【机械类文献翻译】冲压变形1
机械专业中英文对照翻译大全
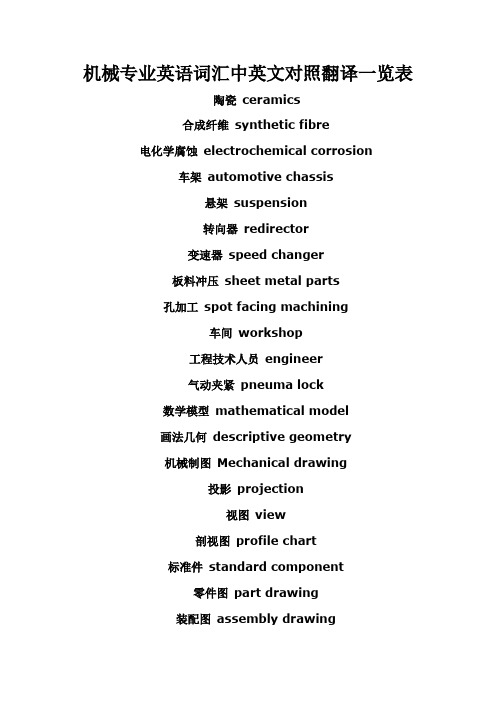
机械专业英语词汇中英文对照翻译一览表陶瓷ceramics合成纤维synthetic fibre电化学腐蚀electrochemical corrosion车架automotive chassis悬架suspension转向器redirector变速器speed changer板料冲压sheet metal parts孔加工spot facing machining车间workshop工程技术人员engineer气动夹紧pneuma lock数学模型mathematical model画法几何descriptive geometry机械制图Mechanical drawing投影projection视图view剖视图profile chart标准件standard component零件图part drawing装配图assembly drawing尺寸标注size marking技术要求technical requirements刚度rigidity内力internal force位移displacement截面section疲劳极限fatigue limit断裂fracture塑性变形plastic distortion脆性材料brittleness material刚度准则rigidity criterion垫圈washer垫片spacer直齿圆柱齿轮straight toothed spur gear 斜齿圆柱齿轮helical-spur gear直齿锥齿轮straight bevel gear运动简图kinematic sketch齿轮齿条pinion and rack蜗杆蜗轮worm and worm gear虚约束passive constraint曲柄crank摇杆racker凸轮cams共轭曲线conjugate curve范成法generation method定义域definitional domain值域range导数\\微分differential coefficient求导derivation定积分definite integral不定积分indefinite integral曲率curvature偏微分partial differential毛坯rough游标卡尺slide caliper千分尺micrometer calipers攻丝tap二阶行列式second order determinant 逆矩阵inverse matrix线性方程组linear equations概率probability随机变量random variable排列组合permutation and combination 气体状态方程equation of state of gas动能kinetic energy势能potential energy机械能守恒conservation of mechanical energy动量momentum桁架truss轴线axes余子式cofactor逻辑电路logic circuit触发器flip-flop脉冲波形pulse shape数模digital analogy液压传动机构fluid drive mechanism机械零件mechanical parts淬火冷却quench淬火hardening回火tempering调质hardening and tempering磨粒abrasive grain结合剂bonding agent砂轮grinding wheel后角clearance angle龙门刨削planing主轴spindle主轴箱headstock卡盘chuck加工中心machining center 车刀lathe tool车床lathe钻削镗削bore车削turning磨床grinder基准benchmark钳工locksmith锻forge压模stamping焊weld拉床broaching machine拉孔broaching装配assembling铸造found流体动力学fluid dynamics流体力学fluid mechanics加工machining液压hydraulic pressure切线tangent机电一体化mechanotronics mechanical-electrical integration气压air pressure pneumatic pressure稳定性stability介质medium液压驱动泵fluid clutch液压泵hydraulic pump阀门valve失效invalidation强度intensity载荷load应力stress安全系数safty factor可靠性reliability螺纹thread螺旋helix键spline销pin滚动轴承rolling bearing滑动轴承sliding bearing弹簧spring制动器arrester brake十字结联轴节crosshead联轴器coupling链chain皮带strap精加工finish machining粗加工rough machining变速箱体gearbox casing腐蚀rust氧化oxidation磨损wear耐用度durability随机信号random signal离散信号discrete signal超声传感器ultrasonic sensor 集成电路integrate circuit挡板orifice plate残余应力residual stress套筒sleeve扭力torsion冷加工cold machining电动机electromotor汽缸cylinder过盈配合interference fit热加工hotwork摄像头CCD camera倒角rounding chamfer优化设计optimal design工业造型设计industrial moulding design有限元finite element滚齿hobbing插齿gear shaping伺服电机actuating motor铣床milling machine钻床drill machine镗床boring machine步进电机stepper motor丝杠screw rod导轨lead rail组件subassembly可编程序逻辑控制器Programmable Logic Controller PLC 电火花加工electric spark machining电火花线切割加工electrical discharge wire - cutting 相图phase diagram热处理heat treatment固态相变solid state phase changes有色金属nonferrous metal陶瓷ceramics合成纤维synthetic fibre电化学腐蚀electrochemical corrosion车架automotive chassis悬架suspension转向器redirector变速器speed changer板料冲压sheet metal parts孔加工spot facing machining车间workshop工程技术人员engineer气动夹紧pneuma lock数学模型mathematical model画法几何descriptive geometry机械制图Mechanical drawing投影projection视图view剖视图profile chart标准件standard component零件图part drawing装配图assembly drawing尺寸标注size marking技术要求technical requirements刚度rigidity内力internal force位移displacement截面section疲劳极限fatigue limit断裂fracture塑性变形plastic distortion脆性材料brittleness material刚度准则rigidity criterion垫圈washer垫片spacer直齿圆柱齿轮straight toothed spur gear 斜齿圆柱齿轮helical-spur gear直齿锥齿轮straight bevel gear运动简图kinematic sketch齿轮齿条pinion and rack蜗杆蜗轮worm and worm gear虚约束passive constraint曲柄crank摇杆racker凸轮cams共轭曲线conjugate curve范成法generation method定义域definitional domain值域range导数\\微分differential coefficient求导derivation定积分definite integral不定积分indefinite integral曲率curvature偏微分partial differential毛坯rough游标卡尺slide caliper千分尺micrometer calipers攻丝tap二阶行列式second order determinant 逆矩阵inverse matrix线性方程组linear equations概率probability随机变量random variable排列组合permutation and combination气体状态方程equation of state of gas动能kinetic energy势能potential energy机械能守恒conservation of mechanical energy 动量momentum桁架truss轴线axes余子式cofactor逻辑电路logic circuit触发器flip-flop脉冲波形pulse shape数模digital analogy液压传动机构fluid drive mechanism机械零件mechanical parts淬火冷却quench淬火hardening回火tempering调质hardening and tempering磨粒abrasive grain结合剂bonding agent砂轮grinding wheel Assembly line 组装线Layout 布置图Conveyer 流水线物料板Rivet table 拉钉机Rivet gun 拉钉枪Screw driver 起子Pneumatic screw driver 气动起子worktable 工作桌OOBA 开箱检查fit together 组装在一起fasten 锁紧(螺丝)fixture 夹具(治具)pallet 栈板barcode 条码barcode scanner 条码扫描器fuse together 熔合fuse machine热熔机repair修理operator作业员QC品管supervisor 课长ME 制造工程师MT 制造生技cosmetic inspect 外观检查inner parts inspect 内部检查thumb screw 大头螺丝lbs. inch 镑、英寸EMI gasket 导电条front plate 前板rear plate 后板chassis 基座bezel panel 面板power button 电源按键reset button 重置键Hi-pot test of SPS 高源高压测试Voltage switch of SPS 电源电压接拉键sheet metal parts 冲件plastic parts 塑胶件SOP 制造作业程序material check list 物料检查表work cell 工作间trolley 台车carton 纸箱sub-line 支线left fork 叉车personnel resource department 人力资源部production department生产部门planning department企划部QC Section品管科stamping factory冲压厂painting factory烤漆厂molding factory成型厂common equipment常用设备uncoiler and straightener整平机punching machine 冲床robot机械手hydraulic machine油压机lathe车床planer |plein|刨床miller铣床grinder磨床linear cutting线切割electrical sparkle电火花welder电焊机staker=reviting machine铆合机position职务president董事长general manager总经理special assistant manager特助factory director厂长department director部长deputy manager | =vice manager副理section supervisor课长deputy section supervisor =vice section superisor副课长group leader/supervisor组长line supervisor线长assistant manager助理to move, to carry, to handle搬运be put in storage入库pack packing包装to apply oil擦油to file burr 锉毛刺final inspection终检to connect material接料to reverse material 翻料wet station沾湿台Tiana天那水cleaning cloth抹布to load material上料to unload material卸料to return material/stock to退料scraped |\\'skr?pid|报废scrape ..v.刮;削deficient purchase来料不良manufacture procedure制程deficient manufacturing procedure制程不良oxidation |\\' ksi\\'dei?n|氧化scratch刮伤dents压痕defective upsiding down抽芽不良defective to staking铆合不良embedded lump镶块feeding is not in place送料不到位stamping-missing漏冲production capacity生产力education and training教育与训练proposal improvement提案改善spare parts=buffer备件forklift叉车trailer=long vehicle拖板车compound die合模die locker锁模器pressure plate=plate pinch压板bolt螺栓administration/general affairs dept总务部automatic screwdriver电动启子thickness gauge厚薄规gauge(or jig)治具power wire电源线buzzle蜂鸣器defective product label不良标签identifying sheet list标示单location地点present members出席人员subject主题conclusion结论decision items决议事项responsible department负责单位pre-fixed finishing date预定完成日approved by / checked by / prepared by核准/审核/承办PCE assembly production schedule sheet PCE组装厂生产排配表model机锺work order工令revision版次remark备注production control confirmation生产确认checked by初审approved by核准department部门stock age analysis sheet 库存货龄分析表on-hand inventory现有库存available material良品可使用obsolete material良品已呆滞to be inspected or reworked 待验或重工total合计cause description原因说明part number/ P/N 料号type形态item/group/class类别quality品质prepared by制表notes说明year-end physical inventory difference analysis sheet 年终盘点差异分析表physical inventory盘点数量physical count quantity帐面数量difference quantity差异量cause analysis原因分析raw materials原料materials物料finished product成品semi-finished product半成品packing materials包材good product/accepted goods/ accepted parts/good parts 良品defective product/non-good parts不良品disposed goods处理品warehouse/hub仓库on way location在途仓oversea location海外仓spare parts physical inventory list备品盘点清单spare molds location模具备品仓skid/pallet栈板tox machine自铆机wire EDM线割EDM放电机coil stock卷料sheet stock片料tolerance工差score=groove压线cam block滑块pilot导正筒trim剪外边pierce剪内边drag form压锻差pocket for the punch head挂钩槽slug hole废料孔feature die公母模expansion dwg展开图radius半径shim(wedge)楔子torch-flame cut火焰切割set screw止付螺丝form block折刀stop pin定位销round pierce punch=die button圆冲子shape punch=die insert异形子stock locater block定位块under cut=scrap chopper清角active plate活动板baffle plate挡块cover plate盖板male die公模female die母模groove punch压线冲子air-cushion eject-rod气垫顶杆spring-box eject-plate弹簧箱顶板bushing block衬套insert 入块club car高尔夫球车capability能力parameter参数factor系数phosphate皮膜化成viscosity涂料粘度alkalidipping脱脂main manifold主集流脉bezel斜视规blanking穿落模dejecting顶固模demagnetization去磁;消磁high-speed transmission高速传递heat dissipation热传rack上料degrease脱脂rinse水洗alkaline etch龄咬desmut剥黑膜D.I. rinse纯水次Chromate铬酸处理Anodize阳性处理seal封孔revision版次part number/P/N料号good products良品scraped products报放心品defective products不良品finished products成品disposed products处理品barcode条码flow chart流程表单assembly组装stamping冲压molding成型spare parts=buffer备品coordinate座标dismantle the die折模auxiliary fuction辅助功能poly-line多义线heater band 加热片thermocouple热电偶sand blasting喷沙grit 砂砾derusting machine除锈机degate打浇口dryer烘干机induction感应induction light感应光response=reaction=interaction感应ram连杆edge finder巡边器concave凸convex凹short射料不足nick缺口speck瑕??shine亮班splay 银纹gas mark焦痕delamination起鳞cold slug冷块blush 导色gouge沟槽;凿槽satin texture段面咬花witness line证示线patent专利grit沙砾granule=peuet=grain细粒grit maker抽粒机cushion缓冲magnalium镁铝合金magnesium镁金metal plate钣金lathe车mill锉plane刨grind磨drill铝boring镗blinster气泡fillet镶;嵌边through-hole form通孔形式voller pin formality滚针形式cam driver铡楔shank摸柄crank shaft曲柄轴augular offset角度偏差velocity速度production tempo生产进度现状torque扭矩spline=the multiple keys花键quenching淬火tempering回火annealing退火carbonization碳化tungsten high speed steel钨高速的moly high speed steel钼高速的organic solvent有机溶剂bracket小磁导liaison联络单volatile挥发性resistance电阻ion离子titrator滴定仪beacon警示灯coolant冷却液crusher破碎机阿基米德蜗杆Archimedes worm安全系数safety factor; factor of safety安全载荷safe load凹面、凹度concavity扳手wrench板簧flat leaf spring半圆键woodruff key变形deformation摆杆oscillating bar摆动从动件oscillating follower摆动从动件凸轮机构cam with oscillating follower 摆动导杆机构oscillating guide-bar mechanism 摆线齿轮cycloidal gear摆线齿形cycloidal tooth profile摆线运动规律cycloidal motion摆线针轮cycloidal-pin wheel包角angle of contact保持架cage背对背安装back-to-back arrangement背锥back cone ;normal cone背锥角back angle背锥距back cone distance比例尺scale比热容specific heat capacity闭式链closed kinematic chain闭链机构closed chain mechanism臂部arm变频器frequency converters变频调速frequency control of motor speed 变速speed change变速齿轮change gear change wheel变位齿轮modified gear变位系数modification coefficient标准齿轮standard gear标准直齿轮standard spur gear表面质量系数superficial mass factor表面传热系数surface coefficient of heat transfer 表面粗糙度surface roughness并联式组合combination in parallel并联机构parallel mechanism并联组合机构parallel combined mechanism并行工程concurrent engineering并行设计concurred design, CD不平衡相位phase angle of unbalance不平衡imbalance (or unbalance)不平衡量amount of unbalance不完全齿轮机构intermittent gearing波发生器wave generator波数number of waves补偿compensation参数化设计parameterization design, PD残余应力residual stress操纵及控制装置operation control device槽轮Geneva wheel槽轮机构Geneva mechanism ;Maltese cross 槽数Geneva numerate槽凸轮groove cam侧隙backlash差动轮系differential gear train差动螺旋机构differential screw mechanism差速器differential常用机构conventional mechanism; mechanism in common use车床lathe承载量系数bearing capacity factor承载能力bearing capacity成对安装paired mounting尺寸系列dimension series齿槽tooth space齿槽宽spacewidth齿侧间隙backlash齿顶高addendum齿顶圆addendum circle齿根高dedendum齿根圆dedendum circle齿厚tooth thickness齿距circular pitch齿宽face width齿廓tooth profile齿廓曲线tooth curve齿轮gear齿轮变速箱speed-changing gear boxes齿轮齿条机构pinion and rack齿轮插刀pinion cutter; pinion-shaped shaper cutter 齿轮滚刀hob ,hobbing cutter齿轮机构gear齿轮轮坯blank齿轮传动系pinion unit齿轮联轴器gear coupling齿条传动rack gear齿数tooth number齿数比gear ratio齿条rack齿条插刀rack cutter; rack-shaped shaper cutter齿形链、无声链silent chain齿形系数form factor齿式棘轮机构tooth ratchet mechanism插齿机gear shaper重合点coincident points重合度contact ratio冲床punch传动比transmission ratio, speed ratio传动装置gearing; transmission gear传动系统driven system传动角transmission angle传动轴transmission shaft串联式组合combination in series串联式组合机构series combined mechanism 串级调速cascade speed control创新innovation creation创新设计creation design垂直载荷、法向载荷normal load唇形橡胶密封lip rubber seal磁流体轴承magnetic fluid bearing从动带轮driven pulley从动件driven link, follower从动件平底宽度width of flat-face从动件停歇follower dwell从动件运动规律follower motion从动轮driven gear粗线bold line粗牙螺纹coarse thread大齿轮gear wheel打包机packer打滑slipping带传动belt driving带轮belt pulley带式制动器band brake单列轴承single row bearing单向推力轴承single-direction thrust bearing单万向联轴节single universal joint单位矢量unit vector当量齿轮equivalent spur gear; virtual gear当量齿数equivalent teeth number; virtual number of teeth 当量摩擦系数equivalent coefficient of friction当量载荷equivalent load刀具cutter导数derivative倒角chamfer导热性conduction of heat导程lead导程角lead angle等加等减速运动规律parabolic motion; constant acceleration and deceleration motion等速运动规律uniform motion; constant velocity motion等径凸轮conjugate yoke radial cam等宽凸轮constant-breadth cam等效构件equivalent link等效力equivalent force等效力矩equivalent moment of force等效量equivalent等效质量equivalent mass等效转动惯量equivalent moment of inertia等效动力学模型dynamically equivalent model底座chassis低副lower pair点划线chain dotted line(疲劳)点蚀pitting垫圈gasket垫片密封gasket seal碟形弹簧belleville spring顶隙bottom clearance定轴轮系ordinary gear train; gear train with fixed axes 动力学dynamics动密封kinematical seal动能dynamic energy动力粘度dynamic viscosity动力润滑dynamic lubrication动平衡dynamic balance动平衡机dynamic balancing machine动态特性dynamic characteristics动态分析设计dynamic analysis design动压力dynamic reaction动载荷dynamic load端面transverse plane端面参数transverse parameters端面齿距transverse circular pitch端面齿廓transverse tooth profile端面重合度transverse contact ratio端面模数transverse module端面压力角transverse pressure angle锻造forge对称循环应力symmetry circulating stress对心滚子从动件radial (or in-line ) roller follower对心直动从动件radial (or in-line ) translating follower对心移动从动件radial reciprocating follower对心曲柄滑块机构in-line slider-crank (or crank-slider) mechanism多列轴承multi-row bearing多楔带poly V-belt多项式运动规律polynomial motion多质量转子rotor with several masses惰轮idle gear额定寿命rating life额定载荷load ratingII 级杆组dyad发生线generating line发生面generating plane法面normal plane法面参数normal parameters法面齿距normal circular pitch法面模数normal module法面压力角normal pressure angle法向齿距normal pitch法向齿廓normal tooth profile法向直廓蜗杆straight sided normal worm法向力normal force反馈式组合feedback combining反向运动学inverse ( or backward) kinematics 反转法kinematic inversion反正切Arctan范成法generating cutting仿形法form cutting方案设计、概念设计concept design, CD防振装置shockproof device飞轮flywheel飞轮矩moment of flywheel非标准齿轮nonstandard gear非接触式密封non-contact seal非周期性速度波动aperiodic speed fluctuation非圆齿轮non-circular gear粉末合金powder metallurgy分度线reference line; standard pitch line分度圆reference circle; standard (cutting) pitch circle 分度圆柱导程角lead angle at reference cylinder分度圆柱螺旋角helix angle at reference cylinder分母denominator分子numerator分度圆锥reference cone; standard pitch cone分析法analytical method封闭差动轮系planetary differential复合铰链compound hinge复合式组合compound combining复合轮系compound (or combined) gear train 复合平带compound flat belt复合应力combined stress复式螺旋机构Compound screw mechanism复杂机构 complex mechanism杆组Assur group干涉interference刚度系数stiffness coefficient刚轮rigid circular spline钢丝软轴wire soft shaft刚体导引机构body guidance mechanism刚性冲击rigid impulse (shock)刚性转子rigid rotor刚性轴承rigid bearing刚性联轴器rigid coupling高度系列height series高速带high speed belt高副higher pair格拉晓夫定理Grashoff`s law根切undercutting公称直径nominal diameter高度系列height series功work工况系数application factor工艺设计technological design工作循环图working cycle diagram工作机构operation mechanism工作载荷external loads工作空间working space工作应力working stress工作阻力effective resistance工作阻力矩effective resistance moment 公法线common normal line公共约束general constraint公制齿轮metric gears功率power功能分析设计function analyses design 共轭齿廓conjugate profiles共轭凸轮conjugate cam构件link鼓风机blower固定构件fixed link; frame固体润滑剂solid lubricant关节型操作器jointed manipulator惯性力inertia force惯性力矩moment of inertia ,shaking moment 惯性力平衡balance of shaking force惯性力完全平衡full balance of shaking force惯性力部分平衡partial balance of shaking force 惯性主矩resultant moment of inertia惯性主失resultant vector of inertia冠轮crown gear广义机构generation mechanism广义坐标generalized coordinate轨迹生成path generation轨迹发生器path generator滚刀hob滚道raceway滚动体rolling element滚动轴承rolling bearing滚动轴承代号rolling bearing identification code 滚针needle roller滚针轴承needle roller bearing滚子roller滚子轴承roller bearing滚子半径radius of roller滚子从动件roller follower滚子链roller chain滚子链联轴器double roller chain coupling 滚珠丝杆ball screw滚柱式单向超越离合器roller clutch过度切割undercutting函数发生器function generator函数生成function generation含油轴承oil bearing耗油量oil consumption耗油量系数oil consumption factor赫兹公式H. Hertz equation合成弯矩resultant bending moment合力resultant force合力矩resultant moment of force黑箱black box横坐标abscissa互换性齿轮interchangeable gears花键spline滑键、导键feather key滑动轴承sliding bearing滑动率sliding ratio滑块slider环面蜗杆toroid helicoids worm环形弹簧annular spring缓冲装置shocks; shock-absorber灰铸铁grey cast iron回程return回转体平衡balance of rotors混合轮系 compound gear train积分integrate机电一体化系统设计mechanical-electrical integration system design机构mechanism机构分析analysis of mechanism机构平衡balance of mechanism机构学mechanism机构运动设计kinematic design of mechanism机构运动简图kinematic sketch of mechanism机构综合synthesis of mechanism机构组成constitution of mechanism机架frame, fixed link机架变换kinematic inversion机器machine机器人robot机器人操作器manipulator机器人学robotics技术过程technique process技术经济评价technical and economic evaluation 技术系统technique system机械machinery机械创新设计mechanical creation design, MCD 机械系统设计mechanical system design, MSD 机械动力分析dynamic analysis of machinery机械动力设计dynamic design of machinery机械动力学dynamics of machinery机械的现代设计modern machine design机械系统mechanical system机械利益mechanical advantage机械平衡balance of machinery机械手manipulator机械设计machine design; mechanical design机械特性mechanical behavior机械调速mechanical speed governors机械效率mechanical efficiency机械原理theory of machines and mechanisms机械运转不均匀系数coefficient of speed fluctuation机械无级变速mechanical stepless speed changes基础机构fundamental mechanism基本额定寿命basic rating life基于实例设计case-based design,CBD基圆base circle基圆半径radius of base circle基圆齿距base pitch基圆压力角pressure angle of base circle基圆柱base cylinder基圆锥base cone急回机构quick-return mechanism急回特性quick-return characteristics急回系数advance-to return-time ratio急回运动quick-return motion棘轮ratchet棘轮机构ratchet mechanism棘爪pawl极限位置extreme (or limiting) position极位夹角crank angle between extreme (or limiting) positions计算机辅助设计computer aided design, CAD计算机辅助制造computer aided manufacturing, CAM计算机集成制造系统computer integrated manufacturing system, CIMS计算力矩factored moment; calculation moment计算弯矩calculated bending moment加权系数weighting efficient加速度acceleration加速度分析acceleration analysis加速度曲线acceleration diagram尖点pointing; cusp尖底从动件knife-edge follower间隙backlash间歇运动机构intermittent motion mechanism减速比reduction ratio减速齿轮、减速装置reduction gear减速器speed reducer减摩性anti-friction quality渐开螺旋面involute helicoid渐开线involute渐开线齿廓involute profile渐开线齿轮involute gear渐开线发生线generating line of involute渐开线方程involute equation渐开线函数involute function渐开线蜗杆involute worm渐开线压力角pressure angle of involute渐开线花键involute spline简谐运动simple harmonic motion键key键槽keyway交变应力repeated stress交变载荷repeated fluctuating load交叉带传动cross-belt drive交错轴斜齿轮crossed helical gears胶合scoring角加速度angular acceleration角速度angular velocity角速比angular velocity ratio角接触球轴承angular contact ball bearing角接触推力轴承angular contact thrust bearing 角接触向心轴承angular contact radial bearing 角接触轴承angular contact bearing铰链、枢纽hinge校正平面correcting plane接触应力contact stress接触式密封contact seal阶梯轴multi-diameter shaft结构structure结构设计structural design截面section节点pitch point节距circular pitch; pitch of teeth节线pitch line节圆pitch circle节圆齿厚thickness on pitch circle节圆直径pitch diameter节圆锥pitch cone节圆锥角pitch cone angle解析设计analytical design紧边tight-side紧固件fastener径节diametral pitch径向radial direction径向当量动载荷dynamic equivalent radial load径向当量静载荷static equivalent radial load径向基本额定动载荷basic dynamic radial load rating径向基本额定静载荷basic static radial load tating径向接触轴承radial contact bearing径向平面radial plane径向游隙radial internal clearance径向载荷radial load径向载荷系数radial load factor径向间隙clearance静力static force静平衡static balance静载荷static load静密封static seal局部自由度passive degree of freedom矩阵matrix矩形螺纹square threaded form锯齿形螺纹buttress thread form矩形牙嵌式离合器square-jaw positive-contact clutch 绝对尺寸系数absolute dimensional factor绝对运动absolute motion绝对速度absolute velocity均衡装置load balancing mechanism抗压强度compression strength开口传动open-belt drive开式链open kinematic chain开链机构open chain mechanism可靠度degree of reliability可靠性reliability可靠性设计reliability design, RD空气弹簧air spring空间机构spatial mechanism空间连杆机构spatial linkage空间凸轮机构spatial cam空间运动副spatial kinematic pair空间运动链spatial kinematic chain 空转idle宽度系列width series框图block diagram雷诺方程Reynolds‘s equation离心力centrifugal force离心应力centrifugal stress离合器clutch离心密封centrifugal seal理论廓线pitch curve理论啮合线theoretical line of action 隶属度membership力force力多边形force polygon力封闭型凸轮机构force-drive (or force-closed) cam mechanism力矩moment力平衡equilibrium力偶couple力偶矩moment of couple连杆connecting rod, coupler连杆机构linkage连杆曲线coupler-curve连心线line of centers链chain链传动装置chain gearing链轮sprocket sprocket-wheel sprocket gear chain wheel联组V 带tight-up V belt联轴器coupling shaft coupling两维凸轮two-dimensional cam临界转速critical speed六杆机构six-bar linkage龙门刨床double Haas planer轮坯blank。
冲压原理及基本变形

(4)加預彎(如圖)
(5)外加調整 (6)設計上 選用彈性系數大, 屈服極限小、機械性能穩定 的材料。
沖壓原理及基本變形
2003.09.10
Page:16
四、彎曲U形件單邊間隙 t:材料厚度
Z=t+△+ct
△料厚正偏差
ct彎曲件高度和彎曲長度而決定之系數 c值一般有 0.04~0.15
五、彎曲問題:1、回彈 1、影響回因素:如前述 2、滑移 產生原因: (1)不對稱工件彎曲
沖壓原理及基本變形
2003.09.10
Page:2
塑性變形:材料在力F2作用下,由OA變形 到OA2, 除去外力,只能回復到OA2’, 不能回復到OA,此時則產生塑性 變形。 (如圖) σ s為屈服極限, σb為強度極限
f
σs
沖壓原理及基本變形
材料拉伸曲線圖
σb
x
Page:3
2003.09.10
三、 1
沖 孔
(2)沖孔面(見下圖)
落 料
沖壓尺寸曲光面尺寸決定,不管是落料還是沖孔。
沖壓原理及基本變形
2003.09.10
Page:5
五、
間隙對沖裁質量影響:
T:料厚、Z:沖裁間隙 1,間隙 合適,b=(1/3-1/2)T (如右圖)
2,間隙過大,b<1/5T 光面少, 不易分離,(如右圖)
3,間隙過小,b>3/4T時,毛刺易掉, 易產生銅絲(如右圖)
b
4, 變形
c
沖壓原理及基本變形
2003.09.10
Page:8
間隙對模具壽命影響:Z 受力F
磨損
在保証沖裁質量和尺寸前提下,Z 磨損 。
越好
Z 受力F 標准間隙: 銅材 3%-5%T, 不鏽鋼板 5%-8%T 、 八、 刀口沖子研磨: A3鋼
机械专业英文翻译

