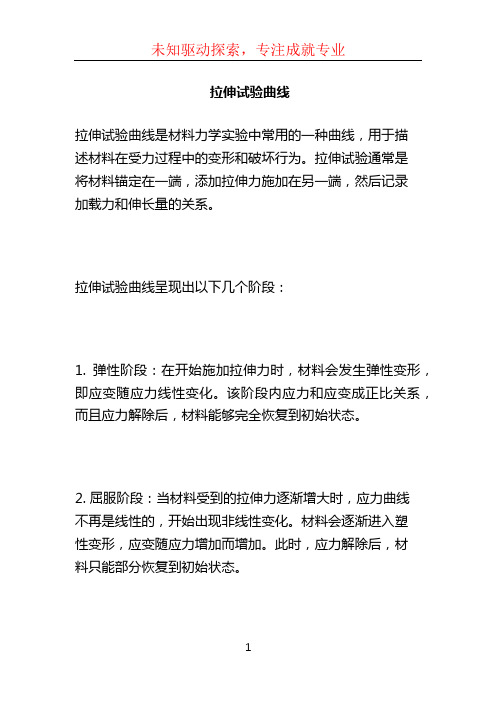
拉伸试验曲线可以通过加载力与伸长量的关系曲线图形来表示。该曲线可用于评估材料的强度、刚度、延性等力学性能,并分析材料的变形和破坏行为。
拉伸试验曲线是材料力学实验中常用的一种曲线,用于描述材料在受力过程中的变形和破坏行为。拉伸试验通常是将材料锚定在一端,添加拉伸力施加在另一端,然后记录加载力和伸长量的关系。
拉伸试验曲线呈现出以下几个阶段:
1. 弹性阶段:在开始施加拉伸力时,材料会发生弹性变形,即应变随应力线性变化。该阶段内应力和应变成正比关系,而且应力解除后,材料能够完全恢复到初始状态。
2. 屈服阶段:当材料受到的拉伸力逐渐增大时,应力曲线不再是线性的,开始出现非线性变化。材料会逐渐进入塑性变形,应变随应力增加而增加。此时,应力解除后,材料只能部分恢复到初始状态。
3. 极限阶段:当拉伸力进一步增加时,材料逐渐接近其极限强。在极限阶段,应力和应变之间关系较为复杂,材料可能发生局部变形和颈缩。
材料拉伸曲线

材料拉伸曲线
材料拉伸曲线是材料力学性能测试中的重要参数之一,它反映了材料在受力作
用下的变形和破坏过程。
通过对材料拉伸曲线的分析,可以了解材料的强度、韧性、塑性等性能,对材料的选择和设计具有重要的指导意义。
首先,材料拉伸曲线通常包括应力-应变曲线和载荷-变形曲线两种类型。
应力-
应变曲线是指在材料拉伸试验中,所施加的拉伸应力与试样的应变之间的关系曲线。
而载荷-变形曲线则是指在材料拉伸试验中,所施加的载荷与试样的变形之间的关
系曲线。
这两种曲线都可以反映材料在受力过程中的性能表现,但侧重点略有不同。
其次,材料拉伸曲线的特征包括线性阶段、屈服阶段、强化阶段和断裂阶段。
在拉伸试验开始时,材料会出现线性阶段,此时应力与应变成正比。
随着应力的增加,材料进入屈服阶段,此时材料开始出现塑性变形。
在经过屈服点后,材料进入强化阶段,此时应力与应变的关系变得更为陡峭。
最终,材料达到断裂点,发生破坏。
此外,材料拉伸曲线的形状与材料的性能密切相关。
比如,曲线的斜率可以反
映材料的弹性模量,屈服点可以反映材料的屈服强度,而强化阶段的斜率则可以反映材料的强化能力。
通过对这些特征的分析,可以全面了解材料的性能表现,为材料的应用提供重要的参考依据。
总之,材料拉伸曲线是材料力学性能测试中的重要参数,通过对其特征的分析,可以全面了解材料在受力过程中的性能表现,为材料的选择和设计提供重要的指导意义。
因此,在工程实践中,对材料拉伸曲线的研究具有重要的意义,可以为材料的应用提供科学的依据。
解读塑料拉力机的拉伸曲线及参数

解读塑料拉力机的拉伸曲线及参数
塑料拉力机是测量塑料制品的拉力等物理性能的,测试拉力性能后就会有一个拉伸曲线图,这个图需要我们去读懂,如果你什么都不知道,那么你肯定不知道上面的符号代表的是什么含义,因此在使用塑料拉力机前应该先了解如何读懂这些参数值。
塑料拉力机的拉伸曲线图:由试验机绘出的拉伸曲线,实际上是载荷-伸长曲线,如将载荷坐标值和伸长坐标值分别除以试样原截面积和试样标距,就可得到应力-应变曲线图。
图中op部分呈直线时,说明应力与应变成正比,其比值就是弹性模量,Pp表示呈正比时的最大载荷,p点应力表示比例极限σp.继续加载时,曲线偏离op,直到e点,这时如卸去载荷,试样仍然可以恢复到原始状态,若过e点试样便不能恢复原始状态。
e点应力为弹性极限σe.工程上由于很难测得真正的σe,常取试样残余伸长达到原始标距的0.01%时的应力为弹性极限,以σ0.01 表示。
继续加载荷,试样沿es曲线变形达到s点,此点应力为屈服点σS或残余伸长为0.2%的条件屈服强度σ0.2.过s 点继续增加载荷到拉断前的最大载荷b点,这时的载荷除以原始截面积即为强度极限σb.在b点以后,试样继续伸长,而横截面积减小,承载能力开始下降,直到k点断裂。
