玻璃钢制作工艺真空导入原理
玻璃钢材料成型工艺介绍

玻璃钢材料成型工艺玻璃钢材料的成型工艺,目前使用最广泛的,主要有三种,分别为:手糊成型、拉挤成型和缠绕成型工艺。
除了这三种,根据加工产品的特点及要求,还有诸如反射注射成型、树脂膜溶浸成型等多种类型。
各种成型工艺各有其自身的优缺点。
详细介绍说明如下:1、手糊成型:用手工的方式,依次在模具表面上施加脱模剂胶衣,然后采用粘度为0.3-0.4PaS的中等活性液体热固性树脂(须待胶衣凝结后)和纤维增强材料(主要有表面毡、无捻粗纱布等几种),以手持辊子或刷子使树脂浸渍纤维增强材料,并驱除气泡,压实基层。
铺层操作反复多次,直到达到制品的设计厚度。
优点:1)适合少量生产;2)可室温成型,设备投资少,模具折旧费低;3)可制造大型制品和型状复杂产品;4)树脂和增强材料可自由组合,易进行材料设计;5)可采用加强筋局部增强,可嵌入金属件;6)可用胶衣层获得具有自由色彩和光泽的表面(如开模成型则一面不平滑);7)玻纤含量较喷射成型高。
缺点:1)属于劳动密集型生产,产品质量由工人训练程度决定;2)玻纤含量不可能太高;树脂需要粘度较低才易手工操作,溶剂/苯乙烯量高,力学与热性能受限制;3)手糊用树脂分子量低;通常可能较分子量高的树脂有害于人的健康和安全。
2、拉挤成型拉挤成型的程序是:1)使玻璃纤维增强材料浸渍树脂;2)玻璃纤维预成型后进入加热模具内,进一步浸渍(挤胶)、基本树脂固化、复合材料定型;3)将型材按要求长度切断。
现在已有变截面的、长度方向呈弧型的拉挤制品成型技术。
优点:1)典型拉挤速度0.5-2m/min,效率较高,适于大批量生产,制造长尺寸制品;2)树脂含量可精确控制;3)由于纤维呈纵向,且体种比可较高(40%-80%),因而型材轴向结构特性可非常好;4)主要用无捻粗纱增强,原材料成本低,多种增强材料组合使用,可调节制品力学性能;5)制品质量稳定,外观平滑。
缺点:1)模具费用较高;2)一般限于生产恒定横截面的制品。
玻璃钢游艇真空导流成型工

玻璃钢游艇体真空导流成型工艺道恩提供游艇作为满足人们精神需要或享受需要的高级消费品,其需求随着经济的发展和购买力的提高必然呈不断上升的趋势。
而随着玻璃钢游艇产业的迅速发展,对艇体成型工艺的要求越来越高,特别是成型工艺的环保及成本方面的要求越来越高。
目前国内外游艇是金属材质的较少,大多采用玻璃钢材质。
道恩游艇设计认为传统的艇体成型大部分采用手糊制,而手糊成型生产率低,劳动强度大,劳动卫生条件差,产品质量不易控制,性能稳定性不高,产品力学性能较低。
尤其对于结构复杂、力学性能要求高、体形庞大的大型船体,应用传统的手糊成型工艺已很难实施,所以道恩游艇设计在游艇材料上选择真空芯材导流工艺来解决这一难题。
真空灌注工艺(Vacuum infusion process),简称VIP,在模具上铺“干”增强材料(玻璃纤维,碳纤维,夹心材料等,有别于真空袋工艺),然后铺真空袋,并抽出体系中的真空,在模具型腔中形成一个负压,利用真空产生的压力把不饱和树脂通过预铺的管路压入纤维层中,让树脂浸润增强材料最后充满整个模具,制品固化后,揭去真空袋材料,从模具上得到所需的制品。
道恩游艇设计总结——真空芯材导流工艺的优势1 更高质量制品:在真空环境下树脂浸润玻纤,与传统制造工艺相比,制品中的气泡极少。
体系中不留有多余的树脂,玻纤含量很高,可达到时70%,甚至更高。
所得制品重量更轻,强度更高。
批与批之间也非常稳定。
2 更少树脂损耗:用VIP 工艺,树脂的用量可以精确预算,对于手糊或喷射工艺来说,会因操作人员的多变性而难于控制。
VIP 可以使得树脂的损耗达到最少,更重要的是,这样可以节约成本。
3 树脂分布均匀:对于一个制品来说,不同部分的真空产生的压力是一致的,因此树脂对玻纤的浸润速度和含量趋于一致。
这个对于重量要求稳定的FRP 制件来是很关键的。
4 过程挥发更少:生产过程中没有刷子或辊子之类,不会造成树脂的泼洒或滴落现象发现,更不会有大量的气味出现。
真空导入工艺和手糊工艺的比较-1

真空导入工艺和手糊工艺的比较手糊工艺(Handlay-up)是一种开模工艺,目前在玻璃纤维增强的聚酯复合材料中占65%。
它的优点是在模具的形状改变上有很大的自由度,模具价格低,适应性强、产品性能得到市场认可和投资少等。
