沥青微表处理方案
浅谈沥青路面微表处施工工艺及安全措施

浅谈沥青路面微表处施工工艺及安全措施摘要:高速公路长期暴露在自然条件下,部分路段路面难免出现微裂缝、贫油等病害,为了防止路面病害的进一步扩展,提前做好预防性养护,根据相关规范要求,最快最有效的办法就是采取微表处施工。
笔者通过实践,总结出高速公路在营运过程中进行微表处施工时,可以从哪些方面进行有效控制。
关键词:沥青路面微表处施工施工工艺Abstract: long exposure to natural conditions, part of the highwaysurface appears unavoidably TVC tiny cracks, disease, in order to prevent the further expansion of the road surface disease, to make the preventive maintenance, according to relevant regulations and the most effective way is the fastest to the micro table place construction. Based on the practice, sums up the highway in the operating process of micro-surfacing construction, can from what respect for effective control.Key Words: asphalt pavement micro-surfacing construction technology一、施工前的准备工作1.材料。
当乳化沥青进场之后,首先要进行取样,对其各个项目技术指标进行检测。
矿料必须在料厂派专人进行筛分,把矿料中的超大粒径筛选出去,并按照之前试验室提供的数据进行配比。
沥青路面病害及微表处理
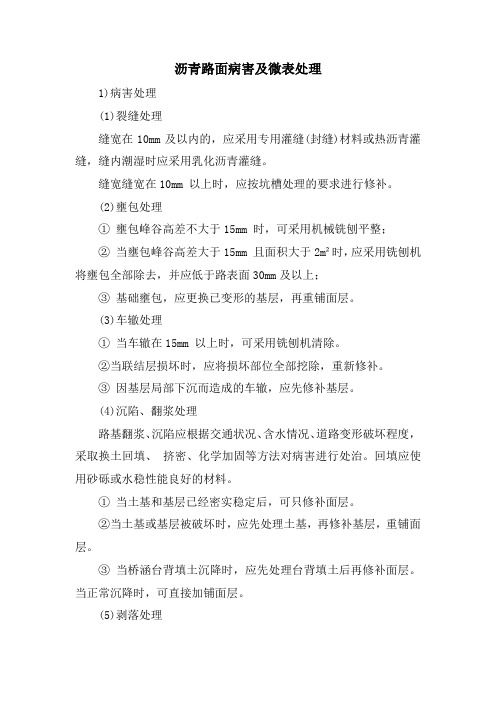
沥青路面病害及微表处理1)病害处理(1)裂缝处理缝宽在10mm及以内的,应采用专用灌缝(封缝)材料或热沥青灌缝,缝内潮湿时应采用乳化沥青灌缝。
缝宽缝宽在10mm 以上时,应按坑槽处理的要求进行修补。
(2)壅包处理①壅包峰谷高差不大于15mm 时,可采用机械铣刨平整;②当壅包峰谷高差大于15mm 且面积大于2m²时,应采用铣刨机将壅包全部除去,并应低于路表面30mm及以上;③基础壅包,应更换已变形的基层,再重铺面层。
(3)车辙处理①当车辙在15mm 以上时,可采用铣刨机清除。
②当联结层损坏时,应将损坏部位全部挖除,重新修补。
③因基层局部下沉而造成的车辙,应先修补基层。
(4)沉陷、翻浆处理路基翻浆、沉陷应根据交通状况、含水情况、道路变形破坏程度,采取换土回填、挤密、化学加固等方法对病害进行处治。
回填应使用砂砾或水稳性能良好的材料。
①当土基和基层已经密实稳定后,可只修补面层。
②当土基或基层被破坏时,应先处理土基,再修补基层,重铺面层。
③当桥涵台背填土沉降时,应先处理台背填土后再修补面层。
当正常沉降时,可直接加铺面层。
(5)剥落处理①已成松散状态的面层,应将松散部分全部挖除,重铺面层,或应按0.8~1.0kg/m²的用量喷洒沥青,撒布石屑或粗砂进行处治。
②沥青面层因贫油出现的轻微麻面,可在高温季节撒布适当的沥青嵌缝料处治。
③大面积麻面应喷洒沥青,并应撒布适当粒径的嵌缝料处治,或重设面层。
④封层的脱皮,应清除已脱落和松动的部分,再重新做上封层。
⑤沥青面层层间产生脱皮,应将脱落及松动部分清除,在下层沥青面上涂刷粘层油,并应重铺沥青层。
(6)坑槽处理①坑槽深度已达基层,应先处治基层,再修复面层。
②修补的坑槽应为顺路方向切割成矩形,坑槽四壁不得松动,加热坑槽四壁,涂刷粘层油,铺筑混合料,压实成型,封缝,开放交通。
槽深大于50mm 时应分层摊铺压实。
③当采用就地热再生修补方法时,应先沿加热边线退回100mm, 翻松被加热面层,喷洒乳化沥青,加入新的沥青混合料,整平压实。
沥青路面微表处技术及施工质量控制

沥青路面微表处技术及施工质量控制摘要:在沥青路面的养护中,微表处技术的应用比较广泛,为此,结合微表处罩面的工程实践,详细论述了在施工中原材料的选用标准、施工准备以及施工质量控制方法,工程结果表明,微表处罩面技术具有施工快、防水性好、节能环保、成本低等优点,具有广阔的发展前景。
关键词:沥青路面;微表处技术;质量控制引言在公路的预防性养护中,微表处技术是沥青路面最常见的处理技术。
微表处技术借用一种稀浆混合物,它是由水、外加剂、集料、改性乳化沥青、填料(水泥、石灰、矿粉等)按照一定比例混合搅拌而成,随后将混合物均匀地铺到路面上,形成一个封层,对路面产生的微小龟裂、块状裂痕、车辙、松散具有一定的修补作用。
G309国道山东潍坊段路面损坏严重,出现大量的纵向裂痕、车辙等问题,本地公路管理局考察调研后,决定通过应用微表处技术对其进行养护,用聚合物改性沥青、填料、集料、水、添加剂等按照一定的比例搅拌成稀浆,通过矩形摊铺槽进行摊铺,使路面形成薄层罩面,施工严格依据《公路沥青路面施工技术规范》(JTGF40—2004)的要求进行。
1.路面微表处技术的定义及优点路面微表处技术是指相关设计单位经过多次配比试验,将具有一定级配的砂、碎石、水、改性乳化沥青以及外加剂按照配合比配制而成,然后通过搅拌机搅拌以后,在正常的天气温度下,均匀地铺设在道路路面上的一种保护层。
路面微表处技术具有较高的防水性和耐磨性,不但能够提高路面的防水能力,而且可以增加路面的抗磨能力,此项技术除了具有这些特性以外,凡是利用这项技术处理过的路面,其平整度和防滑能力都非常高,而且使用寿命还会延长。
