钢中非金属夹杂对质量的影响及控制措施
钢中夹杂物知识.
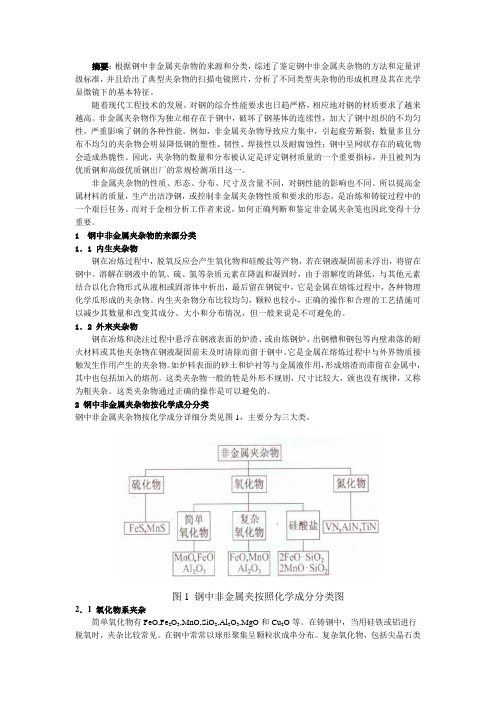
摘要:根据钢中非金属夹杂物的来源和分类,综述了鉴定钢中非金属夹杂物的方法和定量评级标准,并且给出了典型夹杂物的扫描电镜照片,分析了不同类型夹杂物的形成机理及其在光学显微镜下的基本特征。
随着现代工程技术的发展,对钢的综合性能要求也日趋严格,相应地对钢的材质要求了越来越高。
非金属夹杂物作为独立相存在于钢中,破坏了钢基体的连续性,加大了钢中组织的不均匀性,严重影响了钢的各种性能。
例如,非金属夹杂物导致应力集中,引起疲劳断裂;数量多且分布不均匀的夹杂物会明显降低钢的塑性、韧性、焊接性以及耐腐蚀性;钢中呈网状存在的硫化物会造成热脆性。
因此,夹杂物的数量和分布被认定是评定钢材质量的一个重要指标,并且被列为优质钢和高级优质钢出厂的常规检测项目这一。
非金属夹杂物的性质、形态、分布、尺寸及含量不同,对钢性能的影响也不同。
所以提高金属材料的质量,生产出洁净钢,或控制非金属夹杂物性质和要求的形态,是冶炼和铸锭过程中的一个艰巨任务。
而对于金相分析工作者来说,如何正确判断和鉴定非金属夹杂笺也因此变得十分重要。
1 钢中非金属夹杂物的来源分类1.1 内生夹杂物钢在冶炼过程中,脱氧反应会产生氧化物和硅酸盐等产物,若在钢液凝固前未浮出,将留在钢中。
溶解在钢液中的氧、硫、氮等杂质元素在降温和凝固时,由于溶解度的降低,与其他元素结合以化合物形式从液相或固溶体中析出,最后留在钢锭中,它是金属在熔炼过程中,各种物理化学瓜形成的夹杂物。
内生夹杂物分布比较均匀,颗粒也较小,正确的操作和合理的工艺措施可以减少其数量和改变其成分、大小和分布情况,但一般来说是不可避免的。
1.2 外来夹杂物钢在冶炼和浇注过程中悬浮在钢液表面的炉渣、或由炼钢炉、出钢槽和钢包等内壁肃落的耐火材料或其他夹杂物在钢液凝固前未及时清除而留于钢中。
它是金属在熔炼过程中与外界物质接触发生作用产生的夹杂物。
如炉料表面的砂土和炉衬等与金属液作用,形成熔渣而滞留在金属中,其中也包括加入的熔剂。
304不锈钢中夹杂物的控制

304不锈钢中夹杂物的控制304不锈钢是一种广泛应用的奥氏体不锈钢,具有优良的耐腐蚀性和高温强度。
然而,夹杂物的存在可能会对其组织和性能产生不利影响。
因此,控制304不锈钢中的夹杂物对于保证其质量和性能具有重要意义。
本文将介绍夹杂物控制的重要性、夹杂物的来源和分类,以及夹杂物控制的措施和效果。
夹杂物是指存在于金属内部或表面的非金属杂质。
在304不锈钢中,夹杂物可能会破坏材料的连续性,导致应力集中,降低材料的耐腐蚀性和力学性能。
夹杂物对304不锈钢组织和性能的影响主要表现在以下几个方面:降低材料的耐腐蚀性:夹杂物能够破坏不锈钢表面的氧化膜,加速局部腐蚀,降低材料的耐腐蚀性。
降低材料的力学性能:夹杂物会破坏材料的连续性,导致应力集中,降低材料的强度和韧性。
影响材料的加工性能:夹杂物可能引起材料加工过程中的缺陷,如裂纹、折叠等,影响加工质量和精度。
夹杂物主要分为有意夹杂物和无意夹杂物。
有意夹杂物是人为添加的,如为了改善材料的某些性能而特意加入的合金元素。
无意夹杂物是在冶炼、加工过程中引入的,如炉渣、耐火材料、以及与炉气、熔剂、燃料等反应生成的产物。
为了控制304不锈钢中的夹杂物,可以采取以下措施:增加夹杂物球化处理:通过适当的热处理,使夹杂物呈球形颗粒分布,降低其对材料性能的不利影响。
控制原材料及熔炼过程:选用低杂质含量的原材料,严格控制熔炼工艺,避免过度氧化和污染。
精炼和净化处理:采用精炼技术,如电渣重熔、真空熔炼等,去除熔体中的夹杂物;同时,进行净化处理,如加入稀土元素细化晶粒,提高材料的纯净度。
合理安排工艺流程:在加工过程中合理安排工艺流程,避免过度变形和加热,以减少夹杂物的引入。
采取上述控制措施后,可以显著降低304不锈钢中的夹杂物数量和尺寸,改善材料的组织和性能。
具体效果如下:夹杂物形态:通过控制措施,可以使夹杂物呈球形或不规则形态分布,降低其对材料性能的不利影响。
夹杂物分布:采取控制措施后,夹杂物分布更加均匀,避免了局部浓度过高现象,降低材料脆性。
夹杂物对钢性能的影响

