GMP 专用生产线的清洁验证
新版gmp设备清洁验证方案

01 02 03 04
不足
部分设备的复杂结构导致清洁难度较大,需要进一步改进清洁方法。 清洁验证过程中,部分环节仍然依赖人工操作,存在一定的误差风险
。 需要进一步拓展清洁验证的范围,覆盖更多的设备类型和场景。
展望:未来清洁验证方案的发展方向与目标
01
发展方向
02
研究更加高效、环保的清洁剂和清洁技术,提高清洁效率和质
加强人才培养和队伍建 设,提高清洁验证领域 的整体水平。
THANKS
感谢观看
阐述新版GMP设备清洁验证方案对于制药行业的重要性,以及对于提高产品质量、降低风险等方面的 积极作用。
目的和意义
说明新版GMP设备清洁验证方案的 目的和意义,例如确保设备清洁、降 低污染风险、提高产品质量等。
VS
阐述新版GMP设备清洁验证方案对 于制药企业的实际应用和指导价值。
02
清洁验证方案总体概述
新版gmp设备清洁验证方案
汇报人: 2023-12-02
目录
• 引言 • 清洁验证方案总体概述 • 清洁验证方案详细内容 • 清洁验证方案实施步骤 • 清洁验证方案中可能出现的问题及解决方
案 • 清洁验证方案总结与展望
01
引言
背景介绍
介绍新版GMP设备清洁验证方案的产生背景,例如法规要求、技术发展等。
设备清洁标准操作规程(SOP)制定
01
02
明确设备清洁标准操作规程的编 写责任人及审核流程。
确定设备清洁的操作流程及步骤 :包括清洁前准备、清洁实施、
清洁后检查等环节。
制定清洁剂和助剂的选择标准及 使用方法。
03
编写设备清洁效果评估标准及操 作规程。
04
设备清洁验证过程记录表格制定
GMP洁净服洗涤效果验证方案
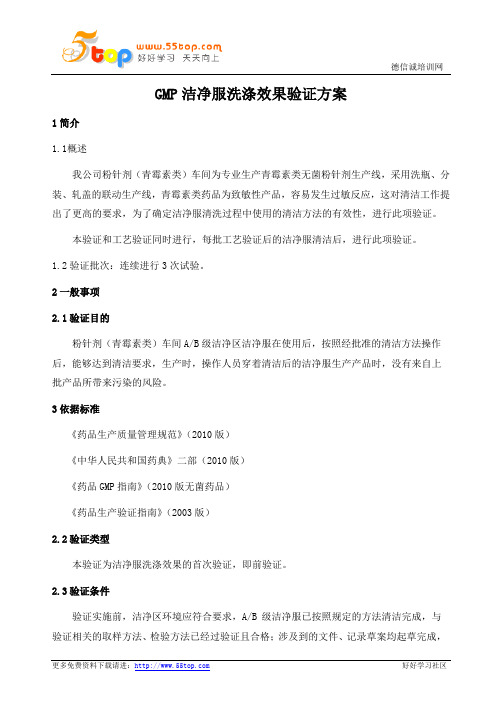
GMP洁净服洗涤效果验证方案1简介1.1概述我公司粉针剂(青霉素类)车间为专业生产青霉素类无菌粉针剂生产线,采用洗瓶、分装、轧盖的联动生产线,青霉素类药品为致敏性产品,容易发生过敏反应,这对清洁工作提出了更高的要求,为了确定洁净服清洗过程中使用的清洁方法的有效性,进行此项验证。
本验证和工艺验证同时进行,每批工艺验证后的洁净服清洁后,进行此项验证。
1.2验证批次:连续进行3次试验。
2一般事项2.1验证目的粉针剂(青霉素类)车间A/B级洁净区洁净服在使用后,按照经批准的清洁方法操作后,能够达到清洁要求,生产时,操作人员穿着清洁后的洁净服生产产品时,没有来自上批产品所带来污染的风险。
3依据标准《药品生产质量管理规范》(2010版)《中华人民共和国药典》二部(2010版)《药品GMP指南》(2010版无菌药品)《药品生产验证指南》(2003版)2.2验证类型本验证为洁净服洗涤效果的首次验证,即前验证。
2.3验证条件验证实施前,洁净区环境应符合要求,A/B级洁净服已按照规定的方法清洁完成,与验证相关的取样方法、检验方法已经过验证且合格;涉及到的文件、记录草案均起草完成,参与验证的所有人员均已培训并考核合格。
2.5执行原则2.5.1执行验证时,必须按本方案的前后顺序一致,不得随机选项。
2.5.2必须修改本方案所列的方法,应经验证领导小组批准,并说明修改理由。
2.5.3执行过程中如出现偏差,要及时进行记录,并按偏差处理程序进行处理。
3验证进度验证实施小组提出完整的进度计划,经验证委员会批准后实施。
清洁验证第一批:2013年2月19日清洁验证第二批:2013年2月20日清洁验证第三批:2013年2月21日起草验证报告:2013年2月19日至2013年2月25日4验证内容4.1相关人员进行的培训确认验证实施前,检查确认与本验证相关人员是否经过验证方案及相关操作规程的培训,将确认结果记录在《人员培训检查确认记录》(附件1)中。
新版GMP-清洁验

EU GMP的要求
清洁验证
清洁验证是为了确保清洁程序的有效性 而进行的。对于产品残留物清除,清洁剂和 微生物污染的限度选择,理论上应该以相关 原料为基础。这些限度应该是可以达到的 并且是可以被证实的。 37. 应该使用经确认的,对于检测残留物或污 染物具有灵敏度的分析方法。每一种分析 方法的检测限度应该足够灵敏来检测出符 合可接受标准要求的残留物或污染物。
2.浓度限度:10ppm(10mg/Kg) L(mg/cm2)=10B*RF/(S*F) B(kg):下批产品的生产批量为B(kg)
S:设备的总内表面积
RF:回收率
F:安全因子,一般选择10
淋洗水法的计算.
