钻削加工零件
模具零件加工方法概述
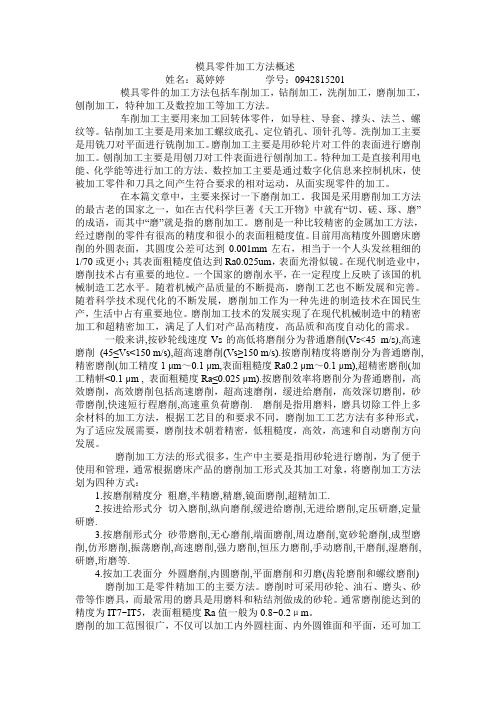
模具零件加工方法概述姓名:葛婷婷学号:0942815201模具零件的加工方法包括车削加工,钻削加工,洗削加工,磨削加工,刨削加工,特种加工及数控加工等加工方法。
车削加工主要用来加工回转体零件,如导柱、导套、撑头、法兰、螺纹等。
钻削加工主要是用来加工螺纹底孔、定位销孔、顶针孔等。
洗削加工主要是用铣刀对平面进行铣削加工。
磨削加工主要是用砂轮片对工件的表面进行磨削加工。
刨削加工主要是用刨刀对工件表面进行刨削加工。
特种加工是直接利用电能、化学能等进行加工的方法。
数控加工主要是通过数字化信息来控制机床,使被加工零件和刀具之间产生符合要求的相对运动,从面实现零件的加工。
在本篇文章中,主要来探讨一下磨削加工。
我国是采用磨削加工方法的最古老的国家之一,如在古代科学巨著《天工开物》中就有“切、磋、琢、磨”的成语,而其中“磨”就是指的磨削加工。
磨削是一种比较精密的金属加工方法,经过磨削的零件有很高的精度和很小的表面粗糙度值。
目前用高精度外圆磨床磨削的外圆表面,其圆度公差可达到0.001mm左右,相当于一个人头发丝粗细的1/70或更小;其表面粗糙度值达到Ra0.025um,表面光滑似镜。
在现代制造业中,磨削技术占有重要的地位。
一个国家的磨削水平,在一定程度上反映了该国的机械制造工艺水平。
随着机械产品质量的不断提高,磨削工艺也不断发展和完善。
随着科学技术现代化的不断发展,磨削加工作为一种先进的制造技术在国民生产,生活中占有重要地位。
磨削加工技术的发展实现了在现代机械制造中的精密加工和超精密加工,满足了人们对产品高精度,高品质和高度自动化的需求。
一般来讲,按砂轮线速度Vs的高低将磨削分为普通磨削(Vs<45 m/s),高速磨削(45≤Vs<150 m/s),超高速磨削(Vs≥150 m/s).按磨削精度将磨削分为普通磨削,精密磨削(加工精度1 μm~0.1 μm,表面粗糙度Ra0.2 μm~0.1 μm),超精密磨削(加工精帡<0.1 μm , 表面粗糙度Ra≤0.025 μm).按磨削效率将磨削分为普通磨削,高效磨削,高效磨削包括高速磨削,超高速磨削,缓进给磨削,高效深切磨削,砂带磨削,快速短行程磨削,高速重负荷磨削. 磨削是指用磨料,磨具切除工件上多余材料的加工方法,根据工艺目的和要求不同,磨削加工工艺方法有多种形式,为了适应发展需要,磨削技术朝着精密,低粗糙度,高效,高速和自动磨削方向发展。
钻 削 加 工

1.1 钻床
1.台式钻床 台式钻床是放置在
台桌上使用的小型钻床, 如图所示。
台式钻床用于钻削 中、小型工件上的小孔, 按最大钻孔直径划分有2 mm、6 mm、12 mm、 16 mm、20 mm等多种 规格,多用于单件、小 批量生产。
台式钻床 1—底座; 2—工作台; 3—进给手柄; 4—主轴; 5— 主轴架; 6—V带; 7—带轮;8—电动机; 9、11—锁
摇臂钻床 1—立柱座; 2—立柱; 3—主轴箱; 4—摇臂;
5—主轴; 6—工作台; 7—底座
4.深孔钻床 深孔钻床是用特制的深孔钻头,专门加工深孔的钻床,常用于
加工如炮筒、枪管和机床主轴等零件中的深孔。深孔钻床的结构特 点如下:
(1)为避免机床过高,深孔钻床一般采用卧式布局。 (2)为减少孔中心线的偏斜,主运动是工件的旋转运动,钻头 只做直线进给运动而不旋转。 (3)为保证获得很好的冷却效果,在深孔钻床上配有周期退刀 排屑装置及切削液输送装置,使切削液由刀具内部输入至切削部位, 如图所示。
2)导向部分 导向部分有两条对称的螺旋槽和两条窄棱面,螺旋槽起 着排屑和输送切削液的作用,窄棱面起着导向和修光孔 壁的作用。导向部分应有微小的锥度,以减小与孔壁的 摩擦。
1.3 扩孔钻
扩孔钻是用来对工件上 已有孔进行扩大的刀具。扩 孔属于半精加工,其目的是 扩大孔径并提高精度和降低 表面粗糙度,常用做铰孔或 磨孔前的预加工或精度要求 不高孔的最终加工。扩孔加 工精度为IT11~IT10,表面 粗糙度Ra为6.3~3.2 μm。扩 孔方法如图所示。
扩孔钻
1.4 铰刀
铰刀是应用较为普遍的孔的精加工刀具之一。铰孔主要是对 未淬硬的中、小尺寸孔进行精加工,一般加工精度为IT9~IT7, 表面粗糙度Ra为1.6~0.4 μm。
加工中心钻削加工精度要求标准

加工中心钻削加工精度要求标准英文回答:Dimensional Accuracy.The dimensional accuracy of a加工中心鑽削加工 process is one of its most important characteristics. It refers to the degree to which the manufactured part conforms to the specified dimensions. The following factors can affect the dimensional accuracy of a加工中心鑽削加工 process:Tool accuracy: The accuracy of the tool used in the machining process can have a significant impact on the dimensional accuracy of the finished part. If the tool is not accurate, it can cause the part to be out of tolerance.Machine accuracy: The accuracy of the machine used in the machining process can also affect the dimensional accuracy of the finished part. If the