路面微表处技术相比其他路面施工技术,施工进度较快,施工造价相对较低,而且对交通车辆通行的影响不大,在道路养护中属于一项性价比非常高的技术。
2.微表处技术2.1原材料选用(1)集料集料在微表处技术中担任着重要角色,起到骨架支撑的作用,集料要求耐磨、坚固、表面干净、无杂质、无风化,如果集料是单一规格,则质量达不到标准,无法使用。
沥青微表处理方案

沥青微表处理方案概述沥青微表是一种常用的路面材料,常用于道路建设和维护。
然而,长期的使用和环境的影响,使得沥青微表会出现老化、开裂、变形等问题,降低了路面的使用寿命。
为了解决这些问题,本文将介绍一种沥青微表的处理方案,以延长路面的使用寿命。
原因分析沥青微表出现问题的主要原因包括: - 长期的交通荷载作用导致沥青微表变形和开裂; - 雨水和湿度的渗透使得沥青微表老化加速; - 温度的变化引起沥青微表的膨胀和收缩; - 不当的施工质量导致沥青微表的问题。
处理方案为了解决沥青微表的问题,可以采取以下处理方案:1. 表层修复对于沥青微表出现的局部裂缝和坑洞,可以进行表层修复。
具体步骤如下: -清理裂缝和坑洞的杂物和灰尘; - 使用热沥青浇灌或热扎修补料填补裂缝和坑洞;- 使用压实设备对修补材料进行压实。
2. 表层再铺设对于比较严重的裂缝和变形问题,需要进行表层再铺设。
具体步骤如下: - 采用机械清理设备清理原有的沥青微表; - 涂布沥青底层混合料,加强基础的稳定性;- 铺设新的沥青微表,确保材料的均匀和密实。
3. 裂缝密封裂缝的出现是沥青微表老化和变形的表现,为了防止裂缝进一步扩大和水分渗透,可以进行裂缝密封。
具体步骤如下: - 清理裂缝的杂物和灰尘; - 使用喷胶剂或热熔胶填充裂缝; - 使用压实设备对填充材料进行压实。
4. 表面处理为了提高沥青微表的耐久性和抗老化能力,可以进行表面处理。
具体步骤如下:- 使用优质的沥青乳液进行表面喷洒; - 在沥青乳液喷洒后,撒布矿物填料以增加摩擦系数。
预防措施除了以上处理方案,还可以采取以下预防措施,以延长沥青微表的使用寿命:- 道路设计阶段选择合适的沥青等级和配方; - 严格控制施工质量,确保沥青微表的均匀和密实; - 定期进行路面维护和检查,及时发现和修复问题。
总结沥青微表的问题会直接影响道路的使用寿命和安全性,因此采取合适的处理方案和预防措施对于道路的维护非常重要。
沥青微表处理方案
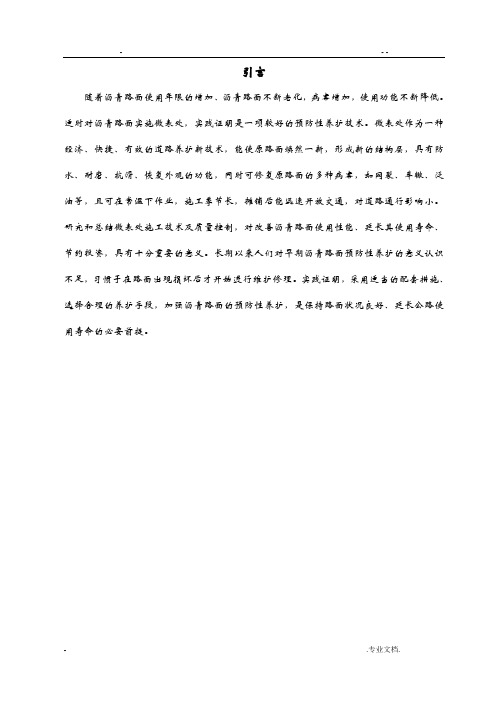
- - -引言随着沥青路面使用年限的增加、沥青路面不断老化,病害增加,使用功能不断降低。
适时对沥青路面实施微表处,实践证明是一项较好的预防性养护技术。
微表处作为一种经济、快捷、有效的道路养护新技术,能使原路面焕然一新,形成新的结构层,具有防水、耐磨、抗滑、恢复外观的功能,同时可修复原路面的多种病害,如网裂、车辙、泛油等,且可在常温下作业,施工季节长,摊铺后能迅速开放交通,对道路通行影响小。
研究和总结微表处施工技术及质量控制,对改善沥青路面使用性能、延长其使用寿命、节约投资,具有十分重要的意义。
长期以来人们对早期沥青路面预防性养护的意义认识不足,习惯于在路面出现损坏后才开始进行维护修理。
实践证明,采用适当的配套措施、选择合理的养护手段,加强沥青路面的预防性养护,是保持路面状况良好、延长公路使用寿命的必要前提。
1、微表处的适用围微表处作为预防性养护的有效方法之一,主要应用在改善路面的抗滑性能、降低路面渗水、进行车辙修复等方面。
因微表处厚度仅l cm左右,实施微表处技术不能增加路面抵抗变形的能力,期望1 cm左右厚的微表处能治百病是不现实的。
因此,必须确定一个微表处的合理适用围,不能什么样的病害路段都用微表处进行处理。
拟实施微表处的路段应满足以下条件:(1)原路面结构强度必须满足要求。
为保证微表处实施效果,就要求拟进行微表处的路段道路结构强度必须满足要求,否则应首先进行补强处理。
应在分析病害成因的基础上选择沥青层挖补、基层翻修甚至路基土的换填等方式进行处理,然后再进行微表处罩面。
以济枣公路为例,在实施微表处前对拟实施路段根据路面病害情况进行钻芯取样分析,发现部分路段的基层强度不足。
据此,对出现严重病害路段进行局部铣刨并加铺沥青面层,然后再在病害处理后的路面上实施微表处。
截止2007年底,该路段微表处使用效果良好。
(2)原路面存在的裂缝、坑槽、龟裂、网裂等病害必须事先进行修补、灌缝处理。
试验证明,原路面上宽度大于5 mm的未处理裂缝、坑槽、龟裂、网裂、严重车辙、拥包、波浪等沥青路面病害,在通车l~2个月左右便会反射到表面上。
沥青路面的裂缝产生与微表处理技术的应用

沥青路面的裂缝产生与微表处理技术的应用摘要:沥青路面裂缝产生的原因是由多种因素造成的,它的防治自然就成为一个综合治理的问题。
本文主要介绍了沥青混凝土路面裂缝产生的主要原因,然后探讨了微表处技术队裂缝处理的应用。
关键词:沥青混凝土路面;裂缝;微表处1 沥青路面的裂缝及产生分析1.1 裂缝(1)裂缝的特征从外观上看大部分是纵向裂缝,从位置上看这些纵缝主要集中在半填半挖,挖填过渡地段。
裂缝本身对路面的承载能力影响不大,最多只不过影响路面的美观而已。
它的危害主要是路表雨水或雪水延裂缝侵入半刚性基层,导致基层的含水量增加饱和,这时会使基层的承载能力下降,从而导致路面的恶化。
(2)产生原因路面设计不合理或厚度不够,某公路路段的上面层为沥青混凝土AC-13,厚度为4cm,而根据经验,各结构层厚度至少应为最大集料公称尺寸的3倍,那么按照标准上面层厚度应为5cm,很显然上面层较薄。
交通量的迅速增长,特别是大量货车的严重超载在路面基层引起的弯拉应力大于基层底部的容许弯拉应力,从而将路面撕裂。
在半填半挖或填挖过渡段处,由于填挖处的路基填料不同,则它们的模量也不同,在行车荷载作用下造成路幅的不均匀沉降而导致裂缝,或者在路面结构内产生不均匀沉降和附加的力学响应从而引起早期裂缝的产生和扩展。
