复合材料成形技术课件
合集下载
复合材料的制造方法PPT课件

技术进行加热和加压。这样生产出的结构件相对于同样的
铝合金零件重量减少25%,成. 本降低20%。
8
(2) 穿刺
▪ 穿刺是复合材料结构三维加强的一种简单方法,在某些方 面优于缝合技术。但是它不能用于制造预成形体。在这个 工艺中利用薄的削棒以正确的角度在固化前或固化时插入 二维的碳纤维环氧复合材料层板中,从而获得三维增强复 合材料结构。Z向削棒可以是金属材料,也可采用非金属材 料。削棒插入的方式有两种,一是采用真空袋热压的方法, 二是采用超声技术。
将熔融的金属压力熔浸于成形模具内的预成形体(可 以由长纤维、短纤维或所颗粒构成)而成形。通常预 成形体是接近最终成品的形状。。
▪ 在大多数情况下,纤维不会成为熔融金属凝固时的晶
核。在熔融金属的凝固过程中,纤维附近的金属最后
固化。结果是通过在高压下纤维与金属的接触而使熔
融金属形成强固的界面,而且一般也不会形成氧化膜。
.
4
聚合物基 金属基 陶瓷基 复合材料 复合材料 复合材料
液相工艺 固相工艺
➢液体状树脂的含 浸 ➢预浸料坯成形 ➢(玻璃钢)片状模 塑料 ➢热塑性塑料的注 射成形
➢热塑性塑料的热 压成形
➢压力熔浸与无压 熔浸 ➢搅拌铸造 ➢喷射沉积成形 ➢定向凝固共晶 ➢热喷射
➢定向氧化 ➢定向凝固共晶 ➢利用有机聚合物 的合成
➢粉末冶金(热压、 ➢粉体烧结 机械合金化、SPS) ➢反应成形 ➢合金箔扩散键合 ➢拉拔等机加工成 形
气相工艺
➢PVD(物理气相 沉积)
.
➢CVD(化学气相
沉积)
➢CVI(化学气相
渗透)
5
塑料基复合材料的制备成形
.
6
4.2 树脂基复合材料
复合材料制备的技术讲义模压成型实例ppt课件
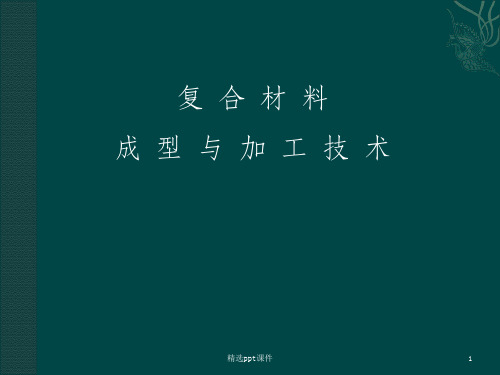
火箭发动机喷管耐热内衬原材料性能指标
产地 北京251厂 陕西玻璃纤维总厂 吉林碳素纤维厂
游离酚 (%) 11.22 SiO2含量 (%) ≥ 96 含碳量 (%) 精选ppt≥课件92
主要性能指标 固体含量 (%) 98.09% 径向强力 (N/mm) 486/25 径向强力 (N/mm) 800/25
精选ppt课件
3
4.3 模压成型工艺过程 (1)模压工艺流程
模压料计量、预热或预压
冷模具
模具预热
涂脱模剂
嵌件放置
加模压料
合模
模具清理
脱模
保压固化
排气
后处理
精选ppt课件
4
①模压料预热目的 ➢提高物料流动性,可预压成型,便于装模; ➢去除物料中大部分的水分和挥发物,提高制品性能; ➢降低模压压力,减少对型腔的磨损,延长模具的使用寿命;
模具预热
制
品
装模,初始压力 制
备
成型压力,保温2h
胶液配精置选ppt课件
脱模,修整
23
6、模压工艺参数确定 (根据树脂的放热曲线) 616#氨酚醛树脂DTA曲线特征温度
固化过程 编号
峰始温度/℃ 峰顶温度/℃
1
87
145
2
89
147
3
85
143
4
90
148
平均
88
146
结束温度/℃ 180 180 180 180 180
温度,也不易成型结构复杂的制品。因此,应根据模压料的流动性能
来选定合适的工艺参数。
精选ppt课件
15
(3)防眩板模压工艺参数的确定