夹杂物对钢性能的影响1.概要1.1钢中非金属夹杂物的来源钢铁冶炼是一个非常复杂的物理化学过程。
随着冶炼技术的不断进步,钢的品质得到不断提升。
但是,不管采用何种先进的冶炼技术,钢中总还是不可避免地存在或多或少的非金属夹杂物,其来源大致为以下几方面:①脱氧、脱硫产物,特别是一些比重大的产物没有来得及排除。
②随着钢液温度的降低,s、o、n等杂质元素的溶解度下降,于是这些不溶解的杂质元素就呈非金属化合物在钢中沉淀。
③带入钢液中的炉渣或耐火材料。
④钢铁被大气氧化所形成的氧化物。
通常,前两种类型的包裹体称为内源性包裹体,后两种类型的包裹体称为外来包裹体。
内源性夹杂物的类型和成分取决于冶炼脱氧过程和钢的成分,尤其是与s、O和N有强亲和力的元素的含量,如铝、硼、锰、稀土、钙等。
与s、O和N亲和力较弱的元素,如Ni和Co,即使其含量变化很大,也不会对夹杂物产生明显影响。
外来夹杂物是意外形成的,通常具有大颗粒和多边形形状。
它们是分布不规则的复杂化合物。
钢中的含量通常只占总夹杂物的一小部分,而且通常很难确定。
1.2夹杂物对钢性能的影响钢中存在非金属夹杂物通常被认为是有害的。
它主要表现为对钢的强度、延展性、韧性和疲劳的影响。
因此,在冶炼过程中应采取各种技术措施,尽可能降低夹杂物的含量,科学调整夹杂物的类型、分布和形态,使其对钢材性能的影响降至最低。
① 夹杂物类型的影响铝镇静钢在连铸时,高熔点的al2o3夹杂物易粘在中间包的水口上面影响浇铸,可通过改变脱氧工艺使钢液中固态的al2o3夹杂物变为液态的铝酸钙,就可以避免夹杂物在水口上面的粘结。
②夹杂物颗粒大小及分布的影响大而集中的夹杂物对钢的性能有害,而分散而细小的夹杂物不仅可以消除这种危害,有时还可以改善钢的性能。
例如,在室温下,Al2O3颗粒超过1μM,钢的屈服强度和抗拉强度降低,但当夹杂物颗粒小于0.3μM时,屈服强度和抗拉强度将增加。
钢液中有同等量的氧、硫含量时,对小型铸件,由于冷却速度快,夹杂物的颗粒小,分布均匀,对铸件的性能几乎不产生影响。
重轨钢中非金属夹杂物控制的研究

甘
肃
冶
金
V 13 N . o. 4 o3
GAN U ME A L RG S T L U Y
J n ,01 u .2 2
文章编号 :6 24 6 ( 02 0 -0 60 17 - 1 2 1 ) 3 3 - 4 0 3
重 轨钢 中非金 属 夹 杂物 控 制 的研 究
12 S]+[ /[i O]=12 i , s / SO ( )
包和铸坯中夹杂有所增大。
4 控 制措 施
非 金属夹 杂 物是 钢 中非 金属 元 素碳 、 、 、 、 氮 硫 磷
氧的化合物 , 以氧、 的化合物为主 , 硫 严重影 响钢轨
的物理 化学性 能 。重 轨钢 中非金 属夹 杂物 来源非 常
W
A¨ [
2 装 备及 工艺情 况
攀 钢 重 轨 钢 生 产 基 本 工艺 流 程 与 工 艺 参 数 如 下 : 水预 处理 ( 铁 脱硫 、 渣 ) +2 顶 底 复 吹提 钒 扒 _ 1Ot
w[ × 。 H] 1‘w[ ] 1. A 。 T 0 X 6
25 . 2 0 2. 5
l ( O )= / ao I2l ( S] + . 8 g [ ] 12l s2 / w [ i ) 6 2 - w g i- g
1 1 15 / 5 7 .5 T () 1
复 杂 : 料本 身含 有 的夹 杂物 ; 及 时去除 的脱 氧产 原 未
物和脱硫产物 ; 钢液和熔渣 、 耐火材料的相互作用; 大包 下 渣 、 中间包 和结 晶器 卷渣 ; 注过程 中产 生 的 浇 二 次氧 化产 物 , 在 随 后 的 热冷 加 工 过 程 中发 生 形 并
夹杂物及其对钢性能的影响

夹杂物及其对钢性能的影响(1)夹杂物的分类钢在加工变形中,各类夹杂物变形性不同,按其变形能力分为三类:1.脆性夹杂物一般指那些不具有塑性变形能力的简单氧化物(Al2O3、Cr2O3、ZrO2等)、双氧化物(如FeO·Al2O3、MgO·Al2O3、CaO·6 Al2O3)、碳化物(TiC)、氮化物(TiN、Ti(CN)AlN、VN等)和不变形的球状或点状夹杂物(如球状铝酸钙和含SiO2较高的硅酸盐等)。
钢中铝硅钙夹杂物具有较高的熔点和硬度,当压力加工变形量增大时,铝硅钙被压碎并沿着加工方向而呈串链状分布,严重破坏了钢基体均匀的连续性。
2.塑性夹杂物这类夹杂物在钢经受加工变形时具有良好的塑性,沿着钢的流变方向延伸成条带状,属于这类的夹杂物含SiO2量较低的铁锰硅酸盐、硫化锰(MnS)、(Fe, Mn)S等。
夹杂物与钢基体之间的交界面处结合很好,产生裂纹的倾向性较小。
3.半塑性变形的夹杂物一般指各种复合的铝硅酸盐夹杂物,复合夹杂物中的基体,在热加工变形过程中产生塑性变形,但分布在基体中的夹杂物(如CaO·Al2O3、尖晶石型的双氧化物等)不变形,基体夹杂物随着钢基体的变形而延伸,而脆性夹杂物不变形,仍保持原来的几何形状,因此将阻碍邻近的塑性夹杂物自由延伸,而远离脆性夹杂物的部分沿着钢基体的变形方向自由延伸。
(2)夹杂物对钢性能的影响大量试验事实说明夹杂物对钢的强度影响较小,对钢的韧性危害较大,其危害程度又随钢的强度的增高而增加。
4.夹杂物变形性对钢性能的影响钢中非金属夹杂物的变形行为与钢基休之间的关系,可用夹杂物与钢基体之间的相对变形量来表示,即夹杂物的变形率v,夹杂物的变形率可在v=0~1这个范围受化,若变形率低,钢经加工变形后.由于钢产生塑性变形,而夹杂物基本不变形,便在夹杂物和钢基体的交界处产生应力集中,导致在钢与夹杂物的交界处产生微裂纹,这些微裂纹便成为零件在使用过程中引起疲劳破坏的隐患。
钢中非金属夹杂实验报告

