PLC灌装机 ,压盖机外文文献翻译
PLC中英文资料外文翻译.doc
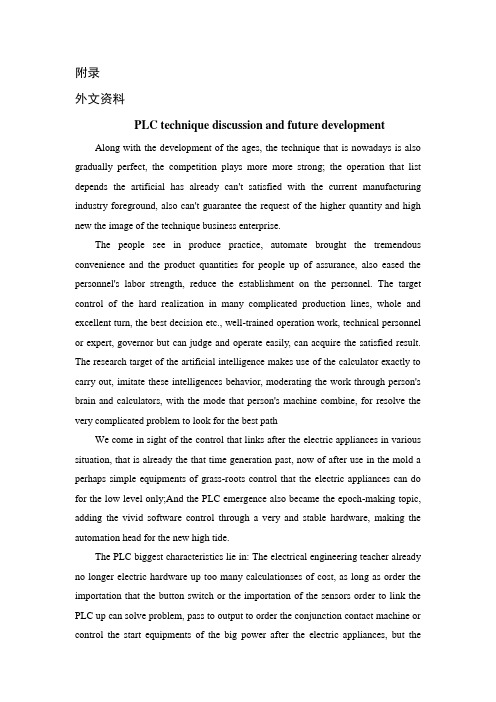
附录外文资料PLC technique discussion and future development Along with the development of the ages, the technique that is nowadays is also gradually perfect, the competition plays more more strong; the operation that list depends the artificial has already can't satisfied with the current manufacturing industry foreground, also can't guarantee the request of the higher quantity and high new the image of the technique business enterprise.The people see in produce practice, automate brought the tremendous convenience and the product quantities for people up of assurance, also eased the personnel's labor strength, reduce the establishment on the personnel. The target control of the hard realization in many complicated production lines, whole and excellent turn, the best decision etc., well-trained operation work, technical personnel or expert, governor but can judge and operate easily, can acquire the satisfied result. The research target of the artificial intelligence makes use of the calculator exactly to carry out, imitate these intelligences behavior, moderating the work through person's brain and calculators, with the mode that person's machine combine, for resolve the very complicated problem to look for the best pathWe come in sight of the control that links after the electric appliances in various situation, that is already the that time generation past, now of after use in the mold a perhaps simple equipments of grass-roots control that the electric appliances can do for the low level only;And the PLC emergence also became the epoch-making topic, adding the vivid software control through a very and stable hardware, making the automation head for the new high tide.The PLC biggest characteristics lie in: The electrical engineering teacher already no longer electric hardware up too many calculationses of cost, as long as order the importation that the button switch or the importation of the sensors order to link the PLC up can solve problem, pass to output to order the conjunction contact machine or control the start equipments of the big power after the electric appliances, but theexportation equipments direct conjunction of the small power can.PLC internal containment have the CPU of the CPU, and take to have an I/ O for expand of exterior to connect a people's address and saving machine three big pieces to constitute, CPU core is from an or many is tired to add the machine to constitute, mathematics that they have the logic operation ability, and can read the procedure save the contents of the machine to drive the homologous saving machine and I/ Os to connect after pass the calculation; The I/ O add inner part is tired the input and output system of the machine and exterior link, and deposit the related data into the procedure saving machine or data saving machine; The saving machine can deposit the data that the I/ O input in the saving machine, and in work adjusting to become tired to add the machine and I/ Os to connect, saving machine separately saving machine RAM of the procedure saving machine ROM and datas, the ROM can can do deposit of the data permanence in the saving machine, but RAM only for the CPU computes the temporary calculation usage of hour of buffer space.The PLC anti- interference is very and excellent, our root need not concern its service life and the work situation bad, these all problems have already no longer become the topic that we fail, but stay to our is a concern to come to internal resources of make use of the PLC to strengthen the control ability of the equipments for us, make our equipments more gentle.PLC language is not we imagine of edit collected materials the language or language of Cs to carry on weaving the distance, but the trapezoid diagram that the adoption is original after the electric appliances to control, make the electrical engineering teacher while weaving to write the procedure very easy comprehended the PLC language, and a lot of non- electricity professional also very quickly know and go deep into to the PLC.Is PLC one of the advantage above and only, this is also one part that the people comprehend more and easily, in a lot of equipmentses, the people have already no longer hoped to see too many control buttons, they damage not only and easily and produce the artificial error easiest, small is not a main error perhaps you can still accept; But lead even is a fatal error greatly is what we can't is tolerant of. Newtechnique always for bringing more safe and convenient operation for us, make we a lot of problems for face on sweep but light, do you understand the HMI? Says the HMI here you basically not clear what it is, also have no interest understanding, change one inside text explains it into the touch to hold or man-machine interface you knew, it combines with the PLC to our larger space.HMI the control not only only is reduced the control press button, increase the vivid of the control, more main of it is can sequence of, and at can the change data input to output the feedback with data, control in the temperature curve of imitate but also can keep the manifestation of view to come out. And can write the function help procedure through a plait to provide the help of various what lies in one's power, the one who make operate reduces the otiose error. Currently the HMI factory is also more and more, the function is also more and more strong, the price is also more and more low, the noodles of the usage are wide more and more. The HMI foreground can say that think ° to be good very.At a lot of situations, the list is is a smooth movement that can't guarantee the equipments by the control of the single machine, but pass the information exchanges of the equipments and equipments to attain the result that we want. For example fore pack and the examination of the empress work preface, we will arrive wrapping information feedback to examine the place, and examine the information of the place to also want the feedback to packing. Pass the information share thus to make both the chain connect, becoming a total body, the match of your that thus make is more close, at each other attain to reflect the result that mutually flick.The PLC correspondence has already come more more body now its value, at the PLC and correspondence between PLCs, can pass the communication of the information and the share of the datas to guarantee that of the equipments moderates mutually, the result that arrive already to repair with each other. Data conversion the adoption RS232 between PLC connect to come to the transmission data, but the RS232 pick up a people and can guarantee 10 meters only of deliver the distance, if in the distance of 1000 meters we can pass the RS485 to carry on the correspondence, the longer distance can pass the MODEL only to carry on deliver.The PLC data transmission is just to be called a form to it in a piece of and continuous address that the data of the inner part delivers the other party, we, the PLC of the other party passes to read data in the watch to carry on the operation. If the data that data in the watch is a to establish generally, that is just the general data transmission, for example today of oil price rise, I want to deliver the price of the oil price to lose the oil ally on board, that is the share of the data; But take data in the watch for an instruction procedure that controls the PLC, that had the difficulty very much, for example you have to control one pedestal robot to press the action work that you imagine, you will draw up for it the form that a procedure combine with the data sends out to pass by.The form that information transport contain single work, the half a work and the difference of a workses .The meaning of the single work also is to say both, a can send out only, but a can receive only, for example a spy he can receive the designation of the superior only, but can't give the superior reply; A work of half is also 2 and can can send out similar to accept the data, but can't send out and accept at the same time, for example when you make a phone call is to can't answer the phone, the other party also; But whole pair works is both can send out and accept the data, and can send out and accept at the same time. Be like the Internet is a typical example.The process that information transport also has synchronous and different step cent: The data line and the clock lines are synchronous when synchronous meaning lie in sending out the data, is also the data signal and the clock signals to be carry on by the CPU to send out at the same time, this needs to all want the specialized clock signal each other to carry on the transmission and connect to send, and is constrained, the characteristics of this kind of method lies in its speed very quick, but correspond work time of take up the CPU and also want to be long oppositely, at the same time the technique difficulty also very big. Its request lies in can'ting have an error margins in a datas deliver, otherwise the whole piece according to compare the occurrence mistake, this on the hardware is a bigger difficulty. Applied more and more extensive in some appropriative equipmentses, be like the appropriative medical treatment equipments, the numerical signal equipments...etc., in compare the one data deliver,its result is very good.And the different step is an application the most extensive, this receive benefit in it of technique difficulty is opposite and want to be small, at the same time not need to prepare the specialized clock signal, its characteristics to lie in, its data is partition, the long-lost send out and accept, be the CPU is too busy of time can grind to a stop sex to work, also reduced the difficulty on the hardware, the data throw to lose at the same time opposite want to be little, we can pass the examination of the data to observe whether the data that we send out has the mistake or not, be like strange accidentally the method, tired addition and eight efficacies method etc., can use to helps whether the data that we examine to send out have or not the mistake occurrence, pass the feedback to carry on the discriminator.A line of transmission of the information contain a string of and combine the cent of: The usual PLC is 8 machines, certainly also having 16 machines. We can be an at the time of sending out the data a send out to the other party, also can be 88 send out the data to the other party, an and 8 differentiationses are also the as that we say to send out the data and combine sends out the data. A speed is more and slowly, but as long as 2 or three lines can solve problem, and can use the telephone line to carry on the long range control. But combine the oscular transmission speed is very quick of, it is a string of oscular of 25600%, occupy the advantage in the short distance, the in view of the fact TTL electricity is even, being limited by the scope of one meter generally, it combine unwell used for the data transmission of the long pull, thus the cost is too expensive.Under a lot of circumstances we are total to like to adopt the string to combine the conversion chip to carry on deliver, under this kind of circumstance not need us to carry on to depositted the machine to establish too and complicatedly, but carry on the data exchanges through the data transmission instruction directly, but is not a very viable way in the correspondence, because the PLC of the other party must has been wait for your data exportation at the time of sending out the data, it can't do other works.When you are reading the book, you hear someone knock on door, you stop tostart up of affair, open the door and combine to continue with the one who knock on door a dialogue, the telephone of this time rang, you signal hint to connect a telephone, after connecting the telephone through, return overdo come together knock on door to have a conversation, after dialogue complete, you continue again to see your book, this kind of circumstance we are called the interruption to it, it has the authority, also having sex of have the initiative, the PLC had such function .Its characteristics lie in us and may meet the urgently abrupt affairs in the operation process of the equipments, we want to stop to start immediately up of work, the whereabouts manages the more important affair, this kind of circumstance is we usually meet of, PLC while carry out urgent mission, total will keep the current appearance first, for example the address of the procedure, CPU of tired add the machine data etc., be like to to stick down which the book that we see is when we open the door the page or simply make a mark, because we treat and would still need to continue immediately after book of see the behind. The CPU always does the affair that should do according to our will, but your mistake of give it an affair, it also would be same to do, this we must notice.The interruption is not only a, sometimes existing jointly with the hour several inside break, break off to have the preferred Class, they will carry out the interruption of the higher Class according to person's request. This kind of breaks off the medium interruption to also became to break off the set. The Class that certainly break off is relevant according to various resources of CPU with internal PLC, also following a heap of capacity size of also relevant fasten.The contents that break off has a lot of kinds, for example the exterior break off, correspondence in of send out and accept the interruption and settle and the clock that count break off, still have the WDT to reset the interruption etc., they enriched the CPU to respond to the category while handle various business. Speak thus perhaps you can't comprehend the internal structure and operation orders of the interruption completely also, we do a very small example to explain.Each equipments always will not forget a button, it also is at we meet the urgent circumstance use of, that is nasty to stop the button. When we meet the Human body trouble and surprised circumstances we as long as press it, the machine stops alloperations immediately, and wait for processing the over surprised empress recover the operation again.Nasty stop the internal I/ O of the internal CPU of the button conjunction PLC to connect up, be to press button an exterior to trigger signal for CPU, the CPU carries on to the I/ O to examine again, being to confirm to have the exterior to trigger the signal, CPU protection the spot breaks off procedure counts the machine turn the homologous exterior I/ O automatically in the procedure to go to also, be exterior interruption procedure processing complete, the procedure counts the machine to return the main procedure to continue to work.Have 1:00 can what to explain is we generally would nasty stop the button of exterior break off to rise to the tallest Class, thus guarantee the safety.When we are work a work piece, giving the PLC a signal, counting PLC inner part the machine add 1 to compute us for a day of workload, a count the machine and can solve problem in brief, certainly they also can keep the data under the condition of dropping the electricity, urging the data not to throw to lose, this is also what we hope earnestly.The PLC still has the function that the high class counts the machine, being us while accept some datas of high speed, the high speed that here say is the data of the in all aspects tiny second class, for example the bar code scanner is scanning the data continuously, calculating high-speed signal of the data processor DSP etc., we will adopt the high class to count the machine to help we carry on count. It at the PLC carries out the procedure once discover that the high class counts the machine to should of interruption, will let go of the work on the hand immediately. The trapezoid diagram procedure that passes by to weave the distance again explains the high class for us to carry out procedure to count machine would automatic performance to should of work, thus rise the Class that the high class counts the machine to high one Class.You heard too many this phrases perhaps:" crash", the meaning that is mostly is a workload of CPU to lead greatly, the internal resources shortage etc. the circumstance can't result in procedure circulate. The PLC also has the similar circumstance, there is a watchdog WDT in the inner part of PLC, we can establish。
关于PLC的英文文献Word版

1. PROGRAMMABLE LOGIC CONTROLLERS1.1 INTRODUCTIONControl engineering has evolved over time. In the past humans was the main method for controlling a system. More recently electricity has been used for control and early electrical control was based on relays. These relays allow power to be switched on and off without a mechanical switch. It is common to use relays to make simple logical control decisions. The development of low cost computer has brought the most recent revolution, the Programmable Logic Controller (PLC). The advent of the PLC began in the 1970s, and has become the most common choice for manufacturing controls. PLC have been gaining popularity on the factory floor and will probably remain predominant for some time to come. Most of this is because of the advantages they offer.. Cost effective for controlling complex systems.. Flexible and can be reapplied to control other systems quickly and easily.. Computational abilities allow more sophisticated control.. Trouble shooting aids make programming easier and reduce downtime. . Reliable components make these likely to operate for years before failure.1.2 Ladder LogicLadder logic is the main programming method used for PLC. As mentioned before, ladder logic has been developed to mimic relay logic. The decision to use the relay logic diagrams was a strategic one. By selecting ladder logic as the main programming method, the amount of retraining needed for engineers and trades people was greatly reduced. Modern control systems still include relays, but these are rarely used for logic.A relay is a simple device that uses a magnetic field to control a switch, as pictured in Figure 2.1. When a voltage is applied to the input coil, the resulting current creates a magnetic field. The magnetic field pullsa metal switch (or reed) towards it and the contacts touch, closing the switch. The contact that closes when the coil is energized is called normally open. The normally closed contacts touch when the input coil is not energized. Relays are normally drawn in schematic form using a circle to represent the input coil. The output contacts are shown with two parallel lines. Normally open contacts are shown as two lines, and will be open (non-conducting) when the input is not energized. Normally closed contacts are shown with two lines with a diagonal line through them. When the input coil is not energized the normally closed contactswill be closed (conducting).Relays are used to let one power source close a switch for another (often high current) power source, while keeping them isolated. An example of a relay in a simple control application is shown in Figure 2.2. In this system the first relay on the left is used as normally closed, and will allow current to flow until a voltage is applied to the input A. The second relay is normally open and will not allow current to flow until a voltage is applied to the input B. If current is flowing through the first two relays then current will flow through the coil in the third relay, and close the switch for output C. This circuit would normally be drawn in the ladder logic form. This can be read logically as C will be on if A is off and B is on.1.3 ProgrammingThe first PLC were programmed with a technique that was based on relay logic wiring schematics. This eliminated the need to teach the electricians, technicians and engineers how to program a computer - but, this method has stuck and it is the most common technique for programming PLC today. An example of ladder logic can be seen in Figure 2.5. To interpret this diagram imagines that the power is on the vertical line on the left hand side, we call this the hot rail. On the right hand side is the neutral rail. In the figure there are two rungs, and on each rung there are combinations of inputs (two vertical lines) and outputs (circles). If the inputs are opened or closed in the right combination the power can flow from the hot rail, through the inputs, to power the outputs, and finally to the neutral rail. An input can come from a sensor, switch, or any other type of sensor. An output will be some device outside the PLC that is switched on or off, such as lights or motors. In the toprung the contacts are normally open and normally closed, which means if input A is on and input B is off, then power will flow through the output and activate it. Any other combinationof input values will result in the output X being off.The second rung of Figure 2.5 is more complex, there are actually multiple combinations of inputs that will result in the output Y turning on. On the left most part of the rung, power could flow through the top if C is off and D is on. Power could also (and simultaneously) flow through the bottom if both E and F are true. This would get power half way across the rung, and then if G or H is true the power will be delivered to output Y. In later chapters we will examine how to interpret and construct these diagrams. There are other methods for programming PLC. One of the earliest techniques involved mnemonic instructions. These instructions can be derived directly from the ladder logic diagrams and entered into the PLC through a simple programming terminal. An example of mnemonics is shown in Figure 2.6. In this example the instructions are read one line at a time from top to bottom. The first line 00000 has the instruction LDN (input load and not) for input 00001. This will examine the inputto the PLC and if it is off it will remember a 1 (or true), if it is on it will remember a 0 (or false). The next line uses an LD (input load) statement to look at the input. If the input is off it remembers a 0, if the input is on it remembers a 1 (note: this is the reverse of the LD). TheAND statement recalls the last two numbers remembered and if they are both true the result is a 1; otherwise the result is a 0. This result now replaces the two numbers that were recalled, and there is only one number remembered. The process is repeated for lines 00003 and 00004, but when these are done there are now three numbers remembered. The oldest number is from the AND, the newer numbers are from the two LD instructions. The AND in line 00005 combines the results from the last LD instructions and now there are two numbers remembered. The OR instruction takes the two numbers now remaining and if either one is a 1 the result is a 1, otherwise the result is a 0. This result replaces the two numbers, and there is now a single number there. The last instruction is the ST (store output) that will look at the last value stored and if it is 1, the output will be turned on; if it is 0 the output will be turned off.The ladder logic program in Figure 2.6, is equivalent to the mnemonic program. Even if you have programmed a PLC with ladder logic, it will be converted to mnemonic form before being used by the PLC. In the past mnemonic programming was the most common, but now it is uncommon for users to even see mnemonic programs.Sequential Function Charts (SFC) have been developed to accommodate the programming of more advanced systems. These are similar to flowcharts, but much more powerful. The example seen in Figure 2.7 is doing two different things. To read the chart, start at the top where is says start. Below this there is the double horizontal line that says follow both paths. As a result the PLC will start to follow the branch on the left and right hand sides separately and simultaneously. On the left there are two functions the first one is the power up function. This function will run until it decides it is done, and the power down function will come after. On the right hand side is the flash function; this will run until it is done. These functions look unexplained, but each function, such as power up will be a small ladder logic program. This method is much different from flowcharts because it does not have to follow a single path through the flowchart.Structured Text programming has been developed as a more modern programming language. It is quite similar to languages such as BASIC.A simple example is shown in Figure 2.8. This example uses a PLC memory location N7:0. This memory location is for an integer, as will be explained later in the book. The first line of the program sets the value to 0. The next line begins a loop, and will be where the loop returns to. The next line recalls the value in location N7:0, adds 1 to it and returns it to the same location. The next line checks to see if the loop should quit. If N7:0 is greater than or equal to 10, then the loop will quit, otherwise the computer will go back up to the REPEAT statement continue from there. Each time the program goes through this loop N7:0 will increase by 1 until the value reaches 10.N7:0 := 0;REPEATN7:0 := N7:0 + 1;UNTIL N7:0 >= 10END_REPEAT;2. PLC ConnectionsWhen a process is controlled by a PLC it uses inputs from sensors to make decisions and update outputs to drive actuators, as shown in Figure 2.9. The process is a real process that will change over time. Actuators will drive the system to new states (or modes of operation). This means that the controller is limited by the sensors available, if an input is not available, the controller will have no way to detect a condition.The control loop is a continuous cycle of the PLC reading inputs, solving the ladder logic, and then changing the outputs. Like any computer this does not happen instantly. Figure 2.10 shows the basic operation cycle of a PLC. When power is turned on initially the PLC does a quick sanity check to ensure that the hardware is working properly. If there is a problem the PLC will halt and indicate there is an error. For example, if the PLC backup battery is low and power was lost, the memory will be corrupt and this will result in a fault. If the PLC passes the sanity checks it will then scan (read) all the inputs. After the inputs values are stored in memory the ladder logic will be scanned (solved) using the stored values - not the current values. This is done to prevent logic problems when inputs change during the ladder logic scan. When the ladder logic scan is complete the outputs will be scanned (the output values will be changed). After this the system goes back to do a sanity check, and the loop continues indefinitely. Unlike normal computers, the entire program will be run every scan. Typical times for each of the stages are in the order of milliseconds.3. SUMMARY. Normally open and closed contacts.. Relays and their relationship to ladder logic.. PLC outputs can be inputs, as shown by the seal in circuit.. Programming can be done with ladder logic, mnemonics, SFC, and structured text.. There are multiple ways to write a PLC program.(注:可编辑下载,若有不当之处,请指正,谢谢!)。
