流化床反应器概述
流化床反应器的机理

流化床反应器的机理
流化床反应器是一种常用于化学反应、热传递和质量传递的装置。
它采用颗粒物料床动态流化的方式来实现传递过程,具有反应速度快、传热传质效率高等优点。
其机理主要包括流化床的流动特性、颗粒物料的运动规律和反应过程中的热传递和质量传递。
流化床反应器中,床层物料通过流体动力学作用来实现动态流化。
在床层内,颗粒物料分散在气流中,并以不规则的运动方式进行流动,形成了类似于液体的流动形态。
这种流动方式对于反应过程有利,因为它可以增加反应物料的接触面积,提高反应速度。
在流化床反应器中,颗粒物料运动的规律对于反应过程也十分关键。
由于颗粒物料之间的碰撞和摩擦作用,会产生不同的运动方式,如滚动、滑动、碰撞等。
这些物料的运动方式和速度对于反应过程和传递过程都有着重要的影响。
例如,反应物料的分散程度和流动速度会影响反应速度和传质效率,而颗粒物料的摩擦和碰撞会产生热量,影响反应过程的温度。
在流化床反应器中,反应过程的热传递和质量传递也是重要的机理之一。
由于床层内的颗粒物料和气流之间的接触,会产生热量和质量的传递。
这种传递方式可以有效地将反应物料的热量和质量传递到床层内部,并提高反应速度和传递效率。
流化床反应器的机理主要包括流化床的流动特性、颗粒物料的运动规律和反应过程中的热传递和质量传递。
通过这些机理的协同作用,流化床反应器可以实现快速反应、高效传递和稳定运行等优点,是一种十分优秀的化学反应装置。
流化床反应器
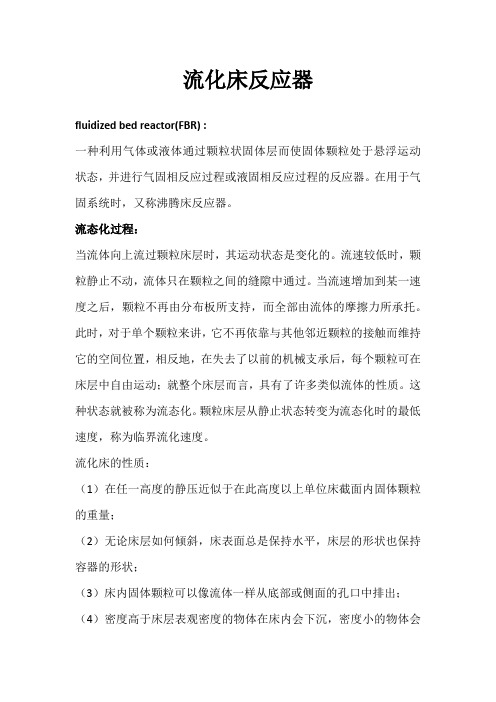
流化床反应器fluidized bed reactor(FBR) :一种利用气体或液体通过颗粒状固体层而使固体颗粒处于悬浮运动状态,并进行气固相反应过程或液固相反应过程的反应器。
在用于气固系统时,又称沸腾床反应器。
流态化过程:当流体向上流过颗粒床层时,其运动状态是变化的。
流速较低时,颗粒静止不动,流体只在颗粒之间的缝隙中通过。
当流速增加到某一速度之后,颗粒不再由分布板所支持,而全部由流体的摩擦力所承托。
此时,对于单个颗粒来讲,它不再依靠与其他邻近颗粒的接触而维持它的空间位置,相反地,在失去了以前的机械支承后,每个颗粒可在床层中自由运动;就整个床层而言,具有了许多类似流体的性质。
这种状态就被称为流态化。
颗粒床层从静止状态转变为流态化时的最低速度,称为临界流化速度。
流化床的性质:(1)在任一高度的静压近似于在此高度以上单位床截面内固体颗粒的重量;(2)无论床层如何倾斜,床表面总是保持水平,床层的形状也保持容器的形状;(3)床内固体颗粒可以像流体一样从底部或侧面的孔口中排出;(4)密度高于床层表观密度的物体在床内会下沉,密度小的物体会浮在床面上;(5)床内颗粒混合良好,因此,当加热床层时,整个床层的温度基本均匀。
一般的液固流态化,颗粒均匀地分散于床层中,称之为“散式”流态化;一般的气固流态化,气体并不均匀地流过颗粒床层,一部分气体形成气泡经床层短路逸出,颗粒则被分成群体作湍流运动,床层中的空隙率随位置和时间的不同而变化,因此这种流态化称为“聚式”流态化。
与固定床反应器相比,流化床反应器的优点是:①可以实现固体物料的连续输入和输出;②流体和颗粒的运动使床层具有良好的传热性能,床层内部温度均匀,而且易于控制,特别适用于强放热反应。
但另一方面,由于返混严重,可对反应器的效率和反应的选择性带来一定影响。
再加上气固流化床中气泡的存在使得气固接触变差,导致气体反应得不完全。
因此,通常不宜用于要求单程转化率很高的反应。
流化床反应器概述
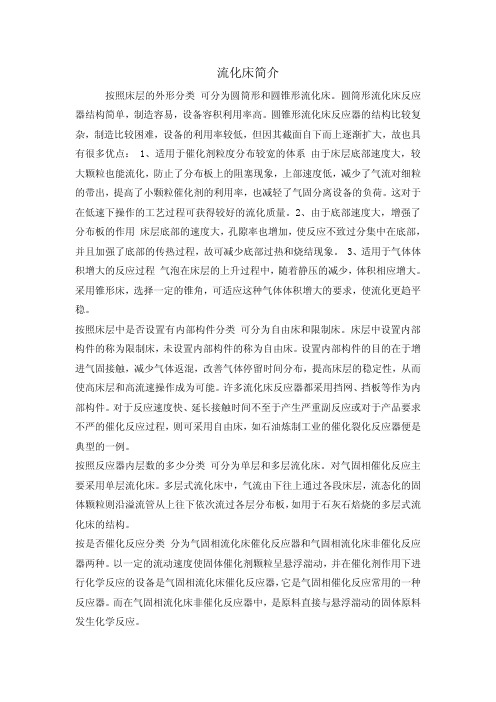
流化床简介按照床层的外形分类可分为圆筒形和圆锥形流化床。
圆筒形流化床反应器结构简单,制造容易,设备容积利用率高。
圆锥形流化床反应器的结构比较复杂,制造比较困难,设备的利用率较低,但因其截面自下而上逐渐扩大,故也具有很多优点: 1、适用于催化剂粒度分布较宽的体系由于床层底部速度大,较大颗粒也能流化,防止了分布板上的阻塞现象,上部速度低,减少了气流对细粒的带出,提高了小颗粒催化剂的利用率,也减轻了气固分离设备的负荷。