断裂瞬间的载荷与断裂处的截面的比值称断裂强度。
一般来说,塑料拉力机拉伸试验需要求取以下几项或七项的参数
1.试样拉伸至断裂过程中出现的最大力值(拉伸强度);
2.试样断裂时的力值(断裂强度);
3.屈服点对应的力值(屈服点拉伸应力);
4.试样拉伸到给定伸长率时的力值(定伸应力);
5.试样拉伸至给定应力时的伸长率(定应力伸长率);
6.屈服点对应的伸长率(屈服点伸长率);
7.试样断裂时的伸长率(扯断伸长率)。
复合材料拉伸曲线
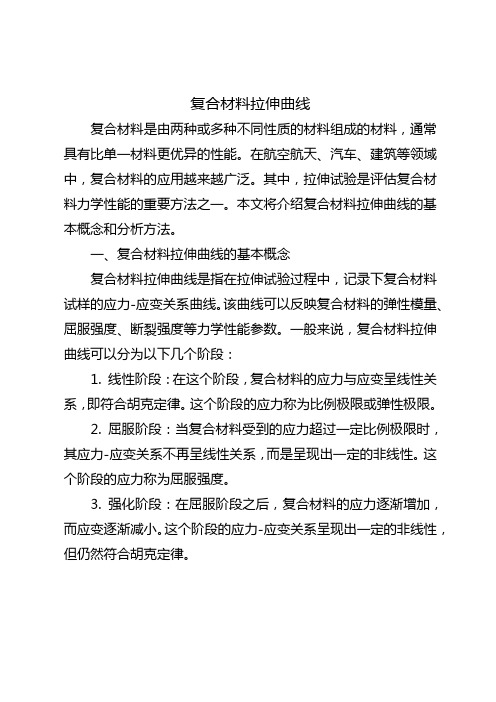
复合材料拉伸曲线复合材料是由两种或多种不同性质的材料组成的材料,通常具有比单一材料更优异的性能。
在航空航天、汽车、建筑等领域中,复合材料的应用越来越广泛。
其中,拉伸试验是评估复合材料力学性能的重要方法之一。
本文将介绍复合材料拉伸曲线的基本概念和分析方法。
一、复合材料拉伸曲线的基本概念复合材料拉伸曲线是指在拉伸试验过程中,记录下复合材料试样的应力-应变关系曲线。
该曲线可以反映复合材料的弹性模量、屈服强度、断裂强度等力学性能参数。
一般来说,复合材料拉伸曲线可以分为以下几个阶段:1. 线性阶段:在这个阶段,复合材料的应力与应变呈线性关系,即符合胡克定律。
这个阶段的应力称为比例极限或弹性极限。
2. 屈服阶段:当复合材料受到的应力超过一定比例极限时,其应力-应变关系不再呈线性关系,而是呈现出一定的非线性。
这个阶段的应力称为屈服强度。
3. 强化阶段:在屈服阶段之后,复合材料的应力逐渐增加,而应变逐渐减小。
这个阶段的应力-应变关系呈现出一定的非线性,但仍然符合胡克定律。
4. 破坏阶段:当复合材料受到的应力超过其断裂强度时,其结构发生破坏,无法继续承受载荷。
这个阶段的应力称为断裂强度。
二、复合材料拉伸曲线的分析方法1. 弹性模量计算:弹性模量是衡量材料抵抗形变的能力的物理量。
在复合材料拉伸曲线中,弹性模量可以通过直线段的斜率来计算。
一般来说,弹性模量越大,材料的刚度越高。
2. 屈服强度计算:屈服强度是衡量材料在受到一定应力时是否会发生塑性变形的物理量。
在复合材料拉伸曲线中,屈服强度可以通过屈服点对应的应力值来计算。
一般来说,屈服强度越高,材料的抗变形能力越强。
3. 断裂强度计算:断裂强度是衡量材料在受到最大应力时是否会发生破坏的物理量。
在复合材料拉伸曲线中,断裂强度可以通过断裂点对应的应力值来计算。
一般来说,断裂强度越高,材料的抗破坏能力越强。
4. 断裂韧性计算:断裂韧性是衡量材料在受到一定应力时是否会发生脆性破坏的物理量。
金属拉伸典型曲线

金属拉伸典型曲线
金属拉伸典型曲线是描述金属在拉伸过程中应力与应变之间关系的曲线。
这个曲线通常由实验获得,并被广泛应用于材料科学和工程领域。
金属拉伸典型曲线通常包括三个阶段:弹性阶段、屈服阶段和强化阶段。
弹性阶段:在拉伸过程中,金属开始表现出弹性行为,应力随着应变的增加而线性增加。
在这个阶段,金属的内部结构并没有发生明显的变化。
屈服阶段:当应力增加到一定程度时,金属开始发生屈服现象,应力不再随着应变的增加而线性增加。
在这个阶段,金属内部开始出现微观结构的变化,如位错滑移、晶界滑移等。
强化阶段:在屈服阶段之后,随着应变的继续增加,金属的应力会重新增加,进入强化阶段。
在这个阶段,金属的内部结构进一步发生变化,如晶粒细化、位错密度增加等,以抵抗进一步的变形。
金属拉伸典型曲线对于理解金属材料的力学性能和加工行为具有重要意义。
通过这个曲线,可以了解金属材料的弹性模量、屈服强度、抗拉强度等关键力学参数,从而指导材料的选择和应用。
此外,通过对拉伸曲线的分析,还可以研究金属材料的微观结构和变形机制,为材料科学和工程领域的发展提供重要依据。
总之,金属拉伸典型曲线是描述金属在拉伸过程中应力与应变之间关系的曲线,对于理解金属材料的力学性能和加工行为具有重要意义。
