课程设计滑动轴承盖工艺工装设计
机械制造技术课程设计-轴承套加工工艺及钻Φ8孔夹具设计【6张优】
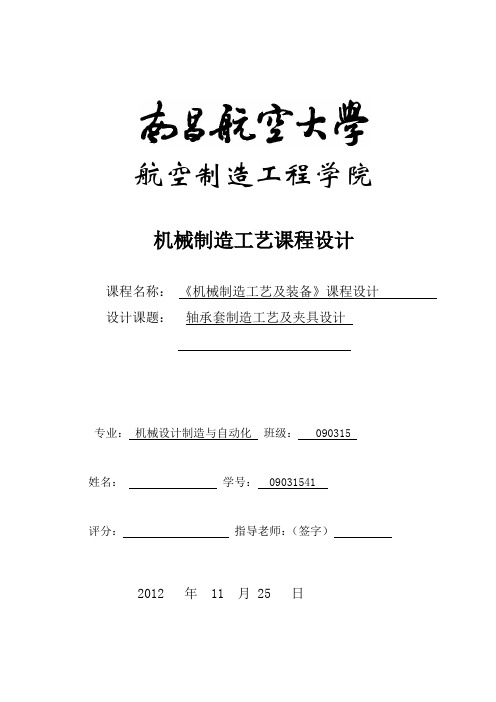
航空制造工程学院机械制造工艺课程设计课程名称:《机械制造工艺及装备》课程设计设计课题:轴承套制造工艺及夹具设计专业:机械设计制造与自动化班级: 090315姓名:学号: 09031541评分:指导老师:(签字)2012 年 11 月 25 日南昌航空大学航空制造工程学院机械设计制造及其自动化专业《机械制造工艺及装备》课程设计课题单全套图纸,加153893706航空制造工程学院班级 090315 学生课题轴承套机械加工工艺规程设计原始条件轴承套零件图生产纲领:中等批量设计要求 1.绘制轴承套零件图2.编制轴承套机械加工工艺规程(含机械加工工艺过程卡和机械加工工序卡)3.设计某工序专用夹具4.编写课程设计说明书课题发给日期 2011年10月17日课程设计完成日期 2011年11月24日指导教师(签名)目录一.零件图分析与绘制--------------------------------3 二.零件的工艺分析----------------------------------41.零件的结构分析----------------------------------42.零件的技术要求分析------------------------------43.毛坯的选择--------------------------------------4 三.机械加工工艺规程--------------------------------51.确定定位、夹紧方案------------------------------52.基准的选择--------------------------------------53.指定工艺路线------------------------------------54.工序设计----------------------------------------7 四.夹具的设计--------------------------------------181.问题的提出--------------------------------------182.夹具结构设计------------------------------------183.设计夹具三维效果图------------------------------20五.总结---------------------------------------------22参考文献--------------------------------------------23一、零件图分析与绘制:该零件为轴承套,主要作用为配合紧定螺丝,以达到内圈周向、轴向固定的目的,广泛应用于轻负荷便于拆装的地方,其内圈内孔是间隙配合,一般只用于轻载、无冲击的场合,同时它可以调整紧松使许多箱体的加工精度得到放宽使箱体加工的工效大大提高。
轴承座加工工艺及工装设计-角铁式车夹具设计

机床夹具的柔性化与机床的柔性化相似,它是指机床夹具通过调整、拼装、组合等方式,以适应可变因素的能力。可变因素主要有:工序特征、生产批量、工件的形状和尺寸等。具有柔性化特征的新型夹具种类主要有:组合夹具、通用可调夹具、成组夹具、拼装夹具、数控机床夹具等。在较长时间内,夹具的柔性化将是夹具发展的主要方向。
在金属切削机床上使用的夹具统称为机床夹具。在现代生产中,机床夹具是一种不可缺少的工艺装备,它直接影响着加工的精度、劳动生产率和产品的制造成本等,帮机床夹具设计在企业的产品设计和制造以及生产技术准备中占有极其重要的地位。机床夹具设计是一项重要的技术工作。
随着科学技术的发展,各种新材料、新工艺和新技术不断涌现,机械制造工艺正向着高质量、高生产率和低成本方向发展。各种新工艺的出现,已突破传统的依靠机械能、切削力进行切削加工的范畴,可以加工各种难加工材料、复杂的型面和某些具有特殊要求的零件。数控机床的问世,提高了更新频率的小批量零件和形状复杂的零件加工的生产率及加工精度。特别是计算方法和计算机技术的迅速发展,极大地推动了机械加工工艺的进步,使工艺过程的自动化达到了一个新的阶段。
1.6
.设计课题:轴承座机械加工工艺规程设计
加工Φ30、Φ35孔专用夹具设计
设计要求:(1)零件毛坯图1张
(2)机械加工工艺过程卡片1张
(3)机械加工主要工序的工序卡片1张
(4)夹具装配图1张
(5)夹具零件图1张
(6)设计说明书1份
零件简图:如图1-1所示.
名称:轴承座
生产批量:中批量
材料:HT200
关键词:轴承座 工艺规格设计夹具设计工序 工艺性
1.1 机械加工工艺概述
机械加工工艺是指用机械加工的方法改变毛坯的形状、尺寸、相对位置和性质使其成为合格零件的全过程,加工工艺是工人进行加工的一个依据。
ht150轴承座课程设计 [滑动轴承座工艺设计课程设计]
![ht150轴承座课程设计 [滑动轴承座工艺设计课程设计]](https://img.taocdn.com/s3/m/efc0cbc3ed630b1c58eeb51f.png)
ht150轴承座课程设计[滑动轴承座工艺设计课程设计]课程设计说明书课程:金属热加工工艺课程设计题目:滑动轴承座铸造工艺设计姓名:专业:机械设计与制造班级:机械学号:指导教师:课题完成时间:至摘要金属毛坯成型是机械制造生产过程的重要组成部分,也是机械零件切削加工的基础,其成形对象是各种铸件、锻件、冲压件、和焊件,成形材料为钢铁材料和非金属材料等,其中钢铁材料是国民经济和现代制造机械产品的支柱材料,也是构成各种机器设备和工程机械的最主要材料。现代科学技术的发展,要求金属铸件具有高的力学性能、尺寸精度和低的表面粗糙度值;要求具有某些特殊性能,如耐热、耐蚀、耐磨等,同时还要求生产周期短,成本低。因此,铸件在生产之前,首先应进行铸造工艺设计,使铸件的整个工艺过程都能实现科学操作,才能有效地控制铸件的形成过程,达到优质高产的效果。铸造工艺设计就是根据铸造零件的结构特点、技术要求、生产批量和生产条件等,确定铸造方案和工艺参数,绘制铸造工艺图,编制工艺卡等技术文件的过程。铸造工艺设计的有关文件,是生产准备、管理和铸件验收的依据,并用于直接指导生产操作。因此,铸造工艺设计的好坏,对铸件品质、生产率和成本起着重要作用。专门的分析表明,铸件的工艺出品率还不能充分表明保温冒口的经济效益,应该用铸件成品率来考核。铸件成品率的定义是铸件质量除以投入熔炉中的金属原料质量,,以百分数表示。它和铸件工艺出品率的差别是计入了熔炼和浇注的损耗。对铸钢来说,这种损耗约占6%。用普通砂型冒口的铸钢件成品率约为43%;而用保温冒口的铸钢件成品率约为68%。相应地,利润率也由原来的5.37%增加为14.16%。