货车轻量化涉及的几种新材料技术
车轻量化(微发泡、薄壁化、以塑代钢)技术应用介绍

薄壁化材料的运用
薄壁化材料运用的优点
能够满足一般产品的性能试验要求,无特殊要求 单品重量减少,能够节省材料投入,通常节省8%~12% 注塑周期缩短,提高生产效率;无需特殊注塑设备,易推广应用
薄壁化材料的运用
模具开发的要求及特点
薄壁化材料的运用
薄壁化材料的运用
产品试制验证及实验方面的要求及特点;
与一般注塑产品相同,无特殊要求
薄壁化材料的运用
应用实例 基本壁厚1.2mm
薄壁化材料的运用
应用实例
用
前端模块简介
• 在汽车行业,为了降低成本,提高竞争力,模块化的设计生产已经成为趋势, “前端模块”应运而生。
• 前端模块将传统意义上的散热器框架集成化,形成一个相对独立的整体连接到 白车身。
• 尤其对于车型改制时,只需变更不同的前端模块(设计)即可。
19
以塑代钢技术的运用
前端模块功能
• 前端安装平台
– 为位于白车身前部的各组件提供挂载 点
• 前端支撑平台
– 挂载各组件后静态&动态载荷下变形 满足设计要求
汽车轻量化(微发泡、薄壁化、以塑代钢) 技术应用介绍
1 背景技术
2 微发泡技术的运用
3
薄壁化技术的运用
4 以塑代钢技术的运用
随着时中国汽车产业的高速发展,汽车的质量要求越来越高产业分布 和结构优化迅猛加速,零部件的整体设计制造及成本控制水平将体现各厂家 的核心竞争力。而零部件的薄壁化设计技术是发展方向之一,特别是近年汽 车轻量化快速发展,零部件的轻量化设计水平已经成为衡量各汽车设计中心 技术能力的一个重要指标。对于轻量化的研究引用, 目前与各材料厂家合作 开发、采用高流动性、高韧性、高强度、高刚性的微发泡材料、薄壁化注塑 材料以及以塑代钢材料,同时进行微发泡、薄壁化以及以塑代钢产品结构设 计。
新型轻量化材料和制造工艺
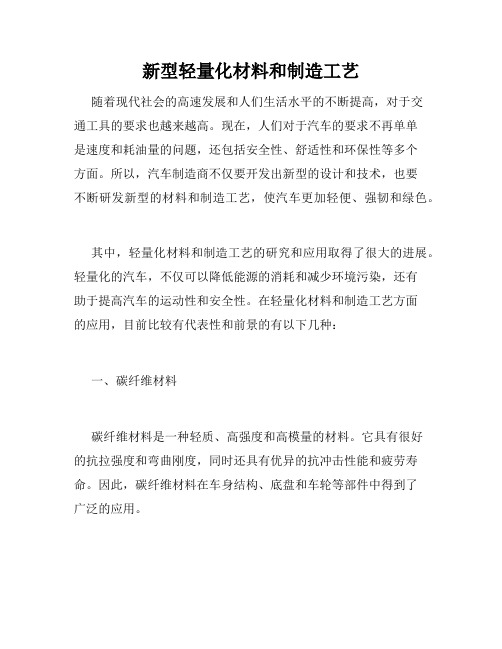
新型轻量化材料和制造工艺随着现代社会的高速发展和人们生活水平的不断提高,对于交通工具的要求也越来越高。
现在,人们对于汽车的要求不再单单是速度和耗油量的问题,还包括安全性、舒适性和环保性等多个方面。
所以,汽车制造商不仅要开发出新型的设计和技术,也要不断研发新型的材料和制造工艺,使汽车更加轻便、强韧和绿色。
其中,轻量化材料和制造工艺的研究和应用取得了很大的进展。
轻量化的汽车,不仅可以降低能源的消耗和减少环境污染,还有助于提高汽车的运动性和安全性。
在轻量化材料和制造工艺方面的应用,目前比较有代表性和前景的有以下几种:一、碳纤维材料碳纤维材料是一种轻质、高强度和高模量的材料。
它具有很好的抗拉强度和弯曲刚度,同时还具有优异的抗冲击性能和疲劳寿命。
因此,碳纤维材料在车身结构、底盘和车轮等部件中得到了广泛的应用。
目前,碳纤维材料的制造和加工工艺已经相对成熟,可以利用碳纤维预浸料等材料进行成型和固化,可以制造出各种不同形状的零部件。
不过,碳纤维材料的价格相对较高,目前仍有一定的市场限制。
但是随着其应用领域的不断扩大,相信碳纤维材料的价格会逐渐下降,产业规模也会得到相应的扩大。
二、镁合金材料镁合金是一种轻质、高强度的材料,具有优异的机械性能和良好的成形性能。
它的比重只有铝合金的两 thirds,却具有比钢材和铝合金更高的比强度和比刚度。
因此,镁合金广泛应用于汽车的轻量化,如车身和发动机等部位。
不过,在镁合金的缺点也是显而易见的,它的低耐腐蚀性和易燃性限制了镁合金的应用范围,因此需要采用涂层等措施进行保护和防火。
而且镁合金的加工难度也较高,需要针对性的改进和优化。
三、3D打印技术3D打印技术是一种新型的制造技术,它可以直接从3D模型中制造所需的物品,具有灵活、快速、节约成本等优点。
随着3D打印技术的不断发展和成熟,它在汽车制造中也得到了广泛的应用。
目前,汽车制造商可以利用3D打印技术制造出各种零部件和模型,在更短的时间内完成产品研发、改进和生产。
车身轻量化技术
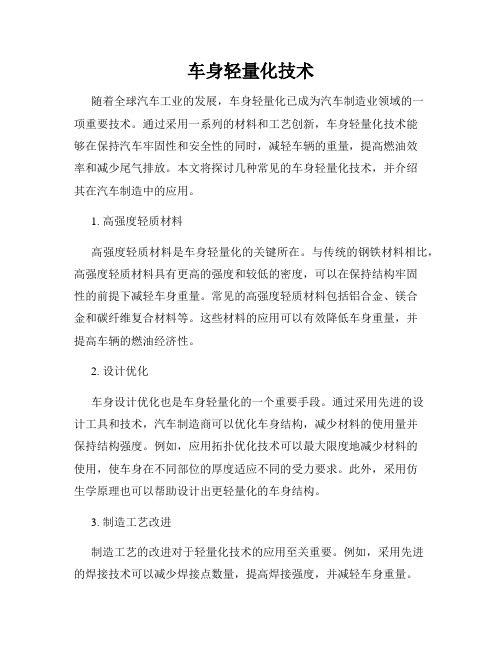
车身轻量化技术随着全球汽车工业的发展,车身轻量化已成为汽车制造业领域的一项重要技术。
通过采用一系列的材料和工艺创新,车身轻量化技术能够在保持汽车牢固性和安全性的同时,减轻车辆的重量,提高燃油效率和减少尾气排放。
本文将探讨几种常见的车身轻量化技术,并介绍其在汽车制造中的应用。
1. 高强度轻质材料高强度轻质材料是车身轻量化的关键所在。
与传统的钢铁材料相比,高强度轻质材料具有更高的强度和较低的密度,可以在保持结构牢固性的前提下减轻车身重量。
常见的高强度轻质材料包括铝合金、镁合金和碳纤维复合材料等。
这些材料的应用可以有效降低车身重量,并提高车辆的燃油经济性。
2. 设计优化车身设计优化也是车身轻量化的一个重要手段。
通过采用先进的设计工具和技术,汽车制造商可以优化车身结构,减少材料的使用量并保持结构强度。
例如,应用拓扑优化技术可以最大限度地减少材料的使用,使车身在不同部位的厚度适应不同的受力要求。