所以特别适合于小公司,也适合于船舶及航空航天产业,这儿通常是一次性的大部件。
但该工艺也存在一系列问题,如可挥发有机物(VOC)排放超标、对操作人员的健康影响大、人员易流失、许用材料限制多、产品性能低,树脂浪费并且用量大等,尤其是产品质量不稳定,产品的玻纤和树脂比例、部件厚度、层材制造速率、层材的均匀性等都受操作人员的影响,要求操作人员有较好的技术、经验和素质。
手糊产品的树脂含量一般在50%-70%左右。
开模工艺的VOC排放超过500PPm,苯乙烯的挥发量高达使用量的35%-45%。
而各国规定都在50-100PPm。
目前国外大都改用环戊二烯(DCPD)或其它低苯乙烯释放树脂,但苯乙烯作为单体还没有好的替代品。
真空树脂导入工艺是近20年来发展的制造工艺,尤适合于大型产品的制造。
优点如下:(1)产品性能优良,成品率高。
在同样原材料的情况下,与手糊构件相比,真空树脂导入工艺成型构件的强度、刚度及其它的物理特性可提高30%-50%以上(表1)。
工艺稳定后成品率可接近100%。
表1典型聚酯玻璃钢性能比较增强材料无捻粗纱布双抽向织物无捻粗纱布双抽向织物成型工艺手糊手糊真空树脂扩散真空树脂扩散玻纤含量45506065 拉伸强度(MPa)273.2389383.5480 拉伸模量(GPa)13.518.517.921.9 压缩强度(MPa)200.4247215.2258 压缩模量(GPa)13.421.315.623.6 弯曲强度(MPa)230.3321325.7385 弯曲模量(GPa)13.41716.118.5 层间剪切强度(MPa)2030.73537.8 纵横剪切强度(MPa)48.8852.17 纵横剪切模量(GPa)1.621.84(2)产品质量稳定,重复性好。
玻璃钢制作工艺真空导入原理教学文案

真空导入工艺原理真空导入工艺的基本原理是指在固化后的胶衣层上铺放玻璃纤维、玻璃纤维织物、各种嵌件、脱模布、树脂渗透层、铺放树脂管路和覆盖尼龙(或橡胶、硅酮)挠性薄膜(即真空袋),薄膜与型腔四周边缘密封严实。
型腔内抽真空,往型腔里注入树脂。
在真空状态下树脂沿树脂管路、纤维外表流动而浸渍纤维束,在室温或加热条件下制品固化的成型工艺。
1机械性能高与手糊构件相比,真空导入工艺成型的构件强度,刚度及其它的物理特性可提高1.5倍。
2重复性好构件有相对恒定的树脂比,孔隙率低≤1%,手糊≥5%.3质量轻纤维含量高达75-80%,无需额外的材料来连接芯材。
4环保真空导入工艺几乎是闭模成型过程,挥发性有机物和有毒空气污染物均被局限在真空袋中。
5成本低,效率高纤维含量高,树脂浪费率低于5%,比开模工艺可节约劳动力50%以上。
在芯材加入的前后,无需等待树脂的固化。
尤其在板中加筋时,材料和人工的节约相当可观。
真空导入工艺步骤1模具表面涂脱模剂(蜡)2铺放干织物和夹芯3铺放隔离层4铺放分散介质层5用真空袋密封6注入树脂同时抽真空7室温固化或放入烘箱真空导入材料的选择适应真空导入工艺的典型树脂包括低收缩聚酯树脂,乙烯基树脂,环氧树脂等。
树脂体系黏度一般0.15~0.8Pa.S。
使树脂仅在真空力作用下能够完全浸渍增强材料。
不同的工艺对凝胶时间有不同的要求,如有些工艺要求在35min内注射完,有些则需要4h完成,因此凝胶时间应可变易控,这是注射成功的关键之一。
在浸渍过程中粘度变化小,固化放热峰值应适中。
高放热峰会损坏模具甚至成型构件。
增强材料的选择手糊工艺常用的纤维增强材料在真空导入中均可使用,其它形式的纤维织物,从短切原丝到厚的针织毡也都可以使用。
新型的针织材料和平纹单向纤维是较理想的选择芯材的选择芯层材料一般为低密度泡沫和轻质木材,还可以是热塑性材料,混凝土材料,固化拉挤材料,金属嵌件等。
在具体使用中需考虑的因素有热膨胀系数差异,表面处理情况,与树脂的相溶性等。
玻璃钢制作工艺真空导入原理
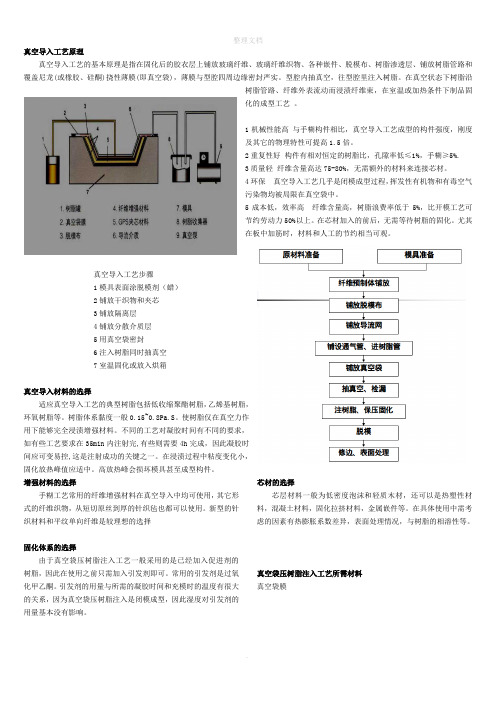
真空导入工艺原理真空导入工艺的基本原理是指在固化后的胶衣层上铺放玻璃纤维、玻璃纤维织物、各种嵌件、脱模布、树脂渗透层、铺放树脂管路和覆盖尼龙(或橡胶、硅酮)挠性薄膜(即真空袋),薄膜与型腔四周边缘密封严实。
