全氢罩式炉介绍
全氢罩式退火炉安全控制(一)

全氢罩式退火炉安全控制(一)1概述强对流全氢罩式退火炉(以下简称全氢罩式炉)是在原低氢罩式炉的基础上于70年代发展起来的,具有低能耗、高效率、退火产品品质优良等众多特点。
国外在1984年开始大量应用于宽带钢卷的退火,至今已有近千座全氢罩式炉在世界各地建成。
在奥地利的奥钢联、德国的克勒克纳冷轧厂和蒂森冷轧厂、美国的l-TV钢厂和USX钢厂等钢铁企业中,都可以见到正在工作的全氢罩式炉。
直到80年代末、90年代初,全氢罩式炉这项先进的生产工艺才随着国外生产工艺、控制技术的成熟逐步引进到国内,并迅速得到推广。
国内已有鞍钢、武钢、本钢、上海益昌冷轧薄板厂、海南鹏达冷轧薄板厂等单位先后引进、建成了全氢罩式炉,生产、使用情况良好。
近年建设或改造的冷轧薄板厂正在大量采用全氢罩式炉,原有的低氢罩式炉正面临被全氢罩式炉替代的局面。
全氢罩式炉的安全性是至关重要的,这主要是由干在退火过程中采用了易燃、易爆的氢气充当退火产品的保护气体和热传导体,稍有不慎即有可能发生着火或爆炸事故。
如果没有可靠的安全保障措施,即控制系统没有完善的控制策略,不仅全氢罩式炉的生产不能进行,而且还有破坏整个生产设施的可能。
本文针对全氢罩式炉保护气体应用的安全性,介绍全氢保护气体控制过程的安全控制策略,以增强对这-问题的认识。
2全氢罩式炉设备及工艺过程简介全氢罩式炉是用来消除由冷轧变形而使带钢产生的内应力的一种处理装置。
通过使带钢升温、保温、降温的过程进行带钢的再结晶退火。
一座全氢罩式炉的基本设备包括:(1)一个带有底部循环风机的炉台及其附属介质供给管路。
(2)一个底部敞开、其余封闭焊接成整体的保护罩(以下简称内罩)。
将它扣在炉台上即与炉台构成一个封闭的小空问(以下简称退火空间),退火带钢就置于退火空间之中。
在退火过程中,退火空间即充满纯氢气以保护带钢在高温下不至干氧化。
(3)一个制成罩形的加热装置(以下简称加热罩)。
加热罩扣在内罩之上,两罩之间形成一个燃烧室,燃料在此燃烧,热量通过内罩传递到退火空间内。
全氢罩式退火炉新设备和新技术

全氢罩式退火炉新设备和新技术在唐钢冷轧厂的成功运用杨建伟吴静(唐钢冷轧薄板厂)摘要:对唐钢冷轧厂全氢式单垛罩式退火生产线基本概况、新设备、新技术、生产工艺进行了论述,以详实的数据对新设备、新技术的良好性能做出的论证,并对现行的退火工艺和工艺制度的优化情况进行了介绍,总结了唐钢冷轧厂罩式退火生产线的现状,提出了未来的发展方向。
关键词:全氢罩式退火炉新设备新技术生产工艺1、前言全氢式保护气体单垛罩式炉采用间歇式生产方式,以焦炉煤气或混合煤气(高炉和焦炉)作为燃料,通过对内罩加热近而间接对带钢卷加热的方式,利用内罩内100%氢气作为保护气体,对带钢卷进行再结晶光亮退火。
退火产品可广泛应用于建材、家电、汽车等领域。
2、基本概况唐钢冷轧厂全氢式单垛罩式退火生产线全部关键设备部件和技术均引进于奥地利艾伯纳炉子公司,拥有该公司目前在中国大陆地区最先进的关键设备部件和技术。
设计能力为年产80万吨退火产品,包括40座炉台及配套的阀站、40个内罩、21个加热罩、19个冷却罩、30座终冷台、2套减压系统、2套液压系统和一套自动控制系统,其中炉台、阀站、减压站、液压站和程序控制系统元件等设备由艾伯纳奥地利总公司提供,加热罩、冷却罩、内罩和终冷台等设备由艾伯纳中国太仓分公司提供,确保了设备的最佳品质。
为满足将来生产发展的需要,另外预留8座炉台,6座终冷台,全部建成投产后,每年可生产退火产品95万吨。
3、设备描述3.1全封闭炉台全封闭炉台由炉台钢结构本体、扩散器以及全封闭炉台循环风机组成。
全封闭炉台结构采用新技术设计制造,由钢板和钢结构焊接而成,承载支撑环应用了同心环状结构的新技术,使支撑环的热膨胀与扩散器总成部件保持一致,比原来采用支柱来支撑炉料的系统优越了很多,因此实现了最大112.5吨的净装炉量和五卷装炉最大6500 mm的堆垛高度,是国内为数不多的采用五卷装炉的机组之一。
扩散器组件采用了重载承重板,能够预防100%的表面接触,使最底层的带钢卷不会出现边缘损伤。
全氢罩式退火炉安全控制

全氢罩式退火炉安全控制引言全氢罩式退火炉是一种常用的化学气相沉积设备,主要用于制备各种材料的薄膜。
在使用过程中,需要加入氢气等特殊气体,因此需要考虑设备的安全性。
为了确保全氢罩式退火炉使用过程中的可靠性和安全性,需要灵活使用各种手段进行控制和管理。
本文将介绍如何对全氢罩式退火炉进行安全控制。
安全控制措施在全氢罩式退火炉的操作过程中,应根据以下措施进行安全控制:设备安全在使用全氢罩式退火炉之前,应确保设备的安全性。
首先应检查所有的管道和阀门是否已经紧闭并且安装正确,电缆是否接好。
其次,需要检查设备中的氢气、氮气等气体储罐的安全性,以避免设备出现爆炸等事故。
火灾安全全氢罩式退火炉使用过程中容易发生爆炸、火灾等事故,因此需要进行火灾安全控制。
在使用全氢罩式退火炉之前,应排除设备中的氢气、氢气出口的管道以及各个部位松散的螺栓等设备隐患。
在炉内进气之前,应先充入气体和气体冷却水,以保证炉内有气流、炉外有冷却。
此外在全氢罩式退火炉的使用过程中,过程变化、异常情况自动诊断功能也要设定完善。
氧含量控制在全氢罩式退火炉的使用过程中,氧含量也需要进行控制。
高氧含量可能导致材料的腐蚀。
因此,在全氢罩式退火炉的使用过程中,应加入足够的氢气,控制气氛所含氧的浓度。