由此可见,铸造工艺设计时,采用不同的工艺,对铸造车间或工厂的金属成本、熔炼金属量、能源消耗、铸件工艺出品率和成品率、工时费用、铸件成本和利润率等,都有显著的影响在制定铸造工艺方案之前,设计人员必须熟悉图样和铸件的使用要求,掌握实际生产的现有条件,以图样技术要求,生产批量和使用信息为依据,分析铸件结构、选择铸件种类,确定造型方法和造芯方法等,以便为铸造工艺的拟定奠定基础。滑动轴承座铸造工艺设计目录一滑动轴承座结构工艺分析……………………………………1二铸造工艺方案的设计及选材…………………………………22--1铸造种类选择及确定材料牌号………………………32--2分型方案的筛选………………………………………52--3确定浇铸位置及造型方法……………………………6三铸造工艺参数确定……………………………………………73--1加工余量的选择………………………………………63--2起模斜度、铸造圆角的选择…………………………73--3收缩量的选择……………………………………………83--4型芯及型芯头的选择…………………………………9四铸造工艺图,工艺卡及铸件图的绘制……………A3图纸六主要参考资料……………………………………………9七总结……………………………………………………10一.零件结构工艺分析滑动轴承座主要由上盖,底座,轴瓦组成。生产批量、合金种类、空处壁厚等有关,如表2-2所列。生产批量最小铸出孔直径Φ铸件厚度δ最小铸出孔直径Φ灰铸铁件铸钢件灰铸铁件球墨铸铁铸钢件大量生产12~1550δ2500--10.0~11.00°15′由表中数值宽度a在1.0-1.5mm之间选取,斜度在1°-1.5°之间,因此综合考虑取起模斜度为1.5°,宽度为1mm,未标注处垂直起模斜度为1.0°。由上下面相交壁厚为14.5mm,13.5mm查表可知应在1/3-1/6范围内,此处圆角选为5mm。3-3)收缩量选择由铸造材料灰铸铁可知,其收缩量在0.7%-1.0%之间,在单件或小批量生产时取上限,故收缩量选为1.0%.3-4)型芯及型芯头选择滑动轴承座内腔成圆柱形孔,由分型方式可知,采用垂直型芯,有利于稳固定位,排气和落砂,由基本尺寸知,型芯长度为65mm,由表查得下型芯高度H1值为25-30mm,确定为25mm;上型芯值为15mm,芯头间隙为0.5-1.5mm,定为1.0mm;下芯头斜度5°-10°选为7°,上芯头斜度6°-15°选择10°浇注系统的设置:由于该构件有多个面,,对向上的表面采用增加加工余量等措施保证质量,由大而薄表面向下原则,滑动轴承座的大面积平直表面或薄壁部分,在浇铸时应放在铸型下部,并尽量让加固肋板垂直,防止出现浇铸不足,冷隔等缺陷;应将滚动轴承座厚大断面两端放在上下面,这样有利于放置冒口和冷铁补缩。浇注口选择应符合铸件凝固方式及特点,保证铸型填充及铸件质量,尽量选取有利浇注位置,分析此结构及造型位置,选用上型面开设浇口杯,从而避免直浇对铸件造成冲击,而且有利于型芯排气,落砂和检验等。五.主要参考资料王爱珍机械工程材料北京航空航天大学出版社2009年2月王爱珍金属成型工艺设计北京航空航天大学出版社2009年5月王爱珍热加工工艺基础北京航空航天大学出版社2009年2月六.课程设计总结通过本次课程设计,我对铸造设计方案拟定到分析设计的基本过程有了较为全面的了解。对铸造设计的步骤、思路等有一定的认识和领悟。这是一个极其重要的过程,需要耐心和技能相配合。在课程设计过程中,我按照规定的程序进行,先针对铸件零件进行分析,先后查看《机械工程材料》,《热加工工艺基础》及《金属成型工艺设计》等书籍,收集、调查了有关资料,然后进入草案阶段,其间与教课老师刘教授进行沟通,然后进行几次方案的讨论、修改,最后定案,进行正式图规划阶段。设计方案确定后,最后进行铸造工艺图和铸件图绘制设计。完成全部课程设计。在此对两周来老师的耐心解答及分析表示深深的感谢!xx 年-XX月-XX日设计人:XXX。
机械课程设计轴承盖

机械课程设计轴承盖一、教学目标本节课的学习目标包括知识目标、技能目标和情感态度价值观目标。
知识目标要求学生掌握轴承盖的基本结构、材料和功能;了解轴承盖的设计原理和制造工艺。
技能目标要求学生能够使用测量工具进行轴承盖的尺寸测量,并能运用基本机械加工技能进行轴承盖的加工。
情感态度价值观目标要求学生培养对机械制造行业的兴趣和热情,增强团队合作意识和创新精神。
二、教学内容本节课的教学内容主要包括轴承盖的基本结构、材料和功能,轴承盖的设计原理和制造工艺,以及轴承盖的加工技能。
教学内容将按照教材的章节进行安排,首先介绍轴承盖的基本知识,然后讲解轴承盖的设计和制造,最后进行轴承盖的加工实践。
三、教学方法本节课将采用多种教学方法,包括讲授法、讨论法、案例分析法和实验法。
讲授法用于讲解轴承盖的基本知识,讨论法用于探讨轴承盖的设计和制造问题,案例分析法用于分析实际工程中的轴承盖应用案例,实验法用于进行轴承盖的加工实践。
通过多样化的教学方法,激发学生的学习兴趣和主动性。
四、教学资源本节课的教学资源包括教材、参考书、多媒体资料和实验设备。
教材和参考书用于提供轴承盖的基本知识和设计制造方法,多媒体资料用于展示轴承盖的应用案例和加工过程,实验设备用于进行轴承盖的加工实践。
教学资源的选择和准备将充分支持教学内容和教学方法的实施,丰富学生的学习体验。
五、教学评估本节课的教学评估将采用多种方式,以全面客观地评价学生的学习成果。
评估方式包括平时表现、作业和考试。
平时表现将根据学生在课堂上的参与程度、提问回答和团队合作等方面进行评估。
作业将根据学生提交的轴承盖设计图纸和加工报告进行评估。
考试将采用闭卷笔试的形式,测试学生对轴承盖知识的掌握和应用能力。
通过这些评估方式,全面反映学生的学习成果。
六、教学安排本节课的教学安排将紧凑合理,确保在有限的时间内完成教学任务。
教学进度将按照教材的章节进行安排,每个章节的教学时间将根据内容的难易程度和学生的实际情况进行调整。
滑动轴承课程设计

滑动轴承课程设计一、课程目标知识目标:1. 学生能理解滑动轴承的基本概念、结构组成和工作原理;2. 学生掌握滑动轴承的类型、特点及其在机械设备中的应用;3. 学生了解滑动轴承的设计原则和步骤,能运用相关公式进行简单计算。
技能目标:1. 学生能够运用所学知识分析滑动轴承在实际工程中的应用,具备一定的实际问题解决能力;2. 学生通过课程学习,掌握滑动轴承的安装、使用和维护方法,提高实际操作能力;3. 学生能够运用所学知识,对滑动轴承进行初步的设计和优化,提高创新意识和实践能力。
情感态度价值观目标:1. 学生在学习过程中,培养对机械工程学科的兴趣和热情,增强学习动力;2. 学生通过团队合作完成课程任务,培养团队协作精神和沟通能力;3. 学生了解滑动轴承在国民经济和工程技术领域的重要作用,增强社会责任感和使命感。
课程性质:本课程为机械工程学科的基础课程,旨在让学生掌握滑动轴承的基本知识、设计方法和应用技能。
学生特点:学生为高中二年级学生,已具备一定的物理和数学基础,对机械工程有一定了解,但缺乏实际操作经验。