实验报告姓名:班级:冶金1401班学号: 20142019实验名称:钢中非金属夹杂物观察与分析实验实验日期: 2017.11.7实验:钢中非金属夹杂物观察与分析实验一、实验目的1.掌握钢的磨制方法。
2.了解球磨机的使用方法。
3.了解金相显微镜的原理及使用。
4.对钢中的非金属夹杂物进行分析。
二、实验原理。
A钢中夹杂物的分类分类方法很多,但常见的有以下四种:1.按来源分类,可分为两类:(1)外来夹杂物:耐火材料、熔渣或两者的反应产物混入钢中并残留在钢中的颗粒夹杂称为外来夹杂。
包括从炉衬或包衬、或从汤道砖、中包绝热板、保护渣进入钢水中的夹杂物(有人还将钢水二次氧化生成的夹杂物包括在内)。
这类夹杂颗粒较大,易于上浮,但在钢中,它们的出现带着偶然性且不规则。
(2)内生夹杂物:在冶炼、浇注和凝固过程中,钢液、固体钢内进行着各种化学反应,对于在冶炼过程中所形成的化合物、脱氧时产生的脱氧产物、或在钢水凝固过程产生的化合物,当这些化合物来不及从钢水中彻底排出而残存在钢中者,叫做内在的非金属夹杂物。
内生夹杂物形成的时间可分为四个阶段:①一次夹杂(原生夹杂):钢液脱氧反应时生成的脱氧产物;②二次夹杂:在出钢和浇注过程中温度下降平衡移动时生成的夹杂物;③三次夹杂(再生夹杂):凝固过程中生成的夹杂;④四次夹杂:固态相变时因溶解度变化生成的夹杂。
一般说来外来夹杂物颗粒较大,在钢中比较集中,而内生夹杂物则与此相反。
从组成来看,内生夹杂物可以是简单组成,也可以是复杂组成;可以是单相的,也可以是多相的。
在铸坯凝固以及随后的冷却过程中,夹杂物不仅与钢基体保持平衡,而且夹杂物本身也不断发生改变,例如析出新的化合物以趋于稳定状态。
在轧制或热处理时,每次加热都为夹杂物和钢基体之间趋向平衡提供了条件,在室温下所观察到的夹杂物,实际上是经过了一系列复杂变化的结果。
2.按化学成分分类,一般分三类。
(1)氧化物:如FeO, Si02 , Al2O3等,有时它们各自独立存在,有时形成尖晶石(如MnO.Al203)或固溶体 (如FeO 和MnO)。
浅谈铁基合金中的非金属夹杂物的产生原因及改善方法

浅谈铁基合金中的非金属夹杂物的产生原因及改善方法一、非金属夹杂物的产生原因1. 原料质量不高铁基合金生产过程中所使用的原料,如铁矿石、废钢、合金等,如果质量不高,其中便容易夹杂着一些氧化物、硫化物等非金属夹杂物。
这些非金属夹杂物会在合金的熔炼和冶炼过程中难以完全清除,最终残留在成品中。
2. 冶炼工艺不合理在铁基合金的冶炼过程中,如果温度、压力、气体流动等因素控制不当,就会导致非金属夹杂物的生成和残留。
在高温条件下,氧化物易于生成,并在熔体中产生。
如果冶炼过程中氧气、硫化氢等有害气体不能有效排除,也会导致非金属夹杂物的生成。
3. 设备磨损铁基合金冶炼设备的磨损、老化也是产生非金属夹杂物的重要原因。
设备的老化会导致设备表面产生氧化物,这些氧化物可能会脱落并夹杂在合金中。
二、改善方法1. 选择优质原料选用质量优良的原料是避免非金属夹杂物的重要手段。
采购者需对原料进行严格把关和筛选,确保原料中的有害夹杂物含量低,以减少对合金质量的不利影响。
2. 优化冶炼工艺优化冶炼工艺也是减少非金属夹杂物的重要方法。
合理控制冶炼过程中的温度、压力、气体流动等因素,以减少非金属夹杂物的生成和残留。
3. 定期维护设备定期维护和更换冶炼设备,能够有效减少设备磨损对合金质量的影响。
设备保养要及时,保证设备表面的清洁和光滑,减少氧化物的生成和残留。
4. 使用精炼剂在冶炼过程中使用精炼剂,能够有效地减少非金属夹杂物的生成和残留。
精炼剂在熔炼过程中能够吸附和分离非金属夹杂物,确保成品的质量。
三、总结在铁基合金的生产过程中,非金属夹杂物的产生是不可避免的。
通过选择优质原料、优化工艺、定期维护设备和使用精炼剂等方法,可以有效减少非金属夹杂物对合金质量的影响,提高铁基合金的品质和性能。
希望通过不断的研究和改进,能够进一步减少非金属夹杂物的生成,并提高铁基合金的质量和竞争力。
中厚板生产中的钢板缺陷及消除这些缺陷的措施

中厚板生产中的钢板缺陷及消除这些缺陷的措施钢板的缺陷是指影响钢板的使用性能,产品标准要求不允许存在的缺陷,主要有:(1)分层。
这种缺陷主要是由于原料中有气泡、缩孔、夹杂等,而在轧制时又未使之焊合,而形成分层。
通常分层要剪切清除。
(2)气泡。
由于原料中存在气泡,在轧制时气泡未焊合,而且中间还充有气体,使得轧后钢板表面有圆包出现。
这种缺陷需要切除。
(3)夹杂。
夹杂分为内部夹杂和表面夹杂。
产生原因是原料中带有非金属夹杂物,或者将非金属杂物等压入钢板表面。
对于面积较小,深度较浅者可以通过清理修磨消除,严重者必须 切除。
(4)发纹。
发纹是指钢板表面细小的裂纹。
其产生原因是原料的皮下气泡在轧制过程中未焊合,而在钢板表面形成细小发纹。
由于钢板中气泡未焊合所形成的发纹则需切除。
(5)裂纹。
在轧制过程中,原料中的气泡破裂,内表面暴露氧化,轧后在钢板表面形成裂纹。
原料清理时,由于沟槽过深也有可能形成裂纹。
如果裂纹较浅,可以修磨清除,否则则需切除。
(6)结疤。
产生结疤的原因是由于原料表面质量不好,或原料表面原有的结疤没有彻底清除所致。
轻微者可以通过修磨清除,严重者则需 切除。
(7)凸包。
在钢板表面形成有周期的凸起。
其产生原因是轧辊或矫直辊表面破坏,形成凹坑所造成。
如果凸包轻微,可通过修磨清除,而严重时则为不合格产品。
(8)麻点。
麻点是指在钢板表面形成的粗糙表面。
产生原因是由于加热时燃料喷溅侵蚀表面或者是氧化严重而形成的粗糙平面,轻微者可以修磨,严重者则需切除。
加热时应控制好加热炉温度波动与喷油量均匀,防止氧化严重,并加强除鳞。
(9)氧化铁皮压入。
在轧制时由于氧化铁皮没有清除干净,而被压入钢板表面,形成粗糙的平面。
为防止氧化铁皮压入,要加强清除氧化铁皮。
较轻微的氧化铁皮压入可以通过修磨清除,而严重影响质量时则要切除。
(10)划伤。
钢板的划伤是指在钢板的表面留有深浅不等的划道。
纵向划伤多为辊道、导板等部位的不光滑棱角刮伤。
金属材料的非金属夹杂物控制技术

