品质管理制度与表格
{品质管理制度表格}质量控制表

{品质管理制度表格}质量控制表品质管理制度表格------品质管理是一个组织内部的系统,旨在确保产品和服务的品质符合预期并超越客户的期望。
为了有效地实施品质管理,一个组织应该拥有一套明确的品质管理制度。
下面是一个品质管理制度表格的示例,帮助组织制定和实施品质管理的标准和程序。
表格标题:品质管理制度表格章节,内容,解释------,------,--------1,引言,对品质管理制度的目的和背景的介绍2,范围,表明品质管理制度适用的领域和范围3,定义,对品质管理相关术语和定义的说明4,组织架构,品质管理的组织结构和职责的描述5,资源管理,确保可靠且适当的资源供应6,计划,制定品质管理计划,确定质量目标和资源需求7,实施,执行品质控制和改进活动的方法和规程8,绩效评估,测量和评估品质绩效的方法和指标9,改进,通过持续改进活动改善品质管理系统10,文档管理,管理品质管理相关的文件和记录11,培训和教育,确保员工具备必要的技能和知识12,审核,定期进行内部和外部审核13,管理审核,管理审核结果的跟踪和审议14,报告,向相关方汇报品质管理的情况15,不符合和纠正措施,处理不符合要求的情况和采取纠正措施16,记录和存储,管理品质管理记录和存储要求17,经验总结,收集、分析和应用相关的经验和教训18,参考文件,引用相关品质管理的国际标准和指南19,附录,提供一些支持材料和例子这是一个基本的品质管理制度表格示例,每个章节都涵盖了品质管理的一个特定方面。
具体组织可以根据自己的需要进行调整和补充。
这个制度表格有助于确保品质管理的一致性和有效性,并提供了一个框架用于组织的品质管理实践。
通过遵循和执行这个制度表格,组织可以不断迭代和改进其品质管理系统,以达到更高的品质水平和客户满意度。
原材料、半成品和成品质量安全控制制度表格
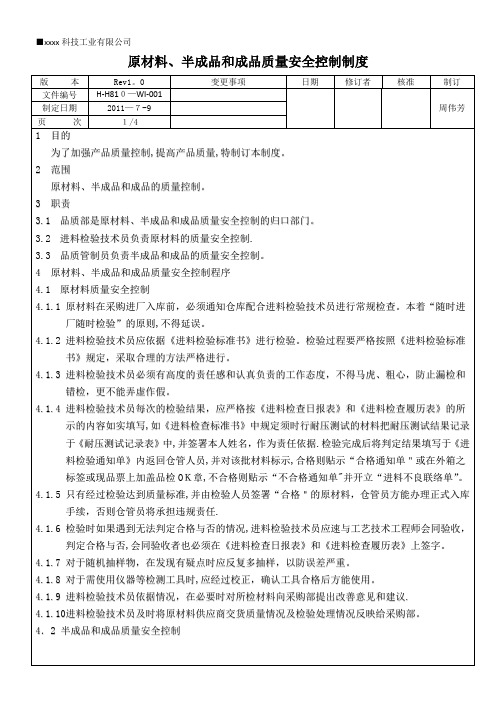
4.1.4进料检验技术员每次的检验结果,应严格按《进料检查日报表》和《进料检查履历表》的所示的内容如实填写,如《进料检查标准书》中规定须时行耐压测试的材料把耐压测试结果记录于《耐压测试记录表》中,并签署本人姓名,作为责任依据.检验完成后将判定结果填写于《进料检验通知单》内返回仓管人员,并对该批材料标示,合格则贴示“合格通知单"或在外箱之标签或现品票上加盖品检OK章,不合格则贴示“不合格通知单"并开立“进料不良联络单”。
3)发现的异常原因与相关部门有关时,光电组装部应及时通知或邀请各相关部门予以解决,不得延误。
4)若有重大质量事故发生,应及时向生产技术总监、副总经理直至总经理予以解决。
4.2。5 生产过程中关于不合格品责任裁定。
1)生产过程中非人为因素造成的不合格品,不得追究操作者的责任。
2)操作者在自检中发现的不合格品,超出标准范围的操作应承担责任。
4.2.3 生产过程中的质量把关实行三检制:自检、互检、总检。
1)自检:由各工序按照质量标准对自己的生产加工对象在生产过程中进行控制把关。
2)互检:光电组装内部各工序之间,在下道工序接到上道工序的制品时,应检查上一工序的质量是否合格,合格后方能继续作业。
3)总检:由品质管制员进行总体把关。
4。2。4 生产过程中申报检验的规定。
4。6 质量事故处理
4。6。1 因客观原因造成的质量问题,应由品质部与生产主管亲临现场协助处理,并报技术生产总监审核。
4。6.2对于生产过程中因操作不当或责任心不强,检验人员工作疏忽等原因造成的质量问题,应由销售部走访客户,对客户提出的问题进行现场验证,依据给予造成的损失及影响大小提出解决处理办法。
{品质管理制度表格}质量记录表格样式
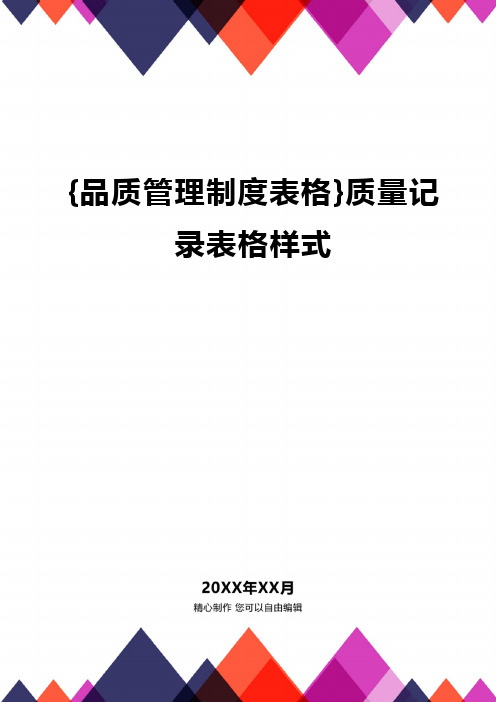
{品质管理制度表格}质量记录表格样式质量记录清单编号:SL/QB06质量记录清单编号:SL/QB06备注:在此说明使用者,日常保持标记符号#,周期形成无标记,本公司记录按月交质检部保存。
编制:审批:日期:控文件清单编号:SL/QB01编制:批准:日期:文件发放、回收记录编号:SL/QB02文件更改单编号:SL/QB03序号:外来文件清单编号:BT/QB04编制:批准:日期:编制:批准:日期:质量记录清单编号:SL/QB05编制:批准:日期:管理评审报告编号:SL/QB07序号:管理评审输入表编号:SL/QB08报告人/日:审批人/日:培训实施计划编号:SL/QB09序号:编制:组织者:日期:年月日培训内容记录编号:SL/QB10注:培训效果由教育人填写(好、中、差或考试得分)。
教育认可:温州市双联机械有限公司员工登记表编号:SL/QB11序号:设施验收单编号:SL/QB12序号:设备台帐编号:SL/QB13页码编制:日期:设施日常保养记录表编号:SL/QB14 设施名称:设施编号:保养人:使用部门负责人:月末确认/日期:设施检修计划编号:SL/QB15 执行部门:序号:编制:日期:批准:日期:设施检修单编号:SL/QB16 设施使用部门:序号:设施检修单编号:SL/QB16 设施使用部门:序号:顾客要求评审表编号:SL/QB17□初次评审□修订(原评审序号:)序号:电话/口头订货记录表编号:SL/QB18新产品可行性分析报告编号:SL/QB19序号:设计和开发策划书编号:SL/QB20序号:设计和开发输入清单编号:SL/QB21序号:设计和开发输入清单编号:SL/QB21序号:设计和开发确认表编号:SL/QB22序号:设计和开发验证报告编号:SL/QB23序号:试产报告编号:SL/QB24序号:客户试用报告编号:SL/QB25序号:新产品鉴定报告编号:SL/QB26序号:编写:日期:批准:日期:供方调查表编号:SL/QB27序号:填写说明:在□内肯定的打√;其他项目详细说明。
{品质管理制度表格}质量管理表格参考
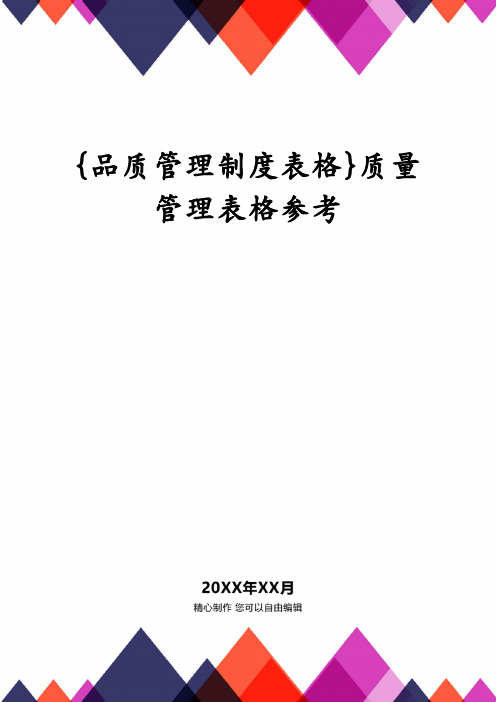
R-QP-004/002-A
培训记录表
No:
时间: 地点:
培训主题:
参加培训人员名单:
培训教师: 培训方式:
应到人员
签到
应到人员
签到
应到人员
签到
培训内容摘要:
考核成绩: 备注
R-QP-004/003-A
年度培训计划
No: 日期 受培训部门 参加培训人员 培训方式 培训内容 考核方式 备注
制造部(评审生 产能力及交货期)
填写人:日期:
评审结论
填写人:日期: 备注:1.本表适用于文本合同和有特殊要求的特殊合同产品的评审; 2.特殊合同产品要求评审部门:全体部门; 3.特殊合同评审结论一栏由总经理签名批准,其他由市场开发与业务部经理批准。
R-QP-008/001-A
合同目录
No.
