锻压成形设备概述
锻压机原理

锻压机原理锻压机是一种常见的金属加工设备,主要用于对金属材料进行锻造加工。
它利用压力对金属材料进行塑性变形,从而改变其形状和内部组织结构。
锻压机的工作原理是通过施加压力使金属材料发生塑性变形,从而实现对金属材料的加工和成形。
下面将详细介绍锻压机的工作原理。
首先,锻压机的工作原理是基于金属材料的塑性变形特性。
金属材料在一定温度和压力下会发生塑性变形,这是由于金属材料的晶粒在受力作用下发生滑移和再结晶现象。
锻压机利用这一特性,通过施加压力使金属材料发生塑性变形,从而实现对金属材料的加工和成形。
其次,锻压机的工作原理是通过机械传动系统实现对金属材料的加工。
锻压机通常由机架、滑块、上模、下模和传动系统等部件组成。
在工作时,传动系统通过电机驱动使机架上的滑块做往复运动,从而带动上模对金属材料进行压力加工。
通过控制传动系统的运动速度和压力大小,可以实现对金属材料的精确加工和成形。
另外,锻压机的工作原理还涉及加热和冷却系统。
在进行锻造加工时,金属材料通常需要在一定温度范围内进行加热处理,以提高其塑性和降低变形阻力。
而在加工完成后,还需要对金属材料进行冷却处理,以使其内部组织结构得以稳定和固化。
因此,锻压机通常配备有加热炉和冷却装置,以实现对金属材料的加热和冷却控制。
最后,锻压机的工作原理还涉及对金属材料的成形和变形控制。
在进行锻造加工时,需要根据金属材料的性质和加工要求,选择合适的成形工艺和工艺参数,以实现对金属材料的精确加工和成形。
而在加工过程中,还需要对金属材料的变形过程进行监测和控制,以确保加工质量和成形精度。
综上所述,锻压机的工作原理是基于金属材料的塑性变形特性,通过机械传动系统实现对金属材料的加工,涉及加热和冷却系统以及对金属材料的成形和变形控制。
了解锻压机的工作原理有助于我们更好地掌握其操作技巧和加工要点,提高加工效率和产品质量。
锻压设备概述

锻压设备概述锻压设备具有高效、高精度、高稳定性的特点,能够有效提高金属材料的强度和硬度,并且能够保持工件的内部结构不变。
因此,在航天航空、汽车制造、机械制造等领域都有广泛的应用。
随着科技的发展,现代化的锻压设备通过自动化、智能化等技术的应用,使得生产效率得以提高,质量得以保证,生产成本得以降低。
总的来说,锻压设备在金属加工领域中起着重要的作用,对提高产品质量、促进工业发展具有重要作用。
随着技术的不断进步,锻压设备的生产制造技术和产品性能也将不断提高和改善,这将进一步推动金属加工产业的发展。
锻压是一种常见的金属加工方法,通过锻压设备可以将金属坯料以较高的压力和速度进行塑性变形,使其形成所需的形状和尺寸。
锻压设备的应用范围广泛,可以用于生产汽车零部件、工程机械、航空航天部件、铁路设备等各种领域的产品。
锻压设备可以分为液压锻压机和机械式锻压机两大类。
液压锻压机利用液压传动和液压缸来实现材料的成形加工,具有液压系统压力调节方便、操作灵活等特点,适用于大型复杂构件的锻造。
机械式锻压机则通过机械传动来实现压力和速度的控制,适用于小中型零部件的锻造。
现代化的锻压设备具备自动化控制、数字化操作、智能化监控等功能,能够提高生产效率和产品质量。
在锻压设备的操作中,需要注意保证设备的安全性和稳定性,以防止发生意外事故。
操作人员需要具备针对锻压设备的专业知识和技能,严格按照操作规程进行操作,遵守相关安全操作规定。
另外,锻压设备的维护和保养也是至关重要的,及时检查设备的润滑、密封、电气系统等部件,以保证设备的正常运行。
锻压设备在工业生产中具有重要作用,它能够提高金属件的综合性能,改善内部晶粒组织,提高材料的密度和均匀性。
与其他加工方法相比,锻压设备在提高产品强度、改善材料性能、减少材料损耗等方面具有独特优势。
随着工业化进程的不断推进,锻压设备在国家经济发展中扮演着至关重要的角色。
它不仅是制造业的重要装备,也是实现国家产业升级和技术进步的重要手段。
流行锻压基本工艺及设备简介
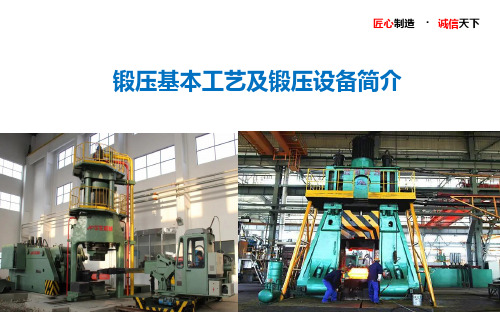
3~4工程
3~4工程 4.热处理
5.后处理
5. 表面处理
Ⅰ.概述
匠心制造 . 诚信天下
a.自由锻造
自由锻造是利用冲击力或后力使金属在上下平面各个方向变形, 不受任何限制而获得形状及尺寸和一定机械性能的加工方法。 (精度要求不高)
b.精密锻造
精密锻造是利用精密模具通 锻压机使材料产生塑性 变形而达到 产品形状及尺寸的一种加工方法。(精度高)--手机手表应用广泛
内外径精度
偏芯 脱炭层 表面粗造度 金属组织
冷锻造
±0.1~±0.25 ±0.02 ~±0.2 0.02~0.15 <0.1 <0.8Ra (6S)
微细
温锻造
±0.1~±0.4 ±0.1 ~±0.2 0.1~0.4
<0.2 <2.5Ra (10S)
微细
热锻造
±1~±2
±0.5 ~±1 0.7~1.0
Ⅰ.概述
匠心制造 . 诚信天下
锻压分为开式锻压和闭式锻压;又分为冷锻,热锻,温锻。又分为自由锻 和精密模锻。
名称
简图
说明
冷锻压是在低于金属再结晶温度下进行的锻压,通常所说的冷锻
压多专指在常温下的锻压,而将在高于常温、但又不超过再结晶
冷锻
温度下的锻压称为温锻压。温锻压的精度较高,表面较光洁而变
形抗力不大。
Ⅰ.概述
5.锻压工艺辅助工序有哪些?