防眩板各部位的厚度不一。根部厚度最大,为10mm。两边厚度次 之,为6mm。中间厚度最薄,仅为3mm。制品属薄壁结构,形状较为复 杂。当防眩板用铁架、螺栓固定竖立后,作为一种悬臂梁受力构件, 要求制品具有较好的抗折强度和弹性,以满足使用要求。从制品性能、 结构和形状要求来看,采用较大的成型压力和较高的成型温度是较理 想的。压力大,温度高,有利于提高制品的强度,且容易成型薄壁制 品。模温高,与固化放热峰的温差就大,制品的表面质量较好。考虑 到模压料的性能与生产效率,合适的保温时间是非常重要的。保温时 间太短,制品有可能固化不完全;保温时间过长,生产效率低。
复合材料的成形工艺PPT课件

• 制品质量稳定,生产率高;但投资大,层间剪切强度低; • 湿法
• 劳动条件差,强度大,质量不易控制,不易自动化; • 半干法
第29页/共33页
七、拉挤成形工艺(pultrusion process)
• 送纱→浸胶→预成形→固化成形→牵引→恒定截 面型材
• 设备价低,生产率高,原料利用率高 • 制品方向性强,剪切强度低 • 适用于不同界面形状的长条状、板状等型材。
第8页/共33页
9.2 金属基复合材料成形工艺
• 制备金属基复合材料(metal matrix composites, MMC),关键在于获得基体与增强体之间良好的浸润 与合适的界面结合。金属基复合材料复合加工较为困难, 主要分为三大类:
• 固态法 基体处于固态的加工方法,以避免金属基体与 增强材料之间的界面反应。包括粉末冶金法、扩散粘结 法(热压法、热等静压法)、形变法(轧制、挤压、拉 拔)、爆炸焊接法等。
品。
第26页/共33页
四、层压成形工艺(lamination p ro c e s s ) • 层叠胶布→模板之间→加热、加压固化→冷却、脱模、修整→层压板
• 制品表面光,质量好且稳定,设备简单,生产率高 • 只能生产板材,且尺寸受限,制品精度低,劳动轻度大。
第27页/共33页
五、模压成形工艺(press m oul di ng ) • 生产率高,制品尺寸精确,质量好且稳定,表面光洁,价低,自动化程度高,无
第6页/共33页
三、复合材料的增强机制和复合原则
• 复合原则 • 基体起粘接作用 • 基体对纤维的润湿性好; • 基体的塑性和韧性好; • 基体能保护好纤维表面。 • 增强材料承载大部分; • 强度、刚度要高,密度小,热稳定性高; • 增强体与基体结合强度高; • 纤维表面处理,增加表面粗糙度或形成活性基团 • 纤维的含量、直径、长度、分布适当; • 纤维、基体热胀系数相近。
• 劳动条件差,强度大,质量不易控制,不易自动化; • 半干法
第29页/共33页
七、拉挤成形工艺(pultrusion process)
• 送纱→浸胶→预成形→固化成形→牵引→恒定截 面型材
• 设备价低,生产率高,原料利用率高 • 制品方向性强,剪切强度低 • 适用于不同界面形状的长条状、板状等型材。
第8页/共33页
9.2 金属基复合材料成形工艺
• 制备金属基复合材料(metal matrix composites, MMC),关键在于获得基体与增强体之间良好的浸润 与合适的界面结合。金属基复合材料复合加工较为困难, 主要分为三大类:
• 固态法 基体处于固态的加工方法,以避免金属基体与 增强材料之间的界面反应。包括粉末冶金法、扩散粘结 法(热压法、热等静压法)、形变法(轧制、挤压、拉 拔)、爆炸焊接法等。
品。
第26页/共33页
四、层压成形工艺(lamination p ro c e s s ) • 层叠胶布→模板之间→加热、加压固化→冷却、脱模、修整→层压板
• 制品表面光,质量好且稳定,设备简单,生产率高 • 只能生产板材,且尺寸受限,制品精度低,劳动轻度大。
第27页/共33页
五、模压成形工艺(press m oul di ng ) • 生产率高,制品尺寸精确,质量好且稳定,表面光洁,价低,自动化程度高,无
第6页/共33页
三、复合材料的增强机制和复合原则
• 复合原则 • 基体起粘接作用 • 基体对纤维的润湿性好; • 基体的塑性和韧性好; • 基体能保护好纤维表面。 • 增强材料承载大部分; • 强度、刚度要高,密度小,热稳定性高; • 增强体与基体结合强度高; • 纤维表面处理,增加表面粗糙度或形成活性基团 • 纤维的含量、直径、长度、分布适当; • 纤维、基体热胀系数相近。
复合材料成型工艺培训课件(PPT 34页)

4、阻燃型树脂 阻燃型树脂是在合成时使用一种能产生阻燃(自熄)的成分,例
如使用四溴苯酐、氯茵酸酐(HET酸酐)取代苯酐代合成树脂。 5、耐气候型树脂
这类树脂使用新戊二醇及甲基丙烯酸酯类交联单体,并添加紫外光 吸收剂,提高了树脂的耐气候性和光稳定性。树脂透明性好,耐用树脂 浇铸体的折射率可与玻璃纤维的折射率相近或一致。 6、高强型树脂
复合材料成型工艺
主讲 金保宏 材料科学与工程学院
第2章 手糊成型工艺
手糊成型的玻璃钢制品,如:船舶、汽车 配件、贮罐、玻璃钢管接头、家具等
2.1 手糊成型的原材料
增强材料 玻璃纤维 碳纤维 芳纶纤维 超高分子量聚乙烯纤维玻璃纤维
基体材料 不饱和聚酯树脂 环氧树脂 酚醛树脂 其它热固性树脂 聚氨酯树脂 热塑性树脂 高性能树脂 双马来酰亚胺树脂
2.2 糊制与固化
铺层糊制
手工铺层糊制分干法和湿法两种: 1 干法铺层
用预浸布为原料,先将预浸料(布)按样板裁剪成坯 料.铺层时加热软化,然后再一层一层地紧贴在模具上.并 注意排除层间气泡,使密实。此法多用于热压罐和袋压成型。
2 湿法铺层
直接在棋具上将增强材料浸胶,一层一层地紧贴在模具上, 排除气泡,使之密实。一般手糊工艺多用此法铺层
树脂和玻纤比:70/(100 - 70)=2.33, 树脂质量:2.7×2.33=6.29kg/m2 填料质量:6.29×40/60=4.1kg/m2 玻璃毡厚:2.7×0.391=1.05mm 树脂厚:6. 29×0.837=5. 265mm 填料厚:4.19×0.4=1.676mm 铺后总厚度;1. 05十5.26十1. 676≈8mm
1、通用型树脂 通用型树脂主要是邻苯型不饱和聚酯树脂,它们大多
复合材料的成型工艺课件

注射成型工艺
注射成型工艺是将热塑性或热固 性复合材料加热至熔融状态,然 后通过注射机将其注入模具中,
冷却后脱模得到制品的工艺。
该工艺适用于制备大型、结构复 杂的制品,如家电外壳、汽车零
部件等。
注射成型工艺具有生产效率高、 自动化程度高等优点,但模具成 本较高,且对材料性能要求较高
。
层压成型工艺