机械专业英文翻译 Company number:【WTUT-WT88Y-W8BBGB-BWYTT-19998】启动轴 starting axle 启动齿轮starting gear启动棘轮 starting ratchet wheel 复位弹簧 restoring, pull back spring弹簧座 spring seating 摩擦簧friction spring推力垫圈 thrust washer 轴挡圈axle bumper ring下料 filling 切断 cut 滚齿机 gear-hobbing machine剪料机 material-shearingmachine车床 lathe 拉床broaching machine垂直度 verticality, verticalextent 平行度 parallelism同心度 homocentricity位置度 position拉伤 pulling damage碰伤 bumping damage缺陷 deficiency严重缺陷 severe deficiency摩擦力 friction 扭距 twist滑动 glide 滚动 roll打滑 skid 脱不开 can’t seperate不复位 can’t restore 直径 diameterM值 = 跨棒距 test rod span公法线 common normal line 弹性elasticity频率特性 frequency characteristic误差 error响应 response 定位 allocation 机床夹具 jig 动力学 dynamic运动学 kinematic静力学 static分析力学 analyse mechanics拉伸 pulling压缩 hitting机床 machine tool刀具 cutter摩擦 friction联结 link传动 drive/transmission轴 shaft剪切 shear扭转 twist弯曲应力 bending stress三相交流电 three-phase AC磁路 magnetic circles变压器 transformer异步电动机 asynchronous motor几何形状 geometrical精度 precision正弦形的 sinusoid交流电路 AC circuit机械加工余量 machining allowance变形力 deforming force变形 deformation电路 circuit半导体元件 semiconductor element拉孔 broaching装配 assembling加工 machining液压 hydraulic pressure切线 tangent机电一体化 mechanotronics mechanical-electrical integration稳定性 stability介质 medium液压驱动泵 fluid clutch 液压泵 hydraulic pump阀门 valve失效 invalidation强度 intensity载荷 load应力 stress安全系数 safty factor可靠性 reliability螺纹 thread螺旋 helix键 spline销 pin滚动轴承 rolling bearing滑动轴承 sliding bearing弹簧 spring制动器 arrester brake十字结联轴节 crosshead联轴器 coupling链 chain皮带 strap精加工 finish machining粗加工 rough machining变速箱体 gearbox casing腐蚀 rust氧化 oxidation磨损 wear耐用度 durability机械制图Mechanical drawing投影 projection视图 view剖视图 profile chart标准件 standard component零件图 part drawing装配图 assembly drawing尺寸标注 size marking技术要求technical requirements刚度 rigidity内力 internal force位移 displacement截面 section疲劳极限 fatigue limit断裂 fracture塑性变形 plastic distortion脆性材料 brittleness material刚度准则 rigidity criterion垫圈 washer垫片 spacer直齿圆柱齿轮straight toothed spur gear斜齿圆柱齿轮helical-spur gear直齿锥齿轮straight bevel gear运动简图 kinematic sketch齿轮齿条 pinion and rack蜗杆蜗轮 worm and worm gear虚约束 passive constraint曲柄 crank摇杆 racker凸轮 cams反馈 feedback发生器 generator直流电源 DC electrical source 门电路 gate circuit外圆磨削 external grinding内圆磨削 internal grinding平面磨削 plane grinding变速箱 gearbox离合器 clutch绞孔 fraising绞刀 reamer螺纹加工 thread processing螺钉 screw铣削 mill铣刀 milling cutter功率 power工件 workpiece齿轮加工 gear mechining齿轮 gear主运动 main movement主运动方向direction of main movement进给方向 direction of feed进给运动 feed movement合成进给运动resultant movement of feed合成切削运动resultant movement of cutting合成切削运动方向 directionof resultant movement of cutting 切削深度 cutting depth前刀面 rake face刀尖 nose of tool前角 rake angle后角 clearance angle龙门刨削 planing主轴 spindle主轴箱 headstock卡盘 chuck加工中心 machining center车刀 lathe tool车床 lathe镗削 bore集成电路 integrate circuit挡板 orifice plate残余应力 residual stress套筒 sleeve扭力 torsion 冷加工 cold machining电动机 electromotor汽缸 cylinder过盈配合 interference fit热加工 hotwork摄像头 CCD camera倒角 rounding chamfer优化设计 optimal design工业造型设计industrial moulding design有限元 finite element滚齿 hobbing插齿 gear shaping伺服电机 actuating motor铣床 milling machine钻床 drill machine镗床 boring machine步进电机 stepper motor丝杠 screw rod导轨 lead rail组件 subassembly可编程序逻辑控制器Programmable LogicController PLC毛坯 rough桁架 truss轴线 axes逻辑电路 logic circuit触发器 flip-flop脉冲波形 pulse shape数模 digital analogy液压传动机构fluid drive mechanism机械零件 mechanical parts产品突出特点ProductHighlights特别优惠 special offersAssembly line组装线Layout布置图Conveyer流水线物料板Rivet table拉钉机Rivet gun拉钉枪Screw driver起子Electric screw driver电动起子Pneumatic screw driver气动起子worktable 工作桌OOBA开箱检查fit together组装在一起fasten锁紧(螺丝)fixture 夹具(治具)pallet栈板barcode条码barcode scanner条码扫描器fuse together熔合fuse machine热熔机repair修理operator作业员QC品管supervisor 课长ME制造工程师MT制造生技cosmetic inspect外观检查inner parts inspect内部检查thumb screw大头螺丝lbs. inch镑、英寸EMI gasket导电条front plate前板rear plate后板chassis 基座bezel panel面板power button电源按键reset button重置键Hi-pot test of SPS高源高压测试Voltage switch of SPS电源电压接拉键sheet metal parts 冲件plastic parts塑胶件SOP制造作业程序material check list物料检查表work cell工作间trolley台车carton纸箱sub-line支线left fork叉车personnel resource department人力资源部production department生产部门planning department企划部QC Section品管科stamping factory冲压厂painting factory烤漆厂molding factory成型厂common equipment常用设备uncoiler and straightener整平机punching machine 冲床robot机械手hydraulic machine油压机lathe车床planer |'plein|刨床miller铣床grinder磨床driller床linear cutting线切割electrical sparkle电火花welder电焊机staker=reviting machine铆合机position职务president董事长general manager总经理special assistant manager特助factory director厂长department director部长deputy manager | =vice manager副理section supervisor课长deputy section supervisor =vice section superisor 副课长group leader/supervisor组长line supervisor线长assistant manager助理to move, to carry, to handle搬运be put in storage入库pack packing包装to apply oil擦油to file burr 锉毛刺final inspection终检to connect material接料to reverse material 翻料wet station沾湿台Tiana天那水cleaning cloth抹布to load material上料to unload material卸料to return material/stock to退料scraped |'skrpid|报废scrape ..v.刮;削deficient purchase来料不良manufacture procedure制程deficient manufacturing procedure制程不良oxidation |' ksi'dein|氧化scratch刮伤dents压痕defective upsiding down抽芽不良defective to staking铆合不良embedded lump镶块feeding is not in place送料不到位stamping-missing漏冲production capacity生产力education and training教育与训练proposal improvement提案改善spare parts=buffer备件forklift叉车trailer=long vehicle拖板车compound die合模die locker锁模器pressure plate=plate pinch压板bolt螺栓name of a department部门名称administration/general affairs dept总务部automatic screwdriver电动启子thickness gauge厚薄规gauge(or jig)治具power wire电源线buzzle蜂鸣器defective product label不良标签identifying sheet list标示单screwdriver holder起子插座pedal踩踏板stopper阻挡器flow board流水板hydraulic handjack油压板车forklift叉车pallet栈板glove(s)手套glove(s) with exposed fingers割手套missing part漏件wrong part错件excessive defects过多的缺陷critical defect极严重缺陷major defect主要缺陷minor defect次要缺陷not up to standard不合规格dimension/size is a little bigger尺寸偏大(小)cosmetic defect外观不良slipped screwhead/slippery screw head螺丝滑头slipped screwhead/shippery screw thread滑手speckle斑点mildewed=moldy=mouldy发霉rust生锈deformation变形burr(金属)flash(塑件)毛边poor staking铆合不良excesssive gap间隙过大grease/oil stains油污inclusion杂质qualified products, up-to-grade products良品defective products, not up-to-grade products不良品waste废料board看板feeder送料机sliding rack滑料架defective product box不良品箱die change 换模to fix a die装模to take apart a die拆模to repair a die修模packing material包材basket蝴蝶竺plastic basket胶筐isolating plate baffle plate; barricade隔板carton box纸箱to pull and stretch拉深to put material in place, to cut material, to input落料to impose lines压线to compress, compressing压缩character die字模to feed, feeding送料transportation运输(be)qualfied, up to grade合格not up to grade, not qualified不合格material change, stock change材料变更feature change 特性变更evaluation评估prepare for, make preparations for 准备parameters参数rotating speed, revolution转速manufacture management制造管理abnormal handling异常处理production unit生产单位lots of production生产批量steel plate钢板roll material卷料manufacture procedure制程vocabulary for stamping冲压常词汇stamping, press冲压punch press, dieing out press冲床uncoiler & strainghtener整平机feeder送料机rack, shelf, stack料架cylinder油缸robot机械手taker取料机conveyer belt输送带transmission rack输送架top stop上死点bottom stop下死点one stroke一行程inch寸动to continue, cont.连动to grip(material)吸料location lump, locating piece, block stop 定位块reset复位smoothly顺利dent压痕scratch刮伤deformation变形filings铁削to draw holes抽孔inquiry, search for查寻to stock, storage, in stock库存receive领取approval examine and verify审核processing, to process加工delivery, to deliver 交货to return delivenry to.to send delinery backto retrn of goods退货registration登记registration card登记卡to control管制to put forward and hand in提报safe stock安全库存acceptance = receive验收to notice通知application form for purchase请购单consume, consumption消耗to fill in填写abrasion磨损die 模具figure file, chart file图档cutting die, blanking die冲裁模progressive die, follow (-on)die连续模compound die复合模punched hole冲孔panel board镶块to cutedges=side cut=side scrap切边to bending折弯to pull, to stretch拉伸Line streching, line pulling线拉伸engraving, to engrave刻印upsiding down edges翻边to stake铆合designing, to design设计design modification设计变化die block模块folded block折弯块sliding block滑块location pin定位销lifting pin顶料销die plate, front board模板padding block垫块stepping bar垫条upper die base上模座lower die base下模座upper supporting blank上承板upper padding plate blank上垫板spare dies模具备品spring 弹簧bolt螺栓document folder文件夹file folder资料夹to put file in order整理资料spare tools location手工备品仓first count初盘人first check初盘复棹人second count 复盘人second check复盘复核人equipment设备waste materials废料plain die简易模pierce die冲孔模forming die成型模progressive die连续模gang dies复合模shearing die剪边模riveting die铆合模pierce冲孔forming成型(抽凸,冲凸)draw hole抽孔bending折弯trim切边emboss凸点dome凸圆semi-shearing半剪stamp mark冲记号deburr or coin压毛边punch riveting冲压铆合side stretch侧冲压平reel stretch卷圆压平groove压线blanking下料stamp letter冲字(料号)shearing剪断tick-mark nearside正面压印tick-mark farside反面压印冲压名称类extension dwg展开图procedure dwg工程图die structure dwg模具结构图material材质material thickness料片厚度factor系数upward向上downward向下press specification冲床规格die height range适用模高die height闭模高度burr毛边gap间隙weight重量total wt.总重量punch wt.上模重量五金零件类inner guiding post内导柱inner hexagon screw内六角螺钉dowel pin固定销coil spring弹簧lifter pin顶料销eq-height sleeves=spool等高套筒pin销lifter guide pin浮升导料销guide pin导正销wire spring圆线弹簧outer guiding post外导柱stop screw止付螺丝located pin定位销outer bush外导套模板类top plate上托板(顶板)top block上垫脚punch set上模座punch pad上垫板punch holder上夹板stripper pad脱料背板up stripper上脱料板male die公模(凸模)feature die公母模female die母模(凹模)upper plate上模板lower plate下模板die pad下垫板die holder下夹板die set下模座bottom block下垫脚bottom plate下托板(底板) stripping plate内外打(脱料板) outer stripper外脱料板inner stripper内脱料板lower stripper下脱料板零件类punch冲头insert入块(嵌入件)deburring punch压毛边冲子groove punch压线冲子stamped punch字模冲子round punch圆冲子special shape punch异形冲子bending block折刀roller滚轴baffle plate挡块located block定位块supporting block for location定位支承块air cushion plate气垫板air-cushion eject-rod气垫顶杆trimming punch切边冲子stiffening rib punch = stinger 加强筋冲子ribbon punch压筋冲子reel-stretch punch卷圆压平冲子guide plate定位板sliding block滑块sliding dowel block滑块固定块active plate活动板lower sliding plate下滑块板upper holder block上压块upper mid plate上中间板spring box弹簧箱spring-box eject-rod弹簧箱顶杆spring-box eject-plate弹簧箱顶板bushing bolck衬套cover plate盖板guide pad导料块barreling 滚光加工 belling 压凸加工bending 弯曲加工 blanking 下料加工bulging 撑压加工 burring 冲缘加工cam die bending 凸轮弯曲加工caulking 合加工coining 压印加工 compressing 压缩加工compression bending 押弯曲加工crowning 凸面加工curl bending 卷边弯曲加工curling 卷曲加工cutting 切削加工 dinking 切断蕊骨double shearing 叠板裁断 drawing 引伸加工drawing with ironing 抽引光滑加工 embossing 浮花压制加工extrusion 挤制加工 filing 锉削加工fine blanking 精密下料加工 finish blanking 光制下料加工finishing 精整加工 flanging 凸缘加工folding 折边弯曲加工 folding 摺叠加工forming 成形加工 impact extrusion 冲击挤压加工indenting 压痕加工 ironing 引缩加工knurling 滚花 lock seaming 固定接合louvering 百叶窗板加工 marking 刻印加工necking 颈缩加工 notching 冲口加工parting 分断加工 piercing 冲孔加工progressive bending 连续弯曲加工 progressiveblanking 连续下料加工progressive drawing 连续引伸加工 progressiveforming 连续成形加工reaming 铰孔加工 restriking 二次精冲加工riveting 接加工 roll bending 滚筒弯曲加工roll finishing 滚压加工 rolling 压延加工roughing 粗加工 scrapless machining 无废料加工seaming 折弯重叠加工 shaving 缺口修整加工shearing 切断加工 sizing 精压加工/矫正加工slitting 割缝加工 spinning 卷边接staking 固 stamping 锻压加工swaging 挤锻压加工 trimming 整缘加工upsetting 锻粗加工 wiring 抽线加工冲压机械及周边关连用语back shaft 支撑轴 blank determination 胚料展开bottom slide press 下传动式压力机 board drophammer 板落锤brake 煞车 buckle 剥砂面camlachie cramp 铸包 casting on flat 合chamotte sand 烧磨砂 charging hopper 加料漏斗clearance 间隙 closed-die forging 合模锻造clump 夹紧 clutch 离合器clutch brake 离合器制动器 clutch boss 离合器轮壳clutch lining 离合器覆盖 coil car 带卷升降运输机coil cradle 卷材进料装置 coil reel stand 钢材卷料架column 圆柱 connection screw 连杆调节螺钉core compound 砂心黏结剂 counter blow hammer 对击锻锤cradle 送料架 crank 曲柄轴crankless 无曲柄式 cross crank 横向曲轴cushion 缓冲 depression 外缩凹孔dial feed 分度送料 die approach 模口角度die assembly 合模 die cushion 模具缓冲垫die height 冲压闭合高度 die life 模具寿命die opening 母模逃孔 die spotting press 调整冲模用压力机double crank press 双曲柄轴冲床 draght angle 逃料倾斜角edging 边锻伸 embedded core 加装砂心feed length 送料长度 feed level 送料高度filling core 埋入砂心 filling in 填砂film play 液面花纹 fine blanking press 精密下料冲床forging roll 辊锻机 finishing slag 炼後熔渣fly wheel 飞轮 fly wheel brake 飞轮制动器foot press 脚踏冲床 formboard 进模口板frame 床身机架 friction 摩擦friction brake 摩擦煞车 gap shear 凹口剪床gear 齿轮 gib 滑块引导部gripper 夹具 gripper feed 夹持进料gripper feeder 夹紧传送装置 hammer 槌机hand press 手动冲床 hand rack pinion press 手动齿轮齿条式冲床hand screw press 手动螺旋式冲床 hopper feed 料斗送料idle stage 空站 inching 微调尺寸isothermal forging 恒温锻造 key clutch 键槽离合器knockout 脱模装置 knuckle mechanic 转向机构land 模具直线刀面部 level 水平loader 供料器 unloader 卸料机loop controller 闭回路控制器 lower die 下模micro inching device 微寸动装置 microinching equipment 微动装置motor 马达 moving bolster 活动工作台notching press 冲缺口压力机 opening 排料逃孔overload protection device 防超载装置 pinch roll 导正滚轮pinion 小齿轮 pitch 节距pressfit 压入 progressive 连续送料pusher feed 推杆式送料 pusher feeder 料片押片装置quick die change system 快速换模系统 regrinding 再次研磨releasing 松释动作 reversedblanking 反转下料robot 机器人 roll formingmachine 辊轧成形roll forming machine 辊轧成形机roll release 脱辊roller feed 辊式送料 roller leveler辊式矫直机rotary bender 卷弯成形机 safetyguard 安全保护装置scrap cutter 废料切刀 scrap press废料冲床seamless forging 无缝锻造separate 分离shave 崩砂 shear angle 剪角sheet loader 薄板装料机 shot 单行程工作shrinkage fit 收缩配合 shutheight 闭合高度sieve mesh 筛孔 sintering of sand铸砂烧贴slide balancer 滑动平衡器 slughole 逃料孔spin forming machine 旋压成形机 spotting 合模stack feeder 堆叠拨送料机stickness 黏模性straight side frame 冲床侧板stretcher leveler 拉伸矫直机strip feeder 料材送料装置stripping pressure 弹出压力stroke 冲程 take out device 取料装置toggle press 肘杆式压力机transfer 传送transfer feed 连续自动送料装置turrent punch press 转塔冲床two speed clutch 双速离合器uncoiler 闭卷送料机unloader 卸载机 vibration feeder振动送料机wiring press 嵌线卷边机业务与贸易关连用语accept order 接受订货 account 帐户after service 售后服务 amendment 修正annual sales 年销售额 at sight 见票即付balance 余额 bank draft 汇票bargain goods 廉价品 batch 批次bid 出价 bid sales 投标买卖bill of landing 提单 bills receivable 应收票据brand 品牌 bulk cargo 散装货business transaction 商业交易 buyer 买方carbon copy 打字副本 cargo collection 揽货carton 纸箱 cash in advance 预付现金catalogue 型录 cheque 支票CLF 运费保险费在内价格 claim 索赔clearance goods 清仓品 commision 佣金commission 批发商 complain 抱怨container 货柜 correspondence bank 往来银行cost 成本 cost and freight; C&F 含运费价格custom broker 报关行 customer 客户D/A 承兑交单 D/P 付款交单deferred payment 分期付款 deferred shipment 分期装运delivery on spot 当场交货 delivery time 交期delivery order 交货单 discount 折扣discount on draft 贴现 documentary draft 跟单汇票down payment 订金 enclosure 附件endorsement 背书 enquete 调查exhibition 展览会 export 出口factory visiy 工厂参观 favourable price 合宜价格foreign exchange 外汇 free on board 船上交货价idea price 希望价格 import 进口Japanese Industrial 日本工业规格 invoice 发票L/C 信用状 margin 利润market 市价 net weight 净重no payment 拒绝付款 odd item 零头offer 报价 open account 交互计算order 订单 over looked 疏漏packing 包装 pamphlet 小册子partial shipment 分批装船 patent 专利paying price 合算价格 payment method 付款方式port of destination 目地港 port of trans-shipment转口港price 价格 price decending 减价price rising 涨价 procurement 采办prompt delivery 即时交货 purchase 购入purchasing agent 采购代理商 quotation 报价单rebate 回扣 reference 查询remittance 汇款 repeat order 追加订货request letter 请求函 rumor 风评second hand goods 二手货 shipper 货主shipping 装船 shipping mark 麦头shipment 出货 sold out 卖完sole agent 总代理商 special discount 特别折扣specification 规格 sample order 指样订货standing 信用情形 storage charge 仓租subcontract 外包 subject to final confirmation 有待确认之报价supplier 供应商 T/T 电汇tie-in sale 搭售 trade fair 商展会trans-shipment 转运 transferred 已转运wharf 码头。
【机械类文献翻译】冲压变形

英文原文Categories of stamping formingMany deformation processes can be done by stamping, the basic processes of the stamping can be divided into two kinds: cutting and forming.Cutting is a shearing process that one part of the blank is cut form the other .It mainly includes blanking, punching, trimming, parting and shaving, where punching and blanking are the most widely used. Forming is a process that one part of the blank has some displacement form the other. It mainly includes deep drawing, bending, local forming, bulging, flanging, necking, sizing and spinning.In substance, stamping forming is such that the plastic deformation occurs in the deformation zone of the stamping blank caused by the external force. The stress state and deformation characteristic of the deformation zone are the basic factors to decide the properties of the stamping forming. Based on the stress state and deformation characteristics of the deformation zone, the forming methods can be divided into several categories with the same forming properties and to be studied systematically.The deformation zone in almost all types of stamping forming is in the plane stress state. Usually there is no force or only small force applied on the blank surface. When it is assumed that the stress perpendicular to the blank surface equal to zero, two principal stresses perpendicular to each other and act on the blank surface produce the plastic deformation of the material. Due to the small thickness of the blank, it is assumed approximately that the two principal stresses distribute uniformly along the thickness direction. Based on this analysis, the stress state and the deformation characteristics of the deformation zone in all kind of stamping forming can be denoted by the point in the coordinates of the plane principal stress(diagram of the stamping stress) and the coordinates of the corresponding plane principal stains (diagram of the stamping strain). The different points in the figures of the stamping stress and strain possess different stress state and deformation characteristics.(1)When the deformation zone of the stamping blank is subjected toplanetensile stresses, it can be divided into two cases, that is σγ>σθ>0,σt=0andσθ>σγ>0,σt=0.In both cases, the stress with the maximum absolute value is always a tensile stress. These two cases are analyzed respectively as follows.2)In the case that σγ>σθ>0andσt=0, according to the integral theory, the relationships between stresses and strains are:εγ/(σγ-σm)=εθ/(σθ-σm)=εt/(σt -σm)=k 1.1where, εγ,εθ,εt are the principal strains of the radial, tangential and thickness directions of the axial symmetrical stamping forming; σγ,σθand σt are the principal stresses of the radial, tangentialand thickness directions of the axial symmetrical stamping forming;σm is the average stress,σm=(σγ+σθ+σt)/3; k is a constant.In plane stress state, Equation 1.13εγ/(2σγ-σθ)=3εθ/(2σθ-σt)=3εt/[-(σt+σθ)]=k 1.2Since σγ>σθ>0,so 2σγ-σθ>0 and εθ>0.It indicates that in plane stress state with two axial tensile stresses, if the tensile stress with the maximum absolute value is σγ, the principal strain in this direction must be positive, that is, the deformation belongs to tensile forming.In addition, because σγ>σθ>0,therefore -(σt+σθ)<0 and εt<0. The strain in the thickness direction of the blankεt is negative, that is, the deformation belongs to compressive forming, and the thickness decreases.The deformation condition in the tangential direction depends on the values ofσγand σθ. When σγ=2σθ,εθ=0;when σγ>2σθ,εθ<0;and when σγ<2σθ,εθ>0.The range of σθis σγ>=σθ>=0 . In the equibiaxial tensile stress state σγ=σθ,according to Equation 1.2,εγ=εθ>0 and εt<0 . In the uniaxial tensile stress stateσθ=0,according to Equation 1.2 εθ=-εγ/2.According to above analysis, it is known that this kind of deformation condition is in the region AON of the diagram of the diagram of the stamping strain (see Fig .1.1), and in the region GOH of the diagram of the stamping stress (see Fig.1.2).2)When σθ>σγ>0 and σt=0, according to Equation 1.2 , 2σθ>σγ>0 and εθ>0,This result shows that for t he plane stress state with two tensile stresses, when the absoluste value of σθ is the strain in this direction must be positive, that is, it must be in the state of tensile forming.Also becauseσγ>σθ>0,therefore -(σt+σθ)<0 and εt<0. The strain in the thickness direction of the blankεt is negative, or in the state of compressive forming, and the thickness decreases.The deformation condition in the radial direction depends on the values ofσγand σθ. When σθ=2σγ,εγ0;when σθ>σγ,εγ<0;and when σθ<2σγ,εγ>0.The range of σγis σθ>= σγ>=0 .When σγ=σθ,εγ=εθ>0, that is, in equibiaxial tensile stress state, the tensile deformation with the same values occurs in the two tensile stress directions; when σγ=0, εγ=-εθ /2, that is, in uniaxial tensile stress state, the deformation characteristic in this case is the same as that of the ordinary uniaxial tensile.This kind of deformation is in the region AON of the diagram of the stamping strain (see Fig.1.1), and in the region GOH of the diagram of the stamping stress (see Fig.1.2).Between above two cases of stamping deformation, the properties ofσθandσγ, and the deformation caused by them are the same, only the direction of the maximum stress is different. These two deformations are same for isotropic homogeneous material.(1)When the deformation zone of stamping blank is subjected to two compressive stressesσγandσθ(σt=0), it can also be divided into two cases, which are σγ<σθ<0,σt=0 and σθ<σγ<0,σt=0.1)When σγ<σθ<0 and σt=0, according to Equation 1.2, 2σγ-σθ<0与εγ=0.This result showsthat in the plane stress state with two compressive stresses, if the stress with the maximum absolute value is σγ<0, the strain in this direction must be negative, that is, in the state of compressive forming.Also because σγ<σθ<0, therefore -(σt+σθ)>0 and εt>0.The strain in the thickness direction of the blankεt is positive, and the thickness increases.The deformation condition in the tangential direction depends on the values ofσγand σθ.When σγ=2σθ,εθ=0;when σγ>2σθ,εθ<0;and when σγ<2σθ,εθ>0.The r ange of σθis σγ<σθ<0.When σγ=σθ,it is in equibiaxial tensile stress state, henceεγ=εθ<0; when σθ=0,it is in uniaxial tensile stress state, hence εθ=-εγ/2.This kind of deformation condition is in the region EOG of the diagram of the stamping strain (see Fig.1.1), and in the region COD of the diagram of the stamping stress (see Fig.1.2).2)When σθ<σγ<0and σt=0, according to Equation 1.2,2σθ-σγ<0 and εθ<0. This result shows that in the plane stress state with two compressive stresses, if the stress with the maximum absolute value is σθ, the strain in this direction must be negative, that is, in the state of compressive forming.Also becauseσθ<σγ <0 , therefore -(σt+σθ)>0 and εt>0.The strain in the thickness direction of the blankεt is positive, and the thickness increases.The deformation condition in the radial direction depends on the values ofσγand σθ. When σθ=2σγ, εγ=0; when σθ>2σγ,εγ<0; and when σθ<2σγ,εγ>0.The range of σγis σθ<= σγ<=0 . When σγ=σθ , it is in equibiaxial tensile stress state, hence εγ=εθ<0; when σγ=0, it is in uniaxial tensile stress state, hence εγ=-εθ/2>0.This kind of deformation is in the region GOL of the diagram of the stamping strain (see Fig.1.1), and in the region DOE of the diagram of the stamping stress (see Fig.1.2).(3) The deformation zone of the stamping blank is subjected to two stresses with opposite signs, and the absolute value of the tensile stress is larger than that of the compressive stress. There exist two cases to be analyzed as follow:1)When σγ>0, σθ<0 an d |σγ|>|σθ|, according to Equation 1.2, 2σγ-σθ>0 and εγ>0.This result shows that in the plane stress state with opposite signs, if the stress with the maximum absolute value is tensile, the strain in the maximum stress direction is positive, that is, in the state of tensile forming.Also because σγ>0, σθ<0 and |σγ|>|σθ|, therefore εθ<0. The strain in the compressive stress direction is negative, that is, in the state of compressive forming.The range of σθis 0>=σθ>=-σγ. When σθ=-σγ, then εγ>0,εθ<0 , and |εγ|=|εθ|;when σθ=0, then εγ>0,εθ<0, and εθ=-εγ/2, it is the uniaxial tensile stress state. This kind of deformation condition is in the region MON of the diagram of the stamping strain (see Fig.1.1), and in the region FOG of the diagram of the stamping stress (see Fig.1.2).2)When σθ>0, σγ<0,σt=0 and |σθ|>|σγ|, according to Equation 1.2, bymeans of the same analysis mentioned above, εθ>0, that is, the deformation zone is in the planestress state with opposite signs. If the stress with the maximum absolut e value is tensile stress σθ, the strain in this direction is positive, that is, in the state of tensile forming. The strain in the radial direction is negative (εγ<=0), that is, in the state of compressive forming.The range of σγis 0>=σγ>=-σθ. When σγ=-σθ, then εθ>0,εγ<0 and |εγ|=|εθ|; when σγ=0, then εθ>0,εγ<0, andεγ=-εθ /2. This kind of deformation condition is in the region COD of the diagram of the stamping strain (see Fig.1.1), and in the region AOB of the diagram of the stamping stress (see Fig.1.2).Although the expressions of these two cases are different, their deformation essences are the same.