教学要求:结合学生特点和课程性质,注重理论与实践相结合,提高学生的实际操作能力和问题解决能力,同时关注学生的情感态度和价值观培养。
在教学过程中,将目标分解为具体的学习成果,便于教学设计和评估。
二、教学内容1. 滑动轴承的基本概念与结构- 滑动轴承的定义、作用及分类- 滑动轴承的典型结构及组成部分- 滑动轴承的材料及性能要求2. 滑动轴承的工作原理与性能- 滑动轴承的工作原理- 滑动轴承的性能指标及影响因素- 滑动轴承的摩擦、磨损与润滑3. 滑动轴承的设计原则与方法- 滑动轴承设计的基本原则- 滑动轴承设计的主要步骤- 滑动轴承设计的相关公式及计算方法4. 滑动轴承的应用与维护- 滑动轴承在机械设备中的应用实例- 滑动轴承的安装、使用和维护方法- 滑动轴承故障分析及排除方法5. 滑动轴承的设计实例与优化- 简单滑动轴承设计实例分析- 滑动轴承结构优化方法- 滑动轴承设计中的创新思维与实践教学内容根据课程目标进行选择和组织,确保科学性和系统性。
轴承座工艺工装设计报告

轴承座工艺工装设计1轴承座零件分析 (1)1.1轴承座的作用 (1)1.2轴承座的工作条件 (1)1.3轴承座的结构分析 (1)1.4轴承座重要表面和技术要求 (2)1.5轴承座材料分析 (2)2毛坯工艺的确定 (3)3轴承座工艺规程的制定 (3)3.1加工方法的选择 (3)3.2加工阶段的划分 (4)3.3工序集中与分散 (4)3.4定位基准选择 (5)3.4.1粗基准的选择 (5)3.4.2精基准的选择 (6)3.5辅助工序的安排 (6)3.6加工方案的制定 (6)4设计总结 (8)参考文献 (9)致谢 ................................................... 错误!未定义书签。
附录:工艺规程 (10)1轴承座零件分析1.1轴承座的作用轴承座用于支撑轴承,轴承的外圈被锁定,只有内圈旋转,外圈保持静止。
它始终匹配并平衡驱动方向(例如,电动机方向)。
轴承座的概念是方便地组装箱体的轴承和外壳。
这样做的好处是可以更好地组装和方便使用,并降低制造商的成本。
1.2轴承座的工作条件内轮毂是通过将零件焊接到轮毂外支座件而形成的。
内托架配备有低压转子前轴承,隔热环被压在轮毂的内部托架上。
该空腔由隔热环和内部支架形成,从低压压缩机排出的空气被引入以确保没有将热空气传递到前轴承。
避免零件在高温高压条件下工作。
1.3轴承座的结构分析图Ll结构示意图本设计轴承座与通常的轴承座不同,后者应属于特殊的轴承座,但是,轴承座的结构相对简单。
轴承座的下部有一个下孔(Φ72)和一个阶梯孔(Φ84)。
在通道的突起和中间槽的左右两端都有孔①18和通孔Φ5°轴承座的基本设计,两端表面和底孔均倾斜。
根据设计特征和对加工精度,底面的粗铳,左右端面的粗铳,轴承座的孔粗糙度以及左右孔的扩大的要求,对两面进行铳削,凸块等的应用。
为了确保加工精度,应适当选择机床和工具,并使用适当的切削参数以防止零件变形并提高加工效率。
冲压模具轴承盖课程设计

冲压模具轴承盖课程设计一、课程目标知识目标:1. 让学生掌握冲压模具轴承盖的基本结构及其在机械制造中的应用。
2. 使学生了解并掌握冲压模具轴承盖的材料选择、工艺参数及其对产品质量的影响。
3. 让学生掌握冲压模具轴承盖的设计原理和步骤,具备独立完成简单轴承盖设计的能力。
技能目标:1. 培养学生运用CAD软件进行冲压模具轴承盖三维建模的能力。
2. 培养学生运用CAE软件对冲压模具轴承盖进行模拟分析,优化设计方案的能力。
3. 培养学生根据实际需求,制定合理的工艺参数,完成轴承盖的生产制造。
情感态度价值观目标:1. 培养学生热爱机械制造专业,增强对工程实践的兴趣和责任感。
2. 培养学生严谨的科学态度,注重团队协作,提高沟通与交流能力。
3. 引导学生关注我国制造业的发展,树立为制造业贡献力量的信念。
课程性质:本课程为机械制造及其自动化专业的一门实践性较强的课程,旨在培养学生具备冲压模具轴承盖设计、制造的基本技能。
学生特点:学生具备一定的机械制图、材料力学、金属工艺学等基础知识,具有一定的动手实践能力。
教学要求:结合学生特点,以实际应用为导向,注重理论知识与实践操作相结合,提高学生的综合运用能力。
通过本课程的学习,使学生能够独立完成冲压模具轴承盖的设计与制造,为将来的职业发展打下坚实基础。
二、教学内容1. 引入基础知识:回顾冲压模具基本概念、轴承盖的结构类型及其在机械制造中的应用,涉及教材第一章内容。
2. 材料选择与工艺参数:讲解轴承盖常用材料及其性能,分析不同工艺参数对产品质量的影响,对应教材第二章。
- 材料选择:介绍常用的碳钢、合金钢等材料特性。
- 工艺参数:探讨冲压速度、模具间隙、摩擦系数等参数的设置。
3. 设计原理与步骤:详细讲解轴承盖设计的基本原理、方法和步骤,结合教材第三章。
- 设计原理:分析受力情况、确定结构尺寸等。
- 设计步骤:阐述从方案设计、详细设计到出图的整个过程。
4. CAD三维建模:教授学生使用CAD软件进行轴承盖的三维建模,对应教材第四章。
课程设计__轴承座 设计 完美版 机械制造工艺、汽车制造工艺

洛阳理工学院《汽车制造工艺学》课程设计说明书设计题目:设计“轴承座”零件的机械加工工艺规程(年产量为5000件)班级:B100211学号:B10021115设计者:刘宝庆指导教师:田全忠目录机械制造工艺学课程设计任务书 (2)前言 (3)课程设计说明书 (4)一、零件的分析(一)零件的作用 (6)(二)零件的工艺分析 (6)二、确定生产类型 (7)三、确定毛坯 (7)四、基准的选择(一)粗基准的选择 (7)(二)精基准的选择 (7)五、制定工艺路线 (7)六、机械加工余量、工序尺寸及毛坯尺寸的确定(一)轴承座底面加工 (9)(二)钻定位销孔2×∅12 (9)(三)钻轴承底座上的∅22通孔 (11)(四)铣轴承座两端面 (12)(五)铣顶面 (13)(六)镗轴承孔∅210 (13)(七)钻顶面M20螺纹孔底孔 (14)(八)轴承座右侧面M12螺纹孔底孔 (14)(九)轴承座放油孔M12螺纹孔底孔 (14)(十)钻轴承座后端面6×M10螺纹孔底孔 (15)(十一)钻轴承座前端面6×M8螺纹孔底孔 (15)(十二) 攻各螺纹孔的螺纹 (15)(十三)锪孔 (16)七、夹具设计 --钻模板的设计 (17)八、设计小结 (18)九、参考文献 (19)洛阳理工学院《汽车制造工艺学》课程设计任务书题目:“轴承座”零件的机械加工工艺规程设计生产纲领:5000件生产类型:批量生产设计内容:1、课程设计说明书一份2、机械加工工艺卡片一套3、零件图一张4、毛坯图一张前言这个学期我们进行了《汽车制造工艺学》课程的学习,并且也到东风发动机厂进行了实习。
为了让我们对理论知识和实际应用之间建立密切联系,在课程结束时我们开始了汽车制造工艺学课程设计。