金属材料的非金属夹杂物控制技术随着工业化的发展,金属材料的应用越来越广泛。
在工业生产和日常生活中,金属材料扮演着不可或缺的角色。
然而,在金属材料的生产和使用过程中,难免会出现一些问题。
其中,非金属夹杂物是一种常见的问题,会影响到金属材料的性能和质量。
因此,金属材料的非金属夹杂物控制技术也成为了一个热门话题。
一、什么是非金属夹杂物非金属夹杂物是指金属材料中的非金属成分,包括氧化物、硫化物、氮化物、碳化物等。
这些非金属成分的存在会影响到金属材料的性能,例如疲劳强度、延展性、韧性等,从而降低金属材料的可靠性和使用寿命。
二、非金属夹杂物的来源非金属夹杂物的来源有很多种,主要包括以下几个方面:1.原料污染:在原料的采购和储存过程中,会受到环境和污染的影响,从而污染材料中的非金属成分。
2.加工工艺:在金属材料的加工过程中,例如熔炼、铸造、锻造、冷加工等,会受到非金属夹杂物的污染。
3.热处理:在金属材料的热处理过程中,例如淬火、回火、退火等,也会受到非金属夹杂物的影响。
4.外界污染:在金属材料的使用过程中,例如在腐蚀、磨损、疲劳等情况下,会受到外界环境和污染的影响。
三、控制非金属夹杂物的技术非金属夹杂物控制技术是一个综合性的技术,需要从多个方面入手。
下面介绍一些常见的非金属夹杂物控制技术:1. 原料控制:原料污染是非金属夹杂物的主要来源之一,因此需要在原料的采购和储存过程中,加强对环境和污染的防控,以减少非金属夹杂物的产生。
2. 加工工艺控制:在金属材料的加工过程中,需要加强对工艺的控制和管理,例如在熔炼和铸造过程中,可以采用真空熔炼和真空铸造技术,减少非金属夹杂物的污染。
在锻造和冷加工过程中,可以加强设备的清洁和维护,避免非金属夹杂物的污染。
3. 热处理控制:在金属材料的热处理过程中,需要加强对炉体的清洁和设备的维护,避免非金属夹杂物的污染。
4. 外界环境控制:在金属材料的使用过程中,需要加强对外界环境的防控,例如在腐蚀、磨损、疲劳等情况下,可以采用防腐、抗磨、防腐蚀等措施,减少非金属夹杂物的产生。
金属冶炼过程中的非金属夹杂物控制

扫描电镜(SEM)
总结词
扫描电镜是一种高分辨率的显微镜,能够观察金属材料表面和内部的微观结构,适用于非金属夹杂物的检测和表 征。
详细描述
扫描电镜利用电子束扫描金属材料的表面,通过收集和分析反射回来的电子信号,形成高分辨率的图像。该方法 能够观察夹杂物的形貌、大小、分布和成分等信息,具有较高的精度和分辨率。
对金属材料性能的影响
力学性能
非金属夹杂物会降低金属的力学性能,如强度、韧性、疲劳寿命等 。夹杂物的存在会导致应力集中,降低材料的抗拉强度和疲劳极限 。
物理性能
非金属夹杂物对金属的物理性能也有显著影响。例如,夹杂物会降 低金属的导电性、导热性和磁性等。
工艺性能
非金属夹杂物还会影响金属的加工性能,如焊接、热处理、塑性加工 等。夹杂物的存在可能导致焊缝开裂、热处理时组织不均匀等问题。
X射线衍射(XRD)
总结词
X射线衍射是一种用于分析金属材料 晶体结构和相组成的检测方法,可以 用于非金属夹杂物的鉴别和定量分析 。
详细描述
X射线衍射利用X射线照射金属材料, 通过分析衍射图谱来判断材料的晶体 结构和相组成。该方法能够鉴别夹杂 物的矿物组成和含量,具有较高的精 度和可靠性。
04
非金属夹杂物的控制技术与实践
金属冶炼过程中的非金属 夹杂物控制
汇报人:可编辑 2024-01-06
目录
• 非金属夹杂物的基本概述 • 非金属夹杂物的来源与控制策略 • 非金属夹杂物检测与表征技术 • 非金属夹杂物的控制技术与实践 • 非金属夹杂物控制的效果评估与优化建议 • 案例分析:某钢厂非金属夹杂物控制实践
01
非金属夹杂物的基本概述
定期检查熔炼炉内衬,确保其完 好无损,防止剥落物混入金属溶 液。
钢中的非金属夹杂物

什么是非金属夹杂?钢中非金属夹杂物,如氧化物、硫化物、硅酸盐、氮化物等一般都呈独立相存在,主要是由炼钢中的脱氧产物和钢凝固时由于一系列物化反应所形成的各种夹杂物组成。
非金属夹杂的影响非金属夹杂物的存在,破坏了钢基体的连续性,使钢组织的不均匀性增大。
一般来说钢中非金属夹杂物,对钢的性能产生不良影响,如降低钢的塑性、韧性和疲劳性能,使钢的冷热加工性能乃至某些物理性能变坏等。
因此评定钢中夹杂物类别、级别对保证钢材质量十分重要。
分类按夹杂物的化学成分:氧化物、硫化物及氮化物。
根据夹杂物的可塑性:塑性夹杂物、脆性夹杂物、不变形夹杂物及半塑性夹杂物。
● 塑性夹杂物钢中塑性夹杂物在钢经受加工变形时具有良好塑性,沿着钢的流变方向延伸成条带状。
● 脆性夹杂物指那些不具有塑性的简单氧化物和复杂氧化物以及氮化物。
●不变形夹杂物这类夹杂物在铸态的钢中呈球状,而在钢凝固并经形变加工后,夹杂物保持球形不变。
● 半塑性夹杂物指各种多相的铝硅酸盐夹杂物。
其中作为基底的夹杂物(铝硅酸盐玻璃)一般当钢在热加工时具有塑性,但是在这基底上分布的析出相晶体(如Al2O3、尖晶石类氧化物)的塑性很差。
钢经热变形后,塑性夹杂物相(基底)随钢变形而延伸,但脆性的夹杂物相不变形,仍保持原来形状,只是彼此之间的距离被拉长。
按夹杂物的来源:内生夹杂物、外来夹杂物。
● 内生夹杂物在钢的熔炼、凝固过程中,脱氧、脱硫产物,以及随温度下降,S、O、N等杂质元素的溶解度下降,于是这些不溶解的杂质元素就形成非金属化合物在钢中沉淀析出,最后留在钢锭中。
内生夹杂物分布相对均匀,颗粒一般比较细小。
可以通过合理的熔炼工艺来控制其数量、分布和大小等,但一般来讲内生夹杂物总是存在的。
● 外来夹杂物炉衬耐火材料或炉渣等在钢的冶炼、出钢、浇铸过程中进入钢中来不及上浮而滞留在钢中称为外来夹杂物。
其特征是:外形不规则、尺寸比较大,偶尔在这里或在那里出现,正确的操作可以避免或减少钢中外来夹杂物的入侵。
钢中常见的元素、夹杂物对钢性能的作用及影响