层压成型工艺是将多层复合材料叠合 在一起,然后在压力和温度作用下使 其粘合在一起并成型的一种工艺。
随着科技的发展,对复合材料的 性能要求越来越高,复合材料成 型工艺正朝着高性能化的方向发
展。
智能化
智能化成型工艺能够提高生产效率 和产品质量,是复合材料成型工艺 的重要发展方向。
绿色化
环保意识的提高,对复合材料的生 产过程中的环保要求也越来越高, 绿色化成型工艺成为未来的发展趋 势。
复合材料成型工艺面临的挑战
。
体育器材领域的应用实例
总结词
轻量、高强度、耐用
VS
详细描述
体育器材领域也是复合材料应用的重要领 域,如滑雪板、羽毛球拍、自行车车架等 。这些应用主要得益于复合材料的轻量、 高强度和耐用等特性,能够提高运动器材 的性能和寿命。
05
复合材料成型工艺的发展趋势与挑战
复合材料成型工艺的发展趋势
高性能化
热压成型工艺的原理与特点
热压成型工艺原理
热压成型是利用热塑性复合材料的热塑性,在加热、加压条 件下,将材料加热至熔点或软化点,然后在压力作用下使材 料塑性变形并贴合在模具表面,冷却固化后形成所需形状的 制品。
热压成型特点
热压成型工艺具有生产效率高、制品尺寸精度高、表面质量 好等优点,适用于生产形状复杂、尺寸精度要求高的复合材 料制品。
复合材料的成型工艺ppt课件
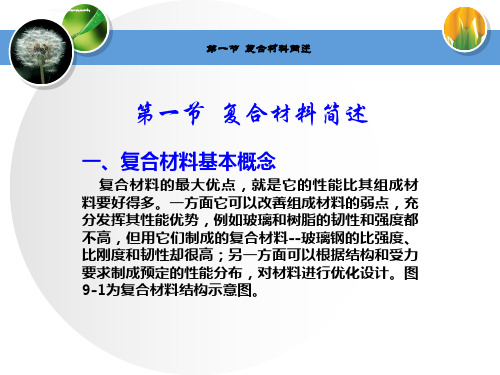
第二节 金属基复合材料(MMC)成形工艺
一、固态法
1.扩散黏结法(Diffusion Bonding) 如图9-2所示,扩散黏结是一种在较长时间、
较高温度和压力下,通过固态焊接工艺,使同类 或不同类金属在高温下互扩散而黏结在一起的工 艺方法。
2.形变法(Plastic Forming) 形变法就是利用金属具有塑性成型的工艺特点
2.复合材料的特点
(1)比强度和比刚度高 (2)抗疲劳性好 (3)高温性能好 (4)减振性能好 (5)断裂安全性高 (6)可设计性好
为 了 规 范 事 业单位 聘用关 系,建 立和完 善适应 社会主 义市场 经济体 制的事 业单位 工作人 员聘用 制度, 保障用 人单位 和职工 的合法 权益
第一节 复合材料简述
四 、 复 合 材 料 的 失 效 (Failure of Composite)
复合材料的失效一般是指其疲劳破坏过程。
1.制造加工损伤
此种损伤产生初始缺陷。,它包括:纤维铺设不 均,扭结、死扣等,树脂不均;纤维切断、错排; 固化不足;有孔隙、气泡;材质污染等。
2.使用引起的损伤
此种损伤导致缺陷发展。它包括:树脂裂纹或老 化;分层;纤维断裂;振动较大导致的纤维断裂; 温度变化较大;机加工产生内应力;碰撞等。
二、复合材料用原料
1.增强材料
(1)碳纤维(Carbon Fiber) (2)硼纤维(Boron Filament) (3)芳纶(Aramid Ring) (4)玻璃纤维(Glass Fiber) (5)碳化硅纤维(Silicon Carbide Fiber) (6)晶须(Whisker)
2.基体材料
3)基体能够很好地保护纤维表面,不产生表面 损伤、不产生裂纹。
复合材料成型工艺(全套课件250P)
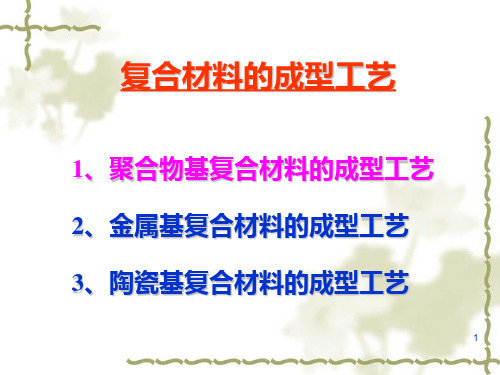
将定量的模塑料或颗粒状树脂与短纤维