序号
顾客名称
起用时间 报废申请人
设施报废单
设备编号 原价格
R-QP-005/008-A
起用时间 报废申请人
R-QP-005/008-A
日期 地点
工作环境卫生检查表
No:
检查记录
检查人 备注
R-QP-006/001-A
合同评审单
ﭐ初次评审ﭐ修订(原评审表号:)No:
顾客名称
定货日期 定货数量
交付 日期
顾客对产品明示
与潜在的要求
(技术要求、质量
要求、支持服务、
价格等)
填写人:日期:
本公司为满足顾 客要求作出的承 诺
市场开发与业务 部(评审合同的 合法、完整性、 明确性
填写人:日期: 填写人:日期:
采购部(评审所 需物料采购的能 力)
品质制度表格-XXXX新版质量记录表格 精品
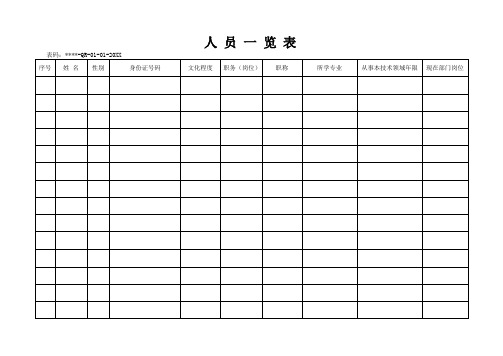
人员一览表人员档案目录人员基本情况登记表表码:****-QR-01-03-20XX专业人员上岗能力评价表表码:****-QR-01-04-20XX项目和设备操作人员授权表编制:审核:批准:时间:外来人员出入登记表注:此表由管理部门负责填写、管理。
年度培训计划表码:****-QR-02-01-20XX编制:批准:日期:人员培训记录表表码:****-QR-02-02-20XX年培训需求申请表表码:****-QR-02-03-20XX上岗前培训考评记录表年质量监督计划表码:****-QR-03-01-20XX编制:批准:日期:质量监督通知书表码:****-QR-03-02-20XX质量监督记录表码:****-QR-03-03-20XX年环境监控记录表码:****-QR-04-01-20XX注:此表由各使用部门负责填写,年底交综合部归档。
仪器设备管理台帐表码:****-QR-05-01-20XX 更新时间:注:“溯源方式”栏填写送校、送检、自校、比对、功能检查等。
编制:审核:日期:辅助设备管理台帐表码:****-QR-05-02-20XX 更新时间:仪器设备购置申请表表码:****-QR-05-03-20XX注:此表在办完手续后,交办公室存档备案。
小型(辅助)设备购置申请表表码:****-QR-05-04-20XX仪器设备验收单表码:****-QR-05-05-20XX仪器设备使用记录表码:****-QR-05-06-20XX仪器设备档案目录表码:****-QR-05-07-20XX年仪器设备维护计划表码:****-QR-05-08-20XX编制:审核:日期:仪器设备维护记录表表码:****-QR-05-09-20XX大型设备配套零部件登记表表码:****-QR-05-10-20XX仪器设备脱离控制后验收记录表码:****-QR-05-11-20XX仪器设备维修记录表码:****-QR-05-12-20XX注:此表格交管理部门存入设备档案。
品质管理制度表单

品质管理制度表单一、总则1.1 为加强对产品品质的管理,提高产品质量,确保产品符合相关法律法规和标准要求,公司特制定本品质管理制度。
1.2 本制度适用于公司的所有生产环节,包括原材料采购、生产制造、检验检测等各个环节。
1.3 公司将持续改进品质管理制度,确保其符合公司及国家相关法律法规。
二、品质管理的基本原则2.1 尊重客户需求,不断提高产品品质。
2.2 以客户为中心,不断优化服务流程,提高客户满意度。
2.3 注重团队合作,倡导员工参与,共同维护品质管理体系。
2.4 依靠科学技术,不断提高生产技术水平,确保产品品质稳定。
2.5 加强内部管理,建立健全的品质管理机制,形成全员品质管理的局面。
三、品质管理责任3.1 公司高层领导履行全面品质管理责任,确保品质管理制度的有效实施。
3.2 公司各部门领导分工负责,确保品质管理制度的顺利推进。
3.3 每位员工都是品质管理的参与者,应当积极配合公司的品质管理要求。
3.4 员工个人对自己的工作负责,保证产品品质符合标准要求。
3.5 品质管理部门负责监督品质管理工作的实施情况,并提出改进建议。
四、品质管理流程4.1 原材料采购环节:公司要求供应商必须提供符合国家标准的产品,严格把关采购品质。
4.2 生产制造环节:公司设立专门的质检部门,对生产过程进行全程监控,确保产品品质符合要求。
4.3 检验检测环节:公司要求所有产品必须经过严格的检验检测,确保产品的品质稳定。
4.4 售后服务环节:公司重视售后服务,对产品质量问题及时进行处理,保证客户权益。
五、品质管理措施5.1 建立健全的品质管理档案,确保产品质量的可追溯性。
5.2 开展定期的品质管理培训,提高员工的品质意识和管理水平。
5.3 建立品质管理奖惩机制,激励员工积极参与品质管理工作。
5.4 定期对品质管理体系进行评估,对制度进行改进和完善。
六、品质管理的监督和审查6.1 公司成立专门的品质管理督导组,负责对品质管理工作进行监督和检查。
品质制度表格-质量管理表格大全1页2 精品

质量管理表格大全第一章质量管理部职责描述 (5)(一)质量管理部的工作职责 (5)第二章质量管理部组织管理 (6)(一)质量管理工作计划表 (6)(二)质量目标达成计划表 (6)(三)质量教育年度计划表 (6)(四)竞争产品质量比较表 (7)(五)质量计划实施情况检查表 (7)第三章质量方针与质量目标管理 (8)(一)质量方针实施对策表 (8)(二)质量方针实施评审表 (8)(三)质量方针管理工作流程 (9)(四)部门(车间)质量目标展开表 (10)(五)质量目标管理统计月报表 (11)(六)质量目标分解实施评审表 (11)(七)质量目标管理工作流程 (13)第四章供应质量管理 (14)(一)质量检验委托单 (14)(二)进厂零件质量检验表 (14)(三)零件质量检验报告表 (14)(四)采购材料检验报告表 (15)(五)材料试用检验通知单 (15)(六)说明书质量检验报告 (15)(七)采购设备检验报告单 (16)(八)特采/让步使用申请单 (17)(九)进厂检验情况日报表 (17)(十)供应商基本资料表 (17)(十一)供应商质量评价表 (18)(十二)合格供应商考核表 (19)(十三)供应商综合评审表 (20)(十四)供应商质量管理检查表 (21)(十五)进料检验工作流程 (22)(十六)检验状态标识流程 (23)(十七)供应商管理工作流程 (24)第五章制程质量管理 (25)(一)制程作业检查表 (25)(二)生产条件通知单 (25)(三)生产事前检查表 (25)(四)生产过程记录卡 (26)(五)过程控制标准表 (26)(六)产品质量标准表 (27)(七)产品质量检验表 (27)(八)质量因素变动表 (27)(九)操作标准变更通知单 (28)(十)生产过程检验标准表 (28)(十一)产品质量抽查记录 (28)(十二)制程质量管理工作流程 (29)(十三)质量分析统计工作流程 (30)(十四)质量指标报告工作流程 (31)(十五)制程质量异常处理工作流程 (32)(十六)工序质量分析表 (33)(十七)工序质量评定表 (33)(十八)工序质量跟踪卡 (34)(十九)工序控制点明细表 (34)(二十)工序质量审核记录表 (34)(二十一)检验工序作业指导书 (34)(二十二)工序质量检验评定表 (35)(二十三)工序操作标准通知单 (36)(二十四)工序质量异常报告表 (36)(二十五)工序质量控制工作流程 (38)(二十六)工序质量检验工作流程 (39)第六章质量检验管理 (40)(一)试验委托单 (40)(二)试验报告单 (40)(三)检验通知单 (40)(四)产品抽查汇总表单 (41)(五)待出厂产品检验表 (41)(六)产品出厂检验表单 (41)(七)产品质量检验报告 (42)(八)检验计划签审工作流程 (43)(九)成品抽样检验工作流程 (44)(十)成品入库送检工作流程 (45)(十一)产品样件检验工作流程 (46)(十二)工厂出货送检工作流程 (47)第七章质量控制管理 (48)(一)质量管理标准表 (48)(二)质量标准变动表 (48)(三)产品质量管理表 (48)(四)质量因素变动表 (49)(五)质量控制管理工作流程 (50)(六)质量标准制定工作流程 (51)(七)质量记录控制工作流程 (52)(八)质量管理小组资料登记表 (53)(九)质量管理小组会议报告表 (54)(十)质量管理小组活动计划表 (54)(十一)质量管理小组活动记录表 (55)(十二)质量管理小组活动报告表 (55)(十三)QC小组活动成果评审表 (55)(十四)质量管理小组组织建立流程 (57)(十五)质量管理小组活动组织流程 (58)(十六)清理和整理活动检查表 (59)(十七)清理和整理效果检查表 (60)(十八)清洁和保养活动检查表 (61)(十九)清洁和保养效果检查表 (62)(二十)素养活动检查表 (63)(二十一)素养效果检查表 (64)第八章不合格品管理 (66)(一)质量异常通知单 (66)(二)质量异常报告单 (66)(三)质量异常处理单 (66)(四)不合格品审理单 (67)(五)质量不良记录表 (67)(六)质量不良分析表 (68)(七)装配不良处理表 (68)(八)产品退货统计表 (68)(九)不良项目调查表 (69)(十)产品返修通知单 (69)(十一)不合格零件处理单 (69)(十二)不合格现象预防表 (70)(十三)不合格产品管理流程 (71)(十四)不合格现象分析流程 (72)(十五)报废品处理工作流程 (73)(十六)质量处罚工作流程 (74)(十七)预防措施工作流程 (75)第九章质量改进管理 (76)(一)产品质量改进记录表 (76)(二)产品质量改进分析表 (76)(三)质量改进评审记录表 (76)(四)质量改进结果记录表 (77)(五)质量持续改进工作流程 (78)(六)质量问题解决工作流程 (79)第十章质量成本管理 (80)(一)质量预防费用统计表 (80)(二)质量鉴定费用统计表 (80)(三)质量内部故障统计表 (80)(四)质量外部故障统计表 (80)(五)质量成本统计报告表 (81)(六)质量成本损失估计表 (81)(七)质量改进费用汇总表 (82)(八)质量培训费用计算表 (82)(九)质量奖励费用计算表 (82)(十)质量停工损失报告表 (82)(十一)质量事故处理费用计算表 (83)(十二)产品降级/降价处理报告表 (83)(十三)车间质量管理费月报表 (83)(十四)车间质量损失费月报表 (84)(十五)质量成本管理工作流程 (86)(十六)质量成本控制工作流程 (87)第十一章质量管理体系审核及建立 (88)(一)质量管理体系审核计划表 (88)(二)质量管理体系审核检查表 (88)(三)质量管理体系审核报告表 (89)(四)质量文件评审记录表 (89)(五)质量文件发放回收表 (92)(六)质量文件更改申请表 (92)(七)质量文件销毁申请表 (93)(八)过程业绩评审报告表 (93)(九)纠正预防措施处理单 (94)(十)质量文件记录清单 (94)(十一)不符合项报告表 (95)(十二)质量体系建立工作流程 (96)(十三)质量体系文件管理流程 (97)(十四)质量体系内审工作流程 (98)(十五)质量体系运行工作流程 (99)(十六)质量体系完善工作流程 (100)第一章质量管理部职责描述(一)质量管理部的工作职责质量管理部工作职责一览表第二章质量管理部组织管理(一)质量管理工作计划表编号:日期:年月(二)质量目标达成计划表编订人:审核人:发布时间:执行期限:(三)质量教育年度计划表填写日期:(四)竞争产品质量比较表产品名称:填写日期:(五)质量计划实施情况检查表填写日期:第三章质量方针与质量目标管理(一)质量方针实施对策表(二)质量方针实施评审表时间:年月日评审人:(三)质量方针管理工作流程(四)部门(车间)质量目标展开表(五)质量目标管理统计月报表单位:填写日期:单位负责人:制表人:(六)质量目标分解实施评审表部门:考核日期:年月日~年月日编制:审核:(七)质量目标管理工作流程第四章供应质量管理(一)质量检验委托单编号:填写日期:(二)进厂零件质量检验表零件编号:零件名称:号码:(三)零件质量检验报告表编号:填写日期:(四)采购材料检验报告表编号:填写日期:(五)材料试用检验通知单编号:填写日期:(六)说明书质量检验报告(七)采购设备检验报告单(八)特采/让步使用申请单编号:特采/让步使用类型:□原材料 □成品 填写日期: 年 月 日(九)进厂检验情况日报表填写日期:页次: (十)供应商基本资料表(十一)供应商质量评价表(十二)合格供应商考核表编号:考核时间:从年月日至年月日制表:审核:批准:(十三)供应商综合评审表编号:填写日期:(十四)供应商质量管理检查表□协作厂商□试用厂商□原料供应商□外协加工厂商填写日期:检查员:(十五)进料检验工作流程(十六)检验状态标识流程(十七)供应商管理工作流程第五章 制程质量管理(一)制程作业检查表注:使用记号:“√”妥善 “×”故障 “△”需改进(二)生产条件通知单编号:填写日期:(三)生产事前检查表(四)生产过程记录卡批号:规格:工令:用途:编号:经办:审核:(五)过程控制标准表(六)产品质量标准表(七)产品质量检验表审核:质量检验:(八)质量因素变动表编号:填写日期:(九)操作标准变更通知单编号:填写日期:审批:复核:(十)生产过程检验标准表产品名称:部门:页次:(十一)产品质量抽查记录机器名称:班别:抽查员:主管:(十四)质量指标报告工作流程(十五)制程质量异常处理工作流程(十七)工序质量评定表工程名称:编号:质检员签字:年月日(十九)工序控制点明细表(二十)工序质量审核记录表(二十一)检验工序作业指导书(二十二)工序质量检验评定表(二十三)工序操作标准通知单审核:填单人:(二十四)工序质量异常报告表(二十五)工序质量控制工作流程(二十六)工序质量检验工作流程第六章质量检验管理(一)试验委托单编号:填写日期:(二)试验报告单报告号码:(三)检验通知单编号:填写日期:主管:检验:(四)产品抽查汇总表单编号:填写日期:(五)待出厂产品检验表编号:填写日期:检验员:复检:(六)产品出厂检验表单编号:填写日期:(七)产品质量检验报告编号:填写日期:主管:检验员:第七章质量控制管理(一)质量管理标准表产品名称:(二)质量标准变动表(三)产品质量管理表(四)质量因素变动表编号:填写日期:(五)质量控制管理工作流程。
