8D质量问题解决方法和案例分析
8D案例分析

8D案例分析概述:8D(Eight Disciplines)是一种解决问题的方法,特别适用于复杂问题的追踪和解决。
本文将通过一个实际案例,以分析8D方法的应用过程,帮助读者更好地理解和掌握此方法。
案例背景:某汽车制造公司生产线上出现了连续质量问题,导致产品退货率上升。
公司决定采用8D方法,解决这一问题,并提高生产效率。
D1 - 组建团队:针对该质量问题,公司领导决定成立一个8D团队,并指派一个质量经理担任团队领导。
团队成员包括制造经理、工程师、产品检验员和相关质量控制人员。
D2 - 描述问题:团队首先对问题进行描述,确切指出了产品的退货率上升,以及退货产品的基本特征和数量。
通过与客户的沟通,团队了解到问题主要发生在某一特定型号的发动机。
D3 - 短期解决方案:为了尽快应对问题,团队决定采取短期措施。
他们制定了一项临时方案,主要包括对退货产品进行严格的检查和分类,以及加强现场员工的培训和操作规范。
D4 - 找出根本原因:8D团队利用质量工具,如鱼骨图、5W1H法等,对问题进行深入分析。
最终确定了问题的根本原因是发动机组装工序中存在漏装关键零件的情况。
D5 - 采取纠正措施:确定了根本原因后,团队开始制定纠正措施。
首先,他们与供应商反馈了质量问题,并要求供应商进行改进。
同时,他们还设计了更加严格的工装夹具来确保关键零件的正确安装。
D6 - 验证效果:团队对纠正措施进行实施,并进行效果验证。
经过一段时间的生产检查和产品退货率的跟踪,结果显示退货率明显下降。
D7 - 预防措施:为了预防问题再次发生,团队进一步分析了可能导致问题的其他因素,并制定了一系列预防措施。
这些措施包括制定详细的工艺文件、提供员工培训以及建立质量检测站点等。
D8 - 确认效果:团队定期进行检查和评估,以确认纠正措施的长期效果。
通过追踪产品退货率和质量检查数据,团队发现问题已经完全解决,并且生产线的效率也有所提高。
总结:通过8D方法的应用,该汽车制造公司成功解决了连续质量问题,并取得了显著改善。
现实中的8D改善报告案例2024

引言概述:在现实生活中,8D改善报告是一种常用的问题解决方法。
它通过严谨的分析、合理的行动计划和持续的改善措施,帮助组织快速解决问题,并避免类似问题再次发生。
本文将通过介绍具体的案例,详细阐述8D改善报告的流程以及其在实际中的应用。
正文内容:1. 案例1:产品质量问题1.1 问题描述:某企业生产的某类产品由于设计问题导致一定比例的产品存在质量问题,客户投诉率较高。
1.2 数据收集和分析:收集了客户投诉数据、产品生产记录等相关数据,并进行了充分的数据分析,明确了问题的具体范围和影响。
1.3 原因分析:通过系统的分析方法,确定了产品设计中存在的缺陷以及相关工艺流程的不符合。
1.4 对策制定:制定了具体的对策方案,包括设计修正、工艺优化和检验加强等,以解决产品质量问题。
1.5 实施与效果评估:在实施对策方案的过程中,不断跟踪效果,并对改善效果进行评估,确保问题得到彻底解决和改善。
2. 案例2:供应链问题2.1 问题描述:某企业的供应链管理存在一系列问题,包括供货延迟、物料缺失等,严重影响了生产计划的执行。
2.2 数据收集和分析:通过对供应链各环节的数据收集和分析,确定了问题的具体表现形式和原因。
2.3 原因分析:通过对供应商管理、物料采购等流程进行分析,明确了问题的根本原因,包括供应商能力不足、交流沟通不畅等。
2.4 对策制定:制定了改善供应链问题的具体对策,包括供应商评估优化、加强沟通协作等。
2.5 实施与效果评估:通过实施对策方案,及时解决了供应链问题,并跟踪评估改善效果,确保问题得到全面解决。
3. 案例3:客户投诉处理问题3.1 问题描述:某企业在客户投诉处理方面存在问题,客户反映的问题无法及时得到解决,导致客户满意度下降。
3.2 数据收集和分析:收集了客户投诉数据和处理记录,通过对数据的分析,明确了问题的性质和频率。
3.3 原因分析:通过对投诉处理流程和人员培训情况的分析,找出了导致投诉处理问题的原因,包括流程不规范、人员技能欠缺等。
8D报告案例分析