温度控制在全氢罩式退火炉操作过程中,温度控制非常关键。
需要根据所需退火温度,逐步升温或降温,并保持一定的升温或降温速率,以避免温度变化太过剧烈,形成热应力,从而导致材料变形、开裂等问题。
气压控制在全氢罩式退火炉操作过程中,气压控制也非常重要。
全氢罩式退火炉的气压一般设定在 100 Pa 左右,以保持非常干净的炉内环境。
需要注意的是,气压过低会导致退火过程不稳定,温度控制不当。
结论全氢罩式退火炉是一种非常重要的化学气相沉积设备,但在使用过程中也存在安全隐患。
为了确保全氢罩式退火炉使用过程中的可靠性和安全性,应根据设备安全、火灾安全、氧含量控制、温度控制以及气压控制等措施进行控制和管理,确保全氢罩式退火炉操作过程的安全,保障设备和操作人员的安全。
全氢罩式炉的特性及在天铁冷轧的应用
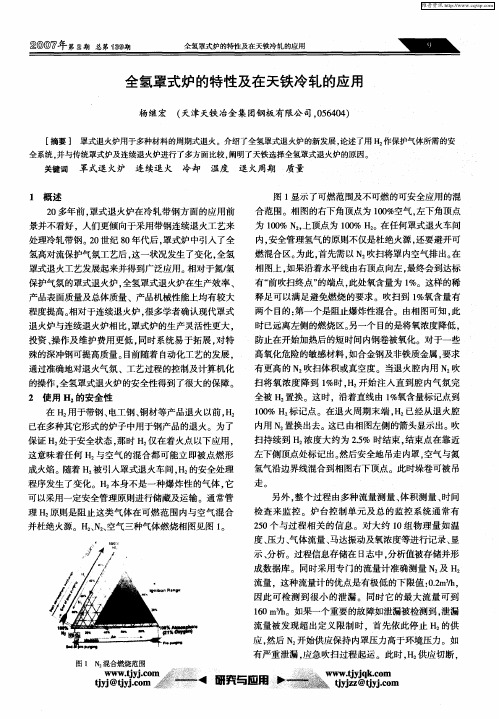
氢气沿 边界线混合到相图右下顶点 。此时垛卷可被 吊
走。
可 以采用 一定安全管理原则进行储 藏及运输 。通常管 理 H 原则是阻止这类气 体在可燃 范 围内与空气 混合
并杜绝火 源。H 、 2空气三种气体燃烧相图见 图量 、 体积测量 、 时间
产品表面质量及 总体质量 、产品机械性能上均有较大 程度提高。 相对于连续退火炉 , 多学者确认现代罩式 很 退火炉与连续退火炉相 比. 罩式炉的生产灵活性更大 , 投资 、 操作及维护 费用更 低 , 同时 系统 易于拓展 , 对特 殊的深 冲钢可提高质量 。 目前 随着 自动化工艺 的发展 , 通过准确地对退火气 氛 、工艺过程 的控制及计算机化 的操作 . 全氢罩式退火炉的安全性得到 了很 大的保 障。 2 使 用 H: 的安全 性 在 H 用于带钢 、 电工钢 、 铜材等产品退火 以前 , 2 } { 已在多种其它形 式的炉子 中用于钢产品的退火。为了 保证 H 处于安全状态 , 那时 H 仅在着火点 以下应用 ,
检查来 监控 。炉 台控制单 元及 总 的监 控系统 通常有
20个 与过 程相关 的信息 。对大约 1 5 0组物理 量如温 度、 压力 、 气体流量 、 马达振动及氧浓度等进行记 录、 显 示、 分析 。过程信息存储在 日志中. 分析值被存储并形 成数据 库 。同时采用专 门的流量计 准确测量 N 及 H
合范 围。相 图的右下角顶点为 10 0%空气 , 左下角顶点
为 10 N , 0% 上顶点为 10 H 。在任何罩式退火车 间 0% 内, 管理氢气 的原则不仅是杜绝火源 , 安全 还要避开可
景并不看好 ,人们更倾 向于采用带钢连续退 火工艺来 处理冷轧带钢。2 0世纪 8 年代后 , 0 罩式炉中引入 了全
全氢罩式退火炉工艺设备及工程化特点

全氢罩式退火炉工艺设备及工程化特点摘要:本文介绍了全氢罩式退火炉工艺及设备主要特点,并依托某钢厂的冷轧退火线,从工程的角度介绍了随着市场的需求,对退火钢卷的需求不断增大,热处理配置需要进行相应提升改造,本文针对其产品方案重点介绍了产线的工艺流程及主体设备的相关参数及工程化特点。
关键词:全氢罩式退火炉;工艺及设备;工程化特点1 前言全氢罩式退火炉,是冷轧钢卷常用的热处理炉型之一,此方式因为其组织生产灵活、设备投资低而被众多用户所采纳。
罩式退火炉采用100%全氢气保护气体,整个退火周期采用耐高温风机使保护气体高速循环,以加强传热效果,提高产品质量和产量。
[1]某钢厂冷轧厂设计年产冷轧卷100 万吨,目前配套的罩式退火炉生产能力68.5 万t/年。
不能满足现有生产要求,因此需要再建设罩式退火炉增加钢卷退火能力。
2 工艺流程及主要设备特点2.1 工艺流程(1)选择退火程序。
在正常生产过程中,退火程序从COS 传送到炉台PLC,并储存PLC 中,直到接收新的退火程序。
(2)放置内罩。
炉台上料后,将内罩放在炉台上,然后用液压夹紧机构夹紧到水冷炉台法兰的圆形密封件上,这样可以达到很好的密封。
(3)冷泄漏测试。
泄漏测试可以在室温度下自动完成。
将内罩内的压力自动地调节到约5000Pa,并关闭所有入口和出口阀门。
(4)初始吹扫。
如果工作空间无漏气,那么将用氮气动吹扫工作空气。
吹扫结束后,炉台准备退火。
(5)压力控制。
为了使内罩内的压力高出外界压力一定范围,可以自动控制工作区压力。
(6)加热。
加热罩燃烧系统由几个位于加热罩周围的高速烧嘴组成。
(7)温度控制。
对于连续控制,将提供两个单独的温度控制器(分别用于加热罩和炉台);对于开/关控制,将提供两个其它控制器(分别用于加热罩和炉台)。
(8)连续控制。
当加热罩(或炉台)控制器发出打开信号时,机动阀将打开;当控制器发出“关闭”信号时,它将逐渐关闭。
在加热罩控制站配备有手动调节的手动/自动方式开关。
全氢罩式光亮退火炉废氢燃烧系统

1 2 4 ・
科技 论 坛
全氢 罩式光 亮退 火炉废氢燃烧 系统
王 文 霞
( 哈尔滨松江电炉厂有限责任公司, 黑龙江 哈尔滨 1 5 0 0 5 0 )
摘 要 : 通过 对全 氢罩式 光 亮退 火炉废 氢燃烧 系统 的介绍 了解废 氢燃 烧在 全氢罩 式光 亮退 火炉 中的应 用 目的。
节能功效。