TD x BS x SF x RF x SW MAC (in mg / ml) = ---------------------------------LDD x SAxVR SW = 溶剂冲洗的设备表面积 TD = 清洁验证产品的单治疗剂量 BS =使用相同设备生产的下一品种的最小批量中活性成分 的量 SF = 安全系数= 1/1000 LDD =使用相同设备生产的下一品种的每日最大剂量. RF = 回收系数= (回收率的 %) / 100 SA = 总的设备内表面积 VR=冲洗剂的体积
*需要清洁验证的方面:
1直接接触物料的生产设备必须进行清洁验证;例: 混合机的混合容器、周转容器具 2同一产品批次间的清洁方法不需要进行清洁验证, 只需要达到“目视清洁”的标准即可。 3同一产品连续生产的最长时间或一定周期 4设备使用完后应及时清洁。“待清洁设备的保留 时间” 5设备清洁后到下次使用前放置的有效期,需要做 验证。“洁净保留时间” 6清洁方法必须经验证,并且应对其有效性、重现 性进行定期监测。
GMP固体制剂车间生产设备清洁验证方案
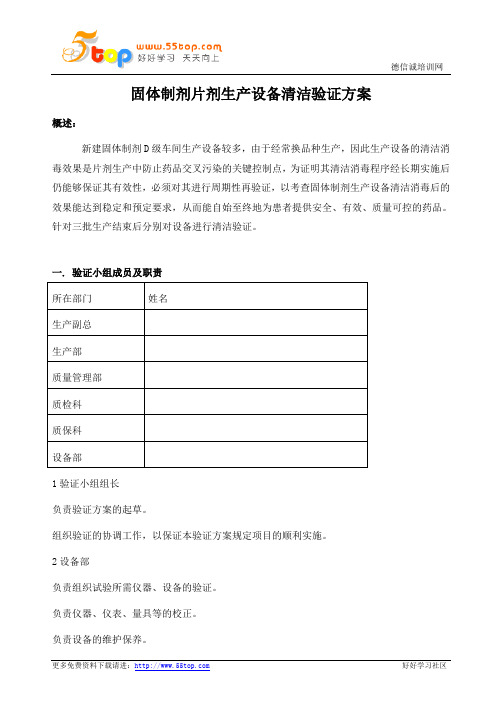
固体制剂片剂生产设备清洁验证方案
概述:
新建固体制剂D级车间生产设备较多,由于经常换品种生产,因此生产设备的清洁消毒效果是片剂生产中防止药品交叉污染的关键控制点,为证明其清洁消毒程序经长期实施后仍能够保证其有效性,必须对其进行周期性再验证,以考查固体制剂生产设备清洁消毒后的效果能达到稳定和预定要求,从而能自始至终地为患者提供安全、有效、质量可控的药品。
针对三批生产结束后分别对设备进行清洁验证。
一.验证小组成员及职责
1验证小组组长
负责验证方案的起草。
组织验证的协调工作,以保证本验证方案规定项目的顺利实施。
2设备部
负责组织试验所需仪器、设备的验证。
负责仪器、仪表、量具等的校正。
负责设备的维护保养。
负责设备的操作。
3 质量部
负责取样及提供验证所需检测数据。
负责收集各项验证、试验记录,并对试验结果进行分析
验证过程监督检查确保结果可靠性
负责验证方案的批准和验证报告的批准
4 生产部
负责验证方案制定和实施。
总结验证记录
本次清洁验证工作自年月日开始,年月日结束。
二. 目的
清洁验证方案的目的是证明GHL-300型高速混合制粒机、GFG-150型高效沸腾干燥机、EYH-4000型二维运动混合机清洁操作规程、YK-250型摇摆式颗粒机、F-320粉碎机、DPP-250D2型平板式铝塑泡罩包装机、BG-400E型高效智能包衣机等设备所使用的清洗程序能够有效地除去产品残留,达到预先确定的限度,从而达到对下批产品无影响。
三.周期
三批生产后,分别进行清洁验证研究。
四.相关的文件
表1
五、设备
表2。
GMP清洁验证特定方法及其验证

GMP清洁验证特定方法及其验证清洁验证特定方法及其验证对于特定的分析方法而言,类似于分析方法验证中的杂技的定量检测,所以基本上验证的项目也是参照这份方法验证指南的要求来进行的,主要的方法学验证包括以下内容:专属性专属性对于清洁方法验证至关重要。
从药品本身而言,清洁验证关注的更多的是药物的活性成份,所以对于制剂而言,往往会有药用辅料的干扰;同时,在清洁的过程中,往往会采用各式清洗剂,微量的清洗剂的残留以及清洗的过程如果涉及到酸碱的化学反应,也有可能会有降解产物的发生;另一方面,在取样过程中的一些器具也有可能会对检测产生干扰。
精密度/重现性精密度是指在规定的测试条件下,分析方法对于同一份样品测量结果的一致性,通常可以通过重复性、中间精密度和重现性三个维度去进行考虑。
重复性通常有两种方式,对于清洁验证而言,更常用的是同一个目标浓度或者同一个均匀样品,多次取样进行测试,6次测试结果的RSD应该在一定的范围内,ICH方法验证指南还有一种三个浓度,每个浓度进行三次测试,一共九个结果进行评判的方法。