PLC及变频器技术论文中英文资料对照外文翻译文献综述

PLC及变频器技术中英文资料对照外文翻译文献综述PLC and inverter technology trends1. The development trend of the programmable controller“PLC is one kind specially for the digital operation operation electronic installation which applies under the industry environment designs. It uses may the coding memory, uses for in its internal memory operation and so on actuating logic operation, sequence operation, time, counting and arithmetic operation instructions, and can through digital or the simulation-like input and the output, controls each type the machinery or the production process. PLC and the related auxiliary equipment should according to form a whole easy with the industrial control system, easy to expand its function the principle to design.”In the 21st century, PLC will have a bigger development. Technologically speaking, computer technology's new achievement more will apply in the programmable controller's design and the manufacture, will have the operating speed to be quicker, the storage capacity to be bigger, an intelligent stronger variety to appear; Looked from the product scale that further develops to subminiature and the ultra-large direction; Looked from the product overcoatability that the product variety will be richer, the specification to be more complete, the perfect man-machine contact surface, the complete communication facility will adapt each industrial control situation demand well; Looked from the market that various countries will produce the multi-variety product the situation to break respectively along with the international competition aggravating, will present the minority several brand monopoly international market the aspect, will present the international general programming language; Looking from the network state of play, the programmable controller and other industrial control computer networkconstitution large-scale control system is the programmable controller technology development direction. Present computer collection and distribution control system DCS (Distributed Control System) had the massive programmable controller application. Is following computer network's development, the programmable controller takes the automation directed net and the international universal network important component, outside industry and industry numerous domain display more and more major function.2. Inverter technology development trendsInverter into the practical phase of more than 1 / 4 century during this period, the frequency converter technology as the basis of power electronics technology and microelectronics technology manager of a leap in the development, as the new power electronic devices and high-performance microprocessor The application of control technology and the development of increasingly high cost performance of the inverter, more and more small size, but manufacturers are still in constant frequency converter to achieve the further miniaturization and doing new efforts. From a technical point of view, with the frequency converter to further expand the market of the future, with the converter and inverter technology will be on the development of technologies in the following areas further development:(1) large capacity and small size;(2) high-performance and multi-function;(3) enhance the ease-of-use;(4) increase in life expectancy and reliability;(5) of pollution-free.Large capacity and small size of the power semiconductor devices will be with the development of continuous development. In recent years, driven by a voltage power semiconductor devices IGBT (Isolated Gate Bipolar Transistor, isolation gate bipolar transistors) has developed very rapidly and quickly into the traditional use of BJT (bipolar power transistor) and power MOSFET (FET) The various fields. In addition, the IGBT switching device for the IPM (Intelligent Power Module, IPM) and Monolithic Power IC chip will power switching devices and driving circuit, such as the protection of integrated circuits in the same package, with high performance andreliability The merits, with their high current and high pressure of the development of small and medium-sized converter will certainly be more widely used.With micro-electronics technology and semiconductor technology development, for Inverter CPU and semiconductor devices and a variety of sensors of getting higher and higher. With the frequency converter technology and the development of the growing maturity of the exchange governor, modern control theory are constantly new applications. These have further improved the performance of inverter provided the conditions. In addition, with the frequency converter to further promote the use and support are also constantly made new demands, the frequency converter manufacturers to continuously improve the performance and frequency converter functions in Inverter new efforts to meet user And the need for the fierce competition in the market in an invincible position.With the frequency converter market continues to expand, how to further enhance the ease-of-use inverter, so that the technical staff and even ordinary non-technical staff can quickly master the use of frequency converter technology has become manufacturers must consider the issue. Because only easy-to-use products can continue to acquire new customers and further expand the market, so the future of the new converter will be more easy to operate.With the development of semiconductor technology and the development of power electronics technology, the frequency converter used in the various components of the life and reliability are constantly improving, they will make their own life and the frequency converter to further increase reliability.In recent years, people have attached great importance to environmental issues, and thus a "green products" name. Therefore, the inverter, must also consider its impact on the surrounding environment.Promote the use of the frequency converter in the early stages of the noise problem was once a big problem. With the low-noise converter IGBT the emergence of this issue has basically been resolved. However, with the noise problem to solve, people's looks and a converter to the surrounding environment and the impact of other continuously explore new solutions. For example, the use of a diode-voltage converter and PWMinverter circuit converter, the frequency converter itself the high harmonics will bring supply voltage and current distortion, and at the same power to affect the other equipment. However, through the use of the frequency converter Rectifier circuit PWM, we can basically solve the problem. Although because of price and control technology and other aspects of the reasons for the current PWM converter has not been promoting the inverter, but, with the frequency converter technology development and the people of the importance of environmental issues.PLC及变频器技术的发展趋势1.可编程控制器的发展趋势可编程控制器是一种数字运算操作的电子系统,专为在工业环境下应用而设计。
PLC灌装机,压盖机外文文献翻译

PLC灌装机,压盖机外文文献翻译Beer filling, Gland machine PLC control system1.IntorductionMalt beer production process is divided into manufacturing, manufacturing wort, before fermentation, after fermentation, filtration sterilization, packaging, and so few procedures. Beer filling, Gland part of a packaging machine processes. The membrane filtration of beer after the pipeline into the rotary Jiugang, then the valve into the bottle of wine, Gland, was bottled beer. Beer filling, Gland machine's efficiency and degree of automation direct impact on the level of beer production.China's beer industry to meet the increasing scale of production and the demand for beer modern high-speed filling machinery filling the requirements of domestic beer manufacturers are actively seeking to transform the unit or the filling of beer production equipment, making it a good use Performance, advanced technology and high production efficiency and operating a safe and secure, low maintenance costs of the modernization of beer filling machine.2. Filling beer, Gland principle and control aircraft partsLiquid filling machine by filling principle can be divided into atmospheric filler,filling machines and vacuum pressure on the filling machine. Beer filling,Gland-filling method used pressure is higher than the atmospheric pressure under the filling, storage of the cylinder pressure than the pressure of the bottle, beer bottle into the liquid on pressure.Technology at home and abroad to achieve the filling line is basically: The Rotary Jiugang the rotating movement, placed in Jiugangslots on the empty bottles through the machinery will be fixed at the upper Jiugang vacuum valve to open, closed Vacuum bottles for good treatment, Bozhuan stem from operating, open the valve of the bottle filling CO2 gases, vacuum convex .Round to open the vacuum valve, the bottle will air mixed with CO2 out of gas, open the valve again, the CO2 gas bottle filling, the filling valve on the pressure valve in the bottle close to back-pressure gas pressure at the open-Jiuye Pingbi into the bottle, through pneumatic or electrical control filling valve to achieve the filling of beer.Today's advanced international beer filling, Gland machine control system mainly by the photoelectric switch position detection part and take the bottles with, Jiugang speed part, dominated by the PLC, touch screen and other components. Filling, Gland of the mechanical structure and PLC programmable control devices, frequency stepless speed regulation, human-computer interface, and other modern means of complete automatic control technology, the combination of a mechanical and electrical integration.3. Controlled part of the programmeMany domestic beer manufacturers are now using the filling, Gland of the control system of uneven degree of automation; button and all the manual switch technology have set up operations in a box on the panel, PLC controller for the majority of Japanese companies or OMRON Mitsubishi's early products, equipment chain of control, less protection settings, plus the beer filling the scene poor environment, humidity, such as contact with the switch contacts serious corrosion, the system's signal detection of the high failure rate, resulting in equipment control system Operation of low reliability, the normal operationof equipment, such as short-cycle phenomenon.To the actual transformation of the Dandong Yalu River Brewery Co., Ltd. of filling, Gland machine control system as an example, the transformation of methods to clarify the control of such equipment thinking and ideas, according to the scene of the actual process conditions, to prepare the operation of the PLC Procedures. For beer filling, Gland control system of the actual situation and in accordance with the actual process conditions at the scene, re-design of the equipment of the PLC control system. This transformation of the same methods and ideas can be applied to other liquids and the transformation of filling equipment.3.1 system hardware configurationJapan's Mitsubishi Corporation to use the FX2N128MRPLC use the system to replace the original 2-OMRON's C60P PLC, the original system of the PLC is due to old models, and computer on-line communications need to configure special converters, the system need to increase the external I / O input points , The extension of spare parts more difficult to find. FX2N128MRPLC is an integrated 128-point I / O controller of the box, a computing speed, command rich, high-cost performance, on-line programming simple and easy extension of the advantages of the Mitsubishi FX series, features the strongest small controller .(1) by the Mitsubishi 900 series of 970 GOT human-computer touch screen system to replace the original use of the button panel display equipment and monitor the operation of operating parameters. 970GOT HMI for the 16-color high-brightness significantly, through the convergence of connectivity and FX2N128MRPLC directly connected to the CPU, achieving rapid response. Has many maintenance features, such as the list-editing features, ladder monitoring (troubleshooting) function, the system monitoring functions to find fault and maintenance of PLC Systems.(2) filling, Gland of the frequency converter in the transformation of no replacement, on-site detection signal means-testing is still used switch, switch for detecting long-term work in the humidity of the great occasions, the choice of capacitive proximity switches, according to PLC I / O terminal of the connection mode, select the type of close PNP switch, the control system of Figure 1.3.2Systems ProgrammingPLC controller programming focus and the core is around Jiugang the rotation speed control and Jiugang on 60 bottles of detecting the location of the displaced, broken bottles, empty bottles at the location of testing and related displacement filling Such as control valves. The bottles displacement of testing procedures, using a Mitsubishi PLC in the left command.Figure 1 control system structure diagram .Bottles displacement of detection, using the left-PLC command, which commands the whole of one of the core control procedures, the main electrical switch detection and bottles at the bottle simultaneously detect mobile, the main motor to every week, just to the corresponding Jiugang Have a bottle of, PLC unit within the internal correspondence that 60 bottles of the unit for the M500 ~ M559, the number of units by the first letter K is set to K60, with each change in a second letter K is set to K1, M50 Reaction of the empty bottles in the short position, and detect the location of the motor speed to go on the frequency shift in the corresponding unit within the built-in "1" or "0", control valves and the corresponding mixing caps The motor stoppedand opened. Continuous detection system in place after the 90 empty bottles, stop stirring caps the motor running, testing the number of bottles in accordance with the user's requirements can be arbitrary.A bottle of detection. Rotary Jiugang through pressure to back pressure with the bottle of liquor in the process of empty bottles in the back-pressure, because the bottle itself may crack and other reasons leading to a sudden burst bottles, which need to detect the location of unexploded bottle bottle, in this bottle - The position opened purge solenoid valves, compressed air out, broken bottles at the bottle-blowing from the position in a row after the purge and several bottles of the electromagnetic valve open jet, a high-pressure spray Shuizhu, in the break Bottle position around a few bottles of spray bottles in a row.Detection of broken bottles and bottle-detection switch simultaneously detect movement of breaking bottles, to the main motor of each week, precisely corresponding Jiugang passed a bottle of, PLC unit within the internal correspondence that 20 broken bottles at the unit for the M600 ~ M619, unit With the number of the first letter K is set to K20, with each change in a second letter K is set to K1, M52 response to the location of the broken bottles and detected the location of the motor speed to the frequency shift continue, In the corresponding unit within the built-in "1" or "0", control and the corresponding jet purge solenoid valve opened and stopped. Continuous Spray and purge solenoid valve open to listen, time stopped in accordance with technological requirements can be arbitrary.System security is to control access to the caps simultaneously tracking, not only accurately detect the electrical switching speed detection, the broken bottles into the bottle anddetection switch detection switch three conditions.970GOT human-computer touch-screen terminals operated by the software company's Mitsubishi GT WORKS package, which is a GT Designer with the entire GOT9000 series of graphics software packages. The packageis simple, prior to a personal computer simulation on the configuration and debug, after the man-machine operators to download terminals. At the same time, because the man-machine interface and a touch-screen role, will set common switch on the screen to facilitate the operation. And also to increase the number of features, such as setting alarm information.4After transformation control systemSystem at the normal operation of the machine for automatic control, in accordance with bottles into and out of the bottle for lack or slow pace set by running into the bottle stall bottles, no less than a bottle cap, automatic washing bottles burst, filling automatic back-pressure position , Covered under the system automatically lose covered a stop and safety protection, such as the coordination of action interlock. All the original button after the operation of the touch screen on.5Detection of the state control system monitoringDetection switch into the bottle and break bottles detection switch bottles of pressure by testing each part of the small metal plates above the location of a photoelectric pulse output, a further PLC acquisition, as each bottle of the pressure above the small metal plates is the location of activities , In the machine running after some time, some pressure above the small bottles of iron tablets and detection switch in the location of displacement, resulting in detection switch mistaken judgement,if not for the judgement of bottles of bottles, bottle explosion Lou Jian, misuse, such as the seizure of output errors So that the PLC have mistaken action, such as a back-pressure, unexploded bottle blowing, washing, stirring cap control system malfunction, such as failure phenomenon.Before the transformation of the daily production process, encountered this phenomenon, the operatives could only switch to thevarious functional or manual control buttons reach the stall so that the equipment work in the absence of monitoring state, the machine lost control function. Caused a lot of production of raw materials such as gas, water, wine waste. Only in the production of intermittent, can be fitter and maintenance electrician in accordance with the detection of small switch on the light-emitting diodes and anti-displacement by adjusting the distance only 5 ~ 8 mm detection switch installation location, and switch to fix detection of small metal plates Gap. This means of detection is very backward, after adjustment reaction to the results, timely response can not be adjusted results.In view of this testing situation, after the transformation of the filling, Gland control system configuration, this part of a new detection and integration in human-computer touch screen, complete bottle of detection.In human-computer touch screen interface on the page display, respectively, at customs, such as electromagnetic motor mixing valve switch state are in different colors to show, very intuitive.Increase the system's functions is to ensure the irrigation of the machine-Gland normal operation of automated control system specifically designed to.6 Concluding remarksAfter the transformation of the control system will greatly simplify the complicated mechanical structure, the running and control of inspection, the degree of automation systems meet the design requirements, greatly reducing the operational strength of the labor so that the shrub-like beer output than in the past Raising more than 30 percent, greatly reduce the failure rate. Embodies the modern equipment of。
(完整版)PLC英文文献+翻译

自动化专业本科毕业设计英文翻译学院(部):专业班级:学生姓名:指导教师:年月日Programmable Logic ControllerONE:PLC overviewProgrammable controller is the first in the late 1960s in the United States, then called PLC programmable logic controller (Programmable Logic Controller) is used to replace relays. For the implementation of the logical judgment, timing, sequence number, and other control functions. The concept is presented PLC General Motors Corporation. PLC and the basic design is the computer functional improvements, flexible, generic and other advantages and relay control system simple and easy to operate, such as the advantages of cheap prices combined controller hardware is standard and overall. According to the practical application of target software in order to control the content of the user procedures memory controller, the controller and connecting the accused convenient target.In the mid-1970s, the PLC has been widely used as a central processing unit microprocessor, import export module and the external circuits are used, large-scale integrated circuits even when the Plc is no longer the only logical (IC) judgment functions also have data processing, PID conditioning and data communications functions. International Electro technical Commission (IEC) standards promulgated programmable controller for programmable controller draft made the following definition : programmable controller is a digital electronic computers operating system, specifically for applications in the industrial design environment. It used programmable memory, used to implement logic in their internal storage operations, sequence control, timing, counting and arithmetic operations, such as operating instructions, and through digital and analog input and output, the control of various types of machinery or production processes. Programmable controller and related peripherals, and industrial control systems easily linked to form a whole, to expand its functional design. Programmable controller for the user, is a non-contact equipment, the procedures can be changed to change production processes. The programmable controller has become a powerful tool for factory automation, widely popular replication.Programmable controller is user-oriented industries dedicated control computer, with many distinctive features.First, high reliability, anti-interference capability;Second,programming visual, simple;Third, adaptability good;Fourth functional improvements, strong functional interface. TWO:History of PLCProgrammable Logic Controllers (PLC), a computing device invented by Richard E. Morley in 1968, have been widely used in industry including manufacturing systems, transportation systems, chemical process facilities, and many others. At that time, the PLC replaced the hardwired logic with soft-wired logic or so-called relay ladder logic (RLL), a programming language visually resembling the hardwired logic, and reduced thereby the configuration time from 6 months down to 6 days [Moody and Morley, 1999].Although PC based control has started to come into place, PLC based control will remain the technique to which the majority of industrial applications will adhere due to its higher performance, lower price, and superior reliability in harsh environments. Moreover, according to a study on the PLC market of Frost and Sullivan [1995], an increase of the annual sales volume to 15 million PLC per year with the hardware value of more than 8 billion US dollars has been predicted, though the prices of computing hardware is steadily dropping. The inventor of the PLC, Richard E Morley, fairly considers the PLC market as a 5-billion industry at the present time.Though PLCs are widely used in industrial practice, the programming of PLC based control systems is still very much relying on trial-and-error. Alike software engineering, PLC software design is facing the software dilemma or crisis in a similar way. Morley himself emphasized this aspect most forcefully by indicatingIf houses were built like software projects, a single woodpecker could d estroy civilization.”Particularly, practical problems in PLC programming are to eliminate software bugs and to reduce the maintenance costs of old ladderlogic programs. Though the hardware costs of PLC are dropping continuously, reducing the scan