Байду номын сангаас
硅(Si): 硅在碳钢的含量≤0.50%。硅也是钢中的有益元素。在沸腾钢中,含硅量很低,硅是 作为脱氧元素加入到钢中。在镇静钢中硅的含量一般为0.12~0.37%。硅增大了钢液的流动 性,除了形成非金属夹杂外,硅溶于铁素体中。随着硅含量的提高,钢的抗拉强度提高,屈 服点提高,伸长率下降,钢的面缩率和冲击韧性显著降低。 锰(Mn): 在碳钢中,锰是有益元素。锰是作为脱氧除硫的元素加入到钢中的。对于镇静钢来 说,锰可以提高硅和铝的脱氧效果,可以同硫形成硫化锰,相当程度上降低硫在钢中的危害。 锰对碳钢的力学性能有良好的影响,它能提高钢热轧后的硬度和强度,原因是锰溶入铁素体 中引起固溶强化。因此,精炼过程中要按照技术要求严格稳定控制各炉次的锰含量。 磷(P): 一般来说,磷是钢中的有害元素。它来源于矿石和生铁等炼钢原料。磷能提高钢的 强度,但使塑性和韧性降低,特别是使钢的脆性转折温度急剧上升,即提高钢的冷脆性(低 温变脆)。由于磷的有害影响,同时考虑到磷有较大的偏析,因而对其含量要严格的控制。 但是在含碳量比较低的钢种中,磷的冷脆危害比较小。在这种情况下,可以用磷来提高钢的 强度,如鞍钢生产的高强度 IF 钢就需要加入磷。另外,在适当的情况下,还利用磷的其他 一些有益作用,如增加钢的抗大气腐蚀能力,如集装箱用钢;提高磁性,如电工硅钢;改善 钢材的易切削加工性,减少热轧薄板的粘结等。
钢夹杂物危害及应对措施

钢夹杂物危害及应对措施钢夹杂物危害及应对措施⼀、前⾔钢铁业是⼏乎所有重⼯业的基础与⽀柱,在国民经济中的重要性不⾔⽽喻。
钢铁材料是⼈类社会最主要使⽤的结构材料,也是产量最⼤应⽤最⼴泛的功能材料,在经济发展中发挥着举⾜轻重的作⽤。
钢铁材料是⼈类社会的基础材料,是社会⽂明的标志。
从纪元年代前后,世界主要⽂明地区陆续进⼊铁器时代以后,钢铁材料在⼈类⽣产、⽣活、战争中起到了举⾜轻重的作⽤。
⼀直到今天,钢铁材料的这种作⽤不但没有减弱,⽽是在不断增强。
房屋建筑、交通运输、能源⽣产、机器制造等都是⽴⾜于钢铁材料的应⽤基础之上;钢铁材料是诸多⼯业领域中的必选材料,既是许多领域不可替代的结构材料,也是产量最⼤覆盖⽽极⼴的功能材料。
钢铁⼯业长期以来是世界各国国民经济的基础产业,在国民经济中具有重要的地位,钢铁⼯业发展⽔平如何历来是⼀个国家综合国⼒的重要指标。
洁净钢是⼀个相对概念,⼀般认为:洁净钢指钢中五⼤杂质元素(S 、P 、H 、N 、O) 含量较低,且对夹杂物(主要指氧化物和硫化物) 进⾏严格控制的钢种, 主要包括:钢中总氧含量低,夹杂物数量少、尺⼨⼩、分布均匀,脆性夹杂物少及其合适的夹杂物形态。
钢的纯净化技术是⽣产⾼性能、⾼质量产品的基础,代表钢铁冶⾦企业的技术装备⽔平。
20 世纪80 年代以来,钢的洁净度不断提⾼。
⽇本2000年批量⽣产的洁净钢中,有害元素(P、S、N、O、H) 总量可达0.005 %,中国宝钢可达0.008 %,国内外钢⼚⽣产洁净钢⽔平见表1 表1 国内外⼀些钢⼚⽣产的洁净钢⽔平单位: ×10 - 6随着现代科技的进步和现代⼯业的发展对钢的质量要求越来越⾼,钢中夹杂物(主要是氧化物夹杂)严重影响钢材质量,随着洁净钢和纯净钢概念的提出,更是对钢中夹杂物的控制提出苛刻的要求。
钢中夹杂物能降低钢的塑性,韧性和疲劳寿命,使钢的加⼯性能变坏,对钢材表⾯光洁度和焊接性能有直接影响。
钢中的夹杂物对于钢材性能影响很⼤例如钢中夹杂物可导致汽车和电⽓产品⽤薄钢板的表⾯缺陷、DI罐⽤薄钢板裂纹、管线钢氢致裂纹、轮胎⼦午线加⼯过程断线、轴承钢疲劳性能恶化,同时钢中⾮⾦属夹杂物对于钢板抗撕裂性能和低温冲击韧性也有不利影响。
钢中非金属夹杂物观察和评级

钢中的非金属夹杂1. 试验目的非金属夹杂物破坏金属基体的连续性,其形态、数量、尺寸和分布影响钢的塑性、韧性、焊接性能、疲劳性能和耐蚀性等,因此,夹杂物的数量和分布被认为是评定钢材质量的一个重要指标。
2. 相关标准标准GBT 10516 2005,该标准代替GBT 10516 1989,于2005年5月13日发布,2005年10月1日实施。
夹杂物试样不经腐蚀,在明场下放大100倍,80mm 直径的视场下进行观察,选取夹杂物污染最严重的视场,与其钢种的相应标准评级图对比评定。
夹杂物分类:硫化物类,标准图谱命名为A 类。
属于塑性夹杂,较宽范围形态比(长度/宽度)的单个灰色夹杂物,一般端部呈圆角,经锻、轧后沿加工方向变形,呈纺锤形或线段形,例如FeS 、MnS 。
氧化铝类:标准图谱命名为B 类。
属于脆性夹杂,形态比(一般<3),为黑色或带蓝色的颗粒,沿轧制方向排成一行(至少有3个颗粒)。
硅酸盐类:标准图谱命名为C 类。
是具有高延展性,较宽范围形态比(一般≥3)的单个呈黑色或深灰色的夹杂物,一般端部呈锐角。
例如2MnO ·SiO 2球状氧化物类:标准图谱命名为D 类。
不变形,带角或圆形的,形态比较小(一般<3),黑色或带蓝色,表现为无规则分布的颗粒。
例如SiO 2单颗粒球状类:标准图谱命名为DS 类。
为圆形或近似圆形,直径≥13μm 的单颗粒夹杂物。
非传统类型夹杂物的评定也可以通过其形状与上述五类夹杂物进行比较,并注明其化学特征。
沉淀相类如碳化物、氮化物、硼化物的评定,也可以根据它们的形态与上述五类夹杂物进行比较,并按上述方法表示其化学特征。
钢中的非金属夹杂物测定夹杂物类别A B C D DS 总长度 总长度 总长度 数量 直径 评级图级别iμmμm μm 个 μm 0.5 37 17 18 1 13 1 127 77 76 4 19 1.5 261 184 176 9 27 2 436 343 320 16 38 2.5 649 555 510 25 53 898 822 746 36 76 3(<1181)(<1147)(<1029)(<49)(<107)注:D 类夹杂物的最大尺寸定义为直径类别细系粗系最小宽度最大宽度最小宽度最大宽度μm μm μm μmA 2 4>4 12B 2 9 >9 15C 2 5 >5 12D 3 8 >8 13注:D类夹杂物的最大尺寸定义为直径3. 试样制备3.1 试样尺寸夹杂物形态很大程度上取决于钢材压缩变形程度,只有在变形度相似的试样坯制备的截面上才能进行结果的比较。
夹杂物对钢性能的影响