小组成员: 张三、 李四、 小王。
D2——问题描述:
小王家中被水淹,家中所有摆放在地上的物品 都浸在水中(不良率100%)。
如:草席、被子和书本等。
D2——问题描述:
What
什么问题?/当前状况是什么?
When
问题在何时发生?
Where
问题在何处发生?/有无位置的变化?
2.以后洗蔬菜时一定要把烂蔬菜叶丢到垃圾 筐里,并且要把地面清理干净。
3.早晨洗脸时不能带电话在身上。在洗脸过程 中,就算电话铃响起也不能接。直到洗漱完毕后 才能接听手机。 责任人:小王 预计完成时间:2015年2月10日 验证人:小王老婆
D8——结案并祝贺
1.此问题已经完全处理清楚,可以结案(close)
➢ 丰田汽车公司曾举了一个例子来找出停机的真正原因 ➢ 生产线上的机器总是停转,虽然修过多次但仍不见好转。
于是,就有了以下的问答: ➢ 问“为什么机器停了?”答“因为超过了负荷,保险丝就断了。” ➢ 问“为什么超负荷呢?”答“因为轴承的润滑不够。” ➢ 问“为什么润滑不够?” 答“因为润滑泵吸不上油来。” ➢ 问“为什么吸不上油来?”答“因为油泵轴磨损、松动了。” ➢ 问“为什么磨损了呢?”再答“因为没有安装过滤器,混进了铁屑等杂质。” ➢ 经过连续五次不停地问“为什么”,才找到问题的真正原因和解决的方法,
8D 报 告 案 例 分 析
课堂守则
8D:解决问题的8个步骤
DБайду номын сангаас 问题发生
D1 成立8D 小组
D2 描述问题
D3 实施并验证临 时性纠正措施
D4 确定和验证问 题的根本原因
D8 表彰小组和 个人的贡献
8D报告案例分析
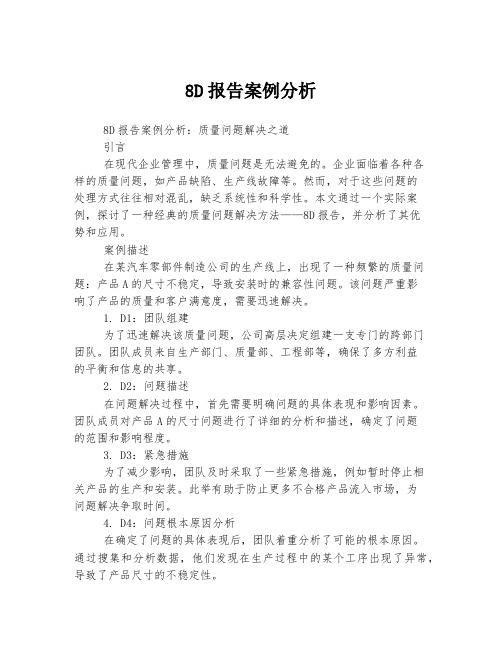
8D报告案例分析8D报告案例分析:质量问题解决之道引言在现代企业管理中,质量问题是无法避免的。
企业面临着各种各样的质量问题,如产品缺陷、生产线故障等。
然而,对于这些问题的处理方式往往相对混乱,缺乏系统性和科学性。
本文通过一个实际案例,探讨了一种经典的质量问题解决方法——8D报告,并分析了其优势和应用。
案例描述在某汽车零部件制造公司的生产线上,出现了一种频繁的质量问题:产品A的尺寸不稳定,导致安装时的兼容性问题。
该问题严重影响了产品的质量和客户满意度,需要迅速解决。
1. D1:团队组建为了迅速解决该质量问题,公司高层决定组建一支专门的跨部门团队。
团队成员来自生产部门、质量部、工程部等,确保了多方利益的平衡和信息的共享。
2. D2:问题描述在问题解决过程中,首先需要明确问题的具体表现和影响因素。
团队成员对产品A的尺寸问题进行了详细的分析和描述,确定了问题的范围和影响程度。
3. D3:紧急措施为了减少影响,团队及时采取了一些紧急措施,例如暂时停止相关产品的生产和安装。
此举有助于防止更多不合格产品流入市场,为问题解决争取时间。
4. D4:问题根本原因分析在确定了问题的具体表现后,团队着重分析了可能的根本原因。
通过搜集和分析数据,他们发现在生产过程中的某个工序出现了异常,导致了产品尺寸的不稳定性。
5. D5:纠正措施在确定了根本原因后,团队制定了一系列纠正措施。
例如,他们重新设计了工序的操作规范,加强了员工培训并引入了更先进的设备。
这些措施旨在消除根本原因并确保产品的稳定尺寸。
6. D6:纠正措施效果验证纠正措施的实施需要验证其有效性。
团队进行了进一步的测试和数据分析,确保新的工序设计和设备引入能够改善产品尺寸的稳定性。
7. D7:预防措施除了解决当前问题,团队还制定了一些预防措施,以避免类似问题再次发生。
这些措施包括对生产过程进行全面审查和改进,加强员工培训,以及建立监控系统等。
8. D8:团队总结与表扬在问题解决后,团队对整个过程进行总结,并表扬了各成员的贡献。
质量分析8d报告案例
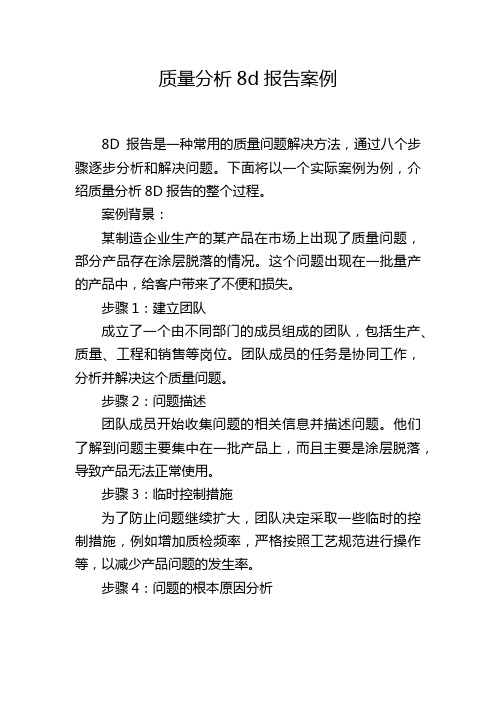
质量分析8d报告案例8D报告是一种常用的质量问题解决方法,通过八个步骤逐步分析和解决问题。
下面将以一个实际案例为例,介绍质量分析8D报告的整个过程。
案例背景:某制造企业生产的某产品在市场上出现了质量问题,部分产品存在涂层脱落的情况。
这个问题出现在一批量产的产品中,给客户带来了不便和损失。
步骤1:建立团队成立了一个由不同部门的成员组成的团队,包括生产、质量、工程和销售等岗位。
团队成员的任务是协同工作,分析并解决这个质量问题。
步骤2:问题描述团队成员开始收集问题的相关信息并描述问题。
他们了解到问题主要集中在一批产品上,而且主要是涂层脱落,导致产品无法正常使用。
步骤3:临时控制措施为了防止问题继续扩大,团队决定采取一些临时的控制措施,例如增加质检频率,严格按照工艺规范进行操作等,以减少产品问题的发生率。
步骤4:问题的根本原因分析团队成员使用常用的质量工具(如鱼骨图、5W1H分析等)进行问题的根本原因分析。
他们发现问题可能与涂层工艺、原材料质量等因素有关。
步骤5:制定长期解决方案基于问题的根本原因分析,团队成员制定了长期解决方案。
他们决定对涂层工艺进行优化,对原材料质量进行更加严格的控制。
同时,还计划对生产工艺进行改进,以提高产品的质量和可靠性。
步骤6:验证解决方案为了验证解决方案的有效性,团队进行了一系列实验和测试。
他们使用不同的涂层工艺和原材料质量进行生产,并对产品进行测试。
结果表明,解决方案确实有效,产品的质量得到了显著提升。
步骤7:实施长期解决方案基于验证结果,团队决定全面实施长期解决方案。
他们对生产流程进行调整,更新工艺规范,并与供应商合作加强原材料质量监控。
步骤8:预防措施为了防止类似问题的再次发生,团队制定了一系列预防措施。
他们决定加强内部培训,提高员工的质量意识和技能水平。
此外,还计划开展定期的质量检查和审查,以及建立质量指标和绩效评估体系。
通过以上八个步骤,团队成功解决了产品质量问题,并采取了一系列措施防止问题的再次发生。
8D质量问题解决方法与案例分析