此外,采用仿生学原理也可以帮助设计出更轻量化的车身结构。
3. 制造工艺改进制造工艺的改进对于轻量化技术的应用至关重要。
例如,采用先进的焊接技术可以减少焊接点数量,提高焊接强度,并减轻车身重量。
而采用先进的注塑成型技术可以生产更薄壁的塑料零部件,提高车身整体的轻量化水平。
此外,采用先进的激光切割和冲压技术也可以有效降低车身零部件的重量。
4. 轻量化零部件除了整车轻量化,轻量化零部件的研发和应用也是车身轻量化技术的一个重要方向。
例如,轻量化座椅和轻量化车门等关键部件的采用可以进一步减轻整车重量。
此外,一些先进的轻量化技术还可以应用于车身附件的制造,如轻量化玻璃、轻量化天窗等。
总之,车身轻量化技术对于提高汽车燃油效率和减少尾气排放具有重要意义。
通过采用高强度轻质材料、设计优化、制造工艺改进和轻量化零部件等手段,汽车制造商可以实现车身的轻量化,并带来更节能环保的汽车产品。
在未来,随着技术的不断进步,预计车身轻量化技术将得到进一步的发展和应用。
轻量化汽车材料的研究与应用分析

轻量化汽车材料的研究与应用分析近年来,随着对环境污染和燃油消耗的关注,轻量化成为了汽车行业的研发重点。
通过使用轻量化材料,可以减轻汽车质量,降低油耗、减少尾气排放,提高车辆性能和使用寿命,为汽车行业的可持续发展贡献力量。
轻量化汽车材料主要包括高强度钢、铝合金、镁合金、碳纤维复合材料等。
这些材料相比传统材料具有重量轻、强度高、密度低等优点,被广泛应用于车身、底盘、发动机等方面。
下面就各种材料的研究和应用进行一一分析。
1. 高强度钢高强度钢是目前应用最广泛的轻量化材料之一,具有强度高、延展性好、重量轻等优点。
目前,高强度钢的种类众多,可以根据所需的强度和塑性来选择不同的材料。
高强度钢主要应用于车身结构中,通过使用高强度钢可以减轻车身重量,提升车身的刚性和安全性能。
2. 铝合金铝合金是另一种常用的轻量化材料,相比于钢材,铝合金的密度更低,重量更轻,强度也比较高。
铝合金具有良好的耐腐蚀性和导热性能,在汽车行业中被广泛应用于汽车车身的覆盖件、底盘、发动机以及轮毂等部件。
3. 镁合金镁合金是一种新型轻量化材料,在汽车行业中使用还比较少。
镁合金具有密度低、强度高、耐腐蚀性好等优点,可以大幅减轻车身重量。
同时,镁合金的熔点较低,容易加工,而且可进行循环利用。
目前,镁合金主要应用于汽车车身结构中。
4. 碳纤维复合材料碳纤维复合材料是一种高性能材料,具有强度高、耐腐蚀性好、重量轻等优点。
在汽车行业中,碳纤维复合材料主要应用于高端豪华车型及赛车型号的车身,通过使用这种材料可以提高车辆的性能和设计美感。
总的来说,轻量化材料在汽车行业中具有广泛应用前景,可以减轻车身重量,降低燃油消耗,提高车辆性能和安全性能。
同时,轻量化材料的研究和应用还存在许多挑战,如材料成本高、加工难度大等问题,需要进一步探索和解决。
相信随着技术的进步和研发经验的累积,轻量化材料必将成为汽车行业的一个重要发展方向。
车身轻量化技术的创新与突破
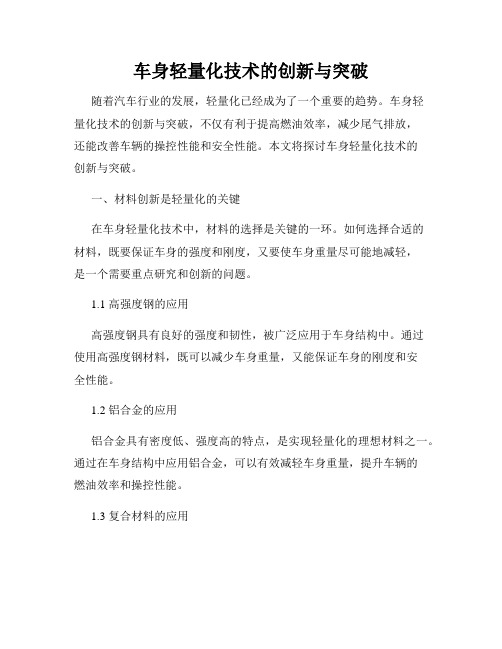
车身轻量化技术的创新与突破随着汽车行业的发展,轻量化已经成为了一个重要的趋势。
车身轻量化技术的创新与突破,不仅有利于提高燃油效率,减少尾气排放,还能改善车辆的操控性能和安全性能。
本文将探讨车身轻量化技术的创新与突破。
一、材料创新是轻量化的关键在车身轻量化技术中,材料的选择是关键的一环。
如何选择合适的材料,既要保证车身的强度和刚度,又要使车身重量尽可能地减轻,是一个需要重点研究和创新的问题。
1.1 高强度钢的应用高强度钢具有良好的强度和韧性,被广泛应用于车身结构中。
通过使用高强度钢材料,既可以减少车身重量,又能保证车身的刚度和安全性能。
1.2 铝合金的应用铝合金具有密度低、强度高的特点,是实现轻量化的理想材料之一。
通过在车身结构中应用铝合金,可以有效减轻车身重量,提升车辆的燃油效率和操控性能。
1.3 复合材料的应用复合材料由多种材料组合而成,具有重量轻、强度高、刚度好的特点。
在车身轻量化中,复合材料的应用可以实现更大范围的重量减轻,提升车辆的整体性能。
二、设计创新是轻量化的关键除了材料创新,设计创新也是实现车身轻量化的重要手段。
通过改变原有的设计思路和方法,可以实现轻量化的突破。
2.1 结构优化设计通过结构优化设计,可以在保证车身强度和安全性的前提下,减少车身的材料使用量,从而实现车身的轻量化。
2.2 制造工艺创新通过改进车身的制造工艺,可以降低车身的成本和重量。
例如,采用先进的焊接技术和粘接技术,可以减少焊接接头的数量和重量。
2.3 外形设计优化合理的外形设计可以减少空气阻力,降低燃油消耗。
通过优化车身外形,可以实现车身的轻量化和空气动力学性能的提升。
三、技术创新是轻量化的关键除了材料和设计的创新,技术的创新也是实现车身轻量化的关键所在。
下面将介绍一些具有创新性的技术在轻量化方面的应用。
3.1 激光焊接技术激光焊接技术具有焊接速度快、焊缝质量好等优点。
