保护渣作用和液渣层厚度测量感想
保护渣对铸坯质量的影响

攀枝花学院Panzhihua University本科毕业设计(论文)文献综述院(系):材料工程学院专业:冶金工程班级:2007冶金工程班学生姓名:曾月斌学号: 2007111030472011 年2 月16 日本科生毕业设计(论文)文献综述评价表文献综述:结晶器保护渣对铸坯质量影响的研究1 结晶器保护渣的发展及现状1.1 保护渣的发展在出钢和浇注过程中,钢液长期接触空气和耐火材料,温度和成分发生了显著变化,钢的质量受到严重影响。
经过长期的探索与实践,发现采用气体、液体、固体保护剂,产生还原性气体,将钢液与空气隔离,并对钢液中上浮的夹杂物进行捕集的保护浇注;或采用真空浇注法,是减少浇注过程中钢液污染的有措施。
常用的保护浇注法如[1]表 1.1所示。
1.1 保护浇注分类以前,在钢锭模内壁刷无水焦油,或向钢锭模内放置木框、石蜡稻草圈进行无渣保护浇注。
之后,逐渐发展到使用固体保护渣进行有渣保护浇注,取得了良好的效果,为了适应连续浇注生产迅速发展的需要,1989年我国推出第一批连铸保护渣系列。
从此我国连铸保护渣的标准化、规范化、生产专业化进入一个新时代。
连铸结晶器保护渣的品[2]种繁多:(1)按其化学成分可分为:223SiO Al O CaO --系、223SiO Al O FeO --系、2232SiO Al O Na O --系,其中以前者的应用最为普通。
在此基础上加入少量添加剂(碱金属或碱土金属氧化物、氟化物、硼化物等)和控制熔速的炭质材料(炭黑、石墨和焦炭等)。
(2)按保护渣的形状可分为粉状渣(机械混合成型)、颗粒渣(挤压成型的产品呈长条形,圆盘法成型的产品呈圆形,喷雾法成型的产品呈空心圆颗粒)。
(3)按使用的原材料可分为原始材料混合型、半预熔型和预熔型。
(4)按其使用特性,根据钢种特性、连铸设备特点和连铸工艺条件可分为各种规格的保护渣(低、中、高碳钢保护渣和特种钢专用渣)、发热型开浇渣等。
1.2 保护渣的发展趋势随着连续铸钢的发展,原有保护渣已满足不了生产工艺需求,现代连铸技术采用的保护渣必须是低黏度、低熔点、高熔化速度、大凝固系数的新型保护渣,且保护渣的选择必须与连铸机工艺条件相匹[3]配。
保护渣正确使用方法

保护渣正确使用方法一个优秀保护渣性能的发挥,与保护渣的正确使用是分不开的,目前有一部分市场由于保护渣不能正确使用,而反映保护渣质量问题,结果给保护渣配方的调整和生产造成了误导,致使一个好的保护渣越搞越糟。
针对保护渣正确使用,结合多年的经验,在此提出几条建议:一、渣层厚度的合适控制保护渣在结晶器内应保持一定的厚度(整个渣层),一般在方坯(包括大方坯、圆坯类)在20~50mm,板坯在40~60mm,超薄板坯应保持在80~100mm。
其目的是为了保持保护渣在结晶器内的均匀熔化,使液渣层相对稳定,同时可以维持一定的粉渣层,以起到绝热保温的作用。
通过多年对钢厂现场的观察,我们发现有以下情况:1、见红加渣钢厂说其主要目的是怕渣层过厚而观察不到钢液面,这是一种错误的加法,原因是:A、见红后,液渣层外露,由于没有粉渣层的保温作用,液渣层将变薄,对均匀消耗不利;B、液渣层外露后,与空气接触的部分将部分凝固,在结晶器内出现结团,造成渣面恶化,对稳定渣子性能不利;C、失去渣子的保温性能作用,造成大量热损失,易造成钢液面结冷壳现象等等;2、厚渣层操作有些钢厂人员喜欢厚渣层操作,主要原因是多加一点渣可以多歇一会,这种现象也是不可取的,原因如下:A、厚渣层操作会影响对钢液面的正确判定,一不小心有可能造成事故的出现,该类情况尤以夏季时最易出现;同时由于在某些钢厂由于没有保护渣渣层控制标准,所以有的班好,有的班差,造成老在某些班渣子出问题。
B、厚渣层会造成液渣层相对过厚,有可能造成渣子消耗不均匀而出现表面质量问题;二、加入方式保护渣要均匀推入结晶器内,这对板坯尤为重要。
而且每次加入时间不要过长,要作用勤加少加均匀加入;这同样是一个加渣标准问题,如果你不按上述标准加,就会造成不是渣层厚就是见红,而会出现第一条中提出到相应问题;正常使用过程注意事项:1、在正常使用情况下,禁止钢钢条搅动钢液面,结晶器壁所结的轻微渣圈,不要去经常挑动。
保护渣的成分及作用
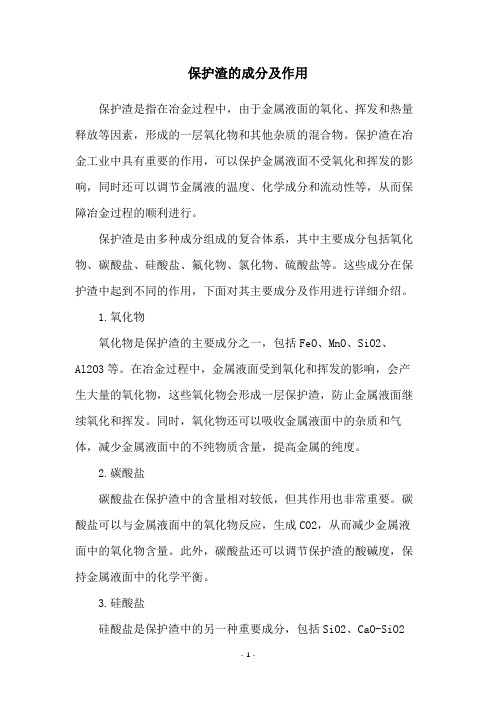
保护渣的成分及作用保护渣是指在冶金过程中,由于金属液面的氧化、挥发和热量释放等因素,形成的一层氧化物和其他杂质的混合物。
保护渣在冶金工业中具有重要的作用,可以保护金属液面不受氧化和挥发的影响,同时还可以调节金属液的温度、化学成分和流动性等,从而保障冶金过程的顺利进行。