课设开始之前我们对所学的各相关课程进行了一次深入的综合性的回忆与温习,这次温习我们对课设的内容也有了一定的认识,大家一致认为本次课程设计对我们非常重要,是我们对自己实际能力的一次历练。
轴承盖设计说明书
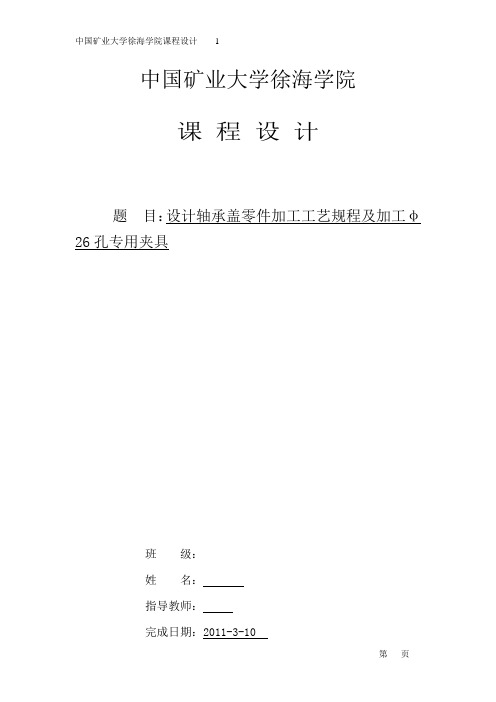
备注
表 1-8 表 1-8 表 1-8 表 1-8
表 1-8 表 1-7 表 1-8 表 1-7
第页
中国矿业大学徐海学院课程设计 10
φ26 的孔
IT11
12.5
钻
表 1-7
3.3、加工阶段的划分
6.2 时间定额的计算 ..................... 错误!未定义书签。
t 6.21 基 本 时 间 j 的 计 算 ............... 错 误 !未 定 义 书 签 。 t 6.22 辅 助 时 间 f 的 计 算 ............... 错 误 !未 定 义 书 签 。
1.2、轴承座的技术要求:
该轴承座的各项技术要求如下表所示:
加工表面 轴承座底面
尺寸偏差(mm) 公差及精度等 表 面 粗 糙 度 形位公差(mm)
级
(um)
140
IT9
6.3
第页
中国矿业大学徐海学院课程设计 7
轴承座上表面 φ54 的上端面 前端面和 后
端面 160x170 的槽 φ120 的半孔 70x140 的槽
第页
中国矿业大学徐海学院课程设计 4
目录
1 轴承座的工艺分析及生产类型的确定 ........................ 6 1.1 轴承座的用途 ....................................... 6 1.2 轴承座的技术要求 ................................... 7 1.3 轴承座工艺分析 ..................................... 7
备注 表 2-4 表 2-4 表 2-4 表 2-4 表 2-4 表 2-4
轴承盖的机械加工工艺规程及工艺装备设计说明书
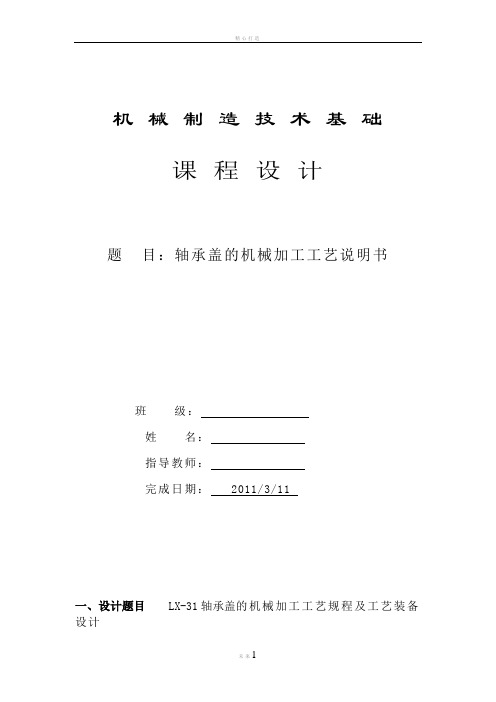
机械制造技术基础课程设计题目:轴承盖的机械加工工艺说明书班级:姓名:指导教师:完成日期:2011/3/11一、设计题目LX-31轴承盖的机械加工工艺规程及工艺装备设计二、原始资料(1) 被加工零件的零件图1张(2) 生产类型:(中批或大批大量生产)三、上交材料1.绘制零件图1张2.毛坯图1张3.编制机械加工工艺过程综合卡片1套4.编制机械加工工艺卡片(仅编制所设计夹具对应的那道工序的机械加工工艺卡片)1套5.绘制夹具装配图(A0或A1)1张6.绘制夹具中1个零件图(A1或A2。
装配图出来后,由指导教师为学生指定需绘制的零件图,一般为夹具体)。
1张7.编写课程设计说明书(约5000-8000字)。
1份四、进度安排本课程设计要求在3周内完成。
1.第l~2天查资料,熟悉题目阶段。
2.第3~7天,完成零件的工艺性分析,确定毛坯的类型、制造方法和机械加工工艺规程的设计并编制出零件的机械加工工艺卡片。
3.第8~10天,完成夹具总体方案设计(画出草图,与指导教师沟通,在其同意的前提下,进行课程设计的下一步)。
4.第11~13天,完成夹具总装图的绘制。
5.第14~15天,零件图的绘制。
6.第16~18天,整理并完成设计说明书的编写。
7.第19天,完成图纸和说明书的输出打印。
8.第20~21天,答辩五、指导教师评语成绩:指导教师日期摘要机械制造技术基础课程设计,是以切削理论为基础,制造工艺为主线,兼顾工艺装备知识的机械制造技术基本涉机能力培养的实践课程;是综合运用机械制造技术的基本知识,基本理论和基本技能,分析和解决实际工程问题的一个重要教学环节;是对学生运用掌握的“机械制造”技术基础知识及相关知识的一次全面的应用训练。
机械制造技术基础课程设计,是已机械制造工艺装备为内容进行的设计。
即以给定的一个中等复杂的程度的中小型机械零件为对象,在确定其毛胚制造工艺的基础上,编制其机械加工工艺规程,并对其一工序进行机床专用卡具设计。
轴承盖零件加工工艺及夹具设计
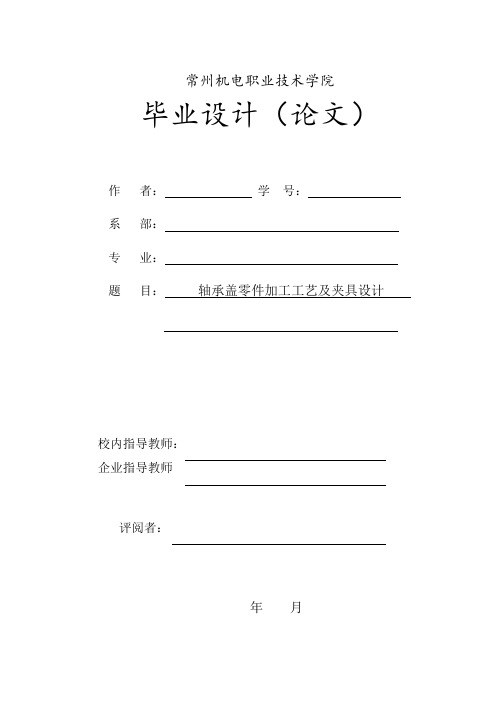
常州机电职业技术学院毕业设计(论文)作者:学号:系部:专业:题目:轴承盖零件加工工艺及夹具设计校内指导教师:企业指导教师评阅者:年月目录目录 (III)1序言 (1)2 零件的分析 (2)2.1零件的形状 (2)2.2零件的工艺分析 (2)3 工艺规程设计 (3)3.1 确定毛坯的制造形式 (3)3.2 基面的选择 (3)3.3 制定工艺路线 (3)3.3.1 工艺路线方案一 (4)3.3.2 工艺路线方案二 (4)3.3.3 工艺方案的比较与分析 (5)3.4 选择加工设备和工艺装备 (6)3.4.1 机床选用 (6)3.4.2 选择刀具 (6)3.4.3 选择量具 (6)3.5 机械加工余量、工序尺寸及毛坯尺寸的确定 (6)3.6确定切削用量及基本工时 (8)4 钻3-Φ9孔夹具设计 (19)4.1 夹具的夹紧装置和定位装置 (19)4.2 夹具的导向 (20)4.3 切削力及夹紧力的计算 (20)4.4 钻孔与工件之间的切屑间隙 (23)4.5 钻模板 (23)4.6定位误差的分析 (24)4.7 钻套、衬套、钻模板设计与选用 (24)4.8 确定夹具体结构和总体结构 (25)4.9 夹具设计及操作的简要说明 (27)总结 (28)致谢 (29)参考文献 (30)1序言机械制造业是制造具有一定形状位置和尺寸的零件和产品,并把它们装备成机械装备的行业。
机械制造业的产品既可以直接供人们使用,也可以为其它行业的生产提供装备,社会上有着各种各样的机械或机械制造业的产品。
我们的生活离不开制造业,因此制造业是国民经济发展的重要行业,是一个国家或地区发展的重要基础及有力支柱。
从某中意义上讲,机械制造水平的高低是衡量一个国家国民经济综合实力和科学技术水平的重要指标。
轴承盖零件加工工艺及钻床夹具设计是在学完了机械制图、机械制造技术基础、机械设计、机械工程材料等的基础下,进行的一个全面的考核。
正确地解决一个零件在加工中的定位,夹紧以及工艺路线安排,工艺尺寸确定等问题,并设计出专用夹具,保证尺寸证零件的加工质量。
课程设计轴承盖设计

课程设计轴承盖设计一、教学目标本节课的学习目标主要包括知识目标、技能目标和情感态度价值观目标。
通过本节课的学习,学生需要掌握轴承盖设计的基本原理和方法,了解轴承盖设计的重要性和应用范围。
在技能方面,学生需要能够运用所学知识进行轴承盖的初步设计,提高解决实际问题的能力。
在情感态度方面,学生需要培养对轴承盖设计的兴趣和热情,增强工程实践的责任感和使命感。
二、教学内容本节课的教学内容主要包括轴承盖设计的基本原理、方法和应用。
首先,我们将介绍轴承盖设计的基本原理,包括轴承盖的功能、结构特点和设计原则。
其次,我们将讲解轴承盖设计的方法,包括轴承盖的材料选择、尺寸计算和形状设计等。
