高炉开炉配料计算
高炉炼铁原材料配比及用量计算

高炉炼铁原材料配比及用量计算
设计中采用高炉炼铁工艺,有效容积为200M³的高炉两座,有效容积为100M³的高炉一座。
选取炉高炉有效容积利用系数ηv=2.2 t/(m3.d),由公式:P Q=M×T ×ηv×V v
式中:P Q——高炉车间年生铁产量,吨;
M——高炉座数;
T——年平均工作日,高炉一代炉役中,扣除大、中、小修时间后每年平均实际生产天数一般为330~350天。
此处采用350天。
所以,有效容积为200M³的高炉年产量为
PQ200M³=M×T ×ηv×Vv=2×350 ×2.2×200=308000t
PQ100M³=M×T ×ηv×Vv=1×350 ×2.2×100=77000t
PQ= PQ200M³+PQ100M³=308000+77000=385000t
根据高炉冶炼原理,生产1吨生铁,需要1.5-2.0吨铁矿石、0.4-0.6吨焦炭以及0.2-0.4吨熔剂。
本次设计采用生产1吨生铁,需要2.0吨铁矿石、0.5吨焦炭以及0.3吨熔剂。
所以经计算可知:
需要铁矿石的量为385000t×2=770000t
焦炭的量为385000t×0.5=192500t
熔剂的量为385000t×0.3=115500t。
文水1380m3高炉开炉配料计算方案
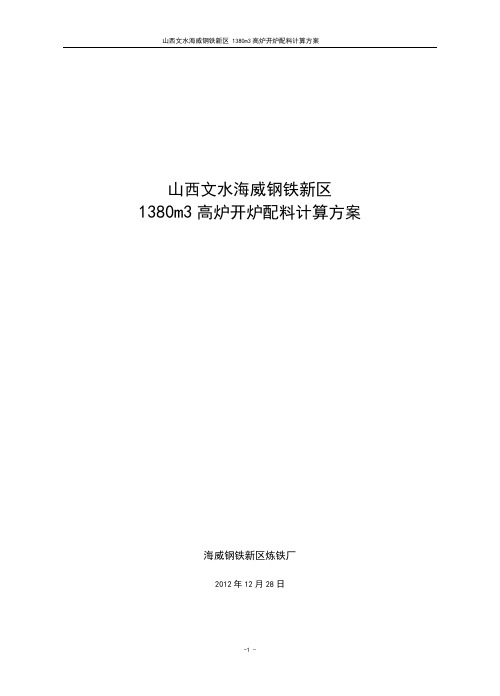
山西文水海威钢铁新区1380m3高炉开炉配料计算方案海威钢铁新区炼铁厂2012年12月28日海威钢铁新区1380m3高炉开炉配料计算一、开炉配料计算基础数据(D注:1.渣碱度调剂不使用灰石,采用硅石和白云石。
3.开炉炉料结构为烧结矿和球团,不使用块矿。
(2)炉料压缩率净焦和空焦压缩率按13%fi行计算;空焦压缩率按12%+算;后续料压缩率按12%+算;(3)焦炭水分:2.9%。
二、配料原则2.1道木加至风口中心线以下1米,净焦加至炉腰上沿炉身下沿,空焦加至炉身下沿以上3米,炉身下沿3米以上为空焦与正常料组成的过渡料,料线 3.2米以上加正常料。
2.2净焦焦批干基8.7t。
2.3空焦:焦碳、白云石、硅石、萤石。
焦批干基8.7t ,炉渣碱度按0.8-0.85校核。
2.4正常料组成:焦炭、结矿、球团矿、钮矿、白云石、硅石、萤石。
负荷2.3,矿批20t。
焦批干基8.7吨,二元碱度按0.9-0.95校核,(CaF2按5-8%核,(MgO按8-9%E右校核。
铁水[Si]按3.0 %校核、[Mn]按0.8〜1.0 % 配加。
全炉碱度按照0.8-0.85 校核。
2.5后续正常料组成:烧结矿、球团矿、钮矿、白云石、硅石、萤石、焦碳。
焦炭负荷2.3-2.4 ,二元碱度 1.05-1.10 。
[Si]按 2.0%、[Mn]按0.8 〜1.0%$核。
(MgO按8-9% 左右校核。
三、各段物料平衡结果至1.5米料线处,全炉入炉焦炭548吨,全炉渣比704kg/t,入炉正常料16批,入炉铁量180吨,全炉焦比3044kg/t;第一段 52 22 2334 692 0.94 0.76 0.93 0.11 0.10 第二段 52 34 1561 566 0.96 1.14 0.92 0.11 0.09 第三段 35 34 1042 550 0.95 1.72 0.95 0.10 0.09 第四段 61 67 912 550 0.95 1.96 0.96 0.09 0.09 第五段 17 22 782 499 0.95 2.29 0.930.100.08总计54818030447040.930.58四、正常料正常料矿批20吨,焦比782kg/t,干基焦炭负荷2.30,批铁量11.17t,谓比499kg/t, 入炉综合品位52.20 %;五、总装炉料量料种焦炭(干基) 烧结矿 镒矿球团矿萤后 硅石白玄后X (t) 548 224 16 80 8.1 15.4 43.8六、开炉料分段示意图ft ------- 1利线 1.3 米_5I I1h- 1.6 源 第七段料25426.9254 7822.3451 1 ,•二 .. —1 --i। । ।h=4.2 米 第六段科 1铝+1刊/6空178 29」617E?L21.97401 1I);,.1.・। ________1h= LK 米 第五段科 空焦 9732.2397104237[iI I 4**J ii■2.2 米 .第四段1*£+1*空焦 12S42.83 128 1561L 1.5 2S i ।|L_| J. J. L L s a a J %++ !■ L4- I- I-l! ■j L।h= LK 米 第三段科 1*2+2*空焦 113 59. 0211S23340.7&20। 1rF ■3 4 * + + + m& d >>++++ - dJ iiI 1h= 2.7.某一段至舔 357 L7.512357的i1 Fa IkhIJ __l1第一段科 挣焦215.83Q 4T576装科位置装料相也积批/组焦比 焦炭负治嫌周期苴充体 ・可•+ ++ +। Emm +++■!■串・・・・11・・F ・・・・・•$+ +•+..・・.七、拉料表注:零米料线为炉喉上沿七、拉料表注:零米料线为炉喉上沿-1 --2 --3 -山西文水海威钢铁新区1380m3高炉开炉配料计算方案-4 -。
高炉开炉配料计算

灰分 0.1313
Fe 57.7 63.9 59.25
10.83
4.13
1.353
0.75 0.25
挥发分 0.0131
SiO2 4.87 6.3 5.23 2.29 11.84 97.67 48.83
5000
Kg
2、则应装净焦的批数为:
二、虚拟矿批及虚拟总批数的计算 矿批=焦批*铁的回收率/(全炉焦比*品位) 1、一批正常料压缩后的体积为: 2、开炉料总批数为:
混合矿的R2=
烧结矿所占的比例:X= 球团矿所占的比例为:1-X=
一、净焦装入的批数(炉缸及炉腹) 1、净焦批重为:
Ⅵ
D3=
Ⅶ
h7=
h"=
料线
正常料焦比 0.86
Mn的回收率 0.5
石灰石 1.6
空料(X) 0.12
料线 1.67
Si 3
渣焦比 0.4
烧结 1.85
正常料(H) 0.12
布料角度 25°×13
h'' D3
Dx5
h7 V7
h6 V6 Dx4
h' Dx3
h5
V5
Dx2 h4 V4
D2 h3 V3
h2
h2-h2' h2'
h-h1 V2
h Dx1
h1
V1
D1 h0
蓝色为人为输入 红色为高炉本身参数 黑色为自动生成
Ⅰ
Ⅱ Ⅲ Ⅳ
D1= h0= h1= Dx1= h=
h-h1= h2= h2’= D2= h3= Dx2=
质量 329.75 142.19 472.16 320.57 448.86
CaO %
810m3高炉开炉料计算

810m3高炉开炉料计算810m高炉开炉料计算开炉工作有两个方面的要求:一是安全顺利地完成开炉工作,即做到炉温适中,铁口易开,下料顺畅,并且无人身、设备事故:二是在开炉后能较快平稳地过渡到正常生产,以获得较好的经济效益。
为此开炉时应该使炉内各区域适时地达到所需要的温度,故开炉料的选择,开炉焦比的确定,以及炉段的安排至关重要。
36.1 开炉焦比的选择所谓开炉焦比(总焦比是指开炉料的总焦量与理论出铁量之比。
开炉时由于高炉炉衬温度、料柱的温度都很低,炉料未经充分的预热和还原直接到炉缸,直接还原增多,渣量打,需要消耗的热量也多,所以开炉焦比要比正常焦比高几倍。
具体数值应该根据高炉容积大小,原燃料条件、风温高低、设备状况及技术操作水平等因素进行选择。
一般情况见表6-1:表6-1 开炉焦比的选择炉容/m 焦比/t?t铁?13100以下 >4100-500 3-4500-1000 2.5-31000以上 <2.6选择合适的开炉焦比对开炉进程有决定性的影响。
焦比选择过高,既不经济,又可能导致炉况不顺,即导致高温区上移,在炉身中上部容易产生炉墙结厚现象,更严重的是延长了开炉时间;焦比选择过低,会导致炉缸温度不足,出渣出铁困难,渣铁流动不畅,严重时会造成炉缸冻结。