a.不锈钢产品有退火 热处理工艺 b.铝合金有固溶/时效等热处理工艺 c.铜 钛产品有热压 加热炉 热处理工艺 d.皮膜表面处理工艺 e.表面抛光处理工艺
匠心制造 . 诚信天下
锻压成型的特点
匠心制造 . 诚信天下
(1) 改善金属的组织,提高金属的力学性能 与物理性能;
锻压设备
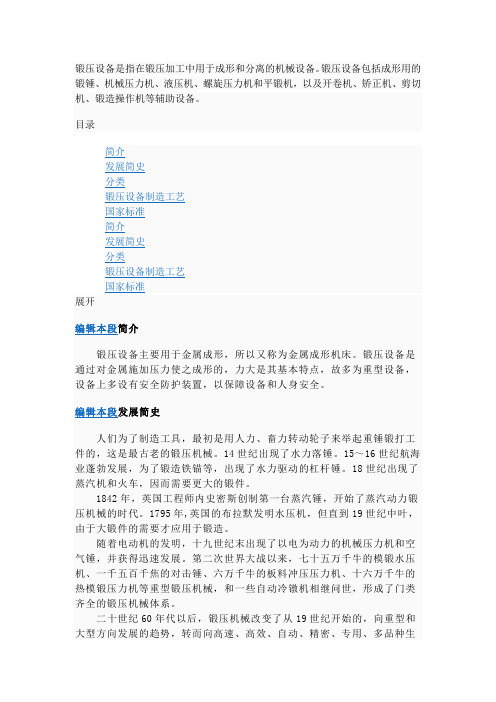
锻压设备是指在锻压加工中用于成形和分离的机械设备。
锻压设备包括成形用的锻锤、机械压力机、液压机、螺旋压力机和平锻机,以及开卷机、矫正机、剪切机、锻造操作机等辅助设备。
目录简介发展简史分类锻压设备制造工艺国家标准简介发展简史分类锻压设备制造工艺国家标准展开编辑本段简介锻压设备主要用于金属成形,所以又称为金属成形机床。
锻压设备是通过对金属施加压力使之成形的,力大是其基本特点,故多为重型设备,设备上多设有安全防护装置,以保障设备和人身安全。
编辑本段发展简史人们为了制造工具,最初是用人力、畜力转动轮子来举起重锤锻打工件的,这是最古老的锻压机械。
14世纪出现了水力落锤。
15~16世纪航海业蓬勃发展,为了锻造铁锚等,出现了水力驱动的杠杆锤。
18世纪出现了蒸汽机和火车,因而需要更大的锻件。
1842年,英国工程师内史密斯创制第一台蒸汽锤,开始了蒸汽动力锻压机械的时代。
1795年,英国的布拉默发明水压机,但直到19世纪中叶,由于大锻件的需要才应用于锻造。
随着电动机的发明,十九世纪末出现了以电为动力的机械压力机和空气锤,并获得迅速发展。
第二次世界大战以来,七十五万千牛的模锻水压机、一千五百千焦的对击锤、六万千牛的板料冲压压力机、十六万千牛的热模锻压力机等重型锻压机械,和一些自动冷镦机相继问世,形成了门类齐全的锻压机械体系。
二十世纪60年代以后,锻压机械改变了从19世纪开始的,向重型和大型方向发展的趋势,转而向高速、高效、自动、精密、专用、多品种生产等方向发展。
于是出现了每分种行程2000次的高速压力机、六万千牛的三坐标多工位压力机、两万五千千牛的精密冲裁压力机、能冷镦直径为48毫米钢材的多工位自动冷镦机和多种自动机,自动生产线等。
各种机械控制的、数字控制的和计算机控制的自动锻压机械以及与之配套的操作机、机械手和工业机器人也相继研制成功。
现代化的锻压机械可生产精确制品,有良好的劳动条件,环境污染很小。
编辑本段分类锻压设备指在锻压加工中用于成形和分离的机械设备,锻压设备包括成形用的锻锤、机械压力机、液压机、螺旋压力机和平锻机,以及开卷机、矫正机、剪切机、锻造操作机等辅助设备。
锻压机的工作原理
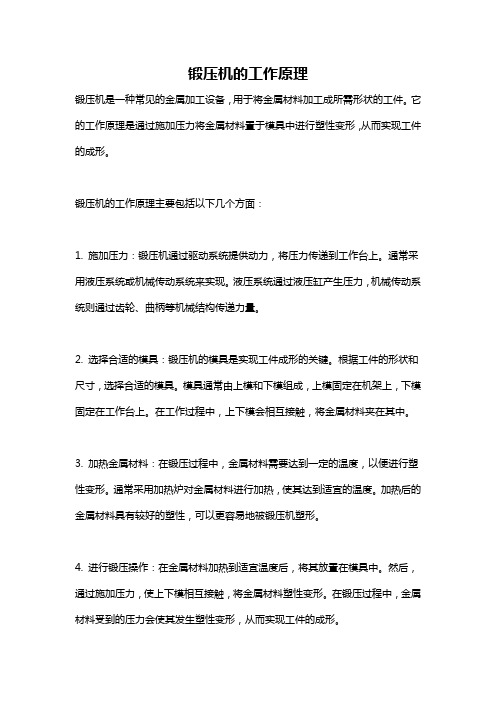
锻压机的工作原理锻压机是一种常见的金属加工设备,用于将金属材料加工成所需形状的工件。
它的工作原理是通过施加压力将金属材料置于模具中进行塑性变形,从而实现工件的成形。
锻压机的工作原理主要包括以下几个方面:1. 施加压力:锻压机通过驱动系统提供动力,将压力传递到工作台上。
通常采用液压系统或机械传动系统来实现。
液压系统通过液压缸产生压力,机械传动系统则通过齿轮、曲柄等机械结构传递力量。
2. 选择合适的模具:锻压机的模具是实现工件成形的关键。
根据工件的形状和尺寸,选择合适的模具。
模具通常由上模和下模组成,上模固定在机架上,下模固定在工作台上。
在工作过程中,上下模会相互接触,将金属材料夹在其中。