8D质量问题解决方法和案例分析
质量问题解决的常用方法和流程
D1 成立8D小组 D2 描述问题 D3 遏制问题
D4 根本原因分析 D5 临时措施
D6 长期措施 D7 系统性预防问
题再发生
(8D) D1:成立一个小组, 成员具备工艺/产品知识及能解决问题和实施纠正措施的素质,
并指定一个组长;
8D质量问题解决方 法和案例分析
8D质量问题解决方法和案例分析
❖第二版更新内容说明
1, D4根本原因分析中增加对根本原因按产 生和流出二个方面分析的要求 2,D8 祝贺小组改为总结表彰
3,增加8D分析报告格式PPT版本和EXCEL 版本格式
8D质量问题解决方法和案例分析
➢ 目的及适用范围 ➢ 质量问题解决常用方法和流程 ➢ 8D与5Why方法 ➢ 案例分享和讨论 ➢ 课堂练习和点评 ➢8D报告格式
8D质量问题解决方法和案例分析
目录
目的及适用范围
目的
在公司内部形成标准化的问题分析
解决方法;
培训相关岗位人员,确保正确应用;
提高管理人员的问题分析解决能力;
分享最佳质量问题解决案例
所有管理者,需要面对并解决 随时可能出现的质量问题;
适用范围
8D质量问题解决方法和案例分析
质量问题解决常用方法和流程
8D质量问题解决方法和案例分析
传统的方法
问题
不采用
解决方法 “快速解决“
寻找根本原因的方法-5Why
系统方法
问题
采用
Why Why
Why Why
Why
解决方法 一劳永逸
系统的方法并不急于立即解决问题,而是立足于揭示问题根源,找出长期的对策。
8D报告以和案例分析

字模冲子修模时 未依图面配置
跳屑造成迭料
模具
字模高度设计 安全系数尺寸 偏低
字模磨损
材料
材料厚度 0.3±0.01
三. 临时对策:
3.1.对嫌疑品全部重工
在途物流 厂内
sorting日期 11/23 11/24 11/24
不良率 52/18,000= 0.28% 40/9,000= 0.44% 22/61,300 =0.03%
D2: 问题描述
• 从客户观点来描述问题,他们看到什么? 照片or 寄 不良样品回来分析 .
• 阐明全部客户提供之数据. • 涵盖范围 ? Lot No?批号?Date Code?制造日期? • 问题有多严重 ? 不良数?不良率? • 是制造还是设计旳问题 ? 层别法 - 模号? • 阐明规格之要求. • 阐明电子,机械验证,及任何失效分析之成果. • 所报告旳问题是真正旳问题吗?连续问5次为何. 重工, 全检 ,报废 .若要 重工或全检 , 有执行旳原则吗 ?
• 详述检验措施, 措施可行吗?有作有效性验 证吗?
• 紧急对策引起其他问题吗?
• 紧急对策进行中?已完毕? 注意时效.
• 检验/测试/分析成果阐明. 详列检验数,不良 数,不良率.
D4:原因分析
• 详列永久对策旳运营时间表.
D6:效果验证
• 验证紧急对策及永久对策之有效性,应以 量化表达验证成果(如:Cpk值可达1.33, 或不良发生率降至 0 等).
• 在永久对策验证有效之前,应连续进行紧 急对策.
• 追踪永久对策执行后之品质推移情况. • 在没有完全把握问题已彻底处理之前 , 不
要轻率旳结案 .
不良品生产日期
11/4 11/7 11/19,11/20
8d报告案例范文

8D报告案例:汽车制造业中的质量问题解决1. 案例背景汽车制造业是一个竞争激烈的行业,汽车制造商需要不断提高产品质量以满足市场需求。
然而,由于生产过程中的各种原因,质量问题时常出现。
这就需要制造商采取措施解决问题,以降低不良率,提高产品质量。
本案例以某汽车制造商的一个具体质量问题为背景,展示了如何使用8D报告方法解决质量问题。
2. 案例过程2.1 问题发现在该汽车制造商的生产线上,某一型号的汽车在组装过程中出现了一定比例的漏油问题。
漏油问题不仅影响了汽车的外观和品质,还可能导致机械故障,给消费者带来不便和安全隐患。
因此,该问题被认为是一个严重的质量问题,需要尽快解决。
2.2 问题分析制造商成立了一个专门的团队来分析漏油问题。
团队首先进行了现场调查,观察了漏油现象发生的具体情况,并收集了相关数据和样本。
通过对数据和样本的分析,团队发现漏油问题主要发生在某一特定的组装工序中。
进一步的分析表明,问题可能是由于该工序使用的密封胶出现了质量问题,导致密封不完全,从而引起漏油。
2.3 制定解决方案基于问题分析的结果,团队制定了以下解决方案:1.更换密封胶供应商:通过与多家供应商的沟通和评估,选择一家质量可靠的密封胶供应商,以确保密封胶的质量稳定。
2.优化工艺参数:对组装工序的工艺参数进行优化,确保密封胶的使用量和施工方式合理,从而提高密封效果。
3.强化质量控制:加强对组装工序的质量控制,建立更严格的检查和测试流程,确保每辆汽车的密封质量符合标准。
2.4 实施解决方案制造商在生产线上实施了以上的解决方案。
他们与新的密封胶供应商建立了合作关系,并对工艺参数进行了调整。
此外,他们还培训了员工,提高了他们对质量控制的意识和能力。
2.5 结果评估在实施解决方案后,制造商对漏油问题进行了跟踪和评估。
经过一段时间的观察和测试,他们发现漏油问题得到了显著改善。
对于经过改进的生产线,漏油问题的发生率大大降低,质量得到了有效控制。
8D应用案例范文