横向裂缝常常是温度变化导致沥青混合料的变化不均匀,因此沥青混合料的性质对是否产生横向裂缝影响很大,沥青老化越严重,含蜡量越高,裂缝越容易产生。
1.2 龟裂(1)龟裂的特征从形成龟裂的位置可知,龟裂主要出现在行车轮迹处,龟裂附近的车辙一般比较大。
一些文献把龟裂划归为裂缝,虽然龟裂在外表上可看成裂缝的恶化,但它们形成的机理是不完全一样的,而且在考虑调查和后续的处理上也应把它们分开。
(2)产生原因局部龟裂可能是路面存在局部缺陷,也可能是整个路段施工所存在的问题,即路面整体强度不足,基层软弱或压实不足,稳定性不良从而在初期产生一些裂缝,但没有进行及时处理,路表雨水或雪水沿裂缝下渗到基层,从而使基层的含水量增加,削弱了基层的承载能力,在行车荷载的作用下使面层的裂缝逐渐增加,最后形成龟裂。
沥青微表处的施工方法

沥青微表处的施工方法嘿,大家好呀!今天咱来聊聊沥青微表处的施工方法。
这事儿啊,还得从我前段时间的一次经历说起。
那天我正好路过一个修路的地方,那场面,可热闹了。
一开始我也不知道他们在干啥,就好奇地凑过去看。
只见一群工人师傅忙得热火朝天,旁边还停着好多大机器。
我就问旁边一个大爷:“大爷,这是在干啥呢?” 大爷说:“这是在做沥青微表处呢。
” 我一听,懵了,啥是沥青微表处啊?大爷还挺热心,给我解释了半天。
原来啊,这沥青微表处就是一种路面养护的方法。
首先呢,工人们得把路面清理干净,就像咱们打扫家里卫生一样,不能有灰尘啊、杂物啥的。
他们拿着大扫帚、吹风机啥的,把路面弄得干干净净。
我看着他们那么认真,心里还挺佩服。
清理完路面,接下来就是上材料了。
那些材料看着黑乎乎的,跟咱们平时看到的沥青差不多。
工人们把这些材料倒在路面上,然后用一个大机器把它们摊平。
那个机器可厉害了,就像一个大熨斗一样,把路面熨得平平整整的。
我看着那个机器在路面上开来开去,觉得特别好玩。
摊平了材料还不算完,还得压实。
这时候就又有一个大机器上场了,那个机器重重地压在路面上,把材料压得结结实实的。
我站在旁边,都能感觉到地面在震动。
工人们还会在旁边检查,看看有没有没压实的地方,如果有,就再压一遍。
看着他们这么辛苦地工作,我心里也挺感慨的。
这修路可真是个不容易的活儿啊。
不过,等这条路修好了,大家走起来就更方便了。
这就是我看到的沥青微表处的施工过程。
虽然我不是专业的,但通过这次经历,我也对这个有了一些了解。
希望以后咱们的路都能修得平平整整的,让大家出行更安全、更顺畅。
嘿嘿!。
沥青路面实施微表处的步骤
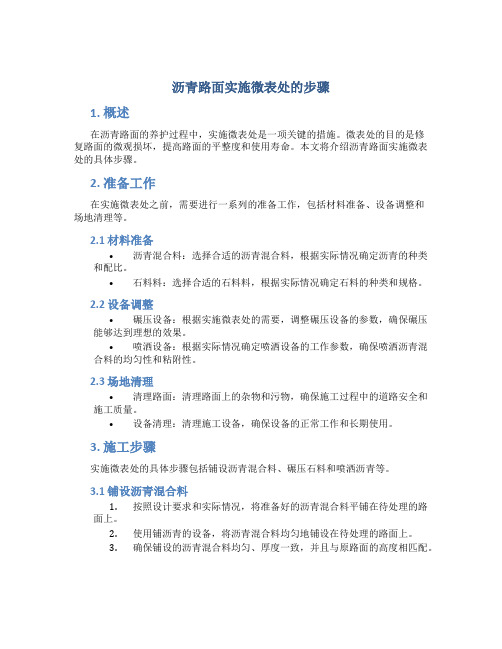
沥青路面实施微表处的步骤1. 概述在沥青路面的养护过程中,实施微表处是一项关键的措施。
微表处的目的是修复路面的微观损坏,提高路面的平整度和使用寿命。
本文将介绍沥青路面实施微表处的具体步骤。
2. 准备工作在实施微表处之前,需要进行一系列的准备工作,包括材料准备、设备调整和场地清理等。
2.1 材料准备•沥青混合料:选择合适的沥青混合料,根据实际情况确定沥青的种类和配比。
•石料料:选择合适的石料料,根据实际情况确定石料的种类和规格。
2.2 设备调整•碾压设备:根据实施微表处的需要,调整碾压设备的参数,确保碾压能够达到理想的效果。
•喷洒设备:根据实际情况确定喷洒设备的工作参数,确保喷洒沥青混合料的均匀性和粘附性。
2.3 场地清理•清理路面:清理路面上的杂物和污物,确保施工过程中的道路安全和施工质量。
•设备清理:清理施工设备,确保设备的正常工作和长期使用。
3. 施工步骤实施微表处的具体步骤包括铺设沥青混合料、碾压石料和喷洒沥青等。
3.1 铺设沥青混合料1.按照设计要求和实际情况,将准备好的沥青混合料平铺在待处理的路面上。
2.使用铺沥青的设备,将沥青混合料均匀地铺设在待处理的路面上。
3.确保铺设的沥青混合料均匀、厚度一致,并且与原路面的高度相匹配。
3.2 碾压石料1.在铺设好的沥青混合料上撒布石料,覆盖沥青混合料的表面。
2.使用碾压设备对石料进行碾压,确保石料与沥青混合料的结合牢固。
3.碾压过程中,注意保持碾压的压力和速度,以达到理想的碾压效果。
3.3 喷洒沥青1.在碾压完石料后,使用喷洒设备喷洒沥青。
2.确保喷洒的沥青均匀且覆盖石料的表面。
4. 施工质量控制为了保证实施微表处的质量,需要进行施工质量控制。
4.1 检查工艺参数在施工过程中,要定期检查和调整工艺参数,确保各项参数符合设计要求,以保证施工的质量。
4.2 保证施工质量•在施工过程中,要定期进行质量检查,确保施工的质量符合要求。
•如发现施工质量不符合要求,及时调整施工参数和工艺流程,进行修复和改进。
沥青混凝土路面高性能微表处施工工法

沥青混凝土路面高性能微表处施工工法沥青混凝土路面高性能微表处施工工法一、前言沥青混凝土路面是目前道路建设中常见的路面类型之一,其高性能微表处施工工法是一种应用于沥青混凝土路面修补和维护的先进工艺。
该工法以提高路面的平整度和耐久性为目标,通过特殊的施工方法和技术措施,能够使路面在长期使用和各种环境条件下保持良好的性能。
二、工法特点该工法的特点主要有以下几点:1. 高精度:通过采用精确的施工工艺和材料,能够在微表面层实现高度平整和精确控制的施工。
2. 耐久性强:采用优质的沥青混凝土材料,加强路面的耐久性和抗疲劳性,延长路面使用寿命。
3. 修补效果好:能够对路面的微裂缝、坑洼等进行精细修复,达到平整度和外观的要求。
4. 施工周期短:采用高效的施工工艺和机械化设备,能够大幅度缩短施工周期,提高工作效率。
三、适应范围该工法适用于各类沥青混凝土路面的高性能微表面修补和维护,包括城市道路、高速公路、停车场等各种道路类型。