的混合物放入敞开的金属对模中,闭模后加 热使其熔化,并在压力作用下充满模腔,形
成与模腔相同形状的模制品;再经加热使树
脂进一步发生交联反应而固化,或者冷却使 热塑性树脂硬化,脱模后得到复合材料制品。
7
金属对 模准备
模塑料、 颗粒树脂
短纤维
制品
加热、加压 涂脱模剂 模压成型 加热 冷却
N,N’-二甲基苯胺
丙酮 玻纤 质量/份 100 1
1
180 270
硬脂酸锌
颜料 玻纤
2
3-4 46
14
2.4.2 模压料的制备工艺:
由纤维(或织物)浸渍树脂制备模压料的生产工艺可分为:预混法、 预浸法
(1)预混法
a. 定义:是先将玻纤切成15-30mm,然后与一定量的树脂搅拌均匀,再经撕松、 烘干而制得。 b.特点:纤维松散且无定向、流动性好,制备过程纤维强度损失大。成型方法,在各种成型工
艺中所占比例仅次于手糊/喷射和连续成型,居第三位。
近年来随着专业化、自动化和生产效率的提高,制品成本不断 降低,使用范围越来越广泛。 模压制品主要用作结构件、连接件、防护件和电气绝缘等,广 泛应用于工业、农业、交通运输、电气、化工、建筑、机械等领域。 由于模压制品质量可靠,在兵器、飞机、导弹、卫星上也都得
13
2.4.1 模压料的组成:
短纤维增强材料 树脂基体材料 辅助材料 应用最多的是玻璃纤维; 应用最多的是酚醛、环氧树脂; 原材料 F-46环氧树脂 NA酸酐 质量/份 100 80
举例:模压料典型配方
原材料 616酚醛树脂 KH-550 乙醇 玻纤 质量/份 100 1 100 150 原材料 液体三聚氰胺树脂 KH-550
的混合物放入敞开的金属对模中,闭模后加 热使其熔化,并在压力作用下充满模腔,形
成与模腔相同形状的模制品;再经加热使树
脂进一步发生交联反应而固化,或者冷却使 热塑性树脂硬化,脱模后得到复合材料制品。
7
金属对 模准备
模塑料、 颗粒树脂
短纤维
制品
加热、加压 涂脱模剂 模压成型 加热 冷却
N,N’-二甲基苯胺
丙酮 玻纤 质量/份 100 1
1
180 270
硬脂酸锌
颜料 玻纤
2
3-4 46
14
2.4.2 模压料的制备工艺:
由纤维(或织物)浸渍树脂制备模压料的生产工艺可分为:预混法、 预浸法
(1)预混法
a. 定义:是先将玻纤切成15-30mm,然后与一定量的树脂搅拌均匀,再经撕松、 烘干而制得。 b.特点:纤维松散且无定向、流动性好,制备过程纤维强度损失大。成型方法,在各种成型工
艺中所占比例仅次于手糊/喷射和连续成型,居第三位。
近年来随着专业化、自动化和生产效率的提高,制品成本不断 降低,使用范围越来越广泛。 模压制品主要用作结构件、连接件、防护件和电气绝缘等,广 泛应用于工业、农业、交通运输、电气、化工、建筑、机械等领域。 由于模压制品质量可靠,在兵器、飞机、导弹、卫星上也都得
13
2.4.1 模压料的组成:
短纤维增强材料 树脂基体材料 辅助材料 应用最多的是玻璃纤维; 应用最多的是酚醛、环氧树脂; 原材料 F-46环氧树脂 NA酸酐 质量/份 100 80
举例:模压料典型配方
原材料 616酚醛树脂 KH-550 乙醇 玻纤 质量/份 100 1 100 150 原材料 液体三聚氰胺树脂 KH-550
复合材料的成型加工技术

优越的抗电弧性、上色的范围广、硬度高、耐磨 性好、耐热性高等。