型腔内抽真空,往型腔里注入树脂。
在真空状态下树脂沿树脂管路、纤维外表流动而浸渍纤维束,在室温或加热条件下制品固化的成型工艺。
1机械性能高与手糊构件相比,真空导入工艺成型的构件强度,刚度及其它的物理特性可提高1.5倍。
2重复性好构件有相对恒定的树脂比,孔隙率低≤1%,手糊≥5%.3质量轻纤维含量高达75-80%,无需额外的材料来连接芯材。
4环保真空导入工艺几乎是闭模成型过程,挥发性有机物和有毒空气污染物均被局限在真空袋中。
5成本低,效率高纤维含量高,树脂浪费率低于5%,比开模工艺可节约劳动力50%以上。
在芯材加入的前后,无需等待树脂的固化。
尤其在板中加筋时,材料和人工的节约相当可观。
真空导入工艺步骤1模具表面涂脱模剂(蜡)2铺放干织物和夹芯3铺放隔离层4铺放分散介质层5用真空袋密封6注入树脂同时抽真空7室温固化或放入烘箱真空导入材料的选择适应真空导入工艺的典型树脂包括低收缩聚酯树脂,乙烯基树脂,环氧树脂等。
树脂体系黏度一般0.15~0.8Pa.S。
使树脂仅在真空力作用下能够完全浸渍增强材料。
不同的工艺对凝胶时间有不同的要求,如有些工艺要求在35min内注射完,有些则需要4h完成,因此凝胶时间应可变易控,这是注射成功的关键之一。
在浸渍过程中粘度变化小,固化放热峰值应适中。
高放热峰会损坏模具甚至成型构件。
增强材料的选择手糊工艺常用的纤维增强材料在真空导入中均可使用,其它形式的纤维织物,从短切原丝到厚的针织毡也都可以使用。
新型的针织材料和平纹单向纤维是较理想的选择芯材的选择芯层材料一般为低密度泡沫和轻质木材,还可以是热塑性材料,混凝土材料,固化拉挤材料,金属嵌件等。
在具体使用中需考虑的因素有热膨胀系数差异,表面处理情况,与树脂的相溶性等。
玻璃钢制作工艺
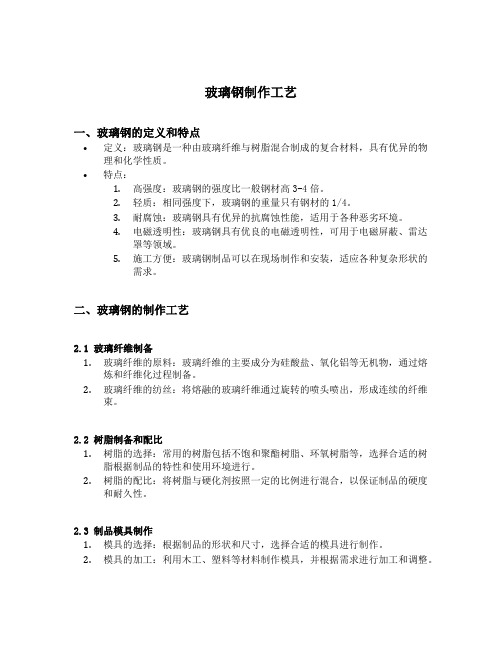
玻璃钢制作工艺一、玻璃钢的定义和特点•定义:玻璃钢是一种由玻璃纤维与树脂混合制成的复合材料,具有优异的物理和化学性质。
•特点:1.高强度:玻璃钢的强度比一般钢材高3-4倍。
2.轻质:相同强度下,玻璃钢的重量只有钢材的1/4。
3.耐腐蚀:玻璃钢具有优异的抗腐蚀性能,适用于各种恶劣环境。
4.电磁透明性:玻璃钢具有优良的电磁透明性,可用于电磁屏蔽、雷达罩等领域。
5.施工方便:玻璃钢制品可以在现场制作和安装,适应各种复杂形状的需求。
二、玻璃钢的制作工艺2.1 玻璃纤维制备1.玻璃纤维的原料:玻璃纤维的主要成分为硅酸盐、氧化铝等无机物,通过熔炼和纤维化过程制备。
2.玻璃纤维的纺丝:将熔融的玻璃纤维通过旋转的喷头喷出,形成连续的纤维束。
2.2 树脂制备和配比1.树脂的选择:常用的树脂包括不饱和聚酯树脂、环氧树脂等,选择合适的树脂根据制品的特性和使用环境进行。
2.树脂的配比:将树脂与硬化剂按照一定的比例进行混合,以保证制品的硬度和耐久性。
2.3 制品模具制作1.模具的选择:根据制品的形状和尺寸,选择合适的模具进行制作。
2.模具的加工:利用木工、塑料等材料制作模具,并根据需求进行加工和调整。
2.4 成型工艺1.喷涂技术:将树脂涂覆在模具表面,然后将玻璃纤维覆盖在树脂上,通过刮涂和压实等手段使其充分浸润。
2.压模技术:采用压模的方式将树脂和玻璃纤维压实在模具内部,通过真空和压力等手段排除气泡。
3.真空吸塑技术:利用真空将树脂和玻璃纤维吸附在模具表面,形成制品的外形。
2.5 固化和后处理1.固化过程:将成型的玻璃钢制品放置在恒温环境中,使树脂和玻璃纤维充分固化和交联。
2.后处理:对制品进行表面处理,如研磨、打磨、喷涂、涂漆等,以提高外观和保护性能。
三、玻璃钢制品的应用领域3.1 建筑领域1.屋顶和墙面材料:玻璃钢具有耐候、耐腐蚀的特性,适用于各种建筑的屋顶和墙面。
2.塔楼和烟囱:玻璃钢制品具有轻质、高强度的特点,适用于高耐受性的建筑结构。
浅谈真空灌注工艺成型条件及常见缺陷修复