四、工艺原理该工法的工艺原理主要是通过采取合理的施工工法和技术措施,来满足路面平整度、耐久性和外观等方面的要求。
具体包括以下几点:1. 路面准备:清理路面,修补埋藏物和裂缝,确保基层的平整度和稳定性。
2. 材料选择:选择适合路面的高性能沥青混凝土材料,包括路面基层和微表层的选择。
3. 施工工艺:采用微表拉毛工艺、微表摊铺工艺等特殊的施工工艺,保证路面的平整度和光滑度。
4. 质量控制:通过严格控制施工工艺和质量检测,确保施工过程中的质量符合设计要求。
5. 养护管理:对施工完工后的沥青混凝土路面进行养护管理,保持路面的良好状态和性能。
五、施工工艺施工工艺主要包括以下几个阶段:1. 路面准备:清理路面、修补裂缝和坑洼。
2. 选材准备:选择适合的沥青混凝土材料,包括基层材料和微表材料。
3. 施工准备:准备施工用的机具设备、调配混凝土等。
4. 施工过程:包括微表拉毛、微表摊铺等工艺的具体施工过程。
5. 施工检测:对施工完成的路面进行质量检测,确保施工质量。
市政道路微表处施工方案

沥青路面封水施工方案一、慨序根据长沙市金霞经济开发区管委会召集专家对湘江大道路面渗水问题进行了认真的分析、讨论就如何处理封堵雨水渗入路面结构处理方案达成的一致意见,决定在湘江大道7至12标6个标段全线采用微表处处理方案。
达到对路面的防水、防磨耗的作用,从而进一步的延缓路面的使用寿命,达到预防性养护的目的。
二、微表处施工工艺1、微表处对原材料要求微表处采用的SBR慢裂快凝型改性乳化沥青,各项指标已满足以下规范要求:微表处用矿料可以采用石灰岩、玄武岩等不同规格的粗细集料掺配而成,也可以用大粒径的块石、卵石等经多极破碎而成。
微表处用粗细集料质量要求微表处矿料级配要求2、微表处摊铺前路面病害处理●挖补处理:对龟裂、块状裂缝、坑槽、沉陷等严重的路面病害采用局部挖补处理;●灌缝处理:对轻微裂缝等病害采用灌缝处理;●铣刨处理:较大面积有轻微车辙,局部涌包、波纹等路面病害采用铣刨、精铣刨处理。
3、微表处的配合比设计微表处是一个系统技术,影响其施工质量的因素很多,有原路况、道路交通量、原材料的质量和性能、施工设备、施工工艺、施工地区气候等等。
不同的混合料对气温、外加水量、填料、外加剂等的敏感程度各不相同,必须事先进行试验验证。
混合料设计是一个绝不可忽视的重要环节,一个合适的混合料设计占成功因素的30%。
混合料设计内容:施工性能:可拌和时间(必须大约3分钟)、成型时间(约2-3小时开放交通)路用性能:湿轮磨耗试验(微表处要求浸水1小时的WTAT值要小于540g/㎡)负荷车轮粘附砂试验(微表处中要求粘砂量测试值应小于450 g/㎡)轮辙变形试验(轮迹宽度变化率小于5%。
)4、微表处的施工4.1、微表处施工前,应对原路面进行检查。
如原路面有较多的裂缝或网裂等其它病害时,宜预先灌缝处理或其它相应的处理才能进行微表处施工。
4.2、施工前对材料应按下列要求进行准备:①施工用的乳化沥青、矿料、水、填料等应进行质量检查,符合要求后方可使用;②矿料中的超粒径颗粒必须筛除;③取矿料堆中间部位的样品进行含水量测定;④检测不同含水量情况下矿料的松装密度,得出矿料的含水量——松装密度关系曲线。
沥青路面预防性养护微表处技术总结

沥青路面预防性养护微表处技术总结引言随着交通量的不断增加,沥青路面的养护工作日益重要。
预防性养护作为一种有效的养护策略,能够延长路面的使用寿命,降低养护成本。
微表处技术作为预防性养护的重要手段之一,因其施工简便、成本低廉、效果显著等优点,在沥青路面养护中得到了广泛应用。
一、微表处技术概述1. 定义微表处技术是一种采用稀浆封层工艺,通过在沥青路面表面铺设一层薄层混合料,以达到改善路面表面功能、延长路面使用寿命的目的。
2. 适用条件微表处技术适用于轻度至中度磨损的沥青路面,特别是那些表面出现裂缝、坑洼、车辙等问题的路面。
二、微表处技术施工流程1. 路面准备施工前,需要对路面进行彻底的清理,包括去除杂物、清扫灰尘、填补裂缝等。
2. 材料准备微表处技术所需材料主要包括沥青、骨料、填料、稳定剂等。
材料的选择和配比对施工效果有直接影响。
3. 施工设备施工过程中需要使用稀浆封层车、摊铺机、压路机等设备。
4. 施工工艺施工时,将混合料均匀地摊铺在路面上,然后使用压路机进行压实。
施工过程中需要控制好摊铺厚度、压实度等关键参数。
三、微表处技术优势分析1. 施工简便微表处技术施工工艺简单,施工速度快,对交通影响小。
2. 成本低廉与传统的路面翻修相比,微表处技术成本更低,经济效益显著。
3. 效果显著微表处能够有效改善路面的抗滑性、抗渗性等性能,延长路面使用寿命。
4. 环境友好微表处技术使用的是冷拌稀浆,施工过程中不会产生有害气体,对环境友好。
四、微表处技术应用案例1. 案例选择选取河南省某高速公路作为微表处技术的应用案例。
2. 施工过程详细描述该高速公路微表处技术的具体施工过程,包括路面准备、材料选择、施工工艺等。
3. 施工效果分析微表处技术在该高速公路上的应用效果,包括路面性能改善情况、使用寿命延长情况等。
五、存在问题与改进建议1. 材料选择在实际施工中,材料选择不当可能会影响微表处技术的效果。
建议加强对材料性能的研究,选择更适合的材料。
浅析沥青路面微表处施工处理

浅析沥青路面微表处施工处理摘要:高速公路长期暴露在自然条件下,部分路段路面难免出现微裂缝、贫油等病害,使用功能不断降低,适时对沥青路面实施微表处提前做好预防性养护,根据相关规范要求,最快最有效的办法就是采取微表处施工。
对改善沥青路面使用性能、延长其使用寿命、节约投资,具有十分重要的意义。
关键词:施工优点节约投资引言:微表处是乳化沥青稀浆罩面的高级形式,它适用于重交通道路的预防性养护和路面轻度车辙等的早期修护和新建路面的抗滑磨耗层,主要应用在改善路面的抗滑性能、降低路面渗水、进行车辙修复等方面。