machine is not accurate, it can cause the part to be out of tolerance.Workholding accuracy: The accuracy of the workholding device used to hold the workpiece during the machining process can also affect the dimensional accuracy of the finished part. If the workholding device is not accurate, it can cause the workpiece to move during the machining process, which can lead to inaccuracies in the finished part.Environmental factors: Environmental factors such as temperature and humidity can also affect the dimensional accuracy of a加工中心鑽削加工 process. If the temperature or humidity is not controlled, it can cause the workpiece to expand or contract, which can lead to inaccuracies in the finished part.Surface Finish.The surface finish of a加工中心鑽削加工 part is another important characteristic. It refers to the texture of the surface of the part. The following factors can affect the surface finish of a加工中心鑽削加工 part:Tool geometry: The geometry of the tool used in the machining process can have a significant impact on the surface finish of the finished part. If the tool geometryis not correct, it can cause the surface of the part to be rough or uneven.Cutting conditions: The cutting conditions used in the machining process can also affect the surface finish of the finished part. If the cutting conditions are not correct,it can cause the surface of the part to be rough or uneven.Workpiece material: The material of the workpiece can also affect the surface finish of the finished part. If the workpiece material is hard or brittle, it can be difficult to achieve a good surface finish.Tolerance.The tolerance of a加工中心鑽削加工 part is another important characteristic. It refers to the allowable variation in the dimensions of the part. The followingfactors can affect the tolerance of a加工中心鑽削加工 part:Machine accuracy: The accuracy of the machine used in the machining process can affect the tolerance of the finished part. If the machine is not accurate, it can cause the part to be out of tolerance.Tool wear: The wear of the tool used in the machining process can also affect the tolerance of the finished part. If the tool is worn, it can cause the part to be out of tolerance.Workpiece material: The material of the workpiece can also affect the tolerance of the finished part. If the workpiece material is hard or brittle, it can be difficultto achieve a tight tolerance.中文回答:尺寸精度。
典型零件的加工工艺
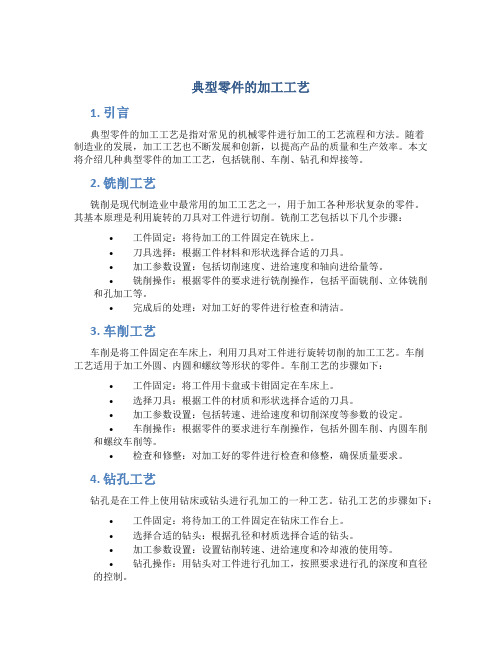
典型零件的加工工艺1. 引言典型零件的加工工艺是指对常见的机械零件进行加工的工艺流程和方法。
随着制造业的发展,加工工艺也不断发展和创新,以提高产品的质量和生产效率。