中间精密度通常是指实验室内部由于设备的差异,分析柱的差异,甚至是取样中采用的棉签的不同导致的可能的分析结果上的差异,通常情况下,清洁验证的样品测试持续时间不会太长,测试条件相对固定,所以在制订计划的时候可以基于风险。
重现性则是指不同的实验室不同的分析人员之间的差异,如果不涉及到清洁验证分析方法的转移,这个步骤可以略去不做。
准确度和回收率这个参数是指测量值与真实值之间的接近程度,一般和%表示。
对于清洁验证而言,回收率应该尽可能接近100%,指南中提到,有的情况下,回收率低至50%也是可以接受的我确实不大能够理解,也希望朋友们能够分享你的观点。
回收率的测试方法,通常是将杂质、辅料、清洁剂与被测物一起制成溶液,在目标的残留限度的50%~150%范围内,选择三个不同的浓度,每个浓度制备三份溶液进行测试。
线性和校正曲线线性是指在设计的范围内,检测结果与试样中被测物质的浓度呈线性比例的关系,谈准确度、精密度和回收率,只有在一定的限度范围内才有意义。
GMP 专用生产线的清洁验证

专用生产线的清洁验证专用生产线什么时候需要做清洁验证基于风险考虑:专用生产线由于不存在与其他产品的残留物的交叉污染,所以我们可以不用考虑交叉污染的风险,我们只需要考虑污染风险。
污染的风险对于不同类型的产品也不尽相同。
污染物比如外来残留物(非其他产品)对于所有产品类型是通用的,是否需要针对外来物质进行清洁验证取决于生产设备的密闭程度及在清洁过程中是否会引入外来物质,比如非生产用的清洁剂。
另一类外来残留是微生物或内毒素,是否针对其进行清洁验证取决于生产设备生产的产品或中间产品或中间体的相应的质量要求,如果没有这方面的要求,则不需要进行验证。
最后需要考虑的是产品工艺产生的残留物对在该生产设备上生产的产品或中间产品或中间体的质量的影响,比如残留物是否会导致产品的某些杂质(一般是降解杂质或副产物)升高,如果批间存在显著影响,首先批间清洁可能是必须的,再者可能还需要对批间清洁的效果进行确认。
如果批间不存在显著影响,如果不需要考虑微生物或内毒素,则批间清洁甚至都不是必须的,可以采用多批清洁的方法,但是对于多批生产后清洁的累积杂质效应需要进行验证。
专用生产线如何进行清洁验证接着上面的进行分析,首先我们还是要用风险来衡量下,我们清洁的目的到底是为了什么??在此列举一下:1、为了降低外来残留物的量。
注意这里使用的是降低而不是去除。
在这种情况下,我们需要考虑我们的专用生产线中可能会有哪些外来残留物,来自于哪里?对于专用生产线,通常来自于环境或设备本身。
弄清楚了外来残留物后我们就需要具体分析一下这些外来残留物对于我们生产线上生产的产品或中间产品或中间体的质量影响,我们通过什么方式来避免外来物质进入我们的生产设备或生产物料中,比如使用密闭系统,比如使用空调净化系统等,如果这些方式可以有效地降低外来物质的残留风险,那么在这种情况下,清洁相对来说就不是最关键的,清洁的风险相对就较低,即可以考虑不对外来物质的残留风险进行清洁的有效性的确认。
GMP什么情况下,需要进行清洁验证

2016年09月29日国家局公布了对于天津金耀集团湖北天药的检查公告,其中一条缺陷,“未开展培养基模拟灌装后的清洁验证。
”引起了大家的争议和讨论。
培养基灌装后,需要做清洁验证么?首先,我们需要确认的是,什么情况下,需要进行清洁验证。
根据GMP 正文:“第一百四十三条清洁方法应当经过验证,证实其清洁的效果,以有效防止污染和交叉污染。
清洁验证应当综合考虑设备使用情况、所使用的清洁剂和消毒剂、取样方法和位置以及相应的取样回收率、残留物的性质和限度、残留物检验方法的灵敏度等因素。
”附录:《验证和确认》第三十九条为确认与产品直接接触设备的清洁操作规程的有效性,应当进行清洁验证。
