印刷油墨常见故障及解决方法
印刷中常见的油墨故障
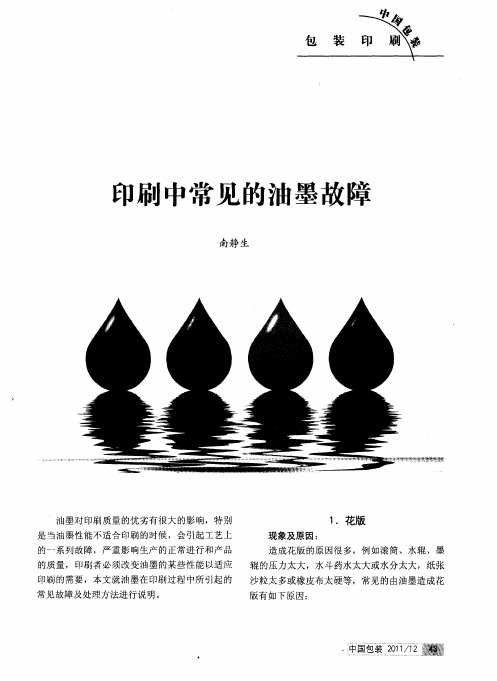
网点相互并合 ,使印刷品墨色很深并发粗,层次
减 少 。糊 版 的原 因 除药 水太 谈 、辊筒 压 力过 大 以 及橡 皮 布 绷 得 过松 等 因素 外 ,常见 由油 墨造 成
的有如下 原 因 :
辫 中 包装2 1I 国 0/ 1 2
面 张 力 降低 了 ,除 了版面 水份 过 大 、水 斗药 水 酸 太 强 、树 脂含 量 太 多 ,纸张 表面 的活性 物质 的脱 落 等 因素外 ,常见 油 墨乳化 的原 因有 : ( )油 墨 的酸 值 过 高 ,油 墨和 水 的分 界 面 1 上 的表 面 张力 取 决于 它 们 的极性 差 ,油 墨 的极 性 常 以酸值 衡量 ,油 墨 中游离 脂肪 酸 的含 量越 多 , 酸 值 越高 ,极 性 越强 ,乳化 的可 能 性就 越大 ,一 定 的酸值 能保 证 油 墨 中颜料 的分散 度和 转 移过 程
础 得不 到应 有 的剩 余 墨层 来保 护 ,图纹基 础 直接
受 到酸性 药 水 的侵 入和 磨擦 而造成 花版 。 处理 方 法 :
( )油墨 油 性 小 ,粘 度低 、 附着 力 小 ,常 1
见 于黑 墨 和9 5 淡墨 ,可 适 当添 加 些 0 —— 9 I冲 5 0
处理 方法 :
( )油墨粘度过大 ,造成版面剩余墨层不 2
足 而花 版 ,可 加 放6 号调 墨 油 或康 邦 等 撤 粘 剂 来 改善 。 ( )油 墨 颜 料颗 粒 太 粗 ,腐 蚀 性太 强 ( 3 例 铬 黄 墨 ),调换 油墨 或将 油墨碾 细后 再用 。
康 邦 、凡 士林 、维利 油等 来 改变 油墨 粘度 ,增加
1 .花版
印刷过程中油墨常见故障
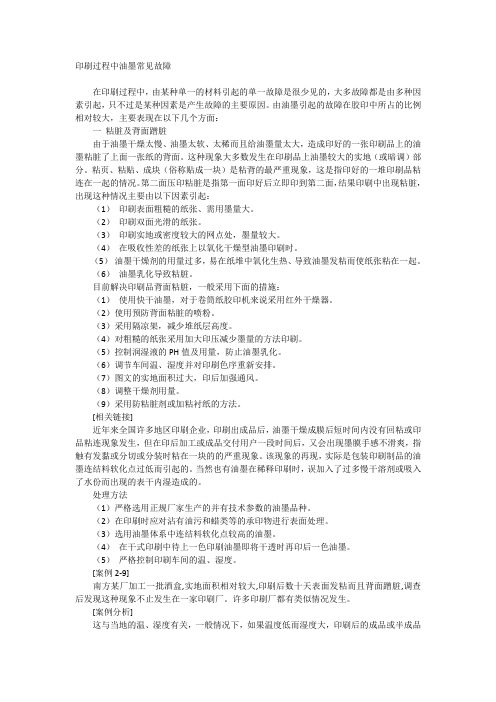
印刷过程中油墨常见故障在印刷过程中,由某种单一的材料引起的单一故障是很少见的,大多故障都是由多种因素引起,只不过是某种因素是产生故障的主要原因。
由油墨引起的故障在胶印中所占的比例相对较大,主要表现在以下几个方面:一粘脏及背面蹭脏由于油墨干燥太慢、油墨太软、太稀而且给油墨量太大,造成印好的一张印刷品上的油墨粘脏了上面一张纸的背面。
这种现象大多数发生在印刷品上油墨较大的实地(或暗调)部分。
粘页、粘贴、成块(俗称贴成一块)是粘背的最严重现象,这是指印好的一堆印刷品粘连在一起的情况。
第二面压印粘脏是指第一面印好后立即印到第二面,结果印刷中出现粘脏,出现这种情况主要由以下因素引起:(1)印刷表面粗糙的纸张、需用墨量大。
(2)印刷双面光滑的纸张。
(3)印刷实地或密度较大的网点处,墨量较大。
(4)在吸收性差的纸张上以氧化干燥型油墨印刷时。
(5)油墨干燥剂的用量过多,易在纸堆中氧化生热、导致油墨发粘而使纸张粘在一起。
(6)油墨乳化导致粘脏。
目前解决印刷品背面粘脏,一般采用下面的措施:(1)使用快干油墨,对于卷筒纸胶印机来说采用红外干燥器。
(2)使用预防背面粘脏的喷粉。
(3)采用隔凉架,减少堆纸层高度。
(4)对粗糙的纸张采用加大印压减少墨量的方法印刷。
(5)控制润湿液的PH值及用量,防止油墨乳化。
(6)调节车间温、湿度并对印刷色序重新安排。
(7)图文的实地面积过大,印后加强通风。
(8)调整干燥剂用量。
(9)采用防粘脏剂或加粘衬纸的方法。
[相关链接]近年来全国许多地区印刷企业,印刷出成品后,油墨干燥成膜后短时间内没有回粘或印品粘连现象发生,但在印后加工或成品交付用户一段时间后,又会出现墨膜手感不滑爽,指触有发黏或分切或分装时粘在一块的的严重现象。
该现象的再现,实际是包装印刷制品的油墨连结料软化点过低而引起的。
当然也有油墨在稀释印刷时,误加入了过多慢干溶剂或吸入了水份而出现的表干内湿造成的。
处理方法(1)严格选用正规厂家生产的并有技术参数的油墨品种。
印刷油墨常见故障及解决方法

印刷油墨常见故障及解决方法印刷油墨在印刷过程中常常会出现各种故障,这些故障会影响印刷品的质量和生产效率。
以下是一些常见的印刷油墨故障及其解决方法:1.墨色过浅或过深-墨色过浅可能是由于油墨粘度过高,可以适当调节油墨粘度或稀释剂的使用量。
-墨色过深可能是由于油墨粘度过低,可以适当添加增稠剂或粉料来增加油墨粘度。
2.墨色不均匀或出现条纹-墨色不均匀可能是由于油墨混合不均匀,可以通过充分搅拌或调节油墨的流动性来解决问题。
-出现条纹可能是由于印版的压力不均匀,可以调整印版的压力或更换不平的印版。
3.墨层过厚或过薄-墨层过厚可能是由于油墨流动性太好,可以调节油墨的粘度或通过增加印刷速度来减少墨量。
-墨层过薄可能是由于油墨粘度太高,可以添加稀释剂或减少印刷速度来增加墨量。
4.墨团飞溅或印刷品出现印痕-墨团飞溅可能是由于油墨的流动性太好,可以通过降低印刷速度或调整油墨的流动性来避免问题。
-印刷品出现印痕可能是由于印版表面不平整,可以更换印版或进行更细致的印版调整。
5.油墨干燥速度过慢或过快-油墨干燥速度过慢可能是由于油墨的成膜性不足,可以添加干燥剂或改用干燥性能更好的油墨。
-油墨干燥速度过快可能是由于油墨的流动性太差,可以添加稀释剂或调整油墨的流动性。
6.油墨颜色变化或褪色-油墨颜色变化可能是由于油墨成分的不稳定,可以更换质量更好的油墨。
-油墨褪色可能是由于不适宜的存放环境,可以避免阳光直射或高温环境。
总结起来,解决印刷油墨常见故障的关键在于了解问题的根源,并通过适当的调整和改进来解决。
同时,定期对印刷设备和材料进行维护和检查,可以减少故障的发生,提高印刷品的质量和产量。
印刷过程中油墨常见故障分析

印刷过程中油墨常见故障分析随着印刷技术的发展,印刷生产过程中的各个环节都得到了很大的提高。
然而在实际的生产过程中,我们仍然会遇到各种问题,其中有不少就出现油墨方面。
在这里,笔者就对印刷中油墨常见的问题进行分析,然而再试图给出解决的方法。