(4) The deformation zone of the stamping blank is subjected to two stresses with opposite signs, and the absolute value of the compressive stress is larger than that of the tensile stress. There exist two cases to be analyzed as follows:1)When σγ>0,σθ<0 and |σθ|>|σγ|, according to Equation 1.2, 2σθ- σγ<0 and εθ<0.This result shows that in plane stress state with opposite signs, if the stress with the maximum absolute value is compressive stress σθ, the strain in this direction is negative, or in the state of compressive forming.Also because σγ>0 and σθ<0, therefore 2σγ- σθ<0 and εγ>0. The strain in the tensile stress direction is positive, or in the state of tensile forming.The range of σγis 0>=σγ>=-σθ.When σγ=-σθ, then εγ>0,εθ<0, and εγ=-εθ;when σγ=0, then εγ>0,εθ<0, and εγ=-εθ/2. This kind of deformation is in the region LOM of the diagram of the stamping strain (see Fig.1.1), and in the region EOF of the diagram of the stamping stress (see Fig.1.2).2)When σθ>0, σγ<0 and |σγ|>|σθ|, according to Equation 1.2 and by means of the same analysis mentioned above,εγ< 0.This result shows that in plane stress state with opposite signs, if the stress with the maximum absolute value is compressive stress σγ,the strain in this direction is negative, or in the state of compressive forming, The strain in the tensile stress direction is positive, or in the state of tensile forming.The range of σθis 0>=σθ>=-σγ.When σθ=-σγ, then εθ>0,εγ<0, and εθ=-εγ;when σθ=0, then εθ>0,εγ<0, and εθ=-εγ/2. Such deformation is in the region DOF of the diagram of the stamping strain (see Fig.1.1), and in the region BOC of the diagram of the stamping stress (see Fig.1.2).The four deformation conditions are related to the corresponding stamping forming methods. Their relationships are labeled with letters in Fig.1.1 and Fig.1.2.The four deformation conditions analyzed above are applicable to all kinds of plane stress states, that is, the four deformation conditions can sum up all kinds of stamping forming in to two types, tensile and compressive. When the stress with the maximum absolute value in the deformation zone of the stamping blank is tensile, the deformation along this stress direction must be tensile. Such stamping deformation is called tensile forming. Based on above analysis, the tensile forming occupies five regions MON, AON, AOB, BOC and COD in the diagram of thestamping stain; and four regions FOG, GOH, AOH and AOB in the diagram of the stamping stress.When the stress with the maximum absolute value in the deformation zone of the stamping blank is compressive, the deformation along this stress direction must be compressive. Such stamping deformation is called compressive forming. Based on above analysis, the compressive forming occupies five regions LOM, HOL, GOH, FOG and DOF in the diagram of the stamping strain; and four regions EOF, DOE, COD and BOC in the diagram of the stamping stress.MD and FB are the boundaries of the two types of forming in the diagrams of the stamping strain and stress respectively. The tensile forming is located in the top right of the boundary, and the compressive forming is located in the bottom left of the boundary.Because the stress produced by the plastic deformation of the material is related to the strain caused by the stress, there also exist certain relationships between the diagrams of the stamping stress and strain. There are corresponding locations in the diagrams of the stamping stress and strain for every stamping deformation. According to the state of stress or strain in the deformation zone of the forming blank, and using the boundary line in the diagram of the stamping stress MD or the boundary line in the diagram of the stamping strain FB, it is easy to know the properties and characteristics of the stamping forming.The locations in the diagrams of the stamping stress and strain for various stress states and the corresponding relationships of the two diagrams are listed in Table 1.1.It shows that the geometrical location for every region are different in the diagrams of the stamping stress and strain, but their sequences in the two diagrams are the same. One key point is that the boundary line between the tensile and the compressive forming is an inclined line at 45°to the coordinate axis. The characteristics of the stamping technique for tensile and compressive forming are listed in Table 1.2.Table 1.2 clearly shows that in the deformation zone of the blank, the characteristics of the force and deformation, and the patterns relevant to the deformation for each stamping method are the same. Therefore, in addition to the research on the detail stamping method, it is feasible to study stamping systematically and comprehensively. The characteristic of the systematic research is to study the common principle of all different types of stamping methods. The results of the systematic research are applicable to all stamping methods. The research on the properties and limit of the sheet metal stamping has been carried out in certain extent. The contents of the research on the stamping forming limit by using systematic method are shown in Fig.1.3.Table 1.1 Comparison between states of stress and strain in stamping Table 1.2 Comparison between tensile and compressive formingFig.1.1 Diagram of stampingstraint en s i l e f o r m i n g b ul g i n g d e e p d r a w i n gf l a ng i n gc om p r e s s i v e f o r m i n g c om p r e s s i v e f o r m i n g e x p a n d i n gd e e p d r a w i n gb ul g i n g t e n s i l e f o r m i n g n e c k i n g n e c k i n g expan ding+εγ-εγ-εθ+εθπ/4π/4f l a ng i n g -σγ+σθ+σγ-σθFig.1.2 Diagram of stamping stress机械专业中英文文献翻译Tensile forming Compressionforming Strength Capability of anti-wrinkle under the tensile and compressive stresses PlasticityCapability ofanti-neckingDeformationuniformity andextensioncapabilityPlasticityCapability ofanti-wrinkleDeformationforce and itsAnisotropy value of rHardening characteristicsDeformation resistanceChemistry componentStructureDeformation conditionsHardening characteristicsState of stressGradient of strainHardening characteristicsDie shapeMechanical proertyThe value of the n and rRelative thicknessChemistry componentStructureDeformation conditionsFig.1.3 Examples for systematic research methods中文译文冲压变形冲压变形工艺可完成多种工序,其基本工序可分为分离工序和变形工序两大类。
【机械类文献翻译】冲压成形特点与板材冲压成形性能

Characteristics of Stamping and Properties of Sheet MetalFormingStamping is a kind of plastic forming process in which a part is produced by means of the plastic forming of the material under the action of a die.Stamping is usually carried out under cold state,so it is also called cold stamping.Heat stamping is used only when the blank thickness is greater than 8~1 00mm.The blank material for stamping is usually in the from sheet or strip,and therefore it is also called sheet metal forming.Some non—metal sheets(such as plywood,mica sheet,asbestos,leather)can also be formed by stamping.Stamping is widely used in various of the metalworking industry, and it plays a crucial role in the industries for manufacturing automobiles, instruments,military parts and household electrical appliances,etc.The process,equipment and die are the three foundational problems that needed t0 be studied in stamping.The characteristics of the sheet metal forming are as follows:(1)High material utilization.(2)Capacity to produce thin—walled parts of complex shape.(3)Good interchangeability between stamping parts due to precision in shape and dimension.(4)Parts with lightweight,high—strength and fine rigidity can be obtained.(5)High productivity,easy to operate and to realize mechanization and automatizationThe manufacture of the stamping die is costly,and therefore it only fits t0 mass production.For the manufacture of products in small batch and rich variety,the simple stamping die and the new equipment such as a stamping machining center,are usually adopted to meet he market demands.The materials for sheet metal stamping include mi ld steel,copper,aluminum,magnesium alloy and high-plasticity alloy—steel,etc.Stamping equipment includes plate shear and punching press.The former shears plate into strips with a definite width,which would be pressed later.The later can be used both in shearing and forming.1.1 Characteristics of stamping formingThere are various processes of stamping forming with different working patterns and names.But these processes are similar to each other in plastic deformation.There are following conspicuous characteristics in stamping:(1)The force per unit area perpendicular to the blank surface is not large but is enough tocause the material plastic deformation.I t is much less than the inner stresses on the plate plane directions.In most cases stamping forming can be treated approximately as that of the plane stress state to simplify vastly the theoretical analysis and the calculation of the process parameters.(2)Due to the small relative thickness,the anti-instability capability of the blank is weak under compressive stress.As a result,the stamping process is difficult to proceed successfully without using the anti-instability device(such as blank holder).Therefore the variety of the stamping processes dominated by tensile stress are more than those dominated by compressive stress.(3)During stamping forming,the Inner stress of the blank is equal to or sometimes less than the yield stress of the material.In this point,the stamping is different from the bulk forming.During stamping forming,the influence of the hydrostatic pressure of the stress state in the deformation zone to the forming limit and the def6nmation resistance is not so important as to the bulk forming.In some circumstances,such influence may be neglected.Even in the case when this influence should be considered,the treating meth()d is also different from that of bulk forming.(4)In stamping forming,the restrain action of the die to the blank is not severe as in the case of the bulk forming(such as die forging).In bulk forming,the constraint forming is proceeded by the die with exactly the same shape of the part.Whereas in stamping,in most cases,the blank has a certain degree of freedom,only one surface of the blank contacts with the die.In some extra cases,such as the forming of the suspended region of sphere or cone,and curling at the end of tube,neither sides of the blank on the deforming zone con-tact with the die.The deformation in these regions are caused and controlled the die applying an external force to its adjacent area.Due to the characteristics of stamping deformation and mechanics mentioned above,the stamping technique is different from the bulk metal forming:(1)The importance of the strength and rigidity of the die in stamping forming is less than that in bulk forming because the blank can be formed without applying large pressure unit area on its surface.Instead,the techniques of the simple die and the pneumatic and hydraulic forming are developed.(2)Due to the plane stress or simple strain state in comparison with bulk forming,more research on deformation or force and power parameters has been done.Stamping forming can be performed by more reasonable scientific methods.Based on the real time measurement and analysis on the sheet metal properties and stamping parameters.by means of computer and some modem testing apparatus research on the intellectualized control of stamping process isalso in proceeding .(3)It is shown that there is a close relationship between stamping forming and raw material-The research on the properties of the stamping forming ,that is ,forming ab1ityand shape stability .has become a key point in stamping technology .The research on the properties of the sheet metal stamping not only meets the need of the stamping technology development ,but also enhances the manufacturing technique of iron and steel industry 。
冲压模具成型外文翻译参考文献
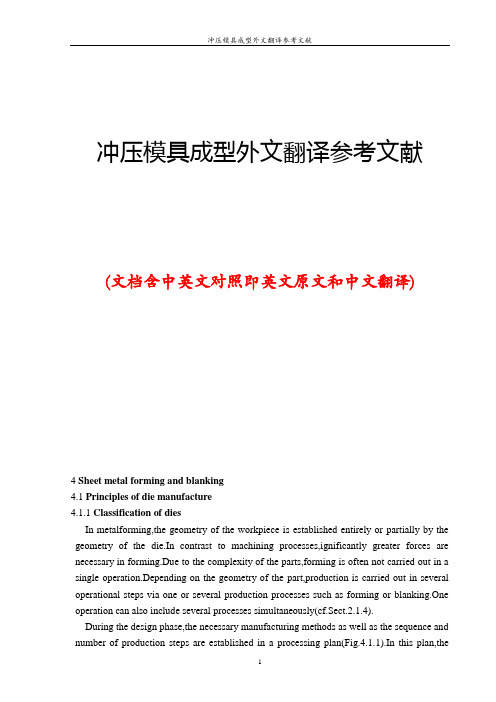
冲压模具成型外文翻译参考文献(文档含中英文对照即英文原文和中文翻译)4 Sheet metal forming and blanking4.1 Principles of die manufacture4.1.1 Classification of diesIn metalforming,the geometry of the workpiece is established entirely or partially by the geometry of the die.In contrast to machining processes,ignificantly greater forces are necessary in forming.Due to the complexity of the parts,forming is often not carried out in a single operation.Depending on the geometry of the part,production is carried out in several operational steps via one or several production processes such as forming or blanking.One operation can also include several processes simultaneously(cf.Sect.2.1.4).During the design phase,the necessary manufacturing methods as well as the sequence and number of production steps are established in a processing plan(Fig.4.1.1).In this plan,theavailability of machines,the planned production volumes of the part and other boundary conditions are taken into account.The aim is to minimize the number of dies to be used while keeping up a high level of operational reliability.The parts are greatly simplified right from their design stage by close collaboration between the Part Design and Production Departments in order to enable several forming and related blanking processes to be carried out in one forming station.Obviously,the more operations which are integrated into a single die,the more complex the structure of the die becomes.The consequences are higher costs,a decrease in output and a lower reliability.Fig.4.1.1 Production steps for the manufacture of an oil sumpTypes of diesThe type of die and the closely related transportation of the part between dies is determined in accordance with the forming procedure,the size of the part in question and the production volume of parts to be produced.The production of large sheet metal parts is carried out almost exclusively using single sets of dies.Typical parts can be found in automotive manufacture,the domestic appliance industry and radiator production.Suitable transfer systems,for example vacuum suction systems,allow the installation of double-action dies in a sufficiently large mounting area.In this way,for example,the right and left doors of a car can be formed jointly in one working stroke(cf.Fig.4.4.34).Large size single dies are installed in large presses.The transportation of the parts from oneforming station to another is carried out mechanically.In a press line with single presses installed one behind the other,feeders or robots can be used(cf.Fig.4.4.20 to 4.4.22),whilst in large-panel transfer presses,systems equipped with gripper rails(cf.Fig.4.4.29)or crossbar suction systems(cf.Fig.4.4.34)are used to transfer the parts.Transfer dies are used for the production of high volumes of smaller and medium size parts(Fig.4.1.2).They consist of several single dies,which are mounted on a common base plate.The sheet metal is fed through mostly in blank form and also transported individually from die to die.If this part transportation is automated,the press is called a transfer press.The largest transfer dies are used together with single dies in large-panel transfer presses(cf.Fig.4.4.32).In progressive dies,also known as progressive blanking dies,sheet metal parts are blanked in several stages;generally speaking no actual forming operation takes place.The sheet metal is fed from a coil or in the form of metal ing an appropriate arrangement of the blanks within the available width of the sheet metal,an optimal material usage is ensured(cf.Fig.4.5.2 to 4.5.5). The workpiece remains fixed to the strip skeleton up until the laFig.4.1.2 Transfer die set for the production of an automatic transmission for an automotive application-st operation.The parts are transferred when the entire strip is shifted further in the work flow direction after the blanking operation.The length of the shift is equal to the center line spacing of the dies and it is also called the step width.Side shears,very precise feeding devices or pilot pins ensure feed-related part accuracy.In the final production operation,the finished part,i.e.the last part in the sequence,is disconnected from the skeleton.A field of application for progressive blanking tools is,for example,in the production of metal rotors or stator blanks for electric motors(cf.Fig.4.6.11 and 4.6.20).In progressive compound dies smaller formed parts are produced in several sequential operations.In contrast to progressive dies,not only blanking but also forming operations areperformed.However, the workpiece also remains in the skeleton up to the last operation(Fig.4.1.3 and cf.Fig.4.7.2).Due to the height of the parts,the metal strip must be raised up,generally using lifting edges or similar lifting devices in order to allow the strip metal to be transported mechanically.Pressed metal parts which cannot be produced within a metal strip because of their geometrical dimensions are alternatively produced on transfer sets.Fig.4.1.3 Reinforcing part of a car produced in a strip by a compound die setNext to the dies already mentioned,a series of special dies are available for special individual applications.These dies are,as a rule,used separately.Special operations make it possible,however,for special dies to be integrated into an operational Sequence.Thus,for example,in flanging dies several metal parts can be joined together positively through the bending of certain metal sections(Fig.4.1.4and cf.Fig.2.1.34).During this operation reinforcing parts,glue or other components can be introduced.Other special dies locate special connecting elements directly into the press.Sorting and positioning elements,for example,bring stamping nuts synchronised with the press cycles into the correct position so that the punch heads can join them with the sheet metal part(Fig.4.1.5).If there is sufficient space available,forming and blanking operations can be carried out on the same die.Further examples include bending,collar-forming,stamping,fine blanking,wobble blanking and welding operations(cf.Fig.4.7.14 and4.7.15).Fig.4.1.4 A hemming dieFig.4.1.5 A pressed part with an integrated punched nut4.1.2 Die developmentTraditionally the business of die engineering has been influenced by the automotive industry.The following observations about the die development are mostly related to body panel die construction.Essential statements are,however,made in a fundamental context,so that they are applicable to all areas involved with the production of sheet-metal forming and blanking dies.Timing cycle for a mass produced car body panelUntil the end of the 1980s some car models were still being produced for six to eight years more or less unchanged or in slightly modified form.Today,however,production time cycles are set for only five years or less(Fig.4.1.6).Following the new different model policy,the demands ondie makers have also changed prehensive contracts of much greater scope such as Simultaneous Engineering(SE)contracts are becoming increasingly common.As a result,the die maker is often involved at the initial development phase of the metal part as well as in the planning phase for the production process.Therefore,a muchbroader involvement is established well before the actual die development is initiated.Fig.4.1.6 Time schedule for a mass produced car body panelThe timetable of an SE projectWithin the context of the production process for car body panels,only a minimal amount of time is allocated to allow for the manufacture of the dies.With large scale dies there is a run-up period of about 10 months in which design and die try-out are included.In complex SE projects,which have to be completed in 1.5 to 2 years,parallel tasks must be carried out.Furthermore,additional resources must be provided before and after delivery of the dies.These short periods call for pre-cise planning,specific know-how,available capacity and the use of the latest technological and communications systems.The timetable shows the individual activities during the manufacturing of the dies for the production of the sheet metal parts(Fig.4.1.7).The time phases for large scale dies are more or less similar so that this timetable can be considered to be valid in general.Data record and part drawingThe data record and the part drawing serve as the basis for all subsequent processing steps.They describe all the details of the parts to be produced. The information given in theFig.4.1.7 Timetable for an SE projectpart drawing includes: part identification,part numbering,sheet metal thickness,sheet metal quality,tolerances of the finished part etc.(cf.Fig.4.7.17).To avoid the production of physical models(master patterns),the CAD data should describe the geometry of the part completely by means of line,surface or volume models.As a general rule,high quality surface data with a completely filleted and closed surface geometry must be made available to all the participants in a project as early as possible.Process plan and draw developmentThe process plan,which means the operational sequence to be followed in the production of the sheet metal component,is developed from the data record of the finished part(cf.Fig.4.1.1).Already at this point in time,various boundary conditions must be taken into account:the sheet metal material,the press to be used,transfer of the parts into the press,the transportation of scrap materials,the undercuts as well as thesliding pin installations and their adjustment.The draw development,i.e.the computer aided design and layout of the blank holder area of the part in the first forming stage–if need bealso the second stage–,requires a process planner with considerable experience(Fig.4.1.8).In order to recognize and avoid problems in areas which are difficult to draw,it is necessary to manufacture a physical analysis model of the draw development.With this model,theforming conditions of the drawn part can be reviewed and final modifications introduced,which are eventually incorporated into the data record(Fig.4.1.9).This process is being replaced to some extent by intelligent simulation methods,through which the potential defects of the formed component can be predicted and analysed interactively on the computer display.Die designAfter release of the process plan and draw development and the press,the design of the die can be started.As a rule,at this stage,the standards and manufacturing specifications required by the client must be considered.Thus,it is possible to obtain a unified die design and to consider the particular requests of the customer related to warehousing of standard,replacement and wear parts.Many dies need to be designed so that they can be installed in different types of presses.Dies are frequently installed both in a production press as well as in two different separate back-up presses.In this context,the layout of the die clamping elements,pressure pins and scrap disposal channels on different presses must be taken into account.Furthermore,it must be noted that drawing dies working in a single-action press may be installed in a double-action press(cf.Sect.3.1.3 and Fig.4.1.16).Fig.4.1.8 CAD data record for a draw developmentIn the design and sizing of the die,it is particularly important to consider the freedom of movement of the gripper rail and the crossbar transfer elements(cf.Sect.4.1.6).These describe the relative movements between the components of the press transfer system and the die components during a complete press working stroke.The lifting movement of the press slide,the opening and closing movements of the gripper rails and the lengthwise movement of the whole transfer are all superimposed.The dies are designed so that collisions are avoided and a minimum clearance of about 20 mm is set between all the moving parts.4 金属板料的成形及冲裁4. 模具制造原理4.1.1模具的分类在金属成形的过程中,工件的几何形状完全或部分建立在模具几何形状的基础上的。
【机械类文献翻译】冲压模具的受力分析