保护渣是由多种成分组成的复合体系,其中主要成分包括氧化物、碳酸盐、硅酸盐、氟化物、氯化物、硫酸盐等。
这些成分在保护渣中起到不同的作用,下面对其主要成分及作用进行详细介绍。
1.氧化物氧化物是保护渣的主要成分之一,包括FeO、MnO、SiO2、Al2O3等。
在冶金过程中,金属液面受到氧化和挥发的影响,会产生大量的氧化物,这些氧化物会形成一层保护渣,防止金属液面继续氧化和挥发。
同时,氧化物还可以吸收金属液面中的杂质和气体,减少金属液面中的不纯物质含量,提高金属的纯度。
2.碳酸盐碳酸盐在保护渣中的含量相对较低,但其作用也非常重要。
碳酸盐可以与金属液面中的氧化物反应,生成CO2,从而减少金属液面中的氧化物含量。
此外,碳酸盐还可以调节保护渣的酸碱度,保持金属液面中的化学平衡。
3.硅酸盐硅酸盐是保护渣中的另一种重要成分,包括SiO2、CaO-SiO2等。
硅酸盐可以增加保护渣的粘度和流动性,从而保护金属液面不受氧化和挥发的影响。
此外,硅酸盐还可以吸收金属液面中的杂质和气体,提高金属的纯度。
4.氟化物氟化物在保护渣中的含量很低,但其作用也非常重要。
氟化物可以降低保护渣的熔点和粘度,从而提高保护渣的流动性和渗透性,使其更容易覆盖在金属液面上。
此外,氟化物还可以吸收金属液面中的氧化物和杂质,提高金属的纯度。
5.氯化物氯化物在保护渣中的含量也很低,但其作用与氟化物类似。
氯化物可以降低保护渣的熔点和粘度,提高保护渣的流动性和渗透性。
此外,氯化物还可以吸收金属液面中的氧化物和杂质,提高金属的纯度。
6.硫酸盐硫酸盐在保护渣中的含量也很低,但其作用非常重要。
硫酸盐可以与金属液面中的氧化物反应,生成SO2,从而减少金属液面中的氧化物含量。
对连铸结晶器保护渣渣层分析
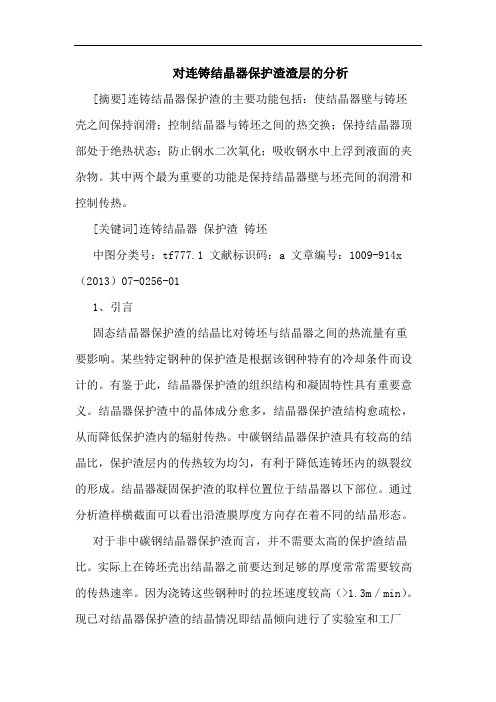
对连铸结晶器保护渣渣层的分析[摘要]连铸结晶器保护渣的主要功能包括:使结晶器壁与铸坯壳之间保持润滑;控制结晶器与铸坯之间的热交换;保持结晶器顶部处于绝热状态;防止钢水二次氧化;吸收钢水中上浮到液面的夹杂物。
其中两个最为重要的功能是保持结晶器壁与坯壳间的润滑和控制传热。
[关键词]连铸结晶器保护渣铸坯中图分类号:tf777.1 文献标识码:a 文章编号:1009-914x (2013)07-0256-011、引言固态结晶器保护渣的结晶比对铸坯与结晶器之间的热流量有重要影响。
某些特定钢种的保护渣是根据该钢种特有的冷却条件而设计的。
有鉴于此,结晶器保护渣的组织结构和凝固特性具有重要意义。
结晶器保护渣中的晶体成分愈多,结晶器保护渣结构愈疏松,从而降低保护渣内的辐射传热。
中碳钢结晶器保护渣具有较高的结晶比,保护渣层内的传热较为均匀,有利于降低连铸坯内的纵裂纹的形成。
结晶器凝固保护渣的取样位置位于结晶器以下部位。
通过分析渣样横截面可以看出沿渣膜厚度方向存在着不同的结晶形态。
对于非中碳钢结晶器保护渣而言,并不需要太高的保护渣结晶比。
实际上在铸坯壳出结晶器之前要达到足够的厚度常常需要较高的传热速率。
因为浇铸这些钢种时的拉坯速度较高(>1.3m/min)。
现已对结晶器保护渣的结晶情况即结晶倾向进行了实验室和工厂的实验研究。
试验室的大部分试验研究,均是在对保护渣控制加热或控制冷却的试验条件下进行,然后再对凝固的保护渣进行分析研究。
在对保护渣的结晶研究中广泛使用了差热分析方法(dta)。
在本研究中,为了确定液态结晶器保护渣在冷却时的结晶温度,在实验时将保护渣的温度变化与参照试样进行了对比。
采用差热分析的方法研究表明,结晶器保护渣的结晶趋势随cao/sio2的比值、li2o、tio2和zro2含量的增加而增强,随b2o3含量的减少而增强。
fonseca等人对自己所采取的保护渣样进行了研究,结果表明,中碳钢保护渣结晶层厚度和保护渣层总厚度均比低碳钢保护渣高。
保护渣作用
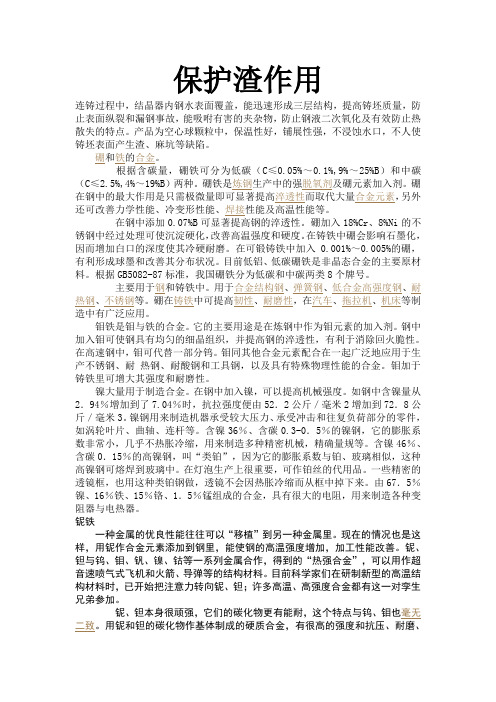
保护渣作用连铸过程中,结晶器内钢水表面覆盖,能迅速形成三层结构,提高铸坯质量,防止表面纵裂和漏钢事故,能吸咐有害的夹杂物,防止钢液二次氧化及有效防止热散失的特点。
产品为空心球颗粒中,保温性好,铺展性强,不浸蚀水口,不人使铸坯表面产生渣、麻坑等缺陷。
硼和铁的合金。
根据含碳量,硼铁可分为低碳(C≤0.05%~0.1%,9%~25%B)和中碳(C≤2.5%,4%~19%B)两种。
硼铁是炼钢生产中的强脱氧剂及硼元素加入剂。
硼在钢中的最大作用是只需极微量即可显著提高淬透性而取代大量合金元素,另外还可改善力学性能、冷变形性能、焊接性能及高温性能等。
在钢中添加0.07%B可显著提高钢的淬透性。
硼加入18%Cr、8%Ni的不锈钢中经过处理可使沉淀硬化,改善高温强度和硬度。