如何分析拉伸曲线
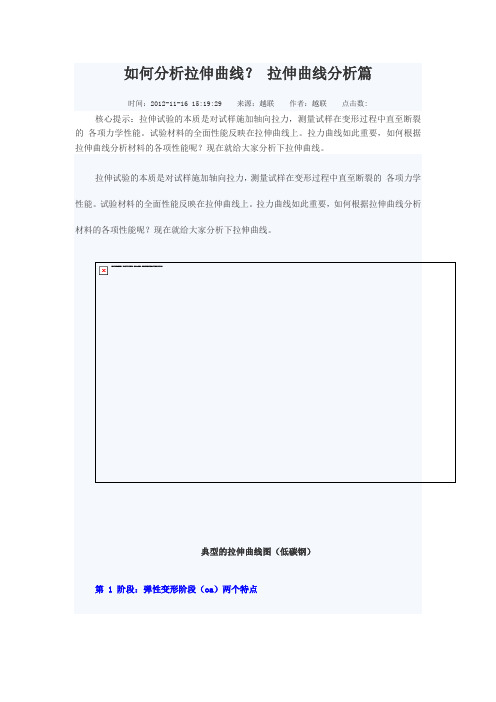
:a 从宏观看,力与伸长成直线关系,弹性伸长与力的大小和试样标距长短成正比,与材料弹性模量及试样横截面积成反比。
b 变形是完全可逆的。
加力时产生变形,卸力后变形完全恢复。
从微观上看,变形的可逆性与材料原子间作用力有直接关系,施加拉力时,在力的作用下,原子间的平衡力受到破坏,为达到新的平衡,原子的位置必须作新的调整即产生位移,使外力、斥力和引力三者平衡,外力去除后,原子依靠彼此间的作用力又回到平衡位置,使变形恢复,表现出弹性变形的可逆性,即在弹性范围保持力一段时间,卸力后仍沿原轨迹回复。
Oa 段变形机理与高温条件下变形机理不同,在高温保持力后会产生蠕变,卸力后表现出不可逆性。
由于在拉伸试验中无论在加力或卸力期间应力和应变都保持单值线性关系,因此试验材料的弹性模量是 oa 段的斜率,用公式求得:E=σ/εoa 线段的 a 点是应力-应变呈直线关系的最高点,这点的应力叫理论比例极限,超过 a 点,应力-应变则不再呈直线关系,即不再符合虎克定律。
比例极限的定义在理论上很有意义,它是材料从弹性变形向塑性变形转变的,但很难准确地测定出来,因为从直线向曲线转变的分界点与变形测量仪器的分辨力直接相关,仪器的分辨力越高,对微小变形显示的能力越强,测出的分界点越低,这也是为什麽在最近两版国家标准中取消了这项性能的测定,而用规定塑性(非比例)延伸性能代替的原因。
第 2 阶段:滞弹性阶段(ab)在此阶段,应力-应变出现了非直线关系,其特点是:当力加到 b 点时然后卸除力,应变仍可回到原点,但不是沿原曲线轨迹回到原点,在不同程度上滞后于应力回到原点,形成一个闭合环,加力和卸力所表现的特性仍为弹性行为,只不过有不同程度的滞后,因此称为滞弹性阶段,这个阶段的过程很短。
这个阶段也称理论弹性阶段,当超过 b 点时,就会产生微塑性应变,可以用加力和卸力形成的闭合环确定此点,当加卸力环第 1 此形成开环时所对应的点为 b 点。
第 3 阶段:微塑性应变阶段(bc)是材料在加力过程中屈服前的微塑性变形部分,从微观结构角度讲,就是多晶体材料中处于应力集中的晶粒内部,低能量易动位错的运动。
材料拉伸曲线
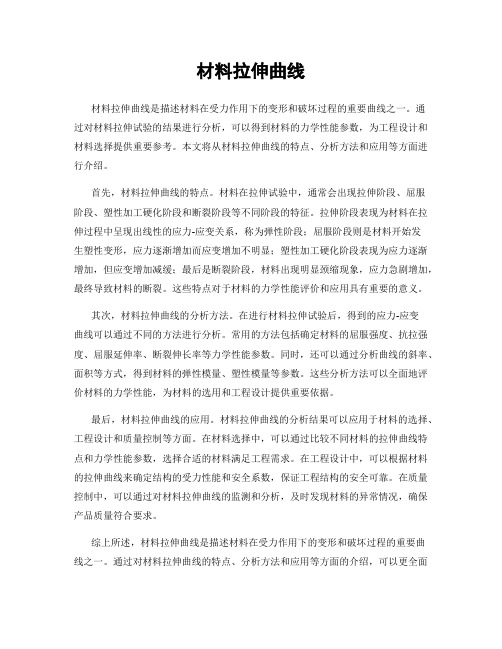
材料拉伸曲线材料拉伸曲线是描述材料在受力作用下的变形和破坏过程的重要曲线之一。
通过对材料拉伸试验的结果进行分析,可以得到材料的力学性能参数,为工程设计和材料选择提供重要参考。
本文将从材料拉伸曲线的特点、分析方法和应用等方面进行介绍。
首先,材料拉伸曲线的特点。
材料在拉伸试验中,通常会出现拉伸阶段、屈服阶段、塑性加工硬化阶段和断裂阶段等不同阶段的特征。
拉伸阶段表现为材料在拉伸过程中呈现出线性的应力-应变关系,称为弹性阶段;屈服阶段则是材料开始发生塑性变形,应力逐渐增加而应变增加不明显;塑性加工硬化阶段表现为应力逐渐增加,但应变增加减缓;最后是断裂阶段,材料出现明显颈缩现象,应力急剧增加,最终导致材料的断裂。
这些特点对于材料的力学性能评价和应用具有重要的意义。
其次,材料拉伸曲线的分析方法。
在进行材料拉伸试验后,得到的应力-应变曲线可以通过不同的方法进行分析。
常用的方法包括确定材料的屈服强度、抗拉强度、屈服延伸率、断裂伸长率等力学性能参数。
同时,还可以通过分析曲线的斜率、面积等方式,得到材料的弹性模量、塑性模量等参数。
这些分析方法可以全面地评价材料的力学性能,为材料的选用和工程设计提供重要依据。
最后,材料拉伸曲线的应用。
材料拉伸曲线的分析结果可以应用于材料的选择、工程设计和质量控制等方面。
在材料选择中,可以通过比较不同材料的拉伸曲线特点和力学性能参数,选择合适的材料满足工程需求。
在工程设计中,可以根据材料的拉伸曲线来确定结构的受力性能和安全系数,保证工程结构的安全可靠。