二、增强材料及其表面处理
(一)玻璃纤维及其织物 1、玻璃纤维:是由玻璃高温拉丝制成,其强度
高于块状玻璃。 主要成份:铝硅硼酸盐和钙钠硅酸盐。
2、玻璃纤维及其织物的制造 1) 玻璃纤维的制造工艺 玻璃球→坩锅→熔化→流出→牵伸→喷浆料
(润滑、耐磨、保护)→卷取
增强塑料性能优越:
1. 密度低、比强度高; 2. 绝热性好; 3. 耐化学腐蚀性强; 4. 介电性能优良。
当然,增强塑料也存在不足之处:弹性模量 低、受力时有较大变形、表面硬度低、耐温性能 差、容易老化等。
增强塑料的基本组成
增强材料:常用的底材有纸张、棉布、木材薄片、 玻璃布或玻璃毡、石棉毡和石棉纸、合成纤维的 织物以及碳纤维及陶瓷纤维等,增强材料如纤维、 片状无机物。
间歇式处理:温度偏低而时间长,可采取 280℃和15-25min。
C、化学处理法: 1、后处理: 玻璃纤维/织物→热处理(浆料留量<1%)→
偶联剂处理→水洗→烘干。纤维表面有一层偶联 剂,最通用的方法。
2、前处理法:将偶联剂加在浆料中,以便偶 联剂在拢丝过程中就附在玻璃纤维的表面上
3、迁移法:方法将偶联剂按一定等例直接加 到树脂中,再经过浸胶涂覆使其与玻璃纤维/织物 发生作用。
如印刷电路版用的覆铜层压板
1. 浸渍
常用树脂:
层压塑料制品常用树脂有:酚醛树脂、环氧树 脂、不饱和聚酯树脂、有机硅树脂、氨基树脂等, 此外也有少数其它品种树脂,如DAP树脂、二苯醚 甲醛树脂、芳烷基醚甲醛树脂、糠醛丙酮树脂、聚 酰亚胺树脂等。
1、聚酯树脂 优点:优越电性能、透明性、抗水、酸性。
缺点:耐热性差、表面不光滑(增强用纤丝 在表面突出、露纤) 2、环氧树脂: 用酸酐/胺类固化剂
二、增强材料及其表面处理
(一)玻璃纤维及其织物 1、玻璃纤维:是由玻璃高温拉丝制成,其强度
高于块状玻璃。 主要成份:铝硅硼酸盐和钙钠硅酸盐。
2、玻璃纤维及其织物的制造 1) 玻璃纤维的制造工艺 玻璃球→坩锅→熔化→流出→牵伸→喷浆料
(润滑、耐磨、保护)→卷取
增强塑料性能优越:
1. 密度低、比强度高; 2. 绝热性好; 3. 耐化学腐蚀性强; 4. 介电性能优良。
当然,增强塑料也存在不足之处:弹性模量 低、受力时有较大变形、表面硬度低、耐温性能 差、容易老化等。
增强塑料的基本组成
增强材料:常用的底材有纸张、棉布、木材薄片、 玻璃布或玻璃毡、石棉毡和石棉纸、合成纤维的 织物以及碳纤维及陶瓷纤维等,增强材料如纤维、 片状无机物。
间歇式处理:温度偏低而时间长,可采取 280℃和15-25min。
C、化学处理法: 1、后处理: 玻璃纤维/织物→热处理(浆料留量<1%)→
偶联剂处理→水洗→烘干。纤维表面有一层偶联 剂,最通用的方法。
2、前处理法:将偶联剂加在浆料中,以便偶 联剂在拢丝过程中就附在玻璃纤维的表面上
3、迁移法:方法将偶联剂按一定等例直接加 到树脂中,再经过浸胶涂覆使其与玻璃纤维/织物 发生作用。
如印刷电路版用的覆铜层压板
1. 浸渍
常用树脂:
层压塑料制品常用树脂有:酚醛树脂、环氧树 脂、不饱和聚酯树脂、有机硅树脂、氨基树脂等, 此外也有少数其它品种树脂,如DAP树脂、二苯醚 甲醛树脂、芳烷基醚甲醛树脂、糠醛丙酮树脂、聚 酰亚胺树脂等。
1、聚酯树脂 优点:优越电性能、透明性、抗水、酸性。