英文原文Stress Analysis of Stamping DiesJ. Mater. Shaping Technoi. (1990) 8:17-22 9 1990 Springer-Verlag New York Inc.R . S . R a oAbstract:Experimental and computational procedures for studying deflections, flit, andalignment characteristics of a sequence of stamping dies, housed in a transfer press, are pre-sented. Die loads are actually measured at all the 12 die stations using new load monitors and used as input to the computational procedure. A typical stamping die is analyzed using a computational code, MSC/NASTRAN, based on finite element method. The analysis is then extended to the other dies, especially the ones where the loads are high. Stresses and deflections are evaluated in the dies for the symmetric and asymmetric loading conditions. Based on our independent die analysis, stresses and deflections are found to be reasonably well within the tolerable limits. However, this situation could change when the stamping dies are eventually integrated with the press as a total system which is the ultimate goal of this broad research program.INTRODUCTIONSheet metal parts require a series of operations such as shearing , drawing , stretching , bending , and squeezing. All these operations are carried out at once while the double slide mechanism descends to work on the parts in the die stations, housed in a transfer press [1]. Material is fed to the press as blanks from a stock feeder. In operation the stock is moved from one station to the next by a mechanism synchronized with the motion of the slide. Each die is a separate unit which may be independently adjusted from the main slide. An automotive part stamped from a hot rolled steel blank in 12 steps without any intermediate anneals is shown in Figure 1.Transfer presses are mainly used to produce different types of automotive and aircraft parts and home appliances. The economic use of transfer presses depends upon quantity production as their usual production rate is 500 to 1500 parts per hour [2]. Although production is rapid in this way, close tolerances are often difficult to achieve. Moreover, the presses produce a set of conditions for off-center loads owing to the different operations being performed simultaneously in several dies during each stroke. Thus, the forming load applied at one station can affect the alignment and general accuracy of the operation being performed at adjacent stations. Another practical problem is the significant amount of set-up time involved to bring all the dies into proper operation. Hence, the broad goal of this research is to study the structural characteristics of press and dies combination as a total system. In this paper, experimental and computational procedures for investigating die problems are presented. The analysis of structural characteristics of the transfer press was pursued separately [3].A transfer press consisting of 12 die stations was chosen for analysis. Typical die problems are excessive deflections, tilt, and misalignment of the upperand lower die halves. Inadequate cushioning and offcenter loading may cause tilt and misalignment of the dies. Tilt and excessive deflections may also be caused by the lack of stiffness of the die bolster and the die itself. Part quality can be greatly affected by these die problems. There are a lot of other parameters such as the die design, friction and lubrication along the die work interface, speed, etc. that play a great role in producing consistently good parts. Realistically, the analysis should be carded out by incorporating the die design and the deforming characteristics of the work material such as the elastic-plastic work hardening properties. In this preliminary study, the large plastic deformation of the workpiece was not considered for the reasons mentioned below.Large deformation modeling of a sheet stretching process was carded out using the computational code based on an elastic-plastic work hardening model of the deformation process [4]. Laboratory experiments were conducted on various commercial materials using a hemispherical punch. The coefficient of friction along the punch-sheet interface was actually measured in the experiment and used as a prescribed boundary to the numerical model. Although a good solution was obtained, it was realized that the numerical analysis was very sensitive to the frictional conditions along the interface. In the most recent work, a new friction model based on the micromechanics of the asperity contact was developed [5]. In the present problem, there are several operations such as deep drawing, several reduction drawing operations, and coining, which are performed using complex die geometries. The resources and the duration of time were not adequate to study these nonlinear problems. Hence,the preliminary study was limited to die problems basedon linear stress analysis.A detailed die analysis was carried out by using MSC /NASTRAN code based on finite ele mentmethod. Die loads were.measured at all the stations using new load monitors. Such measured data were used in the numerical model to evaluate stresses and deflections in the dies for normal operating conditions and for asymmetric loading conditions. Asymmetric loading conditions were created in the analysis by tilting the dies. In real practice, it is customary to pursue trial-and-error procedures such as placing shims under the die or by adjusting the cushion pressure to correct the die alignment problems. Such time consuming tasks can be reduced or even eliminated using the computational and experimental procedures presented here.DIE GEOMETRY AND MATERIALSThe design of metal stamping dies is an inexact process. There are considerable trial-and-error adjustments during die tryout that are often required to finish the fabrication of a die that will produce acceptable parts. It involves not only the proper selection of die materials, but also dimensions. In order to withstand the pressure, a die must have proper cross-sectional area and clearances. Sharp comers, radii, fillets, and sudden changes in the cross section can have deleterious effects on the die life. In this work, the analysis was done on the existing set of dies.The dies were made of high carbon, high chromium tool steel. The hardness of this tool steel material is in the range of Rockwell C 57 to 60. Resistance to wear and galling was greatly improved by coating the dies with titanium nitride and titanium carbide. The dies were supported by several other steel holders made of alloy steels such as SAE 4140. The geometry of a typical stamping die is axisymmetric but it varies slightly from die to die depending on the operation. Detailed information about geometry andmaterials of a reduction drawing die (station number 4) was gathered from blueprints. It was reproducedin three-dimensional geometry using a preprocessor, PATRAN. One quadrant of the die is shown in Figure2. The data including geometry and elastic properties of the die material were fed to the numerical model.The work material used was hot rolled aluminumkilled steel, SAE 1008 A-K Steel and the blank thickness was about 4.5 ram. Stampings used in unexposed places or as parts of some deisgn where fine finish is not essential are usually made from hot rolled steel. The automotive part produced in this die set is a cover for a torque converter. A principal advantage of aluminum-killed steel is its minimum strain aging. EXPERIMENTAL PROCEDURESAs mentioned earlier, this research involved monitoting of die loads which were to be used in the numerical model to staldy the structural characteristicsof dies. The other advantage is to avoid overloadingthe dies in practice. Off-center loading can be detected and also set-up time can be reduced. Thus, any changes in the thickness of stock, dulling of the die,unbalanced loads, or overloadings can be detected using die load monitors.Strain gage based fiat load cells made of high grade tool steel material werefabricated and supplied by IDC Corporation. Four identical load cells were embedded in a thick rectangular plate as shown in Figure 3. They were calibrated both in the laboratory and in the plant.The plate was placed on the top of the die. The knockout pin slips through the hole in the plate. Six such plates were placed on each of six dies. In this way,24 readings can be obtained at a given time. Then they were shifted to the other six dies for complete data. All the 12 die loads are presented in Table 1.COMPUTATIONAL PROCEDURESLinear static analysis using finite element method wasused to study the effect of symmetric and asymmetric loading for this problem. A finite element model of diestation 4 was created using the graphical preprocessor, PATRAN, and the analysis was carried outusing the code MSC/NASTRA N . The code has a wideT a b l e I. Die LoadsDie Station LoadNumber (kN)1 3562 6413 2144 3565 8546 7127 2858 32O9 234910 113911 21412 2100spectrum of capabilities, of which linear static analysis is discussed here.The NASTRAN code initially generates a structural matrix and then the stiffness and the mass matrices from the data in the input file. The theoretical formulations of a static structural problem by the displacement method can be obtained from the references [6]. The unknowns are displacements and are solved for the appropriate boundary conditions. Strains are obtained from displacements. Then they are converted into stresses by using elastic stress-strain relationships of the die material.The solution procedure began with the creation of die geometry using the graphical preprocessor, PATRAN. The solution domain was divided into appropriate hyper-patches. This was followed by the generation of nodes, which were then connected by elements. Solid HEXA elements with eight nodes were used for this problem. The nodes and elements were distributed in such a way that a finer mesh was created at the critical region of the die-sheet metal interface and a coarser mesh elsewhere. The model was then optimized by deleting the unwanted nodes. The element connectivities were checked. By taking advantage of the symmetry, only one quarter of the die was analyzed. In the asymmetric case, half of the die was considered for analysis. Although, in practice, the load is applied at the top of the die, for the purpose of proper representation of the boundary conditions to the computational code, reaction forces were considered for analysis. The displacement and force boundary conditions are shown for the two cases inFigure 4.As mentioned earlier, sheet metal was not modeled in this preliminary research.As shown in Figure 4(a),the nodes on the top surface of the die were constrained (stationary surface) and the measured load of 356 kN was equally distributed on the contact nodes at the workpiece die interface. Similar boundary conditions for the punch are shown in Figure 4(b). It is noticeable that fewer nodes are in contact with the sheet metal due to the die tilt for the asymmetric loading case as shown in Figure 4(c). In real practice, the pressure actually varies along the die contact surface. Since the actual distribution was not known, uniform distribution was considered in the present analysis.DISCUSSION OF RESULTSAs described in the earlier section, the numerical analysis of die Station 4 (both the die and punch) was performed using the code MSC/NASTRAN . Two cases were considered, namely: (a) symmetric loading and (b) asymmetric loadingFig. 4. Boundary conditions. (A) Symmetric case (onequadrant of the die). (B) Symmetric case (one quadrant ofnthe punch). (C) Asymmetric case (half of the die). Symmetric LoadingNumerical analysis of the die was carried out for a measured load o f 356 kN as distributed equally in Figure 4(a). The major displacements in the loading direction are shown in Figure 5(a). These displacement contours can be shown in various colors to represent different magnitudes. The m aximum displacement value is 0.01 m m fora uniformly distributed load of 356 kN. The corresponding critical stress is very small,8.4 MPa in the y direction and 30 MPa in the x direction. The calculated displacements and stresses at the surrounding elements and nodes wereof the same order, but they decreased in magnitude at the nodes away from this critical region. Thus, the die was considered very rigid under this loading condition.Symmetric loading was applied to the punch and the numerical analysis was carried out separately. The displacement values in the protruding region of the punch were high compared to the die. The maximum displacement was 0.08 m m . It should be noted that the displacement values in this critical range of the punch were of the same order ranging from 0.05 mm to 0.08 ram. Although the load acting on the punch (bottom half) was the same as the die (upper half), that is, 356 kN, the values of displacements and stresses were higher in the punch because of the differences in the geometry. This is especially true for the protruding part of the punch. The corresponding maxim u m stress was 232 MPa. This part of the punch is still in the elastic range as the yield strength of tool steel is approximately 1034 MPa. The critical stress value might be varied for different load distributions. Since the actual distribution of the load was not known,the load was distributed equally on all nodes. As the die (upper half) is operating in a region which is extremely safe, a change in the load distribution may not produce any high critical stresses in the die. Although higher loads are applied at other die stations(see Table 1), it is concluded that the critical stresses are not going to be significantly higher due to the appropriate changesin the die geometries.Asymmetric LoadingFor the purpose of analysis, an asymmetric loading situation was created by tilting the die. Thus, only 15 nodes were in contact with the workpiece compared to 40 nodes for the symmetric loading case. As shown in Figure 4(c), a 356 kN load was uniformly distributed over the 15 nodes that were in contact with the workpiece. Although the pressure was high, because of the geometry at the location where the load was acting, the critical values of displacement and stress were found to be similar to the symmetric case. The predicted displacement and stress values were not significantly higher than the values predicted for the symmetric case.Fig. 5. Displacement contours in the loading direction. (A) Symmetric case (one quadrant of thedie). (B) Symmetric case (one quadrant of the punch). (C)Asymmetric case (half of the die).CONCLUSIONSIn this preliminary study, we have demonstrated the capabilities of the computational procedure, based on finite element method, to evaluate the stresses and deflections within the stamping dies for the measured loads. The dies were found to be within the tolerable elastic limits for both symmetric and asymmetric loading conditions. Thus the computational procedure can be used to study the tilt and alignment characteristics of stamping dies. In general, the die load monitors are very useful not only for analysis but also for on-line tonnage control. Future research involves theintegration of the structural analysis of stamping dies with that of the transfer press as a total system.ACKNOWLEDGMENTSProfessor J.G. Eisley, W.J. Anderson, and Mr. D.Londhe are thanked for their comments on this paper.REFERENCES1. R.S. Rao and A. Bhattacharya, "Transfer Process De-flection, Parallelism, and Alignment Characteristics,"Technical Report, January 1988, Department of Mechanical Engineering and Applied Mechanics, the University of Michigan, Ann Arbor.2. Editors of American Machinist, "Metalforming: Modem Machines, Methods, andTooling for Engineers and Operating Personnel," McGraw-Hill, Inc., 1982, pp. 47-50.3. W.J. Anderson, J.G. Eisley, and M.A. Tessmer,"Transfer Press Deflection, Parallelism, and Alignment Characteristics," Technical Report, January 1988, Department of Aerospace Engineering, the University of Michigan, Ann Arbor.4. B.B. Yoon, R.S. Rao, and N. Kikuchi, "Sheet Stretching: A Theoretical Experimental Comparison," International Journal of Mechanical Sciences, V ol. 31, No.8, pp. 579-590, 1989.5. B.B. Yoon, R.S. Rao, and N. Kikuchi, "Experimental and Numerical Comparisons of Sheet Stretching Using a New Friction Model," ASME Journal of Engineering Materials and Technology, in press.6. MSX/NASTRAN, McNeal Schwendler Corporation.22 9 J. Materials Shaping Technology, V ol. 8, No. 1, 1990。
文献翻译译文-模具的历史发展
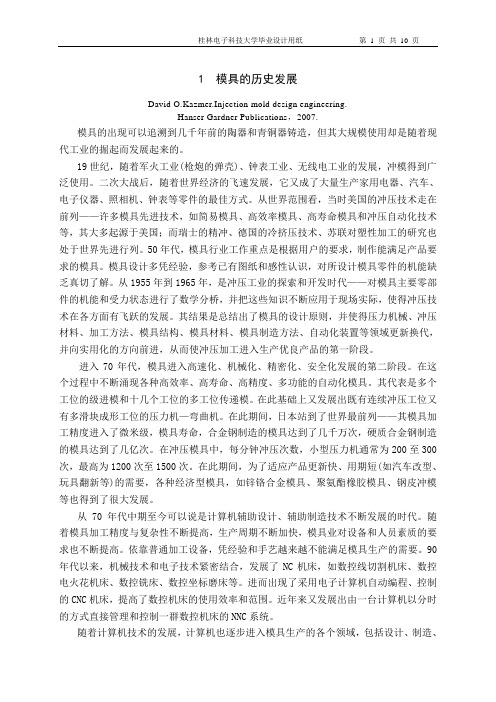
1 模具的历史发展David O.Kazmer.Injection mold design engineering.Hanser Gardner Publications,2007.模具的出现可以追溯到几千年前的陶器和青铜器铸造,但其大规模使用却是随着现代工业的掘起而发展起来的。
19世纪,随着军火工业(枪炮的弹壳)、钟表工业、无线电工业的发展,冲模得到广泛使用。
二次大战后,随着世界经济的飞速发展,它又成了大量生产家用电器、汽车、电子仪器、照相机、钟表等零件的最佳方式。
从世界范围看,当时美国的冲压技术走在前列——许多模具先进技术,如简易模具、高效率模具、高寿命模具和冲压自动化技术等,其大多起源于美国;而瑞士的精冲、德国的冷挤压技术、苏联对塑性加工的研究也处于世界先进行列。
50年代,模具行业工作重点是根据用户的要求,制作能满足产品要求的模具。
模具设计多凭经验,参考已有图纸和感性认识,对所设计模具零件的机能缺乏真切了解。
从1955年到1965年,是冲压工业的探索和开发时代——对模具主要零部件的机能和受力状态进行了数学分桥,并把这些知识不断应用于现场实际,使得冲压技术在各方面有飞跃的发展。
其结果是总结出了模具的设计原则,并使得压力机械、冲压材料、加工方法、模具结构、模具材料、模具制造方法、自动化装置等领域更新换代,并向实用化的方向前进,从而使冲压加工进入生产优良产品的第一阶段。
进入70年代,模具进入高速化、机械化、精密化、安全化发展的第二阶段。
在这个过程中不断涌现各种高效率、高寿命、高精度、多功能的自动化模具。
其代表是多个工位的级进模和十几个工位的多工位传递模。
在此基础上又发展出既有连续冲压工位又有多滑块成形工位的压力机—弯曲机。
在此期间,日本站到了世界最前列——其模具加工精度进入了微米级,模具寿命,合金钢制造的模具达到了几千万次,硬质合金钢制造的模具达到了几亿次。
在冲压模具中,每分钟冲压次数,小型压力机通常为200至300次,最高为1200次至1500次。
(完整版)冲压类外文翻译、中英文翻译冲压模具设计
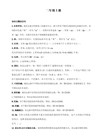
"sheet-metal forming". Sheet-metal forming ( also called stamping or pressing )is
is hard to imagine the scope and cost of these facilities without visiting an
Minimum bend radii vary for different metals, generally, different annealed metals
be bent to a radius equal to the thickness of the metal without cracking or
modes can be illustrated by considering the deformation of small sheet elements
Sheet forming a simple cup
the blank flange as it is being drawn horizontally through
Minimum bend radius for various materials at room temperature
Condition
Hard
0 6T
0 4T
0 2T
5T 13T
0.5T 6T
0.5T 4T
0.7T 3T
2.6T 4T
——thickness of material
one punch to prevent its buckling under pressure from the ram of the press.
【机械类文献翻译】冲压模具
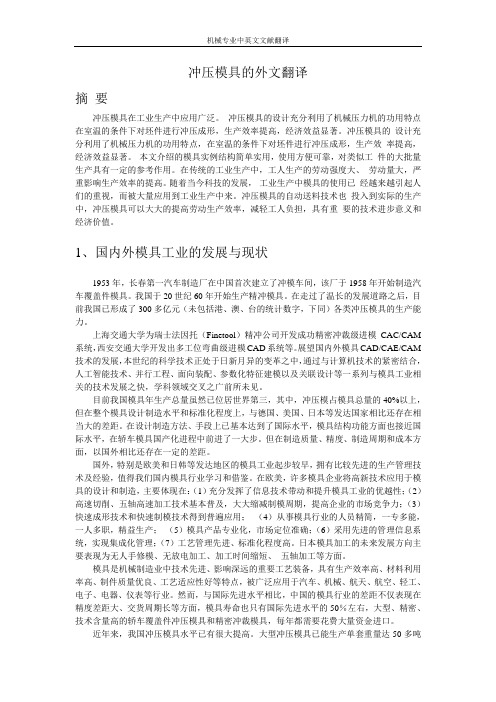
冲压模具的外文翻译摘要冲压模具在工业生产中应用广泛。
冲压模具的设计充分利用了机械压力机的功用特点在室温的条件下对坯件进行冲压成形,生产效率提高,经济效益显著。
冲压模具的设计充分利用了机械压力机的功用特点,在室温的条件下对坯件进行冲压成形,生产效率提高,经济效益显著。
本文介绍的模具实例结构简单实用,使用方便可靠,对类似工件的大批量生产具有一定的参考作用。
在传统的工业生产中,工人生产的劳动强度大、劳动量大,严重影响生产效率的提高。
随着当今科技的发展,工业生产中模具的使用已经越来越引起人们的重视,而被大量应用到工业生产中来。
冲压模具的自动送料技术也投入到实际的生产中,冲压模具可以大大的提高劳动生产效率,减轻工人负担,具有重要的技术进步意义和经济价值。
1、国内外模具工业的发展与现状1953年,长春第一汽车制造厂在中国首次建立了冲模车间,该厂于1958年开始制造汽车覆盖件模具。
我国于20世纪60年开始生产精冲模具。
在走过了温长的发展道路之后,目前我国已形成了300多亿元(未包括港、澳、台的统计数字,下同)各类冲压模具的生产能力。
上海交通大学为瑞士法因托(Finetool)精冲公司开发成功精密冲裁级进模CAC/CAM 系统,西安交通大学开发出多工位弯曲级进模CAD系统等。
展望国内外模具CAD/CAE/CAM 技术的发展,本世纪的科学技术正处于日新月异的变革之中,通过与计算机技术的紧密结合,人工智能技术、并行工程、面向装配、参数化特征建模以及关联设计等一系列与模具工业相关的技术发展之快,学科领域交叉之广前所未见。
目前我国模具年生产总量虽然已位居世界第三,其中,冲压模占模具总量的40%以上,但在整个模具设计制造水平和标准化程度上,与德国、美国、日本等发达国家相比还存在相当大的差距。
在设计制造方法、手段上已基本达到了国际水平,模具结构功能方面也接近国际水平,在轿车模具国产化进程中前进了一大步。
但在制造质量、精度、制造周期和成本方面,以国外相比还存在一定的差距。
【机械类文献翻译】冲压模具柔性设计系统的研究
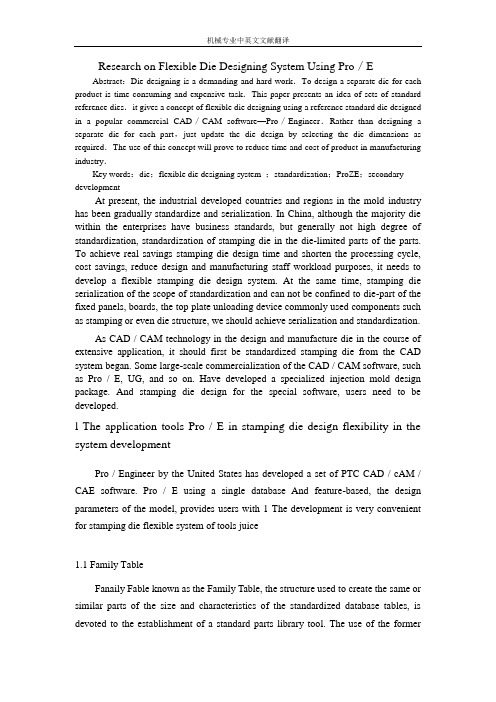
Research on Flexible Die Designing System Using Pro/EAbstract:Die designing is a demanding and hard work.To design a separate die for each product is time consuming and expensive task.This paper presents an idea of sets of standard reference dies.it gives a concept of flexible die designing using a reference standard die designed in a popular commercial CAD/CAM software—Pro/Engineer.Rather than designing a separate die for each part,just update the die design by selecting the die dimensions as required.The use of this concept will prove to reduce time and cost of product in manufacturing industry.Key words:die;flexible die designing system ;standardization;ProZE;secondary developmentAt present, the industrial developed countries and regions in the mold industry has been gradually standardize and serialization. In China, although the majority die within the enterprises have business standards, but generally not high degree of standardization, standardization of stamping die in the die-limited parts of the parts. To achieve real savings stamping die design time and shorten the processing cycle, cost savings, reduce design and manufacturing staff workload purposes, it needs to develop a flexible stamping die design system. At the same time, stamping die serialization of the scope of standardization and can not be confined to die-part of the fixed panels, boards, the top plate unloading device commonly used components such as stamping or even die structure, we should achieve serialization and standardization.As CAD / CAM technology in the design and manufacture die in the course of extensive application, it should first be standardized stamping die from the CAD system began. Some large-scale commercialization of the CAD / CAM software, such as Pro / E, UG, and so on. Have developed a specialized injection mold design package. And stamping die design for the special software, users need to be developed.l The application tools Pro / E in stamping die design flexibility in the system developmentPro / Engineer by the United States has developed a set of PTC CAD / cAM / CAE software. Pro / E using a single database And feature-based, the design parameters of the model, provides users with 1 The development is very convenient for stamping die flexible system of tools juice1.1 Family TableFanaily Fable known as the Family Table, the structure used to create the same or similar parts of the size and characteristics of the standardized database tables, is devoted to the establishment of a standard parts library tool. The use of the formerfirst family table to create a generic representation of the components (the generic), according to the need to target and then added to the family table a series of management.Family sheet management can be the object of a size (dimension), features (feature), parameters (parameter) and assembly parts (component), and so on.A family table can have multiple levels, that is a generic parts can contain multiple sub-components (instance, also known as examples), and each Instance can contain their own Sub Instance. Discharge screw (stripper-bolt) the family table structure as shown in Figure 1.Figure 1 Family Table hierarchy1.2 RelationsRelations (relations) between mathematics and procedures, including grammar, and its main role is to be part or assembly of the relevance of the data by size symbols, and other parameters of grammar (syntax) to establish mathematical formula to meet the design requirements. Pro / E system of relations can be found in Sketch, Feature, Part and in the Assembly. Simple sentence, judgement and sentence is to establish relations of common format. Simple sentence that a simple mathematical relationship between the size of direct response associated situation. The use of simple format, such as d6 = L. BP 1 2 * d3. Judgement on the sentence for certain occasions, by specifying conditions to express design intent, grammar structure: "IF… ENDIF" or "IF… ELSE… ENDIF" in the "ELSE… ENDIF" between conditional statements can be multi-nested. Relations in the standardization and flexible stamping die design system in the building process plays a very important role, it has decided to parts of the geometric shape and characteristics of relations between the digital Xiao, partsrelations between the assembly and parts assembly in the presence of middle - A number of features.1.3 Pro/ProgramPro / Program (program) is the Pro / E of a procedural tool, similar to its grammar VBA and Office software in the Macro (Acer). When users use of Pro / engineer to design .The product of various kinds of information to document the format will be recorded. Through the Pro / Progran document editing, can be achieved on the characteristics of the hide, delete and re-order the assembly of components to add and replacement operation. These features stamping dies for the establishment of standard parts library, standards and flexible design structure of the system is very useful.Program files in the structure can be broadly classified into the title, set of parameters relationship, to add features (parts) and updating the quality attributes, such as five parts. In "INPUT… END