在质量控制中,可以通过对材料拉伸曲线的监测和分析,及时发现材料的异常情况,确保产品质量符合要求。
综上所述,材料拉伸曲线是描述材料在受力作用下的变形和破坏过程的重要曲线之一。
通过对材料拉伸曲线的特点、分析方法和应用等方面的介绍,可以更全面地了解材料的力学性能,为工程设计和材料选择提供重要参考。
希望本文的介绍能够对相关领域的专业人士和学习者有所帮助。
拉伸试验曲线
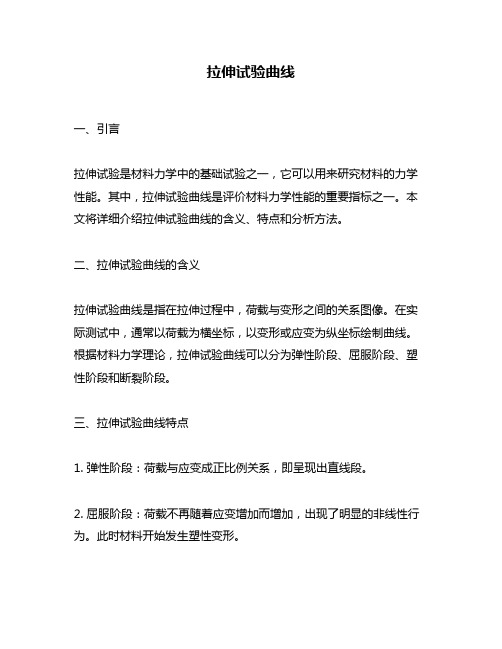
拉伸试验曲线一、引言拉伸试验是材料力学中的基础试验之一,它可以用来研究材料的力学性能。
其中,拉伸试验曲线是评价材料力学性能的重要指标之一。
本文将详细介绍拉伸试验曲线的含义、特点和分析方法。
二、拉伸试验曲线的含义拉伸试验曲线是指在拉伸过程中,荷载与变形之间的关系图像。
在实际测试中,通常以荷载为横坐标,以变形或应变为纵坐标绘制曲线。
根据材料力学理论,拉伸试验曲线可以分为弹性阶段、屈服阶段、塑性阶段和断裂阶段。
三、拉伸试验曲线特点1. 弹性阶段:荷载与应变成正比例关系,即呈现出直线段。
2. 屈服阶段:荷载不再随着应变增加而增加,出现了明显的非线性行为。
此时材料开始发生塑性变形。
3. 塑性阶段:荷载逐渐增大,在应力达到最大值后开始下降。
此时材料已经进入了塑性状态,并且在变形过程中不再回弹。
4. 断裂阶段:材料的应力达到极限值后,开始出现断裂现象。
此时荷载与应变呈现出急剧下降的趋势。
四、拉伸试验曲线分析方法1. 弹性模量的计算在弹性阶段,材料的应力与应变呈线性关系。
根据胡克定律,可以计算出材料的弹性模量。
公式为:E = σ/ε其中,E为弹性模量,σ为应力,ε为应变。
2. 屈服点和屈服强度的确定屈服点是指材料从弹性状态进入塑性状态时的临界点。
通常用0.2%偏差法来确定屈服点。
即从弹性阶段起,在荷载-应变曲线上取一条平行于斜率为初始斜率1/1000(即0.1%)直线,该直线与曲线相交处即为屈服点。
屈服强度是指在材料发生塑性变形时所承受的最大应力值。
通常用屈服点处的荷载值除以试样横截面积来计算。
3. 最大荷载和断裂伸长率的计算最大荷载是指材料在拉伸试验中所承受的最大荷载值。
通常在拉伸试验曲线上读取即可。
断裂伸长率是指材料在断裂前所发生的最大塑性变形程度。
通常用试样断裂后的长度与原始长度之差除以原始长度来计算。
五、结论拉伸试验曲线是评价材料力学性能的重要指标之一,通过对拉伸试验曲线的分析,可以计算出弹性模量、屈服点、屈服强度、最大荷载和断裂伸长率等参数,为研究材料力学性能提供了重要参考。
钢丝绳拉伸曲线
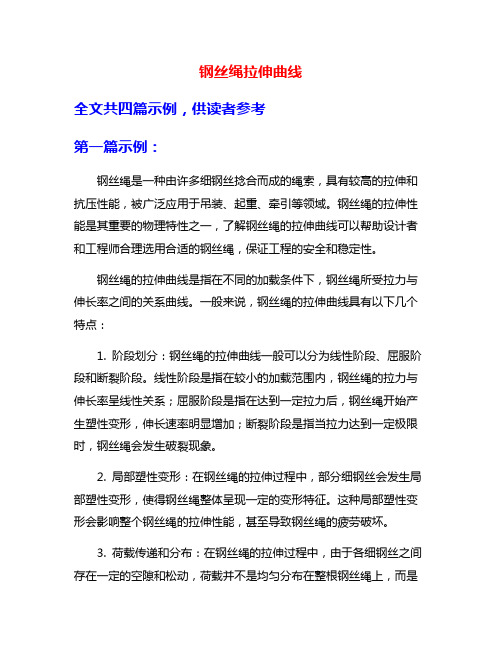
钢丝绳拉伸曲线全文共四篇示例,供读者参考第一篇示例:钢丝绳是一种由许多细钢丝捻合而成的绳索,具有较高的拉伸和抗压性能,被广泛应用于吊装、起重、牵引等领域。
钢丝绳的拉伸性能是其重要的物理特性之一,了解钢丝绳的拉伸曲线可以帮助设计者和工程师合理选用合适的钢丝绳,保证工程的安全和稳定性。
钢丝绳的拉伸曲线是指在不同的加载条件下,钢丝绳所受拉力与伸长率之间的关系曲线。
一般来说,钢丝绳的拉伸曲线具有以下几个特点:1. 阶段划分:钢丝绳的拉伸曲线一般可以分为线性阶段、屈服阶段和断裂阶段。
线性阶段是指在较小的加载范围内,钢丝绳的拉力与伸长率呈线性关系;屈服阶段是指在达到一定拉力后,钢丝绳开始产生塑性变形,伸长速率明显增加;断裂阶段是指当拉力达到一定极限时,钢丝绳会发生破裂现象。
2. 局部塑性变形:在钢丝绳的拉伸过程中,部分细钢丝会发生局部塑性变形,使得钢丝绳整体呈现一定的变形特征。
这种局部塑性变形会影响整个钢丝绳的拉伸性能,甚至导致钢丝绳的疲劳破坏。
3. 荷载传递和分布:在钢丝绳的拉伸过程中,由于各细钢丝之间存在一定的空隙和松动,荷载并不是均匀分布在整根钢丝绳上,而是在细钢丝之间传递和集中,这种荷载传递和分布会影响钢丝绳的整体拉伸性能。