本文将介绍几种典型零件的加工工艺,包括铣削、车削、钻孔和焊接等。
2. 铣削工艺铣削是现代制造业中最常用的加工工艺之一,用于加工各种形状复杂的零件。
其基本原理是利用旋转的刀具对工件进行切削。
铣削工艺包括以下几个步骤:•工件固定:将待加工的工件固定在铣床上。
•刀具选择:根据工件材料和形状选择合适的刀具。
•加工参数设置:包括切削速度、进给速度和轴向进给量等。
•铣削操作:根据零件的要求进行铣削操作,包括平面铣削、立体铣削和孔加工等。
•完成后的处理:对加工好的零件进行检查和清洁。
3. 车削工艺车削是将工件固定在车床上,利用刀具对工件进行旋转切削的加工工艺。
车削工艺适用于加工外圆、内圆和螺纹等形状的零件。
车削工艺的步骤如下:•工件固定:将工件用卡盘或卡钳固定在车床上。
•选择刀具:根据工件的材质和形状选择合适的刀具。
•加工参数设置:包括转速、进给速度和切削深度等参数的设定。
•车削操作:根据零件的要求进行车削操作,包括外圆车削、内圆车削和螺纹车削等。
•检查和修整:对加工好的零件进行检查和修整,确保质量要求。
4. 钻孔工艺钻孔是在工件上使用钻床或钻头进行孔加工的一种工艺。
钻孔工艺的步骤如下:•工件固定:将待加工的工件固定在钻床工作台上。
•选择合适的钻头:根据孔径和材质选择合适的钻头。
•加工参数设置:设置钻削转速、进给速度和冷却液的使用等。
•钻孔操作:用钻头对工件进行孔加工,按照要求进行孔的深度和直径的控制。
•清洁和检查:对加工好的孔进行清理和检查,确保孔的质量。
5. 焊接工艺焊接是将两个或多个工件通过熔化和凝固的过程连接在一起的工艺。
焊接工艺的步骤如下:•工件准备:准备待焊接的工件,包括清洁和坡口处理等。
•焊接机器设置:根据材料和焊接方式设置焊接机器的参数,包括电流、电压和焊接速度等。
机械制造基础(第二版)第6章z钻、铰、镗和拉削加工

6.3 铰削加工
三、铰孔时应注意事项
1. 铰刀的选择 铰刀是定尺寸刀具,铰孔的精度在很大程度上决定于铰刀的 精度。故在使用铰刀前,应仔细测量铰刀的直径是否与被铰 孔相符,刃口有无磨损、裂纹、缺口等缺陷,经试铰合格后 方能使用。
2. 铰刀的安装 铰孔作为精加工,切削余量很小。若安装后铰刀轴线与原工 件孔中心线发生偏斜,将会使孔径铰削后尺寸扩大超差和产 生形状误差。因此,铰刀与机床应采用浮动联接。
6.2 钻削加工
三、钻削要素
1.钻削用量
切削速度c 钻削时的切削速度指钻头外缘处的线速度
c
d o n
1000
进给量f、每齿进给量fz及进给速度f
f nf2nfz
背吃刀量ap 对钻头而言,它就是钻头直径的一半
ap d0 2
6.2 钻削加工
2.切削层截面尺寸
钻削时切削层尺寸平面为过 基点D的基面PD
6.3 铰削加工
3. 铰削用量的选择 合理选择铰削用量,可以提高铰孔精度。 精铰时,一般半径上铰削余量为0.03~0.15mm,其值取决
于工件材料及对孔要求的精度和表面粗糙度。一般铰削钢体
时,切削速度c=1.5~5m/min;铰铸铁件时c=8~l0m/min,
进给量不能取得过小,否则切削厚度hd过薄,铰刀的挤压作 用会明显加大,加速铰刀后刀面的磨损。—般铰制钢件时f= 0.3~2mm/r,铰削铸铁件时f=0.5~3mm/r。
铰刀齿槽方向有直槽和螺旋槽两种。直槽铰刀刃磨、检验方 便,生产中常用;螺旋槽铰刀切削过程平稳。加工铸铁等取 β=7~8;加工钢件取β=12~20;加工铝等轻金属取 β=35~45。
6.3 铰削加工
铰刀的几何角度
前角γo和后角o 一般取γo=0。粗铰塑性材料时,为
第九章--钻削加工

第九章钻削加工钻床是加工内孔的机床,是用钻头在实体材料上加工孔,主要用于加工外形复杂,没有对称旋转轴线的工件,如杠杆、盖板、箱体、机架等零件上的单孔或孔系。
钻孔属粗加工。
·钻削加工的工艺特点(1)钻头在半封闭的状态下进行切削的,切削量大,排屑困难。
(2)摩擦严重,产生热量多,散热困难。
(3)转速高、切削温度高,致使钻头磨损严重。
(4)挤压严重,所需切削力大,容易产生孔壁的冷作硬化。
(5)钻头细而悬伸长,加工时容易产生弯曲和振动。
(6钻孔精度低,尺寸精度为IT13~IT10,表面粗糙度Ra为12.5~6.3μm。
·钻削加工的工艺范围钻削加工的工艺范围较广,在钻床上采用不同的刀具,可以完成钻中心孔、钻孔、扩孔、铰孔、攻螺纹、锪埋头孔和锪凸台端面等,如图所示。
在钻床上钻孔精度低,但也可通过钻孔----扩孔----铰孔加工出精度要求很高的孔(IT6~IT8,表面粗糙度为1.6~0.4μm),还可以利用夹具加工有位置要求的孔系。
在钻床上加工时,工件固定不动,刀具作旋转运动(主运动)的同时沿轴向移动(进给运动)。
第一节钻床钻床的主要类型有:台式钻床、立式钻床、摇臂钻床、铣钻床和中心孔钻床等。
钻床的主参数一般为最大钻孔直径。
一、立式钻床立式钻床是钻床中应用较广的一种,其特点是主轴轴线垂直布置,且位置固定,需调整工件位置,使被加工孔中心线对准刀具的旋转中心线。
由刀具旋转实现主运动,同时沿轴向移动作进给运动。
因此,立式钻床操作不便,生产率不高。
适用于单件小批生产中加工中小型零件。
·立式钻床的传动原理主运动:单速电动机经齿轮分级变速机构传动;主轴旋转方向的变换,靠电动机正反转实现进给运动:主轴随同主轴套筒在主轴箱中作直线移动。
进给量用主轴每转一转时,主轴的轴向移动量来表示二、台钻台式钻床简称台钻,其实质上是一种加工小孔的立式钻床,结构简单小巧,使用灵活方便,适于加工小型零件上的小孔。
钻孔直径一般小于15mm。
常用精密加工和超精密加工方法
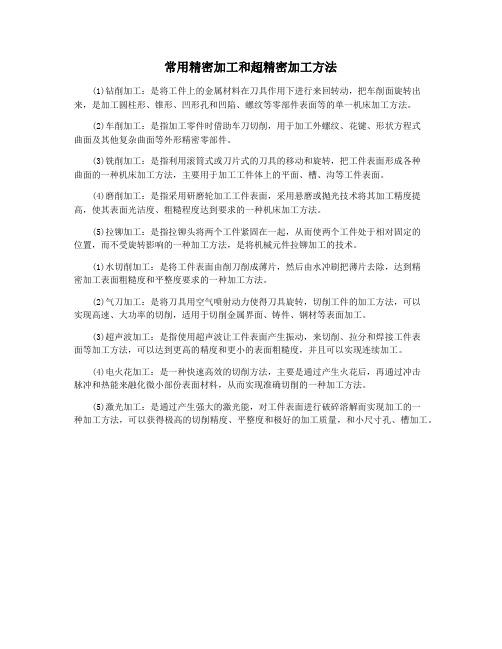
常用精密加工和超精密加工方法(1)钻削加工:是将工件上的金属材料在刀具作用下进行来回转动,把车削面旋转出来,是加工圆柱形、锥形、凹形孔和凹陷、螺纹等零部件表面等的单一机床加工方法。
(2)车削加工:是指加工零件时借助车刀切削,用于加工外螺纹、花键、形状方程式曲面及其他复杂曲面等外形精密零部件。