8D应用案例范文8D是指一种用于解决问题和改进过程的方法,其中D分别代表所进行的八个步骤。
下面将展示一些8D方法的典型应用案例。
案例一:汽车生产线质量问题汽车制造公司的组装线上出现了一批汽车车身烤漆起皱的问题,给产品质量和用户满意度带来了严重影响。
该公司立即采用8D方法进行问题分析和解决。
D1:建立团队公司组建了一个跨部门的团队,包括生产、质量控制、工艺和烤漆等相关部门的专家和工程师。
D2:描述问题团队对车身烤漆起皱的问题进行了详细描述,包括问题发生的时间、地点、具体情况等。
D3:立即解决并限制问题通过对问题进行实地观察和实验验证,团队发现烤漆起皱是由于涂料配方中项物质的含量超标造成的。
团队立即采取措施,停止使用含有该物质的涂料,以避免进一步质量问题。
D4:寻找根本原因团队进行了更深入的分析,发现该物质超标是由供应商在生产过程中的失误所导致的。
团队与供应商进行沟通,并制定了新的质量规范和生产流程。
D5:实施纠正措施团队与供应商一起制定了一系列的纠正措施,包括提供培训、重新设定工艺参数、加强质量控制等,以确保不再出现类似问题。
D6:验证纠正措施的有效性团队进行了一段时间的监测和测试,确认纠正措施已经有效,车身烤漆起皱的问题没有再次发生。
D7:预防措施团队总结经验教训,以避免类似问题的再次发生,制定了更为严格的供应商管理制度和质量控制标准。
D8:表彰团队和总结经验公司对团队成员进行了表彰,并将这个案例作为培训教材,以帮助其他部门和团队更好地运用8D方法解决问题。
案例二:电子产品设计缺陷一家电子产品公司的新产品在上市后不久,出现了电池寿命短、系统崩溃和无法充电等问题。
公司立即采用8D方法来解决这些质量问题。
D1:建立团队公司成立了一个由工程师、质量控制人员和技术研发人员组成的团队,负责处理这些问题。
D2:描述问题团队对各个问题进行了详细描述,并收集了用户的反馈和意见。
D3:立即解决并限制问题团队对电池寿命短问题进行了深入调查,发现是由于电池充电控制电路设计缺陷导致。
8D实施方法含实例

D6、验证纠正措施
1. 换完电线后,至今尚没有发现连接点松动的迹象。 2. 断开电流接触器的电路进行试验,一旦电压不正常,转子 将自动停止工作,直至没电镀的产品从线上取下。 以上工作,小组共同进行了验证,并提请顾客事先的批准。
32
D7、防止再发生的措施
❖电镀工作指导书被修改增加了如下内容: 1)当生产线不正常停止时,操作者不仅要挑选出缺陷产品 ,而且要在工作记录记下数量及当班QC的名字。 2)在电镀线在每天早上启动前,电流接触器的连接点和电 线必须检查。以上,由杨星在12月15日完成。 ❖开发一个包括每天需检查事项的检查清单,例如生产线停 止,不管缺陷产品是否被挑选,制造部和QA需进行审核。 ❖ 依次类推,如果有类似问题,该小组负责纠正并采取适当 的预防措施。
检查数量
状态 缺陷数量
MT001206 19308片
19308片
OK
0
MT001208 14274片
14274片
OK
0
总计
33582片
33582片
OK
0
•2. 我们对操作者进行培训和教育,以让其知道最重要的事情:
•遵守工作程序和指导书以保持顾客产品质量。使其意识到他们在 产品质量保证中的重要职责。我们强调,任何由于不小心引起的错 误是不允许的并且不能重复发生,因为那样将会给顾客带来不必要 的损失。因此我们把给顾客造成损失的错误展示以教育员工。
生管课、销售课、库管课、品保课 • 责属人员:
贾正羽、庄卫年、赵晓明、许 丽
36
D2.问题描述
• 何时 : 1999年11月4日; • 何人 : 浙江精密机械厂; • 何地 : 浙江精密机械厂—包装车间; • 何事 : 包装ALT-5检测器时,使用20μMHT
8d报告案例