在铸铁中硼会影响石墨化,因而增加白口的深度使其冷硬耐磨。
在可锻铸铁中加入0.001%~0.005%的硼,有利形成球墨和改善其分布状况。
目前低铝、低碳硼铁是非晶态合金的主要原材料。
根据GB5082-87标准,我国硼铁分为低碳和中碳两类8个牌号。
主要用于钢和铸铁中。
用于合金结构钢、弹簧钢、低合金高强度钢、耐热钢、不锈钢等。
硼在铸铁中可提高韧性、耐磨性,在汽车、拖拉机、机床等制造中有广泛应用。
钼铁是钼与铁的合金。
它的主要用途是在炼钢中作为钼元素的加入剂。
钢中加入钼可使钢具有均匀的细晶组织,并提高钢的淬透性,有利于消除回火脆性。
在高速钢中,钼可代替一部分钨。
钼同其他合金元素配合在一起广泛地应用于生产不锈钢、耐热钢、耐酸钢和工具钢,以及具有特殊物理性能的合金。
钼加于铸铁里可增大其强度和耐磨性。
镍大量用于制造合金。
在钢中加入镍,可以提高机械强度。
如钢中含镍量从2.94%增加到了7.04%时,抗拉强度便由52.2公斤/毫米2增加到72.8公斤/毫米3。
镍钢用来制造机器承受较大压力、承受冲击和往复负荷部分的零件,如涡轮叶片、曲轴、连杆等。
含镍36%、含碳0.3-0.5%的镍钢,它的膨胀系数非常小,几乎不热胀冷缩,用来制造多种精密机械,精确量规等。
保护渣
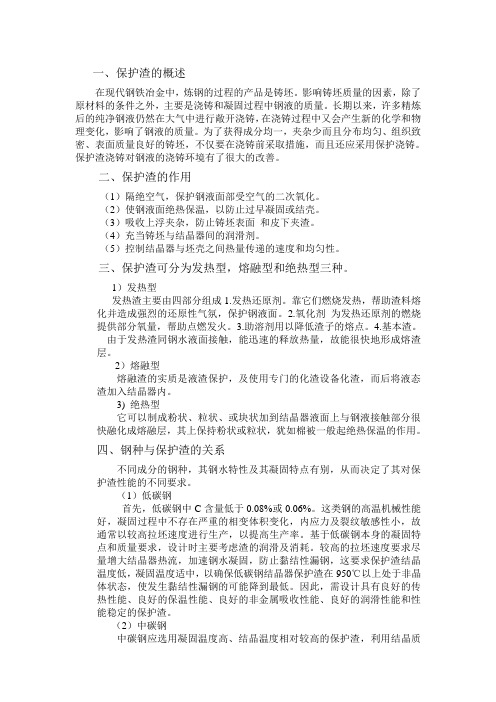
一、保护渣的概述在现代钢铁冶金中,炼钢的过程的产品是铸坯。
影响铸坯质量的因素,除了原材料的条件之外,主要是浇铸和凝固过程中钢液的质量。
长期以来,许多精炼后的纯净钢液仍然在大气中进行敞开浇铸,在浇铸过程中又会产生新的化学和物理变化,影响了钢液的质量。
为了获得成分均一,夹杂少而且分布均匀、组织致密、表面质量良好的铸坯,不仅要在浇铸前采取措施,而且还应采用保护浇铸。
保护渣浇铸对钢液的浇铸环境有了很大的改善。
二、保护渣的作用(1)隔绝空气,保护钢液面部受空气的二次氧化。
(2)使钢液面绝热保温,以防止过早凝固或结壳。
(3)吸收上浮夹杂,防止铸坯表面和皮下夹渣。
(4)充当铸坯与结晶器间的润滑剂。
(5)控制结晶器与坯壳之间热量传递的速度和均匀性。
三、保护渣可分为发热型,熔融型和绝热型三种。
1)发热型发热渣主要由四部分组成1.发热还原剂。
靠它们燃烧发热,帮助渣料熔化并造成强烈的还原性气氛,保护钢液面。
2.氧化剂为发热还原剂的燃烧提供部分氧量,帮助点燃发火。
3.助溶剂用以降低渣子的熔点。
4.基本渣。
由于发热渣同钢水液面接触,能迅速的释放热量,故能很快地形成熔渣层。
2)熔融型熔融渣的实质是液渣保护,及使用专门的化渣设备化渣,而后将液态渣加入结晶器内。
3) 绝热型它可以制成粉状、粒状、或块状加到结晶器液面上与钢液接触部分很快融化成熔融层,其上保持粉状或粒状,犹如棉被一般起绝热保温的作用。
四、钢种与保护渣的关系不同成分的钢种,其钢水特性及其凝固特点有别,从而决定了其对保护渣性能的不同要求。
(1)低碳钢首先,低碳钢中C含量低于0.08%或0.06%。
这类钢的高温机械性能好,凝固过程中不存在严重的相变体积变化,内应力及裂纹敏感性小,故通常以较高拉坯速度进行生产,以提高生产率。
基于低碳钢本身的凝固特点和质量要求,设计时主要考虑渣的润滑及消耗。
较高的拉坯速度要求尽量增大结晶器热流,加速钢水凝固,防止黏结性漏钢,这要求保护渣结晶温度低,凝固温度适中,以确保低碳钢结晶器保护渣在950℃以上处于非晶体状态,使发生黏结性漏钢的可能降到最低。
保护渣的性能测定
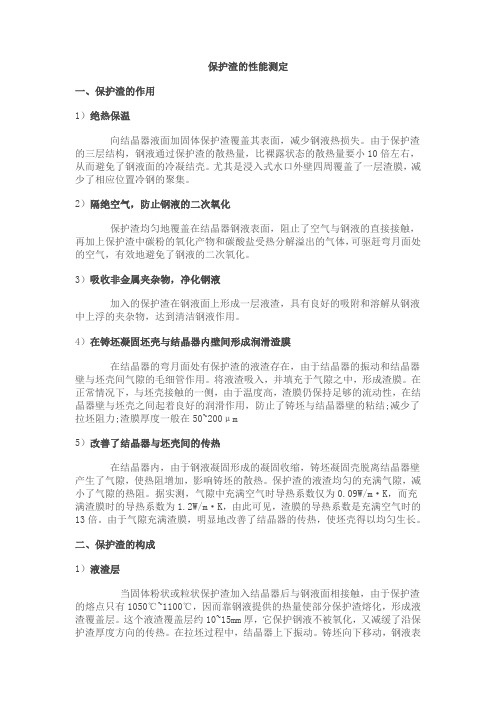
保护渣的性能测定一、保护渣的作用1)绝热保温向结晶器液面加固体保护渣覆盖其表面,减少钢液热损失。
由于保护渣的三层结构,钢液通过保护渣的散热量,比裸露状态的散热量要小10倍左右,从而避免了钢液面的冷凝结壳。
尤其是浸入式水口外壁四周覆盖了一层渣膜,减少了相应位置冷钢的聚集。
2)隔绝空气,防止钢液的二次氧化保护渣均匀地覆盖在结晶器钢液表面,阻止了空气与钢液的直接接触,再加上保护渣中碳粉的氧化产物和碳酸盐受热分解溢出的气体,可驱赶弯月面处的空气,有效地避免了钢液的二次氧化。
3)吸收非金属夹杂物,净化钢液加入的保护渣在钢液面上形成一层液渣,具有良好的吸附和溶解从钢液中上浮的夹杂物,达到清洁钢液作用。
4)在铸坯凝固坯壳与结晶器内壁间形成润滑渣膜在结晶器的弯月面处有保护渣的液渣存在,由于结晶器的振动和结晶器壁与坯壳间气隙的毛细管作用。
将液渣吸入,并填充于气隙之中,形成渣膜。