INPUT" Xiao located between the parameters of the "RE1 ATIONS… ENDREALATIONS" relations between the various add in the "ADD… END ADD" and added features (part mo dule) or parts (assembly module). Pro / Program provides three types of parameters: NUMBER (numerical) STRING (string) and YES-NO (it).2. Standards moldbase of the development2.1 Standards moldbase Classification and organizationsDie-stamping die is an important part. The typical model-there are three types: rear-guided-mode (back pillar sets), the middle-guided-mode (center pillar sets) and the guided-mode-angle (diagonal pillarsets). Each type of die-also includes a variety of specifications. According to Die boundary demarcation size, rear-guided, in a L × B-22 specifications, D0 specifications 6 (L = B), middle-guided, in the nine-D0 specifications, the guided-mode-Kok L × B specifications 7 [2-3].In order to facilitate the management and data calls, the standard mode of the directory of the best-established in the Pro / E installation directory. As three categories-the larger structural differences, it may die-the root of the establishment of three other subdirectories, each subdirectory contains all the component parts-mode, and each type of parts can be adopted Pro / E Software for the family table, and toolssuch as the establishment of standard procedures for the database.2.2 Standards moldbase library buildingDie-stamping die from the main mode on the Block (upper.shoe), nder-Block (1 ower.shoe), I. column (guide.pillar) and I. Case (guidebushing), and other components. In order to make structural integrity of mold, can also die stalk (shank) assembly to die-in. Here are rear-die I.Establishment of the standard method.First of all the various components to create three-dimensional model, and then the standard manual data in the table a series of symbolic dimension added to the group on January 1 Editor (can also use Excel for editing). Add in the size of symbols, Size will be the best symbol to revise the manual and the size of the same symbol. Because people can not distinguish between Table Capitalization is, when both the same size letters, proposed to use capital letters to distinguish between pairs of characters, such as that for the d D, and D that will become a DD.Standard on two-Block: When the L ×B> 200 mm ×160 mn-i have installed Boss, and when L × B is less than or equal to the scope of non-installation of Boss, shown in Figure 2. Determine whether Boss in two ways: one way is to use Family Table, will generate the Boss Extrude Offset two characteristics and the way to Feature added to the family table, and in these two characteristics of the list Enter in the "Y" or "N", to determine the specifications of a certain mode on the Block, whether these two features; Another method is to find these two features in the Pro / Program in the location and characteristics of the process to add Extrude His statement before the judge "IF L> 200 1 B> 160", adding the Offset characteristics of the procedures used "END IF" the end of judgement.Figure2. die on the ground in two types2.3 The establishment of Standards moldbase forIn Pro / Assembly in the same module can be generated by the use of family die-standard database. Family structure in the assembly, when selected COrnponent, select the mode of all the parts-and enter a different group in the table-model specifications required by the standards of sub-components of the name, as shown in Figure 3.Figure 3 rear-guided, in the standard mode of Family TableCommon mode handles four types: pressure-in-stalk, the flange-stalk, Screw-mode and floating stems die stalk. If the four types of module assembly to handle all the common-mode model (Figure 3 in the assembly only two kinds), in the group table by the need to enter the module handles parts of the name, set the parameters of INPUT, with Regenerate Called when the parameters of renewable order to choose the mode of different types of handles. Of course, people can also die of the table do not have to handle characters with "N" to curb, as shown in Figure 3-mode system is used in this method.3 The development of standard stamping die3.1 The typical combination of stamping dieStamping die in the larger structural differences and establish flexible stamping die design systems using the best combination of the typical mold. Use of combinations to determine the structure of the typical mold of the structure, and thus determine the composition of the various components die sizes and assembly relations. Commonly used combination of stamping die typical structure: a fixed combinationof unloading, Tanya unloading combinations, composite model portfolio, such as plate-portfolio. Mold can not be separated from the structure of ISO standardization of parts, in the Pro / Engineer Dies in the standardization of parts can be used in the design of the bottom-up approach can also be used top-down design.3.2 die in the process of assembling data transferBecause of complicated, so stamping die by the standardization of the factors to consider-Modulus than standardized by many more factors to consider, one of the most important factor is the size of the correlation between the components. In the mold of a standard combination, assembly and components, parts and components between the need for data transmission, and in the Pro / Assembly can be very easy to achieve this objective.3.2.1 by the assembly of components to the data transferPro / Program can use the assembly EXECUTE statement will be down the parameters in a sub-assembly or parts delivery, the use of syntax is as follows: EXECUTE PART / ASSEMBLY file name components or sub-assembly of the parameters in the assembly of = END EXECUTE EXECUTE statement parameters can not leapfrog data transmission, not by the assembly to sub-assembly of components in the direct transmission of data.3.2.2 data transfer between the componentsWhen added to the assembly of components are in a Id, it can complete the assembly of components between the data transfer. Id assembly of components, can be used in the menu RELATIONs Session Id command to query. Figure 4 is the combination of Tanya discharge standards in the spring of unloading assembly diagram. As assembly to die in the spring have a pre-compression and thus the length of its assembly (Hs) are no longer equal to the length of freedom (H.). In determining H, you can use the following mathematical relationship:Hs:38= L:32一tbp:0In this way can always guarantee equal to the length of spring assembly from the surface to Dianban discharge board under the surface height, thus eliminating the relevant parts were replaced after the size of Laws. In the design of this mold is very practical, because the mold assembly in a similar situation there are many. Again, in determining the discharge screw on the seat-hole diameter (dI34), they can use thefollowing mathematical relationship:d134:8=D:32+2This Id, established by the mathematical relationship between the need to use Regenerate order to take effect, so different parts on the size of the location of as little as possible in this way, so as not to die in the initial call model will appear at the wrong result will be displayed. But if the parts in between and parameters to transfer data, the location of the various components of size parameters to create a mathematical relationship, the trouble can be avoided.3.2.3 standard replacement partsFamily Table used to establish the standard parts can lookup. inst Replacement statement. Lookup inst allows users to find the standard parts that match the sub-components, if not find the results, then return to a generic [4 J.Lookup.inst :lookup inst(generic—name,match-mode,paramnamel,match—valuel,param-name2,match—value2…)One match. preferred mode of three, representing different meanings: one is to find parameters of less than or equal to find the value of components; parameter values 0 to find an exact match to find value of the sub-components; to find parameters of greater than or equal to find value The sub-components.3.3 structure of the assemblyDie parts to complete the establishment and rationalize the assembly relations between the components, you can generate mold assembly model. Figure 5 for the development of the author Tanya unloading combination of specifications for the 200 mm × 160 mm of die structure (omit all the characteristics of thread).3.4 stamping die callStamping die in the Pro / Assembly call directly, but also can be used Pro / TOOLKIT development of visual user interface to call. Pro / TOOLKIT Pro Ecuador is the second development system software package, its main purpose is to allowusers or third parties through the expansion of C code Pro / E function, based on the development of Pro / E system of application modules to meet user Special needs. Pro/T00LKIT use of the UI dialog, the menu VC + + and Visual Interface technology, designed to facilitate flexible and practical stamping die design system for interactive interface. Use interface called the structure of various stamping dies, the choice of different specifications of the parts, enter a different parameters to determine sheet parameters as well as their positioning in the mold, and further in the system design punch, die and other structures, Thus greatly enhance the efficiency of stamping die design.4 ConclusionSince stamping process a wide range of complex processes, and the shape of various parts die, stamping dies in achieving standardization and development of flexible design system and the process is very complicated, but flexible stamping die design system of stamping die CAD is to improve the level of the cornerstones . Pro / E powerful components, the assembly of the criteria for the establishment of the functions of stamping dies for the standardization and flexible design of the feasibility of developing systems to provide a strong guarantee. In the development of flexible design system, should ingenious application of Pro / E software provided by an effective tool, considering the different types of standard structural composition of the assembly relations. Between the parts and components meet requirements of size structure changes, and the best use RELATIONS Pro / Program prepared by the mathematical relations systems and procedures to increase the flexibility and practicality. Die flexible design and application development system to avoid a mold designers unnecessary duplication of labor, so that the programme will focus on the concept, process optimization, and other creative work, thus mold the rapid design and production standards have a practical application Significance.冲压模具柔性设计系统的研究摘要:冲压模具设计是一项十分复杂的工作。
冲压外文翻译---中英文对照--论文

General all—steel punching die’s punching accuracy(普通全钢冲模的冲压精度分析)作者:不详来源于:机械论文文档在线免费下载网发布时间:2009—1-2 20:04:17 General all-steel punching die’s punching accuracyAccuracy of panel punching part is display the press accuracy of the die exactly. But the accuracy of any punching parts’ linear dimension and positional accuracy almost depend on the blanking and blanking accuracy,。
So that the compound mould of compound punching's accuracy,is typicalness and representation in the majority。
Analyse of the die's accuracyFor the analyse of pracyicable inaccuracy during production of dies to inactivation, we could get the tendency when it is augmentation in most time. From this we could analyse the elements。
When the new punch dies pt into production to the first cutter grinding, the inaccuracy produced called initial error; if the die grinding more than twenty times, until it’s discard,the inaccuracy called conventional error; and before the dies discard,the largest error of the last batch permit, called limiting error. at job site, the evidence to confirm life of sharpening is the higher of the blanking, punched hole or punched parts. Because all finished parts had been blanked ,so it is especially for the compound dies。
【机械类文献翻译】普通全钢冲模的冲压精度分析
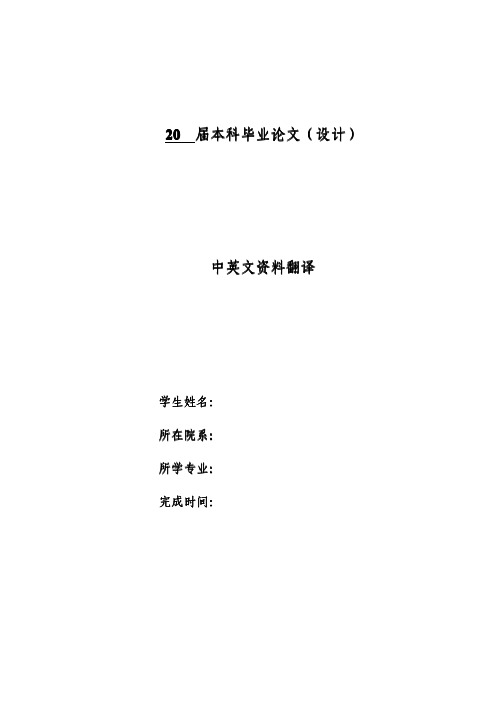
20届本科毕业论文(设计)中英文资料翻译学生姓名:所在院系:所学专业:完成时间:General all-steel punching diedie’’s punching accuracy Accuracy of panel punching part is display the press accuracy of the die exactly.But the accuracy of any punching parts’linear dimension and positional accuracy almost depend on the blanking and blanking accuracy,So that the compound mould of compound punching’s accuracy, is typicalness and representation in the majority.die’’s accuracyAnalyse of the dieFor the analyse of pracyicable inaccuracy during production of dies to inactivation,we could get the tendency when it is augmentation in most time.From this we could analyse the elements. When the new punch dies pt into production to the first cutter grinding,the inaccuracy produced called initial error;if the die grinding more than twenty times,until it’s discard,the inaccuracy called conventional error;and before the dies discard,the largest error of the last batch permit, called limiting error.at job site,the evidence to confirm life of sharpening is the higher of the blanking,punched hole or punched parts.Because all finished parts had been blanked,so it is especially for the compound dies.Therefore,the analyse of burr and measurement is especially important when do them as enterprise standardization or checked with<<the height of punching part>>.The initial error usually is the minimal through the whole life of die.Its magnitude depend on the accuracy of manufacture,quality,measure of the punching part,thickness of panel,magnitude of gap and degree of homogeneity.The accuracy of manufacture depend on the manufacture process.For the1mm thicked compound punching part made in medium steel,the experimental result and productive practice all prove that the burr of dies which produced by spark cutting are higher25%~~30%than produced by grinder,NC or CNC.The reason is that not only the latter have more exact machining accuracy but also the value of roughness Ra is less one order than the formmer,it can be reached0.025μm.Therefore,the die’s initial blanked accuracy depends on the accuracy of manufacture,quality and so on.The normal error of the punch die is the practicable error when the fist cutter grinding and the last cutter grinding before the die produce the last qualified product.As the increase of cutter grinding,caused the measure the nature wear of the dies are gradual increasing,the error of punching part increase also,so the parts are blew proof.And the die will be unused.The hole on the part and inner because the measure of wear will be small and small gradually,and its outside form will be lager in the same reason.Therefore,the hole and inner form in the part will be made mould according to one-way positive deviation or nearly equal to the limit max measure.In like manner,the punching part’s appearance will be made mould according to one-way negative deviation or nearly equal to limit mini measure.For this will be broaden the normal error,and thecutter grinding times will be increased,the life will be long.The limit error in punching parts are the max dimension error which practicable allowed in the parts with limit error.This kind of parts usually are the last qualified products before the die discard.For the all classes of dies,if we analyse the fluctuate,tendency of increase and decrease and law which appeared in the die’s whole life,we will find that the master of the error are changeless; the error that because the abrade of the cutter and impression will be as the cutter grinding times increased at the same time.And that will cause the error oversize gradually;and also have another part error are unconventional,unforeseen.Therefore,every die’s error are composed of fixed error,system error,accident error and so on.fixed errorAt the whole process when the New punching die between just input production to discard, the changeless master error that in qualified part are called fixed error.It’s magnitude is the deviation when the die production qualified products before the first cutter grinding.Also is the initial error,but the die have initial punching accuracy at this time.Because of the abrade of parts, the die after grinding will be change the dimension error.And the increment of deviation will oversize as the times of cutter grinding.So the punching accuracy after cutter grinding also called “grinding accuracy”and lower tan initial accuracy.The fixed error depend on the elements factor as followed:(1)T he material,sorts,structure,(form)dimension,and thick of panelThe magnitude of punching gap and degree of homogeneity are have a important effect for the dimension accuracy.Different punching process,material,thick of panel,have completely different gap and punching accuracy.A gear H62which made in yellow brass with the same mode number m=0.34,2mm thick and had a center hole,when the gap get C=0.5%t(single edge),and punched with compound punching die,and the dimension accuracy reached IT7,the part have a flat surface,the verticality of tangent plane reached89.5°,its roughness Ra magnitude are12.5μm, height of burr are0.10mm;and the punching part are punched with progressive die,the gap C=7%t(single edge),initial accuracy are IT11,and have an more rough surface,even can see the gap with eyes.In the usual situation,flushes a material and its thickness t is theselection punching gap main basis.Once the designation gap haddetermined flushes the plane size the fixed error main body;Flushesthe structure rigidity and the three-dimensional shape affects itsshape position precision.(2)P unching craft and molder structure typeUses the different ramming craft,flushes a precision and the fixederror difference is reallybig.Except that the above piece gearexample showed,the essence flushes the craft and ordinary punching flushes a precision and the fixed error differs outside a magnitude,even if in ordinary punching center,uses the different gap punching,thefixed error difference very is also big.For example material thickt=1.5mm H62brass punching,selects C<=the40%t unilateral I kind ofsmall gap punching compared to select C<=8%t(unilaterally)III kindof big gap punching,will flush a fixed error to enlarge40%~60%,theprecision at least will fall a level.Side in addition, whether thereis picks builds a row of type side,flushes a error to have far to bebigger than has builds a row of type to flush.Side not builds a rowof type to flush.Side not builds a row of type to flush a precisionto be lower than the IT12level side,but most has builds a row oftype to flush a precision in IT11between~IT9level,material thickt>4mm flushes,the size precision can lower some.Different die’s structure type,because is suitable the rammingmaterial to be thick and the manufacture precision difference,causesto flush a fixed error to have pound die center, multi-locations continuous type compound die because flushes continuously toduplicate the localization to add on the pattern making error to bebigger,therefore it flushes a fixed error compound punching die to wantcompared to the single location Big1~2levels.die’’s manufacture(3)T he craft of punching dieThe main work of punching die namely are raised,the concave moldprocessing procedure,to operates on the specification not to behigh,can time form a more complex cavity.But its processing surfaceapproximately is thick>0.03~0.05mm is the high temperatureablation remaining furcated austenite organization,degree ofhardness may reach as high as HRC67~70, has the micro crack,easilywhen punching appears broke the cutter or flaking.The Italian CorradaCorporation''s related memoir called"the line cut the processing contruction to have the disadvantageous influence to the superficialgold,in fact already changed the gold contruction.We must use theJin''gang stone powder to grind or the numerical control continual pathcoordinates rub truncate(cut to line)to make the precision work".In recent years country and so on Switzerland and Japan,has conductedthe thorough research to the electrical finishing equipment and abigger improvement,makes function complete high accuracy NC and theCNC line cutter,the processing precision may reach±0.005~0.001mm,even is smaller.The processing surface roughness Ra value can achieve0.4mum.According to the recent years to the domestic12productionlines cutter factory investigation and study,the domesticallyproduced line cutter processing precision different factory differentmodel line cutter might reach±0.008~±0.005mm,generally all in±0.01mm or bigger somewhat,was individual also can achieve±0.005mm,the processing surface roughness Ra value was bigger than1.6μm.However,the electrical finishing ablation metal surface thus the change and the damage machined surface mental structure character can not change,only if withrubs truncates or other ways removes this harmful level.Therefore,merely uses electricity machining,including the spark cutting and the electricity perforation,achieves with difficulty punching,especially high accuracy,high life punching die to size precision and work components surface roughness Ra value request.普通全钢冲模的冲压精度分析板料冲压件的精度准确显示出其冲模的冲压精度。
文献翻译原文-在冲压过程模拟-产品和工艺设计最新应用