4. 温度和环境因素:钢丝绳的拉伸性能受到温度和环境因素的影响,在高温、潮湿等恶劣环境下,钢丝绳的拉伸性能可能会受到一定程度的损害。
在选用和使用钢丝绳时,需要考虑各种环境因素对钢丝绳的影响。
在日常生活和工程实践中,了解钢丝绳的拉伸曲线对于工程设计和操作具有一定的重要性。
通过对钢丝绳的拉伸曲线进行分析和测试,可以评估钢丝绳的拉伸性能,选择合适的钢丝绳规格和材质,保证工程的安全和稳定性。
及时检测和维护钢丝绳,延长其使用寿命,减少事故发生的可能性。
第二篇示例:钢丝绳是一种由多股细钢丝捻绕而成的绳索,具有较高的强度和耐久性,在吊装、固定和索道等方面被广泛应用。
钢丝绳的性能受到众多因素的影响,其中拉伸曲线是评价其弯曲性能的重要指标之一。
拉伸曲线的名词解释
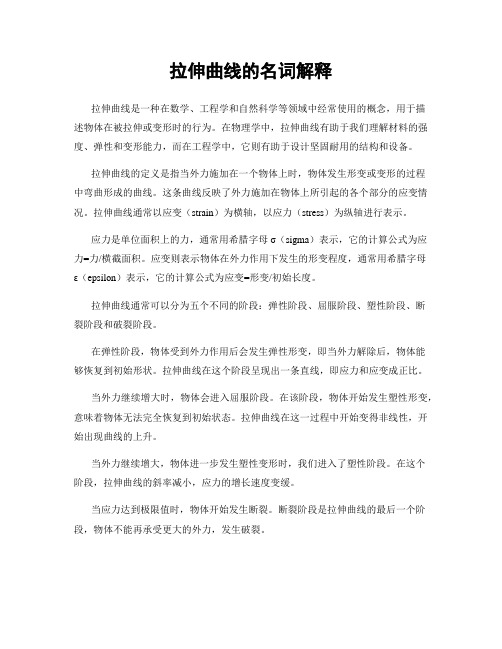
拉伸曲线的名词解释拉伸曲线是一种在数学、工程学和自然科学等领域中经常使用的概念,用于描述物体在被拉伸或变形时的行为。
在物理学中,拉伸曲线有助于我们理解材料的强度、弹性和变形能力,而在工程学中,它则有助于设计坚固耐用的结构和设备。
拉伸曲线的定义是指当外力施加在一个物体上时,物体发生形变或变形的过程中弯曲形成的曲线。
这条曲线反映了外力施加在物体上所引起的各个部分的应变情况。
拉伸曲线通常以应变(strain)为横轴,以应力(stress)为纵轴进行表示。
应力是单位面积上的力,通常用希腊字母σ(sigma)表示,它的计算公式为应力=力/横截面积。
应变则表示物体在外力作用下发生的形变程度,通常用希腊字母ε(epsilon)表示,它的计算公式为应变=形变/初始长度。
拉伸曲线通常可以分为五个不同的阶段:弹性阶段、屈服阶段、塑性阶段、断裂阶段和破裂阶段。
在弹性阶段,物体受到外力作用后会发生弹性形变,即当外力解除后,物体能够恢复到初始形状。
拉伸曲线在这个阶段呈现出一条直线,即应力和应变成正比。
当外力继续增大时,物体会进入屈服阶段。
在该阶段,物体开始发生塑性形变,意味着物体无法完全恢复到初始状态。
拉伸曲线在这一过程中开始变得非线性,开始出现曲线的上升。
当外力继续增大,物体进一步发生塑性变形时,我们进入了塑性阶段。
在这个阶段,拉伸曲线的斜率减小,应力的增长速度变缓。
当应力达到极限值时,物体开始发生断裂。
断裂阶段是拉伸曲线的最后一个阶段,物体不能再承受更大的外力,发生破裂。
在不同的材料和条件下,拉伸曲线的形状和特点可能会有所不同。
一般来说,金属材料的拉伸曲线通常呈现出明显的塑性区域,而脆性材料的拉伸曲线则呈现出较小的塑性区域和更为陡峭的屈服点。
拉伸曲线对于材料工程师来说至关重要,可以帮助他们确定材料的性质及应用范围。
通过分析拉伸曲线,工程师可以确定材料的强度、韧性和变形能力,从而选择合适的材料来设计和制造各种工程和结构。
拉伸试验曲线分析
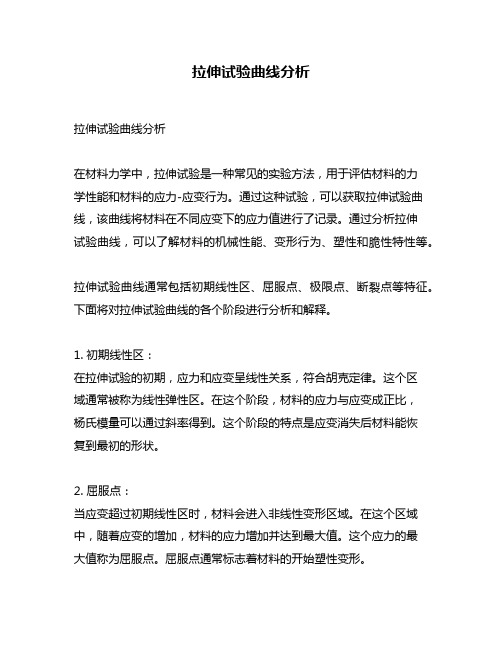
拉伸试验曲线分析拉伸试验曲线分析在材料力学中,拉伸试验是一种常见的实验方法,用于评估材料的力学性能和材料的应力-应变行为。
通过这种试验,可以获取拉伸试验曲线,该曲线将材料在不同应变下的应力值进行了记录。
通过分析拉伸试验曲线,可以了解材料的机械性能、变形行为、塑性和脆性特性等。
拉伸试验曲线通常包括初期线性区、屈服点、极限点、断裂点等特征。
下面将对拉伸试验曲线的各个阶段进行分析和解释。
1. 初期线性区:在拉伸试验的初期,应力和应变呈线性关系,符合胡克定律。
这个区域通常被称为线性弹性区。
在这个阶段,材料的应力与应变成正比,杨氏模量可以通过斜率得到。
这个阶段的特点是应变消失后材料能恢复到最初的形状。
2. 屈服点:当应变超过初期线性区时,材料会进入非线性变形区域。
在这个区域中,随着应变的增加,材料的应力增加并达到最大值。