这对于在低速下操作的工艺过程可获得较好的流化质量。
2、由于底部速度大,增强了分布板的作用床层底部的速度大,孔隙率也增加,使反应不致过分集中在底部,并且加强了底部的传热过程,故可减少底部过热和烧结现象。
3、适用于气体体积增大的反应过程气泡在床层的上升过程中,随着静压的减少,体积相应增大。
采用锥形床,选择一定的锥角,可适应这种气体体积增大的要求,使流化更趋平稳。
按照床层中是否设置有内部构件分类可分为自由床和限制床。
床层中设置内部构件的称为限制床,未设置内部构件的称为自由床。
设置内部构件的目的在于增进气固接触,减少气体返混,改善气体停留时间分布,提高床层的稳定性,从而使高床层和高流速操作成为可能。
许多流化床反应器都采用挡网、挡板等作为内部构件。
对于反应速度快、延长接触时间不至于产生严重副反应或对于产品要求不严的催化反应过程,则可采用自由床,如石油炼制工业的催化裂化反应器便是典型的一例。
按照反应器内层数的多少分类可分为单层和多层流化床。
对气固相催化反应主要采用单层流化床。
多层式流化床中,气流由下往上通过各段床层,流态化的固体颗粒则沿溢流管从上往下依次流过各层分布板,如用于石灰石焙烧的多层式流化床的结构。
按是否催化反应分类分为气固相流化床催化反应器和气固相流化床非催化反应器两种。
以一定的流动速度使固体催化剂颗粒呈悬浮湍动,并在催化剂作用下进行化学反应的设备是气固相流化床催化反应器,它是气固相催化反应常用的一种反应器。
流化床反应器ppt课件
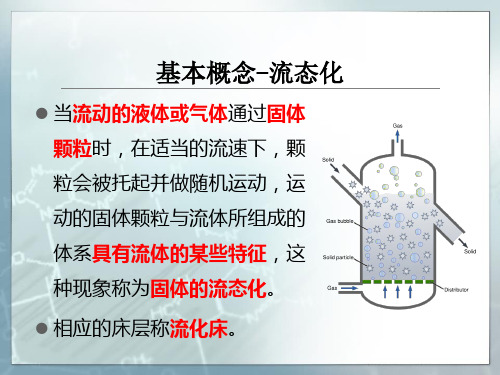
均密度。
颗粒带出速度 u :
t 流化床中流体速度的上限,流体对粒子的曳
力与粒子的重力相等,粒子将被气流带走。
对于球形颗粒等速沉降时,可得出下式:
4 d p ( p f ) g
ut
f D
3
1
2
式中
D
过程原理
过程原理
过程原理
典型装置
壳体
气体分布装置
换热器
内部构件
催化剂的加入与卸
出装置
气固分离装置
流化床反应器的相关参数
流化过程床层压降变化
临界流化速度 u mf(起始流化速度,也称最低流化速度):颗
粒层由固定床转化为流化床时流体的表现速度。
小颗粒
大颗粒
经验公式
umf
d ( p f ) g ( R 20 )
▪ 有气-固相流化床催化反应器和气-固相流化床
非催化反应器两种
▪ 以一定的流动速度使固体催化剂颗粒呈悬浮湍
动,并在催化剂作用下进行化学反应的设备称
为气-固相流化床催化反应器(常简称为流化
床),它是气-固相催化反应常用的一种反应器
▪ 而在气-固相流化床非催化反应器中,是原料气
直接与悬浮湍动的固体原料发生化学反应。
e
1650 f
u
2
mf
2
p
d p ( p f ) g
( Re 1000 )
24.5 f
umf 0.00923
d
1.82
p
( p f )
0.88
f
0.06
流化床反应器

概述
流化床反应器 (fluidized bed reactor) 是利用气体或液体通过颗粒状固体层而使固体颗粒处 于悬浮运动状态,并进行气固相反应过程或液固相反应 过程的反应器。在用于气固系统时,又称沸腾床反应器 流化床反应器通常为一直立的圆筒型容器,容器下部 一般设有分布板,细颗粒状的固体物料装填在容器内,流 体向上通过颗粒层,当流速足够大时,颗粒浮起,呈现流 化状态。由于气固流化床内通常出现气泡相和乳化相,状 似液体沸腾,因而流化床反应器亦称为沸腾床反应器。
△P-u关系图的应用:
• 观察流化床的压力降变化可以判断流化质量。 • 如:正常操作时,压力降的波动幅度一般较小, 波动幅度随流速的增加而有所增加。在一定的流 速下,如果发现压降突然增加,而后又突然下降, 表明床层产生了节涌(腾涌)现象。形成气栓时 压降直线上升,气栓达到表面时料面崩裂,压降 突然下降,如此循环下去。这种大幅度的压降波 动破坏了床层的均匀性,使气固接触显著恶化, 严重影响系统的产量和质量。有时压降比正常操 作时低,说明气体形成短路,床层产生了沟流现 象。
5
1/ 2 ep
当: 500 Rep 2 10 时 CD 0.43
这样,可得到ut计算式:
当Rep 0.4时 ut
2 gd p ( s f )
18
0.5 ep