在正常情况下,与坯壳接触的一侧,由于温度高,渣膜仍保持足够的流动性,在结晶器壁与坯壳之间起着良好的润滑作用,防止了铸坯与结晶器壁的粘结;减少了拉坯阻力;渣膜厚度一般在50~200μm5)改善了结晶器与坯壳间的传热在结晶器内,由于钢液凝固形成的凝固收缩,铸坯凝固壳脱离结晶器壁产生了气隙,使热阻增加,影响铸坯的散热。
保护渣的液渣均匀的充满气隙,减小了气隙的热阻。
据实测,气隙中充满空气时导热系数仅为0.09W/m·K,而充满渣膜时的导热系数为1.2W/m·K,由此可见,渣膜的导热系数是充满空气时的13倍。
由于气隙充满渣膜,明显地改善了结晶器的传热,使坯壳得以均匀生长。
二、保护渣的构成1)液渣层当固体粉状或粒状保护渣加入结晶器后与钢液面相接触,由于保护渣的熔点只有1050℃~1100℃,因而靠钢液提供的热量使部分保护渣熔化,形成液渣覆盖层。
这个液渣覆盖层约10~15mm厚,它保护钢液不被氧化,又减缓了沿保护渣厚度方向的传热。
在拉坯过程中,结晶器上下振动。
连铸保护渣的基本功能及其在结晶器中的行为

个人收集整理勿做商业用途目录中文摘要........................................................................ 错误!未定义书签。
英文摘要........................................................................ 错误!未定义书签。
1 绪论 (1)1。
1连铸保护渣的基本功能及其在结晶器中的行为 (1)1.1。
1连铸保护渣的作用 (1)1。
1。
2连铸保护渣在结晶器内行为 (2)1.2裂纹敏感性钢种连铸面临的问题 (4)1。
3连铸保护渣结晶性能的研究现状 (6)1。
3.1影响连铸保护渣结晶特性的因素 (6)1.3。
2连铸保护渣结晶性能对传热的影响 (7)1。
3。
3结晶器中保护渣控制传热的途径 (8)1.4国内外关于保护渣凝固收缩性能的研究 (9)1。
5本课题的来源、研究的主要内容 (11)2 实验方案与设备 (12)2.1保护渣凝固收缩性能的测试方案 (12)2。
1.1保护渣体积变化率的评价方法 (12)2。
1。
2保护渣结晶体、玻璃体密度的测试方法 (12)2.1.3实验过程中渣样的对比研究方案 (14)2。
2实验渣成分的设计 (15)2. 3与保护渣结晶性能相关的参数的测定 (18)2.3。
1保护渣定点粘度、粘温曲线的测试 (18)2。
3.2保护渣熔化温度的测试 (20)3 实验结果及分析 (22)3.1相同渣系组分对结晶性能、凝固收缩性能影响的探讨 (22)3.2不同渣系的保护渣凝固收缩性能的探讨 (27)3。
3不同冷却速度对凝固收缩性能的影响的探讨 (28)4 结论 (30)5 致谢 (30)参考文献 (32)1 绪论连铸保护渣是连铸过程中关键性辅料,对连铸工艺的顺行和铸坯表面质量的控制具有重要影响。
保护渣从加入到离开结晶器这一过程中所发挥的作用可归结为:对结晶器钢液面绝热保温,避免钢液凝固;保护钢液面不受空气二次氧化;吸收钢液中上浮的夹杂物;润滑运动的铸坯;均匀和调节凝固坯壳向结晶器的传热.在上述诸多功能中,最重要的是润滑铸坯和控制传热两大特性。
保护渣的物性对熔渣摩擦力的影响
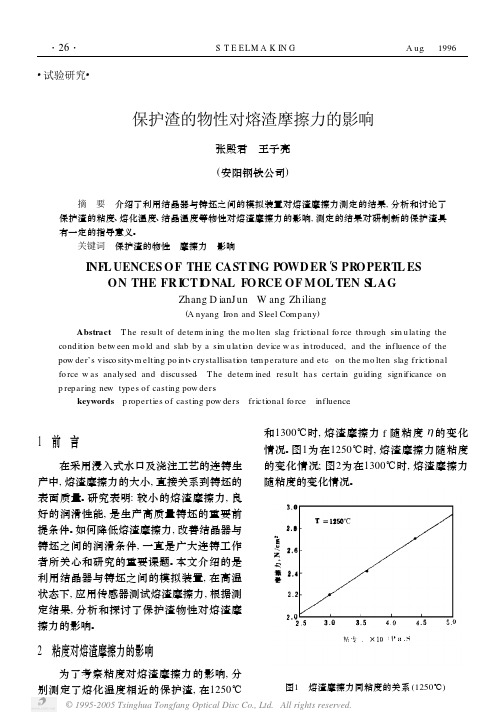
试验研究保护渣的物性对熔渣摩擦力的影响张殿君 王子亮(安阳钢铁公司)摘 要 介绍了利用结晶器与铸坯之间的模拟装置对熔渣摩擦力测定的结果,分析和讨论了保护渣的粘度、熔化温度、结晶温度等物性对熔渣摩擦力的影响,测定的结果对研制新的保护渣具有一定的指导意义。
关键词 保护渣的物性 摩擦力 影响INFL UENCES OF THE CAST ING POWD ER′S PROPERT L ES ON THE FR I CT I ONAL FORCE OF MOL TEN S LAGZhang D ianJun W ang Zh iliang(A nyang Iron and Sleel Company)Abstract T he resu lt of determ in ing the mo lten slag fricti onal fo rce th rough si m u lating the conditi on betw een mo ld and slab by a si m u lati on device w as in troduced,and the influence of the pow der’s visco sity、m elting po in t、crystallisati on temperatu re and etc.on the mo lten slag fricti onal fo rce w as analysed and discu ssed.T he determ ined resu lt has certain gu iding sign ificance on p reparing new types of casting pow ders.keywords p roperties of casting pow ders fricti onal fo rce influence.1 前 言在采用浸入式水口及浇注工艺的连铸生产中,熔渣摩擦力的大小,直接关系到铸坯的表面质量。