Process simulation in stamping – recentapplications for product and process designAbstractProcess simulation for product and process design is currently being practiced in industry. However, a number of input variables have a significant effect on the accuracy and reliability of computer predictions. A study was conducted to evaluate the capability of FE-simulations for predicting part characteristics and process conditions in forming complex-shaped, industrial parts.In industrial applications, there are two objectives for conducting FE-simulations of the stamping process; (1) to optimize the product design by analyzing formability at the product design stage and (2) to reduce the tryout time and cost in process design by predicting the deformation process in advance during the die design stage. For each of these objectives, two kinds of FE-simulations are applied. Pam-Stamp, an incremental dynamic-explicit FEM code released by Engineering Systems Int'l, matches the second objective well because it can deal with most of the practical stamping parameters. FAST_FORM3D, a one-step FEM code released by Forming Technologies, matches the first objective because it only requires the part geometry and not the complex process information.In a previous study, these two FE codes were applied to complex-shaped parts used in manufacturing automobiles and construction machinery. Their capabilities in predicting formability issues in stamping were evaluated. This paper reviews the results of this study and summarizes the recommended procedures for obtaining accurate and reliable results from FE simulations.In another study, the effect of controlling the blank holder force (BHF) during the deep drawing of hemispherical, dome-bottomed cups was investigated. The standard automotive aluminum-killed, drawing-quality (AKDQ) steel was used as well as high performance materials such as high strength steel, bake hard steel, and aluminum 6111. It was determined that varying the BHF as a function of stroke improved the strain distributions in the domed cups.Keywords: Stamping; Process ;stimulation; Process design1. IntroductionThe design process of complex shaped sheet metal stampings such as automotive panels, consists of many stages of decision making and is a very expensive and time consuming process. Currently in industry, many engineering decisions are made based on the knowledge of experienced personnel and these decisions are typically validated during the soft tooling and prototyping stage and during hard die tryouts. Very often the soft and hard tools must be reworked or even redesigned and remanufactured to provide parts with acceptable levels of quality.The best case scenario would consist of the process outlined in Fig. 1. In this design process, the experienced product designer would have immediate feedback using a specially design software called one-step FEM to estimate the formability of their design. This would allow the product designer to make necessary changes up front as opposed to down the line after expensive tooling has been manufactured. One-step FEM is particularly suited for product analysis since it does not require binder, addendum, or even most process conditions. Typically this information is not available during the product design phase. One-step FEM is also easy to use and computationally fast, which allows the designer to play “what if” without much time investment.Fig. 1. Proposed design process for sheet metal stampings.Once the product has been designed and validated, the development project would enter the “time zero” phase and be passed onto the die designer. The die designer would validate his/her design with an incremental FEM code and make necessary design changes and perhaps even optimize the process parameters to ensure not just minimum acceptability of part quality, but maximum achievable quality. This increases product quality but also increase process robustness. Incremental FEM is particularly suited for die design analysis since it does require binder, addendum, and process conditions which are either known during die design or desired to be known.The validated die design would then be manufactured directly into the hard production tooling and be validated with physical tryouts during which the prototype parts would be made. Tryout time should be decreased due to the earlier numerical validations. Redesign and remanufacturing of the tooling due to unforeseen forming problems should be a thing of the past. The decrease in tryout time and elimination of redesign/remanufacturing should more than make up for the time used to numerically validate the part, die, and process.Optimization of the stamping process is also of great importance to producers of sheet stampings. By modestly increasing one's investment in presses, equipment, and tooling used in sheet forming, one may increase one's control over the stamping process tremendously. It has been well documented that blank holder force is one of the most sensitive process parameters in sheet forming and therefore can be used to precisely control the deformation process.By controlling the blank holder force as a function of press stroke AND position around the binder periphery, one can improve the strain distribution of the panel providing increased panel strength and stiffness, reduced springback and residual stresses, increased product quality and process robustness. An inexpensive, but industrial quality system is currently being developed at the ERC/NSM using a combination of hydraulics and nitrogen and is shown in Fig. 2. Using BHF control can also allow engineers to design more aggressive panels to take advantage the increased formability window provided by BHF control.Fig. 2. Blank holder force control system and tooling being developed at the ERC/NSM labs.Three separate studies were undertaken to study the various stages of the design process. The next section describes a study of the product design phase in which the one-step FEM code FAST_FORM3D (Forming Technologies) was validated with a laboratory and industrial part and used to predict optimal blank shapes. Section 4 summarizes a study of the die design stage in which an actual industrial panel was used to validate the incremental FEM code Pam-Stamp (Engineering Systems Int'l). Section 5 covers a laboratory study of the effect of blank holder force control on the strain distributions in deep drawn, hemispherical, dome-bottomed cups.2. Product simulation – applicationsThe objective of this investigation was to validate FAST_FORM3D, to determine FAST_FORM3D's blank shape prediction capability, and to determine how one-step FEM can be implemented into the product design process. Forming Technologies has provided their one-step FEM code FAST_FORM3D and training to the ERC/NSM for the purpose of benchmarking and research. FAST_FORM3D does not simulate the deformation history. Instead it projects the final part geometry onto a flat plane or developable surface and repositions the nodes and elements until a minimum energy state is reached. This process is computationally faster than incremental simulations like Pam-Stamp, but also makes more assumptions. FAST_FORM3D can evaluate formability and estimate optimal blank geometries and is a strong tool for product designers due to its speed and ease of use particularly during the stage when the die geometry is not available.In order to validate FAST_FORM3D, we compared its blank shape prediction with analytical blank shape prediction methods. The part geometry used was a 5 in. deep 12 in. by 15 in. rectangular pan with a 1 in. flange as shown in Fig. 3. Table 1 lists the process conditions used. Romanovski's empirical blank shape method and the slip line field method was used to predict blank shapes for this part which are shown in Fig. 4.Fig. 3. Rectangular pan geometry used for FAST_FORM3D validation. Table 1. Process parameters used for FAST_FORM3D rectangular pan validationFig. 4. Blank shape design for rectangular pans using hand calculations. (a) Romanovski's empirical method; (b) slip line field analytical method.Fig. 5(a) shows the predicted blank geometries from the Romanovski method, slip line field method, and FAST_FORM3D. The blank shapes agree in the corner area, but differ greatly in the side regions. Fig. 5(b)–(c) show the draw-in pattern after the drawing process of the rectangular pan as simulated by Pam-Stamp for each of the predicted blank shapes. The draw-in patterns for all three rectangular pans matched in the corners regions quite well. The slip line field method, though, did not achieve the objective 1 in. flange in the side region, while the Romanovski and FAST_FORM3Dmethods achieved the 1 in. flange in the side regions relatively well. Further, only the FAST_FORM3D blank agrees in the corner/side transition regions. Moreover, the FAST_FORM3D blank has a better strain distribution and lower peak strain than Romanovski as can be seen in Fig. 6.Fig. 5. Various blank shape predictions and Pam-Stamp simulation results for therectangular pan.(a) Three predicted blank shapes; (b) deformed slip line field blank; (c) deformed Romanovski blank; (d) deformed FAST_FORM3D blank.Fig. 6. Comparison of strain distribution of various blank shapes using Pam-Stamp forthe rectangular pan.(a) Deformed Romanovski blank; (b) deformed FAST_FORM3D blank.To continue this validation study, an industrial part from the Komatsu Ltd. was chosen and is shown in Fig. 7(a). We predicted an optimal blank geometry with FAST_FORM3D and compared it with the experimentally developed blank shape as shown in Fig. 7(b). As seen, the blanks are similar but have some differences.Fig. 7. FAST_FORM3D simulation results for instrument cover validation. (a) FAST_FORM3D's formability evaluation; (b) comparison of predicted and experimental blank geometries.Next we simulated the stamping of the FAST_FORM3D blank and the experimental blank using Pam-Stamp. We compared both predicted geometries to the nominal CADgeometry (Fig. 8) and found that the FAST_FORM3D geometry was much more accurate. A nice feature of FAST_FORM3D is that it can show a “failure” contour plot of the part with respect to a failure limit curve which is shown in Fig. 7(a). In conclusion, FAST_FORM3D was successful at predicting optimal blank shapes for a laboratory and industrial parts. This indicates that FAST_FORM3D can be successfully used to assess formability issues of product designs. In the case of the instrument cover, many hours of trial and error experimentation could have been eliminated by using FAST_FORM3D and a better blank shape could have been developed.Fig. 8. Comparison of FAST_FORM3D and experimental blank shapes for theinstrument cover.(a) Experimentally developed blank shape and the nominal CAD geometry; (b) FAST_FORM3D optimal blank shape and the nominal CAD geometry.3. Die and process simulation – applicationsIn order to study the die design process closely, a cooperative study was conducted by Komatsu Ltd. of Japan and the ERC/NSM. A production panel with forming problems was chosen by Komatsu. This panel was the excavator's cabin, left-hand inner panel shown in Fig. 9. The geometry was simplified into an experimental laboratory die, while maintaining the main features of the panel. Experiments were conducted at Komatsu using the process conditions shown in Table 2. A forming limit diagram (FLD) was developed for the drawing-quality steel using dome tests and a vision strain measurement system and is shown in Fig. 10. Three blank holder forces (10, 30, and 50 ton) were used in the experiments to determine its effect. Incremental simulations of each experimental condition was conducted at the ERC/NSM using Pam-Stamp.Fig. 9. Actual product – cabin inner panel.Table 2. Process conditions for the cabin inner investigationFig. 10. Forming limit diagram for the drawing-quality steel used in the cabin innerinvestigation.At 10 ton, wrinkling occurred in the experimental parts as shown in Fig. 11. At 30 ton, the wrinkling was eliminated as shown in Fig. 12. These experimental observations were predicted with Pam-stamp simulations as shown in Fig. 13. The 30 ton panel was measured to determine the material draw-in pattern. These measurements are compared with the predicted material draw-in in Fig. 14. Agreement was very good, with a maximum error of only 10 mm. A slight neck was observed in the 30 ton panel as shown in Fig. 13. At 50 ton, an obvious fracture occurred in the panel.Fig. 11. Wrinkling in laboratory cabin inner panel, BHF=10 ton.Fig. 12. Deformation stages of the laboratory cabin inner and necking, BHF=30 ton.(a) Experimental blank; (b) experimental panel, 60% formed; (c) experimental panel, fully formed;(d) experimental panel, necking detail.Fig. 13. Predication and elimination of wrinkling in the laboratory cabin inner.(a) Predicted geometry, BHF=10 ton; (b) predicted geometry, BHF=30 ton.Fig. 14. Comparison of predicted and measured material draw-in for lab cabin inner,BHF=30 ton.Strains were measured with the vision strain measurement system for each panel, and the results are shown in Fig. 15. The predicted strains from FEM simulations for each panel are shown in Fig. 16. The predictions and measurements agree well regarding the strain distributions, but differ slightly on the effect of BHF. Although the trendsare represented, the BHF tends to effect the strains in a more localized manner in the simulations when compared to the measurements. Nevertheless, these strain prediction show that Pam-Stamp correctly predicted the necking and fracture which occurs at 30 and 50 ton. The effect of friction on strain distribution was also investigated with simulations and is shown in Fig. 17.Fig. 15. Experimental strain measurements for the laboratory cabin inner. (a) measured strain, BHF=10 ton (panel wrinkled); (b) measured strain, BHF=30 ton (panel necked); (c) measured strain, BHF =50 ton (panel fractured).Fig. 16. FEM strain predictions for the laboratory cabin inner.(a) Predicted strain, BHF=10 ton; (b) predicted strain, BHF=30 ton; (c) predicted strain, BHF=50 ton.Fig. 17. Predicted effect of friction for the laboratory cabin inner, BHF=30 ton. (a) Predicted strain, μ=0.06; (b) predicted strain, μ=0.10.A summary of the results of the comparisons is included in Table 3. This table shows that the simulations predicted the experimental observations at least as well as the strain measurement system at each of the experimental conditions. This indicates that Pam-Stamp can be used to assess formability issues associated with the die design.Table 3. Summary results of cabin inner study4. Blank holder force control – applicationsThe objective of this investigation was to determine the drawability of various, high performance materials using a hemispherical, dome-bottomed, deep drawn cup (see Fig. 18) and to investigate various time variable blank holder force profiles. The materials that were investigated included AKDQ steel, high strength steel, bake hard steel, and aluminum 6111 (see Table 4). Tensile tests were performed on these materials to determine flow stress and anisotropy characteristics for analysis and for input into the simulations (see Fig. 19 and Table 5).Fig. 18. Dome cup tooling geometry.Table 4. Material used for the dome cup studyFig. 19. Results of tensile tests of aluminum 6111, AKDQ, high strength, and bake hard steels.(a) Fractured tensile specimens; (b) Stress/strain curves.Table 5. Tensile test data for aluminum 6111, AKDQ, high strength, and bake hard steelsIt is interesting to note that the flow stress curves for bake hard steel and AKDQ steel were very similar except for a 5% reduction in elongation for bake hard. Although, the elongations for high strength steel and aluminum 6111 were similar, the n-value for aluminum 6111 was twice as large. Also, the r-value for AKDQ was much bigger than 1, while bake hard was nearly 1, and aluminum 6111 was much less than 1.The time variable BHF profiles used in this investigation included constant, linearly decreasing, and pulsating (see Fig. 20). The experimental conditions for AKDQ steel were simulated using the incremental code Pam-Stamp. Examples of wrinkled, fractured, and good laboratory cups are shown in Fig. 21 as well as an image of a simulated wrinkled cup.Fig. 20. BHF time-profiles used for the dome cup study.(a) Constant BHF; (b) ramp BHF; (c) pulsating BHF.Fig. 21. Experimental and simulated dome cups.(a) Experimental good cup; (b) experimental fractured cup; (c) experimental wrinkled cup; (d) simulated wrinkled cup.Limits of drawability were experimentally investigated using constant BHF. The results of this study are shown in Table 6. This table indicates that AKDQ had the largest drawability window while aluminum had the smallest and bake hard and high strength steels were in the middle. The strain distributions for constant, ramp, and pulsating BHF are compared experimentally in Fig. 22 and are compared with simulations in Fig. 23 for AKDQ. In both simulations and experiments, it was found that the ramp BHF trajectory improved the strain distribution the best. Not only were peak strains reduced by up to 5% thereby reducing the possibility of fracture, but low strain regions were increased. This improvement in strain distribution can increase product stiffness and strength, decrease springback and residual stresses, increase product quality and process robustness.Table 6. Limits of drawability for dome cup with constant BHFFig. 22. Experimental effect of time variable BHF on engineering strain in an AKDQ steel dome cup.Fig. 23. Simulated effect of time variable BHF on true strain in an AKDQ steel dome cup.Pulsating BHF, at the frequency range investigated, was not found to have an effect on strain distribution. This was likely due to the fact the frequency of pulsation that was tested was only 1 Hz. It is known from previous experiments of other researchers that proper frequencies range from 5 to 25 Hz [3]. A comparison of load-stroke curves from simulation and experiments are shown in Fig. 24 for AKDQ. Good agreement was found for the case where μ=0.08. This indicates that FEM simulations can be used to assess the formability improvements that can be obtained by using BHF control techniques.Fig. 24. Comparison of experimental and simulated load-stroke curves for an AKDQ steel dome cup.5 Conclusions and future workIn this paper, we evaluated an improved design process for complex stampings which involved eliminating the soft tooling phase and incorporated the validation of product and process using one-step and incremental FEM simulations. Also, process improvements were proposed consisting of the implementation of blank holder force control to increase product quality and process robustness.Three separate investigations were summarized which analyzed various stages in the design process. First, the product design phase was investigated with a laboratory and industrial validation of the one-step FEM code FAST_FORM3D and its ability to assess formability issues involved in product design. FAST_FORM3D was successful at predicting optimal blank shapes for a rectangular pan and an industrial instrument cover. In the case of the instrument cover, many hours of trial and error experimentation could have been eliminated by using FAST_FORM3D and a better blank shape could have been developed.Second, the die design phase was investigated with a laboratory and industrial validation of the incremental code Pam-Stamp and its ability to assess forming issuesassociated with die design. This investigation suggested that Pam-Stamp could predict strain distribution, wrinkling, necking, and fracture at least as well as a vision strain measurement system at a variety of experimental conditions.Lastly, the process design stage was investigated with a laboratory study of the quality improvements that can be realized with the implementation of blank holder force control techniques. In this investigation, peak strains in hemispherical, dome-bottomed, deep drawn cups were reduced by up to 5% thereby reducing the possibility of fracture, and low strain regions were increased. This improvement in strain distribution can increase product stiffness and strength, decrease springback and residual stresses, increase product quality and process robustness. It can be expected that improvements in drawability would be further enhanced by optimizing the variation of the BHF in function of time. Further, good agreement was found for experimentally measured and numerically predicted load-stroke curves indicating that FEM simulations can be used to assess the formability improvements that can be obtained using BHF control techniques.Die position in industrial productionMold is a high-volume products with the shape tool, is the main process of industrial production equipment.With mold components, with high efficiency, good quality, low cost, saving energy and raw materials and a series of advantages, with the mold workpieces possess high accuracy, high complexity, high consistency, high productivity and low consumption , other manufacturing methods can not match. Have already become an important means of industrial production and technological development. The basis of the modern industrial economy.The development of modern industrial and technological level depends largely on the level of industrial development die, so die industry to national economic and social development will play an increasing role. March 1989 the State Council promulgated "on the current industrial policy decision points" in the mold as the machinery industry transformation sequence of the first, production and capital construction of the second sequence (after the large-scale power generation equipment and the corresponding power transmission equipment), establish tooling industry in an important position in the national economy. Since 1997, they have to mold and its processing technology and equipment included in the "current national focus on encouraging the development of industries, products and technologies catalog" and "to encourage foreign investment industry directory." Approved by the State Council, from 1997 to 2000, more than 80 professional mold factory owned 70% VAT refund of preferential policies to support mold industry. All these have fully demonstrated the development of the State Council and state departments tooling industry attention and support. Mold around the world about the current annual output of 60 billion U.S. dollars, Japan, the United States and other industrialized countries die of industrial output value of more than machine tool industry, beginning in 1997, China's industrial output value has exceeded the mold machine tool industry output.According to statistics, home appliances, toys and other light industries, nearly 90% of the parts are integrated with production of chopsticks; in aircraft, automobiles,agricultural machinery and radio industries, the proportion exceeded 60%. Such as aircraft manufacturing, the use of a certain type of fighter dies more than 30,000 units, of which the host 8000 sets, 2000 sets of engines, auxiliary 20 000 sets. From the output of view, since the 80's, the United States, Japan and other industrialized countries die industry output value has exceeded the machine tool industry, and there are still rising. Production technology, according to the International Association predicts that in 2000, the product best pieces of rough 75%, 50% will be finished mold completed; metals, plastics, ceramics, rubber, building materials and otherindustrial products, most of the mold will be completed in more than 50% metal . The 19th century, with the arms industry (gun's shell), watch industry, radio industry, dies are widely used. After World War II, with the rapid development of world economy, it became a mass production of household appliances, automobiles, electronic equipment, cameras, watches and other parts the best way. From a global perspective, when the United States in the forefront of stamping technology - many die of advanced technologies, such as simple mold, high efficiency, mold, die and stamping the high life automation, mostly originated in the United States; and Switzerland, fine blanking, cold in Germany extrusion technology, plastic processing of the Soviet Union are at the world advanced. 50's, mold industry focus is based on subscriber demand, production can meet the product requirements of the mold. Multi-die design rule of thumb, reference has been drawing and perceptual knowledge, on the design of mold parts of a lack of real understanding of function. From 1955 to 1965, is the pressure processing of exploration and development of the times - the main components of the mold and the stress state of the function of a mathematical sub-bridge, and to continue to apply to on-site practical knowledge to make stamping technology in all aspects of a leap in development. The result is summarized mold design principles, and makes the pressure machine, stamping materials, processing methods, plum with a structure, mold materials, mold manufacturing method, the field of automation devices, a new look to the practical direction of advance, so that pressing processing apparatus capable of producing quality products from the first stage.Into the 70's to high speed, launch technology, precision, security, development of the second stage. Continue to emerge in this process a variety of high efficiency, business life, high-precision multi-functional automatic school to help with. Represented by the number of working places as much as other progressive die and dozens of multi-station transfer station module. On this basis, has developed both acontinuous pressing station there are more slide forming station of the press - bending machine. In the meantime, the Japanese stand to the world's largest - the mold into the micron-level precision, die life, alloy tool steel mold has reached tens of millions of times, carbide steel mold to each of hundreds of millions of times p minutes for stamping the number of small presses usually 200 to 300, up to 1200 times to 1500 times. In the meantime, in order to meet product updates quickly, with the short duration (such as cars modified, refurbished toys, etc.) need a variety of economic-type mold, such as zinc alloy die down, polyurethane rubber mold, die steel skin, also has been very great development.From the mid-70s so far can be said that computer-aided design, supporting the continuous development of manufacturing technology of the times. With the precision and complexity of mold rising, accelerating the production cycle, the mold industry, the quality of equipment and personnel are required to improve. Rely on common processing equipment, their experience and skills can not meet the needs of mold. Since the 90's, mechanical and electronic technologies in close connection with the development of NC machine tools, such as CNC wire cutting machine, CNC EDM, CNC milling, CNC coordinate grinding machine and so on. The use of computer automatic programming, control CNC machine tools to improve the efficiency in the use and scope. In recent years, has developed a computer to time-sharing by the way a group of direct management and control of CNC machine tools NNC system.With the development of computer technology, computers have gradually into the mold in all areas, including design, manufacturing and management. International Association for the Study of production forecasts to 2000, as a means of links between design and manufacturing drawings will lose its primary role. Automatic Design of die most fundamental point is to establish the mold standard and design standards. To get rid of the people of the past, and practical experience to judge the composition of the design center, we must take past experiences and ways of thinking, for series, numerical value, the number of type-based, as the design criteria to the computer store. Components are dry because of mold constitutes a million other differences, to come up with a can adapt to various parts of the design software almost impossible. But some products do not change the shape of parts, mold structure has certain rules, can be summed up for the automatic design of software. If a Japanese company's CDM system for progressive die design and manufacturing, including the importation of parts of the figure, rough start, strip layout, determine the size and。