一般要求开炉前几次含硅量为3%-3.5%。
6.2 开炉造渣制度的选择为了改善渣铁流动性能,冶炼合格生铁,加热炉缸,稀释渣中的Al2O3(Al2O3含量大于18%时,开炉配料中需增加低Al2O3的造渣剂),开炉时渣量要大一些,渣铁比一般为0.4-0.5.如渣量小,可加干渣调节。
开炉时炉渣碱度SiO2?0.90-1.05。
控制生铁含?Mn?0.8%,为了改善炉渣流动性,可提高渣中的MgO含量,使之维持在8%-10%左右,也可适当加些萤石来稀释炉渣。
小高炉在用全天然矿冷风开炉时,焦比特高,可在空料(即焦炭+石灰石)段加些硅石来调整炉渣成分。
不用干渣,既可以节约焦炭,而且铁口见渣较晚,可以延长喷吹铁口时间,有利于加热炉缸。
1高炉配料计算

高炉炼铁主要经济技术指标 选定 (1) 高炉有效容积利用系数(v η)高炉有效容积利用系数即每昼夜生铁的产量与高炉有效容积之比,即每昼夜1m³有效容积的生铁产量。
可用下式表示:有V Pη=v 式中: v η——高炉有效容积利用系数,t /(m 3·d) P ——高炉每昼夜的生铁产量,t /d有V ——高炉有效容积,m 3V η是高炉冶炼的一个重要指标,有效容积利用系数愈大,高炉生产率愈高。
目前,一般大型高炉超过2.3,一些先进高炉可达到2.9。
小型高炉的更高。
本设计中取2.7。
(2) 焦比(K )焦比即 每昼夜焦炭消耗量与每昼夜生铁产量之比,即冶炼每吨生铁消耗焦炭量。
可用下式表示:式中 K ——高炉焦比,kg/tP ——高炉每昼夜的生铁产量,t /dK Q ——高炉每昼夜消耗焦炭量,kg/d焦比可根据设计采用的原燃料、风温、设备、操作等条件与实际生产情况进行全面分析比较和计算确定。
当高炉采用喷吹燃料时,计算焦比必须考虑喷吹物的焦炭置换量。
本设计中取K = 330 kg/t (3) 煤比(Y )冶炼每吨生铁消耗的煤粉为煤比。
本设计中取煤比为180 kg/t . (4) 冶炼强度(I )和燃烧强度(i )高炉冶炼强度是每昼夜31m 有效容积燃烧的焦炭量,即高炉每昼夜焦炭消耗量与有V 的比值, 本设计I =1.1 t/m 3∙d 。
燃烧强度i 既每小时每平方米炉缸截面积所燃烧的焦炭量。
本设计i = 30 t/m 2∙d 。
(5) 生铁合格率化学成分符合国家标准的生铁称为合格生铁,合格生铁占总产生铁量的百分数为生铁合格率。
它是衡量产品质量的指标。
(6) 生铁成本生产一吨合格生铁所消耗的所有原料、燃料、材料、水电、人工等一切费用的总和,单位为 元/t 。
(7) 休风率休风率是指高炉休风时间占高炉规定作业时间的百分数。
先进高炉休风率小于1%。
(8) 高炉一代寿命高炉一代寿命是从点火开炉到停炉大修之间的冶炼时间,或是指高炉相邻两次大修之间的冶炼时间。
高炉开炉配料计算
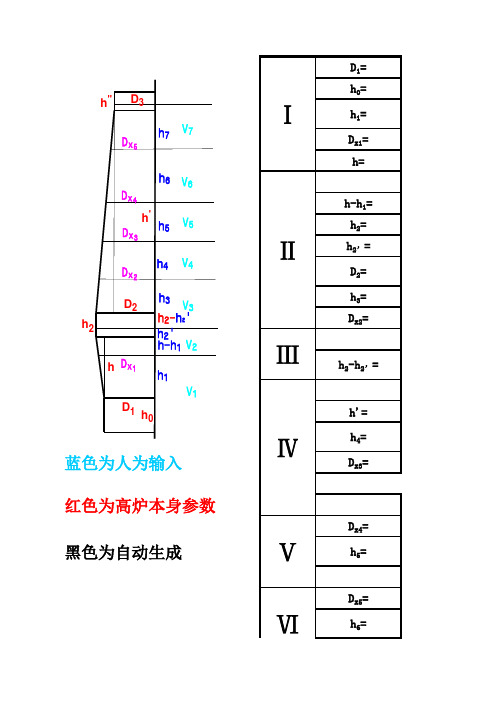
D 1=h 0=h 1=D x1=h=h-h 1=h 2=h 2’=D 2=h 3=D x2=h 2-h 2’=h'=h 4=蓝色为人为输入D x3=红色为高炉本身参数D x4=黑色为自动生成h 5=D x5=h 6=ⅠⅡⅢⅣⅤⅥh 2-h 2'h 2'V 7V 6V 5V 4V3V 2V 1h 3h 4h 5h 6h7D x 4D x 5D x 3D x 2D x 1h-h 1h 1h ''h 'h 2h h 0D 3D 2D 1D 3=h 7=h"=料线ⅥⅦ二、虚拟矿批及虚拟总批数的计算矿批=焦批*铁的回收率/(全炉焦比*品位)虚拟矿批=2986.0431、一批正常料压缩后的体积为:V 正常料=9.4232、开炉料总批数为:n 虚拟矿=48.097三、真实矿批的计算1、真实入炉矿的质量为:m 总入炉矿=143619.712、正常料的矿批为:m 矿批=9027.5733、正常料的总批数为:n 正常料=15.9094、正常料的组成:焦批:5000矿批:9027.573烧结矿:6770.68球团矿:2256.893四、正常料批数及净焦批数正常料:取净焦:取五、炉料的安排(具体的安排由人脑完成)第一段:炉缸及炉腹装入净焦批数为:21批第二段:炉腰、炉身及炉喉(料线以下)正常料16净焦11六、核算总的焦炭消耗量为:240000Kg 总的出铁量为:93027.652Kg 总的焦比为:2.583、各种炉料带入渣中各成分的数量正常料带入量7181.7610640净 焦 带 入 量10258.24848合 计1744011488四种成分总和为:46202.08Kg 假设以上四种成分占渣量的0.98则最终总渣量为:SiO 2CaO 炉料带入渣中成分量渣铁比为:0.51渣焦比为:0.25.623.003.1V1=164.291 6.523.100.001.200.806.52V2=26.71 1.56.2260.40V3=61.21210.201.8V4=51.752 5.8735.2653.1V5=75.5854.8732V6=40.3814.521.80V7=33.2831.801.67V料=453.214参数的选择Mn P S Fe10.250.0592炉渣中的FeO0.005球团硅石Mn矿2.1 1.6 1.8焦炭批重5000硫分M40M100.590.06476.5FeO CaO MgO Mn Al2O3R2Fe2O311.59.23 2.550.27 1.97 1.8950.340.60.860.1 1.450.0958.717.07 2.130.23 1.84 1.3551.5220.2350.430.324.06 4.060.7135.929.46配料计算则体积为:7.857m3取21批Kgm 3批取48批KgKg批取16批KgKg取9028Kg Kg取6771Kg Kg取2257Kg16批32批批批CaO MgO Al 2O 3质量%质量%质量%质量329.759.23624.96 2.55172.66 1.97133.39142.190.613.540.8619.41 1.4532.73472.167.07638.5 2.13192.07 1.84166.12320.570.005326.50.0932 4.66 4.7163235.82448.86665196.73401.94R 2R 3R 46431.043147.687546.24149.1213977.283296.80.660.850.4747144.97959KgAl 2O 3MgO RRR2R3R4 1.3521.482 1.92 1.01。
开炉配料方案
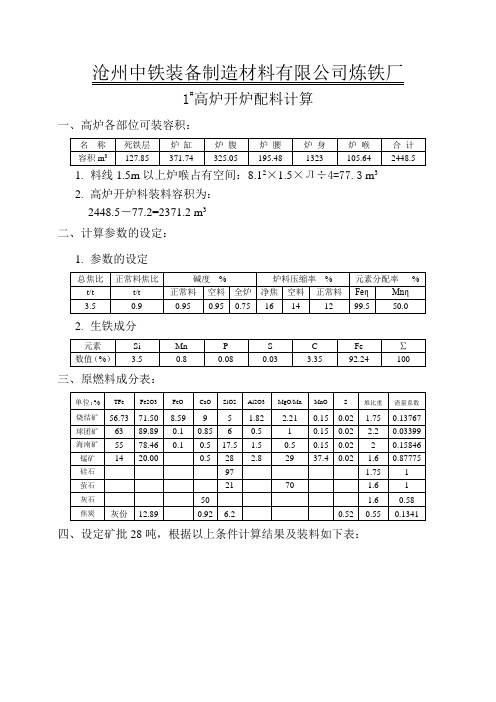
沧州中铁装备制造材料有限公司炼铁厂
1#高炉开炉配料计算
一、高炉各部位可装容积:
1.料线1.5m以上炉喉占有空间:8.12×1.5×Л÷4=77.3 m3
2.高炉开炉料装料容积为:
2448.5-77.2=2371.2 m3
二、计算参数的设定:
1.参数的设定
2.生铁成分
三、原燃料成分表:
四、设定矿批28吨,根据以上条件计算结果及装料如下表:
#
装料误差:0.608% 枕木区的空余体积189 参与造渣的焦炭总量844.7 净焦参与造渣的数量13.4
注: 1、表中H——Kg↓J↓,K-机烧+球团+海南矿+锰矿;J—焦炭;g—萤石;h—灰石;
2、料批组成的焦炭为干焦,装料时注意应该转化为湿焦,焦炭水分为:4%,则实际焦炭批重:13.38kg/批;
3、空焦上完规定料批后实测料线,超过料线继续按装料计划上料,如果低于计划料线则补加空焦到达料线后再装下段料;
4、点火送风2小时如无异常后焦比减到750kg/t,8小时后如无异常焦比减到700kg/t,出完第一次铁后无异常焦比减到650kg/t。
1高炉配料计算

高炉炼铁主要经济技术指标 选定(1) 高炉有效容积利用系数(v η)高炉有效容积利用系数即每昼夜生铁的产量与高炉有效容积之比,即每昼夜1m³有效容积的生铁产量。