在车身轻量化中,可以采用激光焊接技术来替代传统的点焊和线焊,从而减少焊接接头的数量和重量。
汽车轻量化材料及工艺的研究与应用
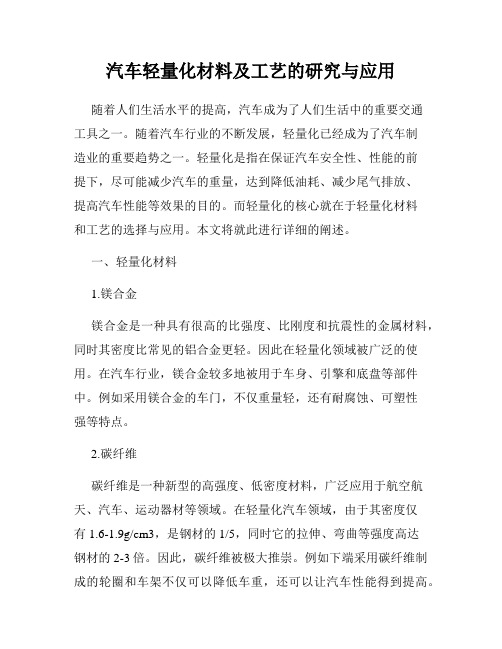
汽车轻量化材料及工艺的研究与应用随着人们生活水平的提高,汽车成为了人们生活中的重要交通工具之一。
随着汽车行业的不断发展,轻量化已经成为了汽车制造业的重要趋势之一。
轻量化是指在保证汽车安全性、性能的前提下,尽可能减少汽车的重量,达到降低油耗、减少尾气排放、提高汽车性能等效果的目的。
而轻量化的核心就在于轻量化材料和工艺的选择与应用。
本文将就此进行详细的阐述。
一、轻量化材料1.镁合金镁合金是一种具有很高的比强度、比刚度和抗震性的金属材料,同时其密度比常见的铝合金更轻。
因此在轻量化领域被广泛的使用。
在汽车行业,镁合金较多地被用于车身、引擎和底盘等部件中。
例如采用镁合金的车门,不仅重量轻,还有耐腐蚀、可塑性强等特点。
2.碳纤维碳纤维是一种新型的高强度、低密度材料,广泛应用于航空航天、汽车、运动器材等领域。
在轻量化汽车领域,由于其密度仅有1.6-1.9g/cm3,是钢材的1/5,同时它的拉伸、弯曲等强度高达钢材的2-3倍。
因此,碳纤维被极大推崇。
例如下端采用碳纤维制成的轮圈和车架不仅可以降低车重,还可以让汽车性能得到提高。
3.铝合金铝合金是一种轻量、结构强度高、耐腐蚀、抗震性好等特点的金属材料。
因此在汽车制造业中得到广泛的应用。
目前,众多汽车生产商,例如宝马、奥迪等都采用铝合金制造车身结构框架,如宝马采用了大量的铝合金制造车身结构框架,使车身重量比同类车型轻500-1,000公斤。
4.钛合金钛合金是一种相对来说比较昂贵的金属材料,但是它的优点也是显而易见的。
例如钛合金比钢材轻40%,比铝材更轻盈,同时其耐腐蚀性能也非常优秀。
在汽车轻量化领域,钛合金可以用于各种零部件的制造,例如发动机、变速器等。
二、轻量化工艺1.冷成形冷成形是一种在保证材料性质和机械性能的前提下,采用冷挤压机进行轻量化成形材料加工工艺的方法。
通过利用外重锤和内空心压头的相互作用,将材料压入模具中成型。
这种工艺可以避免对材料的脆化,保持了材料的强度和抗震性能。
汽车领域的五大轻量化材料
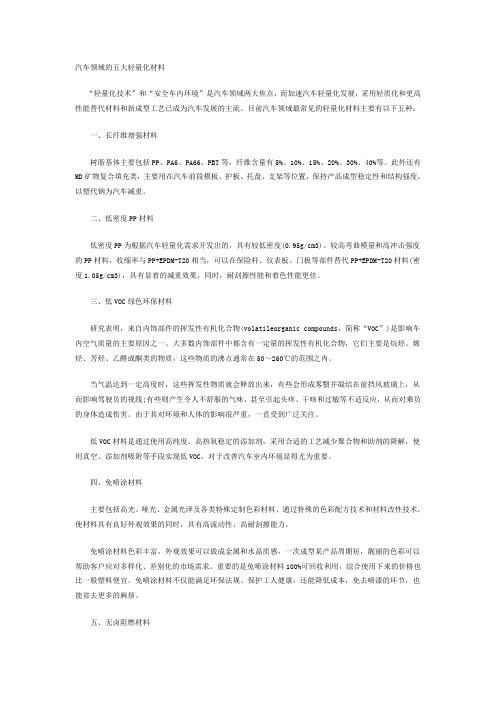
汽车领域的五大轻量化材料“轻量化技术”和“安全车内环境”是汽车领域两大焦点,而加速汽车轻量化发展,采用轻质化和更高性能替代材料和新成型工艺已成为汽车发展的主流。
目前汽车领域最常见的轻量化材料主要有以下五种:一、长纤维增强材料树脂基体主要包括PP、PA6、PA66、PBT等,纤维含量有5%、10%、15%、20%、30%、40%等。
此外还有MD矿物复合填充类,主要用在汽车前段模板、护板、托盘、支架等位置,保持产品成型稳定性和结构强度,以塑代钢为汽车减重。
二、低密度PP材料低密度PP为根据汽车轻量化需求开发出的,具有较低密度(0.95g/cm3)、较高弯曲模量和高冲击强度的PP材料,收缩率与PP+EPDM-T20相当,可以在保险杆、仪表板、门板等部件替代PP+EPDM-T20材料(密度1.05g/cm3),具有显着的减重效果,同时,耐刮擦性能和着色性能更佳。
三、低VOC绿色环保材料研究表明,来自内饰部件的挥发性有机化合物(volatileorganic compounds,简称“VOC”)是影响车内空气质量的主要原因之一。
大多数内饰部件中都含有一定量的挥发性有机化合物,它们主要是烷烃、烯烃、芳烃、乙醛或酮类的物质,这些物质的沸点通常在50~260℃的范围之内。
当气温达到一定高度时,这些挥发性物质就会释放出来,有些会形成雾翳并凝结在前挡风玻璃上,从而影响驾驶员的视线;有些则产生令人不舒服的气味,甚至引起头疼、干咳和过敏等不适反应,从而对乘员的身体造成伤害。
由于其对环境和人体的影响很严重,一直受到广泛关注。
低VOC材料是通过使用高纯度、高热氧稳定的添加剂,采用合适的工艺减少聚合物和助剂的降解,使用真空、添加剂吸附等手段实现低VOC,对于改善汽车室内环境显得尤为重要。
四、免喷涂材料主要包括高光、哑光、金属光泽及各类特殊定制色彩材料、通过特殊的色彩配方技术和材料改性技术,使材料具有良好外观效果的同时,具有高流动性、高耐刮擦能力。
汽车制造中的轻量化材料应用

汽车制造中的轻量化材料应用在当今的汽车制造领域,轻量化已经成为了一个至关重要的发展趋势。
随着环保要求的日益严格和消费者对燃油经济性的关注不断增加,汽车制造商们纷纷致力于减轻车辆的重量,以提高性能、降低能耗和减少排放。
而实现汽车轻量化的关键之一,就在于广泛应用各种轻量化材料。
一、轻量化材料的种类及特点1、铝合金铝合金是汽车制造中应用较为广泛的轻量化材料之一。
它具有密度小、强度高、耐腐蚀等优点。
相较于传统的钢铁材料,铝合金的重量可以减轻约 40% 50%。
在汽车的车身、发动机缸体、轮毂等部件中,铝合金的应用越来越常见。