浅谈真空灌注工艺成型条件及常见缺陷修复沈葛;孙洲【摘要】真空灌注工艺是玻璃钢成型的主流工艺,相比玻璃钢手糊成型工艺有很多优点.分析了两者的区别,对真空灌注工艺的成型条件进行了阐述,提出真空灌注工艺材料和工艺原因都可能导致出现不同的缺陷,而缺陷修复的方式也不相同.【期刊名称】《天津科技》【年(卷),期】2014(041)006【总页数】4页(P88-91)【关键词】真空灌注工艺;手糊工艺;材料选择;工艺研究;缺陷修复【作者】沈葛;孙洲【作者单位】天津东汽风电叶片工程有限公司天津300456;天津东汽风电叶片工程有限公司天津300456【正文语种】中文【中图分类】TH481.1 真空灌注工艺简介真空灌注工艺的原理是:在真空状态下排除纤维增强体中的气体,通过树脂的流动、渗透,实现对纤维的浸渍(见图1)。
1.2 真空灌注工艺和手糊工艺的优缺点比较手糊工艺是一种开模工艺,它的优点是在模具的形状改变上有很大的自由度,模具价格低、适应性强。
但该工艺也存在一系列问题,如可挥发有机物(VOC)超标、对操作人员的健康影响大、人员易流失、需用材料限制多、产品性能低、树脂用量大且浪费多等,尤其是产品质量不稳定,产品的玻璃纤维含量、制件厚度、生产效率等都受操作人员的影响,要求操作人员有较好的技术、经验和素质。
手糊产品的树脂含量一般在 50%~70%左右。
开模工艺的 VOC排放超过 500,mg/mL,而各国规定都在 50~100,mg/mL,苯乙烯的挥发量高达使用量的 35%~45%。
目前国外大都改用环戊二烯(DCPD)或其他低苯乙烯释放树脂,但苯乙烯作为单体还没有好的替代品。
真空灌注工艺是近20年来发展的低成本制造工艺,尤其适合于大型产品的制造。
其优点如下:①产品性能优良,成品率高。
在同样原材料的情况下,与手糊构件相比,真空灌注工艺成型构件的强度、刚度及其他物理特性可提高 30%~50%以上(见表1)。
工艺稳定后成品率可接近100%。
玻璃钢制作工艺真空导入原理讲课教案

玻璃钢制作工艺真空导入原理真空导入工艺原理真空导入工艺的基本原理是指在固化后的胶衣层上铺放玻璃纤维、玻璃纤维织物、各种嵌件、脱模布、树脂渗透层、铺放树脂管路和覆盖尼龙(或橡胶、硅酮)挠性薄膜(即真空袋),薄膜与型腔四周边缘密封严实。
型腔内抽真空,往型腔里注入树脂。
在真空状态下树脂沿树脂管路、纤维外表流动而浸渍纤维束,在室温或加热条件下制品固化的成型工艺。
1机械性能高与手糊构件相比,真空导入工艺成型的构件强度,刚度及其它的物理特性可提高1.5倍。
2重复性好构件有相对恒定的树脂比,孔隙率低≤1%,手糊≥5%.3质量轻纤维含量高达75-80%,无需额外的材料来连接芯材。
4环保真空导入工艺几乎是闭模成型过程,挥发性有机物和有毒空气污染物均被局限在真空袋中。
5成本低,效率高纤维含量高,树脂浪费率低于5%,比开模工艺可节约劳动力50%以上。
在芯材加入的前后,无需等待树脂的固化。
尤其在板中加筋时,材料和人工的节约相当可观。
真空导入工艺步骤1模具表面涂脱模剂(蜡)2铺放干织物和夹芯3铺放隔离层4铺放分散介质层5用真空袋密封6注入树脂同时抽真空7室温固化或放入烘箱真空导入材料的选择适应真空导入工艺的典型树脂包括低收缩聚酯树脂,乙烯基树脂,环氧树脂等。
树脂体系黏度一般0.15~0.8Pa.S。
使树脂仅在真空力作用下能够完全浸渍增强材料。
不同的工艺对凝胶时间有不同的要求,如有些工艺要求在35min内注射完,有些则需要4h完成,因此凝胶时间应可变易控,这是注射成功的关键之一。
在浸渍过程中粘度变化小,固化放热峰值应适中。
高放热峰会损坏模具甚至成型构件。
增强材料的选择手糊工艺常用的纤维增强材料在真空导入中均可使用,其它形式的纤维织物,从短切原丝到厚的针织毡也都可以使用。
新型的针织材料和平纹单向纤维是较理想的选择芯材的选择芯层材料一般为低密度泡沫和轻质木材,还可以是热塑性材料,混凝土材料,固化拉挤材料,金属嵌件等。
在具体使用中需考虑的因素有热膨胀系数差异,表面处理情况,与树脂的相溶性等。
玻璃钢夹芯结构真空导入树脂流动特性分析及验证

1研究现状真空辅助树脂传递模塑(VARTM),是在固定的玻璃钢模具上铺设增强复合材料(玻璃纤维、碳纤维等),在复合材料上面铺设真空袋,在模具边缘敷设密封胶带等,然后将真空袋中的气体抽除,在模具和密封袋间形成负压,利用此负压将树脂直接从预敷的管道中导入此真空袋中,进而浸润纤维层和芯材,最后让树脂充满整个模具,制品固化后,揭除真空袋,进而从模具上得到所需形状的产品。
VARTM技术就是采用单面模具建立一个闭合系统,利用真空导入的技术,将不饱和树脂固化成型。