可用下式表示:有V Pη=v 式中: v η——高炉有效容积利用系数,t /(m 3·d) P ——高炉每昼夜的生铁产量,t /d有V ——高炉有效容积,m 3V η是高炉冶炼的一个重要指标,有效容积利用系数愈大,高炉生产率愈高。
目前,一般大型高炉超过2.3,一些先进高炉可达到2.9。
小型高炉的更高。
本设计中取2.7。
(2) 焦比(K )焦比即 每昼夜焦炭消耗量与每昼夜生铁产量之比,即冶炼每吨生铁消耗焦炭量。
可用下式表示:式中 K ——高炉焦比,kg/t——高炉每昼夜的生铁产量,t /dK Q ——高炉每昼夜消耗焦炭量,kg/d焦比可根据设计采用的原燃料、风温、设备、操作等条件与实际生产情况进行全面分析比较和计算确定。
当高炉采用喷吹燃料时,计算焦比必须考虑喷吹物的焦炭置换量。
本设计中取K = 330 kg/t (3) 煤比(Y )冶炼每吨生铁消耗的煤粉为煤比。
本设计中取煤比为180 kg/t .(4) 冶炼强度(I )和燃烧强度(i )高炉冶炼强度是每昼夜31m 有效容积燃烧的焦炭量,即高炉每昼夜焦炭消耗量与有V 的比值, 本设计I =1.1 t/m 3∙d 。
燃烧强度i 既每小时每平方米炉缸截面积所燃烧的焦炭量。
本设计i = 30 t/m 2∙d 。
(5) 生铁合格率化学成分符合国家标准的生铁称为合格生铁,合格生铁占总产生铁量的百分数为生铁合格率。
它是衡量产品质量的指标。
(6) 生铁成本生产一吨合格生铁所消耗的所有原料、燃料、材料、水电、人工等一切费用的总和,单位为 元/t 。
(7) 休风率休风率是指高炉休风时间占高炉规定作业时间的百分数。
先进高炉休风率小于1%。
(8) 高炉一代寿命高炉一代寿命是从点火开炉到停炉大修之间的冶炼时间,或是指高炉相邻两次大修之间的冶炼时间。
高炉开炉变料计算
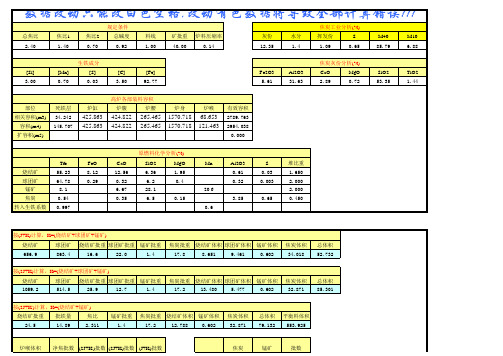
按(2J+K)计算,K=(烧结矿+球团矿+锰矿) 烧结矿 1059.2 球团矿 514.5 烧结矿批重 球团矿批重 锰矿批重 25.9 12.7 1.4 焦炭批重 烧结矿体积 球团矿体积 锰矿体积 17.2 13.480 5.477 0.602 焦炭体积 32.871 总体积 85.301
按(2J+K')计算,K=(烧结矿+锰矿) 烧结矿批重 24.5 炉喉体积 批铁量 14.89 焦比 2.311 锰矿批重 1.4 焦炭批重 烧结矿体积 锰矿体积 17.2 12.788 0.602 焦炭体积 32.871 焦炭 总体积 79.132 锰矿 平衡料体积 553.925 批数
425.863 425.863
424.822 424.822
265.465 265.465
1570.718 1570.718
68.653 121.463
按(J+K)计算,K=(烧结矿+球团矿+锰矿) 烧结矿 656.9 球团矿 863.4 烧结矿批重 球团矿批重 锰矿批重 16.6 22.0 1.4 焦炭批重 烧结矿体积 球团矿体积 锰矿体积 17.8 8.651 9.461 0.602 焦炭体积 34.018 总体积 52.732
净焦批数 (2J+K')批数 (2J+K)批数 (J+K)批数
68.653
26.9
7.3
14.8
1.0
J 2J+K' 2J+K J+K
17.2 17.2 17.2 17.8
1.4 1.4 1.4 1.4
27 7 15 1
每10炭耗量2 700 1400
R终
高炉开炉配料计算
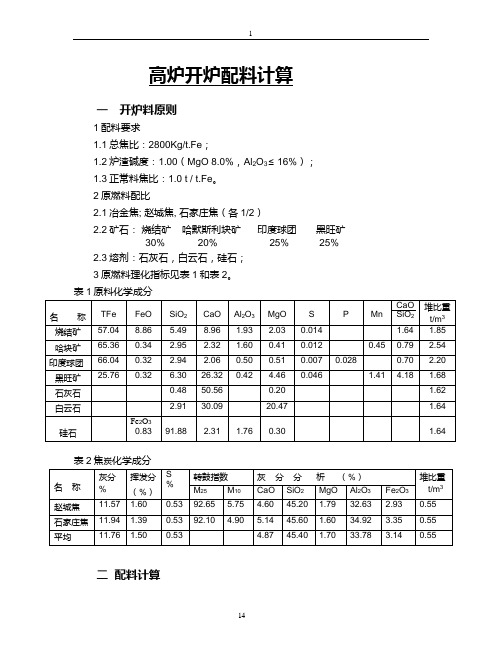
高炉开炉配料计算一开炉料原则1配料要求1.1总焦比:2800Kg/t.Fe;1.2炉渣碱度:1.00(MgO 8.0%,Al2O3≤16%);1.3正常料焦比:1.0 t / t.Fe。
2原燃料配比2.1冶金焦; 赵城焦, 石家庄焦(各1/2)2.2矿石:烧结矿哈默斯利块矿印度球团黑旺矿30% 20% 25% 25%2.3熔剂:石灰石,白云石,硅石;3原燃料理化指标见表1和表2。
二配料计算1、预计生铁成分元素Fe C Si Mn S含量(%) 92.47 4.0 3.0 0.5 0.032 、Fe、Mn回收率Fe回收率: 99.0%;Mn回收率 60.0%; S 分配率:85%进入炉渣,5%进入生铁。
3、以100 Kg混合矿计算:3.1 100 Kg混合矿平均含Fe:30×57.04%+20×65.36%+25×66.04+25×25.76% = 53.134,100 Kg混合矿出铁:100×53.13%×0.99 / 0.9247 = 56.886 Kg。
3.2炉渣成分核算:(1)生铁中Si消耗SiO256.886×3.0%×60 / 28 = 3.657(2)炉渣中FeO量53.134×1.0%×72 / 56 = 0.683(3)入炉料的S负荷30×0.014%+20×0.012%+25×0.007%+25×0.046%+56.886×0.53%=0.321(4)炉渣中的CaS0.321×85%×72 / 32=0.614(5)脱硫消耗CaO0.614×56/72=0.478(6)原燃料成分中进入炉渣的数量(7)炉渣成分调整为使炉渣成分达到要求标准,加白云石和硅石进行调整。
硅石加入量为:x白云石加入量为:y3.927+91.88% x +2.91% y =10.096+2.31% x+30.09% y2.045+0.30% x +20.47% y= 8.0%20.652+96.25% x+53.47% y解方程:x = 7.422 Kg。
开炉计算
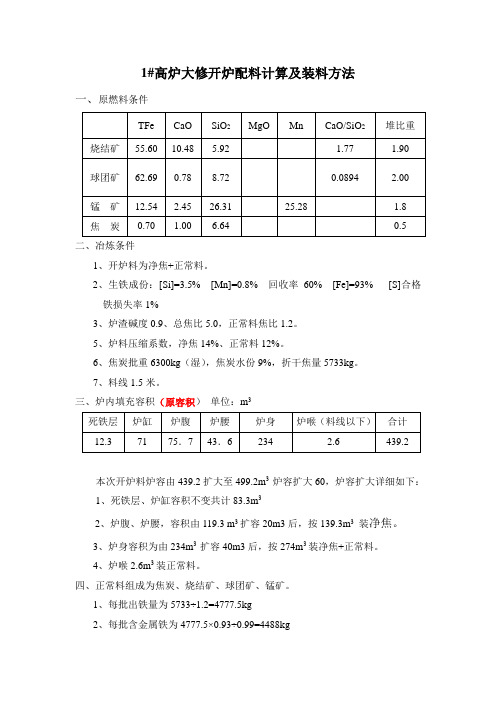
1#高炉大修开炉配料计算及装料方法一、原燃料条件二、冶炼条件1、开炉料为净焦+正常料。
2、生铁成份:[Si]=3.5% [Mn]=0.8% 回收率60% [Fe]=93% [S]合格铁损失率1%3、炉渣碱度0.9、总焦比5.0,正常料焦比1.2。
5、炉料压缩系数,净焦14%、正常料12%。
6、焦炭批重6300kg(湿),焦炭水份9%,折干焦量5733kg。
7、料线1.5米。
三、炉内填充容积(原容积)单位:m3本次开炉料炉容由439.2扩大至499.2m3 炉容扩大60,炉容扩大详细如下:1、死铁层、炉缸容积不变共计83.3m32、炉腹、炉腰,容积由119.3 m3扩容20m3后,按139.3m3装净焦。
3、炉身容积为由234m3 扩容40m3后,按274m3装净焦+正常料。
4、炉喉2.6m3装正常料。
四、正常料组成为焦炭、烧结矿、球团矿、锰矿。
1、每批出铁量为5733÷1.2=4777.5kg2、每批含金属铁为4777.5×0.93÷0.99=4488kg3、需要锰矿量为4777.5×0.8%/60%÷25.28%=252kg 取260kg4、锰矿带入金属铁260×12.54%=32.6kg5、焦炭带入金属铁为5733×0.7%=40kg6、烧结矿、球团矿需带入金属铁应为4488-32.6-40=4415.4kg7、设每批正常料含烧结矿为X,含球团矿为Y,列方程组:0.556X+0.6269Y=4415.40.1048X+0.0078Y+5733×0.01 +260×0.0245 0.90.0592X+0.0872Y+5733×0.0664+260×0.2631-4777.5×0.035×2.14解方程组取X=4500Y=3000即正常料为焦炭6300kg(湿),烧结4500kg,球团3000kg,锰矿260kg,矿石批重7760kg。
高炉开炉配料自动计算表(专利)

7.30 20
0.00 0.00 0.87 7.30
45 45 45 45
总铁量 总渣量 渣铁比 正常料负荷 硫负荷 全炉焦比 226.8957 168.1047097 740.8899 2.164383562 3.658487 2.863431
渣碱度 及成分
212.18736 211.1264232 1.0609368 R2 0.886529628
MgO 批含量 0.000% 0 0.000% 0 3.000% 0.02616 1.470% 0.013532 0.039692