聚合物改性乳化沥青是经聚合物改性的乳化沥青,本条线改性乳化沥青种类为BCR,其软化点大于等于53℃。
因微表处厚度仅1cm左右,实施微表处技术不能增加路面抵抗变形的能力,期望1cm左右厚的微表处能治百病是不现实的。
因此,必须对病害路段进行处理。
一、微表处的原材料选用及质量控制微表处混合料是由合理配比的乳化沥青、改性剂、集料、水和填料等组成的,材料质量的好坏直接关系到混合料的性能。
微表处混合料中,集料重量占到了混合料总重量的90%以上,而改性剂则是微表处区别于普通稀浆封层最重要的特征之一。
因此,集料和改性剂质量的好坏直接影响混合料性能1、沥青的选择改性乳化沥青根据高速公路路面的情况和要求,我们选用BCR改性乳化沥青,主要特点是可提高高温稳定性,提高与骨料的粘附性,提高路面的抗剥落性,具有很好的韧性及粘韧性等。
改性乳化沥青各项技术指标满足下表要求。
微表处用乳化沥青技术要求:2、填料—本混合料填料采用的P. 032.5水泥。
3、水——不得含有有害的可溶性盐类、能引起化学反应的物质和其它污染物,一般饮用水即可。
某一种石料和乳化沥青,当外加水量为某一范围时,可以成为稳定的稀浆。
机械作业时的外加水量,可以采取允许范围的中值。
我们在施工中遇到了加水量过少,拌和时的和易性及均匀性都受影响,甚至拌不出稀浆。
于是对稀封车的水路进行了改造以满足摊铺所需的和易性。
沥青微表处理方案

沥青微表处理方案一、工程概况。
咱这个要做沥青微表处理的地儿啊,大概有多大面积得先搞清楚,是一条长长的马路,还是某个小广场之类的。
还有这路面现在是个啥状况,有没有好多坑洼,或者裂缝多得像蜘蛛网似的,都得好好看看记下来。
这就好比给病人看病,先得知道病症才能对症下药嘛。
二、材料准备。
1. 沥青。
那沥青的选择可不能马虎。
就像挑食材一样,得选质量好的。
咱要那种黏黏糊糊但又不会太稀的沥青,这样才能稳稳地铺在路面上。
要根据当地的气候来选,要是那地方夏天热得像火炉,就得选那种耐高温的沥青,不然到时候路面软趴趴的,像融化的巧克力可就糟了。
2. 集料。
集料就像是给沥青搭骨架的小零件。
大小得合适,不能太大,不然铺上去不平整;也不能太小,那就没什么支撑力了。
要选那种棱角分明的,就像一个个小战士一样,能牢牢地站在路面上,互相咬紧,这样路面才结实。
而且还得干净,不能带着泥巴啥的,那就像小战士身上脏兮兮的,肯定影响战斗力。
3. 添加剂。
添加剂就像是给这个沥青微表的“小团队”里的秘密武器。
它能让沥青和集料更好地融合在一起,就像胶水一样把大家紧紧粘住。
不过这添加剂的量得控制好,放多了像饭里盐放多了,齁得慌;放少了又没效果。
三、施工设备。
1. 摊铺机。
摊铺机可是个大宝贝。
它得把沥青混合料均匀地铺在路面上,就像摊煎饼一样,要摊得又平又薄。
所以这摊铺机得调试好,速度不能太快,快了就像赶鸭子上架,铺得乱七八糟;也不能太慢,不然耽误工期,就像乌龟爬一样,那可不行。
2. 压路机。
压路机就是来给刚铺好的路面“压压惊”的。
它要把路面压实,让沥青和集料亲密无间。
压路机的重量和型号要选对,就像挑鞋子一样,得合脚。
太轻了压不实,路面松松垮垮的;太重了又怕把路面压坏了,那就好心办坏事了。
四、施工步骤。
1. 路面清理。
首先得把路面打扫得干干净净的。
把那些石头子儿、垃圾啥的都清走,就像给路面洗个澡一样。
要是路面不干净,就像在脏桌子上画画,怎么能画得好呢?特别是那些裂缝里的杂物,得用小刷子或者小钩子把它们掏出来,这样后面的沥青才能好好地填充进去。
沥青混凝土路面高性能微表处施工工法(2)

沥青混凝土路面高性能微表处施工工法沥青混凝土路面高性能微表处施工工法一、前言沥青混凝土路面是现代道路建设中常见的路面类型,其性能直接影响到道路的使用寿命和安全性。
而在实际施工中,沥青混凝土路面表面的微缺陷成为了影响其整体性能的主要因素。
为了解决这一问题,沥青混凝土路面高性能微表处施工工法应运而生。
该工法通过采取一系列技术措施,有效地提高了沥青混凝土路面的耐久性和平整度,为道路的安全性和舒适性提供了保障。
二、工法特点沥青混凝土路面高性能微表处施工工法的主要特点如下:1. 采用微表处材料:选择高强度及优质耐久性极高的特殊微表处沥青混凝土材料,以提高路面的承载能力和耐久性。
2. 采用微表处机械:使用先进的微表处机械设备,能够精确控制施工过程,提高路面的平整度和牢固性。
3. 严格施工工艺:根据沥青混凝土路面高性能微表处施工的特点,制定了一套科学合理的施工工艺,保证施工效果。
4. 强化质量控制:通过对施工过程中质量的全方位控制,确保沥青混凝土路面的每一个细节都符合设计要求。
5. 关注工程安全:在施工过程中,重视安全管理,采取相应的安全措施,确保施工人员的安全。
三、适应范围沥青混凝土路面高性能微表处施工工法适用于各类道路,特别适用于高速公路、机场跑道等对路面平整度和耐久性要求较高的场所。
四、工艺原理沥青混凝土路面高性能微表处施工工法的工艺原理是通过采用特殊材料和机械设备,加强施工工艺和质量控制,使得微表处施工达到预期效果。
具体的工艺原理如下:1. 强化基层处理:在施工前,对基层进行充分的处理,确保基层的牢固性和稳定性。
2. 选择适宜的微表处材料:选择高强度及优质耐久性材料,以提高路面的承载能力和耐久性。
3. 精确控制施工温度:通过控制沥青温度和施工温度,确保沥青的黏附性和密实度。
4. 使用微表处机械:采用先进的微表处机械设备,如微表处机械摊铺机,能够精确控制施工厚度和平整度。
5. 强化质量控制:通过对施工过程中的温度、厚度、密实度等指标进行全面监控,确保施工质量达到设计要求。
沥青路面微表处施工方案