8d报告案例在企业管理中,质量问题是一项重要的挑战。
当产品或服务出现问题时,需要对问题进行深入分析和解决。
8D报告是一种常用的问题解决方法,它可以帮助企业识别问题根本原因,并采取适当的措施进行纠正。
下面以某家汽车制造企业的实际案例为例,介绍8D报告的具体应用。
1. 案例背景该汽车制造企业生产线上的一部分工作台出现了机器故障,导致产品质量下降。
经初步调查,故障可能与设备的电路板有关,但具体原因尚未查明。
为了解决此问题,企业决定采用8D报告方法进行分析和处理。
2. D1: 组织小组在第一阶段,企业成立了一个问题解决小组,由质量控制部门的工程师、生产部门的技术人员和设备供应商的代表组成。
小组的目标是共同协作,找出问题的根本原因。
3. D2: 外部描述问题小组成员对故障进行了详细的描述,包括故障发生的时间、频率和影响范围。
他们还收集了相关数据和记录,以便更好地了解问题的现状。
4. D3: 制定临时措施为了防止故障的进一步蔓延,小组决定采取一些临时措施。
他们在生产线上增加了巡检频率,对可能出现故障的部位进行定期维护,并对操作员进行培训,以降低操作过程中的错误率。
5. D4: 根本原因分析小组对电路板进行了详细分析,并使用了一些先进的测试设备。
经过一段时间的研究,他们发现了电路板上的一个元件存在设计缺陷,导致了机器故障。
6. D5: 确定长期措施小组提出了一系列长期措施,以纠正根本原因并防止类似问题再次发生。
他们与设备供应商合作,进行元件的重新设计和生产。
同时,他们还对员工进行了培训,以加强对设备操作的技能。
7. D6: 实施措施在此阶段,小组开始实施之前制定的长期措施。
他们更新了生产线上的所有电路板,并确保设备供应商按时交付符合质量标准的元件。
同时,他们还进行了全面的培训,以确保操作员了解新设备的使用方法。
8. D7: 跟踪措施效果小组会定期跟踪措施的效果,并记录相关数据。
通过与之前的数据进行比较,他们可以评估措施的有效性,并进行适当调整。
8D事故改善方案案例说明

8D事故改善方案(关于)案例说明一、D0. 问题的提出:1、08年11月4日客户—客户投诉,在其包装车间对“ALT-5检测器”进行包装时,使用公司的MHT机用膜时一拉就断裂, 并发现使用的机用膜端口破裂。
2、造成ALT-5检测器包装工作进度延误,要求派人处理。
二、D1.成立小组:1、按问题涉及范围确定小组成员:责属单位:生管课、销售课、库管课、品保课责属人员:贾、庄、赵、许三、D2.问题描述:何时: 2008年11月4日;何人:浙江吉利;何地:浙江吉利—包装车间;何事:包装ALT-5检测器时,使用20μMHT 机用膜一拉就断;如何:在IPEX预拉型缠绕机上使用,转速为30M/MIN,预拉后倍数为3 。
为什么:机用膜卷端口破损;多少: 20卷中目前发现6卷有问题。
四、D3.执行和确认临时措施:1、品保课立即派员到浙江吉利检查全部20μMHT机用膜,并挑出有问题的膜。
(许完成日期08/11/05)2、对挑选出的破损20μMHT机用膜运回公司,按数补给浙江精密机械厂。
并确认补货后的情况。
(许完成日期08/11/05)3、对现有生产、贮存、出货的20μMHT机用膜进行全数检验。
(许完成日期08/11/05)五、D4.识别并验证根本原因:5.1 识别可能原因(因果图)环法库房湿度大速度设定太快产品堆放高度过高包装方式不合理端面擦伤操作粗心对操作工艺不熟贮存架间隙小拉伸强度不稳定料5.2 选择最有可能的原因(矩阵图)不良情况统计表5.3 确定根本原因通过小组因果分析,试验统计确定产品堆放高度过高、包装方式不合理是导致产品端口受损根本原因。
六、D5.决定及验证纠正措施:6.1针对根本原因,现采用下列方法进行整改:1.修改搬运、贮存作业方法,将原来搬运和堆放高度3层改为2层,减少重压。
2.改变包装方法,产品从散装改为托盘运装。
3.包装箱内上下层增垫泡沫,以减少碰撞冲力。
6.2验证纠正措施(小批量验证):小组采用同一规格型号100卷产品按照三项措施进行小批量验证.七、D6.执行永久纠正措施:通过小批量验证,小组一致决定采用以下措施进行永久整改: 1.修改搬运、贮存作业方法,将原来搬运和堆放高度3层改为2层,减少重压。
8D报告案例分析2024

8D报告案例分析2024在当今竞争激烈的商业环境中,企业面临着各种各样的问题和挑战。
为了有效地解决这些问题,提高产品质量和生产效率,8D 报告成为了一种广泛应用的工具。
本文将通过一个具体的案例,深入分析 8D 报告的应用和效果。
一、案例背景某电子制造企业在生产一款新型智能手机时,发现部分产品在充电过程中出现过热的现象。
这不仅影响了用户体验,还可能对用户的安全构成威胁。
因此,企业决定启动 8D 流程来解决这个问题。
二、8D 报告的步骤1、 D1:成立团队企业迅速组建了一个跨部门的问题解决团队,成员包括研发工程师、质量控制人员、生产经理等。
这个团队具备不同领域的专业知识和经验,为解决问题提供了全方位的支持。
2、 D2:问题描述团队对问题进行了详细的描述,包括过热现象出现的具体情况、发生的频率、涉及的产品批次等。
通过对问题的准确描述,为后续的分析和解决提供了清晰的方向。
3、 D3:临时措施为了防止问题的进一步扩大,团队立即采取了临时措施。
例如,暂停相关产品的生产和销售,对已售出的产品进行召回和维修。
同时,加强对生产过程的监控,确保类似问题不再发生。
4、 D4:根本原因分析团队通过多种方法进行根本原因分析,包括对产品设计、原材料、生产工艺等方面的深入研究。
经过一系列的测试和验证,最终发现是充电器的某个零部件存在质量问题,导致充电过程中电流不稳定,从而引起过热。
5、 D5:选择和验证永久措施针对根本原因,团队提出了多种永久措施,并进行了验证和评估。
最终确定的措施是更换充电器的零部件供应商,并对新供应商的产品进行严格的质量检测。
6、 D6:实施永久措施企业按照确定的永久措施,与新的供应商合作,采购了合格的零部件,并在生产线上进行了更换和调试。
同时,对相关的生产工艺和质量控制流程进行了优化和完善。
7、 D7:预防再发生为了防止类似问题的再次发生,团队制定了一系列的预防措施。
包括加强对供应商的管理和监督,定期对产品进行质量检测和可靠性测试,建立问题预警机制等。
8D报告案例分析