夹杂物对钢性能的影响钢中的非金属夹杂物主要是指钢中的氧化物、硫化物、硅酸盐和氮化物等。
其中,氧及硫的化合物最主要,对钢性能的影响最大。
这些化合物一般不具有金属的性质,并机械地混杂在钢的组织中,虽然对钢的强度影响很小,但对疲劳性能、冲击韧性和塑性影响很大。
由于夹杂物与基体金属的物性及机械性能,如弹性、塑性及热膨胀系数均有较大差别,在受力过程中,夹杂物不能随金属相应变形。
变形大的铁就会在变形小的夹杂物的周围产生塑性流动,它们的连接处应力的分布不均匀,出现了应力集中[8],并急剧地升高,导致微裂纹的发生,为材料的破坏提供了受力的薄弱区,加速了塑性破裂的过程。
因而导致钢的塑性、韧性及疲劳强度降低,方向性加强,加工性能变坏等。
不锈钢中的夹杂物对钢的机械性能,特别是钢的韧塑性、疲劳性能、冷加工性能以及切削加工性能等有强烈的影响。
在轧制过程中,夹杂物的存在不但影响不锈钢的内部质量和板材的表面光洁度,而且将降低产品的防锈蚀能力,目前国内不锈钢厂由于夹杂导致的产品报废率高达20%,甚至更高,大大降低了钢厂的生产效率和经济效益。
因此严格控制夹杂物的类型、大小、数量、形态和分布,提高钢的纯净度,向“零夹杂钢”努力已经是许多研究者的共识[9-11]。
因此,炼钢工作者应首先力求降低夹杂物的含量,利用复合脱氧剂,使脱氧过程中生成的夹杂物尽可能地浮出,并设法降低凝固过程中出现的二次脱氧产物的形成量。
对不可能排除而残留在钢中的夹杂可采用变形处理,改变其存在状态,以减小其对钢性能的危害性。
[8].陈聪.减少钢中夹杂物的途径及其变形处理[J].科技情报开发与经济,2005,15(13).275.[9].上海交通大学《金相分析》编写组. 金相分析[M].北京: 国防工业出版社. 1982,117~133.[10].李正邦. 超洁净钢的新进展[J]. 材料与冶金学报,2002,1(3): 161-465.[11].Fukumoto S,Mutcgell A.The manufacture of alloy swithzero oxidein clusion content[C],Proceedings of the 1991 Vacuum Metallurgy Conference on the Melting and Processing of Specialty Materials I&SS,Inc.Pitts-burgh, USA, 1991:3~7.典型夹杂物对不锈钢性能的影响MgO-Al2O3尖晶石是Al作奥氏体不锈钢的终脱氧剂时的主要氧化物夹杂。
连铸过程钢中非金属夹杂物控制

连铸过程钢中非金属夹杂物控制1.洁净钢概念2.钢中夹杂物控制原理3.连铸坯中夹杂物来源与分布4.连铸过程夹杂物控制对策5.结语1. 洁净钢基本概念纯净钢(purity steel)ΣS+P+N+O+H总和水平:60年代≤900ppm70年代≤800ppm80年代≤600ppm90年代≤100ppm2000年后 < 50ppm高纯净钢对炼钢工艺要求:(1)去除杂质元素●超低[C]:如汽车板;●超低[S]:如输气管线;●超低[N]:如铁素体不锈钢废气管,冷锻线棒材;●超低[P]:如高压容器钢板。
(2)去除夹杂物●超低[O]:如滚珠钢,汽车板;●形态控制:如拉拔钢丝,管线钢。
(3)成分控制●化学成分控制在窄的范围,性能均一性。
国内外一些钢厂生产纯净钢水平如表1:2000年后杂质元素含量预测水平如表2:纯净钢除S+P+N+H+O五大元素外,随电炉短流程的发展,废钢用量的增加,还包括Cu、Zn、Sn、Bi、Pb等伴生元素。
洁净钢(clean steel):钢中非金属夹杂物总量、形态和尺寸。
它决定于钢种和产品用途。
不同用途的产品对钢中洁净度要求如表3。
钢的清洁度与产品制造和使用过程中所出现的众多缺陷密切相关,一些厂家对某些高纯度钢种发生缺陷所作的调查如表4所示,可以看出钢中的夹杂物尤其是大颗粒夹杂物是引起产品缺陷的主要原因。
日本一向对钢材质量有着严格的要求,最近日本夹杂物委员会提出的不同成品对钢中夹杂物含量及尺寸的要求如表5所示。
A23M i高附加值产品洁净度:高附加值产品对洁净度要求是:●T[O]要低<20ppm;●夹杂物数量要少;●夹杂物尺寸要小<50µm;●夹杂物形态要合适。
由上述讨论,可得出以下认识:●纯净钢或洁净钢是一个相对概念;●某一杂质含量降低到什么水平决定于钢种和产品用途;●有害元素的降低的程度决定于装备和工艺现代化水平;●不管生产什么用途的钢,总是要求钢中夹杂物数量尺寸、形态得到控制。
常存杂质对钢性能的影响

常存杂质对钢性能的影响实际使用的钢中,除了含有铁、碳与合金元素外,在冶炼过程中,不可避免地要带入一些杂质(如锰、硅、硫、磷、非金属类杂质以及某些气体,如氮、氢、氧等)。
这些杂质对钢的质量有很大的影响。
1.锰锰在钢中作为杂质存在时,一般均小于0.8%。
它来自作为炼钢原料的生铁及脱氧剂锰铁。
锰有很好的脱氧能力,还能与硫形成mns,以消除硫的有害作用。
这些反应产物大部分进入炉渣而被除去,小部分残留于钢中成为非金属夹杂物。
此外,在室温下锰能溶于铁素体,对钢有一定强化作用。
锰也能溶于渗碳体中,形成合金渗碳体。
但锰作为少量杂质存在时,它对钢的性能影响不显著。
2.硅硅在钢中作为杂质存在时,一般均小于0.4%,它也来自生铁与脱氧剂。
在室温下硅能溶于铁素体,对钢有一定的强化作用。
但硅作为少量杂质存在时,它对钢的性能影响也不显著。
3.硫硫是由生铁及燃料带入钢中的杂质。
在固态下,硫在铁中的溶解度极小,而是以fes的形态存在于钢中。
由于fes 的塑性差,使含硫较多的钢脆性较大。
更严重的是,fes与fe可形成低熔点(985℃)的共晶体,分布在奥氏体的晶界上。
当钢加热到约1200℃进行热压力加工时,晶界上的共晶体已溶化,晶粒间结合被破坏,使钢材在加工过程中沿晶界开裂,这种现象称为热脆性。
为了消除硫的有害作用,必须增加钢中含锰量。
锰与硫优先形成高熔点(1620℃)的硫化锰,并呈粒状分布在晶粒内,它在高温下具有一定塑造性,从而避免了热脆性。
硫化物是非金属夹杂物,会降低钢的机械性能,并在轧制过程中形成热加工纤维组织。
因此,通常情况下,硫是有害的杂质。
在钢中要严格限制硫的含量。
但含硫量较多的钢,可形成较多的mns,在切削加工中,mns能起断屑作用,可改善钢的切削加工性,这是硫有利的一面。
1.磷磷由生铁带入钢中,在一般情况下,钢中的磷能全部溶于铁素体中。
磷有强烈的固溶强化作用,使钢的强度、硬度增加,但塑性、韧性则显著降低。
这种脆化现象在低温时更为严重,故称为冷脆。
钢中夹杂物知识