3. 加热金属材料:在锻压过程中,金属材料需要达到一定的温度,以便进行塑性变形。
通常采用加热炉对金属材料进行加热,使其达到适宜的温度。
加热后的金属材料具有较好的塑性,可以更容易地被锻压机塑形。
4. 进行锻压操作:在金属材料加热到适宜温度后,将其放置在模具中。
然后,通过施加压力,使上下模相互接触,将金属材料塑性变形。
在锻压过程中,金属材料受到的压力会使其发生塑性变形,从而实现工件的成形。
5. 控制锻压参数:在锻压过程中,需要对锻压机的参数进行控制,以确保工件的质量和成形效果。
例如,需要控制施加的压力大小、锻压速度、保持时间等。
这些参数的选择与工件的材料、形状和尺寸有关。
锻压机的工作原理可以简单总结为:通过施加压力将金属材料置于模具中进行塑性变形,从而实现工件的成形。
在工作过程中,需要选择合适的模具、加热金属材料、控制锻压参数等。
锻压机在金属加工领域具有广泛的应用,可以用于制造各种工件,如汽车零部件、航空零件、机械零件等。
锻造设备介绍

锻造设备介绍摘要:一、引言二、锻造设备的分类与介绍1.热锻设备2.冷锻设备3.精密锻造设备4.大型锻造设备5.数控锻造设备三、锻造设备的选择与应用1.依据锻造工艺选择设备2.考虑锻造设备的技术参数3.关注设备的安全性与稳定性四、锻造设备的管理与维护1.设备日常维护2.定期检查与维修3.操作人员的培训与管理五、展望锻造设备的发展趋势1.高度智能化2.高效率与节能3.绿色环保正文:一、引言锻造作为一种重要的金属成型工艺,在我国工业发展中占有举足轻重的地位。
锻造设备是锻造工艺的核心组成部分,其性能和技术水平直接影响到锻造产品的质量和生产效率。
为了更好地了解锻造设备,本文将对锻造设备的分类、选择、管理及发展趋势进行详细介绍。
二、锻造设备的分类与介绍1.热锻设备热锻设备主要用于金属在高温下进行的锻造加工。
这类设备包括热锻锤、热模锻压力机、热挤压机等。
热锻设备具有良好的锻造性能,可以获得较高的锻件精度和表面质量。
2.冷锻设备冷锻设备主要用于金属在室温下进行的锻造加工。
这类设备包括冷锻锤、冷模锻压力机、冷挤压机等。
冷锻设备具有较高的生产效率和节能效果,适用于大批量生产。
3.精密锻造设备精密锻造设备主要用于生产高精度、高品质的锻造件。
这类设备包括精密压力机、精密锻造锤等。
精密锻造设备具有高精度、高速度、高稳定性等特点,可以满足各类复杂零件的锻造需求。
4.大型锻造设备大型锻造设备主要用于生产大型、重型锻造件。
这类设备包括大型压力机、大型锻造锤等。
大型锻造设备具有较大的锻造力、宽泛的加工范围,可满足各类大型零件的锻造需求。
5.数控锻造设备数控锻造设备是采用现代数控技术进行控制的锻造设备。
这类设备具有高精度、高效率、易操作等特点,适用于各类锻造工艺的生产。
三、锻造设备的选择与应用1.依据锻造工艺选择设备在选择锻造设备时,首先要根据锻造工艺的要求进行选择。
不同的锻造工艺对应着不同的设备类型,如热锻、冷锻、精密锻造等。
2.考虑锻造设备的技术参数在选择锻造设备时,要充分考虑设备的技术参数,如锻造力、加工范围、生产效率等。
锻压设备通用操作规程

锻压设备通用操作规程一、设备概述锻压设备是用于金属材料的加工设备,其工作原理为利用机械力将金属材料置于特定的模具中,通过切削或挤压等方式,将材料塑形成所需的形状。
根据不同的用途和需求,锻压设备分为很多种类和规格。
二、操作前准备1. 检查设备的电源、水源和气源是否充足,有无异常。