大小方坯连铸机保护渣厚度测量和控制系统

大小方坯连铸机保护渣厚度电磁测量和控制系统
自动加渣是一个优先事项,以确保保护渣厚度和钢材质量的稳定性。
实现这个全自动的首要任务是实时测量熔池的保护渣厚度。
将放射性水平传感器或光学系统组合作为主液位控制装置,PTC系统可以保证在大小方坯连铸机上的保护渣厚度控制。
每一流测量系统包括:ILD 200-07 电磁传感器、耐热电缆、接线盒、信号处理和控制单元。
通常,在每个结晶器中永久性安装一只 ILD 200-07 传感器,其安装在水套的插槽中(提供详细的安装工程说明)。
大小方坯连铸机保护渣厚度测量和控制系统
ILD 200-07 型用于保护渣厚度
ILD 200-07 安装示例。
保护渣对板坯连铸表面质量的影响

保护渣对板坯连铸质量的影响丁寅(新疆八一钢铁股份公司)摘要: 通过对板坯纵裂纹形成原理及其影响因素进行分析、重点对于保护渣对板坯表面质量的影响进行探讨、从保护渣的角度解释了板坯易产生表面质量缺陷的原因、并对保护渣的性能提出了改进方法、从而进一步提高板坯铸坯质量。
关键词: 保护渣;表面质量;连铸;理化性能1 引言保护渣浮在钢液上,熔化成液渣渗入凝固坯壳与结晶器之间的缝隙中,形成渣膜。
该渣膜由靠近坯壳侧的液渣层和靠近结晶器侧的固态层构成,它不仅能润滑坯壳,防止黏结漏钢的发生,同时还能调节结晶器和凝固坯壳之间的热流,减少热流波动,以保证在弯月露区域形成的坯壳厚度均匀,降低表面纵裂纹产生的概率,提高铸坯表面质量[1-2]。
我厂浇铸大断面前期使用的保护渣为适应高拉速的需要,不可避免的要对保护渣的熔速、粘度、熔点、配碳等进行调整,这样,高速保护渣在浇铸低速钢时,虽然发生漏钢的几率小,但却不能形成良好的三层结构,影响到质量的控制和稳定。
轻微的纵裂纹经板坯精整后对下工序不会产生影响,但会降低金属收得率,影响整个物流的运转,使连铸连轧不能顺利进行,从而降低了生产效率。
2 保护渣的几个重要理化性能2.1 粘度(η)粘度是考查保护渣物理性能的一个重要指标。
浇注时,保护渣的粘度影响其渗透,合适的粘度可以使保护渣在结晶器与坯壳之间形成有一定厚度的渣膜。
并能均匀铺展,这对改善板坯的润滑性能及稳定传热有重要作用。
保护渣的粘度太低会对水口造成侵蚀,渣耗增大,渣膜变厚,影响板坯的水平传热;但粘度太高,又易形成渣条,渣耗过低,渣膜变薄且不均匀,易造成板坯的纵裂缺陷甚至漏钢。
粘度的操作范围主要是凭经验,控制好保护渣的粘度,保持稳定,可以把渣耗量稳定在一个合适的范围内,保证板坯的润滑与传热。
狄林成章等人研究低碳铝镇静钢保护渣时[3],认为粘度(η)与拉速(v e:m/min)之间在1300℃时的最佳范围遵循经验公式:η1300℃.v e=0.2—0.35(η:Pa·s)。
保护渣交流学习笔记
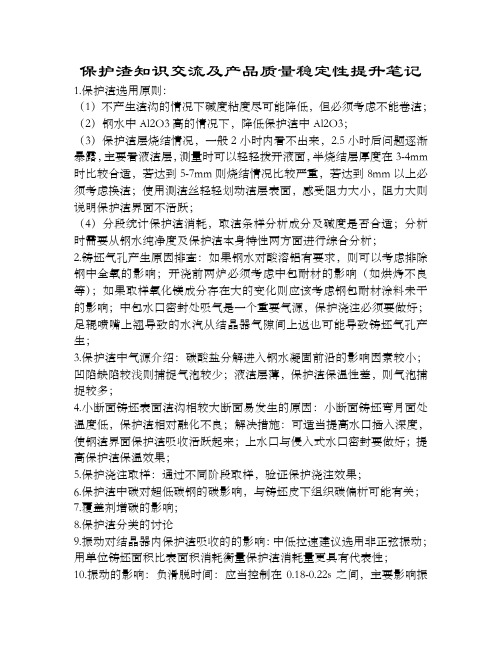
保护渣知识交流及产品质量稳定性提升笔记1.保护渣选用原则:(1)不产生渣沟的情况下碱度粘度尽可能降低,但必须考虑不能卷渣;(2)钢水中Al2O3高的情况下,降低保护渣中Al2O3;(3)保护渣层烧结情况,一般2小时内看不出来,2.5小时后问题逐渐暴露,主要看液渣层,测量时可以轻轻拨开液面,半烧结层厚度在3-4mm 时比较合适,若达到5-7mm则烧结情况比较严重,若达到8mm以上必须考虑换渣;使用测渣丝轻轻划动渣层表面,感受阻力大小,阻力大则说明保护渣界面不活跃;(4)分段统计保护渣消耗,取渣条样分析成分及碱度是否合适;分析时需要从钢水纯净度及保护渣本身特性两方面进行综合分析;2.铸坯气孔产生原因排查:如果钢水对酸溶铝有要求,则可以考虑排除钢中全氧的影响;开浇前两炉必须考虑中包耐材的影响(如烘烤不良等);如果取样氧化镁成分存在大的变化则应该考虑钢包耐材涂料未干的影响;中包水口密封处吸气是一个重要气源,保护浇注必须要做好;足辊喷嘴上翘导致的水汽从结晶器气隙间上返也可能导致铸坯气孔产生;3.