2d p ( s f ) gR 当0.4 Rep 500时 ut 15 f
对球形粒子作力平衡:
6
d s g
3 p
6
d f g CDS
3 p
4
2 dp (
f ut2
2
)
CDS 为单颗粒的曳力系数 式中:
流化床反应器概念
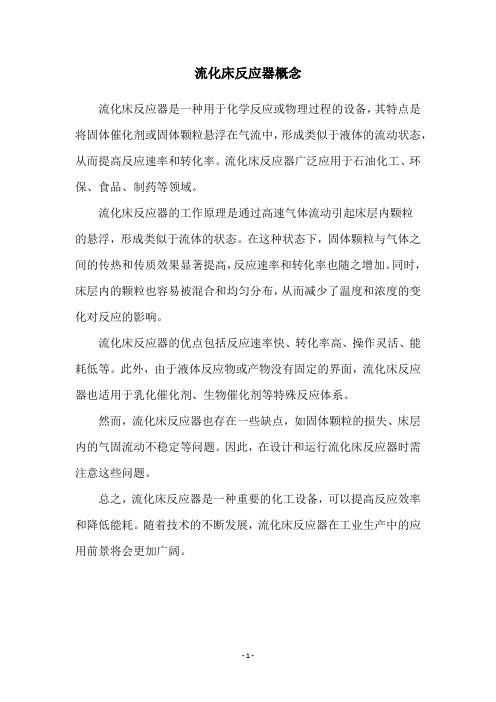
流化床反应器概念
流化床反应器是一种用于化学反应或物理过程的设备,其特点是将固体催化剂或固体颗粒悬浮在气流中,形成类似于液体的流动状态,从而提高反应速率和转化率。
流化床反应器广泛应用于石油化工、环保、食品、制药等领域。
流化床反应器的工作原理是通过高速气体流动引起床层内颗粒
的悬浮,形成类似于流体的状态。
在这种状态下,固体颗粒与气体之间的传热和传质效果显著提高,反应速率和转化率也随之增加。
同时,床层内的颗粒也容易被混合和均匀分布,从而减少了温度和浓度的变化对反应的影响。
流化床反应器的优点包括反应速率快、转化率高、操作灵活、能耗低等。
此外,由于液体反应物或产物没有固定的界面,流化床反应器也适用于乳化催化剂、生物催化剂等特殊反应体系。
然而,流化床反应器也存在一些缺点,如固体颗粒的损失、床层内的气固流动不稳定等问题。
因此,在设计和运行流化床反应器时需注意这些问题。
总之,流化床反应器是一种重要的化工设备,可以提高反应效率和降低能耗。
随着技术的不断发展,流化床反应器在工业生产中的应用前景将会更加广阔。
- 1 -。
流化床反应器
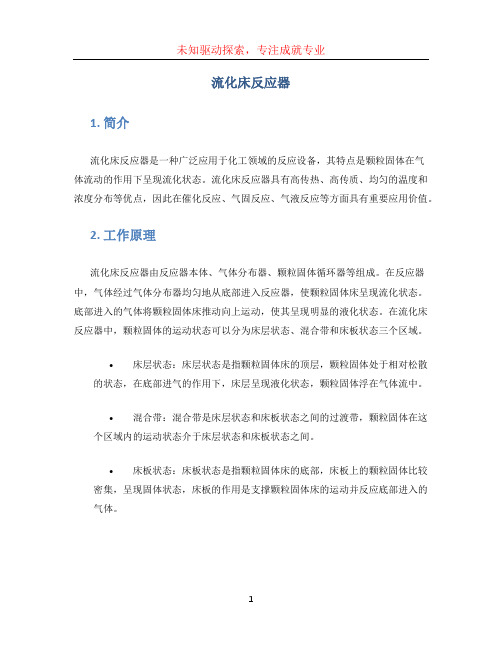
流化床反应器1. 简介流化床反应器是一种广泛应用于化工领域的反应设备,其特点是颗粒固体在气体流动的作用下呈现流化状态。
流化床反应器具有高传热、高传质、均匀的温度和浓度分布等优点,因此在催化反应、气固反应、气液反应等方面具有重要应用价值。
2. 工作原理流化床反应器由反应器本体、气体分布器、颗粒固体循环器等组成。
在反应器中,气体经过气体分布器均匀地从底部进入反应器,使颗粒固体床呈现流化状态。
底部进入的气体将颗粒固体床推动向上运动,使其呈现明显的液化状态。
在流化床反应器中,颗粒固体的运动状态可以分为床层状态、混合带和床板状态三个区域。
•床层状态:床层状态是指颗粒固体床的顶层,颗粒固体处于相对松散的状态,在底部进气的作用下,床层呈现液化状态,颗粒固体浮在气体流中。
•混合带:混合带是床层状态和床板状态之间的过渡带,颗粒固体在这个区域内的运动状态介于床层状态和床板状态之间。
•床板状态:床板状态是指颗粒固体床的底部,床板上的颗粒固体比较密集,呈现固体状态,床板的作用是支撑颗粒固体床的运动并反应底部进入的气体。
3. 应用领域3.1 催化反应流化床反应器在催化反应方面有着广泛的应用。
其优点是具有较大的接触面积和较高的传质速率,可以提高催化反应的反应速率和转化率。
此外,流化床反应器还具有温度均匀和活性物质的均匀分布等特点,从而有助于提高催化反应的选择性和稳定性。
常见的催化反应包括催化裂化、催化重整、催化加氢等。
3.2 气固反应流化床反应器在气固反应方面也有着重要的应用。
气固反应是指气体与固体之间发生的化学反应。
流化床反应器由于其颗粒固体床的特点,使气体与固体之间的接触充分,从而实现高效的气固反应。
常见的气固反应包括氧化反应、还原反应、氯化反应等。
3.3 气液反应流化床反应器在气液反应方面也有广泛的应用。
气液反应是指气体与液体之间发生的化学反应。
流化床反应器可以通过调节气体和液体的进料速度和浓度,实现气液相的均匀分布和快速混合。
流化床反应器概念

流化床反应器概念
流化床反应器是一种广泛应用于化学工业中的反应器,它是一种高效
的反应器,能够实现高效的传质和反应。
流化床反应器的主要特点是
反应物在反应器中呈现出流化状态,即反应物在反应器中呈现出类似
于流体的状态,这种状态下反应物能够充分混合,反应速率也会得到
提高。
流化床反应器的主要构成部分包括反应器本体、气体分配器、床层材料、反应物进料口、产物出料口等。
反应器本体是流化床反应器的主
要部分,它通常由一个圆柱形的容器构成,容器内部填充有一定的床
层材料。