S 0.000% 0.000% 0.150% 0.820%
批含量
0 0 0.001308 0.007548346 0.008856346 (CaO+MgO)/(SiO2+Al2O3) 0.741313276 MgO 3.150% 1.630% 0.000% 0.000% 0.000% 批含量 0.3528 0 0.07009 0 0 0 0
45
586.112
22
447.503
汇 总 配 料 表
名称 烧结 矿烧 球团 澳矿 锰矿 海南矿 硅石 萤石 石灰石 焦炭 合计 入铁 入渣 参数计算
批重
批重
空焦 批数
24 24 24 24 24 24
Tfe 54.200% 0.000% 63.180% 0.000% 18.000% 0.000%
总重 145.6896 0 65.20176 0 1.296 0
8.84114 8.796934 0.044206 批铁量 渣量 渣铁比 参数计算 9.453986 4.02181317 425.4092
炉料分类 净焦
空焦 料 批 计 算 正常料
高炉开炉配料计算
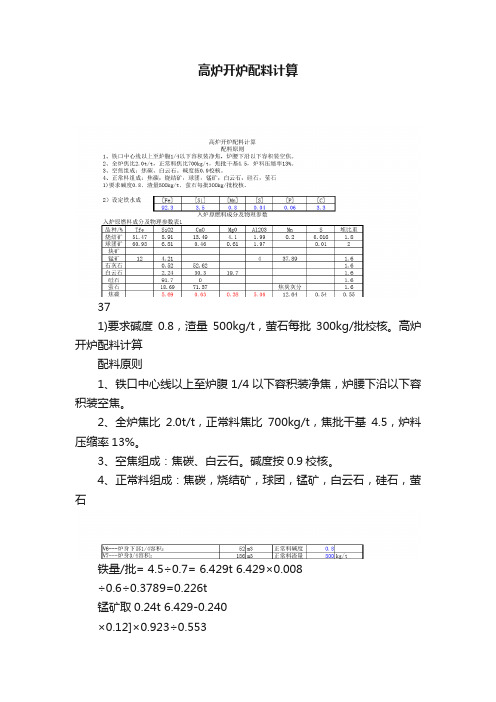
高炉开炉配料计算371)要求碱度0.8,渣量500kg/t,萤石每批300kg/批校核。
高炉开炉配料计算配料原则1、铁口中心线以上至炉腹1/4以下容积装净焦,炉腰下沿以下容积装空焦。
2、全炉焦比2.0t/t,正常料焦比700kg/t,焦批干基4.5,炉料压缩率13%。
3、空焦组成:焦碳、白云石。
碱度按0.9校核。
4、正常料组成:焦碳,烧结矿,球团,锰矿,白云石,硅石,萤石铁量/批= 4.5÷0.7= 6.429t 6.429×0.008÷0.6÷0.3789=0.226t锰矿取0.24t 6.429-0.240×0.12]×0.923÷0.553=10.691t混合矿取11t 焦炭: 4.5t 烧结矿: 6.6t 球团: 4.4t 锰矿:0.2t6.429×500= 3.214t锰矿量/批=混合矿量/批=[根据计算正常料批组成:上述计算的正常料炉渣成分校对见表2一批正常料需配渣量=配渣前炉渣成分表2配渣调整炉渣成分变化见表3硅石量=[ 2.239×(0.2369×0.8-0.4194)]÷0.917÷0.8=-0.702t0.702t 3.214- 2.883=0.332t 0.332×0.4073÷0.917=0.147t 0.147×0.917×0.8÷(0.5262-0.0052×0.8)=0.207t0.207×1×52.62÷30.300=0.359t 0.207×0.000=0.000t0.702+0.147=0.849t硅石取0.849t 石灰石取0t 白云石取0.359t焦炭:4.5t烧结矿: 6.6t配平碱度硅石量取需要配渣量=需配硅石量=需配石灰石量=正常料配硅石=配渣后的正常料组成:石灰石100%换成白云石=石灰石00%量=球团: 4.4t 锰矿:0.240t硅石:0.849t 石灰石:0t 萤石:0.3t 白云石:0.359t 6.6÷ 1.8+(0.240+0.849+0+0.3+0.359)÷1.6+ 4.4÷2+ 4.5÷0.55]×0.87=13.17m3/批R31.090.632)÷(30.3- 2.24×0.9)=0.714t0.714×0.5×30.3÷52.62=0.206t正常料体积=[正常料炉渣成分校对见表4空焦白云石0%换成石灰石=0.714×0.5=0.357t 白云石取0.714t 石灰石取0t 焦炭: 4.5t白云石:0.714t 石灰石:0t 4.5÷0.55+(0.714+0)÷1.6)×0.87=7.506m3=7.12m3/批空焦=7.506m3/批正常料=13.17m3/批69+41=110m3110÷7.118182=15.45批净焦取16.00批7.506X+13.17Y =3114.5×16+ 4.5×(X+Y)÷( 6.429×Y)=213.173Y+7.51X=311(3)开炉料组成空焦白云石100%量=空焦组成:空焦体积计算=((1)净焦批数:净焦容积为炉腹1/4以下容积;净焦容积=V3+1/4V4=净焦批数=(2)空焦与正常料设X——空焦 Y——正常料列方程为:整理方程得:8.357143Y - 4.5X =72110.0858Y +62.73222X =2599.071110.0858Y-59.27696X =948.4313X=13.53批正常料取16批Y=15.90批空焦取13批61.5m3加空焦=61.5÷7.506=8.19批取8.00批3OC+Cn 3OC+Cn 3OC+Cn 7OC+2cn死铁层+16C +8Cn ++++7OC+2cn202.5÷( 6.429×16)= 1.97t/t7.118182×16+7.506×13+13.17×16=422.237m3422.2369÷421=100.29%全炉开炉料按排:3OC+Cn解方程:空焦与正常料按排:炉腹3/4容积3/4V4=其余炉身和炉喉的容积炉料按排:3OC+Cn 3OC+Cn 其中:C——为净焦;Cn——为空焦;OC——正常料。
450m3高炉开炉配料计算
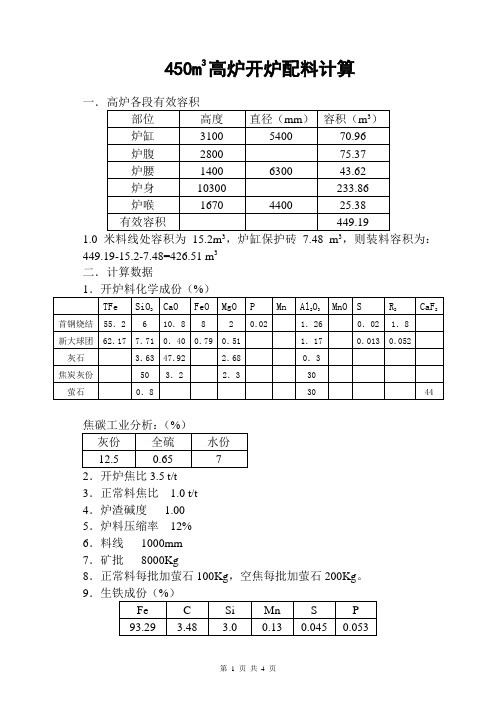
450m3高炉开炉配料计算1.0米料线处容积为15.2m3,炉缸保护砖7.48 m3,则装料容积为:449.19-15.2-7.48=426.51 m3二.计算数据2.开炉焦比3.5 t/t3.正常料焦比 1.0 t/t4.炉渣碱度 1.005.炉料压缩率12%6.料线1000mm7.矿批8000Kg8.正常料每批加萤石100Kg,空焦每批加萤石200Kg。
910.三. 开炉料计算1.正常料计算(吨铁耗用矿石量) (1) 一吨铁中含铁量 1000×93.29%=932.9Kg (2) 吨铁需矿量 配比 机烧:球团=55.45其中:机烧 1594.4×55%=876.91Kg 球团 1594.4×45%=717.50Kg (3) 吨铁焦炭灰份量 1000×12.5%=125Kg 2.炉渣成份校核 (1) 矿焦带入CaO 量及萤石带入的CaO 量876.91×10.8%+717.50×0.40%+125×3.2%+1594.4/8000×100×44.8%×70%=107.83 Kg (2) 矿焦SiO 2量及进入渣中SiO 2量876.91×6%+717.5×7.71%+125×50%=170.43 Kg 还原Si 消耗SiO 2量:1000×3.0%×60/28=64.30 Kg 进入渣中SiO 2量:170.43-64.3=106.13Kg (3) 终渣S 量=876.91×0.02%+717.5×0.013%+1000×0.65%=6.77 Kg 进入生铁S 量 6.77×3%=0.2031 Kg 进入煤气S 量 6.77×12%=0.8124 Kg 进入炉渣S 量 6.77×85%=5.755 Kg (4) 吨铁终渣FeO 量 932.9÷99.7%×0.5%×72÷56=6.02 Kg (5) 吨铁终渣MgO 量 876.91×2%+717.5×0.51%=21.20 Kg (6) 吨铁终渣Al 2O 3量 876.91×1.26%+717.5×1.17%+125×30%=56.94 Kg (7) 吨铁终渣MnO 量 (8) 正常料中带入渣量107.83+106.13+5.755+6.02+21.2+56.94+MnO=304Kg (9) 炉渣碱度校正矿耗= 932.9×99.7% 55%×55.2%+45%×62.17%=1594.4KgR2=107.83÷106.13=1.02R3=(107.83+21.2)÷106.13=1.22R4=(107.83+21.2)÷(106.13+56.94)=0.79四.料批组成1.料批的确定矿批8000Kg批料出铁量8000×(55%×55.2%+45%×62.17%)×0.997+93.29%=4.987 t每批料渣量 4.987×0.304=1.516 t焦批的确定 4.987×1000×1.00=4987Kg2注:正常料每批加萤石100kg。