2全 氢 罩 式炉 废 氢 烧嘴 结 构原 理 废 氢 燃烧 系统 在 生 产使 用 过 程 中稳 定 可 靠 , 减 少 了对 大 气 全 氢 罩式 退 火 炉 采 用 的 废 氢烧 嘴 , 主要包括燃烧室 、 空气 排 放 污 染 , 同 时也 节 约 了能 源 。热 处 理 炉 是 消 耗 能源大户 , 也 配 风盘 、 煤气喷头 、 空气 导 管 、 煤气流通管 、 双 电极 ; 将煤 气 、 废 是严 重 污 染 源 之 一 ,节 能 减 排 已 经 成 为 我 国 国 民经 济 中 的一 氢 燃 烧 整 合 于 同一 烧 嘴 中 , 废氢通人时 , 煤气做 长明火使用 , 引燃废氢 , 确保 废 氢 燃 烧 的安 全 性 及 稳 定 性 ; 空 气 在 配 风 盘 处 项大 事 。 参 考 文 献 被 分 为 三级 进 行 混 合燃 烧 , 煤气采用端面均布射流喷出 , 加 速 1 1 工 业 炉设计 手 册 『 M】 . 北京: 机 械 工 业 出版 社 , 1 9 9 6 . 了煤气 、 废氢及空气 的混合速度 , 保证烧嘴燃烧 的稳定性及点 【 [ 2 1 钢铁 厂 工 业 炉设 计参 考 资料 f M1 . 北京 : 冶金 工 业 出版社 . 火 及 火 焰 监测 的可 靠 性 , 利 用 高 速烧 嘴对 废 氢 进 行 高 速燃 烧 , 在 回 收利 用 资 源 的 同时 , 通 过 烟 气 高 速对 流 循 环 , 确 保 炉膛 温
罩式退火和连续退火优缺点
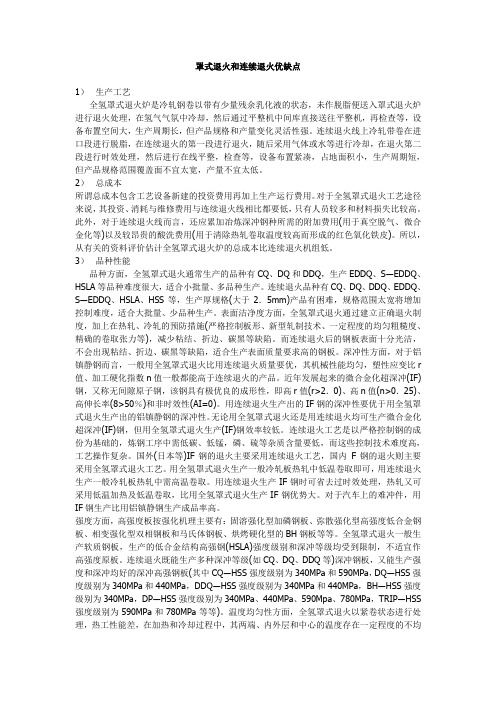
罩式退火和连续退火优缺点1)生产工艺全氢罩式退火炉是冷轧钢卷以带有少量残余乳化液的状态,未作脱脂便送入罩式退火炉进行退火处理,在氢气气氛中冷却,然后通过平整机中间库直接送往平整机,再检查等,设备布置空间大,生产周期长,但产品规格和产量变化灵活性强。
连续退火线上冷轧带卷在进口段进行脱脂,在连续退火的第一段进行退火,随后采用气体或水等进行冷却,在退火第二段进行时效处理,然后进行在线平整,检查等,设备布置紧凑,占地面积小,生产周期短,但产品规格范围覆盖面不宜太宽,产量不宜太低。
2)总成本所谓总成本包含工艺设备新建的投资费用再加上生产运行费用。
对于全氢罩式退火工艺途径来说,其投资、消耗与维修费用与连续退火线相比都要低,只有人员较多和材料损失比较高。
此外,对于连续退火线而言,还应累加冶炼深冲钢种所需的附加费用(用于真空脱气、微合金化等)以及较昂贵的酸洗费用(用于清除热轧卷取温度较高而形成的红色氧化铁皮)。
所以,从有关的资料评价估计全氢罩式退火炉的总成本比连续退火机组低。
3)品种性能品种方面,全氢罩式退火通常生产的品种有CQ、DQ和DDQ,生产EDDQ、S―EDDQ、HSLA等品种难度很大,适合小批量、多品种生产。
连续退火品种有CQ、DQ、DDQ、EDDQ、S―EDDQ、HSLA、HSS等,生产厚规格(大于2.5mm)产品有困难,规格范围太宽将增加控制难度,适合大批量、少品种生产。
表面洁净度方面,全氢罩式退火通过建立正确退火制度,加上在热轧、冷轧的预防措施(严格控制板形、新型轧制技术、一定程度的均匀粗糙度、精确的卷取张力等),减少粘结、折边、碳黑等缺陷。
而连续退火后的钢板表面十分光洁,不会出现粘结、折边、碳黑等缺陷,适合生产表面质量要求高的钢板。
深冲性方面,对于铝镇静钢而言,一般用全氢罩式退火比用连续退火质量要优,其机械性能均匀,塑性应变比r 值、加工硬化指数n值一般都能高于连续退火的产品。
近年发展起来的微合金化超深冲(IF)钢,又称无间隙原子钢,该钢具有极优良的成形性,即高r值(r>2.0)、高n值(n>0.25)、高伸长率(8>50%)和非时效性(AI=0)。
浅谈全氢燃气罩式退火炉的温度控制
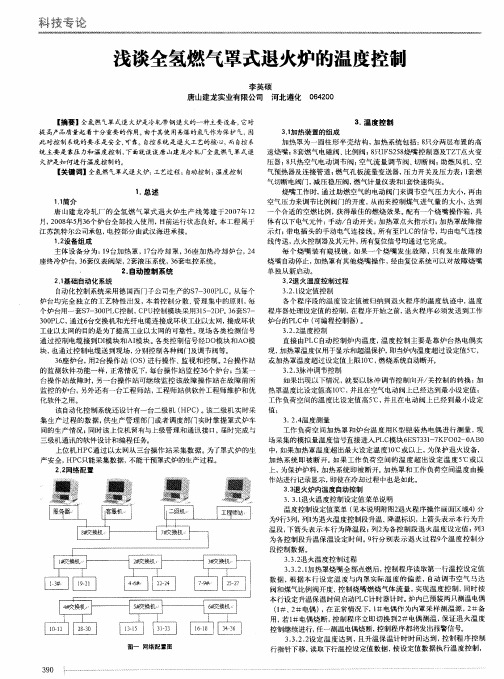
2 . 自动控 ห้องสมุดไป่ตู้系 统
烧嘴 自动停止 , 加热 罩有其他烧嘴 操作 , 经由复位系统可以对 故障烧 嘴 单独从新 启动。 3 . 2 退火 温度控制过程 3 . 2 . 1 设定值控制 各个 程序 段的温度 设定值被 归纳 到退火 程序 的温度轨 迹 中, 温 度
2 . 1 基础 自动化系统 自动化 控制 系统 采用德 国西 门子公司生产 的S 7 — 3 0 0 P LC。 从每 个
0 6 4 2 0 0
3 . 温 度控 制
3 . 1 加热装 置的组 成 加热 罩为一 圆柱 形半 壳结构 , 加热 系统包括 : 8 R分两层布置 的高 速烧 嘴; 8 套燃气 电磁 阀、 比例 阀; 8 只I F S 2 5 8 烧嘴控制 器及T Z T 点火变 压器 ; 8 只热 空气电动调 节阀 ; 空 气流量调 节阀、 切 断阀 ; 助燃风 机 、 空
弼羧毒谂
浅谈全氢燃气罩式退火炉的温度控制
李英硕 唐山建龙实业有 限公司 河北遵化
【 摘要l全氢燃气罩式退火炉是冷轧带钢退 火的一种主要设备, 它对 提 高产品质量起 着十分重要 的作用。 由于其使用易爆的氢气作为保 护气,因
此 对控 制 系统 的要 求是 安 全、 可靠 。自 控 系统 是 退 火 工 艺的核 心 , 而自 控系
该自 动 化控制 系统还设 计有一 台二 级机 ( H P C ) 。 该 二级机实 时采 值 ; 集 生产 过程 的数据 , 供生产 管理部 门或者调 度部 门实时掌 握罩式炉 车 间的生 产情况 ; 同时该 上位机留有与上级管 理和通讯 接 口。 届时完成 与
三级机 通讯的软件设计 和编程任务。 3 . 2 . 4 温度测量
全氢罩式退火炉氢气用量对退火时间的影响分析
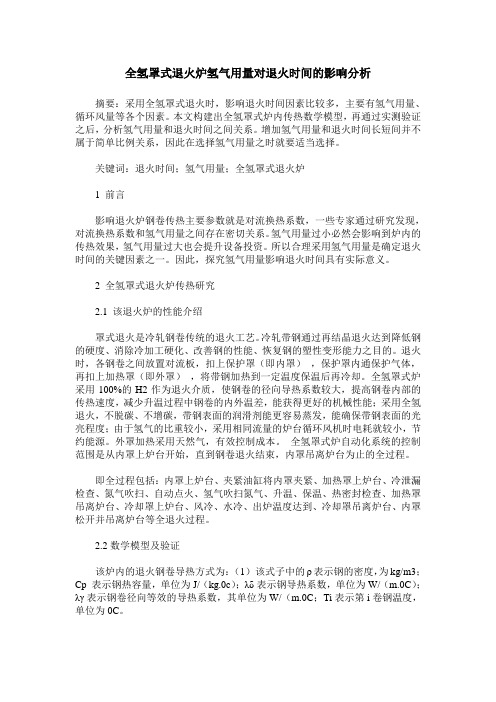