目前VARTM技术在汽车和风力发电领域应用较多,在船艇船体成型工艺上的应用方面,由于船艇自身型线复杂,模具制造困难,工艺存在失败风险等诸多原因,致使玻璃钢真空导入成型工艺在船舶建造领域仍处于起步阶段。
国外对灌注工艺较重视,相继开展研究,不仅复合材料行业对此进行专门研究,玻璃钢船生产厂商如意大利船舶制造商Agostini Nautica等自行研究开发船艇生产专用的灌注技术,在改善树脂含量、提高产品机械性能上有显著作用,可在满足力学性能的前提下,有效降低船艇自身重量,这对船艇的性能十分有利[1];P.Sinacek,Y.S Songs等人建立VARTM工艺后注射过程的控制模型和探索此过程的数值模拟,并研究了后注射阶段的影响因素和浸润机理,以及厚度的变化规律[2];Chensong Dong等应用二次衰退模型研究双重渗透性多孔介质的三维流动,以及探索VARTM工艺的数值模拟和优化设计[3]。
S.Xiu Dong等提出了VARTM工艺的流动模型,将树脂在导流介质中的流动看作是一种存在垂直渗玻璃钢夹芯结构真空导入树脂流动特性分析及验证Analysis and Verification of Flow Characteristics of Vacuum Imported Resin for FRPSandwich Structure孙风胜,张维英,黄亚南,栾剑(大连海洋大学,辽宁大连116023)SUN Feng-sheng,ZHANG Wei-ying,HUANG Ya-nan,LUAN Jian(Dalian Ocean University,Dalian116023,China)【摘要】真空辅助树脂传递模塑(VARTM)是制备高性能复合材料尤其是船用玻璃钢(FRP)的有效方法。
真空导入

铺放脱模布
真空袋压树脂注入工艺流程
5铺放导流网
铺放导流网时,导流网的边缘离增强材料的边缘3-5cm 左右远,即导流网的面积比增强材料的面积略微小一 些,当树脂在浸润没有导流网的增强材料时,速度比 有导流网的地方要慢得多,这样可以使树脂有充分的 时间来浸润增强材料,还能减少树脂的浪费。导流网 与导流网之间的搭接距离应尽可能小,但不应出现没 有导流网得地方。导流网一般也用极少量的黑色密封 胶带粘在脱模布上,而不用定位胶。
固化体系的选择
由于真空袋压树脂注入工艺一般采用的是已经 加入促进剂的树脂,因此在使用之前只需加入 引发剂即可。常用的引发剂是过氧化甲乙酮。 引发剂的用量与所需的凝胶时间和充模时的温 度有很大的关系,因为真空袋压树脂注入是闭 模成型,因此湿度对引发剂的用量基本没有影 响。
真空袋压树脂注入工艺所需材料
(3)脱模布:低孔隙率、低渗透率的纤维 织物可改善制品的表观,防止真空袋粘在 制品上。 (4)中空螺旋管:主要用作树脂流道和袋 膜内抽气管。 (5)树脂进料管:用来连接树脂灌和注入 口的塑料管,在承受一个大气压的情况下 而不变形。 (6)抽气管:用来连接抽气口和树脂收集 气及树脂收集器与真空泵的塑料管,能承 受一个大气压而不变形,通常直径比树脂 进料管要小。
真空导入工艺图
真空导入工艺的发展
真空导入是一种新颖的复合材料成型工艺,以即经济 又安全的方法生产高品质的大型复合材料制品见长。 真空导入工艺始于80年代末,1990年初获得专利,最 初公众反应平平。在1996年SPI复合材料年会上引起 重视并成为热点。
真空导入产生的背景
(1)环保法规的要求。 (2)巨型制品成型工艺的要求。
玻璃钢制作工艺真空导入原理

真空导入工艺原理真空导入工艺的基本原理是指在固化后的胶衣层上铺放玻璃纤维、玻璃纤维织物、各种嵌件、脱模布、树脂渗透层、铺放树脂管路和覆盖尼龙(或橡胶、硅酮)挠性薄膜(即真空袋),薄膜与型腔四周边缘密封严实。
型腔内抽真空,往型腔里注入树脂。
在真空状态下树脂沿树脂管路、纤维外表流动而浸渍纤维束,在室温或加热条件下制品固化的成型工艺。
1机械性能高与手糊构件相比,真空导入工艺成型的构件强度,刚度及其它的物理特性可提高1.5倍。
2重复性好构件有相对恒定的树脂比,孔隙率低≤1%,手糊≥5%.3质量轻纤维含量高达75-80%,无需额外的材料来连接芯材。
4环保真空导入工艺几乎是闭模成型过程,挥发性有机物和有毒空气污染物均被局限在真空袋中。