摘要:根据钢中非金属夹杂物的来源和分类,综述了鉴定钢中非金属夹杂物的方法和定量评级标准,并且给出了典型夹杂物的扫描电镜照片,分析了不同类型夹杂物的形成机理及其在光学显微镜下的基本特征。
随着现代工程技术的发展,对钢的综合性能要求也日趋严格,相应地对钢的材质要求了越来越高。
非金属夹杂物作为独立相存在于钢中,破坏了钢基体的连续性,加大了钢中组织的不均匀性,严重影响了钢的各种性能。
例如,非金属夹杂物导致应力集中,引起疲劳断裂;数量多且分布不均匀的夹杂物会明显降低钢的塑性、韧性、焊接性以及耐腐蚀性;钢中呈网状存在的硫化物会造成热脆性。
因此,夹杂物的数量和分布被认定是评定钢材质量的一个重要指标,并且被列为优质钢和高级优质钢出厂的常规检测项目这一。
非金属夹杂物的性质、形态、分布、尺寸及含量不同,对钢性能的影响也不同。
所以提高金属材料的质量,生产出洁净钢,或控制非金属夹杂物性质和要求的形态,是冶炼和铸锭过程中的一个艰巨任务。
而对于金相分析工作者来说,如何正确判断和鉴定非金属夹杂笺也因此变得十分重要。
1 钢中非金属夹杂物的来源分类1.1 内生夹杂物钢在冶炼过程中,脱氧反应会产生氧化物和硅酸盐等产物,若在钢液凝固前未浮出,将留在钢中。
溶解在钢液中的氧、硫、氮等杂质元素在降温和凝固时,由于溶解度的降低,与其他元素结合以化合物形式从液相或固溶体中析出,最后留在钢锭中,它是金属在熔炼过程中,各种物理化学瓜形成的夹杂物。
内生夹杂物分布比较均匀,颗粒也较小,正确的操作和合理的工艺措施可以减少其数量和改变其成分、大小和分布情况,但一般来说是不可避免的。
1.2 外来夹杂物钢在冶炼和浇注过程中悬浮在钢液表面的炉渣、或由炼钢炉、出钢槽和钢包等内壁肃落的耐火材料或其他夹杂物在钢液凝固前未及时清除而留于钢中。
它是金属在熔炼过程中与外界物质接触发生作用产生的夹杂物。
如炉料表面的砂土和炉衬等与金属液作用,形成熔渣而滞留在金属中,其中也包括加入的熔剂。
- 1、下载文档前请自行甄别文档内容的完整性,平台不提供额外的编辑、内容补充、找答案等附加服务。
- 2、"仅部分预览"的文档,不可在线预览部分如存在完整性等问题,可反馈申请退款(可完整预览的文档不适用该条件!)。
- 3、如文档侵犯您的权益,请联系客服反馈,我们会尽快为您处理(人工客服工作时间:9:00-18:30)。
1) 液体钢的脱氧产物; 2) 钢液从浇注温度冷却到凝固温度过程中,由
于温度的降低使溶液中溶质的溶解度降低,
即钢水温度的变化使反应平衡移动,重新析 出脱氧产物;
3) 钢液冷凝时发生溶质树枝形偏析所析出的脱 氧产物;
4) 固相线温度以下钢继续冷却或者由于相变的
缘故,引起的夹杂物重新析出。
1.2
1.5
按化学成分分类
FeS、MnS
A类夹杂:硫化物
B类夹杂: 氧化铝、氧化铁 Al2O3+FeO C类夹杂:硅酸盐、氮化物 2MnO.SiO2 TiN、BN、NbN等 D类夹杂:球状氧化物类 小型氧化物 FeO、MnO、TiO2等
Ds类夹杂:单个大型球状氧化物类
1.6
钢中夹杂物的形貌
25
2.2夹杂物的检测
1.钢材出厂检验:
• • • ASTM标准(A、B、C、D、Ds类夹杂物); 用户标准(SKF、米其林、贝卡尔特等); 分析检验手段:光学显微镜。
2.科学研究:
• • 光学显微镜; 扫描电镜(+EDS);
•
• •
投射电镜(+EPMA、EDS);
图像分析; PDA(Pulse Distribution Analysis)。
炼钢钢坯
氧化铝+硫化钙
氧化铝
15102486N
氧化铁 视场50X
硫化钙
氧化铝
轧钢钢板
氮化物
2、非金属夹杂物对性能影响
使用性能的影响: 1、疲劳性能↓ 2、冲击韧性↓ 塑性↓ 3、耐腐蚀性↓
对工艺性能的影响: 1 、对锻造和冷加工、淬火加热和焊接过程 易开裂。 2 、轧制后表面质量以及磨削后零件表面粗 糙度降低。
在精炼过程中发生主要反应: 2[Al]+3[O]=Al2O3
[Si]+2[O]=SiO2
[Ca]+[S]=CaS [C]+[O]=CO/CO2
3.1 夹杂物的来源
根据加人脱氧剂的类型、数量和钢液静压 力,脱氧产物可能为固态、液态或气态。钢液 的温度决定了氧化物夹杂的化学稳定性。随着 温度的降低,越来越多的脱氧产物从钢液中析 出。它们的成分决定于脱氧产物形成时的温度 和钢水成分。夹杂物在脱氧过程中的生成是不 可避免的,随着温度的降低夹杂物也还会继续 生成直到钢液全部凝固。
钢中析出的夹杂主要来自四部分
1)是在炼钢温度下合金化和铝终脱氧时析出的脱氧产 物,称为一次脱氧产物。主要发生在LF或出钢过程中。 LF炉加入Si-C、C、Si-Mn、Ti等都是作为脱氧剂使用, LF主要主要之一为脱氧,去除夹杂物。
2)钢水从精炼温度冷却至液相线温度过程中析出的脱 氧产物,称为二次脱氧产物。主要发生连铸前半过程 中,包括VD,RH,大包、中间包以及结晶器中。
夹杂物对钢材的性能以及实例
夹杂物的来源以及夹杂物控制技术
1、夹杂物概念以及分类
钢中氧化物夹杂可分为:内生夹杂 互反应夹杂物
外来夹杂
相
非金属夹杂物是一种非金属的化合物,它是钢材在 脱氧过程和钢液凝固过程中产生的。
1.1内生夹杂物
内生夹杂物:钢在冶炼过程中,脱氧反应会产生氧化 物等产物,若这些产物在钢液凝固前未浮出,将留在钢中。 溶解在钢液中的氧、硫、氮等杂质元素在降温和凝固时, 由于溶解度的降低,与其他元素结合以化合物形式从液相 或固溶体中析出,最后留在钢锭中。 内生夹杂物分布比较均匀,颗粒也较小,正确的操作 和合理的工艺措施可以减少其数量和改变其成分、大小和 分布情况,但一般来说是不可避免的。