全氢罩式退火炉氢气用量对退火时间的影响分析摘要:采用全氢罩式退火时,影响退火时间因素比较多,主要有氢气用量、循环风量等各个因素。
本文构建出全氢罩式炉内传热数学模型,再通过实测验证之后,分析氢气用量和退火时间之间关系。
增加氢气用量和退火时间长短间并不属于简单比例关系,因此在选择氢气用量之时就要适当选择。
关键词:退火时间;氢气用量;全氢罩式退火炉1 前言影响退火炉钢卷传热主要参数就是对流换热系数,一些专家通过研究发现,对流换热系数和氢气用量之间存在密切关系。
氢气用量过小必然会影响到炉内的传热效果,氢气用量过大也会提升设备投资。
所以合理采用氢气用量是确定退火时间的关键因素之一。
因此,探究氢气用量影响退火时间具有实际意义。
2 全氢罩式退火炉传热研究2.1 该退火炉的性能介绍罩式退火是冷轧钢卷传统的退火工艺。
冷轧带钢通过再结晶退火达到降低钢的硬度、消除冷加工硬化、改善钢的性能、恢复钢的塑性变形能力之目的。
退火时,各钢卷之间放置对流板,扣上保护罩(即内罩),保护罩内通保护气体,再扣上加热罩(即外罩),将带钢加热到一定温度保温后再冷却。
全氢罩式炉采用100%的H2作为退火介质,使钢卷的径向导热系数较大,提高钢卷内部的传热速度,减少升温过程中钢卷的内外温差,能获得更好的机械性能;采用全氢退火,不脱碳、不增碳,带钢表面的润滑剂能更容易蒸发,能确保带钢表面的光亮程度;由于氢气的比重较小,采用相同流量的炉台循环风机时电耗就较小,节约能源。
外罩加热采用天然气,有效控制成本。
全氢罩式炉自动化系统的控制范围是从内罩上炉台开始,直到钢卷退火结束,内罩吊离炉台为止的全过程。
即全过程包括:内罩上炉台、夹紧油缸将内罩夹紧、加热罩上炉台、冷泄漏检查、氮气吹扫、自动点火、氢气吹扫氮气、升温、保温、热密封检查、加热罩吊离炉台、冷却罩上炉台、风冷、水冷、出炉温度达到、冷却罩吊离炉台、内罩松开并吊离炉台等全退火过程。
2.2数学模型及验证该炉内的退火钢卷导热方式为:(1)该式子中的ρ表示钢的密度,为kg/m3;Cp 表示钢热容量,单位为J/(kg.0c);λδ表示钢导热系数,单位为W/(m.0C);λγ表示钢卷径向等效的导热系数,其单位为W/(m.0C;Ti表示第i卷钢温度,单位为0C。
罩式炉设备运行安全策略

二、全氢煤气罩式炉安全策略
1、氢气的安全使用与控制策略
在一般情况下,空气中氢气的爆炸浓度为4% ~72% ,且着火点很 低。避免燃烧爆炸的关键在于着火点、混合气体浓度达到爆炸极限、 相对密闭空间。由于罩式炉设备结构的特点,避免明火难度较大且空 间又是密封的。因此,安全使用全氢保护气体进行退火生产的核心就 杜绝氧气与氢气的混合,使退火空间气体无法达到爆炸浓度。同时, 务必保证设备正压操作,杜绝爆炸的可能性。全氢罩式炉使用纯氮气 作为氢气和氧气的隔离气体。在正常情况下,氮气仅用来吹扫退火空 间。只有在故障处理等不得已情况下才用这种氮气对退火空间进行事 故吹扫或充当保护气体继续完成退火过程。
全氢罩式退火炉传热机理示意图
一、全氢煤气罩式炉设备基础
1、全氢罩式炉工作基本原理
传 导
钢 卷 辐 射
内 罩 对 流
辐 射
加热罩
全氢罩式退火炉内的主要传热形式:内罩内的 传热包括内罩与钢卷的辐射换热,氢气与钢卷 及内罩的对流换热和钢卷内部传热。在加热阶 段,内外罩间的传热主要是高温烟气与内外罩
气体辐射
二、全氢煤气罩式炉安全策略
全氢罩式炉的安全性是至关重要的,这 主要是由干在退火过程中采用了易燃、易 爆的氢气充当退火产品的保护气体和热传 导体,稍有不慎即有可能发生着火或爆炸 事故。如果没有可靠的安全保障措施,即 控制系统没有完善的控制策略,不仅全氢 罩式炉的生产不能进行,而且还有破坏整 个生产设施的可能。
三、全氢煤气罩式炉安全控制的重要意义
全氢罩式炉危险气体使用安全控制是全氢罩式炉控制 系统中极为重要的控制功能,是工艺控制功能不可缺少的 补充。不同生产厂家的罩式炉设备,虽然炉型不同、工艺 过程不同,但整套安全控制策略却几乎相同,对整个退火 过程中可能遇到的各种情况都作了详细的考虑。这套安全 控制方法已经非常成熟,全氢保护气体在全氢罩式炉中应 用的安全性已经有了可靠的保证。
全氢式罩式退火炉简介
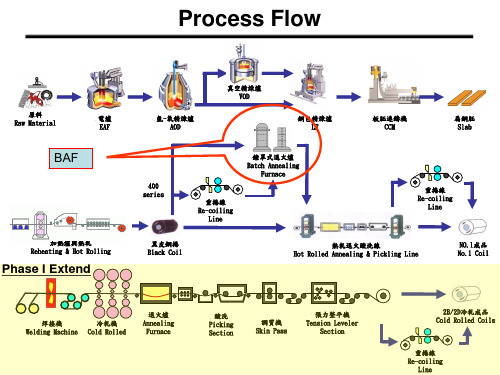
冷却系统〆
氮氢罩式炉配有冷却罩,冷却罩内有冷却风 机々还装备有位于炉台下的旁路冷却系统, 旁路冷却系统采用水冷对炉内气氛进行循环 冷却。炉台橡胶密封圈的下面还有专门的流 动水冷却槽,用以对密封圈进行冷却
退火工艺过程简述
全氢罩式炉设备包括炉台、内罩、加热罩和冷却罩。其工艺 过程如下〆 炉台装料,放置内罩并利用液压装置压紧内罩々 检验氢气人口阀和炉台内罩密封性,确保系统安全々 用氮气吹扫内罩内空气,使炉内氧含量减少到1% 以下,为 通入氢气做好准备(在内罩外放置加热罩,内罩和加热罩之 间为燃烧区间)々 用氮气置换空气完成后,氧含量低于1%时,开始加热点 火,并用氢气置换氮气实现全氢气氛退火过程々 退火过程的加热段、均热段,氢气定流量吹扫々 带加热罩冷却、辐射冷却々 带冷却罩冷却、分流冷却々 用氮气吹扫炉内氢气々 料卷出炉。
冷却过程可细分为四个阶段:
带加热罩冷却 辐射冷却 带冷却罩冷却 快速冷却
带加热罩冷却:
從均热阶段后的热态密封试验结束开始,这 时停止燃气供应,由烧嘴中喷射常温空气直 接冷却内罩,达到冷却钢卷的目的