5成本低,效率高纤维含量高,树脂浪费率低于5%,比开模工艺可节约劳动力50%以上。
在芯材加入的前后,无需等待树脂的固化。
尤其在板中加筋时,材料和人工的节约相当可观。
真空导入工艺步骤1模具表面涂脱模剂(蜡)2铺放干织物和夹芯3铺放隔离层4铺放分散介质层5用真空袋密封6注入树脂同时抽真空7室温固化或放入烘箱真空导入材料的选择适应真空导入工艺的典型树脂包括低收缩聚酯树脂,乙烯基树脂,环氧树脂等。
树脂体系黏度一般0.15~0.8Pa.S。
使树脂仅在真空力作用下能够完全浸渍增强材料。
不同的工艺对凝胶时间有不同的要求,如有些工艺要求在35min内注射完,有些则需要4h完成,因此凝胶时间应可变易控,这是注射成功的关键之一。
在浸渍过程中粘度变化小,固化放热峰值应适中。
高放热峰会损坏模具甚至成型构件。
增强材料的选择手糊工艺常用的纤维增强材料在真空导入中均可使用,其它形式的纤维织物,从短切原丝到厚的针织毡也都可以使用。
新型的针织材料和平纹单向纤维是较理想的选择芯材的选择芯层材料一般为低密度泡沫和轻质木材,还可以是热塑性材料,混凝土材料,固化拉挤材料,金属嵌件等。
在具体使用中需考虑的因素有热膨胀系数差异,表面处理情况,与树脂的相溶性等。
玻璃钢制作工艺简介

玻璃钢制作工艺简介玻璃钢制品是由树脂、增强材料和多种辅助成分合理组合而成,制造工艺种类繁多。
1 FRP制品成型工艺FRP的制品往往是材料制造和产品成型同时完成。
成型工艺有手糊、RTM、SMC、缠绕、热塑性塑料(GF/PP)注射模塑及GMT冲压成型等。
1.1 手糊成型工艺手糊成型工艺是一种简单成熟的成型工艺,其典型工艺过程是:在涂有脱模剂的模具上,将加有固化剂的树脂混合料和玻璃纤维织物手工逐层铺放,浸胶并排除气泡,层合至确定厚度,然后固化形成制件。
手糊成型技术的优点是:无需专用设备,投资少;不受制品形状和尺寸的限制,特别适于数量少、整体式及结构复杂的大型制品的制作;可以根据设计要求合理利用增强材料,能随意局部增强,做到以最低成本实现设计要求,而且当设计不合理时能方便地进行修改;操作方便,容易掌握,便于推广。
手糊工艺的缺点是:制品质量不易控制,人为因素大;制品的强度和尺寸精度较低;劳动条件差,生产效率低。
1.2 喷射成型工艺喷射成型工艺是手糊成型的改进,属于半机械化成型工艺。
它是将混有引发剂和促进剂的两种聚酯树脂分别从喷枪两侧喷出,同时将切断的玻纤粗纱由喷枪中心喷出,使其与树脂均匀混合,沉积到模具上;当沉积到一定厚度时,用辊轮压实,使纤维浸透树脂,排除气泡,固化后成制品。
喷射成型的优点是:用玻纤粗纱代替织物,可降低材料成本;生产效率比手糊的高2~4倍;产品整体性好,无接缝,层间剪切强度高,树脂含量高,耐腐蚀、耐渗漏性好;产品尺寸、形状不受限制。
喷射成型的缺点是:树脂含量高,制品强度低;产品只能做到单面光滑;污染环境,有害工人健康。
1.3 SMC及BMC成型工艺片状模塑料(Sheet Molding Comp,SMC)和团状模塑料(Bulk Molding Compoun,BMC)是由树脂糊浸渍纤维或短切纤维毡,两边覆盖聚乙烯薄膜而制成的一类片状模压料,属于预浸毡料范围。
使用时,将两面的薄膜撕去,按制品的尺寸裁剪、叠层,放入金属模具中加温加压,即得所需要的制品。
- 1、下载文档前请自行甄别文档内容的完整性,平台不提供额外的编辑、内容补充、找答案等附加服务。
- 2、"仅部分预览"的文档,不可在线预览部分如存在完整性等问题,可反馈申请退款(可完整预览的文档不适用该条件!)。
- 3、如文档侵犯您的权益,请联系客服反馈,我们会尽快为您处理(人工客服工作时间:9:00-18:30)。
真空导入工艺原理
真空导入工艺的基本原理是指在固化后的胶衣层上铺放玻璃纤维、玻璃纤维织物、各种嵌件、脱模布、树脂渗透层、铺放树脂管路和覆盖尼龙(或橡胶、硅酮)挠性薄膜(即真空袋),薄膜与型腔四周边缘密封严实。
型腔内抽真空,往型腔里注入树脂。
在真空状态下树脂沿树脂管路、纤维外表流动而浸渍纤维束,在室温或加热条件下制品固化的成型工艺。
1机械性能高与手糊构件相比,真空导入工艺成型的构件强度,刚度
及其它的物理特性可提高1.5倍。
2重复性好构件有相对恒定的树脂比,孔隙率低≤1%,手糊≥5%.