这个应力的最大值称为屈服点。
屈服点通常标志着材料的开始塑性变形。
3. 极限点:在屈服点之后,随着应变的进一步增加,材料会逐渐失去它的承载能力,并在达到一定应变值时达到极限点。
这个阶段通常叫做延展区。
极限点标志着材料的强度极限。
4. 断裂点:当材料继续受到拉力并进一步延展时,最终会发生断裂。
断裂点通常标志着材料的韧性。
通过分析拉伸试验曲线,我们可以得到很多有关材料性能的信息。
例如,通过观察屈服点,我们可以评估材料的强度。
如果屈服点较高,表示材料的强度很高。
另外,通过延展区的长度,我们可以了解材料的延展性和塑性。
在一些特殊情况下,拉伸试验曲线可能会显示一些额外的特征。
例如,对一些脆性材料,拉伸试验曲线可能没有明显的延展区,而是在屈服点之后迅速达到断裂点。
这表明材料在受到应变后很快就会发生断裂,缺乏塑性。
总结起来,拉伸试验曲线是评估材料性能和行为的重要工具。
通过分析曲线的各个阶段,我们可以了解材料的力学性能、变形行为和塑性特性。
各阶段的特征值得我们深入研究和理解,以提高材料的设计和应用。
低碳钢的拉伸曲线
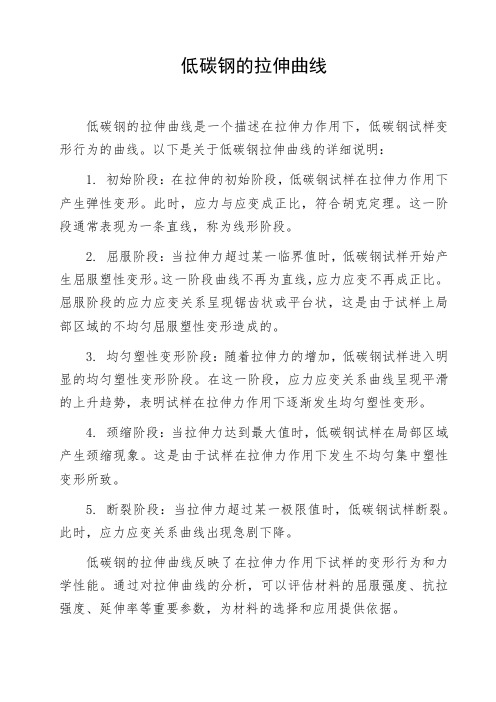
低碳钢的拉伸曲线
低碳钢的拉伸曲线是一个描述在拉伸力作用下,低碳钢试样变形行为的曲线。
以下是关于低碳钢拉伸曲线的详细说明:
1. 初始阶段:在拉伸的初始阶段,低碳钢试样在拉伸力作用下产生弹性变形。
此时,应力与应变成正比,符合胡克定理。
这一阶段通常表现为一条直线,称为线形阶段。
2. 屈服阶段:当拉伸力超过某一临界值时,低碳钢试样开始产生屈服塑性变形。
这一阶段曲线不再为直线,应力应变不再成正比。
屈服阶段的应力应变关系呈现锯齿状或平台状,这是由于试样上局部区域的不均匀屈服塑性变形造成的。
3. 均匀塑性变形阶段:随着拉伸力的增加,低碳钢试样进入明显的均匀塑性变形阶段。
在这一阶段,应力应变关系曲线呈现平滑的上升趋势,表明试样在拉伸力作用下逐渐发生均匀塑性变形。
4. 颈缩阶段:当拉伸力达到最大值时,低碳钢试样在局部区域产生颈缩现象。
这是由于试样在拉伸力作用下发生不均匀集中塑性变形所致。
5. 断裂阶段:当拉伸力超过某一极限值时,低碳钢试样断裂。
此时,应力应变关系曲线出现急剧下降。
低碳钢的拉伸曲线反映了在拉伸力作用下试样的变形行为和力学性能。
通过对拉伸曲线的分析,可以评估材料的屈服强度、抗拉强度、延伸率等重要参数,为材料的选择和应用提供依据。
材料拉伸曲线
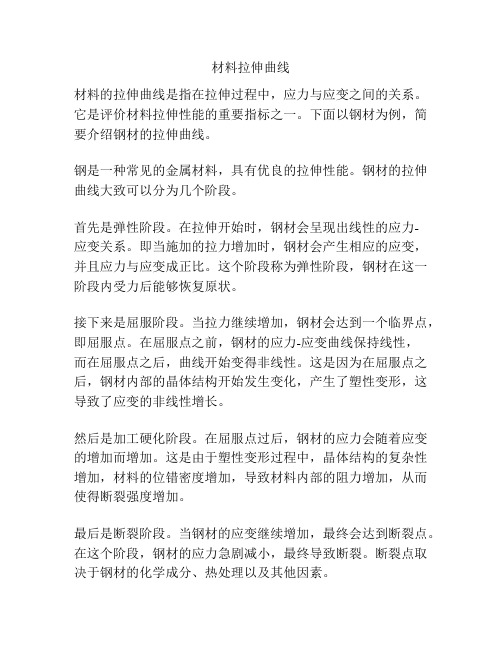
材料拉伸曲线材料的拉伸曲线是指在拉伸过程中,应力与应变之间的关系。
它是评价材料拉伸性能的重要指标之一。
下面以钢材为例,简要介绍钢材的拉伸曲线。
钢是一种常见的金属材料,具有优良的拉伸性能。
钢材的拉伸曲线大致可以分为几个阶段。
首先是弹性阶段。
在拉伸开始时,钢材会呈现出线性的应力-应变关系。
即当施加的拉力增加时,钢材会产生相应的应变,并且应力与应变成正比。
这个阶段称为弹性阶段,钢材在这一阶段内受力后能够恢复原状。
接下来是屈服阶段。
当拉力继续增加,钢材会达到一个临界点,即屈服点。
在屈服点之前,钢材的应力-应变曲线保持线性,而在屈服点之后,曲线开始变得非线性。
这是因为在屈服点之后,钢材内部的晶体结构开始发生变化,产生了塑性变形,这导致了应变的非线性增长。
然后是加工硬化阶段。
在屈服点过后,钢材的应力会随着应变的增加而增加。
这是由于塑性变形过程中,晶体结构的复杂性增加,材料的位错密度增加,导致材料内部的阻力增加,从而使得断裂强度增加。
最后是断裂阶段。
当钢材的应变继续增加,最终会达到断裂点。
在这个阶段,钢材的应力急剧减小,最终导致断裂。
断裂点取决于钢材的化学成分、热处理以及其他因素。
需要注意的是,拉伸曲线的形状和特点不仅与材料的性质有关,还和拉伸速率、温度等因素有关。