辐射冷却阶段
当炉内控制热电偶温度达到600℃时,结束带 加热罩冷却,移走加热罩〃从移走加热罩到 吊盖冷却罩一般约有12min的等待时间〃在这 一时间段内,内罩的散热方式为对环境的辐 射和自然对流,称为辐射冷却阶段
带冷却罩冷却
扣上冷却罩后,开始带冷却罩冷却〃此阶段 中,由大流量、高流速的冷风对内罩进行冷 却
快速冷却
当炉内控制热电偶的温度达到一定值(根据不 同的快冷方式,此温度为300~450oC不等) 时,启动快速冷却装置,进行快速冷却
快速冷却方式
通常有两种快速冷却方式: 氢气旁路冷却 (将内罩内的循环氢气按比例抽取通过气/水 换热器冷却后,再输入炉内,以快速降低循环氢气的温度)在退火过程的 快冷过程中,旁路冷却风机对不同介质和不同温度情况下也有不同要 求。针对这种情况,旁路冷却风机和旁路冷却阀的动作需按行程控制。 经过现场使用,行程控制的方式满足快冷过程的工艺要求。 水喷淋冷 却(JA冷却罩顶部直接向内罩喷水进行冷却) 当钢卷达到规定的出炉温度时,结束此过程,也即结束整个退火过程
带钢退火工艺及其装备(全氢罩式退火炉)
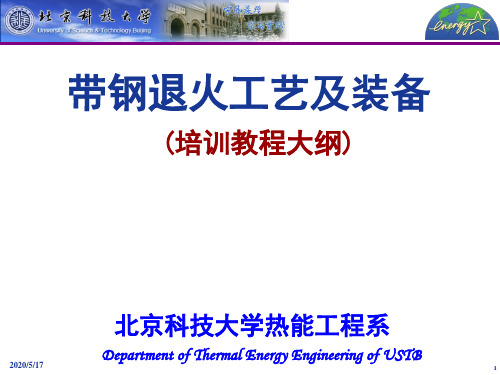
(培训教程大纲) 培训教程大纲)
北京科技大学热能工程系
2011-3-18
Department of Thermal Energy Engineering of USTB
1
第一部分—全氢罩式炉退火工艺及其装备 第一部分 全氢罩式炉退火工艺及其装备
一、发展历程(历史沿革) 发展历程(历史沿革) 二、基本构造与操作过程 三、炉内传热过程的分析 四、数值模拟与实验验证 五、参数优化及其分析 六、主要结论
38<t ≤ 58.5 f=f 0 + a 1 e -(t-t0)/x1 f 0 =0.79184 t 0 =38.03 a 1 =0.21853 x 1 = 3.07573 f=a+b 1 t+b 2 t 2 + b 3 t 3 a= -23.79697 b 1 =1.48994 b 2 =-0.02926 b 3 =1.89788 × 10 -4
2011-3-18
全氢罩式退火炉热过程 离线数学模型计算结果及分析
2011-3-18
8
加热过程
加热过程 均热过程
冷却过程
带加热罩冷却过程 辐射冷却过程 带冷却罩冷却过程 快速冷却(氢气旁路冷却或水喷淋冷却)
2011-3-18
9
建立数学模型的目的
建立全氢罩式炉退火过程数学模型, 建立全氢罩式炉退火过程数学模型 , 进行离线 预报钢卷退火工艺曲线, 预报钢卷退火工艺曲线 , 为今后实现钢卷温度 的在线跟踪和炉温的动态计算提供基础。 的在线跟踪和炉温的动态计算提供基础。 对不同来料、 不同产品的退火过程, 对不同来料 、 不同产品的退火过程 , 只要将原 始数据作为模型输入条件, 始数据作为模型输入条件 , 模型即可计算出相 应的退火曲线, 应的退火曲线 , 为工艺优化与过程控制提供依 据。 建立、 完善不同钢种、 建立 、 完善不同钢种 、 不同规格的钢卷在不同 产量条件下的优化退火工艺制度, 产量条件下的优化退火工艺制度 , 为今后实现 在线控制提供坚实的理论基础。 在线控制提供坚实的理论基础。
全氢罩式炉技术特点
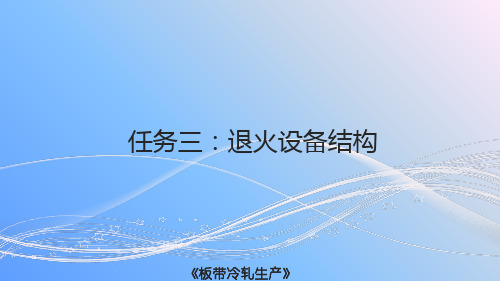
强对流全氢炉子技术特点
提高保护罩壁的温度, 形成较高的温度差
增加内罩壁与保护气体 之间对流传热
强对流全氢炉子技术特点
增加内罩壁与保护气体之间
对流传热的主要途径是加大保护
气体的流速,采用保护气体流速
高、流量大的循环系统,把内罩
上的热量尽快传递给钢卷。
因此,大多退火炉都采取这
叶
一措施。
轮
中间 对流板
钢 卷
导
循 环
2、全氢 选择全氢作为保护气体,主要有以下几点: (1) 氢气的密度仅是氮气的1/14,氢气的导热系数是氮气的7倍。
氢气重量轻,渗透能力强,可以渗入钢卷层间,充分发挥导热系数大的 特点,显著提高传热效率;并可提高内罩内保护气体的循环量。
强对流全氢炉子技术特点
(2) 氢气作为还原性气体,在高温下能使FeO还原为铁,并能大幅 度降低由冷轧机带来的轧制油(残碳)。
任务三:退火设备结构
《板带冷轧生产》
强对流全氢炉子技术特点
1、强对流 罩式退火炉通过内罩对带钢进行间接加热,带钢获得热量多少取决
于内罩壁的辐射传热和气体对流传热的能力。 带钢层间存在间隙,而间隙中充满着空气,由于空气导热系数远远
低于钢板的导热系数,因此,带钢卷的径向导热能力很差。
提高带钢的传热效率
宝钢hph全氢罩式退火炉钢卷加热时间的研究

宝钢hph全氢罩式退火炉钢卷加热时间的研究随着社会的发展,轧制和热处理工业正在发展。
宝钢HPH全氢罩式退火炉钢卷加热时间的研究将有助于提高钢铁行业的效率和质量。
宝钢HPH全氢罩式退火炉是一种先进的退火设备。
它囊括了一种全新的技术,它利用全氢密封的复合罩来作为保护罩,而不是传统的氩气密封的罩子。
这种新技术可以更有效地把钢卷加热,并将有助于提高行业的效率和质量。
在使用宝钢HPH全氢罩式退火炉加热钢卷之前,首先要进行一定的热处理过程。
这种热处理流程主要包括热处理前的检查、适当的热处理温度的确定、恒定温度的维持以及加热时间的控制等。
此外,为了有效提高加热时间,应采用合理的加热温度和加热速率。
热温度过低造成的质量问题是影响宝钢HPH全氢罩式退火炉加热效率的主要
因素。