2. 检查温度是否适宜,如果设备处于高温状态,必须等待设备冷却后方可操作。
3. 检查设备各部分安全装置是否完好。
如未安装或故障,禁止操作设备。
4. 检查刀具、模具、测量工具等是否齐全,完好。
5. 按照设备使用说明书对润滑、清理设备进行操作。
6. 操作工人应熟知设备的构造和操作流程,若员工不熟悉设备操作流程,请经过正式培训后方可操作。
三、操作流程1.待锻压设备就绪后,按下设备的开机按钮,在设备显示屏上能够看到开机成功的提示信息。
2.将需要加工的金属材料放入设备内部,并固定好。
3.根据需要设定不同的参数,如加工速度、加工力度等,确保设备能够达到预期的加工效果。
4.启动设备,开始加工金属材料。
5.观察加工状态,在加工过程中时刻关注设备的变化,如有异常立即停机检查。
6.加工结束后,使用测量工具对产品进行测量,确保其符合要求。
7.清理设备并关机,将剩余材料和垃圾进行清理。
四、安全注意事项1.在设备开机期间禁止工作人员接近或触摸设备。
2.平时需对设备进行定期检查,确保各种安全装置、传感器等设备正常运作。
3.工作人员在操作期间应穿戴好防护装备,如手套、吸尘面罩等。
4.操作前必须确认模具和刀具是否安装完好,避免操作期间发生意外。
5.加工金属材料前必须检查材料是否干净、油脂或其他物质是否清理干净,避免材料加工过程中出现异常。
6.根据设备的使用说明书要求,定期对设备进行保养和维护。
五、结语锻压设备是金属加工行业中非常重要的设备之一,操作时一定要注意安全,并按照操作流程进行操作,在日常保养和维护方面也要做好相关工作,以确保设备长时间稳定运行,保障加工产品的质量。
材料成形设备

材料成形设备一、锻压机锻压机是锻压设备的核心,它是通过液压或机械传动,使模具产生一定的压力和速度,使工件形变达到所需的形状和尺寸。
根据其工作特性,锻压机可以分为冷锻机、热锻机、自由锻机、精密锻机、多项式锻机等。
冷锻机主要用于对硬度较低或熔点较高的金属材料进行冷加工,如低碳钢、铝合金等,在常温下进行成形。
热锻机主要用于对硬度较高或熔点较低的金属材料进行热加工,如高碳钢、合金钢、铁合金等,需要在一定的温度下进行成形。
自由锻机可以在任意方向进行成形,无需固定模具,操作灵活,广泛应用于工件的初步成形和粗糙加工。
精密锻机主要用于高精度和复杂形状的工件,在锻压过程中可以精确控制力、速度和位移,以达到精确成形。
多项式锻机可以在一个工序中完成多个成形工序,提高生产效率和产品质量。
二、模具模具是锻压设备的重要工具,它主要包括冲头、凹模、凸模、铲模、吹气动化模等。
冲头主要用于压入工件中,使其产生一定的形状和尺寸。
凹模和凸模是对应的一对模具,通过凸模对工件施加压力,使其在凹模中形变,形成所需的形状和尺寸。
铲模主要用于剪切、切断或拉伸工件,以达到所需的形状和尺寸。
吹气动化模主要用于金属粉末冶金,通过气流将粉末均匀吹入模具内,然后通过锻压机进行压实,形成所需的形状和尺寸。
三、锻压工艺锻压工艺是根据工件的材料性能、结构形状、尺寸精度和生产规模,选择合适的锻压设备和模具,设计出的生产过程。
在锻压工艺中,要充分考虑工件的材料性能,如硬度、韧性、塑性、热膨胀系数等,以选择合适的锻压温度和速度。
同时,还要考虑工件的结构形状,如壁厚、孔径、曲率半径等,以设计合适的模具。
对于尺寸精度要求高的工件,还要进行精密锻压,或在锻压后进行切削、研磨等后续加工。
对于生产规模大的工件,可以使用多项式锻机,提高生产效率。