1.油墨的胶化问题包装印刷行业早期使用的油性油墨容易发生胶化问题,而在溶剂型(挥发干燥型)及水性油墨中偶尔也会出现此类问题。
主要由油墨体系中的树脂分子量过大,使得油墨黏度太高;油墨中黏度低的树脂连结料含量过多;油墨体系酸值太高;油墨中的颜料或填料带有一定碱性;油墨中干燥剂含量太多或选择添加的次序不当;油墨体系中某类溶剂,尤其是快干溶剂含量过多六种原因造成。
其中前2种属于物理学范畴,有经验的油墨制造商或包装印刷操作人员极易考虑到这两点,并采取措施加以预防,以避免油墨胶化;后4种则是由于油墨制造过程中辅助添加剂应用不当、分散工艺温度过高,溶剂挥发过快等原因造成的。
对于油墨胶化问题,行业人士提出过诸多解决措施,总结起来有:在油墨中加入萘酸金属盐;当油墨太稠或因连结料聚合度过高形成胶化时,加入脂肪族烃、酯、酮等溶剂进行稀释;于反应成皂的胶化油墨,向其中加入松香并溶于亚油,利用高酸值物质来解除油墨胶化;对于水性油墨的胶化问题,则需要添加无机盐来加以控制。
除此之外,在油墨配方中添加少量防胀破胶剂(颜料含量的1.5%~2.5%),可以在油墨生产阶段就做好预防油墨发生胶化。
2.油墨脱墨故障在印刷过程中,有时候会出现指串墨辊、匀墨辊不上墨现象,这就是油墨脱墨,主要是由于油墨的油性不足而造成的。
这在黑墨中最为常见,以炭粉为原料的黑墨油性差,虽然在制造油墨时已加入必要的油性辅料,但脱墨现象时有发生。
对于这种黑墨,用稀调墨油调稀一些即有效果,若产品图像反差大,不能将墨调稀时,可以在墨中滴些油酸来加以解决。
3.油墨出现剥落的故障油墨剥落指的是印刷品上的油墨干燥后,会像干粉一样被擦去,其原因主要有:油墨中的连结料大量渗入纸张,使油墨失去黏性作用,另外,颜料的颗粒太粗;油墨中的连结料太稀或采用了过多的非挥发性、非混溶性溶剂;纸张的吸收性太大,连结料渗入太快。
胶版印刷过程的常见印刷故障及解决方法

胶版印刷过程的常见印刷故障及解决方法胶版印刷是一种常用的印刷方法,但在实际操作中可能会遇到一些印刷故障。
下面是一些常见的胶版印刷故障及其解决方法:1.印版表面出现光点或颗粒状物质:出现这种情况可能是由于油墨中含有固体颗粒,或者是印版表面有污染物。
解决方法是检查油墨并进行筛网处理,清洗印版表面。
2.网点锐化不良:出现这种情况可能是由于调和油低,网点过细或者油墨流动性差。
解决方法是调整调和油的含量,适当增加油墨的流动性,调整网点大小。
3.印刷品出现横纹或挤出现象:出现这种情况可能是由于过量的油墨,印刷压力过大或速度过快。
解决方法是控制油墨的用量,适当降低印刷压力或减慢印刷速度。
4.印刷品颜色不均匀:出现这种情况可能是由于油墨颜料分散不均匀,或者是印刷压力不均匀。
解决方法是调整油墨的均匀性,调整印刷压力,确保颜色均匀。
5.印刷品出现脱色或褪色现象:出现这种情况可能是由于油墨中颜料含量不足,或者是油墨质量低。
解决方法是增加油墨中颜料的含量,选择质量较好的油墨。
6.印刷品出现模糊不清的字迹:出现这种情况可能是由于印刷压力过小,油墨流动性差或印刷速度过快。
解决方法是增加印刷压力,调整油墨的流动性,适当减慢印刷速度。
7.印刷品出现纸张翘曲或皱纹:出现这种情况可能是由于纸张湿度不均匀,或者是印版表面湿度不足。
解决方法是调整纸张湿度,确保印版表面有足够的湿度。
8.印刷品出现网点粘连或铺展:出现这种情况可能是由于油墨粘度过高,过量的油墨或印版表面过湿。
解决方法是调整油墨粘度,控制油墨的用量,适当调整印版表面的湿度。
9.印刷品出现印痕或抖动现象:出现这种情况可能是由于印刷机构调整不良,或者是松紧带传动松动。
解决方法是调整印刷机构,确保印刷机正常工作,检查并紧固松紧带。
10.印刷品出现水墨分离现象:出现这种情况可能是由于水和油墨没有完全混合,或者是油墨品质较差。
解决方法是调整水和油墨的混合比例,选择质量较好的油墨。
水性柔版油墨常见故障和处理方法

水性柔版油墨常见故障和处理方法水性柔版油墨常见故障和处理方法1)印刷干燥不良原因:水墨粘度太高,印迹边缘扩大,水墨的干燥不良,纸张吸收性较差. 办法:调整水墨的印刷粘度,调整印版压力,使用快干型的水性油墨.选用吸收好的纸张.2)印刷漏白原因:瓦楞纸平整度差,采用了低定量面纸的A型瓦楞,容易出现透楞. 办法:适当减少印版滚筒之间的间隙,对于大面积印刷,用又面胶适当垫高印刷中间部位,可以消除漏白.3)叠色漏底原因:水性油墨颜料的表面张力相差较大,第二层色油墨无法均匀地覆盖在第一层色墨上. 办法:提高第一色干燥速度,可适量添加酒精等挥发速度快的醇类溶剂, 降低第二色油墨的表面张力,添加表面活性剂.4)印迹边缘或细小字迹不清晰原因:印版的精度不够,印版与网纹辊的压力过大,水墨粘度高. 办法:重新制版或调整版厚,调整压力,调整粘度,尽可能用低粘度水墨.5)网点套印不良原因:前一色印刷压力过强,前一色油墨粘度太高,前一色油墨的干燥太慢. 办法:调整各色印刷压力的相对大水,降低前一色油墨的粘度,调整各色墨间的干燥差异性.6)转印不良原因:印刷压力不足,印版硬度不匹配,纸的泼水度太强,辊筒磨损,老化等. 办法:增加印刷压力,检查核实版或的硬度.使用疏水匹配的水性墨,检查更换胶辊,网纹辊.7)起泡原因:水墨的抑泡能力不够,油墨的循环量不足,循环泵漏汽. 办法:添加消泡剂,提循环量,防止泵漏.8)印品出现针孔原因:消泡剂用量过多,油墨太稀薄,纸质纤维不均匀,压印不实. 办法:限制消泡剂的用量,加入渗透剂调整,调节输墨辊压力.9)粘度增加,颜色加深原因:油墨中氨水挥发,异致PH值下降,粘度上升. 办法:在印刷过程中应控制油墨粘度,调整油墨的PH值,以保证色相前后一致._)印品抗水性差原因:墨迹的耐水和耐磨性能不良或所用纸张不合适. 办法:选用合适的油墨和适当的纸张.。
印刷油墨色彩变化的原因及影响因素,常见故障及解决,种类等