在加热过程中,还需要控制燃气混合物的组成,考虑炉温、料厚度、卷径等因素;加热时间也必须是恒定的,它取决于温度、料厚度和燃气混合物的组成。
除了确保热处理温度恒定,也要确保其它参数如送料速度、燃气混合物组成等也是恒定的。
此外,为了确保宝钢HPH全氢罩式退火炉加热时间的有效性,热处理室应建立完整的系统,经常对设备进行检查和保养,严格控制燃气混合物的比例,保持设备的清洁,及时更换滤芯,定期检查放料口的水质等。
宝钢HPH全氢罩式退火炉加热时间的研究在热处理行业中发挥
着重要作用。
它不仅可以改善钢铁行业的效率和质量,而且可以更有效地利用热处理技术,减少热处理过程中产生的费用。
因此,宝钢HPH全氢罩式退火炉加热时间的研究值得我们去发掘和深入探索,以更好地为热处理行业的发展和进步做出贡献。
全氢罩试退火炉1

• • • • • • • •
风量:80000-90000Nm3/h 风压:2100-2300Pa 电机主轴材质:1Cr25Ni20Si(固溶处理) 轴承及润滑脂:瑞典SKF进口产品 叶轮直径:φ950mm 叶轮材质:高镍合金耐热钢(去应力处理与转子组合平衡试验) 5)管路阀站 组成:充保护气分路(含阻隔氮分路)、充氮洗炉分路(含平衡氮 分路)、燃气分路、燃气放散分路、排废气分路、工艺水分路、冷却 水进水分路、炉台冷却水回水分路、内罩冷却水回水分路、阀门控制 仪表气分路。其中阀门为精选气动球阀、电磁阀、不锈钢手动球阀。 关键阀门带有状态反馈微动开关,确保自动控制安全。保护气和氮气 进气自动控制,通过高精度涡街流量计和智能浮子流量计实现瞬时流 量和累积量的现场测量显示压力和上位输出。炉内压力自动控制调节, 冷却水流量报警保护。并设置有阻隔氮和燃气过滤装置。 • 技术数据: • 保护气用量10-30Nm3/h.炉台
• 燃料:天然气 • 燃烧控制方式:比例连续调节+ON/OFF • 2,能源介质条件 • 1)保护气氛 氢气(H2) 纯度:H2 :>99.99% • 露点:<-60℃ 含O2 (氧气):<5PPm
•
• • •
气体用量:5~25N m³、座(气体用量根据不同工艺段改变) 接点压力(炉前):20000Pa
底座用于盛放钢卷、内罩和外罩。装有风机和导流装置。在底座上安 装了一个底座密封圈,当夹紧内罩时,它会将底座空间密封。 台循环风机:高效直联炉用风机,变频调速电机。 炉台底座:型钢和护板制成支撑底架与基础定位相联,承重保温座为 耐热钢板旋压反封头结构。内置绝热耐火纤维和耐热钢支撑。 对流托盘:高效扩散导流盘,全部由耐热钢构件制成,坚固耐用。在 额定荷载下,长期使用不变形。 炉座大法兰:材质普碳钢,镶有真空水冷密封胶圈,压紧后,保证工 作区间的气密性。洗炉氮气进气口、保护气进气口、排废气进出口、平 衡进排气口及炉台冷却水进水接口均在炉座上。罐内热电偶也均由炉座 引入,用于工作区温度控制、显示,记录和工艺控制(风机换速、冷却 喷淋、报警和过程结束)。 技术数据: 炉台有效承载能力:100吨 电机功率:22KW 电机转速:2080r/min 工作转速:1850r/min
全氢罩式炉
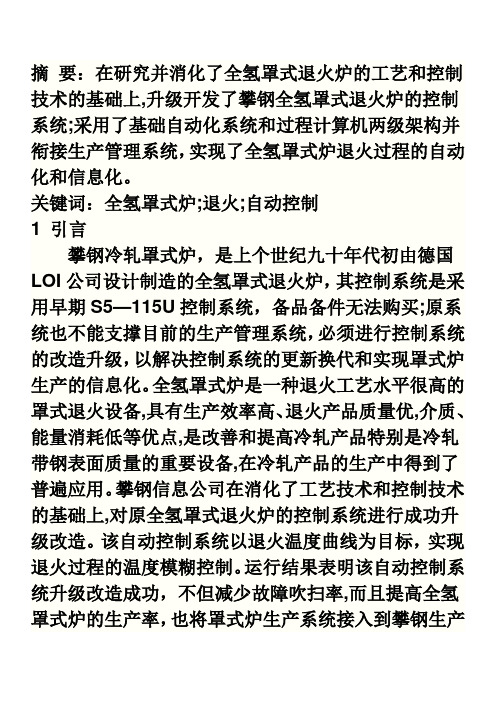
摘要:在研究并消化了全氢罩式退火炉的工艺和控制技术的基础上,升级开发了攀钢全氢罩式退火炉的控制系统;采用了基础自动化系统和过程计算机两级架构并衔接生产管理系统,实现了全氢罩式炉退火过程的自动化和信息化。
关键词:全氢罩式炉;退火;自动控制1 引言攀钢冷轧罩式炉,是上个世纪九十年代初由德国LOI公司设计制造的全氢罩式退火炉,其控制系统是采用早期S5—115U控制系统,备品备件无法购买;原系统也不能支撑目前的生产管理系统,必须进行控制系统的改造升级,以解决控制系统的更新换代和实现罩式炉生产的信息化。
全氢罩式炉是一种退火工艺水平很高的罩式退火设备,具有生产效率高、退火产品质量优,介质、能量消耗低等优点,是改善和提高冷轧产品特别是冷轧带钢表面质量的重要设备,在冷轧产品的生产中得到了普遍应用。
攀钢信息公司在消化了工艺技术和控制技术的基础上,对原全氢罩式退火炉的控制系统进行成功升级改造。
该自动控制系统以退火温度曲线为目标,实现退火过程的温度模糊控制。
运行结果表明该自动控制系统升级改造成功,不但减少故障吹扫率,而且提高全氢罩式炉的生产率,也将罩式炉生产系统接入到攀钢生产管理系统,实现了全氢罩式炉退火过程的自动化和信息化。
2 罩式炉退火工艺过程简述全氢罩式炉设备包括炉台、内罩、加热罩和冷却罩。
其工艺过程如下:炉台装料,放置内罩并利用液压装置压紧内罩;检验H2阀和炉台内罩密封性,确保系统安全;用氮气吹扫内罩内空气,使内罩内氧含量减少到1%以下,为通入氢气做好准备;在内罩外放置加热罩,内罩和加热罩之间为燃烧区间,用空气吹扫燃烧区间的残余煤气。
当内罩内氧含量低于1%时,开始加热点火;并用氢气置换内罩的氮气实现全氢气氛退火过程;退火过程的加热段、均热段,控制氢气流量吹扫;热密封测试;带加热罩冷却;吊走加热罩/热辐散/安装冷却罩;冷却罩冷却、喷淋水冷却;用氮气吹扫炉内氢气;钢卷吊运出炉。
3 控制系统设计根据全氢罩式炉工艺的特点和实施自动控制的需要,自动化系统架构采用两级控制系统和三级网络系统。
全氢罩式退火炉的工作原理

全氢罩式退火炉的工作原理全氢罩式退火炉是一种用于退火处理的热处理设备。
其工作原理是利用高温下氢气的还原性,通过氢气的作用,将金属材料表面的氧化层还原成金属,并消除材料内部的应力,使其获得更好的物理性能。