在不同条件下,材料的应力-应变曲线会呈现出不同的形态。
总之,拉伸曲线是材料力学性能评价的重要指标之一,它反映了材料在拉伸过程中的性能变化。
通过分析材料的拉伸曲线,我们可以了解材料的强度、韧性等性能,并为工程设计和材料选择提供依据。
- 1、下载文档前请自行甄别文档内容的完整性,平台不提供额外的编辑、内容补充、找答案等附加服务。
- 2、"仅部分预览"的文档,不可在线预览部分如存在完整性等问题,可反馈申请退款(可完整预览的文档不适用该条件!)。
- 3、如文档侵犯您的权益,请联系客服反馈,我们会尽快为您处理(人工客服工作时间:9:00-18:30)。
如何分析拉伸曲线?拉伸曲线分析篇
时间:2012-11-16 15:19:29 来源:越联作者:越联点击数:核心提示:拉伸试验的本质是对试样施加轴向拉力,测量试样在变形过程中直至断裂的各项力学性能。
试验材料的全面性能反映在拉伸曲线上。
拉力曲线如此重要,如何根据拉伸曲线分析材料的各项性能呢?现在就给大家分析下拉伸曲线。
拉伸试验的本质是对试样施加轴向拉力,测量试样在变形过程中直至断裂的各项力学性能。
试验材料的全面性能反映在拉伸曲线上。
拉力曲线如此重要,如何根据拉伸曲线分析材料的各项性能呢?现在就给大家分析下拉伸曲线。
典型的拉伸曲线图(低碳钢)
第 1 阶段:弹性变形阶段(oa)两个特点
a 从宏观看,力与伸长成直线关系,弹性伸长与力的大小和试样标距长短成正比,与材料弹性模量及试样横截面积成反比。
b 变形是完全可逆的。
加力时产生变形,卸力后变形完全恢复。
从微观上看,变形的可逆性与材料原子间作用力有直接关系,施加拉力时,在力的作用下,原子间的平衡力受到破坏,为达到新的平衡,原子的位置必须作新的调整即产生位移,使外力、斥力和引力三者平衡,外力去除后,原子依靠彼此间的作用力又回到平衡位置,使变形恢复,表现出弹性变形的可逆性,即在弹性范围保持力一段时间,卸力后仍沿原轨迹回复。
Oa 段变形机理与高温条件下变形机理不同,在高温保持力后会产生蠕变,卸力后表现出不可逆性。
由于在拉伸试验中无论在加力或卸力期间应力和应变都保持单值线性关系,因此试验材料的弹性模量是 oa 段的斜率,用公式求得:
E=σ/ε
oa 线段的 a 点是应力-应变呈直线关系的最高点,这点的应力叫理论比例极限,超过 a 点,应力-应变则不再呈直线关系,即不再符合虎克定律。
比例极限的定义在理论上很有意义,它是材料从弹性变形向塑性变形转变的,但很难准确地测定出来,因为从直线向曲线转变的分界点与变形测量仪器的分辨力直接相关,仪器的分辨力越高,对微小变形显示的能力越强,测出的分界点越低,这也是为什麽在最近两版国家标准中取消了这项性能的测定,而用规定塑性(非比例)延伸性能代替的原因。
第 2 阶段:滞弹性阶段(ab)
在此阶段,应力-应变出现了非直线关系,其特点是:当力加到 b 点时然后卸除力,应变仍可回到原点,但不是沿原曲线轨迹回到原点,在不同程度上滞后于应力回到原点,形成一个闭合环,加力和卸力所表现的特性仍为弹性行为,只不过有不同程度的滞后,因此称为滞弹性阶段,这个阶段的过程很短。
这个阶段也称理论弹性阶段,当超过 b 点时,就会产生微塑性应变,可以用加力和卸力形成的闭合环确定此点,当加卸力环第 1 此形成开环时所对应的点为 b 点。
第 3 阶段:微塑性应变阶段(bc)
是材料在加力过程中屈服前的微塑性变形部分,从微观结构角度讲,就是多晶体材料中处于应力集中的晶粒内部,低能量易动位错的运动。
塑性变形量很小,是不可回复的。
大小仍与仪器分辨力有关。
第 4 阶段:屈服阶段(cde)