例如,一些高端汽车品牌的车身结构采用了全铝合金材质,不仅减轻了车身重量,还提升了车辆的操控性能和加速性能。
2、镁合金镁合金是目前已知的最轻的金属结构材料之一,其密度约为铝合金的三分之二。
它具有良好的减震性能和电磁屏蔽性能,在汽车仪表板骨架、座椅骨架、方向盘等部件中有着广阔的应用前景。
然而,镁合金的强度相对较低,且耐腐蚀性较差,这在一定程度上限制了其在汽车制造中的大规模应用。
3、碳纤维复合材料碳纤维复合材料具有极高的强度和刚度,同时重量极轻。
它的强度可以达到钢铁的数倍,而重量却只有其几分之一。
在高性能跑车和赛车中,碳纤维复合材料常用于车身、底盘等关键部件,以实现极致的轻量化效果。
但由于其成本高昂,目前在普通量产汽车中的应用还相对较少。
4、高强度钢高强度钢并非传统意义上的轻量化材料,但通过采用先进的制造工艺和材料配方,新型高强度钢在保持强度的同时,可以显著减轻重量。
例如,热成型高强度钢的应用,可以使车身结构在满足安全性能要求的前提下,实现一定程度的轻量化。
二、轻量化材料在汽车制造中的应用案例1、特斯拉 Model S特斯拉 Model S 作为一款具有代表性的电动汽车,在轻量化方面做了很多努力。
其车身采用了铝合金和高强度钢的混合结构,既保证了车身的强度和安全性,又有效地减轻了重量。
此外,车内的一些零部件也采用了碳纤维复合材料,进一步降低了整车重量。
新材料在汽车轻量化技术中的应用

新材料在汽车轻量化技术中的应用随着汽车工业的快速发展,轻量化技术已经成为了汽车制造业的一个重要趋势。
轻量化技术可以降低汽车的油耗和排放,提高汽车的性能和安全性。
而新材料的应用则是轻量化技术的重要手段之一。
本文将介绍新材料在汽车轻量化技术中的应用。
一、碳纤维复合材料碳纤维复合材料是一种轻质高强度的材料,具有优异的机械性能和耐腐蚀性能。
在汽车制造中,碳纤维复合材料可以用于制造车身、底盘、发动机罩等部件,可以大幅度降低汽车的重量,提高汽车的性能和燃油经济性。
目前,许多汽车制造商都已经开始采用碳纤维复合材料来制造高端车型,如保时捷、法拉利等。
二、镁合金镁合金是一种轻质高强度的金属材料,具有良好的加工性能和耐腐蚀性能。
在汽车制造中,镁合金可以用于制造车身、底盘、发动机等部件,可以大幅度降低汽车的重量,提高汽车的燃油经济性和安全性。
目前,许多汽车制造商都已经开始采用镁合金来制造汽车部件,如宝马、奥迪等。
三、铝合金铝合金是一种轻质高强度的金属材料,具有良好的加工性能和耐腐蚀性能。
在汽车制造中,铝合金可以用于制造车身、底盘、发动机等部件,可以大幅度降低汽车的重量,提高汽车的燃油经济性和安全性。
目前,许多汽车制造商都已经开始采用铝合金来制造汽车部件,如特斯拉、福特等。
四、高强度钢高强度钢是一种轻质高强度的钢材,具有良好的机械性能和耐腐蚀性能。
在汽车制造中,高强度钢可以用于制造车身、底盘、发动机等部件,可以大幅度降低汽车的重量,提高汽车的燃油经济性和安全性。
目前,许多汽车制造商都已经开始采用高强度钢来制造汽车部件,如大众、丰田等。
总之,新材料在汽车轻量化技术中的应用已经成为了汽车制造业的一个重要趋势。
随着新材料技术的不断发展和应用,汽车的轻量化将会越来越普及,汽车的性能和燃油经济性也将会得到进一步提高。
汽车轻量化材料成型工艺分析

汽车轻量化材料成型工艺分析汽车轻量化是现代汽车工业发展的重要趋势之一,它能够显著提高汽车的燃油效率、降低排放、提升操控性能和安全性。
轻量化材料的应用和成型工艺是实现汽车轻量化的关键。
本文将探讨汽车轻量化材料的种类、成型工艺及其在汽车制造中的应用。
一、汽车轻量化材料的种类汽车轻量化材料主要包括高强度钢、铝合金、镁合金、复合材料等。
这些材料具有密度低、强度高、耐腐蚀性好等特点,是实现汽车轻量化的理想选择。
1.1 高强度钢高强度钢是汽车轻量化中应用最广泛的材料之一。
它通过优化合金成分和热处理工艺,实现了强度和韧性的双重提升。
高强度钢在汽车车身、底盘等关键部位的应用,可以有效降低整车重量,同时保持良好的安全性能。
1.2 铝合金铝合金以其低密度、高比强度和良好的铸造性能,成为汽车轻量化的另一重要材料。
铝合金可以通过铸造、锻造、挤压等工艺成型,广泛应用于汽车的发动机、变速箱、车身结构件等部件。
1.3 镁合金镁合金是所有结构材料中密度最低的金属,其密度仅为铝的2/3,钢的1/4。
镁合金的强度和刚度较高,且具有良好的阻尼性能和电磁屏蔽性能,适用于汽车的仪表板、座椅框架、轮毂等部件。
1.4 复合材料复合材料是由两种或两种以上不同材料组合而成的新型材料,具有重量轻、强度高、耐腐蚀等优点。
在汽车领域,常用的复合材料包括碳纤维增强塑料(CFRP)、玻璃纤维增强塑料(GFRP)等。
这些材料在汽车的车身、内饰、底盘等部位的应用,可以显著降低汽车的重量。
二、汽车轻量化材料的成型工艺汽车轻量化材料的成型工艺是实现材料性能的关键环节,不同的材料和应用场景需要采用不同的成型工艺。
2.1 铸造工艺铸造是将熔融金属倒入模具中,待其冷却凝固后形成所需形状的工艺。