应当根据所涉及的物料,合理地确定活性物质残留、清洁剂和微生物污染的限度标准。
总结一下两个法规的规定,就是对于有可能产生污染和交叉污染(和产品直接接触设备或区域)的清洁方法,为了证明清洁方法能够有效的清除可能的污染和交叉污染,需要对清洁方法进行清洁验证。
培养基灌装中,使用到的设备是会和产品直接接触的,培养基是有可能会对产品产生污染的,所以培养基灌装后的清洁方法是符合以上对于清洁验证的要求,毫无疑问是需要进行验证的,如果没有做,肯定是不符合法规要求。
那么该如何去做培养基灌装后的清洁验证呢?因为清洁验证,针对的是清洁程序,所以也分为以下情况来分析:一. 培养基灌装后的清洁方式和产品生产后的清洁方式一致在这种情况下,你需要做的是在你原始的清洁验证方案中,将培养基当成是你的产品来进行分析,分析各类产品的溶解性、毒性指标等,然后再来确定清洁验证的目标物,选择残留限度和检测方法。
这个并不需要单独针对培养基灌装的清洁写方案。
二.培养基灌装后的清洁方式和产品生产后的清洁方式不一致在这种情况下,你需要单独起草方案,方案的内容和要求和清洁验证的一样,确定残留限度和检验方法。
怎么去做,不在这里讨论,因为这是技术活,每个公司的选择都不同,以后有时间再讨论了。
药品GMP检查中清洁验证常见问题
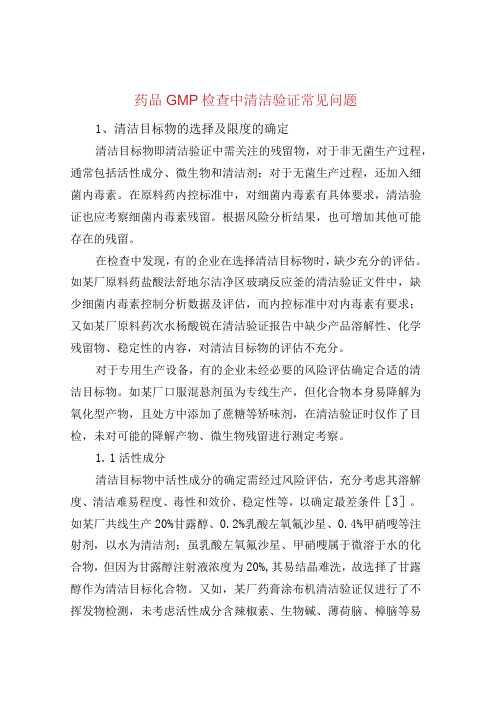
药品GMP检查中清洁验证常见问题1、清洁目标物的选择及限度的确定清洁目标物即清洁验证中需关注的残留物,对于非无菌生产过程,通常包括活性成分、微生物和清洁剂;对于无菌生产过程,还加入细菌内毒素。
在原料药内控标准中,对细菌内毒素有具体要求,清洁验证也应考察细菌内毒素残留。
根据风险分析结果,也可增加其他可能存在的残留。
在检查中发现,有的企业在选择清洁目标物时,缺少充分的评估。
如某厂原料药盐酸法舒地尔洁净区玻璃反应釜的清洁验证文件中,缺少细菌内毒素控制分析数据及评估,而内控标准中对内毒素有要求;又如某厂原料药次水杨酸锐在清洁验证报告中缺少产品溶解性、化学残留物、稳定性的内容,对清洁目标物的评估不充分。
对于专用生产设备,有的企业未经必要的风险评估确定合适的清洁目标物。
如某厂口服混悬剂虽为专线生产,但化合物本身易降解为氧化型产物,且处方中添加了蔗糖等矫味剂,在清洁验证时仅作了目检,未对可能的降解产物、微生物残留进行测定考察。
1.1活性成分清洁目标物中活性成分的确定需经过风险评估,充分考虑其溶解度、清洁难易程度、毒性和效价、稳定性等,以确定最差条件[3]。
如某厂共线生产20%甘露醇、0.2%乳酸左氧氟沙星、0.4%甲硝嗖等注射剂,以水为清洁剂;虽乳酸左氧氟沙星、甲硝嗖属于微溶于水的化合物,但因为甘露醇注射液浓度为20%,其易结晶难洗,故选择了甘露醇作为清洁目标化合物。
又如,某厂药膏涂布机清洁验证仅进行了不挥发物检测,未考虑活性成分含辣椒素、生物碱、薄荷脑、樟脑等易溶或可溶的化合物;经整改评估后,最终选择生物碱为目标化合物。
再如,某湿法混合制粒机,清洁目标化合物的选择比较困难,因共线品种有非洛地平缓释片、阿奇霉素分散片、复方曲尼司特片等;其中非洛地平、阿奇霉素溶解度较差,两者日治疗剂量分别为 2.5mg、167mg,最终选择日治疗剂量小的非洛地平为目标化合物。
12微生物和细菌内毒素在检查中发现,有的企业对生产设备和器具未制定清洁后的保存时效,缺少微生物等方面的数据支持。
GMP口服固体生产线清洁验证方案

GMP口服固体生产线清洁验证方案
1. 概述
我公司新厂区口服固体生产线目前主要生产品种有:
其设备及容器具使用情况见附表1。
为了避免交叉污染,评估现行清洁标准操作规程的效果,须对与药品直接接触的设备、容器具的清洁效果进行确认。
2. 验证对象
口服固体生产线设备及容器具清洁标准操作规程
3. 验证小组成员
4. 验证目的