最后,我们将结合实际案例,展示轴承盖设计在工程实践中的应用。
三、教学方法为了提高学生的学习兴趣和主动性,我们将采用多种教学方法进行授课。
首先,我们将运用讲授法,系统地讲解轴承盖设计的基本原理和方法。
其次,我们将采用案例分析法,通过分析实际案例,使学生更好地理解和掌握轴承盖设计的应用。
此外,我们还将学生进行讨论和实验,以培养学生的实践能力和创新精神。
四、教学资源为了支持教学内容和教学方法的实施,我们将选择和准备适当的教学资源。
教材将是主要的教学资源,我们将选用权威、实用的教材,以确保学生能够获得准确、全面的知识。
此外,我们还将提供参考书、多媒体资料和实验设备等,以丰富学生的学习体验和提高实践能力。
五、教学评估为了全面、客观、公正地评估学生的学习成果,我们将采用多种评估方式。
平时表现将占评估总分的30%,包括课堂参与度、提问回答和团队协作等方面。
作业将占评估总分的20%,通过布置相关的设计练习和研究报告,检验学生对轴承盖设计知识的掌握程度。
考试将占评估总分的50%,包括选择题、填空题和计算题等,以测试学生对轴承盖设计原理和方法的熟悉程度。
六、教学安排本节课的教学安排将分为10个课时,每课时45分钟。
第一课时用于介绍轴承盖设计的基本原理,第二课时讲解轴承盖设计的方法,接下来的课时将通过案例分析和实验操作,使学生更好地理解和掌握轴承盖设计。
轴承座的工艺及工装设计
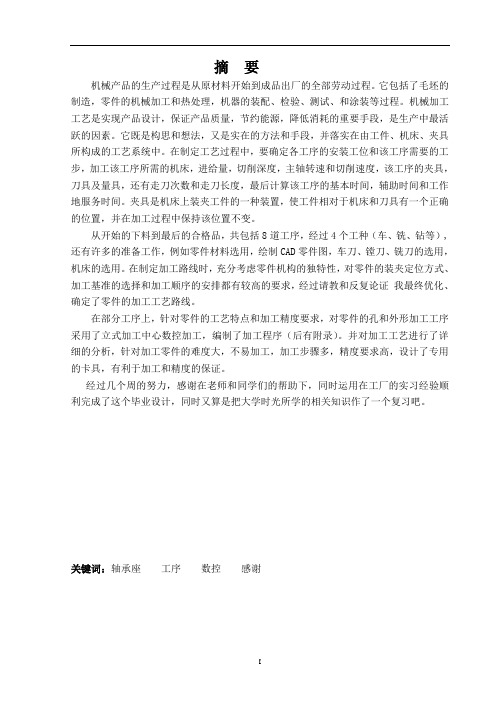
摘要机械产品的生产过程是从原材料开始到成品出厂的全部劳动过程。
它包括了毛坯的制造,零件的机械加工和热处理,机器的装配、检验、测试、和涂装等过程。
机械加工工艺是实现产品设计,保证产品质量,节约能源,降低消耗的重要手段,是生产中最活跃的因素。
它既是构思和想法,又是实在的方法和手段,并落实在由工件、机床、夹具所构成的工艺系统中。
在制定工艺过程中,要确定各工序的安装工位和该工序需要的工步,加工该工序所需的机床,进给量,切削深度,主轴转速和切削速度,该工序的夹具,刀具及量具,还有走刀次数和走刀长度,最后计算该工序的基本时间,辅助时间和工作地服务时间。
夹具是机床上装夹工件的一种装置,使工件相对于机床和刀具有一个正确的位置,并在加工过程中保持该位置不变。
从开始的下料到最后的合格品,共包括8道工序,经过4个工种(车、铣、钻等),还有许多的准备工作,例如零件材料选用,绘制CAD零件图,车刀、镗刀、铣刀的选用,机床的选用。
在制定加工路线时,充分考虑零件机构的独特性,对零件的装夹定位方式、加工基准的选择和加工顺序的安排都有较高的要求,经过请教和反复论证我最终优化、确定了零件的加工工艺路线。
在部分工序上,针对零件的工艺特点和加工精度要求,对零件的孔和外形加工工序采用了立式加工中心数控加工,编制了加工程序(后有附录)。
并对加工工艺进行了详细的分析,针对加工零件的难度大,不易加工,加工步骤多,精度要求高,设计了专用的卡具,有利于加工和精度的保证。
经过几个周的努力,感谢在老师和同学们的帮助下,同时运用在工厂的实习经验顺利完成了这个毕业设计,同时又算是把大学时光所学的相关知识作了一个复习吧。
关键词:轴承座工序数控感谢AbstractThe mechanical production process from raw materials to finished product all the labor process. It includes blank manufacturing, machining and heat treatment of parts, machine assembly, inspection, testing, and coating process. Machining process is to achieve product design, product quality assurance, save energy, reduce consumption of the important means, is the most active factor of production. It is not only the concepts and ideas, and ways and means of the truth, and implement in the process system composed of machine tool, workpiece, fixture. In the development process, to determine the installation position of each process and the process need the labor step, processing the required process machine, feed rate, depth of cut, and cutting speed spindle speed, the process of the fixture, tool and measuring, and walk the knife cutting the number and length of time, finally calculate the basic procedures, work time and support to business hours. The fixture is a device for machine tool clamping workpiece, the workpiece relative to the tool and the tool has a correct position, and keep in the process of the position.From the beginning of the next expected qualified last, including a total of 8 processes, after 4 types (cars, milling, drilling, etc.), there are many preparations, such as parts material selection, drawing CAD parts diagram, selection of turning, boring, milling cutter, machine tool selection. In the development of processing route, fully consider the uniqueness of parts of the body, the parts of the clamping and locating method, machining datum