气体分配器是用来分配气体的装置,它通常位于反应器底部,能够将气体均匀地分配到床层中。
床层材料是反应器中填充的材料,
它通常是一些具有良好流动性的颗粒状物质,如砂子、石英砂等。
反
应物进料口和产物出料口则是用来进出反应物和产物的装置。
流化床反应器的工作原理是,反应物进入反应器后,通过气体分配器
将气体均匀地分配到床层中,使床层中的颗粒物质呈现出流化状态。
在这种状态下,反应物能够充分混合,反应速率也会得到提高。
反应
物在床层中反应后,产生的产物会随着气体一起流动,最终通过产物
出料口排出反应器。
流化床反应器具有许多优点,如反应速率快、传质效率高、反应物质
料利用率高等。
同时,流化床反应器也存在一些缺点,如床层材料易
于磨损、反应器内部易于积垢等。
因此,在使用流化床反应器时,需
要注意反应器的维护和清洗。
总之,流化床反应器是一种高效的反应器,能够实现高效的传质和反应。
它在化学工业中有着广泛的应用,是一种非常重要的反应器类型。
流化床反应器简介

流化床分类: 散式流化床聚Biblioteka 流化床液固流化为 散式流化
颗粒与流体之间的密度差是它们的主要 区别
气固流化为 聚式流化
散式流化床
以气泡形式夹带少量颗粒穿过床
层向上运动的不连续的气泡称为 气泡相
图1-1 流化床的模型
聚式流化床
颗粒浓度与空隙率分布 较为均匀且接近初始流 态化状态的连续相,称 为乳化相。
旋风分离器
塞阀
图1-4 塞阀的剖视图
翼阀
翼阀的作用:就是避免由于这 一压差的存在而使催化剂由料 腿倒窜。正常的情况下,翼阀 的翼板和阀座处于良好密阀的 状态。当料腿内的催化剂量蓄 积到料腿内的静压超过旋风器 的压降,以及翼阀上方床层静 压及找开翼阀所需压力这三者 之和时,翼阀及时自行打开, 料腿内的催化剂流入床层。若 料腿内的静压低于上述三者压 力之和时,翼阀自行关闭,防 止催化剂倒窜。
• 分布器 • 换热器 • 旋风分离器 • 塞阀 • 翼阀
分布器
图1-3-1平板型分布板
图1-3-2 拱型分布板
分布器的作用
• 气体分布器是流化床反应器的一个重要的 构件,气体分布器位于流化床底部
• 支撑全部催化剂颗粒,其作用是将反应气 体均匀地送入流化床
• 保证良好的起始流化条件和稳定操作状态, 其引发流化,维持床层颗粒连续运动和均 匀分布气体的作用。
气-固流化床反应器结构
气体 料锁
加料口 换热介质
循环管 换热介质 固体粒子
……….. ………. ..
气体
旋风分离器 壳体
内部构件 换热器 卸料口 气体分布板 预分布器
3
主体设备
壳 体 壳体 主要是保证流化过程局限在一定范围内 进行,对于存在有强烈放热或吸热过程, 保证热量不散失或少散失。
流化床反应器-资料

: 1 .7 3 5(d Pu m f)2 1 5 0 (1 2 3m f)(d Pu m f) d P 3(P 2)g(7-2)
Sm f
Sm f
对于小粒子,可忽略左第一项:
u m f 1 S5 d 0 P2(P)(1 m 3fm f)g
气
床
流
流
床
床
态
(散式)
(聚式)
化
输 送
L0
L Lmf
L Lf
L Lf
流体
流体
流体
流体
流体 流体
2020/5/31
• 固定床阶段:气流速率较小,从粒子空隙间通过,床层不动。 • 起始流化床:随着流速渐增,粒子间空隙率将开始增加,床层体
积逐渐增大,当流速达到某一限值,床层刚刚能被流体托起时, 床内粒子就开始流化起来了,此时的流化床称为起始流化床。 • 散式流化床:流速进一步提高时,如果床层膨胀均匀且波动很小 , 粒子在床内的分布也比较均匀, 故称作散式流化床,也称液 体流化床。 • 聚式流化床:对气-固系统,气速达到起始鼓泡速度umf后,通常 将出现气泡,气速愈高,气泡的聚并及造成的扰动亦愈剧烈,使 床层波动频繁,此形态的流化床称聚式流化床,也称鼓泡床。 • 气流输送阶段:气流速率大到使固体随之带出。
ut dP 2( 1 P 8 )g ut 2 4 25(P )2g2 1/3
R eP0.4 0.4R eP500
(7-14) (7-15)
u t 3 .1 d P (P)g 1 /2
5 0 0R eP2 0 0 0 0 0 (7-16)
带出速度也可采用经验式计算.如:式(7-19)等.