确认口服固体生产线与药品直接接触的设备、容器具按现行标准操作规程清洁后,残留物达到了规定的清洁限度要求,不对产品造成污染和交叉污染,确定的清洁有效期可行。
5. 验证方法、程序及合格标准
5.1 合格标准
5.1.1化学取样可接受标准
共用设备及容器具单位面积最大允许残留量R,见附表5。
(参照产品选择和残留限度标准设定参见附1。
)
5.1.1.1擦拭样
本方案中,每个棉签的擦拭取样面积为25 cm2,并以10ml流动相洗脱,按取样回收率F为50%计算,其浓度限度
P=[R(mg/ cm2)×25 cm2×50%]/(10ml×1000)=5×10-6g/ml
详见表1:
注:2.43E-05即2.43×10-5,下同。
5.1.1.2冲洗水样
设定取冲洗水样的设备部件与药粉接触部分的表面积S0(cm2),冲洗水用量为V(ml),按取样回收率F为50%计算,每个冲洗水样品中允许的最高限度P=0.001*R*S0*F/V=0.0005*R* S0/V(g/ml)。
详见表2:。
制药工程GMP(清洁验证)

100 mg
微生物取样
对难以接触的表面用棉签取样
对平直表面用RODAC板
微生物取样应在化学取样前进行
清洁验证检验方法
检验方法对于分析物是特定的
检验方法必须经过验证
– 专属性 – 灵敏度 – 精密度 – 线性范围
– 回收率(取样和检验)
分析方法选 择和验证
常用的分析 方法:
分析方法选 择和验证
良好的清洁结果的重要性
降低交叉污染的风险 使得产品受污染报废的可能性最小 患者的负面效应可能性最小 降低产品投诉的发生率 降低卫生部门或其他机构检查不合格的风险 延长设备的使用寿命
设备清洁的类型
手工清洗
*
由操作人员用擦洗或用高压软管等进行的清洗
自动清洗
*
由自动控制系统进行洗刷直至干燥的清洗
清
洗
验
证
第八十四条 应当按照详细规定的操作规程清洁 生产设备。 生产设备清洁的操作规程应当规定具体而完 整的清洁方法、清洁用设备或工具、清洁剂的名 称和配制方法、去除前一批次标识的方法、保护 已清洁设备在使用前免受污染的方法、已清洁设 备最长的保存时限、使用前检查设备清洁状况的 方法,使操作者能以可重现的、有效的方式对各 类设备进行清洁。
清洁规程要点
拆卸(程度)要求 每一步的清洗要求 – 浸泡/预冲洗/清洗/喷淋时间、温度要求 – 清洗剂名称/浓度/数量/配制方法 – 清洁工具要求 消毒/灭菌,方法及相关参数 干燥方法 清洁后检查要求
清洁规程要点
生产结束至开始清洁的最长时间要求 设备连续使用的最长时间 清洁后设备的储存和条件 已清洁设备的最长存放时间 设备的清洁状况标识 过清洁有效期设备的处理 设备使用前的检查 装配要求
【最新GMP验证】生产设备清洁验证方案
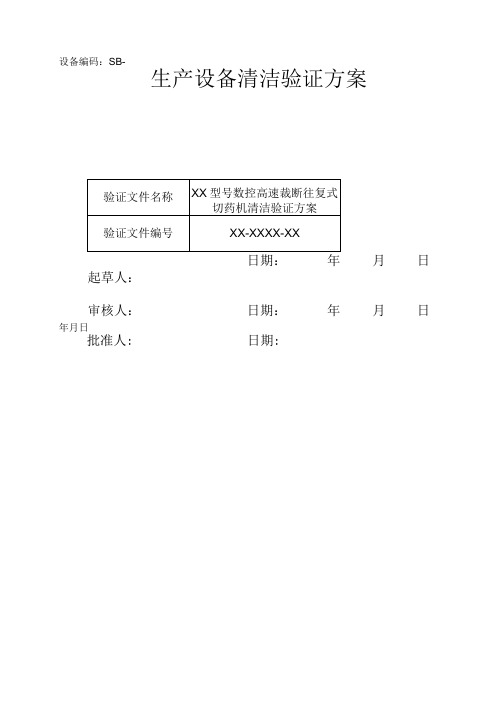
设备编码:SB-生产设备清洁验证方案月日起草人:审核人:日期:年月日年月日批准人: 日期:目录1.验证立项申请表2.验证所需仪器仪表3.验证小组成员4.验证时间安排5.验证方案内容XXXXXX药业有限公司一、验证立项申请表二、验证所需仪器仪表三、验证小组成员四、验证时间安排年月曰〜年月曰对该生产设备清洁进行验证。
五、验证方案内容1.目的:为确认XX型号数控高速裁断往复式切药机清洁规程符合要求,证明直接接触药品的设备按规定的清洁程序清洁后,设备残留的污染物符合规定的限度标准,证明该设备的清洁规程是可靠的,从而消除了设备清洁不彻底造成残留物对下一个产品污染的发生,有效地保证药品质量。
为了增强此次验证的可靠性,清洁验证需进行三个批次。
2.范围:适用于XX型号数控高速裁断往复式切药机清洁规程的验证。
3.责任:验证小组负责对此设备清洁进行验证,生产人员实施对设备清洁的操作。
4.内容:4.1概述根据GMP要求,每次更换生产品种和生产批号时,需按清洁规程对设备进行有效清洁。