保护渣中气源介绍:碳酸盐分解进入钢水凝固前沿的影响因素较小;凹陷缺陷较浅则捕捉气泡较少;液渣层薄,保护渣保温性差,则气泡捕捉较多;4.小断面铸坯表面渣沟相较大断面易发生的原因:小断面铸坯弯月面处温度低,保护渣相对融化不良;解决措施:可适当提高水口插入深度,使钢渣界面保护渣吸收活跃起来;上水口与侵入式水口密封要做好;提高保护渣保温效果;5.保护浇注取样:通过不同阶段取样,验证保护浇注效果;6.保护渣中碳对超低碳钢的碳影响,与铸坯皮下组织碳偏析可能有关;7.覆盖剂增碳的影响;8.保护渣分类的讨论9.振动对结晶器内保护渣吸收的的影响:中低拉速建议选用非正弦振动;用单位铸坯面积比表面积消耗衡量保护渣消耗量更具有代表性;10.振动的影响:负滑脱时间:应当控制在0.18-0.22s之间,主要影响振痕深度,时间越长则振痕越深而且深度方向保护渣消耗增加;正滑脱时间:影响保护渣消耗量,时间越长,保护渣消耗越大;加速度:影响振痕方向冲击力;11.胡厂安排完成目前圆坯钢种设定负滑脱时间核算,结合提拉速核定振动模型选用是否合适;12.方坯60Mn保护渣调整,根据漏钢形貌可以判定主要问题为:保护渣润滑不够,渣层厚度不足,正常应当达到8-12mm,测量液渣层厚度的时候注意激冷层处液渣层厚度的测量;粘度不足,保护渣的稳定性和均匀性差等原因;13.方坯凹陷形成机理:角部:冷却太强,保护渣烧结性强;结晶器倒角半径选择不当;面部:包晶钢则为弯月面不均匀线性收缩,一般凹陷深的地方通常伴随裂纹,表征为方向性则比较随意,在弯月面产生热应力,应力裂纹的产生;中高碳钢:线性,通常比较直,产生原因为弯月面以下润滑不够,发生撕裂导致凹陷的产生;14.圆坯渣沟的形成:温度流场的不均匀性,无角部支撑,坯壳收缩的随意性更大,包晶钢表现的比方坯更强;15.螺旋形渣沟的产生,与电磁搅拌强度过大存在直接关系,二次冷却不均匀导致缺陷加剧;16.小断面足辊水量设计不宜太大,大断面足辊水量的设计要大,如果水量小进入气雾冷却段会发生回温现象;17.直线型渣沟产生原因判定:液渣分布不均匀,结晶器内渣多富集导致冷却弱,而且保护渣消耗量大;如果某一个方向保护渣少则形成的渣膜局部变薄,导致传热快,坯壳的冷却变强,产生的热应力大,相应的摩擦阻力大,这种情况下一般反复性强;18.直线型渣沟产生机理:保护渣烧结严重,导致结晶器内液渣流入少,保护渣与结晶器壁间润滑不好,有可能出现粘结,而且与结晶器水封偏斜有关系;19.直线型渣沟解决措施:降低粘度,调整保护渣中C的配比,增加均匀性;20.负滑脱时间选择原则:低碳及包晶钢,凝固收缩量大,负滑脱时间宜短;中高碳钢焊接性差,塑性及粘结性差,负滑脱时间要长,21.加速度的选择以1-2m/s2为宜,超过2.5是比较危险的的,增加振痕处冲击力,导致横向裂纹的产生;22.中碳锰钢与中碳钢保护渣选择原则:锰钢保护渣粘度碱度适当低;23.钢中N元素超标的影响:加入V,Ti,N含量超过50PPm,易导致NC化合物提前析出形成夹杂物,甚至形成晶间裂纹,起不到细化晶粒的作用;24.方坯40Cr棒材细小裂纹的产生原因:热装臵度,温度太低落在脆性区间内宜形成裂纹,也加热炉温度的均匀性有关,升温速度太快对棒材细小裂纹的产生有一定的影响。
结晶器保护渣的性能和特性
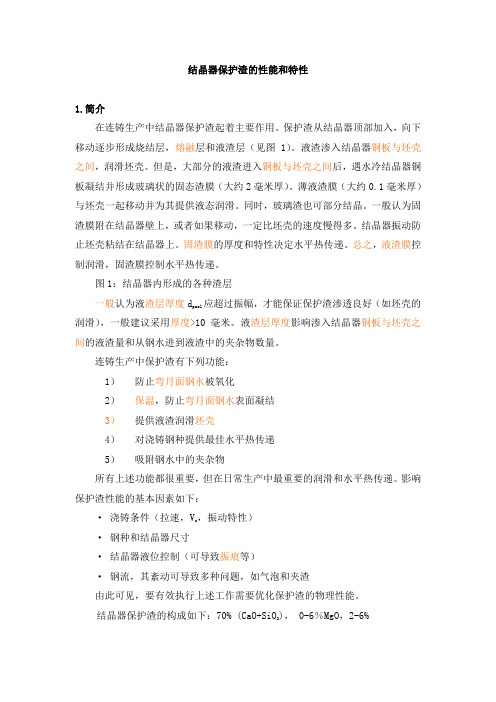
结晶器保护渣的性能和特性1.简介在连铸生产中结晶器保护渣起着主要作用。
保护渣从结晶器顶部加入,向下移动逐步形成烧结层,熔融层和液渣层(见图1)。
液渣渗入结晶器铜板与坯壳之间,润滑坯壳。
但是,大部分的液渣进入铜板与坯壳之间后,遇水冷结晶器铜板凝结并形成玻璃状的固态渣膜(大约2毫米厚)。
薄液渣膜(大约0.1毫米厚)与坯壳一起移动并为其提供液态润滑。
同时,玻璃渣也可部分结晶。
一般认为固渣膜附在结晶器壁上,或者如果移动,一定比坯壳的速度慢得多。
结晶器振动防止坯壳粘结在结晶器上。
固渣膜的厚度和特性决定水平热传递。
总之,液渣膜控制润滑,固渣膜控制水平热传递。
图1:结晶器内形成的各种渣层应超过振幅,才能保证保护渣渗透良好(如坯壳的一般认为液渣层厚度dpool润滑),一般建议采用厚度>10毫米。
液渣层厚度影响渗入结晶器铜板与坯壳之间的液渣量和从钢水进到液渣中的夹杂物数量。
连铸生产中保护渣有下列功能:1)防止弯月面钢水被氧化2)保温,防止弯月面钢水表面凝结3)提供液渣润滑坯壳4)对浇铸钢种提供最佳水平热传递5)吸附钢水中的夹杂物所有上述功能都很重要,但在日常生产中最重要的润滑和水平热传递。
影响保护渣性能的基本因素如下:,振动特性)·浇铸条件(拉速,Vc·钢种和结晶器尺寸·结晶器液位控制(可导致振痕等)·钢流,其紊动可导致多种问题,如气泡和夹渣由此可见,要有效执行上述工作需要优化保护渣的物理性能。