time of the ladder logic is still an issue in industry so that low-cost PLC can be used.In general, the productivity in generating PLC is far behind compared to other domains, for instance, VLSI design, where efficient computer aided design tools are in practice. Existent software engineering methodologies are not necessarily applicable to the PLC based software design because PLC-programming requires a simultaneous consideration of hardware and software. The software design becomes, thereby, more and more the major cost driver. In many industrial design projects, more than of the manpower allocated for the control system design and installation is scheduled for testing and debugging PLC programs.In addition, current PLC based control systems are not properly designed to support the growing demand for flexibility and reconfigurability of manufacturing systems. A further problem, impelling the need for a systematic design methodology, is the increasing software complexity in large-scale projects.The objective of this thesis is to develop a systematic software design methodology for PLC operated automation systems. The design methodology involves high-level description based on state transition models that treat automation control systems as discrete event systems, a stepwise design process, and set of design rules providing guidance and measurements to achieve a successful design. The tangible outcome of this research is to find a way to reduce the uncertainty in managing the control software development process, that is, reducing programming and debugging time and their variation, increasing flexibility of the automation systems, and enabling software reusability through modularity. The goal is to overcome shortcomings of current programming strategies that are based on the experience of the individual software developer. Three:now of PLCFrom the structure is divided into fixed PLC and Module PLC, the two kinds of PLC including CPU board, I/O board, display panel, memory block, power, these elements into a do not remove overall. Module type PLC including CPU module, I/O modules, memory, thepower modules, bottom or a frame, these modules can be according to certain rules combination configuration.In the user view, a detailed analysis of the CPU's internal unnecessary, but working mechanism of every part of the circuit. The CPU control works, by it reads CPU instruction, interprets the instruction and executes instructions. But the pace of work by shock signal control.Unit work under the controller command used in a digital or logic operations.In computing and storage register of computation result, it is also among the controller command and work. CPU speed and memory capacity is the important parameters fot PLC . its determines the PLC speed of work, IO PLC number and software capacity, so limits to control size.Central Processing Unit (CPU) is the brain of a PLC controller. CPU itself is usually one of the microcontrollers. Aforetime these were 8-bit microcontrollers such as 8051, and now these are 16-and 32-bit microcontrollers. Unspoken rule is that you’ll find mostly Hitachi and Fujicu microcontrollers in PLC controllers by Japanese makers, Siemens in European controllers, and Motorola microcontrollers in American ones. CPU also takes care of communication, interconnectedness among other parts of PLC controllers, program execution, memory operation, overseeing input and setting up of an output.System memory (today mostly implemented in FLASH technology) is used by a PLC for a process control system. Aside form. this operating system it also contains a user program translated foram ladder diagram to a binary form. FLASH memory contents can be changed only in case where user program is being changed. PLC controllers were used earlier instead of PLASH memory and have had EPROM memory instead of FLASH memory which had to be erased with UV lamp and programmed on programmers. With the use of FLASH technology this process was greatly shortened. Reprogramming a program memory is done through a serial cable in a program for application development.User memory is divided into blocks having special functions. Some parts of a memory are used for storing input and output status. The real status of an input is stored either as “1”or as “0”in a specific memory bit/each input or output has one corresponding bit in memory. Other parts of memory are used to store variable contents for variables used in used program. For example, time value, or counter value would be stored in this part of the memory.PLC controller can be reprogrammed through a computer (usual way), but also through manual programmers (consoles). This practically means that each PLC controller can programmed through a computer if you have the software needed for programming. Today’s transmission computers are ideal for reprogramming a PLC controller in factory itself. This is of great importance to industry. Once the system is corrected, it is also important to read the right program into a PLC again. It is also good to check from time to time whether program in a PLC has not changed. This helps to avoid hazardous situations in factory rooms (some automakers have established communication networks which regularly check programs in PLC controllers to ensure execution only of good programs).Almost every program for programming a PLC controller possesses various useful options such as: forced switching on and off of the system input/outputs (I/O lines), program follow up in real time as well as documenting a diagram. This documenting is necessary to understand and define failures and malfunctions. Programmer can add remarks, names of input or output devices, and comments that can be useful when finding errors, or with system maintenance. Adding comments and remarks enables any technician (and not just a person who developed the system) to understand a ladder diagram right away. Comments and remarks can even quote precisely part numbers if replacements would be needed. This would speed up a repair of any problems that come up due to bad parts. The old way was such that a person who developed a system had protection on the program, so nobody aside from this person could understand how it was done. Correctly documented ladder diagram allows any technician to understand thoroughly how system functions.Electrical supply is used in bringing electrical energy to central processing unit. Most PLC controllers work either at 24 VDC or 220V AC. On some PLC controllers you’ll find electrical supply as a separatemodule. Those are usually bigger PLC controllers, while small and medium series already contain the supply module. User has to determine how much current to take from I/O module to ensure that electrical supply provides appropriate amount of current. Different types of modules use different amounts of electrical current.This electrical supply is usually not used to start external input or output. User has to provide separate supplies in starting PLC controller inputs because then you can ensure so called “pure” supply for the PLC controller. With pure supply we mean supply where industrial environment can not affect it damagingly. Some of the smaller PLC controllers supply their inputs with voltage from a small supply source already incorporated into a PLC.Four:PLC design criteriaA systematic approach to designing PLC software can overcome deficiencies in the traditional way of programming manufacturing control systems, and can have wide ramifications in several industrial applications. Automation control systems are modeled by formal languages or, equivalently, by state machines. Formal representations provide a high-level description of the behavior of the system to be controlled. State machines can be analytically evaluated as to whether or not they meet the desired goals. Secondly, a state machine description provides a structured representation to convey the logical requirements and constraints such as detailed safety rules. Thirdly, well-defined control systems design outcomes are conducive to automatic code generation- An ability to produce control software executable on commercial distinct logic controllers can reduce programming lead-time and labor cost. In particular, the thesis is relevant with respect to the following aspects.In modern manufacturing, systems are characterized by product and process innovation, become customer-driven and thus have to respond quickly to changing system requirements. A major challenge is therefore to provide enabling technologies that can economically reconfigure automation control systems in response to changing needs and new opportunities. Design and operational knowledge can be reused inreal-time, therefore, giving a significant competitive edge in industrial practice.Studies have shown that programming methodologies in automation systems have not been able to match rapid increase in use of computing resources. For instance, the programming of PLC still relies on a conventional programming style with ladder logic diagrams. As a result, the delays and resources in programming are a major stumbling stone for the progress of manufacturing industry. Testing and debugging may consume over 50% of the manpower allocated for the PLC program design. Standards [IEC 60848, 1999; IEC-61131-3, 1993; IEC 61499, 1998; ISO 15745-1, 1999] have been formed to fix and disseminate state-of-the-art design methods, but they normally cannot participate in advancing the knowledge of efficient program and system design.A systematic approach will increase the level of design automation through reusing existing software components, and will provide methods to make large-scale system design manageable. Likewise, it will improve software quality and reliability and will be relevant to systems high security standards, especially those having hazardous impact on the environment such as airport control, and public railroads.The software industry is regarded as a performance destructor and complexity generator. Steadily shrinking hardware prices spoils the need for software performance in terms of code optimization and efficiency. The result is that massive and less efficient software code on one hand outpaces the gains in hardware performance on the other hand. Secondly, software proliferates into complexity of unmanageable dimensions; software redesign and maintenance-essential in modern automation systems-becomes nearly impossible. Particularly, PLC programs have evolved from a couple lines of code 25 years ago to thousands of lines of code with a similar number of 1/O points. Increased safety, for instance new policies on fire protection, and the flexibility of modern automation systems add complexity to the program design process. Consequently, the life-cycle cost of software is a permanently growing fraction of the total cost. 80-90% of these costs are going into software maintenance, debugging, adaptation and expansion to meet changing needs.Today, the primary focus of most design research is based on mechanical or electrical products. One of the by-products of this proposed research is to enhance our fundamental understanding of design theory and methodology by extending it to the field of engineering systems design. A system design theory for large-scale and complex system is not yet fully developed. Particularly, the question of how to simplify a complicated or complex design task has not been tackled in a scientific way. Furthermore, building a bridge between design theory and the latest epistemological outcomes of formal representations in computer sciences and operations research, such as discrete event system modeling, can advance future development in engineering design.From a logical perspective, PLC software design is similar to the hardware design of integrated circuits. Modern VLSI designs are extremely complex with several million parts and a product development time of 3 years [Whitney, 1996]. The design process is normally separated into a component design and a system design stage. At component design stage, single functions are designed and verified. At system design stage, components are aggregated and the whole system behavior and functionality is tested through simulation. In general, a complete verification is impossible. Hence, a systematic approach as exemplified for the PLC program design may impact the logical hardware design.可编程控制器一、PLC概述可编程控制器是60年代末在美国首先出现的,当时叫可编程逻辑控制器PLC(Programmable Logic Controller),目的是用来取代继电器。
plc英文文献

1. CONVEYOR SYSTEMS Conveyor systems are often modular in nature and can be built up from basic units (or primitives) such as linear conveyor modules, either belt or roller type, and connecting devices such as lift stations and conveyor junction modules. Complex conveyor systems can easily be configured from combinations of these standard modules. Modules are available from a range of vendors in a wide portfolio of styles and varieties [1]. Conventional conveyor systems are typically installed as simple straight assembly lines and a number of workplaces are set on each side of the conveyor for manual and/or automated operations. For simple configurations of this type, the design and implementation is a relatively trivial task. Control programs are easily designed and coded using conventional Ladder Logic Diagrams (LLDs) which can be executed by Programmable Logic Controllers (PLCs) [2]. However, today's demands for multi-product mixes and flexibility for quick system reconfiguration can require more complex conveyor systems. Traditional types of sequentially controlled conveyor installations are often found to be too rigid for such demanding operational requirements. Conveyor systems which support multiple product mixes and variable product 799
PLC灌装机 ,压盖机外文文献翻译
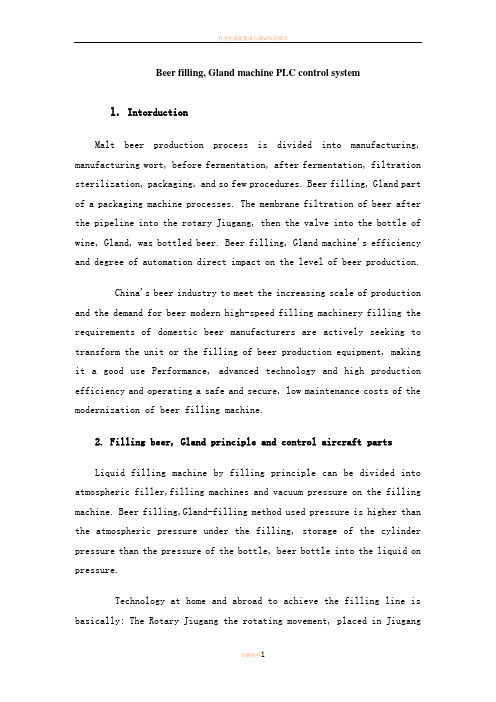
Beer filling, Gland machine PLC control system1.IntorductionMalt beer production process is divided into manufacturing, manufacturing wort, before fermentation, after fermentation, filtration sterilization, packaging, and so few procedures. Beer filling, Gland part of a packaging machine processes. The membrane filtration of beer after the pipeline into the rotary Jiugang, then the valve into the bottle of wine, Gland, was bottled beer. Beer filling, Gland machine's efficiency and degree of automation direct impact on the level of beer production.China's beer industry to meet the increasing scale of production and the demand for beer modern high-speed filling machinery filling the requirements of domestic beer manufacturers are actively seeking to transform the unit or the filling of beer production equipment, making it a good use Performance, advanced technology and high production efficiency and operating a safe and secure, low maintenance costs of the modernization of beer filling machine.2. Filling beer, Gland principle and control aircraft partsLiquid filling machine by filling principle can be divided into atmospheric filler,filling machines and vacuum pressure on the filling machine. Beer filling,Gland-filling method used pressure is higher than the atmospheric pressure under the filling, storage of the cylinder pressure than the pressure of the bottle, beer bottle into the liquid on pressure.Technology at home and abroad to achieve the filling line is basically: The Rotary Jiugang the rotating movement, placed in Jiugangslots on the empty bottles through the machinery will be fixed at the upper Jiugang vacuum valve to open, closed Vacuum bottles for good treatment, Bozhuan stem from operating, open the valve of the bottle filling CO2 gases, vacuum convex .Round to open the vacuum valve, the bottle will air mixed with CO2 out of gas, open the valve again, the CO2 gas bottle filling, the filling valve on the pressure valve in the bottle close to back-pressure gas pressure at the open-Jiuye Pingbi into the bottle, through pneumatic or electrical control filling valve to achieve the filling of beer.Today's advanced international beer filling, Gland machine control system mainly by the photoelectric switch position detection part and take the bottles with, Jiugang speed part, dominated by the PLC, touch screen and other components. Filling, Gland of the mechanical structure and PLC programmable control devices, frequency stepless speed regulation, human-computer interface, and other modern means of complete automatic control technology, the combination of a mechanical and electrical integration.3. Controlled part of the programmeMany domestic beer manufacturers are now using the filling, Gland of the control system of uneven degree of automation; button and all the manual switch technology have set up operations in a box on the panel, PLC controller for the majority of Japanese companies or OMRON Mitsubishi's early products, equipment chain of control, less protection settings, plus the beer filling the scene poor environment, humidity, such as contact with the switch contacts serious corrosion, the system's signal detection of the high failure rate, resulting in equipment control system Operation of low reliability, the normal operation of equipment, such as short-cycle phenomenon.To the actual transformation of the Dandong Yalu River Brewery Co., Ltd. of filling, Gland machine control system as an example, the transformation of methods to clarify the control of such equipment thinking and ideas, according to the scene of the actual process conditions, to prepare the operation of the PLC Procedures. For beer filling, Gland control system of the actual situation and in accordance with the actual process conditions at the scene, re-design of the equipment of the PLC control system. This transformation of the same methods and ideas can be applied to other liquids and the transformation of filling equipment.3.1 system hardware configurationJapan's Mitsubishi Corporation to use the FX2N128MRPLC use the system to replace the original 2-OMRON's C60P PLC, the original system of the PLC is due to old models, and computer on-line communications need to configure special converters, the system need to increase the external I / O input points , The extension of spare parts more difficult to find. FX2N128MRPLC is an integrated 128-point I / O controller of the box, a computing speed, command rich, high-cost performance, on-line programming simple and easy extension of the advantages of the Mitsubishi FX series, features the strongest small controller .(1) by the Mitsubishi 900 series of 970 GOT human-computer touch screen system to replace the original use of the button panel display equipment and monitor the operation of operating parameters. 970GOT HMI for the 16-color high-brightness significantly, through the convergence of connectivity and FX2N128MRPLC directly connected to the CPU, achieving rapid response. Has many maintenance features, such as the list-editing features, ladder monitoring (troubleshooting) function, the system monitoring functions to find fault and maintenance of PLC Systems.(2) filling, Gland of the frequency converter in the transformation of no replacement, on-site detection signal means-testing is still used switch, switch for detecting long-term work in the humidity of the great occasions, the choice of capacitive proximity switches, according to PLC I / O terminal of the connection mode, select the type of close PNP switch, the control system of Figure 1.3.2Systems ProgrammingPLC controller programming focus and the core is around Jiugang the rotation speed control and Jiugang on 60 bottles of detecting the location of the displaced, broken bottles, empty bottles at the location of testing and related displacement filling Such as control valves. The bottles displacement of testing procedures, using a Mitsubishi PLC in the left command.Figure 1 control system structure diagram .Bottles displacement of detection, using the left-PLC command, which commands the whole of one of the core control procedures, the main electrical switch detection and bottles at the bottle simultaneously detect mobile, the main motor to every week, just to the corresponding Jiugang Have a bottle of, PLC unit within the internal correspondence that 60 bottles of the unit for the M500 ~ M559, the number of units by the first letter K is set to K60, with each change in a second letter K is set to K1, M50 Reaction of the empty bottles in the short position, and detect the location of the motor speed to go on the frequency shift in the corresponding unit within the built-in "1" or "0", control valves and the corresponding mixing caps The motor stopped and opened. Continuous detection system in place after the 90 empty bottles, stop stirring caps the motor running, testing the number of bottles in accordance with the user's requirements can be arbitrary.A bottle of detection. Rotary Jiugang through pressure to back pressure with the bottle of liquor in the process of empty bottles in the back-pressure, because the bottle itself may crack and other reasons leading to a sudden burst bottles, which need to detect the location of unexploded bottle bottle, in this bottle - The position opened purge solenoid valves, compressed air out, broken bottles at the bottle-blowing from the position in a row after the purge and several bottles of the electromagnetic valve open jet, a high-pressure spray Shuizhu, in the break Bottle position around a few bottles of spray bottles in a row.Detection of broken bottles and bottle-detection switch simultaneously detect movement of breaking bottles, to the main motor of each week, precisely corresponding Jiugang passed a bottle of, PLC unit within the internal correspondence that 20 broken bottles at the unit for the M600 ~ M619, unit With the number of the first letter K is set to K20, with each change in a second letter K is set to K1, M52 response to the location of the broken bottles and detected the location of the motor speed to the frequency shift continue, In the corresponding unit within the built-in "1" or "0", control and the corresponding jet purge solenoid valve opened and stopped. Continuous Spray and purge solenoid valve open to listen, time stopped in accordance with technological requirements can be arbitrary.System security is to control access to the caps simultaneously tracking, not only accurately detect the electrical switching speed detection, the broken bottles into the bottle and detection switch detection switch three conditions.970GOT human-computer touch-screen terminals operated by the software company's Mitsubishi GT WORKS package, which is a GT Designer with the entire GOT9000 series of graphics software packages. The packageis simple, prior to a personal computer simulation on the configuration and debug, after the man-machine operators to download terminals. At the same time, because the man-machine interface and a touch-screen role, will set common switch on the screen to facilitate the operation. And also to increase the number of features, such as setting alarm information.4After transformation control systemSystem at the normal operation of the machine for automatic control, in accordance with bottles into and out of the bottle for lack or slow pace set by running into the bottle stall bottles, no less than a bottle cap, automatic washing bottles burst, filling automatic back-pressure position , Covered under the system automatically lose covered a stop and safety protection, such as the coordination of action interlock. All the original button after the operation of the touch screen on.5Detection of the state control system monitoringDetection switch into the bottle and break bottles detection switch bottles of pressure by testing each part of the small metal plates above the location of a photoelectric pulse output, a further PLC acquisition, as each bottle of the pressure above the small metal plates is the location of activities , In the machine running after some time, some pressure above the small bottles of iron tablets and detection switch in the location of displacement, resulting in detection switch mistaken judgement, if not for the judgement of bottles of bottles, bottle explosion Lou Jian, misuse, such as the seizure of output errors So that the PLC have mistaken action, such as a back-pressure, unexploded bottle blowing, washing, stirring cap control system malfunction, such as failure phenomenon.Before the transformation of the daily production process, encountered this phenomenon, the operatives could only switch to thevarious functional or manual control buttons reach the stall so that the equipment work in the absence of monitoring state, the machine lost control function. Caused a lot of production of raw materials such as gas, water, wine waste. Only in the production of intermittent, can be fitter and maintenance electrician in accordance with the detection of small switch on the light-emitting diodes and anti-displacement by adjusting the distance only 5 ~ 8 mm detection switch installation location, and switch to fix detection of small metal plates Gap. This means of detection is very backward, after adjustment reaction to the results, timely response can not be adjusted results.In view of this testing situation, after the transformation of the filling, Gland control system configuration, this part of a new detection and integration in human-computer touch screen, complete bottle of detection.In human-computer touch screen interface on the page display, respectively, at customs, such as electromagnetic motor mixing valve switch state are in different colors to show, very intuitive.Increase the system's functions is to ensure the irrigation of the machine-Gland normal operation of automated control system specifically designed to.6 Concluding remarksAfter the transformation of the control system will greatly simplify the complicated mechanical structure, the running and control of inspection, the degree of automation systems meet the design requirements, greatly reducing the operational strength of the labor so that the shrub-like beer output than in the past Raising more than 30 percent, greatly reduce the failure rate. Embodies the modern equipment ofautomatic control technology. In the digestion and absorption of today's industrial control on the basis of advanced technology innovation, development of domestic technology from the most advanced filling control system.啤酒灌装、压盖机PLC控制系统1. 引言啤酒生产过程分为麦芽制造、麦芽汁制造、前发酵、后发酵、过滤灭菌、包装等几道工序。