生产设备的清洁是指从设备表面(尤其是直接接触药品的内表面及各部件)去除可见及不可见物质的过程。
为评价该设备清洁规程的效果,需进行清洁验证。
由于影响设备清洁效果及清洁有效期的因素较多,各种因素的风险严重性、发生概率及可检测性不同,产生的影响及后果的严重程度也不相同,因此清洁验证前首先要进行风险分析及风险评估,以确定设备清洁验证方案的验证项目及验证方法。
本次验证引入风险评估内容,以证明清洁规程的可靠性。
4.2风险分析工具利用失效模式与影响分析(FMEA)对主要设备清洁再验证方案进行系统的风险分析。
具体如下:从严重性、发生概率、可检测性三方面进行风险定性评估分级。
风险严重性(S)划分为轻度(1)、中度(2)、严重(3),风险发生概率(O)划分为很少(1)、偶尔(2)、经常(3),可检测性(D)划分为可检测效果明显(1)、通过管理手段可检测(2)、几乎无法检测(3)o风险优先数(RPN)二风险严重性(S)X风险发生概率(O)X可检测性(D),一般情况下,RPN<4为可接受,4WRPN<8为合理可行降低,8WRPN为不可接受。
GMP检查内容验证(检查核心)
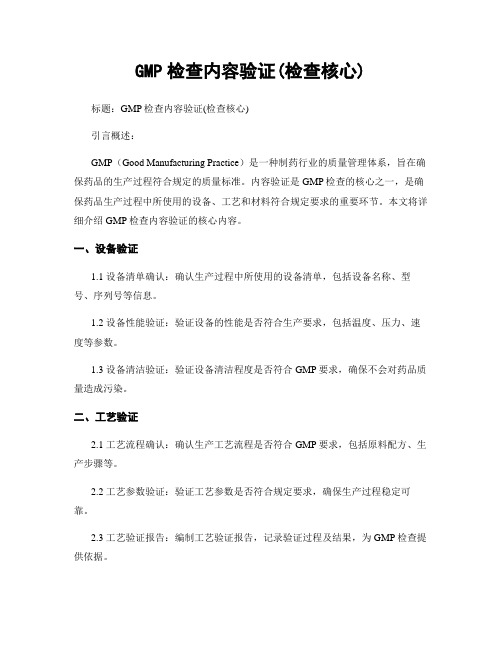
GMP检查内容验证(检查核心)标题:GMP检查内容验证(检查核心)引言概述:GMP(Good Manufacturing Practice)是一种制药行业的质量管理体系,旨在确保药品的生产过程符合规定的质量标准。
内容验证是GMP检查的核心之一,是确保药品生产过程中所使用的设备、工艺和材料符合规定要求的重要环节。
本文将详细介绍GMP检查内容验证的核心内容。
一、设备验证1.1 设备清单确认:确认生产过程中所使用的设备清单,包括设备名称、型号、序列号等信息。
1.2 设备性能验证:验证设备的性能是否符合生产要求,包括温度、压力、速度等参数。
1.3 设备清洁验证:验证设备清洁程度是否符合GMP要求,确保不会对药品质量造成污染。
二、工艺验证2.1 工艺流程确认:确认生产工艺流程是否符合GMP要求,包括原料配方、生产步骤等。
2.2 工艺参数验证:验证工艺参数是否符合规定要求,确保生产过程稳定可靠。
2.3 工艺验证报告:编制工艺验证报告,记录验证过程及结果,为GMP检查提供依据。
三、材料验证3.1 原料供应商审核:审核原料供应商是否符合GMP要求,确保原料质量可靠。
3.2 原料检验:对原料进行检验,确保符合规定的质量标准。
3.3 原料追溯:建立原料追溯体系,确保原料来源可追溯,保证药品质量稳定。
四、环境验证4.1 温湿度控制:验证生产环境的温湿度控制是否符合GMP要求,确保药品生产稳定。
4.2 洁净度验证:验证生产环境的洁净度是否符合要求,避免对药品质量产生污染。
4.3 环境监测:建立环境监测体系,定期对生产环境进行监测,确保符合GMP 标准。
五、文档验证5.1 SOP文件审核:审核SOP文件是否符合GMP要求,确保生产操作规范。
5.2 记录管理:建立记录管理体系,确保生产过程中的记录完整、准确。
5.3 培训记录:记录员工培训情况,确保员工了解GMP要求,提高生产质量。
结论:GMP检查内容验证是确保药品生产过程符合质量标准的重要环节,涉及设备、工艺、材料、环境和文档等多个方面。
gmp清洁验证toc标准

gmp清洁验证toc标准
GMP(良好生产规范)清洁验证的TOC(总有机碳)标准是指在进行清洁验证时,需要将设备表面的有机碳含量控制在一定范围内,以确保设备的清洁效果和药品生产的质量。
具体而言,清洁验证的TOC标准需要根据设备和产品的具体情况而定,一般需要符合相关法规和规范的要求。
在清洁验证过程中,需要对设备进行清洗和检测,以确保设备表面的有机碳含量符合标准。
如果设备表面残留的有机碳含量超标,需要进行进一步的处理和清洁,直到符合标准为止。