海南路面微表处车辙填充及罩面工程施 工 方 案一、路况分析通过路况调查,我们发现海南路面除有轻微压密性车辙外主要问题是路面级配中起骨架支撑作用的骨料风化、氧化石含量较大,压碎值偏低,经重车荷载的反复作用发生断裂并因海南雨水较多,在雨水的侵蚀下断裂骨料逐步分离、剥落从而使集料间失去嵌套,带动周边石料发生松动产生小坑槽,致使路用性能下降且在水的侵害下长期下去必将不断恶化!因此,必须及时采取预防性的封水措施,阻止雨水的进一步侵害.二、养护方案针对上述路况,应在坑槽挖补的基础上对于路面轻微车辙采用MS-Ⅱ型级配先进行车辙填充(恢复路面平整度)并使填充层横断面的中部隆起3mm 左右的余拱,以考虑行车压密作用.待车辙填充层行车自然碾压24h 后进行MS-Ⅱ微表罩面作为原路面的磨耗防水层,及时将水封于路表之外,阻止路用性能的进一步恶化,延长路面的使用寿命.. 以上方案图示如下:6mm 微表罩面后整体效果 原路面三、材料的选择1、级配矿料 1.1级配矿料要求矿料的级配和质量与封层的耐久性、耐磨性、抗滑性等使用性能均有密切关系。
其级配组成应符合《微表处和稀浆封层技术指南》中关于微表处的要求且所用粗集料应表面洁净、质地坚硬、耐磨、扁平细长颗料小于15%;所用细集料应不含泥土和有机杂质,砂当量大于65%,亚甲蓝值符合规定要求(<10ml )。
所需规格为:(0-3mm )、(3-5mm)两档,具体质量要求如下:粗细集料质量要求施工前集料如有超大粒径应提前筛除后将粗、细集料以设计配合比的级配曲线为依据调整生产配合比并用铲车按比例掺配级配料并充分搅拌,经筛分达到相关级配要求后,将级配料装车用于路面施工。
2、重交改性乳化沥青为保证公路路面的力学性能及微表处的质量,本次施工拟采用壳牌佛山厂"一对一"改性乳化沥青,其具有优良的高温稳定性适用于高温区,所用改性乳化沥青采样检测合格后,用油灌车运至施工现场备用,其检测指标应达如下要求:微表处用改性乳化沥青质量要求3选用普通硅酸盐325#或425#水泥,所选水泥应干燥、疏松、无结块现象.4、施工用水选用洁净无化学污染物的饮用水.四、施工及辅助施工设备的选择1、料场拌料及装料选用50型装载机,沥青及水的储存与加注采用储罐配潜水泵进行.2、路面保通及废料清理选用双排车一辆及配套标志、标牌两套,锥形标不低于300个.3、路面施工选用西安筑路机械厂产MS-9型摊铺机及配套车辙填充"V"型摊铺箱、美国原装进口博坎微表罩面摊铺箱及9-16吨胶轮压路机一台.五、施工方案1、根据养护方案,我们制定了详细的施工方案,其施工工艺流程图如下:2、铺筑试验路段 正式施工前,首先按生产配合比进行精确的设备标定并铺设200m 的试验路,检验施工工艺及配合比的可行性,查找不足、检测设备运行情况,从而总结经验,为正式施工提供可靠的实践依据. 3、施 工 3.1封闭交通施工前由安全组按安全技术规范的要求将已铣刨的工作面封闭交通,留超车道通行,以保证施工设备及人员的安全,同时也保证了生产的顺利进行. 3.2路面清扫微表处施工前原路面应清洁、干燥,泥丁等杂物应提前刮除并由专人手持吹风机对路面浮尘进行仔细吹除,防止因原路面洁净度差造成的封层后"脱皮"现象的出现.3.3施样放线在进行路面清扫的同时,应派专人进行放线,为摊铺车作业提供参照物,从而保证微表摊铺后路面纵向边缘的顺直.3.4车辙填充作业在做好以上施工准备工作后,将装好级配料、乳液、填料、水等材料的摊铺车开至施工起点,对准控制线调整好行车标尺放下"V"型摊铺箱并调正使摊铺箱的中线与车辙中线垂直对齐后开机放料至混合料的体积为摊铺槽容积的1/2左右时开动摊铺车匀速前进并调整后置油门使行车速度与槽内1/2料量相平衡;调整"V"型摊铺箱二次刮平装置使微表填充层横断面中部自然隆起3mm左右的拱度,以考虑行车压密作用.在施工过程中出现的局部缺陷应及时用橡胶耙等工具进行人工修复,如超大粒径造成的划痕等.3.5碾压养生微表处车辙填充后,应待混合料初凝后采用9-16吨胶轮压路机进行慢压2-3遍,从而加速混合料水份的排出,缩短固化成型时间并使车辙填充层得到一定程度的压实,使表面更加密实,封水效果更佳并有效防止突出的大粒径骨料的行车剥落.3.6开放交通24h待车辙填充层养生结束后(一般1-2h)便可开放交通进行行车自然碾压,从而充分压实填充层,使隆起的3mm余拱逐步消除至与原路面平齐,为微表罩面创造有利条件.3.7微表罩面车辙填充碾压24h后可进行微表罩面,通过交通封闭、路面清洁、施样放线(与车辙填充时方式相同)后可进行罩面作业,详细的罩面作业程序为:在进行完以上工序的处理后(车辙填充等)由专职安全员引导封层车进入工作面,调整好车位及行车标尺并在微表罩面摊铺箱下放置铁皮,由操作手检查各系统工作正常后开机放料,待摊铺箱内混合料均匀分布且达到叶轮1/2时指示封层车匀速行驶并使摊铺箱内混合料始终处于叶轮1/2的位置以防因缺料漏铺。
沥青路面养护的微表处理技术应用
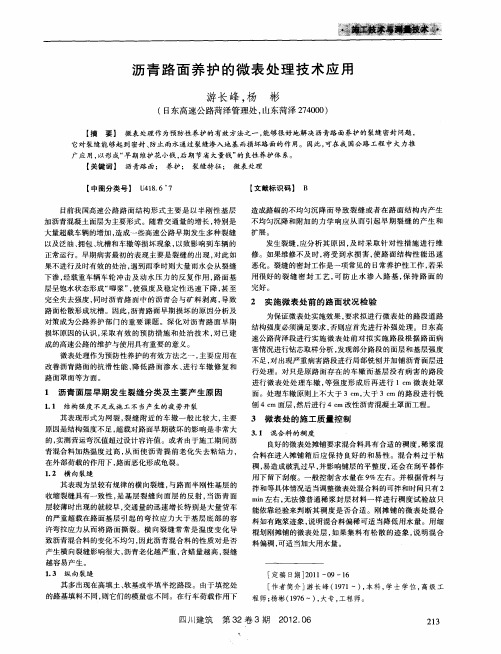
探测与施工难 以并 行。T P超前 预报 系统 , G 为了避免干 扰, 需要停止施工作业 , 才能取得较好 的探 测结果 , 而使施工 不能得 以进行 , 这将影响施工单位的施工进度与效 益。
[ ] 刘云祯 . G 隧道地震波预报系统与技 术 [ ] 5 TP J .物探与化 探 ,
报方法。
[ ] 李术才 , 1 李树忱 , 张庆松 , 岩溶裂 隙水 与不 良地 质情 况超前 等. 预报研究[ ] J .岩石力学与工程学报 ,0 7 2 ( ) 2 0 ,6 2 [ ] 王梦恕 .对岩溶地 区隧道施工水文地质超前预报 的意见 [ ] 2 J.
铁 道 勘 查 , 0 4 1 20 ( )
程 师 ; 彬 (9 6一) 大 专 , 程 师。 杨 17 , 工
其多出现在高填土 、 软基或半填半挖路 段。由于填挖处 的路基填料不同 , 则它们 的模量也不 同。在行 车荷载作用下
四川建 筑
第3 2卷 3期
2 1 .6 0 2 0
23 1
32 .