综上,材料成形设备(锻压)是通过锻压机和模具,通过冷、热的锻压来实现对工件的加工成形,以达到所需的形状、尺寸和精度,为各行业的机械制造提供关键的生产工具和工艺。
锻造设备介绍
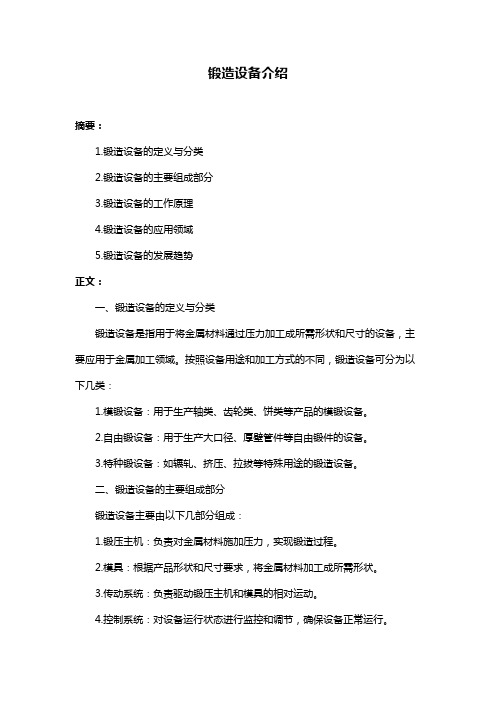
锻造设备介绍摘要:1.锻造设备的定义与分类2.锻造设备的主要组成部分3.锻造设备的工作原理4.锻造设备的应用领域5.锻造设备的发展趋势正文:一、锻造设备的定义与分类锻造设备是指用于将金属材料通过压力加工成所需形状和尺寸的设备,主要应用于金属加工领域。
按照设备用途和加工方式的不同,锻造设备可分为以下几类:1.模锻设备:用于生产轴类、齿轮类、饼类等产品的模锻设备。
2.自由锻设备:用于生产大口径、厚壁管件等自由锻件的设备。
3.特种锻设备:如辗轧、挤压、拉拔等特殊用途的锻造设备。
二、锻造设备的主要组成部分锻造设备主要由以下几部分组成:1.锻压主机:负责对金属材料施加压力,实现锻造过程。
2.模具:根据产品形状和尺寸要求,将金属材料加工成所需形状。
3.传动系统:负责驱动锻压主机和模具的相对运动。
4.控制系统:对设备运行状态进行监控和调节,确保设备正常运行。
5.辅助设备:如加热炉、冷却系统等,为锻造过程提供必要的条件。
三、锻造设备的工作原理锻造设备的工作原理主要是利用锻压主机对金属材料施加压力,使其产生塑性变形。
在模具的配合下,金属材料经过多次镦粗、拔长等工序,最终形成所需形状和尺寸的产品。
四、锻造设备的应用领域锻造设备广泛应用于航空、航天、汽车、船舶、能源、化工等产业领域。
其中,航空航天和汽车产业对锻造设备的需求最大,因为这两个领域的产品对锻造工艺和设备的要求较高。
五、锻造设备的发展趋势随着科技的进步和各行业对锻造设备需求的不断提高,锻造设备发展趋势如下:1.自动化程度不断提高,减少人工操作。
2.设备性能不断优化,提高生产效率和产品质量。
3.设备结构设计更加合理,降低设备故障率和维修成本。
自动锻压机简介

12.Z12系列双击整模自动冷镦机
压
机
产 品
双击整模自动冷镦机是用于制造螺钉、
分 类
铆钉或其它类似的制品。工件头部用一
个阴模经预镦及成形两次镦锻镦出所需
要的形状。我厂有4mm~16mm规格共7
个品种产品。
一
、
自
动 锻 压
13.Z19系列三击双工位自动冷镦机
机
的BP-440SS和BP-430SS型两个
品种分别冷镦M14和M10螺栓毛
坯及杆形零件。
一
、
自
BP
动
锻
压
机
产
系
品
列
分
螺
类
栓
自
动
冷
镦
机
产品特点:1、生产率高达210件/分 2、机器调整自动化程度高 带有送料系统自动化调整功能 3、高精度
一
、
自
动
锻
压 机
11. MN80型制钉机
产
品 分
引进意大利MORONI莫朗尼技术单击冷镦钉
滚柱自动冷镦机是采用轴承钢棒料
分 类
(或盘料)为原材料,单击制造滚
柱毛坯的高效自动化设备。我厂有
8~25规格共8个品种产品。
一
、
自
动
锻 压 机
2. Z32系列钢球自动冷镦机
产
品
分 类
该系列产品采用轴承钢棒料或
盘料,单击制造钢球毛坯。我
厂有7.5-28规格8个品种产品。
一
、
自
动
锻
压 机
3. Z33系列钢球滚柱自动冷镦机
缩细(25%) :
切 边:
冲 孔: 搓 丝: 及其上述工艺复合等,通常沿原材料 轴向进行镦锻。
锻造压力机的分类及特点分析
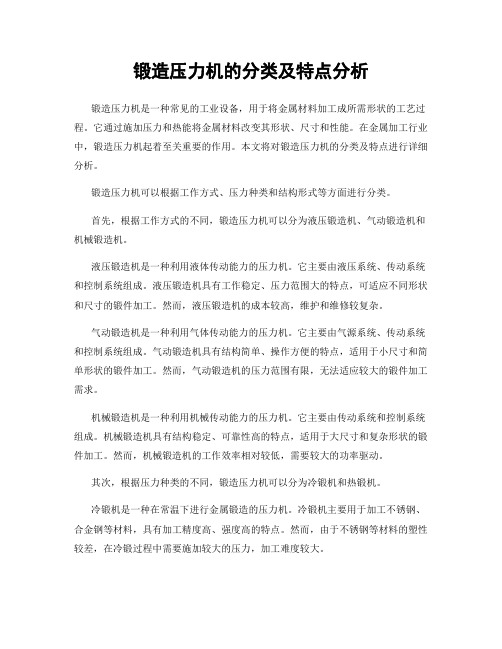