以上内容仅供参考,建议查阅关于GMP清洁验证的书籍或者咨询制药工程领域专业人士获取更多专业解答。
新版GMP药企药品车间清洁验证管理制度

车间清洁验证管理制度实施:生产技术部:负责组织清洁验证方案、验证报告的起草及验证的实施。
QC负责人:负责按计划完成清洁验证中的相关检验任务,确保检验结论正确可靠。
QA验证管理员:负责验证工作的管理,协助清洁验证方案的起草,组织协调验证工作,并总结验证结果。
QA主管:负责清洁验证方案及报告的审核。
质量部负责人:负责清洁验证方案及报告的批准。
目的:通过对制定的清洁标准操作规程进行验证,考察清洁过程是否能始终如一地符合预定标准,降低交叉污染的风险。
范围:本标准适用于本公司药品生产中使用的所有与产品接触的设备、容器具、工具清洗效果的验征。
包括化学和微生物两项指标。
内容:1 清洁验证小组成员:生产技术部人员、质量部负责人、QA主管、QA验证管理员、QC主管、检验员、设备管理员。
2 清洁验证范围的确定:2.1 清洁验证的对象:包括所有与产品直接接触的生产设备、容器、工具。
2.2 清洁验证前应明确:2.2.1 生产产品的类型和数量(批量)。
2.2.3 产品处方及材料的特性。
2.2.4 设备的特性。
2.2.5 设备在生产过程中的作用。
2.2.6 评价清洗过程可能存在的问题。
3 清洁验证的前提条件:3.1 检查是否制定有清洁操作规程,清洁操作规程应包括以下内容:3.1.1 操作规程名称;3.1.2 操作规程适用范围;3.1.3 职责(本操作规程涉及的责任部门或责任人);3.1.4 操作规程的操作步骤或程序;3.1.5 清洁的范围或对象;3.1.6 清洁实施的条件及频次;3.1.7 进行清洁的地点;3.1.8 清洁用的设备及设施;3.1.9 清洁所用的清洁剂及其配制方法;3.1.10 清洁方法及清洁用水;3.1.11 清洁设备及器具的干燥与存放;3.1.12 消毒剂及其配制;3.1.13 消毒频次及方法;4 清洁(及消毒)效果的评价:4.1 清洁操作规程的执行检查。
4.2 对照操作规程检查是否有效执行。
4.3 保证对所有关键步骤进行监控。
- 1、下载文档前请自行甄别文档内容的完整性,平台不提供额外的编辑、内容补充、找答案等附加服务。
- 2、"仅部分预览"的文档,不可在线预览部分如存在完整性等问题,可反馈申请退款(可完整预览的文档不适用该条件!)。
- 3、如文档侵犯您的权益,请联系客服反馈,我们会尽快为您处理(人工客服工作时间:9:00-18:30)。
专用生产线的清洁验证
专用生产线什么时候需要做清洁验证
基于风险考虑:专用生产线由于不存在与其他产品的残留物的交叉污染,所以我们可以不用考虑交叉污染的风险,我们只需要考虑污染风险。
污染的风险对于不同类型的产品也不尽相同。
污染物比如外来残留物(非其他产品)对于所有产品类型是通用的,是否需要针对外来物质进行清洁验证取决于生产设备的密闭程度及在清洁过程中是否会引入外来物质,比如非生产用的清洁剂。
另一类外来残留是微生物或内毒素,是否针对其进行清洁验证取决于生产设备生产的产品或中间产品或中间体的相应的质量要求,如果没有这方面的要求,则不需要进行验证。
最后需要考虑的是产品工艺产生的残留物对在该生产设备上生产的产品或中间产品或中间体的质量的影响,比如残留物是否会导致产品的某些杂质(一般是降解杂质或副产物)升高,如果批间存在显著影响,首先批间清洁可能是必须的,再者可能还需要对批间清洁的效果进行确认。
如果批间不存在显著影响,如果不需要考虑微生物或内毒素,则批间清洁甚至都不是必须的,可以采用多批清洁的方法,但是对于多批生产后清洁的累积杂质效应需要进行验证。
专用生产线如何进行清洁验证
接着上面的进行分析,首先我们还是要用风险来衡量下,我们清洁的目的到底是为了什么??在此列举一下:
1、为了降低外来残留物的量。
注意这里使用的是降低而不是去除。
在这种情况下,我们需要考虑我们的专用生产线中可能会有哪些外来残留物,来自于哪里?对于专用生产线,通常来自于环境或设备本身。
弄清楚了外来残留物后我们就需要具体分析一下这些外来残留物对于我们生产线上生产的产品或中间产品或中间体的质量影响,我们通过什么方式来避免外来物质进入我们的生产设备或生产物料中,比如使用密闭系统,比如使用空调净化系统等,如果这些方式可以有效地降低外来物质的残留风险,那么在这种情况下,清洁相对来说就不是最关键的,清洁的风险相对就较低,即可以考虑不对外来物质的残留风险进行清洁的有效性的确认。
2、为了降低微生物残留或内毒素指标。
如果明确了需要通过清洁的方式来降低微生物残留或保证内毒素合格,则需要通过对清洁后的微生物残留或内毒素指标来对清洁方法进行验证。
微生物残留或内毒素残留指标可以通过在该专用设备上生产的产品的相应质量指标来反推出该专用设备与工艺物料接触表面允许的最大的微生物负荷或内毒素负荷。
3、为了降低残留物对该设备中生产的下批次产品的杂质限度的影响;这种情况下通常需要两个方面,一方面是清洁剂是否有影响,另一方面需要考虑产品生产过程中的物料及其降解产物、副产物对产品质量的影响。
在设定残留限度时可以使用反推的方法,但由于残留物本身通常量比较少,计算出的限度可能会很高,所
以通过计算大部分情况实际是不需要制定详细的残留限度指标的。
当然这个需要比较比较详尽的风险推导的过程。
当然要注意的是这个过程需要研发数据和历史数据的充分支持。
专用生产线的清洁验证可以考虑的方式
专用生产线的清洁验证本质上其实并不同于多产品共线的生产线,要真正梳理清楚专用生产线的清洁验证,明确两者的区别至关重要。
从风险的角度考虑,专用生产线的清洁风险远远小于多产品共线生产线的清洁风险。
原因在于多产品共线生产时,来自于另一产品的残留物很难体现在下一产品的质量标准中,主要原因是产品的一些专属性的分析方法和质量指标通常只对本产品有效,对其他产品可能就会存在无法检出的情况。
从风险三要素来考虑就是可检测性很低,所以相对而言风险就很高。
这也是为什么GMP 对于多产品共线生产的清洁验证给予非常高的重视的根本原因。
历史上很多著名的药害事故也源于此。
明确了这一点后,我们在做专用生产线的清洁验证时也可以考虑采用比多产品共线生产线清洁验证较为简洁的方式。
在这里推荐两种方式:
方式一:对于需要批间清洁,可以考虑将清洁作为工艺的一部分在工艺验证中进行验证;
方式二:如果不是批间清洁的或者无法将清洁作为工艺的一部分的,可以考虑单独验证。
目前在很多企业都存在专用生产线清洁验证过度的问题,主要问
题就在于没有理清楚专用生产线的清洁风险在哪里,生搬硬套了本来适用于多产品共线生产清洁验证的一些指南文件。
一个典型的例子是曾经有人与小编交流:如何确定专线生产线残留物的毒性?很遗憾,小编给他的答案是不需要去确定,因为理论上讲,专用生产线中可能残留到产品中的杂质都是应该被研究过的,如果没有被研究过,那就是本身工艺研究不充分,基于此,专用生产线中残留在设备上后又进入产品的任何杂质都应该在质量标准中有体现,也就是说这些残留物最终在产品中不能超过产品的质量标准限度。
那么这些残留物的限度该如何定??是否需要定?这个就需要从风险的角度来衡量。
如何衡量,还是可以从风险三要素入手:严重程度需要考虑残留物与产品质量标准中对应的杂质的关系来确定,清洁后残留到产品中导致产品质量标准中杂质超标或超趋势的概率有多大,残留物的量通过什么方式可以被检测出,检测可以是直接的,比如直接检测清洗水中的残留物的量,比如目测,也可以是间接的,比如通过该设备生产的产品或中间体或中间产品的检测结果来间接反映等。
通过综合考虑这三方面的因素就可以明确是否需要定残留物的限度,使用什么样的检测手段来检测。