PLC中英文对照外文翻译文献

中英文对照翻译外文资料:PLC technique discussion and future developmentAlong with the development of the ages, the technique that is nowadays is also gradually perfect, the competition plays more more strong; the operation that list depends the artificial has already can't satisfied with the current manufacturing industry foreground, also can't guarantee the request of the higher quantity and high new the image of the technique business enterprise.The people see in produce practice, automate brought the tremendous convenience and the product quantities for people up of assurance, also eased the personnel's labor strength, reduce the establishment on the personnel. The target control of the hard realization in many complicated production lines, whole and excellent turn, the best decision etc., well-trained operation work, technical personnel or expert, governor but can judge and operate easily, can acquire the satisfied result. The research target of the artificial intelligence makes use of the calculator exactly to carry out, imitate these intelligences behavior, moderating the work through person's brain and calculators, with the mode that person's machine combine, for resolve the very complicated problem to look for the best pathWe come in sight of the control that links after the electric appliances in various situation, that is already the that time generation past, now of after use in the mold a perhaps simple equipments of grass-roots control that the electric appliances can do for the low level only;And the PLC emergence also became the epoch-making topic, adding the vivid software control through a very and stable hardware, making the automation head for the new high tide.The PLC biggest characteristics lie in: The electrical engineering teacher already no longer electric hardware up too many calculationses of cost, as long as order the importation that the button switch or the importation of the sensors order to link the PLC up can solve problem, pass to output to order the conjunction contact machine or control the start equipments of thebig power after the electric appliances, but the exportation equipments direct conjunction of the small power can.PLC internal containment have the CPU of the CPU, and take to have an I/ O for expand of exterior to connect a people's address and saving machine three big pieces to constitute, CPU core is from an or many is tired to add the machine to constitute, mathematics that they have the logic operation ability, and can read the procedure save the contents of the machine to drive the homologous saving machine and I/ Os to connect after pass the calculation; The I/ O add inner part is tired the input and output system of the machine and exterior link, and deposit the related data into the procedure saving machine or data saving machine; The saving machine can deposit the data that the I/ O input in the saving machine, and in work adjusting to become tired to add the machine and I/ Os to connect, saving machine separately saving machine RAM of the procedure saving machine ROM and datas, the ROM can can do deposit of the data permanence in the saving machine, but RAM only for the CPU computes the temporary calculation usage of hour of buffer space.The PLC anti- interference is very and excellent, our root need not concern its service life and the work situation bad, these all problems have already no longer become the topic that we fail, but stay to our is a concern to come to internal resources of make use of the PLC to strengthen the control ability of the equipments for us, make our equipments more gentle. PLC language is not we imagine of edit collected materials the language or language of Cs to carry on weaving the distance, but the trapezoid diagram that the adoption is original after the electric appliances to control, make the electrical engineering teacher while weaving to write the procedure very easy comprehended the PLC language, and a lot of non- electricity professional also very quickly know and go deep into to the PLC.Is PLC one of the advantage above and only, this is also one part that the people comprehend more and easily, in a lot of equipmentses, the people have already no longer hoped to see too many control buttons, they damage not only and easily and produce the artificial error easiest, small is not a main error perhaps you can still accept; But lead even is a fatal error greatly is what we can't is tolerant of. New technique always for bringing more safe and convenient operation for us, make we a lot of problems for face on sweep but light, do you understand the HMI? Says the HMI here you basically not clear what it is, also have no interest understanding, change one inside text explains it into the touch to hold or man-machine interface you knew, it combines with the PLC to our larger space.HMI the control not only only is reduced the control press button, increase the vivid of the control, more main of it is can sequence of, and at can the change data input to output thefeedback with data, control in the temperature curve of imitate but also can keep the manifestation of view to come out. And can write the function help procedure through a plait to provide the help of various what lies in one's power, the one who make operate reduces the otiose error. Currently the HMI factory is also more and more, the function is also more and more strong, the price is also more and more low, the noodles of the usage are wide more and more. The HMI foreground can say that think ° to be good very.At a lot of situations, the list is is a smooth movement that can't guarantee the equipments by the control of the single machine, but pass the information exchanges of the equipments and equipments to attain the result that we want. For example fore pack and the examination of the empress work preface, we will arrive wrapping information feedback to examine the place, and examine the information of the place to also want the feedback to packing. Pass the information share thus to make both the chain connect, becoming a total body, the match of your that thus make is more close, at each other attain to reflect the result that mutually flick. The PLC correspondence has already come more more body now its value, at the PLC and correspondence between PLCs, can pass the communication of the information and the share of the datas to guarantee that of the equipments moderates mutually, the result that arrive already to repair with each other. Data conversion the adoption RS232 between PLC connect to come to the transmission data, but the RS232 pick up a people and can guarantee 10 meters only of deliver the distance, if in the distance of 1000 meters we can pass the RS485 to carry on the correspondence, the longer distance can pass the MODEL only to carry on deliver. The PLC data transmission is just to be called a form to it in a piece of and continuous address that the data of the inner part delivers the other party, we, the PLC of the other party passes to read data in the watch to carry on the operation. If the data that data in the watch is a to establish generally, that is just the general data transmission, for example today of oil price rise, I want to deliver the price of the oil price to lose the oil ally on board, that is the share of the data; But take data in the watch for an instruction procedure that controls the PLC, that had the difficulty very much, for example you have to control one pedestal robot to press the action work that you imagine, you will draw up for it the form that a procedure combine with the data sends out to pass by.The form that information transport contain single work, the half a work and the difference of a workses .The meaning of the single work also is to say both, a can send out only, but a can receive only, for example a spy he can receive the designation of the superior only, but can't give the superior reply; A work of half is also 2 and can can send out similar to accept the data, but can't send out and accept at the same time, for example when you make a phonecall is to can't answer the phone, the other party also; But whole pair works is both can send out and accept the data, and can send out and accept at the same time. Be like the Internet is a typical example.The process that information transport also has synchronous and different step cent: The data line and the clock lines are synchronous when synchronous meaning lie in sending out the data, is also the data signal and the clock signals to be carry on by the CPU to send out at the same time, this needs to all want the specialized clock signal each other to carry on the transmission and connect to send, and is constrained, the characteristics of this kind of method lies in its speed very quick, but correspond work time of take up the CPU and also want to be long oppositely, at the same time the technique difficulty also very big. Its request lies in can'ting have an error margins in a datas deliver, otherwise the whole piece according to compare the occurrence mistake, this on the hardware is a bigger difficulty. Applied more and more extensive in some appropriative equipmentses, be like the appropriative medical treatment equipments, the numerical signal equipments...etc., in compare the one data deliver, its result is very good.And the different step is an application the most extensive, this receive benefit in it of technique difficulty is opposite and want to be small, at the same time not need to prepare the specialized clock signal, its characteristics to lie in, its data is partition, the long-lost send out and accept, be the CPU is too busy of time can grind to a stop sex to work, also reduced the difficulty on the hardware, the data throw to lose at the same time opposite want to be little, we can pass the examination of the data to observe whether the data that we send out has the mistake or not, be like strange accidentally the method, tired addition and eight efficacies method etc., can use to helps whether the data that we examine to send out have or not the mistake occurrence, pass the feedback to carry on the discriminator.A line of transmission of the information contain a string of and combine the cent of: The usual PLC is 8 machines, certainly also having 16 machines. We can be an at the time of sending out the data a send out to the other party, also can be 88 send out the data to the other party, an and 8 differentiationses are also the as that we say to send out the data and combine sends out the data. A speed is more and slowly, but as long as 2 or three lines can solve problem, and can use the telephone line to carry on the long range control. But combine the oscular transmission speed is very quick of, it is a string of oscular of 25600%, occupy the advantage in the short distance, the in view of the fact TTL electricity is even, being limited by the scope of one meter generally, it combine unwell used for the data transmission of the long pull, thus the cost is too expensive.Under a lot of circumstances we are total to like to adopt the string to combine the conversion chip to carry on deliver, under this kind of circumstance not need us to carry on to depositted the machine to establish too and complicatedly, but carry on the data exchanges through the data transmission instruction directly, but is not a very viable way in the correspondence, because the PLC of the other party must has been wait for your data exportation at the time of sending out the data, it can't do other works.When you are reading the book, you hear someone knock on door, you stop to start up of affair, open the door and combine to continue with the one who knock on door a dialogue, the telephone of this time rang, you signal hint to connect a telephone, after connecting the telephone through, return overdo come together knock on door to have a conversation, after dialogue complete, you continue again to see your book, this kind of circumstance we are called the interruption to it, it has the authority, also having sex of have the initiative, the PLC had such function .Its characteristics lie in us and may meet the urgently abrupt affairs in the operation process of the equipments, we want to stop to start immediately up of work, the whereabouts manages the more important affair, this kind of circumstance is we usually meet of, PLC while carry out urgent mission, total will keep the current appearance first, for example the address of the procedure, CPU of tired add the machine data etc., be like to to stick down which the book that we see is when we open the door the page or simply make a mark, because we treat and would still need to continue immediately after book of see the behind. The CPU always does the affair that should do according to our will, but your mistake of give it an affair, it also would be same to do, this we must notice.The interruption is not only a, sometimes existing jointly with the hour several inside break, break off to have the preferred Class, they will carry out the interruption of the higher Class according to person's request. This kind of breaks off the medium interruption to also became to break off the set. The Class that certainly break off is relevant according to various resources of CPU with internal PLC, also following a heap of capacity size of also relevant fasten.The contents that break off has a lot of kinds, for example the exterior break off, correspondence in of send out and accept the interruption and settle and the clock that count break off, still have the WDT to reset the interruption etc., they enriched the CPU to respond to the category while handle various business. Speak thus perhaps you can't comprehend the internal structure and operation orders of the interruption completely also, we do a very small example to explain.Each equipments always will not forget a button, it also is at we meet the urgent circumstance use of, that is nasty to stop the button. When we meet the Human body trouble and surprised circumstances we as long as press it, the machine stops all operations immediately, and wait for processing the over surprised empress recover the operation again.Nasty stop the internal I/ O of the internal CPU of the button conjunction PLC to connect up, be to press button an exterior to trigger signal for CPU, the CPU carries on to the I/ O to examine again, being to confirm to have the exterior to trigger the signal, CPU protection the spot breaks off procedure counts the machine turn the homologous exterior I/ O automatically in the procedure to go to also, be exterior interruption procedure processing complete, the procedure counts the machine to return the main procedure to continue to work.Have 1:00 can what to explain is we generally would nasty stop the button of exterior break off to rise to the tallest Class, thus guarantee the safety.When we are work a work piece, giving the PLC a signal, counting PLC inner part the machine add 1 to compute us for a day of workload, a count the machine and can solve problem in brief, certainly they also can keep the data under the condition of dropping the electricity, urging the data not to throw to lose, this is also what we hope earnestly.The PLC still has the function that the high class counts the machine, being us while accept some datas of high speed, the high speed that here say is the data of the in all aspects tiny second class, for example the bar code scanner is scanning the data continuously, calculating high-speed signal of the data processor DSP etc., we will adopt the high class to count the machine to help we carry on count. It at the PLC carries out the procedure once discover that the high class counts the machine to should of interruption, will let go of the work on the hand immediately. The trapezoid diagram procedure that passes by to weave the distance again explains the high class for us to carry out procedure to count machine would automatic performance to should of work, thus rise the Class that the high class counts the machine to high one Class.You heard too many this phrases perhaps:" crash", the meaning that is mostly is a workload of CPU to lead greatly, the internal resources shortage etc. the circumstance can't result in procedure circulate. The PLC also has the similar circumstance, there is a watchdog WDT in the inner part of PLC, we can establish time that a procedure of WDT circulate, being to appear the procedure to jump to turn the mistake in the procedure movement process or the procedure is busy, movement time of the procedure exceeds WDT constitution time, the CPU turn but the WDT reset the appearance. The procedure restarts the movement, but will not carry on the breakage to the interruption.The PLC development has already entered for network ages of correspondence from the mode of the one, and together other works control the net plank and I/ O card planks to carry on the share easily. A state software can pass all se hardwares link, more animation picture of keep the view to carries on the control, and cans pass the Internet to carry on the control in the foreign land, the blast-off that is like the absolute being boat No.5 is to adopt this kind of way to make airship go up the sky.The development of the higher layer needs our continuous effort to obtain.The PLC emergence has already affected a few persons fully, we also obtained more knowledge and precepts from the top one experience of the generation, coming to the continuous development PLC technique, push it toward higher wave tide.中文翻译:可编程控制器技术讨论与未来发展随着时代的发展,当今的技术也日趋完善、竞争愈演愈烈,单靠人工的操作已不能满足于目前的制造业前景,也无法保证更高质量的要求和高新技术企业的形象。
PLC-外文文献+翻译

Programmable logic controllerA programmable logic controller (PLC) or programmable controller is a digital computer used for automation of electromechanical processes, such as control of machinery on factory assembly lines, amusement rides, or lighting fixtures. PLCs are used in many industries and machines。
Unlike general—purpose computers,the PLC is designed for multiple inputs and output arrangements, extended temperature ranges, immunity to electrical noise, and resistance to vibration and impact. Programs to control machine operation are typically stored in battery—backed or non-volatile memory. A PLC is an example of a real time system since output results must be produced in response to input conditions within a bounded time, otherwise unintended operation will result。
1。
HistoryThe PLC was invented in response to the needs of the American automotive manufacturing industry。
外文翻译-关于PLC的外文及翻译

PLCs --Past, Present and FutureEveryone knows there's only one constant in the technology world, and that's change. This is especially evident in the evolution of Programmable Logic Controllers (PLC) and their varied applications. From their introduction more than 30 years ago, PLCs have become the cornerstone of hundreds of thousands of control systems in a wide range of industries.At heart, the PLC is an industrialized computer programmed with highly specialized languages, and it continues to benefit from technological advances in the computer and information technology worlds. The most prominent of which is miniaturization and communications.The Shrinking PLCWhen the PLC was first introduced, its size was a major improvement - relative to the hundreds of hard-wired relays and timers it replaced. A typical unit housing a CPU and I/O was roughly the size of a 19 television set. Through the 1980s and early 1990s, modular PLCs continued to shrink in footprint while increasing in capabilities and performance (see Diagram 1 for typical modular PLC configuration).In recent years, smaller PLCs have been introduced in the nano and micro classes that offer features previously found only in larger PLCs. This has made specifying a larger PLC just for additional features or performance, and not increased I/O count, unnecessary, as even those in the nano class are capable of Ethernet communication, motion control, on-board PID with autotune, remote connectivity and more.PLCs are also now well-equipped to replace stand-alone process controllers in many applications, due to their ability to perform functions of motion control, data acquisition, RTU (remote telemetry unit) and even some integrated HMI (human machine interface) functions. Previously, these functions often required their own purpose-built controllers and software, plus a separate PLC for the discrete control and interlocking.The Great CommunicatorPossibly the most significant change in recent years lies in the communications arena. In the 1970s Modicon introduction of Modbus communications protocol allowed PLCs to communicate over standard cabling. This translates to an ability to place PLCs in closer proximity to real world devices and communicate back to other system controls in a main panel.In the past 30 years we have seen literally hundreds of proprietary and standard protocols developed, each with their own unique advantages.Today's PLCs have to be data compilers and information gateways. They have to interface with bar code scanners and printers, as well as temperature and analog sensors. They need multiple protocol support to be able to connect with other devices in the process. And furthermore, they need all these capabilities while remaining cost-effective and simple to program.Another primary development that has literally revolutionized the way PLCs are programmed, communicate with each other and interface with PCs for HMI, SCADA or DCS applications, came from the computing world.Use of Ethernet communications on the plant floor has doubled in the past five years. While serial communications remain popular and reliable, Ethernet is fast becoming the communications media of choice with advantages that simply can't be ignored, such as: * Network speed. * Ease of use when it comes to the setup and wiring. * Availability of off-the-shelf networking components. * Built-in communications setups.Integrated Motion ControlAnother responsibility the PLC has been tasked with is motion control. From simple open-loop to multi-axis applications, the trend has been to integrate this feature into PLC hardware and software.There are many applications that require accurate control at a fast pace, but not exact precision at blazing speeds. These are applications where thestand-alone PLC works well. Many nano and micro PLCs are available withhigh-speed counting capabilities and high-frequency pulse outputs built into the controller, making them a viable solution for open-loop control.The one caveat is that the controller does not know the position of the output device during the control sequence. On the other hand, its main advantage is cost. Even simple motion control had previously required an expensive option module, and at times was restricted to more sophisticated control platforms in order to meet system requirements.More sophisticated motion applications require higher-precision positioning hardware and software, and many PLCs offer high-speed option modules that interface with servo drives. Most drives today can accept traditional commands from host (PLC or PC) controls, or provide their own internal motion control. The trend here is to integrate the motion control configuration into the logic controller programming software package.Programming LanguagesA facet of the PLC that reflects both the past and the future is programming language. The IEC 61131-3 standard deals with programming languages and defines two graphical and two textual PLC programming language standards: * Ladder logic (graphical). * Function block diagram (graphical). * Structured text (textual).Instruction list (textual).This standard also defines graphical and textual sequential function chart elements to organize programs for sequential and parallel control processing. Based on the standard, many manufacturers offer at least two of these languages as options for programming their PLCs. Ironically, approximately 96 percent of PLC users recently still use ladder diagrams to construct their PLC code. It seems that ladder logic continues to be a top choice given it's performed so well for so long.Hardware PlatformsThe modern PLC has incorporated many types of Commercial off the Shelf (COTS) technology in its CPU. This latest technology gives the PLC a faster, more powerful processor with more memory at less cost. These advances have also allowed the PLC to expand its portfolio and take on new tasks like communications, data manipulation and high-speed motion without giving up the rugged and reliable performance expected from industrial control equipment.New technology has also created a category of controllers called Programmable Automation Controllers, or PACs. PACs differ from traditional PLCs in that they typically utilize open, modular architectures for both hardware and software, using de facto standards for network interfaces, languages and protocols. They could be viewed as a PC in an industrial PLC-like package.The FutureA 2005 PLC Product Focus Study from Reed Research Group pointed out factors increasingly important to users, machine builders and those making the purchasing decisions. The top picks for features of importance were.