selection and processing sequence arrangement have higher requirements, through the consult and repeated demonstration, I finally optimization process to determine the parts.In the part of the operation, according to the process characteristics of the parts and machining precision of parts, and the shape of the holes machining process using CNC vertical machining center, machining program. (after the appendix). And the machining process was analyzed in detail, the parts of the processing difficulty is big, not easy processing, processing steps, high precision, is designed with a special fixture, to ensure the accuracy of processing and.After a few weeks of hard work, thanks to the help of the teacher and classmates, also used in the factory internship experience successfully completed the graduation design, also is the knowledge of the university time for a review.Key words:Bearing block Processes Numerical control Thank摘要 (I)Abstract (II)引言 (1)1 零件的工艺性分析 (2)1.1零件的材料和结构分析 (2)1.2零件精度和基准的分析 (3)2 刀具的选择 (6)2.1刀具材料 (6)2.2刀具的结构 (6)2.3刀具类型 (6)2.4刀具长度的选择 (6)2.5几何参数包括以下内容 (7)2.6刀具半径 (7)3 量具的使用 (7)3.1测量方法 (8)3.2量具类型 (8)3.3量具范围 (8)3.4量具精度 (8)4 机床选择 (9)4.1机床型号的选择 .................................... 错误!未定义书签。
(精选)滑动轴承UG造型课程设计说明书
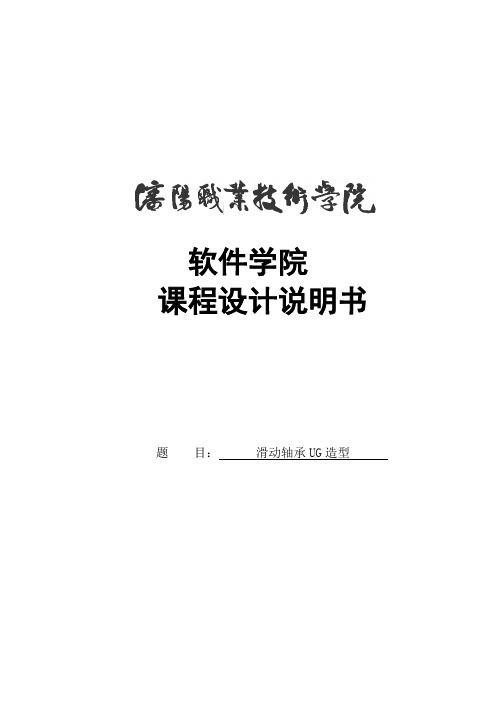
软件学院课程设计说明书题目:滑动轴承UG造型毕业设计(论文)原创性声明和使用授权说明原创性声明本人郑重承诺:所呈交的毕业设计(论文),是我个人在指导教师的指导下进行的研究工作及取得的成果。
尽我所知,除文中特别加以标注和致谢的地方外,不包含其他人或组织已经发表或公布过的研究成果,也不包含我为获得及其它教育机构的学位或学历而使用过的材料。
对本研究提供过帮助和做出过贡献的个人或集体,均已在文中作了明确的说明并表示了谢意。
作者签名:日期:指导教师签名:日期:使用授权说明本人完全了解大学关于收集、保存、使用毕业设计(论文)的规定,即:按照学校要求提交毕业设计(论文)的印刷本和电子版本;学校有权保存毕业设计(论文)的印刷本和电子版,并提供目录检索与阅览服务;学校可以采用影印、缩印、数字化或其它复制手段保存论文;在不以赢利为目的前提下,学校可以公布论文的部分或全部内容。
作者签名:日期:学位论文原创性声明本人郑重声明:所呈交的论文是本人在导师的指导下独立进行研究所取得的研究成果。
除了文中特别加以标注引用的内容外,本论文不包含任何其他个人或集体已经发表或撰写的成果作品。
对本文的研究做出重要贡献的个人和集体,均已在文中以明确方式标明。
本人完全意识到本声明的法律后果由本人承担。
作者签名:日期:年月日学位论文版权使用授权书本学位论文作者完全了解学校有关保留、使用学位论文的规定,同意学校保留并向国家有关部门或机构送交论文的复印件和电子版,允许论文被查阅和借阅。
本人授权大学可以将本学位论文的全部或部分内容编入有关数据库进行检索,可以采用影印、缩印或扫描等复制手段保存和汇编本学位论文。
涉密论文按学校规定处理。
作者签名:日期:年月日导师签名:日期:年月日指导教师评阅书评阅教师评阅书教研室(或答辩小组)及教学系意见课程设计任务书指导教师签字:摘要在滑动摩擦下工作的轴承。
滑动轴承工作平稳、可靠、无噪声。
在液体润滑条件下,滑动表面被润滑油分开而不发生直接接触,还可以大大减小摩擦损失和表面磨损,油膜还具有一定的吸振能力。
课程设计滑动轴承盖工艺工装设计(有夹具)

一、零件的分析(一)零件的作用题目所给的零件是滑动轴承盖。
它一般与滑动轴承配套使用中,与滑动轴承一起是用来支撑轴的部件,有时也用来支撑轴上的回转零件。
主要起安装、定位支承滑动轴承的作用,零件上方的Φ60孔用来安装滑动轴承,底面用来将滑动轴承组件固定在机器上,2-Φ13孔联接滑动轴承下半部分与轴承座,起联接、调整间隙用。
(二)零件的工艺分析零件的材料为HT200,灰铸铁生产工艺简单,铸造性能优良,但塑性较差、脆性高,不适合磨削,为此以下是滑动轴承盖需要加工的表面以及加工表面之间的尺寸公差要求:1、以φ60为中心的加工表面这一组加工表面包括:φ60的孔,以及其前后端面,前后端面与孔有位置要求,2—φ13通孔与φ60孔有位置要求。
2、以顶部为中心的加工表面这一组加工表面包括:M10螺纹孔、端面。
由上面分析可知,加工时应先加工一组表面,再以这组加工后表面为基准加工另外一组。
由上面分析可知,可以粗加工滑动轴承盖下端面,然后以此作为基准采用专用夹具进行加工,并且保证位置精度要求。
再根据各加工方法的经济精度及机床所能达到的位置精度,并且此滑动轴承盖零件没有复杂的加工曲面,所以根据上述技术要求采用常规的加工工艺均可保证。
二、确定生产类型已知此滑动轴承盖零件的生产纲领为大批生产,所以初步确定工艺安排为:加工过程划分阶段;工序适当集中;加工设备以通用设备为主,大量采用专用工装。
三、确定毛坯(一)确定毛坯种类零件材料为HT200。
考虑零件在机床运行过程中所受冲击不大,零件结构又比较简单,生产类型为中批生产,故选择木摸手工砂型铸件毛坯。
查《机械制造工艺设计简明手册》第41页表2.2-5,选用铸件尺寸公差等级为CT-8。