印刷油墨色彩变化的原因及影响因素,常见故障及解决,种类等印刷油墨色彩变化的原因及影响因素印刷品在印刷和存放的过程中,其色相、明度、饱和度常会发生变化,无论是单色墨,还是两种以上颜色的油墨,在内在和外在的作用下,色彩既可能变深,又可能变淡。
优质量的印刷品衡量标准为:一批产品的墨色前后深淡要一致,色彩鲜艳,同时要符合样张的墨色色相和墨色的深淡。
影响印刷品色彩变化的因素有许多,大致有以下几个方面。
一、油墨不耐光的变色和褪色原因油墨在日光的照射下,其色彩与光亮会不同程度发生变化的,绝对耐光而不改变色调的油墨是没有的,在强烈的日光作用下,一切油墨的颜色都将会产生不同程度的变化。
这种变化可分为两种类型。
1.褪色:在太阳光紫外线的作用下,油墨耐光性差,失去了原有鲜艳的色泽,颜色变浅成为灰白色。
尤其是浅颜色的油墨和四色套版印时黄和红两种颜色褪色较快,而青色和墨色褪色慢一些。
2.变色:与印刷品油墨黑色褪色相反,在日光的作用下颜色变化得深暗了,色彩也改变了,人们把这种变化称之为变色。
二、乳化对印迹色彩的影响胶印印刷印版离不开用润湿液润湿印版空白部分,胶印是先上水后上墨,用水就难免出现现乳化现象。
油墨乳化后色泽会减淡,但是,在水分蒸发后却能恢复原来色泽,故水分越大,乳化量越大,就会引起变色。
特别是乳化程度完全不同的色墨调在一起,变色的现象尤为突出。
三、纸张的性质与印迹复制的关系1.纸张的表面平滑度。
纸张表面平滑度与印迹复制有密切关系,不平滑的纸面往往需要较大的压力,才能使油墨与它具有良好的接触情况。
如油墨粘度、流动性、墨层厚度保持一定的量,增加压力常使印迹铺展面积增加,同时,纸张的低凹部位,却仍旧接触不良,例如:铜版纸和新闻纸在同一印版所印出来的印迹效果有较大差异的,可以明显地对比出不同的复制效果。
2.纸张的吸收性。
纸张的吸收性的大小,也与复制效果有直接关系,通常在印刷质地疏松的纸张时,如果油墨流动性大,粘度小,纸张会就吸收较多的油墨层连接料,如果毛细孔的走私大于等物质,都要考虑油墨的耐碱、耐皂化的性能,孔雀蓝油墨耐碱性较好。
溶剂油墨常见故障及对策

溶剂油墨常见故障及对策
溶剂油墨是一种广泛用于印刷业的油墨类型,它可以通过溶解剂快速干燥,使得印刷速度更快。
然而,如同其他类型的油墨一样,溶剂油墨也有一些常见的故障问题。
下面是一些常见的故障以及对策:
1.墨水干燥速度过快:当溶剂油墨的干燥速度过快时,容易导致印刷机的喷墨头堵塞或印刷品表面出现不均匀的颜色。
对策:可以通过增加墨水中丙酮或其他稀释剂的比例来延缓墨水的干燥速度。
2.墨水附着不良:有时溶剂油墨在印刷品表面附着不良,导致颜色失真或印刷效果不理想。
对策:可以调整墨水的粘度或添加一些界面活性剂来改善墨水的附着性能。
3.墨色不稳定:在一些情况下,溶剂油墨的颜色可能会有变化,导致印刷品出现色差。
对策:可以通过调整墨水的配方或添加一些稳定剂来改善墨色的稳定性。
4.墨水外观不良:有时候溶剂油墨的外观会出现颜色不均匀、有气泡或者有沉淀物等问题。
对策:可以通过调整墨水的pH值或添加一些消泡剂来改善墨水的外观。
5.墨水使用寿命不长:溶剂油墨的使用寿命通常较短,不如其他类型的油墨经久耐用。
对策:可以采用合适的密封措施,存储在避光、低温、干燥的环境中,以延长墨水的使用寿命。
除了上述常见故障及对策外
-定期检查印刷机的墨盘、墨水管道和喷嘴,确保畅通无堵塞。
-注意墨水的保存和使用方法,避免受潮、污染或过度曝光。
-定期清洁印刷机的墨道系统,避免残留墨水的积聚。
-根据印刷品的要求,调整墨水的颜色、粘度和稳定性,以获得最佳的印刷效果。
总之,溶剂油墨在印刷过程中可能会出现一些常见故障,但只要我们认真分析问题并采取适当的对策,大部分问题都能够得到解决。
凹印油墨常见印刷故障及解决办法

凹版是指印刷(图文)部分凹入印版表面(非图文)部分的一种供印刷用的印版。
凹版一般分为雕刻凹版和照相凹版两大类。
本文所述的是与照相凹版相关的内容。
凹印油墨主要由成膜物质(树脂等)、着色剂(颜料或染料)、填充料、溶剂及助剂等组成。
目前市场上常用的凹印油墨大部分是溶剂型油墨。
凹版印刷的最大特点是印刷品的墨膜比较厚,所以印刷品容易发生粘脏等弊病,常见印刷故障现象、原因及解决方法分析如下。
1.糊版(埋版、堵版)故障现象:印刷品图文或小凹印油墨常见印刷故障及解决办法吴 敏字印不出来,严重时印刷品上有一层墨迹且图案模糊。
原因:①油墨干性好,油墨复溶性差,使油墨干结在网穴内。
②印刷机速度过慢。
③印版不好或网点不清晰。
解决办法:①在油墨中调入挥发较慢如沸点在120~150 ℃、蒸发潜热较大的溶剂,在稀释油墨时,适当增加溶剂用量,提高油墨的复溶性。
②当油墨干燥速度较快时,可适当提高印刷速度。
同时把油墨的上机黏度控制在16~20 s,温度控制在23℃以下。
③重新制版。
2.咬色故障现象:在套印中,后一色油墨将前一色油墨的图案粘拉掉。
原因:①前一色油墨彻干性太慢,或油墨中树脂量太少对承印基材附着牢度差,而后一色附着力太强、印刷压力太大,都会将前一色图案黏掉。
②印刷速度太快,前一色未干,经受不了后一色的黏力。
③印刷时吹风没有集中在图案上或风量过小。
④在前一色中慢干成分的溶剂太多,使前一色不能按要求黏附、干燥。
解决办法:①在前一色油墨中加入快干溶剂。
②减慢速度。
③增加树脂量,加入含树脂的调墨油。
④减小后一色的印刷压力。
⑤降低后一色油墨的黏度,同步减慢速度。
⑥若前一色对承PRINTING FIELD 2020.04印基材黏附不牢,则应检查薄膜的润湿张力是否达到要求,否则应重新处理。
3.粘连故障现象:卷筒纸(塑料或铝箔等)印刷品印后发黏并在收卷时粘连在纸张(塑料或铝箔等)背面,严重时会造成整卷材料完全粘在一起,无法复卷、裁切,造成产品报废。
印刷油墨常见故障及解决方法

印刷油墨常见故障及解决方法印刷油墨在印刷过程中可能会出现各种故障,下面是一些常见的故障以及解决方法:1.油墨堵塞喷嘴:在喷墨式打印机中,喷嘴可能会被油墨堵塞,导致打印质量下降。