* The ability to network, and do so easily. Ethernet communications is leading the charge in this realm. Not only are new protocols surfacing, but many of the industry de facto standard serial protocols that have been used for many years are being ported to Ethernet platforms. These include Modbus (ModbusTCP), DeviceNet (Ethernet/IP) and Profibus (Profinet). Ethernet communication modules for PLCs are readily available with high-speed performance and flexible protocols. Also, many PLC CPUs are now available with Ethernet ports on board, saving I/O slot space. PLCs will continue to develop more sophisticated connectivity to report information to other PLCs, systemcontrol systems, data acquisition (SCADA) systems and enterprise resource planning (ERP) systems. Additionally, wireless communications will continue to gain popularity.* The ability to network PLC I/O connections with a PC. The same trends that have benefited PLC networking have migrated to the I/O level. Many PLC manufacturers are supporting the most accepted fieldbus networks, allowing PLC I/O to be distributed over large physical distances, or located where it was previously considered nearly impossible. This has opened the door for personal computers to interface with standard PLC I/O subsystems by using interface cards, typically supplied by the PLC manufacturer or a third party developer. Now these challenging locations can be monitored with today a PC. Where industrial-grade control engines are not required, the user can take advantage of more advanced software packages and hardware flexibility at a lower cost.* The ability to use universal programming software for multipletargets/platforms. In the past it was expected that an intelligent controller would be complex to program. That is no longer the case. Users are no longer just trained programmers, such as design engineers or systems integrators, butend-users who expect easier-to-use software in more familiar formats. The Windows-based look and feel that users are familiar with on their personal computers have become the most accepted graphical user interface. What began as simple relay logic emulation for programming PLCs has evolved into languages that use higher level function blocks that are much more intuitive to configure. PLC manufacturers are also beginning to integrate the programming of diverse functions that allow you to learn only one package in configuring logic, HMI, motion control and other specialized capabilities. Possibly the ultimate wish of the end-user would be for a software package that could seamlessly program many manufacturers PLCs and sub-systems. After all, Microsoft Windows operating system and applications work similarly whether installed on a Dell, HP or IBM computer, which makes it easier for the user.Overall, PLC users are satisfied with the products currently available, while keeping their eye on new trends and implementing them where the benefits are obvious. Typically, new installations take advantage of advancing technologies, helping them become more accepted in the industrial world.PLC的过去、现在与未来众所周知,科技世界里只有一个永恒真理,那就是变化。
PLC控制系统外文文献翻译、中英文翻译、外文翻译
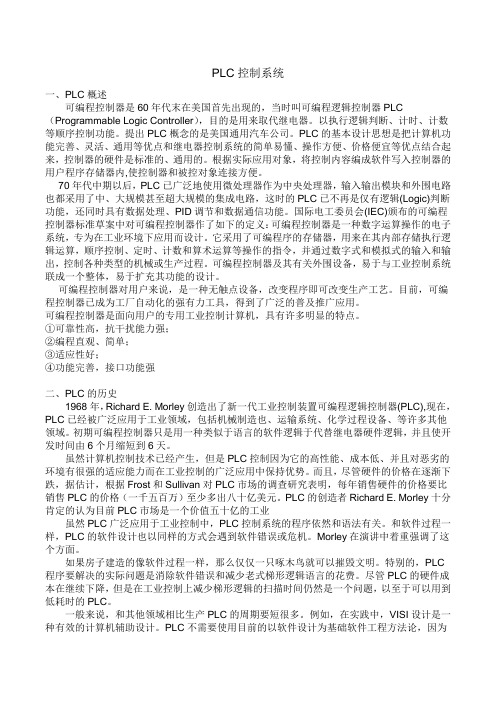
PLC控制系统一、PLC概述可编程控制器是60年代末在美国首先出现的,当时叫可编程逻辑控制器PLC (Programmable Logic Controller),目的是用来取代继电器。
以执行逻辑判断、计时、计数等顺序控制功能。
提出PLC概念的是美国通用汽车公司。
PLC的基本设计思想是把计算机功能完善、灵活、通用等优点和继电器控制系统的简单易懂、操作方便、价格便宜等优点结合起来,控制器的硬件是标准的、通用的。
根据实际应用对象,将控制内容编成软件写入控制器的用户程序存储器内,使控制器和被控对象连接方便。
70年代中期以后,PLC已广泛地使用微处理器作为中央处理器,输入输出模块和外围电路也都采用了中、大规模甚至超大规模的集成电路,这时的PLC已不再是仅有逻辑(Logic)判断功能,还同时具有数据处理、PID调节和数据通信功能。
国际电工委员会(IEC)颁布的可编程控制器标准草案中对可编程控制器作了如下的定义:可编程控制器是一种数字运算操作的电子系统,专为在工业环境下应用而设计。
它采用了可编程序的存储器,用来在其内部存储执行逻辑运算,顺序控制、定时、计数和算术运算等操作的指令,并通过数字式和模拟式的输入和输出,控制各种类型的机械或生产过程。
可编程控制器及其有关外围设备,易于与工业控制系统联成一个整体,易于扩充其功能的设计。
可编程控制器对用户来说,是一种无触点设备,改变程序即可改变生产工艺。
目前,可编程控制器已成为工厂自动化的强有力工具,得到了广泛的普及推广应用。
可编程控制器是面向用户的专用工业控制计算机,具有许多明显的特点。
①可靠性高,抗干扰能力强;②编程直观、简单;③适应性好;④功能完善,接口功能强二、PLC的历史1968年,Richard E. Morley创造出了新一代工业控制装置可编程逻辑控制器(PLC),现在,PLC已经被广泛应用于工业领域,包括机械制造也、运输系统、化学过程设备、等许多其他领域。
PLC相关的外文英语文献及翻译

PLC有关的外文英语文件及翻译RelaysThe Programmable Logic ControllerEarly machines were controlled by mechanical means using cams, gears, levers andother basic mechanical devices. As the complexity grew, so did the need for a more sophisticated control system. This system contained wired relay and switch control elements. These elements were wired as required to provide the control logic necessary for the particular type of machine operation. This was acceptable for a machine that never needed to be changed or modified, but as manufacturing techniques improved and plant changeover to new products became more desirable and necessary,a more versatile means of controlling this equipment had to be developed. Hardwired relay and switch logic was cumbersome and time consuming to modify. Wiring had to be removed and replaced to provide for the new control scheme required. This modification was difficult and time consuming to design and install and any small "bug" in the design could be a major problem to correct since that also required rewiring of the system. A new means to modify control circuitry was needed. The development and testing ground for this new means was the U.S. auto industry. The time period was the late 1960's and early 1970's and the result was the programmable logic controller, or PLC. Automotive plants were confronted with a change in manufacturing techniques every time a model changed and, in some cases, for changes on the same model if improvements had to be made during the model year. The PLC provided an easy way to reprogram the wiring rather than actually rewiring the control system.The PLC that was developed during this time was not very easy to program. The language was cumbersome to write and required highly trained programmers. These early devices were merely relay replacements and could do very little else. The PLC has at first gradually, and in recent years rapidly developed into a sophisticated and highly versatile control system component. Units today are capable of performing complex math functions including numerical integration and differentiation and operate at the fast microprocessor speeds now available. Older PLCs were capable of only handling discrete inputs and outputs (that is, on-off type signals), while today's systems can accept and generate analog voltagesPLC有关的外文英语文件及翻译and currents as well as a wide range of voltage levels and pulsed signals. PLCs arealso designed to be rugged. Unlike their personal computer cousin, they can typicallywithstand vibration, shock, elevated temperatures, and electrical noise to whichmanufacturing equipment is exposed.As more manufacturers become involved in PLC production and development, and PLC capabilities expand, the programming language is also expanding. This is necessary to allow the programming of these advanced capabilities. Also, manufacturers tend to develop their own versions of ladder logic language (the language used to program PLCs). This complicates learning to program PLC's in general since one language cannot be learned that is applicable to all types. However, as with other computer languages, once the basics of PLC operation and programming in ladder logic are learned, adapting to the various manufacturers ’ devices is not a complicated process. Most system designers eventually settle on one particular manufacturer that produces a PLC that is personally comfortable to program and has the capabilities suited to his or her area of applications.It should be noted that in usage, a programmable logic controller is generally referred toas a “ PLC” or “ programmable controller ” . Although the term “ programmable contr generally accepted, it is not abbreviated “ PC”becausethe abbreviation “ PC” is usuallyused in reference to a personal computer. As we will see in this chapter, a PLC is by nomeans a personal computer.Programmable controllers (the shortened name used for programmable logic controllers) are much like personal computers in that the user can be overwhelmed by the vast array of options and configurations available. Also, like personal computers, the best teacher of which one to select is experience. As one gains experience with the various options and configurations available, it becomes less confusing to be able to select the unit that will best perform in a particular application.The typical system components for a modularized PLC are:1. Processor.The processor (sometimes call a CPU), as in the self contained units, is generally specified according to memory required for the program to be In the rmodularizeversions,capability can also be a factor. This includes features such as highe math functions, PID control loops and optional programming commands. The processor consists of the microprocessor, system memory, serial communication ports for printer, PLC LAN link and external programming device and, in some cases, the system power supply to power the processor and I/O modules.2. Mounting rack.This is usually a metal framework with a printed circuit board backplane which provides means for mounting the PLC input/output (I/O) modules and processor. Mounting racks are specified according to the number of modules required to implement the system. The mounting rack provides data and power connections to the processor and modules via the backplane. For CPUs that do not contain a power supply, the rack also holds the modular power supply. There are systems in which the processor is mounted separately and connected by cable to the rack. The mounting rack can be available to mount directly to a panel or can be installed in a standard 19" wide equipment cabinet. Mounting racks are cascadable so several may be interconnected to allow a system to accommodate a large number of I/O modules.3. Input and output modules.Input and output (I/O) modules are specified according to the input and output signals associated with the particular application. These modules fall into the categories of discrete, analog, high speed counter or register types.Discrete I/O modules are generally capable of handling 8 or 16 and, in some cases 32, on-off type inputs or outputs per module. Modules are specified as input or output but generally not both although some manufacturers now offer modules that can be configured with both input and output points in the same unit. The module can be specified as AC only, DC only or AC/DC along with the voltage values for which it is designed.Analog input and output modules are available and are specified according to the desired resolution and voltage or current range. As with discrete modules, these are generally input or output; however some manufacturers provide analog input and output in the same module. Analog modules are also available which can directly accept thermocouple inputsfor temperature measurement and monitoring by the PLC.Pulsed inputs to the PLC can be accepted using a high speed countermodule. This module can be capable of measuring the frequency of an inputsignal from a tachometer or other frequency generating device. These modules can also count the incoming pulses if desired. Generally, both frequency and count are available from the same module at the same time if both are required in the application.Register input and output modules transfer 8 or 16 bit words of information to and from the PLC. These words are generally numbers (BCD or Binary) which are generated from thumbwheel switches or encoder systems for input or data to be output to a display device by the PLC.Other types of modules may be available depending upon the manufacturer of thePLC and it's capabilities. These include specialized communication modules to allow for the transfer of information from one controller to another. One new development is an I/O Module which allows the serial transfer of information to remote I/O units that can be as far as 12,000 feet away.4. Power supply.The power supply specified depends upon the manufacturer's PLC being utilized in the application. As stated above, in some cases a power supply capable of delivering all required power for the system is furnished as part of the processor module. If the power supply is a separate module, it must be capable of delivering a current greater than the sum of all the currents needed by the other modules. For systems with the power supply inside the CPU module, there may be some modules in the system which require excessive power not available from the processor either because of voltage or current requirements that can only be achieved through the addition of a second power source. This is generally true if analog or external communication modules are present since these require DC supplies which,± in the case of analog modules, must be well regulated.5. Programming unit.The programming unit allows the engineer or technician to enter and edit the programto be executed. In it's simplest form it can be a hand held device with a keypad for programentry and a display device (LED or LCD) for viewing program steps or functions, as shown. More advanced systems employ a separate personal computer which allows the programmer to write, view, edit and download the program to the PLC. This is accomplished with proprietary software available from the PLC manufacturer. This software also allows the programmer or engineer to monitor the PLC as it is running the program. With this monitoring system, such things as internal coils, registers, timers and other items not visible externally can be monitored to determine proper operation. Also, internal register data can be altered if required to fine tune program operation. This can be advantageous when debugging the program. Communication with the programmable controller with this system is via a cable connected to a special programming port on the controller. Connection to the personal computer can be through a serial port or from a dedicated card installed in the computer.A Programmable Controller is a specialized computer. Since it is a computer, it has all the basic component parts that any other computer has; a Central Processing Unit,Memory, Input Interfacing and Output Interfacing.The Central Processing Unit (CPU) is the control portion of the PLC. It interprets the program commands retrieved from memory and acts on those commands. In present day PLC's this unit is a microprocessor based system. The CPU is housed in the processor module of modularized systems.Memory in the system is generally of two types; ROM and RAM. The ROM memory contains the program information that allows the CPU to interpret and act on the Ladder Logic program stored in the RAM memory. RAM memory is generally kept alive with an on-board battery so that ladder programming is not lost when the system power is removed. This battery can be a standard dry cell or rechargeablenickel-cadmium type. Newer PLC units are now available with Electrically Erasable Programmable Read Only Memory (EEPROM) which does not require a battery. Memory is also housed in the processor module in modular systems.Input units can be any of several different types depending on input signals expected as described above. The input section can accept discrete or analog signals of various voltage and current levels. Present day controllers offer discrete signal inputs of both AC and DCvoltages from TTL to 250 VDC and from 5 to 250 VAC. Analog input units can accept input levels such as ±10 VDC, ±5 VDC and 4-20 ma. current loop values. Discrete input units present each input to the CPU as a single 1 or 0 while analog input units contain analog to digital conversion circuitry and present the input voltage to the CPU as binary number normalized to the maximum count available from the unit. The number of bits representing the input voltage or current depends upon the resolution of the unit. This number generally contains a defined number of magnitude bits and a sign bit. Register input units present the word input to the CPU as it is received (Binary or BCD).Output units operate much the same as the input units with the exception that the unit is either sinking (supplying a ground) or sourcing (providing a voltage) discrete voltages or sourcing analog voltage or current. These output signals are presented as directed by the CPU. The output circuit of discrete units can be transistors for TTL and higher DC voltage or Triacs for AC voltage outputs. For higher current applications and situations where a physical contact closure is required, mechanical relay contacts are available. These higher currents, however, are generally limited to about 2-3 amperes. The analog output units have internal circuitry which performs the digital to analog conversion and generates the variable voltage or current output.The first thing the PLC does when it begins to function is update I/O. This means that all discrete input states are recorded from the input unit and all discrete states to be output are transferred to the output unit. Register data generally has specific addresses associated with it for both input and output data referred to as input and output registers. These registers are available to the input and output modules requiring them and are updated with the discrete data. Since this is input/output updating, it is referred to as I/O Update. The updating of discrete input and output information is accomplished with the use of input and output image registers set aside in the PLC memory. Each discrete input point has associated with it one bit of an input image register. Likewise, each discrete output point has one bit of an output image register associated with it. When I/O updating occurs, each input point that is ON at that time will cause a 1 to be set at the bit address associated with that particular input. If the input is off, a 0 will be set into the bit address. Memory in today's PLC's is generallyconfigured in 16 bit words. This means that one word of memory can store the states of 16 discrete input points. Therefore, there may be a number of words of memory set aside asthe input and output image registers. At I/O update, the status of the input image register isset according to the state of all discrete inputs and the status of the output image register is transferred to the output unit. This transfer of information typically only occurs at I/O update.It may be forced to occur at other times in PLC's which have an Immediate I/O Update command. This command will force the PLC to update the I/O at other times although this would be a special case.Before a study of PLC programming can begin, it is important to gain a fundamental understanding of the various types of PLCs available, the advantages and disadvantagesof each, and the way in which a PLC executes a program. The open frame, shoebox, and modular PLCs are each best suited to specific types of applications based on the environmental conditions, number of inputs and outputs, ease of expansion, and method of entering and monitoring the program. Additionally, programming requires a prior knowledgeof the manner in which a PLC receives input information, executes a program, and sends output information. With this information, we are now prepared to begin a study of PLC programming techniques.When writing programs for PLCs, it is beneficial to have a background in ladder diagramming for machine controls. This is basically the material that was covered in Chapter 1 of this text. The reason for this is that at a fundamental level, ladder logic programs for PLCs are very similar to electrical ladder diagrams. This is no coincidence.The engineers that developed the PLC programming language were sensitive to the fact that most engineers, technicians and electricians who work with electrical machines on a day-to-day basis will be familiar with this method of representing control logic. This would allow someone new to PLCs, but familiar with control diagrams, to be able to adapt very quickly to the programming language. It is likely that PLC programming language is one of the easiest programming languages to learn.可编程序控制器初期的机器用机械的方法采纳凸轮控制、齿轮、杠杆和其余基本机械设施。
灌装机的发展史中英文对照资料外文翻译文献
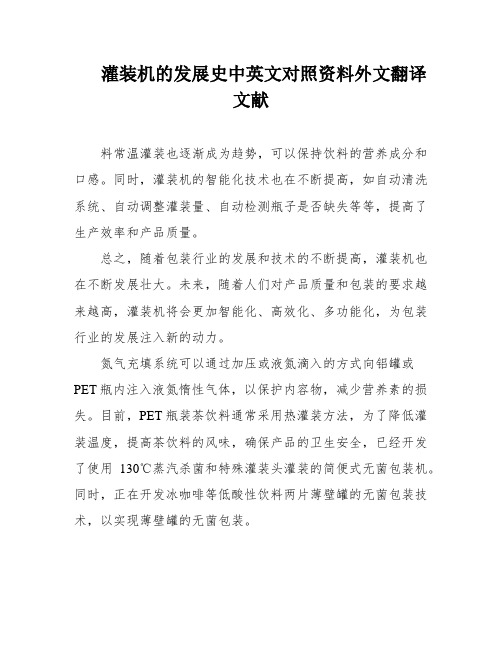
灌装机的发展史中英文对照资料外文翻译文献料常温灌装也逐渐成为趋势,可以保持饮料的营养成分和口感。
同时,灌装机的智能化技术也在不断提高,如自动清洗系统、自动调整灌装量、自动检测瓶子是否缺失等等,提高了生产效率和产品质量。
总之,随着包装行业的发展和技术的不断提高,灌装机也在不断发展壮大。
未来,随着人们对产品质量和包装的要求越来越高,灌装机将会更加智能化、高效化、多功能化,为包装行业的发展注入新的动力。
氮气充填系统可以通过加压或液氮滴入的方式向铝罐或PET瓶内注入液氮惰性气体,以保护内容物,减少营养素的损失。
目前,PET瓶装茶饮料通常采用热灌装方法,为了降低灌装温度,提高茶饮料的风味,确保产品的卫生安全,已经开发了使用130℃蒸汽杀菌和特殊灌装头灌装的简便式无菌包装机。
同时,正在开发冰咖啡等低酸性饮料两片薄壁罐的无菌包装技术,以实现薄壁罐的无菌包装。
我国的饮料灌装设备基本是在引进设备和技术的基础上发展起来的。
在八十年代,我国引进了各种饮料灌装生产线300多条,其中包括500多条啤酒灌装线。
引进的灌装生产线主要分为以下几类:玻璃瓶饮料灌装线:八十年代引进了116条玻璃瓶饮料灌装线,主要用于碳酸饮料。
其中80多条是以记账贸易方式从东欧国家引进的。
生产线主要设备有卸箱机、洗瓶机、灌装机、压盖机、贴标机、喷码机、气水混合机和装箱机等。
在线检测设备有真空检测仪、液面检测仪,灌装能力为150、200、300~400瓶/分。
设备的主要生产厂家有德国SEN、H&K、O+H、XXX、意大利希莫拉兹(Simonazzi)、美国迈耶等。
1984年,XXX引进了XXX和XXX啤酒灌装线制造技术,制造了每小时2万瓶的瓶装啤酒灌装线。
XXX和XXX引进了XXX技术,制造了每小时1.8万瓶的汽水灌装线。
其他还有重庆轻机厂的32/8设备,每小时可灌装瓶,XXX,每小时可灌装6000~8000瓶。
易拉罐饮料灌装线:在“八五”期间,我国引进了15条易拉罐饮料灌装线,同时还引进了14条易拉罐啤酒灌装线。
灌装容器的机器设备毕业课程设计外文文献翻译、中英文翻译