品质管理制度表格产品质量和食品安全专项整治工作总体情况表
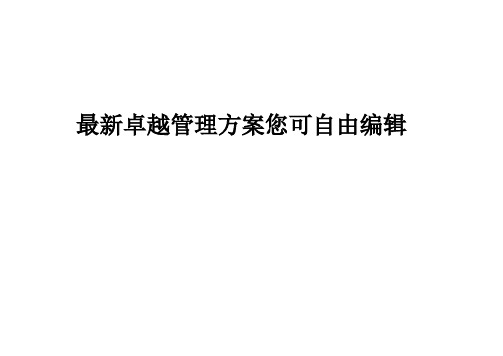
最新卓越管理方案您可自由编辑附件1:检查地区:荆州市产品质量和食品安全专项整治工作总体情况表检查时间:验收内容验收要点评价记录验收方法备注质是否事实记录管理制度表格产品1.1组织机构建立和工作机制运行情况1.2结合实际,制定工作实施方案情况1.3深一、各级入动员,政府组织部署专领导情况项整治工作情况1.4深入基层,督察督办情况1.5广泛宣传,营造良好舆论氛围宣传二、农产2.1目1.1.1各级政府领导高度重视,召开会议研究、部署专项整治工作。
1.1.2将专项整治工作列入政府工作目标,建立工作责任制;1.1.3成立领导小组和工作机构,配备专职工作人员,场所、经费得到落实。
1.2.1结合辖区实际制定了书面行动方案,明确了整治重点、措施和目标。
1.2.2明确职责分工,将整治任务分解落实到具体单位。
1.2.3各有关职能部门按照职责制定专项工作实施方案,协调配合共同开展专项整治。
1.3.1通过召开会议、印发文件、举办出征仪式等进行层层动员部署。
1.3.2乡镇基层政府和街道、企业等基层单位了解专项整治工作目标、任务,积极参与专项整治。
1.3.3三次现场会议后,及时传达贯彻落实会议精神,进行再动员、再部署。
1.4.1各级政府领导带队,深入基层,督促检查专项整治工作;1.4.2各职能部门组织工作组、督查组等,深入基层,指导、督促专项整治工作。
1.5.1各级政府和职能部门的工作方案中包括宣传工作计划,或制定有专门的宣传工作方案;1.5.2在报刊、广播、电视、网络等媒体上,定期和不定期的宣传专项整治成果;1.5.3建立并有效运转举报投诉制度,广泛发动和正确引导公众积极参与专项整治。
2.1.1全省大中城市的农产品批发市场100%纳入质量安全听取汇报,查阅文档听取汇报,查阅文档听取汇报,查阅文档,现场检查听取汇报,查阅文档听取汇报,查阅文档听取汇报,查阅文档,座谈调查听取汇报,查阅文档听取汇报,查阅文档。
座谈调查听取汇报,查阅文档听取汇报,查阅文档,座谈调查听取汇报,查阅文档,座谈调查,听取汇报,查阅文档听取汇报,查阅文档听取汇报,查阅文档,座谈调查听取汇报,查阅文档,现事实记录品质量安全整治标完成情况2.2工作开展情况2.3长效机制建立情况监测范围;场检查2.1.2农产品生产基地、规模种植养殖场、农业标准化示听取汇报,查阅文档,现事实记录范区(场)使用违禁农药兽药和饲料添加剂问题基本解决;场检查2.1.3蔬菜、畜(禽)、水产品农药兽药残留超标率及检出听取汇报,查阅文档,现事实记录率进一步下降;场检查2.1.4杜绝违规生产、销售和使用甲胺磷、对硫磷、甲基听取汇报,查阅文档,现事实记录对硫磷、久效磷、磷胺等5种高毒农药。
品质制度表格-质量管理记录表格 精品
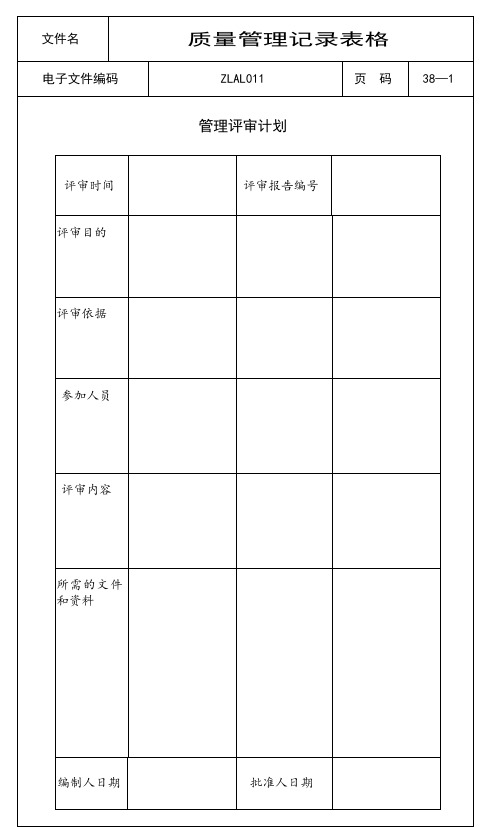
星期四
星期五
月日
星期六
月日
星期日
月日
文件名
质量管理记录表格
电子文件编码
ZLAL011
页码
38—17
设备仪器保养记录
编号
设备仪器名称
保养内容
保养人
时间
文件名
质量管理记录表格
电子文件编码
ZLAL011
页码
38—18
设备仪器维修记录表
维修日期
维修人员
设备责任人
设备名称
统一编号
设备故障原因:
维修过程及安全措施:
项目名称:
项目编号:
立项时间:
完成时间:
项目性质:
运行日期:
项目设计和开发目标
项目试运行的基本情况
项目实际功能概述
业务主管意见
年月日
文件名
质量管理记录表格
电子文件编码
ZLAL011
页码
38—10
现有产品功能改进项目报告书
编号:
需求单位:
改进项目编号:
主要需求
需求单位负责人审批:
年月日
文件名
质量管理记录表格
单位
数量
单价
金额
保质期
质量
备注
合计
主管
会计
复核
实物负责人
制表
文件名
质量管理记录表格
电子文件编码
ZLAL011
页码
38—25
质量记录表格清单
序号
质量记录名称
记录编码
对应文
件编码
版号
保存
期限
保存部
门/人
备注
文件名
质量管理记录表格
品质管理制度与表格
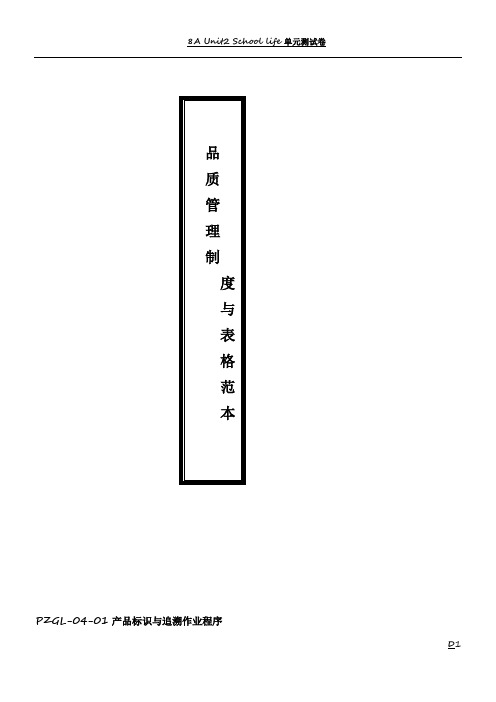
PZGL-04-01产品标识与追溯作业程序产品标识与追溯作业程序1.目的:明确生产各个过程中的标识要求,以防止物料及产品的混用或误用,特制定本程序。
2.适用范围各种产品、物料。
3.实施程序3.1.标示作业要求。
3.1.1.采购负责要求供货商对送货的每个大小包装物料均需有物料品名、料号、数量的标志。
3.1.2.对物料框上残留的旧有物料标志依“谁使用谁清除”原则,由各使用单位负责作清除。
3.1.3.进料检验后,由检验员标示每批物料的检验状态(贴不合格标、合格标或待处理标),一批物料只能有一种有效检验状态标识,并根据检验结果存入相应分区。
检验现场仓库应保证有待检区、良品区、不良品区,并有明显的区域划分和标志牌。
3.1.4.在进料仓储过程中,由仓管员将品管员检验后的物料存入相应类别分区。
仓库现场应保证有良品区、不良品区及特殊物料分区(DR铜物料区等),并有明确的区域划分及标志。
良品与不良品不可混放。
特殊情况下(如库位紧张时)需暂借用与本物料质量不相适的区域时,相关人员必须做好沟通,并有大而显眼的警告标志,确保物料不被误用,仓储作业员在备料时对每种物料进行料号、数量、工单等内容的标示。
3.1.5.在制程过程中分检出来的不良品须用专用收集容器存放,并用显眼的红色标志物或标签进行标示。
3.1.6.制程品管对不良品进行确认时,须对每篮每袋包装物贴红色不合格标,除此不合格标外,不能有其它贴标。
3.1.7.生产现场由制造单位划分出不良品区,并有醒目标志。
3.1.8.在成品检验过程中,由生产单位对送检的成品进行数量、机型、订单及工单的标志即工单入库条,由成品检验员根据检验结果加盖QC合格章或红色不合格贴标。
生产单位应保证生产现场有待检区,并有明确的区域划分及标志。
3.2.标示要求。
3.2.1.进料检验、半成品入库检验所用检验标见《进料检验作业规范》。
3.2.2.在仓库存放和发放的物料应有品管人员检验后的标志、品名、型号或规格、必要的制造商及制造日期,保持原包装状态的用包装上的标志。
品质部管理制度表
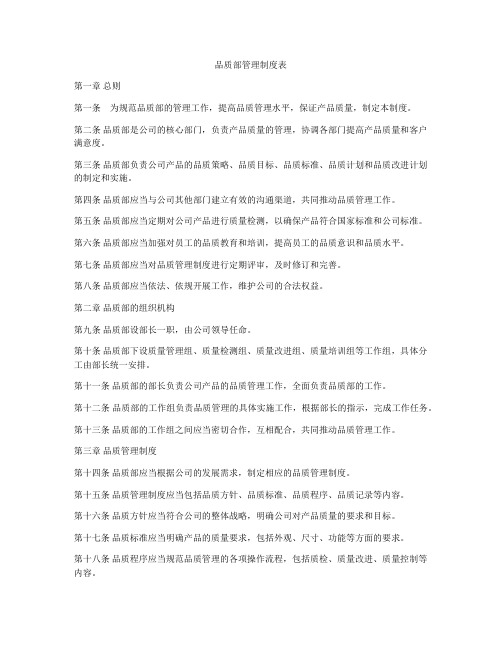
品质部管理制度表第一章总则第一条为规范品质部的管理工作,提高品质管理水平,保证产品质量,制定本制度。
第二条品质部是公司的核心部门,负责产品质量的管理,协调各部门提高产品质量和客户满意度。
第三条品质部负责公司产品的品质策略、品质目标、品质标准、品质计划和品质改进计划的制定和实施。
第四条品质部应当与公司其他部门建立有效的沟通渠道,共同推动品质管理工作。