锻造压力机的分类及特点分析锻造压力机是一种常见的工业设备,用于将金属材料加工成所需形状的工艺过程。
它通过施加压力和热能将金属材料改变其形状、尺寸和性能。
在金属加工行业中,锻造压力机起着至关重要的作用。
本文将对锻造压力机的分类及特点进行详细分析。
锻造压力机可以根据工作方式、压力种类和结构形式等方面进行分类。
首先,根据工作方式的不同,锻造压力机可以分为液压锻造机、气动锻造机和机械锻造机。
液压锻造机是一种利用液体传动能力的压力机。
它主要由液压系统、传动系统和控制系统组成。
液压锻造机具有工作稳定、压力范围大的特点,可适应不同形状和尺寸的锻件加工。
然而,液压锻造机的成本较高,维护和维修较复杂。
气动锻造机是一种利用气体传动能力的压力机。
它主要由气源系统、传动系统和控制系统组成。
气动锻造机具有结构简单、操作方便的特点,适用于小尺寸和简单形状的锻件加工。
然而,气动锻造机的压力范围有限,无法适应较大的锻件加工需求。
机械锻造机是一种利用机械传动能力的压力机。
它主要由传动系统和控制系统组成。
机械锻造机具有结构稳定、可靠性高的特点,适用于大尺寸和复杂形状的锻件加工。
然而,机械锻造机的工作效率相对较低,需要较大的功率驱动。
其次,根据压力种类的不同,锻造压力机可以分为冷锻机和热锻机。
冷锻机是一种在常温下进行金属锻造的压力机。
冷锻机主要用于加工不锈钢、合金钢等材料,具有加工精度高、强度高的特点。
然而,由于不锈钢等材料的塑性较差,在冷锻过程中需要施加较大的压力,加工难度较大。
热锻机是一种在高温下进行金属锻造的压力机。
热锻机主要用于加工高温合金、钛合金等材料,具有加工效率高、热变形能力强的特点。
然而,热锻机加工过程中需要控制温度和时间,以避免材料烧结或过热。
最后,根据结构形式的不同,锻造压力机可以分为冲击式锻压机、摆辊式锻压机和摆架式锻压机。
冲击式锻压机是一种通过高速下落的压头对工件进行冲击的压力机。
冲击式锻压机主要用于大型锻件的成型,具有冲击力大的特点。
锻压成形及锻件毛坯概述
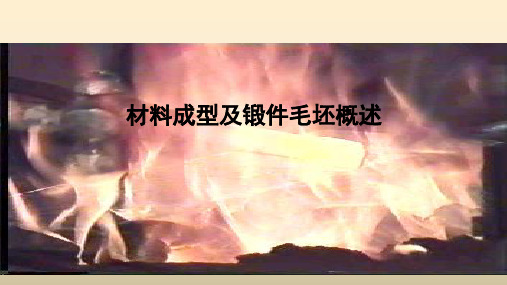
毛坯类型 材料利用率 生产周期 生产成本
主要适用范围
受力不大或承压为主的 主要用于制造各种金属 零件,或要求减震、耐 结构,部分用于制造零 件毛坯 磨的零件;球铁、铸钢、 铝、铜合金用于重载或 复杂载荷零件 机架、床身、底座、工 作台、导轨、变速箱、 泵体、阀体、带轮、轴 承座、曲轴、齿轮等
形状简单的零件
锻件的特点
锻造通常是在高温(再结晶温度以上)下进行的,因此也称热锻。锻造加工获得 的产品称为锻件,广义上的锻件还包含部分热轧、热挤的产品,比如环形锻件毛坯, 六角头螺栓毛坯等。
世界上最大的钛合金锻件— —中机身隔框
锻造铝合金轮毂
世界最大船用曲轴
1.材料成型方法概述 锻件由于是压力的作用下成形,可以将坯料中的疏松处压合,提高金属的致密 度;可以击碎高合金工具钢中的碳化物,并使其均匀地分布;可以使粗大的晶粒细 化并形成具有一定方向性的纤维组织(金属流线),因此锻件的机械性能明显比同 成分的铸件或机加工件高。
24
国内大型模锻液压机
中国大飞机关键支撑装备——8 万吨航空模锻液压机,位于大型 运输机总装地和大型客机主要研 发生产地——西安阎良国家航空 产业基地 大飞机工程配套的大型模锻液压 机项目——苏州昆仑先进制造技 术装备有限公司正式落户周市 镇 ,压力10万吨。
25
26
谢谢!