高炉配料计算

《钢铁冶金学I(炼铁)》大计算学院:高等工程师学院指导教师:***专业班级:冶金E111*名:***学号: ********2014年5月1日设计高炉计算物料平衡计算(1)原料消耗量计算——配料计算Fe平衡方程Fe生=94.561*10=945.61kgFe焦=474.21*(0.0102*55.85/71.85)=3.760kgFe煤=68*0.0096*55.85/71.85=0.507kgFe渣=945.61*0.0015/0.9985=1.421kgFe碎=20*0.85=17.000kgFe尘=16.6*0.3820=6.341kgP*Fe%=945.61+1.421+6.341-0.507-3.760-17.000=932.105kg设配烧结矿x,澳矿y(P、Fe平衡联立)0.52427x+0.64983y=932.105(1)474.21*0.0005*62/142+68*0.0006*62/142+0.00157x+0.00070y=2.85+16.6*0.00109(2)解得:x=1754.176kg y=19.148kg碱度平衡方程CaO矿=1754.18*0.1178=206.642kgCaO焦=474.21*0.0085=4.031kgCaO煤=68.0*0.0083=0.564kgCaO尘=16.6*0.0811=1.346kgCaO矿+CaO焦+CaO煤-CaO尘=209.891kgSiO2矿=1754.18*0.0929+19.15*0.0247=163.436kgSiO2焦=474.21*0.06=28.453kgSiO2煤=68*0.0551=3.747kgSiO2碎=20*0.1=2.000kgSiO2尘=16.6*0.0987=1.638kg[Si]——SiO2生=0.52*60/28*10=11.143kgSiO2矿+SiO2焦+SiO2煤+SiO2碎-SiO2尘-SiO2生=184.855kgQ=(184.855*1.13-209.891)/(0.5530-0.0103*1.13)=-1.86不加熔剂,重新计算矿石消耗量1.13*(x*0.0929+y*0.0247+28.453+3.747+2.000-1.638-11.143)=x*0.1178+4.031+0.564-1.346(3)联立(1)(3)式,解得x=1725.74kg y=42.09kg(2)渣量和渣成分计算FeO渣=94.561*10*71.85/55.85*0.0015/0.9985=1.828kgCaO渣=1725.74*0.1178+4.031+0.564-1.346=206.541kgMnO渣=0.14*10*71/55*0.3/0.7=0.775kgSiO2渣= 1725.74*0.0929+42.09*0.0247+28.453+3.747+2.000-1.638-11.143=182.780kgAl2O3渣=1725.74*0.0283+42.09*0.0152+474.21*0.0447+68.0*0.0443+20*0.01-16.6*0.0262=73.453kgMgO渣=1725.74*0.0236+42.09*0.0028+474.21*0.0023+68*0.0026-16.6*0.0330=41.565kgS/2渣=0.5*(0.95*(1725.74*0.00051+42.09*0.00016+474.21*0.0074+68*0.0035)-(3)生铁成分核算[Mn]=0.001*(1725.74*0.00116+42.09*0.00082-16.6*0.00093-0.775*55/71)=0.142%[P]=0.001*(1725.74*0.00157+42.09*0.00070-16.6*0.00109+474.21*0.0004*62/142+68*0.0006*62/142)=0.282%(4)风量计算C平衡a)计算风口前燃烧碳量C矿=0C熔=0C碎=20.0*0.04=0.8kgC焦=474.21*0.8513=403.695kgC煤=68.0*0.8194=55.719kgC尘=16.6*0.20156=3.346kgCdFe=12/55.85*(10*94.561-20*0.94561)*0.45=89.600kgCdsi,Mn,P,S=24/28*10*0.52+12/55*10*0.14+60/62*10*0.282+12/32*509.00*0.008=9 .019kgC[C]=10*4.473=44.730kgCH2O化=0.3*12/18*42.09*0.0224=0.189kgC风口=0.8+403.695+55.719-3.346-89.600-9.019-44.73-0.189=313.291kgb)计算风量鼓风中O2的浓度=(1-0.0175)*0.21+0.5*0.0175=0.215燃烧C风口需O2量=22.4/24*313.291=292.405 Nm3/t其中,喷吹物可供O2=68*(0.0081*22.4/32+0.0180*22.4/36)=1.147则V风=(292.405-1.147)/0.215=1354.688鼓风比重=32/22.4*(1-0.0175)*0.21+28/22.4*(1-0.0175)*(1-0.21)+18/22.4*0.0175=1.279kg/ Nm3鼓风重量=1354.688*1.279=1732.65kg/t风中水分=0.0175*1354.688=23.70704Nm3/t干风体积=(1-0.0175)*1354.777=1330.981干风重量=1330.981*(32/22.4*0.21+28/22.4*(1-0.21))=1713.638 kg/t(5)炉顶煤气量及成分计算H2:入炉总H2=0.0175*1354.777+11.2*474.21*(0.0051+4/16*0.0051)+11.2*68*(0.0217+2/18*0.0180)+0.3*22.4/18*42.09*0.0224=75.969 Nm3H2还=0.4*75.969=30.388 Nm3VH2=0.6*75.969=45.581CO2:a:22.4/159.7*(1725.74*0.5747+42.09*0.9241-16.6*0.46063)+22.4/87*(42.09*0.0013)=143.5076b:22.4/55.85*(1-0.45-0.081591)*(10*94.561-20*0.85)=174.455rh2=55.85/22.4*30.388/(10*94.561-20*0.85)=0.082c:22.4/44*(42.09*0.0033-16.6*0.0162)=-0.06619Vco2=317.896CO:A:22.4/12*313.311=584.8472B:22.4/12*(89.600+9.019+0.189)=184.4416C: 174.455+143.5076=317.9626Vco=451.3262N2:A: 1354.777*(1-0.0175)*(1-0.21)=1051.544B:22.4/28*(474.21*0.0050+68*0.0088)=2.37556Vn2=1053.92H2O:A:18/22.4*30.388=24.41893B:0.7*42.09*0.0224=0.659971H2O=22.4/18*(24.41893+0.659971)=31.2093干煤气比重=44/22.4*0.1701+28/22.4*(0.2415+0.564)+2/22.4*0.0244=1.343179kg/Nm3干煤气重量=1868.723*1.343179=2510.066Kg/t两次迭代nco和nH2计算、核算直接还原度(1)nco和nH2计算nco=41.21nH2=41.20%nH2/ nco=1(2)核算直接还原度rdRd=1-rico-riH2=1-riΒ=41.21%/(1-41.21%)=0.7009696Ri=(55.85/(945.61-20))*((412.0835/12)*(16.97%+0.7009696*2.39%)/(16.97%+24.21%)-(16.6*0.046063+1725.74*0.5747+49.02*0.9241)/159.7-42.09*0.0013)=0.55 C气化=565.2974*12/28+622.6485*12/44=412.0835kgRd=0.45 与预选定的rd一致热平衡计算(1)热收入项风口前碳燃烧放出的热量:qc=9800*313.291=3.070252GJ直接还原C氧化成CO qcd=9800*(89.600+9.019)=0.966间接还原CO:qico=(143.5076+173.5433)*12650=4.010间接还原H2:qiH2=10800*32.12093=0.346906热风带入物理热:q=1354.688*(1.437438*1056-10800*0.0175)=1.800292C风=0.21*(1-0.0175)*1.486+0.79*(1-0.0175)*1.418+0.0175*1.727=1.437438 成渣热:1130*42.09*0.0028=133.1728*10^-6炉料带入的物理热:0Σq入=10.13544(2)热支出项铁氧化物分解耗热:=6.442314Fesi=329*55.85/71.85*(474.21*0.0102+68*0.0096+0.2*(1725.74*0.1562+49.02*0.0 043))=0.01520199Fe2o3=2370*111.7/159.7*(1725.74*0.5747+42.09*0.9241) =1.708518Feo=4990*945.61=4.718594硅:=31360*0.52*10=0.163072锰:=7015*0.142*10=0.0099613磷:=36000*0.282*10=0.101520总=6.716868脱硫:8300*509*0.008=0.0337976直还:=2890*0.45*(10*94.561-20+22960*10*0.52+4877*10*0.142+26520*10*0.282)=1.404859545碳酸盐分解=(4040+0.5*3770)*49.02*0.0033=0.000958喷吹燃料分解=68*(1005+(331+13440)*0.018)=0.085195704熔渣带走热焓=509*1780=0.906020铁水带走热焓=1000*1240=1.240000炉顶煤气带走热焓=1867.81198*1.3913685*209+32.12093*1.519*209=0.5533497水分蒸发:2450*(49.02*0.028+474.21*0.042)+1.244*(49.02*0.028+474.21*0.042)*1.519*209=0.06056688C煤气=1.301*0.0239+1.786*0.1697+1.311*(0.5643+0.2421)=1.3913685高炉煤气热值=1868.723*(12650*0.2421+10800*0.0239)未燃烧碳热值=33390*(10*4.473+16.6*0.20156)冷却带走热=0.681891有效热能利用系数:Q有=10.19345-(0.55335+0.060567+0.681891)=8.897642 =8.897642/10.19345=87.29%碳素热能利用系数:=0.2932*0.07068*41.21%=0.58447228区域热平衡热收入项:风口前碳素=3.070252热风带入=1.800292中温区=1.360058+0.6732759Q焦=(474.21-16.6*20.156/85.13)*1.507*950=0.6732759 Q矿=(1767.83-16.6*(1-20.156/85.13)-32/44.8*(143.5076+173.5433+30.388))*0.95*950=1.360058热支出项:直还:=1.404859545脱硫:4650*509*0.008=0.018935碳酸盐:0.000958-0.000133=0.000825炉渣:0.90602铁水:=1240*1000=1.240000煤气:q=1867.593*1.411*1000=2.635174V间=1867.81198-22.4/44*(49.02*0.0033+16.6*0.0162)=1867.593操作线(1)O/Fe=(0.583019*48/160+0.152583*16/72)/16/(0.527259/56)=1.386123 (2)Yf=9.019/12/(945.61/56)=0.04451(3)Yb=313.29/12/(945.6/56)=1.546129(4)xA=1+16.97%/(16.97%+24.21%)=1.412093(5)。
450高炉开炉配料计算

450m3高炉开炉配料计算
一、原燃料化学成份:
二、计算参数
1、全炉焦比 3.0
2、全炉碱度 1.0
3、正常料碱度 1.05
4、料线(m) 1.0
5、正常料焦比0.9
6、炉料压缩率% 12.0
7、铁元素回收率% 99.0
8、风温℃>800
9、焦批(干):4600kg 10、生铁中含[Si]%:2.5
11、生铁中含铁:93%
12、各种入炉料堆比重:t/m3
13、木柴装到风口中心线
3)
三、配料计算
1、正常料配比:
烧结矿56% 4.51t/ch 球团矿44% 3.55t/ch
批铁量 5.11t/ch
2、空焦加灰石量(T):共9.9吨,每批0.715吨
3、炉料体积:m3
1)正常料:K 体积7.931 P 体积 4.424
压缩体积10.873
2)空焦:K 体积7.931 N 体积0.447
压缩体积7.37
3)净焦:K 体积7.931 压缩体积 6.979
4、确定填料组成:
1)炉缸填木柴:61.8 m3(风口中由线到炉缸上部容积为9.16 m3)
2)料线1.0米占炉喉体积:15.20 m3
3)净焦装到炉腰高度的1/2占体积:106.34 m3
4)净焦装到炉腰高度的1/2折合净焦批数:15
5)高炉装正常料和空焦的体积为:270.87
6)正常料批数:14 空焦批数为:17
四、开炉料用量
五、开炉料装入表(见Excle)。
《高炉炼铁技术》项目11任务111配料计算

三、计算过程
以下以一吨生铁作为计算单位,进行计算。 1.根据铁平衡求铁矿石需要量 焦炭带入Fe量=450×(56×0.0075/72+56×0.0005/88)=2.78
公斤 煤粉带入Fe量=75×0.0145×56/72=0.85公斤。 进入炉渣铁量=949.9×0.003/0.997=2.86公斤(相当FeO=3.67
Fe
Mn
P
S
生铁
0.997
0.5
1.0
炉渣
0.003
0.5
0
煤气
0
0
0
0.6
8.炉渣碱度R= CaO/SiO2=1.03
二、原料成分的换算:
矿石分析现场一般只给出Fe,Mn,P,S,FeO,SiO2,CaO, MgO,A12O3,烧损等,配成全分析要通过换算
所以原料分析的核算,一要确定存在形态,二要掌握元素量与化合 物量之间的换算关系。换算之后各成分之和应平衡成100%,其 办法有两种:其一是根据化验室对某种化学成分的分析误差范围, 人为的调成100%,其二是用均衡扩大或缩小的方法去配成100 %。
(3)终渣MnO量为:1808.11×0.00095×0.5×71/55=1.11公斤 (4)终渣SiO2量为:214.21—15=199.21公斤 (5)终渣CaO量为:198.57+16.85×0.4068=205.45公斤 (6)终渣A12O3量为: 1808.11×0.0105+450×0.00483+75×0.0742+16.85×0.0034=46.