(二)确定铸件加工余量及形状查《机械制造工艺设计简明手册》第41页表2.2-5,选用加工余量为MA-F级,并查表2.2-4确定各个加工面的铸件机械加工余量,铸件的分型面的选用及加工余量,如下表所示:表1-1(三)绘制铸件零件图四、工艺规程设计(一)选择定位基准1、粗基准的选择:以零件的底部大端面为主要的定位粗基准,以侧面为辅助粗基准。
(完整版)工艺课程设计实例(轴承座)

大学机械制造工艺及夹具设计》课程设计林冲机电工程学院机械加工工艺规程设计任务书一、设计题目制定轴承座零件的机械加工工艺规程设计数据:年产量:2000 件车间工作制度: 2 班制生产三、设计工作内容一) 生产特征及设计对象的分析选择毛坯件并确定其总余量二) 编制机械加工工艺规程1.2制订机械加工工艺规程.3计算和填写机械加工工艺工序卡片.1 ) 绘制机械加工工序简图2 ) 选择设备3 ) 选择机床工艺装备4 ) 确定切削用量及工时定额(三)零件的加工制造四、设计的组成课程设计作业组成利 用 CAD 软 件 绘 制 零 件图图 1 轴承 座 零 件图零件——毛坯综合图图 3 零件— —毛坯综 合图三. 机械加工工艺过程卡和机械加工工艺过程综合卡1. 机械加工工艺过程卡(A4 图纸、横放)2. 机械加工工艺过程综合卡片四、轴承座工艺规程设计说明书轴承座工艺规程设计说明书设计题目:制定轴承座的机械加工工艺规程(年产量2000 件)第一节零件分析1.1 轴承座零件的用途轴承座零件结构如图 1 所示。
轴承座用于定位与支承转动轴,该零件上的主要表面是Φ 30mm 孔和平面C。
Φ 30mm孔用于安装轴承,以支承轴的转动。
Φ 30mm 孔的加工精度直接影响所装配轴的转动精度,孔的加工精度是轴承座加工过程中的关键。
平面C和两个距离尺寸为42mm的侧立面是轴承座的装配基准面,装配时用于轴承座在机器中的定位。
这几个平面影响轴承座的装配精度,轴承座通常需要成对使用,一对轴承座的装配精度影响轴的回转精度,以及轴的位置精度(由尺寸15±0. 021 决定)等。
1.2 轴承座图样的技术要求根据图 1 ,轴承座加工表面精度分析如下:1. 平面 C 是孔φ30H7 的设计基准,也是轴承座在机器中的装配基准。
加工中必须保证C平面的平面度要求和位置要求。
2. 轴座的工作面是孔φ30H7mm,该孔是主要加工表面,也是确定尺寸为42 的两个平面位置的设计基准。
- 1、下载文档前请自行甄别文档内容的完整性,平台不提供额外的编辑、内容补充、找答案等附加服务。
- 2、"仅部分预览"的文档,不可在线预览部分如存在完整性等问题,可反馈申请退款(可完整预览的文档不适用该条件!)。
- 3、如文档侵犯您的权益,请联系客服反馈,我们会尽快为您处理(人工客服工作时间:9:00-18:30)。
机电及自动化学院《机械制造工艺学》课程设计说明书设计题目:滑动轴承盖工艺规程设计姓名:林世吟学号:1211113027班级:机电(1)班届别:2014指导教师:谢明红2015 年7月前言《机械制造工艺学》课程设计是我们学完了机械制图、机械制造工艺学、工程材料、机械设计、CAD/CAM等专业基础课和主要专业课,又经过了机械设计课程设计之后,进行的又一次实践性环节,特别强调对机械制造工艺学和工程材料这两门课程的运用,同时也有对刀具和切屑的部分知识的综合,因此这是我们对以前所学各门课程的一次较为深入的综合总复习,同时还要对相关课外知识进行查阅和学习,也是一次对我们实际运用知识解决问题能力的练习。
并且,这次课程设计同样也会用到以前的金工实习和认知实习的相关知识,也可以说这是对两次实习效果的一次检验。
通过这次课程设计,将会巩固对机械加工工艺规程设计的理论知识,并初步学会自己完成制定简单零件加工工艺规程。
这次的工艺规程课程设计,我的题目是滑动轴承盖的工艺规程设计。
希望通过对总滑动轴承盖的加工工艺规程的设计,可以进一步学习《机械制造工艺学》并掌握简单零件的加工工艺设计。
虽然这是大学以来的第二次课程设计,但毕竟还是第一次接触制造工艺设计,对知识掌握、熟悉程度以及综合运用还会存在问题,因此在设计中难免会有考虑不周全或错误的地方,这些也是第一次设计时常见的问题,希望老师多多批评和指正。
目录一、任务介绍 (4)二、零件的分析 (4)三、确定生产类型 (4)四、确定毛坯 (5)五、工艺规程设计1、选择定位基准 (6)2、制定工艺路线 (6)3、机械加工余量、工序尺寸及公差的确 (7)4、确定切削用量及工时定额 (8)六、参考文献 (13)一、任务介绍本次《机械制造工艺学》课程设计我拿到的题目是“总泵缸体”。
材料为HT200,生产批量为中批量生产,技术要求见左臂壳体的二维图,要求设计该机械加工工艺规程,具体要求内容为:(1)根据生产类型,对零件进行工艺分析;(2)选择毛坯种类及制造方法,绘制毛坯图;(3)制订零件的机械加工工艺过程,选择工序加工设备及工艺装备,确定各工序切削用量及工序尺寸,并计算工序的工时定额;(4)填写工艺文件;(5)撰写设计说明书;二、零件的分析(一)零件的作用题目所给的零件是滑动轴承盖。
它一般与滑动轴承配套使用中,与滑动轴承一起是用来支撑轴的部件,有时也用来支撑轴上的回转零件。
主要起安装、定位支承滑动轴承的作用,零件上方的Φ60孔用来安装滑动轴承,底面用来将滑动轴承组件固定在机器上,2-Φ13孔联接滑动轴承下半部分与轴承座,起联接、调整间隙用。
(二)零件的工艺分析零件的材料为HT200,灰铸铁生产工艺简单,铸造性能优良,但塑性较差、脆性高,不适合磨削,为此以下是滑动轴承盖需要加工的表面以及加工表面之间的尺寸公差要求:1、以φ60为中心的加工表面这一组加工表面包括:φ60的孔,以及其前后端面,前后端面与孔有位置要求,2—φ13通孔与φ60孔有位置要求。
2、以顶部为中心的加工表面这一组加工表面包括:M10螺纹孔、端面。
由上面分析可知,加工时应先加工一组表面,再以这组加工后表面为基准加工另外一组。
由上面分析可知,可以粗加工滑动轴承盖下端面,然后以此作为基准采用专用夹具进行加工,并且保证位置精度要求。
再根据各加工方法的经济精度及机床所能达到的位置精度,并且此滑动轴承盖零件没有复杂的加工曲面,所以根据上述技术要求采用常规的加工工艺均可保证。
三、确定生产类型已知此滑动轴承盖零件的生产纲领为大批生产,所以初步确定工艺安排为:加工过程划分阶段;工序适当集中;加工设备以通用设备为主,大量采用专用工装。
四、确定毛坯(一)确定毛坯种类零件材料为HT200。
考虑零件在机床运行过程中所受冲击不大,零件结构又比较简单,生产类型为中批生产,故选择木摸手工砂型铸件毛坯。
查《机械制造工艺设计简明手册》第41页表2.2-5,选用铸件尺寸公差等级为CT-8。
(二)确定铸件加工余量及形状查《机械制造工艺设计简明手册》第41页表2.2-5,选用加工余量为MA-F级,并查表2.2-4确定各个加工面的铸件机械加工余量,铸件的分型面的选用及加工余量,如下表所示:表1-1简图加工面代号基本尺寸加工余量等级加工余量说明D1 φ60 F 2 2D2 φ64 3.5 铸坯设计D3 Φ1313 铸坯设计D4 Φ8.58.5 铸坯设计T1 44 F 2 单侧加工T2 8 F 2 方便钻孔T3 56 F 2 单侧加工T4 φ66 F 2X2 单侧加工(三)绘制铸件零件图五、工艺规程设计(一)选择定位基准1、粗基准的选择:以零件的底部大端面为主要的定位粗基准,以侧面为辅助粗基准。