这个阶段是金属材料的不连续屈服的阶段,也称间断屈服阶段,其现象是当力加至 c 点时,突然产生塑性变形,由于试样变形速度非常快,以致试验机夹头的拉伸速度跟不上试样的变形速度,试验力不能完全有效的施加于试样上,在曲线这个阶段上表现出力不同程度的下降,而试样塑性变形急剧增加,直至达到 e 点结束,当达到 c 点,在试样的外表面能观察到与试样轴线呈 45 度的明显的滑移带,这些带称为吕德斯带,开始是在局部位置产生,逐渐扩展至试样整个标距内,宏观上,一条吕德斯带包含大量滑移面,当作用在滑移面上的切应力达到临界值时,位错沿滑移方向运动。
在此期间,应力相对稳定,试样不产生应变硬化。
C 点是拉伸试验的一个重要的性能判据点,范围内的最低点也是重要的性能判 de 据点,分别称上屈服点和下屈服点。
e 点是屈服的结束点,所对应的应变是判定板材成型性能的重要指标。
第 5 阶段:塑性应变硬化阶段(ef)
屈服阶段结束后,试样在塑性变形下产生应变硬化,在 e 点应力不断上升,在这个阶段内试样的变形是均匀和连续的,应变硬化效应是由于位错密度增加而引起的,在此过程中,不同方向的滑移系产生交叉滑移,位错大量增殖,位错密度迅速增加,此时必须不断继续施加力,才能使位错继续滑移运动,直至 f 点。
f 点通常是应力-应变曲线的最高点(特殊材料除外),此点所对应的应力是重要的性能判据。
第 6 阶段:缩颈变形阶段(fg)
力施加至 f 点时,试验材材料的应变硬化与几何形状导致的软化达到平衡,此时力不再增加,试样最薄弱的截面中心部分开始出现微小空洞,然后扩展连接成小裂纹,试样的受力状态由两向变为三向受力状态。
裂纹扩展的同时,在试样表面可看到产生缩颈变形,
在拉伸曲线上,从 f 点到 g 点力是下降的,但是在试样缩颈处,由于截面积已变小,其真应力要大大高于工程应力。
试验达到 g 点试样完全断裂。
从以上典型的拉伸曲线上,可以测定金属材料如下性能:
1 上屈服强度:(c点)试样发生屈服而力首次下降前的最高应力
2 下屈服强度:(e 点)屈服期间的最低应力,要注意这里要排除初始瞬时效应最低应力点所对应的应力。
初始瞬时效应是表现于上屈服过后,力的突然降低的现象,其大小与试验机加力系统的柔度、试样的柔度、拉伸速度、试样屈服特性以及测力系统的惯性守恒各种因素有关。
3 抗拉强度:(f 点)在最大力点所对应的应力。
注意:新标准最大力的定义与GB/T228-87 不同,新标准规定:最大力是指屈服阶段之后的最大力,当材料无明显屈服时,是试验期间的最大力。
4 屈服点延伸率:(ae)对于呈现明显屈服现象的材料,从屈服开始至均匀硬化开始之间的延伸率。
要注意起点和终点的判定。
5 最大力总伸长率: F点处作一垂线, f 横座标原点与交点长度对应的伸长率(包括在此条件下的弹性伸长和塑性伸长率)。
6最大力非比例伸长率:f 点处作一平行于弹性段的直线,横座标原点与交点对应的伸长率。
7 断裂总伸长率:(g点)断裂时刻的试样总伸长率(包括弹性伸长和塑性伸长率),这里要注意的是断裂瞬间的判定,根据自动测试系统采样频率作合理测定。
当扣除断裂瞬间的弹性伸长率时,则是断后伸长率 A。
许多脆性材料在拉伸过程中不出现明显屈服现象,只有 3~4 阶段: oa-弹性变形阶段 ab-滞弹变形阶段 bf-应变硬化阶段(对淬火钢,到 f 断裂,对中强钢有缩颈)在此情况下,用规定条件强度表示屈服强度
8 规定塑性延伸强度 Rp:规定非比例延伸率对应的应力,即在代表伸长的横坐标上取规定的伸长量,平行于弹性线段作一直线。
在与曲线交点处作一水平线与力轴的交点力值所对应的应力为 Rp。
一般称平行线法,适用于弹性段为直线的拉伸曲线。
对于弹性段不是直线的拉伸曲线,上述方法无法用,此时要用滞后环法或逐步逼近法进行测定。
9 规定残余延伸强度 Rr:是对于拉伸过程中不出现明显屈服现象材料,用规定条件强度表示屈服强度另一性能,包括规定残余延伸强度 Rr 的测定和验证。
10 规定总延伸强度 Rt:规定总延伸率对应的应力,即在代表伸长的横坐标上取规定的伸长量,平行于力轴作一直线。
在与曲线交点处作一水平线与力轴的交点力值所对应的应力为 Rt。