(3)铣削加工:是指利用滚筒式或刀片式的刀具的移动和旋转,把工件表面形成各种曲面的一种机床加工方法,主要用于加工工件体上的平面、槽、沟等工件表面。
(4)磨削加工:是指采用研磨轮加工工件表面,采用悬磨或抛光技术将其加工精度提高,使其表面光洁度、粗糙程度达到要求的一种机床加工方法。
(5)拉铆加工:是指拉铆头将两个工件紧固在一起,从而使两个工件处于相对固定的位置,而不受旋转影响的一种加工方法,是将机械元件拉铆加工的技术。
(1)水切削加工:是将工件表面由削刀削成薄片,然后由水冲刷把薄片去除,达到精密加工表面粗糙度和平整度要求的一种加工方法。
(2)气刀加工:是将刀具用空气喷射动力使得刀具旋转,切削工件的加工方法,可以实现高速、大功率的切削,适用于切削金属界面、铸件、钢材等表面加工。
(3)超声波加工:是指使用超声波让工件表面产生振动,来切削、拉分和焊接工件表面等加工方法,可以达到更高的精度和更小的表面粗糙度,并且可以实现连续加工。
(4)电火花加工:是一种快速高效的切削方法,主要是通过产生火花后,再通过冲击脉冲和热能来融化微小部份表面材料,从而实现准确切削的一种加工方法。
(5)激光加工:是通过产生强大的激光能,对工件表面进行破碎溶解而实现加工的一种加工方法,可以获得极高的切削精度、平整度和极好的加工质量,和小尺寸孔、槽加工。
车削,铣削,磨削,刨削,钻削的工艺特点

车削,铣削,磨削,刨削,钻削的工艺特点
车削的工艺特点:
1. 利用旋转刀具对工件进行切削加工,工件固定在回转工作台上。
2. 适用于加工轴类工件和旋转对称零件。
3. 刀具与工件之间有相对运动,可以实现高精度的切削加工。
4. 可以实现多种切削操作,如外圆车削、内圆车削、平面车削等。
铣削的工艺特点:
1. 利用旋转刀具在工件表面上进行直线或曲线方向的切削加工,工件固定在工作台上。
2. 适用于加工平面、曲面、齿轮等复杂形状的工件。
3. 切削速度较高,加工效率高。
4. 可以实现多种切削方式,如平面铣削、立铣、侧铣等。
磨削的工艺特点:
1. 利用磨料粒子对工件进行磨擦切削,工件固定在工作台上。
2. 适用于加工高硬度、高精度要求的工件,如模具、工具等。
3. 能够实现高精度的尺寸和形状加工。
4. 磨料粒子具有自锋性,切削力小,可加工硬度高的材料。
刨削的工艺特点:
1. 利用刨刀对工件进行切削加工,工件固定在工作台上。
2. 主要用于加工大型工件的面、平面和槽的加工。
3. 加工速度较低,但能够达到高表面精度和平面度。
4. 切削力大,适用于切削材料的加工。
钻削的工艺特点:
1. 利用旋转钻头对工件进行切削加工,工件固定在工作台上。
2. 主要用于加工孔类零件,可以实现精确的孔径和孔位。
3. 可以加工各种孔型,如圆孔、长孔、螺纹孔等。
4. 切削速度较慢,但能够达到较高精度和光洁度。
常用加工工艺

常用加工工艺随着工业的发展,各种加工工艺也越来越多样化。
本文将介绍几种常用的加工工艺,并对其原理和应用进行详细阐述。
一、车削加工车削加工是一种通过旋转工件,利用切削刀具将工件上的材料削除的工艺。
它是金属加工中最常用的一种工艺之一。
在车床上进行车削加工时,切削刀具的刀尖沿工件轴向移动,同时工件也在旋转。
通过控制切削刀具和工件的相对运动,可以实现对工件形状和尺寸的精确控制。
车削加工广泛应用于制造各种轴类零件和外表面精度要求较高的零件。
二、铣削加工铣削加工是一种通过切削刀具旋转的刀尖,对工件上的材料进行切削的工艺。
与车削加工相比,铣削加工可以实现对工件表面的各种不规则形状的加工,如凹槽、齿轮等。
铣削加工通常在铣床上进行,通过控制切削刀具和工件的相对运动,可以获得所需的加工效果。
铣削加工广泛应用于制造各种复杂形状的零件。
三、钻削加工钻削加工是一种通过旋转刀具,在工件上进行孔加工的工艺。
钻削加工通常在钻床上进行,钻床上的刀具称为钻头。
钻头的刀尖具有尖锐的切削边,可以将工件上的材料削除,形成孔洞。
钻削加工可以实现对工件的径向孔和轴向孔的加工。
钻削加工广泛应用于制造各种孔加工。
四、铸造工艺铸造工艺是一种通过将熔融金属或其他物质倒入模具中,待其冷却凝固后取出的工艺。
铸造工艺可以制造出各种形状复杂的零件,且成本较低。
铸造工艺通常包括砂型铸造、金属型铸造和压铸等。
砂型铸造是最常用的一种铸造工艺,它通过在模具中填充湿砂,然后将熔融金属倒入模具中,待其冷却凝固后取出。
金属型铸造是一种使用金属模具进行铸造的工艺,它可以制造出更精确的零件。
压铸是一种通过将熔融金属注入金属模具中,并施加高压使其充满模具并冷却凝固的工艺。
五、焊接工艺焊接工艺是一种通过加热工件和填充材料,使其熔化并形成牢固连接的工艺。
焊接工艺广泛应用于金属材料的连接。
常见的焊接工艺包括电弧焊、氩弧焊和激光焊等。
电弧焊是一种通过电弧产生高温,使工件和填充材料熔化并形成连接的工艺。
第十七讲钻削加工三

④ 铰削过程中或退出铰刀时,要始终保持铰刀正转,不允 许反转,否则将拉毛孔壁,甚至使铰刀崩刃。
⑤ 铰定位锥销孔时,两结合零件应位置正确,铰削过程中 要经常用相配的锥销来检查铰孔尺寸,以防将孔铰深。一般用 手按紧锥销时,其头部应高于工件表面2mm~3mm,然后用铜 锤敲紧。根据具体要求,锥销头部可略低或略高于工件平面。
锥孔。 ② 莫氏锥铰刀用来铰削0号~6号莫氏锥孔。
----------------------------------------
4
6.5 铰 孔
③ 1∶30锥铰刀用来铰削套式刀具上的锥孔。 ④ 1∶50锥铰刀用来铰削定位销孔。
1∶10锥孔和莫氏锥孔的锥度较大,为了铰孔省力,这 类铰刀一般制成两至三把一套,其中一把精铰刀,其余是 粗铰刀。两把一套的锥铰刀,如图6.21所示,粗铰刀的切 削刃上开有螺旋形分布的分屑槽,以减轻切削负荷。
铰削余量的选择如表6.6所示。
----------------------------------------
7
6.5 铰 孔
表6.6