第五条品质部应当定期对公司产品进行质量检测,以确保产品符合国家标准和公司标准。
第六条品质部应当加强对员工的品质教育和培训,提高员工的品质意识和品质水平。
第七条品质部应当对品质管理制度进行定期评审,及时修订和完善。
第八条品质部应当依法、依规开展工作,维护公司的合法权益。
第二章品质部的组织机构第九条品质部设部长一职,由公司领导任命。
第十条品质部下设质量管理组、质量检测组、质量改进组、质量培训组等工作组,具体分工由部长统一安排。
第十一条品质部的部长负责公司产品的品质管理工作,全面负责品质部的工作。
第十二条品质部的工作组负责品质管理的具体实施工作,根据部长的指示,完成工作任务。
第十三条品质部的工作组之间应当密切合作,互相配合,共同推动品质管理工作。
第三章品质管理制度第十四条品质部应当根据公司的发展需求,制定相应的品质管理制度。
第十五条品质管理制度应当包括品质方针、品质标准、品质程序、品质记录等内容。
第十六条品质方针应当符合公司的整体战略,明确公司对产品质量的要求和目标。
第十七条品质标准应当明确产品的质量要求,包括外观、尺寸、功能等方面的要求。
第十八条品质程序应当规范品质管理的各项操作流程,包括质检、质量改进、质量控制等内容。
第十九条品质记录应当记录品质管理的各个环节,包括质检结果、质量改进措施、质量控制情况等。
第四章品质管理的实施第二十条品质部应当按照品质管理制度的要求,定期开展产品质量检测工作。
第二十一条品质部应当加强对产品生产过程的监控,及时发现并解决生产中的质量问题。
品控管理规章制度汇编表
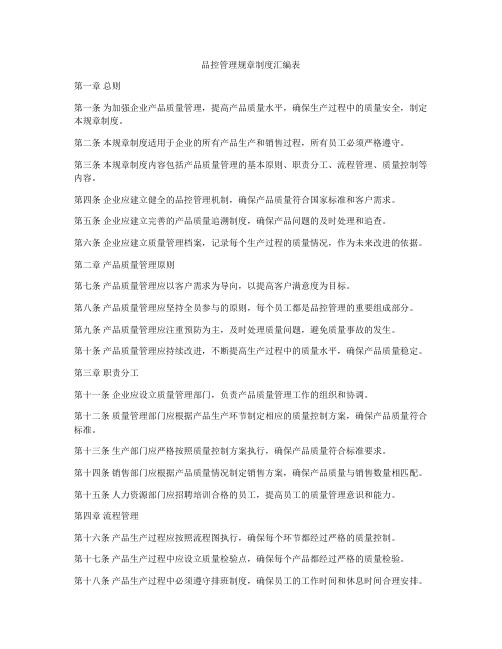
品控管理规章制度汇编表第一章总则第一条为加强企业产品质量管理,提高产品质量水平,确保生产过程中的质量安全,制定本规章制度。
第二条本规章制度适用于企业的所有产品生产和销售过程,所有员工必须严格遵守。
第三条本规章制度内容包括产品质量管理的基本原则、职责分工、流程管理、质量控制等内容。
第四条企业应建立健全的品控管理机制,确保产品质量符合国家标准和客户需求。
第五条企业应建立完善的产品质量追溯制度,确保产品问题的及时处理和追查。
第六条企业应建立质量管理档案,记录每个生产过程的质量情况,作为未来改进的依据。
第二章产品质量管理原则第七条产品质量管理应以客户需求为导向,以提高客户满意度为目标。
第八条产品质量管理应坚持全员参与的原则,每个员工都是品控管理的重要组成部分。
第九条产品质量管理应注重预防为主,及时处理质量问题,避免质量事故的发生。
第十条产品质量管理应持续改进,不断提高生产过程中的质量水平,确保产品质量稳定。
第三章职责分工第十一条企业应设立质量管理部门,负责产品质量管理工作的组织和协调。
第十二条质量管理部门应根据产品生产环节制定相应的质量控制方案,确保产品质量符合标准。
第十三条生产部门应严格按照质量控制方案执行,确保产品质量符合标准要求。
第十四条销售部门应根据产品质量情况制定销售方案,确保产品质量与销售数量相匹配。
第十五条人力资源部门应招聘培训合格的员工,提高员工的质量管理意识和能力。
第四章流程管理第十六条产品生产过程应按照流程图执行,确保每个环节都经过严格的质量控制。
第十七条产品生产过程中应设立质量检验点,确保每个产品都经过严格的质量检验。
第十八条产品生产过程中必须遵守排班制度,确保员工的工作时间和休息时间合理安排。
第十九条产品生产过程中应做好材料和设备的保养和维护工作,确保生产设施的正常运转。
第二十条产品生产过程中应保持生产环境的清洁和整洁,确保产品质量不受外界因素影响。
第五章质量控制第二十一条产品质量控制应遵循AQL标准,根据不同产品类型设定合理的抽样检验方案。
品质管理制度表格项目质量办法
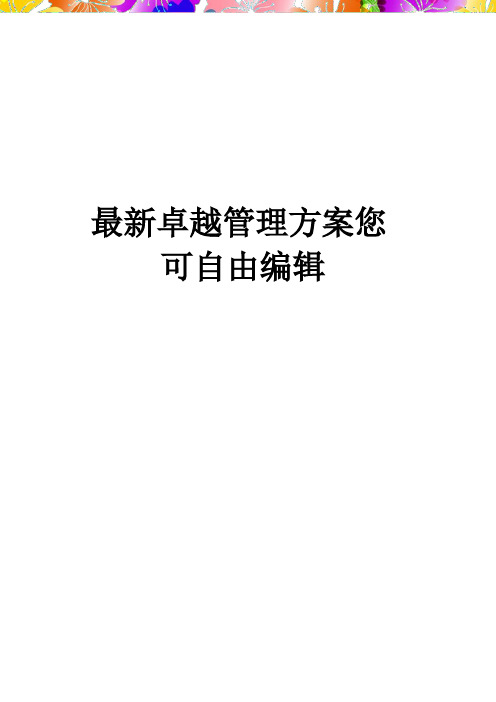
最新卓越管理方案您可自由编辑第一条三个部门直接受总工程师领导,全面履行质量技术管理工作。
第二条项目经理部的经营部、物资部、设备部、人劳部是质量工作的相关部门,其部门职能人员是质量工作的相关责任者。
第三条项目经理是企业法人代表在项目上的代理人,对项目工程质量实行全面管理。
品质管理制度表格项目质量办法项目总工程师在项目经理授权下,代表经理对质量管理实施组织、领导和质量决策,并接受上级总工程师的指导。
第四条项目内部监理工程师在总工程师或工程部的直接领导下行使其质量工作权利,项目管理层应支持内部监理的工作。
第五条操作层生产班组(或工段)设质检员,从事自检、互检、交接检等质检工作。
第六条项目质量质量管理体系配合“政府监督”、“社会监理”工作,确保“企业自检”环节的有效性。
及时收集质量信息,并采取有效的纠正和预防措施。
第一章项目质量管理职责及权限第七条项目经理的质量职责1.项目经理是工程质量第一责任人,对工程质量负全面领导责任。
2.负责贯彻执行国家有关质量工作方针政策,工程建设法律、法规、技术标准和规范。
3.负责组织建立质量管理体系,使其有效运行,并在运行中不断改进。
4.根据公司质量目标控制计划要求,组织编制质量目标实施计划和具体实施措施。
5.组织编写项目施工组织设计,并合理进行资源配备(人员、设备、资金等)。
6.指定并授权总工程师负责质量管理日常工作。
7.负责加强全面质量管理,处理好费用、进度与质量的关系,在确保质量的前提下抓好进度和费用管理。
8.主持建立项目的激励机制,根据局及公司有关要求组织制定具体的质量奖罚办法(方案)。
第八条项目副经理的质量职责1.项目副经理对工程质量负直接领导责任2.贯彻执行国家质量工作方针政策,落实执行工程建设技术标准和规范。
3.全面负责项目施工组织设计和质量目标实施计划的落实。
4.监督检查各部门质量职责的执行情况,协调和处理有关接口工作。
5.贯彻“预防为主”的方针,并领导处理质量缺陷工作。
{品质管理制度表格}完整质量管理表格

{品质管理制度表格}完整质量管理表格完整质量管理表格目录第一章质量管理部职责描述 (6)(一)质量管理部的工作职责 (6)第二章质量管理部组织管理 (7)(一)质量管理工作计划表 (7)(二)质量目标达成计划表 (7)(三)质量教育年度计划表 (7)(四)竞争产品质量比较表 (8)(五)质量计划实施情况检查表 (8)第三章质量方针与质量目标管理 (9)(一)质量方针实施对策表 (9)(二)质量方针实施评审表 (9)(三)质量方针管理工作流程 (10)(四)部门(车间)质量目标展开表 (11)(五)质量目标管理统计月报表 (11)(六)质量目标分解实施评审表 (12)(七)质量目标管理工作流程 (13)第四章供应质量管理 (14)(一)质量检验委托单 (14)(二)进厂零件质量检验表 (14)(三)零件质量检验报告表 (14)(四)采购材料检验报告表 (15)(五)材料试用检验通知单 (15)(六)说明书质量检验报告 (15)(七)采购设备检验报告单 (16)(八)特采/让步使用申请单 (17)(九)进厂检验情况日报表 (17)(十)供应商基本资料表 (17)(十一)供应商质量评价表 (18)(十二)合格供应商考核表 (19)(十三)供应商综合评审表 (20)(十四)供应商质量管理检查表 (21)(十五)进料检验工作流程 (22)(十六)检验状态标识流程 (23)(十七)供应商管理工作流程 (24)第五章制程质量管理 (25)(一)制程作业检查表 (25)(二)生产条件通知单 (25)(三)生产事前检查表 (25)(四)生产过程记录卡 (26)(五)过程控制标准表 (26)(六)产品质量标准表 (27)(七)产品质量检验表 (27)(八)质量因素变动表 (27)(九)操作标准变更通知单 (28)(十)生产过程检验标准表 (28)(十一)产品质量抽查记录 (28)(十二)制程质量管理工作流程 (29)(十三)质量分析统计工作流程 (30)(十四)质量指标报告工作流程 (31)(十五)制程质量异常处理工作流程 (32)(十六)工序质量分析表 (33)(十七)工序质量评定表 (33)(十八)工序质量跟踪卡 (34)(十九)工序控制点明细表 (34)(二十)工序质量审核记录表 (34)(二十一)检验工序作业指导书 (34)(二十二)工序质量检验评定表 (35)(二十三)工序操作标准通知单 (36)(二十四)工序质量异常报告表 (36)(二十五)工序质量控制工作流程 (38)(二十六)工序质量检验工作流程 (39)第六章质量检验管理 (40)(一)试验委托单 (40)(二)试验报告单 (40)(三)检验通知单 (40)(四)产品抽查汇总表单 (41)(五)待出厂产品检验表 (41)(六)产品出厂检验表单 (41)(七)产品质量检验报告 (42)(八)检验计划签审工作流程 (43)(九)成品抽样检验工作流程 (44)(十)成品入库送检工作流程 (45)(十一)产品样件检验工作流程 (46)(十二)工厂出货送检工作流程 (47)第七章质量控制管理 (48)(一)质量管理标准表 (48)(二)质量标准变动表 (48)(三)产品质量管理表 (48)(四)质量因素变动表 (49)(五)质量控制管理工作流程 (50)(六)质量标准制定工作流程 (51)(七)质量记录控制工作流程 (52)(八)质量管理小组资料登记表 (53)(九)质量管理小组会议报告表 (54)(十)质量管理小组活动计划表 (54)(十一)质量管理小组活动记录表 (55)(十二)质量管理小组活动报告表 (55)(十三)QC小组活动成果评审表 (55)(十四)质量管理小组组织建立流程 (57)(十五)质量管理小组活动组织流程 (58)(十六)清理和整理活动检查表 (59)(十七)清理和整理效果检查表 (60)(十八)清洁和保养活动检查表 (61)(十九)清洁和保养效果检查表 (62)(二十)素养活动检查表 (63)(二十一)素养效果检查表 (64)第八章不合格品管理 (66)(一)质量异常通知单 (66)(二)质量异常报告单 (66)(三)质量异常处理单 (66)(四)不合格品审理单 (67)(五)质量不良记录表 (67)(六)质量不良分析表 (68)(七)装配不良处理表 (68)(八)产品退货统计表 (68)(九)不良项目调查表 (69)(十)产品返修通知单 (69)(十一)不合格零件处理单 (69)(十二)不合格现象预防表 (70)(十三)不合格产品管理流程 (71)(十四)不合格现象分析流程 (72)(十五)报废品处理工作流程 (73)(十六)质量处罚工作流程 (74)(十七)预防措施工作流程 (75)第九章质量改进管理 (76)(一)产品质量改进记录表 (76)(二)产品质量改进分析表 (76)(三)质量改进评审记录表 (76)(四)质量改进结果记录表 (77)(五)质量持续改进工作流程 (78)(六)质量问题解决工作流程 (79)第十章质量成本管理 (80)(一)质量预防费用统计表 (80)(二)质量鉴定费用统计表 (80)(三)质量内部故障统计表 (80)。
{品质管理制度表格}品质管理表格文件和质量记录控制程序

{品质管理制度表格}品质管理表格文件和质量记录控制程序品质管理制度表格包括了品质管理表格文件和质量记录控制程序。
以下是一个示例:品质管理表格文件:1.品质目标设定表格:用于记录公司或部门的品质目标设定,并对每个目标进行详细描述,包括目标的量化指标、完成期限和负责人。
2.品质责任分配表格:用于明确品质管理的责任分配,并记录每个岗位或部门的品质管理职责和权限。
3.品质风险评估表格:用于评估品质管理过程中的风险,并采取相应的控制措施。
4.品质管理流程图和流程描述表格:用于记录每个品质管理流程的具体步骤,并明确流程中的关键控制点和相关部门或岗位。
5.品质改进计划表格:用于记录品质改进计划,并对计划进行跟踪和评估。
6.客户投诉管理表格:用于记录客户投诉,并进行分类和统计,以便对常见问题进行分析和解决。
7.品质培训记录表格:用于记录品质培训的内容、时间、地点和参与人员,并对培训效果进行评估。
8.供应商评价表格:用于评估供应商的品质管理水平,并根据评估结果决定是否与供应商保持合作关系。
质量记录控制程序:1.质量记录管理流程:明确质量记录的管理流程,包括记录的创建、审批、存档、检索和销毁等步骤。
2.质量记录索引表格:用于记录所有质量记录的详细信息,包括记录的名称、编号、日期、创建者和存档位置等。
3.质量记录存档要求表格:明确质量记录的存档要求,包括存档的格式、存储介质、存档期限和存档责任等。
4.质量记录检索程序:描述如何根据需要检索质量记录,并明确相关的程序和要求。
5.质量记录销毁程序:明确质量记录销毁的程序和要求,包括销毁的条件、方式和责任等。
6.质量记录审计程序:描述如何对质量记录进行审计,确保记录的完整性和准确性。
以上所列的品质管理表格文件和质量记录控制程序是一个示例,可以根据实际情况进行个性化的调整和修改。
这些表格和程序的目的是为了确保公司的品质管理工作能够有条不紊地进行,从而提高产品和服务的质量,满足客户的需求和期望。
品质管理制度表格全套

品质管理制度表格全套目录第一章总则第一条本制度的目的和依据第二条适用范围第三条重要术语定义第二章质量管理职责第四条质量管理部门的职责第五条生产部门的职责第六条销售部门的职责第三章品质管理体系第七条品质管理体系的构建第八条质量管理流程第九条质量管理文件管理第四章品质检验标准第十条检验标准的制定第十一条检验项目第十二条检验方法第五章不合格品处理第十三条不合格品处理程序第十四条责任追究第六章品质管理评估第十五条品质管理评估程序第十六条改善措施第七章品质管理培训第十七条品质管理培训计划第十八条品质管理考核第八章其他规定第十九条其他相关规定第一章总则第一条本制度的目的和依据为了规范企业的质量管理工作,提高产品和服务的质量,确保客户满意度,特制定本品质管理制度。
本制度遵循相关法律法规和企业内部管理制度,制定并执行,具有法律效力。
第二条适用范围本制度适用于企业内部各部门及相关人员,在企业的品质管理工作中必须遵守本制度规定。
第三条重要术语定义1. 品质管理:指企业在生产经营活动中对产品和服务的质量进行规范管理的工作。
2. 检验标准:指产品或服务的检验要求和标准。