7.1流化床反应器

µ
5.3 × 10 −3 × 0.733 × 10 −3 × 0.058 = = 6.09 × 10 − 4 < 20 3.7 × 10 − 4
(3)计算ut: )计算
• 如果全床空隙率均匀,处于压力最低处的床顶 如果全床空隙率均匀, 粒子将首先被带出,故取最小粒子 粒子将首先被带出,故取最小粒子dp=10µm计 µ 计 算。设Re<0.4
再 生
石油 催化 空气 剂输 消除内扩散;固定床因有△ 限制不能用 消除内扩散;固定床因有△P限制不能用 送
3. 强放热反应 氧化反应:萘氧化剂制苯酐需熔盐冷却; 氧化反应:萘氧化剂制苯酐需熔盐冷却; 丙烯氨氧化法制丙烯腈
流化床反应器的优点:( 流态化技术) 流化床反应器的优点:( 流态化技术)
• 传热效能高,且床内温度易于维持均匀; 传热效能高,且床内温度易于维持均匀; • 大量固体粒子可方便地往来输送; 大量固体粒子可方便地往来输送; • 由于粒子细,可消除内扩散阻力,充分发挥催 由于粒子细,可消除内扩散阻力, 化剂的效能。 化剂的效能。 缺点: 缺点: 1. CSTR:转化率甚至小于CSTR(气泡短路) :转化率甚至小于 (气泡短路) 2. 颗粒磨损:催化剂要贱,设备要被磨 颗粒磨损:催化剂要贱, 3. 气流出口分离粉尘,回收系统麻烦 气流出口分离粉尘, 4. 副反应:∵RTD太宽 副反应: 太宽
压力波动 达极大值 聚式 压力波动 趋于0 快床 Uc 相变 泡分散相 湍床 Cluster 分散相 Ut 夹带
散式
0
Umf
Ub 鼓泡床
快 床 颗 粒 的 径 向 分 布
颗粒含率 实际分布 模型分布 高 度
气流输送 快床 湍流床 鼓泡流化床 0.2 0.4 0.6 密度
第七章 流化床反应器

ΔPd 为床层压
ΔPb 的 10%~20%,开孔率约 1%。 u or :
2 Δp d
设计筛孔分布板,先求小孔阻力系数,在求小孔气速
' ( u or = c d
ρ
π
)1 / 2
定出开孔数
N or :
2 N or = u o /( d or or ) 4
2.内部构件:为了传热或控制气——固间接触,常在床内设置内部构件。 7.1-6 乳相的动态
500 < Rep < 200,000
130
化学反应工程课程讲稿
CD =
24 0.8431g
φs
Rep < 0.05 Rep 2 × 10 3 < Rep < 2 × 10 5
0.065 C D = 5.31 − 1.88φ s
Rep < 0.4
可利用公式,可用来考察对于大,小粒子范围的大小 细粒子
U br
u br = 0.711( gd b )1 / 2
d b = 0.853 1 + 0.272(U − U mf )
[
]
1/ 3
(1 + 0.0684 ρ )1.21
0.7
(U − U mf ) ⎡ At 4 / 7 ⎤ 1.5 g 1 / 7 + 1 ( ) ⎥ d b = 1.28 ⎢ 2/7 no g 0.3 ⎢ (U − U mf ) ⎥ ⎣ ⎦
3
(二维床)
(三维床)
Rc , Rb 分别为气泡云及气泡的半径
三维床指一般的圆柱形床,二维床为截面狭长的扁形床 气泡中气体的穿流量 q
q = 4u mf Rb = 4u f ε mf Rb
(二维床 )
流化床知识培训

(一)、正常的开车程序是: )、正常的开车程序是: 正常的开车程序是
流化床设备知识培训
2009.6
第一章基础知识
一、流化床反应器概念: 流化床反应器概念: 一种利用气体或液体通过颗粒状固体 层而使固体颗粒处于悬浮运动状态,并进 行气固相反应过程或液固相反应过程的反 气固相反应过程或液固相反应过程的 应器。在用于气固系统时,又称沸腾床反 应器。在用于气固系统时,又称沸腾床反 应器。
近年来,细颗粒和高气速的湍流流化 床及高速流化床均已有工业应用。在气 速高于颗粒夹带速度的条件下,通过固 体的循环以维持床层,由于强化了气固 两相间的接触,特别有利于相际传质阻 力居重要地位的情况。但另一方面由于 大量的固体颗粒被气体夹带而出,需要 进行分离并再循环返回床层,因此,对 气固分离的要求也就很高了。
1.气固相流化床催化反应器。 1.气固相流化床催化反应器。 一定的流动速度使固体催化剂颗粒呈悬浮湍 动,并在催化剂作用下进行化学反应的设备是 气固相流化床催化反应器,它是气固相催化反 应常用的一种反应器。 2. 气固相流化床非催化反应器。 原料直接与悬浮湍动的固体原料发生化学反 应。
四、流化床的操作与控制
高低并列式流化床1
高低并列式流化床2
(二)、按照床层的外形分类: )、按照床层的外形分类: 按照床层的外形分类
1.圆筒形流化床。 1.圆筒形流化床。 圆筒形流化床 圆筒形流化床反应器结构简单,制造 容易,设备容积利用率高。
流化床反应器的类别

流化床反应器的类别流化床反应器是一种广泛应用于化工领域的反应器,根据不同的反应类型和要求,可以分为多种不同的类别。
本文将介绍几种常见的流化床反应器类别,包括催化剂流化床反应器、液固两相流化床反应器、生物质流化床反应器和气固两相流化床反应器。
一、催化剂流化床反应器催化剂流化床反应器是指在反应床中使用催化剂来催化反应的流化床反应器。
它具有催化剂与反应物之间接触面积大、传质速度快、反应效率高的特点。