3质量轻纤维含量高达75-80%,无需额外的材料来连接芯材。
4环保真空导入工艺几乎是闭模成型过程,挥发性有机物和有毒空气
污染物均被局限在真空袋中。
5成本低,效率高纤维含量高,树脂浪费率低于5%,比开模工艺可
节约劳动力50%以上。
在芯材加入的前后,无需等待树脂的固化。
尤
其在板中加筋时,材料和人工的节约相当可观。
真空导入工艺步骤
1模具表面涂脱模剂(蜡)
2铺放干织物和夹芯
3铺放隔离层
4铺放分散介质层
5用真空袋密封
6注入树脂同时抽真空
7室温固化或放入烘箱
真空导入材料的选择
适应真空导入工艺的典型树脂包括低收缩聚酯树脂,乙烯基树脂,
环氧树脂等。
树脂体系黏度一般0.15~0.8Pa.S。
使树脂仅在真空力作
用下能够完全浸渍增强材料。
不同的工艺对凝胶时间有不同的要求,
如有些工艺要求在35min内注射完,有些则需要4h完成,因此凝胶时
间应可变易控,这是注射成功的关键之一。
在浸渍过程中粘度变化小,
固化放热峰值应适中。
高放热峰会损坏模具甚至成型构件。
增强材料的选择
手糊工艺常用的纤维增强材料在真空导入中均可使用,其它形式的纤维织物,从短切原丝到厚的针织毡也都可以使用。
新型的针织材料和平纹单向纤维是较理想的选择芯材的选择
芯层材料一般为低密度泡沫和轻质木材,还可以是热塑性材料,混凝土材料,固化拉挤材料,金属嵌件等。
在具体使用中需考虑的因素有热膨胀系数差异,表面处理情况,与树脂的相溶性等。
固化体系的选择
由于真空袋压树脂注入工艺一般采用的是已经加入促进剂的树脂,因此在使用之前只需加入引发剂即可。
常用的引发剂是过氧化甲乙酮。
引发剂的用量与所需的凝胶时间和充模时的温度有很大的关系,因为真空袋压树脂注入是闭模成型,因此湿度对引发剂的用量基本没有影响。
真空袋压树脂注入工艺所需材料真空袋膜
导流网
脱模布
中空螺旋管
树脂进料管
抽气管
真空袋密封胶
吸胶毡
定位喷胶
聚丙烯膜是最常用的真空袋膜,可以在形状复杂的模具上拉伸,无折叠和褶皱,真空效率高。
2.导流网
可采用孔隙率高的机织纤维,便于树脂的渗透。
导流网的作用是将铺层和模具表面、真空软膜分开,同时保持了具有一定相互连接的垂直间隙和相互横向连接的网状结构。
树脂从注射点、分配槽经由分配介质自由流向分配介质并完全覆盖整个产品一个表面,然后纵向均匀渗透铺层后通过上表面的分配介质,从而完成整个浸渍过程。
3脱模布:低孔隙率、低渗透率的纤维织物可改善制品的表观,防止真空袋粘在制品上。
4中空螺旋管:主要用作树脂流道和袋膜内抽气管。
5树脂进料管:用来连接树脂灌和注入口的塑料管,在承受一个大气压的情况下而不变形。
6抽气管:用来连接抽气口和树脂收集气及树脂收集器与真空泵的塑料管,能承受一个大气压而不变形,通常直径比树脂进料管要小。
7真空袋密封胶:真空袋密封材料成粘稠状,铺放于模具边框,以保证真空袋膜的密封性,在真空成袋过程中,密封材料具有足够的“粘性”,可以粘接在各种表面上,同时其“粘性”不能过大,可以保证固化脱模后,能将其及时清理掉。
8吸胶毡:透气毡为无纺聚酯或尼龙,其作用是将增强材料和树脂固化过程中产生的气体驱向真空排气口,也可用来吸取过量的树脂。
9定位喷胶:定位喷胶主要是用来使增强材料或真空导入树脂注入材料之间的粘接,以达到定位的效果。
真空袋压树脂注入工艺流程
1打脱模蜡或脱模剂
模具清洁后应放置8小时以上,待模具表面的水分充分干燥后方可上脱模蜡(剂),采用聚乙烯醇脱模剂时应仔细检查其成膜的均匀性,不得有遗漏和流挂,充分干燥后方可涂刷胶衣;采用脱膜蜡时新模必须打4-6度蜡,旧模打2-3度,每度蜡的间隙必须在2小时以上,脱模蜡不能遗漏和堆积。
2喷涂胶衣e3
喷涂胶衣的厚度应控制在0.4-0.6mm, 必须达到“指干”才能铺放增强材料,不得遗漏、堆积或流挂。