(2)毛坯的结构特征
形状复杂件,特别是有复杂内腔的毛坯,只能用铸造的方法获得。圆饼、 方块、套环、齿轮等形状简单的零件,可以采用自由锻工艺;外形较为复杂, 并且表面质量要求较高时,则要采用胎膜锻或模锻完成。
1.材料成型方法概述
C. 经济性原则
(1)生产批量较小时 生产批量较小时,毛坯生产的生产率不是主要问题,材料利用率的 矛盾也不太突出,这时应主要考虑的总是是减少设备、模具等方面的投资,即使用 价格比校便宜的设备和模具,以降低生产成本。如使用型材、砂型铸造件、自由锻 件、胎模锻件、焊接结构件等作为毛坯。
材料成形设备

材料成形设备
锻压成形设备
锻压是指将金属材料在挤压机上进行挤压成形的一种加工方法。
它是
一种金属材料的热处理方法,常用于制造汽车、摩托车、拖拉机等复杂形
状的部件和零件。
精密度高、成型效率高,是汽车、摩托车、拖拉机等行
业中常用的金属成形方式之一
锻压成形设备又称作挤压机,它是用来把金属材料经过膨胀压力形成
一定形状的物体的设备。
它由一个油缸、锻压机床头、锻压模具、电控系统、运输系统和其他辅助设备组成。
锻压成形设备油缸的功能是把能量从机床传递到锻压模具中,它可以
是气缸、油缸、气压缸或者其他形式。
一般来说,油缸的容量和压力越大,锻压力越大,成形效果也越好。
锻压成形机床头是锻压成形设备的核心部件,它决定着设备的性能和
生产效率,能够直接影响机器的成形精度。
从构造上讲,机床头由滑块、
连接座、滑块衬板和调整柱组成,利用电机带动滑块的上下作用力,对锻
件进行挤压成形。
锻压模具是锻压成形设备的重要组件,由两个或多个锻压模构成,它
能够把金属材料挤压成各种复杂形状的零件和组件,要求模具设计要精确,模具制作要有质量保证,以确保材料正确无误地被挤压成型。
4000吨锻压机参数
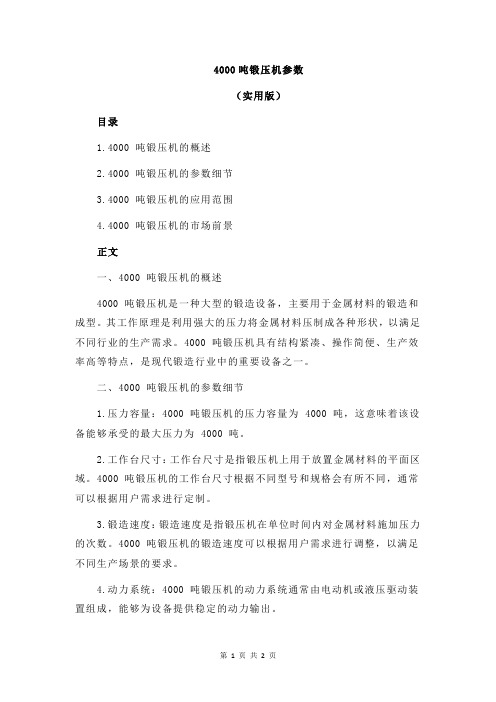
4000吨锻压机参数(实用版)目录1.4000 吨锻压机的概述2.4000 吨锻压机的参数细节3.4000 吨锻压机的应用范围4.4000 吨锻压机的市场前景正文一、4000 吨锻压机的概述4000 吨锻压机是一种大型的锻造设备,主要用于金属材料的锻造和成型。
其工作原理是利用强大的压力将金属材料压制成各种形状,以满足不同行业的生产需求。
4000 吨锻压机具有结构紧凑、操作简便、生产效率高等特点,是现代锻造行业中的重要设备之一。
二、4000 吨锻压机的参数细节1.压力容量:4000 吨锻压机的压力容量为 4000 吨,这意味着该设备能够承受的最大压力为 4000 吨。
2.工作台尺寸:工作台尺寸是指锻压机上用于放置金属材料的平面区域。
4000 吨锻压机的工作台尺寸根据不同型号和规格会有所不同,通常可以根据用户需求进行定制。
3.锻造速度:锻造速度是指锻压机在单位时间内对金属材料施加压力的次数。
4000 吨锻压机的锻造速度可以根据用户需求进行调整,以满足不同生产场景的要求。
4.动力系统:4000 吨锻压机的动力系统通常由电动机或液压驱动装置组成,能够为设备提供稳定的动力输出。
5.控制系统:4000 吨锻压机的控制系统是指用于控制设备运行的系统,通常包括操作面板、PLC 控制系统等,用户可以通过控制系统对设备进行操作和监控。
三、4000 吨锻压机的应用范围4000 吨锻压机广泛应用于各种金属材料的锻造和成型领域,如航空航天、汽车制造、船舶制造、电力设备制造等。
在这些行业中,4000 吨锻压机主要用于制造各种锻件、齿轮、轴类零件等。
四、4000 吨锻压机的市场前景随着我国经济的持续发展,装备制造业和锻造行业的需求不断增长,4000 吨锻压机的市场前景十分广阔。
- 1、下载文档前请自行甄别文档内容的完整性,平台不提供额外的编辑、内容补充、找答案等附加服务。
- 2、"仅部分预览"的文档,不可在线预览部分如存在完整性等问题,可反馈申请退款(可完整预览的文档不适用该条件!)。
- 3、如文档侵犯您的权益,请联系客服反馈,我们会尽快为您处理(人工客服工作时间:9:00-18:30)。
1、汽车发动机的进、排气阀,过去在空气锤上用胎模锻生产,现在采用六工位电热镦机和专用机械压力机组成的电镦自动线进行生产,使材料利用率由原来的40~50%提高到80~85%,生产效率提高40倍以上,劳动强度大大降低,工作条件得到改善,零件质量也有所提高。
2、1955年世界上第—台数控(NC)冲模回转头压力机在英国问世之后,揭开了塑性成形设备技术发展史上新篇章。
3、1970年,第一台计算机控制(CNC)的冲模回转头压力机研制成功,数控技术很快在各类塑性成形设备中得到应用。
4、塑性成形设备采用的数控系统有点位控制的,也有轮廓控制的;有单功能的,也有多功能的;有单轴的,也有多轴的。
5、我国现已开发了数控冲模回转头压力机、数控步冲——冲孔压力机、CNC弯管机、数控三点式板料折弯机、各类数控液压机等。
6、高速机械压力机1975年德国舒勒公司生产的A2-80型800KN 高速压力机,行程次数为600次/min,现在同类型压力机已达900次/min,有的公司高速压力机的行程次数甚至高达2500~3000次/min。