3.2.1 精炼、渣系对夹杂物的去除
控制钢中非金属夹杂的途径,一是减少冶炼 及浇注工艺操作过程中夹杂的产生和外来夹杂对 钢水的污染,二是设法排除已存在于钢水中的夹 杂物或减轻夹杂物对钢的危害。
不管采用何种精炼方法(如RH、LF、 VD),合理精炼渣组成是获得洁净钢水 的基础。
精炼过程可采取的控制措施包括,真空吹 氩搅拌去除夹杂物,加入粉剂进一步去除钢中的 杂质元素,钢液中夹杂物的变性,造合适的精炼 渣去除夹杂物。中问包可采取的控制措施包括: 保证足够的停留时间,使夹杂物充分上浮; 采用长水口氩封保护浇注,减少来源于气体 的污染; 优化中间包钢液流场,促进夹杂物上浮,并 可使用过滤器强制吸附夹杂物; 使用高碱度覆盖剂吸收夹杂物,造还原性中 间包渣,使用碱性耐火材料,降低侵蚀。
★
1.4 按夹杂物尺寸分类
1) 亚显微夹杂,粒径<lμm。在纯净钢中亚显微夹杂包括氮 化物、硫化物和氧化物,总数约为 1011 个/cm3 ,其中氧化物 夹杂个数约占 108/cm3 。一般认为这种微小氧化物对钢质 ( 除 硅钢片外)多半无害,对它在钢中的作用,目前研究得不够。 2) 显微夹杂,粒径 l~1OOμm,主要是脱氧产物。它对高强 度钢的疲劳性能和断裂韧性影响极大,它的含量与钢中溶解 氧含量有很好的对应关系。 3) 大型夹杂,粒径>1OOμm。大颗粒(大型)夹杂在干净钢中 的数量占钢坯中整个夹杂总体积的 1%,但对钢的表面和内部 质量影响最大,很多产品由于存在这种大型夹杂,致使超声 波探伤时不合格,造成钢材报废。这类夹杂物成分上的特点 是与钢中溶解氧量无关。
常规检测方法的不足: 问题:
•试样检测面积小; •分析检验耗时长; •分析检验结果(夹杂物数量、尺寸、成分、位置) 可信度低。
2.3 夹杂物统计学
夹杂物统计学是一种现代高级、建立在实际生产上,对夹 杂物进行批量的分析(采用电子散射仪以及电解夹杂等手 段),以及量子力学和模型模拟等技术学科。用来研究钢 中夹杂物的分布、大小,以及产生的动力学和热力学的基 础。
夹杂物对钢板强度、延伸的影响 当夹杂物颗粒比较大(>10μm),特别是夹杂物 含量较低时。明显降低钢的屈服强度,且同时降低钢的 抗拉强度;当夹杂物颗粒小到一定尺寸(<10μm)时, 钢的屈服强度和抗拉强度都将提高。当钢中弥散的小颗 粒的夹杂物数量增加时。钢的屈服强度和抗拉强度都有 所提高,但延伸率有很小的下降。
12351
14520 52061
26
35 164
0
0 0
4
4 21
6
平 均
0.241
0.315
0
0
0.028
0.040
29
正常坯夹杂物数量分布
30
正常浇铸铸坯夹杂物
• 检测面积总计52061mm2(超过JFE同类研究一倍),大于 50m夹杂物数量密度在0.21~0.45个/cm2,低于JFE铸坯同 类夹杂物数量; 正常坯表层试样中大于50m夹杂物主要为簇群状Al2O3, 保护渣卷入形成夹杂物微量;因此通过常规的手段,夹杂 物水平是可控的 不能避免 >100m有害夹杂物存在(数量:0.028~0.057个 /cm 2 ),生产高端用户钢板应对铸坯采用表面清理(扒 皮)。
氧化铝夹杂
冲击为3J P460NL1
夹杂+FeO夹杂
延伸 9
12Cr2Mo1VR
多处铝酸盐夹杂
16MnDR 探伤不合国标 I级
多处铝酸盐夹杂
Q345R 形成内裂纹
不同类别夹杂物对塑性的影响
“D类”或“DS类”
“D类”或“DS类”
J. Monnot, et al., Amer. Soc. For Test Mat., 1988, p.149属夹杂物尺寸大于50um时,降低了钢的塑性、韧性 和疲劳寿命,使钢的冷热加工性能乃至某些物理性能变坏。 一般 我们钢水中夹杂物尺寸都为大于50um。 大型夹杂物不利用钢板 韧性、塑性以及强度指标。除了这些性能外,还有降低抗酸性能、 疲劳性能、表面光洁度 以及焊接性能。
正常坯夹杂物数量(>50m)
炉 次 1
3 5 数量密度 (个/cm2) 检测面 绝对数量 (个数) 积mm2 Al2O3 保护渣 >100m Al2O3 保护渣 >100m 11120 14070 41 62 0 0 5 8
0.369
0.441 0.211
0
0 0
0.045
0.057 0.032
1.
“洁净”→“高洁净”→“超高洁净”趋势:
-
强化内生类夹杂物去除效果;
严格“杜绝”二次氧化; 对夹杂物成分、尺寸、分布、性能的控制。
2.
开发新工艺,降低成本,提高对夹杂物控制效率:
缩短或取消LF精炼; 强化LF、VD、RH精炼; 针对不同类型钢材,对夹杂物实行“重点控制”。
3
目
录
夹杂物概念、种类以及分类
夹杂物对钢板冲击的影响
当夹杂物颗粒比较大(>50μm),特别是夹 杂物含量较多、尺寸较大时,明显降低钢的冲击。 且冲击功曾几何状下降,尤其冲击断口出现夹渣时, 冲击值几乎为个位数。主要原因是夹杂物阻碍了冲 击的扩展功能量的释放。
夹杂物对钢板厚拉(Z向)的影响
当厚拉断口出现夹杂物含量较多、尺寸较大时, 明显降低钢的Z向性能,性能几乎为个位数。尤其 是硫化物夹杂和氧化铝夹杂,破坏钢板基体组织的 连续性,厚度方向被该类别夹杂物穿晶破坏。
外来夹杂物
1) 出钢过程中卷入钢液内的夹渣,钢液或炉 渣与耐火材料接触时的侵蚀产物,中间包 渣的乳化,结晶器内保护渣的卷入等等。这 种夹杂物在浇注过程中未来得及上浮而残 留在钢中。 2)钢液二次氧化产物。
1.3 相互反应夹杂物
相互反应夹杂物 (意思是内生和外来相交错), 可列入尖晶石、某些铝酸盐、 硅酸盐和许多其他反 应产物。
•
•
31
3、夹杂物的来源与控制