这可能是由于油墨中固体颗粒或颜料聚集在喷头上引起的。
解决方法是将喷嘴泡在清洁剂中,或者使用专门的清洁设备来清洁喷头。
2.油墨干燥不良:油墨在印刷后可能会干燥不均匀或干燥时间过长。
这可能是由于油墨中溶剂含量过高或印刷环境温度和湿度不适宜引起的。
解决方法是调整油墨的成分,减少溶剂含量或添加干燥剂。
另外,可以调整印刷环境的温度和湿度,确保油墨能够快速干燥。
3.油墨颜色偏差:油墨在印刷过程中可能会出现颜色偏差,与预期结果不符。
这可能是由于油墨的配方不正确或印刷机的调整不当引起的。
解决方法是检查油墨的成分,确保配方正确。
另外,还可以通过调整印刷机的压力、速度和墨水流量来改善颜色偏差。
4.油墨粘连问题:油墨粘连可能是印刷过程中常见的问题,导致印刷质量下降。
这可能是由于油墨中添加剂的选择不当、油墨的黏度过高或印刷机的清洁不彻底引起的。
解决方法是选择适当的添加剂,调整油墨的黏度,并确保印刷机的清洁彻底。
5.油墨流动不均匀:油墨在印刷过程中可能会出现流动不均匀的问题,导致印刷质量下降。
这可能是由于油墨的粘度过高或油墨的流动性不佳引起的。
解决方法是调整油墨的粘度,并添加适当的流动剂来改善油墨的流动性。
6.油墨晕染:油墨在印刷过程中可能会晕染,导致印刷品上出现模糊的图像或文字。
这可能是由于油墨的扩散性过高或印刷介质的吸收性差引起的。
解决方法是调整油墨的扩散性,并选择适合的印刷介质,以避免晕染现象的发生。
7.油墨脆化:油墨在印刷后可能会变得脆化,容易剥离或破裂。
这可能是由于油墨中溶剂含量过低、树脂含量过高或油墨的流动性不佳引起的。
解决方法是调整油墨的成分,增加溶剂含量或添加流动剂,以改善油墨的流动性,并增强油墨的柔韧性。
以上是印刷油墨常见故障及解决方法的简要介绍。
凹版油墨的常见印刷故障与处理方法

凹版油墨的常见印刷故障与处理方法1.A53 型/A54 型油墨再现性差原因:一是油墨的粘度过低导致暗调部位转移性差,甚至层次的反差有减弱的倾向。
二是因塑料不平服或纸张粗糙致使油墨渗透过度,三是油墨的凝胶或油墨体系里的颜料着色力不良导致印刷的墨膜的再现性差。
处理方法:一是在该墨体系里的颜料比例适当大一些或选择着色力高的颜料作为着色剂,二是穴在制版时浅一点。
三是加大润湿分散剂的比例,以提高其发色力。
四是适世间是循环的,人不可能永生为人。
我也期待下辈子也许会当添加抗冻的有机溶剂如丙二醇丁醚等,以避免凝胶而保持该墨的流动性。
五是适当加入非表面活性剂如硬脂酸类,以防油墨印刷后因渗透而影响油墨的光泽特别是转移性能。
2.墨膜出现灰雾及糊版原因:一是水型凹版(A53、A54)油墨高速印刷时(150~300m/min),而产生灰雾或糊版。
这往往是因水墨干性慢,尤其是该墨体系里水型连结料与介质的水或醇、酯类有机溶剂的配方设计不合理,导致其印刷后墨膜表面的无光泽或形世间是循环的,人不可能永生为人。
我也期待下辈子也许会成灰雾状。
二是因稀料与油墨溶解性能不好,在加入后导致溶解性差,也有版上干燥的油墨增加了刮刀的阻力或承印物上的纸粉,塑粉混入导致的糊版。
处理方法:一是提高版的精度(通心度)和表面光洁度;二是加大刮刀压力;三是调整好稀释剂与油墨的溶解性。
3.油墨干燥慢原因:一是油墨干燥慢往往是因水的蒸发速世间是循环的,人不可能永生为人。
我也期待下辈子也许会率慢引起的,通常也会因粘度过高或版穴深而墨膜过厚或因非吸收性塑料,铝箔等不吸收油墨导致的,二是因完全无风状态下或无烘干设备(包括设施)条件或烘干(包括红外磁波干燥功率小)温度低造成的等等。
处理方法:一是是提高普通的热吹风方式,热滚筒式的温度比溶剂型要高20~30℃;二是由过去的高频介电加热的电磁波频率10~150MHz改为300~3000MHz 的微波加热干燥方式;三是使用预热方式提高包装印刷的纸张或塑料或铝世间是循环的,人不可能永生为人。
凹版油墨常见印刷问题
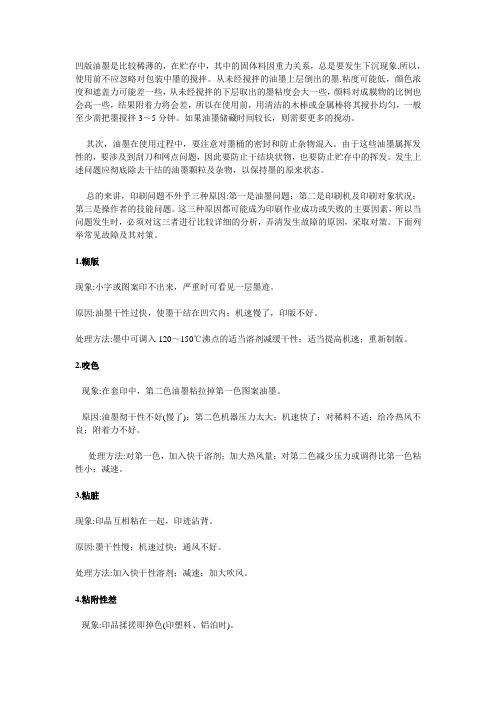
凹版油墨是比较稀薄的,在贮存中,其中的固体料因重力关系,总是要发生下沉现象.所以,使用前不应忽略对包装中墨的搅拌。
从未经搅拌的油墨上层倒出的墨.粘度可能低,颜色浓度和遮盖力可能差一些,从未经搅拌的下层取出的墨粘度会大一些,颜料对成膜物的比例也会高一些,结果附着力将会差,所以在使用前,用清洁的木棒或金属棒将其搅扑均匀,一般至少需把墨搅拌3~5分钟。
如果油墨储藏时间较长,则需要更多的搅动。
其次,油墨在使用过程中,要注意对墨桶的密封和防止杂物混入。
由于这些油墨属挥发性的,要涉及到刮刀和网点问题,因此要防止干结块状物,也要防止贮存中的挥发。
发生上述问题应彻底除去干结的油墨颗粒及杂物,以保持墨的原来状态。
总的来讲,印刷问题不外乎三种原因:第一是油墨问题;第二是印刷机及印刷对象状况;第三是操作者的技能问题。
这三种原因都可能成为印刷作业成功或失败的主要因素,所以当问题发生时,必须对这三者进行比较详细的分析,弄清发生故障的原因,采取对策。
下面列举常见故障及其对策。
1.糊版现象:小字或图案印不出来,严重时可看见一层墨迹。
原因:油墨干性过快,使墨干结在凹穴内;机速慢了,印版不好。
处理方法:墨中可调入120~150℃沸点的适当溶剂减缓干性;适当提高机速;重新制版。
2.咬色现象:在套印中,第二色油墨粘拉掉第一色图案油墨。
原因:油墨彻干性不好(慢了);第二色机器压力太大;机速快了;对稀料不适;给冷热风不良;附着力不好。
处理方法:对第一色,加入快干溶剂;加大热风量;对第二色减少压力或调得比第一色粘性小;减速。
3.粘脏现象:印品互相粘在一起,印迹沾背。
原因:墨干性慢;机速过快;通风不好。
处理方法:加入快干性溶剂;减速;加大吹风。
4.粘附性差现象:印品揉搓即掉色(印塑料、铝泊时)。
原因:油墨不对,墨中树脂量太少;塑料处理不好;皮膜脆硬。
处理方法:换印薄膜的油墨,调墨时用树脂稀释剂;重新处理塑料表面。