铰削余量
铰孔直径 铰孔余量
<5 0.1~0.2
5~20 0.2~0.3
21~370 0.8
此外,铰削余量的确定,与上道工序的加工质量有
图6.22 阶梯孔
----------------------------------------
6
6.5 铰 孔
2.铰孔方法
(1)铰削余量确定 铰削余量是指上道工序(钻孔或扩孔)完成后,在直径
方向所留下的加工余量。
钻削加工

,走刀量
=式中D——
• 钻头直径 n——主轴每分钟转速 • fmin:钻头每分化总前进距离 • ②影响钻削用量的因素:
• a.耐用度的生产率:切削速度V对耐用度上的影响 • 来表示,m一般在0.1~0.33之间。m大,表示V对t的影响 小,在这种情况下,钻头比较耐用,钻削材料加工性越差 (硬度越高)钻头切削性能越差,为了保证钻削寿命,切 削速度只能降低。进给量对耐用度的影响程度不如对t的 影响来得大。它的变化将影响切削和切削区别温度,f增 加时,增加了压力和温度机械作用不会正比增加。就钻孔 生产率而言,V的增加,耐用度会下降,所以应尽量取大 的f最后才取大的V。 • b 加工精度要求:当钻孔精度和表面质量要求较高时,除 了降低切速度V<15m/min外,还要相应减小进给量,一 可以减小切削温度的影响,二可以避开产生刀瘤的切削速 度范围,使钻削时的残留面积也能减少。
• ⑵群钻:群钻是群众集体在工作实践中,耕具实际经验所 创造的结晶,其中最具代表性的是倪志福钻头。誉称钻头 大王,倪志福本人是全国劳动模范,为国家作出了显著的 贡献,曾担任全国总工会主席。 • 群钻是修磨过了的标准麻花钻,与标准麻花钻相比, 群钻切削部分修磨了横刃,形成了两条内刀刃,使钻尖变 窄变低,磨出月牙槽圆弧刃,形成两个新的钻尖,直径较 大的钻头还在一侧外刃上开出了分屑槽。这些修磨都是针 对麻花钻的一系列结构缺点进行的,群钻也就是具有了不 同于麻花钻的下列优点。 • ①在表转麻花钻的两个切削刃的中心部分,磨出两个对称 的月牙槽,这种月牙槽由于其顶角的增大,使该处原来较 小的主切削刃前角平均增大10%左右,从而使转矩降低 10%~30%,另外,对称的月牙槽能限制钻头偏移,提高 了孔的位置精度。 • ②横刃大大减窄,只剩下原来的1/3~1/7。内刃前角平均 比修磨前增大25°,使轴向力降低35~47%
模具零件的机械加工

模具零件的机械加工介绍模具零件是指用于生产制造中的模具的组成部分,它们通常需要经过各种机械加工工艺来获得所需的形状和尺寸。
机械加工是指通过机械设备对工件进行切削、磨削、车削等工艺操作,以改变工件的形状、尺寸和表面质量。
本文将介绍模具零件的机械加工过程及常用的加工方法。
机械加工过程机械加工过程通常包括以下几个步骤:1.设计:根据模具的设计要求,绘制出模具零件的图纸,并确定所需的材料和加工工艺。
2.材料准备:根据零件的材料要求,选择合适的材料,并进行切割、锯割等工艺,将材料切割成合适的尺寸。
3.加工:根据零件的图纸要求,选择合适的机械设备和工具进行加工操作。
常见的加工方法包括切削、磨削、铣削、钻削、车削等。
4.检验:在零件加工完成后,需要进行尺寸测量和表面质量检查,以确保零件符合设计要求。
5.调整和修正:如果零件出现尺寸偏差或表面质量问题,需要进行适当的调整和修正,以使其符合要求。
常用的机械加工方法切削加工切削加工是一种通过与工件相对运动的刀具切削工件材料的加工方法。
常见的切削加工包括车削、铣削、钻削等。
•车削:车削是通过旋转工件并将刀具沿着工件轴向移动,切削掉工件表面的金属。
它可以用于加工圆柱形、圆锥形、球面和其他形状的零件。
•铣削:铣削是通过将刀具沿着工件表面的直线或曲线路径运动,切削掉工件表面的金属。
它可以用于加工平面、曲面和复杂形状的零件。
•钻削:钻削是通过旋转刀具并将其进给到工件来切削孔洞的加工方法。
它可以用于加工圆孔、方孔和其他形状的孔洞。
磨削加工磨削加工是通过磨削砂轮与工件相对运动,切削工件表面的金属。
常见的磨削加工包括平面磨削、外圆磨削、内圆磨削等。
•平面磨削:平面磨削是通过将平面磨削砂轮与工件表面相对运动,在工件表面上磨削出所需的平面形状。
•外圆磨削:外圆磨削是通过将外圆磨削砂轮与工件外表面相对运动,将工件外表面磨削出所需的圆柱形状。
•内圆磨削:内圆磨削是通过将内圆磨削砂轮与工件内表面相对运动,将工件内表面磨削出所需的圆柱形状。
典型零件机械加工工艺与实例

典型零件机械加工工艺与实例一、引言在制造业中,机械加工是一项至关重要的工艺,它用于将原材料加工成各种形状和尺寸的零件。
典型零件机械加工工艺是指那些在机械加工过程中常见且广泛应用的工艺方法。
本文将探讨几种典型的零件机械加工工艺,并提供实例进行说明。
二、铣削加工铣削加工是一种常见的机械加工工艺,通过旋转刀具将工件上的材料切削掉,从而得到所需形状和尺寸的零件。
铣削加工可以分为平面铣削、立铣、端铣等多种形式。
2.1 平面铣削平面铣削是将刀具与工件平行或近似平行于工件表面进行切削的加工方式。
它适用于平面、凸轮槽、直齿轮等零件的加工。
平面铣削的实例包括制作平面底座、平面销轴等。
2.2 立铣立铣是将刀具与工件垂直或近似垂直于工件表面进行切削的加工方式。
它适用于开槽、钻孔、倒角等零件的加工。
立铣的实例包括制作键槽、孔加工等。
2.3 端铣端铣是将刀具与工件端面进行切削的加工方式。
它适用于平面、凹槽、凸齿轮等零件的加工。
端铣的实例包括制作平面销轴端面、齿轮端面等。
三、车削加工车削加工是通过旋转工件,并将刀具沿工件轴向移动,将工件上的材料切削掉的加工方式。
车削加工可分为外圆车削和内圆车削两种形式。
3.1 外圆车削外圆车削是将刀具与工件外表面接触,并进行切削的加工方式。
它适用于制作轴、销轴、螺纹等零件。
外圆车削的实例包括制作轴、销轴等。
3.2 内圆车削内圆车削是将刀具放置在工件内部,并进行切削的加工方式。
它适用于制作孔、内螺纹等零件。
内圆车削的实例包括制作孔、内螺纹等。