对于铝合金和镁合金等材料,铸造工艺可以实现复杂形状的成型,且成本相对较低。
常见的铸造工艺包括砂型铸造、金属型铸造、低压铸造等。
2.2 锻造工艺锻造是通过施加外力使金属形成所需形状的工艺,它能够提高材料的密实度和强度。
电动载货车多材料底盘结构轻量化关键技术开发

电动载货车多材料底盘结构轻量化关键技术开发1. 引言随着环境保护意识的增强和对燃油消耗的担忧,电动载货车在物流运输领域的应用越来越受到关注。
然而,为了提高电动载货车的续航里程和运载能力,轻量化技术成为必不可少的关键技术之一。
本文将重点介绍电动载货车多材料底盘结构轻量化的关键技术开发。
2. 多材料底盘结构设计多材料底盘结构设计是实现电动载货车轻量化的核心内容之一。
传统的钢铁底盘结构具有良好的刚性和强度,但重量较大。
因此,采用多种材料组合设计可以在保证强度和刚性的同时减少整体重量。
2.1 材料选择在多材料底盘结构设计中,需要根据不同部位对强度、刚性和耐磨性等要求选择合适的材料。
常见的轻质材料包括铝合金、复合材料和高强度钢等。
铝合金具有优异的轻量化性能和良好的耐腐蚀性能,可以用于底盘结构的关键部位。
复合材料由纤维增强基体和树脂基体组成,具有高强度、低密度和优异的耐腐蚀性能,可用于减少底盘结构的自重。
高强度钢具有较高的抗拉强度和刚性,可以用于提高底盘结构的整体强度。
2.2 结构设计多材料底盘结构设计需要考虑到不同材料之间的连接方式和布局。
常见的设计方法包括焊接、铆接和粘接等。
焊接是一种常用的连接方式,可以在不同材料之间实现牢固的连接。
然而,焊接会导致热变形和应力集中等问题,需要合理选择焊接位置和参数。
铆接是一种适用于多材料连接的方法,具有较好的可靠性和可拆卸性。
粘接技术可以在不同材料之间实现均匀分布应力,并且无需进行热处理。
3. 轻量化关键技术除了多材料底盘结构设计外,还有一些关键技术可以进一步实现电动载货车的轻量化。
3.1 结构优化通过结构优化可以在不改变底盘总体形状和功能的情况下减少材料使用量。
结构优化方法包括拓扑优化、参数优化和材料优化等。
拓扑优化是一种基于有限元分析的方法,通过调整结构的连通性和形状来达到减重的目的。
参数优化是在给定约束条件下,通过调整设计参数来实现最佳轻量化效果。
材料优化是选择合适的材料以满足设计要求并减少重量。
汽车轻量化技术中新材料的发展及应用
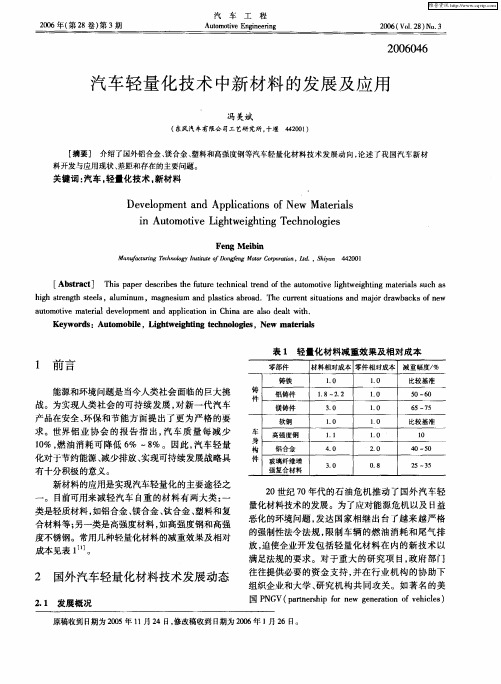
[ bt c] T i ppr ec bsh t eeh i lr d fh t o v lh e h n a r lsc A s at r h ae ds i eu r t n a t n e u m te i t i t g t is uh s s r e t f u c c e o t a o i g w g i m e a a
求。世界铝业 协会 的报 告指 出, 车质 量每 减少 汽
镁铸件
软钢 生 身 构 高强度钢
3O .
1O . 11
.
1O .
1O .
1O .
6 7 5— 5
比较基准
1 0
1% , 0 燃油 消耗可降低 6 一 % 。因此 , % 8 汽车轻量 化对于节约能源、 减少排放、 实现可持续发展战略具
a tmoiemae ild v lp n n p l aini hn r l e l wi . uo t tr e eo me t d a pi t C iaaeas d at t v a a c o n o h
Ke w r s Auo bl, ihw i ln c n lge , w ma r l y o d : tmo i L g t eg f gt h oo i Ne t i s e ii e s e a
类是轻质材料 , 如铝合金 、 镁合金 、 钛合金 、 塑料和复
合材料等; 另一类是高强度材料 , 如高强度钢和高强 度不锈钢。常用几种轻量化材料的减重效果及相对
成本 见表 1 。 …
的强制性法令法规 , 限制车辆的燃 油消耗和尾气 排 放, 迫使企业开发包括轻量化材料在 内的新技 术以 满足法规的要求。对 于重大 的研究项 目, 政府部门
汽车轻量化材料技术发展现状
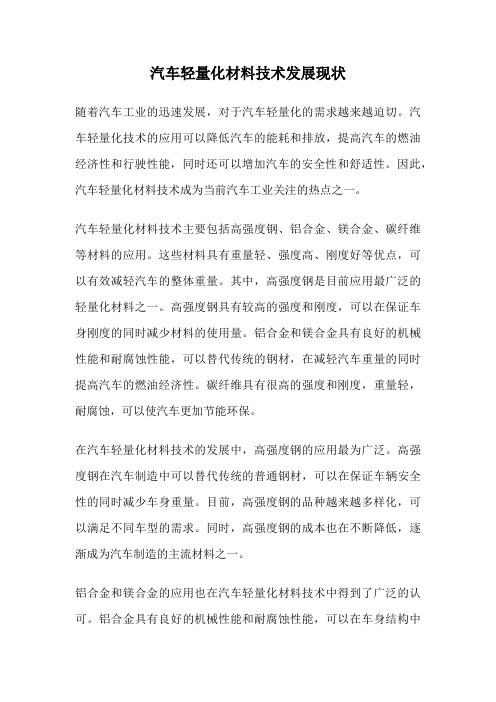
汽车轻量化材料技术发展现状随着汽车工业的迅速发展,对于汽车轻量化的需求越来越迫切。
汽车轻量化技术的应用可以降低汽车的能耗和排放,提高汽车的燃油经济性和行驶性能,同时还可以增加汽车的安全性和舒适性。
因此,汽车轻量化材料技术成为当前汽车工业关注的热点之一。
汽车轻量化材料技术主要包括高强度钢、铝合金、镁合金、碳纤维等材料的应用。
这些材料具有重量轻、强度高、刚度好等优点,可以有效减轻汽车的整体重量。
其中,高强度钢是目前应用最广泛的轻量化材料之一。
高强度钢具有较高的强度和刚度,可以在保证车身刚度的同时减少材料的使用量。
铝合金和镁合金具有良好的机械性能和耐腐蚀性能,可以替代传统的钢材,在减轻汽车重量的同时提高汽车的燃油经济性。