MnO FeO
69.71 1.11 3.67
开炉方案

4#高炉开炉方案配料计算一、开炉料参数选择:1、带风装料、全焦开炉、热风点火;2、开炉焦比:3.0t/tFe,正常焦比:1.0t/tFe;3、焦批重(千):5.0t;4、矿批重:7.5t,配比:机烧60%,球团40%;5、生铁成分:【Si】:3.0%,【S】:≤0.050%,【Fe】:92%;6、炉渣碱度:CaO/SiO2=1.0~1.05倍;7、炉料压缩率:12%(平均压缩率);8、送风温度:700~800℃;9、入炉料堆比重:t/m³烧结矿球团矿焦炭石灰石1.802.20 0.57 1.6010 高炉各部容积:m311开炉料化学成分:二配料计算:1)开炉焦比3.0t/tTe,焦批5.0t时的矿批重计算:矿批重=5÷3×92%÷58.95%=2.602t2)开炉料批组成:焦批:5.0t 体积v焦=5÷0.57×(1—12%)=7.72m3矿批:2.602 体积v矿=(2.602×60%÷1.80+2.602×40%÷2.20)×(1—12%)=1.19m33)一批料体积(压缩后)V料=7.72+1.19=8.91m3,4)高炉装料体积:606.54m35)开炉总批数:606.54÷8.91=68.07 取68批。
6)高炉总装焦量:5.0×68=340t高炉总装矿量2.602×68=176.94.7)将矿石折合成7.5t/批时正常矿批数:176.94÷7.5=23.59 取23批。
校正总矿量:=23×7.5=172.5t总矿量铁水:Fe总=172.5×58.95%÷92%=110.53t校正开炉焦比:焦比=340÷110.53=3.08t/tTe8)计算空焦石灰石加入量:1)因死铁层和炉缸的焦炭80%不参加与第一周期的造渣反应,所以计算炉渣碱度时把这段焦炭数量除去;(1)(死铁层+炉缸)×80%的焦炭量=(27.164+97.979)×0.57×80%=57.07t(2)参与反应的总焦量=340—57.07=282.93t2)校正炉渣碱度,空焦加石灰量:(1)∑矿CaO=172.5×1000×6.55%=11298.75Kg∑焦CaO=282.93×1000×12.3%×3%=1044.01Kg∑总;CaO=11298.75+1044.01=12342.76Kg(2)∑矿SiO2=172.5×1000×5.14=8866.5Kg∑焦SiO2=282.93×1000×12.3%×45%=15660.18Kg3 进入铁水中的SiO2量=110.53×1000×3%×2.14=7096.11Kg4:进入渣中∑总SiO2=8866.5+15660.18-7096.11=17430.57Kg 5:∑总CaO1t∑总SiO2相比:∑CaO/∑SiO2=0.71%碱度低须配加灰石,6;需加石灰石量=17430.57-12342.76×1.0=10632.83Kg 50%-2.15%9)开炉料安排:1)死铁层,炉缸,2/3炉腹填充:净焦净焦批数=(27.164+97.929+107.820×2/3)÷7.72=25.5批取26批。
九江1080立方米高炉开炉配料计算

九江1080立方米高炉开炉配料计算
一、配料参数的选择
全炉焦比3.2t/t,正常料焦比0.9t/t.
全炉碱度R2=0.86,正常料碱度R2=1.06,全炉Al2O3≤14%全炉压缩率13%
生铁成分及元素回收率
二、炉型参数,装料料线为1.6米
三、原燃料成分及全炉用料计算结果
装料情况
炉渣成分
四、正常料计算
1、焦批设定为6吨/批,焦比0.9吨/吨,碱度=1.06
2、矿批数确定:批铁量为:6/0.9=6.67吨/批,正常料批数=20批
3、锰矿量为:0.41吨/批,共计20批
五、炉料安排
1、全炉料批数为71批,其中正常料为20批,净焦20批,空焦
1段19批,空焦2段12批
2、依据经验净焦从风口中心线开始一直加至炉腹上沿,则净焦批
数为(22.68+174.584)/10.38=19.652批,取20批
3、空焦2段组成:石灰石:0.73吨/批,白云石:0.63吨/批,硅
石:0.18吨/批,萤石:0.2吨/批
4、空焦1段组成:依据经验空焦1段炉身高度的18%处,体积
为130.19立方米,则空焦1段批数为(97.31+130.19/11.78)
=19.31,取19批。
空焦2段和正常料占容积为429.71立方米。
5、空焦1段组成:石灰石:1.2吨/批,白云石1吨/批,萤石0.2
吨/批
六、计算结果
1、风口中心线一下装木柴
2、表中焦炭量为干焦量,上料时按实际焦炭水份计算成湿
焦碳量。
- 1、下载文档前请自行甄别文档内容的完整性,平台不提供额外的编辑、内容补充、找答案等附加服务。
- 2、"仅部分预览"的文档,不可在线预览部分如存在完整性等问题,可反馈申请退款(可完整预览的文档不适用该条件!)。
- 3、如文档侵犯您的权益,请联系客服反馈,我们会尽快为您处理(人工客服工作时间:9:00-18:30)。
高炉开炉配料计算一开炉料原则1配料要求1.1总焦比:2800Kg/t.Fe;1.2炉渣碱度:1.00(MgO 8.0%,Al2O3≤16%);1.3正常料焦比:1.0 t / t.Fe。
2原燃料配比2.1冶金焦; 赵城焦, 石家庄焦(各1/2)2.2矿石:烧结矿哈默斯利块矿印度球团黑旺矿30% 20% 25% 25%2.3熔剂:石灰石,白云石,硅石;3原燃料理化指标见表1和表2。
二配料计算1、预计生铁成分元素Fe C Si Mn S含量(%) 92.47 4.0 3.0 0.5 0.032 、Fe、Mn回收率Fe回收率: 99.0%;Mn回收率 60.0%; S 分配率:85%进入炉渣,5%进入生铁。
3、以100 Kg混合矿计算:3.1 100 Kg混合矿平均含Fe:30×57.04%+20×65.36%+25×66.04+25×25.76% = 53.134,100 Kg混合矿出铁:100×53.13%×0.99 / 0.9247 = 56.886 Kg。
3.2炉渣成分核算:(1)生铁中Si消耗SiO256.886×3.0%×60 / 28 = 3.657(2)炉渣中FeO量53.134×1.0%×72 / 56 = 0.683(3)入炉料的S负荷30×0.014%+20×0.012%+25×0.007%+25×0.046%+56.886×0.53%=0.321(4)炉渣中的CaS0.321×85%×72 / 32=0.614(5)脱硫消耗CaO0.614×56/72=0.478(6)原燃料成分中进入炉渣的数量(7)炉渣成分调整为使炉渣成分达到要求标准,加白云石和硅石进行调整。
硅石加入量为:x白云石加入量为:y3.927+91.88% x +2.91% y =10.096+2.31% x+30.09% y2.045+0.30% x +20.47% y= 8.0%20.652+96.25% x+53.47% y解方程:x = 7.422 Kg。
y = 0.947 Kg。
(8)加熔剂后的炉渣成分4. 吨铁渣量和熔剂用量(Kg)4.1吨铁渣量1000 / 56.886×28.524= 501.424.2吨铁加硅石量1000 / 56.886×7.442 =130.824.3吨铁白云石量1000 / 56.886×0.947 = 16.645.生铁成分核算(%)[Mn] =(20×0.45%+25×1.41%)×0.60% / 56.88 6= 0.47%[S] = 0.321×0.05 / 56.88 6= 0.028%[P] = 0.028%×25 / 56.886 = 0.012%三高炉装料计算1.正常料计算正常料矿批5000Kg,炉料压缩率按13%计算。