催化剂流化床反应器广泛应用于石油化工、化学制药、环保等领域。
例如,在石油化工中,催化剂流化床反应器常用于催化裂化、加氢、脱氢等反应过程中。
二、液固两相流化床反应器液固两相流化床反应器是指在反应床中同时存在液体和固体两相的流化床反应器。
液固两相流化床反应器常用于液相催化反应、氧化反应、水解反应等。
它具有传质速度快、反应效率高、携带液体催化剂方便等优点。
在化工生产中,液固两相流化床反应器广泛应用于酯化、醚化、氧化等反应过程中。
三、生物质流化床反应器生物质流化床反应器是指在反应床中利用生物质作为原料进行反应的流化床反应器。
生物质流化床反应器主要用于生物质能源转化和生物质化学品的生产。
生物质流化床反应器具有能源效率高、废弃物资源化利用等优点。
在生物质能源领域,生物质流化床反应器被广泛应用于生物质燃烧、生物质气化等过程中。
四、气固两相流化床反应器气固两相流化床反应器是指在反应床中同时存在气体和固体两相的流化床反应器。
气固两相流化床反应器常用于气相催化反应、气体分离、吸附等。
它具有气体和固体之间传质速度快、反应效率高、易于分离固体产物等优点。
在化工生产中,气固两相流化床反应器广泛应用于合成氨、裂解氨、高分子聚合等过程中。
总结:流化床反应器是一种重要的反应器,在化工领域具有广泛的应用。
根据不同的反应类型和要求,流化床反应器可以分为催化剂流化床反应器、液固两相流化床反应器、生物质流化床反应器和气固两相流化床反应器等类别。
每种类别的流化床反应器都有其独特的特点和应用领域。
流化床反应器简介

流化床反应器简介一、概述流化床反应器是一种利用气体或液体通过颗粒状固体层而使固体颗粒处于悬浮运动状态 ,并进行气固相反应过程或液固相反应过程的反应器。
在用于气固系统时 ,又称沸腾床反应器。
流化床反应器在现代工业中的早期应用为2O世纪2O年代出现的粉煤气化的温克勒炉,但现代流化反应技术的开拓,是以4O年代石油催化裂化为代表的。
目前,流化床反应器已在化工、石油、冶金、核工业等部门得到广泛应用。
二、基本流态化现象固定式和临界流化态将一批固体颗粒对方在多孔的分布板上形成床层(图1),使流体自下而上通过床层。
由于流体的流动及其与颗粒表面的摩擦,造成流体通过床层的压力降。
当流体通过床层的表观流速(按床层截面计算的流速)不大时,颗粒之间仍保持静止和互相接触,这种床层称为固定床。
当表观流速增大至起始流化速度时,床层压力降等于单位分布板面积上的颗粒浮重(颗粒的重力减去同体积流体的重力),这时颗粒不再相互支撑,并开始悬浮在流体之中。
进一步提高表观流速,床层随之膨胀,床层压力降近乎不变,但床层中颗粒的运动加剧。
而当流速达到某一限值,床层刚刚能被流体拖动时,床内颗粒就开始流化起来了,这时的流体空床线速称为临界流化速度。
散式流态化和聚式流态化这两种流态化现象,是根据流化床内颗粒和流体的运动状况来区分的。
在散式流态化时,颗粒均匀分布在流体中,并在各方向上作随机运动,床层表面平稳且清晰,床层随流体表观流速的增加而均匀膨胀。
在聚式流态化时,床层内出现组成不同的两个相,即含颗粒甚少的不连续气泡相,以及含颗粒较多的连续乳化相。
乳化相的气固运动状况和空隙率,与起始流化状态相近。
通过床层的流体,部分从乳化相的颗粒间通过,其余以气泡形式通过床层。
增加流体流量时,通过乳化相的气量基本不变,而气泡量相应增加。
气泡在分布板上生成,在上升过程中长大;小气泡会合并成大气泡;大气泡也会破裂成小气泡。
气泡上升至床面时破裂,使床面频繁地波动起伏,同时将一部分固体颗粒抛撒到界面以上,形成一个含固体颗粒较少的稀相区;与此相对应,床面以下的床层称为浓相区。
流化床反应器

流化床反应器
流化床反应器是一种在化学反应或固体催化反应中广泛应
用的特殊反应器。
它采用一种称为流化床的技术,通过在
床层中通入气体或液体以使颗粒物质悬浮和流动。
流化床
反应器具有以下特点:
1. 高传质和传热效率:由于颗粒物质在床层中悬浮和流动,流化床反应器能够实现反应物质与催化剂或固体颗粒的充
分接触,从而提高传质和传热效率。
2. 反应条件易于控制:通过调节床层中的气体或液体速度、温度和压力等参数,可以精确控制反应条件,以实现特定
的反应效果。
3. 高催化活性:流化床反应器中的催化剂颗粒可以均匀悬
浮在床层中,不会发生聚集或堵塞现象,从而保证催化剂
的活性和稳定性。
4. 高载体利用率:由于颗粒物质在床层中悬浮和流动,催
化剂的载体利用率较高,不会出现局部堵塞现象。
5. 反应器结构简单:流化床反应器的结构相对简单,易于
操作和维护。
流化床反应器在许多领域中应用广泛,例如石油化工、化
学工程、环保等领域。
它被用于各种气相、液相和固相反应,例如氢化反应、氧化反应、催化裂化、流化床燃烧等。
- 1、下载文档前请自行甄别文档内容的完整性,平台不提供额外的编辑、内容补充、找答案等附加服务。
- 2、"仅部分预览"的文档,不可在线预览部分如存在完整性等问题,可反馈申请退款(可完整预览的文档不适用该条件!)。
- 3、如文档侵犯您的权益,请联系客服反馈,我们会尽快为您处理(人工客服工作时间:9:00-18:30)。
流化床简介按照床层的外形分类可分为圆筒形和圆锥形流化床。
圆筒形流化床反应器结构简单,制造容易,设备容积利用率高。