破 乳 时 间
中 间各 一点 , 具 用 钢 尺 即 可 , 度 必 须 在 要 求 范 围 内 。 在 工 厚
造成路幅的不均匀沉降 而导致裂 缝或者 在路 面结构 内产生 不均匀沉降和附加的力学 响应从 而引起 早期 裂缝 的产 生和
扩展。
加沥青混凝土 面层为主要形式 。随着交通量 的增长 , 特别是 大量超载 车辆 的增加 , 造成一些高速公 路早期发生 多种裂缝 以及泛油 、 拥包 、 坑槽和车辙等损坏现象 , 以致影 响到 车辆 的 正常运行 。早期病 害最初 的表现主要是裂 缝的出现 , 对此如
沥青微表处理工艺
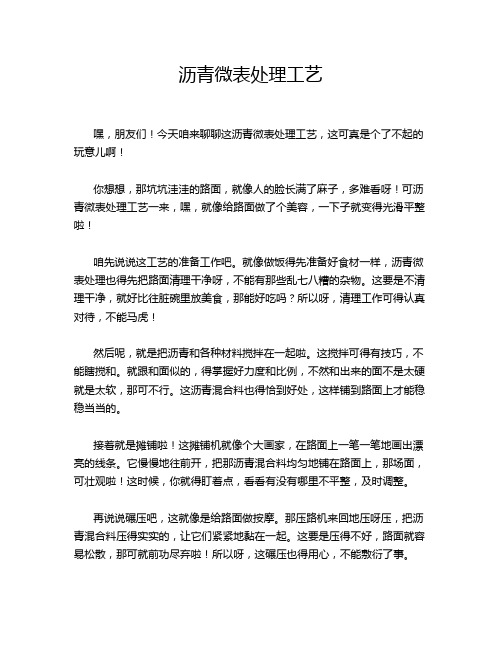
沥青微表处理工艺嘿,朋友们!今天咱来聊聊这沥青微表处理工艺,这可真是个了不起的玩意儿啊!你想想,那坑坑洼洼的路面,就像人的脸长满了麻子,多难看呀!可沥青微表处理工艺一来,嘿,就像给路面做了个美容,一下子就变得光滑平整啦!咱先说说这工艺的准备工作吧。
就像做饭得先准备好食材一样,沥青微表处理也得先把路面清理干净呀,不能有那些乱七八糟的杂物。
这要是不清理干净,就好比往脏碗里放美食,那能好吃吗?所以呀,清理工作可得认真对待,不能马虎!然后呢,就是把沥青和各种材料搅拌在一起啦。
这搅拌可得有技巧,不能瞎搅和。
就跟和面似的,得掌握好力度和比例,不然和出来的面不是太硬就是太软,那可不行。
这沥青混合料也得恰到好处,这样铺到路面上才能稳稳当当的。
接着就是摊铺啦!这摊铺机就像个大画家,在路面上一笔一笔地画出漂亮的线条。
它慢慢地往前开,把那沥青混合料均匀地铺在路面上,那场面,可壮观啦!这时候,你就得盯着点,看看有没有哪里不平整,及时调整。
再说说碾压吧,这就像是给路面做按摩。
那压路机来回地压呀压,把沥青混合料压得实实的,让它们紧紧地黏在一起。
这要是压得不好,路面就容易松散,那可就前功尽弃啦!所以呀,这碾压也得用心,不能敷衍了事。
沥青微表处理工艺还有个好处,就是速度快呀!你想想,要是用传统的方法修个路,那得多久呀,还得封路,多不方便。
但这个工艺呢,很快就能把路修好,不耽误大家通行。
咱平常走在路上,可能不会特别注意路面,但你想想,如果没有这些工艺,那路得烂成啥样呀?我们的出行不就变得困难重重啦?所以说呀,沥青微表处理工艺可真是太重要啦!它就像是路面的保护神,让我们的路一直保持着良好的状态。
我们开车在路上,也会觉得平稳舒服。
这难道不是一件很棒的事情吗?总之呢,沥青微表处理工艺就是个宝,让我们的路面变得又美又好。
我们得感谢那些从事这项工作的人,是他们让我们的出行更加顺畅。
大家说是不是呀?以后再看到那平整的路面,可别忘了这背后的沥青微表处理工艺哦!。
- 1、下载文档前请自行甄别文档内容的完整性,平台不提供额外的编辑、内容补充、找答案等附加服务。
- 2、"仅部分预览"的文档,不可在线预览部分如存在完整性等问题,可反馈申请退款(可完整预览的文档不适用该条件!)。
- 3、如文档侵犯您的权益,请联系客服反馈,我们会尽快为您处理(人工客服工作时间:9:00-18:30)。
引言随着沥青路面使用年限的增加、沥青路面不断老化,病害增加,使用功能不断降低。
适时对沥青路面实施微表处,实践证明是一项较好的预防性养护技术。
微表处作为一种经济、快捷、有效的道路养护新技术,能使原路面焕然一新,形成新的结构层,具有防水、耐磨、抗滑、恢复外观的功能,同时可修复原路面的多种病害,如网裂、车辙、泛油等,且可在常温下作业,施工季节长,摊铺后能迅速开放交通,对道路通行影响小。
研究和总结微表处施工技术及质量控制,对改善沥青路面使用性能、延长其使用寿命、节约投资,具有十分重要的意义。
长期以来人们对早期沥青路面预防性养护的意义认识不足,习惯于在路面出现损坏后才开始进行维护修理。
实践证明,采用适当的配套措施、选择合理的养护手段,加强沥青路面的预防性养护,是保持路面状况良好、延长公路使用寿命的必要前提。
微表处作为预防性养护的有效方法之一,主要应用在改善路面的抗滑性能、降低路面渗水、进行车辙修复等方面。
因微表处厚度仅l cm左右,实施微表处技术不能增加路面抵抗变形的能力,期望1 cm左右厚的微表处能治百病是不现实的。
因此,必须确定一个微表处的合理适用范围,不能什么样的病害路段都用微表处进行处理。
拟实施微表处的路段应满足以下条件:(1)原路面结构强度必须满足要求。
为保证微表处实施效果,就要求拟进行微表处的路段道路结构强度必须满足要求,否则应首先进行补强处理。
应在分析病害成因的基础上选择沥青层挖补、基层翻修甚至路基土的换填等方式进行处理,然后再进行微表处罩面。
以济枣公路为例,在实施微表处前对拟实施路段根据路面病害情况进行钻芯取样分析,发现部分路段的基层强度不足。
据此,对出现严重病害路段进行局部铣刨并加铺沥青面层,然后再在病害处理后的路面上实施微表处。
截止2007年底,该路段微表处使用效果良好。
(2)原路面存在的裂缝、坑槽、龟裂、网裂等病害必须事先进行修补、灌缝处理。
试验证明,原路面上宽度大于5 mm的未处理裂缝、坑槽、龟裂、网裂、严重车辙、拥包、波浪等沥青路面病害,在通车l~2个月左右便会反射到表面上。
(3)当桥面为沥青混凝土铺装时,若路面湿度较大情况下实施微表处工程,因微表处具有封水效果,会将沥青面层的水分封住,在车辆荷载作用下,会加速桥面混凝土的破损。
2.1集料的选择微表处成败与否的关键是集料.由于其功能是制造一个封闭、粗糙的表面,石料的耐磨耗性特别重要。
故微表处所用集料,特别是粗骨料部分应该使用耐磨耗的硬质石料,这与中国对高速公路沥青面层用粗集料应采用耐磨耗的要求相同。
微表处用集料应采用耐磨损的硬质石料,特别是粗骨料部分应该使用耐磨耗的硬质石料。
优质的微表处集料,我们通常采用石灰石、玄武岩石二级破碎料按照一定比例混合后,进行三级破碎,并满足ISSA标准中的Ⅲ型标准级配要求(压碎值<28%;洛杉矶法磨耗值<30%;磨光值>42;磨碎面=100%;细长扁平颗粒含量<10%)规范要求集料的砂当量不低于65%,高于对普通稀浆封层用集料砂当量不低于45%的要求。
也高于规范中高速公路沥青面层用细集料砂当量不小于60%的要求。
对不同砂当量值的集料进行湿轮磨耗试验,结果表明:砂当量越低,混合料的湿轮磨耗值就越大,耐磨耗能力也就越差;砂当量低的集料还可能使改性剂无法发挥改性效果;因此微表处用集料砂当量不宜低于65%。
微表处使用的集料要求坚硬、耐磨的石料,并满足规范要求。
粗集料(4.75-9.5mm)选用硬质的玄武岩石料以确保微表处的抗滑能不会随使用期限的延长而迅速衰减;4.75mm以下部分采用洁净、针片状含量少的石灰岩石屑,以改善沥青与石料的粘结,降低材料成本。
材料试验结果如下:表2.1 粗集料性能试验结果表2.2 细集料性能试验结果2.2胶乳改性剂的选择微表处混合料大多选用胶乳改性剂。