文献翻译-在冲压过程模拟-产品和工艺设计最新应用
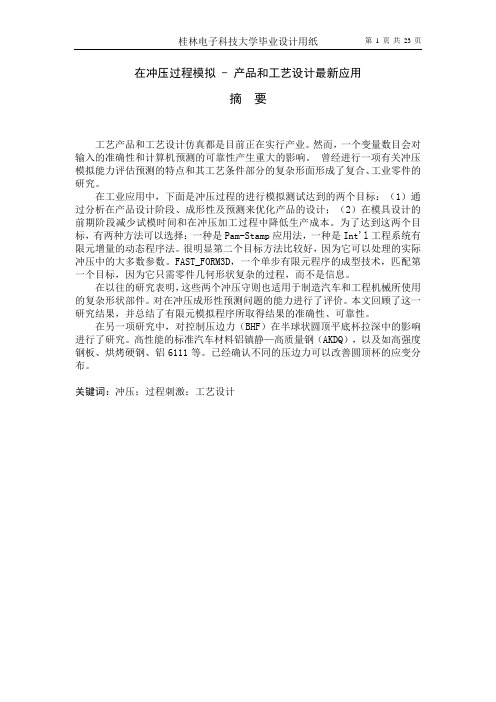
在冲压过程模拟 - 产品和工艺设计最新应用摘要工艺产品和工艺设计仿真都是目前正在实行产业。
然而,一个变量数目会对输入的准确性和计算机预测的可靠性产生重大的影响。
曾经进行一项有关冲压模拟能力评估预测的特点和其工艺条件部分的复杂形面形成了复合、工业零件的研究。
在工业应用中,下面是冲压过程的进行模拟测试达到的两个目标:(1)通过分析在产品设计阶段、成形性及预测来优化产品的设计;(2)在模具设计的前期阶段减少试模时间和在冲压加工过程中降低生产成本。
为了达到这两个目标,有两种方法可以选择:一种是Pam-Stamp应用法,一种是Int'l工程系统有限元增量的动态程序法。
很明显第二个目标方法比较好,因为它可以处理的实际冲压中的大多数参数。
FAST_FORM3D,一个单步有限元程序的成型技术,匹配第一个目标,因为它只需零件几何形状复杂的过程,而不是信息。
在以往的研究表明,这些两个冲压守则也适用于制造汽车和工程机械所使用的复杂形状部件。
对在冲压成形性预测问题的能力进行了评价。
本文回顾了这一研究结果,并总结了有限元模拟程序所取得结果的准确性、可靠性。
在另一项研究中,对控制压边力(BHF)在半球状圆顶平底杯拉深中的影响进行了研究。
高性能的标准汽车材料铝镇静—高质量钢(AKDQ),以及如高强度钢板、烘烤硬钢、铝6111等。
已经确认不同的压边力可以改善圆顶杯的应变分布。
关键词:冲压;过程刺激;工艺设计1.简介对于形状复杂的板材(如汽车覆盖件金属冲压件的设计过程,包括决策的许多阶段)的设计过程是一个非常昂贵和耗时的过程。
在目前的工业上,许多工程决策是基于工作人员的经验和他们的知识,这些决策通常是经过软工装模具成型阶段和硬模选拔赛验证阶段后才做出的。
很多时候软、硬工具必须重新编制,甚至重新设计和提供的零件到达可接受的质量水平。
现在将最好的设计过程列在图1中。
在这个设计过程中,经验丰富的产品设计人员会使用一个称为一步有限元法的专门设计的软件来估计其设计成形性。
冲压模具技术外文文献翻译中英文
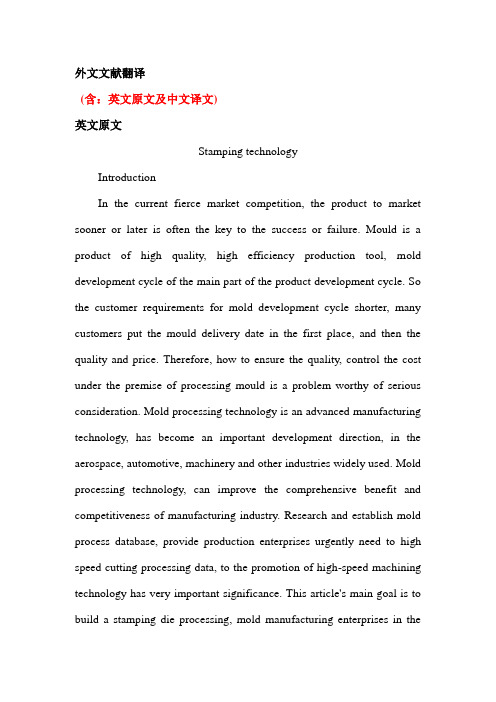
外文文献翻译(含:英文原文及中文译文)英文原文Stamping technologyIntroductionIn the current fierce market competition, the product to market sooner or later is often the key to the success or failure. Mould is a product of high quality, high efficiency production tool, mold development cycle of the main part of the product development cycle. So the customer requirements for mold development cycle shorter, many customers put the mould delivery date in the first place, and then the quality and price. Therefore, how to ensure the quality, control the cost under the premise of processing mould is a problem worthy of serious consideration. Mold processing technology is an advanced manufacturing technology, has become an important development direction, in the aerospace, automotive, machinery and other industries widely used. Mold processing technology, can improve the comprehensive benefit and competitiveness of manufacturing industry. Research and establish mold process database, provide production enterprises urgently need to high speed cutting processing data, to the promotion of high-speed machining technology has very important significance. This article's main goal is to build a stamping die processing, mold manufacturing enterprises in theactual production combined cutting tool, workpiece and machine tool with the actual situation of enterprise itself accumulate to high speed cutting processing instance, process parameters and experience of high speed cutting database selectively to store data, not only can save a lot of manpower and material resources, financial resources, but also can guide the high speed machining production practice, to improve processing efficiency, reduce the tooling cost and obtain higher economic benefits.1. The concept, characteristics and application of stampingStamping is a pressure processing method that uses a mold installed on a press machine (mainly a press) to apply pressure to a material to cause it to separate or plastically deform, thereby obtaining a desired part (commonly referred to as a stamped or stamped part). Stamping is usually cold deformation processing of the material at room temperature, and the main use of sheet metal to form the required parts, it is also called cold stamping or sheet metal stamping. Stamping is one of the main methods of material pressure processing or plastic processing, and is affiliated with material forming engineering.The stamping die is called stamping die, or die. Dies are special tools for the batch processing of materials (metal or non-metallic) into the required stampings. Stamping is critical in stamping. There is no die that meets the requirements. Batch stamping production is difficult. Without advanced stamping, advanced stamping processes cannot be achieved.Stamping processes and dies, stamping equipment, and stamping materials constitute the three elements of stamping. Only when they are combined can stampings be obtained.Compared with other methods of mechanical processing and plastic processing, stamping processing has many unique advantages in both technical and economic aspects, and its main performance is as follows;(1) The stamping process has high production efficiency, easy operation, and easy realization of mechanization and automation. This is because stamping is accomplished by means of die and punching equipment. The number of strokes for ordinary presses can reach several tens of times per minute, and the high-speed pressure can reach hundreds or even thousands of times per minute, and each press stroke is You may get a punch.(2) Since the die ensures the dimensional and shape accuracy of the stamping part during stamping, and generally does not destroy the surface quality of the stamping part, the life of the die is generally longer, so the stamping quality is stable, the interc hangeability is good, and it has “the same” Characteristics.(3) Stamping can process parts with a wide range of sizes and shapes, such as stopwatches as small as clocks, as large as automobile longitudinal beams, coverings, etc., plus the cold deformation hardening effect of materials during stamping, the strength of stamping and Thestiffness is high.(4) Stamping generally does not generate scraps, material consumption is less, and no other heating equipment is required. Therefore, it is a material-saving and energy-saving processing method, and the cost of stamping parts is low.However, the molds used for stamping are generally specialized, and sometimes a complex part requires several sets of molds for forming, and the precision of the mold manufacturing is high and the technical requirements are high. It is a technology-intensive product. Therefore, the advantages of stamping can only be fully realized in the case of large production volume of stamping parts, so as to obtain better economic benefits.Stamping is widely used in modern industrial production, especially in mass production. A considerable number of industrial sectors are increasingly using punching to process product components such as automobiles, agricultural machinery, instruments, meters, electronics, aerospace, aerospace, home appliances, and light industry. In these industrial sectors, the proportion of stamped parts is quite large, at least 60% or more, and more than 90%. Many of the parts that were manufactured in the past using forging = casting and cutting processes are now mostly replaced by light-weight, rigid stampings. Therefore, it can be said that if the stamping process cannot be adopted in production, it isdifficult for many industrial departments to increase the production efficiency and product quality, reduce the production cost, and quickly replace the product.2. Basic process and mould for stampingDue to the wide variety of stamped parts and the different shapes, sizes, and precision requirements of various parts, the stamping process used in production is also varied. Summarized, can be divided into two major categories of separation processes and forming processes; Separation process is to make the blank along a certain contour line to obtain a certain shape, size and section quality stamping (commonly referred to as blanking parts) of the process; forming process refers to The process of producing a stamped part of a certain shape and size by plastic deformation of the blank without breaking.The above two types of processes can be divided into four basic processes: blanking, bending, deep drawing and forming according to different basic deformation modes. Each basic process also includes multiple single processes.In actual production, when the production volume of the stamped part is large, the size is small and the tolerance requirement is small, it is not economical or even difficult to achieve the requirement if the stamping is performed in a single process. At this time, a centralized scheme is mostly used in the process, that is, two or more singleprocesses are concentrated in a single mold. Different methods are called combinations, and they can be divided into compound-graded and compound- Progressive three combinations.Composite stamping - A combination of two or more different single steps at the same station on the die in one press stroke.Progressive stamping - a combination of two or more different single steps on a single work station in the same mold at a single working stroke on the press.Composite - Progressive - On a die combination process consisting of composite and progressive two ways.There are many types of die structure. According to the process nature, it can be divided into blanking die, bending die, drawing die and forming die, etc.; the combination of processes can be divided into single-step die, compound die and progressive die. However, regardless of the type of die, it can be regarded as consisting of two parts: the upper die and the lower die. The upper die is fixed on the press table or the backing plate and is a fixed part of the die. During work, the blanks are positioned on the lower die surface by positioning parts, and the press sliders push the upper die downwards. The blanks are separated or plastically deformed under the action of the die working parts (ie, punch and die) to obtain the required Shape and size of punching pieces. When the upper mold is lifted, the unloading and ejecting device of the moldremoves or pushes and ejects the punching or scrap from the male and female molds for the next punching cycle.3. Current status and development direction of stamping technologyWith the continuous advancement of science and technology and the rapid development of industrial production, many new technologies, new processes, new equipment, and new materials continue to emerge, thus contributing to the constant innovation and development of stamping technology. Its main performance and development direction are as follows:(1) The theory of stamping and the stamping process The study of stamping forming theory is the basis for improving stamping technology. At present, the research on the stamping forming theory at home and abroad attaches great importance, and significant progress has been made in the study of material stamping performance, stress and strain analysis in the stamping process, study of the sheet deformation law, and the interaction between the blank and the mold. . In particular, with the rapid development of computer technology and the further improvement of plastic deformation theory, computer simulation techniques for the plastic forming process have been applied at home and abroad in recent years, namely the use of finite element (FEM) and other valuable analytical methods to simulate the plastic forming process of metals. According to the analysis results, the designer can predict the feasibility and possiblequality problems of a certain process scheme. By selecting and modifying the relevant parameters on the computer, the process and mold design can be optimized. This saves the cost of expensive trials and shortens the cycle time.Research and promotion of various pressing technologies that can increase productivity and product quality, reduce costs, and expand the range of application of stamping processes are also one of the development directions of stamping technology. At present, new precision, high-efficiency, and economical stamping processes, such as precision stamping, soft mold forming, high energy high speed forming, and dieless multi-point forming, have emerged at home and abroad. Among them, precision blanking is an effective method for improving the quality of blanking parts. It expands the scope of stamping processing. The thickness of precision blanking parts can reach 25mm at present, and the precision can reach IT16~17; use liquid, rubber, polyurethane, etc. Flexible die or die soft die forming process can process materials that are difficult to process with ordinary processing methods and parts with complex shapes, have obvious economic effects under specific production conditions, and adopt energy-efficient forming methods such as explosion for processing. This kind of sheet metal parts with complex dimensions, complex shapes, small batches, high strength and high precision has important practical significance; Superplastic forming of metal materialscan be used to replace multiple common stampings with one forming. Forming process, which has outstanding advantages for machining complex shapes and large sheet metal parts; moldless multi-point forming process is an advanced technology for forming sheet metal surfaces by replacing the traditional mold with a group of height adjustable punches. Independently designed and manufactured an international leading-edge moldless multi-point forming equipment, which solves the multi-point press forming method and can therefore be Changing the state of stress and deformation path, improving the forming limit of the material, while repeatedly using the forming technology may eliminate the residual stress within the material, the rebound-free molding. The dieless multi-point forming system takes CAD/CAM/CAE technology as the main means to quickly and economically realize the automated forming of three-dimensional surfaces.(2) Dies are the basic conditions for achieving stamping production. In the design and manufacture of stampings, they are currently developing in the following two aspects: On the one hand, in order to meet the needs of high-volume, automatic, precision, safety and other large-volume modern production, stamping is To develop high-efficiency, high-precision, high-life, multi-station, and multi-function, compared with new mold materials and heat treatment technologies, various high-efficiency, precision, CNC automatic mold processing machine toolsand testing equipment and molds CAD/CAM technology is also rapidly developing; On the other hand, in order to meet the needs of product replacement and trial production or small-batch production, zinc-based alloy die, polyurethane rubber die, sheet die, steel die, combination die and other simple die And its manufacturing technology has also been rapidly developed.Precision, high-efficiency multi-station and multi-function progressive die and large-scale complex automotive panel die represent the technical level of modern die. At present, the precision of the progressive die above 50 stations can reach 2 microns. The multifunctional progressive die can not only complete the stamping process, but also complete welding, assembly and other processes. Our country has been able to design and manufacture its own precision up to the international level of 2 to 5 microns, precision 2 to 3 microns into the distance, the total life of 100 million. China's major automotive mold enterprises have been able to produce complete sets of car cover molds, and have basically reached the international level in terms of design and manufacturing methods and means. However, the manufacturing methods and methods have basically reached the international level. The mold structure and function are also close to international Level, but there is still a certain gap compared with foreign countries in terms of manufacturing quality, accuracy, manufacturing cycle and cost.4. Stamping standardization and professional productionThe standardization and professional production of molds has been widely recognized by the mold industry. Because the die is a single-piece, small-volume production, the die parts have both certain complexity and precision, as well as a certain structural typicality. Therefore, only the standardization of the die can be achieved, so that the production of the die and the die parts can be professionalized and commercialized, thereby reducing the cost of the die, improving the quality of the die and shortening the manufacturing cycle. At present, the standard production of molds in foreign advanced industrial countries has reached 70% to 80%. Mould factories only need to design and manufacture working parts, and most of the mold parts are purchased from standard parts factories, which greatly increases productivity. The more irregular the degree of specialization of the mold manufacturing plant, the more and more detailed division of labor, such as the current mold factory, mandrel factory, heat treatment plant, and even some mold factories only specialize in the manufacture of a certain type of product or die The bending die is more conducive to the improvement of the manufacturing level and the shortening of the manufacturing cycle. China's stamp standardization and specialized production have also witnessed considerable development in recent years. In addition to the increase in the number of standard parts specialized manufacturers, the number ofstandard parts has also expanded, and the accuracy has also improved. However, the overall situation can not meet the requirements of the development of the mold industry, mainly reflected in the standardization level is not high (usually below 40%), the standard parts of the species and specifications are less, most standard parts manufacturers did not form a large-scale production, standard parts There are still many problems with quality. In addition, the sales, supply, and service of standard parts production have yet to be further improved.中文译文冲压模具技术前言在目前激烈的市场竞争中, 产品投入市场的迟早往往是成败的关键。
机械专业英语和翻译