缺点:耐热性差、表面不光滑(增强用纤丝 在表面突出、露纤) 2、环氧树脂: 用酸酐/胺类固化剂
- 1、下载文档前请自行甄别文档内容的完整性,平台不提供额外的编辑、内容补充、找答案等附加服务。
- 2、"仅部分预览"的文档,不可在线预览部分如存在完整性等问题,可反馈申请退款(可完整预览的文档不适用该条件!)。
- 3、如文档侵犯您的权益,请联系客服反馈,我们会尽快为您处理(人工客服工作时间:9:00-18:30)。
料成为首选结构复合材料。其在宇航、汽车、电子、建筑工业中
占有重要的位置。
例:碳化硅强化的铝基复合材料已在轿车发动机汽缸内套和
活塞、摩托车刹车片、山地自行车钢圈等耐磨材料和航天航空用 仪表材料等方面获得应用。
复合材料实际应用
电子工业
航空航天工业 汽车工业
2 金属基复合材料的制备与制坯工艺
简称PM法,是利用粉末冶金原理,将基体粉末与增强颗粒按设计要 求的比例进行机械混合,然后再压坯、烧结或直接用混合料进行热压 、热轧、热挤成型来制备金属基基复合材料的方法。是较早用来制备 镁基复合材料的工艺。 粉末冶金的特点 :可控制增颗粒的体积分数 ,增强体在基体中分 布均匀;制备温度较低 ,一般不会发生过量的界面反应。该法工艺设 备较复杂,成本较高,不易制备形状复杂的零件。
纤维与基体间形成良好的界面结合,得到复合材料制件。
:(1)工艺参数易于精确控制; (2)纤维在制件中的空间位置可按构件受力情况进行精确铺排, 制件质量好。
:由于模型加压的单向性,使该工艺限于制作形状较为简单的板 材、某些型材或叶片。
: 、拉拔、轧制、锻造、热等静压等。 通过热挤压的方法可将金属基复合材料坯料加工成各种 断面形状的制品,赋予复合材料各种断面形状的同时,也达到 及提 高材料 、强度、塑性等目的。
:
(1)挤压比:一般挤压比在4~30之间,随挤压比的增大,挤压制品中晶 须或纤维沿挤压方向的定向排列程度增强,但过大的挤压比会使晶须或纤
维折断程度也增大。对于颗粒相增强复合材料,同样随着挤压比的增大,
复合材料抗拉强度和延伸率亦随之增大。 (2)挤压温度:一般挤压温度低于固相线温度20~100℃,并随强化相含 量的增加而增加。在较低温度范围内,提高挤压温度有利于晶须或纤维的 定向排列,有利于松弛应力,使晶须在变形中损伤与折断减少,复合材料 的抗拉强度明显上升。在较高温度范围内,提高挤压温度可降低变形力, 但对晶须或纤维的定向排列影响不大,并使挤压件表面质量下降。 (3)挤压速度:挤压速度通常要求很低,极限挤压速度一般为 3~120mm/min。
5
:
热挤压模具结构
由于热挤压模具是在高温和高负荷下工作的,因此其抗磨性
和耐疲劳性能要求很高,模具设计中必须考虑冷却问题。
热挤压模具设计中的重要参数:
(1)反挤压杆底端的锥顶角α1。 (2)正挤压凹模锥角α2. (3)圆角半径R的大小。
随着α1、α2及R的增大,挤压力降低,同时晶须或纤维的折断程度明显降低, 大幅度提高了制件的抗拉强度和塑性。
谢 谢
人有了知识,就会具备各种分析能力, 明辨是非的能力。 所以我们要勤恳读书,广泛阅读, 古人说“书中自有黄金屋。 ”通过阅读科技书籍,我们能丰富知识, 培养逻辑思维能力; 通过阅读文学作品,我们能提高文学鉴赏水平, 培养文学情趣; 通过阅读报刊,我们能增长见识,扩大自己的知识面。 有许多书籍还能培养我们的道德情操, 给我们巨大的精神力量, 鼓舞我们前进。