碳纤维具有很高的强度和刚度,重量轻,耐腐蚀,可以使汽车更加节能环保。
在汽车轻量化材料技术的发展中,高强度钢的应用最为广泛。
高强度钢在汽车制造中可以替代传统的普通钢材,可以在保证车辆安全性的同时减少车身重量。
目前,高强度钢的品种越来越多样化,可以满足不同车型的需求。
同时,高强度钢的成本也在不断降低,逐渐成为汽车制造的主流材料之一。
铝合金和镁合金的应用也在汽车轻量化材料技术中得到了广泛的认可。
铝合金具有良好的机械性能和耐腐蚀性能,可以在车身结构中替代钢材,减少车身重量,提高汽车的燃油经济性。
镁合金具有更轻的重量和更好的刚度,可以在发动机和底盘等部位替代传统的铝合金材料,进一步减轻汽车的整体重量,提高汽车的操控性能。
碳纤维作为一种新型的轻量化材料,具有很高的强度和刚度,重量轻,耐腐蚀,因此在高端汽车制造中得到了广泛的应用。
然而,碳纤维的成本较高,制造工艺复杂,限制了其在大规模汽车生产中的应用。
目前,科学家和工程师们正在研究和开发更加经济高效的碳纤维制造工艺,以降低碳纤维材料的成本,推动其在汽车轻量化领域的应用。
总的来说,汽车轻量化材料技术的发展取得了显著的进展。
高强度钢、铝合金、镁合金和碳纤维等轻量化材料的应用不断推动汽车工业的发展。
汽车轻量化材料研究及应用

汽车轻量化材料研究及应用随着经济的发展和人们生活水平的提高,汽车越来越成为人们生活中不可或缺的一部分。
随之而来的问题就是汽车对环境的影响以及能源的消耗。
为了解决这些问题,汽车制造业界将目光聚焦在轻量化技术上。
轻量化技术是指计算机辅助设计、材料科学、制造加工、车辆技术等多学科综合应用技术,主要是采用轻质、高强耐用且成本相对较低的材料来替代重量大、质量低、成本高的传统材料,从而降低汽车的整车重量,提高汽车的环保性能和使用效能。
1. 轻量化材料的种类及特点目前,在轻量化技术中被广泛应用的材料主要包括高强度钢、铝合金、镁合金、塑料、碳纤维等。
这些新型材料在强度与刚度、耐腐蚀性、成本和加工性等方面具有独特的优点,已经广泛应用于汽车工业和其他领域。
高强度钢是目前企业广泛选择的一种轻量化材料。
与普通钢相比,高强度钢密度低,强度和刚度高,因此可以用较少的材料量制造出相同的零件,也可以站在更高的安全标准。
铝合金是另一种被广泛应用于汽车轻量化的新型材料。
轻质而高强度是铝合金的突出优点。
据估算,用铝合金取代钢材制造部分汽车结构,整车重量可以减轻20%-30%。
镁合金的密度比铝合金更低,强度也高。
镁合金的优点在于加工性能好,可以采用压铸和挤压成型等技术制造车身件,综合考虑经济、生产成本、安全和环保等因素,镁合金的使用量可能会稳步增加。
塑料是轻量化面板、覆盖件和内饰件的流行选项。
不同种类的塑料具有不同的性能特点,比如PEI(多酰胺酰亚胺醚)和PPO (聚苯醚),这些塑料可以与阻燃剂等添加剂共同使用,以实现更好的机械性能和耐磨性。
碳纤维是一种非常轻的、但仍然很强的材料,它的密度只有钢材的1/5左右。
使用碳纤维可以将整车重量降低30%-60%。
但是,碳纤维的成本比传统材料高,不过在进一步的发展和进步下,它有望成为未来汽车轻量化的主流。
2. 轻量化材料的应用及优点使用轻量化材料的优点在于,它们可以显著降低汽车整体的重量,从而达到节能降耗、降低相关排放、提高行驶里程、增强安全性等多重目标的效果。
汽车制造中的轻量化技术研究

汽车制造中的轻量化技术研究一、引言随着汽车市场的不断扩大,人们对汽车的需求也越来越高。
轻量化技术是现代汽车制造中的一个重要技术,它可以降低汽车的重量,减少能源消耗和环境污染。
本文将介绍汽车制造中的轻量化技术研究,包括轻量化材料、结构优化和制造技术等方面。
二、轻量化材料1. 铝合金铝合金是一种轻质高强度的材料,具有良好的耐腐蚀性、可塑性和热处理性能。
在汽车制造中,铝合金常用于制造车身、底盘和发动机部件等,可以有效地降低汽车的重量。
2. 高强度钢高强度钢具有较高的强度和刚度,并且可以在耐冲击性方面表现良好。
在汽车制造中,高强度钢用于制造车身、车门和悬挂系统等,可以显著地降低汽车的重量。
3. 碳纤维复合材料碳纤维复合材料是一种轻量化高强度材料,具有良好的刚性和抗拉强度。
在汽车制造中,碳纤维复合材料常用于制造车身和底盘等部件,可以显著地降低汽车的重量。
三、结构优化1. 设计优化通过采用优化的设计方案,例如优化车身结构,可以最大限度地减轻汽车重量,并提高车身刚度和强度。
此外,设计优化还可以减少零部件数量,简化生产工艺。
2. 模拟仿真通过使用计算机辅助设计软件对汽车结构进行模拟仿真分析,可以帮助优化和改进汽车的结构和构造,以提高汽车的性能和轻量化程度。
此外,模拟仿真还可以提前发现潜在的设计缺陷,从而提高汽车的安全性。
四、制造技术1. 先进制造技术先进制造技术可以提高汽车零部件的精度和质量,减少生产过程中的浪费和损耗,从而降低汽车的制造成本和重量。
例如,采用先进的3D打印技术可以生产轻量化的复杂零部件,并减少废料和成本。