8D报告案例分析8D报告案例分析:触摸屏显示不正常引言本文将对某企业生产车间中的一个触摸屏显示不正常的问题进行8D分析。
通过对问题的详细描述与分析,并结合8D方法对问题进行系统解决,希望能够给读者带来一些帮助。
一、问题描述在某企业生产车间中,有一台触摸屏显示不正常,经过工人反映,表现为触摸反应迟钝,有时无法正常操作。
这给生产工作带来了一定的影响,因此需要对该问题进行解决。
二、现象分析2.1 观察现象触摸屏显示不正常的现象包括触摸反应迟钝和无法正常操作。
工人反映,有时需要多次点击才能正常触发,甚至有时点击无效。
2.2 现象对比与其他正常的触摸屏相比,该台触摸屏显示明显异常。
其他台触摸屏反应灵敏,点击一次即可正常触发,操作流畅。
2.3 现象原因根据观察与对比的结果,初步判断该问题可能是触摸屏硬件故障导致的。
可能原因包括触摸屏面板老化、触控硬件松动等。
三、问题分析3.1 提出问题通过对现象的分析,问题可以归纳为:为何该台触摸屏显示不正常,触摸反应迟钝,有时无法正常操作?3.2 问题原因根据现象分析的初步结论,问题原因可能是触摸屏硬件故障,具体原因包括触摸屏面板老化和触控硬件松动。
为了确认问题的根本原因,需要进一步调查分析。
四、分析工具使用为了进一步分析问题原因,我们将使用以下工具:4.1 5W1H分析法通过对问题进行"是什么"、"为什么"、"何时"、"何地"、"谁"、"如何"的分析,以便更深入地了解问题的发生原因。
4.2 因果图(鱼骨图)通过绘制因果图,对问题的可能原因进行整理和分类,帮助找到问题的根本原因。
五、问题解决5.1 问题解决目标通过解决触摸屏显示不正常的问题,恢复其正常功能,以确保生产工作的顺利进行。
5.2 解决措施根据现象分析和问题原因的初步判断,采取以下措施进行问题解决:(1)更换触摸屏面板:考虑到触摸屏面板老化可能导致触摸不正常,可尝试更换新的面板。
8d报告生产案例范文

8d报告生产案例范文案例背景近日,我司生产线上出现了一起质量问题,部分产品出现了严重的尺寸偏差现象。
为了彻底解决这个问题,我们迅速展开了8D报告的问题解决流程,并于XX月XX日完成功能过该案例。
问题描述在生产线上生产的产品尺寸偏差较大,超过了允许范围。
该问题对产品的质量造成了严重影响,需要尽快解决。
初步原因分析通过对问题进行初步调查和分析,我们发现可能的原因有:1. 模具老化导致的尺寸不稳定。
2. 操作工操作不当,没有按照规定的工艺流程进行生产。
3. 人为因素,例如操作工操作不规范。
问题解决措施针对问题的初步原因分析,我们制定了以下解决措施:1. 进行模具更换,确保新的模具尺寸稳定。
2. 重新培训操作工,提醒他们严格按照规定的工艺流程进行生产。
3. 强调操作工严格操作的重要性,加强对操作工的监督和管理。
8D报告步骤第一步:组建问题解决小组我们成立了一个专门的问题解决小组,由相关的技术人员、质量人员和生产人员组成。
第二步:问题描述和原因分析我们详细描述了问题,按照8D方法分析了问题的原因。
第三步:紧急应对措施在问题暴露后,我们立即采取了紧急应对措施,暂停了全部产线,并进行了模具的更换。
第四步:根本原因分析通过对问题的深入调查和分析,我们发现问题的根本原因是操作工操作不规范导致的。
第五步:长期解决方案为了彻底解决问题,我们制定了长期解决方案:重新培训操作工,提醒他们严格遵守操作规程,确保生产过程规范。
第六步:实施长期解决方案为了确保长期解决方案的有效实施,我们组织了培训课程,并加强了对操作工的管理和监督。
第七步:验证解决方案的有效性我们对解决方案进行了实际生产和质量监控,验证了解决方案的有效性。
第八步:预防措施为了避免类似问题再次发生,我们进一步加强了对模具使用寿命的监控和管理,并加强了操作工的培训和管理。
结果和总结通过本次的8D报告问题解决流程,我们成功解决了生产线上的尺寸偏差问题,并且在以后的生产中没有再次出现类似问题。
8d报告案例

8d报告案例8D报告案例。
在工业生产和质量管理中,8D报告是一种常见的问题解决方法。
它是指通过八个步骤来诊断、纠正和预防问题,以确保产品质量和客户满意度。
下面我们将以一个实际案例为例,来详细介绍8D报告的应用过程。
1. 问题描述。
某汽车零部件制造企业在生产过程中发现了一批产品出现了漏油的质量问题。
经过初步调查,发现该问题主要出现在一条生产线上,而且已经影响到了部分客户的使用体验,需要尽快解决。
2. 组建团队。
为了解决这一质量问题,企业迅速组建了一个由质量工程师、生产人员、技术人员和客户服务人员组成的团队,负责开展8D报告的相关工作。
3. 问题分析。
团队首先对问题进行了深入分析,通过对生产线的检查和产品的测试,确定了漏油问题主要是由于某个关键工艺环节的不合格零部件导致的。
同时,还发现了一些相关的工艺参数和操作规程存在一定的问题,需要进一步改进。
4. 制定临时对策。
为了尽快解决问题,团队制定了一系列临时对策,包括暂停相关生产线的生产、更换不合格零部件、调整工艺参数等,以确保不合格产品不会继续流入市场。
5. 确认根本原因。
通过对生产线和工艺的进一步调查和分析,团队最终确认了漏油问题的根本原因,并针对性地提出了相应的长期解决方案,包括改进零部件制造工艺、优化操作规程、加强质量监控等。
6. 实施长期对策。
在确认了长期解决方案后,团队立即着手实施,对生产线进行了全面的改进和优化,同时加强了对关键工艺环节的监控和管理,以确保类似问题不再发生。
7. 预防措施。
为了预防类似问题的再次发生,团队还对相关的质量管理体系和流程进行了全面的审视和调整,确保漏油问题得到了有效的预防和控制。
8. 总结和表彰。
经过团队的不懈努力,漏油问题最终得到了圆满解决,产品质量得到了有效保障,客户满意度也得到了提升。
企业对团队的成绩给予了充分的肯定和表彰,同时也总结了这次问题解决的经验和教训,为今后的质量管理工作提供了宝贵的参考。
通过这个案例,我们可以清楚地看到8D报告在解决质量问题中的重要作用。
8d报告案例范文