强化材料
普通铸 造法 金属 粉末
混合
直接水冷铸造
坯料
:在高温下施加静压力,使纤维与基体
扩散结合在一起的方法。
:按照制件形状、纤维体积密度及增强方向的要 求,将金属基复合材料预制条带及基体金属箔或粉末布,经 剪裁、铺设、叠层、组装,在低于复合材料基体金属熔点的 温度下加压并保持一定时间;基体金属产生 与扩散,使
强化 材料 粉末冶 金法 混合 金属 粉末 预制 成形
烧结
坯料
:首先使晶须或颗粒(SiC)预成形体,然后将该成形 体和合金熔液倒入金属模内固化,再在1000大气压的高压下铸造,生产
出供挤压用的坯锭(坯锭直径可大到200毫米)。
强化材料预成形体
高压铸 造法 金属 熔体
高压 铸造
坯料
:把强化材料和金属粉末混合后,再加热熔化,之后 把金属熔体引入到一个铸模里进行冷却从而得到坯料。铸造模具采用 一套流体或水冷却系统对水冷金属铸型或者模样板进行冷却,冷却介 质可以是油、空气或水等,通过对进入管道的流体温度和流量等的调 节,可以控制冷却速度。
(1)容易产生黏模现象。 (2)制品表面产生粗糙、条纹等缺陷。
复合材 料坯料 摩擦力 凹模 宏观裂纹
坯料表 面晶须
摩擦力
凹模
坯料表面 拉应力
表面裂纹
(1)采用无死角挤压、包覆挤压、陶瓷模挤压等方法有利于减少 挤压时的黏模现象,有效降低复合材料表面摩擦力,并能提高挤压速 度。 (2)为降低摩擦力,挤压前在坯料与凹模及挤压筒间均采用油剂 石墨进行润滑。
;后续加工生产灵活性大,有利于获得管、棒、线、空心
或实心型材。而对于粉末冶金法制备的复合材料,利用高温挤压变形时强三向 压应力和强剪切变形作用,可以破坏粉末表面的氧化膜,改善粉末颗粒之间的
接触状态,压合内部的空洞和孔隙,提高制品的致密度与性能。
利用挤压加工时基体金属的塑性流动,可增加晶须或短纤维的沿流 动方向的取向,从而达到强化效果。 为了利用取向性提高复合材料的强化效果,要求强化相的长径比达到 某一临界值以上。
复合材料结构
பைடு நூலகம்金属
纤维
基体
颗粒
增强相
晶须
基体 复合 材料 增强 体
例:“25%SiCp/6061复合材料”表示在6061铝合金基体中分散有 25%SiC颗粒(体积分数)增强体的复合材料。 注:分散颗粒用下标p表示,晶须或纤维用下标w表示。
金属基复合材料多以铝及铝合金、镁及镁合金和钛及钛合金
作为基体,由于具有密度低、比强度和比弹性模量高、导电导热 性能高、韧性和抗冲击性能高、耐磨性好等优点,金属基复合材
材 料 学 李 小 强
复 合 材 料 成 形 技 术
目录
1
金属基复合材料
2 金属基复合材料的制备与制坯工艺 3
热压扩散成形法
4 金属基复合材料的坯料的热挤压成型 5
热挤压模具结构
1
金属基复合材料
复合材料的定义
由两种或两种以上物理和化学性质不同的物质组合而成的 一种多相固体材料。
复合材料的种类
(1)聚合物基复合材料。其中含有热固性树脂基复合材料,热塑 性树脂基和橡胶基复合材料。 (2)金属基复合材料。其中含有轻金属基,高熔点金属基,金属 间化合物基复合材料。 (3)无机非金属基复合材料。其中含有陶瓷基,碳基,水泥基复 合材料。