结晶器保护渣的构成如下:70% (CaO+SiO),0-6%MgO,2-6%2Al2O3,2-10%Na2O(+K2O), 0-10%F带有其他添加物,如 TiO2, ZrO2, B2O3, Li2O和MnO。
碱度(%CaO/%SiO2)范围为0.7-1.3。
碳以焦碳,碳黑和石墨方式加入(2-20%),1)可控制保护渣的熔化速度,2)可在结晶器上部形成CO(g),防止钢水氧化。
结晶器保护渣的性能及研究进展

《连续铸钢》论文论文题目:结晶器保护渣的性能及研究进展作者:李昌齐专业:冶金工程指导教师:刘宇雁教授结晶器保护渣的性能及研究进展李昌齐(材料与冶金学院、08冶金一班、0861107143)摘要:连铸时保护渣对改善连铸坯表面质量具有明显的效果,在设计和选择保护渣时,首先必须了解保护渣的基本性能,来提高连铸效率和质量。
本文综述了保护渣的主要物理性能、化学性能及最新的研究技术成果及应用。
关键词:结晶器;保护渣;物理化学性能;研究进展引言结晶器保护渣是连铸操作过程中使用的多功能冶金辅料,是一项高技术含量的辅料,保护渣对连铸工序生产稳定顺行和铸坯质量的提高有着密切关系[1]。
在连铸过程中,结晶器内钢液面上的保护渣层可绝热保温、隔绝空气防止对钢液的二次氧化、吸收从钢液中到大钢液面的夹杂物。
结晶器与坯壳之间的渣膜具有润滑坯壳、控制坯壳与结晶器间的传热等作用。
保护渣最重要的性能有粘度、熔渣层厚度、熔化温度、熔化速度、、熔化均匀性、玻璃性、吸收和溶解非金属夹杂物等。
这些性能主要与化学成分有关,并且对结晶器内渣膜的传热性有很大的影响。
1 保护渣的物理性能1.1 粘度粘度是决定渣消耗量的均匀渗入的重要性能之一。
它直接关系到溶化后的渣在弯月面区域的行为,对铸坯的表面质量有明显的影响。
如铸坯表面振痕的形状,结晶器铜壁与铸坯坯壳间均匀渣膜的形状,熔渣层吸收和溶解非金属夹杂物以及对浸入式水口的腐蚀等,其中影响最为重要的是对渣膜厚度和均匀性的影响。
为了吸收钢液中上浮的夹杂物,要求保护渣的粘度尽可能低,但是低粘度的保护渣对水口的侵蚀不利,为防止卷渣,在允许的条件下使用高粘度渣。
但粘度不能太高,否则会使保护渣渣耗降低,熔渣流入量减少,渣膜变薄且不均匀,引起摩擦力增大,结果会使坯壳受力,造成纵裂缺陷甚至漏钢。
对于相同的拉速,铸坯的断面增大,渣的单耗量下降,因此,粘度应低一些。
保护渣的粘度,必须与浇注的钢种、连铸机的类型、连铸的工艺参数和保护渣的融化特性相匹配。
- 1、下载文档前请自行甄别文档内容的完整性,平台不提供额外的编辑、内容补充、找答案等附加服务。
- 2、"仅部分预览"的文档,不可在线预览部分如存在完整性等问题,可反馈申请退款(可完整预览的文档不适用该条件!)。
- 3、如文档侵犯您的权益,请联系客服反馈,我们会尽快为您处理(人工客服工作时间:9:00-18:30)。
保护渣作用和液渣层厚度测量感想(完)
2008-10-16 20:16:28 作者:zhaoluo 来源:制钢参考网浏览次数:405 文字大小:【大】【中】【小】
连铸结晶器保护渣是连铸工艺过程必须的关键性材料,对铸坯质量及连铸工艺顺行具有非常重要和不可替代的作用。
随着拉速的不断提高、连铸品种的不断扩大、连铸坯质量要求的不断上升,连铸保护渣也不断成为连铸发展的技术瓶颈。
如何充分发挥连铸保护渣的各种功能和作用,保证不同钢种在不同连铸工艺条件下的顺利生产并得到高质量的铸坯,成为冶金工作者关注的重要问题,需要在不同的实践阶段从理论和实践上解决相关技术难题。
保护渣的主要作用为:绝热保温;隔绝空气,防止钢水二次氧化;吸附钢水夹杂,净化钢水;在结晶器壁和钢水凝固壳之间形成渣膜,减少拉坯阻力,防止凝固壳与结晶器壁粘连;填充凝固壳与结晶器壁之间的气隙,改善结晶器传热条件。
由于保护渣在连铸过程的的重要作用和地位,各国连铸工作者始终予以高度重视,并进行了大量研究,建立了相关理论基础,并开发了许多适合各国国情及连铸钢种和工艺的保护渣系列,从而使铸坯质量不断改善提高,品种不断增加。
近年来,以高拉速、高连浇率、高作业率及高质量为特征的高效连铸得到迅速的发展,成为钢铁企业降低成本、降低能耗、减少投资成本、开拓市场、在激烈的世界钢铁市场竞争中立于不败之地的重要技术创新和钢铁企业结构优化的必然需要。
以高拉速为主要特征的高效连铸技术的开发、应用、推广是优化我国连铸技术,提高连铸水平的重要发展方向。
由于高效连铸中的高拉速使结晶器中的热流及摩擦力增大、结晶器中钢液面波动加剧、出结晶器的铸坯坯壳变薄、•渣耗急剧下降造成润滑不良和传热不均等,使得从常速连铸(≤1.5m/min)到高速连铸(≥1.5m/min)遇到了粘结漏钢和铸坯表面质量差两大难题。