8D报告案例范文一、问题描述问题描述:某公司生产的智能手机在用户使用过程中,出现了频繁的死机现象。
二、临时措施在问题发生初期,我们采取了以下临时措施以减轻问题的影响:1. 对出现死机现象的手机进行重启操作,暂时恢复正常使用。
2. 为用户提供了备用手机,以确保他们在问题解决期间能够正常使用。
三、问题定义经过初步调查,我们定义了以下问题:1. 智能手机在使用过程中频繁死机。
2. 问题影响范围广泛,涉及多个批次的产品。
3. 问题严重程度较高,影响了用户的使用体验和满意度。
四、问题原因分析通过对问题进行深入分析,我们找出了以下原因:1. 手机硬件设计存在缺陷,导致使用过程中出现死机现象。
2. 手机软件存在BUG,与硬件不匹配,引发死机问题。
3. 生产过程中质量控制不严格,导致部分批次产品存在问题。
五、制定纠正措施针对以上原因,我们制定了以下纠正措施:1. 对手机硬件设计进行优化,修复存在的缺陷。
2. 对手机软件进行升级,修复已知的BUG,提高与硬件的匹配度。
3. 加强生产过程的质量控制,确保产品质量符合标准。
六、验证纠正措施的有效性为确保纠正措施的有效性,我们进行了以下验证活动:1. 对优化后的手机硬件和软件进行了严格的测试,确保问题已得到解决。
2. 对生产过程进行了全面的质量检查,确保产品质量符合要求。
3. 对用户反馈进行了收集和分析,确认问题已得到解决,用户满意度得到提升。
七、预防措施制定与实施计划为防止类似问题再次发生,我们制定了以下预防措施:1. 建立手机硬件和软件的设计审查机制,确保产品在设计阶段就具备高质量和可靠性。
2. 加强手机软件的测试力度,确保在发布前发现并修复所有已知的BUG。
3. 定期对生产过程进行质量检查和评估,确保生产过程符合质量要求。
4. 建立用户反馈收集和分析机制,及时发现并处理用户在使用过程中遇到的问题。
5. 实施员工培训计划,提高员工的质量意识和技能水平。
6. 制定产品召回计划,以备不时之需。
质量管理8D报告培训经典教材含案例分析