全氢罩式退火炉的主要组成部分包括炉体、加热元件、保护气体供应系统、氢气循环系统和控制系统等。
炉体是全氢罩式退火炉的主体部分,通常由高温合金材料制成,具有良好的耐高温性能。
炉体内部设有加热元件,可通过电阻加热方式提供高温环境。
加热元件通常采用电阻丝或电阻片,通过电流的通入,使其发热产生高温。
保护气体供应系统是为了保护金属材料表面不受氧化而设置的。
通常使用氢气作为保护气体。
氢气具有很强的还原性,能够将金属表面的氧化层还原成金属,从而减少表面氧化的程度。
保护气体供应系统由氢气源、气体管道和喷嘴等组成。
氢气源通过管道输送到喷嘴,然后喷射到金属材料表面,形成一个密闭的氢气环境,从而保护金属材料不受氧化。
全氢罩式退火炉还配备有氢气循环系统。
氢气循环系统的作用是将炉内的氢气循环使用,提高氢气的利用率。
氢气通过循环系统进入炉腔,与金属材料表面发生反应后,再通过循环系统回收,经过净化处理后再次使用。
这样可以节约氢气资源,提高设备的经济性。
全氢罩式退火炉还配备有控制系统,用于控制炉体的温度、氢气流量、氢气压力等参数。
控制系统通常采用计算机和仪表联动控制的方式,可以实现对退火过程的精确控制和参数记录。
通过控制系统,操作人员可以设定所需的退火温度和时间,并实时监控炉体的工作状态,确保退火过程的稳定性和安全性。
总结起来,全氢罩式退火炉是一种利用氢气的还原性对金属材料进行退火处理的设备。
通过高温加热和氢气的作用,可以消除材料内部的应力,还原金属表面的氧化层,从而改善材料的物理性能。
全氢罩式退火炉具有操作简便、效果稳定、能耗低等优点,广泛应用于金属制品的生产过程中。
- 1、下载文档前请自行甄别文档内容的完整性,平台不提供额外的编辑、内容补充、找答案等附加服务。
- 2、"仅部分预览"的文档,不可在线预览部分如存在完整性等问题,可反馈申请退款(可完整预览的文档不适用该条件!)。
- 3、如文档侵犯您的权益,请联系客服反馈,我们会尽快为您处理(人工客服工作时间:9:00-18:30)。
(2)退火类型: 光亮退火,球化退火、再结晶退火 退火温度:最高 870℃
(3)燃料种类: 混合煤气,焦炉煤气,天然气,液化石油气
(4)最大装炉量: 最大装炉量为125t,装炉高度5600mm
1.出炉时的照片
2.产品质量结果DDQ
抗拉强度 303 断裂延伸 43
屈服强度 177 90度R值 2.02 均匀延伸 24.0 90度N值 0.213
工艺阶段10 带冷却罩冷却
工艺阶段11 喷淋冷却
工艺阶段12 抽真空 / 充氮
工艺阶段13 移去冷却罩
工艺阶段14 移去内罩 / 炉台卸料
4、全氢罩式退火炉数学模型
(1) 退火过程模型: 对于特定的堆垛量,给出加热时间、保温时间、冷却时间。
重点是给出钢卷中心点温度变化值。 (2) 堆垛模型:
根据合同号和钢卷参数,给出最佳装炉量。 (3)车间管理模型:
达到钢卷力学性能及表面的光亮度的要求。 热处理分为中间退火,再结晶退火和完全退火。
未轧制前
轧制后
退火后
加热速度 对带钢的性能和表面质量有较大影响,一般为40~60℃/h,
400~723℃是再结晶形成阶段,加热速度必须控制。 保温温度和保温时间
再结晶温度在570~720℃ 带钢越薄,内能越大,越易形成再结晶,退火温度低。 带钢越厚,保温温度要高,保温时间要长。 冷却速度和出炉温度 对汽车板等特殊要求的钢种,冷却速度要求慢一些。 一般的钢种冷却速度尽可能快一些。 出炉温度一般在90~150℃。
使车间设备运行处于最佳状态,以降低运行成本。
★退火过程热工分析; 计算燃料消耗量; 计算退火过程钢卷断面温度分布; 计算退火过程保护气体温度分布; 计算监视点与卷边及卷芯温度的关系曲线; 操作参数和结构参数的影响分析。
★钢卷加热过程数学模型
★钢卷均热过程数学模型
★钢卷冷却过程数学模型
3、全氢罩式退火炉退火工艺
全氢罩式炉内钢
普通罩式炉内钢
800 卷外表面温度
卷外表面温度
5~10℃
25~30 ℃
600
400
普通罩式炉内
钢卷芯部温度
200
全氢罩式炉内 钢卷芯部温度
温度,℃
10
20
30
40
50
60
70
时 间,h
全氢罩式炉和普通罩式炉退火曲线比较
L3
Excel(VBA) Pro Print Delphi
2、全氢罩式退火炉设备组成
(1)机械设备 加热罩、冷却罩、内罩、炉台、对流板、液压系统、辅助设备。
(2)燃烧系统 烧嘴配置,点火和火焰监测。
(3)仪表系统 全氢管线仪表特点,氮气管线仪表特点,排放管线仪表特点,
冷却水管线特点。 (4)控制系统
基础控制系统:PLC功能,ET200,网络配置,OP监测。 上位计算机监控系统:计算机功能,服务器(数据库),工程 师站,操作计算机,数据输送。
800 700 600 500 400
全氢罩式退火炉温度测试
退火工艺曲线
炉台监测
生产管理
消息日志管理
模拟运行
时间估算
公辅管理
报表
温度跟踪
设定参数
故障信息
钢卷信息
炉群运行状态
状态信息
6、宝钢全氢罩式退火炉生产技术
(1)产品种类: 带钢:CQ、DQ、DDQ、EDDQ、HSS、HSLA、O5、IF钢、 电工钢,400系列不锈钢 线材和盘卷:82B、72B、57B、轴承钢、合金钢
(5)加热罩换热器----耐热式换热器使用一段时间后出现破损断裂。 原因:材质选择不当,结构不太合理。 对策:改进结构和材质。