2. 节能制造技术节能制造技术可以降低汽车制造过程中的耗能和排放,从而减少对环境的影响。
例如,采用节能的喷涂工艺可以降低汽车涂装过程中的排放和浪费,同时提高喷涂的质量和效率。
五、结论通过介绍汽车制造中轻量化技术的研究,可以看出轻量化材料、结构优化和制造技术是汽车轻量化的重要手段。
未来,随着汽车市场的不断发展和消费者对环保、节能、安全的需求不断提高,汽车制造业将进一步探索和研究轻量化技术,促进汽车制造业的可持续发展。
卡车轻结构趋势引发的新材料应用

卡车轻结构趋势引发的新材料应用摘要:卡车轻量化就是在不断优化零部件结构、尺寸基础上,再应用各种新型轻量化材料,实现汽车轻量化的目的。
通过对一些创新性材料的应用,如高强度钢、铝镁合金、工程塑料、碳纤维复合材料等应用,以达成整车轻量化的设计目标。
现阶段各汽车生产商已经认识到新材料应用在轻量化方面的重要性。
卡车做为运输的生产工具,轻量化是其产品竞争力的重要指标之一,轻量化优势可以为用户带来实在收益,做好相关的新材料研究与应用分析,以提升整车的整体的性能,进一步实现对市场的开拓。
关键词:卡车轻结构;新材料;应用研究引言近年来,随着能源与环境危机的恶化程度加剧,各国都加强了对汽车行业产品能耗和排放的控制,卡车轻量化能使产品能耗大大降低,因此受到各国政府大力扶持。
在《节能与新能源汽车技术路线图》以及《节能与新能源汽车技术路线图2.0》中均明确了汽车轻量化技术路线图,并提出到2030年汽车单车用铝量超过350kg,单车使用镁合金45kg,碳纤维使用量占车重5%。
而在“中国制造2025”规划中也明确要求,通过高强度钢、铝镁合金等复合材料在汽车上的应用,实现平均整车减重目标5%至20%。
这就迫使轻量化设计成为汽车产业发展方向之一。
1、卡车轻量化发展现状受能源危机影响和人们对环保要求的日益苛刻,欧、美、日等发达国家很早就开始了卡车轻量化的研究,目前卡车轻量化材料最广泛应用的是高强度钢、铝合金材料、复合材料等,而这些轻量化材料采用技术主要是在一些对成本敏感度不高和对重量较为敏感的高端车型中使用较多。
在欧洲和美国,一方面由于在能耗和排放的政策上越发严格,另一方面目前高端品牌卡车车型主要的生产国家,在新材料、新技术的使用上显得更为热衷,尤其乘用车方面对铝合金、碳纤维等新材料应用方面都处于行业领先地位。
在我国,卡车轻量化越来越受到空前的重视,但受制于技术水平,国内卡车轻量化主要是采用结构轻量化策略,主要结构件基本为钢材,部分非主要承载结构件上如:变速箱、传动轴、钢圈、车架部分横梁、储气筒、油箱、工作台、各种固定支架类等采用铝合金材料,悬架系统钢板弹簧也从少片簧向非金属材料板簧转变,但所占比例较低。
电动载货车多材料底盘结构轻量化关键技术开发
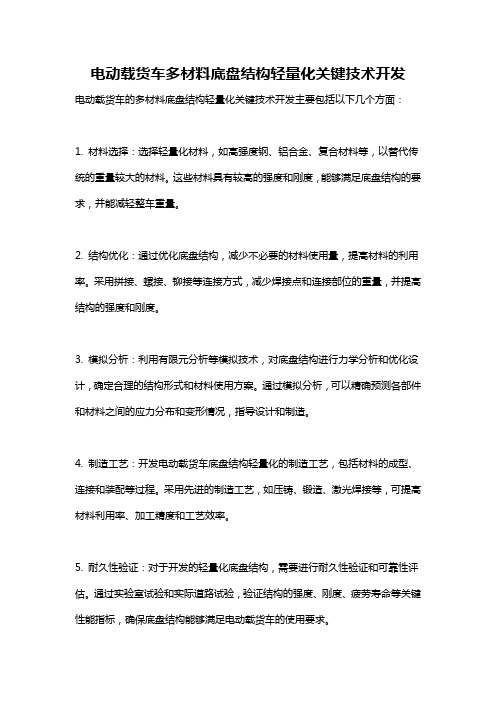
电动载货车多材料底盘结构轻量化关键技术开发电动载货车的多材料底盘结构轻量化关键技术开发主要包括以下几个方面:
1. 材料选择:选择轻量化材料,如高强度钢、铝合金、复合材料等,以替代传统的重量较大的材料。
这些材料具有较高的强度和刚度,能够满足底盘结构的要求,并能减轻整车重量。
2. 结构优化:通过优化底盘结构,减少不必要的材料使用量,提高材料的利用率。
采用拼接、螺接、铆接等连接方式,减少焊接点和连接部位的重量,并提高结构的强度和刚度。
3. 模拟分析:利用有限元分析等模拟技术,对底盘结构进行力学分析和优化设计,确定合理的结构形式和材料使用方案。
通过模拟分析,可以精确预测各部件和材料之间的应力分布和变形情况,指导设计和制造。
4. 制造工艺:开发电动载货车底盘结构轻量化的制造工艺,包括材料的成型、连接和装配等过程。
采用先进的制造工艺,如压铸、锻造、激光焊接等,可提高材料利用率、加工精度和工艺效率。
5. 耐久性验证:对于开发的轻量化底盘结构,需要进行耐久性验证和可靠性评估。
通过实验室试验和实际道路试验,验证结构的强度、刚度、疲劳寿命等关键性能指标,确保底盘结构能够满足电动载货车的使用要求。
综上所述,电动载货车多材料底盘结构轻量化关键技术开发需要从材料选择、结构优化、模拟分析、制造工艺和耐久性验证等方面综合考虑,以实现轻量化和高性能的底盘结构设计。
卡车低风阻新概念及卡车轻量化措施模板
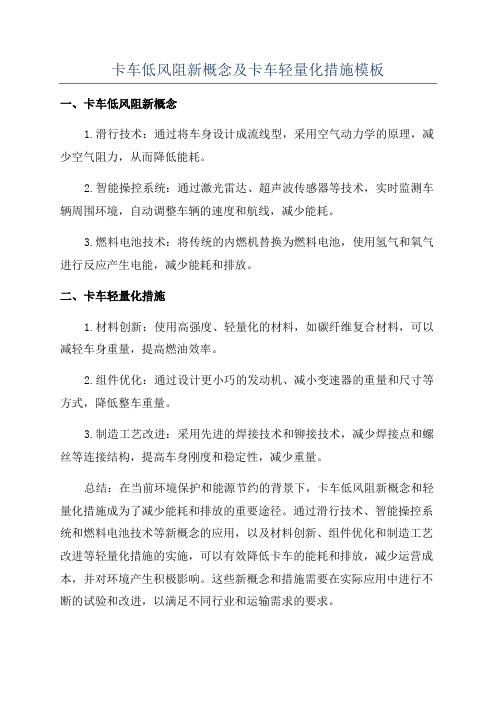
卡车低风阻新概念及卡车轻量化措施模板
一、卡车低风阻新概念
1.滑行技术:通过将车身设计成流线型,采用空气动力学的原理,减少空气阻力,从而降低能耗。
2.智能操控系统:通过激光雷达、超声波传感器等技术,实时监测车辆周围环境,自动调整车辆的速度和航线,减少能耗。
3.燃料电池技术:将传统的内燃机替换为燃料电池,使用氢气和氧气进行反应产生电能,减少能耗和排放。
二、卡车轻量化措施
1.材料创新:使用高强度、轻量化的材料,如碳纤维复合材料,可以减轻车身重量,提高燃油效率。
2.组件优化:通过设计更小巧的发动机、减小变速器的重量和尺寸等方式,降低整车重量。