1英文文献翻译1.1 英文文献原文题目Given the challenge to fill any kind of container with any kind of liquid, engineers have diligently researched hundreds of product applications—from adhesives and sealants to coatings, and chemicals and lubricants to foods and beverages—in order to design machines that will fill containers rapidly and accurately. One critical specification needed in any industrial filling application is the viscosity of the liquid. Viscosity is the measure of a liquid’s ability to resist flow.Easy-flowing, water-like liquids have low viscosity, while thicker liquids have higher viscosities.Additional characteristics of industrial liquids include temperature, particle size, pH and degree of foaminess. Characteristics such as “lubricity” and “abrasiveness” are also taken into account to determine the best choice of nozzle configuration. The nozzle is the proprietary fixture (or “head”) that controls the flow of liquid as it streams into the container.NOZZLE TYPESPrecision-made nozzles of the correct size and materials are an important component of liquid filling machines. Ongoing technological innovation and continuous improvements are required to adapt to the wide range of liquid fillingApplications. Examples of nozzles for filling industrial liquids include plug, vented cone, shower head and probe; they are designed to optimize the filling of virtually any liquid product. Nozzles for liquid filling machines need to be reliable, durable, corrosion resistant and easy to clean.The plug nozzle is designed for filling through a variety of F-styleand screw-cap container openings. Plug nozzles fill thin to viscous products, provide drip control, and are available in a wide range of plug sizes as well as sanitary configurations (for foods). Recent improvements in plug nozzle technology eliminate leaking, which is especially problematic for high-lubricity liquids. Filling applications include adhesives, spackling, grout, peanut butter, fruit fillings and other food applicationsVented cone nozzles support both low- and high-viscosity filling applications where the container’s open top diameter is large enough to accept the “cone-style” shape this nozzle produces. The cone shape of the liquid stream directs product flow to the inside diameter walls of the container,thereby reducing splashing. Vented cone nozzles are an excellent choice for various filling applications, including stains, inks, oils, putties, paint, chemicals and adhesives. Shower head nozzles with interchangeable plates are designed for rapid laminar flow filling of ½-pint to 6-gal open-top containers. Shower head nozzles allow for fast, uninterrupted, non-turbulent flow of the liquid product, thereby reducing splashing. Shower head nozzles handle low- to medium-viscosity products from light liquids such as solvents and stains to higher viscosity products such as adhesives and inks.The probe nozzle is designed to fill foamy products without the production of foam caused by the turbulence of standard top filling. Probe nozzles fill containers from the bottom up, thereby reducing the turbulence that causes certain products to foam. Probe nozzles typically handle a broad range of container sizes from small containers to drums and totes. Filling applications often include detergents, herbicides, solvents, hydraulic fluids, fertilizers and cleaners.FILL SYSTEMSMoving beyond traditional nozzle technology, the gravity-feddirect-fill system has been an important innovation in liquid filling. The liquid filling industry is in an economic environment where the current trend is to maximize efficiency, increase ROI, and make the most of capital investments. Whether an adhesive or sealant manufacturer is choosing to install new liquid filling systems that incorporate the latest technology or retrofit a legacy system to extend the life and productivity of existing equipment, the right decision on where to invest requires a full understanding of the proven fill technologies available today.Liquid filling technology has progressed in stages, from manual hand filling to funnel and hose filling, to nozzle filling and pressurized drum, and now gravity-fed direct filling. Alternative systems place product in a pressurized vessel. The disadvantages of pressurized systems include splattering of product when pressurized nozzles are opened, leaking, product loss and complicated disassembly for cleaning. Volumetric systems fill by volume and can be less accurate.Shower head nozzles allow for fast, uninterrupted, non-turbulent flow of the liquid product, thereby reducing splashing.The negative effects of outdated and poorly performing liquid filling machines or systems include slower fill rates, decreased accuracy, and higher maintenance and cleanup. This results in longer batch changeover times. Any product delivery system that creates excessive spilling wastes valuable product and erodes profitability.As mentioned previously, viscosity is a measure of a liquid’s ability to resist flow. Laminar flow, sometimes known as streamline flow, occurs when a fluid flows in parallel layers with no disruption between the layers. In nonscientific terms, laminar flow is “smooth,” while turbulent flow is “rough.” Gravity-fed filling is best for water-thin liquid viscosities to liquids that are semi-viscous.The gravity-fed, direct-fill system is a liquid filling solution that delivers faster fill rates and improved accuracy, and reduces costs in liquid filling environments that handle products in the low- to medium-viscosity range. Gravity-fed liquid filling systems offer a new opportunity to expand the capabilities of any liquid filling machine, including the retrofit and upgrade of legacy liquid filling machines.Common liquids and their relative range of viscosities from thin to thick as measured in centipoise include water, turpentine, vegetable oil, SAE40 motor oil, varnish, glycerin, molasses, latex paint, honey, SAE70 motor oil, water-based paint, solvents and glue.BENEFITS OF A GRAVITY-FED DIRECT-FILL SYSTEMThe gravity head pressure process delivers more uniform filling for greater throughput. Balanced flow delivers faster fill rates (up to 35%), more consistent filling, and greater batch yields. A balanced flow lends itself to greater control of nozzle cut-off during the filling cycle for greater accuracy.The gravity head pressure process also eliminates splattering and reduces cleanup time. All surfaces on direct-fill systems can be easily accessed for more thoroughcleaning. Fewer wetted parts allow a 50% reduction in cleanup and batch changeover time. Direct fill systems feature a welded reservoir tank with integrated nozzles that increase fill rates, improve uptime and reduce maintenance. The simple innovative design and fewer serviceable parts of a gravity-fed direct-fill system reduce operating costs and maintenance requirements, eliminating the need for surge tanks, hoses, valves, and surge dampeners.Gravity-fed filling is best for water-thin liquid viscosities to liquids that are semi-viscous.The main environmentally friendly attribute of gravity-feddirect-fill systems is the reduction of product residue. The result is lower hazardous waste and lower cleaning material needed for cleanup.Adjustment controls for rapid fill rate and dribble rate enable the filling of a variety of liquid industrial applications, including adhesives, coatings, inks and lubricants. Direct-fill systems can be configured with one, two, four, six or eight nozzles to complement a variety of filling machine nozzle configurations and deliver a wide range of container filling throughput rates.Selection of PLCThe former relay control mode has many disadvantages. With the combination of mature computer technology and virtual technology with relay control, the contact point of interference relay control is virtualized and used as internal relay or soft component of controller, and applied in industrial manufacture, that is, PLC system control. Therefore, according to the principle, PLC is the exclusive computer designed for the application in the industrial environment. Its composition and layout also have the advantages of the general computer: the central processing unit is taken as the core and executed under the management of the system program.The design requirements of the control system for liquid filling machine are as follows: accurate, stable, easy to adjust, stronganti-interference and so on, and according to the requirements of the control object of the filling machine, The control system selected in this thesis is Mitsubishi Motor Q series PLC, which usually acts on medium and large scale control system. The modules not only have more common power modules, such as CPU module, input module, output module, but also include positioning module, analog input module and so on. According to specificneeds, other modules such as temperature adjustment module, high speed counter and so on can be selected. The Q series PLC can be assembled in the form of main substrates and extended substrates, not only by adding extended modules, but also by adding extended modules. The number of installations and the number of I / O available can also increase storage capacity.The programmable logic controller used here is Q06HCPU.It is usually used in medium, medium and large control systems. Compared with Q06HCPU, Q06HCPU has the advantages of strong execution, fast processing, small delay and large memory to meet the needs of large systems in multiple programs.I / O module is an input / output module whose specification and number are determined by the number of required points of the control system. The more the number of I / O modules is, but the maximum number of modules and the maximum number of points are determined by the selected CPU. The Q06HCPUs selected by the system are high performance Q series PLC CPUs. The maximum I / O control points of the system are 4096 points and the number of controllable modules can reach 64 blocks. If the number of I / O controls required is more, the extended I / O modules can be selected to increase the control number.Motion control module is one of the most popular motion control modules in Mitsubishi PLC intelligent function module. It is used in combination with step motor or servo motor in order to complete complex speed and positioning control. According to the number of control axes, the motion control module has one axis, two axes, four axes and eight axes, which not only completes the linear control and interpolation, but alsohas the functions of circular arc interpolation, spiral interpolation, multi-origin regression and so on. The QD70P8 positioning module which can be used in 8 axis control is selected here to control the speed of filling servo motor and commutating step motor. [7:.]The determination of input and output points: tables 3.1 and 3.2 are the distribution tables of input points and output points of liquid filling machines respectively.selection of actuatorsAccording to the above described control system selection of the executive mechanism, this part of the control of filling and capping servo motor, commutation step motor, the system of the working motor and stopper and cover electromagnet selection, analysis of the characteristics, The connection control method is further explained.Selection of stepping MotorStepping motor is also a common executive element in electrical system. It converts electric pulse into angular displacement or linear displacement and drives other components to rotate and position precisely. When a pulse is input, the fixed angle of rotation is defined as a step angle or step distance. Step angle is an important basis for motor selection. After the motor is selected, the step angle and the number of subdivision are determined. The ratio of the step angle to the fine fraction is the movement amount of the step motor when each pulse is input, which is called pulse equivalent, which determines the motion accuracy of the step motor. The function of step motor is to realize the rotation of servo pump and fixed angle in a very short time. According to the design, Each commutation, servo pump, according to the requirements of the accurate rotation of 120 degrees, and there can be no cumulative error. The existence of cumulative error will interfere with the positionrelationship between the servo pump and the two filling heads because of the persistent operation of the system, resulting in the whole filling can not be carried out. The system is composed of stepping motor and driver DCH-30806 series driver of Changzhou Dechang. The output current range is 0.4A0. 6A and the output current range is 0.4A0. 6A. The output current is adjusted by different combinations of the drive side board 7 / 8 / 9 / 10 four-bit switch. A total of 16 current values are available.The speed of step motor is controlled by the input of pulse signal, and the fifth position switch of the side plate of the driver can choose either monopulse mode or double pulse mode. In monopulse mode, the step pulse is connected by the pulse port, and the direction of the motor is determined by the level of the direction port. In the dual pulse mode, the driver receives the positive turn pulse from the pulse port and the reverse pulse from the direction port. Both single and double pulses take the optical root from cutoff to conduction as an effective reception signal.When the off-line signal is input, the driver will cut off the electric current of each phase of the motor to make the motor shaft free, and the step pulse will not be responded at this time. This state can effectively reduce the power and temperature rise of the drive and motor. After the off-line control signal is revoked, the drive automatically returns to the phase sequence before the offline and restore the motor current. When no need for this is needed When the offline end is suspended, when the motor stops moving, the stepping motor shaft is in the stop state when the motor stops moving. When the off-line signal is input, the motor shaft is in free state after the motor is stopped and the motor can be rotated manually.The direction and speed of the stepping motor are set by QD70P8 module to make the motor move according to the predetermined curve.Key Technology of liquid fillingNo. 24 filling head is at No. 1. When filling, the filling head and bottle one-to-one correspondence for filling. Press the start button, the filling wheel starts to rotate and fill. Position 1 is the start of filling, 9 is filling stop, 17 is out of bottle. For each filling head, its work flow is as follows: 1 work station begins filling-9 station filling end-17 position out of bottle.The biggest feature of the liquid filling machine is that one servo pump corresponds to the continuous filling of two filling heads, and the two filling heads controlled by the same servo pump are installed at 180 degrees. Take No.1 servo pump as an example, control 1 filling head and 13 filling head, 1 filling head and 13 filling head carry out the above filling one stop one bottle out action, respectively, so each servo pump's work flow is as follows: filling liquid, sucking liquid and sucking liquid.Arrangement of sensorsSensor layout, No. 1 as a reset sensor, its main role is: press the reset button, filling the main motor drive system rotation, when the reset sensor 1 detects the filling head 1 rotation to this position, PLC control filling main motor stop, The main motor reset is completed, the purpose is to make the No. 1 filling head stop at the starting position of filling before each start operation. 3 is the detection sensor with or without bottle. When the bottle is detected, the sensor sends the detection signal to PLC so that the corresponding servo pump can be started. Perform filling action; if there is no bottle, the corresponding servo pump does not act, thus realizing the function of no bottle without filling. The sensor, when the filling head rotates to this position, stops filling. This is alsothe filling mark position. 5- 16 sensor is the limit position detection sensor on the filling pump, and the 17-28 sensor is the limit position detection sensor under the filling pump. The filling pump moves up and down in a straight line with the servo motor driving the fixed stroke. Normally, the sensor 5- 28 will not be outside the motion stroke. At the same time, when the servo motor is reset, the servo motor drives the ceramic pump to the lower limit position. Ensure that all ceramic pumps are at the bottom before filling begins, so sensor 17-28 is also a reset sensor for servo motors Apparatus.Sensor 29 is a bottle cap sensor. The filled bottle enters the cap assembly through the III. If the sensor 29 detects that the work station has no bottle, then the cap electromagnetic body moves, so that the corresponding rotary cap head has no cover, so that the bottle without cap is realized. Improve the use rate of lid and automation level of filling machine, at the same time can prevent the remaining cover from falling into the filling system to cause mechanical failure. Sensor 30 as position detection sensor, when the cover head drops to this position, The sensor transmits the signal to the PLC, then controls the capping servo motor to stop, and the capping action is completed.changing-overThe biggest feature of the filling machine is the control of two filling heads by the same servo pump and continuous filling. In addition, as the servo pump is to control two filling heads, the ceramic pump needs to be converted between three openings in the filling cycle, and the change of the ceramic pump has a stepper motor to achieve. There are three 120 degrees on the outer side of the ceramic pump. The opening is for the inlet, the outlet 1 and the outlet 2, and the two outlet ports are connected with two 180 degrees of filling head. The inner rotation range is based on the inlet (middle), and turns 120 degrees.Gravity and Pressure FillersThe Gravity and Pressure/Gravity Fillers are suitable for bottling virtually any water-thin to medium consistent viscosity liquid. Gravity fillers are ideally suited for thin, foamy products wherepressure/gravity fillers handle heavier viscosity products.Pump FillersE-PAK offers several different types of pump fillers to accommodate a wide variety of products. They provide an accurate and versatile method for filling low, medium and high viscosity liquids into a wide range of containers. E-PAK uses a variety of pumps including progressive cavity pumps, gear pumps, lobe pumps, rotor pumps or whichever is best for the application. We work with each customer to choose the right pumps, valves, and fittings for each application.Gravity, Pressure & Vacuum Overflow Bottle FillersOverflow Fillers provide the same cosmetic fill level, making them ideal for filling transparent containers that must have a consistent fill level. Gravity and pressure overflow fillers are designed to handle thin to medium viscosity products. The E-PAK Vacuum Overflow Filler is used for specialty filling applications and is typically used to fill small volume glass containers with low viscosity liquids.Piston Filling SystemsPiston fillers are another great option for packaging liquids. They offer fast and accurate fill rates, versatility with the ability to handle many different types of products, and they’re gentle on products. They’re ideal for viscous liquids including batters, sauces, pastes, icing, chunky fillings, and certain aerated products. Generally, these liquid packing machines are used to fill liquids that are squeezed through pastry bags or similar packaging.Net Weigh Bottle FillersNet weigh liquid filling systems are great for making sure that each container you fill contains the same amount of product. They are particularly efficient at packaging bulk quantities of products, along with products that are of high value and require the maximum accuracy when weighing them to avoid lost profits.1.2中文翻译考虑到需要填充任何容易的难题,工程师们都在仔细研究着从粘合剂和密封剂中所提取出的数百种产品,对食品和饮料进行化学、润滑等的处理,以便设计能准确灌装容器的机器,任何工业填料应用中需要的一个关键规格是液体的粘度,粘度是衡量液体抵抗流动能力的尺度,流动性好,水状液体粘度低,粘稠液体粘度高。
(完整word版)PLC英文文献翻译

附录外文资料PLC technique discussion and future developmentAlong with the development of the ages, the technique that is nowadays is also gradually perfect, the competition plays more strong; the operation that list depends the artificial has already can't satisfied with the current manufacturing industry foreground, also can't guarantee the request of the higher quantity and high new the image of the technique business enterprise.The people see in produce practice, automate brought the tremendous convenience and the product quantities for people up of assurance, also eased the personnel's labor strength, reduce the establishment on the personnel. The target control of the hard realization in many complicated production lines, whole and excellent turn, the best decision etc., well-trained operation work, technical personnel or expert, governor but can judge and operate easily, can acquire the satisfied result. The research target of the artificial intelligence makes use of the calculator exactly to carry out, imitate these intelligences behavior, moderating the work through person's brain and calculators, with the mode that person's machine combine, for resolve the very complicated problem to look for the best pathWe come in sight of the control that links after the electric appliances in various situation, that is already the that time generation past, now of after use in the mold a perhaps simple equipments of grass-roots control that the electric appliances can do for the low level only; And the PLC emergence also became the epoch-making topic, adding the vivid software control through a very and stable hardware, making the automation head for the new high tide.The PLC biggest characteristics lie in: The electrical engineering teacher already no longer electric hardware up too many calculations of cost, as long as order the importation that the button switch or the importation of the sensors order to link the PLC up can solve problem, pass to output to order the conjunction contact machine or control the start equipments of the big power after the electric appliances, but the exportation equipments direct conjunction of the small power can.PLC internal containment have the CPU of the CPU, and take to have an I/ O for expand of exterior to connect a people's address and saving machine three big pieces to constitute, CPU core is from an or many is tired to add the machine to constitute, mathematics that they have the logic operation ability, and can read the procedure save the contents of the machine to drive the homologous saving machine and I/ Os to connect after pass the calculation; The I/ O add inner part is tired the input and output system of the machine and exterior link, and deposit the related data into the procedure saving machine or data saving machine; The saving machine can deposit the data that the I/ O input in the saving machine, and in work adjusting to becometired to add the machine and I/ Os to connect, saving machine separately saving machine RAM of the procedure saving machine ROM and dates, the ROM can do deposit of the data permanence in the saving machine, but RAM only for the CPU computes the temporary calculation usage of hour of buffer space.The PLC anti- interference is very and excellent, our root need not concern its service life and the work situation bad, these all problems have already no longer become the topic that we fail, but stay to our is a concern to come to internal resources of make use of the PLC to strengthen the control ability of the equipments for us, make our equipments more gentle.PLC language is not we imagine of edit collected materials the language or language of Cs to carry on weaving the distance, but the trapezoid diagram that the adoption is original after the electric appliances to control, make the electrical engineering teacher while weaving to write the procedure very easy comprehended the PLC language, and a lot of non- electricity professional also very quickly know and go deep into to the PLC.Is PLC one of the advantage above and only, this is also one part that the people comprehend more and easily, in a lot of equipments, the people have already no longer hoped to see too many control buttons, they damage not only and easily and produce the artificial error easiest, small is not a main error perhaps you can still accept; But lead even is a fatal error greatly is what we can't is tolerant of. New technique always for bringing more safe and convenient operation for us, make we a lot of problems for face on sweep but light, do you understand the HMI? Says the HMI here you basically not clear what it is, also have no interest understanding, change one inside text explains it into the touch to hold or man-machine interface you knew, and it combines with the PLC to our larger space.HMI the control not only is reduced the control press button, increase the vivid of the control, more main of it is can sequence of, and at can the change data input to output the feedback with data, control in the temperature curve of imitate but also can keep the manifestation of view to come out. And can write the function help procedure through a plait to provide the help of various what lies in one's power, the one who make operate reduces the otiose error. Currently the HMI factory is also more and more, the function is also more and more strong, the price is also more and more low, and the noodles of the usage are wide more and more. The HMI foreground can say that think ° to be good very.At a lot of situations, the list is a smooth movement that can't guarantee the equipments by the control of the single machine, but pass the information exchanges of the equipments and equipments to attain the result that we want. For example fore pack and the examination of the empress work preface, we will arrive wrapping information feedback to examine the place, and examine the information of the place to also want the feedback to packing. Pass the information share thus to make both the chain connect, becoming a total body, the match of your that thus make is more close,at each other attain to reflect the result that mutually flick.The PLC correspondence has already come more body now its value, at the PLC and correspondence between PLCs, can pass the communication of the information and the share of the dates to guarantee that of the equipments moderates mutually, the result that arrive already to repair with each other. Data conversion the adoption RS232 between PLC connect to come to the transmission data, but the RS232 pick up a people and can guarantee 10 meters only of deliver the distance, if in the distance of 1000 meters we can pass the RS485 to carry on the correspondence, the longer distance can pass the MODEL only to carry on deliver.The PLC data transmission is just to be called a form to it in a piece of and continuous address that the data of the inner part delivers the other party, we, the PLC of the other party passes to read data in the watch to carry on the operation. If the data that data in the watch is a to establish generally, that is just the general data transmission, for example today of oil price rise, I want to deliver the price of the oil price to lose the oil ally on board, that is the share of the data; But take data in the watch for an instruction procedure that controls the PLC, that had the difficulty very much, for example you have to control one pedestal robot to press the action work that you imagine, you will draw up for it the form that a procedure combine with the data sends out to pass by.The form that information transport contain single work, the half a work and the difference of a workers .The meaning of the single work also is to say both, a can send out only, but a can receive only, for example a spy he can receive the designation of the superior only, but can't give the superior reply; A work of half is also 2 and can send out similar to accept the data, but can't send out and accept at the same time, for example when you make a phone call is to can't answer the phone, the other party also; But whole pair works is both can send out and accept the data, and can send out and accept at the same time. Be like the Internet is a typical example.The process that information transport also has synchronous and different step cent: The data line and the clock lines are synchronous when synchronous meaning lie in sending out the data, is also the data signal and the clock signals to be carry on by the CPU to send out at the same time, this needs to all want the specialized clock signal each other to carry on the