圆锥形流化床反应器的结构比较复杂,制造比较困难,设备的利用率较低,但因其截面自下而上逐渐扩大,故也具有很多优点: 1、适用于催化剂粒度分布较宽的体系由于床层底部速度大,较大颗粒也能流化,防止了分布板上的阻塞现象,上部速度低,减少了气流对细粒的带出,提高了小颗粒催化剂的利用率,也减轻了气固分离设备的负荷。
这对于在低速下操作的工艺过程可获得较好的流化质量。
2、由于底部速度大,增强了分布板的作用床层底部的速度大,孔隙率也增加,使反应不致过分集中在底部,并且加强了底部的传热过程,故可减少底部过热和烧结现象。
3、适用于气体体积增大的反应过程气泡在床层的上升过程中,随着静压的减少,体积相应增大。
采用锥形床,选择一定的锥角,可适应这种气体体积增大的要求,使流化更趋平稳。
按照床层中是否设置有内部构件分类可分为自由床和限制床。
床层中设置内部构件的称为限制床,未设置内部构件的称为自由床。
设置内部构件的目的在于增进气固接触,减少气体返混,改善气体停留时间分布,提高床层的稳定性,从而使高床层和高流速操作成为可能。
许多流化床反应器都采用挡网、挡板等作为内部构件。
对于反应速度快、延长接触时间不至于产生严重副反应或对于产品要求不严的催化反应过程,则可采用自由床,如石油炼制工业的催化裂化反应器便是典型的一例。
按照反应器内层数的多少分类可分为单层和多层流化床。
对气固相催化反应主要采用单层流化床。
多层式流化床中,气流由下往上通过各段床层,流态化的固体颗粒则沿溢流管从上往下依次流过各层分布板,如用于石灰石焙烧的多层式流化床的结构。
按是否催化反应分类分为气固相流化床催化反应器和气固相流化床非催化反应器两种。
以一定的流动速度使固体催化剂颗粒呈悬浮湍动,并在催化剂作用下进行化学反应的设备是气固相流化床催化反应器,它是气固相催化反应常用的一种反应器。
而在气固相流化床非催化反应器中,是原料直接与悬浮湍动的固体原料发生化学反应。
流化床反应器的优点流化床内的固体粒子像流体一样运动,由于流态化的特殊运动形式,使这种反应器具有如下优点:1、由于可采用细粉颗粒,并在悬浮状态下与流体接触,流固相界面积大(可高达3280~16400m²/m³),有利于非均相反应的进行,提高了催化剂的利用率。
2、由于颗粒在床内混合激烈,使颗粒在全床内的温度和浓度均匀一致,床层与内浸换热表面间的传热系数很高[200~400W/(m²•K)],全床热容量大,热稳定性高,这些都有利于强放热反应的等温操作。
这是许多工艺过程的反应装置选择流化床的重要原因之一。
3、流化床内的颗粒群有类似流体的性质,可以大量地从装置中移出、引入,并可以在两个流化床之间大量循环。
这使得一些反应—再生、吸热—放热、正反应—逆反应等反应耦合过程和反应—分离耦合过程得以实现。
使得易失活催化剂能在工程中使用。
4、流体与颗粒之间传热、传质速率也较其它接触方式为高。
5、由于流—固体系中孔隙率的变化可以引起颗粒曳力系数的大幅度变化,以致在很宽的范围内均能形成较浓密的床层。
所以流态化技术的操作弹性范围宽,单位设备生产能力大,设备结构简单、造价低,符合现代化大生产的需要。
流化床反应器的缺点1、气体流动状态与活塞流偏离较大,气流与床层颗粒发生返混,以致在床层轴向没有温度差及浓度差。
加之气体可能成大气泡状态通过床层,使气固接触不良,使反应的转化率降低。
因此流化床一般达不到固定床的转化率。
2、催化剂颗粒间相互剧烈碰撞,造成催化剂的损失和除尘的困难。
3、由于固体颗粒的磨蚀作用,管子和容器的磨损严重。
虽然流化床反应器存在着上述缺点,但优点是主要的。
流态化操作总的经济效果是有利的,特别是传热和传质速率快、床层温度均匀、操作稳定的突出优点,对于热效应很大的大规模生产过程特别有利。
综上所述,流化床反应器比较适用于下述过程:热效应很大的放热或吸热过程;要求有均一的催化剂温度和需要精确控制温度的反应;催化剂寿命比较短,操作较短时间就需更换(或活化)的反应;有爆炸危险的反应,某些能够比较安全地在高浓度下操作的氧化反应,可以提高生产能力,减少分离和精制的负担。
流化床反应器一般不适用如下情况:要求高转化率的反应;要求催化剂层有温度分布的反应。
对于一般的工业流化床反应器,需要控制和测量的参数主要有颗粒粒度、颗粒组成、床层压力和温度、流量等。
这些参数的控制除了受所进行的化学反应的限制外,还要受到流态化要求的影响。
实际操作中是通过安装在反应器上的各种测量仪表了解流化床中的各项指标,以便采取正确的控制步骤达到反应器的正常工作。
1.颗粒粒度和组成的控制如前所述,颗粒粒度和组成对流态化质量和化学反应转化率有重要影响。
下面介绍一种简便而常用的控制粒度和组成的方法。
在氨氧化制丙烯腈的反应器内,采用的催化剂粒度和组成中,为了保持<44μm的“关键组分(即对流态化质量起关键作用的较小粒度的颗粒。
)”粒子在20%~40%之间,在反应器上安装一个“造粉器”。
当发现床层内<44μm的粒子小于12%时,就启动造粉器。
造粉器实际上就是一个简单的气流喷枪,它是用压缩空气以大于300m/s的流速喷入床层,粘结的催化剂粒子即被粉碎,从而增加了小于44μm粒子的含量。
在造粉过程中,要不断从反应器中取出固体颗粒样品,进行粒度和含量的分析,直到细粉含量达到要求为止。