3.制造工艺改进:采用先进的焊接技术和铆接技术,减少焊接点和螺丝等连接结构,提高车身刚度和稳定性,减少重量。
总结:在当前环境保护和能源节约的背景下,卡车低风阻新概念和轻量化措施成为了减少能耗和排放的重要途径。
通过滑行技术、智能操控系统和燃料电池技术等新概念的应用,以及材料创新、组件优化和制造工艺改进等轻量化措施的实施,可以有效降低卡车的能耗和排放,减少运营成本,并对环境产生积极影响。
这些新概念和措施需要在实际应用中进行不断的试验和改进,以满足不同行业和运输需求的要求。
汽车轻量化材料及制造工艺研究现状
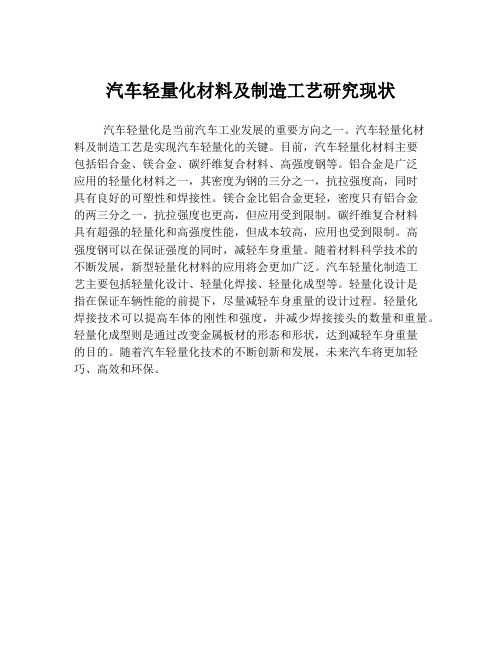
汽车轻量化材料及制造工艺研究现状
汽车轻量化是当前汽车工业发展的重要方向之一。
汽车轻量化材
料及制造工艺是实现汽车轻量化的关键。
目前,汽车轻量化材料主要
包括铝合金、镁合金、碳纤维复合材料、高强度钢等。
铝合金是广泛
应用的轻量化材料之一,其密度为钢的三分之一,抗拉强度高,同时
具有良好的可塑性和焊接性。
镁合金比铝合金更轻,密度只有铝合金
的两三分之一,抗拉强度也更高,但应用受到限制。
碳纤维复合材料
具有超强的轻量化和高强度性能,但成本较高,应用也受到限制。
高
强度钢可以在保证强度的同时,减轻车身重量。
随着材料科学技术的
不断发展,新型轻量化材料的应用将会更加广泛。
汽车轻量化制造工
艺主要包括轻量化设计、轻量化焊接、轻量化成型等。
轻量化设计是
指在保证车辆性能的前提下,尽量减轻车身重量的设计过程。
轻量化
焊接技术可以提高车体的刚性和强度,并减少焊接接头的数量和重量。
轻量化成型则是通过改变金属板材的形态和形状,达到减轻车身重量
的目的。
随着汽车轻量化技术的不断创新和发展,未来汽车将更加轻巧、高效和环保。
- 1、下载文档前请自行甄别文档内容的完整性,平台不提供额外的编辑、内容补充、找答案等附加服务。
- 2、"仅部分预览"的文档,不可在线预览部分如存在完整性等问题,可反馈申请退款(可完整预览的文档不适用该条件!)。
- 3、如文档侵犯您的权益,请联系客服反馈,我们会尽快为您处理(人工客服工作时间:9:00-18:30)。
附件:
货车轻量化涉及的几种新材料技术
铝合金。
与钢铁相比,铝合金具有质量轻(其密度为钢的1/3)、耐腐蚀性好、易于加工等特点,但成本较高,是近20年来在国内外载货汽车上使用最多的轻量化材料。
常用的包括:铸造铝合金——活塞、气缸盖、车轮、离合器盖、曲轴箱、进气歧管等;型变铝合金——发动机罩、货箱地板、保险杠、车轮、热交换器(散热器与加热器)、温度调节器(冷凝器与蒸发器)、油冷却器以及冷藏车厢、保温车厢、半挂车的车厢与车架等。
欧、美、日等国多年来铝合金在汽车上的用量平均年增幅为10%。
据统计,2003年全球每辆汽车用铝已从1978年的50kg上升为140kg,增长1.8倍。
镁合金。
与钢铁相比,镁合金密度小(比铝还小)、易于加工、压铸经济,其最大特点是阻尼减振性和抗凹性好。
镁合金早在20世纪40年代末就开始被一些公司采用。
镁合金在应用上比铝合金发展得慢,主因是因为其铸造性差、后处理工艺复杂、成本较高。
当前世界上所有汽车镁合金平均用量仅2.3kg。
随着研制该材料技术水平的提高,目前正以每年15%-20%的速度递增。
塑料及其复合材料。
汽车塑料制品一般分为内饰件、外装件和功能件等。
据统计,美国的汽车塑料使用量自1975年至1980年曾经以每年30%-40%左右的增速发展,后来因某些部件用塑趋于饱和及发展新品技术难度日益增大等因素增速逐渐放缓。
目前世界主要汽车用塑料件的内饰化已基本完成。
玻璃纤维增强塑料(FRP)等新品种已随着技术的成熟而正在扩大应用,主要用于车身的外装件和功能件。
可用于车门、发动机罩、前脸板、叶子板、保险扛骨架、门梁柱、通风百叶窗、导流罩等近20种车身板件。
具有高比强度和高比弹性模量的碳纤维增强塑料(CFRP)及有机
合成纤维复合材料(Kevlar)是欧美等国已着手研究的新材料,并已开始使用,但成本较高。
如果能将其成本降至当前的1/3,将有望成为汽车功能件和结构件轻量化的优选用才。
高强度钢。
在轻量化材料中,与铝合金、塑料相比,高强度钢具有以下特点:(1)价格低;(2)基本上可利用原有生产线;(3)其弹性模量高、刚性好、耐冲击性好及较高的疲劳强度,有些高强度钢的抗拉强度为普通钢的2~3倍;(4)耐腐蚀性差。
受能源短缺、环境污染等问题的影响,货车轻量化以涉及的高强钢的应用成为了重要发展方向。
但受高强钢板材强度的提高,传统的冷冲压工艺在成型过程中容易产生破裂现象,无法满足高强度钢板的加工工艺要求。
在无法满足成型条件的情况下,目前国际上逐渐研究超高强度钢板的热冲压成形技术。
该技术是综合了成形、传热以及组织相变的一种新工艺,主要是利用高温奥氏体状态下,板料的塑性增加,屈服强度降低的特点,通过模具进行成形的工艺。
但是热成型需要对工艺条件、金属相变、CAE分析技术进行深入研究,目前该技术被国外厂商垄断,国内发展缓慢。