机械专业英语词汇金属切削metal cutting机床machine tool金属工艺学technology of metals刀具cutter摩擦friction联结link传动drive/transmission轴shaft弹性elasticity频率特性frequency characteristic误差error响应response定位allocation机床夹具jig动力学dynamic运动学kinematic静力学static分析力学analyse mechanics拉伸pulling压缩hitting剪切shear扭转twist弯曲应力bending stress强度intensity三相交流电three-phase AC磁路magnetic circles变压器transformer异步电动机asynchronous motor几何形状geometrical精度precision正弦形的sinusoid交流电路AC circuit机械加工余量machining allowance变形力deforming force变形deformation应力stress硬度rigidity热处理heat treatment退火anneal正火normalizing脱碳decarburization渗碳carburization电路circuit半导体元件semiconductor element反馈feedback发生器generator直流电源DC electrical source门电路gate circuit逻辑代数logic algebra外圆磨削external grinding内圆磨削internal grinding平面磨削plane grinding变速箱gearbox离合器clutch绞孔fraising绞刀reamer螺纹加工thread processing螺钉screw铣削mill铣刀milling cutter功率power工件workpiece齿轮加工gear mechining齿轮gear主运动main movement主运动方向direction of main movement 进给方向direction of feed进给运动feed movement合成进给运动resultant movement of feed 合成切削运动resultant movement of cutting合成切削运动方向direction of resultant movement of cutting切削深度cutting depth前刀面rake face刀尖nose of tool前角rake angle后角clearance angle龙门刨削planing主轴spindle主轴箱headstock卡盘chuck2加工中心machining center车刀lathe tool车床lathe钻削镗削bore车削turning磨床grinder基准benchmark钳工locksmith锻forge压模stamping焊weld拉床broaching machine拉孔broaching装配assembling铸造found流体动力学fluid dynamics流体力学fluid mechanics加工machining液压hydraulic pressure切线tangent机电一体化mechanotronics mechanical-electrical integration气压air pressure pneumatic pressure 稳定性stability介质medium液压驱动泵fluid clutch液压泵hydraulic pump阀门valve失效invalidation强度intensity载荷load应力stress安全系数safty factor可靠性reliability螺纹thread螺旋helix键spline销pin滚动轴承rolling bearing滑动轴承sliding bearing弹簧spring制动器arrester brake十字结联轴节crosshead联轴器coupling链chain皮带strap精加工finish machining粗加工rough machining变速箱体gearbox casing腐蚀rust氧化oxidation磨损wear耐用度durability随机信号random signal离散信号discrete signal超声传感器ultrasonic sensor集成电路integrate circuit挡板orifice plate残余应力residual stress套筒sleeve扭力torsion冷加工cold machining电动机electromotor汽缸cylinder过盈配合interference fit热加工hotwork摄像头CCD camera倒角rounding chamfer优化设计optimal design工业造型设计industrial moulding design 有限元finite element滚齿hobbing插齿gear shaping伺服电机actuating motor铣床milling machine钻床drill machine镗床boring machine步进电机stepper motor丝杠screw rod导轨lead rail组件subassembly可编程序逻辑控制器Programmable Logic Controller PLC电火花加工electric spark machining电火花线切割加工electrical discharge wire - cutting相图phase diagram热处理heat treatment固态相变solid state phase changes有色金属nonferrous metal3陶瓷ceramics合成纤维synthetic fibre电化学腐蚀electrochemical corrosion 车架automotive chassis悬架suspension转向器redirector变速器speed changer板料冲压sheet metal parts孔加工spot facing machining车间workshop工程技术人员engineer气动夹紧pneuma lock数学模型mathematical model画法几何descriptive geometry机械制图Mechanical drawing投影projection视图view剖视图profile chart标准件standard component零件图part drawing装配图assembly drawing尺寸标注size marking技术要求technical requirements刚度rigidity内力internal force位移displacement截面section疲劳极限fatigue limit断裂fracture塑性变形plastic distortion脆性材料brittleness material刚度准则rigidity criterion垫圈washer垫片spacer直齿圆柱齿轮straight toothed spur gear 斜齿圆柱齿轮helical-spur gear直齿锥齿轮straight bevel gear运动简图kinematic sketch齿轮齿条pinion and rack蜗杆蜗轮worm and worm gear虚约束passive constraint曲柄crank摇杆racker凸轮cams共轭曲线conjugate curve范成法generation method定义域definitional domain值域range导数\\微分differential coefficient求导derivation定积分definite integral不定积分indefinite integral曲率curvature偏微分partial differential毛坯rough游标卡尺slide caliper千分尺micrometer calipers攻丝tap二阶行列式second order determinant 逆矩阵inverse matrix线性方程组linear equations概率probability随机变量random variable排列组合permutation and combination 气体状态方程equation of state of gas 动能kinetic energy势能potential energy机械能守恒conservation of mechanical energy动量momentum桁架truss轴线axes余子式cofactor逻辑电路logic circuit触发器flip-flop脉冲波形pulse shape数模digital analogy液压传动机构fluid drive mechanism 机械零件mechanical parts淬火冷却quench淬火hardening回火tempering调质hardening and tempering磨粒abrasive grain结合剂bonding agent砂轮grinding wheel机械零件mechanical parts淬火冷却quench淬火hardening回火tempering4调质hardening and tempering磨粒abrasive grain结合剂bonding agent砂轮grinding wheel机床行业部分英汉对照(1):按英文字母排序3-Jaws indexing spacers 三爪、分割工具头A.T.C.system 加工中心机刀库Aluminum continuous melting & holding fu rnaces 连续溶解保温炉Balancing equipment 平衡设备Bayonet 卡口Bearing fittings 轴承配件Bearing processing equipment 轴承加工机Bearings 轴承Belt drive 带传动Bending machines 弯曲机Blades 刀片Blades,saw 锯片Bolts,screws & nuts 螺栓,螺帽及螺丝Boring heads 搪孔头Boring machines 镗床Cable making tools 造线机Casting,aluminium 铸铝Casting,copper 铸铜Casting,gray iron 铸灰口铁Casting,malleable iron 可锻铸铁Casting,other 其他铸造Casting,steel 铸钢Chain drive 链传动Chain making tools 造链机Chamfer machines 倒角机Chucks 夹盘Clamping/holding systems 夹具/支持系统CNC bending presses 电脑数控弯折机CNC boring machines 电脑数控镗床CNC drilling machines 电脑数控钻床CNC EDM wire-cutting machines 电脑数控电火花线切削机CNC electric discharge machines 电脑数控电火花机CNC engraving machines 电脑数控雕刻机CNC grinding machines 电脑数控磨床CNC lathes 电脑数控车床CNC machine tool fittings 电脑数控机床配件CNC milling machines 电脑数控铣床CNC shearing machines 电脑数控剪切机CNC toolings CNC 刀杆CNC wire-cutting machines 电脑数控线切削机Conveying chains 输送链Coolers 冷却机Coupling 联轴器Crimping tools 卷边工具Cutters 刀具Cutting-off machines 切断机Diamond cutters 钻石刀具Dicing saws 晶圆切割机Die casting dies 压铸冲模Die casting machines 压铸机Dies-progressive 连续冲模Disposable toolholder bits 舍弃式刀头Drawing machines 拔丝机Drilling machines 钻床Drilling machines bench 钻床工作台Drilling machines,high-speed 高速钻床Drilling machines,multi-spindle 多轴钻床Drilling machines,radial 摇臂钻床Drilling machines,vertical 立式钻床drills 钻头Electric discharge machines(EDM) 电火花机Electric power tools 电动刀具Engraving machines 雕刻机Engraving machines,laser 激光雕刻机Etchin g machines 蚀刻机Finishing machines 修整机Fixture 夹具Forging dies 锻模Forging,aluminium 锻铝Forging,cold 冷锻Forging,copper 铜锻Forging,other 其他锻造Forging,steel 钢锻Foundry equipment 铸造设备Gear cutting machines 齿轮切削机5Gears 齿轮Gravity casting machines 重力铸造机Grinde r bench 磨床工作台Grinders,thread 螺纹磨床Grinders,tools & cutters 工具磨床Grinders,ultrasonic 超声波打磨机Grinding machines 磨床Grinding machines,centerless 无心磨床Grinding machines,cylindrical 外圆磨床Grinding machines,universal 万能磨床Grinding tools 磨削工具Grinding wheels 磨轮Hand tools 手工具Hard/soft and free expansion sheet making plant 硬(软)板(片)材及自由发泡板机组Heat preserving furnaces 保温炉Heating treatment funaces 熔热处理炉Honing machines 搪磨机Hydraulic components 液压元件Hydraulic power tools 液压工具Hydraulic power units 液压动力元件Hydra ulic rotary cylinders 液压回转缸Jigs 钻模Lapping machines 精研机Lapping machines,centerless 无心精研机Laser cutting 激光切割Laser cutting for SMT stensil 激光钢板切割机Lathe bench 车床工作台Lathes,automatic 自动车床Lathes,heavy-duty 重型车床Lathes,high-speed 高速车床Lathes,turret 六角车床Lathes,vertical 立式车床Lubricants 润滑液Lubrication Systems 润滑系统Lubricators 注油机Machining centers,general 通用加工中心Machining centers,horizontal 卧式加工中心Machining centers,horizontal & vertical 卧式及立式加工中心Machining centers,vertical 立式加工中心Machining centers,vertical double-column ty pe 立式双柱加工中心Magnetic tools 磁性工具Manifolds 集合管Milling heads 铣头Milling machines 铣床Milling machines,bed type 床身式铣床Milling machines,duplicating 仿形铣床Milling machines,horizontal 卧式铣床Millin g machines,turret vertical 六角立式铣床Milling machines,universal 万能铣床Milling machines,vertical 立式铣床Milling machines,vertical & horizontal 立式及卧式铣床Mold & die components 模具单元Mold changing systems 换模系统Mold core 模芯Mold heaters/chillers 模具加热器/冷却器Mold polishing/texturing 模具打磨/磨纹Mold repair 模具维修Molds 模具Nail making machines 造钉机Oil coolers 油冷却器Overflow cutting machines for aluminium w heels 铝轮冒口切断机P type PVC waterproof rolled sheet making plant P型PVC 高分子防水PCB fine piecing systems 印刷电器板油压冲孔脱料系统Pipe & tube making machines 管筒制造机Planing machines 刨床Planing machines vertical 立式刨床Pneumatic hydraulic clamps 气油压虎钳Pneumatic power tools 气动工具Powder metallurgic forming machines 粉末冶金成型机Presses,cold forging 冷锻冲压机presses,crank 曲柄压力机Presses,eccentric 离心压力机Presses,forging 锻压机Presses,hydraulic 液压冲床Presses,knuckle joint 肘杆式压力机Presses,pneumatic 气动冲床Presses,servo 伺服冲床Presses,transfer 自动压力机Pressing dies 压模Punch formers 冲子研磨器Quick die change systems 速换模系统6Quick mold change systems 快速换模系统Reverberatory furnaces 反射炉Rollers 滚筒Rolling machines 辗压机Rotary tables 转台Sawing machines 锯床Sawing machines,band 带锯床Saws,band 带锯Saws,hack 弓锯Saws,horizontal band 卧式带锯Saws,vertical band 立式带锯shafts 轴Shapers 牛头刨床Shearing machines 剪切机Sheet metal forming machines 金属板成型机Sheet metal working machines 金属板加工机Slotting machines 插床spindles 主轴Stamping parts 冲压机Straightening machines 矫直机Switches & buttons 开关及按钮Tapping machines 攻螺丝机Transmitted chains 传动链Tube bending machines 弯管机Vertical hydraulic broaching machine 立式油压拉床Vises 虎钳Vises,tool-maker 精密平口钳Wheel dressers 砂轮修整器Woven-Cutting machines 织麦激光切割机Wrenches 扳手螺丝词汇的中英文对照六角盖头螺帽HEX CAP NUTS六角锯齿螺帽HEX SERRATED NUTS六角轮缘螺帽HEX FLANGE NUTS 高脚螺帽HEX COUPLING NUTS(HIGH NUTS)圆螺帽ROUND NUTS四角螺帽SQUARE NUTS7HEA VY HEX NUTS不锈钢六角螺帽STAINLESS STEEL HEXNUTS不锈钢尼龙嵌入螺帽STAINLESS STEELNYLON INSERT LOCK NUTS普通六角螺帽HEX NUTS六角重型螺帽HEA VY HEX NUTS薄型螺帽HEX JAM NUTS尼龙嵌入防松螺帽NYLON INSERT LOCK NUTS 机械螺丝用六角螺帽HEX MACHINE SCREW NUT 机械工具英语机械工具spanner 扳子(美作:wrench) double-ended spanner 双头扳子adjustable spanner, monkey wrench 活扳子,活络扳手box spanner 管钳子(美作:socket wrench) calipers 卡规pincers, tongs 夹钳shears 剪子hacksaw 钢锯wire cutters 剪线钳multipurpose pliers,universal pliers 万能手钳adjustable pliers 可调手钳punch 冲子drill 钻chuck 卡盘scraper 三角刮刀reamer 扩孔钻callipergauge 孔径规rivet 铆钉nut 螺母locknut 自锁螺母,防松螺母bolt 螺栓pin, peg, dowel 销钉washer 垫圈staple U形钉oil can 油壶jack 工作服grease gun 注油枪机械加工抛光polishing 安装to assemble 衬套bushing外贸常用机械英语大全Assembly line 组装线Layout 布置图Conveyer 流水线物料板Rivet table 拉钉机Rivet gun 拉钉枪Screw driver 起子Pneumatic screw driver 气动起子worktable 工作桌OOBA 开箱检查fit together 组装在一起fasten 锁紧(螺丝)fixture 夹具(治具)pallet 栈板barcode 条码barcode scanner 条码扫描器fuse together 熔合fuse machine热熔机8repair修理operator作业员QC 品管supervisor 课长ME 制造工程师MT 制造生技cosmetic inspect 外观检查inner parts inspect 内部检查thumb screw 大头螺丝lbs. inch 镑、英寸EMI gasket 导电条front plate 前板rear plate 后板chassis 基座bezel panel 面板power button 电源按键reset button 重置键Hi-pot test of SPS 高源高压测试V oltage switch of SPS 电源电压接拉键sheet metal parts 冲件plastic parts 塑胶件SOP 制造作业程序material check list 物料检查表work cell 工作间trolley 台车carton 纸箱sub-line 支线left fork 叉车personnel resource department 人力资源部production department生产部门planning department企划部QC Section 品管科stamping factory冲压厂painting factory烤漆厂molding factory成型厂common equipment常用设备uncoiler and straightener整平机punching machine 冲床robot机械手hydraulic machine油压机lathe车床planer |plein|刨床miller 铣床grinder磨床linear cutting线切割electrical sparkle电火花welder电焊机staker=reviting machine铆合机position 职务president董事长general manager总经理special assistant manager特助factory director厂长department director部长deputy manager | =vice manager 副理sectio n supervisor课长deputy section supervisor =vice section supe risor副课长group leader/supervisor组长line supervisor线长assistant manager助理to move, to carry, to handle搬运be put in storage入库pack packing包装to apply oil 擦油to file burr 锉毛刺final inspection终检to connect material接料to reverse material 翻料wet station沾湿台Tiana天那水cleaning cloth抹布to load material上料to unload material卸料to return material/stock to退料scraped |\\'skr?pid|报废scrape ..v.刮;削deficient purchase来料不良manufacture procedure制程deficient manufacturing procedure制程不良oxidation |\\' ksi\\'dei?n|氧化scratch刮伤dents压痕defective upsiding down抽芽不良defective to staking铆合不良embedded lump镶块feeding is not in place送料不到位stamping-missing漏冲production capacity生产力education and training教育与训练9proposal improvement提案改善spare parts=buffer备件forklift叉车trailer=long vehicle拖板车外贸常用机械英语大全(续)compound die合模die locker锁模器pressure plate=plate pinch压板bolt 螺栓administration/general affairs dept总务部automatic screwdriver电动启子thickness gauge厚薄规gauge(or jig)治具power wire电源线buzzle蜂鸣器defective product label不良标签identifying sheet list 标示单location地点present members出席人员subject主题conclusion结论decision items决议事项responsible department负责单位pre-fixed finishing date预定完成日approved by / checked by / prepared by核准/ 审核/承办PCE assembly production schedule sheet PCE 组装厂生产排配表model 机锺work order工令revision版次remark备注production control confirmation生产确认checked by初审approved by核准department部门stock age analysis sheet 库存货龄分析表on-hand inventory现有库存available material良品可使用obsolete material良品已呆滞to be inspected or reworked 待验或重工total 合计cause description原因说明part number/ P/N 料号type形态item/group/class类别quality品质prepared by制表notes说明year-end physical inventory difference analysis sheet 年终盘点差异分析表physical inventory盘点数量physical count quantity帐面数量difference quantity差异量cause analysis原因分析raw materials原料materials物料finished product成品semi-finished product半成品packing materials包材good product/accepted goods/ acceptedparts/good parts良品defective product/non-good parts不良品disposed goods 处理品warehouse/hub仓库on way location在途仓oversea location海外仓spare parts physical inventory list备品盘点清单spare molds location模具备品仓skid/pallet 栈板tox machine自铆机wire EDM线割EDM放电机coil stock卷料sheet stock片料tolerance工差score=groove压线cam block滑块pilot 导正筒trim 剪外边pierce剪内边drag form压锻差pocket for the punch head挂钩槽slug hole 废料孔10feature die公母模expansion dwg展开图radius半径shim(wedge)楔子torch-flame cut火焰切割set screw止付螺丝form block折刀stop pin 定位销round pierce punch=die button圆冲子shape punch=die insert异形子stock locater block定位块under cut=scrap chopper清角active plate活动板baffle plate挡块cover plate盖板male die公模female die母模groove punch压线冲子air-cushion eject-rod气垫顶杆spring-box eject-plate弹簧箱顶板bushing block 衬套insert 入块club car高尔夫球车capability能力parameter参数factor系数phosphate皮膜化成viscosity涂料粘度alkalidipping脱脂main manifold主集流脉blanking穿落模dejecting顶固模demagnetization去磁;消磁high-speed transmission高速传递heat dissipation热传rack上料degrease脱脂rinse水洗alkaline etch龄咬desmut 剥黑膜D.I. rinse纯水次Chromate铬酸处理Anodize阳性处理seal封孔revision版次part number/P/N料号good products良品scraped products报放心品defective products不良品finished products成品disposed products处理品barcode条码flow chart流程表单assembly组装stamping冲压molding成型spare parts=buffer备品coordinate座标dismantle the die折模auxiliary fuction辅助功能poly-line多义线heater band 加热片thermocouple热电偶sand blasting喷沙grit 砂砾derusting machine除锈机degate打浇口dryer烘干机induction 感应induction light 感应光response=reaction=interaction感应ram连杆edge finder巡边器concave凸short 射料不足nick缺口speck瑕??shine亮班splay 银纹gas mark焦痕delamination起鳞cold slug冷块blush 导色gouge沟槽;凿槽satin texture段面咬花witness line证示线patent专利grit 沙砾granule=peuet=grain细粒11grit maker抽粒机cushion缓冲magnalium 镁铝合金magnesium镁金metal plate钣金lathe车mill 锉plane刨grind磨drill 铝boring镗blinster 气泡fillet 镶;嵌边through-hole form通孔形式voller pin formality滚针形式cam driver铡楔shank摸柄crank shaft曲柄轴augular offset角度偏差velocity速度production tempo生产进度现状torque扭矩spline=the multiple keys 花键quenching淬火tempering回火annealing退火carbonization碳化tungsten high speed steel钨高速的moly high speed steel钼高速的organic solvent有机溶剂bracket小磁导liaison 联络单volatile 挥发性resistance电阻ion 离子titrator滴定仪beacon警示灯coolant冷却液crusher破碎机机械类常用英语:生产类PCS Pieces 个(根,块等)PRS Pairs 双(对等)CTN Carton 卡通箱PAL Pallet/skid 栈板PO Purchasing Order 采购订单MO Manufacture Order 生产单D/C Date Code 生产日期码ID/C Identification Code (供应商)识别码SWR Special Work Request 特殊工作需求L/N Lot Number 批号P/N Part Number 料号阀门种类英汉术语对照Air valves 空气阀门Angle Stop valves 角式截止阀Angle Throttle Valves 角式节流阀Angle Type Globe Valves 门角式截止阀Ash valves 排灰阀Aspirating valves 吸(抽)气阀Auxiliary valves 辅助(副)阀Balance valves 平衡阀Bellows valves 波纹管阀Blowdown valves 泄料(放空,排污)阀Brake valves 制动阀Butterfly Type Non-slam Check 蝶式缓冲止回阀Butterfly Valves with Gear Actuator 蜗轮传动蝶阀Buttwelding valves 对焊连接阀Clamp valves 对夹式阀门Cock 二通Combination valves 组合阀CQ Thread Ball Valves CQ螺纹球阀Culvert valves 地下管道阀Deceleration valves 减速阀Diaphragm Valves 隔膜阀Decompression valves 泄压阀Double Disc Flat Gate Valves 双闸板平板闸阀Double Disk Parallel Gate V alves明杆平行式双闸板闸板Double Opening Exhaust Valves 双口排气球12Drainage valves 排水阀Electric Actuated Stop V alves 电动截止阀Electric Actuated Wedge Gate Valves 电动楔式闸阀Electric Double Disk Parallel Gate Valve s 电动平行式双闸板闸板Emergeny Cut-off Valves 紧急切断阀Exhaust valves 排气阀Free Float Type Steam Trap 浮球式疏水阀Flange Ball Valves 法兰球阀Flange Gate Valves 法兰闸阀Flange Globe Valves 法兰截止阀Gauge Valves 仪表阀Hand-operated valves 手动阀Hard Seal Butterfly Valves 金属密封碟阀High Temperature Pressure Power Statio n Gate Valves 高温高压电站闸阀High Temperature Pressure Power Statio n Globe Valves 高温高压电站截止阀Hydraulic relay valves 液压继动阀Lift Check Valves 升降式止回阀Lift Check Valves 升降式止回阀Limit valves 限位阀Lining Ball Valves 衬里球阀Lining Butterfly Valves 衬里碟阀Lining Check Valves 衬里止回阀Lining Cock 衬里二通Lining Globe Valves 衬里截止阀Lining T-Cock Valves 衬里三通旋塞阀Liquid Indicator 液位计LPG Pipe Fitting 液化气管件Magnetic Co-operate Globe Valves 磁耦合截止阀Magnetism Forle Pumps 磁力泵Manual Oil Pumps Valves 手摇油泵(阀) Meter Needle Type Globe Valves 仪表针形截止阀Oblique Stop Valves 直流式截止阀Parallel Slide Valves 浆液阀Pintle valve 针形阀Piping Centrifugal Pumps 管道离心泵Plunger valves 柱塞阀Pressure valve 压力(増压)阀Piping Pumps 管道泵Piping Safety Valves 管道安全阀Plunger Globe Valves 柱塞截止阀Quick Draining Valves 快速排污阀Restrictor Valves 过流阀(或节流阀) Safety Valves 安全阀Screw Pumps 螺杆泵Scum Gate Valves 排渣闸阀Solenoid valves 电磁阀Single Disc Flat Gate Valves 单闸板平板闸阀Single Opening Exhaust Valves 单口排气球Slurry Pumps 泥浆泵Stop Valves 截止阀Strainer 过滤器Submerged Motor Pumps 潜水电泵(排污泵)Swing Check Valves 旋启式止回阀Swing Check Valves 旋启式止回阀Tank Lorry Ball Valves 槽车球阀T-Cock 三通Thin Gate Valves 薄型闸阀Throttle Valves 节流阀Tiny Drag Slow Shut Check Valves 微阻缓闭止回阀Triple (tee) valves 三通阀Two-way valves 二通阀Under Water Pumps 液下泵Vacuum Pumps 水力喷射器(真空泵)Vertical Lift Check Valves 立式止回阀Wafer Check Valves 对夹式止回阀Wafer plate valves 对夹蝶板阀Wafer Type Butterfly Valves with Rubber Itning对夹式衬胶蝶阀Waste Valves 排污箱(阀)Water Seal Gate Valves 水封闸阀Wedge Gate Valves 楔式闸阀Y Type and Cylinder Filters Y型筒型过滤器阀门零部件英汉术语对照Axis Guide 轴套Ball 球、球芯13Ball seat 密封圈Blowdown Sealing Face 启、阀件密封面Body 阀体Bonnet 阀盖Disc 阀瓣Mut 螺母Screw 螺栓Sealing 密封件Spring 弹簧Stem 阀杆Stem Mut 阀杆螺母Stem seal 填料Wedge Disc 闸板阀门规范技术英语术语对照Applicable medium 适用介质Applicable temperature 适用温度Butt Clamp 对夹Chemical analysis 化学成份Connecting format 连接形式Double disc 双闸板Flexible disc 弹性闸板Flange 法兰Hoop 卡箍Inside thread 内螺纹Jacket 夹套Mains 电源Material chemical analysis and mechanical capacity材料化学成份和机械性能materials 材料Materials for main parts 主要零件材料Mechanical capacity 机械性能Max. Discharging Capacity 最大排水量Max. Operating Temperature 最高工作温度Max. Allowable Temperature 最高允许温度Max. Allowable Pressure 最高允许压力Model 型号Name of parts 零件名称nitrogen (N) 氮Nominal bore 公称通径Nominal Pressure 公称压力Nozzle 排气口Outside thread 外螺纹Oxidant 氧化性介质Parallel 平行Piping 管路Piston 活塞Reductant 还原性介质Rising stem 明杆Seal 阀座,密封面Seat testing pressure 压力气密封试验压力Socket 卡套Specifications 性能规范Single disc 单闸板Solid 刚性Strengh testing pressure 强度试验压力Steam , condensate 蒸汽,凝结水Stroke 冲程,行程Water,oil,steam 水,温度,气Wedge 楔式Welding 焊接阀门材质术语英汉对照Atbas metal 镍铬钢Buna-N rubber 丁晴橡胶Casting aluminium brass 铸铝黄铜Casting aluminium bronze 铸铝青铜Ceramic metal 陶瓷金属Chromel alloy 镍铬合金CHR rubber 氯晴橡胶Chrominm-molybdenum-vanadium steel 铬钼钒钢Chromium stainless steel 铬不锈钢Chromium-molybdenum steel 铬钼钢Corrugation pad 波形垫Cuprum alloy 铜合金Ductile Cast iron 球墨铸铁Expanded graphite 柔性石墨Fine Steel Casting iron 优质碳素钢Fluorous rubber 氟橡胶Gray Cast iron 灰铸铁Hayne's alloy 钴铬钨合金High tem perature steel 高温钢Monel 蒙乃尔合金Low temperature steel 低温钢Nylon 尼龙塑料Polytetrafluoroethylene(PTEF) 聚四氟乙烯Polythene 聚乙烯Pure aluminium 纯铝Pure cupper 纯铜14Rubber graphite board 橡胶石墨板Spring steel 弹簧钢Stainless acid-resisting steel 不锈耐酸钢Stainless and Graphite 不锈钢/石墨Stainless steel 不锈钢Steel Casting iron 碳素钢铸件Shell Test Pressure 壳体试验压力Service Fluid 工作介质机械类常用英语:钢材类alloy tool steel 合金工具钢aluminium allo y 铝合金钢bearing alloy 轴承合金blister steel 浸碳钢bonderized steel sheet 邦德防蚀钢板carbon tool steel 碳素工具钢clad sheet 被覆板clod work die steel 冷锻模用钢emery 金钢砂ferrostatic pressure 钢铁水静压力forging die steel 锻造模用钢galvanized ste el sheet 镀锌铁板hard alloy steel 超硬合金钢high speed too l steel 高速度工具钢hot work die steel 热锻模用钢low alloy to ol steel 特殊工具钢low manganese casting steel 低锰铸钢marg ing steel 马式体高强度热处理钢martrix alloy 马特里斯合金meehanite castiron 米汉纳铸钢meehanite metal 米汉纳铁merchant iron 市售钢材molybdenum high speed steel 钼系高速钢molybdenum steel 钼钢nickel chromium steel 镍铬钢prehardened steel 顶硬钢silicon steel sheet 矽钢板stainless steel 不锈钢tin plated steel sheet 镀锡铁板tough pitch copper 韧铜troostite 吐粒散铁tungsten steel ?钢vinyl tapped steel sheet 塑胶覆面钢板塑件模具相关英文compre sion molding压缩成型flash mold 溢流式模具plsitive mold 挤压式模具split mold 分割式模具cavity型控母模core模心公模taper锥拔leather cloak仿皮革shiver饰纹flow mark流痕welding mark溶合痕post screw insert螺纹套筒埋值self tapping screw自攻螺丝striper plate脱料板piston 活塞cylinder汽缸套chip细碎物handle mold手持式模具encapsulation molding低压封装成型、射出成型用模具two plate两极式(模具)well type蓄料井insulated runner绝缘浇道方式hot runner热浇道runner plat浇道模块valve gate阀门浇口band heater环带状的电热器spindle 阀针spear head刨尖头slag well冷料井cold slag冷料渣air vent排气道welding line熔合痕eject pin顶出针knock pin顶出销return pin回位销反顶针sleave套筒stripper plate脱料板insert core放置入子runner stripper plate浇道脱料板15guide pin 导销eject rod (bar)(成型机)顶业捧subzero深冷处理three plate三极式模具runner system浇道系统stress crack应力电裂orientation定向sprue gate射料浇口,直浇口nozzle射嘴sprue lock pin料头钩销(拉料杆) slag well冷料井side gate侧浇口edge gate侧缘浇口tab gate搭接浇口film gate薄膜浇口flash gate闸门浇口slit gate 缝隙浇口fan gate扇形浇口dish gate因盘形浇口diaphragm gate隔膜浇口ring gate环形浇口subarine gate潜入式浇口tunnel gate隧道式浇口pin gate针点浇口Runner less无浇道(sprue less)无射料管方式long nozzle 延长喷嘴方式sprue浇口;溶渣机械工程专业英语翻译第一课机械工程专业英语概述English in Mechanical Engineering一、专业英语概述1. 什么是翻译:翻译就是将一种语言文字的意义用另一种语言文字表达出来。
冲压类外文翻译、中英文翻译--冲压变形
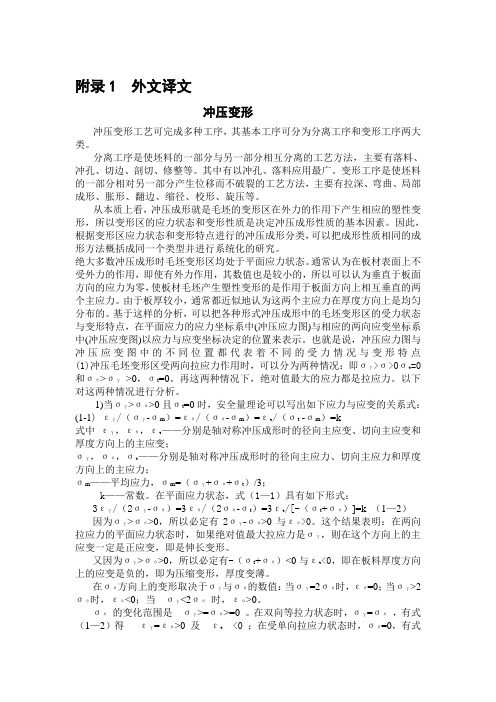
附录1 外文译文冲压变形冲压变形工艺可完成多种工序,其基本工序可分为分离工序和变形工序两大类。
分离工序是使坯料的一部分与另一部分相互分离的工艺方法,主要有落料、冲孔、切边、剖切、修整等。
其中有以冲孔、落料应用最广。
变形工序是使坯料的一部分相对另一部分产生位移而不破裂的工艺方法,主要有拉深、弯曲、局部成形、胀形、翻边、缩径、校形、旋压等。
从本质上看,冲压成形就是毛坯的变形区在外力的作用下产生相应的塑性变形,所以变形区的应力状态和变形性质是决定冲压成形性质的基本因素。
因此,根据变形区应力状态和变形特点进行的冲压成形分类,可以把成形性质相同的成形方法概括成同一个类型并进行系统化的研究。
绝大多数冲压成形时毛坯变形区均处于平面应力状态。
通常认为在板材表面上不受外力的作用,即使有外力作用,其数值也是较小的,所以可以认为垂直于板面方向的应力为零,使板材毛坯产生塑性变形的是作用于板面方向上相互垂直的两个主应力。
由于板厚较小,通常都近似地认为这两个主应力在厚度方向上是均匀分布的。
基于这样的分析,可以把各种形式冲压成形中的毛坯变形区的受力状态与变形特点,在平面应力的应力坐标系中(冲压应力图)与相应的两向应变坐标系中(冲压应变图)以应力与应变坐标决定的位置来表示。
也就是说,冲压应力图与冲压应变图中的不同位置都代表着不同的受力情况与变形特点(1)冲压毛坯变形区受两向拉应力作用时,可以分为两种情况:即σγ>σ>0σt=0和σθ>σγ>0,σt=0。
再这两种情况下,绝对值最大的应力都是拉应力。
以下对这两种情况进行分析。
1)当σγ>σθ>0且σt=0时,安全量理论可以写出如下应力与应变的关系式:(1-1) εγ/(σγ-σm)=εθ/(σθ-σm)=εt/(σt -σm)=k式中εγ,εθ,εt——分别是轴对称冲压成形时的径向主应变、切向主应变和厚度方向上的主应变;σγ,σθ,σt——分别是轴对称冲压成形时的径向主应力、切向主应力和厚度方向上的主应力;σm——平均应力,σm=(σγ+σθ+σt)/3;k——常数。
冲压翻译1-zrg

第一节冲模的精度判断对于模具精度,一般把产品的尺寸精度或者形状精度作为标准运用。
公差要求严格的产品,比如IC引线框或者连接器等需要高精度的产品,所以应该认识加工它的高精度模具(为了加工这些精度需要较高的产品,我们大家都知道对模具的精度要求也是很高的)。
这个观点应该没人反对吧。
那么,这样的模具的高精度在哪里呢?(那这样的模具的哪一部分是高精度的呢)由于产品是临摹冲子和刀口的形状,通过对冲子和刀口的形状进行轮廓研磨加工(PG加工)及电火花线切割(W/EDM)等多重切割方式,制作出良好精度的形状进行使用。
的确地,对应产品尺寸公差的冲子和刀口的形状制作,能说是判断精度的一个重要因素。
冲子、刀口形状的制作,也是在必要的情况下为了保持间隙。
产品的产量厚度太薄的话,下料的间隙比例就会变小。
为了使这个达成一致是相当有难度的(为了维持间隙均衡)。
因此,即使产品的形状尺寸的公差较大,但是对于薄材加工,为了维持较小间隙,冲子、刀口形状的制作方法,以及维持对模具内组装位置的高精度都是有必要的。
可以说产品材料厚度也是观察模具精度的“标准”。
关于产品的形状精度,如果材料厚度变得较薄的话,稍有打偏(变化)就会失常(材料较薄的话,一点点的间隙变化就会使产品形状发生变化)。
因此,冲子、刀口形状的制作很重要。
凭借冲子、刀口形状的制作,可以达到满意的部品。
由于,冲子、刀口装置在上模和下模,为了上下模之间的合模精度制作出的导柱和导套,间接地给模具精度带来了重要的作用。
如果能考虑用脱料板引导冲子,脱料板(内部导套)或者卸料螺栓以及弹簧等的制作也能关联起来。
不明确“标准”,就没有讨论模具精度的意向。
比如,内部导套应该在哪之类的。
根据精度要求,使用部品也好组装方法也好都要随之改变。
在没有明确要求的内容下即使看到了加工好的那样的模具,也很难说是高精度模具。
明确前提的话就容易明白。
比如,加工薄材的前提下考虑模具的话,间隙小→冲子·刀口的形状精度/表面粗糙度→冲子、刀口的位置精度→通过联想导杆的制作,模具应有的形状就浮现出来了。
- 1、下载文档前请自行甄别文档内容的完整性,平台不提供额外的编辑、内容补充、找答案等附加服务。
- 2、"仅部分预览"的文档,不可在线预览部分如存在完整性等问题,可反馈申请退款(可完整预览的文档不适用该条件!)。
- 3、如文档侵犯您的权益,请联系客服反馈,我们会尽快为您处理(人工客服工作时间:9:00-18:30)。
附录1 外文译文冲压变形冲压变形工艺可完成多种工序,其基本工序可分为分离工序和变形工序两大类。
分离工序是使坯料的一部分与另一部分相互分离的工艺方法,主要有落料、冲孔、切边、剖切、修整等。
其中有以冲孔、落料应用最广。
变形工序是使坯料的一部分相对另一部分产生位移而不破裂的工艺方法,主要有拉深、弯曲、局部成形、胀形、翻边、缩径、校形、旋压等。
从本质上看,冲压成形就是毛坯的变形区在外力的作用下产生相应的塑性变形,所以变形区的应力状态和变形性质是决定冲压成形性质的基本因素。
因此,根据变形区应力状态和变形特点进行的冲压成形分类,可以把成形性质相同的成形方法概括成同一个类型并进行系统化的研究。
绝大多数冲压成形时毛坯变形区均处于平面应力状态。
通常认为在板材表面上不受外力的作用,即使有外力作用,其数值也是较小的,所以可以认为垂直于板面方向的应力为零,使板材毛坯产生塑性变形的是作用于板面方向上相互垂直的两个主应力。
由于板厚较小,通常都近似地认为这两个主应力在厚度方向上是均匀分布的。
基于这样的分析,可以把各种形式冲压成形中的毛坯变形区的受力状态与变形特点,在平面应力的应力坐标系中(冲压应力图)与相应的两向应变坐标系中(冲压应变图)以应力与应变坐标决定的位置来表示。
也就是说,冲压应力图与冲压应变图中的不同位置都代表着不同的受力情况与变形特点(1)冲压毛坯变形区受两向拉应力作用时,可以分为两种情况:即σγ>σ>0σt=0和σθ>σγ>0,σt=0。
再这两种情况下,绝对值最大的应力都是拉应力。
以下对这两种情况进行分析。
1)当σγ>σθ>0且σt=0时,安全量理论可以写出如下应力与应变的关系式:(1-1) εγ/(σγ-σm)=εθ/(σθ-σm)=εt/(σt -σm)=k式中εγ,εθ,εt——分别是轴对称冲压成形时的径向主应变、切向主应变和厚度方向上的主应变;σγ,σθ,σt——分别是轴对称冲压成形时的径向主应力、切向主应力和厚度方向上的主应力;σm——平均应力,σm=(σγ+σθ+σt)/3;k——常数。
在平面应力状态,式(1—1)具有如下形式:3εγ/(2σγ-σθ)=3εθ/(2σθ-σt)=3εt/[-(σt+σθ)]=k (1—2)因为σγ>σθ>0,所以必定有2σγ-σθ>0与εθ>0。
这个结果表明:在两向拉应力的平面应力状态时,如果绝对值最大拉应力是σγ,则在这个方向上的主应变一定是正应变,即是伸长变形。
又因为σγ>σθ>0,所以必定有-(σt+σθ)<0与εt<0,即在板料厚度方向上的应变是负的,即为压缩变形,厚度变薄。
在σθ方向上的变形取决于σγ与σθ的数值:当σγ=2σθ时,εθ=0;当σγ>2σθ时,εθ<0;当σγ<2σθ时,εθ>0。
σθ的变化范围是σγ>=σθ>=0 。
在双向等拉力状态时,σγ=σθ,有式(1—2)得εγ=εθ>0 及εt <0 ;在受单向拉应力状态时,σθ=0,有式(2—2)可得,εθ=-εγ/2。
根据上面的分析可知,这种变形情况处于冲压应变图中的AON范围内(见图1—1);而在冲压应力图中则处于GOH范围内(见图1—2)。
(1)当σθ>σγ>0且σt=0时,有式(1—2)可知:因为σθ>σγ>0,所以1)定有2σθ>σγ>0与εθ>0。
这个结果表明:对于两向拉应力的平面应力状态,当σθ的绝对值最大时,则在这个方向上的应变一定时正的,即一定是伸长变形。
又因为σγ>σθ>0,所以必定有-(σt+σθ)<0与εt<0,即在板料厚度方向上的应变是负的,即为压缩变形,厚度变薄。
在σθ方向上的变形取决于σγ与σθ的数值:当σθ=2σγ时,εγ0;当σθ>σγ,εγ<0;当σθ<2σγ时,εγ>0。
σγ的变化范围是σθ>= σγ>=0 。
当σγ=σθ时,εγ=εθ>0,也就是在双向等拉力状态下,在两个拉应力方向上产生数值相同的伸长变形;在受单向拉应力状态时,当σγ=0时,εγ=-εθ/2,也就是说,在受单向拉应力状态下其变形性质与一般的简单拉伸是完全一样的。
这种变形与受力情况,处于冲压应变图中的AOC范围内(见图1—1);而在冲压应力图中则处于AOH范围内(见图1—2)。
上述两种冲压情况,仅在最大应力的方向上不同,而两个应力的性质以及它们引起的变形都是一样的。
因此,对于各向同性的均质材料,这两种变形是完全相同的。
(1)冲压毛坯变形区受两向压应力的作用,这种变形也分两种情况分析,即σγ<σθ<σt=0和σθ<σγ<0,σt=0。
1)当σγ<σθ<0且σt=0时,有式(1—2)可知:因为σγ<σθ<0,一定有2σγ-σθ<0与εγ<0。
这个结果表明:在两向压应力的平面应力状态时,如果绝对值最大拉应力是σγ<0,则在这个方向上的主应变一定是负应变,即是压缩变形。
又因为σγ<σθ<0,所以必定有-(σt+σθ)>0与εt>0,即在板料厚度方向上的应变是正的,板料增厚。
在σθ方向上的变形取决于σγ与σθ的数值:当σγ=2σθ时,εθ=0;当σγ>2σθ时,εθ<0;当σγ<2σθ时,εθ>0。
这时σθ的变化范围是σγ与0之间。
当σγ=σθ时,是双向等压力状态时,故有εγ=εθ<0;当σθ=0时,是受单向压应力状态,所以εθ=-εγ/2。
这种变形情况处于冲压应变图中的EOG范围内(见图1—1);而在冲压应力图中则处于COD范围内(见图1—2)。
2) 当σθ<σγ<0且σt=0时,有式(1—2)可知:因为σθ<σγ<0,所以一定有2σθσγ<0与εθ<0。
这个结果表明:对于两向压应力的平面应力状态,如果绝对值最大是σθ,则在这个方向上的应变一定时负的,即一定是压缩变形。
又因为σγ<σθ<0,所以必定有-(σt+σθ)>0与εt>0,即在板料厚度方向上的应变是正的,即为压缩变形,板厚增大。
在σθ方向上的变形取决于σγ与σθ的数值:当σθ=2σγ时,εγ=0;当σθ>2σγ,εγ<0;当σθ<2σγ时,εγ>0。
这时,σγ的数值只能在σθ<= σγ<=0 之间变化。
当σγ=σθ时,是双向等压力状态,所以εγ=εθ<0;当σγ=0时,是受单向压应力状态,所以有εγ=-εθ/2>0。
这种变形与受力情况,处于冲压应变图中的GOL范围内(见图1—1);而在冲压应力图中则处于DOE范围内(见图1—2)。
(1)冲压毛坯变形区受两个异号应力的作用,而且拉应力的绝对值大于压应力的绝对值。
这种变形共有两种情况,分别作如下分析。
1)当σγ>0,σθ<0及|σγ|>|σθ|时,由式(1—2)可知:因为σγ>0,σθ<0及|σγ|>|σθ|,所以一定有2σγ-σθ>0及εγ>0。
这个结果表明:在异号的平面应力状态时,如果绝对值最大应力是拉应力,则在这个绝对值最大的拉应力方向上应变一定是正应变,即是伸长变形。
又因为σγ>0,σθ<0及|σγ|>|σθ|,所以必定有εθ<0,即在板料厚度方向上的应变是负的,是压缩变形。
这时σθ的变化范围只能在σθ=-σγ与σθ=0的范围内。
当σθ=-σγ时,εγ>0εθ<0且|εγ|=|εθ|;当σθ=0时,εγ>0,εθ<0,而且εθ=-εγ/2,这是受单向拉的应力状态。
这种变形情况处于冲压应变图中的MON范围内(见图1—1);而在冲压应力图中则处于FOG范围内(见图1—2)。
2)当σθ>0,σγ<0,σt=0及|σθ|>|σγ|时,由式(1—2)可知:用与前项相同的方法分析可得εθ>0。
即在异号应力作用的平面应力状态下,如果绝对值最大应力是拉应力σθ,则在这个方向上的应变是正的,是伸长变形;而在压应力σγ方向上的应变是负的(εγ<=0),是压缩变形。
这时σγ的变化范围只能在σγ=-σθ与σγ=0的范围内。
当σγ=-σθ时,εθ>0,εγ<0且|εγ|=|εθ|;当σγ=0时,εθ>0,εγ<0,而且εγ=-εθ/2。
这种变形情况处于冲压应变图中的COD范围内(见图1—1);而在冲压应力图中则处于AOB范围内(见图1—2)。
虽然这两种情况的表示方法不同,但从变形的本质看是一样的。
(1)冲压毛坯变形区受两个方向上的异号应力的作用,而且压应力的绝对值大于拉应力的绝对值。
以下对这种变形的两种情况分别进行分析。
1)当σγ>0,σθ<0而且|σθ|>|σγ|时,由式(1—2)可知:因为σγ>0,σθ<0及|σθ|>|σγ|,所以一定有2σθ- σγ<0及εθ<0。
这个结果表明:在异号的平面应力状态时,如果绝对值最大应力是压应力σθ,则在这个方向上应变是负的,即是压缩变形。
又因为σγ>0,σθ<0,必定有2σγ- σθ<0及εγ>0,即在拉应力方向上的应变是正的,是伸长变形。
这时σγ的变化范围只能在σγ=-σθ与σγ=0的范围内。
当σγ=-σθ时,εγ>0εθ<0且εγ=-εθ;当σγ=0时,εγ>0,εθ<0,而且εγ=-εθ/2。
这种变形情况处于冲压应变图中的DOF范围内(见图1—1);而在冲压应力图中则处于BOC范围内(见图1—2)。
2)当σθ>0,σγ<0,σt=0及|σγ|>|σθ|时,由式(1—2)可知:用与前项相同的方法分析可得εγ<σγ0。
即在异号应力作用的平面应力状态下,如果绝对值最大应力是压应力σγ,则在这个方向上的应变是负的,是压缩变形;而在拉应力σθ方向上的应变是正的,是伸长变形。
这时σθ的数值只能介于σθ=-σγ与σθ=0的范围内。
当σθ=-σγ时,εθ>0,εγ<0且εθ=-εγ;当σθ=0时,εθ>0,εγ<0,而且εθ=-εγ/2。
这种变形情况处于冲压应变图中的DOE范围内(见图1—1);而在冲压应力图中则处于BOC范围内(见图1—2)。
这四种变形与相应的冲压成形方法之间是相对的,它们之间的对应关系,用文字标注在图1—1与图1—2上。
上述分析的四种变形情况,相当于所有的平面应力状态,也就是说这四种变形情况可以把全部的冲压变形毫无遗漏地概括为两大类别,即伸长类与压缩类。