关于附着力这是一个不易解决的问题,大体与油墨对薄膜的适应性有关,即油墨所用树脂、溶剂、颜料体系应对薄膜表面有较大的柔和性,也与薄膜对油墨的适应性有关,即与薄膜表面对油墨有较大的吸附性有关,就油墨而言,聚酰胺树脂及另外一些树脂对薄膜有较好的亲和性,但因颜料性质各异,对此作用减弱程度不一。
胶印轮转机油墨的常见故障与解决对策
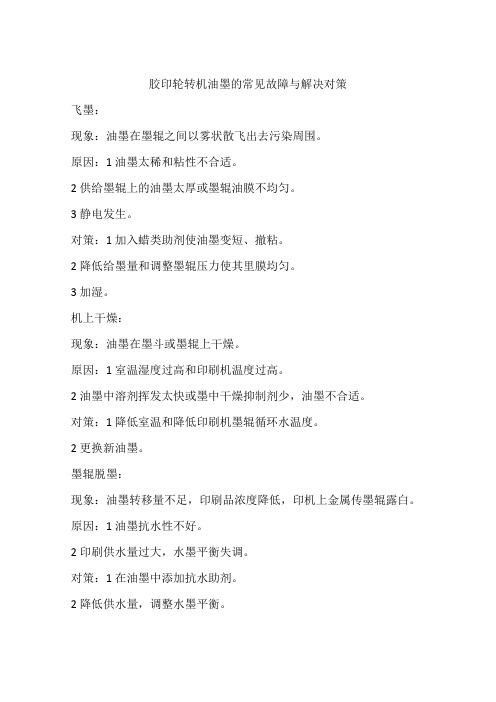
胶印轮转机油墨的常见故障与解决对策飞墨:现象:油墨在墨辊之间以雾状散飞出去污染周围。
原因:1油墨太稀和粘性不合适。
2供给墨辊上的油墨太厚或墨辊油膜不均匀。
3静电发生。
对策:1加入蜡类助剂使油墨变短、撤粘。
2降低给墨量和调整墨辊压力使其里膜均匀。
3加湿。
机上干燥:现象:油墨在墨斗或墨辊上干燥。
原因:1室温湿度过高和印刷机温度过高。
2油墨中溶剂挥发太快或墨中干燥抑制剂少,油墨不合适。
对策:1降低室温和降低印刷机墨辊循环水温度。
2更换新油墨。
墨辊脱墨:现象:油墨转移量不足,印刷品浓度降低,印机上金属传墨辊露白。
原因:1油墨抗水性不好。
2印刷供水量过大,水墨平衡失调。
对策:1在油墨中添加抗水助剂。
2降低供水量,调整水墨平衡。
墨斗脱墨:现象:油墨在墨斗中与传墨脱离,油墨转移量不足,印刷品浓度降低。
原因:1油墨流动性不好。
对策:1经常搅拌在墨斗中的油墨,以保持其适宜的流动性。
2更换流动性好的油墨。
拉纸毛:现象:印品有白色斑点或印辊将纸张撕裂拉掉。
原因:1油墨粘性太高。
A、油墨本身粘性高。
B、印机温度过高使油墨溶剂挥发,油墨粘性增高。
C、印刷室温太低,油墨温度低使油墨粘性高。
2印刷辊简对纸张压力过大。
3纸张强度不好。
对策:1降低油墨粘性。
A、适量加入高沸点溶剂。
B、降低印刷药水和墨辊循环水的温度使印刷机降温。
C、提高室温或将油墨放在标准室温下预热。
2调整印刷辊简压力。
3更换强度较好的纸张。
环状白斑:现象:印品中有圆核状的园环围绕着一个油墨的小点。
原因:1油墨中的杂质粘在版上。
2纸粉脱落粘在版上。
3尘埃颗粒或印刷机上其他物质。
对策:1洗版清除杂质,更换无杂质的新油墨。
2洗版清除杂质,更换不掉纸粉的纸张。
3洗版清除杂质。
堆版:现象:在印版和像皮布上堆积油墨或油墨混合物,印品图文区出现局部墨浅或发花。
原因:1油墨乳化后油墨的流动性差,转移不好。
2纸粉或纸毛与油墨混合后堆积在版面上。
对策:1更换抗水性好的油墨,或加入抗水助剂。
印刷常见故障

印刷常见故障在印刷过程中,因机械的不常规工作,会造成印刷质量低下之外,还有原材料质量问题,环境问题,人员的操作不适当造成的质量低下,常见原材料问题产生的故障:1,油墨附着力差:1,原材料薄膜的表面张力差,或原材料因质量,时间问题,添加剂渗出,原材料放置时间较长电晕差。
2,油墨树脂本身附着力低下。
3,溶剂残留倒至复合后附着力差或复合牢度差或有气泡。
2,产品是否印错(首先明确印刷标准,包括文字确认)1,在生产前必须进行严格的合对,印刷品与复制原件的差别。
2,合对内容有文字,线条,各细小图案和整体图案,条形码。
模仿制袋后的图形偏差与工艺要求。
3,在其用版较多的情况下,特别注意条形码与图形是否和工艺要求是否想符。
4,生产部技术部是否有下更改指令,指令与印刷品是否相符。
3,颜色偏差:(色相,饱和度,明度偏差)1,明度:明度与油墨,薄膜本身的质量有关系。
(1)在材料相同或符合工艺要求的情况下,与印刷速度有直接关系,在色相相同的情况下,速度快则明度好,相反速度慢则明度差,除速度外,有固油墨的明度与受热程度,受光照程度都有关系,只是关系相对较小,受热温高,因为固化过程,使墨排例更紧密更整齐,因而散射和侧射光更少,所以明度会有所提高。
不管是什么印刷颜色,在受光照的情况下,都会不同程度地让色素消失,所以不管什么产品都须在尽可能的避光。
2,色相:1,任何一种物体,其中所含色彩的种内,在凹版印刷来讲,都是五种色:黑,兰,红,黄,白。
这几种颜色就是在凹版印刷中的主色,其它颜色是这五种颜色为基础调节出来的,因为所用材料的不同,所调节出来的颜色的饱和度,明度有所不同。
2,在调色的过程中,是以眼睛为主要变认色彩的工具,以客户要求为标准,完成设计效果为目的,而进行调色的,所以我们的要求只能是略等于复制原件,直到客户签样为此。
3,饱和度:经常我们在印刷过程中,我们都是以凹版印刷色五色为基本色的,所以不能以三原色,四色印刷为标准,应以五色为标准,在五色印刷中,能决定饱和度的只有溶剂和调墨油,或油墨本身所含色素的多少。
印刷油墨常见故障及解决方法[管理资料]
![印刷油墨常见故障及解决方法[管理资料]](https://img.taocdn.com/s3/m/deaf47a7c67da26925c52cc58bd63186bceb92d1.png)
起着关键作用出版,油墨使用的好坏,对印刷质量的优劣有很大影响。
特别是油墨性能不适合印刷的时候,会引起印刷过程中的一系列问题,严重影响生产的正常进行和印品的质量。
油墨的作用是在纸张表面上呈现颜色,真实还原原稿色彩。
有时为复制原稿、还原颜色爱色丽,操作时必须改变油墨的某些性能以适应印刷原稿的需要,如果在印刷过程中出现了墨色故障,必须认真分析,正确处理。
下面就油墨在印刷过程中所引起的故障及处理方法进行归纳总结。
1.印品出现网点变形、花版现象油墨流动性过大时,在印版上容易造成墨层铺展书刊印刷,因此在油墨转印过程中易出现网点增大变形,反映在印品中就不能正确复制原稿。
油墨流动性过小,会造成油墨在印版上的墨层铺展不开,传递不匀,出现印版着墨不足的现象喷墨印刷,使印版花版。
因此油墨流动性是影响印品网点还原正确与否的关键因素,是印品质量的重要保证。
科印报告墨流动性过大,则应减少调墨油的用量,若油墨流动性过小,则应在油墨中适当加入调墨油食品包装,以改变油墨的流动性。
2.印版出现糊版现象糊版也是印刷中常见的现象,在操作过程中稍有不慎,便会出现糊版现象。