四、钻削加工钻削加工是通过旋转刀具,使刀具的尖端与工件接触,并将工件上的材料切削掉的加工方式。
钻削加工适用于制作孔、沉孔等零件。
4.1 钻孔钻孔是将刀具的尖端放置在工件上,并进行切削的加工方式。
它适用于制作各种规格和深度的孔。
钻孔的实例包括制作螺纹孔、沉孔等。
五、铣床加工铣床加工是一种常用的机械加工工艺,它通过铣刀在工件上进行切削,得到所需形状和尺寸的零件。
车削,铣削,磨削,刨削,钻削的工艺特点(一)

车削,铣削,磨削,刨削,钻削的工艺特点(一)车削工艺•车削工艺是一种通过旋转工件并用刀具切削的加工方法。
•车削可以用来加工各种形状的工件,包括圆柱、锥体、球体等。
•在车削过程中,刀具与工件之间会产生切削力,需要注意刀具的刃口磨损。
车削工艺的特点•高效率:车床可以实现自动化加工,提高生产效率。
•精度高:车削可以达到很高的加工精度,适用于精密零件的加工。
•可加工材料广泛:车削适用于各种材料,包括金属、塑料、陶瓷等。
铣削工艺•铣削工艺是通过刀具的旋转和工件的移动,将刀具的刃口与工件表面接触,实现切削加工的方法。
•铣削可以用来加工平面、曲线、槽口、齿轮等各种形状的工件。
•铣削切削力较大,需要注意刀具与工件的配合及刃口的磨损情况。
铣削工艺的特点•多功能性:铣削可以实现各种形状的加工,具有较高的加工灵活性。
•高效率:铣床可以实现自动化加工,提高生产效率。
•可加工材料广泛:铣削适用于各种材料,包括金属、塑料、木材等。
磨削工艺•磨削工艺是通过砂轮与工件表面的相对运动,将工件表面的材料去除的加工方法。
•磨削可以用来加工精度要求较高的工件,如轴、孔等。
•磨削过程中,砂轮会产生较大的热量,需要注意冷却与润滑。
磨削工艺的特点•高精度:磨削可以达到很高的加工精度,适用于精密零件的加工。
•表面光洁度高:磨削可以在工件表面留下光洁的加工面。
•可加工硬度较高的材料:磨削对硬材料的加工能力较强。
刨削工艺•刨削工艺是通过在刀具和工件之间施加压力,使刀具顺着工件的表面削去一层材料的加工方法。
•刨削可以用来加工大尺寸的平面和槽口等工件。
•刨削过程中,刀具需要具备较高的刚性和稳定性,以保证加工质量。
刨削工艺的特点•快速:刨削可以一次加工较大面积的工件,加工速度较快。
•平整度高:刨削能够获得平整度较高的加工面。
•可加工大尺寸工件:刨削适用于大型工件的加工。
钻削工艺•钻削工艺是通过钻杆的旋转和施加压力,将工件上的材料削除,实现加工的方法。
•钻削主要用于加工圆孔,可以在各种材料上进行钻削。
轴类零件加工工艺过程
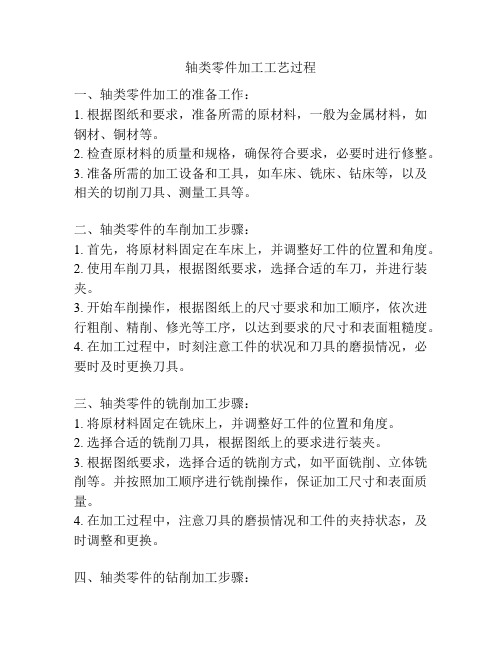
轴类零件加工工艺过程一、轴类零件加工的准备工作:1. 根据图纸和要求,准备所需的原材料,一般为金属材料,如钢材、铜材等。
2. 检查原材料的质量和规格,确保符合要求,必要时进行修整。
3. 准备所需的加工设备和工具,如车床、铣床、钻床等,以及相关的切削刀具、测量工具等。
二、轴类零件的车削加工步骤:1. 首先,将原材料固定在车床上,并调整好工件的位置和角度。
2. 使用车削刀具,根据图纸要求,选择合适的车刀,并进行装夹。
3. 开始车削操作,根据图纸上的尺寸要求和加工顺序,依次进行粗削、精削、修光等工序,以达到要求的尺寸和表面粗糙度。
4. 在加工过程中,时刻注意工件的状况和刀具的磨损情况,必要时及时更换刀具。
三、轴类零件的铣削加工步骤:1. 将原材料固定在铣床上,并调整好工件的位置和角度。
2. 选择合适的铣削刀具,根据图纸上的要求进行装夹。
3. 根据图纸要求,选择合适的铣削方式,如平面铣削、立体铣削等。
并按照加工顺序进行铣削操作,保证加工尺寸和表面质量。
4. 在加工过程中,注意刀具的磨损情况和工件的夹持状态,及时调整和更换。
四、轴类零件的钻削加工步骤:1. 将原材料固定在钻床上,并调整好工件的位置和角度。
2. 选择合适的钻孔刀具,根据图纸要求进行装夹。
3. 根据图纸上的孔径要求,选择合适的钻头,并进行设定,调整钻头的速度和进给量。
4. 开始钻削操作,根据图纸上的孔径位置进行钻孔,保证加工尺寸和孔壁的质量。
5. 在加工过程中,注意刀具的磨损情况和冷却液的使用,及时调整和更换。
五、轴类零件加工的后续工序:1. 进行工件的检验,包括尺寸测量、表面质量等,确保符合要求。
2. 进行必要的热处理、表面处理等工艺,以提高工件的性能和耐用度。
3. 进行最后的整理和打磨工作,使工件达到最终的要求。
4. 进行产品的包装和出库。
以上就是轴类零件加工的基本工艺过程,通过严格按照要求进行加工操作,可以确保加工出高质量的轴类零件。
加工过程中需要密切关注工件的状况和刀具的磨损情况,及时调整和更换,以保证加工质量和工艺效率。
交叉孔的钻削加工
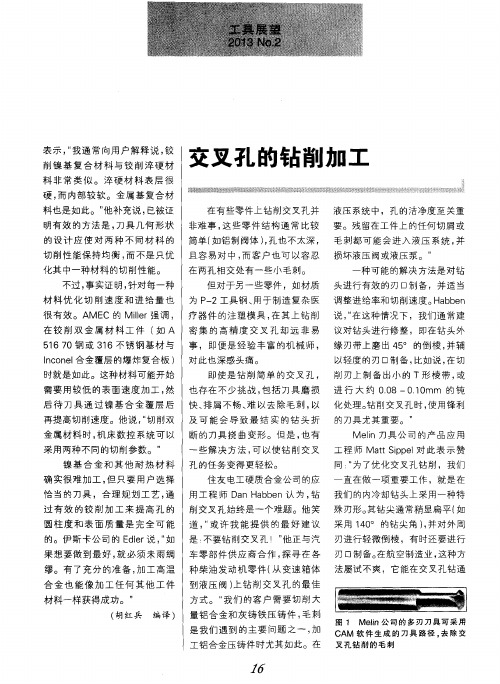
明有 效 的 方法 是 , 刀具 几何 形 状 非难 事 , 这 些 零 件 结 构 通 常 比较 要 。残 留在 工 件上 的任 何 切 屑 或
的设 计应 使对 两种 不同材 料 的 简单( 如 铝 制 阀体 ) , 孔 也 不太 深 , 毛 刺 都 可 能 会进 入液 压 系统 , 并
圆柱 度 和表面 质量 是完 全可 能 道 , “ 或 许 我 能 提 供 的 最 好 建 议 采 用 1 4 0 。 的钻 尖 角 ) , 并 对 外 周
的。 伊 斯 卡 公 司 的 E d l e r 说, “ 如 是 : 不 要钻 削 交 叉孔 !” 他 正 与汽 刃进 行 轻微 倒 棱 ,有 时还 要 进 行 果 想 要做 到 最 好 , 就 必须 未 雨 绸 车零部件供 应商合作 , 在航 空 制造 业 , 这 种 方 探寻在 各 刃 口制 备 。
表示 , “ 我 通 常 向用 户 解 释 说 , 铰
削镍基 复合材 料 与铰 削淬硬 材
料 非 常类似 。淬硬 材料 表层 很 硬, 而内部较软 。金属基复合材
料 也 是如 此。 ” 他 补充 说 , 已被 证