系统正常运转中,从床层取固体颗粒样品,虽然简单,但又要特别注意并妥善处理好。
如图5-39所示的是王尊孝提出的取样器。
在平时,锥形活动堵头3是关闭的,阀6是开启的,取样器本体内充满了压力高于床层内压力的干燥空气,以防止反应产物渗入取样器内,造成启动时的困难(例如苯酐反应器,当温度低于150℃时,苯酐呈液体析出;当温度低于130.8℃时,苯酐变成固体,如果没有反吹气,取样器将因苯酐冻结而堵死)。
取样时先关闭阀6,然后转动拉杆2,打开堵头3,粒子便自动流入取样杯4,然后再关闭堵头3,卸下取样杯4,将料样倒出,最后装上取样杯4,打开充气阀6,取样完毕。
流化床用固体颗粒取样器1—取样器本体,φ32~φ38mm;2—拉杆:3—锥形活动堵头;4—手动装卸取样杯,φ38×150mm;5—气密填料;6—针形阀;7—节流小孔板,孔φ0.6~1.0mm;8—逆止阀2.压力的测量与控制压力和压降的测量,是了解流化床各部位是否正常工作较直观的方法。
对于实验室规模的装置,U型管压力计是常用的测压装置,通常压力计的插口需配置过滤器,以防止粉尘进入U型管。
工业装置上常采用带吹扫气的金属管做测压管。
测压管直径一般为12~25.4mm,反吹风量至少为1.7m3/h。
反吹气体必须经过脱油、去湿方可应用。
测压管线的典型安装如图5-40所示。
为了确保管线不漏气,所有丝接的部位最后都是焊死的,阀门不得漏气。
流化床差压计安装管线示意图小孔板是用1mm厚的不锈钢或铜板制造的,钻0.64~1.0mm小孔。
为了了解在流态化情况下的床层高度,可用下式推算:用同样的取样方式,我们可以推算旋风分离器料腿内的料柱高度。
就是说,为了随时了解旋风分离器料腿内的料柱高度及它的稳定工作情况,可在料腿上也安装三个测压管,同样要接吹扫风。
特别是在用细颗粒催化剂时,旋风分离系统的设计,常常是过程能否成功的关键,应当特别慎重处理。
由于流化床呈脉冲式运动,需要安装有阻尼的压力指示仪表,如差压计、压力表等。
有经验的操作者常常能通过测压仪表的运动预测或发现操作故障。
3.温度的测量与控制流化床催化反应器的温度控制取决于化学反应的最优反应温度的要求。
一般要求床内温度分布均匀,符合工艺要求的温度范围。
通过温度测量可以发现过高温度区,进一步判断产生的原因是存在死区,还是反应过于剧烈,或者是换热设备发生故障。
通常由于存在死区造成的高温,可及时调整气体流量来改变流化状态,从而消除死区。
如果是因为反应过于激烈,可以通过调节反应物流量或配比加以改变。
换热器是保证稳定反应温度的重要装置,正常情况下通过调节加热剂或致冷剂的流量就能保证工艺对温度的要求。
但是设备自身出现故障的话,就必须加以排除。
最常用的温度测量办法是采用标准的热敏元件。
如适应各种范围温度测量的热电偶。
可以在流化床的轴向和径向安装这样的热电偶组,测出温度在轴向和径向的分布数据,再结合压力测量,就可以对流化床反应器的运行状况有一个全面的了解。
4.流量控制气体的流量在流化床反应器中是一个非常重要的控制参数,它不仅影响着反应过程,而且关系到流化床的流化效果。
所以作为既是反应物又是流化介质的气体,其流量必须要在保证最优流化状态下,有较高的反应转化率。
一般原则是气量达到最优流化状态所需的气速后,应在不超过工艺要求的最高或最低反应温度的前提下,尽可能提高气体流量,以获得最高的生产能力。
气体流量的测量一般采用孔板流量计,要求被测的气体是清洁的。
当气体中含有水、油和固体粉尘时,通常要先净化,然后再进行测量。
系统内部的固体颗粒流动,通常是被控制的,但一般并不计量。
它常常被调节在一个推理的基础上,如根据温度、压力、催化剂活性、气体分析等要求来调整。
在许多煅烧操作中,人们常根据煅烧物料的颜色来控制固体的给料。
5.开停车及防止事故的发生由粗颗粒形成的流化床反应器,开车启动操作一般不存在问题。
而细颗粒流化床,特别是采用旋风分离器的情况下,开车启动操作需按一定的要求来进行。
这是因为细颗粒在常温下容易团聚。
当用未经脱油、脱湿的气体流化时,这种团聚现象就容易发生,常使旋风分离器工作不正常,导致严重后果。
正常的开车程序是:①先用被间接加热的空气加热反应器,以便赶走反应器内的湿气,使反应器趋于热稳定状态。
对于一个反应温度在300~400℃的反应器,这一过程要达到使排出反应器的气体温度达到200℃为准。
必须指出,绝对禁止用燃油或燃煤的烟道气直接加热。
因为烟道气中含有大量燃烧生成的水,与细颗粒接触后,颗粒先要经过吸湿,然后随着温度的升高再脱水,这一过程会导致流化床内旋风分离器的工作不正常,造成开车失败。
②当反应器达到热稳定状态后,用热空气将催化剂由贮罐输送到反应器内,直至反应器内的催化剂量足以封住一级旋风分离器料腿时,才开始向反应器内送入速度超过umf不太多的热风(热风进口温度应大于400℃),直至催化剂量加到规定量的1/2~2/3时,停止输送催化剂,适当加大流态化热风。
对于热风的量,应随着床温的升高予以调节,以不大于正常操作气速为度。
③当床温达到可以投料反应的温度时,开始投料。
如果是放热反应,随着反应的进行,逐步降低进气温度,直至切断热源,送入常温气体。
如果有过剩的热能,可以提高进气温度,以便回收高值热能的余热,只要工艺许可,应尽可能实行。