在喷涂的过程中,一般涂刷两遍,两边之间涂刷方向以相互垂直为宜,这样可以避免出现漏涂。
3铺放增强材料
玻璃纤维增强材的接头和重叠位置尺寸应符合工艺要求,搭接宽度为50mm,接头应错开100mm以上,五层后允许重叠。
在变形的地方,如果铺放不方便,可以用剪刀将增强材料进行裁剪,裁剪的地方应进行局部补强,如果层与层之间出现空隙,应压实,或用定位喷胶将它们粘在一起,在喷定位胶时,喷嘴与喷涂的地方应距离30cm以上,这样才能使胶喷涂均匀,如果喷涂过多,则会影响树脂对增强材料的浸润,甚至出现白斑。
增强材料铺放好后,用剪刀剪去多余的纤维,并将裙边用黄色密封胶带反复滚擦,粘去裙边上的灰尘和细小纤维束。
4铺放脱模布
在铺放脱模布之前可以将大块的脱模布适当裁小,这样有利于脱模。
脱模布要盖住整个增强材料,且在增强材料的边缘一般还多出1cm左右。
脱模布于脱模布之间的搭接宽度在1cm即可,太宽既浪费材料,又影响浸润速度。
脱模布一般用极少量的黑色密封胶带粘在增强材料上,而不用定位胶,这样既不会影响浸润效果,又能节约成本。
5铺放导流网
铺放导流网时,导流网的边缘离增强材料的边缘3-5cm左右远,即导流网的面积比增强材料的面积略微小一些,当树脂在浸润没有导流网的增强材料时,速度比有导流网的地方要慢得多,这样可以使树脂有充分的时间来浸润增强材料,还能减少树脂的浪费。
导流网与导流网之间的搭接距离应尽可能小,但不应出现没有导流网得地方。
导流网一般也用极少量的黑色密封胶带粘在脱模布上,而不用定位胶。
6铺放树脂导流管和抽真空管
按照预先设计好的流道在模腔中相应位置放置中空螺旋管作为树脂流道和抽真空管。
在铺放中空螺旋管时,不应用力将螺旋管拉得过长,在抽真空时可能会将螺旋管压塌,而起不道流道和抽真空的作用
7安放树脂注入口和抽气口
在预先的设计,在螺旋管上安放树脂注入口和抽气口,在制作形状规则的产品时,树脂注入口和抽气口一般放置在均分点的位置,如在一条螺旋管上放置两个抽气口时,抽气口一般放在三分之一和三分之二的点上。
在安放树脂注入口和抽气口即三通时,可在三通接树脂进料管和抽气管的那头先缠上一圈黑色的密封胶带。
为了避免三通移动,可用适量黑色密封胶带将三通粘在导流网上。
8接抽气管
将抽气口三通和树脂收集器接口用抽气管连接起来。
在接口处再缠上一圈黑色密封胶带。
9真空袋膜的密封
10抽气、整理袋膜和检漏
11接树脂注入管
12检测
13抽气检漏
当达到所需的保压效果时,就可以注入树脂。
注入树脂时一般按照先打开同一树脂流道上的注入口,由内向外注,当树脂流过另一排流道时,可将这一排的注入口打开,开始注入树脂,按照这样的方法注满整个膜腔。
由于模具形状不规则,树脂很难同时到达模具的边缘,当一部分树脂先到达模具的边缘,进入抽气管后,可将这根抽气管用大力钳卡住。
这样既不影响其它部位的充模效果,又可以减少树脂的浪费。
15保真空固化
在树脂固化之前,可以用大力钳卡住大部分树脂进料管和抽气管,这样可以减少树脂的浪费。
至于哪些树脂进料管和抽气管应该卡住,没有一定的要求。
一般按照轮流的办法。
后处理
1脱模
当玻璃钢固化到一定程度时,便可在不损伤制品和模具的前提下把制品从模具上取下来。
首先将制品的四周松脱,然后将制品脱下。
在脱模时须注意:(1)脱模时要细心、耐心,不要操之过急;(2)敲击工具应是木榔头或橡胶榔头;(3)敲击点要要击中关键部位,不要乱击;(4)注意产品表面切不可出现白斑或白点。
2表面检测
主要看是否有胶衣皱皮、光泽不好、制品表面发粘、制品翘曲变形、胶衣层星状龟裂、分层、气泡与空泡、针眼等缺陷并做好标记以便以后修复。
3修边
先在毛坯制品上划基准线,用与制品基本呈直角的切割刀进行,并尽量切割平直。
s。