3. 不合格品:指未能符合检验标准要求的产品或服务。
第二章质量管理职责第四条质量管理部门的职责1. 制定和完善品质管理制度,指导全公司质量管理工作;2. 负责产品和服务的质量检验,并制定检验标准;3. 定期对质量管理体系进行评估,提出改进建议。
第五条生产部门的职责1. 严格执行品质管理制度,确保产品符合质量要求;2. 按照质量管理部门的检验标准进行产品检验;3. 及时处理不合格品,追究责任。
第六条销售部门的职责1. 确保销售的产品符合质量要求;2. 及时反馈客户的质量问题,协助质量管理部门进行处理;3. 做好售后服务工作,提高客户满意度。
第三章品质管理体系第七条品质管理体系的构建1. 建立完善的质量管理体系,明确各项质量管理流程和标准;2. 制定品质管理文件,包括质量手册、程序文件、记录表等。
品质制度表格-质量记录表卡 精品
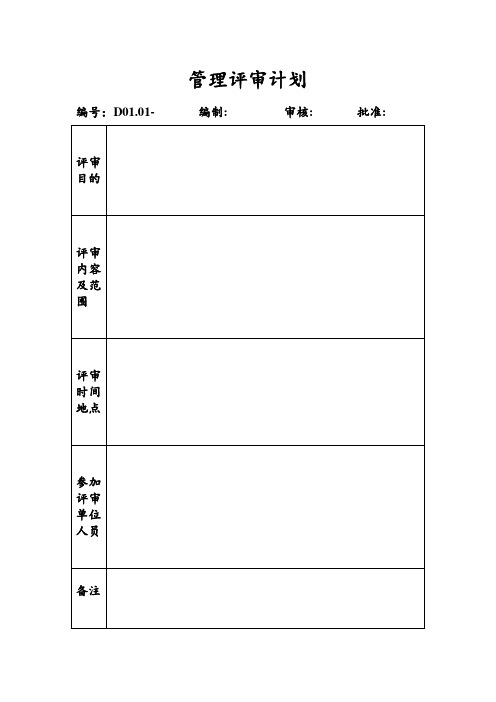
编号:D01.01- 编制: 审核: 批准:编号:D01.02- 编制: 审核: 批准:管理评审会议记录编号:D01.03-产品追溯报告编号:D01.04-内部质量审核计划编号:D01.05- 编制: 批准:内部质量审核检查表编号:D01.06-内审项目和日程安排表编号:D01.07- 编制: 审核:内部质量体系审核不合格项分布表编号:D01.08-内部质量审核报告编号:D01.09- 编制: 审核:不合格项报告单编号:D01.10-纠正和预防措施处理单编号:D01.11-不合格品评审记录编号:D01.12-质量印签台账编号:D01.13-焊缝施焊记录编号:D02.01-焊接检查记录表理化试验委托单检查委托人委托日期年月日压力容器压力试验记录编号:D02.04-焊缝返修通知单返修焊缝施焊记录顾客提供产品的验收记录检测设备采购计划检测设备分布表仪器设备周期检定计划编号:D02.10 拟制: 审核:检测设备维修记录工序质量传递卡编号D02.13压力容器产品质量证明书产品名称产品编号质量保证工程师(签章)单位法定代表人(签章)质量检验专用(公章)编号D02.14产品合格证制造单位制造许可证编号产品名称类别设计单位设计批准书编号图号订货单位产品编号制造编号制造完成日期年月日本压力容器产品经质量检验符合《压力容器安全技术监察规程》、设计图样和技术条件的要求。
质量总检验员签字:年月日质量检验专用(公章)年月日产品技术特性年月日产品主要受压元件使用材料一览表产品焊接试板力学和弯曲性能检验报告压力容器外观及几何尺寸检验报告热处理检验报告压力试验检验报告□水压□气压□气密性产品制造变更报告钢板、锻件超声检测报告焊缝射线检测底片评定表编号:D02.28固定式压力容器使用证编号—————压力容器名称—————压力容器编号—————注册编号—————使用单位—————压力容器安全监察机构(盖章)本台压力容器已经地、市级(或省级)锅炉压力容器安全监察机构按《压力容器使用登记管理规则》的规定办理注册登记,准予使用。
- 1、下载文档前请自行甄别文档内容的完整性,平台不提供额外的编辑、内容补充、找答案等附加服务。
- 2、"仅部分预览"的文档,不可在线预览部分如存在完整性等问题,可反馈申请退款(可完整预览的文档不适用该条件!)。
- 3、如文档侵犯您的权益,请联系客服反馈,我们会尽快为您处理(人工客服工作时间:9:00-18:30)。
PZGL-04-01产品标识与追溯作业程序产品标识与追溯作业程序1.目的:明确生产各个过程中的标识要求,以防止物料及产品的混用或误用,特制定本程序。
2.适用范围各种产品、物料。
3.实施程序3.1.标示作业要求。
3.1.1.采购负责要求供货商对送货的每个大小包装物料均需有物料品名、料号、数量的标志。
3.1.2.对物料框上残留的旧有物料标志依“谁使用谁清除”原则,由各使用单位负责作清除。
3.1.3.进料检验后,由检验员标示每批物料的检验状态(贴不合格标、合格标或待处理标),一批物料只能有一种有效检验状态标识,并根据检验结果存入相应分区。
检验现场仓库应保证有待检区、良品区、不良品区,并有明显的区域划分和标志牌。
3.1.4.在进料仓储过程中,由仓管员将品管员检验后的物料存入相应类别分区。
仓库现场应保证有良品区、不良品区及特殊物料分区(DR铜物料区等),并有明确的区域划分及标志。
良品与不良品不可混放。
特殊情况下(如库位紧张时)需暂借用与本物料质量不相适的区域时,相关人员必须做好沟通,并有大而显眼的警告标志,确保物料不被误用,仓储作业员在备料时对每种物料进行料号、数量、工单等内容的标示。
3.1.5.在制程过程中分检出来的不良品须用专用收集容器存放,并用显眼的红色标志物或标签进行标示。
3.1.6.制程品管对不良品进行确认时,须对每篮每袋包装物贴红色不合格标,除此不合格标外,不能有其它贴标。
3.1.7.生产现场由制造单位划分出不良品区,并有醒目标志。
3.1.8.在成品检验过程中,由生产单位对送检的成品进行数量、机型、订单及工单的标志即工单入库条,由成品检验员根据检验结果加盖QC合格章或红色不合格贴标。
生产单位应保证生产现场有待检区,并有明确的区域划分及标志。
3.2.标示要求。
3.2.1.进料检验、半成品入库检验所用检验标见《进料检验作业规范》。
3.2.2.在仓库存放和发放的物料应有品管人员检验后的标志、品名、型号或规格、必要的制造商及制造日期,保持原包装状态的用包装上的标志。
3.2.3.仓库备料时使用标志卡,用单面粘贴纸制作。
3.2.4.不良品作区分时所用的红色不合格标。
3.2.5.所有标志卡在填写时必须保证其完整性并维持其有效性。
3.2.6.检验用合格标用绿色,不合格标用红色。
3.3.产品的追溯根据产品型号、生产日期、标志条、生产批号,可以追溯到材料的进料时间,从而追查到供应商的原材料质量状况。
4.表单及附件无PZGL-04-02成品检验作业规范成品检验作业规范1.目的为确保成品﹑样品质量,使检验工作有据可依特制定此办法。
2.适用范围成品检验。
3.实施程序3.1 检验准备3.1.1 成品检验员根据订单资料﹑样品单或工单入库条,备齐相关数据(抽样计划表﹑爆炸图﹑BOM ﹑不良经历书﹑设变单等)及检验工具。
3.1.2 成品或样品检验合格入库后若超过30天需出货,由生管提前五天通知品管并提供机型明细﹑订单号及成品入库的时间表,成品检验员根据生管提供的出货单于出货前重新做检验。
3.1.3 各需求单位在下样品单时,须在样品单上注明样品用途或样品的特别要求。
3.1.4新品第一次出货时须准备包装材料标准件以备核对检验及检验杂色系产品发现整组颜色有差异时要核对颜色标准件。
3.2 检验的执行。
3.2.1 成品检验人员抽样时,依据成品待检区每天工单机型数量为检验批,进行抽样检验入库。
3.2.2 成品检验员根据“成品检验报告”或“样品检验报告”的每项检验项目内容进行查检。
合格时则在合格项“□”内打“√”,不合格在不合格项“□”内打“√”。
如为检验不合格,需将不良内容填入“不良品描述”栏内。
按《不合格品作业程序》处理。