交叉孔的钻削加工
在 有 些零 件上 钻 削 交叉 孔并 液压 系统 中 ,孔 的洁 净度 至 关 重
需 要 用 较低 的 表 面 速 度 加 工 , 然 也 存 在 不 少 挑 战 , 包括 刀 具 磨 损 进 行 大 约 0 . 0 8—0 1 0 mm 的 钝
后待 刀具 通过 镍基合 金 覆层后 快 、 排屑不畅 、 难 以去 除毛 刺 , 以 化 处理 。 钻 削 交 叉7 L I l t, 使 用锋 利
在铰 削双 金属 材 料工 件 ( 如A 密 集 的高精度 交 叉孔却 远非 易 议 对 钻头 进 行修 整 ,即在 钻头 外
第六章 钻削、铰削与镗削加工

(1)铰刀的直径及公差
1)加工后孔径扩大时: dmax =Dmax-Pmax dmin =Dmax-Pmax-G
铰 刀 的 结 构
铰刀直径应选小一些
铰刀直径公差分布图
(1)铰刀的直径及公差 2)孔径缩小时:
dmax =Dmax+Pmin
铰 刀 的 结 构 dmin =Dmax+Pmin-G 铰刀直径应选大一些
6)特种钻头
(1)扩孔钻
(2)中心钻
用于孔加工的预制精确定位,引导麻花钻进行孔加工,减少误差 。
(3)枪钻
用于加工 L/D>20~100的深孔加工。
1、钻削加工
钻削运动
回转体零件上的孔——在车床上加工; 箱体类零件上的孔或孔系——在钻床上加工。
主运动:钻头的旋转运动(钻床),或工件的旋转 运动(车床)。 进给运动:钻头沿轴线作直线进给运动(钻床), 或工件沿钻头轴线作直线进给运动(铣床)
上加工出孔的道具,如麻花钻、中心钻及深孔钻等;另一类 是对工件上已有孔进行再加工的道具,如扩孔钻、锪钻、铰 刀及镗刀等。
深孔:孔深与孔径之比大于5~10倍的孔称为深孔。 孔加工刀具的共同特点:刀具工作部分处于加工表面包 围之中,刀具的强度、刚度及导向、容屑及冷却润滑等都比 切削外表面时问题更突出。
二、孔的种类
钻孔
扩孔
铰孔
攻螺纹
锪埋头孔
锪端面
2. 扩孔钻的结构
图 扩孔钻 1) 齿数多(3、4齿); 2)不存在横刃;
3)切削余量小,排屑容易。
锪孔
在已加工的孔上加工圆柱形沉头孔、锥形沉头孔和凸台断面 等。 锪孔的目的是为了保证孔口与孔中心线的垂直度,以便与孔 连接的零件位置正确,连接可靠。在工件的连接孔端锪出柱形或 锥形埋头孔,用埋头螺钉埋入孔内把有关零件连接起来,使外观 整齐,装配位置紧凑。将孔口端面锪平,并与孔中心线垂直,能 使连接螺栓(或螺母)的端面与连接件保持良好接触。
轴类零件的加工方法

轴类零件的加工方法
轴类零件的加工方法包括以下几种:
1. 车削加工:通过旋转的刀具将工件的材料逐渐削除,形成所需的轴状结构。
车削加工可以分为外圆车削和内圆车削两种形式。
2. 镗削加工:利用旋转刀具进行波纹状运动,将工件内孔的材料逐渐削除,形成所需的内轴孔。
3. 铣削加工:通过刀具在工件表面上进行旋转和直线运动,将工件表面的材料逐渐削除,形成所需的轴状结构。
铣削加工可以分为平铣和立式铣两种形式。
4. 磨削加工:利用磨削工具对工件进行高速磨削,精确地去除工件表面的材料,以达到精密加工的目的。
磨削加工可以分为平面磨削和外圆磨削两种形式。
5. 钻削加工:通过旋转刀具对工件进行钻孔,形成所需的孔状结构。
钻削加工可以使用钻头进行,也可以使用钻床进行。
6. 切削加工:通过使用切削刀具对工件进行切削,将工件材料一部分削除,形成所需的轴形结构。
切削加工可以包括切削、切削、切割等操作。
此外,还可以使用其他加工方法如冲压、锻造、热处理等进行轴类零件的加工。
具体的加工方法选择取决于轴类零件的材料、尺寸、形状等要求。
机械零件加工方法
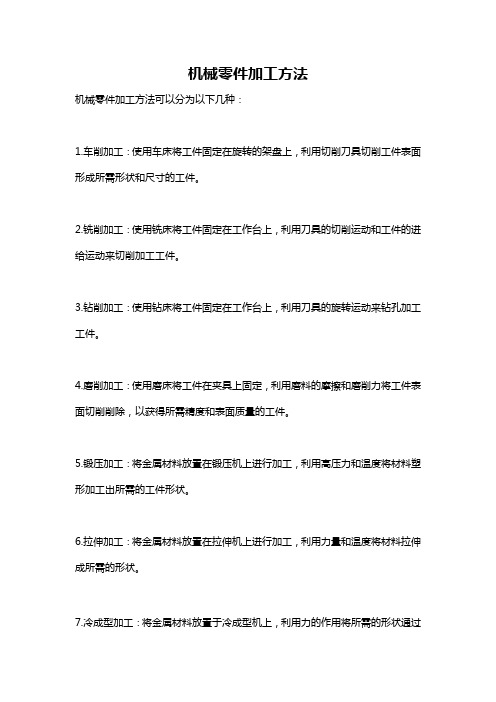
机械零件加工方法
机械零件加工方法可以分为以下几种:
1.车削加工:使用车床将工件固定在旋转的架盘上,利用切削刀具切削工件表面形成所需形状和尺寸的工件。
2.铣削加工:使用铣床将工件固定在工作台上,利用刀具的切削运动和工件的进给运动来切削加工工件。
3.钻削加工:使用钻床将工件固定在工作台上,利用刀具的旋转运动来钻孔加工工件。
4.磨削加工:使用磨床将工件在夹具上固定,利用磨料的摩擦和磨削力将工件表面切削削除,以获得所需精度和表面质量的工件。
5.锻压加工:将金属材料放置在锻压机上进行加工,利用高压力和温度将材料塑形加工出所需的工件形状。
6.拉伸加工:将金属材料放置在拉伸机上进行加工,利用力量和温度将材料拉伸成所需的形状。
7.冷成型加工:将金属材料放置于冷成型机上,利用力的作用将所需的形状通过
压制和挤压加工过程完成。
- 1、下载文档前请自行甄别文档内容的完整性,平台不提供额外的编辑、内容补充、找答案等附加服务。
- 2、"仅部分预览"的文档,不可在线预览部分如存在完整性等问题,可反馈申请退款(可完整预览的文档不适用该条件!)。
- 3、如文档侵犯您的权益,请联系客服反馈,我们会尽快为您处理(人工客服工作时间:9:00-18:30)。
1 钻削过程的数值仿真与残余应力分析
在金属零件的各种加工方法中,精度和表面质量要求较高的零件几乎都要进行钻削加工。
钻削时,工件的表面不可避免地产生大小不同的残余应力, 这种分布不均匀的残余应力会使工件发生变形,影响工件的形状和尺寸精度。
本课题拟采用有限元方法建立起二维金属钻削仿真模型,对整个加工过程中工件的受力情况及加工后已加工表面的残余应力的分布情况进行数值模拟,这对工程中的实际应用具有重要的意义。
主要研究内容有:(1)二维金属钻削有限元模型的建立;(2)加工过程中工件受力情况的有限元分析;(3)已加工表面残余应力分布情况的有限元分析。
在金属切削加工中,大约有1/3的工作量是孔加工,有22%是实心料的钻削加工.世界各国生产刀具总产量的60%是钻头,每年全世界大约有2200万吨切屑是由钻头来切除的.由此可见钻削加工在机械加工中占有十分重要的池位.人类认识和使用钻头的历史可以上溯到史前时代。