(6)烧嘴损坏----变形断裂。 原因:材质选择和结构不太合理。 对策:改进结构和材质。
(7)压紧装置----使用一段时间后,出现转向不到位。 原因:油质问题,管道不清洁。已初步解决。
1、全氢罩式退火炉设备概述
(1)全氢罩式退火炉在钢铁生产中的地位: 罩式炉是带钢生产中的一个重要工序。
(2)热处理工艺 钢的塑性变形:钢在轧制过程中,各晶粒顺着轧制方向伸长,
压扁,破碎,在晶界形成大量位错,晶格变形,导致加工硬化。 冷轧钢板的σb≥680MPa,σs是670~660MPa, 产品要求σb 260~350MPa, σs ≤240MPa。 产品热处理的目的是消除轧制内应力和加工硬化及表面氧化,
显示器
OP
OP
PLC
3Com
PLC
3Com
操作终端
以太网
OP
服务器 OP
PLC
3Com
PLC
3Com
炉台1
炉台2
炉台40
炉台50
H2 N2
抽真空
真空泵
排放
现场照片:
罩式炉业务汇报
柳钢罩式炉炉群—2008年8月投产
柳钢罩式炉出炉钢卷
目前拥有的宝钢自主知识产权核心部件: 不锈钢罩式炉900 ℃高温特种电机(国内独家); 不锈钢罩式炉900 ℃高温叶轮(国内独家) ;
(3) 罩式退火炉的功能 达到产品热处理需要的温度,退火工艺曲线;
保证炉内温度均匀性 产品需要的加热速度、保温时间、冷却速度。
卷边温度点 卷心温度点
宝信全氢罩式炉目前的热处理能力覆盖范围: 400系列不锈钢带钢全氢罩式退火炉(国内独家); 碳钢冷轧带钢全氢罩式退火炉; 合金盘卷多垛纯氮、氮氢罩式退火炉; 铜管盘卷多垛全氢罩式退火炉; 铜带全氢罩式退火炉;
目前拥有的宝钢自主知识产权核心部件: 低噪恒压助燃风机(国内独家); 外置翅片式预热器(国内独家);
目前拥有的宝钢自主知识产权核心部件: 外置式烧嘴(国内独家);
目前拥有的宝钢自主知识产权核心部件: 液压油缸(国内独家); 燃烧控制器(国内独家); 氧含量变送器(国内独家); 宝信应用软件(国内独家);
Pro Archive
计划
实绩
ZSL L3 (Socket)
ODBC
ODBC
SQL Server Data Base
Delphi MMI
ODBC
Delphi Data Provider
设定值
实际信息
PLC
(Socket)
命令
DDE
Cimplicity 炉台系统状态图
全氢罩式退火炉计算机数据结构
下载退火计划
★内罩内的传热:
传导
•内罩与钢卷的辐射换热
•保护气与钢卷及内罩的对流换热
钢卷
•钢卷内部传热
辐射
★加热罩内传热:
对流板
•烟气与内外罩的对流与辐射换热
•内外罩表面的辐射换热 •加热罩外表面散热 •加热罩壁的传热
对 流
钢卷
内罩 对流
辐辐射射
加热罩
对流 辐射
气体辐射 对流
散热
导热 烧嘴
保护气体
燃气
ature /C
全氢罩式炉技术与设备简介
机电成套事业本部机电一体化事业部 工业炉窑部
2012年10月11日
内容简介
1、全氢罩式退火炉设备概述 2、全氢罩式退火炉设备组成 3、全氢罩式退火炉退火工艺 4、全氢罩式退火炉数学模型 5、全氢罩式退火炉的安全 6、宝钢全氢罩式退火炉生产技术 7、罩式退火炉生产中易出现的问题及解决方案 8、全氢罩式退火炉发展技术
RP02(N) 177 杯突
12.4
硬度A时效 46
屈服延伸 --
7、罩式退火炉生产中易出现的问题及解决方案
产品质量方面
(1)轧硬----卷心硬度超过产品允许硬度形成质量不合。 原因:保温时间太短,数学模型出现偏差。 对策:测试钢卷温度,校准数学模型。
(2)抗拉强度不合----抗拉强度和延伸断裂不合,晶粒粗大。 原因:保温时间太长,数学模型出现偏差。 对策:测试钢卷温度,校准数学模型。
★保护气体传热和燃料加热过程数学模型
宝钢宝信罩式炉专利技术:
罩式退火炉炉台:L00216961.4 罩式退火炉助燃空气预热器: 00218545.8 罩式退火炉热管换热器: 00218546.6 罩式炉用石油液化气烧嘴: 03270450.X 罩式退火炉炉台: 200320122844.0 罩式炉炉台:200620042254.0 罩式炉加热罩:200620042253.6
(6)卷边----退火后钢卷边部向内弯曲,这是罩式炉一大难题。 原因:中间对流板对钢卷边部造成伤害。 对策:已研究解决,有明显改善。
设备使用方面 (1)生产备件----尽可能在国内采购,缩短采购周期。特别是一些
变送器,应采用通用型,避免备件价格大大高于现 有设备的价格。 (2)备用液氮站----防止氮气管网中氧含量超标事故。 (3)烧嘴点火问题----使用一段时间后,出现许多烧嘴点不着火。 原因:主要是点火煤气质量问题,含水量超标。现已解决。 (4)O型密封圈----容易老化,使炉内漏气。 原因:冷却系统不合理,水质不好。在设计时要充分考虑 当地的水质情况设计冷却系统。
(3)表面结碳----出炉钢卷表面有碳黑层。 原因:轧制油太多,低温时保温时间偏短。 对策:延长低温保温时间,检查循环风机转速。
(4)表面发黄----出炉后钢卷表面有不均匀的黄色斑点。 原因:炉内可能有水,内罩法兰不密封。 对策:监测露点,更换O型密封圈。
(5)粘卷----带钢层间有粘结,严重时,两层无法分开。 原因:保温时间太长,冷却工艺有错。 对策:校准数学模型,优化冷却工艺。
工艺阶段1 炉台装料 / 设置内罩
工艺阶段2 压紧内罩
工艺阶段3 氢气阀密封试验
工艺阶段4 内罩和炉台 冷态密封试验