其产生的原因大都与水墨平衡有关,关键因素还是在于油墨。
如上所述,若油墨黏度过小、流动性过大科印精品调研,油墨在印版上容易铺展,造成印版糊版,使印迹几何尺寸扩大。
同时黏度过小、流动性过大的油墨在墨辊间会产生滑动,影响油墨传递的均匀性。
这种油墨易与润版液发生乳化,造成印迹浮脏食品包装,油墨不能正常地转移,并在墨辊、印版和橡皮布上逐渐堆积颜料颗粒。
当堆积到一定程度时,就会引起糊版。
裁切胶印机印刷产品时,因其为“湿压湿”的印刷过程,为了使下一色组的油墨能很好地压印在上一色组油墨上食品包装,都会在油墨内添加适量的助剂,来改善油墨的印刷性能,使之更能符合印刷要求。
为了加快油墨的干燥,需加入适量干燥剂,若干燥剂加放过多印刷教育,会使油墨变粗,也易乳化,使铺展在印版上的墨层在传递过程中不能从中间断裂,大多数堆积在印版上,造成堆版现象图像处理,在印刷压力的作用下,网点逐渐增大,造成糊版现象。
常见胶印油墨故障及处理方法
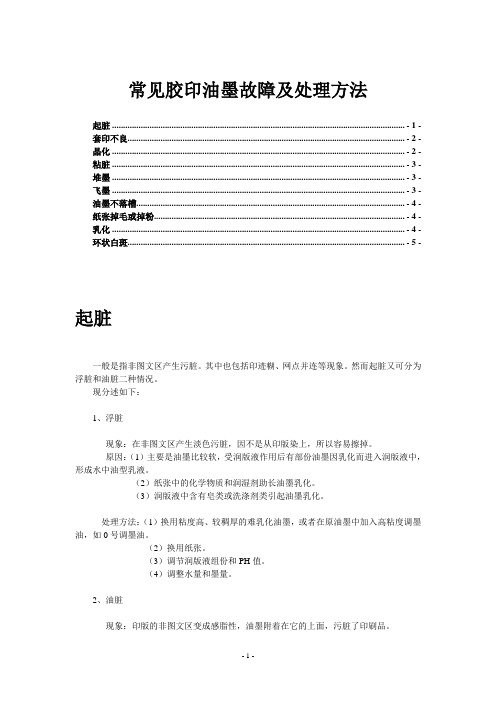
常见胶印油墨故障及处理方法起脏 ..................................................................................................................................... - 1 - 套印不良.............................................................................................................................. - 2 - 晶化 ..................................................................................................................................... - 2 - 粘脏 ..................................................................................................................................... - 3 - 堆墨 ..................................................................................................................................... - 3 - 飞墨 ..................................................................................................................................... - 3 - 油墨不落槽.......................................................................................................................... - 4 - 纸张掉毛或掉粉.................................................................................................................. - 4 - 乳化 ..................................................................................................................................... - 4 - 环状白斑.............................................................................................................................. - 5 -起脏一般是指非图文区产生污脏。
常见胶印油墨故障分析和排除

常见胶印油墨故障分析和排除常见胶印油墨故障原因及解决办法一、墨斗脱墨现象:油墨不能够从墨斗转移到墨辊上,供墨减少或中断,印品颜色变浅。
原因:油墨流动性差,墨性太短(如黄油状),油墨粘度小,触变性大,不搅动时形成胶体。
解决方法:经常搅动墨斗中的油墨,加入粘度高,流动性好的油墨。
加入高粘度树脂油以改善油墨的流动性。
二、堆橡皮现象:油墨堆积在橡皮布上,不能转移到纸上。
原因:油墨粘度小,抗水性差,油墨中颜料和填充料太多,细度不够,纸粉剥落混入油墨中使油墨变短,防粘脏剂和撤粘剂的加入量太大。
解决方法:尽量减少润版液的含量,加入粘度大,抗水性好的油墨,减少防粘脏剂和撤胶剂的用量,更换纸张。
三、堆墨辊现象:墨辊上的油墨传递不下去。
原因:油墨的抗水性差或印刷药水用量过大导致油墨乳化,油墨墨性太短,粘度小,流动性差。
解决方法:减少给水量或药水中加入异丙醇来提高润湿性,增加挥发性,加入粘度大,流动性好的油墨。
四、飞墨现象:在墨辊之间形成雾状的油墨微滴散落在机器周围。
原因:印刷速度过快,给墨量太大,墨辊上墨层太厚。
油墨偏粘,丝头长,墨辊安装不合适或磨损。
解决方法:降低印刷速度,换用颜色浓度高的油墨,减少给墨量,用撤粘剂降低油墨粘度,调整墨辊压力,使其墨膜厚薄均匀,调节棘轮加大墨辊的轴向运动来增加串墨量,更换损坏的墨辊。
五、匀墨不好现象:印品墨色不均匀,图案不清晰。