高速压力机的精度大为提高,一些高速压力机冲压件的精度达±0.01mm。
7、快速液压机快速液压机是1970年代中期开发的。
英国Norton 公司生产的60kN快速液压机的最高行程次数达1000次/min。
8、大型板料加工压力机由于汽车及电器工业发展的需要,大型板料压力机迅速发展。
德国米勒万家顿公司向比利时提供了1台62000KN 多工位压力机。
整套设备长60m,高18m,总重3800吨,该机于1992年投产运行,可加工1700mm×3500mm的板料,每分钟可加工14个汽车车
身件。
目前世界上大约有200台大型多工位压力机在运行使用中。
我国济南第二机床厂开发的J47—1250/2000型四点双动拉深压力机是目前我国最大规格的双动压力机,其内滑块公称压力为12500kN,外滑块公称压力为7500kN,工作台尺寸为4600mm×2500mm。
9、激光与等离子切割机械自1970年以来,激光技术和等离子技术开始应用于塑性成形装备,主要用于切割各种金属和非金属板材。
激光冲压复合机,高功率(已发展到5kW)、高精度(由±0.5mm/500mm提高到±0.01mm/500mm)、高柔性和多轴(已发展到5轴)。
10、液压成形装备是材料成形装备的一大类,它是飞机、汽车和拖拉机等工业部门不可缺少的加工设备。
液压成形装备具有一系列特点,能适应不同工艺要求。
当前液压成形装备的发展水平和趋势具体表现在以下几方面:
(1)提高速度和生产率:
现代液压机的空程和回程速度一般都在400mm/s左右,有的甚至更高。
例如:意大利埃马努尔压力机公司的DEA型单动冲压液压机系列,其空程和回程速度为300~650mm/s;德国埃特公司的UR5100型1000kN 快速液压机,其空程和回程速度为400mm/s。
日本川崎机工生产的8000kN多工位液压机,其空程速度达到350mm/s,一台12500kN三工位冷挤压液压机,其行程次数可达12~22次/min。
德国SMG公司制造的用于生产浴盆的液压机自动生产线,由
31500kN和8000kN两台液压机及一台冲孔装置组成,仅由一人监控,其生产率为100件/h。
(2)提高刚度和精度
德国SMG公司对冷挤压液压机,可使滑块的运动精度在300mm行程上保持在0.05mm以内。
(3)高压化和大型化
瑞典通用电器(ASEA)公司生产了用于航空工业的600,000 kN橡胶模式冲压液压机和用于汽车工业的630,000kN橡胶囊式冲压液压机;我国太原重型机器厂生产150,000kN橡胶囊式冲压液压机,40,000kN汽车纵梁冲压液压机。
(4)控制系统的数控化
目前采用可编程序控制器(PLC)控制的液压机和采用计算机数控(CNC)的液压机得到了很大发展。
国内外现代液压机采用CNC的比例正在逐年增加。
(5)液压系统的集成化
(6)电液比例技术的应用
11、液压机与其它材料成形装备相比具有以下特点:
(1)基于液压传动的原理,执行元件(缸及柱塞或活塞)结构简单,结构上易于实现很大的工作压力、较大的工作空间和较长的工作行程,因此适应性强,便于压制大型或较长较高的制件。
(2)在行程的任何位置均可产生压力机额定的最大压力。
(3)可以用简单的方法(各种阀)在一个工作循环中调压或限压,不易超载,模具容易得到保护。
(4)滑块的总行程可以在一定范围内任意改变,滑块行程的下转换点可以根据压力或行程位置来控制和改变。
(5)滑块速度可以在一定范围内进行调节,从而可以适应各种工艺对滑块速度的不同要求。
(6)工作平稳,撞击、振动和噪声较小,对工人健康、厂房基础、周围环境及设备本身都有很大好处。
12、锻造液压机的工艺特点
图3-5是锻造液压机的工作过程曲线。
锻造液压机多用于快锻生产,系统的快速性和平稳性指标十分重要,因此液压伺服系统的设计必须充分考虑其影响因素。
快速性主要受以下几方面的影响:
①下降速度如速度过大,则在动梁突然停止时,将有“水击”现象出现,管道振动很大。
此外由于动梁运动部分质量较大,尤其在下拉式框架结构中,运动部分质量更大,突然停止,还会引起压机振动。
②加压速度提高加压行程速度,能减少工作循环时间,并减少上砧与热锻件接触时间,但这样会使液压机传动功率成比例地增加,很不经济。
③回程速度如速度变化太大,在行程很小时,由于惯性引起的冲击和位置超程也就较大。
④建压时间由于工作液体、管道、工作缸及立柱等都是弹性体,当液体压力增加时,它们都会产生相应的弹性变形,必须补充一定量的工
作液体,因此建压需要占用一定的时间。
系统必须供给的附加液体量主要有三部分:①弹性液体压缩;②工作缸及管道膨胀;③加载时工作缸及管道拉伸变形。
其中影响最大的是第一项,约占总附加液体量的80%~90%左右,因此要减少增压所需时间,应尽可能减少工作缸及高压管道的初始容积。
⑤卸压时间主工作缸卸压时间较短,但如果卸压阀口通径过小,或开启过慢,也可使卸压时间加长。
由于主缸卸压时间一般与回程缸建压时间相重合,可包括在回程时间里。
⑥上、下转换点的滞后时间主要是指动梁运动反向时所需时间。
从保证液压机的快速性来看,协调阀组间启闭关系,减少阀组动作所需时间以及通过减少高压系统的初始容积来减少系统的建压时间等是主要措施。
影响其平稳性的主要原因是液压振动与冲击。