2、精基准的选择:考虑要保证零件的加工精度和装夹准确方便,依据“基准重合”原则和“基准统一”原则,以粗加工后的底面为主要的定位精基准,以中心半圆柱表面为辅助的定位精基准。
(二)制定工艺路线根据零件的几何形状、尺寸精度及位置精度等技术要求,以及加工方法所能达到的经济精度,在生产纲领已确定的情况下,可以考虑采用万能性机床配以专用工卡具,并尽量使工序集中来提高生产率。
除此之外,还应当考虑经济效果,以便使生产成本尽量下降。
查《机械制造工艺设计简明手册》第20页表1.4-7、1.4-8、1.4-11,选择零件的加工方法及工艺路线方案如下:(三)机械加工余量、工序尺寸及公差的确定1、圆柱表面工序尺寸:前面根据资料已初步确定工件各面的总加工余量,现在确定各表面的各个加工工序的加工余量如下:表1-22、平面工序尺寸:表1-3(四)确定切削用量及工时定额1、工序03 粗铣、精铣T1端面,以T1端面距离为44的表面粗基准。
(1)加工条件工件材料:HT200,σb =170~240MPa ,铸造;工件尺寸:a emax =55mm ,l=236mm; 加工要求:粗铣、精铣T1端面,加工余量2mm; 机床:X51立式铣床;刀具:YG6硬质合金端铣刀。
铣削宽度a e ≤90,深度a p ≤6,齿数z=12,故根据《机械制造工艺设计简明手册》(后简称《简明手册》)表3.1,取刀具直径d 0=125mm 。
根据《切削用量手册》(后简称《切削手册》)表3.16,选择刀具前角γ0=0°后角α0=8°,副后角α0’=10°,刃倾角:。
,副偏角过渡刃主偏角’OO O O =K =K =K -=530,60,10γγεγλs (2)切削用量 ①确定切削深度a p因为余量较小,故选择a p =2mm ,一次走刀即可完成。
②确定每齿进给量f z由于本工序为粗加工,尺寸精度和表面质量可不考虑,从而可采用不对称端铣,以提高进给量提高加工效率。
根据《切削手册》表3.5,使用YG6硬质合金端铣刀加工,机床功率为4.5kw (据《简明手册》表4.2-35,X51立式铣床)时: f z =0.09~0.18mm/z 故选择:f z =0.18mm/z 。
③确定刀具寿命及磨钝标准根据《切削手册》表3.7,铣刀刀齿后刀面最大磨损量为1.5mm ;由于铣刀直径d 0=125mm ,故刀具使用寿命T=180min (据《简明手册》表3.8)。
④计算切削速度v c 和每分钟进给量v f根据《切削手册》表3.16,当d 0=125mm ,Z=12,a p ≤7.5,f z ≤0.18mm/z 时,v t =98m/min,n t =250r/min,v ft =471mm/min 。
各修正系数为:k MV = 1.0,k SV = 0.8。
切削速度计算公式为:v pv e v z v p T vv c k z u a y f x a q d c v vm0=其中 mm a e 55=,mm a p 2=,245=v C ,2.0=q v ,15.0=x v ,35.0=y v ,8.08.00.1=⨯=⋅=k k k Sv Mv v ,2.0=u v ,0=p v ,32.0=m ,min 180=T ,z mm f z /18.0=,12=Z ,将以上数据代入公式:min/3.2868.0122.05535.008.015.021802.012524532.0m v c =⨯⨯⨯⨯⨯⨯⨯⨯⨯⨯=确定机床主轴转速: min /7291000r d v n wcs ==π。
根据《简明手册》表4.2-36,选择n c =725r/min,v fc =390mm/min,因此,实际进给量和每分钟进给量为:v c =10000n d π=100072512514.3⨯⨯m/min=284.5m/minf zc =v fc /n c z=390/300×12 mm/z=0.1mm/z⑤校验机床功率根据《切削手册》表3.24,近似为Pcc=3.3kw,根据机床使用说明书,主轴允许功率Pcm=4.5×0.75kw=3.375kw>Pcc 。
故校验合格。
最终确定:a p =2.0mm ,n c =725r/min ,v f =390mm/s ,v c =118m/min ,f z =0.1mm/z 。
⑥计算基本工时t m =L/ v f ,L=l+ y+Δ,l=236mm.查《切削手册》表3. 26,入切量及超切量为:y+Δ=40mm ,则: t m =L/ V f =(236+40)/390=0.71min 。
2、工序04 粗铣、精铣T3端面,以T1为定位基准。
刀具:YG6硬质合金端铣刀; 机床:X51立式铣床;查《切削手册》表3.5,进给量为:min /0.1~5.0mm f z =,取为0.5mm/r参考有关手册,确定min /124m v =,采用YG6硬质合金端铣刀,12,125==z mm d w ,则:min /31612512410001000r d vn ws =⨯⨯==ππ现采用X51立式铣床,根据《简明手册》表4.2-36,取min /300r n w =,故实际切削速度:min /75.11710003001251000m n d v ww =⨯⨯==ππ当min /300r n w =时,工作台每分钟进给量:min /1800300125.0mm n z f f w z m =⨯⨯=⋅⋅=,取为980mm/min 本工序切削时间为:153.098012525=+===f l t t mm min3、工序05 粗铣、精铣Φ60孔后端面,以T1、Φ60孔前端面为定位基准。
刀具:YG6硬质合金端铣刀; 机床:X51立式铣床;查《切削手册》表3.5,进给量为:min /0.1~5.0mm f z =,取为0.5mm/r参考有关手册,确定min /124m v =,采用YG6硬质合金端铣刀,12,125==z mm d w ,则:min /31612512410001000r d vn ws =⨯⨯==ππ现采用X51立式铣床,根据《简明手册》表4.2-36,取min /300r n w =,故实际切削速度:min /75.11710003001251000m n d v ww =⨯⨯==ππ当min /300r n w =时,工作台每分钟进给量:min /1800300125.0mm n z f f w z m =⨯⨯=⋅⋅=,取为980mm/min 本工序切削时间为:161.098012533=+===f l t t m m min 4、工序06 粗铣、精铣Φ60孔前端面,以T1、Φ60孔后端面为定位基准。