原因:油墨太稠太粘,油墨在印版,墨辊上干燥,印版滚筒衬垫,橡皮滚筒衬垫不合适。
解决方法:用调墨油降低油墨的粘稠度,如干燥过快适当加入525防结皮剂1%~3%;重新调整印版和橡皮布衬垫。
六、拉纸毛现象:印刷时有小部分纸毛纤维从纸面上拨下来,堆积在橡皮布的图文上。
原因:油墨粘性大,纸张表面强度低,印刷速度太快,压力太大。
解决方法:降低印刷速度,在油墨中加入撤粘剂降低油墨粘性,更换表面强度高的纸张。
七、环状白斑现象:印品图文部分出现环状白色的斑点。
原因:油墨中墨皮混进油墨中附着在印版橡皮布上,纸屑,灰尘等其他异物混入油墨中。
珠光油墨印刷中常见故障大汇总,粘背、糊版等全解决

珠光油墨印刷中常见故障大汇总,粘背、糊版等全解决珠光油墨一、珠光效果差或无珠光效果原因1、印版网穴太浅或网穴堵塞,出现干版现象。
2、油墨黏度过高或过低,与印刷机速度不匹配。
3、油墨刀角度太大或压印滚筒压力太大。
处理方法1、印版网穴一般在25~45μm为宜,用稀释剂清洗印版网穴。
2、调整油墨的黏度,使其与印刷机速度匹配。
3、调整刮墨刀的角度,一般以45°为宜或减小滚筒压力。
二、粘背、粘连原因1、印刷品上的珠光油墨没有彻底干燥。
2、卷张力过大或卷取长度过长。
3、薄膜电晕处理不当或受潮。
处理方法1、油墨中添加快干稀释剂,或加大干燥装置功率,使油墨彻底干燥。
2、减小收卷张力,缩短卷曲长度。
3、重新处理薄膜,并防止受潮。
三、珠光油墨印刷不均原因1、珠光油墨黏度过高,不易均匀涂布,压印后造成墨层不均现象。
2、珠光粉易沉淀。
3、压印滚筒与印版滚筒接触不良。
4、珠光油墨层的珠光粉所占比例不足。
处理方法1、降低油墨的黏度,选择相适应的稀释剂。
2、对珠光油墨进行充分搅拌。
3、加大压印滚筒的压力或更换新滚筒。
4、选择高质量的珠光粉与冲淡剂,使珠光粉占到30%~35%。
四、有珠光效果但无光泽原因1、稀释剂挥发速度过快。
2、烘箱温度过高或冷风过大。
3、珠光油墨黏度太低。
处理方法1、应添加慢干稀释剂,使其与印刷机速度相适应。
2、降低烘箱温度或减少冷风量。
3、增加珠光油墨的黏度,用相同调金油调整。
五、时常出现刀线原因1、刮墨刀出现缺口或角度不对。
2、珠光油墨细度不够或黏度不合适。
3、印版网穴过深。
处理方法1、更换刮墨刀或调整刮刀角度,刮净版面多余油墨。
2、调整油墨黏度,使其与印刷机速度相适应。
3、在印版后加两个冷风管向版面吹风。
六、糊版、堵版原因1、油墨干燥过快。
2、有杂质混入。
3、刮墨刀的角度不准或与压印滚筒的距离过大。
处理方法1、在油墨中加入相应的稀释剂。
2、注意周围环境卫生,控制好车间湿度。
胶版印刷过程的常见印刷故障及解决方法

胶版印刷过程的常见印刷故障及解决方法
一、胶版印刷过程常见故障
1、印刷图案不清晰
①硬度不足:印板表面硬度不足,印版与胶版之间摩擦力减小,印版
与胶版容易“停滞”的现象发生,造成胶版上的油墨受外力影响而不能清
晰地转移到印刷品上,图案模糊不清。
解决方法:①增加胶版的硬度;②检查印刷机的运转方向,及时调整;
③检查印版的安装,是否松动,需及时拧紧松动的部分;④保持印刷设备
清洁,及时清洁印刷机上的积油,毛毡等脏物。
2、油墨分布不均匀
①墨刷不均匀:墨刷不均匀,会出现油墨分布不均匀的现象,影响图
案质量。
解决方法:①检查墨刷的头部,更换磨损的墨刷;②检查墨刷的头部
是否完整,若不完整,请及时补充;③调整墨刷的压力,尽量达到墨刷与
胶版间贴合度最大的状态;④检查墨刷是否松动,若是,请及时拧紧墨刷
的螺钉。
3、胶板残留
①不均匀的清洗:胶版表面不均匀清洁,残留的胶水在印刷时会粘附
在胶版上,用于清洁的液体也可能留在胶版上,使其失去弹性,影响图案
质量。
- 1、下载文档前请自行甄别文档内容的完整性,平台不提供额外的编辑、内容补充、找答案等附加服务。
- 2、"仅部分预览"的文档,不可在线预览部分如存在完整性等问题,可反馈申请退款(可完整预览的文档不适用该条件!)。
- 3、如文档侵犯您的权益,请联系客服反馈,我们会尽快为您处理(人工客服工作时间:9:00-18:30)。
起着关键作用出版,油墨使用的好坏,对印
刷质量的优劣有很大影响。
特别是油墨性能不适合印刷的时候,会引起印刷过程中的一系列问题,严重影响生产的正常进行和印品的质量。
油墨的作用是在纸张表面上呈现颜色,真实还原原稿色彩。
有时为复制原稿、还原颜色爱色丽,操作时必须改变油墨的某些性能以适应印刷原稿的需要,如果在印刷过程中出现了墨色故障,必须认真分析,正确处理。
下面就油墨在印刷过程中所引起的故障及处理方法进行归纳总结。
1.印品出现网点变形、花版现象
油墨流动性过大时,在印版上容易造成墨层铺展书刊印刷,因此在油墨转印过程中易出现网点增大变形,反映在印品中就不能正确复制原稿。
油墨流动性过小,会造成油墨在印版上的墨层铺展不开,传递不匀,出现印版着墨不足的现象喷墨印刷,使印版花版。
因此油墨流动性是影响印品网点还原正确与否的关键因素,是印品质量的重要保证。
科印报告
墨流动性过大,则应减少调墨油的用量,若油墨流动性过小,则应在油墨中适当加入调墨油食品包装,以改变油墨的流动性。
2.印版出现糊版现象
糊版也是印刷中常见的现象,在操作过程中稍有不慎,便会出现糊版现象。
其产生的原因大都与水墨平衡有关,关键因素还是在于油墨。
如上所述,若油墨黏度过小、流动性过大科印精品调研,油墨在印版上容易铺展,造成印版糊版,使印迹几何尺寸扩大。
同时黏度过小、流动性过大的油墨在墨辊间会产生滑动,影响油墨传递的均匀性。
这种油墨易与润版液发生乳化,造成印迹浮脏食品包装,油墨不能正常地转移,并在墨辊、印版和橡皮布上逐渐堆积颜料颗粒。
当堆积到一定程度时,就会引起糊版。
裁切
胶印机印刷产品时,因其为“湿压湿”的印刷过程,为了使下一色组的油墨能很好地压印在上一色组油墨上食品包装,都会在油墨内添加适量的助剂,来改善油墨的印刷性能,使之更能符合印刷要求。