燧人氏“钻木取火”所使用的石钻,可以看作最原始的钻头。
现代工业加工中广泛使用的麻花钻(俗称钻头),是一种形状复杂的实工件孔加工刀具,诞生于一百多年前。
现在,全世界每年消耗的各类钻头数以亿计。
据统计,在美国的汽车制造业,机械加工中钻孔工序的比重约占50%;而在飞机制造业,钻孔工序所占的比重则更高。
尽管钻头的使用如此广泛,但众所周知,钻削加工也是最复杂的机械加工方法之一。
正因为如此,人们一直致力于钻头改进和钻削过程的研究。
近几十年来,人们关于钻头和钻削的研究除了钻头制作材料的改进以外,主要集中在以下四个方面:
①钻头数学模型和几何设计研究:包括螺旋沟槽、后刀面、主刃和横刃数学模型的建立,横向截形与钻尖结构参数的优化,切削角度(分布)的计算与控制,钻头结构的静态和动态特性分析,钻尖几何形状与切削和排屑性能关系的研究。
②钻头制造方法研究:包括钻头几何参数与后刀面刃磨参数之间关系的建立与优化,钻头制造精度和刃磨质量的评价与制造误差的测控,钻头螺旋沟槽加工工具截形的设计计算,钻头加工设备特别是数控磨床与加工软件的开发等。
③钻削过程与钻削质量研究:包括影响钻削过程的各种因素及出现的各种物理现象的分析、建模与监控(如钻削力、切削刃应力和温度分布的测量、建模和预报);钻头磨损、破损机理与钻头寿命的研究;钻头的变形、偏斜、入钻时的打滑和钻尖摆动现象的研究;钻削工艺(如振动钻削、高速钻削、深孔钻削、钻削过程的稳定性等)与钻削质量(孔的位置精度、直线度、表面粗糙度、圆柱度、
直径、孔口毛刺等)的研究。
④钻削机理与各种高性能钻头(如群钻、枪钻、干切削钻头、微孔、深孔钻头、长钻头、可转位钻头、合成材料加工用钻头、木工钻头、多螺旋槽钻头等)的研究。
(3)残余应力产生的原理和分析
残余应力是在无外力的作用时,以平衡状态存在于物体内部的应力。
在外力的作用下,当没有通过物体表面向物体内部传递应力时,在物体内部保持平衡的应力统称固有应力或初始应力。
热应力和残余应力是固有应力的一种,而固有应力也称为内应力。
残余应力产生的原因,可分为因外部作用的外在原因,和源于物体内部组织结构不均匀的内在原因
1.不均匀变形
不均匀的变形状态,是不均匀塑料变形产生的条件。
外在原因;不均一的作用应力,例如弯曲、压延、拉拔。
内在原因;由于物体内各部分组织的浓度差或晶粒的位向差等,各部分显示的不同的屈服行为。
2.热的作用
①热应力产生的塑性变形;当加热、冷却过程中产生热应力时,由于高温下屈服强度低,在这种应力作用下易于产生塑性变形。
外在原因:物体各部分的弹性模量、导热系数热膨胀系数等不同而且它们的温度也不相同
②相变或沉淀析出引起的体积变化
外在原因;冷却时,各部分的冷却不均匀,冷却速度也不同。
故而当出现有完全相变终了的部分和相变尚未进行的部分时,两者便显出体积变化的差异。
内在原因:在具有组织结构的浓度差时,固相变和沉淀析出等,所引起的体积变化的程度也不同。
本文是研究钻削工程中的基础上,结合有限元仿真来分析材料表面的残余应力。
(4)钻削过程的塑性有限元数值模拟
随着机械行业的发展,对加工精度要求越来越高,精密加工技术越发重要。
孔的精密加工作为精密加工技术重要内容,在机械加工中具有重要地位。
随着精密
加工的发展,对孔的钻削加工工艺和技术的要求越来越高,迫切需要对钻削加工技术作进一步研究。
在切削过程和切屑形成方面的研究,有限元方法已经被证明是非常有效的一种方法,这种方法通过在计算机上模拟来部分代替费时、费力的实验。
有限元方法于70年代开始应用于切削工艺的模拟,在金属切削的有限元模拟分析方面,许多外国学者已经作了大量的研究工作,建立了诸多简化的有限元模型。
由于钻孔工具及加工过程的复杂性,钻削加工动态模拟方面的研究鲜见报道。
大多学者在应用有限元模拟钻削时,都将之简化为直角切削。
而且大部分的研究者都只局限于切削机理的研究,对于成形工件加工质量的研究较少。
麻花钻和枪钻是钻削加工中两种最普通的加工工具,本文采用有限元分析软件DEFORM-3D,建立了麻花钻和枪钻钻削的三维有限元模型,用有限元方法动态模拟了钻削加工过程,获得了麻花钻和枪钻加工过程中的连续切屑,验证了钻削过程动态有限元模拟的可行性;分析预测了加工过程中工件的应力、应变、应变速率、温度分布以及刀具所受的扭矩,分析比较了不同钻削速度下工件的温度变化以及应变和应变率的变化情况;计算预测了钻削过程中麻花钻的应力和变形。
通过比较这两种加工刀具在钻削模拟过程所受的变形和应力进而间接分析了他们垂直度的差别。
模拟结果表明,在麻花钻和枪钻钻削中,工件具有相似的应力、应变场,温度分布,材料流动以及切屑成形等。
由于枪钻的自导向装置和较强的刚性使枪钻的弹性变形比麻花钻的小很多,因而由枪钻所钻削孔的垂直度较高。
对于精密加工枪钻是一种有效的加工工具。
(5)本研究的意义
随着时代的发展,人们对产品加工精度的要求越来越高。
如何提高零件的加工精度日益成为设计者所关心的问题。
同时,随着计算机技术的迅速发展,仿真技术已经越来越多的应用于工业设计中。
通过仿真技术研究机床切削振动特征及其对加工精度的影响,就是一种有效的提高加工精度的手段,对实际生产具有重要指导意义。
麻花钻普通钻削中,孔轴线的偏斜和孔径的扩大是影响其加工精度的主要问题。
本文研究了麻花钻加工中的仿真建模,以及振动对其加工精度的影响。
应用ANSYS有限元分析,确定孔轴线偏斜和孔径扩大的数值,并对普通钻床进行改造,使钻削加工精度满足产品的要求。
随着科技进步,建立预报钻削力模型方法也在不断发展。
1997年,Islam A U 和Liu M C提出了用人工神经网络预报群钻轴向力和扭矩方法,其训练用数据直接从文献资料中提取。
2001年Kawaji S等人也提出了一种用神经网络模型估计和控制钻削轴向力方法:①离线构建一个轴向力神经网络模型;②以该模型为基础,通过在线最小二乘法训练,建立一个模拟神经控制器;③将经过训练神经控制器应用于钻削系统,得到轴向力。
1999年,Chen Y应用有限元方法分析具有。