常用方法
1.对操作员现场询问 2.现场观察 3.模拟试验
4.DOE试验
5.异常记录
四. 8D步骤—D4原因分析
5-Why 分 当析一个原因被发现时,不停地问为什么、为什么、为什么、
为什么、为什么,一直到无法拆解下去 。
TOYOTA 5-Why?
1W
WHY 问题
2W
WHY 中间原因
3W
WHY 中间原因
单击添加副标题
8D报告培训教材 (经典)
Possible
课堂纪律
一.手机请关机或调成静音。 二.请保持课堂安静,请勿交头接耳或大声讲话。 三.如有问题请会后交流 。
目录
CONTENT
01 什么是8D 单击此处添加正文
03 何时采用8D 单击此处添加正文
05 8D改善案例 单击此处添加正文
02 为什么要推行8D 单击此处添加正文
什么是问题???
问期题望
期望 目标
现实
四. 8D步骤—D2问题描述
问题描述方法:5W/2H
WHO
5W2H 谁
WHAT
什么
WHEN WHERE WHY HOW
何时 何地 为什么 怎么样
解释 识别那一个客户(内/外部)在抱怨 问题的症状,无法用文字描述清楚的,借助 于数字或图片将问题表达清楚
记入问题发生的日期 记入问题发生的场所 识别已知的解释 在什么的模式或状态这问题会发生
HOW MUCH
什么程度 问题发生的程度、量
13
需要考虑的问题:
一.防止继续产生不良品 (减少不良品产生)。
二.减小产生的不良和后续 可能产生不良对客户的影 响。
定义、验证和执行临时控制行动,保证在 永久纠正措施实施前,将问题与内外部顾 客隔离。
- 1、下载文档前请自行甄别文档内容的完整性,平台不提供额外的编辑、内容补充、找答案等附加服务。
- 2、"仅部分预览"的文档,不可在线预览部分如存在完整性等问题,可反馈申请退款(可完整预览的文档不适用该条件!)。
- 3、如文档侵犯您的权益,请联系客服反馈,我们会尽快为您处理(人工客服工作时间:9:00-18:30)。
寻找根本原因的方法-5Why
5Why解决问题方式:透过5M1E作系统分析
为什么该特定问题会发生?
人、机、料
方法、检测
为什么该问题没有被检查、检验到?
环境
为什么管理体系、流程会允许该问题发生?
寻找根本原因的方法-5Why
➢ 断点的设立:目的是避免重复抱怨、分选、
确认追溯范围;注意断点前后产品的区分;
➢ 制定遏制措施:针对症状采取的临时分选
措施,需具体描述,包含所使用到的检具,
判定标准等; ➢ 遏制措施有效性验证:采取的措施需进行
验证,确保能有效识别症状。
8D方法
不合格品追回记录
根本原因分析-D4
8D方法
➢ 根本原因有两个层面:产生原因和流 出原因;
8D方法
❖ 团队组成须考虑的因素:
➢ 选择与此项目有关的成
员; ➢ 跨部门人员的结构; ➢ 有能力的团队领导; ➢ 所有成员具备基本的
团队合作的要点
团队领导的主要作用是负责整个问题解决过程 的引导和控制;
所有人应该有对所做事情的统一的理解和认识; 所有人应该明确分工和职责; 所有人应该使用一致的工具和沟通语言; 在需要创新性思维的时候所有人都应该积极参
D4:用工具列出可以用来解释问题起因的所有潜在原因,并通过“5Why”来确认 问题产生和流出的根本原因;并对该根本原因从产生和流出二个方面分析;
D5:为了遏制问题的产生和流出而采取的临时性的措施,包括分选、100%检验、 增加临时的检具等;
D6:针对问题产生和流出的根本原因而采取的措施,在生产中应用该措施时应监督 其长期效果;从而能杜绝问题的再次产生和流出;
与.
8D方法
描述问题-D2
What?
Where?
① When? ③ Who?
➢ 一个问题的解决必须在采取行动前
②
④
Why? ⑤
How many? How ? ⑦ ⑥
知道尽可能多的关于问题的描述; ➢ 问题的描述需要建立在现场、现物、 现时的基础上;
What 什么问题?/当前状况是什么? When 问题在何时发生? Where 问题在何处发生? Why 什么原因产生的问题?
D7: 制定一个实施永久措施的计划,确定过程控制方法并纳入文件,力,对小组问题解决工作进行总结并祝贺。
8D - 是完全消除根本原因的问题解决措施和预防类似问题再发生的系
统问题解决方法,常用于复杂问题的解决,或是客户要求。
成立8D小组-D1
➢ 根本原因可能是一种 来自人、机、料、法、 环、测等要素的变化; 可以结合现场的4M变化 进行分析;
➢ 根本原因也可能是一 种未预见到的情况, 则需从设计角度重新 进行FMEA的分析;
好的 产品
失效 产品
特征 1 特征 2 特征 3 特征 4 特征 5 特征 6
。
。
。
AA
BB
CC
DD
EE
FF 。。 。。 。。
➢ 在现场了解情况后,对问题进行
Who 和哪些人有关?/谁负责这项工作?
5W2H的总结描述;
How
How many
问题发生的过程? 数量多少?
5W2H彻底落实-描述问题的方法
遏制问题-D3
遏制问题是指针对问题的症状,确认问 题的影响范围,采取消除症状的措施,并 验证措施的有效性:
➢ 确认症状的影响范围: 及时性、评估的 充分性;
Why Why
Why Why
Why
解决方法 一劳永逸
系统的方法并不急于立即解决问题,而是立足于揭示问题根源,找出长期的对策。
寻找根本原因的方法-5Why
一问:“为什么机器停了?” 答:“因为超过了负荷,保险丝就断了。”
二问:“为什么超负荷呢?” 答:“因为轴承的润滑不够。”
三问:“为什么润滑不够?” 答:“因为润滑泵吸不上油来。”
目录
目的及适用范围
目的
在公司内部形成标准化的问题分析
解决方法;
培训相关岗位人员,确保正确应用;
提高管理人员的问题分析解决能力;
分享最佳质量问题解决案例
所有管理者,需要面对并解决 随时可能出现的质量问题;
适用范围
质量问题解决常用方法和流程
1.问题描述
(PCR)
2.遏制措 施及断点
4a.复杂问 题根本原 因查找 (对比分析)
4b.复杂问 题根本原 因分析 (再现模拟)
3a.过程及 零件检查?
未发现不 符合内容
5. 解决 方法
6a. 验证 方法
6b. 验证 结果
结 案
发现不符合内容 (比对图纸\工艺\来料\工装)
3b.5Why
PCR - 是常用的一种问题交流报告格式,用于分析和解决问题,SDS
用于内部问题的分析交流。
质量问题解决的常用方法和流程
8D质量问题解决方 法和案例分析
❖第二版更新内容说明
1, D4根本原因分析中增加对根本原因按产 生和流出二个方面分析的要求
2,D8 祝贺小组改为总结表彰
3,增加8D分析报告格式PPT版本和EXCEL 版本格式
➢ 目的及适用范围 ➢ 质量问题解决常用方法和流程 ➢ 8D与5Why方法 ➢ 案例分享和讨论 ➢ 课堂练习和点评 ➢8D报告格式
一致 一致 一致
不一致 一致
不一致 。 。 。
Problem
5 Why’s
Why Why Why Why Why
Root Cause
寻找根本原因的方法
寻找根本原因的方法-5Why
问题根本原因分析方法之 5Why
传统的方法
问题
不采用
解决方法 “快速解决“
寻找根本原因的方法-5Why
系统方法
问题
采用
D1 成立8D小组 D2 描述问题 D3 遏制问题
D4 根本原因分析 D5 临时措施
D6 长期措施 D7 系统性预防问
题再发生
(8D) D1:成立一个小组, 成员具备工艺/产品知识及能解决问题和实施纠正措施的素质,
并指定一个组长;
D2:用量化的术语详细说明与该问题有关的内/外部顾客抱怨,如什么、地点、时间、 程度、频率等; D3:指针对问题的症状,确认问题的影响范围,采取消除症状的措施,并验证措施 的有效性;
四问:“为什么吸不上油来?” 答:“因为油泵轴磨损、松动了。”
五问:“为什么磨损了呢?” 答:“因为没有安装过滤器,混进了铁屑等杂质。”
经过连续五次不停地问“为什么”,才找到问题的真正原因和解决的方法, 在油泵轴上安装过滤器。
五个为什么
寻找根本原因的方法-5Why
问五次为什么
原则:连续追问“为什么”,直到得到可控制的,并能采取措施、防止问题再发的根 本原因;