其中最为常用的是SBR胶乳。
胶乳改性剂的加入,一方面改善了沥青本身的高温稳定性和低温延伸性,同时又可以增进沥青与石料之间的裹附性能,改善混合料的耐磨耗能力。
研究表明,国外知名厂家生产的沥青改性专用SBR胶乳(用量3%)可以使乳化沥青蒸发残留物的针入度降低20%~30%,软化点增高5℃~7℃,5 ℃延度增至80cm以上.混合料的湿轮磨耗值减少20%以上。
对乳化沥青和微表处混合料均表现出好的改性效果。
各项性能指标见下表:表2.3 改性乳化沥青性能指标3、微表处混合料的设计3.1矿料级配微表处级配宜粗不宜细。
随着微表处使用期的延长,最初外观表现较好,级配较细的微表处,出现抗滑功能不足的问题,而最初表观粗糙的微表处,不仅外观效果变得美观,而且保持了良好的抗滑性能。
因此,微表处用于交通量大、重载车多的高速公路时,不宜采用Ⅱ型级配,而应采用Ⅲ型级配。
交通量特别大的,级配曲线宜在Ⅲ型级配范围中值与下限之间。
根据集料筛分结果,粗集料与细集料按照1:3的比例掺配,合成级配满足微表处MS-3型级配要求,集料筛分结果见表:表3.1 集料筛分结果3.2油石比的确定3.2.1混合料设计时,应根据实际情况选择合理的油石比1)原路面情况。
如果原路面有泛油,特别是对于采用以前高标号沥青的,微表处材料层可以采用较小的油石比;如果原路面贫油。
或者原路面沥青老化较严重时,可以考虑采用稍大的油石比;原路面表面层空隙率大或渗水严重的,宜采用稍大的油石比。
2)交通量的大小。
交通量大,微表处应采用较小的油石比;交通量较小的,微表处可以采用相对较大的油石比。
3)高温季节微表处施工,油石比宜小不宜大。
3.2.2允许的油石比范围内,微表处混合料的油石比宜小不宜大按照确定的矿料配合比,以及《路面稀浆封层施工规程》(CJJ66-95)推荐油石比范围,选择6.0%、7.0%、8.0%、9.0%、10.0%五种油石比,对MS-3进行湿轮磨耗试验和负荷车轮试验,湿轮磨耗试验确定沥青的最低用量,负荷车轮试验确定沥青的最佳用量。
3.2.3最佳用水量的确定通过粘稠度试验可以检验施工的和易性,确定微表处混合料的最佳用水量为:5.0%。
3.2.4试验配合比通过湿轮磨耗试验和负荷车轮试验确定最佳用油量为MS-3混合料为7.5%(沥青占矿料的百分比含量),该改性乳化沥青的固含量为62.6%,所以最佳改性乳化沥青用量为12.0%。
微表处混合料技术指标如下:表3.2 混合料技术指标表3.3混合料配合比3.2.5 稀浆混合料试验3.2.5.1 可拌和时间试验(Mix Time Test)可拌和时间试验是模拟摊铺施工现场的工作状况,通过该试验来确定乳化沥青的基本配方。
可拌和时间的长短与沥青、乳化剂性能、乳化剂用量、乳化效果、集料性能、温度等有直接的关系,当沥青、集料、温度已相对确定的前提下,可以通过改变乳化剂的品种或乳化剂用量或皂液的PH 值或添加其它化学物质的方法来获得最佳的可拌和时间。
按ISSA 的规定及大量实践证明,在温度为250C 条件下,拌和时间必须大于120 秒。
3.2.5.2 内聚粘结力试验(Cohesion Test)内聚粘结力试验可以测定微表处的凝固速度,确定其初凝时间和开放交通时间。
粘结力-时间曲线与改性乳化沥青的配方、混合料的配比、气候温度、摊铺厚度等有关。
当气候温度、摊铺厚度等预先假定的条件下,可通过改变改性乳化沥青的配方和混合料的配比来选择最合理的粘结力-时间曲线。
在ISSA 的技术规范中,将稀浆混合料(包括稀浆封层和微表处混合料)分为慢凝慢开放交通型、快凝慢开放交通型、假凝慢开放交通型、快凝快开放交通型和直线开放交通型。
3.2.5.3 湿轮磨耗试验(简称WTAT)(Wet track abrasion test)将拌和好的混合料制成直径大约30cm 左右的试件,成型后放入烘箱中,烘干后取出冷却至室温,称重(干重),之后放入250C±30C 的水中浸泡6 天(稀浆封层浸泡1 天),然后在湿轮磨耗机上磨5min,清洗表面碎屑,再放入600C 的烘箱中烘至恒重,于室温中冷却,然后称重,计算出试样磨耗前后重量的差值。
WTAT 的结果以每平方米磨耗的克数表示之。
这项试验是检验稀浆混合料质量的重要项目,它模拟汽车轮胎对路面在潮湿状态下的耐磨耗情况,重点是检验沥青乳液用量、骨料质量、填料与水等配合比的设计。
3.2.5.4 荷载车轮试验LWT(Load Wheel test)该项试验是用稀浆混合料制成5×35cm 的试件,在试件上选6 个点,放在荷载车轮试验仪上,在荷重56.7kg 车轮下辗压1000 次,碾压频率为44 次/分钟,碾压1000 次后看6 个点的长、宽、高的变化。
辗压后称重,然后再放回车轮试验仪上,向试体表面上撒砂(820C),碾压100 次后,再取下试样称重(去掉松散砂子),减去原重即为砂的粘附量。
LWT 试验是检验稀浆混合料中沥青用量是否有过多现象。
WTAT 试验中,随着沥青用量增加,磨耗值有降低的趋势。
但是,沥青用量过多,路面行车后将引起车辙和油包,为了防止路面出现过软现象,对稀浆混合料进行荷载车轮试验,从而得出稀浆混合料最理想的沥青用量(即乳化沥青用量)。
以上的WTAT 和LWT 两项试验,对于稀浆混合料中的沥青含量可以起到相互制约的作用,应在满足这两项指标的前提下,选择其中最佳方案。
3.2.5.5 水敏感度试验将 2.36mm 以下的混合料压实成直径为5cm 左右的圆柱型试件,在水中浸泡六天后,再放入仪器中装水冲刷3 小时,取出再煮半个小时,通过测定其体积和重量的变化,来确定其抗水能力,如抗水性好,试验后的试件不会松散。
而普通稀浆封层不做该项试验。
4.施工方案及工艺4.1原有旧路面的处理通过对原有旧路面的病害调查及分析,我们在微表处施工前分别对裂缝、车辙、龟裂三种病害进行处理。
(1)裂缝处理对0-5㎜裂缝首先采用扫帚和毛刷进行清理,然后用森林灭火器吹掉尘土,再灌改性乳化沥青;对大于5㎜裂缝,待清洁干净后,采用改性乳化沥青混合料填充裂缝。
(2)车辙处理在旧路面上,对深度在12.7㎜以下的轻度车辙,直接进行微表处;对深度大于12.7㎜之间的中度车辙,先用1.4m车辙摊铺箱进行车辙填充,然后再微表处。
(3)龟裂处理根据损坏的不同程度和结构物层次分别采用不同的方法进行挖补处理。
4.2、施工前的准备微表处施工前应做好相应的施工准备工作,主要有以下几个方面:(1)机械的调试和标定;施工前应对施工的专用机械进行调试和标定。
调试:改性稀浆封层机的计量、行车、拌和、摊铺、清洗等各个系统进行调试检查。
标定:在每次施工和更换某种材料,设备中各种料仓出料应进行标定,以求微表处混合料的比例达到配合比。
(2)交通管制:为保证施工安全,应对施工路段进行交通管制,设置标志牌、限速标志及锥形帽,条件许可时就封闭交通施工。
(3)清洁原路面:若原路面不干净,应用高压水枪清洗干净。