3.2.3 所有成品或样品检验完毕,须将检验结果分别填写于“成品检验报告”或“样品检验报告”上。
成品检验员判定合格的批次,产品可先放行,报表每天下班前缴交上级主管审核。
3.2.4 样品检验合格后须在“产品检验卡”QA一栏签名确认。
3.3 品管员对检验合格成品及样品需在产品外包装上盖“QC合格”章,并在入库单上签名确认。
3.4 对检验不合格的成品、样品,在外包装上贴“不合格”标,并填写“不合格品处理通知单”经部门主管审核后,发放责任单位。
若为重工或分选,生产单位返检完毕,QC重新进行检验,若复检合格,盖“QC合格”章,并写一份“成品检验复检报告”,在“成品检验报告”备注栏中注明复检二字;若为特采则撕掉“不合格”标,直接盖“QC合格”章。
3.5 对急于出货的成品、样品,成品检验人员可提前在制程时进行检验,若检验不合格应第一时间通知厂品管主管、装配部和生管部主管,再发“不合格品处理通知单”给责任单位。
3.6 成品、样品检验人员发放的《不合格品处理通知单》,必须依据“不合格品作业程序”执行。
3.7 品管成品或样品检验人员发放的《不合格品处理通知单》,由责任单位进行纠正与预防。
3.8 对新产品、客户有特别要求的产品、厂内包装方式改变的产品及检验员认为有异常的产品,都须做成品落地测试,并将执行结果记录于“成品落地测试报告”。
3.9 成品检验人员如接到客户报怨或在成品或样品检验过程中发现质量异常问题点,均记录于“不良经历书”上,以作为日后检验参考。
3.10客户验货3.10.1 客户有验货时,由销售人员通知品管准备,在确认验货人员信息时,由人力资源部在会客室接待,确认后,以电话方式通知品管,再由品管带客户到验货现场。
3.10.2 在客户验货前,生管应提前检查仓库货物数量是否生产完工,并把结果通知品管。
如产品未生产完,生管要求客户验货时,应由生管与客户沟通。
3.10.3 客户验货点数抽样时,由仓库和品管部派人员陪客人点数,并由仓库人员把客人抽样的产品拉到成品验货区。
3.10.4 客户验货时,出现签样错误及客户数据与工厂数据不相符造成客户对产品中止检验,由陪验人员通知相关人员与客人沟通,客户中止验货报告由品管主管签字确认,并通知相关人员。
3.11成品统计分析。
3.11.1 成品检验员每月底将本月成品验货情况统计汇总于“成品检验统计表”上,特采的在异常现象一栏标识特采。
3.11.2 对成品﹑样品异常缺失由责任单位实施检讨。
3.11.3 成品质量报表汇总于“QA一次合格率目标与实际推移图”。
4.表单及附件4.1 成品检验报告。
4.2 样品检验报告。
4.3 产品检验卡。
4.4 QC合格章。
4.5 成品落测试报告。
4.6 成品/样品检验统计表。
4.7 QA一次合格率目标与实际推移图。
PZGL-04-03 不合格品处理作业程序不合格品处理作业程序1.目的为使了进料、制程检验、成品、零件出货检验的不合格品能得到有效管制,以预防由于疏忽而被不当的使用或安装.特制定本程序。
2.适用范围适用于进料、制程检验、成品、零件出货检验的不合格品。
3.工作程序3.1检验不合格品处理程序3.1.1品管员在检验过程中发现不合格品时,由各品管进行标识区分,并及时填写“不合格品处理通知单”。
3.1.2相关单位在接到“不合格品处理通知单”时,需确认签名并注明接收时间,由责任部门提出处理申请,并在接单后原则上8小时(有效工作日)内完成签核。
(成品不合格处理除外),不合格品处理责任与权限见下表:不合格品处理责任与权限表物料进行分选并对质量结果进行记录;同时统计分选、重工的人员人数时间,提供给品保部,由品保部进行统计,并对厂商扣款处理提出,呈副(总)经理核决后进行扣款。
扣款作业见《供货商扣款作业程序》。
3.2.3对于批退物料采购部及时通知供货商,仓库把批退物料放于退货区并进行标示,待外协厂商送货时退回厂商。
3.2.4对特采处理品需依责任与权限来处理。
3.2.5品管对不合格品处理单内容确认和责任追踪查核与改善。
3.3制程检验不合格品处理3.3.1 制程品管检验发现不合格品时,由制程品管进行判定并标示区分,并及时填写“不合格品处理通知单”,发放给厂内生管科进行提出处理意见及应急措施,依不合格品处理权限签核。
3.3.2制程重工或分选后,应由相应品管对其进行重新检验,并记录检验结果与标示。
3.4成品、零件出货检验不合格品处理3.4.1 针对成品、零件出货检验不良批次,成品检验品管发放“不合格品处理通知单”给生产部,生产部在接单后必须在2小时内针对不良现象提出具体的处理方式,通知给品管检验人员,品管对签回的“不合格品处理单”上的处理内容进行确认和责任追踪查核,异常处理完毕后,检验品管需再次进行检验,检验合格后进行标示方可做入库动作(特采除外),成品、零件出货检验发现不良如为功能或少零配件的异常,同时对当批产品须发出纠正预防单。
3.5成品功能稽核测试不合格品处理巡检、成品检验对成品功能稽核测试发现有不合格时,及时填写“不合格品处理通知单”,经部门主管确认后,发放给责任单位由责任单位进行提出处理意见及应急措施,依不合格品处理权限签核。
4.使用表单4.1 不合格品处理通知单。
4.2 不合格品处理权限一览表。
PZGL-04-04纠正与预防作业程序纠正与预防作业程序1.目的为指导责任分析单位及事发单位正确规范纠正与预防的动作,使本公司各单位在发生异常时,能够有效地进行纠正并预防其再度发生,特制订本程序。
2.适用范围适用于责任分析单位及事发单位的异常。
3.实施程序3.1 立案(P)3.1.1 对于客诉,销售部人员在接到客户抱怨(客诉立案表)后,首先应将信息登录于“客诉服务管理记录表”。
3.1.2 由销售部人员发出纠正预防单给品保部客诉处理人员进行纠正预防作业。
3.1.3 对于质量异常,内部稽核及外部审核中发生的异常,责任分析单位应发出“纠正预防单”。
3.1.4 对于其它类异常,应由责任分析单位主管考虑发放“纠正预防单”。
3.1.5 责任分析单位承办人需将异常事实填写于异常现象栏位,并做现象解析。
3.1.6 责任分析(1)立案单位经办人员对异常做责任分析,填写事发单位,并经单位主管签核。
(2)责任分析单位应及时将“纠正预防单”登录在“文件发放/回收记录表”并发给事发单位(事发单位主管需签名确认)处理.当分析出现有几个单位时,应同时进行复印发放。
3.2.处理对策(D)3.2.1 原因分析针对责任分析单位所提出的异常,事发单位均应依照异常状况,用5W1H的方式找出其根本原因并填写于原因分析栏目.3.2.2 纠正及纠正措施事发单位应根据所填写的原因分析,有针对性的填写纠正与纠正措施.填写内容应符合5W1H,并切实有效、合理、可行。
3.2.3 预防措施针对纠正预防单,事发单位除填写纠正及纠正措施外,还应追溯异常产生的根源,以5W1H方式填写预防措施,并且预防措施必须能从根源上消除异常,防止以后潜在再发的可能。
3.2.4 属客诉的纠正预防时还需填写损失费估算及惩处措施.3.2.5 事发单位在接到纠正预防单后,应在“希望答复日期”内完成填写及签核过程,并交还责任分析单位。