transmission and connect to send, and is constrained, the characteristics of this kind of method lies in its speed very quick, but correspond work time of take up the CPU and also want to be long oppositely, at the same time the technique difficulty also very big. Its request lies in canting have an error margins in a dates deliver, otherwise the whole piece according to compare the occurrence mistake, this on the hardware is a bigger difficulty. Applied more and more extensive in some appropriative equipments, be like the appropriative medical treatment equipments, the numerical signal equipments...etc., in compare the one data deliver, its result is very good.And the different step is an application the most extensive, this receive benefit init of technique difficulty is opposite and want to be small, at the same time not need to prepare the specialized clock signal, its characteristics to lie in, its data is partition, the long-lost send out and accept, be the CPU is too busy of time can grind to a stop sex to work, also reduced the difficulty on the hardware, the data throw to lose at the same time opposite want to be little, we can pass the examination of the data to observe whether the data that we send out has the mistake or not, be like strange accidentally the method, tired addition and eight efficacies method etc., can use to helps whether the data that we examine to send out have or not the mistake occurrence, pass the feedback to carry on the discriminator.A line of transmission of the information contains a string of and combine the cent of: The usual PLC is 8 machines, certainly also having 16 machines. We can be an at the time of sending out the data a send out to the other party, also can be 88 send out the data to the other party, an and 8 differentiations are also the as that we say to send out the data and combine sends out the data. A speed is more and slowly, but as long as 2 or three lines can solve problem, and can use the telephone line to carry on the long range control. But combine the ocular transmission speed is very quick of, it is a string of ocular of 25600%, occupy the advantage in the short distance, the in view of the fact TTL electricity is even, being limited by the scope of one meter generally, it combine unwell used for the data transmission of the long pull, thus the cost is too expensive.Under a lot of circumstances we are total to like to adopt the string to combine the conversion chip to carry on deliver, under this kind of circumstance not need us to carry on to deposited the machine to establish too and complicatedly, but carry on the data exchanges through the data transmission instruction directly, but is not a very viable way in the correspondence, because the PLC of the other party must has been wait for your data exportation at the time of sending out the data, it can't do other works.When you are reading the book, you hear someone knock on door, you stop to start up of affair, open the door and combine to continue with the one who knock on door a dialogue, the telephone of this time rang, you signal hint to connect a telephone, after connecting the telephone through, return overdo come together knock on door to have a conversation, after dialogue complete, you continue again to see your book, this kind of circumstance we are called the interruption to it, it has the authority, also having sex of have the initiative, the PLC had such function .Its characteristics lie in us and may meet the urgently abrupt affairs in the operation process of the equipments, we want to stop to start immediately up of work, the whereabouts manages the more important affair, this kind of circumstance is we usually meet of, PLC while carry out urgent mission, total will keep the current appearance first, for example the address of the procedure, CPU of tired add the machine data etc., be like to stick down which the book that we see is when we open the door the page or simply make a mark, because we treat and would still need to continue immediately after book of see the behind. The CPU always does the affair that should do according to our will, but your mistake of give it an affair, it also would be same to do, this we must notice.The interruption is not only a, sometimes existing jointly with the hour several inside break, break off to have the preferred Class, they will carry out the interruption of the higher Class according to person's request. This kind of breaks off the medium interruption to also became to break off the set. The Class that certainly break off is relevant according to various resources of CPU with internal PLC, also following a heap of capacity size of also relevant fasten.The contents that break off has a lot of kinds, for example the exterior break off, correspondence in of send out and accept the interruption and settle and the clock that count break off, still have the WDT to reset the interruption etc., they enriched the CPU to respond to the category while handle various business. Speak thus perhaps you can't comprehend the internal structure and operation orders of the interruption completely also, we do a very small example to explain.Each equipment always will not forget a button, it also is at we meet the urgent circumstance use of, which is nasty to stop the button. When we meet the Human body trouble and surprised circumstances we as long as press it, the machine stops all operations immediately, and wait for processing the over surprised empress recover the operation again. Nasty stop the internal I/ O of the internal CPU of the button conjunction PLC to connect up, be to press button an exterior to trigger signal for CPU, the CPU carries on to the I/ O to examine again, being to confirm to have the exterior to trigger the signal, CPU protection the spot breaks off procedure counts the machine turn the homologous exterior I/ O automatically in the procedure to go to also, be exterior interruption procedure processing complete, the procedure counts the machine to return the main procedure to continue to work. Have 1:00 can what to explain is we generally would nasty stop the button of exterior break off to rise to the tallest Class, thus guarantee the safety.When we are work a work piece, giving the PLC a signal, counting PLC inner part the machine add 1 to compute us for a day of workload, a count the machine and can solve problem in brief, certainly they also can keep the data under the condition of dropping the electricity, urging the data not to throw to lose, this is also what we hope earnestly.The PLC still has the function that the high class counts the machine, being us while accept some dates of high speed, the high speed that here say is the data of the in all aspects tiny second class, for example the bar code scanner is scanning the data continuously, calculating high-speed signal of the data processor DSP etc., we will adopt the high class to count the machine to help we carry on count. It at the PLC carries out the procedure once discover that the high class counts the machine to should of interruption, will let go of the work on the hand immediately. The trapezoid diagram procedure that passes by to weave the distance again explains the high class for us to carry out procedure to count machine would automatic performance to should of work, thus rise the Class that the high class counts the machine to high one Class.You heard too many this phrases perhaps:" crash", the meaning that is mostly is a workload of CPU to lead greatly, the internal resources shortage etc. the circumstance can't result in procedure circulate. The PLC also has the similar circumstance, there is a watchdog WDT in the inner part of PLC, we can establish time that a procedure of WDT circulate, being to appear the procedure to jump to turn the mistake in the procedure movement process or the procedure is busy, movement time of the procedure exceeds WDT constitution time, the CPU turn but the WDT reset the appearance. The procedure restarts the movement, but will not carry on the breakage to the interruption.The PLC development has already entered for network ages of correspondence from the mode of the one, and together other works control the net plank and I/ O card planks to carry on the share easily. A state software can pass all se hardwires link, more animation picture of keep the view to carries on the control, and cans pass the Internet to carry on the control in the foreign land, the blast-off that is like the absolute being boat No.5 is to adopt this kind of way to make airship go up the sky.The development of the higher layer needs our continuous effort to obtain. The PLC emergence has already affected a few persons fully, we also obtained more knowledge and precepts from the top one experience of the generation, coming to the continuous development PLC technique, push it toward higher wave tide.Knowing the available PLC network options and their best applications will ensure an efficient and flexible control system design.The programmable logic controller's (PLC's) ability to support a range of communication methods makes it an ideal control and data acquisition device for a wide variety of industrial automation and facility control applications. However, there is some confusion because so many possibilities exist. To help eliminate this confusion, let's list what communications are available and when they would be best applied.To understand the PLC's communications versatility, let's first define the terms used in describing the various systems.ASCII: This stands for "American Standard Code for Information Interchange." As shown in Fig. 1, when the letter "A" is transmitted, for instance, it's automatically coded as "65" by the sending equipment. The receiving equipment translates the "65" back to the letter "A." Thus, different devices can communicate with each other as long as both use ASCII code.ASCII module: This intelligent PLC module is used for connecting PLCs to other devices also capable of communicating using ASCII code as a vehicle.Bus topology: This is a linear local area network (LAN) arrangement, as shown in Fig. 2A, in which individual nodes are tapped into a main communications cable at a single point and broadcast messages. These messages travel in both directions on thebus from the point of connection until they are dissipated by terminators at each end of the bus.CPU: This stands for "central processing unit," which actually is that part of a computer, PLC, or other intelligent device where arithmetic and logical operations are performed and instructions are decoded and executed.Daisy chain: This is a description of the connection of individual devices in a PLC network, where, as shown in Fig. 3, each device is connected to the next and communications signals pass from one unit to the next in a sequential fashion.Distributed control: This is an automation concept in which portions of an automated system are controlled by separate controllers, which are located in close proximity to their area of direct control (control is decentralized and spread out over the system).Host computer: This is a computer that's used to transfer data to, or receive data from, a PLC in a PLC/computer network.Intelligent device: This term describes any device equipped with its own CPU.I/O: This stands for "inputs and outputs," which are modules that handle data to the PLC (inputs) or signals from the PLC (outputs) to an external device.Kbps: This stands for "thousand bits per second," which is a rate of measure for electronic data transfer.Mbps: This stands for "million bits per second."Node: This term is applied to any one of the positions or stations in a network. Each node incorporates a device that can communicate with all other devices on the network.Protocol: The definition of how data is arranged and coded for transmission on a network.Ring topology. This is a LAN arrangement, as shown in Fig. 2C, in which each node is connected to two other nodes, resulting in a continuous, closed, circular path or loop for messages to circulate, usually in one direction. Some ring topologies have a special "loop back" feature that allows them to continue functioning even if the main cable is severed.RS232. This is an IEEE standard for serial communications that describes specific wiring connections, voltage levels, and other operating parameters for electronic data communications. There also are several other RS standards defined.Serial: This is an electronic data transfer scheme in which information istransmitted one bit at a time.Serial port: This the communications access point on a device that is set up for serial communications.Star topology. This is a LAN arrangement in which, as shown in Fig. 2B, nodes are connected to one another through a central hub, which can be active or passive. An active hub performs network duties such as message routing and maintenance. A passive central hub simply passes the message along to all the nodes connected to it.Topology: This relates to a specific arrangement of nodes in a LAN in relation to one another.Transparent: This term describes automatic events or processes built into a system that require no special programming or prompting from an operator.Now that we're familiar with these terms, let's see how they are used in describing the available PLC network options.PLC network optionsPLC networks provide you with a variety of networking options to meet specific control and communications requirements. Typical options include remote I/O, peer-to-peer, and host computer communications, as well as LANs. These networks can provide reliable and cost-effective communications between as few as two or as many as several hundred PLCs, computers, and other intelligent devices.Many PLC vendors offer proprietary networking systems that are unique and will not communicate with another make of PLC. This is because of the different communications protocols, command sequences, error-checking schemes, and communications media used by each manufacturer.However, it is possible to make different PLCs "talk" to one another; what's required is an ASCII interface for the connection(s), along with considerable work with software.Remote I/0 systemsA remote I/O configuration, as shown in Fig. 4A, has the actual inputs and outputs at some distance from the controller and CPU. This type of system, which can be described as a "master-and-slave" configuration, allows many distant digital and analog points to be controlled by a single PLC. Typically, remote I/Os are connected to the CPU via twisted pair or fiber optic cables.Remote I/O configurations can be extremely cost-effective control solutions where only a few I/O points are needed in widely separated areas. In this situation, it's not always necessary, or practical for that matter, to have a controller at each site. Noris it practical to individually hard wire each I/O point over long distances back to the CPU. For example, remote I/O systems can be used in acquiring data from remote plant or facility locations. Information such as cycle times, counts, duration or events, etc. then can be sent back to the PLC for maintenance and management reporting.In a remote I/O configuration, the master controller polls the slaved I/O for its current I/O status. The remote I/O system responds, and the master PLC then signals the remote I/O to change the state of outputs as dictated by the control program in the PLC's memory. This entire cycle occurs hundreds of times per second.Peer-to-peer networksPeer-to-peer networks, as shown in Fig. 4B, enhance reliability by decentralizing the control functions without sacrificing coordinated control. In this type of network, numerous PLCs are connected to one another in a daisy-chain fashion, and a common memory table is duplicated in the memory of each. In this way, when any PLC writes data to this memory area, the information is automatically transferred to all other PLCs in the network. They then can use this information in their own operating programs.With peer-to-peer networks, each PLC in the network is responsible for its own control site and only needs to be programmed for its own area of responsibility. This aspect of the network significantly reduces programming and debugging complexity; because all communications occur transparently to the user, communications programming is reduced to simple read-and-write statements.In a peer-to-peer system, there's no master PLC. However, it's possible to designate one of the PLCs as a master for use as a type of group controller. This PLC then can be used to accept input information from an operator input terminal, for example, sending all the necessary parameters to other PLCs and coordinating the sequencing of various events.Host computer linksPLCs also can be connected with computers or other intelligent devices. In fact, most PLCs, from the small to the very large, can be directly connected to a computer or part of a multi drop host computer network via RS232C or RS422 ports. This combination of computer and controller maximizes the capabilities of the PLC, for control and data acquisition, as well as the computer, for data processing, documentation, and operator interface.In a PLC/computer network, as shown in Fig. 4C, all communications are initiated by the host computer, which is connected to all the PLCs in a daisy-chain fashion. This computer individually addresses each of its networked PLCs and asks for specific information. The addressed PLC then sends this information to the computer for storage and further analysis. This cycle occurs hundreds of times per second.Host computers also can aid in programming PLCs; powerful programming and documentation software is available for program development. Programs then can be written on the computer in relay ladder logic and downloaded into the PLC. In this way, you can create, modify, debug, and monitor PLC programs via a computer terminal.In addition to host computers, PLCs often must interface with other devices, such as operator interface terminals for large security and building management systems. Although many intelligent devices can communicate directly with PLCs via conventional RS232C ports and serial ASCII code, some don't have the software ability to interface with individual PLC models. Instead, they typically send and receive data in fixed formats. It's the PLC programmer's responsibility to provide the necessary software interface.The easiest way to provide such an interface to fixed-format intelligent devices is to use an ASCII/BASIC module on the PLC. This module is essentially a small computer that plugs into the bus of the PLC. Equipped with RS232 ports and programmed in BASIC, the module easily can handle ASCII communications with peripheral devices, data acquisition functions, programming sequences, "number crunching," report and display generation, and other requirements.Access, protocol, and modulation functions of LANsBy using standard interfaces and protocols, LANs allow a mix of devices (PLCs, PCs, mainframe computers, operator interface terminals, etc.) from many different vendors to communicate with others on the network.Access: A LAN's access method prevents the occurrence of more than one message on the network at a time. There are two common access methods.Collision detection is where the nodes "listen" to the network and transmit only if there are no other messages on the network. If two nodes transmit simultaneously, the collision is detected and both nodes retransmit until their messages get through properly.Token passing allows each node to transmit only if it's in possession of a special electronic message called a token. The token is passed from node to node, allowing each an opportunity to transmit without interference. Tokens usually have a time limit to prevent a single node from tying up the token for a long period of time.Protocol: Network protocols define the way messages are arranged and coded for transmission on the LAN. The following are two common types.Proprietary protocols are unique message arrangements and coding developed by a specific vendor for use with that vendor's product only.Open protocols are based on industry standards such as TCP/IP or ISO/OSI。
最新PLC毕业设计的外文文献(及翻译)资料

PLC technique discussion and future developmentT.J.byersElectronic Test Equipment-principles and ApplicationsPrinceton University .AmericaAlong with the development of the ages, the technique that is nowadays is also gradually perfect, the competition plays more strong; the operation that list depends the artificial has already can't satisfied with the current manufacturing industry foreground, also can't guarantee the request of the higher quantity and high new the image of the technique business enterprise.The people see in produce practice, automate brought the tremendous convenience and the product quantities for people up of assurance, also eased the personnel's labor strength, reduce the establishment on the personnel. The target control of the hard realization in many complicated production lines, whole and excellent turn, the best decision etc, well-trained operation work, technical personnel or expert, governor but can judge and operate easily, can acquire the satisfied result. The research target of the artificial intelligence makes use of the calculator exactly to carry out, imitate these intelligences behavior, moderating the work through person's brain and calculators, with the mode that person's machine combine, for resolve the very complicated problem to look for the best path.We come in sight of the control that links after the electric appliances in various situation, that is already the that time generation past, now of after use in the mold a perhaps simple equipments of grass-roots control that the electric appliances can do for the low level only; And the PLC emergence also became the epoch-making topic, adding the vivid software control through a very and stable hardware, making the automation head for the new high tide.The PLC biggest characteristics lie in: The electrical engineering teacher already no longer electric hardware up too many calculations of cost, as long as order the importation that the button switch or the importation of the sensors order to link the PLC up can solve problem, pass to output to order the conjunction contact machine or control the start equipments of the big power after the electric appliances, but the exportation equipmentsdirect conjunction of the small power can.PLC internal containment have the CPU of the CPU, and take to have an I/ O for expand of exterior to connect a people's address and saving machine three big pieces to constitute, CPU core is from an or many is tired to add the machine to constitute, mathematics that they have the logic operation ability, and can read the procedure save the contents of the machine to drive the homologous saving machine and I/ Os to connect after pass the calculation; The I/ O add inner part is tired the input and output system of the machine and exterior link, and deposit the related data into the procedure saving machine or data saving machine; The saving machine can deposit the data that the I/ O input in the saving machine, and in work adjusting to become tired to add the machine and I/ Os to connect, saving machine separately saving machine RAM of the procedure saving machine ROM and dates, the ROM can do deposit of the data permanence in the saving machine, but RAM only for the CPU computes the temporary calculation usage of hour of buffer space.The PLC anti- interference is very and excellent, our root need not concern its service life and the work situation bad, these all problems have already no longer become the topic that we fail, but stay to our is a concern to come to internal resources of make use of the PLC to strengthen the control ability of the equipments for us, make our equipments more gentle.PLC language is not we imagine of edit collected materials the language or language of Cs to carry on weaving the distance, but the trapezoid diagram that the adoption is original after the electric appliances to control, make the electrical engineering teacher while weaving to write the procedure very easy comprehended the PLC language, and a lot of non- electricity professional also very quickly know and go deep into to the PLC.Is PLC one of the advantage above and only, this is also one part that the people comprehend more and easily, in a lot of equipments, the people have already no longer hoped to see too many control buttons, they damage not only and easily and produce the artificial error easiest, small is not a main error perhaps you can still accept; But lead even is a fatal error greatly is what we can't is tolerant of. New technique always for bringing more safe and convenient operation for us, make we a lot of problems for face on sweep but light, do you understand the HMI? Says the HMI here you basically not clear what it is, also have no interest understanding, change one inside text explains it into the touch to hold orman-machine interface you knew, it combines with the PLC to our larger space.HMI the control not only is reduced the control press button, increase the vivid of the control, more main of it is can sequence of, and at can the change data input to output the feedback