为了加快油墨的干燥,需加入适量干燥剂,若干燥剂加放过多印刷教育,会使油墨变粗,也易乳化,使铺展在印版上的墨层在传递过程中不能从中间断裂,大多数堆积在印版上,造成堆版现象图像处理,在印刷压力的作用下,网点逐渐增大,造成糊版现象。
解决方法:对油墨作适当调整,以改变油墨的印刷效果。
对黏度小、流动性大的油墨,要在墨槽内加入适量原墨印刷工艺,以降低原有助剂的比例,或将原墨槽内的油墨清理干净,重新调配新油墨。
一般来说,只要能够正常供墨,以不发生纸张剥离困难、油墨的流动性偏小为宜数字出版,适当提高油墨黏度。
而对于因干燥剂添加过多引起的糊版现象,我们只能把原设备上使用的油墨全部清洗干净,更换上重新添加适量干燥剂调配好的油墨,特别注意不能靠增大版面水分的方法来解决此问题。
3.印刷出现脱墨现象
脱墨,顾名思义包装材料,就是油墨不能正常传递,不能正常地吸附在传墨辊、串墨辊、匀墨辊上,不能随墨斗正常地转动,不能吸附在出墨辊上或吸附后难以与出墨辊分离。
包装材料
就是所使用、调配出来的油墨黏度小、油墨流动性差,使油墨不能很好地吸附在墨辊上传递而出现脱墨现象。
其二是油墨干燥太快或油墨内的墨皮、残渣等杂质过多北人股份,使出墨辊上的油墨干结固化,阻塞了出墨辊与墨斗刀片之间的间隙,造成油墨无法传递。
其三是版
面水分太大,印版不上墨,同时会使大量水分被着墨辊带在匀墨部分印刷厂,造成油墨乳化现象,影响油墨的传递和下墨效果。
解决方法:根据不同情况,应分别对待解决。
若是油墨调配问题,可加入适当稀调墨油调稀一些;若是因油墨黏度小造成,则可在油墨中加入适量浓调墨油以增加油墨黏度;若油墨流动性差洗涤用品包装,可适当加入6号调墨油来增加其流动性;油墨干燥太快,则要减少干燥剂的用量。
出现脱墨现象时,应尽量减小版面水分并降低润版液的酸度,勤搅拌墨斗油墨并去除油墨内的墨皮,残渣等杂物。
4.印品印迹出现白斑点现象
这种现象是我们平时所说的拉纸毛现象印前设备,产生这种现象的原因主要是油墨黏度大、流动性小,油墨内的助剂加入量不合适造成的。
如燥油放得过多会使油墨黏度增强、变厚,油墨在机械压力作用下与纸张剥离的过程中,若纸张纤维之间的内聚力小于油墨间的内聚力,则纸张纤维结构就会被破坏设备,出现拉纸毛现象,在印品印迹上反映出白斑点,严重影响印品质量。
电子商务
入适量减黏剂来改变油墨的黏度;若油墨流动性差、墨层厚,则可在油墨中加入适量6号调墨油来稀释油墨,以提高油墨的流动性;如果因为油墨中的燥油过多包装设计,可加入适量的新墨搅拌,以降低燥油在油墨中所占比例,达到改变油墨性能的目的,从而适应印刷要求。
5.油墨乳化现象
胶印离不开水覆膜,也不能有过量的水。
墨与水经过一定机械压力最终要以乳状形式混合,水分成细小的液滴分散在油墨中,这种现象称为乳化现象。
油墨的乳化是始终存在的,只要是适量的乳化,乳化状态不再扩大RFID,水墨就是平衡的,应该是对印刷无害的。
洗涤用品包装
油墨乳化的形式一般有两种,一种是“油包水”,即水分散在油墨中;另一种是“水包油”,即油墨分散在水中。
正常的油墨乳化状态应该是“油包水”形式UV印刷,这种形式不扩大,它对油墨的性能就不会产生影响。
若此种形式再扩大,油墨中水量增加,就会发展到“水包油”形式的油墨乳化状态,油墨被乳化的成分中水多墨少标签,墨与水的平衡受到破坏,使油墨性能受到影响,从而出现油墨故障。
如脱墨、花版、脏版等现象,这种现象的存在,对印刷有很大的危害性排版,会使印迹变淡、失去光泽。
而润版液酸性过强是油墨乳化的最大原因,同时与油墨成分也有关系,如油墨颜料颗粒较粗、抗水性差、黏度不够。
不同品种的颜料物理结构和化学结构也不相同,抗酸性程度也不一样,因此与水挤压乳化的程度也不相同。
但酸性强的润版液在印刷中与油墨挤压接触后容易吸收水分而自身产生膨胀网络出版,逐渐与连结料脱离而产生乳化。
解决方法:当所使用的油墨产生严重油墨乳化现象时,应将设备上原有油墨清洗干净,更换新油墨重新调整油墨中助剂的用量,减少对油墨乳化影响较大的助剂,如调墨油、稀释剂、冲淡剂、干燥剂等的用量供水/润版,减少润版液内的酸性助剂的用量,降低润版液的酸度,控制好印刷时的水量等等。
纸箱纸盒
6.印品色彩发生变化
印刷过程中,印品色彩发生变化的现象,除水墨平衡的掌握外海德堡,同油墨的使用性能还有极大的关系。
油墨黏度大,易造成印品印迹色彩变暗,干燥速度减慢,增加油墨的用量;油墨黏度过小,印品色彩也会发生变化包装贸易,影响印品质量。
在调配油墨的过程中,油墨应该具有一定程度的黏度,以保证油墨在印刷中的顺利传递。
根据不同样张、印刷速度、机型等情况,对油墨的黏度要求也有所不同。
若印刷速度低于6000转/小时,油墨的黏度应适当高些数字印刷机,若速度高于6000转/小时,油墨的黏度应适当降低些。
印刷网线版时,
油墨的黏度可小些,印刷实地版时,油墨的黏度应适当提高些(因网线版与实地版在用墨量及墨层厚度上的需求不一样);从使用机型来说喷墨,单色机油墨黏度应适当高些,多色机油墨黏度应按印刷顺序逐渐降低,以避免上一色油墨层的剥离,保证前后色墨的正常叠印。
印前设备
用机型,对油墨的黏度进行合理调整数字印刷机,并保持油墨黏度的一致以保证印品色彩复原一致性。
7.印品出现网点缩小现象
网点是印刷图像的最小单位,也是吸附油墨的最小单位,我们称之为图像像素,它担负着传递原稿的色调和阶调的任务。
油墨对色彩的还原性主要通过油墨的色相、亮度、饱和度3方面来表现,色彩丰富的印品印刷工艺,要表现其色彩效果,主要通过三原色油墨,即黄,品红,青三色油墨网点多次叠加在一起制版,通过改变网点覆盖率,来表现丰富多彩的印品效果。
若在油墨转印过程中,油墨黏度大,屈服值高,造成油墨流动性差光盘印刷,使墨层在印版上铺展不开,此时即便是在印刷压力作用下使油墨铺展,印版网点上的油墨同样会因油墨黏度过大而向中心收缩,不能将印版网点完全复原至印刷纸张上,造成网点缩小现象。
晒版
以降低油墨的黏度。
油墨流动性差投资采购,则适量加入6号调墨油以改变油墨的流动性。