1.1正常料矿批组成矿石名称烧结矿哈块矿印度球团黑旺矿组成数量(Kg) 1500 1000 1250 12501.2正常料焦批,焦炭水分按6%计算。
5000 ×53.13%×0.99 / 0.9247=3025.86,取3025Kg。
1—0.061.3正常料熔剂量硅石:7.442×5000/100=372,取370 Kg。
白云石:0.947×5000/100=47.35,取50 Kg。
1.4正常料每批料体积(V1)1.5 1.0 1.25 1.25 3.025 0.050 0.370 V1=( + + + + + + )1.852.54 2.20 1.68 0.55 1.64 1.64×(1— 0.13)= 7.197m32净焦料批体积(V2),净焦压缩率12.5%。
V2=3.025/ 0.55×(1—0.125)= 4.812 m33空料料批体积(V3),焦批为3025Kg,空料压缩率12.5%。
每批空料需加石灰石数量(X)3025×0.94×11.69%×4.87%+50.56% X=1.003025×0.94×11.69×45.40% +0.48% XX=269.29 ,取270Kg。
V2 =(3.025 / 0.55+0.270 / 1.62)×(1—0.125)= 4.958 m3正常料(H)空料(Y)净焦(J)7.197 m3 4.958 m3 4.812 m3四高炉装料方案1.高炉各部位装料容积及品种部位填充容积(m3)装料品种炉缸和2/3炉腹 67.92+50.45 = 118.37 J1/3炉腹和炉腰 30.27+36.82 = 67.09 Y炉身 205.56 Y + H炉喉 8.71 H Σ 401.771.2净焦批数(J)118.37 / 4.812 = 24.598 ,取25批;1.3空料批数(Y)67.09 / 4.958 =13.531,取14批;1.4炉身和炉喉填充正常料和空料批数设空料批数为A,正常料批数为B。
4.812×25+4.958×14 + 4.958A +7.197 B = 401.773.025×0.94×(25+14+A+B)= 2.805.0×53.134% / 0.9247 ×B解方程得:A = 6.27取6批B = 25.15取25批1.5核算全焦比:3025 ×0.94×(25+14+6+25)= 2799.21Kg / t . Fe。
5000 /100×56.886×25填充容积:4.812 ×25 + 4.958×20 + 7.197 ×25 = 399.385 m3。
2炉内实际装料批数2.1装净焦批数(炉缸和2/3炉腹)118.37 / 4.812 = 24.60,取25批。
2.2装空料批数(1/3炉腹和炉腰)67.09 / 4.958 = 13.53 ,取14批。
2.3 空料+正常料(炉身+炉喉)空料:6批;正常料:25批。
2.4累计装料: J+ Y+ H = 25+14+6+25 = 70批3 高炉各部位装料品种及顺序3.1各部位装料品种部位填充容积(m3)装料品种装入方式炉缸和2/3炉腹 118.37 25 J 25KK1/3炉腹和炉腰 67.09 14 Y 14KK炉身和炉喉 214.27 6 Y +25 H 6KK+12KKPP+13PPKK Σ 401.773.2 装入顺序(1)净焦:J ——KK×25(2)空料:Y——KK×14(3)6 Y + 25 H:1. KK+ PPKK +KKPP22. KK+PPKK + 2KKPP33. KK+ 2PPKK + 2KKPP44. KK+PPKK + KKPP + 2PPKK+KKPP55. KK+ 2PPKK +2 KKPP +PPKK + KKPP66. KK+ 2PPKK +2 KKPP+ PPKK5(2+3+4+5+6+5=25;11KKPP,14PPKK)如果装料未到料线,继续装焦比1.0的正常料。
五送风后装料的配料计算1、第一次铁的铁量和渣量1.1铁量的确定第一次铁的铁量以10~15吨为宜,死铁层贮铁30~40吨,则需14~15批正常料到达风口后变成液态渣铁。
因而,第一次炉渣则是由14~15批正常料和空料及净焦燃烧后的灰分所组成。
1.2渣量和炉渣成分核算SiO2 CaO Al2O3 MgO FeO CaS Σ正常料(14批) 7541.8 7541.8 2390.5 1584.8 478.1 429.8石灰石 25.92 2730.24 10.8焦炭 6832.9 732.96 5084.04 225.86 35640Σ 14401 11005 7475 1851 478 430 % 40.41 30.88 20.97 5.19 1.34 1.20 99.99 R = 0.76(因为送风前期焦炭灰分有部分被吹出,实际碱度高于此计算值)估计在0.90左右。
2、送风后变料(750 Kg/t.Fe)计算2.1预计生铁成分元素Fe C Si Mn S含量(%) 93.47 4.0 2.0 0.5 0.032.2 R=1.05,Fe回收率99.5%。
2.3以100 Kg混合矿计算:(1) 100 Kg混合矿平均含Fe:30×57.04%+20×65.36%+25×66.04+25×25.76% = 53.134,(2) 100 Kg混合矿出铁:53.134×0.995/0.9347=56.562(3) 100 Kg混合矿需焦炭56.562×0.75=42.421(4) Si还原消耗SiO256.562×2.0%×60/28=2.424(5)进入炉渣中的FeO53.134×0.005×72/56=0.342(6)入炉料S负荷30×0.014%+20×0.012%+25×0.007%+25×0.046%+42.42×10.53%=0.245(7)进入炉渣的CaS0.245×0.85×72/32=0.468消耗CaO:0.468×56/72=0.364(8)炉渣组分核算设:硅石用量为X,白云石用量为Y。
4.388+0.9188X+0.0291Y)×1.05=10.126+0.231X+0.3009 Y2.019+0.0030X+0.2047 Y= 0.0820.157+0.9625X+0.5347Y解方程:X=5.916Y=0.194(10)加熔剂后的炉渣成分SiO2 CaO Al2O3 MgO FeO CaS ΣR数量 9.829 10.321 2.918 2.076 0.342 0.468 25.954(%) 37.87 39.77 11.24 8.00 1.32 1.80 100.00 1.05(11)吨铁渣量及熔剂量硅石:1000/56.562×5.916=104.59Kg白云石:1000/56.562×0.914=3.43 Kg渣量:1000/56.562×25.954=458.86 Kg2.4矿批组成(1)矿批出铁量2.845/0.75=3.793t(2) 矿批3.793×0.9347/ 0.53134×0.995 =6.706t,取6.70t(3) 矿批组成矿批硅石量:104.59×3.793=396.71,取400Kg矿批白云石量:3.43×3.793=13.01,取15 Kg烧结矿哈块矿印球团黑旺矿硅石白云石2010 1340 1675 1675 400 15(4) 料批体积2.010 1.340 1.675 1.675 0.400 0.0153.025+ + + + + + =9.125m31.852.54 2.20 1.68 1.64 1.64 0.55压缩率12.5%, 9.125m3×87.5% = 7.98 m33焦比700 Kg/t.Fe的配料计算3.1预计生铁成分元素Fe C Si Mn S含量(%) 93.72 4.0 1.75 0.5 0.033.2 R=1.08,Fe回收率99.5%。