with data, control in the temperature curve of imitate but also can keep the manifestation of view to come out. And can write the function help procedure through a plait to provide the help of various what lies in one's power, the one who make operate reduces the otiose error. Currently the HMI factory is also more and more, the function is also more and more strong, the price is also more and more low, and the noodles of the usage are wide more and more. The HMI foreground can say that think to be good.At a lot of situations, the list is a smooth movement that can't guarantee the equipments by the control of the single machine, but pass the information exchanges of the equipments and equipments to attain the result that we want. For example fore pack and the examination of the empress work preface, we will arrive wrapping information feedback to examine the place, and examine the information of the place to also want the feedback to packing. Pass the information share thus to make both the chain connect, becoming a total body, the match of your that thus make is more close, at each other attain to reflect the result that mutually flick.The PLC correspondence has already come more body now its value, at the PLC and correspondence between Places, can pass the communication of the information and the share of the data’s to guarantee that of the equipments moderates mutually, the result that arrive already to repair with each other. Data conversion the adoption RS232 between PLC connect to come to the transmission data, but the RS232 pick up a people and can guarantee 10 meters only of deliver the distance, if in the distance of 1000 meters we can pass the RS485 to carry on the correspondence, the longer distance can pass the MODEL only to carry on deliver.The PLC data transmission is just to be called a form to it in a piece of and continuous address that the data of the inner part delivers the other party, we, the PLC of the other party passes to read data in the watch to carry on the operation. If the data that data in the watch is a to establish generally, that is just the general data transmission, for example today of oil price rise, I want to deliver the price of the oil price to lose the oil ally on board, that is the share of the data; But take data in the watch for an instruction procedure that controls the PLC, that had the difficulty very much, for example you have to control one pedestal robot to pressthe action work that you imagine, you will draw up for it the form that a procedure combine with the data sends out to pass by.The form that information transport contain single work, the half a work and the difference of a workers .The meaning of the single work also is to say both, a can send out only, but a can receive only, for example a spy he can receive the designation of the superior only, but can't give the superior reply; A work of half is also 2 and can send out similar to accept the data, but can't send out and accept at the same time, for example when you make a phone call is to can't answer the phone, the other party also; But whole pair works is both can send out and accept the data, and can send out and accept at the same time. Be like the Internet is a typical example.The process that information transport also has synchronous and different step cent: The data line and the clock lines are synchronous when synchronous meaning lie in sending out the data, is also the data signal and the clock signals to be carry on by the CPU to send out at the same time, this needs to all want the specialized clock signal each other to carry on the transmission and connect to send, and is constrained, the characteristics of this kind of method lies in its speed very quick, but correspond work time of take up the CPU and also want to be long oppositely, at the same time the technique difficulty also very big. Its request lies in canting have an error margins in a dates deliver, otherwise the whole piece according to compare the occurrence mistake, this on the hardware is a bigger difficulty. Applied more and more extensive in some appropriative equipments, be like the appropriative medical treatment equipments, the numerical signal equipments...etc., in compare the one data deliver, its result is very good.And the different step is an application the most extensive, this receive benefit in it of technique difficulty is opposite and want to be small, at the same time not need to prepare the specialized clock signal, its characteristics to lie in, its data is partition, the long-lost send out and accept, be the CPU is too busy of time can grind to a stop sex to work, also reduced the difficulty on the hardware, the data throw to lose at the same time opposite want to be little, we can pass the examination of the data to observe whether the data that we send out has the mistake or not, be like strange accidentally the method, tired addition and eight efficacies method etc, can use to helps whether the data that we examine to send out have or not themistake occurrence, pass the feedback to carry on the discriminator.A line of transmission of the information contains a string of and combines the cent of: The usual PLC is 8 machines, certainly also having 16 machines. We can be at the time of sending out the data a send out to the other party, also can be 88 send out the data to the other party, and 8 differentiations are also the as that we say to send out the data and combine sends out the data. A speed is more and slowly, but as long as 2 or three lines can solve problem, and can use the telephone line to carry on the long range control. But combine the ocular transmission speed is very quick of, it is a string of ocular of 25600%, occupy the advantage in the short distance, the in view of the fact TTL electricity is even, being limited by the scope of one meter generally, it combine unwell used for the data transmission of the long pull, thus the cost is too expensive.Under a lot of circumstances we are total to like to adopt the string to combine the conversion chip to carry on deliver, under this kind of circumstance not need us to carry on to deposited the machine to establish too and complicatedly, but carry on the data exchanges through the data transmission instruction directly, but is not a very viable way in the correspondence, because the PLC of the other party must has been wait for your data exportation at the time of sending out the data, it can't do other works.When you are reading the book, you hear someone knock on door, you stop to start up of affair, open the door and combine to continue with the one who knock on door a dialogue, the telephone of this time rang, you signal hint to connect a telephone, after connecting the telephone through, return overdo come together knock on door to have a conversation, after dialogue complete, you continue again to see your book, this kind of circumstance we are called the interruption to it, it has the authority, also having sex of have the initiative, the PLC had such function .Its characteristics lie in us and may meet the urgently abrupt affairs in the operation process of the equipments, we want to stop to start immediately up of work, the whereabouts manages the more important affair, this kind of circumstance is we usually meet of, PLC while carry out urgent mission, total will keep the current appearance first, for example the address of the procedure, CPU of tired add the machine data etc., be like to stick down which the book that we see is when we open the door the page or simply make a mark, because we treat and would still need to continue immediately after book of see the behind.The CPU always does the affair that should do according to our will, but your mistake of give it an affair, it also would be same to do, this we must notice.The interruption is not only a, sometimes existing jointly with the hour several inside break, break off to have the preferred Class, they will carry out the interruption of the higher Class according to person's request. This kind of breaks off the medium interruption to also became to break off the set. The Class that certainly breaks off is relevant according to various resources of CPU with internal PLC; also following a heap of capacity size of also relevant fasten.The contents that break off has a lot of kinds, for example the exterior break off, correspondence in of send out and accept the interruption and settle and the clock that count break off, still have the WDT to reset the interruption etc., they enriched the CPU to respond to the category while handle various business. Speak thus perhaps you can't comprehend the internal structure and operation orders of the interruption completely also, we do a very small example to explain.Each equipment always will not forget a button, it also is at we meet the urgent circumstance use of that is nasty to stop the button. When we meet the Human body trouble and surprised circumstances we as long as press it, the machine stops all operations immediately, and wait for processing the over surprised empress recover the operation again. Nasty stop the internal I/ O of the internal CPU of the button conjunction PLC to connect up, be to press button an exterior to trigger signal for CPU, the CPU carries on to the I/ O to examine again, being to confirm to have the exterior to trigger the signal, CPU protection the spot breaks off procedure counts the machine turn the homologous exterior I/ O automatically in the procedure to go to also, be exterior interruption procedure processing complete, the procedure counts the machine to return the main procedure to continue to work. Have 1:00 can what to explain is we generally would nasty stop the button of exterior break off to rise to the tallest Class, thus guarantee the safety.When we are work a work piece, giving the PLC a signal, counting PLC inner part the machine add 1 to compute us for a day of workload, a count the machine and can solve problem in brief, certainly they also can keep the data under the condition of dropping the electricity, urging the data not to throw to lose, this is also what we hope earnestly.The PLC still has the function that the high class counts the machine, being us while accept some dates of high speed, the high speed that here say is the data of the in all aspects tiny second class, for example the bar code scanner is scanning the data continuously, calculating high-speed signal of the data processor DSP etc., we will adopt the high class to count the machine to help we carry on count. It at the PLC carries out the procedure once discover that the high class counts the machine to should of interruption, will let go of the work on the hand immediately. The trapezoid diagram procedure that passes by to weave the distance again explains the high class for us to carry out procedure to count machine would automatic performance to should of work, thus rise the Class that the high class counts the machine to high one Class.You heard too many this phrases perhaps:" crash", the meaning that is mostly is a workload of CPU to lead greatly, the internal resources shortage etc. the circumstance can't result in procedure circulate. The PLC also has the similar circumstance, there is a watchdog WDT in the inner part of PLC, we can establish time that a procedure of WDT circulate, being to appear the procedure to jump to turn the mistake in the procedure movement process or the procedure is busy, movement time of the procedure exceeds WDT constitution time, the CPU turn but the WDT reset the appearance. The procedure restarts the movement, but will not carry on the breakage to the interruption.The PLC development has already entered for network ages of correspondence from the mode of the one, and together other works control the net plank and I/ O card planks to carry on the share easily. A state software can pass all se hardwires link, more animation picture of keep the view to carries on the control, and cans pass the Internet to carry on the control in the foreign land, the blast-off that is like the absolute being boat No.5 is to adopt this kind of way to make airship go up the sky.The development of the higher layer needs our continuous effort to obtain. The PLC emergence has already affected a few persons fully, we also obtained more knowledge and precepts from the top one experience of the generation, coming to the continuous development PLC technique, push it toward higher wave tide.可编程控制器技术讨论与未来发展T.J.拜尔斯(电子测试设备原理及应用普林斯顿大学)随着时代的发展,当今的技术也日趋完善、竞争愈演愈烈;单靠人工的操作已不能满足于目前的制造业前景,也无法保证更高质量的要求和高新技术企业的形象。
- 1、下载文档前请自行甄别文档内容的完整性,平台不提供额外的编辑、内容补充、找答案等附加服务。
- 2、"仅部分预览"的文档,不可在线预览部分如存在完整性等问题,可反馈申请退款(可完整预览的文档不适用该条件!)。
- 3、如文档侵犯您的权益,请联系客服反馈,我们会尽快为您处理(人工客服工作时间:9:00-18:30)。
Beer filling, Gland machine PLC control system1.IntorductionMalt beer production process is divided into manufacturing, manufacturing wort, before fermentation, after fermentation, filtration sterilization, packaging, and so few procedures. Beer filling, Gland part of a packaging machine processes. The membrane filtration of beer after the pipeline into the rotary Jiugang, then the valve into the bottle of wine, Gland, was bottled beer. Beer filling, Gland machine's efficiency and degree of automation direct impact on the level of beer production.China's beer industry to meet the increasing scale of production and the demand for beer modern high-speed filling machinery filling the requirements of domestic beer manufacturers are actively seeking to transform the unit or the filling of beer production equipment, making it a good use Performance, advanced technology and high production efficiency and operating a safe and secure, low maintenance costs of the modernization of beer filling machine.2. Filling beer, Gland principle and control aircraft partsLiquid filling machine by filling principle can be divided into atmospheric filler,filling machines and vacuum pressure on the filling machine. Beer filling,Gland-filling method used pressure is higher than the atmospheric pressure under the filling, storage of the cylinder pressure than the pressure of the bottle, beer bottle into the liquid on pressure.Technology at home and abroad to achieve the filling line is basically: The Rotary Jiugang the rotating movement, placed in Jiugang slots on the empty bottles through the machinery will be fixed at the upper Jiugang vacuum valve to open, closed Vacuum bottles for good treatment, Bozhuan stem from operating, open the valve of the bottle filling CO2 gases, vacuum convex .Round to open the vacuum valve, the bottle will air mixed with CO2 out of gas, open the valve again, the CO2gas bottle filling, the filling valve on the pressure valve in the bottle close to back-pressure gas pressure at the open-Jiuye Pingbi into the bottle, through pneumatic or electrical control filling valve to achieve the filling of beer.Today's advanced international beer filling, Gland machine control system mainly by the photoelectric switch position detection part and take the bottles with, Jiugang speed part, dominated by the PLC, touch screen and other components. Filling, Gland of the mechanical structure and PLC programmable control devices, frequency stepless speed regulation, human-computer interface, and other modern means of complete automatic control technology, the combination of a mechanical and electrical integration.3. Controlled part of the programmeMany domestic beer manufacturers are now using the filling, Gland of the control system of uneven degree of automation; button and all the manual switch technology have set up operations in a box on the panel, PLC controller for the majority of Japanese companies or OMRON Mitsubishi's early products, equipment chain of control, less protection settings, plus the beer filling the scene poor environment, humidity, such as contact with the switch contacts serious corrosion, the system's signal detection of the high failure rate, resulting in equipment control system Operation of low reliability, the normal operation of equipment, such as short-cycle phenomenon.To the actual transformation of the Dandong Yalu River Brewery Co., Ltd. of filling, Gland machine control system as an example, the transformation of methods to clarify the control of such equipment thinking and ideas, according to the scene of the actual process conditions, to prepare the operation of the PLC Procedures. For beer filling, Gland control system of the actual situation and in accordance with the actual process conditions at the scene, re-design of the equipment of the PLC control system. This transformation of the same methods and ideas can be applied to other liquids and the transformation of filling equipment.3.1 system hardware configurationJapan's Mitsubishi Corporation to use the FX2N128MRPLC use the system to replace the original 2-OMRON's C60P PLC, the original system of the PLC is due to old models, and computer on-line communications need to configure special converters, the system need to increase the external I / O input points , The extension of spare parts more difficult to find. FX2N128MRPLC is an integrated 128-point I / O controller of the box, a computing speed, command rich, high-cost performance, on-line programming simple and easy extension of the advantages of the Mitsubishi FX series, features the strongest small controller .(1) by the Mitsubishi 900 series of 970 GOT human-computer touch screen system to replace the original use of the button panel display equipment and monitor the operation of operating parameters. 970GOT HMI for the 16-color high-brightness significantly, through the convergence of connectivity and FX2N128MRPLC directly connected to the CPU, achieving rapid response. Has many maintenance features, such as the list-editing features, ladder monitoring (troubleshooting) function, the system monitoring functions to find fault and maintenance of PLC Systems.(2) filling, Gland of the frequency converter in the transformation of no replacement, on-site detection signal means-testing is still used switch, switch for detecting long-term work in the humidity of the great occasions, the choice of capacitive proximity switches, according to PLC I / O terminal of the connection mode, select the type of close PNP switch, the control system of Figure 1.3.2Systems ProgrammingPLC controller programming focus and the core is around Jiugang the rotation speed control and Jiugang on 60 bottles of detecting the location of the displaced, broken bottles, empty bottles at the location of testing and related displacement filling Such as control valves. The bottles displacement of testing procedures, using a Mitsubishi PLC in the left command.Figure 1 control system structure diagram .Bottles displacement of detection, using the left-PLC command, whichcommands the whole of one of the core control procedures, the main electrical switch detection and bottles at the bottle simultaneously detect mobile, the main motor to every week, just to the corresponding Jiugang Have a bottle of, PLC unit within the internal correspondence that 60 bottles of the unit for the M500 ~ M559, the number of units by the first letter K is set to K60, with each change in a second letter K is set to K1, M50 Reaction of the empty bottles in the short position, and detect the location of the motor speed to go on the frequency shift in the corresponding unit within the built-in "1" or "0", control valves and the corresponding mixing caps The motor stopped and opened. Continuous detection system in place after the 90 empty bottles, stop stirring caps the motor running, testing the number of bottles in accordance with the user's requirements can be arbitrary.A bottle of detection. Rotary Jiugang through pressure to back pressure with the bottle of liquor in the process of empty bottles in the back-pressure, because the bottle itself may crack and other reasons leading to a sudden burst bottles, which need to detect the location of unexploded bottle bottle, in this bottle - The position opened purge solenoid valves, compressed air out, broken bottles at the bottle-blowing from the position in a row after the purge and several bottles of the electromagnetic valve open jet, a high-pressure spray Shuizhu, in the break Bottle position around a few bottles of spray bottles in a row.Detection of broken bottles and bottle-detection switch simultaneously detect movement of breaking bottles, to the main motor of each week, precisely corresponding Jiugang passed a bottle of, PLC unit within the internal correspondence that 20 broken bottles at the unit for the M600 ~ M619, unit With the number of the first letter K is set to K20, with each change in a second letter K is set to K1, M52 response to the location of the broken bottles and detected the location of the motor speed to the frequency shift continue, In the corresponding unit within the built-in "1" or "0", control and the corresponding jet purge solenoid valve opened and stopped. Continuous Spray and purge solenoid valve open to listen, time stopped in accordance with technological requirements can be arbitrary.System security is to control access to the caps simultaneously tracking, not onlyaccurately detect the electrical switching speed detection, the broken bottles into the bottle and detection switch detection switch three conditions.970GOT human-computer touch-screen terminals operated by the software company's Mitsubishi GT WORKS package, which is a GT Designer with the entire GOT9000 series of graphics software packages. The package is simple, prior to a personal computer simulation on the configuration and debug, after the man-machine operators to download terminals. At the same time, because the man-machine interface and a touch-screen role, will set common switch on the screen to facilitate the operation. And also to increase the number of features, such as setting alarm information.4After transformation control systemSystem at the normal operation of the machine for automatic control, in accordance with bottles into and out of the bottle for lack or slow pace set by running into the bottle stall bottles, no less than a bottle cap, automatic washing bottles burst, filling automatic back-pressure position , Covered under the system automatically lose covered a stop and safety protection, such as the coordination of action interlock. All the original button after the operation of the touch screen on.5Detection of the state control system monitoringDetection switch into the bottle and break bottles detection switch bottles of pressure by testing each part of the small metal plates above the location of a photoelectric pulse output, a further PLC acquisition, as each bottle of the pressure above the small metal plates is the location of activities , In the machine running after some time, some pressure above the small bottles of iron tablets and detection switch in the location of displacement, resulting in detection switch mistaken judgement, if not for the judgement of bottles of bottles, bottle explosion Lou Jian, misuse, such as the seizure of output errors So that the PLC have mistaken action, such as a back-pressure, unexploded bottle blowing, washing, stirring cap control systemmalfunction, such as failure phenomenon.Before the transformation of the daily production process, encountered this phenomenon, the operatives could only switch to the various functional or manual control buttons reach the stall so that the equipment work in the absence of monitoring state, the machine lost control function. Caused a lot of production of raw materials such as gas, water, wine waste. Only in the production of intermittent, can be fitter and maintenance electrician in accordance with the detection of small switch on the light-emitting diodes and anti-displacement by adjusting the distance only 5 ~ 8 mm detection switch installation location, and switch to fix detection of small metal plates Gap. This means of detection is very backward, after adjustment reaction to the results, timely response can not be adjusted results.In view of this testing situation, after the transformation of the filling, Gland control system configuration, this part of a new detection and integration in human-computer touch screen, complete bottle of detection.In human-computer touch screen interface on the page display, respectively, at customs, such as electromagnetic motor mixing valve switch state are in different colors to show, very intuitive.Increase the system's functions is to ensure the irrigation of the machine-Gland normal operation of automated control system specifically designed to.6 Concluding remarksAfter the transformation of the control system will greatly simplify the complicated mechanical structure, the running and control of inspection, the degree of automation systems meet the design requirements, greatly reducing the operational strength of the labor so that the shrub-like beer output than in the past Raising more than 30 percent, greatly reduce the failure rate. Embodies the modern equipment of automatic control technology. In the digestion and absorption of today's industrial control on the basis of advanced technology innovation, development of domestic technology from the most advanced filling control system.啤酒灌装、压盖机PLC控制系统1. 引言啤酒生产过程分为麦芽制造、麦芽汁制造、前发酵、后发酵、过滤灭菌、包装等几道工序。