为解决这些问题,就必须研究和开发研究具有相应物理和化学性能的结晶器保护渣,保证连铸过程中结晶器内的物理化学反应处于良好的状态。
以连铸连轧为基础的紧凑型生产流程是降低冶金产品生产成本、提高企业经济效益的一个重要途径,无缺陷铸坯生产技术是实现连铸连轧的关键,这对铸坯表面质量提出了更高要求。
连铸保护渣对高表面质量铸坯的生产
起着重要的保障作用。
以薄板坯、异型坯生产为代表的近终形连铸,是近年来迅猛发展的连铸新技术,与之相适应的保护渣开发即成为一个亟待解决的问题。
由于薄板坯结晶器断面小、工作拉速快,而异型坯结晶器断面不规整,对保护渣的熔融特性、铺展性能提出了更新的要求。
为此,国内外各炼钢厂都在寻求适合本厂连铸工艺特点的无缺陷铸坯生产用结晶器保护渣。
加入到结晶器高温钢液(1500℃左右)面上的低熔点(1000~1150℃)保护渣,靠钢液提供热量,在钢液面上形成一定厚度的液渣层(6~15mm),钢水向粉渣层传热减慢,液渣层上的保护渣受热作用,形成烧结层(600~900℃),烧结层之上的渣由于从钢水接受的热量更少,保持为粉状,均匀覆盖在钢水面上,防止钢水散热,阻止空气中的氧进入钢水中。
在拉坯过程中,由于结晶器上下振动和凝固坯壳向下运动的作用,钢液面上的液渣层进入坯壳与铜壁之间的气隙,起到改善润滑和传热的作用。
随着拉坯的进行,液渣不断被消耗,烧结层下降到钢液面熔化成液渣层,粉渣层变成烧结层,往结晶器添加新的保护渣,使其保持为三层结构,如此循环,保护渣不断消耗。
液渣层的正常厚度为6~15mm,,液渣层太薄,结晶器壁与凝固坯壳之间的渣膜达不到要求,易导致凝固壳与结晶器壁粘连,严重者发生粘结漏钢;液渣层厚度小于某一值,沿结晶器周边形成的渣圈,会使弯月面液渣流入坯壳与铜壁之间的通道堵死,使液渣不能顺利流入,不能形成均匀渣膜,导致凝固壳厚度不均匀,在应力作用下产生裂纹,严重者发生裂纹漏钢。
如板坯拉速为1.2~1.5m/min,液渣层厚度小于5mm,板坯纵裂纹明显增加,液渣层厚度6~15mm,纵裂纹几乎消失,液渣层大于20mm,纵裂纹又有所增加。
烧结层的正常厚度为5~10mm,太厚或太薄会影响液渣层厚度。
粉渣层正常厚度为5~10mm,粉渣层太薄,起不到保温作用,粉渣层太厚,形成渣条增多,严重时引起夹渣漏钢。
因此,结晶器保护渣状况的好坏,直接关系到浇钢生产顺行和铸坯质量好坏,保护渣厚度检测方法及其精确程度直接影响操作工对渣况的判断。
目前在生产中测定液渣层厚度的方法有单丝法和双丝法。
单丝法将一根铁丝插入结晶器钢水中,保持平稳,几秒钟后取出,观察铁丝表面颜色变化和粘渣情况,确定液渣层厚度。
双丝法把一根钢丝和铜丝(或铝丝)绑在一起,插入结晶器液渣层中,由于液渣温度高于铜熔点而低于钢熔点,所以铜丝熔化,而钢丝未熔,量出铜丝熔化的长度即为液渣层厚度。
这两种检测方法不仅增加了工人的劳动强度,而且由于检测时人手的抖动、结晶器振动、钢水液面波动等原因,导致测量不准确,误差较大,影响浇钢工对结晶器渣况的正确判断,造成漏钢事故的发生,影响浇钢生产的顺行。
宝钢发明了一种检测工具专利,其基本原理与双丝法相同,该装置由铜管、木夹、木板或石棉板、铁钉和镀铜铁丝组成,铜管内穿有镀铜铁丝或长度相同的一根铜丝和铁丝。
检测时将穿出木板的镀铜铁丝或铁丝与铜丝插入结晶器钢水中,并使木板漂浮在钢水液面上保持平稳,根据金属丝熔损和颜色变化来确定粉渣层、烧结层和液渣层厚度。
该专利在各渣层厚度的确定上存在人为影响因素。
熔融炉渣可以导电,X射线衍射研究表明,固态炉渣具有离子特性,而且随着温度的升高,其离子特性增强。
粉渣中没有电离的离子,又由于保护渣颗粒之间的间隙较大,含量很少的炭也被阻隔开,所以导电性很差,几乎不导电。
烧结层中已经开始生成液相物质,电离出一些离子,有一定的导电性。
随着液相的增加,电离出的离子越来越多,导电性随之增强。
当保护渣熔化达到半球点时,保护渣主要以离子状态存在,导电性会迅速增大。
沈文珍等人分析了连铸结晶器保护渣的导电机理, 研究了保护渣在不同状态下的导电性能, 并且利用电路原理计算出了液渣的电阻率。
研究结果表明:保护渣的熔化状态直接影响着其导电性能,利
用导电性能可以推断出保护渣的熔化状态;液渣在1 350 ℃时的电阻率约为
0.22Ω·cm。
日本的中森由纪将结晶器保护渣放在坩锅中加热,用电极法测定它的电学特性,并与已知的KCl水溶液进行比较,发现保护渣温度大于800℃以上时可视为导体。
由于粉状层和烧结层的电阻比液渣层大很多,故这两层可忽略不计,试制了涡流型保护渣液渣层厚度测量仪,并在新日铁君津厂2号铸机上进行试验性运行,检测精度为±2mm,但之后未见任何后续报道,可能该设备未得到推广使用。